Intech Instruments Ltd Ezeio User manual

1 | Page Ezeio v9 - 120317
Eze Cloud Based Monitoring Systems. Created by Intech Instruments Ltd December 2014
Important Supplementary Manual to the main Ezeio manual.
Index:
Page
2. Section 1: Ezeio Controller input configurations.
3. Ezeio Configuration of the Ezeio Controller inputs.
5. Section 2a: Introducing the 2400 input and output expansion field stations.
6. Configuring the 2400-A16 and connecting to the Ezeio Controller.
7. Setting the 2400-A16 Station number, Polling Address.
8. Configuring the Ezeio with the 2400-A16.
10. 2400-A16 input examples on the Ezeio.
11. Section 2b: Introducing the 2300 input and output expansion field stations.
15. Calibration Offset adjustment during a calibration survey
16. Digital on/off inputs.
17. Alarm options and configuration, including alarm relay outputs, alarm text messages, and
alarm email messages.
19 Activating GSM sims in the ezeio Controller
Ezeio Controller and the 2400-A16 input expansion.
Antennas on GSM model only
GPS (Positioning) Antenna
GSM/3G (communication) antenna

2 | Page Ezeio v9 - 120317
Section 1 covers the Ezeio Controller 4 local inputs, and Section 2 covers adding the
power of the 2400-A16, to expand the inputs up to 40, plus adding more outputs.
Section 1: Configuring the Ezeio Controller local inputs:
The Ezeio™ controller has four standard inputs. Each input may be configured individually in one of the four
ways described here:
To access the input jumper settings, open the Ezeio™ by removing the four black screws.
Read the Ezeio manual pages 12 through to and including 15, covering input connections.
Jumper setting Description
0~5Vdc.
Input impedance is >70kOhm.
Raw reading is about 10000 at 5.0V (0.5V per count).
0~10Vdc.
Input impedance is >70kOhm.
Raw reading is about 10000 at 10.0V (1mV per count).
0~30mA (suitable for 4~20mA transducers).
An internal 100 Ohm resistor connects the input terminal to Common.
Raw reading is about 10000 at 30mA (3uA per count).
Contact, Pulse or Resistive (0~50Ohm).
An Internal 10K resistor will hold the input to 5V.
This is the factory default setting.
4~20mA Resistance or
Pulse input

3 | Page Ezeio v9 - 120317
Getting started with configuration:
Go to www.ezecontrol.com
Click on the ‘Configure’ tag
And then the + by the inputs:
Now select which input you wish to configure. Select the ‘Input Type’ to match the configuration of the
‘Jumper’ setting in the table above. Always remember to select ‘Save Changes’ after making a change.
Important Note: The analogue inputs have a nominal calibration only (ex factory), and where accuracy is
required, individual calibration of each channel is required. This is done with the use of an accurate signal
calibrator.
Follow these easy steps:
1. As an example, on the Ezeio Controller Input 2, the analogue input is set to 0~10v dc. Apply an accurate
10v signal to this input and on the Ezeio ‘Status Page’, note the ‘Raw’ reading on channel 2.
In this example below the Raw reading = 9798.
Enter your Account number, Login and Password.

4 | Page Ezeio v9 - 120317
2. Now go to the Eze Ezeio Configure page and click on ‘Input Type’ and select ‘Custom’ as shown.
3. Now click on ‘Linear Analogue’ and enter the values as shown next:
4. Now click on ‘Save Changes’ and go back to the Ezeio ‘Status’.
Point 1 and Point 2 are what we want this input to read, which in this
example is ‘0~10v’.
Point 1 is the zero point, which is 0 for the Raw Value and 0 for the Value.
Point 2 = 9798 which is the Raw Value from step 1 at 10v dc input, and the
‘Value’ for this example we want to read 10.
If you wish this to actually read another value, for example 100% then
enter 100.
Click on ‘Use’.

