Horton Easy Access 7500 Series User manual

To be used in conjunction with H-SW C4190 Setup Instructions
G705, OCT 2000
7.079d
Installation Instructions
Overhead Concealed & Direct Drive
Swing Door Operator
with C4190 Control
Series 7500 Easy Access™

CONTENTS
1. Instructions to installer................................................................. G705.1
2. General requirements.................................................................. G705.1
3. Handicap code requirements.......................................................G705.1
4. Operator handing.........................................................................G705.1
5. Installing frame.............................................................................G705.2
6. Installing bottom pivot.................................................................. G705.2
7. Installing door with overhead concealed arm for 7500 / 7800..... G705.3
8. Installing door with direct drive arm .............................................G705.3
9. Door panel prep 7600 / 7800 for wood or metal doors.................G705.4
10. Door panel adjustments...............................................................G705.4
11. Installing activation switches........................................................G705.5
12. Operator adjustments ..................................................................G705.5
13. Changing operator hand and / or closing spring..........................G705.6
Changing operator hand cont. .....................................................G705.7
14. Placement of safety decals..........................................................G705.8
7.094d1

Switch location may be selected by the owner,however the switch must be in view of the door and not on the door or frame.
See ANSI 117 for accessibility requirements.
RH
32" Clear min.
(813)
Confirm handing of door before installing operator. Refer to section 15 for instructions if changing hand of operator is
required.
EXTERIOR
4. OPERATOR HANDING
Refer to section 16 for required
decals.
ALTERNATE
LOCATION
LH
NOTE:
LHR
Bottom horizontal rail must be at
least 7 1/2"(190) on aluminum / glass
doors. (Local codes may require more)
Beveled threshold with a maximum
height of 1/2"(6)
The maneuvering room can be
eliminated if actuating switch is
placed in accessible location out
of the swing of the door.
EXTERIOR
7.075d
RHR
Minimum of 5'(1524) x 5'(1524)
clear and level floor is required on both
sides of the door way.
Located 36" (914) to 42" (1067)
from floor.
Minimum 24" (610) opening
clearance from door jamb at
opening side to any structure.
24" min.
(610)
•Power: 120 VAC, 60Hz, 15 Amp service (in conduit) to the header.
•Non North American voltages can be 240 VAC, if so be sure
the operator has a 240VAC power supply.
•Power may be brought in through the top of the jamb on single
swing units or at the center of the header on pairs.
•For remote switch locations, routing of low voltage class II
wiring (in conduit) to the operator controls will be required.
•Remote switch locations should be predetermined and wired
before installation begins.
•Opening size should be 1/4" (6) taller and 1/2" (13) wider than the unit / frame.
•The opening must be plumb and square. The threshold and swing area must be
level.
G705.1
INFORMATION TO BE PROVIDED BY THE DISTRIBUTOR TO THE OWNER
•This door is to be installed by a trained and experienced installer with knowledge of local codes and ANSI A156.19
standards for power operated doors.
•To ensure safe and proper operation, the door must be installed and adjusted to conform to Horton Automatics
recommendations, all code requirements and ANSI A156.19.
•If there are any questions about these instructions, call Horton Automatics Technical Assistance.
•After installation instruct the owner on the safe operation of the door.
•Present the Owners Manual M310 and explain how to perform the daily safety check.
•Location of power cut off switch.
•Necessary warnings not covered in these general instructions.
•Date equipment shipped from Horton Automatics.
•Date equipment placed in service.
•Horton Automatics' invoice number for warranty reference.
•Equipment type.
•Accessories included.
•Phone number to call regarding problems or request for service.
•Give caution to owner: if a potentially hazardous situation is suspected, the door should be taken out of automatic
service until a professional inspection is made and the problem is corrected.
2. GENERAL REQUIREMENTS
3. HANDICAP CODE REQUIREMENTS
1. INSTRUCTIONS TO INSTALLER
PAIR
SINGLE
Recommended power
input location
L
CPivot
L
CPivot
CPivot
L
Recommended power
input location

