Hitachi NEXT Series User manual

Confidential
DSP-45WT6N
DSP-55WT6N
DSP-75WT6N
DSP-55VWTN
DSP-75VWTN
“Instructions for the use of this manual”
Use this Service Manual in conjunction with Instruction Manual.
HITACHI
OIL-FREE SCREW COMPRESSOR
NEXT series
Water-Cooled
DSP–017
Mechanical SERVICE MANUAL
DSP-45AT6N
DSP-55AT6N
DSP-75AT6N
DSP-55VATN
DSP-75VATN
Air-Cooled

Contents
1. GENERAL DESCRIPTION
1.1 Appearance [Air-Cooled]…………………………………………………………………………………… 1
1.2 Components [Air-Cooled] ………………………………………………………………………………… 2
1.3 Appearance [Water-Cooled] ……………………………………………………………………………… 3
1.4 Components [Water-Cooled]……………………………………………………………………………… 4
2. FLOW DIAGRAM
2.1 Flow Diagram [Air-Cooled]………………………………………………………………………… 5
2.2 Flow Diagram [Water-Cooled] …………………………………………………………………… 7
2.3
Capacity Control System Standard
…………………………………………………………………10
3. MAINTENANCE
3.1 Standard Maintenance Schedule ……………………………………………………………………… 13
3.2 Maintenance Schedule for Oil Mist Remover………………………………………………………… 17
4. HOW TO SERVICE THE AIR COMPRESSOR
4.1 Replacement of Air Intake Filter (Bi-Annually) ……………………………………………………… 18
4.2
Condensate drain port (Intercooler/Aftercooler) (Daily check)
Clean the strainer elements (Bi-Annually) &Orifices (Annually)………………………………… 19
4.3 Lubricating oil Replacement (Annually)……………………………………………………………… 23
4.4 Cleaning of Oil Strainer (Primary Side) (Bi-Annually)……………………………………………… 24
4.5 Replacement of Oil Filter (Secondary Side) (Annually) …………………………………………… 24
4.6 Operation Check of Air Relief Valve (Bi-Annually)…………………………………………………… 25
4.7 Cleaning of Control Line Filter (Bi-Annually) [Fixed speed type]………………………………… 25
4.8 Clean Cooler (Annually) ………………………………………………………………………………… 26
4.9 Replacement of Check Valve (2-Yearly) ……………………………………………………………… 27
4.10 Main Motor Greasing …………………………………………………………………………………… 28
4.11 Maintenance of Main Motor …………………………………………………………………………… 29
4.12 Maintenance of Oil Mist Remover……………………………………………………………………… 30
4.13 Maintenance of Cooling fan and cooling fan motor ……………………………………………… 31
4.14 The procedure to attach the motor cover[Water-Cooled]………………………………………… 32
4.15 Maintenance of Oil Pump ……………………………………………………………………………… 34
4.16 Maintenance of SuctionThrottle Valve………………………………………………………………… 37
4.17 Oil Pump motor and Airend removal ………………………………………………………………… 43
4.18 Oil casing and Gear casing removal…………………………………………………………………… 45
4.19 Main motor removal……………………………………………………………………………………… 46
4.20 Replace the Bushing……………………………………………………………………………………… 48
4.21 Pinion Gear Replacement Procedure ………………………………………………………………… 52
4.22 Battery Replacement (6-Yearly)………………………………………………………………………… 54
4.23 Inspection ofThermistor and Pressure Sensor……………………………………………………… 55
5. PARTS LIST …………………………………………………………………………………………… 57

1
1. GENERAL DESCRIPTION
1.1 Appearance Air-Cooled
Enclosure
Oil Filling Port
Air Intake
(Inlet to the Air End)
Oil Level Gauge
Sling Fitting
Instrument Panel
Left Door
Plate of Operating/
Servicing Instructions
Air Exhaust
(Air Compressor Package)
Compressed Air Discharge
Power Supply Port
Air Intake
(Air Compressor Package)
Air Exhaust
Enclosure panels
lower the sound level
of the air compressor
package.
Use the port to fill the
gear case with oil.
This indicates the
quantity of the oil in
the gear case. Check
the oil level before
starting the DSP and
when operating it.
Use the sling fitting
when moving and
installing the DSP air
compressor.
Read carefully the
plate before operating
and servicing the DSP.
Open the left door only
when servicing the
DSP air compressor.
Keep it closed when
operating the DSP air
compressor.
This panel discharges
the hot air generated
in the air compressor.
Check the
specifications, power
supply and voltage
before connecting the
power supply.
Air Intake
Air Exhaust Air Intake
Air Intake
OMR
[Front View]
[Rear View]

2
1.2 Components Air-Cooled
Oil cooler
Intercooler
Aftercooler
Air intake filter
Oil mist remover
(OMR)
Discharge pipe
(Compressed air discharge)
Oil level gauge
Control panel
Enclosure
Instrument panel
Main motor
Oil filter
1st-stage
Airend
2nd-stage
Airend
Check valve
Cooling fan
Common base
Air relief valve
[Front View]
[Rear View]

3
1.3 Appearance Water-Cooled
Enclosure
Oil Filling Port
Oil Level Gauge
Sling Fitting
Instrument Panel
Plate of Operating /
Servicing Instructions
Compressed Air Discharge
Power Supply Port
Air Intake
(Air for Package)
Enclosure panels
lower the sound level
of the air compressor
package.
Use the port to fill the
gear case with oil.
This indicates the
quantity of the oil in
the gear case. Check
the oil level before
starting the DSP and
when operating it.
Read carefully the
plate before operating
and servicing the DSP.
This panel discharges
the hot air generated in
the air compressor.
Check the
specifications, supply
voltage and frequency
before connecting the
power.
(Vtype only)
Air Exhaust
(Air Compressor Package)
Air Intake
(Inlet to the Air End)
Left Door
Open the left door only
when servicing the
DSP air compressor.
Keep it closed when
operating the DSP air
compressor. Air Intake
Air Exhaust
Air Intake
Air Intake
Air Exhaust
Use the sling fitting
when moving and
installing the DSP air
compressor.
Air Intake
(Air Compressor Package)
OMR
[Front View]
[Rear View]

