Hathaway Replay PlusV3 User manual

IDM T3
User Manual
incorporating
™
Replay Plus V3
40-8506-01

i
Introduction
IDMOverview ............................ 2
About this Manual ................................ 2
WheretoGoforFurtherHelp ....................... 2
WhatisanIDM? ................................. 2
IDMT1 ........................................ 2
IDMT2 ........................................ 3
IDMT3 ........................................ 3
IDMT4 ........................................ 3
IDMT5 ........................................ 3
IDMT6 ........................................ 4
LSU(LocalStorageUnit) .......................... 4
InstallationConfigurations .................. 5
TypicalInstallations ............................... 5
IDMFunctions ............................ 6
DFRFaultRecording .............................. 6
TSSTriggeredSlowScan .......................... 6
CSS Continuous Slow Scan ......................... 6
HarmonicsRecording ............................. 6
Sags and Swells - Power Quality Sensor ............... 7
Power Quality Data Logging ........................ 7
FlickerRecordingFunction ......................... 7
Replay™Plus Overview......................... 8
About Replay™Plus ................................. 8
Installation
UserConnections......................... 10
System Layout .................................. 10
Input / Output Connections ........................ 10
Power Supply and Earthing ........................ 10
Analog Inputs ................................... 10
Event / Digital Inputs (Standard) .................... 11
AlarmOutputs .................................. 11
EthernetConnections ............................. 11
SerialPorts ..................................... 12
ClockSynchronisation ............................ 13
UsinganExternalPPS ............................ 13
UsingNGTS.................................... 14
LCD/KeypadOperation .................... 15
NormalOperation ............................... 15
DisplayAlarms?................................. 15
ManualTrigger?................................. 15
TestRelays? .................................... 15
Satellite Info? ................................... 15
ExamineIDs?................................... 16
DisableTriggers................................. 16
ChannelCheck? ................................. 16
VersionNumbers? ............................... 17
ShowBaudRates? ............................... 17
Toggle IP / Name ................................ 17
EraseNVStorage................................ 18
DTFResults .................................... 18
LEDs-NormalRunTimeMode .............. 19
IDM DAU LEDs ................................ 19
OK / GPS / PPS LEDs ............................ 19
AlarmLED..................................... 19
LEDs1-6 ..................................... 19
ConnectingPeripherals .................... 20
PeripheralTypes ................................ 20
Peripherals-LSU................................ 21
Peripherals-HubShelf ........................... 21
Peripherals-Modem ............................. 22
Peripherals-Printer .............................. 22
Peripherals-LocalPC ............................ 23
ReplayPlus
Replay™Plus Installation ...................... 25
Installing Replay™Plus ............................. 25
SystemRequirements............................. 26
TheAccessDatabaseandFileStorage ........ 27
About the Access Database ........................ 27
FolderStructure ................................. 27
ChangingtoaDifferentDatabase ................... 27
Backup Database ................................ 28
AccessingtheDemoDatabase ...................... 28
Replay™Plus Security......................... 29
Replay™Plus SecurityOverview ...................... 29
User-Administrator ............................. 29
AdministratorPrivileges .......................... 29
UserAccessLevelPrivileges....................... 31
Replay™Plus Explorer ........................ 32
The Replay™Plus Explorer Window ................. 32
UsingTheDeviceListTree ........................ 33
TheRecordsDisplayOption ....................... 33
The Filter Display Option ......................... 35
ConfiguringEthernetCommunications ....... 36
InstallingTCP/IPforNetworkCommunications........ 36
Installing TCP/IP for Dial-Up or Direct Connect
Asynchronous Communications .................... 36
Installing Direct Connect Communications - Windows 95/98
.............................................. 36
Installing Direct Connect Communications - Windows NT
.............................................. 37
MakingaNetworkConnectiontotheIDM ............ 38
Configuring Replay™Plus for Network Communications . . . 38

ii
Configuring Replay™Plus for Dial-Up or Direct
Communications ................................ 38
AddingaNewInstallation ................. 39
CreatingaNewStation ........................... 39
CreatingaNewDevice ........................... 39
EthernetCommunications ......................... 39
ModemCommunications.......................... 39
Direct Connection (RS232) ........................ 40
ConfiguringanIDM.............................. 40
Adding a DAU, LSU or PC ........................ 40
SettingtheDefaultGateway ....................... 41
ChangingIPAddresses ........................... 42
AddingaTimeSourcetoaDAU.................... 42
AddingandConfiguringaModem .................. 45
Adding a Remote Replay™Plus Dial-UpPC ............. 46
AddingandConfiguringaLocalPrinter .............. 47
IDMConfiguration........................ 49
IDMConfigurationOverview ...................... 49
GlobalSettings-Environment...................... 49
GlobalSettings-OutputDestinations ................ 49
GlobalSettings-DFR ............................ 50
GlobalSettings-TSS............................. 50
GlobalSettings-CSS ............................ 50
GlobalSettings-SER ............................ 51
DAU Configuration - DFR ........................ 51
DAU Configuration - TSS ......................... 52
DAU Configuration - CSS ......................... 52
DAU Configuration - Logging ...................... 53
DAU Configuration - Harmonics .................... 53
DAU Configuration - Power Quality Sensor ........... 54
DAU Configuration - Flicker ....................... 54
DAU Configuration - Cross-Triggering ............... 55
DAU Configuration - Security ...................... 55
ConfigureAnalogChannels........................ 57
ConfigureEventChannels ......................... 58
ConfigureCircuits ............................... 58
Report DAU and Report Calculations ................ 59
ConfigureSensors ............................... 60
DAU Configuration - Trigger Groups ................ 61
SendingConfigurationtotheDAU .................. 62
Communications ......................... 63
CommunicationsOverview ........................ 63
LoadingDirectories .............................. 63
RetrievingDFRandTSSRecords ................... 64
RetrievingCSSRecords........................... 64
RetrievingFlickerRecords ........................ 64
Retrieving Logging Records ....................... 64
RetrievingHarmonicsRecords ..................... 65
RetrievingSequenceofEventData .................. 65
IDM Polling ............................. 66
PollingOverview ................................ 66
AutoPollingConfiguration ........................ 66
PollingOperation ................................ 67
PollingHistoryErrors ............................ 70
Pausing and Disabling Polling ...................... 70
StopPollJob(s),FlushQueue ...................... 71
PollNow(ManualPoll) ........................... 71
Replay Settings - Polling .......................... 72
RecordViewer ........................... 74
RecordViewerOverview.......................... 74
TypicalRecordViewer ........................... 74
AnalogChannelLabelMenu ....................... 75
GraphicsConfiguration ........................... 76
AdvancedFeatures-Sources ....................... 76
AdvancedFeatures-DisplayConfigurations .......... 77
AdvancedFeatures-CalculatedChannels............. 77
AdvancedFeatures-CombinationChannels........... 77
AdvancedFeatures-DistanceToFaultCalculation ..... 78
Advanced Features - Sequence Components ........... 79
Advanced Features - Microsoft Excel Export .......... 80
AdvancedFiltering........................ 81
Advanced Filtering Overview ...................... 81
Creating a New Filter ............................. 81
Saving and Using a Newly Created Filter ............. 83
Importing and Exporting Filters ..................... 84
Editing or Deleting a Filter ........................ 84
Filter Auto Refresh ............................... 84
Creating and Using Profiles™.................. 85
Profiles™Overview ................................ 85
CreatingaNewProfile............................ 85
Running a Profile ................................ 86
EditingorDeletingaProfile ....................... 87
ProfileProperties ................................ 88
ProfileTimeLine ................................ 88
Replay™Plus Troubleshooting .................. 90
Replay™Plus Troubleshooting Overview ............... 90
Replay™Plus Module Cleaner ........................ 90
Appendices
Appendix A - Sample IDM T3 DAU Configuration
Form ................................... 93
AppendixB-DSPCalculations .............. 95
Calculated Quantities ............................. 95
Appendix C - DFR Record Lengths and Sensor OP
Limits .................................. 96
DFRRecords ................................... 96
AppendixD-AboutIPAddresses............ 97
Introduction .................................... 97
InSummary .................................... 98
Appendix E - Changing the IP Address of a DAU or
LSU .................................... 99
Introduction .................................... 99
ChangingtheIPAddressofaDAU.................. 99
ChangingtheIPAddressofaLSU .................. 99
Appendix F - IDM Hardware Overview and Jumper
Settings ............................... 100
IDM T3DAU Hardware Overview ................. 100
TheCPUBoard ................................ 100

