Hoffer Flow Controls MF SERIES User manual

HFC 9907-A
HP-210
January 2010
MF SERIES
Mini-Flowmeters
for Low Flow Applications
USER’S MANUAL
HP-210
January 2013
107 Kitty Hawk Lane ●P.O. Box 2145 ●Elizabeth City, NC 27909
1-800-628-4584 ●(252) 331-1997 ●Fax (252) 331-2886
www.hofferflow.com email: [email protected]


HFC 9907-B
NOTICE
Hoffer Flow Controls, Inc. makes no warranty of any kind with regard to this
material, including, but not limited to, the implied warranties of merchantability and
fitness for a particular purpose.
This manual has been provided as an aid in installing, connecting, calibrating, operating,
and servicing this unit. Every precaution for accuracy has been taken in the
preparation of this manual; however, Hoffer Flow Controls, Inc. neither assumes
responsibility for any omissions or errors that may appear nor assumes liability for
any damages that result from the use of the products in accordance with information
contained in the manual.
HOFFER FLOW CONTROLS' policy is to provide a user manual for each item
supplied. Therefore, all applicable user manuals should be examined before
attempting to install or otherwise connect a number of related subsystems.
During installation, care must be taken to select the correct interconnecting wiring
drawing. The choice of an incorrect connection drawing may result in damage to the
system and/or one of the components.
Please review the complete model number of each item to be connected and locate the
appropriate manual(s) and/or drawing(s). Identify all model numbers exactly before
making any connections. A number of options and accessories may be added to the
main instrument, which are not shown on the basic user wiring. Consult the appropriate
option or accessory user manual before connecting it to the system. In many cases, a
system wiring drawing is available and may be requested from Hoffer Flow Controls.
This document contains proprietary information, which is protected by copyright.
All rights are reserved. No part of this document may be photocopied, reproduced,
or translated to another language without the prior written consent of Hoffer Flow
Controls, Inc.
HOFFER FLOW CONTROLS’ policy is to make running changes, not model
changes, whenever an improvement is possible. This affords our customers the
latest in technology and engineering. The information contained in this document is
subject to change without notice.
THIS WARRANTY IS EXPRESSLY IN LIEU OF ALL OTHER WARRANTIES, EXPRESSED
OR IMPLIED, INCLUDING ANY IMPLIED WARRANTY OF MERCHANTABILITY OR
FITNESS FOR A PARTICULAR PURPOSE. HFC SHALL NOT BE LIABLE FOR ANY LOSS OR
DAMAGE RESULTING, DIRECTLY OR INDIRECTLY, FROM THE USE OR LOSS OF USE OF THE GOODS.
WITHOUT LIMITING THE GENERALITY OF THE FOREGOING, THIS EXCLUSION FROM LIABILITY
EMBRACES THE PURCHASER'S EXPENSES FOR DOWNTIME OR FOR MAKING UP DOWNTIME, DAMAGES
FOR WHICH THE PURCHASER MAY BE LIABLE TO OTHER PERSONS, DAMAGES TO PROPERTY, AND
INJURY TO OR DEATH OF ANY PERSONS. HFC NEITHER ASSUMES NOR AUTHORIZES ANY PERSON TO
ASSUME FOR IT ANY OTHER LIABILITY IN CONNECTION WITH THE SALE OR USE OF HFC'S GOODS,
AND THERE ARE NO ORAL AGREEMENTS OR WARRANTIES COLLATERAL TO OR AFFECTING THE
AGREEMENT. PURCHASER'S SOLE AND EXCLUSIVE REMEDY IS THE REPAIR AND/OR REPLACEMENT OF
NONCONFORMING GOODS AS PROVIDED IN THE PRECEDING PARAGRAPHS.HFC SHALL NOT BE LIABLE
FOR ANY OTHER DAMAGES WHATSOEVER INCLUDING INDIRECT,INCIDENTAL,OR CONSEQUENTIAL
DAMAGES.