Remove the face plate and place the header and jambs on the floor to
assemble. Note: place on a protective surface to avoid damage to the
finish. The operator may be removed, if necessary, to provide ease in
installation.
Backup plate
FASTENER
SIZE / TYPE
All the pivots shown below are secured to the floor with FHSMS and plastic anchors. For bottom prep of doors by others
see section 9.
THRESHOLD PIVOT
PIVOTS FOR OVER HEAD CONCEALED UNITS
FASTENER CHART
#10 SMS&
#10-24 MS
#14 SMS &
#1/4-20 MS
#6 SMS &
#6-32 MS
NON THRESHOLD PIVOT
Use pivot to mark hole
locations on floor.
3 3/4"
(95) 3 3/4"
(95)
6. INSTALLING BOTTOM PIVOT
End bracket
THRESHOLD PIVOT
PIVOT FOR DIRECT DRIVE UNITS
3 3/4"
(95)
For non threshold condition omit bottom plate.
Mount pivot to floor with 1/4-20 x 1 1/2" FHSMS
& anchors.
7.076d
#7 (.149)
#36 (.106)
TAP
DRILL
#25 (.149)
3/16 (.187)
#F (.257) &
#14 csk
#7 (.201) &
#10 csk #21 (.159)
#31 (.120)
SHEET METAL
DRILL HOLE
CLEAR
DRILL / CSK
#25 (.149) &
#6 csk
Drill 5/16" (.312) & use
C1424 blue anchor
1/4-20
#10-24 Drill 1/4" (.25) & use
C1423 green anchor
MASONRY
#6-32
TAP
SIZE
1st Step
Level, plumb & shim.
Shim bottom of jambs to
be level with the highest
point.
Take care the frame is not racked. Wood shingles will be needed to shim the unit. All fasteners shown below are provided
with each unit. If these are inappropriate, alternate fasteners are shown in the fastener chart.
G705.2
If backup plates are not
preinstalled,Secure as
shown with #10 screws.
Assemble header to jambs as shown
OPTIONAL 6"X 6" HEADER
7/8" access holes for
power supply & low
voltage wiring.
2nd Step
End cap
5. INSTALLING FRAME
Attach header to jamb
brackets with #10 machine
screws.
4th Step
Attach jamb brackets
to jambs. 2 per side.
3rd Step
6th Step
Tilt unit up
into place.
5th Step
NOTE:
Be sure face plate is
on the correct side
for hand of unit.
7th Step
Drill and countersink 3/16"(5mm)
dia. holes and secure jambs with
#14 x 3" FHSMS. Secure header
with #14 HHSMS.
8th Step
Secure finger guard
on the pivot side.

Bottom pivot
bearing
For 7600 / 7800 series (doors by others) see section 9 for door prep.
8. INSTALLING DOOR WITH DIRECT DRIVE ARM
Position power arm
onto output shaft (90°
to the opening).
Tighten 1/4" SCS to
10 FP (13.5N)
NOTE: To remove the panel
for pivot adjustment use a flat
screwdriver to release the
spring catch.
Place the door panel
on the bottom pivot.
Adjustable, non threshold,
pivot assembly.
2nd Step
2nd Step
Apply Loc Tite
242 to threads
Tilt top of panel & place
under the power arm.
Swing the panel bottom
up & over the bottom
floor pivot.
7000 operator header.
(shown as dashed line)
Adjustment
screw.
Secure the power arm to
the panel.
Adjust the door position
as required.
Adjustment
slots
3rd Step
7.077d
4th Step
Height
adjustment
BOTTOM DOOR CLEARANCE
Energize operator, shaft will rotate to
full open position.
Maintain operator in this position until
door panel installation is complete.
1st Step
5/16"
(8) 5/16"
(8)
1/2"
Max
G705.3
Output shaft
7. INSTALLING DOOR WITH OVERHEAD CONCEALED ARM FOR 7500 / 7800 SERIES
Re-install the operator if it was removed during frame installation.
CAUTION: When installing the power arm or when servicing any swing door operator, be sure to keep your face, hands
and arms clear of the power arm's swing path. Serious injury could result should the operator be accidently
activated to an open position or should the operator return to a relaxed position.
Apply Loc Tite
242 to threads
Align the door in the
closed position. When
alignment is correct,
tighten bolts in pin
assembly.
4th Step
Align the top bearing
as shown and insert
the pivot pin. Do not
tighten bolts yet.
3rd Step
Pivot base
plate
Remove the 5/16" bolts
and pin assembly.
INSTALLING THE DOOR PANEL
1st Step Apply Loc Tite
242 to threads
1st Step
Manually open the
door to 90°
•Position the power arm so that one of
the 3 holes lines up with the hole in the
slide block.
•Slide the arm onto the output shaft.
(Tighten the 1/4" socket screw to
10 FP 13.5N)
•With the door at 90° insert drive pin.
(Tighten pin to 25FP 33.9N)
4th Step
Slide drive block
into track.
2nd Step
Drive
pin
Drive
block Track
INSTALLING THE POWER ARM
3rd Step
Energize operator, shaft will
rotate to full open position.
Pivot
pin