4
1.4 Components Water-Cooled
Cooling fan
Intercooler
Aftercooler
Oil cooler
Air intake filter
Oil mist remover
(OMR)
Control panel
Enclosure
Instrument panel
Main motor
Discharge pipe
(Compressed air discharge)
Check valve
Common Base
Air relief valve
Oil filter
1st-stage
Airend
2nd-stage
Airend
Oil level gauge
[Front View]
[Rear View]

5
2. FLOW DIAGRAM
2.1 Flow Diagram Air-Cooled
2.1.1 Fix speed type
14
15
13
Air exhaust
Air exhaust Air exhaust
23
24
22
9
21
53
32
52
11
PS2
4
3
5
33
31
TH3
1
PS1
TH4
TH5
63SV
Air intake for
main motor
Air intake for
compressed air
Oil drain
Oil drain
38
39
13
35
14
PS4
Intercooler
condensate
drain
15
2
Aftercooler condensate drain
Control air for OMR
Cooling air flow Compressed air flow Lubricating oil flow
MOHR
17
36
19
6
7834
51
TH2
54
20
10
18
M
Compressed
air discharge
Compressed Air Flow and Oil Flow
Legend of the Diagram
Compressor Air Flow
11st-Stage Airend
22nd-Stage Airend
3Gear Case
4Step-up Gear
5Main Motor
6Intercooler
7Check Valve
8Aftercooler
9Air Relief Valve
10 Discharge Port
11 Check Valve
13 Orifice
14 Drain Solenoid
15 Y strainer
16 Drain trap
17 Demister
18 Motorized Isolation Valve
19
Hi-Precooler (only for 125 psi (0.86 MPa type))
20
Drain separator
Capacity Control & Blowoff Air Flow
21 Air Intake Filter
22 Suction Throttle Valve
23 Blowoff Valve
24 Blowoff Silencer
Oil Flow
31 Oil Strainer
32 Oil Pump
33 Oil Relief Valve
34 Oil Cooler
35 Oil Filter
36 Temperature Control Valve
38 Oil Drain Valve
39 Oil Mist Remover
Air Flow and Other
51 Fan Motor
52 Enclosure
53
Air Intake Duct
54 Cooling fan
Legend of Sensors and Switches
Symbol
Part name
PS2
Pressure Sensor (discharge air pressure)
PS4
Pressure Sensor (oil pressure)
PS1
Pressure Sensor (interstage pressure)
TH2
Temperature Sensor (2nd-stage in)
TH4
Temperature Sensor (1st-stage out)
TH3
Temperature Sensor (2nd-stage out)
TH5 Temperature Sensor (oil)
MOHR
Thermostat (for main motor
bearing temperature)
63SV
Pressure Differential Sensor (For
suction filter clogging detection)

6
2.1.2 Air-Cooled
14
15
13
Air exhaust
Air exhaust Air exhaust
20
17
9
21
53
32
52
11
10
PS2
4
3
5
33
31
TH3
1
PS1
TH4
TH5
63SV
24
22
22
Air intake for
compressed air
38
39
13
35
14
PS4
15
2
Aftercooler condensate drain
Coolin
g
air flow Com
p
ressed air flow Lubricatin
g
oil flow
18
THM
23
23
36
19
6
7834
51
TH2
54
M
Oil drain
Oil drain
Control air for OMR
Air intake for
main motor
Compressed
air discharge
Intercooler
condensate
drain
Compressed Air Flow and Oil Flow
Legend of Sensors and Switches
Symbol
Part name
PS2
Pressure Sensor (discharge air pressure)
PS4
Pressure Sensor (oil pressure)
PS1
Pressure Sensor (interstage pressure)
TH2
Temperature Sensor (2nd-stage in)
TH4
Temperature Sensor (1st-stage out)
TH3
Temperature Sensor (2nd-stage out)
TH5 Temperature Sensor (oil)
THM Temperature Sensor (for main
motor surface temperature)
63SV
Pressure Differential Sensor (For
suction filter clogging detection)
Capacity Control & Blowoff Air Flow
21 Air Intake Filter
22 Blowoff Solenoid Valve (1)
23 Blowoff Solenoid Valve (2)
24 Blowoff Silencer
Oil Flow
31 Oil Strainer
32 Oil Pump
33 Oil Relief Valve
34 Oil Cooler
35 Oil Filter
36 Temperature Control Valve
38 Oil Drain Valve
39 Oil Mist Remover
Air Flow and Other
51 Fan Motor
52 Enclosure
53 Air Intake Duct
54 Cooling fan
Legend of the Diagram
Compressor Air Flow
1 1st-Stage Airend
2 2nd-Stage Airend
3 Gear Case
4 Step-up Gear
5 Main Motor
6 Intercooler
7 Check Valve
8 Aftercooler
9 Air Relief Valve
10 Discharge Port
11 Check Valve
13 Orifice
14 Drain Solenoid
15 Y-type Strainer
16 Drain trap
17 Demister
18 Motorized isolation valve
19
Hi-Precooler (only for 125 psi (0.86 MPa type))
20
Drain separator

7
2.2 Flow Diagram Water-Cooled
2.2.1 Fix speed type
MOHR
10
18
M
Compressed
air discharge
9
38 13
TH5
63SV
TH4
TH2
PS1
TH3
PS2
1
6
3
5
4
7
51
8
11
52
32
23
31
53 22
21
33
24
34
35
14
39
PS4
36
2
15
13 17
25
20
14
15
Air exhaust Air exhaust
Aftercooler condensate drain
Cooling air flow Compressed air flow Lubricating oil flow
Air intake for
main motor
Control air for OMR
Air intake for
compressed air
Oil drain
Oil drain
Intercooler
condensate
drain
Compressed Air Flow and Oil Flow
Legend of the Diagram
Compressor Air Flow
1 1st-Stage Airend
2 2nd-Stage Airend
3 Gear Case
4 Step-up Gear
5 Main Motor
6 Intercooler
7 Check Valve
8 Aftercooler
9 Air Relief Valve
10 Discharge Port
11 Check Valve
13 Orifice
14 Drain Solenoid
15 Y-type Strainer
16 Drain trap
17 Demister
18 Motorized isolation valve
20
Drain separator
Capacity Control & Blowoff Air Flow
21 Air Intake Filter
22 Suction Throttle Valve
23 Blowoff Valve
24 Blowoff Silencer
25 Blowoff Cooler
Oil Flow
31 Oil Strainer
32 Oil Pump
33 Oil Relief Valve
34 Oil Cooler
35 Oil Filter
36 Temperature Control Valve
38 Oil Drain Valve
39 Oil Mist Remover
Air Flow and Other
51 Fan
52 Enclosure
53 Air Intake Duct
Legend of Sensors and Switches
Symbol
Part name
PS2
Pressure Sensor (discharge air pressure)
PS4
Pressure Sensor (oil pressure)
PS1
Pressure Sensor (interstage pressure)
TH2
Temperature Sensor (2nd-stage in)
TH4
Temperature Sensor (1st-stage out)
TH3
Temperature Sensor (2nd-stage out)
TH5 Temperature Sensor (oil)
MOHR
Themostat (for main motor
bearing temperature)
63SV
Pressure Differential Sensor (For
suction filter clogging detection)