5 | Page Ezeio v9 - 120317
5. The Status screen now displays input 2 at exactly 10.00 (or whatever value you have entered).
6. If you require good accuracy at a particular point of the span, then calibrate at that point instead of the full
span point.
7. Apply this procedure (as applicable) to all other analogue inputs on the Ezeio Controller inputs to achieve
accurate calibration.
Section 2a:
Adding a 2400-A16 station to an Ezeio controller:
The 2400-A16 is a high quality, high accuracy I/O station
(input/output expansion station), designed for a wide variety of
applications, and is easily implemented with the Ezeio.
Up to 16 Isolated Universal Analogue Inputs, with Plug In
Terminals.
Each Input is fully Isolated and Individually Selected & Scaled.
RTD, T/C, mA, mV, V & Pulse/Digital as follows:
RTD: Pt100/Pt1000, -200~320°C to -200~800°C.
T/C: B, E, K, J, N, R, S, T, with CJC.
mA: 4~20mA, 0~2.5mA.
mV: -25~25mV to -200~200mV.
V: 0~1V to 0~15V.
Pulse/Digital: Meter pulses, Counting and Frequency.
Max speed 2500Hz.
Four Isolated Digital Inputs.
State or Count.
Max speed 8000Hz.
Two Analogue, Isolated, 4~20mA Outputs.
Two Isolated, Relay Outputs for alarm or control.
Comms Ports:
Port 1: Isolated RS422/RS485 or Ethernet TCP/IP (option).
Port 2: Isolated RS232/RS485.
USB programming port via XU-USB programming key.

6 | Page Ezeio v9 - 120317
Please note: The 2400-A16 I/O expansion station is shortened to ‘A16’ below.
Notes:
a. More than one A16 can be added to an Ezeio controller.
b. The Ezeio Controller will accept up to 40 inputs per Ezeio controller, after which, add another Ezeio.
c. The A16 is available with 3 options for the number of analogue inputs:
8 inputs, 16 inputs.
Follow these steps to add one or more A16’s:
Disconnect both the Ezeio Controller and A16 from the power supply.
First is to connect the A16 to the Ezeio Controller ‘ModBus 485’ port.
The A16 has 2 ports which are both ModBus RTU RS485 capable.
Connection to the Ezeio Controller ‘ModBus 485’ port is by using a standard Ethernet cable plugged into the
Ezeio Controller and broken out to twisted pairs.
Getting started with configeration :
The first task is to configure the A16.
Connect the A16 to a computer as covered bottom page 16 of the ‘2400-A16 Installation Guide’.
If you do not already have a copy of the ‘Intech Micro Station Programmer Software’, download and install
from this link:
http://www.intech.co.nz/downloads/download-software.html
Run the ‘Intech Micro Station Programmer Software’.
Eze Controller
Two of these pairs are used to connect to one of the A16 RS485 ports, to the ‘ModBus 485’
ports of the Ezek Controller as follows:
Blue pair: Blue = 70 on A16 comms.
Blue/White = 71 on A16 comms.
Brown pair: Brown = 74 on A16.
Brown/White = not connected.
After the connections are complete, power up both the Eze Controller and A16.

7 | Page Ezeio v9 - 120317
Click on the ‘Auto Detect 2400 Station’.
Configure the required input channel settings as shown below.
The 2 important areas to make the same as the Ezeio is the Baud rate, the ‘Port Settings’. This A16
configuration screen below displays the parameters the A16 should be set to with special attention to the
‘Address’ which is referred to on the Ezeio Controller as the ‘Polling Address’.
Note that on the A16, the ‘Address number’ can be set differently for each (comms) port, so make sure the
A16 port used for the Ezeio Controller is the same as that used in the Ezeio Controller.
A16 Ezeio
Remember that if two or more A16’s are connected to the Eze
Controller, the A16 ‘Address’ and corresponding Eze ‘Polling Address’
on the 2nd unit must set to a different number. Never use the same
number twice.
For example, the 2nd A16 ‘Address’ and Eze corresponding ‘Polling
Address’ may be set to 2.

8 | Page Ezeio v9 - 120317
Configuring the Ezeio Controller:
Go to www.ezecontrol.com
The first task is to add the A16 onto the Ezeio Controller. Click on the ‘Configure’ option on the tags and wait
for the Configure screen to appear:
Click on ‘Devices’ and then click on ‘Add Device’.
Next, enter the ‘Serial/ModBus Polling Address’, which must be set the same in the A16 as well.
In this example, 1 has been entered and the A16 has been configured as “address 1”:
Enter your Account number, Login and Password.
Scroll down to :
“Intech”
Next select from the list,
either :
“Intech A16”
or
“Intech A16 onboard RE”
The two”Intech A16” options concerns the A16 relay outputs only:
“Intech A16” supports the 2400-R2 (16 Channel Relay Output Expander).
“Intech A16 onboard RE” supports the A16 two onboard relay outputs.
Generally, the most popular option is the “Intech A16 onboard RE”

9 | Page Ezeio v9 - 120317
Next, click on ‘System’.
Next task is to add the A16 inputs onto the Ezeio Controller:
Click on ‘Inputs’ and then click on ‘Add Input’.
Set the Modbus Baud to the same as that
of the A16 (as shown above).
Note: Not all the options are shown.

