GKD 1 L Series User manual

TOTAL MOMENT INDICATOR
M1000002 V1.2 - 11/2021
COPYRIGHT NOTICE
Intended audience: This document contains sensitive
information. It may not be shared with other parties without
the express written permission of GKD Technologies Ltd.
INSTALLATION MANUAL

M1000002 V1.2 - 11/2021
www.gkdtechnologies.com 2
CONTENTS
Page
1 INTRODUCTION 4
1.1 System Layout 4
2 COMPONENT IDENTIFICATION 5
2.1 Series 1-L Display 5
2.2 Angle Sensor 5
2.3 Pressure Transducer 5
2.4 CAN to USB Interface 5
3 INSTALLATION 6
3.1 Series 1-L Display 6
3.2 Angle Sensor 6
3.3 Pressure Transducer 7
3.4 Alarm 7
4 SERIES 1-L GENERAL INFORMATION & WIRING (TYPE 1) 8
4.1 Alarm 8
5 SERIES 1-L GENERAL INFORMATION & WIRING TYPE 2) 9
5.1 Alarm 9
6 CAN BUS AND PRESSURE SENSOR WIRING 10
6.1 CAN Bus 10
6.2 Pressure Sensor 10

www.gkdtechnologies.com M1000002 V1.2 - 11/2021
3
Page
7 INITIAL SETUP 11
7.1 Machine dimensions with Boom Ram pushing from below the Stub Boom Pin 11
7.2 Machine dimensions with Boom Ram pulling from above the Stub Boom Pin 12
7.3 CAN Bus Connections 12
8 PC CONNECTION AND SOFTWARE 13
9 CALIBRATION 14
9.1 Stage 1 - Zero Angle Sensor 14
9.2 Stage 2 - Zero Pressure Sensor 15
9.3 Stage 3 - Data Logger On/O Control 15
9.4 Stage 4 - Set Maximum Moment 16
9.5 Verification 16
10 PC SETUP AND MONITOR 17
10.1 PC Connection 17
10.2 PC Indicator Monitoring 17
10.3 PC Advanced User 18
10.4 Calibrate Screen 18
APPENDIX - GKD USB DRIVER INSTALLATION 19

M1000002 V1.2 - 11/2021
www.gkdtechnologies.com 4
1 INTRODUCTION
This manual contains the installation and set-up instructions for the Series 1-L Total Moment
Indicator.
Installation should only be carried out by competent and trained sta as this product is a
safety product.
During installation it is assumed that industry standards will be observed and all cabling will
be protected against damage either from the movement of the machine or from collisions
that may occur during
normal operations (trees & branches, etc.)
All welding or bare metalwork should be treated to ensure that rust does not form.
1.1 System Layout
The system layout depends on which version of the Series 1-L is being installed.
• For the series 1 system layout, refer to page 9.
• For the series 2 system layout, refer to page 10.

www.gkdtechnologies.com M1000002 V1.2 - 11/2021
5
2 COMPONENT IDENTIFICATION
2.1 Series 1-L Display
The display unit utilizes a 4 LED indication of tipping moment based on 50 to 105 % of the
Alarm threshold. (As default, this is set to 66% of the hydraulic limit of the machine).
Indicates 105% of Alarm threshold
Indicates 100% of Alarm threshold
Indicates 75% of Alarm threshold
Indicates 50% of Alarm threshold
Indicates System Power is ON
Test Button:
When pressed and held, will make the LEDs
cycle from 50% green through to 105% RED
2.2 Angle Sensor
The Angle sensor should be fitted to the first excavator boom and
connected to the pressure transducer that is fitted to the main lift rams.
The sensor is connected to the display via a M12 0CAN bus cable. An LED
on the Angle Sensor flashes green to show that it is powered and working
correctly. Where possible, ensure that the green LED on the Angle Sensor
is visible during operation to show the Angle Sensor is working correctly.
2.3 Pressure Transducer
A pressure transducer is used to monitor the forward hydraulic pressure
in the boom lift ram. The pressure sensor connects to the angle sensor
module by a 4 way M12 cable. The forward pressure reading directly relates
to the load lifted by the machine. The sensor measures up to 400 Bar.
A second pressure transducer may be required to monitor the reverse side pressure ( rod
side ) for additional pressure compensation.
2.4 CAN to USB Interface
A USB to CAN Converter Interface is used to allow a PC to communicate
with the Series 1-L during initial set-up and for later monitoring purposes.
IMPORTANT NOTE: ENSURE USB DRIVERS ARE INSTALLED
FOR THE USB TO CAN CONVERTER. SEE GKD USB DRIVER
INSTALLATION NOTICE!

