Hirata Corporation HNC-544 User manual

The information contained herein is the property of Hirata Corporation and shall not be
reproduced in whole or in part without prior written approval of Hirata Corporation. The
information contained herein is subject to change without notice and should not be
constructed as a commitment by Hirata Corporation.
Hirata Corporation assumes no responsibility for any errors or omissions in this document.
Warranty
All of Hirata's products which is passed our formal inspection test shall be guaranteed against
faults due to the negligence of Hirata for either earlier period of one year or four thousand
hours of operation from the day of shipment from Hirata Factory.
This warranty shall be applicable to the parts replacement and/or labor for repair in our factory
and transportation cost shall not be applied.
We will charge the repair of faults caused by the following reasons:
* Wrong usage which are prohibited in the instruction manual.
* After the expiration of guarantee period.
* Earthquake, fire, riot, violence, war and other force majeure.
* Modification, repair or adjustment is performed by unauthorized person.
Contact your sales agent for individual warranty coverage.
HNC-544
USER'S GUIDE (HD-3814E-3)
Copyright 1999 by Hirata Corporation All right reserved.
First published in June 1998
First revision in August 1998
Second revision in January 1999
Third revision in July 1999
Printed in Japan
Hirata Corporation
Tokyo Head Quarters
3-9-20 Togoshi, Shinagawa, Tokyo 142-0041 JAPAN
Phone (03) 3786-1226
Facsimile (03) 3786-1264
Robotics Division
1016-6 Kusuno, Kumamoto 861-5511 JAPAN
Phone (096) 245-1333
Facsimile (096) 245-0816

World Leader in Production Technology
ROBOT CONTROLLER
USER'S GUIDE
HNC-544
HD-3814E-3
3

FEHLER! FORMATVORLAGE NICHT DEFINIERT. FEHLER! FORMATVORLAGE NICHT
DEFINIERT.FEHLER! FORMATVORLAGE NICHT DEFINIERT.
1-1
CHAPTER 1 INTRODUCTION
1.1 General
This manual describes the controller HNC-544 which controls AC servo mo-
tor from 1 to 4 axes.
Position data of robot can be entered by optional Teach Pendant. Manual
Data Input (MDI) by numeric keys and teaching/Off-line programming is
available as entering method of the data.
Automatic operation executed to confirm the programmed positions in
CHECK mode using the Teach Pendant after entering the position data.
Refer to separate volume of "OPERATION MANUAL" for the detail to use
of the Teach Pendant
HNC controller performs automatic operation by exchanging the signals
with an external programmable controller through DI/DO interface.
Read carefully before use of this machine.
1.2 Notice on Operation
(1) Before switch on the main power, confirm all the cable between the
robot and the controller are firmly connected. Also, confirm the ca-
ble connection for Emergency Stop connector.
(2) Do not use the controller at higher than 50 deg. C and high humid-
ity. The surroundings must be no dust, no smoke, no combustion,
and no corrosion.
(3) Confirm the operation conditions, such as power supply frequency
or dielectric strength, and use the robot in the specified conditions.
(4) Do not operate the robot except as described in the instruction
manual for avoiding the wrong movement of the robot.
(5) The robot must be operated by a trained person.
(6) Before operating the robot, make sure all the personnel and ob-
structions are outside of the maximum reach of the robot.
(7) During teaching or maintenance of the robot, put a warning sign
saying "The robot is in use. Do not touch it." around the robot.
(8) Do not drop or throw the Teach Pendant. Do not carry the Teach
Pendant by holding its cable. Hold the Teach Pendant body firmly.
(9) Dead-man switch is attached on the Teach Pendant for the safety of
the robot operator. Therefore, do not lock the dead-man switch by
tape and so on. This switch works in TEACH mode and CHECK
mode. In case the dead-man switch is not pressed, the robot is in
emergency stop status and does not move.

FEHLER! FORMATVORLAGE NICHT DEFINIERT. FEHLER! FORMATVORLAGE NICHT
DEFINIERT.FEHLER! FORMATVORLAGE NICHT DEFINIERT.
1-2
(10) Before performing the automatic operation, confirm the location of
Emergency Stop (E.S.) button. The controller provided with an ex-
ternal connector for E.S. signal, and the Teach Pendant is provided
with E.S. button. Put the controller to the position you can press or
input E.S. immediately upon occurrence of abnormal status of the
robot.
(11) Do not enter the working area of the robot during automatic opera-
tion.
(12) Before staring the automatic operation, confirm the peripheral de-
vices are ready to start.
(13) The controller is equipped with self-diagnosis function. When ab-
normal states occur, the contents of the states are displayed on the
Teach Pendant. Restore the robot according to this manual. (If
overrun occurs during automatic operation, the code according to
the error is output.)
(14) Dust filter replacement (if necessary)
The controller is cooled by forced air circulation. The controller
cabinet is provided with a dust filter at air intake and exhaust
ports. If the dust filter is clogged, air intake will be hampered and
cause overheating. This can produce erratic behavior in the robot.
Replace the dust filter depends on the environment the controller is
used.
Check it regularly every one or two weeks at dusty place or at least
once a month in normal situation. In case the filter is dirty, clean it
by detaching the filter cover from the controller.
(15) Servo driver inspection
Servo drivers are adjusted before shipment of the robot. However,
if the conditions of using robot is changed, noise or error may hap-
pen. Adjust the trimmers on servo driver. Refer to later chapter for
detail.
Do not touch the controller enclosure at least five minutes after unplugged.
This may hurts the operator by high voltage.