8
2.2.2 Water-Cooled
13
9
7
51
6
21
53
32
52
11
10
PS2
4
3
5
8
33
31
TH3
TH2
1
PS1
TH4
TH5
63SV
24
22
22
23
23
38
39
13
34
35
14
14
PS4
15
2
36
18
THM
M
17
20
15
Air exhaust Air exhaust Air exhaust
Drain discharge
Cooling air flow Compressed air flow Lubricating oil flow
Compressed
air discharge
Air intake for
main motor
Control air for OMR
Air intake for
compressed air
Oil drain
Oil drain
Intercooler
condensate
drain
Compressed Air Flow and Oil Flow
Legend of Sensors and Switches
Symbol
Part name
PS2
Pressure Sensor (discharge air pressure)
PS4
Pressure Sensor (oil pressure)
PS1
Pressure Sensor (interstage pressure)
TH2
Temperature Sensor (2nd-stage in)
TH4
Temperature Sensor (1st-stage out)
TH3
Temperature Sensor (2nd-stage out)
TH5 Temperature Sensor (oil)
THM Temperature Sensor (for main
motor surface temperature)
63SV
Pressure Differential Sensor (For
suction filter clogging detection)
Capacity Control & Blowoff Air Flow
21 Air Intake Filter
22 Blowoff Solenoid Valve (1)
23 Blowoff Solenoid Valve (2)
24 Blowoff Silencer
Oil Flow
31 Oil Strainer
32 Oil Pump
33 Oil Relief Valve
34 Oil Cooler
35 Oil Filter
36 Temperature Control Valve
38 Oil Drain Valve
39 Oil Mist Remover
Air Flow and Other
51 Fan
52 Enclosure
53 Air Intake Duct
Legend of the Diagram
Compressor Air Flow
1 1st-Stage Airend
2 2nd-Stage Airend
3 Gear Case
4 Step-up Gear
5 Main Motor
6 Intercooler
7 Check Valve
8 Aftercooler
9 Air Relief Valve
10 Discharge Port
11 Check Valve
13 Orifice
14 Drain Solenoid
15 Y-type Strainer
16 Drain trap
17 Demister
18 Motorized isolation valve
20
Drain separator

9
Cooling water
outlet
Cooling
water outlet Cooling water
inlet
Water relief pet cock
Compressed air flow Cooling water flow
M
1st-stage
airend
2nd-stage
airend
Aftercooler
Intercooler
Oil cooler
Motorized
water isolation
valve (WIVM)
Cooling Water Flow

10
2.3 Capacity Control System Standard
2.3.1 Fix speed type (Load-Unload Operation) Air-Cooled Water-Cooled
Vacuum valve
1st-stage
airend
Intercooler
Check valve Aftercooler
To the
Atmosphere
Blowoff
valve
Pressure sensor
Control Line Filter
NC
NO
COM
NC
NO
COM
NC
NO COM
20U3
20U2
20U1
PS
Control air flow
2nd-stage
airend
Compressed Air Discharge
Check valve
NO
NC
COM
20U4
NC
NO
COM
20US
STARTING UNLOADING RELOADING STOPPING
Suction throttle valve (STV) closed
START button ON
Airend starts rotation to
compress minor amounts of air
Starts in no load
Changes to full voltage delta connection
3-way solenoid valve (20Ux)
switched over to connect
Chamber (A) & Chamber (C)
Suction throttle valve (STV) opens
Loading
Air demand decreases
Discharge pipe pressure rises
Pressure sensor (PS) operates
3-way solenoid valve (20Ux)
switched over to pressurize
Chamber (A)
Suction throttle valve
(STV) closes
Blowoff valve opens
Internal air in discharge pipe
is exhausted to atmosphere
Air demand increases
Discharge pipe pressure drops
Pressure sensor (PS) operates
3-way solenoid valve (20Ux)
switched over to pressurize
Chamber (B)
Suction throttle valve
(STV) opens
Blowoff valve closes
Loading
3-way solenoid valve (20Ux)
switched over to pressurize
Chamber (A)
STOP button ON
Suction throttle valve
(STV) closes
Blowoff valve opens
Internal air in discharge pipe
is exhausted to atmosphere
Compressor stops
To Chamber (B)
To Chamber (A)
3-Way Solenoid Valve (4)
3-Way Solenoid Valve (20US)
3-Way Solenoid
Valve (1)
Starting/Stopping
Loading
Unloading
For 20 seconds
after starting with
a star-delta starter.
3-Way Solenoid
Valve (2)
3-Way Solenoid Valve (3)
NC-COM connected for
5 seconds after reactor
is changed over to a
fullvoltage connection.
Suction Throttle Valve
Chamber
(C)
Chamber (B)
Chamber (A)
The unloading process occurs when the compressed
air demand decreases and the discharge pressure rises
as high as cut-out pressure. The pressure sensor (PS)
detects the high pressure and energizes the 3-way
solenoid valve (20Ux), changing its port to port
connection. The control air is now flowing to and
pressurizing chamber (A) of the suction throttle valve
(STV), consequently closing the suction throttle valve
(STV) and unloading the airend while the blowoff valve
opens and exhausts the internal compressed air to
atmosphere.
The loading process occurs when the compressed air
demand increases and the discharge pressure dropped
as low as cut-in pressure. When the pressure sensor
(PS) detects the low pressure, 3-way solenoid valve
(20Ux), suction throttle valve (STV), and blowoff valve
work in reverse action and the airend reloads.