M1000002 V1.2 - 11/2021
www.gkdtechnologies.com 6
3 INSTALLATION
3.1 Series 1-L Display
The back of the display is fitted with a ball-joint mount. The joint base should be secured
with 2 x M5 bolts on fixing holes at 48.5mm spacing, and can be mounted on a horizontal,
angled, or vertical surface as appropriate. The display should be mounted within easy reach
of the operator, in a position that avoids direct sunlight on the indicator LEDs and exposure
to water ingress. Care should be taken to
ensure that the display is mounted to a surface or structure that is capable of supporting the
display when travelling over rough terrain.
A 2m long cable carries the DC supply and Change-over relay contact signals. The DC
Positive supply should be connected to an ignition switched power source and be protected
by a 5A fuse.
A 4 core, M12 cable is supplied to connect the Series 1-L Control Unit to the Angle Sensor.
Dierent lengths of cable, or extension cables are available as required on any particular
machine. The cable should be protected from physical damage during machine operation.
3.2 Angle Sensor
The sensor monitors the angle of an imaginary line drawn between the two articulation
points of the boom. For the best operation the sensor should be installed with the long edge
parallel to this imaginary line. Position and oset from the imaginary line should achieve the
best location taking factors such as cable runs and protection into consideration.
The sensor is provided with a mounting bracket that should be welded to the boom and
painted to the boom colour.
A green LED on the Angle Sensor flashes when it is working correctly. An M12 cable then
runs from the Angle Sensor to the pressure sensor M12 connector.
Diagrams show typical angle sensor Pre-boom (stub) locations and orientations.
If boom CAN be set to zero
Max AngleAngle Sensor
Ram Stub Pin
Stub Boom Pin
If boom CANNOT be set to zero
Angle Sensor
Ram Stub Pin
Stub Boom Pin
Max Angle

www.gkdtechnologies.com M1000002 V1.2 - 11/2021
7
3.3 Pressure Sensor
Pressure sensors use a G1/4 hydraulic interface to the machine hydraulics.
The ram full side pressure transducer, and the optional reverse side (rod side) pressure
transducer, must measure the pressure in the lift ram at all times. Therefore, the measuring
point must be on the ram side of any hose burst check valves that may be fitted. This port
is often designated with an ‘E” stamped into the valve body. If in doubt check. [Note hoses
should be fitted with restrictors (typically with a 0.75mm hole) to control the rate of descent
of the boom in the event of failure of the balance hose].
The pressure sensors should be mounted in such a position that the electrical connector may
be accessed and the cable securely routed. The mounting position should also protect against
damage caused by persons climbing the machine or other objects striking the machine.
Typical pressure transducer installations.
3.4 Alarm
The alarm is wired as a relay change over contact output and uses 3 wires in the Series
1-L Display power cable. The output has a limited current capability of 1A. Any alarm that
exceeds this current capability will need to be controlled via another relay.

M1000002 V1.2 - 11/2021
www.gkdtechnologies.com 8
4 SERIES 1-L GENERAL INFORMATION & WIRING (TYPE 1)
The Series 1-L Type 1 system is CAN based and requires only use of a four wired daisy chain
interconnection to function. However, to facilitate the installation the CAN bus may be
branched.
The system utilizes industry standard M12 connectors which are field serviceable. Cable
looms can be provided to ensure plug and play installation.
Power connections to the system are as per the table below.
NOTE: THIS IS THE
CABLE PROTRUDING
FROM THE BASE OF
THE DISPLAY UNIT
NOT THE M12.
4.1 Alarm
The alarm is wired as a relay change over contact output and uses 3 wires in the Series
1-L Display power cable. The output has a limited current capability of 1A. Any alarm that
exceeds this current capability will need to be controlled via another relay.
Supply Description Wire Fuse Rating
Switched Ignition (+12/24V DC) Red 5A
System Ground (0V) Black 5A
Duty Select (0V = Duty 2) White Not Required
Overload Alarm Wire Fuse Rating
COM Blue 1A
N/O Yellow 1A
N/C Green 1A
9
GKD Technik LtdM1000002
1TMI Series 1 General informaon & wiring
The 1TMI Series 1 system is CAN based and requires only use of a four wired daisy chain interconnecon
to funcon. However, to facilitate the installaon the CAN bus may be branched.
The system ulizes industry standard M12 connectors which are eld serviceable. Cable looms can be
provided to ensure plug and play installaon.
Supply Descripon Wire Fuse Rang
Switched Ignion (+12/24V DC) Red 5A
System GND (0V) Black 5A
Duty Select (0V = Duty 2) White Not Required
Alarm
The alarm is wired as a relay change over contact output and uses 3 wires in the 1TMi Display power
cable. The output has a limited current capability of 1A. Any alarm that exceeds this current capability
will need to be controlled via another relay.
Overload Alarm Wire Rang
COM Blue 1A
N/O Yellow 1A
N/C Green 1A
Supply +12/24V DC
Ground/Supply 0V
Alarm or
Solenoid
Angle
Sensor
Pressure
Transducer
Normally Open relay
contact is used so that an
Alarm funcon is o if the
1TMI is unpowered, in a
Fault state, or in a
load-limited state.
M12 CAN Cable
G
L
A
N
D
Duty Input
Power connecons to the system
are as per the table to the right.
NOTE: THIS IS THE CABLE
PROTRUDING FROM THE BASE OF
THE DISPLAY UNIT NOT THE M12.

