Hitachi SJ300 Series Manual
Other Hitachi Power Tools manuals
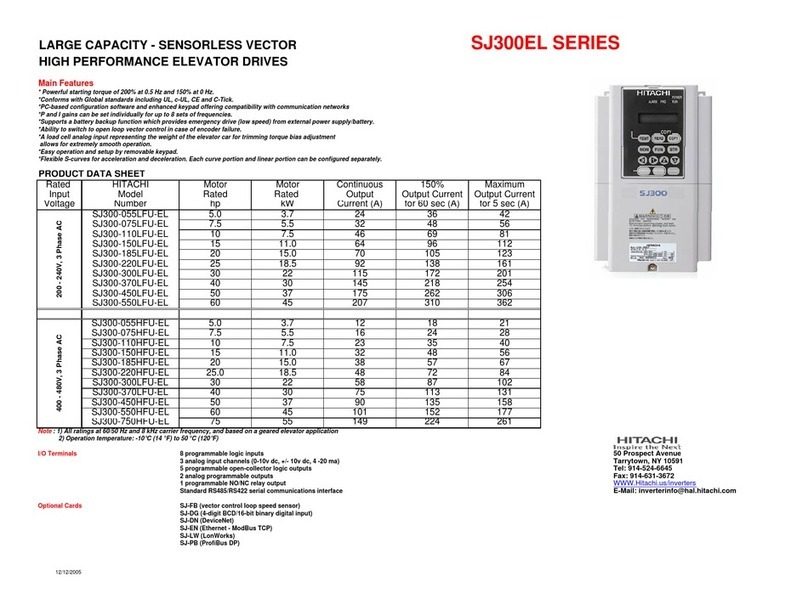
Hitachi
Hitachi SJ300-EL Series User manual
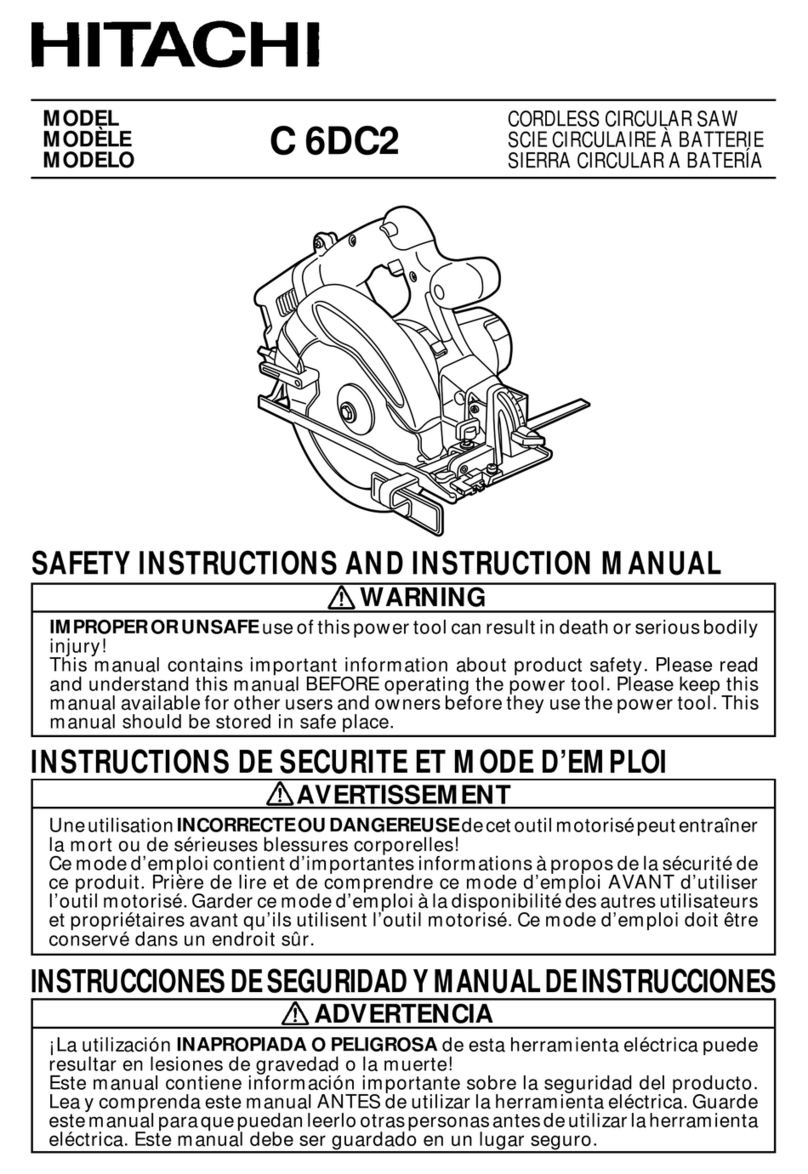
Hitachi
Hitachi C 6DC2 Operator's manual
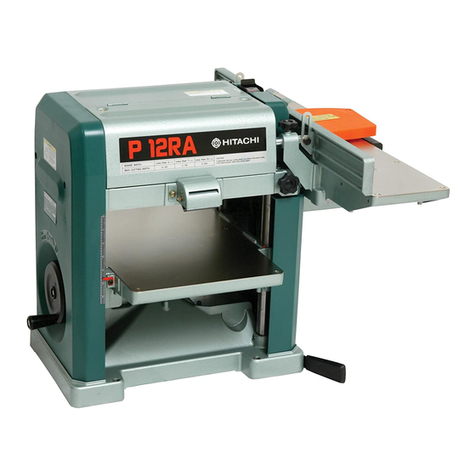