HFC 9907-B
LIMITED WARRANTY POLICY FOR HOFFER FLOW CONTROLS
HOFFER FLOW CONTROLS, INC. ("HFC") warrants HFC's Precision Series, API Series and
CT Series of turbine flowmeters to be free from defects in material and workmanship under
normal use and service, only if such goods have been properly selected for the service
intended, properly installed and properly operated and maintained as described in the turbine
flowmeter manual. Reference "turbine flowmeter manual" for specific details. This warranty
shall extend for a period of five (5) years from the date of shipment to the original purchaser
and covers the Precision Series, API Series and CT Series of flowmeters supplied with their
standard hybrid ceramic ball bearings only. All other HFC products carry a one (1) year
warranty. This warranty is extended only to the original purchaser ("Purchaser"). Purchaser's
sole and exclusive remedy is the repair and/or replacement of nonconforming goods as
provided in the following paragraphs.
In the event Purchaser believes the Hoffer product is defective, the product must be returned to
HFC, transportation prepaid by Purchaser, within the appropriate warranty period relative to
the product. If HFC's inspection determines that the workmanship or materials are defective
and the required maintenance has been performed and, has been properly installed and
operated, the product will be either repaired or replaced, at HFC's sole determination, free of
additional charge, and the goods will be returned, transportation paid by HFC, using a
transportation method selected by HFC.
Prior to returning the product to HFC, Purchaser must obtain a Returned Material
Authorization (RMA) Number from HFC's Customer Service Department within 30 days after
discovery of a purported breach of warranty, but not later than the warranty period; otherwise,
such claims shall be deemed waived. See the Return Requests/inquiries Section of this manual.
If HFC's inspection reveals the Hoffer product to be free of defects in material and
workmanship or such inspection reveals the goods were improperly used, improperly installed,
and/or improperly selected for service intended, HFC will notify the purchaser in writing and
will deliver the goods back to Purchaser upon receipt of Purchaser's written instructions and
agreement to pay the cost of transportation. If Purchaser does not respond within thirty (30)
days after notice from HFC, the goods will be disposed of in HFC's discretion.
HFC does not warrant the product to meet the requirements of any safety code of any state,
municipality, or other jurisdiction, and Purchaser assumes all risk and liability whatsoever
resulting from the use thereof, whether used singlely or in combination with other machines or
apparatus.
This warranty shall not apply to any HFC product or parts thereof, which have been repaired
outside HFC's factory or altered in any way, or have been subject to misuse, negligence, or
accident, or have not been operated in accordance with HFC's printed instructions or have been
operated under conditions more severe than, or otherwise exceeding, those set forth in the
specifications.
FOR NON-WARRANTY REPAIRS OR CALIBRATIONS, consult HOFFER FLOW
CONTROLS for current repair/calibration charges. Have the following information available
BEFORE contacting HOFFER FLOW CONTROLS:
1. P.O. number to cover the COST of the repair/calibration,
2. Model and serial number of the product, and
3. Repair instructions and/or specific problems relative to the product.

HP-210
CONTENTS
1. Introduction....................................................................................1
1.1 Model Number Designation...................................................2
1.2 Specification ..........................................................................7
2. Operation .......................................................................................9
2.1 Principle.................................................................................9
2.2 Precautions.............................................................................9
3. Installation ...................................................................................11
3.1 General Piping .....................................................................11
3.2 Strainers/Filters....................................................................12
3.3 Installation Kits....................................................................12
4. Maintenance.................................................................................13
4.1 General.................................................................................13
4.2 Disassembly.........................................................................13
4.3 Inspection & Repair.............................................................13
4.4 Assembly .............................................................................15
4.5 Pickup Coil Testing .............................................................15
4.6 Trouble Shooting .................................................................17
4.7 Spare Parts ...........................................................................18

HP-210

Introduction 1
HP-210
1Introduction
We are proud that you have selected a Hoffer Turbine Mini-
Flowmeter, the finest precision flow transducer on the market.
The Hoffer MF Series of Mini-Flowmeters are designed to meet the
need for a high quality low flow measurement device for service in
low to moderate viscosity clean liquids and for gas applications.
The information in this manual is provided to assist in the proper
installation, use, and maintenance of your instrument.
Please take a few minutes to read through this manual before
installing and operating your meter. If you have any problems with
the meter, refer to the maintenance and troubleshooting sections of
this manual.
If you need further assistance, contact your local Hoffer
Representative or contact the Hoffer Flow Controls customer service
department by telephone, fax, or email for advice.
We welcome you to our growing family of satisfied customers. If
you are not completely satisfied with either our product or service,
we encourage you to let us know. We want to improve!

Introduction 2
HP-210
1.1 Model Number Designation
The model number of the meter describes various fittings and options.
MINI-FLOWMETER SERIES FOR LIQUID
MODEL MF1/2X( A )- ( B )-( C )-( D )-( E/F )-(MS)-(G )
PROCESS CONNECTION/END FITTING SIZE
FLOWMETER SIZE
MINIMUM FLOW RATE IN GPM
MAXIMUM FLOW RATE IN GPM
BEARING TYPE
PICKUP COILS
RISER AND EXPLOSION PROOF COIL ENCLOSURES
END FITTING TYPE
SPECIAL FEATURES
PROCESS CONNECTION
ALL MINI-FLOWMETERS ARE 1/2", 37 DEG. MALE FLARE PER MS33656
MODEL MF1/2X( A )-( )-( )-( )-( / )-( )-( )
END FITTING X ( A )
MF1/2X20B
MF1/2X30B
MF1/2X40B
MF1/2X50B
MF1/2X60B
MF1/2X70B
MF1/2X80B
MF1/2X90B
MF1/2X100B
MF1/2X125B
MF1/2X150B
MF1/2X175B
MINIMUM FLOW AND MAXIMUM FLOW RATE IN GPM (LINEAR RANGE)
MODEL MF1/2X( )-( B )-( C )-( )-( / )-( )-( )
( B ) ( C )
FLOWMETER SIZE MINIMUM FLOW TO MAXIMUM FLOW
MF20 .015 GPM .049 GPM
MF30 .017 GPM .120 GPM
MF40 .020 GPM .150 GPM
MF50 .023 GPM .2 GPM
MF60 .025 GPM .25 GPM
MF70 .050 GPM .5 GPM
MF80 .075 GPM .75 GPM
MF90 .085 GPM .85 GPM
MF100 .1 GPM 1 GPM
MF125 .13 GPM 1.3 GPM
MF150 .2 GPM 2 GPM
MF175 .3 GPM 3 GPM