FEHLER! FORMATVORLAGE NICHT DEFINIERT. FEHLER! FORMATVORLAGE NICHT
DEFINIERT.FEHLER! FORMATVORLAGE NICHT DEFINIERT.
2-1
CHAPTER 2 SPECIFICATIONS
2.1 Dimensions
Consider the space for the Teach Pendant and MS connectors.
Fig. 2.1 HNC-544 Dimensions
2.2 Weight
HNC-544 : 12.5 kg
320
140
120
120
57

FEHLER! FORMATVORLAGE NICHT DEFINIERT. FEHLER! FORMATVORLAGE NICHT
DEFINIERT.FEHLER! FORMATVORLAGE NICHT DEFINIERT.
2-2
2.3 Cooling
The controller is cooled by forced air circulation. The locations of the air in-
take and exhaust openings are shown are shown in below.
Fig. 2.2 Cooling Method
At least 30cm clearance must be reserved in front of the air intake and ex-
haust
2.4 Power Supply
Table 2.1 Power Supply
Primary power Single phase AC200V (±10%)
Frequency 50Hz/60Hz
Do not touch the controller enclosure at least five minutes after unplugged.
This may hurts the operator by high voltage.
The power cable is attached when factory shipment. Connect the AC power
supply to light blue and brown lines. The spiral of yellow and green lines is
connected to the controller cabinet. Connect this line to the earth.
2.5 Environmental and Facility Require-
ments
Table 2.2 Facility Ambient Air Quality
Temperature -15-60(at storage)
5-40(during operation)
Relative hu-
midity
10%-90% (at storage)non-condensing
20%-80% (during operation) non-
condensing
Vibration Maximum 0.5G, 120Hz continuous (during
operation)
Air intake fan
Air exhaust fa
n

FEHLER! FORMATVORLAGE NICHT DEFINIERT. FEHLER! FORMATVORLAGE NICHT
DEFINIERT.FEHLER! FORMATVORLAGE NICHT DEFINIERT.
2-3
2.6 Specifications
Table 2.3 Specifications
Item Specifications
Applicable robot Cartesian type robot, SCARA type robot, etc.
Control axis 1 to 4 axes
Control method Numeric control by microprocessor.
Positioning method PTP: Gate motion, Arch motion, Insert motion, Pass mo-
tion etc.
CPC: Linear interpolation, Circular interpolation
Number of pro-
grammed position 1,000 points (max. 2,500 points: with an optional mem-
ory card
Memory back-up Battery back-up by C-MOS-RAM
Memory back-up by optional memory card
Programming reso-
lution 0.01mm
Operation mode KEY-IN, RO-TECH, LI-TEACH, CHECK, AUTO
External interface
Input : SELECT, START, NEXT, POS/INCHING, STOP, HOLD,
Address number
Output : READY, ERROR, PCA, BP, ZONE, CPOUT, A-CAL, M-
data
RS-232C1,200bps, 2,400bps, 4,800bps, 9,600bps
Data input MDI system and teaching system by optional Teach Pen-
dant.
Data load from optional memory card
Data communication by optional HRCS through RS-232C

FEHLER! FORMATVORLAGE NICHT DEFINIERT. FEHLER! FORMATVORLAGE NICHT
DEFINIERT.FEHLER! FORMATVORLAGE NICHT DEFINIERT.
3-1
CHAPTER 3 Hardware Composition
3.1 Outside Structure
Fig.3.1 Front Panel
Table 3.1 Parts List
No. Item
Memory card port
DC24V power fuse holder
Serial I/F connector
Teach Pendant I/F connector
Pendant remove switch
Power switch
AC power fuse holder
Motor power fuse holder
Cooling fan
Time counter
‡@‡A‡B ‡C ‡D
‡E‡F ‡G ‡H

FEHLER! FORMATVORLAGE NICHT DEFINIERT. FEHLER! FORMATVORLAGE NICHT
DEFINIERT.FEHLER! FORMATVORLAGE NICHT DEFINIERT.
3-2
Fig.3.2 Back Panel
Table 3.2 Parts List
No. Item
DO-1connector
DI-1 connector
DO-2 connector
DI-2 connector
Encoder/sensor connector for Z/W-Axis
Encoder/sensor connector for X/Y(A/B)-
Axis
Motor connector
E.S. connector
Power inlet
‡@
‡H
‡A
‡B
‡C ‡E
‡G
‡F
‡D

FEHLER! FORMATVORLAGE NICHT DEFINIERT. FEHLER! FORMATVORLAGE NICHT
DEFINIERT.FEHLER! FORMATVORLAGE NICHT DEFINIERT.
3-3
3.2 Inside Structure
Fig.3.3 Inside Structure (Base Plate)
Table 3.3 Parts List
No. Item
Noise filter
Regenerative register
Switching regulator (24V)
Switching regulator (5V)
Terminal board for power connection
Fig.3.4 Inside Structure
Table 3.4 Parts List
No. Item
System/servo control board (HPC-740A)
Servo power board (HPC-741A)
‡A‡@
‡B
‡D
‡C
Back side
Front side
‡@
‡A

FEHLER! FORMATVORLAGE NICHT DEFINIERT. FEHLER! FORMATVORLAGE NICHT
DEFINIERT.FEHLER! FORMATVORLAGE NICHT DEFINIERT.
3-4
3.3 Block Composition
The hardware mainly comprise the following 8 blocks.
(1) System control (System board HPC-740A
•Controls the entire robot motion.
•Stores the position and the system data.
•Interfaces motor drivers.
(2) Servo interface
Interfaces system board and motor drivers.
(3) DI/DO interface
Interfaces signal from the controller and input signal from PLC.
(4) Memory card interface
Data load from memory card to system board(RAM), and data save
from system board(RAM) to memory card.
(5) RS-232C interface
Interfaces the external device PC via RS-232C.
(6) Teach Pendant interface
Determines the operation mode and handle transactions with Teach
Pendant.
(7) Servo driver control
Interfaces with servo drivers.
(8) Servo driver power generation
Drives the motor.