iii
TheAnalogBoard .............................. 100
TheEventBoard ............................... 100
TheVT/CTBoard .............................. 101
TheFrontPanelBoard ........................... 101
PSUAsembly.................................. 101
IDM T3 Mk I CPU Board (12-8299) Jumpers ......... 101
IDM T3 Mk I Analog Board (12-8300) Jumpers ....... 102
IDM T3 Mk II CPU Board (12-8313) and Mk III CPU Board
(12-8321) Jumpers .............................. 102
IDM T3 Mk II Analog Board (12-8314) ............. 102
Appendix G - IDM T3/T5 8 Channel DC Isolation
Board ................................. 104
Introduction ................................... 104
ChannelRanges ................................ 105
Channel Input Connections ....................... 105
AppendixH-ConversiontoExternalCTs..... 106
Introduction ................................... 106
Default VT and CT Configurations - VT/CT Board and
AnalogBoard .................................. 109
Internal VT to External CT Conversion - VT/CT Board . 109
Internal CT to External CT Conversion - VT/CT Board . 110
Internal VT or CT to External CT Conversion - Analog Board
............................................. 110
AppendixI-CTRack..................... 111
Introduction ................................... 111
CT Rack Input / Output Connections ................ 112
CTRackUserConnectionDetails .................. 113
4ChannelIDMDCIsolationBoard ................ 114
Appendix J - Generic IDM Calibration Procedure
....................................... 116
Step1-EquipmentChecklist...................... 116
Step 2 - Initial Tests ............................. 116
Step3-CalibrationConfiguration.................. 116
Step4-ZeroOffsetCalibration.................... 117
Step5-FullScaleCalibration ..................... 118
Step6-FinishCalibration ........................ 118
AppendixK-IDMConfigurationCD-ROM .... 119
Introduction ................................... 119
Copy from CD / Read-Only Attribute ............... 119
ReplacingInstalledDatabase ...................... 119
GeneratingIDMDefaultConfigurations ............. 120
SendingIDMDefaultConfigurations ............... 121
About IDM Calibration Files ...................... 121
SendingCalibrationFiles......................... 121
DatabaseVersionNumber ........................ 122
AppendixL-IDMDAURecovery ........... 124
Introduction ................................... 124
Files Required for DAU Recovery .................. 124
DAU Recovery Procedure ........................ 125
BootLoaderMode .............................. 126
AppendixM-UpgradingLSUCode.......... 127
LSUUpgradeProcedure ......................... 129

Introduction
1

2
The IDM T1 DAU
About this Manual
This manual assumes no previous knowledge of operation of
this type of test equipment. Although details are given on the
manner in which the IDM should be used, reference should also
be made to the Help menu within Replay™Plus software for
further instructions.
Introduction (This Section)
First time users of the IDM should read this section which
describes the capabilities of the system and the operational
overview to understand how the IDM functions.
Installation
Gives information on IDM installation with details of the
various inputs and outputs.
Replay™Plus
Describes how to configure IDM parameters using the Qualitrol
Hathaway Replay™Plus software package.
Note:
Some Replay™Plus and IDMCal software screens and
dialog boxes shown in this manual may have updated
due to continuous product enhancement.
Where to Go for Further Help
If problems are experienced with the setup or the use of the
IDM Data Acquisition System, please contact:
Qualitrol - Hathaway Instruments Division
15 Wildflower Way, Belfast, BT12 6TA, Northern Ireland
Telephone: +44 28 9022 5200
Fax: +44 28 9022 5225
Qualitrol - Hathaway Instruments Division
2 Inverness Drive East, Englewood, Colorado 80112, USA
Telephone: +1 303 799 8200
Fax: +1 303 799 8200
e-mail: [email protected]
Internet: www.qualitrolcorp.com
What is an IDM?
The IDM is an advanced multifunction distributed data
acquisition system designed to address the data recording
requirements of a modern transmission or distribution power
substation. The product, when coupled with the Qualitrol
Hathaway Replay™Plus software package, provides a powerful
platform for the acquisition, analysis and reporting of data from
power system substations.
The IDM Data Acquisition Unit (DAU) has six standard formats
(or types):
#A 3U rack mounting model, the IDM T1 (Type 1)
#The IDM T2 (Type 2), an upgrade kit for Qualitrol
Hathaway DFR 0, DFR I, DFR II and DFR II (B) fault
recorders giving them the functions of the IDM T3
#A 6U rack mounting model, the IDM T3 (Type 3)
#A portable model, the IDM T4 (Type 4), which is
based on the 3U IDM T1
#A 6U rack mounting model, the IDM T5 (Type 5)
#A portable model, the IDM T6 (Type 6), which is
based on the 6U IDM T3
IDM T1
The IDM T1 DAU is equipped with 10 analog channels and 16
or 32 event channels, in a 3U 19” rack mountable enclosure that
is 312mm deep.