Introduction 3
HP-210
BEARING TYPE
MODEL MF1/2X( )-( )-( )-( D )-( / )-( )-( )
TURBINE SIZES OPTION ( D )
MF1/2X20B (PB) CERAMIC HYBRID BALL BEARING, SELF LUBRICATING
(C) HARD CARBON COMPOSITE SLEEVE BEARING
(T) TUNGSTEN CARBIDE SLEEVE BEARING
MF1/2X30B (BP) CERAMIC HYBRID BALL BEARING, SELF LUBRICATING
(C) HARD CARBON COMPOSITE SLEEVE BEARING
(T) TUNGSTEN CARBIDE SLEEVE BEARING
MF1/2X40B (BP) CERAMIC HYBRID BALL BEARING, SELF LUBRICATING
(C) HARD CARBON COMPOSITE SLEEVE BEARING
(T) TUNGSTEN CARBIDE SLEEVE BEARING
MF1/2X50B (BP) CERAMIC HYBRID BALL BEARING, SELF LUBRICATING
MF1/2X60B (C) HARD CARBON COMPOSITE SLEEVE BEARING
MF1/2X70B (T) TUNGSTEN CARBIDE SLEEVE BEARING
MF1/2X80B (BP) CERAMIC HYBRID BALL BEARING, SELF LUBRICATING
MF1/2X90B (C) HARD CARBON COMPOSITE SLEEVE BEARING
MF1/2X100B (T) TUNGSTEN CARBIDE SLEEVE BEARING
MF1/2X125B
MF1/2X150B
MF1/2X175B
PICKUP COILS
MODEL MF1/2X( )-( )-( )-( )-( E / )-( )-( )
OPTION ( E )
(1M) ONE MAG COIL
(1MC3PA) ONE RF COIL
(1MC2PAHT) ONE HIGH TEMP RF COIL
(1HTM) HIGH TEMP MAG COIL
(1ISM) ONE INTRINSICALLY SAFE MAG COIL, NORTH AMERICA
(1ISM-ATEX) ONE ISM ATEX COIL
(1RPMXXX) ONE REDI-PULSE MAG COIL
(1RPRXXX) ONE REDI-PULSE RF COIL
(1DMXXXX) ONE REDI-PULSE INTRINSICALLY SAFE MAG COIL
(1DRXXXX) ONE REDI-PULSE INTRINSICALLY SAFE RF COIL
(-ATEX)* WHEN ANY COIL IS GOING TO HAVE AN ATEX ENCLOSURE MOUNTED
ON THE FLOWMETER ADD (-ATEX) AFTER THE COIL PART NUMBER.
(THE COIL NEEDS TO BE MODIFIED TO FIT INTO A 3/4" RISER WELDED TO
THE BODY REQUIRED BY ATEX)
*OPTIONAL SPECIAL TOOL
IN ORDER TO REPLACE THE COIL IN THE FIELD, A SPECIAL WRENCH
IS REQUIRED TO REPLACE THE COIL.
(-P*) PIGTAIL OR FLYING LEADS, ADD -P AND THE *LENGTH OF LEADS
AFTER ANY COIL EXCEPT THE HIGH TEMPERATURE COILS.