FEHLER! FORMATVORLAGE NICHT DEFINIERT. FEHLER! FORMATVORLAGE NICHT
DEFINIERT.FEHLER! FORMATVORLAGE NICHT DEFINIERT.
3-5
3.4 Connection Composition
Fig.3.5 Connection Composition
MotorX/Y
MotorZ/W
Noise filter
Memory card
RS232C
Teach
Pendant
Fan
(intake,exhaust)
Motorline IN
PowerAC200V
AC 24V
Motorpower
DI
DO
Power
sw itch
+5‚ u
HPC-740A
System board
System control
Axis control
Servo controlboard
300 ~300 4 boards Z/W axis
encoder
A/B (X/Y)
axis encoder
Z/W encodersi
g
nal
A/B encoder si
g
nal
Powersupply
Transformer
Switching regulator
Terminaltable
HPC-741A
Servo pow erboard
E.S
Timecounter

FEHLER! FORMATVORLAGE NICHT DEFINIERT. FEHLER! FORMATVORLAGE NICHT
DEFINIERT.FEHLER! FORMATVORLAGE NICHT DEFINIERT.
4-1
CHAPTER 4 FUNCTION
The basic function of the controller is to move the robot to programmed po-
sition. To operate the robot easily, the controller has necessary function as
following below.
4.1 Basic Functions
(1) Automatic origin calibration
(2) Store the programmed position
(3) Display the current position of the robot
(4) Move the robot to a target position
(5) Communicate with external PLC or HARL-
(6) Position data handling
(7) Data transfer through RS-232C
(8) Self-diagnosis
When an error occurs in AUTO mode, displays the error message on
the Teach Pendant, and outputs the error signals to the external
device through the robot interface (OUT signal and ERROR signal
corresponding to the error message). When an error occurs in ON-
LINE mode, the error code can be obtained from the external de-
vice, such as PLC.
(9) Stops the robot immediately by Emergency Stop signal
(10) Monitoring parallel(DI/DO) communication
(11) Memory card (option)
Save the position and system data (Refer to the separated volume of
Operation Manual) memory card via memory card port.
The controller has 1,000 position data, 000 to 999. These numbers are
called position data address or just address.

FEHLER! FORMATVORLAGE NICHT DEFINIERT. FEHLER! FORMATVORLAGE NICHT
DEFINIERT.FEHLER! FORMATVORLAGE NICHT DEFINIERT.
4-2
4.2 Emergency Stop (E.S.) Function
To stop the robot immediately upon occurrence of abnormal status of the
robot, the controller is provided with an emergency stop(E.S) function.
(1) Emergency stop
E.S. will be activated at following condition.
•E.S. switch on the Teach Pendant is pressed when the
power is ON.
•Deadman switch is not pressed in TEACH or CHECK mode
when the power is ON.
•External E.S. input (ES-IN: 1-4 pin connectors) terminals
are opened.
•DC24 fuse is opened (blown).
•Neither of the Teach Pendant nor the dummy connector is
connected.
•Encoder error.
•Servo alarm occurrence.
When the all of above condition occurred, E.S function is activated.
•Shut OFF the power supply to the motor.
•Turn OFF the all output signals.
•Ignores the all input signals and command.
•Contact outputs of the external E.S. output (ES-OUT: 2-3
pin connectors) terminals are opened.
•The E-STOPindicator on the Teach Pendant lights up
and a buzzer sounds.
The back panel is provided with an external E.S connector(10P) as
shown following figure.
Fig.4.1 External E.S. Connector
Arrange the E.S button outside of the robot working envelope and
make sure that an operator can access easily. When the abnormal
status occurs, press the E.S button to stop the robot.
System safeguard should be prepared for your safety. Unless having the
device may result sever injury.
81
792
61
3
54
RM15QRD-10S: HIROSE
(Controller side)
RM15QPS-10PH: HIROSE
(External cable side)

FEHLER! FORMATVORLAGE NICHT DEFINIERT. FEHLER! FORMATVORLAGE NICHT
DEFINIERT.FEHLER! FORMATVORLAGE NICHT DEFINIERT.
4-3
(2) Wiring for the E.S. connector
Fig.4.2 E.S. Wiring
and pins connect to external E.S. Close (Short) and pins unless
you use. The current 40mA runs on the line if shorting the pins. E.S. will
be activated when and pins are opened.
and pins are the relay contact output to generate a status signal to an
external device when the E.S. is activated. It is closed in normal status.
The relay is closed (turns ON) when the power source of the controller is
supplied and it is not in E.S. status. The relay is opened (turns OFF) when
E.S. is activated or the power is OFF.
!Specification for the relay contact output (and pins)
G6A-434P-U (OMRON) DC24V(1A)
Encoder disconnect
detection circuit
Teach Pendant
E.S. switch
R1
R2
Fuse
+24V
Internal E.S.
circuit R1 R2
0V
Controller inside
1
2
3
4
Controller outside
External E.S. switch
E.S. output
(Opens at E.S. output)
10P E.S. connector
R1
R0

