Hog Technologies Stripe Hog SK2000 User manual

SE Slater Street Stuart, FL 34997 1-877-HOG-ROAD (001) (772) 223-7393
WWW. STRIPEHOGSUPPORT.COM
SK2000 Stripe Hog
Integrated Model Operation Manual

2

3
TABLE OF CONTENTS
WELCOME ......................................................................................................................... 7
Hog Technologies LIMITED WARRANTY .................................................................................. 8
CAUTION & WARNING LABELS ............................................................................................. 9
Section 1:
Safety Information
1.1 General Safety............................................................................................................11
1.2 Blasting Safety ...........................................................................................................12
1.3 Nozzle Safety .............................................................................................................14
1.4 Hose Safety ...............................................................................................................14
1.5 High Pressure Fitting Safety..........................................................................................15
1.6 Dumping Safety..........................................................................................................15
Section 2:
Stripe Hog Systems
2.1 Stripe Hog System Introduction ....................................................................................17
2.2 Skid Mounted Auxiliary Engine......................................................................................18
2.3 Ultra-High Pressure Water System.................................................................................19
2.4 Hog Arm and Hog Heads..............................................................................................30
2.5 Hog Head...................................................................................................................34
2.6 Thru-shaft, Spray Bars, Protectors And Nozzles..............................................................36
2.7 High Pressure Hoses, Connections & Fittings...................................................................43
2.8 Debris Recovery System .............................................................................................45
2.9 Remote Blasting Tool Connection...................................................................................53
2.10 Electrical System ......................................................................................................54
2.11 Hydraulic System & Truck PTO.....................................................................................59
2.12 Hydrostatic Drive Wheel.............................................................................................61
Section 3:
Water Blasting Operation
3.1 Start Up/Shutdown Introduction....................................................................................63
3.2 Pre-Start Inspection ....................................................................................................63
3.3 Filling The Clean Water Tank.........................................................................................64
3.4 Water Blasting System Startup .....................................................................................66
3.5 Setting Blasting Pressure & Verifying UHP System Operation.............................................69
3.6 Auxiliary Engine Throttle Control Modes .........................................................................70
3.7 Water Blasting Operations............................................................................................71
3.8 Dumping Debris..........................................................................................................74
3.9 Routine Shutdown ......................................................................................................75
3.10 Emergency Shutdown Procedure .................................................................................76
3.11 Operation & Shutdown In Freezing Conditions...............................................................77
3.12 Operation Routine Maintenance ...................................................................................79

4
Section 4:
Lubrication & General Maintenance
4.1 Lubrication & General Maintenance Introduction..............................................................81
4.2 Lubrication & Grease Point Locations..............................................................................82
4.3 Stando Adjustment Procedure.....................................................................................84
4.4 Clean Water Filter Replacement.....................................................................................86
4.5 Bleeding Air From Charge Water Pump...........................................................................88
4.6 Wear Boot Assembly Replacement.................................................................................89
4.7 Dirt Shield Replacement...............................................................................................90
4.8 Nozzle Installation ......................................................................................................91
4.9 Rupture Disc Replacement ...........................................................................................93
4.10 Swivel Seal Replacement ...........................................................................................94
4.11 Vacuum Separator Filter.............................................................................................96
Section 5:
Scheduled Maintenance
5.1 Scheduled Maintenance Introduction..............................................................................97
5.2 Periodic Maintenance Items ..........................................................................................97
5.3 Auxiliary Engine & Reduction Gear.................................................................................99
5.4 High Pressure Hose Installation ..................................................................................100
5.5 Ultra High Pressure Pump Scheduled Maintenance.........................................................101
5.6 Checking UHP Pump Oil Level & Changing Crankcase Oil.................................................103
5.7 High Pressure Pump UNI-VALVE Service................................................................... 106
5.8 High Pressure Pump Stung Box Packing Replacement .................................................110
5.9 Ultra High Pressure Pump Assembly ............................................................................113
5.10 Dump Valve Assembly..............................................................................................114
5.11 Vacuum Blower Scheduled Maintenance .....................................................................115
5.12 Checking & Changing Blower Gear Case Oil.................................................................116
5.13 Vacuum Hose Replacement & Rotation Procedure........................................................118
5.14 Shroud Installation..................................................................................................119
5.15 Hydraulic System Scheduled Maintenance...................................................................121
5.16 Changing Hydraulic Fluid & Flushing Tank ...................................................................121
5.17 Replacing Hydraulic Filter .........................................................................................122
5.18 Winterization & Storage Procedures ...........................................................................123
5.19 Thru-Shaft Motor Bearing Pre-Load............................................................................127
5.20 SK2000 Maintenance Matrix......................................................................................141
Appendix 1:
Troubleshooting
Water Blasting System Troubleshooting ..............................................................................143
Appendix 2:
Tools & Spare Parts
Mobile Tool Systems.........................................................................................................147
Mobile Spare Parts System................................................................................................148
TABLE OF CONTENTS

5
TABLE OF CONTENTS
Appendix 3:
Daily Report & Pre-Op Checklist
Daily Report....................................................................................................................149
Pre-Op Checklist..............................................................................................................150
Appendix 4:
Nozzle & Spray Bar Conguration
Nozzle Conguration Chart................................................................................................151
Spray BAR Conguration Charts ........................................................................................152
Nozzle Calculation Sheet ..................................................................................................157
Appendix 5:
Glossary of Terms
Water Blasting Terms .......................................................................................................159
Appendix 6:
Customer Support & Support Web Site
Customer Support ...........................................................................................................163