Hitachi
Hitachi P 12RA User manual
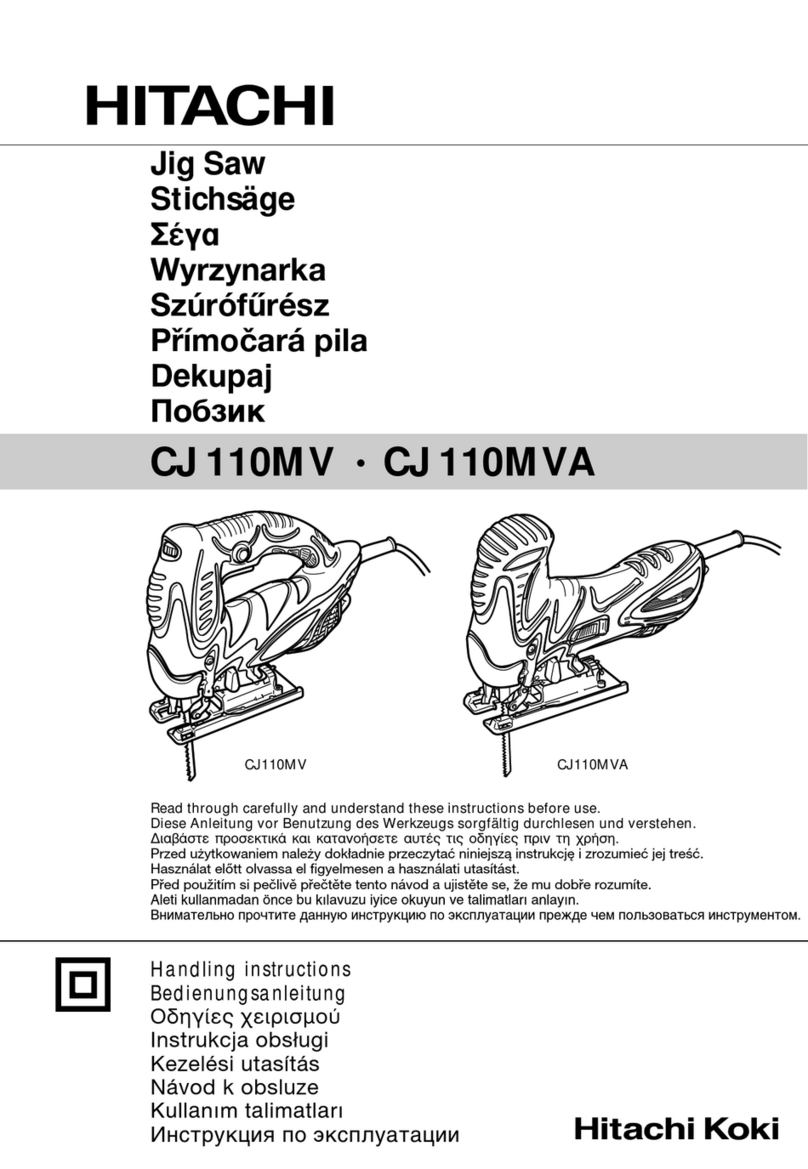
Hitachi
Hitachi CJ 110MVA User manual
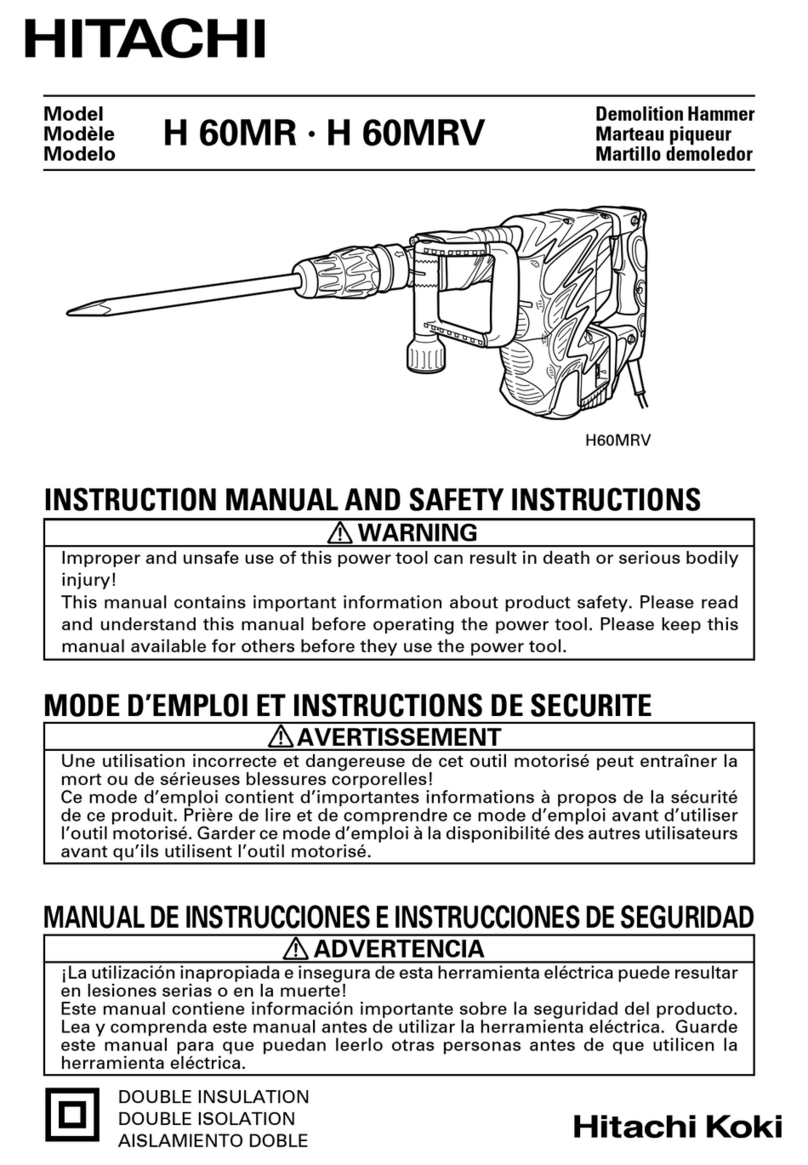
Hitachi
Hitachi H 60MRV User manual
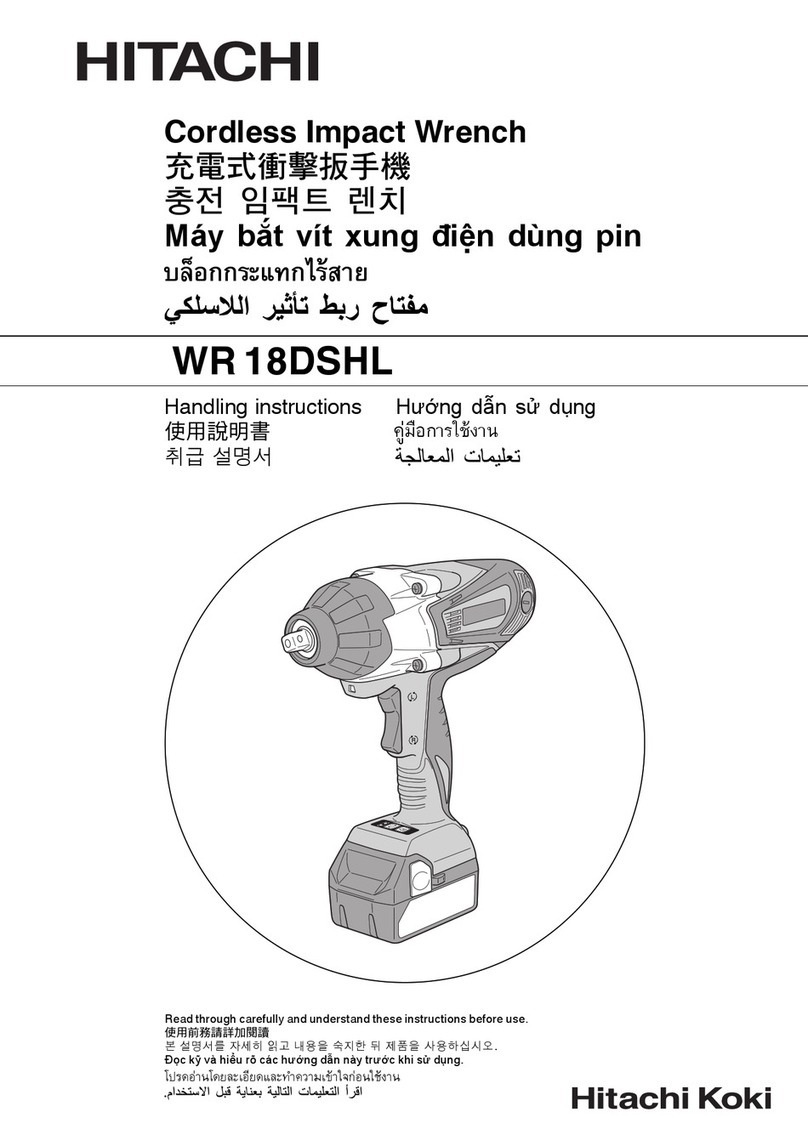
Hitachi
Hitachi WR18DSHL User manual