FEHLER! FORMATVORLAGE NICHT DEFINIERT. FEHLER! FORMATVORLAGE NICHT
DEFINIERT.
6-1
CHAPTER 6 Hardware Setting
6.1 DIP Switch (SW2) on HNC System
Board
There is a DIP switch on the system board (HPC-740A.) Refer to the
following table below for the DIP switch function.
SW2
1 2 3 4 5 6 7 8
ON ON
OFF
Fig.6.1 DIP Switch (SW2)
Table 6.1 DIP Switch Function
Switch
NO. Meaning
1
2
Turn ON switch 1 when using 1 or 2 axes
configuration.
Turn ON switch 1 and 2 when using 3 or 4 axes
configuration.
3 Normally OFF
4 Normally OFF
5 Normally OFF
6
I/O setting for DI/DO
OFF: DI1 0-15
DI2 16-31
DO1 0-15
DO2 16-31
ON : DI1 16-31
DO1 16-31
DO2 0-15
7 Normally ON
8 Normally OFF
The setting of the switch 1, 2, and 4 varies according to the number of axis
to control.
!1 or 2 axes configuration : Turn ON switch 1.
!3 or 4 axes configuration : Turn ON switch 1 and 2.
!Turn OFF the switch 3 and 4 normally.
!Turn OFF the switch 5 except using the absolute encoder motor.
These switches are set before factory shipment. Unless otherwise
necessary or instructed, do not change the switch setting.

FEHLER! FORMATVORLAGE NICHT DEFINIERT. FEHLER! FORMATVORLAGE NICHT
DEFINIERT.
6-2
6.2 System Indicator
An error code will be displayed on the system indicator on system
board(HPC-740A) in case of the error .
!Example : Overrun
Indicator will display “E51” repeatedly.
Table 6.2 Error code
Error message Meaning ON-LINE
mode
output
POS. ERROR XXXX Positioning is not completed. 09
EMERGENCY STOP Emergency stop status 10
A-CAL ERROR N…A-CAL is not completed correctly. 20
ADDRESS ERROR Address over the restriction is
designated. 30
M DATA ERROR M DATA is invalid. 31
SENSOR NOT FIND W-Axis does not stop by the sensor
input. 32
SPLINE DATA
ERROR The data of free curve movement is
invalid. 33
AREA ERROR XXXX Position data is out of area. 40
OVERRUN XXXX Overrun 51
SYSTEM DATA
ERROR System data is corrupted. 63
POINT DATA
ERROR Position data is corrupted. 64
FORMAT ERROR
XXXX Communication format is invalid. 60
COMMAND ERROR Communication command is invalid. 61
UNKNOWN COMMAND Illegal command. 62
SERVO ERROR
XXXX Servo error 70
DUPLICALE
COMMAND Receiving another command while
processing a command. 80
Scene set Error Scene set is out of range with
vision. 81
Work not Find Work-piece is not found. 82
Measurement
Error Measurement conditions are invalid. 83
Out of range Measured data is out of the range. 84
Vision not
ready “NAK”transmission continued. 88
Vision not
Online No response from the vision. 89
IMPOSSIBLE
ERROR The distance for PASS motion is too
short. 90
M NUMBER ERROR M number is not correct. 94
XY CONVERT
ERROR Position data is destroyed. 95
POSITIONING
ERROR Positioning is not completed. 96
START MOTION
ERROR Motor does not rotate. 99
DRIVER ERROR
XXXX Abnormal status occurs in the driver. A0 ( )
ENCODER
DISCONNECT Encoder signal is lost. B0 ( )
The display above is repeated.

FEHLER! FORMATVORLAGE NICHT DEFINIERT. FEHLER! FORMATVORLAGE NICHT
DEFINIERT.
6-3

FEHLER! FORMATVORLAGE NICHT DEFINIERT. FEHLER! FORMATVORLAGE NICHT
DEFINIERT.
6-4
6.3 Pendant Remove Switch
The Pendant remove switch is used for connecting or disconnecting while
the power is supplied to the controller. This feature allows you to read the
error message when any event of error occurrence.
Fig.6.2 Pendant Remove Switch
(1) When disconnecting the Teach Pendant from the controller
1Keep pressing the pendant remove switch.
2Disconnect the Teach Pendant while pressing the pendant remove
switch.
3Connector the dummy connector while pressing the remove switch.
4Detach your finger from the pendant remove switch.
This operation will interrupt the outer mode signal. Thus, the robot may
stop if it is in automatic mode. Do not connect/disconnect the Teach
Pendant except for error verification purpose.
(2) When connecting the Teach Pendant :
1Keep pressing the pendant remove switch.
2Disconnect the dummy connector while pressing the remove
switch.
3Connect the Teach Pendant with pressing the pendant remove
switch. (The mode on the Teach Pendant must be in the ON-
LINE mode.)
4Detach your finger from the pendant remove switch.
5Press the READ key or spd
CAN key. The display on the Teach Pendant
normally shows;
6If the monitor display is not normal, press the pendant remove
switch and connect the Teach Pendant again.
Connecting and disconnecting the Teach Pendant during the automatic
operation may interrupt the PLC communication. Unless otherwise
necessary, do not connect or disconnect the Teach Pendant.
Neither the Teach Pendant nor the dummy connector is connected, the
controller is in Emergency Stop (E.S.) status.
Pendant remove switc
h