If the door is equiped with a fixed or emergency breakout stop,
it should be tested several times to be sure the stop flips
over and turnes off the operator when the door is put in the
breakout position.If it does not work properly, the door height
may need adjustment.
10. DOOR PANEL ADJUSTMENTS
1.If the drive block binds the arm must be adjusted parallel
to the track.
2.To adjust the door to 90° at full open. The drive pin may
be located at 3 different locations. Swing is decreased by
moving the pin closer to the operator shaft.
3.After adjustments are complete replace power arm cover
and face plate (be sure screws are replaced in face plate).
Manually open the door, it should swing smoothly without binding. If adjustment is required follow the outline below.
NOTE: The added weight of the glass can influence adjustments to the panel. Glazing at this point is advised.
After glazing adjust the glass leveling screw located in the top rail close to the strike rail. The door must not drag at any
point.
BREAKOUT STOP
90°
Output shaft
See Section 7
for illustrations
Emergency
stop
Drive
block
Track
Glass
leveling
screw
approx.
120°
Pivot
OVERHEAD CONCEALED
1.The panel can be adjusted by loosening the socket head
screws that secure the power arm and adjusting the screw
at the end of the arm (see section 8).
2.To adjust the bottom pivot the panel will have to be
removed.
•Place the operator in hold open position.
•Remove the socket head screws that secure the power arm.
•Use a small flat screwdriver to release the catch on the
back of the bottom pivot (See section 8).
•Loosen the pivot bolts to adjust the pivot in the slots.
Output shaft
& pivot
90°
See Section 8
for illustrations
Emergency
stop
Glass
leveling
screw
7.078d
Power arm
Adjustment
screw
DIRECT DRIVE
Apply Loc Tite
242 to threads
9. DOOR PANEL PREP (7600 & 7800) FOR WOOD OR METAL DOORS
G705.4
1 3/16" (30)
11/4"(32)
Web size
1"(25)deep x
11/4"(32)wide
5/8"(16)
45/8"
(117)
33/4"(95)
1"(25)
Pivot C
L
11/4"(32)
Web size
1"(25)deep x
11/4"(32)wide
Drill for #14 HHSMS
3-places
1/2"(13)
Drill for #10SMS
14places
11/4"(32)
43/4" (121)
OVERHEAD CONCEALED (7800)
1"
(25) 1"
(25)
1 1/4"
(32)
Pivot C
L
4" (102)
14" (356)
1"(25) 13" (330) Minimum
1 3/16"
(30) Drill for 5/16" for wood or
metal screws 3-places
C
L
Minimum web 1 7/16" (35)wide
x1"(25)deep
41/8" (105)
1 3/16"
(30)
1"(25)
web
33/4"(95)
3 3/4"(95)
2 3/4"(70)
without
finger guard 1 3/4"
(44)
Finger
guard Pivot
Drill for #14x1 1/2"
HHSMS 2-places
2 1/2"
(64)
2 1/2"
(64)
DIRECT DRIVE (7600)
3 3/4"
(95)

