GPS Prueftechnik Digital Colour Analyzer User manual

02.11.2018 1
User Manual for Digital Colour Analyzer
GPS Prueftechnik GmbH
www.gps-prueftechnik.de
E-Mail: info@gps-prueftechnik.de

02.11.2018 2
1. LED Digital Colour Analyzer
1.1 Mounting the Digital Colour Analyzer
1.2 Mounting the fiber-optic
1.3 Cutting the fiber
2. Interface and Power Wiring
2.1 Mounting a stand-alone unit
2.2 Mounting connected units
2.3 Mounting interconnected units for USB
2.4 Mounting interconnected units for RS 232
3. Setting the Digital Colour Analyzer
3.1 The Digital Colour Sensor
3.2 Setting an offset to calculate the components of the standard colour values x and y
3.3 Manual for the GPS LED Analyzer Software
3.3.1 The main screen of the LED Analyzer Software with PopUp-menus
3.3.2 Configuration of the LED Analyzer
3.3.3 To perform a measurement by using the functional elements of the main screen
3.3.4 To perform a measurement and compare several LEDs by using
“Measurement Window” and “Settings Window”.
3.3.5 How to use “Terminal Modes”
4. List of Commands for the LED Analyzer
Table of contents:

02.11.2018 3
1.LED Digital Colour Analyzer
The construcon of the xture is one of the most crical aspects of a successful implementaon of the Digital Colour
Analyzer. If this step is implemented properly the resulng tests will be more stable and repeatable with low risk of
false failures.
Figure 1: GPS Digital Colour Analyzer
1.1 Mounting the Digital Colour Analyzer
The LED Analyzer can be mounted on the top as well as on the bottom side of the fixture.
When mounting the LED Analyzer be careful that the fibers can move freely and are not exposed to sharp bends.
The minimum bend radius is 15 mm. Sharper bends can cause a loss of light which can affect the measurements.
In order to get a clean measurement it must be guaranteed that all light from the LEDs can travel through the fiber
to the sensor on the board.
Figure 2: Mounting measurements
The mounting holes will accept M3 screws. Take care that the mounting holes are connected to the unit
ground

02.11.2018 4
1.2 Mounting the fiber optic
Figure 3: Plastic Fiber
Figure 4: Positioning the Fiber
The fiber must be located over optical centre of the LED. For further information please look up the producers
datasheet. The gap between the LED and the fiber should be 1 - 3 mm.
This must be find out empirical in individual cases.
Figure 5: Offset and Gap
The intensity of a measurement depends strongly on the gap and the offset from the LED to the fiber.
Construction of the fixture is one of the most critical aspects of a successful implementation of a LED Colour
Analyzer. If this step is implemented properly the resulting tests will be more stable and repeatable with a low
risk of false measurements.
Some important characteristics of the fiber are:
Minimum bend radius 10mm
Operating temperature range –40 to +70 C°
Numerical aperture 0.5
Angle of incidence ca. 60 degrees
Attenuation at 650 nm 0,18 dB/m (ca. 2%/m)

02.11.2018 5
1.3 Cutting the Fiber
The fibers of the LED Analyser are delivered standardly with a length of about 600 mm.
To avoid damages it is recomended to shorten the fibers to the correct length.
While cutting take care that the fiber is in a 90° to the razor otherwise a loss of light has to be expected.
It is recommended to use each hole only once in order to guarantee a clean cut of the fiber.
2. Attachment for thin fibers:
Additional to the 75mil sockets you can also use the attachment E39-F9 In that case the fixing with silicon is
not necessary.
The advantage: the fiber is fixed permanently and can be changed easily if required.
There are different possibilities to position a fiber above the LED which has to be tested.
1.Mounting with a 75 mil socket:
The recommended method of mounting the fiber is using the supplied 1mm ID, with a 75 mil socket. Another advantage
of the socket is the internal indentation, which fixes the fiber effectively in position during the debugging.
After the debugging the fiber can be held in position using a small dot of silicon adhesive.
Figure 6: 75 mil Socket
Figure 8: Cutting tool for the fibers
Figure 7: Attachment E39-F9

02.11.2018 6
2. Interface and Power Wiring
2.1. Mounting a stand-alone unit for USB Interface
The Digital Colour Analyzer can be operated by RS 232 as well as by an USB Interface.
During RS 232 operating a voltage of 7-15V, 80mA has to be applied additionally.
RS 232 Connect:
Female 2, Pin 23 Rx 2 RS 232 Kabel: Pin 2 Tx 2 yellow mark
Pin 24 Tx 2 Pin 3 Rx 2
Pin 25,26 GND Pin 5 GND
Female 2, Pin 23,24 Jumper (if using several boards the jumper has to be set only at the last board)
Supply Voltage:
Setting Jumper
Female 2, Pin 1,2 U In 7-15V
Pin 5,6 GND
BR1 Pin 2+3 Jumper
RS 232 cable can be ordered from GPS.
Figure 9: Physical Layout

02.11.2018 7
2. Interface and Power Wiring
2.2. Mounting a stand-alone unit for RS 232 Interface
The Digital Colour Analyzer can be operated by RS 232 as well as by an USB Interface.
During USB operating the power supply for the board takes place through the USB Interface.
USB Connect: USB Cable:
Connector BU2,Pin 29 +5V USB Female: Pin1 (yellow mark) USB Connector: Pin 1 +5V
Pin 30 —Pin2 — —-
Pin 31 Data- Pin3 Data- Pin 2 Data -
Pin 32 Data+ Pin4 Data+ Pin 3 Data +
Pin 33 GND Pin5 GND Pin 4 GND
Pin 34 —Pin6 — —-
BR1 Pin 1+2 Jumper
USB cable can be ordered from GPS.
Figure 9: Physical Layout