6
NOTES

7
WELCOME
Congratulations on your recent purchase of the Stripe Hog! The Stripe Hog is the world’s most ad-
vanced equipment for removing pavement markings and runway rubber deposits. Your purchase
demonstrates your commitment to excellence and positions you as a world leader in the removal of
road surface markings and/or airport runway rubber deposits.
Hog Technologies is excited to welcome you and your crew to the Stripe Hog Operators’ Team. Together
we embrace the challenge of constantly developing our equipment, knowledge and skills so that our
highways will be safer for all who rely on them and our pavement surfaces will last longer for those
who pay for them. The Stripe Hog, in the hands of a trained/certied/licensed operator with this work
ethic, will be a tting complement to our mutual commitment to excellence.
As you know, no machine is capable of outperforming its operator so we have designed a training
experience that will equip your operators with the tools needed to maximize productivity and mini-
mize operational expenses while building our mutual reputation of no surface damage. This manual
is designed to be used by operators trained by Hog Technologies. During the training experience your
team will be given the basic knowledge and skills necessary to maintain, operate, troubleshoot and
repair your Stripe Hog.
Please take the time to read this operation manual before attempting to operate your water blasting
system. This manual is an important aid in the operation and maintenance of your new equipment.
The information is intended as a guide and cannot cover every question you may have about your
Stripe Hog or every operating situation. We encourage you to contact Hog Technologies for any ad-
ditional information you might need. We provide support to our customers for all of the equipment
we sell. We maintain an experienced support team that is available 24 hours a day 7 days a week
along with a well-stocked inventory of parts and accessories for your convenience. Please contact us
for any and all of your support issues and questions toll free at (877) 223-7393 or online at www.
hogtechnologies.com or www.stripehogsupport.com
From our family to yours we would like to take a moment to say thank you from all of us at Hog Tech-
nologies! We look forward to many successful years working together to provide maximum productivity
at minimal operational cost without damage. Only together can we both succeed!

8
WARRANTY
Hog Technologies Limited Warranty
Hog Technologies warrants its components to be free from defects in material and workmanship while
under normal use and service. Hog Technologies will, at its option, either repair or replace free of
charge any such part that appears to us to be defective in material or workmanship during the warranty
period. The warranty evaluation by Hog Technologies as to the cause of the defect shall be conclusive.
For approved warranty shipments, Hog Technologies will provide no charge Fed-ex ground or Fed-Ex
Economy shipping. If customer requests expedited shipping, the dierence in the shipping costs will
be invoiced to the customer.
Hog Technologies reserves the right to request the component(s) to be returned, freight pre-paid, for
analysis before proceeding with any warranty claim. The customer shall be responsible for payment
of any replacement components requested. If the warranty claim is approved by Hog Technologies,
credit will be issued for the components under warranty.
No warranty is made, either expressed or implied, for defects, failures or malfunctions resulting from
corrosion, misapplication, over-pressurization, insucient or lack of maintenance and any modica-
tions to the component as supplied by Hog Technologies.
Any components replaced during the period of warranty will be warranted only during the period of
the initial warranty, and no extensions shall be made, unless in writing by Hog Technologies in addi-
tion to the provision of the terms of the original warranty.
Hog Technologies will not be liable for damage, abnormal wear or consequential damage to their sys-
tem components resulting from the use of replacement components that are not furnished by Hog
Technologies.
Hog Technologies will not be liable for charges incidental to the removal of damaged or defective com-
ponents, lost time and prots, or any consequential damages resulting from failure of the component.
Hog Technologies reserves the right to make improvements to future models without the need to retrot
or upgrade prior models. Hog Technologies shall not be obligated to perform retrots and/or modi-
cations to components manufactured prior to the incorporation of the new design and specications.
Components that are not originally manufactured by Hog Technologies, including but not limited to,
the truck chassis, Jetstream Pump, OMSI (Gear Box), Dresser Roots Blower, are warranted only to
the extent of the original manufacturer’s warranty and are subject to their allowance to us if found
defective by them. Copies of other manufacturers warranty statements are supplied at the time of
sale. Hog Technologies will assist with warranty claims on components not originally manufactured
by Hog Technologies.
*For approved warranty claims that include labor: If such labor is provided at customer location and
not at Hog Technologies headquarters, Hog Technologies reserves the right to invoice customer for
reimbursement of travel-related expenses.
Hog Technologies Warranty Schedule
Warranty starts from the date of acceptance by the purchaser. Date of acceptance shall
be dened as the time that the Stripe Hog is received by the purchaser. Acceptance of
the Stripe Hog shall imply agreement to the terms and conditions of this warranty.
• 1 - 365 Days: 100% Parts and 100% Labor *

9
IMPORTANT NOTE:
Every precaution has been taken by Hog Technologies to reduce the risks associated with possible injury
and damage from electrical faults, high pressure water and hydraulic components or mechanical failure.
However, your own precaution and good maintenance procedures are necessary in order to maintain
a safe working environment.
All instructions given in this book are as seen from the rear looking forward. Common industry ter-
minology is used throughout the manual.
NOTICE:
INDICATES A SITUATION WHICH CAN CAUSE DAMAGE
TO THE MACHINE, PERSONAL PROPERTY, AND/OR THE
ENVIRONMENT OR CAUSE THE EQUIPMENT TO OPERATE
IMPROPERLY.
CAUTION
HAZARDS OR UNSAFE PRACTICES WHICH COULD RESULT
INMINOR PERSONALINJURYOR PRODUCTAND PROPERTY
DAMAGE.
WARNING
HAZARDS OR UNSAFE PRACTICES WHICH COULD RESULT
IN SEVERE PERSONAL INJURY OR DEATH.
DANGER
INDICATES A HAZARDOUS SITUATION WHICH, IF NOT
AVOIDED, WILL RESULT IN DEATH OR SERIOUS INJURY.
CAUTION & WARNING LABELS
High pressure, water blasting equipment can cause serious injury or even death if it is not operated
or maintained properly. This manual has been written to include a number of safety instructions to
assure the safe operation and maintenance of the equipment. These instructions are in the form of a
General Safety Section as well as individual NOTICE, CAUTION, WARNING and DANGER statements.
There are also WARNING AND DANGER LABELS located on some components. You should read these
warnings carefully and make sure you understand the nature of the hazard as well as the precau-
tions and recommended procedures required to ensure your safety. The following denitions apply:

10
Caution & Warning Labels
WARNING
INCORRECT USE OF HIGH PRESSURE WATER BLASTING EQUIPMENT MAY CAUSE
SERIOUS INJURY OR EVEN DEATH.
DO NOT USE THIS EQUIPMENT WITHOUT PROPER SUPERVISIONAND TRAINING.
ALL OPERATING AND MAINTENANCE PERSONNEL MUST BE THOROUGHLY
TRAINED IN SAFE OPERATION, INSTALLATION AND MAINTENANCE OF THIS
EQUIPMENT AND PROVIDED WITH ADEQUATE SUPERVISION.
BEFORE ATTEMPTING TO CONNECT, OPERATE, OR REPAIR THIS EQUIPMENT,
THOROUGHLY READ THESE INSTRUCTIONS AND ANY SAFETY WARNING OR
INSTRUCTION PAMPHLETS INCLUDED WITH YOUR SHIPMENT.
FOR ANY QUESTIONS CONCERNING SAFE OPERATIONS AND MAINTENANCE
PROCEDURES, CONTACT YOUR HOG TECHNOLOGIES REPRESENTATIVE PRIOR
TO USE.
(772) 223-7393 OR (877) 964-7312
HOG TECHNOLOGIES
WWW.HOGTECHNOLOGIES.COM

11
Section 1:
Safety Information
1.1 General Safety
Use Professional Training
Operating high pressure water blasting equipment
requires professional training, including safe work
practices and procedures. Only professionally
trained personnel should be allowed to setup,
operate, or maintain high pressure water blast-
ing equipment. If you have not completed the
Hog Technologies basic training course you will
be a danger to yourself and others. The velocity
of water at the nozzle tip exceeds that of a bullet
coming out of a gun. Contact with the high pres-
sure blast can result in the loss of a limb or water
injection into the bloodstream. If injection occurs
in a vulnerable part of the body death may result.
Always Read Instructions
Read this manual and all other water blasting
equipment operation manuals and instructions
prior to using any Hog Technologies product. Con-
tact Hog Technologies (877-HOG ROAD) should
any questions arise.
Major Component Operation Manuals
The suppliers of some major components such
as truck chassis, tractors, engines, pumps, and
drive units, provide their own operation manuals
which have been included with your equipment.
You should read the information in this manual
and the manuals of other manufacturers com-
pletely and have a thorough understanding of all
component systems and their proper operation
before operating your equipment.
REMEMBER - IT IS YOUR RESPONSIBILITY
TO ENSURE THAT YOUR EQUIPMENT IS SAFE
FOR YOU AND YOUR CREW. ALWAYS EXER-
CISE GOOD JUDGMENT WHEN INSTALLING
OR REPAIRING EQUIPMENT AND WHILE
OPERATING WATER BLASTING EQUIPMENT.
Work Area Safety
Remember, safety is rst! Only set up to work in
areas properly protected from trac and other
hazards. Individuals being struck by vehicles or
mobile equipment lead to many work zone fatali-
ties or injuries. Work zones need trac controls
identied by signs, cones, barrels and barriers.
You should always wear high visibility clothing
with a uorescent background and made of retro-
-reective material to be more visible to motorists
and reduce the possibility of an accident. Work
stations should always be illuminated.
Outt all operators with proper safety apparel.
Always use eye protection to shield from projected
debris. Use ear protection to protect from noise
levels generated from pump, vacuum and water
blasting heads. It is very important to wear steel
toed boots that provide good traction on slippery
surfaces such as on top of water and debris tanks.
Never wear loose clothing. Loose clothing can get
caught on moving or rotating parts causing serious
injury or even death.
Most ultra-high pressure water blasting opera-
tions generate noise levels above 90 dB. Hearing
protection is required in accordance with OSHA
standards.
OSHA’s Permissible Noise Exposure
90 dB 8.0 hours
92 dB 6.0 hours
95 dB 4.0 hours
97 dB 3.0 hours
100 dB 2.0 hours
102 dB 1.5 hours
105 dB 1.0 hours
110 dB 30 minutes
115 dB 15 minutes
WARNING
ALL PERSONNEL EXPOSED TO 90 DB OR GREATER NOISE
LEVELS SHOULD RECEIVE INSTRUCTION IN THE CORRECT
USE OFEAR PROTECTION SOTHAT THEIRNOISE EXPOSURE
LIES WITHINTHE LIMITSSPECIFIED BYOSHA. NEVERALLOW
ANYONE NEAR THE WORK AREA WITHOUT PROPER EAR
PROTECTION.
REMEMBER: ULTRA-HIGH PRESSUREBLASTING CANCAUSE
DEBRIS TO BEPROJECTEDUNEXPECTEDLY INANDAROUND
THE WORKAREA THAT CAN CAUSE SEVERE INJURY. MAKE
SUREALLPERSONNELSTAYCLEAROFTHE BLASTINGAREA
AND USE HARD HATS, EYE AND EAR PROTECTION.