10 | Page Ezeio v9 - 120317
Example 1: Ezeio temperature input scaling for RTD’s and thermocouples.
Before proceeding any further, Click on ‘Save Changes’.
Select ‘Custom’ for all A16 input configurations.
Type in these 2 calibration details for all listed temperature probes,
both RTD and Thermocouple.
The A16 sends the exact temperature to the Eze Controller.
Chose a ‘Logging’ time.
Note: Failure to select a Logging time will result in this input not
being Viewable on Eze.
In this case, the Ambient Temperature Probe is wired in the A16,
input 1.
Click on ‘Status’ to see the flow meter reading.

11 | Page Ezeio v9 - 120317
------------------------------------------------------------------------------------------------------------------------------
Section 2b:
Adding a 2300 station to an Ezeio controller:
Notes:
a. More than one 2300 can be added to an Ezeio controller, including a mixture of A16’s and 2300 stations.
b. The Ezeio Controller will accept up to 40 inputs per Ezeio controller, after which, add another Ezeio.
Follow these steps to add one or more A16’s:
Disconnect both the Ezeio Controller and 2300 from the power supply.
Connection to the Ezeio Controller ‘ModBus 485’ port is by using a
standard Ethernet cable plugged into the Ezeio Controller
‘ModBus 485’ port and broken out to twisted pairs.
The 2300 series field stations are a family of modular I/O
Remote Stations, that add an even lower cost option to Intech’s
already extensive intelligent I/O Remote Station family and
connect directly to the Ezeio.
The 2300 series I/O stations are made up of stand-alone
Analogue and Digital—Input or Output stations. Communications
between the Ezio and the 2300 series stations is RS485 (1 pair
with screen cable) multi drop as standard
RTD, T/C, mA,mV & V, plus Digital input and relay outputs as
follows:
Model
2300-RTD6 : RTD: Pt100/Pt1000, -200~320°C to -200~800°C.
2300-Tc8 : T/C: B, E, K, J, N, R, S, T, with CJC.
2300-A8II : mA: 4~20mA, 0~2.5mA.
mV: -25~25mV to -200~200mV.
V: 0~1V to 0~15V.
Relay outputs, Contact rating: 240Vac
Eze Controller

12 | Page Ezeio v9 - 120317
Getting started with configeration :
The first task is to configure the A16.
On the Ezeio, ‘Set the 2300 Station ID address’ which is referred to on the Ezeio as the ‘Polling Address’.
Note that on the 2300 station, the ‘Address number’ (station ID), is set via dip switches.
Refer to the 2300 “Installation Guide”.
After the connections are complete, power up both the Eze Controller and 2300.
Two of these pairs are used to connect to one of the A16 RS485 ports, to the ‘ModBus 485’
ports of the Ezek Controller as follows:
Blue pair: Blue = 70 on A16 comms.
Blue/White = 71 on A16 comms.
Brown pair: Brown = 74 on A16.
Brown/White = not connected.
Ezeio
Remember that if two or more 2300’s are connected to the Eze
Controller, the 2300 ‘Address’ and corresponding Eze ‘Polling Address’
on the 2nd unit must set to a different number. Never use the same
number twice.
For example, the 2nd 2300 ‘Address’ and Eze corresponding ‘Polling
Address’ may be set to 2.

13 | Page Ezeio v9 - 120317
The first task is to add the 2300 onto the Ezeio Controller. Click on the ‘Configure’ option on the tags and wait
for the Configure screen to appear:
Click on ‘Devices’ and then click on ‘Add Device’.
Next, enter the ‘Serial/ModBus Polling Address’, which must be set the same in the 2300 as well.
In this example, 1 has been entered and the 2300 has been configured as “address 1”:
Note : The ‘Polling Address’ is set via dip switches. Refer to the 2300 Installation Guide.
Click on ‘Add Device’.
Enter your Account number, Login and Password.
Scroll down to :
“Intech”
Next select from the list,
2300-Input/6-8Ain

14 | Page Ezeio v9 - 120317
Next, click on ‘System’.
Next task is to add the 2300 inputs onto the Ezeio Controller:
Click on ‘Inputs’ and then click on ‘Add Input’.
Set the Modbus Baud to the same as that
of the 2300.
Note: Not all the options are shown.