02.11.2018 8
USB Connect:
Pin-strip Pin 29,30 +5V USB Cable: Pin 1+5V yellow mark
Pin 31 Data- Pin 2Data -
Pin 32 Data+ Pin 3Data +
Pin 33,34 GND Pin 4GND
Bridge Pin 1+2 Jumper for USB operating
Current receiving is 80 mA for each device. With USB you can support up to 5 devices (max. 400 mA)
Data-bus: Board 1 up to N-1: Pin 19 Rx4 Board N: Pin 24 Tx2
Pin 20 Tx4 Pin 23 Rx2
Pin 6 GND Pin 5 GND
Pin 4 5V Pin 3 5V
Pin 19, 20 Jumper
Figure 10a: Connection Dia-
2.2. Mounting interconnected units for USB
If the power input is 80 mA per board
up to 5 boards can be operated through
the USB Interface.
(Complete supply voltage about 400mA).
In this case the LED Colour Analyzer can
be tested 25 LEDs.
See the physical layout below:

02.11.2018 9
2.4. Mounting interconnected units for RS 232
The Digital Colour Analyzer can be connected
to 99 boards so that 495 LEDs can be tested.
See the physical layout below:
RS 232 Connect:
Female2, Pin 23 Rx 2 RS 232 Cable: Pin 2 Tx 2 yellow mark
Pin 24 Tx 2 Pin 3 Rx 2
Pin 25,26 GND Pin 5 GND
Data Bus:
Female2, Pin 19 Rx 4 Pin 21,22GND
Pin 20 Tx 4
Pin 23 Rx 2 Pin 25,26GND
Pin 24 Tx 2
Last board setting Jumper
Female 2, Pin 19,20 Jumper
Supply Voltage: Each board has an own power supply unit and can be operated + 7V to 15V (power input about 80mA).
Female 2, Pin 1,2 U In 7-15V
Pin 5,6 GND
BR1 Pin 2+3 Jumper USB and RS 232 cable can be ordered from GPS .
Figure 10b: Connecting Diagram

02.11.2018 10
3. Setting the Digital Colour Analyzer
After the software has been installed and the Digital Colour Analyzer has been attached the following settings have to be
respected.
Configuration:
Interface
The USB Port is configured as a virtual Com Port and will be designated a name such as Com5, Com6, etc.
The Baud Rate can be changed to any between 9600 and 115200 .
Set the serial port to Auto and the baud rate to 115200.
The Digital Colour Analyzer Test Program is a graphical tool that can be used to send commands and receive results
from the Analyzer.
One LED can be tested at a time. The results are stored in a data e.g. TestReport.txt.
This program allows to determine the correct setting for the LED which has to be tested.
For further details, please refer to chapter 3.3.3 .
Alternately, a customised program may be generated that sends commands and receives data through the virtual
USB Com Port or RS 232 interface.
Figure 11: Settings

02.11.2018 11
3.1 The Digital Colour Sensor
To enable a measurement over a wide range of illuminance, the photodiode sensitivity can be selected by
modes ( high sensitivity mode and low sensitivity mode). The photodiode active area which is used to
measure the light depends on which sensitivity mode has been selected
(high sensitivity mode: 9x9 elements, low sensitivity mode: 3x3 elements in center).
Figure12: Digital Colour Sensor
Beneath the modes High Sensitivity Mode and Low Sensitivity Mode the light intensity also can be affected by a
measure time of 1ms to 10000 ms . Under Test Modes „Fast Capture“ the most important settings which allow
to measure very dim and very bright LEDs without operating with additional mechanical filter are listed.
The Digital Sensor measures the colours and the intensity of the LED that has to be tested in RGB size.
The results can be shown as RGBI, HUE and Saturation or CIE Chromaticity Diagram.

02.11.2018 12
3.2 Setting an offset to calculate the tristimulus values x and y
There are three possibilities to store an offset for the calculation of the tristimulus values x and y.
These are explained in the following:
1. GPS Prüftechnik offers a service for the calibration of the LED Analyzer Board. In this process customers
LEDs to be tested are measured with a proven calibrated spectrometer under a standardized process in
our company. In the next step tristimulus values which have been measured with the LED Analyzer are
adjusted to the values of the spectrometer. This takes place during uploading the firmware using a
non-volatile stored offset.
2. In addition to that there is a possibility to integrate the LED Analyzer in an existing test system through
an initialisation of the com-port and a command listed in chapter 4. At this application an offset for each
LED that has to be measured can be stored using the commands “setxoffset#+-0.xxxxb” or
“setyoffset#+-0.xxxxb” . However this is a volatile stored offset which get lost after switching off the board
from the current source or after using the command “setdefaultb”.
3. Furthermore an offset can be stored using the included software GPS LED Analyzer. This is, as
described in point 2, a volatile storage space and get lost after switched off from the current source or the
command “Reset board”. The following steps explain how an offset can be stored at the board using the
software.
Regarding to the LED Analyzer Software it has to be mentioned that stored offsets and modifications were
taken over and are shown in the menu displays “Measurement settings” or “Setting for sensor” only during
the measurement. See details for setting and adjusting an offset in chapter 3.3.4 .
Below you will find a brief explanation of an offset setting.
To set an offset through the LED Analyzer Software the ticker in the control box at “Don’t allow any
changes to the xy offset values” has to be removed. You find this control box under “Configuration” in
The PopUp-menu “Communication” In the next step you open “Measurement settings” under the PopUp-
Menu “Test” After opening all sensors, which are on the board , and their setting parameters are shown.
Now chose through double click on the line the wanted sensor to change the settings. Then the menu
display “Settings for sensor” appears (see figure below). To set an offset for the chromaticity coordinates
x and y it has to be guaranteed that the ticker in the control box “Don’t change x y offset” is removed.
After setting the wanted offsets close the “Settings for sensor” display through the OK-button.
Figure 13: Settings