D3- Green
*JB3 Jumper:
Inserts a 0.25 second delay to
allow the lockto release before the
door starts to move.
C7115-1
Motor
C9156
Harness
Power Failure: manual pressure not to exceed 15 lbf (67N) at a
point one inch (25) from the latch edge (may vary by local code).
in Inches(mm) 100 (45.4) 125 (56.7) 150 (68.0) 175 (79.4) 200 (90.7)
The force required to prevent a door from opening or closing shall not
exceed 15 lbf (67N) applied one inch (25) from the latch edge at any
point of opening or closing.The kinetic energy of a door in motion shall
not exceed 1.25 lbf (5.56N). Note: To be in compliance with the force
and energy requirements set closing and opening speeds as per the
chart above.
3.5 Sec.
4.0
4.5
5.5
Closing Speed Adjustment:
rotate counterclockwise to increase.
suggested setting: 4 seconds min.
ANSI CHART - OPENING & CLOSING TIME IN SECONDS
DoorWeightinPounds (kg)
3.0 Sec.
3.5
4.0
4.5
30 (762)
36 (914)
42(1067)
48(1219)
3.0 Sec.
3.0
3.5
4.0
DoorLeaf Width
Output shaft
3.0 Sec.
4.0
4.5
5.0
3.0 Sec.
3.5
4.0
4.5
Open/Close Check
Microswitches
MotorLeads
JB1 Jumper:
(Push-n-Go) With jumperin place,
a slight pushon the door will actuate the
operator and open the door.
CLOSING TIME: Doorsshall be field
adjusted to close from 90 deg to10
deg in three seconds or longer.Doors
shallclose from 10deg to fully closed
in 1.5 sec. or more.
The door shall
remain fully
open forat
least 5 sec.
unlessa
sensing device
is used.
Total
opening
time to
full-open
shall be
four sec.
or more. 80 deg
OPENING TIME:
Doorsshall be field adjusted
sothat opening time toopen
check or80 deg shall be
three sec. or more.
90 deg
10 deg
7.065d2
To ground wire on
incoming line
JB2 Jumper:
Removeto disable touch stop
C3959-1
5 pin
Power
Supply
Lace
Power in:
120 VAC,15Amp.
F1, F2 & F3
Fuses:
Located to right
of transformer
CN1 CN2-
Power
Supply
CN2-
Switching
Circuit
D2- Red
D1- Green
S1
CN4
DELAY:
Time Delay
Adjustment -
Suggested setting
is 5 seconds
minimum after full
open. Rotate
clockwise to
increase.
11. INSTALLING ACTUATION SWITCHES
12. OPERATOR ADJUSTMENTS
Note: See Section 2
For switch location
requirements.
G705.5
Remove cover
plate and drill
1/4" hole for
wiring. Location
will vary with
job conditions.
Drill and mount
box with the four
#10 x1" screws
provided. C1319-1 Cover
CloseCheck Switch Cam:
Adjust for switchto fall onto cam flat
when door is 10 deg from full-closed.
The following information is provided as a
recommendation for safe operating
speed adjustments and should
be adhered to when installing
or servicing the series 7000
swing door operator.
See ANSI 156.19.
Pull the low voltage wire into the box.
Open Check Switch Cam:
Adjust for switchto fall onto
cam flat when door is 10 deg
from full-open.
2nd Step
L.OUT:
Lock Out Time Delay -
Sets the length oftime
neededtoignore the
safetysensor during
door closing. Rotate
clockwise to increase.
LIMIT: Current Limiting -
Sets the amountof opening force.
Rotate counter-clockwise to
increase.
OBST: Replacestime delay cancel
on old C7160-3 controls. Rotate
clockwise to increase.
Surface applied 4" x 4" x 1 1/2"
plastic junction box. Use same
size metal box for flush mount
(not supplied).
AUTOMATIC DOOR
C1316-2 SWITCH ASSEMBLY
3rd Step
1/4"
Hole
1st Step
HORTON
PRESS
BUTTON
Provide support for box
Access Holes to
Allen Screws
*JB3Jumper
lock enable
CHECK:
Open Check Speed
Adjustment - Sets the
speed after the open
check switch falls onto
thecam flat. Rotate
clockwise to increase.
SPEED:
Open Speed Adjustment -
Sets the open speed of the
operator.Rotate clockwise
to increase.
HOLD:
Hold Voltage
Function - Control
switches to hold-
open voltage after a
nominal 10-12
second delay from
beginning to actuate
signal. Also sets
speed for Stop&
Seek mode.
Rotate clockwise to
increase.
ACCEL:
Open
Acceleration
Adjustment -
Sets motor
acceleration to
open speed
setting. Rotate
clockwise to
increase.
D4- Orange
DACCL:
Open
Deceleration
Adjustment -
Determines how
quickly the door
slows after the
open check
switch is tripped.
Rotate clockwise
to increase.
Note: Junction box not
included in assembly.
C1260 SWITCH ASSEMBLY
Attach the
microswitch &
pushplate to the
junction box
using the four
Allen screws
provided.
2nd Step
PRESS
TO OPEN
61/4"diameter plate.
C1260-4 shown.
See catalog for optional
designs.
Pull the 24 VAC, 2 conductor
wire into the box and connect
to the microswitch terminals.
Do not connect to
high voltage.
1st Step