www.gkdtechnologies.com M1000002 V1.2 - 11/2021
9
5 SERIES 1-L GENERAL INFORMATION & WIRING (TYPE 2)
The Series 1-L Type 2 system is CAN based and requires only use of a four wired daisy chain
interconnection to function. However, to facilitate the installation the CAN bus may be
branched. The Series 1-L Type 2 Unit oers 2 Relay outputs and can be connected to a data
Logger unit to monitor and store operation of the vehicle.
The system utilizes industry standard M12 connectors which are field serviceable. Cable
looms can be provided to ensure plug and play installation.
Power connections to
the system are as per
the table to the right.
NOTE: THIS IS THE
CABLE PROTRUDING
FROM THE BASE OF THE DISPLAY UNIT NOT THE M12.
5.1 Alarm
The alarm is wired as a relay change over contact output and uses 3 wires in the Series
1-L Display power cable. The output has a limited current capability of 1A. Any alarm that
exceeds this current capability will need to be controlled via another relay.
Supply Description Wire Fuse Rating
Switched Ignition (+12/24V DC) Red 5A
System Ground (0V) Black 5A
Duty Select (0V = Duty 2) White Not Required
10
GKD Technik LtdM1000002
1TMI Series 2 General informaon & wiring
The 1TMI Series 2 system is CAN based and requires only use of a four wired daisy chain interconnecon
to funcon. However, to facilitate the installaon the CAN bus may be branched. The 1TMI Series 2 Unit
oers 2 Relay outputs and can be connected to a data Logger unit to monitor and store operaon of the
vehicle.
The system ulizes industry standard M12 connectors which are eld serviceable. Cable looms can be
provided to ensure plug and play installaon.
Supply Descripon Wire Fuse Rang
Switched Ignion (+12/24V DC) Red 5A
System GND (0V) Black 5A
Duty Select (0V = Duty 2) White Not Required
Alarm
The alarm is wired as a relay change over contact output and uses 3 wires in the 1TMi Display power
cable. The output has a limited current capability of 1A. Any alarm that exceeds this current capability
will need to be controlled via another relay.
RL1 Wire RL2 Wire RangRL1 RL2
Blue Blue 1ACOM COM
Yellow Violet 1AN/O N/O
Green Brown 1AN/C N/C
Supply +12/24V DC
Ground/Supply 0V
Alarm or
Solenoid
Angle
Sensor
Pressure
Transducers
Normally Open relay
contact is used so that an Alarm
funcon is o if the 1TMI is
unpowered, in a Fault state, or
in a load-limited state.
M12 CAN Cable
G
L
A
N
D
Duty Input
Power connecons to the system
are as per the table to the right.
NOTE: THIS IS THE CABLE
PROTRUDING FROM THE BASE OF
THE DISPLAY UNIT NOT THE M12.
Data Logger
A = Full Side
B = Rod Side (Oponal)
A
B

M1000002 V1.2 - 11/2021
www.gkdtechnologies.com 10
6 CAN BUS AND PRESSURE SENSOR WIRING 10
6.1 CAN Bus
The CAN bus connections are as follows:
The angle sensor and display connect to a CAN bus. Hi speed CAN bus is provided as an
interface to exchange information within the system and may be used to set-up or monitor
the system using the USB to CAN converter and special Series 1-L PC software.
The Hi-speed CAN is custom programmed during production.
6.2 Pressure Sensor
NOTE: Pressure transducers do not use the same wiring as the CAN bus, where pressure
transducers are being connected, the following applies:
CAN Lo +V Supply 0V (Ground) CAN High
CAN Bus M12 Connector Pin 1 - Brown Pin 2 - White Pin 3 - Blue Pin 4 - Black
+V Supply Signal 2 0V (Ground) Signal 1
Single Pressure Switch Pin 1 - Brown Pin 2 - N/C Pin 3 - Blue Pin 4 - Black