02.11.2018 13
3.3.1 The main screen of the LED Analyzer Software with PopUp-menus
After starting the LED Analyzer Software the main screen appears (see figure below). Through this main screen you reach
all required functions and control elements.
The upper line shows several PopUp-menus which are explained shortly below and are described in details in the follow-
ing chapters:
File Through this menu you close the software.
View Through this you can change between the colour spaces, which are shown in the right half.
For that the HSI colour wheel, the RGB colour palette and the CIE colour space is available.
Using the CIE colour space you can chose between three representations through the menu
“Communication“ → „Configuration“. You find the particular measurement values of the several
colour spaces in the right half of the „Test result“ display.
Communication Through this the LED Analyzer Board is connected or disconnected. Furthermore the
configuration settings of the LED Analyzer can be opened through the
„Communication“ menu (see chapter 3.3.2).
Test Through the „Test“ PopUp menu the manual for measuring and comparing several
LEDs is opened (see chapter 3.3.4). In addition test reports can be stored an opened.
The function „Reset board“ is used if offsets were set during the operating and the initial
state has to be re-established. Basically the software has to be restarted after a
„Reset board” (see also chapter 3.3.4).
Terminal Mode After opening one terminal you can communicate directly with the LED Analyzer Board
with the aid of the command list from chapter 4 .
Help The help function informs you about the used GPS LED Analyzer version.
3.3 Manual for the GPS LED Analyzer Software
Figure 14.1: Main screen

02.11.2018 14
Figure 14.2: Detail main screen
The graphic beside shows a detail of the main screen of the LED
Analyzer. The following steps explain the functions of the individual
controls:
Connect Button After pressing the “Connect Button” the
LED Analyzer is connected with the
software. In doing so the button label
turns into “Disconnect”. After pressing
once again the LED Analyzer Board is
logged off.
Not Connected Label Shows the particular connection status
of the LED Analyzer Board.
Start-Test-Button Software performs a measurement with
the actual configuration.
Select Board Allows the selection of the connected
boards.
Select LED Allows the selection of a determined sensor on the LED Analyzer Board .
Test Modes Depending on the application different test modes are available:
- The Manual Capture mode allows to select predefined exposure times and sensor
surfaces through the sensor range menu. The right choice of the exposure time depends
on the light intensity of the test object.
- The User Capture mode enables the user to specify exposure time and sensor surface
through the sensor configuration individual. The software allows exposure times from
1 ms—1000 ms .
- The PVM Capture mode is predestinated to define the colour values of pulsed LEDs.
In this procedure this mode transfers the settings of the sensor regarding exposure
time and sensor surface of the last performed measurement. By selecting the average
factor which appears after choosing the PVM mode the user defines the number of
measurements which have to be done. As soon as the LED Analyzer captures the LED
in the ON-state, during the automatically performed measurements, the colour
parameters are stored and are shown to the user after the complete measurement
process is done.
Information Screen The yellow marked information window informs about the used LED Analyzer Board
firmware and the number of the connected boards. It also informs about eventually
appearing errors.
In the window “Test results” (see figure below)all light parameters which have been captured and calculated by the LED
Analyzer are shown to the user.
The captured colour values are shown to user in three different colour spaces. In the window on the left, you see the RGB
values, followed by the HIS ( Hue—Saturation—Intensity) up to the chromaticity coordinates x and y from the CIE 1931
Colour space. In the lower right part the Corelated Colour Temperature (CCT) is shown additionally.
Bild 14.3: Test Results ( main screen )

02.11.2018 15
3.3.2 Configuration of the LED Analyzer
Before a measurement can be carried out with the LED Analyzer the following
configuration settings have to be selected.
Serial port Through this PopUp menu you select the Com-port
which Windows assigns the LED Analyzer. Through
The selection of “Auto” the programme searches the
assigned Com-port automatically. If you want to
determine the assigned Com-port manually than go to
the connections (COM&LPT) via the control panel and
the device manager.
Baud rate Here you can adjust the baud rate. Recent devices
have a baud rate of 115200 .
Logfile window In this window the Logfile is defined. This box do not
really matter for the usual application. It is only needed
for an error analysis for the GPS Analyzer programme.
Storage window Defines the locations for the Test Report File and the
Sensor Settings File.
CIE C. diagrams If the CIE colour space was selected through the View
PopUp menu, different CIE colour spaces can be
selected through this window. These are shown on
the main screen.
Figure 14.3: Configuration window
Deviation for intensity This options define a tolerance window which is respected at comparative
measurements of LEDs.
If the measurement value is within the tolerance window regarding the reference
value, the LED is considered to be good.
The tolerances for the individual LEDs can be changed in the “Measurement
settings” window additionally (see chapter 3.3.4)
Deviation for XY values Conducts analogously with “Deviation for Intensity “.
Don’t allow any changes … This control box is like a safety query, if a XY-offset should be changed by the
user through the “List of settings” window . As long as the ticker is set, there is
no possibility to change the offsets of a sensor. The status of the control box is
stored when closing the software and is recaptured when opened again.