11
2.3.2 Fix speed type (AUTO Operation) Air-Cooled Water-Cooled
15 sec or
more
STARTING UNLOADING RELOADING STOPPING
Suction throttle valve (STV) closed
START button ON
Airend starts rotation to
compress minor amounts of air
Starts in no load
Changes to full voltage
delta connection
3-way solenoid valve (20Ux)
switched over to connect
Chamber (A) & Chamber (C)
Suction throttle valve (STV) opens
Loading
Air demand decreases
Discharge pipe pressure rises
Pressure sensor (PS) operates
3-way solenoid valve (20Ux)
switched over to pressurize
Chamber (A)
Suction throttle valve
(STV) closes
Blowoffvalve opens
Internal air in discharge
pipe is exhausted to
atmosphere
Air demand increases
Discharge pipe pressure drops
Pressure sensor (PS) operates
3-way solenoid valve (20Ux)
switched over to pressurize
Chamber (B)
Suction throttle valve
(STV) opens
Blowoff valve closes
Loading
3-way solenoid valve (20Ux)
switched over to pressurize
Chamber (A)
STOP button ON
Suction throttle valve
(STV) closes
Blowoff valve opens
Internal air in discharge
pipe is exhausted to
atmosphere
Compressor stops
Load-Unload Operation
AUTO Operation
How long has
motor been
running ?
Load rate ?
Has motor stopped and
restarted 3 times or more for
90 minutes ?
Motor stops automatically
Less
than
specified
What is the plant
compressed air piping
pressure ?
How long has
motor been
stopped ?
Less than
15 seconds
More than specified
10 minutes or more
Less than 30%
30% or more
Less than 10 minutes
YES
NO
If the third stop is done after 70
minutes or more has passed
after the first stop, the motor
continues to operate for 20
minutes after restart of the air
compressor, and then return to
the initial cycle.
STV: Suction Throttle Valve
20Ux: 3-Way Solenoid Valve
AUTO operation is the Auto start - stop function in
addition to a standard on-off line, 0% or 100% capacity
2-step control. The CPU on the PC board is continually
calculating a load ratio.
When the load ratio is less than 30%, CPU stop the main
motor. And automatically restart when the line
pressure is dropped to cut-in pressure.

12
2.3.3 Capacity Control System Air-Cooled Water-Cooled
Air intake
Air Intake filter
1st-stage
airend
Intercooler
Check valve
Aftercooler
Blowoff
silencer
Pressure sensor
Air
discharge
1st-stage blowoff solenoid valve (1)
2nd-stage blowoff solenoid valve (1)
2nd-stage blowoff solenoid valve (2)
1st-stage blowoff solenoid valve (2)
2nd-stage
airend
PS2
Purging Air Flow and Action of Blowoff Solenoid Valve
Operation phase
Blowoff solenoid
valve (1)
Blowoff solenoid
valve (2)
Starting Fully opened Fully closed
Loading Fully closed Fully closed
Purging Fully opened Fully closed
Stop Fully opened Fully opened
Power Interruption
Fully closed Fully opened
■Relationship between Air Consumption Rate and Capacity Control System
※The value in ( ) is indicated for water-cooled type.
Model
Rated
pressure
psi [MPa]
Air
consumption
(%)
Operating
frequency (Hz) Capacity control system
Pressure setting
psi [MPa]
Capacity
control type
Initial Example
of Lower
55 kW
125 [0.86]
100 - 75 (65)
134 (136) - 108 (108)
①CPCS motor
speed control
Control
pressure 125 [0.86] 120 [0.83]
AUTO ON
VSDA
or
AUTO OFF
VSDB
75 kW
100 - 60 (50)
133 (137) - 80 (72)
55 kW
125 [0.86]
75 (65) - 5 82
②Two-step purge
control
Cut-out
pressure 138 [0.95] 125 [0.86] AUTO ON
VSDA
or
AUTO OFF
VSDB
75 kW 60 (50) - 5 66 (60) Cut-in
pressure 131 [0.90] 120 [0.83]
All
model 125 [0.86] 5 - 0
Main motor stop
③Motor stop/
restart control
Cut-in
pressure 131 [0.90] 120 [0.83] AUTO ON
VSDA
The air compressor supports the three (3) capacity control systems as shown above.
Depending on the varying air consumption, an appropriate system is automatically selected. For more information, see
the following page. Operation frequency is shown by Digital monitor. LCD monitor displays up to first figure after
decimal place.