Introduction 4
HP-210
RISER AND EXPLOSION PROOF COIL ENCLOSURES
MODEL MF1/2X( )-( )-( )-( )-( / F )-( )-( )
OPTION ( F )
(X) 1" MNPT RISER, WELDED TO BODY
(X-ATEX) 3/4" MNPT RISER, WELDED TO BODY
(XE2) 1" MNPT RISER WITH E2 ENCLOSURE*
INCLUDES STOCK #300-8375 1"X3/4" ADAPTER
(X-ATEX)E2 3/4" MNPT RISER WITH E2 ENCLOSURE*
(X8S) 8" LONG S/S 1" MNPT RISER
FOR FLUID TEMPERATURES BELOW-40°F (-40°C) OR ABOVE
+140°F (+60°C)
(X8S-ATEX) 8" LONG S/S 3/4" MNPT RISER FOR FLUID TEMPERATURES BELOW-40°F
(-40°C) OR ABOVE +140°F (+60°C)
*NOTES: EXPLOSION-PROOF/FLAME-PROOF ENCLOSURE WITH ¾” FNPT MOUNT
AND 3/4" CABLE ENTRY
FM: CLASS I, DIV. 1, GR. ABCD, CLASS II/III, DIV. 1, GR. EFG, TYPE 4X
CSA: CLASS I, DIV. 1, GR. ABCD, CLASS II, DIV 1, GR. EFG, CLASS III,
TYPE 4X EX D IIC, CLASS I, ZONE 1, IP 66
ATEX: EX II 2GD Ex d tD IIC, IP66/68
IEC: EX D IIC IP68
PROCESS CONNECTION/END FITTING TYPE
MODEL MF1/2X( )-( )-( )-( )-( / )-(MS)-( )
OPTION
(MS) ALL MINI-FLOWMETERS ARE 1/2", 37 DEG. MALE FLARE PER MS33656
(1/4-TS) 1/4" TUBE STUB
(1/2-TS) 1/2" TUBE STUB
SPECIAL FEATURES
MODEL MF1/2X( )-( )-( )-( )-( / )-( )-( G )
OPTION ( G )
(6W ) HIGH PRESSURE UNITS, OVER 1000 PSIG TO MAX OF 6000 PSIG*
(6CW) CRYOGENIC SERVICE
RATED TO 6000 PSIG AND CLEANED FOR LOX SERVICE*
(CE) CE MARK REQUIRED FOR EUROPE
(PED-CE) PED REQUIRES THAT BOTH THE OPERATING PRESSURE AND TEMPERATURE
MUST BE KNOWN AND ENTERED ON THE ORDER. THIS INFORMATION
WILL BE MARKED ON THE HOUSING TO MEET PED REQUIREMENTS.
(SEP-CE) SOUND ENGINEERING PRACTICE.
(SP) ANY SPECIAL FEATURES THAT ARE NOT COVERED IN THE MODEL
NUMBER, USE A WRITTEN DESCRIPTION OF THE -SP.
*WELDED CAP-MINI MUST BE RETURNED TO THE FACTORY FOR
REPAIR – NOT FIELD REPAIRABLE.
FOR UL LISTED ENCLOSURE CONTACT FACTORY

Introduction 5
HP-210
MINI-FLOWMETER SERIES FOR GAS
MODEL MF1/2X(A)-(G)-(B)-(C/D)-(MS)-(PT)-(E)
PROCESS CONNECTION/END FITTING SIZE
FLOWMETER SIZE
MAXIMUM FLOW RATE IN ACFM
BEARING TYPE
PICKUP COILS
RISER AND EXPLOSION PROOF COIL ENCLOSURES
END FITTING TYPE
1/4" PRESSURE TAP @ ROTOR
SPECIAL FEATURES
PROCESS CONNECTION
ALL MINI-FLOWMETERS ARE 1/2", 37 DEG. MALE FLARE PER MS33656
MODEL MF1/2X( A )-( )-( )-( / )-( )-( )-( )
END FITTING X ( A )
MF1/2X30B
MF1/2X50B
MF1/2X80B
MF1/2X90B
MF1/2X125B
MF1/2X175B
MAXIMUM FLOW RATE IN ACFM
MODEL MF1/2X( )-( G )-( )-( / )-( )-( )-( )
OPTION
( G ) RATE IS DETERMINED BY THE GAS SIZING PROGRAM BY SALES
BEARING TYPE
MODEL MF1/2X( )-( )-( B )-( / )-( )-( )-( )
TURBINE SIZES OPTION ( B )
MF1/2X30B (SB) STAINLESS STEEL BALL BEARING, SELF LUBRICATING
MF1/2X50B (SB) STAINLESS STEEL BALL BEARING, SELF LUBRICATING
MF1/2X80B (SB) STAINLESS STEEL BALL BEARING, SELF LUBRICATING
MF1/2X90B (SB) STAINLESS STEEL BALL BEARING, SELF LUBRICATING
MF1/2X125B
MF1/2X175B

Introduction 6
HP-210
PICKUP COILS
MODEL MF1/2X( )-( )-( )-( C / )-( )-( )-( )
OPTION ( C )
(1M) ONE MAG COIL
(1MC3PA) ONE RF COIL
(1MC2PAHT) ONE HIGH TEMP RF COIL
(1ISM) ONE INTRINSICALLY SAFE MAG COIL, NORTH AMERICA
(1ISM-ATEX) ONE ISM ATEX COIL
(1RPRXXX) ONE REDI-PULSE RF COIL
(1DRXXXX) ONE REDI-PULSE INTRINSICALLY SAFE RF COIL
(-ATEX)* WHEN ANY COIL IS GOING TO HAVE AN ATEX ENCLOSURE MOUNTED
ON THE FLOWMETER ADD (-ATEX) AFTER THE COIL PART NUMBER.
(THE COIL NEEDS TO BE MODIFIED TO FIT INTO A 3/4" RISER WELDED TO
THE BODY REQUIRED BY ATEX)
*OPTIONAL SPECIAL TOOL
IN ORDER TO REPLACE THE COIL IN THE FIELD, A SPECIAL WRENCH
IS REQUIRED TO REPLACE THE COIL.
(-P*) PIGTAIL OR FLYING LEADS, ADD -P AND THE *LENGTH OF LEADS
AFTER ANY COIL EXCEPT THE HIGH TEMPERATURE COILS.
RISER AND EXPLOSION PROOF COIL ENCLOSURES
MODEL MF1/2X( )-( )-( )-( / D )-( )-( )-( )
OPTION ( D )
(X) 1" MNPT RISER, WELDED TO BODY
(X-ATEX) 3/4" MNPT RISER, WELDED TO BODY
(XE2) 1" MNPT RISER WITH E2 ENCLOSURE*
INCLUDES STOCK #300-8375 1"X3/4" ADAPTER
(X-ATEX)E2 3/4" MNPT RISER WITH E2 ENCLOSURE*
(X8S) 8" LONG S/S 1" MNPT RISER
FOR FLUID TEMPERATURES BELOW-40°F (-40°C) OR ABOVE
+140°F (+60°C)
(X8S-ATEX) 8" LONG S/S 3/4" MNPT RISER FOR FLUID TEMPERATURES BELOW-40°F
(-40°C) OR ABOVE +140°F (+60°C)
*NOTES: EXPLOSION-PROOF/FLAME-PROOF ENCLOSURE WITH ¾” FNPT MOUNT
AND 3/4" CABLE ENTRY
FM: CLASS I, DIV. 1, GR. ABCD, CLASS II/III, DIV. 1, GR. EFG, TYPE
4X
CSA: CLASS I, DIV. 1, GR. ABCD, CLASS II, DIV 1, GR. EFG, CLASS III,
TYPE 4X EX D IIC, CLASS I, ZONE 1, IP 66
ATEX: EX II 2GD Ex d tD IIC, IP66/68
IEC: EX D IIC IP68
FOR UL LISTED ENCLOSURE CONTACT FACTORY

