Group3 DTM-152 User manual

GROUP3 TECHNOLOGY LIMITED WWW.GROUP3TECHNOLOGY.COM
DTM-152
Digital Teslameter
Operations Manual
Group3 reserves the right to change the specifications at any time without notice. 01092018-D152
Group3 Technology Ltd.
2 Charann Place, Avondale
Auckland 1026 , New Zealand
PO Box 71-111, Rosebank, Auckland 1348, New Zealand
Phone: +64 9 828 3358
Fax: +64 9 828 3357
Email: [email protected]
Web: http://www.group3technology.com
Calibration/Repair: www.group3technology.com/service
Made in New Zealand

GROUP3 TECHNOLOGY LIMITED WWW.GROUP3TECHNOLOGY.COM
INTRODUCTION
Thank you for purchasing and using a Group3 Digital Teslameter. We hope you will join the many thousands of users worldwide who are
enthusiastic about our products.
The DTM-152 Digital Teslameter is the latest product of Group3 that boast a touch screen interface to operate the DTM. Instead of
mechanical switches and buttons that are still being used on the older versions to operate the unit, the DTM-152 display is touchscreen-
based so setting the unit to user’s specification is quick and easy. The digital readout now shows not just the field reading but the
temperature of the sample at the same time.
Another new feature of the DTM-152 is its data logging capability where user can now do their data gathering on the DTM itself and saves
the output CSV file on to an external memory drive such as a USB drive or hard disk. This eliminates the need for a separate computer
terminal and software to do a data log of a particular session such as field mapping of a magnet.
Also, a new feature is the Graph function of the DTM-152. Users can now see the behavior of a particular session instead of just looking
at the field reading, the graphical display lets the user monitor visually if there are sudden or abrupt changes in the field over a period of
time. The time and field range are configurable depending on the user’s preferences.
Lastly, the DTM-152 now can be monitored and controlled over a network, thanks to the built –in Ethernet connectivity and our custom-
built LabView VI that comes with this unit. Applications such as synching the timing of a robot arm when mapping the field of a magnet
makes this an important and useful feature.
Group3 has been designing and building magnetic field measuring equipment since 1983. We are constantly upgrading our products and
support documentation. We welcome input from our customers, so if there are aspects of the instrument which you particularly like, or
which you would like to see improved, please contact your Group3 supplier (see back page for a complete list) or Group3 directly with your
suggestions to sales@group3technology.com .
The Group3 website, www.group3technology.com contains details of all our products.
This site is regularly updated, so check it from time to time to learn about recent developments.

GROUP3 TECHNOLOGY LIMITED WWW.GROUP3TECHNOLOGY.COM
DTM-152 Digital Teslameter Features
FRONT PANEL
1 Power Button Press to turn ON and OFF the unit
2 HOME Tab Touch to show the Main Readings screen
3 GRAPH Tab Touch to show and access Graph and configure controls
4 DATA LOG Tab Touch to do data logs and change Date/Time
5 MENU Tab Touch to access the DTM’s manual controls
6 NETWORKING Touch to access Ethernet networking controls
7 LED Buttons Touch to turn ON/OFF the Readings/Commands/Web Service controls
8 TOGGLE Button Touch to change the DTM range
9 FILTER Button Touch to turn ON/OFF the filter. Lights up a green color when ON.
10 ZERO Button Touch to set the reading to Zero. A green color indicates current unit.
11 RESET Button Touch to reset the unit.
12 UNIT Button Touch to choose either Gauss or Tesla.
13 Channel, Range & Filter Indicates the Channel/Axis, current range and filter status
14 Field Indicator Shows the measured magnetic field and temperature reading
15 Maximum Field Indicator Shows the maximum field measured
16 Temperature Indicator Shows the temperature of the sample as measured from the probe head
17 Session Indicator A GREEN light shows when an ongoing session. Otherwise, LED is in RED
18 USB Port Insert your USB Drive or memory stick to save data log files
REAR PANEL
1 DC Input Socket Attach the supplied DC Power supply and lock to secure the power plug.
2 Analogue Output Attach BNC connector to get analogue output
3 Hall Probe Socket Attach the probe plug into this socket and secure using 2 jackscrews
4 Ethernet Port Attach Ethernet jack (RJ45) to communicate with LabView interface
5 USB Port Additional USB port for memory drives
CONNECTIVITY
Ethernet Port Unit has a built-in Ethernet port for communication over network
1
5
4
3
2
7
6
14
13
12
11
10
9
8
15
16
17
18
5
4
2
1
3