13
3. MAINTENANCE
3.1 Standard Maintenance Schedule
Maintenance Schedule A (for 8,000 hours/year or less operation)
Follow this schedule (A) if the MAINT.SCHEDULE : A appears on the LCD monitor.
○●… Replace △○… Complete service in house
△▲… Clean or check ▲●… Ask your distributor to service
Part or Item Action Category Type Remarks
Air intake fitter Replace ○Fixed / V
Oil filter (secondary) – Pressure Check △Fixed / V Replace as required.
Control line filter – Condensate Clean △Fixed
Strainer – Aftercooler/ Intercooler condensate drain
Clean △Fixed / V
Oil strainer (primary) Clean ▲Fixed / V Clean as required.
Aftercooler/ Intercooler/ Oil cooler (air side)
Check / Clean
▲Fixed / V Clean as required.
Hi-Precooler
Check / Clean
▲Fixed / V
Clean as required. (Air-cooled 125psi (0.86)MPa type)
Blowoff solenoid valve - Operation Check ▲Fixed / V
Check valve - Leakage Check ▲Fixed / V
Air relief valve - Operation Check ▲Fixed / V
1Daily and 3-month Schedule (for 8,000 hours/year or less operation)
2Bi-Annual Schedule (for 8,000 hours/year or less operation)
Part or Item Action
Category
Type Remarks
Dally
Every
3 months
LCD indications Check △Fixed / V
Record data in the OPERATION RECORD LOGBOOK.
Oil level Check △Fixed / V Add as required
Aftercooler/ Intercooler - Condensate Drain △Fixed / V
Control line filter - Condensate Check △Fixed
Main motor greasing – △Fixed / V
Fixed speed type: both DE / NDE side, Vtype: DE side
3Annual and 3-Year Schedule (for 8,000 hours/year or less operation)
Part or Item Action Category Type Remarks
1-year 3-year
Lubricating oil Replace ○Fixed / V
Joints, Bolts, Nuts
Tighten / Check
△Fixed / V
Air intake filter Replace ○Fixed / V
Gasket - Inter/aftercooler condensate strainer
Replace ○Fixed / V
O ring - Inter/aftercooler condensate strainer
Replace ○Fixed / V
Oil strainer (primary) Clean ▲Fixed / V
Oil filter (secondary) Replace ●Fixed / V
Consumable parts - Suction throttle valve
Replace ●Fixed
Seal washer - Suction throttle valve Replace ●Fixed
Seal gasket - Suction throttle valve Replace ●Fixed
Thermistor, Pressure sensor, PCB other Electric parts
Check ▲Fixed / V
Change any operating parts in need replacement.
Cooling fan
Check for crack
/ Clean
▲Fixed / V
Contoller fan (1), DCBL controller
Check for crack
/ Clean
▲V Clean the fin and duct
Cooling fan for fan inverter
Check for crack
/ Clean
▲Fixed Clean the fin (Air-cooled type)

14
Part or Item Action Category Type Remarks
Control line filter element Replace ○Fixed
Blowoff solenoid valve (1) (2) Replace ●V
Consumable parts - Oil Pump Replace ●Fixed / V
Check valve Replace ●Fixed / V
Solenoid valve - Intercooler/ Aftercooler condensate
Replace ●Fixed / V Replace the strainer together
Check valve & strainer- Intercooler condensate
Replace ●Fixed / V
Check valve - Control line Replace ●Fixed
DCBL Controller
Check / Clean
▲V Clean the fin and duct.
Controller fan (1), DCBL controller Replace ●V
Cooling fan for control panel Replace ●Fixed Clean the fin (Air-cooled type)
Cooling fan for control panel Replace ●Fixed / V Except 45/55kW fixed speed type
Part or Item Action Category Type Remarks
Airend (1st-stage, 2nd-stage) Replace ●Fixed / V A whole airend is replaced with a new
Main motor bearing Replace ●Fixed / V
Fan motor bearing Replace ●Fixed / V Air-cooled type
Demister - Drain separator Replace ●Fixed / V
3-Way solenoid valve Replace ●Fixed
Oil strainer (primary) Replace ●Fixed / V
Control line filter - Condensate Replace ●Fixed
Oil level gauge Replace ●Fixed / V
Shaft seal - Main motor
Check / Clean
●Fixed / V
Temperature control valve Replace ●Fixed / V
Smoothing condenser - Controller Replace ●V
PC board assembly (Including LCD)
Check / Clean
/ Replace
●Fixed / V
Check for contamination and discoloration.
Replace as required.
Can be used further if appropriate.
Power PCB - Controller
Check / Clean
/ Replace
●V
Communication board
Check / Clean
/ Replace
●Fixed / V
Electromagnetic contactor Check ▲Fixed / V Replace as required.
Lithium battery Replace ●Fixed / V
Fan inverter Replace ●Fixed / V Air-cooled type
42-Year Schedule (for 8,000 hours/year or less operation)
56-Year Schedule: Overhauling (for 8,000 hours/year or less operation)
Part or Item Action Category Type Remarks
1-year 3-year
Orifice- Aftercooler condensate
Check / Clean
▲Fixed / V Clean as required.
Orifice and check valve- Intercooler condensate
Check / Clean
▲Fixed / V Clean as required.
Aftercooler/ Intercooler/ Oil cooler
Check / Clean
▲Fixed / V
Hi-Precooler
Check / Clean
▲Fixed / V
Clean as required. (Air-cooled 125psi (0.86)MPa type)
Demister - Drain separator
Check / Clean
▲Fixed / V
3-Way solenoid valve & capacity control system
Check ▲Fixed Replace as required.
Blowoff solenoid Valve Check ▲V
Air relief valve
Check / Clean
▲Fixed / V
Protection, Safety device Check ▲Fixed / V
Change any operating parts in need of replacement.
Motors
Check / Clean
▲Fixed / V
Clean and measure the insulation for any resistance.
Relay (Drain solenoid valve) Replace ●Fixed / V

15
Maintenance Schedule B (for 4,000 hours/year or less operation)
Follow this schedule (B) if the MAINT.SCHEDULE : B appears on the LCD monitor.
○●… Replace △○… Complete service in house
△▲… Clean or check ▲●… Ask your distributor to service
Part or Item Action Category Type Remarks
LCD indications Check △Fixed / V
Record data in the OPERATION RECORD LOGBOOK.
Oil level Check △Fixed / V Add as required
Aftercooler/ Intercooler - Condensate Drain △Fixed / V
Control line filter - Condensate Check △Fixed
Part or Item Action Category Type Remarks
Air intake fitter Replace ○Fixed / V
Main motor greasing – △Fixed / V
Fixed speed type: both DE / NDE side, Vtype: DE side
Oil filter (secondary) – Pressure Check △Fixed / V Replace as required.
Control line filter – Condensate Clean △Fixed
Strainer – Aftercooler/ Intercooler condensate drain
Clean △Fixed / V
Oil strainer (primary)
Check / Clean
▲Fixed / V Clean as required.
Aftercooler/ Intercooler/ Oil cooler (air side)
Check / Clean
▲Fixed / V Clean as required.
Hi-Precooler
Check / Clean
▲Fixed / V
Clean as required. (Air-cooled 125psi (0.86)MPa type)
Blowoff solenoid valve - Operation Check ▲Fixed / V
Check valve - Air leak Check ▲Fixed / V
Air relief valve - Operation Check ▲Fixed / V
1Daily Schedule (for 4,000 hours/year or less operation)
2Bi-Annual Schedule (for 4,000 hours/year or less operation)
Part or Item Action Category Type Remarks
Lubrication oil Replace ○Fixed / V
Replace every 8,000h operating hour or 2 year, whichever comes earlier
Joints, Bolts, Nuts
Tighten / Check
△Fixed / V
Air intake filter Replace ○Fixed / V
Gasket - Inter/Aftercooler condensate strainer
Replace ○Fixed / V
O ring - Inter/Aftercooler condensate strainer
Replace ○Fixed / V
Oil strainer (primary) Clean ▲Fixed / V
Thermistor, Pressure sensor, PCB other Electric parts
Check ▲Fixed / V
Change any operating parts in need replacement.
Cooling fan
Check for crack
/ Clean
▲Fixed / V
Contoller fan (1), DCBL controller
Check for crack
/ Clean
▲V Clean the fin and duct
Cooling fan for fan inverter
Check for crack
/ Clean
▲Fixed / V Clean the fin (Air-cooled type)
Orifice- Aftercooler condensate
Check / Clean
▲Fixed / V Clean as required.
Orifice and check valve- Intercooler condensate
Check / Clean
▲Fixed / V Clean as required.
Aftercooler/ Intercooler/ Oil cooler (air side)
Check / Clean
▲Fixed / V
3Annual Schedule (for 4,000 hours/year or less operation)