FEHLER! FORMATVORLAGE NICHT DEFINIERT. FEHLER! FORMATVORLAGE NICHT
DEFINIERT.
7-1
CHAPTER 7 Preventive Maintenance
Confirm that surroundings meet specifications; frequency, dielectric
strength, etc. Periodical maintenance is highly recommended for full
performance and longer life time. If malfunction happens, follow the
“troubleshooting flowchart” in later chapter.
7.1 Dust Filter
The controller is cooled by forced air circulation. To prevent overheating of
system, the control cabinet is provided with an air vent. A fan-operated
aspirator section is installed on its front. Clean up the filter to maintain
smooth air circulation.
Guar
d
Filte
r
Retaine
r
7.2 Servo Driver
Adjustment of the servo driver is described at later section. Although they
are adjusted before shipment, adjust the servo drivers if the erratic sound
or malfunction should occur because of surrounding changes. Refer to the
next chapter for more detail.
7.3 Battery Voltage
A battery is provided to back-up the position data and other motion
parameter. Lower voltage may cause loosing data. Measure the voltage
between VMEM and GND on system board (HPC-740A) two minutes after
shut down.
Replace the battery when it turns lower than 3.2V or after 4 years or 7,000
hours operation.
7.4 Others
Confirm the operation conditions, such as power supply frequency or
dielectric strength, and use the robot in the specified conditions. Daily and
periodically maintenance is essential to maintain the performance and
lifetime.
Follow the instruction which is described in later chapter of “Trouble
Shooting” in case of abnormal occurrence.
Table of contents
Other Hirata Corporation Controllers manuals
Popular Controllers manuals by other brands