15 | Page Ezeio v9 - 120317
Example 1: Ezeio temperature input scaling for RTD’s and thermocouples.
Before proceeding any further, Click on ‘Save Changes’.
Select ‘Custom’ for 2300-RTD6 and 2300-Tc8 input configurations.
Type in these 2 calibration details for all temperature inputs.
The 2300 sends the exact temperature of the RTD’s and
thermocouple’s to the Eze Controller.
Chose a ‘Logging’ time for this input to be logged.
Note: Failure to select a Logging time will result in this input not
being logged.
In this case, the Ambient Temperature Probe is wired into the
2300-RTD6, input 1.
Click on ‘Status’ to see the flow meter reading.

16 | Page Ezeio v9 - 120317
------------------------------------------------------------------------------------------------------------------------------
Warning : When changing the A16 or 2300 station number (Polling Address), the inputs do not automatically
reconfigure. They will still poll the old address.
So if you change the modbus polling address under Device, you need to also refresh the input settings.
The quickest way to do that is to simply go to each input, change of the inputs to another input (under “Input
Location” on the Ezeio), - Click on ‘Save Changes’ - change back and save again.
This will refresh the setting, and it will poll the correct A16 station.
Calibration Offset adjustment during a calibration survey
Instructions for applying an offset (zero) adjustment :
Example 1. In this example, the temperature on the Eze is reading 0.5°C low.
A +0.5°C offset needs to be applied to correct the error :
------------------------------------------------------------------------------------------------------------------------------------
Type +0.5 as shown here, , to the
end of the existing calibration value.

17 | Page Ezeio v9 - 120317
Example 2. In this example, the Main Incomer power supply to a factory is reading 4.8 Kilowatts high.
A -4.8Kw offset needs to be applied to correct the error :
This procedure is the same for any reading eg : flow meter, pH, pressure etc.
Note : be careful not to overwrite or alter the existing calibration values. A copy of the existing
calibration values should be made before proceeding to protect against accidental overwrite.
Next input configuration example is displaying an on/off state e.g. motor run/stop, valve open/closed, alarm
on/off.
.
Type -4.8 as shown here, to the end
of the existing calibration value.

18 | Page Ezeio v9 - 120317
Alarms
Ezeio provide a powerful mix of alarm outputs including: alarm relay actuation on the Ezeio controller, A16 and
2300 relay outputs, email alarm messages, SMS text messages. All of this is covered in the Ezeio manual
starting on page 35.
Supplementary notes: Terminology varies a little compared to SCADA but is easy to follow.
1. Each input can have upto 4 alarms.
To add alarm 1, click “Add Alarm” , or to modify an existing alarm, select the alarm at bottom of channel
configuration screen.
Two set point settings are required, one for setting the alarm, and the 2nd for unsetting the alarm as per this
screen shot:
Now we need to link this to an actual Relay Output :
Setting up an Alarm Relay Output
When in this alarm configuration screen,
leave this configuration as it is shown here.
Give the alarm a name.
Set point value for triggering the alarm on.
Time delay – alarm condition must be present for this period
before the alarm activates (from 1 sec to 100 mins)
Set point for turning the alarm off.
Time delay – alarm condition has cleared and must remain
cleared for this period before the alarm deactivates
(from 1 sec to 100 mins).
Setup both these areas.
“Add Alarm Action” relates to the “Alarm Settings” Hi Temp
Alarm setpoint above that activates the alarm relay or message.
“Add Restore Action” relates to the “Restore Settings”
setpoint above that deactivates the alarm relay or message when
temperature drops within alarm limits.
1st setup “Add Alarm Action” for a high alarm relay output
on the ezeio Controller (or the 2400-A16 or 2300).
Relay outputs have more options than txt or email messages.
On the next screen, we give this alarm a name.
Then we select “Set Output” so as we can select
Relay output – in this case, Relay 1, which is a label only and is
not yet linked to an actual relay output.
Set “Cadence” to “On” to activate the relay output action.
“Cutoff” has 2 useful options :
“0” as shown will permanently activate the relay output until the
“Restore Action” setpoint deactivates the relay when the
temperature drops within alarm limits.
Alternatively, enter a number greater than 15, and the output
relay will, on an alarm condition, activate for that period and
then deactivate.
Eg 30 seconds will activate the output relay for approximately
30 seconds and then deactivate.
The alarm output will not activate again until the temperature
returns within alarm limits, and then enters a new alarm
condition.
Please note : These times are approximate only, depending on
band width etc.
A
B