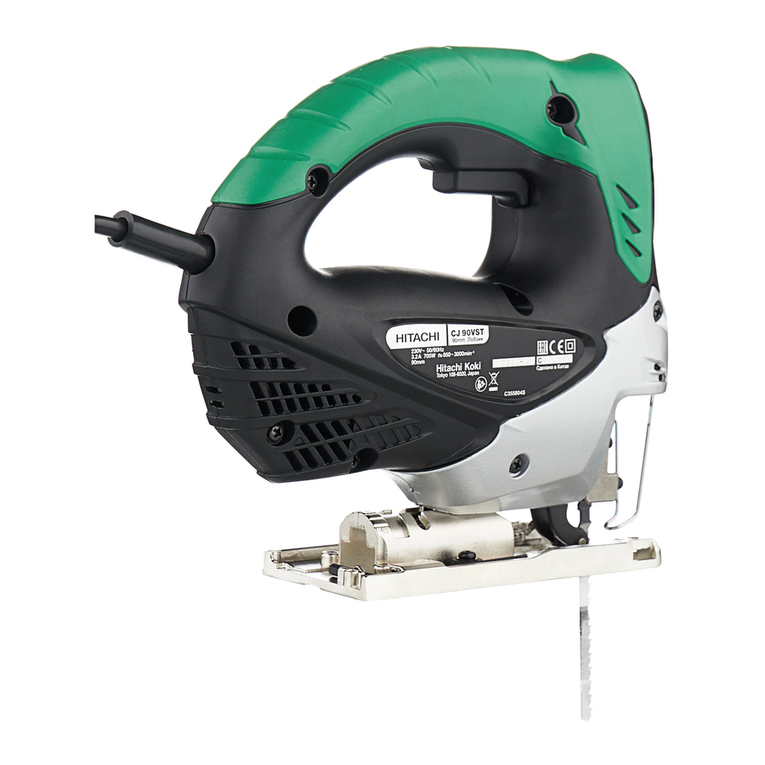
Hitachi
Hitachi CJ 90VST Instruction Manual

Hitachi
Hitachi WH14DBDL User manual

Hitachi
Hitachi RH600T User manual
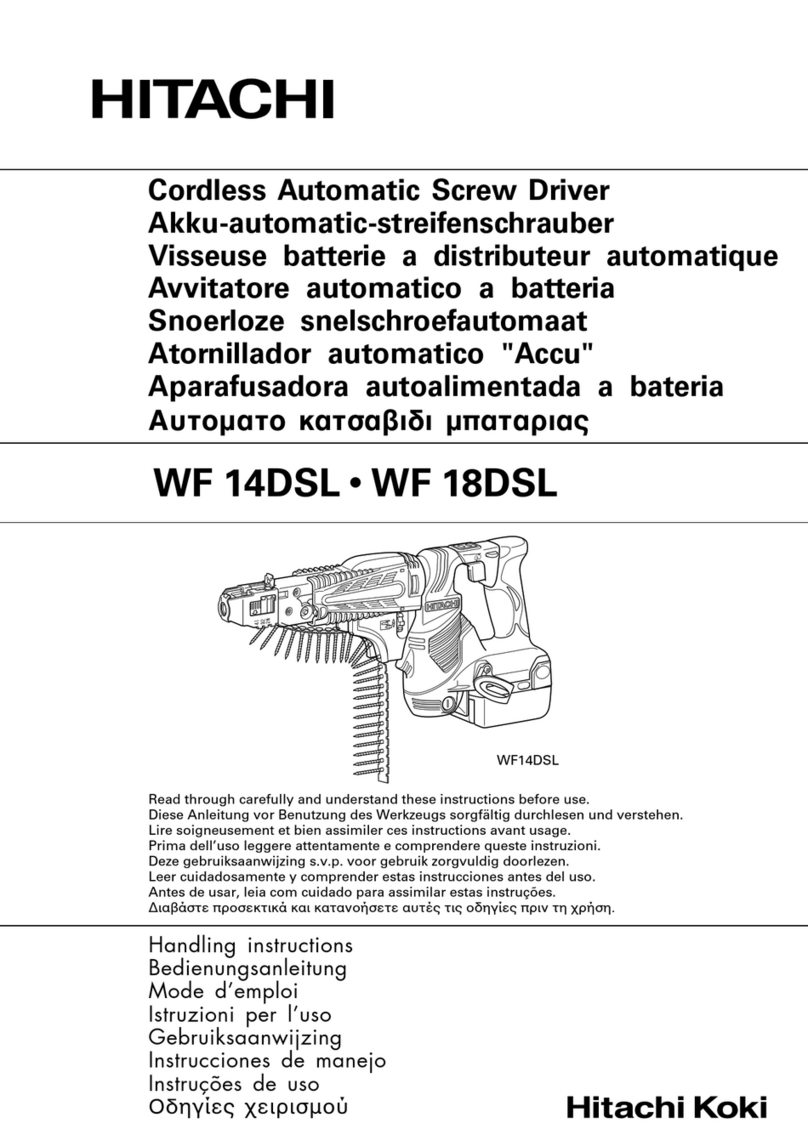
Hitachi
Hitachi WF 14DSL User manual