GROUP3 TECHNOLOGY LIMITED WWW.GROUP3TECHNOLOGY.COM
SPECIFICATIONS OF DTM-152 SYSTEM
Specifications of DTM-152 with LPT-141 or MPT-141 Hall Probe.
Measurements field value and time-varying (ac) component of field
Field ranges 0.3 0.6 1.2 3.0 tesla full-scale,
3 6 12 30 kilogauss full-scale,
with polarity indication
maximum calibration field ±2.2 tesla, ±22 kilogauss
ResolutionDC mode with digital filtering ON:
1 in 600,000 of bipolar span as shown on front panel display.
range display resolution
gauss tesla
0.3 tesla 0.001 0.0000001
0.6 tesla 0.01 0.000001
1.2 tesla 0.01 0.000001
3.0 tesla 0.01 0.000001
Resolution DC mode with digital filtering OFF, and AC mode:
1 in 120,000 of bipolar full-scale span in display:
range display resolution serial/GPIB resolution
gauss tesla gauss tesla
0.3 tesla 0.05 0.000005 0.001 0.0000001
0.6 tesla 0.1 0.00001 0.01 0.000001
1.2 tesla 0.2 0.00002 0.01 0.000001
3.0 tesla 0.5 0.00005 0.01 0.000001
20-bit digitizing of field reading.
Accuracy DTM-152 with LPT-141 or MPT-141 probe:
±0.01% of reading ±0.006% of full-scale max. at 25°C
Temperature DTM-152 with LPT-141 or MPT-141 probe:
Stability calibration: ±10 ppm of reading/°C max.
zero drift: ±(1 microtesla + 0.0003% of full-scale)/°C max.
add -3ppm/°C for each meter of probe cable
Time stability ±0.1% max. over 1 year
Measurement rate 10 measurements per second
Response time Full-scale change of displayed field reading settles to within
resolution in less than 0.3 second (filtering off - see below)
Peak hold mode Displays maximum field since mode entered or reset.
Peak hold is implemented digitally with zero sag or decay.
Display Touchscreen, soft key navigation, simulated 7-character, 7-segment alphanumeric display
Tabs HOME:
•Field and Temperature reading in simulated 7-segment display
•Field Unit in either GAUSS or TESLA indicated by GREEN backlight
•FILTER is set to ON by default as indicated by a GREEN backlight, press to turn OFF.
•Press RESET button to do a power cycle and reset the unit.
•Press ZERO button to zero any stray field.
•Maximum Field, Filter, Mode and Range status are displayed inside the readings display.

GROUP3 TECHNOLOGY LIMITED WWW.GROUP3TECHNOLOGY.COM
•SESSION indicator lights up GREEN when there is a session running. Graph can be zoomed in or out if a
session is in progress.
•Displays the number of Out of Range readings in that session
•Range indicator is lit in RED. Press the TOGGLE button to select the range.
•Networking –LAN port available. Communicates with any Windows PC using DHCP.
GRAPH:
•Graphical representation of field
•Field reading including maximum field
•Configuration button to set time frame, offsets and zeroing
•SESSION indicator lights up GREEN when there is a session running. Graph can be zoomed in or out if a
session is in progress.
•Displays the number of Out of Range readings in that session
DATA LOG:
•Set the sample number and sample rate
•Displays the memory capacity information when a USB memory stick / drive is inserted
•Display the Time/Date and is configurable by pressing the time/date text
•Multiple session is available
MENU:
•Master functions as well as other control features such as restting, zeroing, filtering, etc. are available
in this tab.
Analog outputs dc output - instantaneous field analog:
full-scale output: ±3V nominal
source impedance: 1000Ω
accuracy: ±10%
bandwidth: 3kHz at -3dB, rolloff 3-pole 60dB/decade
ac output - rectified analog of time-varying (ac) field:
frequency response: 8Hz to 3kHz at -3dB points
time-constant: 0.2 seconds
average responding, delivers rms value of sinusoidal field
full-scale output: 3V nominal
source impedance: 1000Ω
accuracy: ±12%
Memory backup user-entered data storage for 30 days with power off.
Power source
Model No. GSM36B12
Input: 100-240VAC, 50/60Hz, 0.9-0.45A
Output: 12V , 3A, 36W Max.max 15V, 0.35A rms
Power fuse on processor board: 1 amp anti-surge 5 x 20mm
Data Log Via USB, data log file saved in CSV format
Enclosure All metal, with tilt stand on bench models, mounting cheeks on rack
Dimensions 350 (L) x 320 (W) x 150 (H, including feet ) mm ,
Instrument Weight 5.8 kg,
Shipping Weight 12.5Kg (includes power pack, mounting cheeks and hard case)
Ambient field Maximum operating field for electronics package:
10 millitesla with single-range probe,
0.5 millitesla with multi-range probe.
Temperature range 0 to 50°C operating, absolute maximum temperature of probe 60°C