19 | Page Ezeio v9 - 120317
Under “Outputs”, select “Relay 1” to match that selected above.
We now need to go back and click on “Add Restore Action” above in A, to setup the setpoint that deactivates
the alarm relay when the temperature drops within alarm limits. The next screen is :
This completes the configuration of the High Temperature Alarm setpoints and alarm ouput relay.
If a Low Temperature Alarm is required, repeat this configuration process again, starting from the start of the
“Alarms” section above.
The same alarm relay output can be chosen, or a separate Low Alarm Relay Output can be configured instead.
Example for configuration of an alarm SMS text or an email alarm message:
To configure an SMS alarm text or an email alarm message, select
“Send Message”. Refer “B” above on page 15.
Important note: The monthly ‘Service plan’ fee you chose from Eze has a monthly
limit on text messages. Be careful when configuring and saving configuration changes,
as this resets the alarm code and will generate another text message on any text alarms
that have been activated.
Move the alarm set point clear of any alarm point to prevent wasting text messages
when editing.
For SMS alarm text message, enter the mobile
phone number in this box
Use full international format.
For email alarm messages, enter your email
address in this box,
Select the actual hardware relay. In
this case, it is the eze Controller
Relay Output 1.
We give this alarm a name.
Then we select “Set Output” so as we can select
Relay output – in this case, Relay 1.
Set “Cadence” to “Off” to deactivate the relay output
action.
“Cutoff” in this example, has been set to “0”, as no time
delay is required to deactivate the alarm relay.

20 | Page Ezeio v9 - 120317
Activating GSM sims in the Ezeio Controller :
1. Obtain a data GSM sims with no password.
2. Place sims in a mobile phone to activate as per the providers instructions.
3. Place the sims in the Ezeio Controller with the chisel edge of the sims at the top :
.
The Ezeio Controller must be plugged into the local Ethernet with access to the internet.
Log into the Ezeio Configuration area, click on “System”.
Each provider has a special word that must be typed in as explained below :
Note : to get the Ezeio communicating on the simms after setting up with TCP connected, requires the
power to be turned off/on for a connection to be re-established via the simms card.
Setting required for Vodafone New Zealand
Connect via Ethernet after changing the SIM over.
Changed the APN setting to vodafone
Reboot after removing Ethernet cable.
Telecom: Steps:
Connect via Ethernet after changing the SIM over.
Changed the APN setting to internet
Reboot after removing Ethernet cable.
2degrees: Steps:
Connect via Ethernet after changing the SIM over.
Changed the APN setting to internet
Reboot after removing Ethernet cable.
Table of contents
Other Intech Instruments Ltd Measuring Instrument manuals
Popular Measuring Instrument manuals by other brands
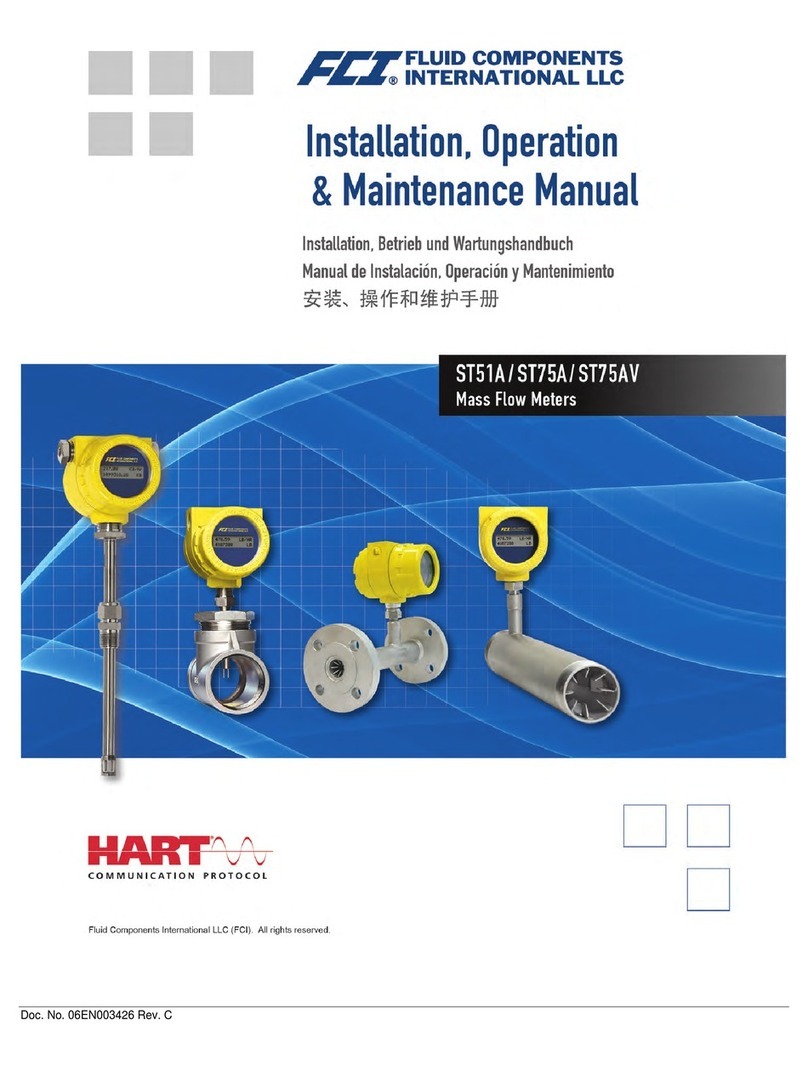
Fluid Components Intl
Fluid Components Intl ST51A Installation, Operation & Maintenance Instruction Manual