www.gkdtechnologies.com M1000002 V1.2 - 11/2021
11
7 INITIAL SETUP
When all of the components have been installed then the system is ready for Calibration.
Diagrams below show typical measurements for Stub with pulling Ram.
7.1 Machine dimensions with Boom Ram pushing from below the Stub Boom Pin
Measure and record the vital machine dimensions X1, X2, Y1, Y2 in mm as shown below.
Note that the measurements may need to be entered as Positive or Negative values,
depending on the precise geometry of the machine.
If boom CAN be set to zero
Max AngleAngle Sensor
Ram Stub Pin
Stub Boom Pin
If boom CANNOT be set to zero
Angle Sensor
Ram Stub Pin
Stub Boom Pin
Max Angle
Stub Boom Pin
Ram Chassis Pin
X1: Typically
+280mm
X2: Typically
+1450mm
Y2: Typically
+760mm
Ø
Y1:
Typically
-430mm
Machine dimensions with
Ram pushing from below
the Stub Boom Pin.
DISTANCES BETWEEN
STUB BOOM PIN &
RAM CHASSIS PIN ARE
NEGATIVE DOWN OR
BACK.

M1000002 V1.2 - 11/2021
www.gkdtechnologies.com 12
7 INITIAL SETUP (CONT.)
7.2 Machine dimensions with Boom Ram pulling from above the Stub Boom Pin
Measure and record the vital machine dimensions X1,
X2, Y1, Y2 in mm as shown below.
7.3 CAN Bus Connections
Connect the USB to CAN Converter interface to a USB
port of a PC and through an M12 “T” connector into
the CAN bus of the Series 1-L system. This ensures that
the Angle Sensor M12 connection is still made during
the set-up and calibration process.
IMPORTANT NOTE: ENSURE USB DRIVERS ARE
INSTALLED FOR THE USB TO CAN CONVERTER. SEE
APPENDIX - GKD USB DRIVER INSTALLATION NOTE.
Apply power to the Series 1-L System.
Stub Boom Pin
Ram Chassis Pin
X1: Typically
-280mm
X2: Typically
+1450mm
Y2: Typically
+760mm
Ø
Y1:
Typically
+430mm
Machine dimensions with
Ram pulling from above
the Stub Boom Pin.
DISTANCES BETWEEN
STUB BOOM PIN &
RAM CHASSIS PIN ARE
NEGATIVE DOWN OR
BACK.

www.gkdtechnologies.com M1000002 V1.2 - 11/2021
13
8 PC CONNECTION & SOFTWARE
IMPORTANT NOTE: ENSURE GKD USB DRIVERS ARE INSTALLED FOR THE USB TO CAN
CONVERTER. SEE APPENDIX - GKD USB DRIVER INSTALLATION NOTE.
On a laptop PC create a new directory named with the Machine Type/Serial Number of the
crane on which the Series 1-L system is to be installed. Copy the latest GKD Series 1-L PC
software supplied (e.g. GKD1TMI2.xx.exe) into the new directory and double click on that file
to run the software. The following screen appears:-
Click the COM Port selection and the dropdown menu shows active USB ports. Select the
port that is connected to the GKD USB to CAN Interface. A message “USB-CAN Found”
appears at the bottom left of the screen.
Enter the values X1, X2, Y1 & Y2, in mm, for the machine being calibrated. Set the required
Alarm Threshold as a % of the maximum allowed capacity. Set Angle Reversed if the Angle
sensed seems to decrease as the boom rises (depends on the Angle Sensor orientation as
fitted on the boom).
When the data is complete, click “Send Data to Interface Unit” to download the data via the
interface unit into the Series 1-L controller. A message “Data Transmitted” appears at the
bottom left of the screen.
IMPORTANT: WRITE DOWN & KEEP A CAREFUL RECORD OF THE CALIBRATION DATA!
The Series 1-L is now set up ready for calibration..