GROUP3 TECHNOLOGY LIMITED WWW.GROUP3TECHNOLOGY.COM
CONNECTING THE HALL PROBE
Before handling the probe, please read the following:
Group3 Hall probes are built to be as robust as possible for a small, precision device. However, it is most important that certain precautions
be taken when handling and installing probes so that they are not damaged or destroyed, and to preserve their accurate calibration.
Mount the probe head so there is no pressure which will tend to bend or depress its ceramic rear surface. If the probe head is clamped,
make sure the surface in contact with the ceramic is flat and covers the whole of the ceramic surface. Do not apply more force than is
required to hold the probe in place. Any strain on the ceramic will alter the probe's calibration, and excessive force will destroy the Hall
element inside. When the probe head is mounted, the cable should be clamped firmly nearby so it cannot be torn away from the probe head
if accidentally pulled. The flexible section adjacent to the probe head can be carefully folded to allow the cable to come away in
any direction but avoid repeated flexing of this section.
Keep the cable out of the way of foot traffic. Do not pinch the cable or drop sharp or heavy objects on it. A severed cable cannot be re-
joined without altering the probe's performance and requires factory repair and re-calibration.
The DTM-152 must be used with a Group3 Hall probe. Probe models LPT-141, LPT-231, MPT-141, or MPT-231 are the most suitable for
use with the DTM-152. The probe may be one supplied with your teslameter, or it may have been obtained separately. In any case,
calibration is preserved when probes are exchanged between instruments.
The standard probe cable length is 2 meters. Probes with non-standard cable lengths up to 30 meters may be ordered from your Group3
supplier. The cable used for Group3 probes is shielded to reduce pickup of induced noise from external sources. Such noise may reduce the
accuracy of the instrument, cause malfunctioning, or in extreme circumstances even result in damage to the internal circuitry.
ANALOG OUTPUT
An analog output signal is available at the rear of the teslameter. This output is the Hall probe signal amplified to 3 volts full-scale and gives
an indication of the instantaneous field value from dc to 9kHz (-3dB), with a roll-off of 60dB/decade above 9 kHz. Field direction is indicated
by the output voltage polarity. There is a small zero offset (10 millivolts maximum), arising from the probe zero-field output and amplifier
offsets. The output impedance is 1000 ohm with a 1nF capacitor to common for noise filtering.
pin signal
1 ground
2 dc output
Analog Output Connector Pin Assignments
GROUNDING
All parts of the teslameter's metal case are connected together to form an integral electric shield around the circuitry inside. When the
probe connector is plugged into the teslameter and the retaining screws are tightened, the probe connector case and the teslameter case
are connected together and form an integral shield around the circuitry inside. The cable shield is added to the case shield and extends
protection from electrical interference almost up to the probe head.
Because there is an internal connection between teslameter circuit common and the probe connector case, when the probe connector is
engaged, and the retaining screws tightened the teslameter circuit common will be connected to the case. Do not make an additional
connection between circuit common and the case at any point. Such additional connection will form a ground loop and may introduce errors
in the measured field value.
The shielding provided with the above arrangement should be sufficient protection against EMI in most cases, especially when the probe
cable is shielded. Sometimes it may be found helpful to ground the teslameter case to a good electrical ground point. Connection can be
made to the case by inserting an appropriate lug or terminal under the head of one of the rear panel fixing screws.