C4028
Spring
Retainer
Bracket
IF CHANGING SPRING DIRECTION FROM LH TO LHR
OR RH TO RHR ( INSWING TO OUTSWING ):
A. After spring is removed, turn upside-down and replace on
output shaft (after shaft has been rotated 1/4 turn). Be
careful to place inner spring hook in same slot in shaft as
before.
B. Re-install the rest of the assembly as outlined in steps B
thru D ( left ).
C. Reverse motor leads at potentiometer ( see Operator
Adjustments, Section #9 ).
IF CHANGING BOTH SPRING DIRECTION & OPERATOR
HAND (FROM LHR TO RHR OR RHR TO LHR) :
A. After changing spring direction, as outlined above, follow
steps on next page for changing operator hand.
B. After both tasks are done, reverse motor leads at
potentiometer ( see Operator Adjustments, Section #9 ).
4th Step
Remove the two
assembly bolts, spacers
& lower bearing plate.
Note: Before proceeding
to next step, be carefull to
note location of inner
spring hook in output
shaft, as well as, the
direction the spring is
wound.
IF SPRING WAS BROKEN:
A. Replace new spring on output shaft. Be careful to place
inner spring hook in same slot in shaft as before.
B. Re-install lower bearing plate with it's assembly bolts,
spacers and mounting screws.
C. Slide arm on output shaft and manually rotate until the
outer spring hooks clip into the spring retainer bracket.
Next rotate the shaft approximately 1/2 turn (180°) and
hold in that position.
D. Re-install chassis stop and secure with mounting
screws. Allow arm to slowly counter-rotate until the stop
lug on the output shaft rests against the chassis stop.
The spring is now preloaded for most general
applications.
7.091d2
C7132
Lower Bearing
Mounting Plate
C7078
1/4-20 x 4"FHMS
C7043-1 Spacer
1/2"O.D. x 2 1/2"
C7079
1/4-20 x 4 1/2"FHMS
5th Step
Slide an arm back
on the operator
shaft and manually
rotate until outer spring hooks release from
spring retainer bracket. Slide arm off and
remove spring.
ClosingSpring:
C7050 Type'D',
C7051Types 'E'.
1st Step
Slide an arm on the operator shaft and manually rotate arm
approximately 1/4 turn to relieve pressure on chasis stop.
Hold in that position.
13. CHANGING OPERATOR HAND AND/OR CLOSING SPRING
NOTE: IN ALL CASES, SECURE THE BASEPLATE OF THE GEAR TRAIN ASSEMBLY (PREFERABLY IN A VISE)
WITH THE OUTPUT SHAFT FACING UP.
The following information is provided as a guide for:
• Removing and replacing a broken spring.
• Changing spring direction.
• Changing both spring direction and operator hand.
• Changing operator hand but not spring direction.
2nd Step
Remove three chassis mounting screws
thus allowing spring to slowly unwind
and push out the chassis stop.
Remove both arm and
chassis stop.
3rd Step
Remove the two screws for lower
bearing mounting
plate.
C576
5/16-18 x 1/2"
FHMS
C7130-1
Upper Bearing
Mounting Plate
C7037
Chassis
Stop
REMOVING THE SPRING:
C576
1/4-20 x 3/4"
FHSCS
G705.6
Optional Step
To clear work space, detach C7083
Wire Guide & Operator Wiring
Harness from upper bearing plate
and move out of way.