M1000002 V1.2 - 11/2021
www.gkdtechnologies.com 14
9 CALIBRATION
Set up & Calibration of the Series 1-L is achieved in 4 stages:
1) Zero Angle sensor setting (75% LED Lit in Calibrate mode).
2) Zero Pressure sensor setting for no-load condition (100% LED Lit in Calibrate mode).
3) Data logger function On or O control (75 & 100% LEDs lit in Calibrate mode).
4) Maximum Tipping Moment setting (50% LED Lit in Calibrate mode).
Make sure the machine data has been entered into the Series 1-L as described on the
previous page. Ensure that there is a clear area around the machine and that there is no
danger to personnel.
Position the magnet supplied, as shown, on
top of the display box using adhesive tape or
Blu-Tac to enable Calibration to be performed
(Stops inadvertent setting changes).
9.1 Stage 1 - Zero Angle Sensor
Place the machine on level ground. Lower the boom to the Horizontal position with No load.
The position of any Dipper or Extending Boom fitted does not matter at this stage as it only
zeros the Angle Sensor reading at Horizontal.
Ensure the magnet is fitted on the top of the display as shown above. The Display will be in
Indicator mode. (Probably just bottom green “Power On” indicator lit.)
Press and hold the RED test button for more than 3 seconds to enter the Calibrate mode. All
the LEDs come on to show it is now in Calibrate mode. Release the Red button and the top !
Red and bottom green Power On LEDs are lit, as well as the 50% Green LED.
!! DON’T REMOVE THE MAGNET !!
REMOVING IT, OR NO ACTIVITY FOR 100 SECS WILL EXIT THE CALIBRATE MODE.
Press the Red button momentarily. The 75% LED lights to show “Zero Angle Sensor” mode.
Press & hold the Red button for over 2 secs to make the Series 1-L Acquire and Store the
Angle Sensor reading representing the Horizontal Boom position.
Now release the button. All the LEDs should come on momentarily, then all but the Green
Power On LED go o before all the LEDs come on momentarily again to confirm the
Zero Angle has been acquired and stored. The unit will then go from Calibration mode to
Indicator mode with just the Green Power LED lit.

www.gkdtechnologies.com M1000002 V1.2 - 11/2021
15
9 CALIBRATION (CONT.)
9.2 Stage 2 - Zero Pressure Sensor
With No Load and the machine set to the minimum radius combination of the boom, dipper
or any extending boom fitted, the hydraulic ram pressure will be at the minimum value
supporting the weight of the boom etc. but no load.
Ensure the magnet is fitted on the top of the display as shown on page 14. The Display will
be in Indicator mode. (Probably just bottom green “Power On” indicator lit.)
Press and hold the RED test button for more than 3 seconds to enter the Calibrate mode. All
the LEDs come on to show it is now in Calibrate mode. Release the Red button and the top !
Red and bottom green Power On LEDs are lit, as well as the 50% Green LED.
!! DON’T REMOVE THE MAGNET !!
REMOVING IT, OR NO ACTIVITY FOR 100 SECS WILL EXIT THE CALIBRATE MODE.
Press the Red button twice. The 100% LED lights to show “Zero Pressure Sensor” mode.
Press & hold the Red button for over 2 secs to make the Series 1-L Acquire and Store the
Pressure Sensor reading representing the No Load pressure.
Now release the button. All the LEDs should come on momentarily, then all but the Green
Power On LED go o before all the LEDs come on momentarily again to confirm the
Zero Angle has been acquired and stored. The unit will then go from Calibration mode to
Indicator mode with just the Green Power LED lit.
9.3 Stage 3 - Data Logger On/O Control
Ensure the magnet is fitted on the top of the display as shown on page 14. The Display will
be in Indicator mode. (Probably just bottom green “Power On” indicator lit.)
Press and hold the RED test button for more than 3 seconds to enter the Calibrate mode. All
the LEDs come on to show it is now in Calibrate mode. Release the Red button and the top !
Red and bottom green Power On LEDs are lit, as well as the 50% Green LED.
!! DON’T REMOVE THE MAGNET !!
REMOVING IT, OR NO ACTIVITY FOR 100 SECS WILL EXIT THE CALIBRATE MODE.
Press the Red button three times. The Red 100% & Yellow 75% LEDs will light to show the
unit is in Data logger Control Mode (If both 100% & 75% LEDs don’t light the unit may not be
equipped with the Data logger control function, and may need to be upgraded).
If the Red “!” LED is lit as well as the 100% & 75% LEDs the Data logger is enabled. If the Red
“!” LED is NOT lit but the 100% & 75% LEDs are lit the Data logger is disabled (If you don’t
want to change the Data logger status, remove the magnet at this point).
With the magnet in place, to swap the Data logger function from On to O, or O to
On, press and hold the Red button for more than 2 seconds. All the LEDs then come on
momentarily, All but the Green LED then go O, All the LEDs then come On momentarily to
show the Data logger function has changed. The unit will then go from Calibration mode to
Indicator mode with just the Green Power LED lit.