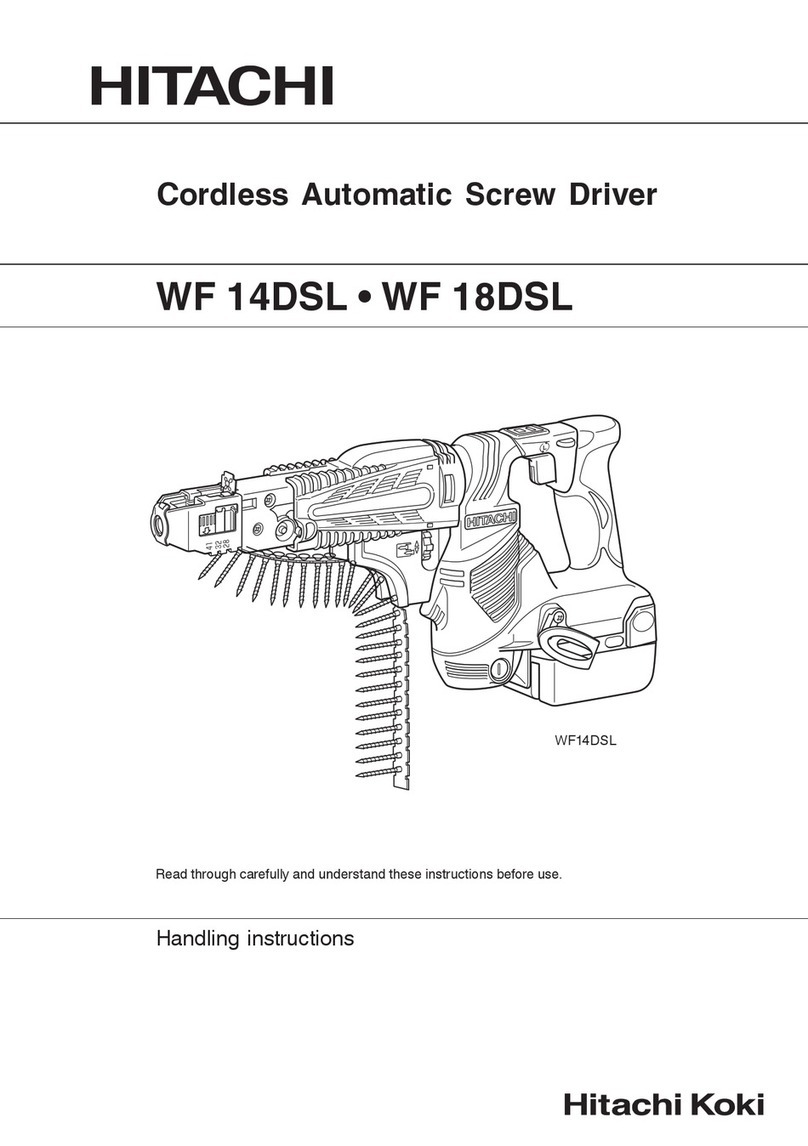
Hitachi
Hitachi WF 14DSL User manual

Hitachi
Hitachi CE16SA - 16 Gauge Sheet Metal Shear User manual
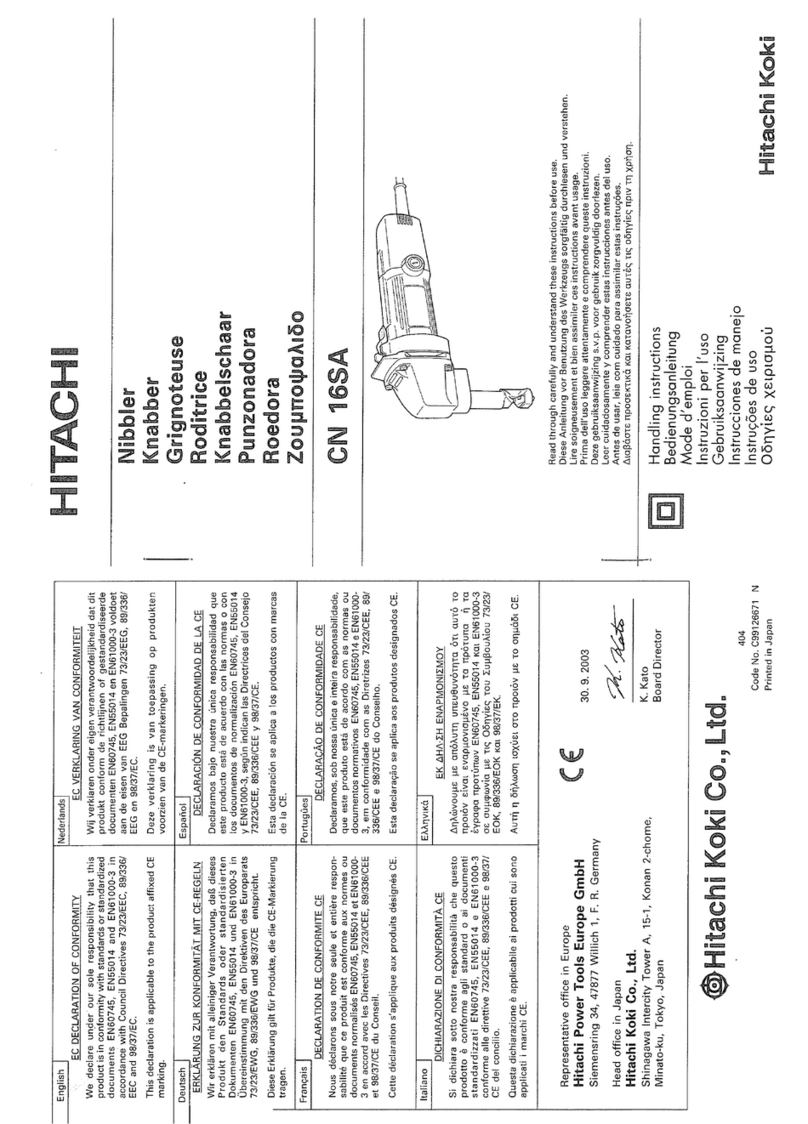
Hitachi
Hitachi CN 16SA User manual
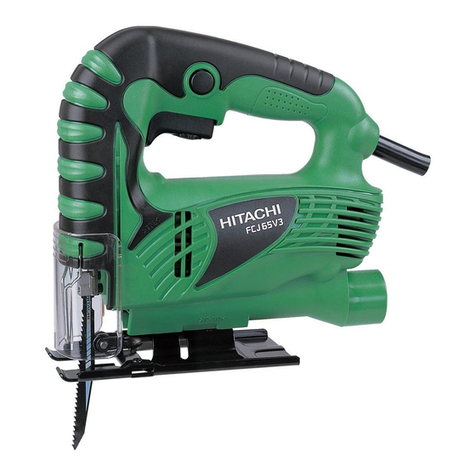
Hitachi