Relocated
Chassis
Stop
4. REINSTALLING CHASSIS STOP:
A. Slide arm on output shaft and manually
rotate shaft until outer spring hook clips
into spring retainer bracket. Then rotate
1/2 turn (180°) and hold in that position.
B. Reinstall chassis stop in new location as
shown. Allow arm to slowly counter
rotate until the stop lug on the output
shaft rests against the chassis stop. The
spring is now pre-loaded for most
applications.
NOTE: AFTER SPRING IS PRE-LOADED IT WILL BE NECESSARY TO ADJUST OPEN
CHECK CAM AND CLOSE CHECK CAM WHEN OPERATOR IS INSTALLED.
Relocated Spring
Retainer Bracket
Check
Switches
Wire Guide
Relocated Face
Plate Clip
2. REMOVING GEAR TRAIN ASSEMBLY:
A. Remove closing speed potentiometer by removing
mounting screws.
B. Loosen two screws securing check switch mounting bracket
and slide bracket from slots.
C. Remove wire guide installed on front of gear train.
D. Remove seven bolts securing bearing plates of gear train to
chassis base plate. Set gear train aside.
3. REINSTALLING GEAR TRAIN AND CONTROLS:
A. Remove spring retainer bracket and relocate to opposite
end of chassis as shown.
B. Re-install gear train assembly at same end of chassis as
shown. Note that motor assembly is nearest center of
chassis.
C. Re-install control assembly as shown. Reconnect all plugs.
D. Re-install all previously removed brackets onto gear train.
Closing Speed
Potentiometer
7.092d2
Gear
Train
IF CHANGING OPERATOR HAND BUT NOT SPRING DIRECTION
( FROM LH TO RHR OR RH TO LHR ):
Follow the steps outlined in the previous page for removing the chassis
stop and allowing the spring to unwind. The gear train and controls will
then have to be moved to opposite sides of the operator base plate
chassis.
1. REMOVING C4160-2 CONTROLS ASSEMBLY:
A. Disconnect all plugs from controls assembly and remove
from chassis.
B. Remove controls from mounting plate, rotate 180° and
reinstall. Do Likewise with power supply assembly.
C. Remove face plate mounting clip below control.
Reassembled C4160-2
Controls / Power Supply Assembly
Power
Supply
Assy .
G705.7
Mounting
Plate
Controls

C1690-2
Daily safety check decal
should be adhered to
the interior side of the
door jamb in full view.
58"(1473)
± 5"(127)
THE DECALS SHOWN BELOW ARE AVAILABLE OPTIONS.
C1631-3
C7282 C7281
For Push-n-Go™ option
Interior elevation
7.093d1
G705.8
C
L
C1688
14. PLACEMENT OF SAFETY DECALS
Decals should be a minimum of 6"(152) diameter and be visible from both sides of the door. Apply decals as shown.
For one-way traffic non-approach side.
C7280
Required to meet ANSI
standards. This decal is
included with each
door package.
ACTIVATE SWITCH
HORTONAUTOMATICS
AUTOMATIC
DOOR
CAUTION
OR
PUSH TO OPERATE
ONE-WAY
AUTOMATIC DOOR
HORTON AUTOMATICS
DO NOT
ENTER
ACTIVATE SWITCH
HORTON AUTOMATICS
AUTOMATIC
DOOR
CAUTION
OR
PUSH TO OPERATE
ACTIVATE SWITCH
HORTON AUTOMATICS
AUTOMATIC
DOOR
CAUTION
OR
PULL TO OPERATE
ACTIVATE SWITCH
TO OPERATE
HORTON AUTOMATICS
AUTOMATIC
DOOR
CAUTION

Form G705, Oct 2000 printed in U.S.A.
Product equipment depicted in the various figure drawings are approximate and for illustration purposes only. Consult manufacturerfordetail
product specifications. Horton Automatics reserves the right to improve the product and change its specifications without notice.
A Division ofOverheadDoor Corporation
Horton Automatics, Ltd.
Unit A, Hortonwood 31
Telford, Shropshire
England TFI-4GS
Tel: 01952 670169
Fax: 01952 670181
International Numbers:
Tel: ++44 1952 670169
Fax: ++44 1952 670181
4242 Baldwin Boulevard
Corpus Christi, Texas 78405-3399
Tel: 361-888-5591
Fax: 361-888-6510
Toll Free in North America:
Tel: 1-800-531-3111
Fax: 1-800-531-3108
Internet: http://www.hortondoors.com
Table of contents
Other Horton DC Drive manuals
Popular DC Drive manuals by other brands

LED Lighting
LED Lighting EX-3 product manual

LinMot
LinMot E1100-CO Drive Data Sheet & Installation Guide
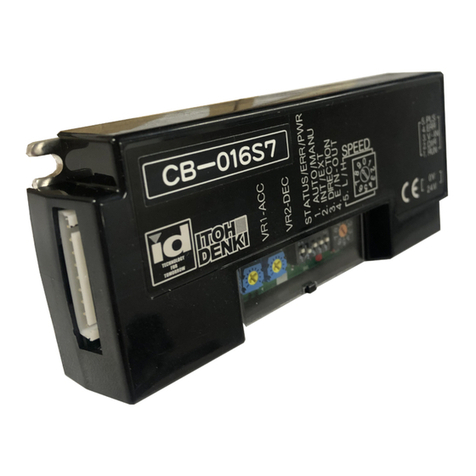
ITOH DENKI
ITOH DENKI CB-016BP7 user manual