Introduction 7
HP-210
PROCESS CONNECTION/END FITTING TYPE
MODEL MF1/2X( )-( )-( )-( )-( / )-(MS)-( )-( )
OPTION
(MS) ALL MINI-FLOWMETERS ARE 1/2", 37 DEG. MALE FLARE PER MS33656
(1/4-TS) 1/4" TUBE STUB
(1/2-TS) 1/2" TUBE STUB
PRESSURE TAP @ ROTOR
MODEL MF1/2X( )-( )-( )-( )-( / )-( )-(PT)-( )
OPTION
(PT) 1/4" PRESSURE TAP @ ROTOR
SPECIAL FEATURES
MODEL MF1/2X( )-( )-( )-( )-( / )-( )-( )-( E )
OPTION ( E )
(6W ) HIGH PRESSURE UNITS, OVER 1000 PSIG TO MAX OF 6000 PSIG*
(6CW) CRYOGENIC SERVICE RATED TO 6000 PSIG AND CLEANED FOR LOX
SERVICE.*
(CE) CE MARK REQUIRED FOR EUROPE (PED-CE)
(PED-CE) PED REQUIRES THAT BOTH THE OPERATING PRESSURE AND
TEMPERATURE MUST BE KNOWN AND ENTERED ON THE ORDER.
THIS INFORMATION WILL BE MARKED ON THE HOUSING TO MEET PED
REQUIREMENTS.
(SEP-CE) SOUND ENGINEERING PRACTICE
(SP) ANY SPECIAL FEATURES THAT ARE NOT COVERED IN THE MODEL
NUMBER, USE A WRITTEN DESCRIPTION OF THE -SP.
*WELDED CAP-MINI MUST BE RETURNED TO THE FACTORY FOR
REPAIR – NOT FIELD REPAIRABLE.
1.2 Specification
Linearity: 1.0% of reading over 10:1 flow range
Repeatability: 0.25% of reading
Flow Ranges:
Liquid Applications: 0.02 to 3.5 GPM w/ MAG pickup in 10:1 turndown
0.007 to 3.5 GPM w/ MCP pickup in 25:1 turndown
Gas Applications: 0.005 to 1 ACFM w/ MCP pickup; turndown
dependent on gas density
Temperature Range: -450 °F to +450 °F
Output: Dependent on pickup coil selected

Introduction 8
HP-210
This page intentionally left blank.

Operation 9
HP-210
2Operation
2.1 Principle
The Hoffer MF Series has been developed to meet the need for a
low flow measurement device for use with low to moderate
viscosity clean liquids and for gas measurement applications.
The MF Series is a family of low flow rate measurement devices
whose design is based on a Pelton Wheel-like rotor. The measured
fluid is directed tangentially through a velocity nozzle against the
rotor causing it to spin. The pickup coil senses the spinning
motion of the rotor through the housing and converts it into a
pulsing electrical signal. Summation of the pulsing electrical
signal relates directly to the total flow, while the frequency is
related to the flow rate.
2.2 Precautions
Do not drop the meter. Dropping the meter may result in damage
to the meter housing and/or internals.
Do not operate the meter at flowrates greater than the maximum
flowrate marked on the meter. Operating at flowrates greater than
the maximum flowrate may over-spin the meter. Over-spinning
may result in damage to the meter.
CAUTION:Avoid over-spinning the meter. Over-spinning the meter may
result in damage to the meter internals and lead to meter
failure.

Operation 10
HP-210
This page intentionally left blank.