Hitachi FCJ 65V3 User manual
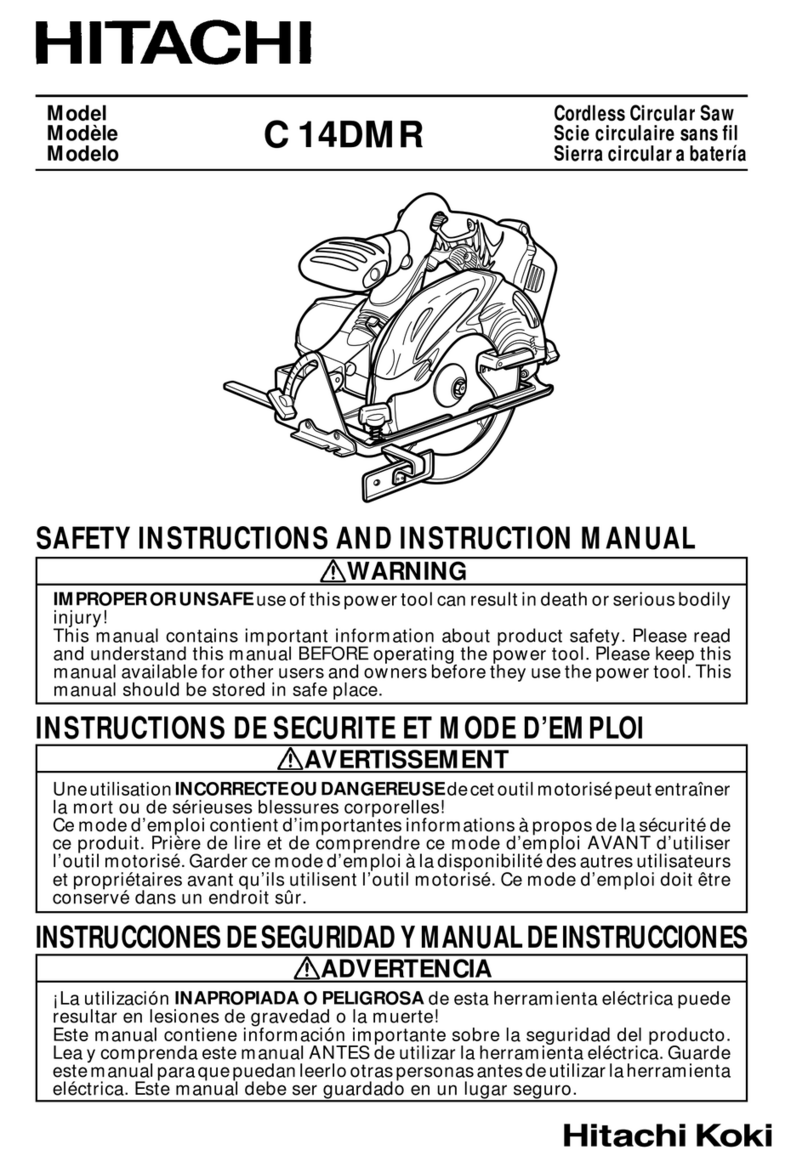
Hitachi
Hitachi C 14DMR Troubleshooting guide
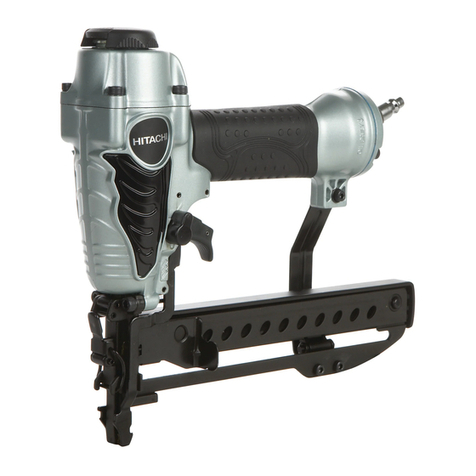
Hitachi
Hitachi N 3804AB3 Instruction Manual

Hitachi
Hitachi VH650 - Fencing Nailer, Full Head User manual