3
Upgraded IDM T2 DAU
The IDM T3 DAU
The IDM T4 DAU
The IDM T5 DAU
IDM T2
The IDM T2 DAU is a powerful, cost effective upgrade that
extends the life of existing DFRs providing all the functions of
the IDM, including GPS time synchronization, higher scan rates
and software sensors. The upgrade retains the signal
conditioning of the original DFR allowing an upgrade to be
performed without requiring any modification to protection
wiring.
IDM T3
The IDM T3 DAU is equipped with 16 analog channels and 32
event channels, in a 6U 19” rack mountable enclosure that is
326mm deep.
IDM T4
The IDM T4 DAU is an IDM T1 DAU enclosed in a carrying
case for portable use.
Access to the 10 analog and 16 event channels is via 4mm
safety connectors accessible at the rear of the case. External VT
boxes and CT clamps are used for monitoring feeder circuits.
These isolated signals are then fed to the 10 analog channels of
the IDM DAU.
IDM T5
The IDM T5 DAU is equipped with two IDM T3s in a 6U 19”
rack mountable enclosure that is 326mm deep. Each has 16
analog and 32 event channels independent of each other.

4
The IDM T6 DAU
IDM T6 DAU Rear
The LSU (Local Storage Unit)
IDM T6
The IDM T6 DAU is an IDM T3 DAU enclosed in a carrying
case for portable use.
Access to the 16 analog and 32 event channels is via 4mm
safety connectors accessible at the rear of the case.
All IDM DAU types are equipped with fully internal signal
conditioning making them very compact units and suitable for
mounting in the relay panel of the feeder or item of equipment
being monitored. They can be equipped with an optional
internal GPS decoder or synchronized by an external time
source (e.g. IRIG B).
The DAU Channel Configuration Sheet provided with each
recorder gives full details of the analog and event channel
configuration and the supply voltage for each recorder. Sample
forms for each recorder type are included in Appendix A.
LSU (Local Storage Unit)
The LSU is a industrial PC based device that provides the
following functions in an IDM installation:
#Non-volatile storage for DFR, TSS and CSS records
#Modem sharing between multiple DAUs
#Printing records from multiple DAUs
The LSU is equipped with two serial ports, an internal 56K
modem, a minimum 20Gbyte hard drive and a network interface
card equipped with a 10 base T and AUI port. It runs the
multi-tasking Linux operating system.

5
DAU
Modem Printer
Single DAU Installation
HUB
10Base-T or 10Base-FL network
PC
DAU 1 DAU 2 DAU 3
LSU
Modem
Networked IDM Installation
PC
LAN/WAN
HUB
10Base-T or 10Base-FL network
DAU 1 DAU 2 LSU Printer
Networked IDM Installation with Connection to a WAN
Typical Installations
In those installations where more than one IDM DAU is
installed at a given location then they communicate with
each other using twisted pair or fibre-optic Ethernet. To
interconnect devices using Ethernet a hub is required and
some sample network topologies are shown below. Twisted
pair Ethernet communications , also known as 10Base-T,
has a maximum range of 100m (300 feet) under normal
conditions however care should be taken in substation
installations to avoid induced transients from other
conductors. For this reason it is not normally recommended
to extend twisted pair Ethernet cables beyond an adjacent
cubicle in a substation environment. Fibre-optic Ethernet
networks, also known as 10Base-FL, can be extended to
over 1 kilometre while using multi-mode fibre.
This figure
shows a single
DAU installation
with modem
communications and
local printer.
The figure below shows a networked IDM installation with a
local PC, and LSU for mass storage, local printing and remote
communications.
The figure above shows a networked IDM installation with a
connection to a Wide Area Network where data can be
automatically transferred to a remote PC on the network.

6
Fault Recording Function
Triggered Slow Scan Function
Continuous Slow Scan Function
DFR Fault Recording
High speed recording, monitoring the transient response of the
power system and equipment during and just after a system fault
or transient disturbance.
TSS Triggered Slow Scan
Slow speed recording monitoring specified calculated power
quantities for up to 30 minutes before, during and after a
transient fault or disturbance at scan rates up to once per cycle.
Calculated quantities available include rms voltage and current,
real and reactive power, sequence components and frequency.
CSS Continuous Slow Scan
A slow scan function providing recorded calculated quantities
for up to 15 days for long term power stability monitoring. This
function requires a Local Storage Unit (LSU), an industrial PC
based storage device with a hard disk drive providing the long
term data storage facility. Quantities available for recording are
the same as those available for TSS recording.
Harmonics Recording
The power quality recording function in the IDM provides a
comprehensive harmonic recording function in compliance with
IEC 61000-4-7 class B. Harmonics can be recorded on two three
phase groups of analog channels - two groups of voltage
channels or one group of voltage channels and one group of
current channels. Up to 40 user selectable harmonic quantities
can be selected for each three-phase group of analog channels to
be recorded at a sample interval of one minute or 10 minutes.
Data is stored in substation memory as a contiguous block of
data and blocks of data of up to 365 days in size can be
retrieved for display and analysis using Replay™Plus Master
Station software.

7
Harmonics Recording Function
Power Quality Sensor Function
Power Quality Data Logging Function
Flicker Recording Function
Sags and Swells - Power Quality
Sensor
The power quality recording is equipped with a software power
quality sensor that automatically detects voltage sags (dips) and
swells. Each incident that is detected and characterised, in
compliance with IEC 61000-4-30 and the duration and
magnitude of each is stored in the recorder memory.
The last 1000 incidents are retained in memory and can be
retrieved for display and analysis by Replay™Plus Master Station
software.
Power Quality Data Logging
The data logging function also provides the ability to record
calculated quantities such as rms voltage and current, real and
reactive power, sequence components and frequency at sample
intervals of 10 seconds or 10 minutes. In addition to recording
the sample value at the selected rate the maximum and
minimum values over the sample interval can also be recorded.
Up to 60 days of data can be recorded at the 10s sample interval
and in excess of one year's worth of data can be recorded at a
sample interval of 10 minutes.
Flicker Recording Function
Flicker recording in compliance with the IEC 61000-4-15
standard is also provided with Pst and Plt values being provided.
Flicker is calculated on a group of three phase voltage inputs
and the resulting data is stored in recorder memory. Up to 512
days of flicker data can be stored in the recorder memory where
it can be retrieved using Replay™Plus Master Station software.