16
Part or Item Action Category Type Remarks
Control line filter element Replace ○Fixed
Oil filter (secondary) Replace ●Fixed / V
Consumable parts - Suction throttle valve Replace ●Fixed ※
Seal washer - Suction thorottle valve Replace ●Fixed ※
Seal gasket - Suction thorottle valve Replace ●Fixed ※
Blowoff solenoid valve (1) (2) Replace ●V
Consumable parts - Oil Pump Replace ●Fixed / V
Check valve Replace ●Fixed / V
Solenoid valve - Intercooler/ Aftercooler condensate
Replace ●Fixed / V
Check valve & strainer- Intercooler condensate
Replace ●Fixed / V
Check valve - Control line Replace ●Fixed
DCBL Controller Check ▲V Clean the fin and duct.
Controller fan (1), DCBL controller Replace ●V
Cooling fan for fan inverter Replace ●Fixed Clean the fin (Air-cooled type)
Cooling fan for control panel Replace ●Fixed / V Except 45/55kW fixed speed type
Relay (Drain solenoid valve) Replace ●Fixed / V
※When the power-saving operation is used, the parts need to be replaced every 2 years.
Part or Item Action Category Type Remarks
Airend (1st-stage, 2nd-stage) Replace ●Fixed / V A whole airend is replaced with a new
Main motor bearing Replace ●Fixed / V
Fan motor bearing Replace ●Fixed / V Air-cooled type
Demister - Drain separator Replace ●Fixed / V
3-Way solenoid valve & capacity control system
Replace ●Fixed
Oil strainer (primary) Replace ●Fixed / V
Control line filter - Condensate Replace ●Fixed
Oil level gauge Replace ●Fixed / V
Shaft seal - Main motor
Check / Clean
●Fixed / V
Temperature control valve Replace ●Fixed / V
Smoothing condenser - Controller Replace ●V
PC board assembly (Including LCD)
Check / Clean
/ Replace
●Fixed / V
Check for contamination and discoloration.
Replace as required.
Can be used further if appropriate.
Power PCB - Controller
Check / Clean
/ Replace
●V
Communication board
Check / Clean
/ Replace
●Fixed / V
Electromagnetic contactor Check ▲Fixed / V Replace as required.
Lithium battery Replace ●Fixed / V
Fan inverter Replace ●Fixed / V Air-cooled type
43-Year Schedule (for 4,000 hours/year or less operation)
56-Year Schedule: Overhauling (for 4,000 hours/year or less operation)
Part or Item Action Category Type Remarks
Hi-Precooler
Check / Clean
▲Fixed / V
Clean as required. (Air-cooled 125psi (0.86)MPa type)
Demister - Drain separator
Check / Clean
▲Fixed / V
3-Way solenoid valve & capacity control system
Check ▲Fixed Replace as required.
Blowoff solenoid Valve Check ▲V
Air relief valve
Check / Clean
▲Fixed / V
Protection, Safety device Check ▲Fixed / V
Change any operating parts in need of replacement.
Motors
Check / Clean
▲Fixed / V
Clean and measure the insulation for any resistance.

17
①To ensure long and successful operation of the Oil
Mist Remover, follow the standard maintenance
schedule attached below.
②The standard maintenance schedule service intervals
stated below are based on normal environmental and
operating conditions. If the Oil Mist Remover is in
severe environmental and operating conditions, use
more frequent service intervals.
③These maintenance intervals are not considered
warranty.
④If an inspected part is worn, faulty or damaged,
replace it as soon as possible.
⑤○●: Replace △▲: Clean or check
○△: Complete service in house
●▲: Ask your distributor to service
3.2 Maintenance Schedule for Oil Mist Remover
The oil mist remover reduces oil consumption to almost zero. However, the oil should still be replaced
annually.
CAUTION
Item Daily
Bi-annually
Annually
6-yearly
Remarks
Regulator settings △
Vacuum indicator △
Relief valve △
Regulator performance △
Float trap nozzle △Disassemble and clean.
Vacuum indicator △Disassemble and clean.
Filter element △Disassemble and clean.
Remover element ●
Filter element ●
Relief valve sheet/spring ●
Vacuum indicator ●
Filter regulator ●Disassemble and clean.
Replace diaphragm and valve stem.
Ejector ▲Disassemble and clean.
Replace if it is too dirty.
Solenoid valve ▲Disassemble and clean. Replace as
required.
Solenoid valve coil assembly ●