GROUP3 TECHNOLOGY LIMITED WWW.GROUP3TECHNOLOGY.COM
INSTALLATION TECHNIQUES FOR ELECTRICALLY NOISY ENVIRONMENTS
The DTM-152 is a precision electronic measuring device. Because of the nature of the measurements it is asked to do, it is frequently
exposed to conditions that are considerably worse than are normally encountered by precision instruments. Therefore, the teslameter has
been carefully engineered to be as immune as possible to sparks and other forms of interference through the use of several kinds of power
input filtering and a special high-isolation switchmode power module built into its circuitry. The design has been verified by extensive
testing, using high energy sparking in close proximity to both the teslameter instrument case and the probe. Nevertheless, due care should
always be taken when installing the teslameter system.
The teslameter and its probe must be protected from any chance of receiving a direct hit by a high voltage discharge. The probe should
have shielded cable if the meter is to be used in an electrically noisy environment. The cable shield is an RFI screen, not a high
current path, so if there is any possibility of an arcing discharge hitting the probe area, then the probe head and part or all of the cable must
be enclosed in a metal tube (nonmagnetic near the probe head) or shielded in some other way.
The probe cable should be routed away from any power, high current or high voltage wiring. It should be shielded from any capacitively
coupled noise effects. If the cable runs close to any section of the apparatus that could be subjected to a very rapid change of potential
when a spark discharge occurs, then the probe cable may need additional shielding to prevent capacitive coupling of the noise.
The retaining jack screws designed to hold the probe connector onto the teslameter must be screwed up finger tight, as they form part of
the electrical connection of the shield system. The woven braid of the probe cable is terminated to the probe connector case. The retaining
screws then connect the probe connector case to the teslameter case.
The teslameter itself should be sited in a sheltered location, where it will not be exposed to spark discharges or radiated or capacitively
coupled noise. The teslameter case is made of metal for shielding reasons. However, of necessity it is less than perfect, as apertures have
to be left in the case for the display and various connectors etc. The unit is a precision measuring device, and should be treated with care,
not subjected to adverse environmental conditions.
The plugpacks supplied with each teslameter should be plugged in to a clean mains power supply. Noise on the mains will work its way
through the transformers and disturb the teslameter. Simple mains filters are readily available if there is only one mains supply for the
whole machine. Route the low voltage lead away from high current or high voltage wiring. Ideally cut the low voltage lead to the minimum
length required for the installation and re-connect the plug to it.

GROUP3 TECHNOLOGY LIMITED WWW.GROUP3TECHNOLOGY.COM
DISPLAY MAP
A. HOME Tab
Default Setting:
Filter ON, TESLA unit, Range 3.0T
•Shows the Field, Temperature, and MAX field reading
1. To Zero the field, press “ZERO”
2. To change unit to Gauss, press “GAUSS”
3. To change range, Press “TOGGLE”.
Range Operation
Range Standard Probe High Sensitivity Probe
4. Range 0 0.3T 0.03T
5. Range 1 0.6T 0.06T
6. Range 2 1.2T 0.12T
7. Range 3 3.0T 0.3T
NETWORKING: USING DTM-152 LABVIEW VI
1. Attach Ethernet connector RJ45 to the port found at the rear of unit marked to connect to the local network or router.
2. Ethernet communication is automatically set to ON and DHCP when a network is detected using the Ethernet port.
3. To manually input the IP address of your computer, de-select DHCP and input the desired IP address.
4. Touch and slide your finger upwards on the screen to show the rest of the window.
5. Press OK to save your settings and exit the dialogue box.

GROUP3 TECHNOLOGY LIMITED WWW.GROUP3TECHNOLOGY.COM
Once activated, user can access and control the DTM remotely using the Group3 DTM-152 LabView Virtual interface. See separate
manual on “How to install DTM-152 LabView VI”.
B. GRAPH
The graph displays the reading in real time and can be configurable to auto scaling, unipolar or bipolar field. The graph window also
shows if there is a current data log session as well as a counter for out of range readings (if on unipolar and bipolar).
Configuring the Graph Settings
1. Press the CONFIGURATION button.
2. Set the time frame as desired.
3. Press the Range button to select AUTO, UNIPOLAR or BIPOLAR scaling.
4. Selecting the AUTO scaling range hides the option to set the lower and upper bounds. Selecting the UNIPOLAR scaling range hides the
lower bound while selecting BIPOLAR scaling range gives you the option of setting the lower and upper bounds.
5. User can also set the readings to ZERO to clear residual fields.

GROUP3 TECHNOLOGY LIMITED WWW.GROUP3TECHNOLOGY.COM
6. User can also set an offset if user needs to add or subtract a field value to set as benchmark field.
7. User can erase the offset that was added to return to the original field reading.
8. Press OK to save and exit the configuration dialogue box or press Cancel to exit without saving the configured settings.