M1000002 V1.2 - 11/2021
www.gkdtechnologies.com 16
9 CALIBRATION (CONT.)
9.4 Stage 4 - Set Maximum Moment
With the machine set to the maximum radius combination of the boom, dipper or any
extending boom fitted, and apply the maximum load rated for that machine at the maximum
radius position. This represents the Maximum Moment allowed.
Ensure the magnet is fitted on the top of the display as shown on page 14. The Display will
be in Indicator mode. (Probably just bottom green “Power On” indicator lit.)
Press and hold the RED test button for more than 3 seconds to enter the Calibrate mode. All
the LEDs come on to show it is now in Calibrate mode. Release the Red button and the top
! Red and bottom green Power On LEDs are lit, as well as the 50% Green LED. This indicates
that it is in “Maximum Moment” set-up mode.
!! DON’T REMOVE THE MAGNET !!
REMOVING IT, OR NO ACTIVITY FOR 100 SECS WILL EXIT THE CALIBRATE MODE.
Press & hold the Red button for over 2 secs to make the Series 1-L Acquire & Store the
“Maximum Moment” pressure, showing the MAXIMUM MOMENT state.
Now release the button. All the LEDs should come on momentarily, then all but the Green
Power On LED go o before all the LEDs come on momentarily again to confirm the Zero
Pressure has been acquired & stored.
The unit will then go from Calibration mode to Indicator mode with all the LEDs lit as the
machine is in a maximum moment condition. Reduce the load to return normal operation.
Repeat with Duty Input set to Duty 2 (Duty input, white wire, grounded or connected to 0V)
if a second duty is to be used.
THE Series 1-L IS NOW CALIBRATED.
NOTE: REMOVE THE MAGNET SO THAT THE CALIBRATION CANNOT BE MODIFIED.
9.5 Verification
To verify the calibration, select random positions & lift duties. Check overload warning
against tip load.

www.gkdtechnologies.com M1000002 V1.2 - 11/2021
17
10 PC SETUP & MONITOR
The PC software is used to enter the initial machine data, X1, X2 etc. but can also be used
to monitor the condition of the machine, store the calibration settings and even adjust the
calibration settings as required.
10.1 PC Connection
The machine data etc. is entered
and sent to the Series 1-L Control
unit as described in the Initial
set-up section on page 13.
10.2 PC Indicator Monitoring
Click on the Calibrate heading
on the command line and the
Indicator screen, shown below,
appears.
The Calibrate box is inactive
(“Greyed Out”). The current
values of the Series 1-L Angle
& Pressure are shown, with
numbers representing the
current Load Moment and the
Capacity (Maximum Moment) of
the system. A Bar Column on the
left mimics the Green, Amber
& Red LEDs on the Series 1-L
Display unit. Increasing the load
will be shown as an increase in Load Moment. Increasing the boom angle (decreasing the
radius) will be shown as a decrease in Load Moment.

M1000002 V1.2 - 11/2021
www.gkdtechnologies.com 18
10 PC SETUP & MONITOR (CONT.)
10.3 PC Advanced User
In the Indicator screen, enter the
Password 861961. The central
Calibrate box now becomes
active (not greyed out). Click
the Calibrate box and enter the
Calibrate screen.
10.4 Calibrate Screen
In the Calibrate screen, click
“Receive Settings” to download
the Series 1-L Calibration values
of Angle, Zero Pressure and
Maximum Moment set up in the
calibration process conducted
on the machine in the Calibration
section on page 15. A message is
shown to confirm data received.
The Received data is stored
in a data file held in the same
directory as the GKD1TMI.exe
file, which can be viewed by a
PC text editor. The Calibrate
data can be recovered from the
stored file or edited on the screen as necessary for fine adjustments to be made. The data
can be uploaded back to the Series 1-L by clicking “Send Settings”.

www.gkdtechnologies.com M1000002 V1.2 - 11/2021
19
APPENDIX - GKD USB DRIVER INSTALLATION
Introduction
The GKD USB to CAN Converter includes an FTDI USB interface chip and a special Windows
driver is needed to allow the GKD Series 1-L PC software to use a USB port to talk to the
Series 1-L Display Unit. This note details how the driver software can be installed.
Windows version
The version of USB Driver required for a particular PC may depend on which version of
Windows operating system is installed on that PC. Many modern computers with Internet
access may automatically search for a suitable driver on the internet and install it for you.
Older PCs, or where there is no Internet access, may require the drivers to be available on
the PC already and a Windows Driver Installation Wizard told where to look for the driver.
Note that ONLY Windows XP, Vista & Windows 7 are supported.
Plug in USB to CAN Converter and install drivers
Plug the USB to CAN converter into a USB port and a Found New Hardware report is seen
indicating a USB Serial port. A Found New Hardware Wizard appears, as shown below:
If the PC has Internet Access you may be able to set the “Yes, this time only” button and
click Next for the PC to find and install the right driver. Advice may also be obtained from
the FTDI website on how to obtain a suitable VCP driver for their USB chip.
If there is no Internet Access, or a driver can’t be found then at this stage click the “No, not
this time” button and Next. A new screen appears asking for the location of the driver file.
If Windows can’t find a driver load driver interface files onto PC
If windows can’t find a driver, or there is no internet access, GKD supplies driver files on a
CD. Create a new “USB Driver” folder on the PC, typically entitled C:\USB Drivers, and load
GKD’s driver folder from the CD into that folder. The folder is typically called “USB FTDI
Drivers”.
In the “USB FTDI Drivers” folder there should be two .pdf files that give instructions for
Windows XP and Windows 7 Computers Installations. Typically run the setup file:
CDM 20814_ Setup.exe to run the installation file & load drivers.
The USB to CAN Converter should now work correctly with the GKD Series 1-L PC software.