18
4. HOW TO SERVICE THE AIR COMPRESSOR
4.1 Replacement of Air Intake Filter (Bi-Annually)
■Filter Specifications
Effective filtration area: 40.8 ft² (3.79 m2)
Filtration efficiency: 98% or higher (full life)
12.7mm 254mm
φ241.2mm
(0.50inch) (10.0inch)
(φ9.50inch)
Before servicing the air compressor, stop it, disconnect the power (turn off the earth leakage (ground) circuit
breaker) and verify that the compressor’s internal pressure has dropped to atmospheric pressure.
The maintenance intervals shown refer to the standard Maintenance Schedule (A).
A pressure sensor is provided on the suction throttle
valve to detect the pressure differential across the air
intake filter. When the sensor detects a pressure
differential as large as 0.72 psi (4.98 kPa) during
operation, AIR FILTER appears on the LCD display
with E0.21 on digital monitor. If this occurs, clean or
replace the air intake filter in accordance with
Maintenance Schedule (A) or (B). The procedure for
cleaning the air intake filter is as follows.
①Stop the air compressor, disconnect the power and
verify no internal pressure.
②Remove the front door (1).
③Remove the cover and wipe away the dirt inside of
the duct before removing the air intake filter.
④Loosen the wing nut and remove the air intake filter.
Make sure the contamination and/or dust doesn’t
enter the airend side.
⑤Tap the air intake filter to remove large particles.
Then blow air to clean the surface of filter.
⑥In the case of oily or carbon dust, dip the element
into neutral detergent and water solution for about 30
minutes. Rinse the element several times with clean
water (water pressure is less than 39 psi (0.27MPa))
and air-dry it. Confirm the element is dried
completely.
⑦Reinstall and tighten the wing nut.
Differential pressure sensor
Cover
Air Intake filter
Wing nut
Duct
CAUTION
If the air intake filter is clogged with dust/dirt particles; Differential pressure (resistance of flow) across
the air intake filter increases, which results in decreased air intake to the airend and a rise in discharge
air temperature. To avoid a problem, service the air intake filter regularly. If the compressor room
environment is dusty or dirty, service the air intake filter more frequently than instructed on the
Maintenance Schedule.
Other manuals for NEXT Series
3
This manual suits for next models
10
Table of contents
Popular Compressor manuals by other brands