Installation 11
HP-210
3Installation
Upon receipt of the flowmeter carefully inspected it, checking for
any indications of damage which may have occurred during
shipment. Inspect all packing material carefully for parts or
components which may have been packed with the shipment.
Refer to the packing list/invoice for a detailed list of items
included in the shipment.
3.1 General Piping
The MF Series Flowmeters are capable of sensing fluid flow in one
direction only. The meter housing is marked by a flow direction
arrow to indicate the direction of flow through the meter. The
meter must be installed in the piping in the correct orientation to
ensure the most accurate and reliable operation. Care should be
taken in the proper selection of the mating fittings. Size, type of
material, and pressure rating should be the same as the flowmeter
supplied.
When it is expected that flow will be intermittent, the meter should
not be mounted at a low point in the piping system. Solids which
settle or congeal in the meter may affect meter performance.
In order to achieve optimum electrical signal output from the
flowmeter, due consideration must be given to its isolation from
ambient electrical interference such as nearby motors,
transformers, and solenoids.
A typical flowmeter installation is shown below:
Blocking and Bypass valves should be installed if it is necessary to
do preventive maintenance on the flowmeter without shutting
down the flow system. The Bypass valve can be opened before the
Blocking valves are closed allowing the flow to continue while
removing the turbine flowmeter for service.
BYPASS RUN
Blocking Valve
Bypass Valve
Blocking Valve
Turbine Flowmeter
METER RUN
Strainer

12 Installation
HP-210
IMPORTANT: All flow lines should be purged prior to installing the
meter. To prevent possible damage to the meter, install the
meter ONLY in flow lines that are clean and free of debris.
Upon initial start-up of the system a spool piece should be installed
in place of the flowmeter so that purging of the system can be
performed to remove all particle debris which could cause damage
to the meter internals. In applications where meter flushing is
required after meter service, care should be taken as to not over-
spin the meter, as severe meter damage may occur.
CAUTION:Avoid over-spinning the meter. Over-spinning the meter may
result in damage to the meter internals and lead to meter
failure.
3.2 Strainers/Filters
The MF Series flowmeters are designed for use in a clean fluid
service. However, the service fluid may carry some particulate
material which would need to be removed before reaching the
flowmeter. Under these conditions a strainer/filter may be required
to reduce the potential hazard of fouling or damage that may be
caused by foreign matter.
METER SIZE MESH SIZE PARTICLE SIZE
(Maximum)
MF Series 100 .0055
¼” to ½” 100 .0055
5/8” to 1¼” 70 .008
1½” to 3” 40 .015
If a strainer/filter is required in the system, it should be located
upstream of the flowmeter taking care that the proper minimum
distance is kept between the strainer and flowmeter.
3.3 Installation Kits
Installation kits for the Hoffer MF Series Flowmeter consist of two
lengths of appropriate tubing cut to a length appropriate for the
upstream and downstream straight pipe run with appropriate end
fittings.

Maintenance 13
HP-210
4Maintenance
4.1 General
Preventive maintenance for the MF Series mini-flowmeter
consists of a thorough general inspection. Remove the meter
from the service line and take to a clean work area. Use the
following procedures and exploded component views to
remove, inspect, and reinsert the flowmeter internals.
4.2 Disassembly
1. Hold the Mini-Flowmeter securely using a vise. Meter
orientation should be such that the threaded plug is facing up.
Use extreme care not to damage the meter housing or piping
connections when placing in the vise.
2. Using a large-blade screwdriver, turn the plug
counterclockwise to remove.
3. To remove the shaft assembly, carefully thread a 10-32 screw
into the hole provided in insert. Thread the screw into the
insert until it bottoms out (finger tight only).
4. Turn the housing over and slowly and carefully pull the shaft
assembly and internals out of the housing. Take care not to
damage the shaft, rotor, and/or bearings.
5. Remove and discard the gasket/seal.
4.3 Inspection & Repair
1. Examine the flowmeter internals for signs of corrosion or
fouling by foreign materials.
2. Examine the shaft, rotor, and bearings for signs of wear and/or
damage.
3. If wear or damage is present, replace with new parts.
NOTE: Clean all of the internals in an approved cleaning
solution.