12
Safety Information
Always be sure your work area is clear of people
whenever the ultra-high pressure pump is en-
gaged. When working on the water blasting head
with an operator in the cab of the truck you should
always make sure you can see his hands.
Use Only Products Intended for High
Pressure water blasting Use
Know the pressure ratings of all equipment be-
ing used and never exceed the service rating of
the weakest component. This system is designed
to work with pressures up to but not exceed-
ing 40,000 psi (2758 bar). Ultra-High Pressure
replacement parts must have a stated minimum
burst rating of 1.5 times the maximum operat-
ing pressure. All equipment pressure rating and
warning tags should be left intact.
Product changes
Hog Technologies is committed to the continuous
improvement of our products. As a result, some
of the equipment described in this manual or
pictured in the catalog may change or no longer
be available.
All information, illustrations, and specications
contained in this manual are based on the lat-
est product information available at the time of
publication. Hog Technologies reserves the right
to make changes at any time, without notice, in
colors, materials, equipment, specications, and
models.
If you have questions about the equipment on
your Stripe Hog, please contact the Customer
support Department at (877) HOG ROAD or (001)
772-223-7393.
Never Alter a Hog Technologies Product
Do not alter any product without written consent
from the manufacturer. Any alterations could have
serious consequences including bodily harm or
death. Alterations without manufacturer consent
will void the warranty.
Inspect Equipment
Inspect the condition of all components prior to
use. Do not use any item that is in questionable
condition. Use only components which are marked
with the recommended operating pressure. Never
exceed the operating pressure of the weakest
component in the system.
IMPORTANT NOTE:
YOUR WATERBLASTING EQUIPMENT USES INTERNAL
COMBUSTION ENGINES AND FLAMMABLE FUEL. EVERY
PRECAUTION HAS BEEN TAKEN BY HOG TECHNOLOGIES
TO REDUCE THE RISKS ASSOCIATED WITH POSSIBLE
INJURY AND DAMAGE FROM FIRE OR EXPLOSION, BUT
YOUR OWN PRECAUTION AND GOOD MAINTENANCE
PROCEDURES ARE NECESSARY TO ENSURE THE SAFE
OPERATION OF YOUR EQUIPMENT.
Store Components Properly
Protect all components from damage when not in
use. Secure for travel.
Freezing Conditions
The water and vacuum systems, hoses and the
water blasting head should be drained of all wa-
ter or lled with an antifreeze solution. For the
40K pump system, refer to pump manufacturer’s
procedures for maintaining equipment in freez-
ing climates. If the unit is operated in freezing
temperatures or even temperatures below 60
degrees Fahrenheit, it is necessary to operate the
system with the high pressure pump engaged and
the engine set at IDLE speed only, until the oil
temperature rises above 60 degrees Fahrenheit.
1.2 Blasting Safety
Safety First – ALWAYS!
Whenever the high pressure pump is engaged for
setting pressure or operations, always be sure
work area is clear of people, hands, feet, etc.
before engaging the high pressure (DUMP VALVE
40K) switch.
WARNING
INJURIES FROM ULTRA-HIGH PRESSURE WATER BLASTING
ARE VERY SERIOUS AND CAN RESULT IN A FATALITY.
ALWAYS MAKE SURE ALL PERSONNEL ARE A SAFE
DISTANCEFROM THE WORKAREA BEFORETHE PRESSURE
PUMPIS ENGAGED. NEVER PUTHANDS, FEETOR ANYPART
OF YOUR BODYIN OR NEAR THE HIGH PRESSURE STREAM.
Check Water Supply
Use only clean water in any Ultra-High Pressure
system. DO NOT accept water drawn from reten-
tion ponds, canals or other non-potable sources.

13
Safety Information
Purge System
Before attaching a spray bar to the Hog Head as-
sembly, engage the high pressure pump at low
speed to purge the system. Any dirt or debris
in the system can clog nozzle orices and cause
system pressure to spike excessively, causing
damage to components.
Check Water Blasting Heads
Check blasting heads for smooth and proper
operation before each shift. Do not use equipment
that has not been checked thoroughly.
Check Control Components
Check all switches and control panel devices to
ensure each is working properly before beginning
operations. Do not use equipment if any device is
malfunctioning.
Use Safety Protection
Always use eye protection to protect eyes from
projected debris. Use ear protection to protect
from noise levels generated from pump, vacuum
and water blasting operations.
WARNING
ULTRA-HIGH PRESSURE BLASTING CAN CAUSE DEBRIS TO
BE PROJECTEDUNEXPECTEDLYINANDAROUND THEWORK
AREATHAT CAN CAUSE SEVERE INJURY. MAKE SURE ALL
PERSONNEL STAY WELL CLEAR OF THE BLASTING AREA
AND USE HARD HATS, EYE AND EAR PROTECTION.
Know Your Surroundings
Always be aware of, and pay attention to your
surroundings. – i.e. - truck, hoses, people, walls,
moving vehicles, live lanes of trac, etc.
Test System
With the spray bar and high cohesive nozzles
installed, operate the pump at low pressure to
check for nozzle accuracy and leaks in spray bars,
connections or nozzles. Should any repairs or ad-
justments be necessary, disengage the pump to
relieve all pressure before making any required
repairs or adjustments.
CAUTION
TOAVOID POSSIBLE INJURYAND DAMAGE TO EQUIPMENT,
USE ONLY THOROUGHLY TRAINED PERSONNEL TO
PERFORM MAINTENANCE OR REPAIRS. ALWAYS TESTALL
COMPONENTS AT LOW PRESSURE.
Start at Low Pressure
Always start blasting with the system at low
pressure (low RPM) and slowly increase RPM to
operating pressure. Engage and disengage 40K
switch two times at operating pressure to check
the operation of the blasting head and dump valve
before starting blasting operations.
Set System Pressure
With system operating properly, set your pressure
according to methods described by pump manu-
facturer’s instructions. Refer to the Pump oper-
ating manual for specications and instructions.
Check Dumping Pressure
When setting pressure ALWAYS ensure that the
system pressure drops to less than 100 psi (7 bar)
immediately when the DUMP VALVE 40K STOP
switch is pressed. If this does not relieve system
pressure immediately to below 100 psi (7 bar)
when released, do not use the unit until repairs
are made to the dump valve.
Use the Minimum Pressure Required
Do not exceed the operating pressure of the sys-
tem’s lowest pressure-rated component. All equip-
ment pressure rating and warning tags should be
left intact.
Be Prepared
If the equipment malfunctions or a malfunction is
suspected, immediately stop all blasting activity
and relieve the pressure in the system before at-
tempting any repair. Always follow manufacturer’s
repair instructions.
Never Blast When Stopped
Always make sure Ultra-High Pressure is dis-
engaged before forward or reverse motion is
stopped. Damage to road surface will occur if
blasting continues when the truck is brought to
a stop.