02.11.2018 16
3.3.3 To perform a measurement by using the functional elements of the main screen
Figure 14.4: Sensor values (left) und Intensity in % (below)
After having done all required settings through the configuration window it is now to find out the right test mode and
the settings for your application.
Basically it is recommended to capture with a greatest possible light intensity. The intensity refers to the by the sensor
initially measured RGB values (see figure 14.4). The value for the light intensity should be between 30% and 80% .
This avoids that the sensor is operated outside the linear sensor sensitivity function referring to the colour parameters.
So an optimal test result can be reached.
In the first step select the wanted sensor. After that, start measuring with a sensor range of 9x9 and a large exposure time.
In the next steps reduce the exposure time so long until you are in a light intensity range of 30% - 80%. In case that the
reduction of the exposure time is not enough, set the sensor range from 9x9 to 3x3 and repeat the determination of the
optimal exposure time, as just described.
If you have to capture several LEDs per measurement it is recommended to find the optimal setting for each sensor over
the main screen and then switch through the PopUp menu “Test” to the windows “Measurement settings” and
“Measurements” (see chapter 3.3.4) At this the sensor settings referring the exposure time and the sensor range were
taken over.
For an application with several LEDs which have the same light intensity it is sufficient to determine the sensor setting for
one LED in this way. In the following this setting can be transferred through the “Measurements” window to the other
sensors (see chapter 3.3.4)

02.11.2018 17
3.3.4 To perform a measurement and compare several LEDs by using
“Measurement Window” and “Settings Window”.
3.3.4.1 Measuring and comparing LEDs with differnet light intensities
In order to compare LEDs use the “Measurement“ window in connection with the “Measurement settings“
window (see figure).
As described in chapter 3.3.3 it is recommended to find out the optimal sensor settings through the main screen first.
These were taken over by opening the “Measurement settings“ window. During the take over of the exposure time and
sensor range it is shown, if a sensor is occupied by an offset. In the below-mentioned example five sensors were set via
the main screen. Thereby sensor three with a non-volatile stored offset is occupied by fixed calibration.
By opening the “Measurement“ window the colour values for the five set sensors, which have been find out over the main
screen, appear (see figure).
Figure 14.5: List of settings
Figure 14.6:
List of measurement

02.11.2018 18
Let us assume that the five read in LEDs are considered as reference LEDs by which the following LEDs of the same type
are compared.
To this the determined values have to be stored with the “Save reference“ button and uploaded with the “Load reference“
button. Now perform a re-measurement with the “Perform measurement“ button without changing the test environment.
The colour values appear green. That means that the software has recognized the values as reference.
It is recommended to store the setting over “Save settings“ otherwise the settings have to be entered again, when the
software is rebooted.
When you exchange the reference LEDs with the LEDs which have to be proofed and perform a re-measurement through
the “Perform measurement“ button , the programme compares the capture with the reference values (see figure).
If there is a deviation this is shown red. The test result can be archived with the “Save test report” button.
3.3.4.2 Changing of tolerances, sensor settings and an offset
To define an offset or a tolerance field refering the capture values during a comparing measurement the following
possibility is available:
For that double click with the mouse in the “Measurement settings“ window on the wanted sensor line. The window
“Settings for sensor“ appears (see figure) .
Through this window tolerances referring to the intensity and the chromaticity coordinates XY can be entered. These
tolerances are provided by comparing the capture values with the reference values.
Furthermore any sensor settings referring to the test mode, the exposure time and the range can be modified during
Operation.
To enter an offset for the chromaticity coordinates XY you first have to deactivate the control box
“Don‘t allow any changes to XY values“ in the “Configuration“ window and confirm it by clicking the OK button.
Here too, modifications are taken over only at the nest measurement through the “Measurements“ window.
Figure 14.7: Comparing measurement
Figure 14.8: Settings for sensor

02.11.2018 19
3.3.4.3 Measuring and comparing several LEDs of the same light intensity
To compare LEDs of the same light intensity it is sufficient to determine the optimal sensor settings through the
main screen. Enter the “Measurement settings“ window. By clicking the sensor line then select the sensor of which
You want to take over the parameters. Now press the “Change all settings“ button to take over the sensor settings.
Following that carry out a measure through the “Measurement“ window in order to determine the reference values.
During the take-over of the sensor settings particular care should be paid whether you want to take the offset over or
not. For this there are control boxes in the “Configuration“ window and in the “Settings for Sensor“ window whose
Functions are described in the following:
If you want to transfer sensor parameters without an offset from one sensor to all the other sensors, then
you have to activate the control box “Don‘t allow any…“ in the “Configuration” window and confirm it
with OK . Select the sensor of which the parameters should be taken over. By clicking t he” Change all settings“
button the parameters are transferred to the other sensor lines. After a measure through the “Measurement“
window the modifications will become effective.
If you want to take over the offsets of one sensor for the other sensors only partially or totally you have to
deactivate the control box in the “Configuration“ window . At the same time the control box in the
“Settings for sensor“ window has to be deactivated fo reach sensor for which you want to take the offset over.
At sensors where the old offset setting should remain the control box in the „Settings for sensor“ window has to
stay activated. Following that select the sensor whose parameters should be transferred by clicking and check
Whether the control box in the “Settings for sensor“ window is also deactivated. Then press the
“Change all settings“ button after selecting the sensor. At least carry out a measurement through the
“Measurement“ window in order to take over the parameters in the measurement.
Modifications referring to the offset and sensor settings are taken over basically only after another measurement through
the “List of measurement“ window!
3.3.4.3 Reset the offset settings to the delivery status
To restore the delivery status of the LED Analyzer boards use the command “Reset Board“ in the PopUp menu “Test“.
After carrying out this command the LED Analyzer has to be logged out through the “Disconnect “ button and the software
has to be rebooted to take over the delivery status.
3.3.5 Using the Terminal mode
The GPS LED Analyzer Software offers the user a terminal mode in addition. With the help of this terminal mode the
user can familiarize with the commands in chapter 4 to integrate the LED Analyzer in an existing system (see figure) .
Figure 14.9:: Terminal Mode