GROUP3 TECHNOLOGY LIMITED WWW.GROUP3TECHNOLOGY.COM
C. DATA LOG
The DTM-152 has the capability to data log a field measurement session. This feature makes field measurement quite easy and
eliminates the use of additional computer and specialized software to do the operation. All the user needs is a USB memory stick (at least 4 GB
and max 256 GB) to save the file. The data is stored as a CSV file which user can manipulate using MS Excel. User is informed of how much
data the USB stick can hold based on the sampling quantity and rate.
Sample: A 4GB of memory can save around 40 days’ worth of data at 30 samples/seconds (Hz).
•Sampling rate and number of samples can be adjusted either by using the UP arrow or DOWN arrows or by pressing the value and a
dialogue box appears to input the desired value.
C.1. HOW TO ACQUIRE DATA USING DATA LOGGING
1. Attach a memory stick or hard drive to any of the unused USB ports where data can be saved.
2. Select the sampling rate and number of samples. The software will automatically calculate how much data that can be stored on
external memory and the time it can run the data.
3. Press “START” to start the session. The Green LED on the DATA LOG Tab indicates an ongoing session.
4. You can STOP the recording session at any time by doing a 2-second press on the active session and press “CANCEL”. It will ask you
if you want to “SAVE” the halted session or “CANCEL” the session completely.

GROUP3 TECHNOLOGY LIMITED WWW.GROUP3TECHNOLOGY.COM
oIf you want to run multiple sessions, just select the parameters and press “ADD”.
NOTE:
To Change DATE and TIME
In case you need to change the date and time setting, press the date and time” and display will pop up to change the date and time.

GROUP3 TECHNOLOGY LIMITED WWW.GROUP3TECHNOLOGY.COM
D. MENU
The MENU Tab is where the rest of the controls of the DTM are located.
•MENU is subdivided into 5 pages.
oMASTER FUNCTIONS
oFILTERING
oI/O
oSIMULATIONS
oSCALE & CALIBRATION
D.1. MASTER FUNCTIONS PAGE
MASTER FUNCTIONS COLUMN
•GET FIELD READING –Press to get the current field reading.
•GET TEMPERATURE READING –Press to get the temperature reading.
•SET RANGE SELECTION –Press to set the field range.
•GET RANGE –Press to get the current range of the unit.
•GET ZERO –Press to get the current zero offset.
•SET GENERAL FUNCTION –Press to set the function either DC or AC.
•GET PEAK HOLD VALUE –Press to get the peak hold value.
DISPLAY COLUMN
•SET DISPLAY MODE –Press to set show current display mode to either Hold (H) or Normal (N).
•GET DISPLAY MODE –Press to get the current display mode in either Hold (H) or Normal (N).
RESET & ERASE COLUMN
•ERASE ZERO CORRECTION –Press to erase the ZERO correction value added by user.
•RESET –Press to reset the whole unit.
•GET GENERAL FUNCTION –Press to show current function either in DC or AC.
•ERASE PEAK HOLD VALUE –Press to erase the peak hold value.
•RESTART DTM SOFTWARE –Press to power cycle the DTM unit.
D.2. FILTERING PAGE
FILTERING COLUMN
•SET DIGITAL FILTERING –Press to set the digital filtering to ON or OFF.
•GET FILTER FACTOR –Press to get the current filter factor to the field reading.

GROUP3 TECHNOLOGY LIMITED WWW.GROUP3TECHNOLOGY.COM
•SET FILTER FACTOR –Press to set the filter factor
•GET DIGITAL FILTERING STATUS –Press to get the filtering status in either ON (1) or OFF (0).
•SET WINDOW –Press to set window within digital filtering occurs
•GET WINDOW –Press to get the currently active window in which digital filtering occurs
D.3 I/O PAGE
I/O COLUMN
•SET SEND MODE –Press to set DTM continuous data output to ON (1) or OFF (0).
•SET INCLUDE UNIT SYMBOL –Press to turn the inclusion of Tesla (T) or Gauss (G) symbol on or off
•SET UNIT SYMBOL –Press to set the unit to either Tesla (T) or Gauss (G).
•SET ADDRESS DEVICE –Press to set the DTM remote address (0 to 11).
SAMPLING COLUMN
•GET SAMPLING INTERVAL –Press to get the current number of seconds between consecutive readings.
•SET SAMPLING INTERVAL –Press to set the number of seconds between consecutive readings.
•GET TRIGGERED FIELD READING –Press to get a triggered field reading from the DTM
•SET TEMPERATURE SAMPLING INTERVAL –Press to set the interval of temperature sampling in seconds.
•SET TEMPERATURE SAMPLING MODE –Press to turn temperature sampling ON or OFF.
D.4 SIMULATIONS PAGE
SIMULATIONS COLUMN
•SET SIMULATED FIELD VALUE –Press to replace a measured field reading with a simulated value
•SET SIMULATED TEMPERATURE VALUE - Press to replace a measured temperature reading with a simulated value
•SET SIMULATED RAW FIELD VALUE AT ADC OUTPUT –Press to set simulated raw field value after EEPROM calibration.
•SET SIMULATED RAW FIELD VALUE AFTER ZEROING –Press to set the simulated raw field value after zeroing
•CANCEL SIMULATED FIELD AND TEMPERATURE –Press to cancel field and temperature simulated values.