Invacare
Invacare Venture HomeFill II Owner's operator and maintenance manual
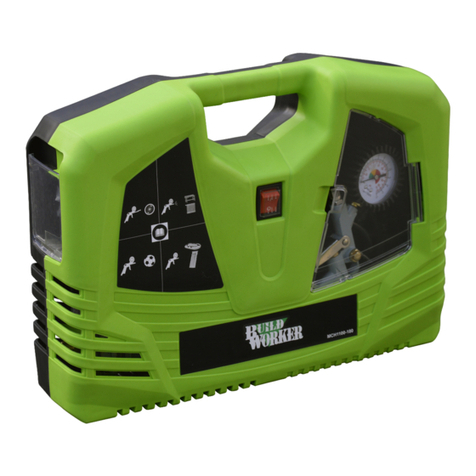
Build Worker
Build Worker MCH1100-180 Operation and safety notes
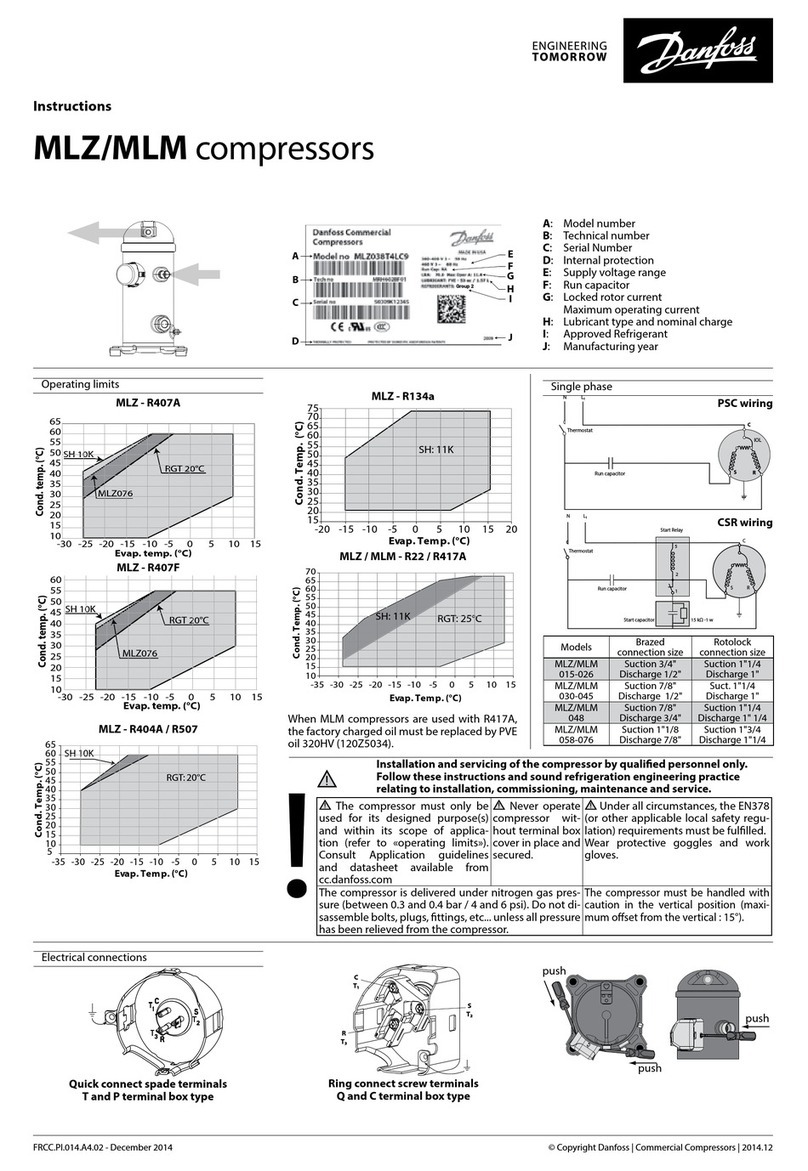
Danfoss
Danfoss MLZ Series instructions
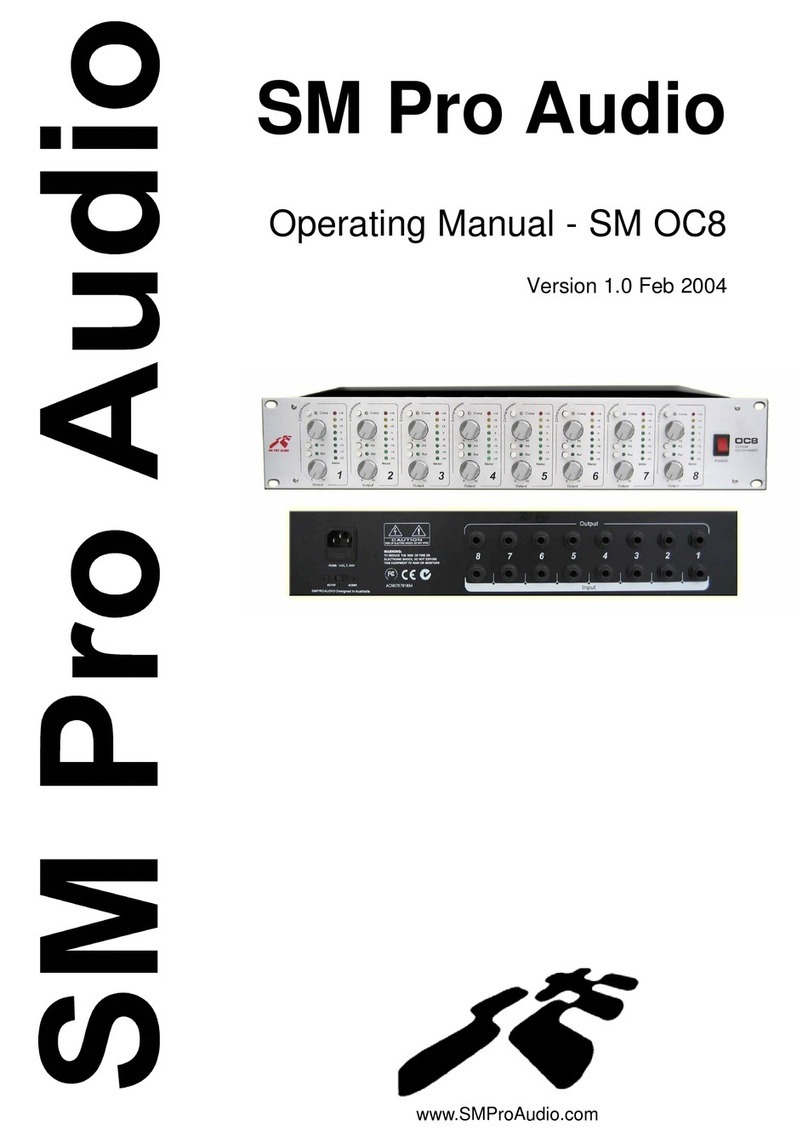
SM Pro Audio
SM Pro Audio OC8 operating manual
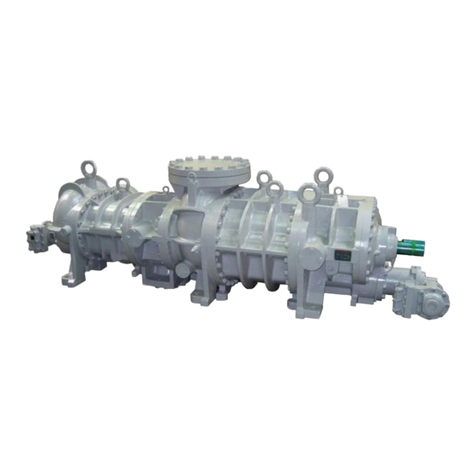
mycom
mycom 3225**C Series instruction manual
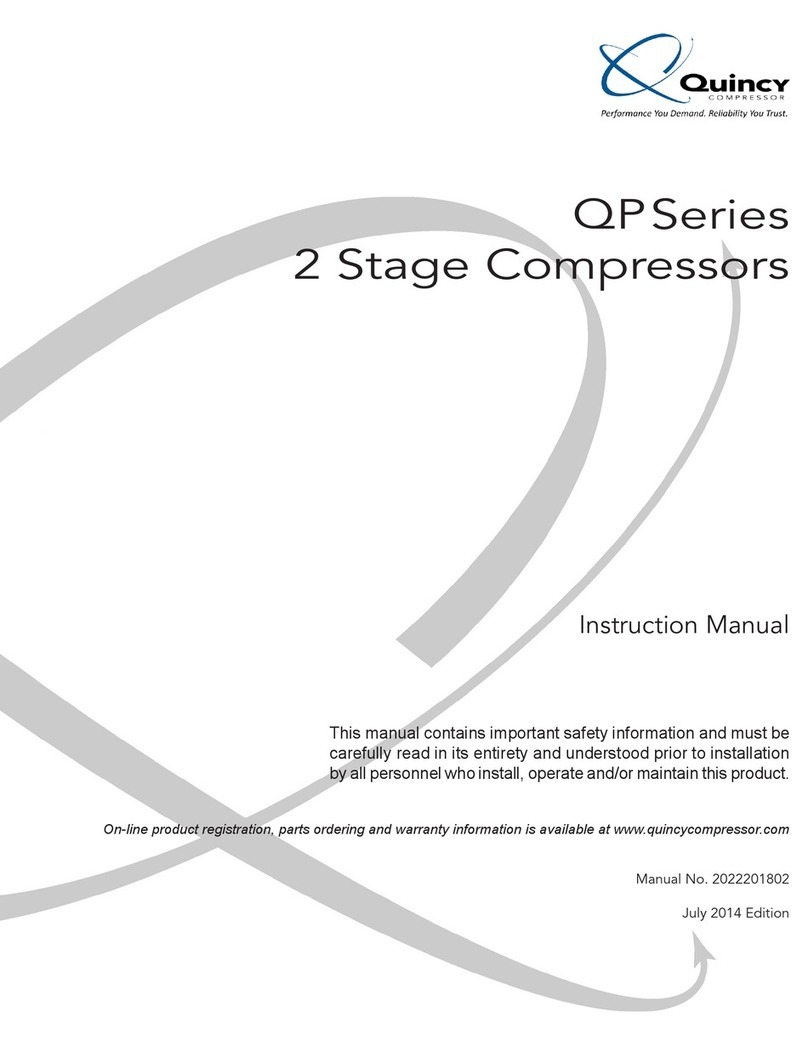
Quincy
Quincy QP Series instruction manual