02.11.2018 20
4. Capture Commands for the LED Analyzer
4.1. Connection Test
Transmit Description Receive Example Comment
testcon Connection test OK oder xOK testcon 2 OK x = number of boards
Description:
This command tests the connection between the test system/PC and the Analyzer.
If only one board is connected to the tester and the connection works the Analyzer will transmit the character OK.
If several boards are connected the number of the boards is transmitted like 2 OK.
Important: This command has to be sent as first command so that all connected boards will be recogniced.
4.2. Standard Capture
Captures and stores the colour and Intensity of the LEDs.
Transmit Description Receive Example Comment
capture Start Capture Colour, Saturation Intensity OK capture OK Capture all boards
and sensors with the
current set up
Description:
This command instructs the LED Analyzer to capture and store the colour and intensity of all LEDs simultaneously.
With the command „setcaptimexyz b“ the capture time and sensor area can be set before the real capture.
Table of contents
Popular Control Unit manuals by other brands

Samson
Samson TROVIS 6600 Mounting and operating instructions
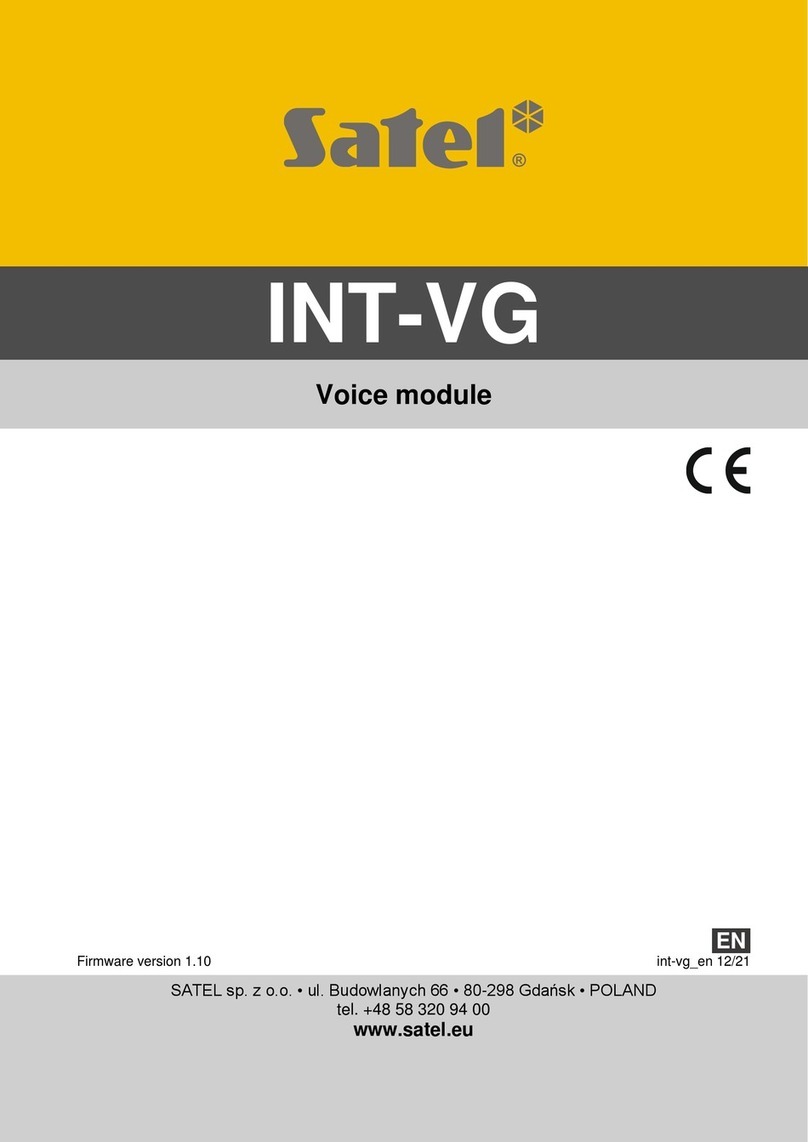
Satel
Satel INT-VG manual
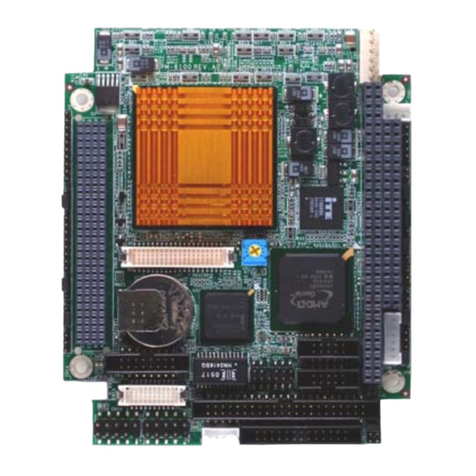
WIN Enterprises
WIN Enterprises PC/104-PLUS user manual
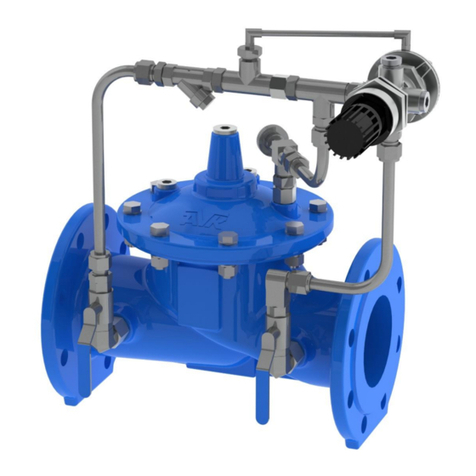
AVK
AVK 869 Series Installation, operation and maintenance manual
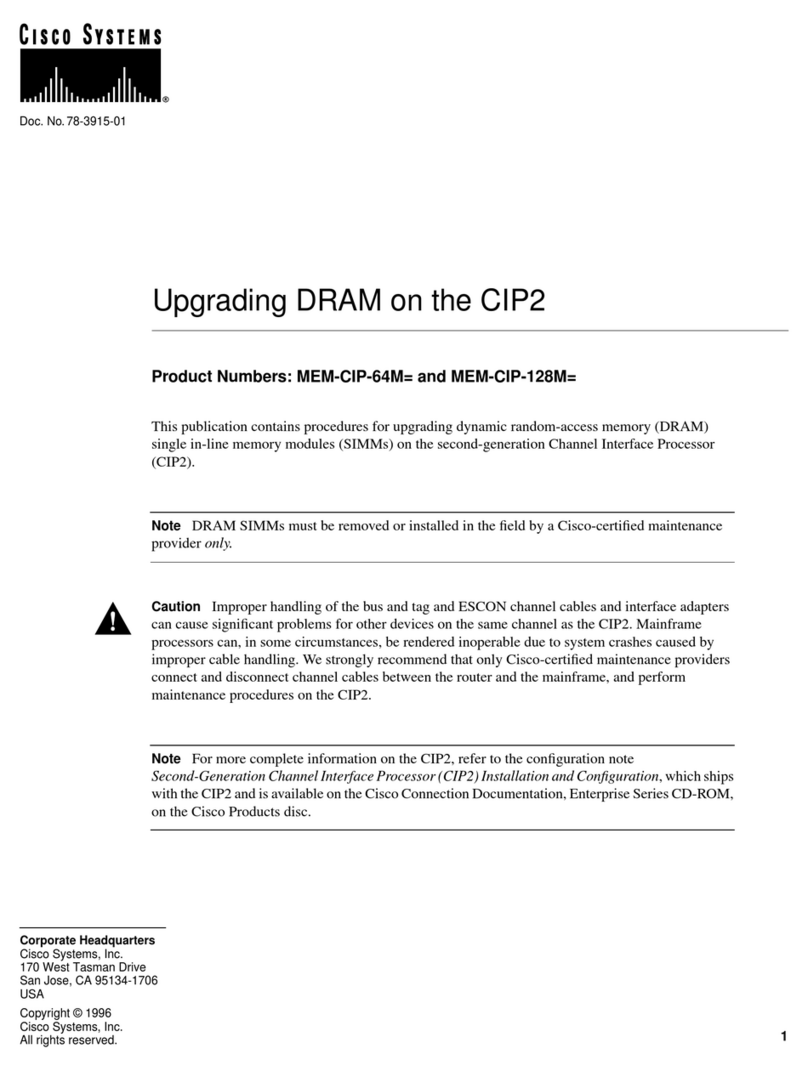
Cisco
Cisco MEM-CIP-64M manual
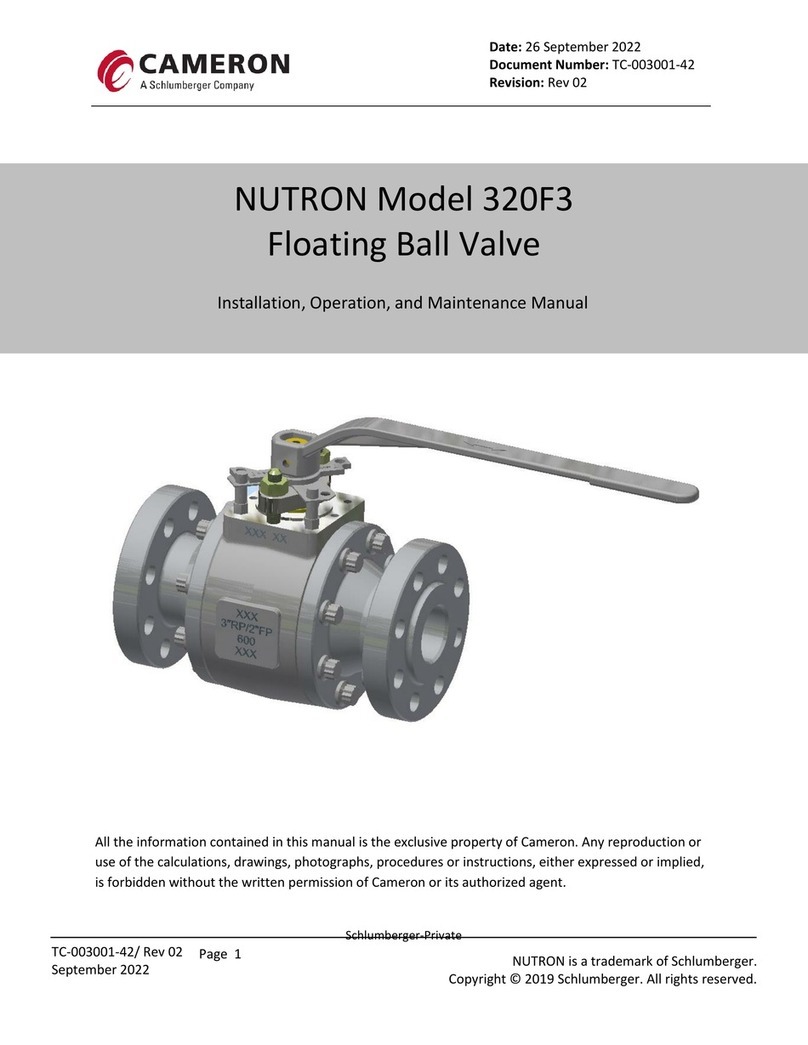
Schlumberger
Schlumberger CAMERON NUTRON 320F3 Installation, operation and maintenance manual
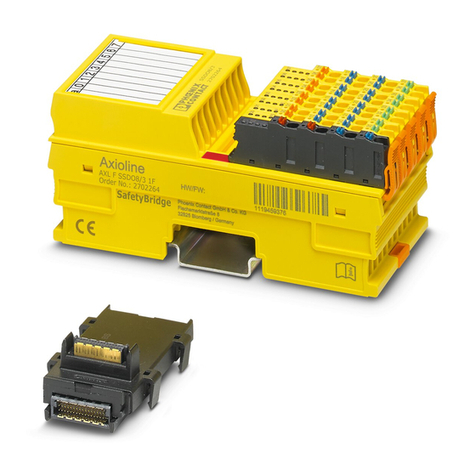