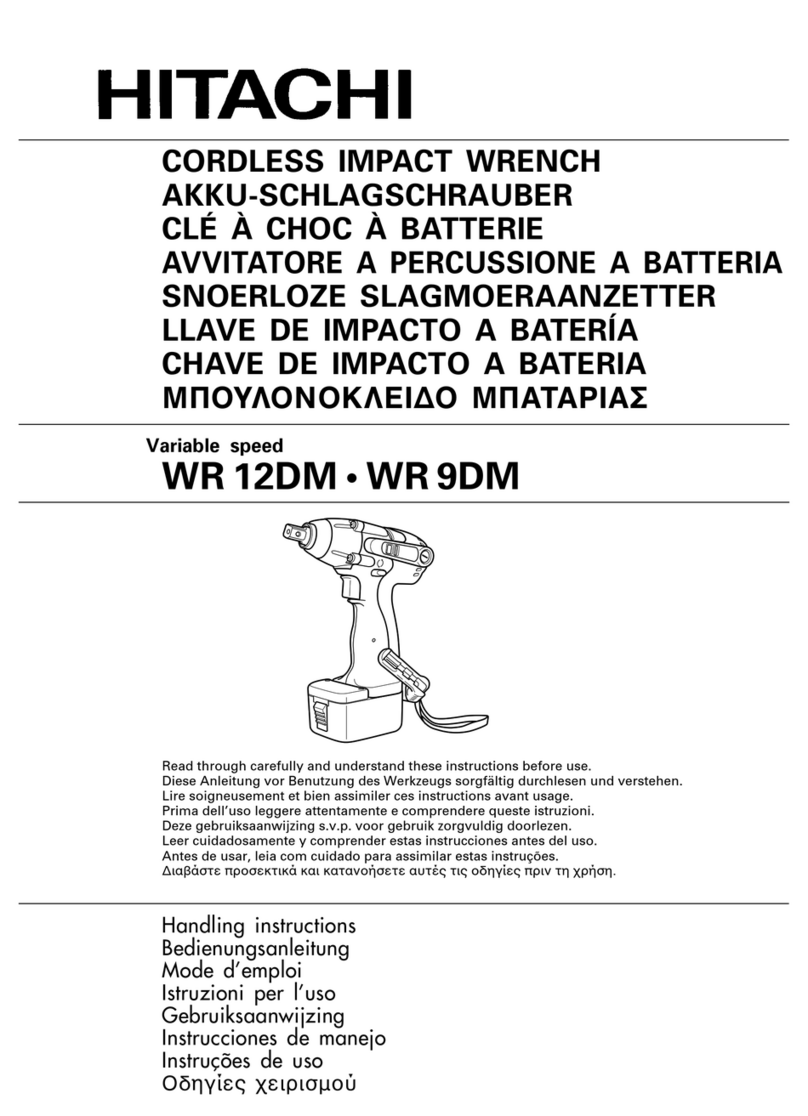
Hitachi
Hitachi WR 9DM User manual

Hitachi
Hitachi M 12VC Manual
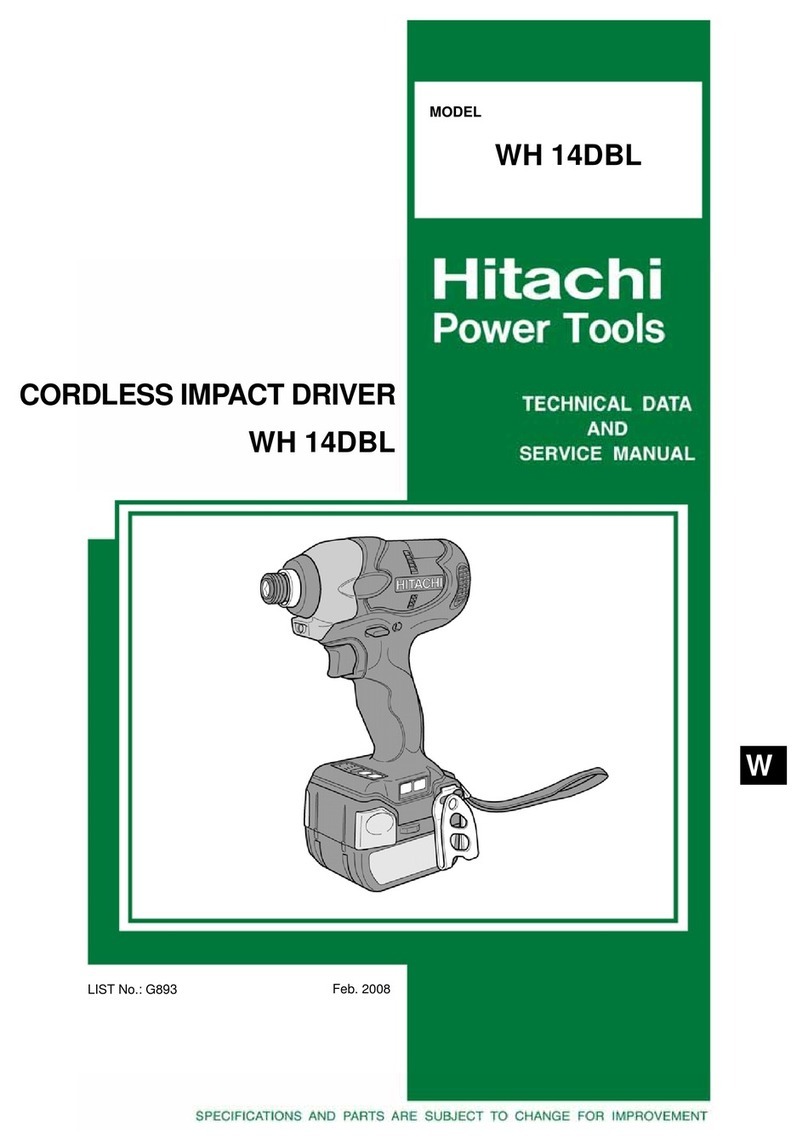
Hitachi
Hitachi WH14DBL Manual
Popular Power Tools manuals by other brands
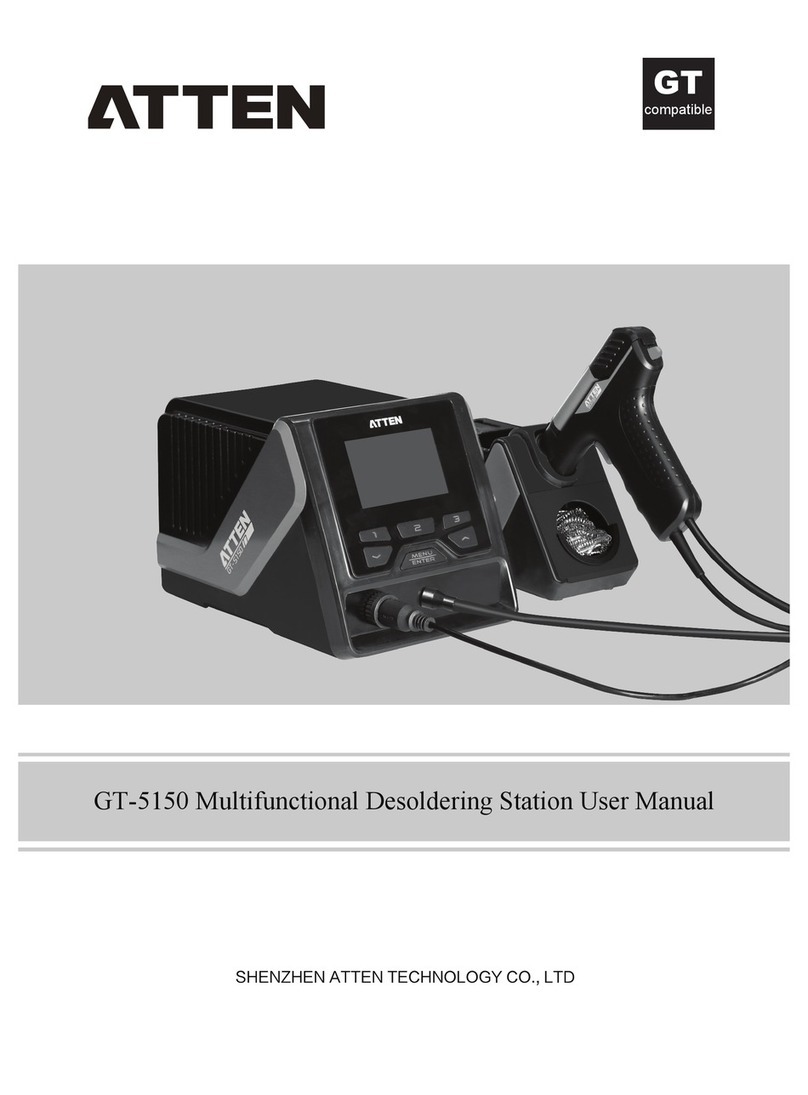
Atten