GROUP3 TECHNOLOGY LIMITED WWW.GROUP3TECHNOLOGY.COM
OFFSETS COLUMN
•GET OFFSET –Press to get the current offset field value
•SET OFFSET - Press to set an offset field value that is added to all field readings
•ERASE OFFSET –Press to erase the user offset field value
•SET ZERO –Press to set the current field reading to zero
RAW DATA COLUMN
•SET SCALE FACTOR (ALL RANGES) –Press to set the actual scale factor to apply to field readings for all ranges (negative or positive)
•GET CALIBRATED READING AFTER USER ZERO CORRECTION - Press to get a calibrated reading after probe correction and user zero
correction.
•GET UNCALIBRATED RAW READING AFTER DIGITIZING –Press to get the uncalibrated raw reading from the ADC (after digitizing).
•GET CALIBRATED READING BEFORE CORRECTION –Press to get a calibrated reading before probe correction (after DTM internal
calibration)
D.5 SIMULATIONS PAGE
SCALE AND CALIBRATION COLUMN
•GET CALIBRATION FACTOR –Press to get the current calibration factor as a mantissa and exponent
•ERASE CALIBRATION FACTOR –Press to erase the calibration factor
•ERASE SCALE FACTOR –Press to erase the set scale factor
•GET SCALE FACTOR - Press to get the current scale factor applied to field readings
•SET SCALE FACTOR –Press to set the current scale factor to make the current field reading equal to the entered value
•SET CALIBRATION FACTOR –Press to set the calibration factor for field readings to the currently selected field range

GROUP3 TECHNOLOGY LIMITED WWW.GROUP3TECHNOLOGY.COM
E. MAINTENANCE
USB PORT
•The USB port can only be use for attaching a memory drive such as a USB stick or external hard drive to save sessions. It is not to
be use for accessing the serial output of the DTM.
TURNING OFF THE UNIT
•Before turning the unit off, make sure that data logging session has stopped or has been saved.
•Press the Power button to turn off the unit.
•UNPLUG the power supply connector at the back of the unit to completely turn OFF the unit.
TROUBLESHOOTING
•Display shows no probe –Press the power button to turn off the display. Unplug the power from the socket. Disconnect the
probe plug and check that no pins are bent. Check too that the socket is not damaged. Re-insert the plug when no abnormality seen
on plug. Tighten the jackscrew to the unit and turn on unit again.
•Display shows “Bad Cal” – call or email Group3 for support
•Display freezes or hangs up –Turn off the power by pressing the power button to re-start the unit. Unplug the power from the
socket. Check if previous settings are still retained. Re-enter if necessary.
•Display shows erroneous data –If field readings shows abnormality or that readings on each range is different or inconsistent,
go to the MENU page and under the RESET & ERASE column, press the RESET button. All previous settings entered would return
to default and user settings must be re-entered.
•ALL OTHER ERRORS –if unit is still misbehaving or not operating correctly after doing a reset, kindly contact Group3 through our

GROUP3 TECHNOLOGY LIMITED WWW.GROUP3TECHNOLOGY.COM
LIMITED WARRANTY
Group3 Technology Ltd. (hereinafter called the Company) warrants instruments and other products of its manufacture to be free from
defects in materials and workmanship that adversely affect the product's normal functioning under normal use and service for a period of
one year from the date of shipment to the purchaser.
The obligation of this warranty shall be limited to repairing or replacing, at the discretion of the Company and without charge, any
equipment which the Company agrees is defective as set out above within its warranty period. The Company will reimburse lowest freight
rate two-way charges on any item returned to the Company's factory or any authorised distributor or service centre, provided that prior
written authorisation for such return has been given by the Company.
This warranty shall not apply to any equipment which the Company determines to have become defective owing to mishandling, improper
installation, alteration, negligence, inadequate maintenance, incorrect use, exposure to environmental conditions exceeding specifications,
or any other circumstance not generally acceptable for equipment of a similar type.
The Company reserves the right to make changes in design without incurring any obligation to modify previously manufactured units. No
other warranties are expressed or implied, including, but not limited to, the implied warranties of merchantability and fitness for a particular
purpose. The Company is not liable for consequential damages.
83000001