Phoenix Contact
Phoenix Contact Axioline F user manual
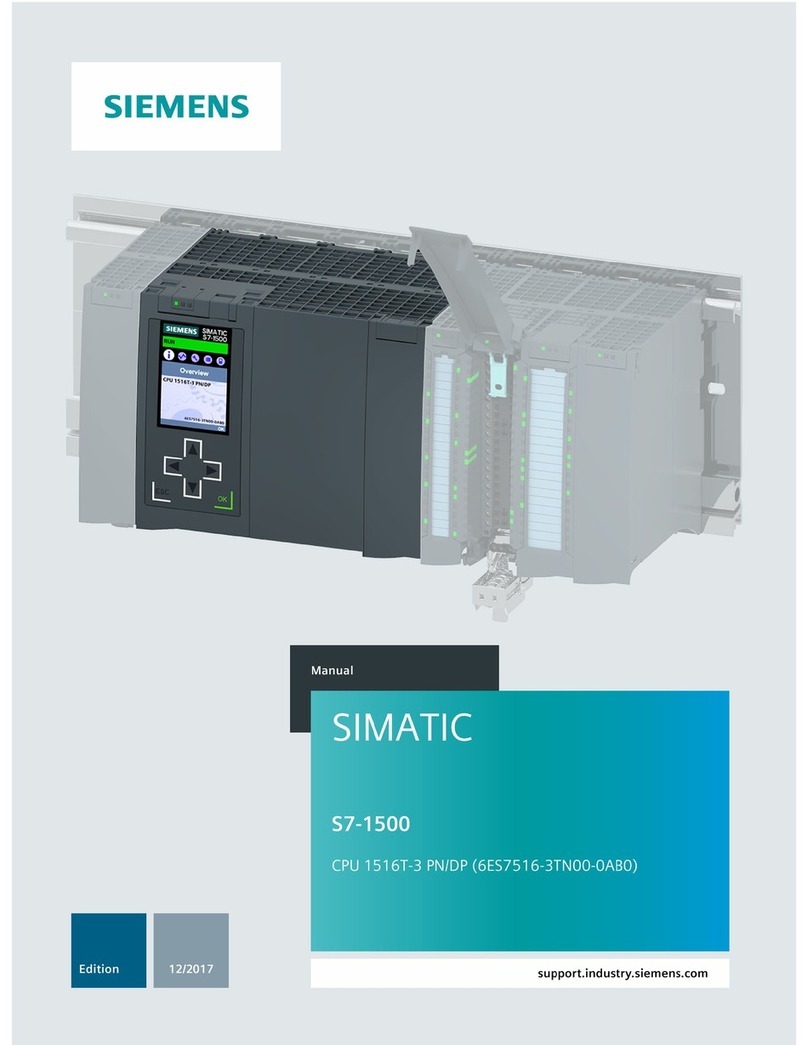
Siemens
Siemens Simatic S7-1500 manual
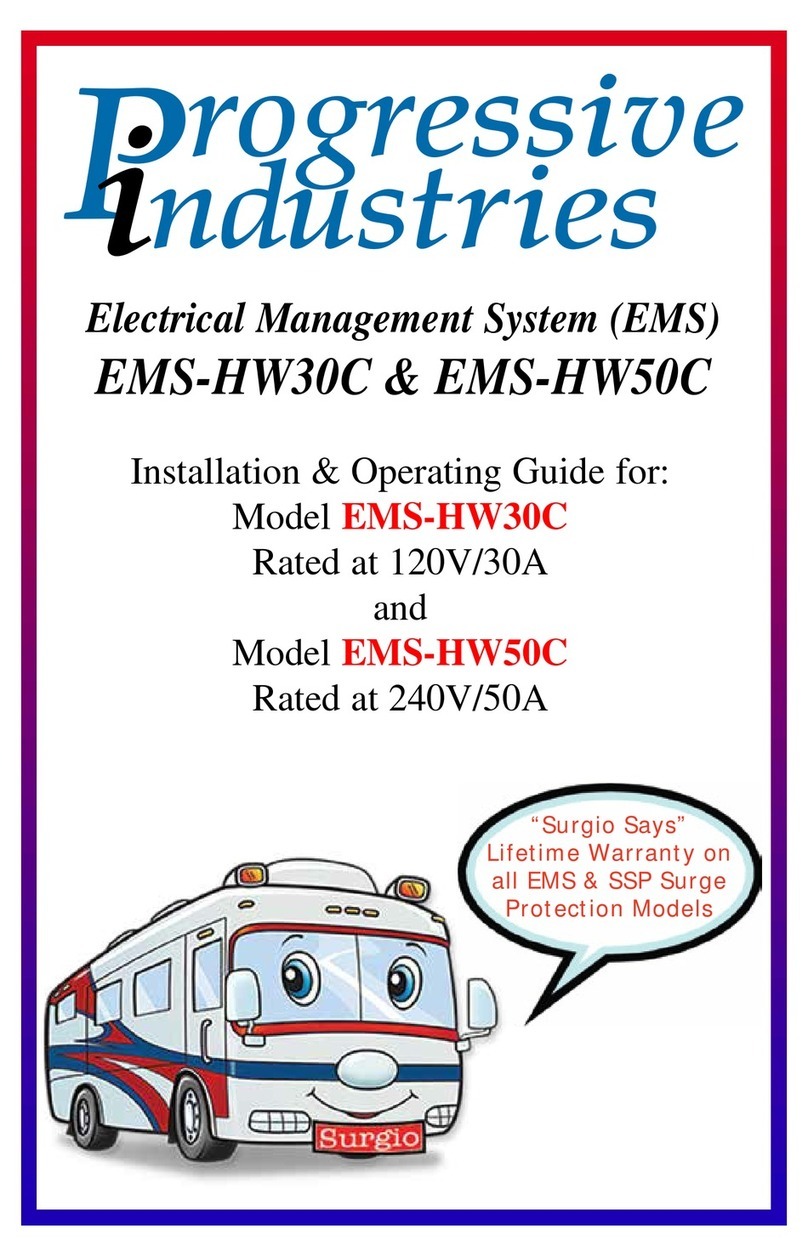
Progressive Industries
Progressive Industries EMS-HW50C Installation and operation
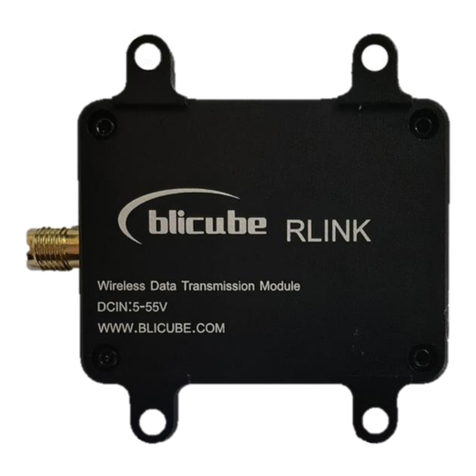
blicube
blicube RLINK user manual
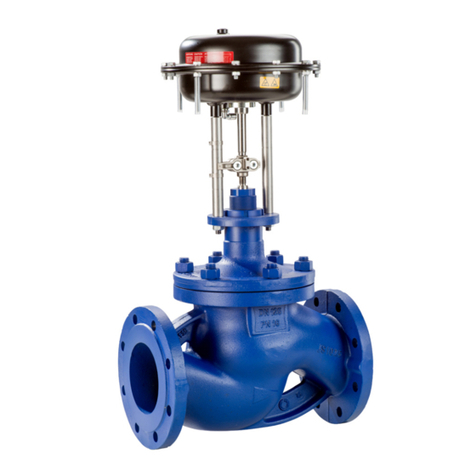
KSB
KSB BOA-H Mat P Installation & operating manual
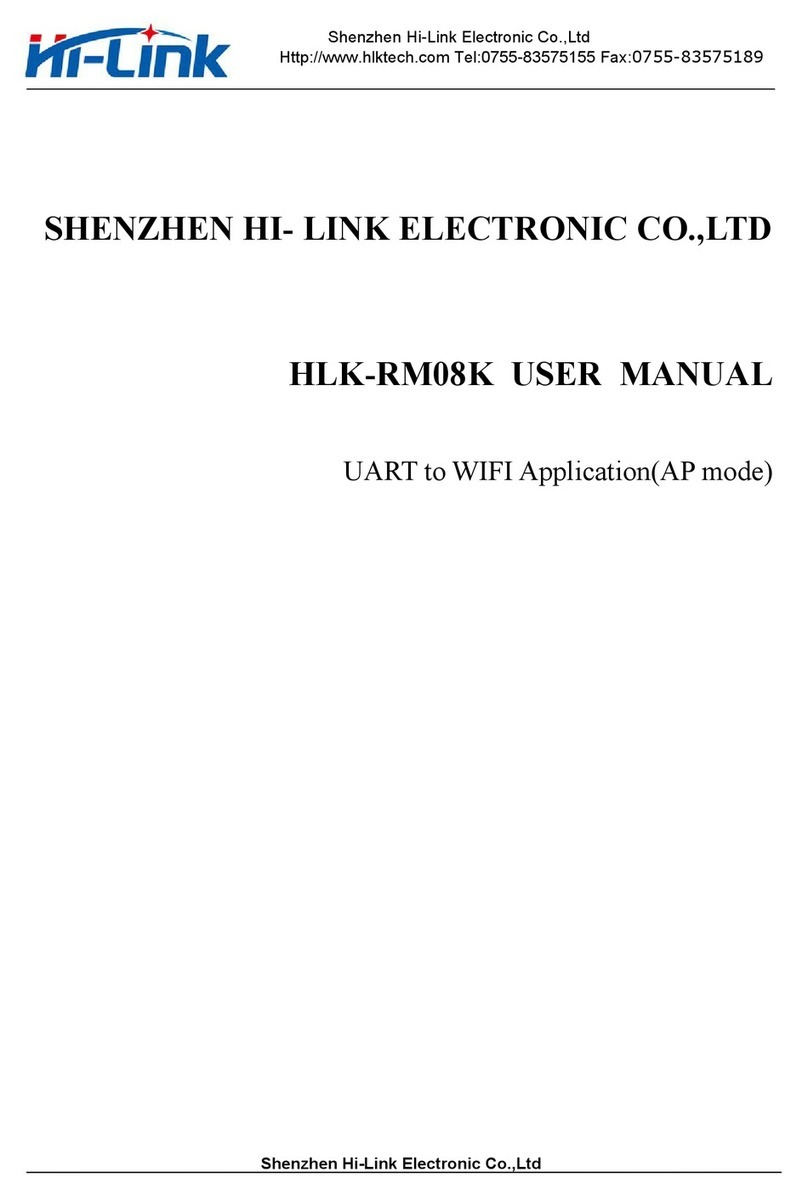
SHENZHEN HI- LINK ELECTRONIC
SHENZHEN HI- LINK ELECTRONIC HLK-RM08K user manual