©GKD Technologies 11-2021
GKD Technologies reserve the
right to change these instructions in
line with the policy of continuous improvement.
17 Cobham Road, Ferndown Industrial Estate, Wimborne, Dorset, UK. BH21 7PE
+44 (0)1202 861 961 sales@gkdtec.com www.gkdtechnologies.com
DISCLAIMER
Incorrect installation of any part and or incomplete calibration
will aect the correct operation of the Series 1-L.
If in doubt contact GKD Technologies.
Table of contents
Other GKD Measuring Instrument manuals
Popular Measuring Instrument manuals by other brands
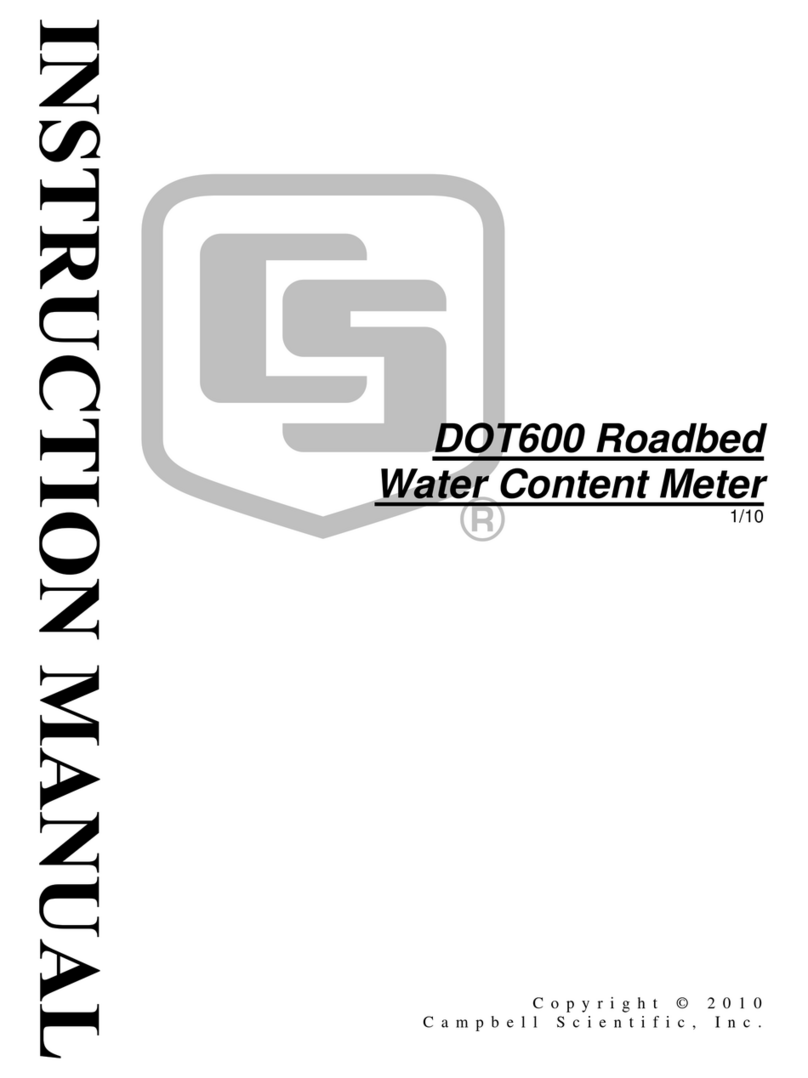
Campbell
Campbell DOT600 instruction manual