8
Replay™Plus Master Station Software
™
About Replay™Plus
The Replay™Plus Master Station suite of software applications
provides configuration, communication, data analysis and
management for a range of Qualitrol Hathaway Products.
When used with the IDM it provides the following functions.
#Communications via direct connection, modem, or
twisted pair or fibre-optic Ethernet network
#Local or remote configuration of IDM DAUs
#Data retrieval from IDMs
#Data analysis, presentation and management
A user interface similar to Windows Explorer is used to display
lists of records and installed devices and a “drag and drop”
interface is used for IDM configuration. All device
configuration information, lists of records and record summary
results are stored in a Microsoft Access database to provide
open access to the data however Microsoft Access is not
required to run Replay™Plus.
Replay™Plus will run on Windows 9X / Me / NT 4.0 / 2000 / XP.

Installation
9

10
IDM T3 DAU Dimensions
System Layout
A dimensioned picture of the 6U rack mounting IDM T3 DAU
is shown below. It is an easy device to mount. All analog, event
and alarm signal conditioning is internal to the chassis. All input
signal connections to the device are via screw terminal blocks
on the rear panel. The IDM is small enough to mount directly
into the protection panel of the equipment being monitored.
Input / Output Connections
See IDM T3 DAU Rear picture, next page.
Power Supply and Earthing
The standard DAU power supply is a universal input with the
following ranges:
#80V to 300Vdc
#110V to 220Vac, 50/60Hz
The burden of each DAU is 40VA.
The power is connected to terminals 1and 2on TB8. The labels
Land Nare for live and neutral of an AC supply. The labels +
and –show the polarity of the DC supply.
It is very important to connect an earth to the main earth stud.
This earth stud should be connected to the system substation
earth.
An on / off toggle switch is provided on the rear panel to switch
the power to the DAU.
Analog Inputs
Each DAU has 16 analog
inputs connected to #1TB1,
#1TB2, #1TB3 and #1TB4.
Channels 1to 16 are AC
coupled via interposing
transformers mounted inside
the 6U chassis.
The AC coupled inputs can
be configured at the factory
for voltage or current. The
DAU configuration sheet
provided at the back of this
manual will confirm the
channel allocation.
The sensitivity of the analog
channels is given in the
following table:
CHANNEL
TYPE
NOMINAL
VALUES
FULL SCALE
DEFLECTION
AC Voltage 63.5V or 110V 80V, 130V or
260V
AC Current 1A or 5A 20 x nominal
Selection of the nominal value is via a link on the internal signal
conditioning board in each DAU. These links are set in the
factory to customer requirements and full details are included on
the DAU configuration sheet provided at the back of this
manual.

11
IDM T5 DAU Rear
All analog channels are calibrated in the factory and there is no
need for site adjustments. The DAU configuration sheet
provided at the back of this manual will list the calibration
details of each analog channel.
Each analog channel is fully isolated from each other and to
earth. The following also applies:
#Accuracy of reading better than 0.5% of full scale
#Phase angle error better than 0.5 degrees
#Common mode rejection ratio better than 85dB
Where a DAU is supplied with a combination of current and
voltage channels always ensure that the selected input channel is
a current channel before connecting a CT circuit.
Event / Digital Inputs (Standard)
Each DAU is fitted with 32 digital inputs. The digital input
sensitivity can be 24V, 48/125V or 220Vdc with a tolerance of
±20%. The DAU configuration sheet gives the digital input
details.
The purpose of the digital inputs is to monitor the state of
external contacts normally associated with protection relays and
plant.
The digital input connections are via a screw terminal adapter
block that plugs into #1TB5. Event inputs are on terminals 1 - 8
with the common or neutral on terminal 9. Terminal 10 is earth
and should be connected to the system star earth.
This arrangement makes it easy to
change a complete DAU without
having to disconnect a large number of
wires.
An external DC wetting voltage is
required to operate the digital inputs.
This voltage is normally from the
station battery.
A DC voltage (in the correct range)
applied across an input is interpreted
as a closed contact while the absence
of voltage is interpreted as an open
contact. The current drawn by each
input, when rated voltage is applied is
approximately 1mA.
The digital inputs are arranged in
groups of eight with one common
connection. The digital inputs are
bipolar meaning that the switch wires
and common can be either plus and
minus or minus and plus respectively.
Each group of eight digital inputs is isolated from each other
and from earth.
Alarm Outputs
Each DAU is fitted with Alarm 1 and 2 on #1TB7. Each alarm is
in the form of a voltage free contact rated as follows:
#125VA, 150W
The alarm output connections are via a screw terminal adapter
block that plugs into #1TB7.
Alarm 1 (terminals 1and 2) is an energised closed watchdog
alarm that opens when the DAU is switched off or when a
critical alarm occurs in the system.
Alarm 2 (terminals 3and 4) is a fleeting alarm which is closed
for 250ms every time the DAU is triggered.
Terminal 6 is earth and should be connected to the system star
earth.
Ethernet Connections
There are two types of ethernet connection, a 10Base-T and a
10Base-FL. Both operate at a speed of 10Mbits/sec.
The 10Base-T connection is via the RJ45 socket and is used for
short range communication over standard twisted pair cables.