14 Maintenance
HP-210
Exploded View:
C – Hard Carbon Bearing Models
Exploded View:
BB - Ball Bearing Models
Exploded View:
TC - Tungsten Carbide Sleeve Models
Shaft AssemblyThreaded Plug Seal
Housing
TC Journal Rotor Pickup Coil
Coil Locknut
Shaft AssemblyThreaded Plug Seal
Housing
Rotor Pickup Coil
Coil Locknut
Shaft AssemblyThreaded Plug Seal Ball Bearing Ball Bearing
Housing
Rotor Pickup Coil
Coil Locknut
Table of contents
Other Hoffer Flow Controls Measuring Instrument manuals
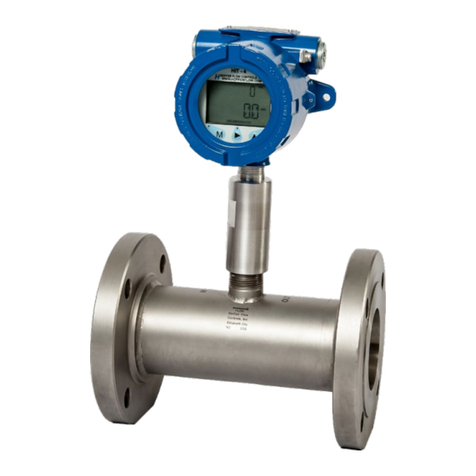
Hoffer Flow Controls
Hoffer Flow Controls HIT-4L User manual
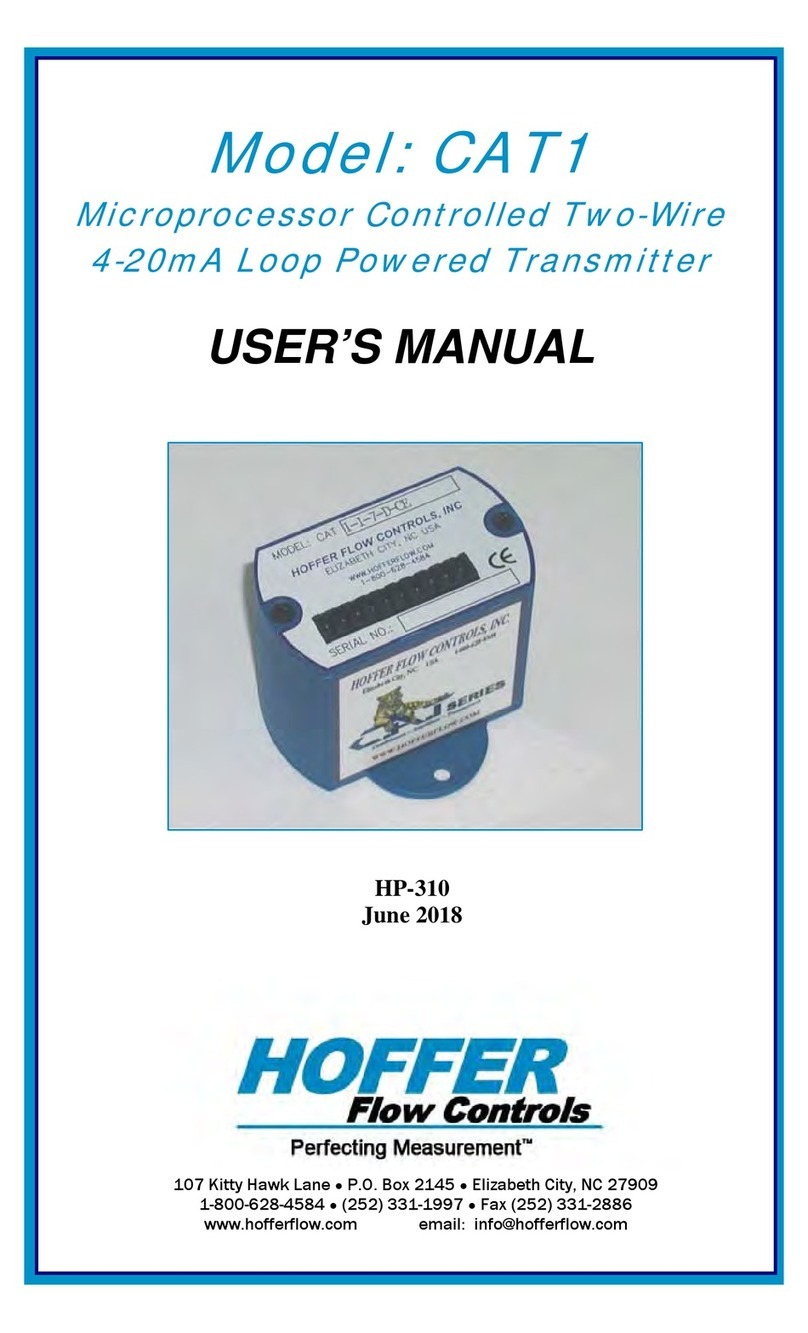
Hoffer Flow Controls
Hoffer Flow Controls CAT1 Series User manual

Hoffer Flow Controls
Hoffer Flow Controls HIT-4U User manual
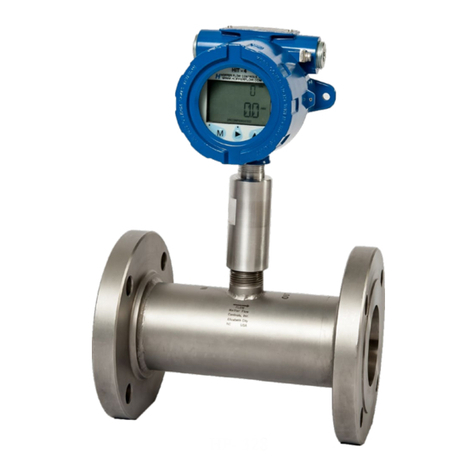
Hoffer Flow Controls
Hoffer Flow Controls HIT-4G User manual