14
Safety Information
WARNING
MOST HIGH PRESSURE WATER BLASTING OPERATIONS
PRODUCE NOISE LEVELS THAT EXCEED 90 DB WHICH CAN
CAUSE PERMANENT HEARING LOSS.
ALL OPERATORS AND SUPPORT PERSONNEL MUST WEAR
EAR PROTECTIONINACCORDANCE WITHOSHASTANDARDS
AND PROVISIONS SHOULD BE MADE FOR REGULAR
INSPECTION AND MAINTENANCE.
REMEMBER: ULTRA-HIGH PRESSUREBLASTING CANCAUSE
DEBRIS TO BEPROJECTED UNEXPECTEDLY INANDAROUND
THE WORKAREA THAT CAN CAUSE SEVERE INJURY. MAKE
SUREALLPERSONNEL STAYWELLCLEAR OF THEBLASTING
AREAAND USE HARD HATS, EYE AND EAR PROTECTION.
1.3 Nozzle Safety
Check Flow Rating
Combined nozzle ow rate must be compatible
with the pump discharge and pressure rating.
Refer to the nozzle ow chart in this manual.
Check Pressure Rating
Use only nozzles with a manufacturer’s pressure
rating of at least the pump’s operating pressure
or a burst rating of no less than 60,000 psi (4,137
Bar.)
Check Orices
Prior to installation, make sure the nozzles have
no clogged orices. Also, check to ensure nozzles
are sharp and not excessively worn.
Check Connections
Be sure to never force a nozzle into the blasting
head. Clean threads to ensure nozzle is not cross-
threading. Use an ample amount of anti-seize
on threads only, never on the seat of the nozzle.
Inspect the seat area on nozzle to ensure a tight
seal. If it is damaged, do not use.
Clogged Nozzles
If a nozzle appears clogged, immediately disen-
gage pump. Remove any clogged nozzles and
replace with new nozzles. Any particles of the
smallest size will clog nozzles. Clogged nozzles
can create excessive pressure in pump.
Remove Nozzle from Service if:
A) Nozzle is split or damaged.
B) Nozzle is clogged.
C) Nozzle water spray is fanned out.
D) Nozzle’s ability to hold pressure is suspect.
E) Nozzle’s hex head is worn excessively from
blasting.
F) Nozzle threads are damaged.
1.4 Hose Safety
General
Ultra-High Pressure hoses are tough, but not in-
vincible. They require proper care and handling
to achieve the normal service life of 300 - 600
hours. If the hoses are abused, the service life
will be much shorter.
Stretched or abused hose can fail prematurely
and unexpectedly, which could cause injury to
personnel. Hoses that have been exposed to
excessive stretching or kinks should be removed
from service and discarded.
Check Connections
Check the condition of the connection threads
prior to connecting any ttings or hoses. Use an
anti-seize compound on all ttings and hoses
to prevent “galling,” as galling will destroy the
threads, ttings and/or hose ends.
Tighten Connections
Properly tighten all high pressure connections.
Usually, snug plus a 15% tightening will properly
seal connections.
Take Proper Care of Your Hose
A) Protect the hose from contact with sharp
objects, abrasive surfaces and foot or wheel
trac.
B) Never subject Ultra-High Pressure hose to a
tight radius (less than 30” (.8 m) or pull on a
coiled hose. Always make sure the hoses are
straight with no coils before pulling on the hose
to deploy it.

15
Safety Information
C) Never pull hard on an Ultra-High Pressure hose
or expose the hose to heavy loads like drag-
ging equipment or deploying long lengths of
hose. This can stretch the hose and weaken
it. Never pull more than 25 feet of hose by a
coupler or tting. Always move long lengths
of hose by the hose itself to keep the strain
o the ttings.
D) When using a tractor or a hog tool, always op-
erate the equipment well within the maximum
distance to avoid straining or damaging hoses.
Check Burst Rating
Do not use an Ultra-High Pressure hose that does
not have a listed burst rating or with a burst rating
of less than 60,000 PSI (4,137 Bar).
Retire Hose from Service if:
A) Cover is damaged and reinforcing wires are
exposed to rust and corrosion.
B) Cover is loose and/or has blisters or bulges.
C) Hose has been crushed or kinked.
D) End tting shows evidence of damage, slippage
or leakage.
E) Hose has been exposed to pressures of 2 times
the operating pressure.
F) Hose has been stressed or stretched.
Check Dump Valve Water Hose
Any hose used for returning dumped water back
to the pump or vacuum line must have a large
enough diameter and psi strength so that poten-
tially dangerous release pressure is allowed full
ow and release pressure is contained safely. Keep
hose in good condition.
1.5 High Pressure Fitting Safety
Fitting Ratings
Use high pressure ttings with a rating of 60,000
psi (4137 Bar.)
Check Fittings
Do not use ttings that have been cross threaded
or have damaged threads.
Fitting Connections
Use anti-seize compound on all hose and tting
connections to prevent galling. Do NOT apply
anti-seize to the seating area of any connections.
1.6 Dumping Safety
A) Always drain all the liquid from the debris
tank before dumping the solids.
B) Always dump on level ground, never uneven
or sloped ground.
C) Always choose solid ground, not soft sand or
wet soil.
D) Always use the remote control to tilt the
tank.
E) Make sure the operator and all personnel are
well clear of the truck before tilting the tank.
F) Never allow personnel under a raised tank
without safety supports in place.
G) Always be careful to avoid any pinch points
which could cause injury.

16
Safety Information
DANGER
AN INJURY CAUSED BY HIGH PRESSURE WATERJETS CAN BE SERIOUS. YOU
SHOULD READ THIS WARNING STATEMENT CAREFULLYANDALWAYS CARY THE
MEDICAL INFORMATION CARD WITH YOU.
• IN THE EVENT OF ANY WATERJET INJURY:
• SEEK MEDICAL ATTENTION IMMEDIATELY. DO NOT DELAY.
• INFORM THE DOCTOR OF THE CAUSE OF THE INJURY.
• SHOW THE DOCTOR THE MEDICAL INFORMATION CARD OR THIS WARNING
STATEMENT AND NOTE TO PHYSICIAN BELOW.
• TELL THE PHYSICIAN WHAT TYPE OF WATERJET PROJECT WAS BEING
PERFORMEDAT THE TIME OF THEACCIDENTAND THE SOURCE OF THE WATER.
MEDICAL ALERT
NOTE TO PHYSICIAN
This patient may be suering from a waterjet injury. Evaluation and
management should parallel that of a gunshot injury. The external mani-
festations of the injury cannot be used to predict the extent of internal
damage. Initial management should include stabilization and a thorough
neurovascular examination. X-rays can be used to asses subcutaneous
air and foreign distant from the site of the injury. Injuries to extremities
can involve extensive nerve, muscle, vessel damage as well as cause a
distal compartment syndrome. Injuries to the torso can involve internal
organ damage. Surgical consultation should be obtained. Aggressive
irrigation and debridement is recommended. Surgical decompression
and exploration may also be necessary. Angiographic studies are recom-
mended preoperatively if arterial injury is suspected. Bandages with a
hygroscopic solution (mgso4 ) and hyperbaric oxygen treatment have been
used as adjunctive therapy to decrease pain, edema and subcutaneous
emphysema. Unusual infections with uncommon organisms in immuno-
competent patients have been seen; the source of the water is important
in deciding on initial, empiric antibiotic treatment, and broad-spectrum
intravenous antibiotics should be administered. Cultures should be ob-
tained.