System air
System air fantech IPF05-1L installation instructions

United CoolAir
United CoolAir Marvel Plus Installation, operation and maintenance manual
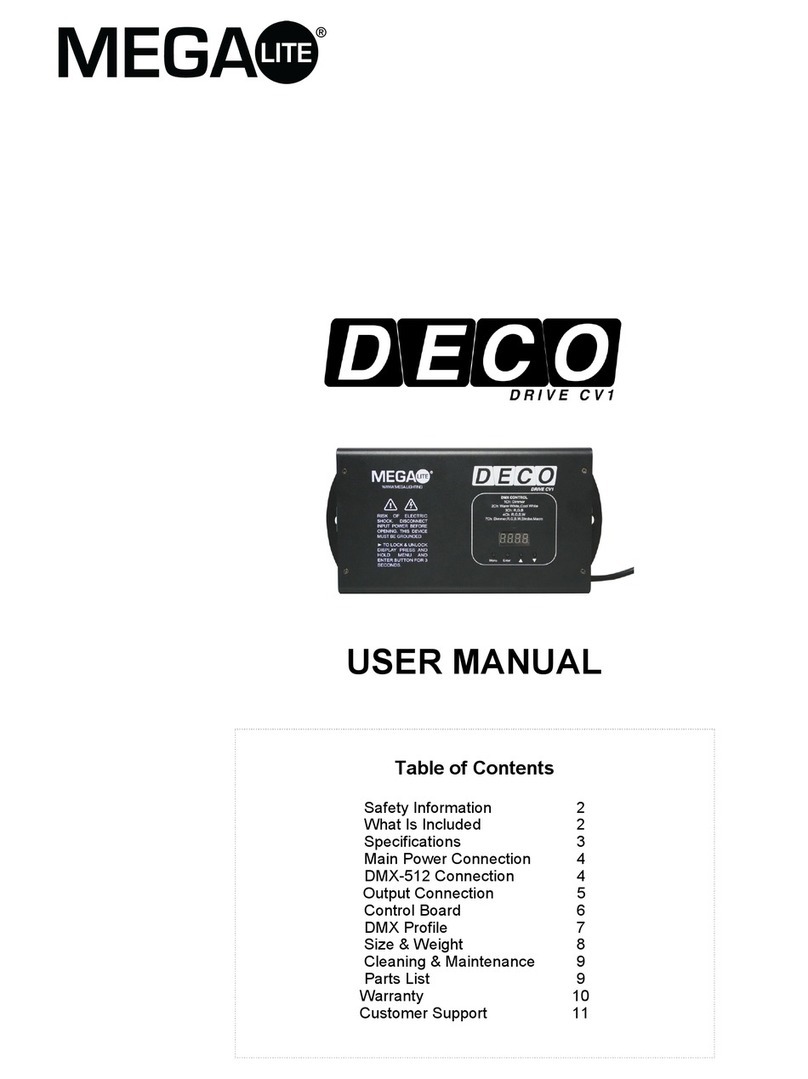
MegaLite
MegaLite DECO Series user manual
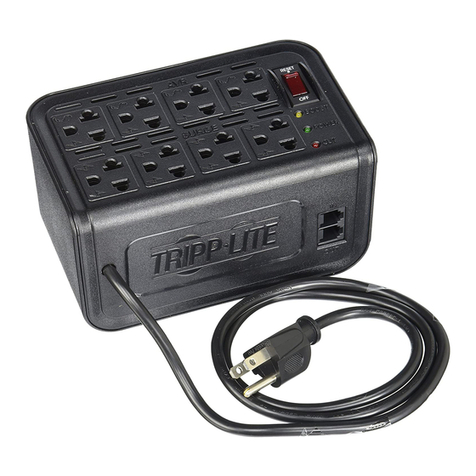
Tripp Lite
Tripp Lite VR1208R owner's manual
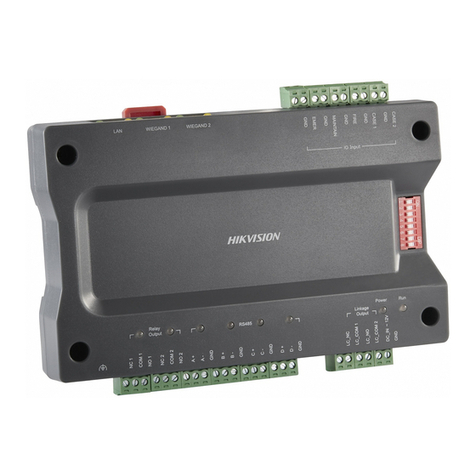