Hoffer Flow Controls
Hoffer Flow Controls HIT-2A User manual
Popular Measuring Instrument manuals by other brands
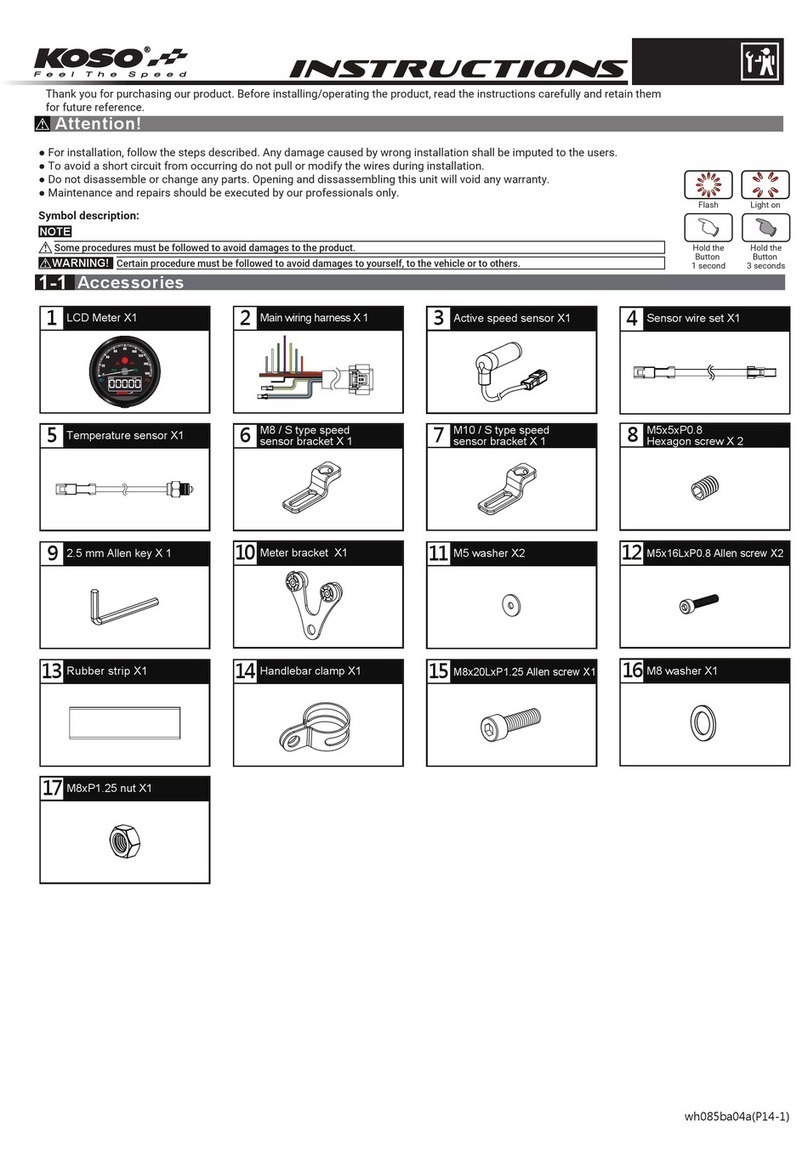
Koso
Koso TNT-05S D60 instructions
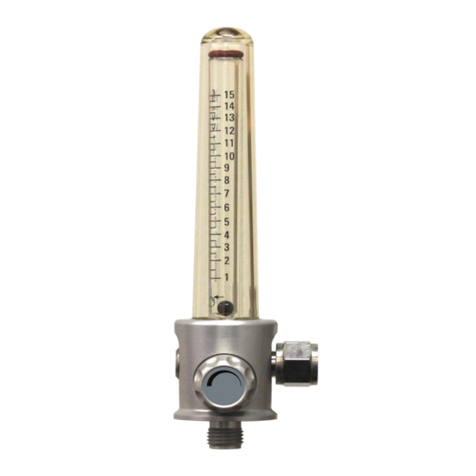
DEHAS
DEHAS D-B-FL-3 operating instructions

Aquaread
Aquaread Aquaprobe AP-800 instruction manual

LOVATO ELECTRIC
LOVATO ELECTRIC DMED302 instruction manual
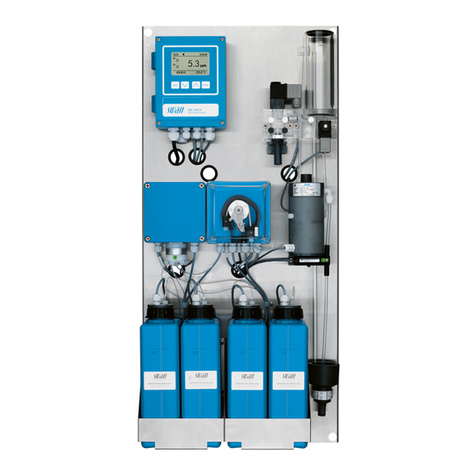
Swan Analytical Instruments
Swan Analytical Instruments AMI Silica Operator's manual

Hanna Instruments
Hanna Instruments HI5321 instruction manual