17
2.1 Stripe Hog System Introduction
The SK2000 water blasting system is mounted
to the truck chassis and powered by an onboard
diesel engine and a hydraulic pump mounted to
the power take-o on the truck transmission. The
water blasting system includes an Ultra-High Pres-
sure water system, vacuum system, water tank
with an integrated wastewater bladder, hydraulic
system, hydrostatic drive system and a DC elec-
trical system for the auxiliary engine and water
blasting system that is totally isolated from the
truck electrical system.
Most components are controlled by switches in a
cab mounted control panel. Dumping and other
operations are controlled by a removable remote
switch panel connected to a plug on the chassis.
The SK2000 also supports the connection of
the optional HT1000 Ground Hog when the job
requires the extended reach and/or additional
maneuverability.
The operation and maintenance requirements for
the truck engine, drive train and chassis compo-
nents are unique to the manufacturer and the
selected options. Each truck chassis manufacturer
provides owners information manuals with their
product. It is important that you read the manu-
als carefully and become familiar with the proper
care and operation of engine, drive system, chas-
sis, safety equipment and all components of your
truck chassis.
The operation and maintenance requirements
for the skid mounted engine are unique to the
manufacturer. Each major component of the power
unit provides an owners information manual with
their product. It is important that you read the
manuals carefully and become familiar with the
proper care and operation of the engine and re-
lated components.
Section 2:
Stripe Hog Systems
SK2000 Mounted On An Isuzu Truck Chassis

1818
Stripe Hog Systems
Typical Skid Auxiliary Engine
2.2 Skid Mounted Auxiliary Engine
The Ultra-High Pressure pump is powered by the
onboard auxiliary diesel engine. The vacuum sys-
tem, charge water pump and all other hydrauli-
cally powered systems are powered by a hydraulic
pump connected to the power take-o on the
truck transmission. An electronic engine control
panel provides complete control of the engine
and monitors critical engine functions from the
cab. It also provides warnings and/or automatic
shutdown to prevent costly engine repairs in the
event a critical engine function fails.
A skid mounted tank provides fuel for the auxiliary
engine. The fuel system is completely isolated
from the truck fuel system. A digital gauge in the
engine control panel monitors fuel ow to the
engine and total gallons consumed. Some tanks
are also equipped with a fuel level gauge in the
top of the tank. The fuel tank should lled at the
start of each shift.
The auxiliary engine DC electrical system is
equipped with an onboard battery, circuit protec-
tion and charging system. It is totally isolated
from the truck DC electrical system. Refer to the
Electrical System section for additional informa-
tion on the auxiliary engine and water blasting
electrical system.
The Ultra-High Pressure (UHP) pump is directly
driven by the auxiliary engine. The pump is
mounted to a reduction gear case that reduces the
output shaft RPM to between 500-600 RPM, which
is the operating range for the pump. A exible
coupler between the engine and pump reduces
vibration and reduces the possibility of engine
damage from a catastrophic pump failure. The
gear case is equipped with a site glass to monitor
oil level level. Refer to the Scheduled Maintenance
section for addition information on the reduction
gear case.
The engine should be started only when the Stripe
Hog is on the job site and ready to go to work.
Always check the uid levels and all systems be-
fore starting the engine. Typical Auxiliary Engine Control Panel

1919
Stripe Hog Systems
2.3 Ultra-High Pressure Water System
Each manufacturer of the high pressure water
blasting system components provides an informa-
tion and operating manual with its product. It is
extremely important that you read the manuals
and become familiar with the proper care and
operation of the components before operating the
water blasting system.
WARNING
HIGH PRESSURE WATER FROM SPRAY JETS OR RUPTURED
HOSES CAN CAUSE SEVERE INJURY OR EVEN DEATH.
ALWAYS BE SURE WORK AREA IS CLEAR OF PEOPLE,
HANDS, FEET, ETC., BEFORE ENGAGING THE 40K CLUTCH
SWITCHTOACTIVATE THEULTRA-HIGHPRESSURE SYSTEM.
Clean Water Tank
The forward tank on the truck chassis provides
storage for the clean water supply. The tank is a
modular design constructed of polyethylene ma-
terial to provide a constant supply of clean, fresh
water to the charge water pump. A site tube pro-
vides a quick view of the water level from outside
the truck during lling operations.
An expandable bladder inside the freshwater tank
provides a reservoir for wastewater pumped to
the bladder from the debris cage drain system
during operation. As the clean water in the tank
is consumed, wastewater from the debris drain
system is pumped into the bladder which expands
into the space created in the tank as the clean
water is consumed. Refer to the Debris cage and
Debris bag at the end of this section for additional
information on the wastewater drain system.
The clean water ll connection on the passenger
side of the tank accommodates large hoses that
are typically connected to a metered source like
a re hydrant to expedite the lling of the tank.
Operators must always monitor the tank closely
during lling operations as the ow of water from
Typical Clean Water Tank Conguration & Valves
CLEAN
WATER TANK
DRAIN VALVE
CLEAN
WATER TANK
FILL VALVE
CLEAN
WATER TANK
SITE TUBE