GROUP3 TECHNOLOGY LIMITED WWW.GROUP3TECHNOLOGY.COM
Copyright 2018 G3 333- V1.13 150517
www.group3technology.com
Table of contents
Other Group3 Measuring Instrument manuals
Popular Measuring Instrument manuals by other brands
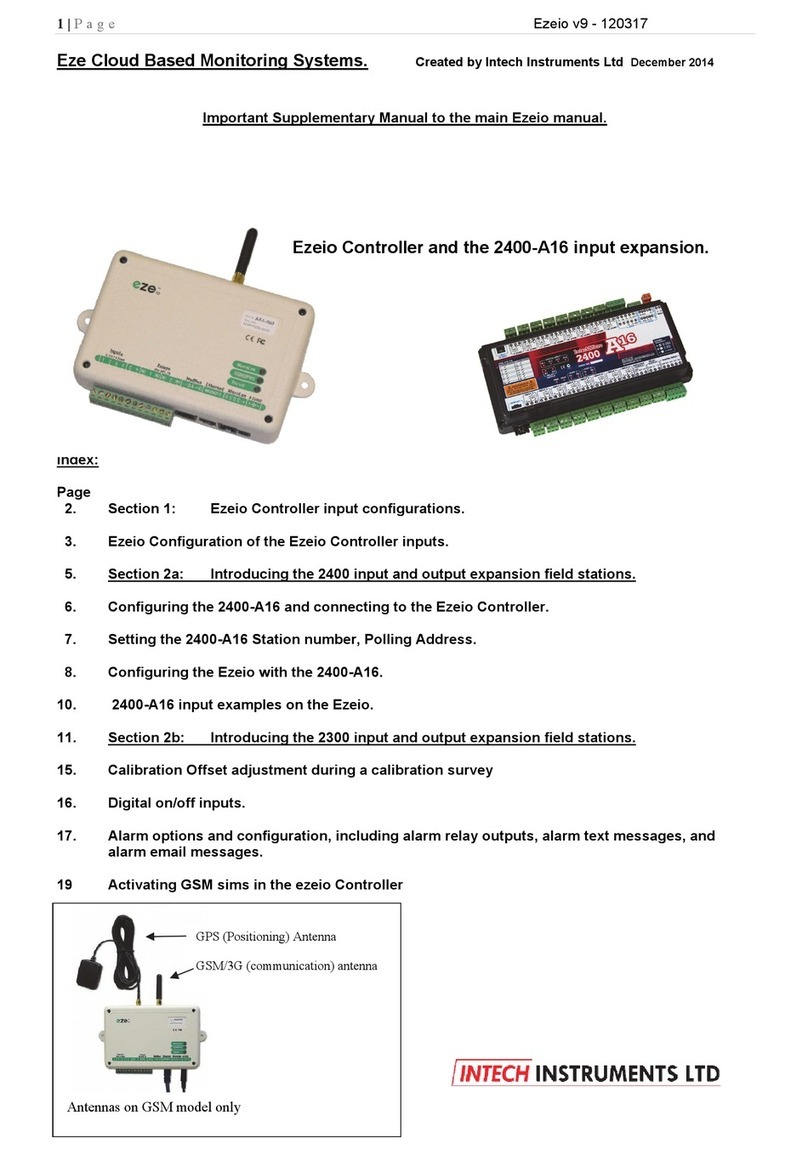
Intech Instruments Ltd
Intech Instruments Ltd Ezeio manual
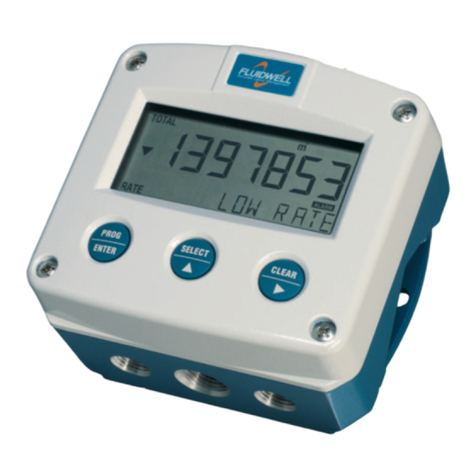
Fluidwell