HIK VISION
HIK VISION DS-k2210 quick start guide
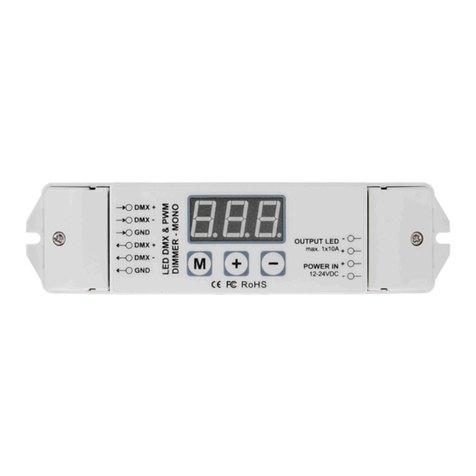
superbrightleds
superbrightleds DMX-1CH-10A Instructional Sheet
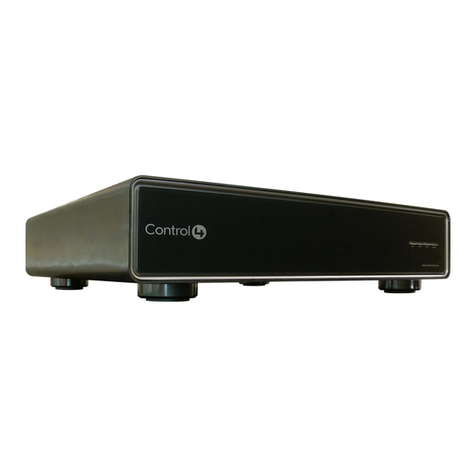
Contro l4
Contro l4 C4-HC500-E-B Technical specifications
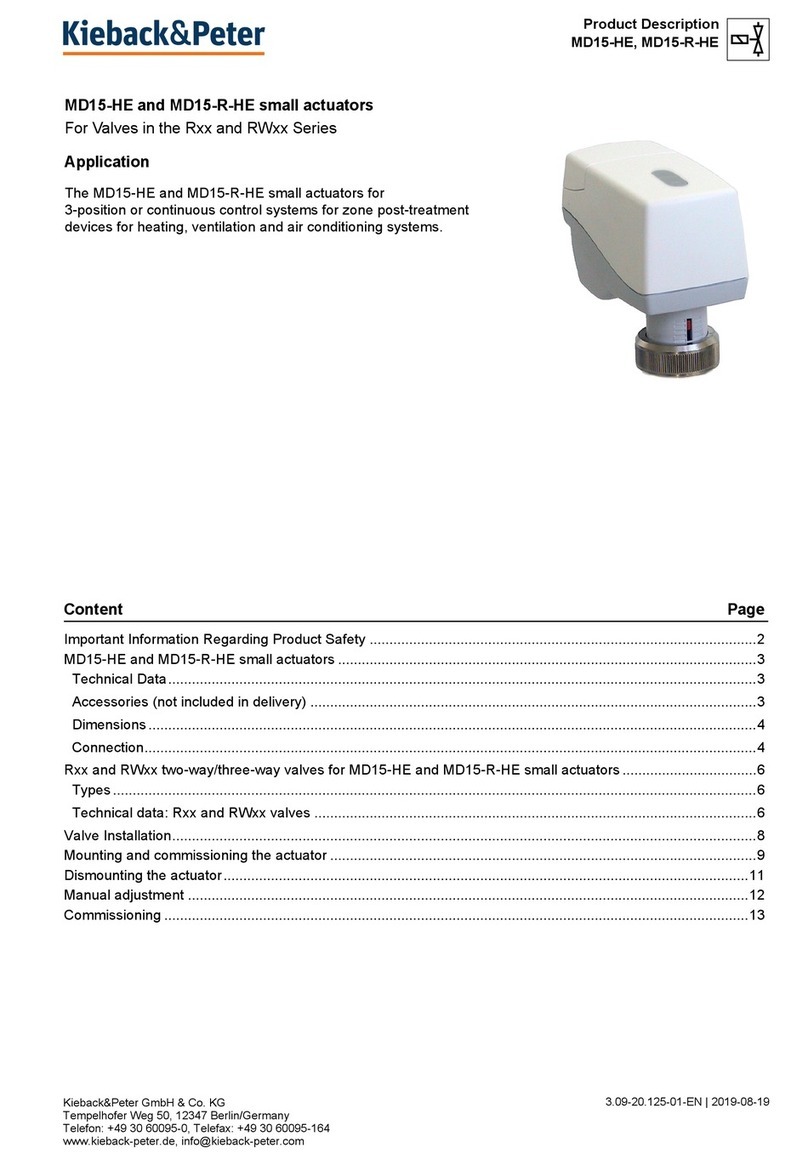
Kieback&Peter
Kieback&Peter MD15-R-HE Product description