Atten GT-5150 user manual
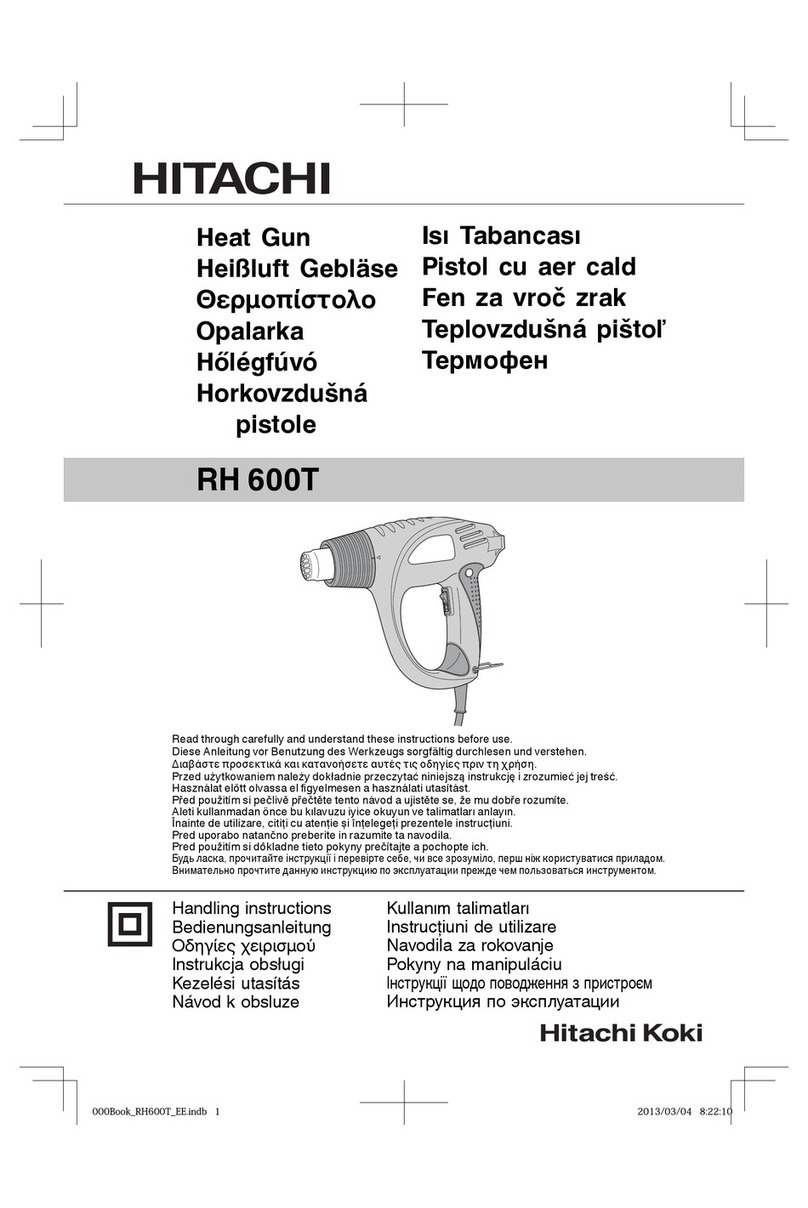
Hitachi Koki
Hitachi Koki RH600T Handling instructions
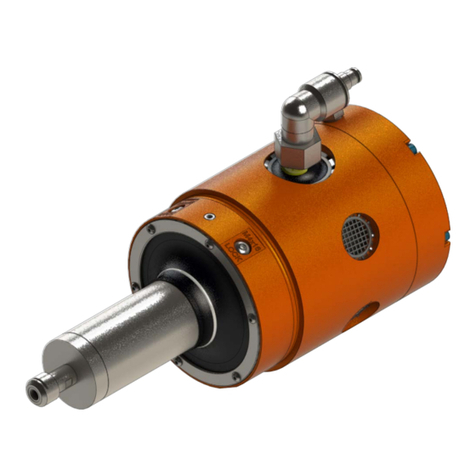
ATI Technologies
ATI Technologies Flexdeburr RC-1000 Series product manual
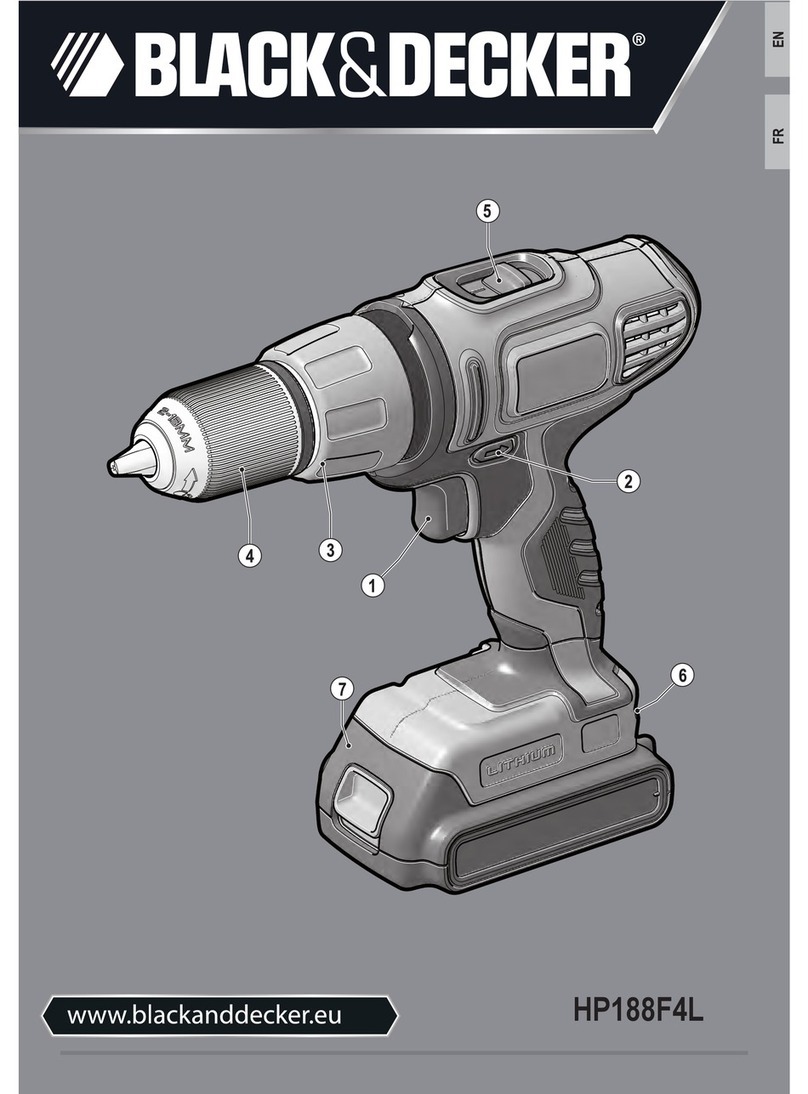