12
The 10Base-FL connection is via the two ST fibre connectors
and is used for longer range communication over fibre optic
cables.
The white coloured connector is for transmit and the grey colour
for receive.
The connectors are suitable for 62.5/125 multi-mode micron
fibre cable. The wavelength used is 1300nm.
The IDM uses TCP/IP protocol.
Ethernet Firmware Installation
Two versions of firmware exist for IDMs. A typical file name,
where x, yand zare the firmware version numbers, would be as
follows:
#vx080201_x-y-z.bin - For RJ45 twisted pair
ethernet only
#vxAUI080201_x-y-z.bin - For fibre optic ethernet
only
Unless otherwise stated, the shipping default firmware is of the
vx type, which will only support RJ45 twisted pair networking.
If fibre optic network cabling is being used the vxAUI firmware
needs to be uploaded to the DAU.
Firmware is updated using IDMCal software. Refer to
Appendix K, IDM DAU Recovery, for more information on
updating firmware.
As the network will not be active if the wrong firmware is
installed, the uploading will have to be executed through direct
connect or XModem.
The firmware is referred to as Application within IDMCal.
Serial Ports
Each DAU has two serial ports, RS232 (1) and RS232 (2). Port
(1) is accessible on the front panel as well as each rear panel.
The pin out for the RS232 (1) and (2) is given in the following
table:
RS232 (1) RS232 (2)
Pin 1 Pin 1
Pin 2 RXD Pin 2 RXD
Pin 3 TXD Pin 3 TXD
Pin 4 DTR Pin 4 DTR
Pin 5 GND Pin 5 GND
Pin 6 Pin 6 DSR
Pin 7 RTS Pin 7 RTS
Pin 8 CTS Pin 8
Pin 9 Pin 9
A modem, PC or printer can be connected to the serial ports via
standard serial cables.
Port (2) can be configured as an RS485 output via internal link
selection and the RS485 D-type connector on the rear panel.
When a DAU is equipped with an internal GPS time decoder or
IRIG-B time decoder theses devices use the COM 2 port to
interface to the processor and it is no longer available for
external use. Inside the front panel two jumpers, J3 and J4,
select whether the ports is available for external use or is
configured for use by an internal time decoder. For both jumpers
position Ais selected for external use and position Bis selected
for an internal time decoder.
The pin out for the RS485 connection is given in the following
table:
Pin 1
Pin 2 A
Pin 3 B
Pin 4
Pin 5
Pin 6
Pin 7
Pin 8
Pin 9 GND

13
IN
IN
IN
OUT
OUT
OUT
OUT
OUT
OUT
EXT
T/S
EXT
T/S
EXT
T/S
IN
IN
IN
1
1
1
2
2
2
3
3
3
4
4
4
5
5
5
6
6
6
T
ime Maste
r
T
ime Slave #1
T
ime Slave #2
T
ime Slave #3
RS485 Twisted
Pair Cable
IN OUT OUT EXT
T/S
IN
1
#1
TB6
#1
TB6
#1
TB6
#1
TB6
23456
DAU Interconnection for 1pps Synchronisation
Clock Synchronisation
Each IDM DAU has an internal free running clock for time
stamping recorded data. This clock can be synchronized to an
external source via a 1 pulse per second (1pps) applied on one
of three inputs:
#The BNC co-axial connector (TTL level)
#The ST fibre connector
#Pins 1 and 3 of #1TB6 (RS485 multidrop)
Master DAUs can be equipped with an internal GPS or IRIG-B
time decoder. The ANTENNA BNC socket is provided for the
connection of the GPS, or the 1PPS BNC for IRIG-B 003, DC
level, no carrier, BCD/SB data format signal.
Note:
The DAU can be equipped with either a GPS decoder
or an IRIG B decoder.
Where multiple DAUs are installed at one site, one DAU (the
Time Master) can be used to synchronize other DAUs (time
slaves) using a 1pps (one pulse per second) signal. In this way
all DAUs are synchronized to the same time, +/- 10:s, even if
there is no accurate external time source.
The following figure shows how DAUs are interconnected for
1pps synchronisation via RS485.
Note:
For DAUs with clock synchronisation using RS485
multidrop, the last Slave in the chain has jumper J1a
on the Analog board inserted for correct RS485
termination.
The pin out for #1TB6 is given in the following table. The
connections are via a screw terminal adapter block that plugs
into #1TB6.
Pin 1 A (loop in)
Pin 2 A (loop out)
Pin 3 B (loop in)
Pin 4 B (loop out)
Pin 5 External Time Stamp
Pin 6 External Time Stamp
Using an External PPS
An external pulse, 0Vdc and rising to 8Vdc, may be connected
to the 1PPS BNC connector on the rear of the DAU. (BNC
centre = 8Vdc pulse, BNC outer = 0Vdc).
The pulse must be greater than a minimum of 10:s wide. The
pulse must not exceed 20Vdc.
The second is marked as the rising edge of this pulse.
Note:
If an external pps is to be used then jumper J2 on
the Analog board must be set to the Aposition.
For DAUs using IRIG-B via the 1PPS BNC connector
ensure jumper J2 on the Analog board is set to
position B.

14
P2
9-way ‘D’ Type
Connector, Female
P1
9-way ‘D’ Type
Connector, Female
Screen
GRND
TX_D 3
5
2RX_D
5GRND
RED
BLUE
DAU RS232
Serial Port
Tel efault
COM1
DAU RS232 Port to Telefault GPS Cable (16-2017)
The DAU to which this pulse is connected will be the Time
Master DAU.
This Time Master DAU may now be used to provide time
synchronisation to other DAUs, using the RS485 pps connection
described previously.
Using NGTS
NGTS is the definition for a serial time code format and a
device providing this serial time code data format may be
connected to a serial port of an IDM DAU.
The serial connection to the DAU is as detailed below.
DAU COM
PORT DESCRIPTION
Pin 2 RS232 serial data to DAU
Pin 5 Serial data grnd.
If the NGTS device is a Telefault GPS from Qualitrol
Hathaway, then connection to COM1 on the Telefault GPS is
made via Qualitrol Hathaway cable 16-2017 and its details are
shown below.
Note:
If using DAU COM2, jumpers J3 and J4 on the CPU
board must be in position Aand J8 must be in
position B. Additionally on the Analog board, J2 must
be in position A.
Using NGTS with PPS
The NGTS standard, in addition to the serial time code packet,
defines a pulse per minute epoch marker. This pulse is too
infrequent and cannot be used by the DAU (the DAU requires a
pulse per second). Thus, connection of only the NGTS serial
time code packet to a DAU will prevent time errors due to drift,
as a NGTS serial time code packet is issued every minute, but
accuracy to absolute time may be deviant by up to half a second
worst case.
If a pulse per second is available, this should be connected to
the DAU, in addition to the NTGS serial time. The Telefault
GPS manufactured by Qualitrol Hathaway provides a pulse per
second output and this pulse (or equivalent) may be connected
to a DAU as detailed in the table below.
DAU PPS
BNC DESCRIPTION
Inner Pulse signal
Outer Pulse signal grnd.
Caution!
For successful clock synchronisation, the configuration
of the DAU in Replay™Plus must be made to match the
physical installation.