Fluidwell F1-A-PD-OS Series installation guide
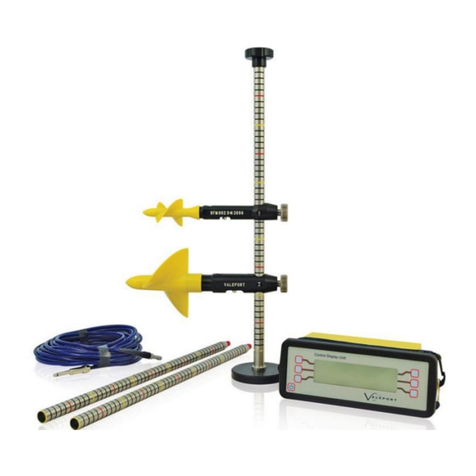
Valeport
Valeport BFM001 operating manual
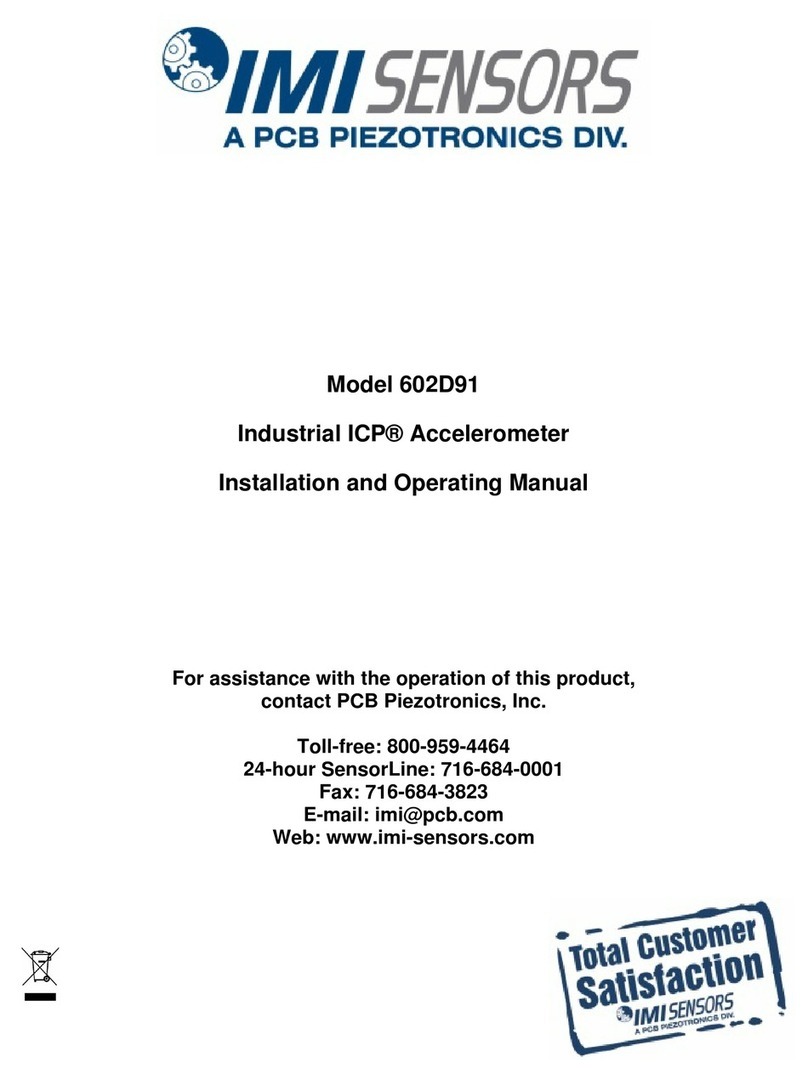
PCB Piezotronics
PCB Piezotronics IMI SENSORS 602D91 Installation and operating manual

TV Logic
TV Logic LUM-095G Operation manual
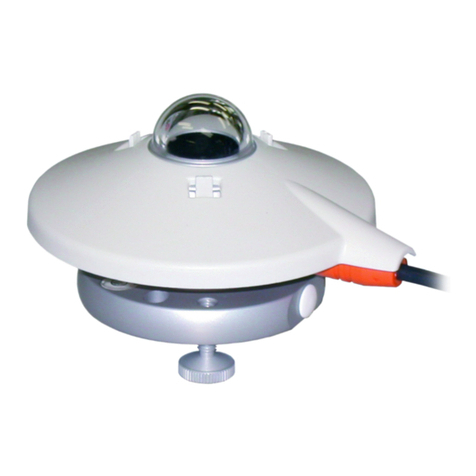
Campbell
Campbell CMP3 product manual