Pentair
Pentair Pentek Intellidrive quick start guide
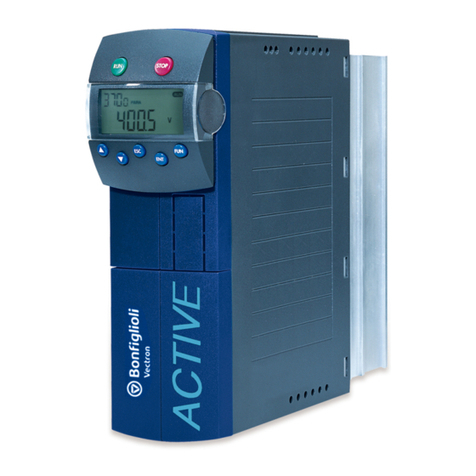
BONFIGLIOLI
BONFIGLIOLI ACTIVE ACT2 Series quick start guide
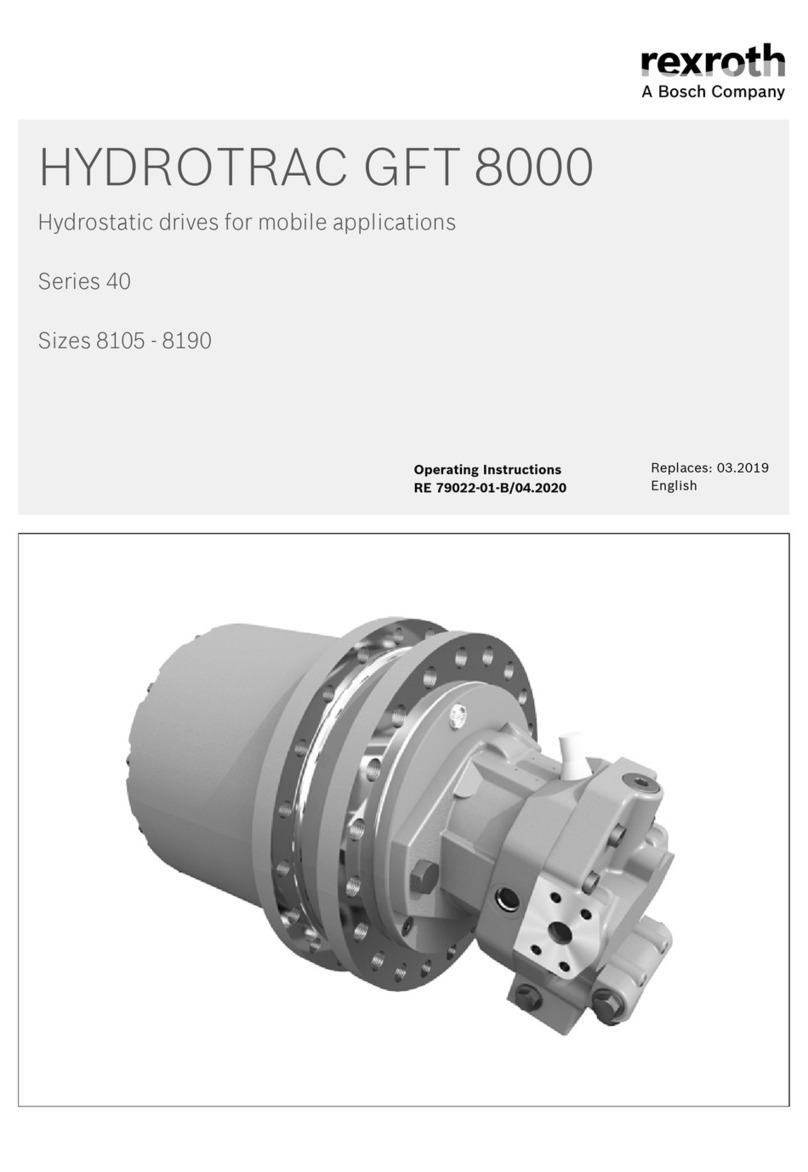
Bosch
Bosch REXROTH HYDROTRAC GFT 8000 operating instructions