15
Normal Operation
The LCD displays the following during run time operation:
Line 1
This displays the time and date <hh><mm><ss>
<dd><mm><yy>
The display is updated every second.
An underscore will appear between the time and date to indicate
that time synchronisation cannot be guaranteed.
Line 2
This displays the DAU name.
To view the IP address of the DAU, from the keypad use key
sequence:
<left arrow> <up arrow> <right arrow> <down arrow>
Then press <down arrow> again to toggle between the DAU
name and the IP address.
Note - Exiting Menu Options:
All the following menu options can be accessed from
the normal run time display.
Pressing <esc> at any time whilst in the menu option
will return the DAU to the run time display.
Display Alarms?
To view the last eight alarms use the key sequence:
<Enter> <Enter>
The LCD will then display the following:
Line 1
Displays the alarm time and date <hh><mm><ss>
<dd><mm><yy>
Line 2
Displays the alarm message.
From the keypad use <left arrow> and/or <right arrow> to
scroll along the alarm text.
Use <up arrow> <down arrow> to go through the available
alarms.
At this stage pressing the <Reset> key will clear any LEDs
associated with an alarm.
Manual Trigger?
To initiate a manual trigger use the key sequence:
<Enter> <down arrow> <Enter>
After a manual trigger has been sent the DAU will return to run
time mode.
Test Relays?
To test the two status relays use the key sequence:
<Enter> <down arrow> <down arrow> <Enter>
Then <up arrow> or <down arrow> to select which relay.
Then <Enter> <up arrow> Relay closed, <down arrow>
Relay open, <Enter> pulse.
Satellite Info?
To examine the satellite information use the key sequence:
<Enter> <down arrow> <down arrow> <down arrow>
<Enter>
If the master DAU is configured for and locked to the GPS, then
the number of satellites and length of time locked will be
displayed.
If the master DAU is configured for but not locked to the GPS
then the time satellite lock has been lost will be displayed.
If the master DAU does not receive the GPS time string then a
error message to this effect will be displayed.
A Slave DAU displays the time elapsed in minutes since the last
hourly time synchronisation packet was received from the
master DAU.