Black & Decker
Black & Decker HP188F4L user guide
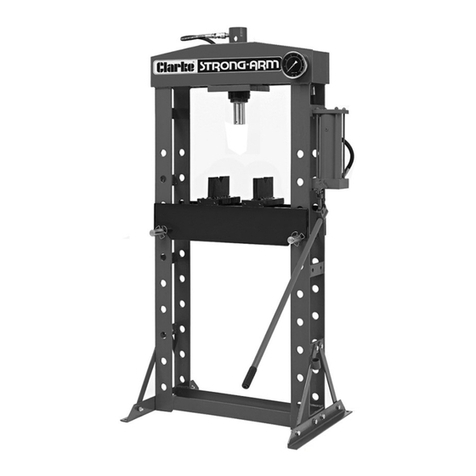
Clarke
Clarke Strong-Arm CSA20F Operation & maintenance instructions
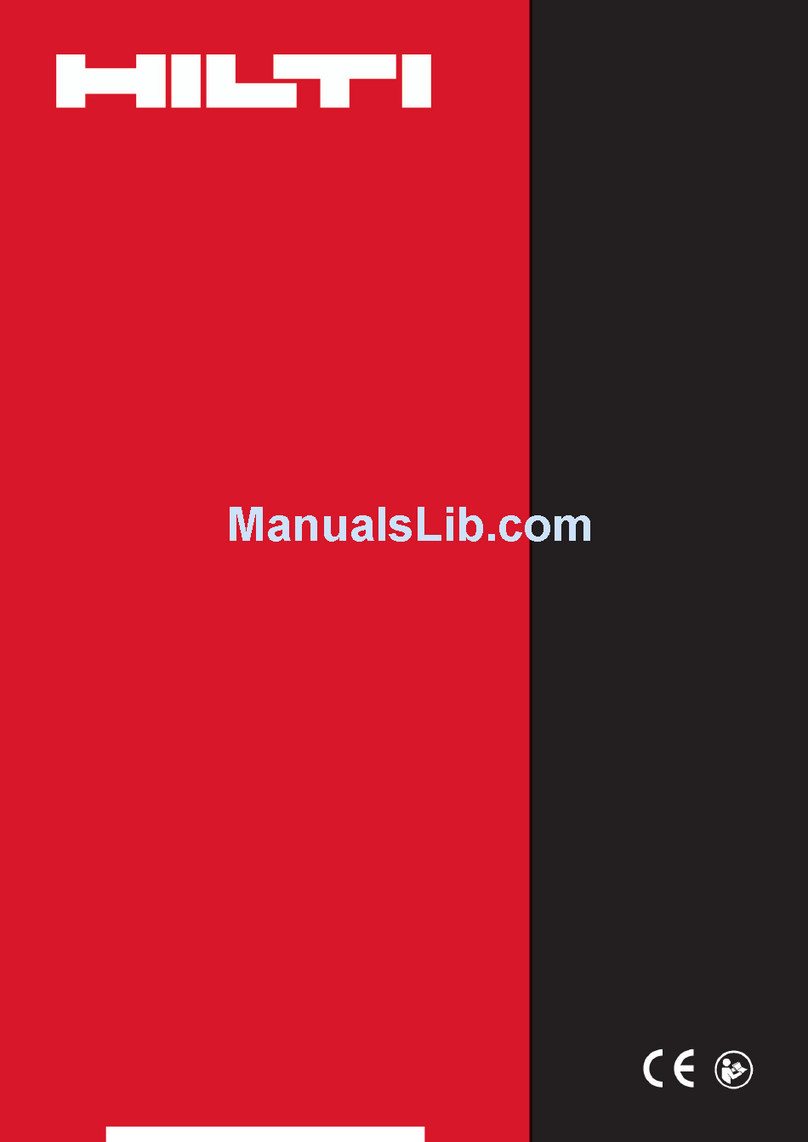
Hilti
Hilti SID 4-A22 operating instructions