2020
Stripe Hog Systems
a hydrant may be greater than the ow capacity
of tank air vent. Overlling the tank will cause
excessive pressure and damage the tank.
Only use potable water (clean enough to drink)
to increase the service life of the components in
the Ultra-High Pressure system. Always ush the
water source for several minutes prior to lling
the tank to help ensure that no debris enters the
system. Additionally, the tank should be ushed
frequently with clean, fresh water to prevent the
accumulation of debris that may accidently enter
the tank.
There is a 4” ball valve on the passenger side bot-
tom of the tank that allows for quick draining of
the tank when ushing is required and complete
draining for system winterization. Another 4”
valve on the driver side provides drainage for the
wastewater bladder. A large man-way hatch on
the top of the tank provides access to the interior
of the tank or wastewater bladder for inspection
or to facilitate cleaning.
Remember that the wastewater bladder displaces
clean water in the tank as it lls, causing the site
gauge to show more water than is actually in the
tank. The site gauge is intended to provide an ac-
curate indication of the water level during lling
Wastewater Bladder Drain Valve
operations only. It is not a reliable level indicator
during operation when the transfer pump is being
used to collect recovered wastewater.
Use actual blasting time during operation with
an average pump consumption of 5 gallons per
minute to estimate the remaining clean water in
the tank. To ensure maximum clean water volume,
always completely drain the wastewater bladder
before lling the clean water tank.
Man-Way Hatch On Clean Water Tank
Table of contents
Other Hog Technologies Utility Vehicle manuals
Popular Utility Vehicle manuals by other brands