16
Note:
On power up/reset the master DAU sends a series of
time packets every minute for the first five minutes
and then every hour to the slave DAUs.
Additionally, with the Satellite Info option displayed, pressing
<Enter> again will give details on the antenna status.
The antenna status will be reported as passed, open or short.
These antenna status messages are self explanatory, and the
antenna status option is included to facilitate diagnosis of
potential cable/antenna problems:
#passed - Antenna correctly detected
#OPEN - Open circuit in cable from GPS module to
antenna
#SHORT - Short circuit in cable from GPS module to
antenna
This antenna status information is available to be updated every
minute, after receipt of the GPS time string from the GPS
module (which is observed as a short flash of the GPS LED on
the keypad).
Upon receipt of a GPS time packet, the antenna status displayed
on the LCD of the DAU may be refreshed by pressing <Enter>
Note:
The Antenna Status option is not available for Slave
DAUs or Master DAUs without GPS.
Examine IDs?
To examine the DAU node and network ID use the key
sequence:
<Enter> <down arrow> <down arrow> <down arrow>
<down arrow> <Enter>
This displays the current DAU node within the specified
network.
Disable Triggers
To disable the triggers use the key sequence:
<Enter><down arrow> <down arrow> <down arrow>
<down arrow> <down arrow> <Enter>
The LCD will then display the following:
Esc to confirm
Enter to cancel
Use <Enter> to cancel disabling triggers.
Use <Esc> to display the following:
DISABLED 60min
Esc to re-enable
Use <up arrow> to increase disable time in 30min steps.
Use <down arrow> to decrease disable time in 30min steps.
Use <enter> to default to 60min disabling.
Use <Esc> to re-enable triggers.
Channel Check?
Channel Check Mode Overview
Channel check mode enables the DAU to display analog and
event information on the LCD display to facilitate checking of
user inputs. It can assist in commissioning or checking of user