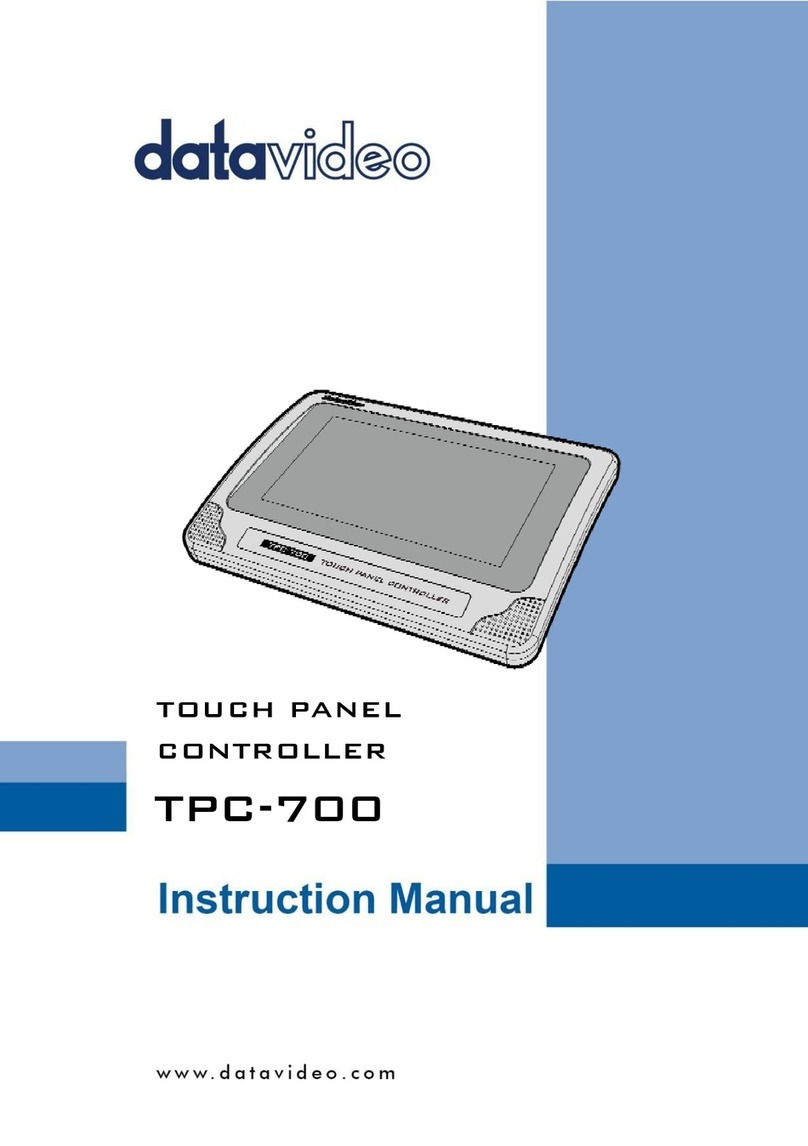
Data Video
Data Video TPC-700 instruction manual
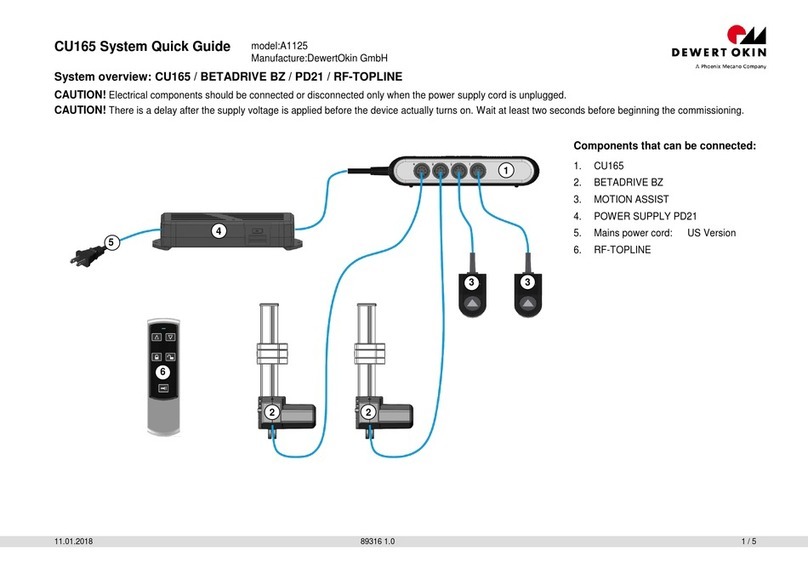
dewert okin
dewert okin CU165 Product Quick Guide
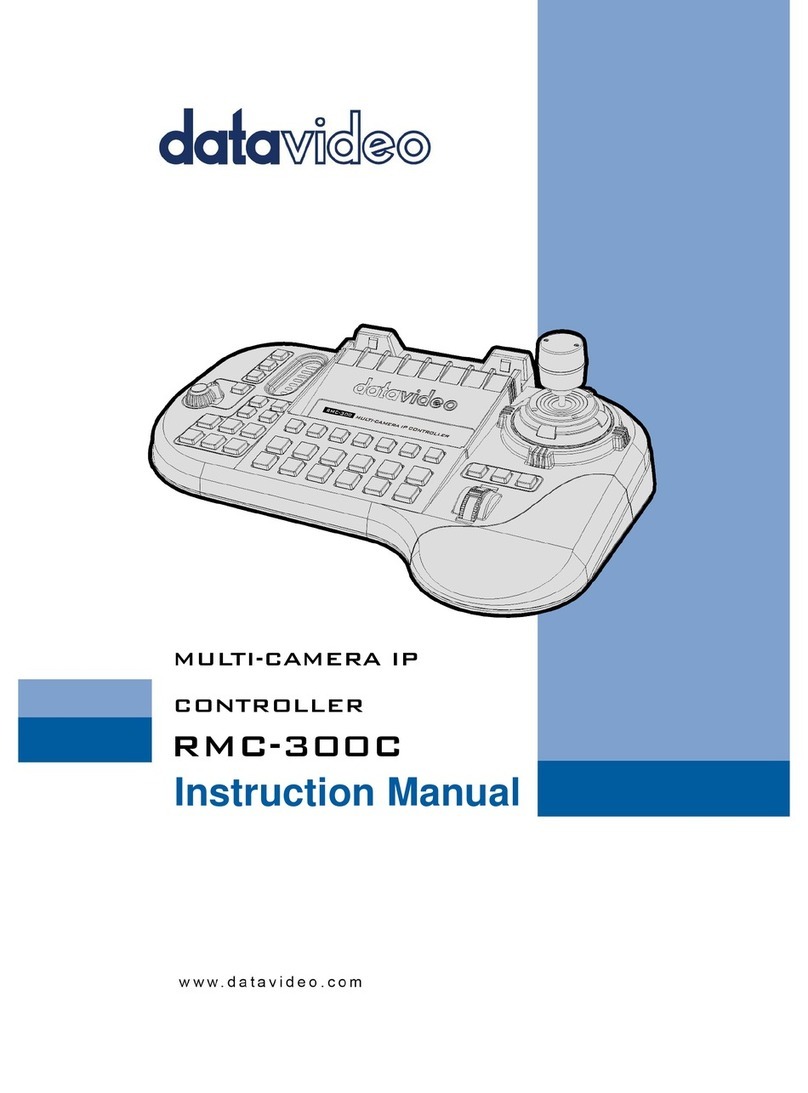
Data Video
Data Video RMC-300C instruction manual
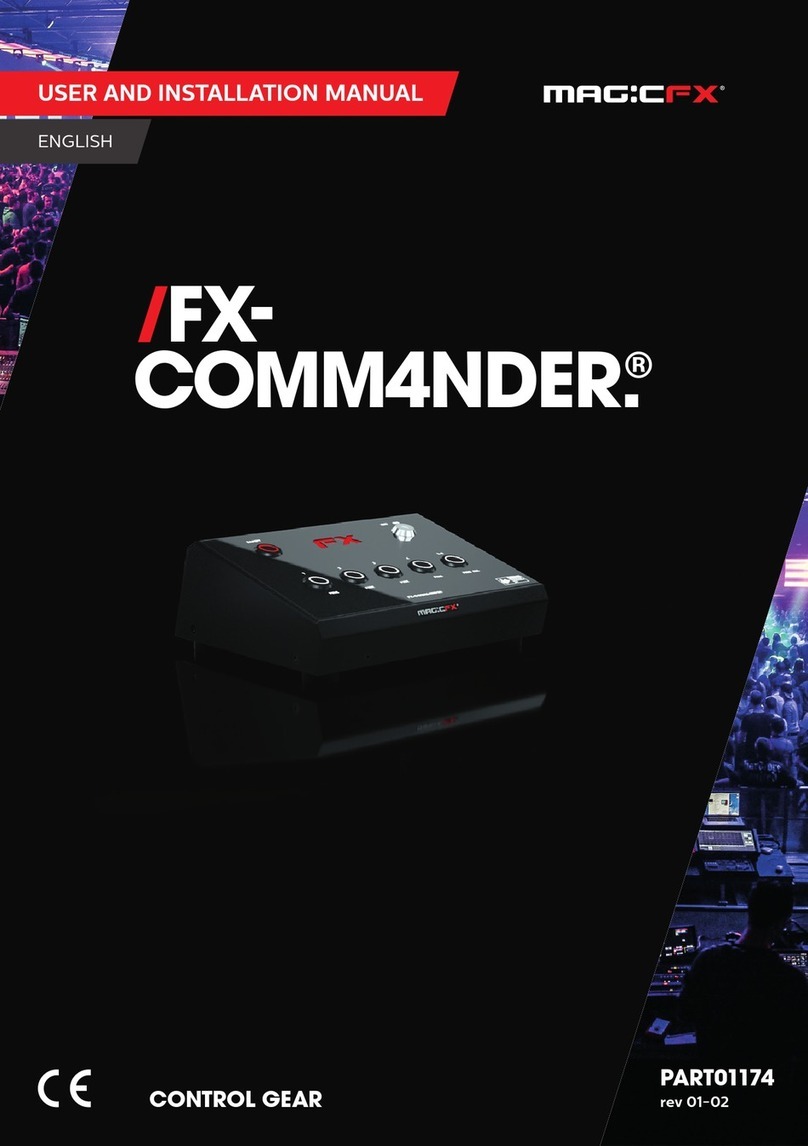
Magicfx
Magicfx FX-Comm4der User and installation manual