Globalstar
Globalstar LinkStar-STX3-ME quick start
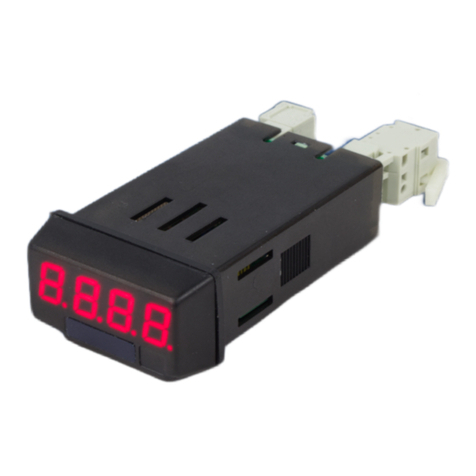
London Electronics
London Electronics PICA-P manual
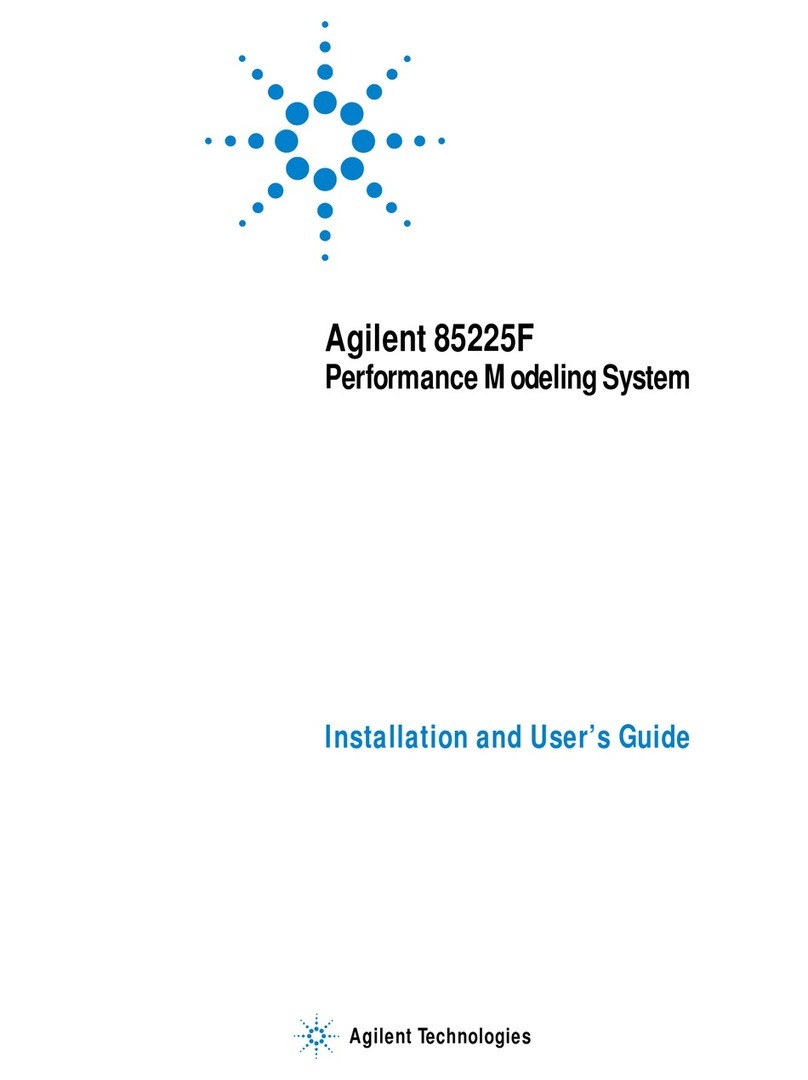
Agilent Technologies
Agilent Technologies 85225F Installation and user guide
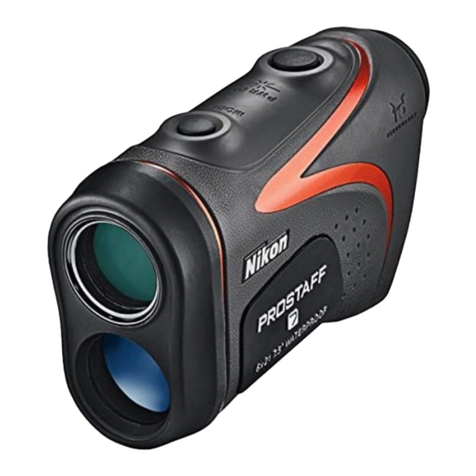
Nikon
Nikon PROSTAFF 7 instruction manual
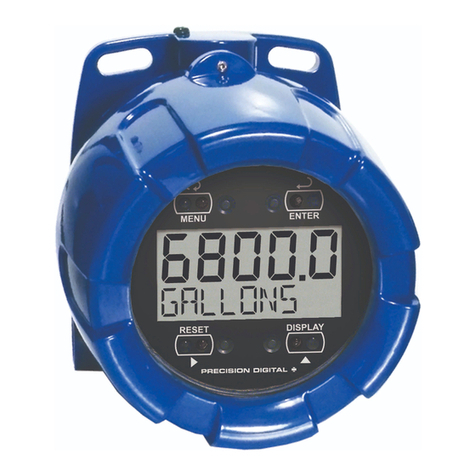
Precision Digital Corporation
Precision Digital Corporation ProtEx-Pro PD6800 instruction manual