inputs to an DAU where a pc running Replay™Plus is not
available.
Using the integral keypad of an DAU the user may select an
individual analog channel and its present, secondary value will
be displayed on the LCD. This value will be updated
approximately once per second.
Similarly, event state may be displayed. Groups of 16 events are
displayed simultaneously on the LCD where, by default, a ‘1’
indicates current flow in the event channel and a ‘0’ indicates no
current flow in the event channel.
Channel check mode only allows display of analog and event
channels that are physically available and connected to the IDM
DAU. Quantities computed by the DAU (such as real and
reactive power) are not available for selection by Channel
Check Mode.
To access channel check mode use the key sequence:
<Enter> <up arrow> <up arrow> <up arrow> <up
arrow> <up arrow> <up arrow> <Enter>
The LCD will then display the following:
Enter to confirm
Esc to cancel
Use <Enter> to start channel check mode in the last used
mode, or in the analog check mode if the IDM DAU has been
restarted since this option was last used.
There are two modes of operation, analog and event mode, to
display analogue values and event states respectively.
Use <Esc> to terminate channel check mode.
This manual suits for next models
1
Table of contents
Popular Measuring Instrument manuals by other brands
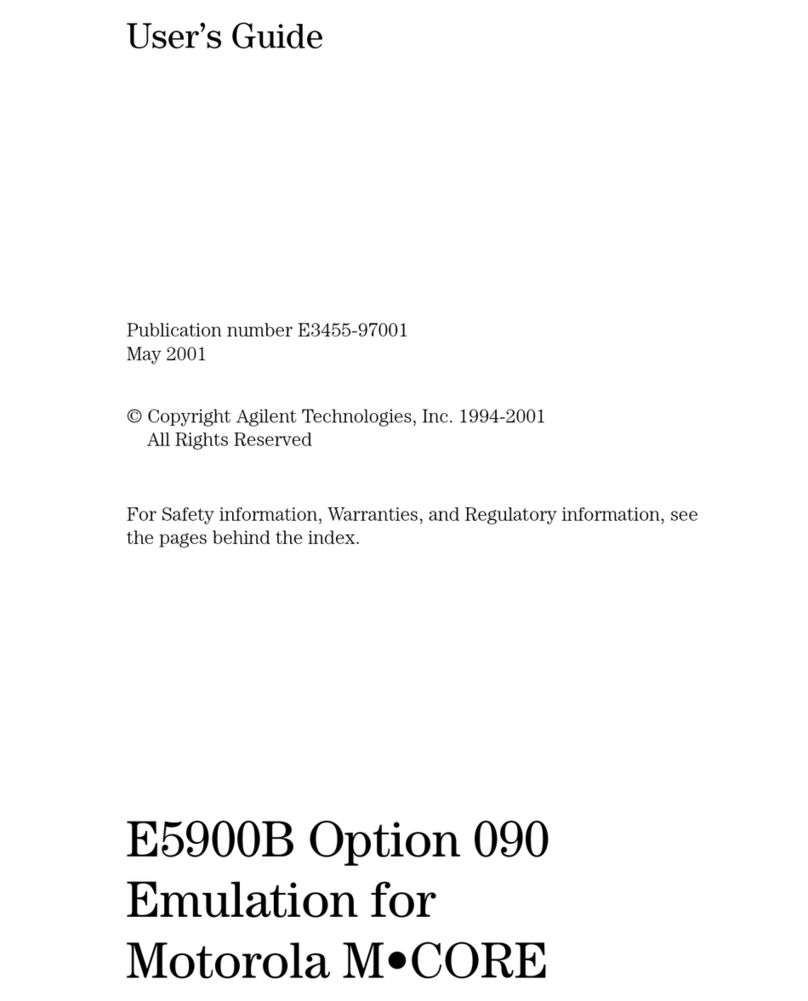
Agilent Technologies
Agilent Technologies E5900B user guide
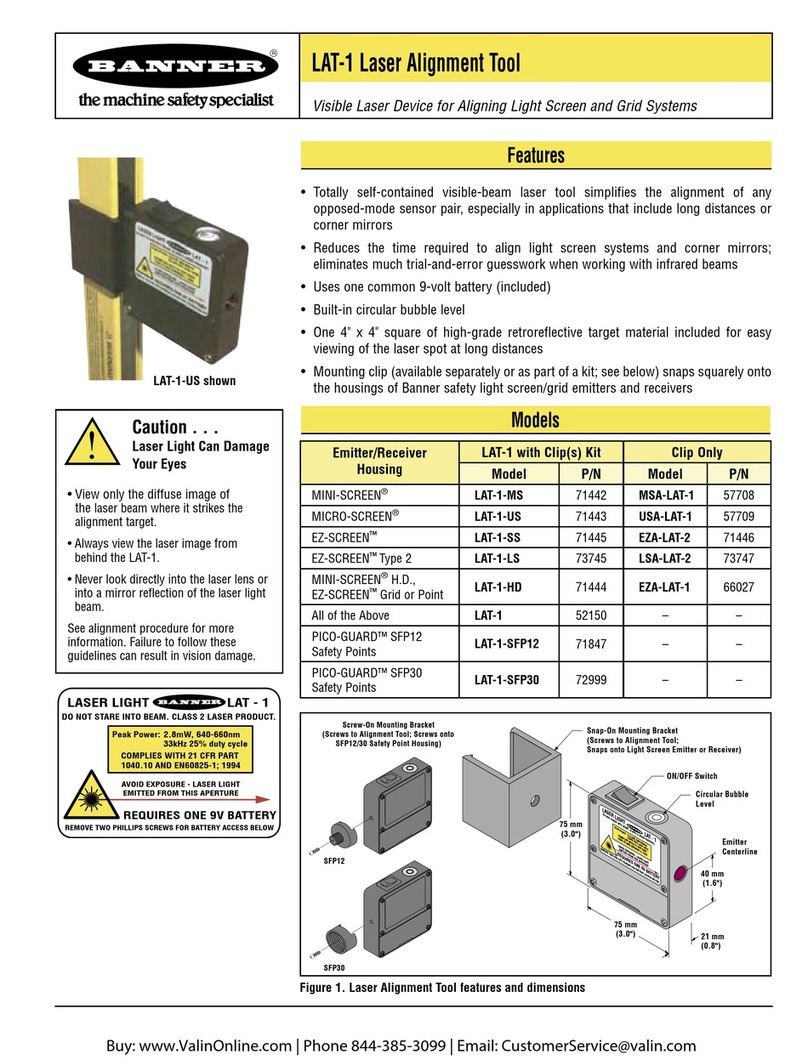
Banner
Banner LAT-1 quick start guide
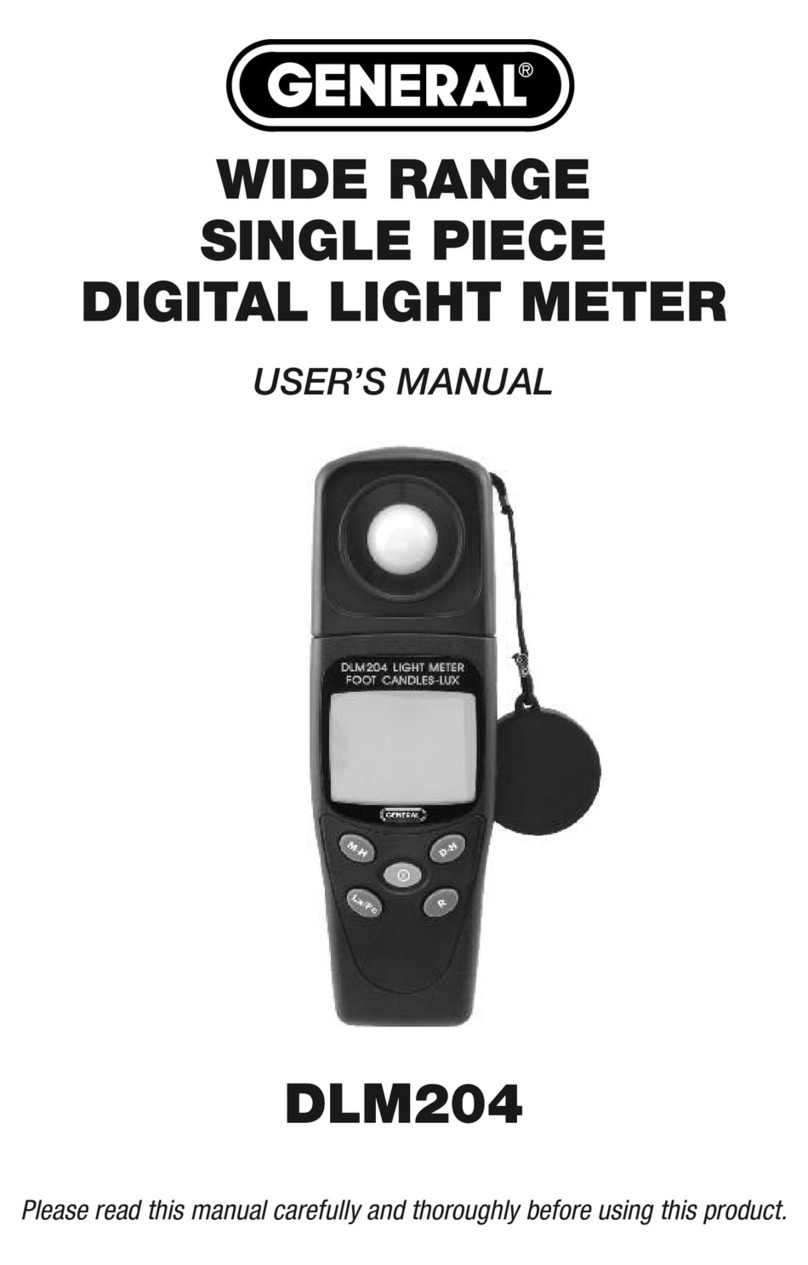
General
General DLM204 user manual
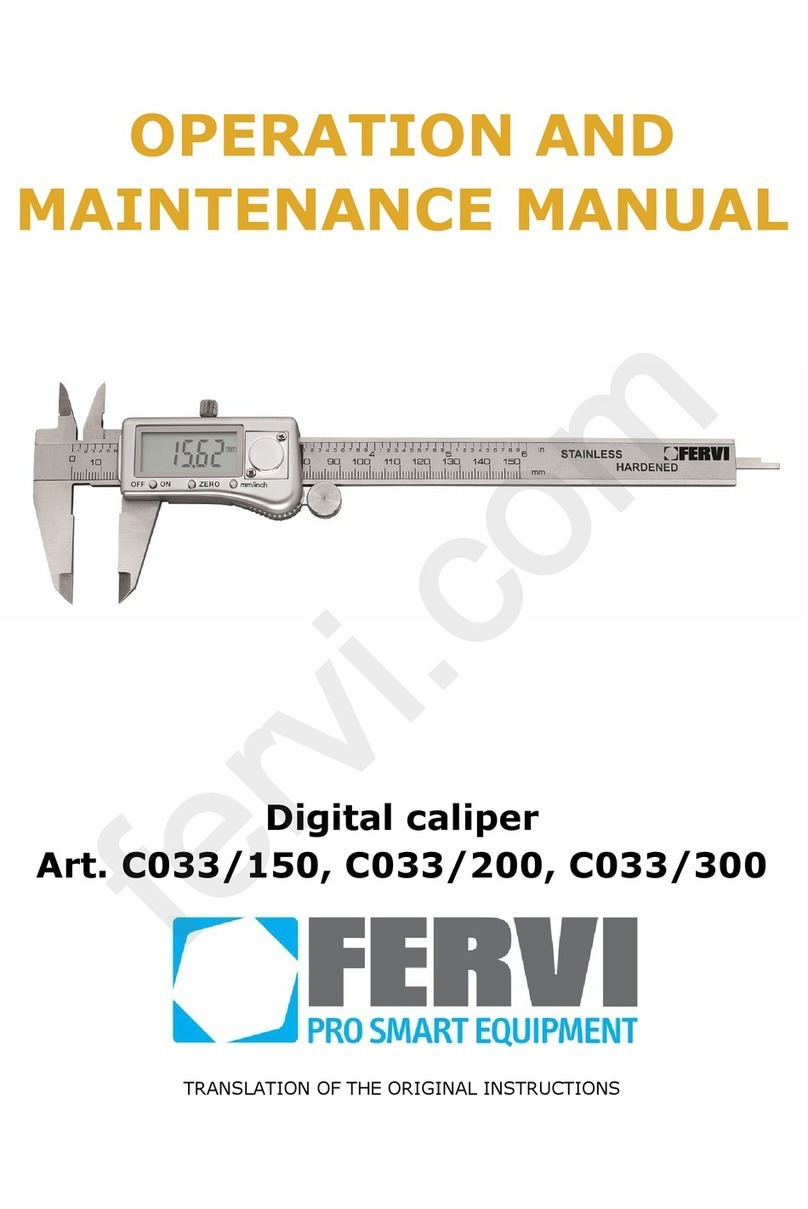
Fervi
Fervi C033/150 Operation and maintenance manual
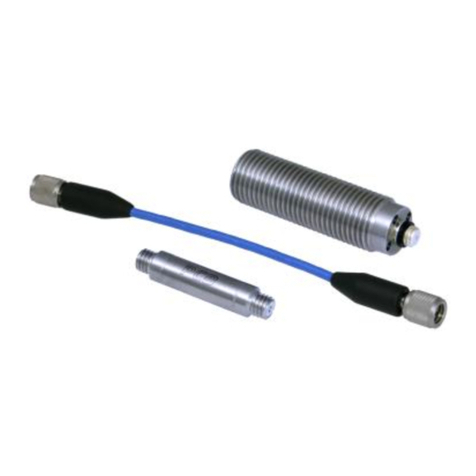
PCB Piezotronics
PCB Piezotronics Tourmaline ICP 134A24 Installation and operating manual
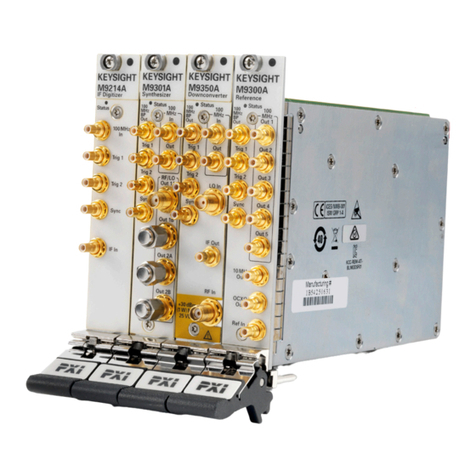
Keysight Technologies
Keysight Technologies M9391A PXIe Guide