Norav Medical
Norav Medical NR-1207-3 Installation and operation guide
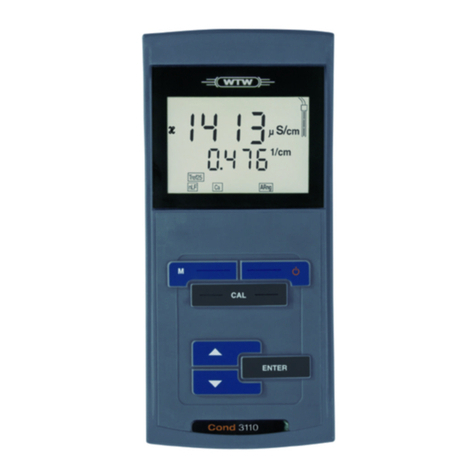
Xylem
Xylem wtw Cond 3110 Quick start manual

Holex
Holex 421727 user guide
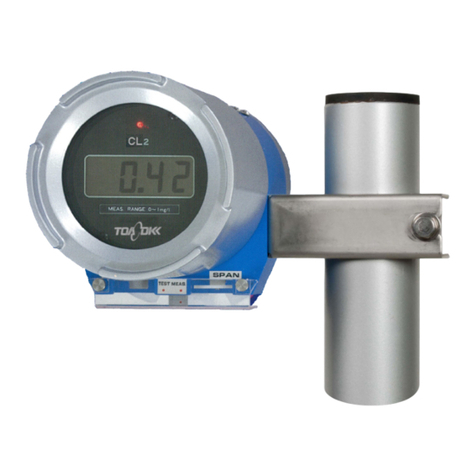
TOA-DKK
TOA-DKK CD-36D instruction manual
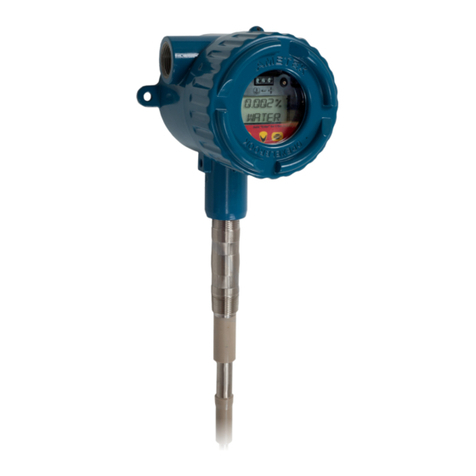
Ametek
Ametek Drexelbrook Universal IV quick start guide