Club Car
Club Car IQ PLUS 2008 Maintenance and service manual supplement
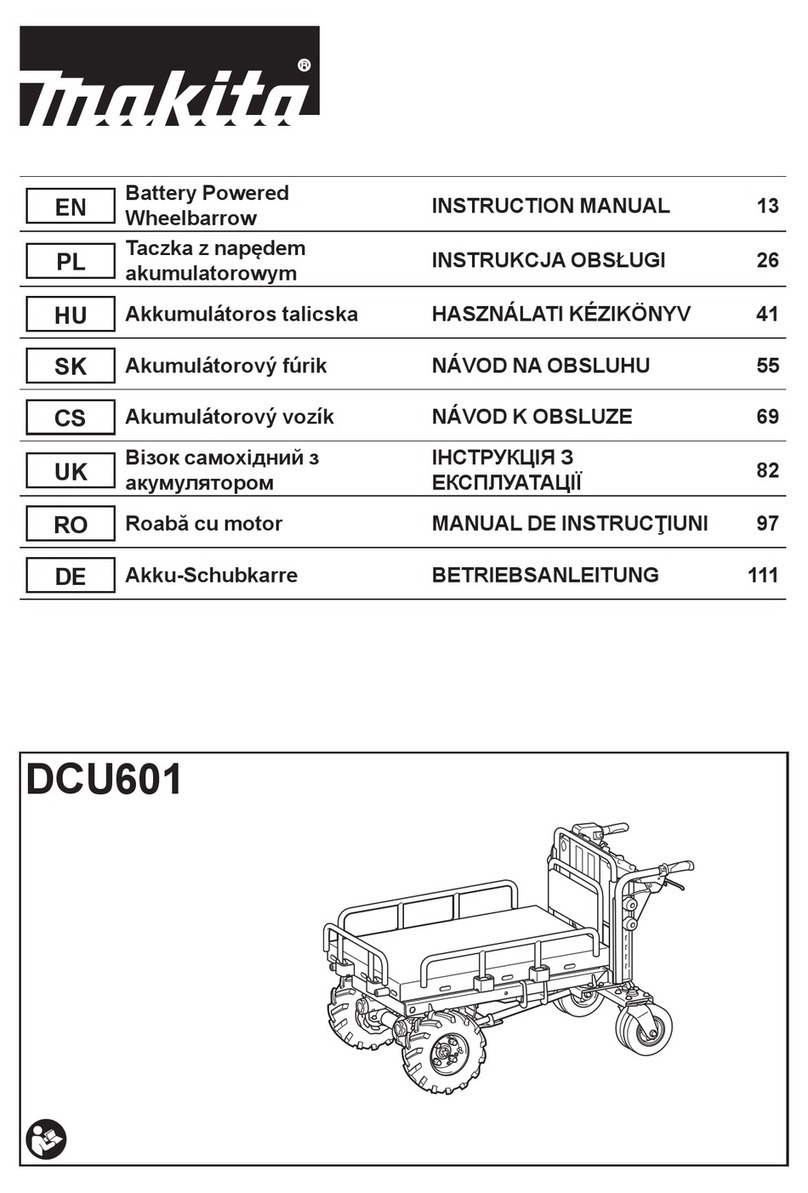
Makita
Makita DCU601 instruction manual
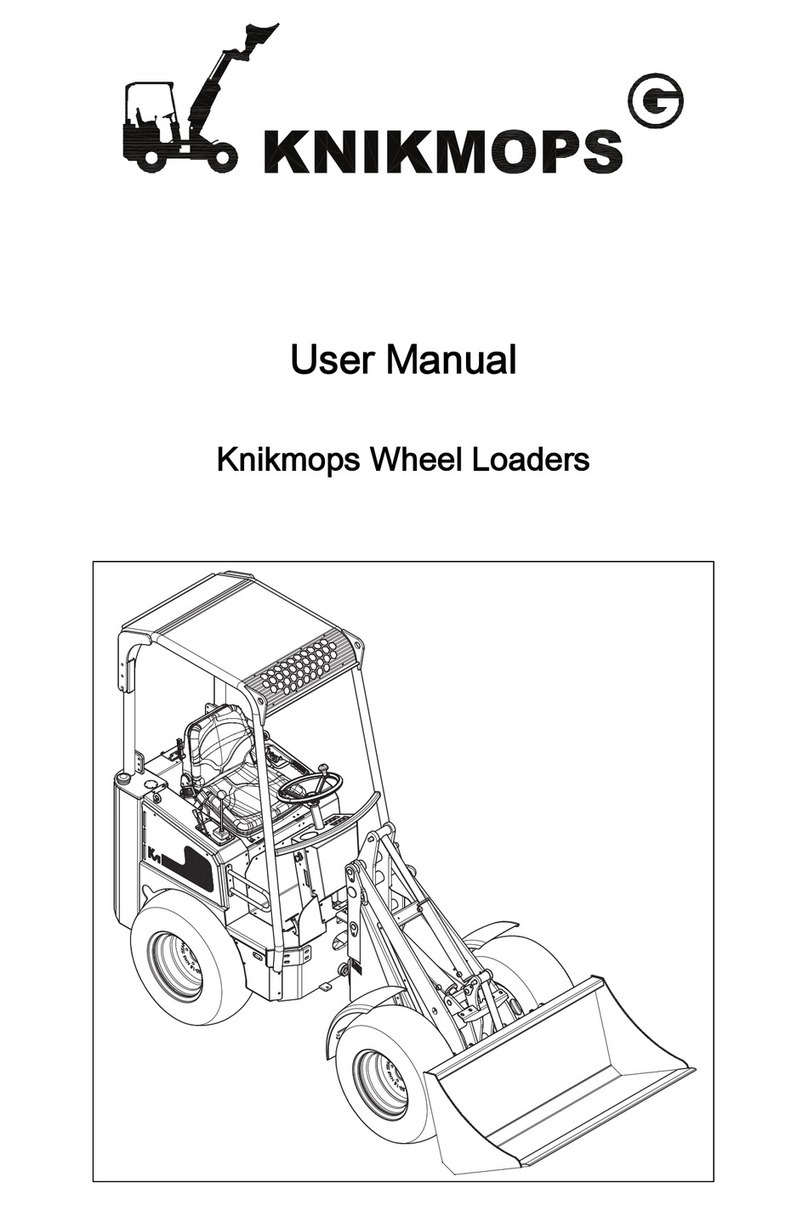
intrepid
intrepid KM100 user manual
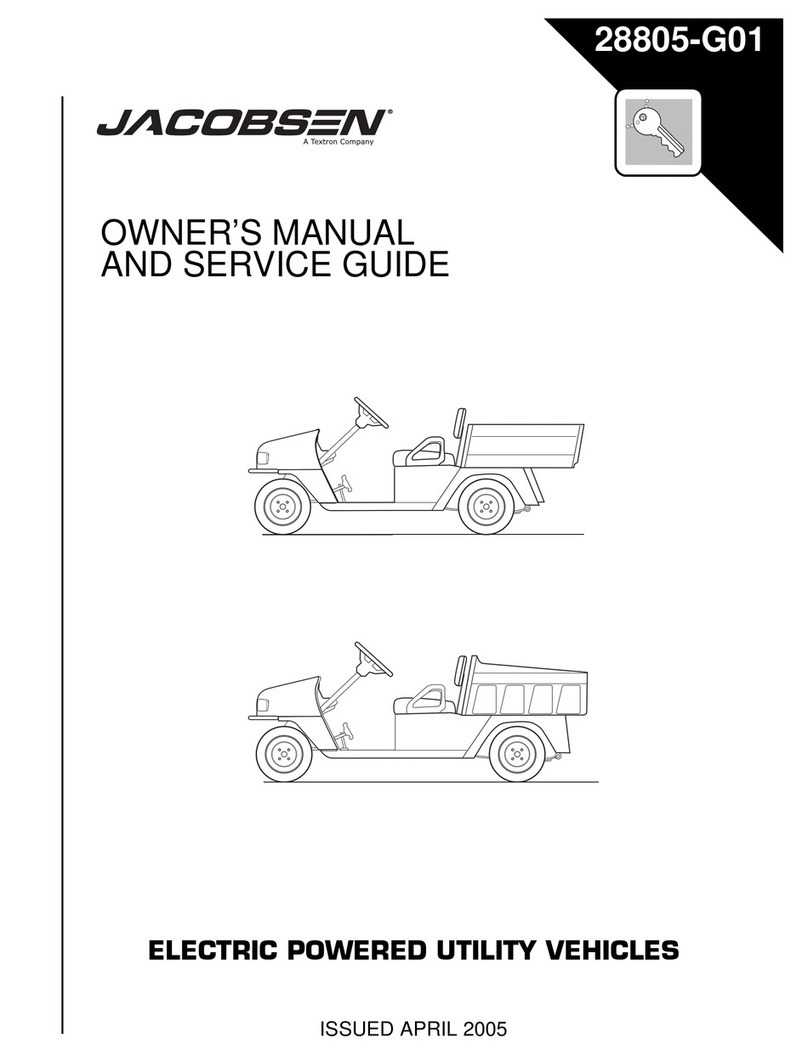
Jacobsen
Jacobsen Hauler 800 Owner's manual and service guide
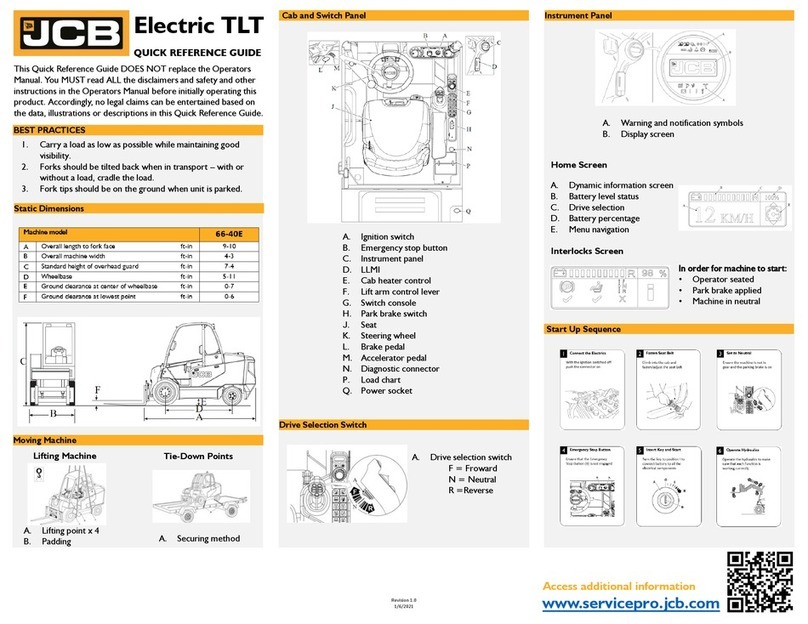
jcb
jcb 66-40E Quick reference guide

American Landmaster
American Landmaster LandStar LS670 Owner manual and safety manual