Drivecon XT Series User manual

Owner's Manual
Drivecon Toll Free Ph: 1-800-374-8266
Drivecon reserves the right to alter or amend the above information without notice
Owner’s Manual
Drivecon XT Series
Owner’s Manual
820 Lakeside Drive - Gurnee, IL 60031
Phone: (847) 855-9150 Fax: (847) 855-9650
1-800-DRIVCON (374-8266)
www.drivecon.com Email: drive.sales@drivecon.com
Revision 5.4D Pro1V050
6-01-04

Owner's Manual
Drivecon Toll Free Ph: 1-800-374-8266
Drivecon reserves the right to alter or amend the above information without notice
Table of Contents
CHAPTER A - SAFETY
Forward A-1
Examination before installation and Purchase History A-2
Safety Precautions A-3
Understanding and selecting the correct part number A-7
CHAPTER B - TECHNICAL DATA
Introduction B-1
Technical Data B-2
CHAPTER C - INSTALLATION INSTRUCTIONS
Installation instructions C-1
Stripping length of motor and main cables C-2
Cooling C-3
Inverter Dimensions C-5
CHAPTER D - WIRING AND SIZING INFORMATION
Cable installation and the UL standards D-1
Cable and Motor insulation checks D-1
Cable and Fuse sizing D-2
Frame sizes and installation of cables D-3
Control unit D-7
I/O and Relay Boards D-8
Digital Input Connections D-13
XTD-4000 Series Open Loop Traverse Wiring Diagram D-14
XTD-4000 Series Closed Loop Traverse Wiring Diagram D-15
XTD-4000 Series Open Loop Load Brake Hoist Wiring Diagram D-16
XTD-4000 Series Closed Loop Hoist Wiring Diagram D-17
CHAPTER 1 - DESCRIPTION
Functional Discription 1
Control Methods 2-3
Mechanical Brake Control 4
Motor Control Modes 5
EMC 6
CHAPTER 2 – START-UP PROCEDURE
Checks 7
Test Run 8
CHAPTER 3 – PARAMETER ADJUSTMENTS
Control Keypad 9-10
Monitoring 11
Parameter Groups 12
CHAPTER 4 – COMPONENTS
Spare Parts List 13
Spare Parts List 14
Fault Codes 15-19
Fault Counter 20
CHAPTER 5 – SERVICE
Service 21

Owner's Manual
Drivecon Toll Free Ph: 1-800-374-8266
Drivecon reserves the right to alter or amend the above information without notice
CHAPTER A – SAFETY
Foreward
To fully employ all functions of the inverter, and to ensure the safety of users, please read through
this operating manual in detail. Should you have any further inquiry, contact your local distributor or
Drivecon at 1-800-374-8266 toll free or 847- 855-9150.
Precaution: Inverter is a power electronic device. For safety reason, please note paragraphs with
“WARNING” or “CAUTION” heading.
WARNING!: Personal injury may result with improper operation.
CAUTION!: The inverter or mechanical system may be damaged by improper operation.
WARNING!
• Do not touch the PCB or components on the PCB while power is on or immediately after
turning off the power. Wait for the charging indicator light to extinguish.
• Do not attempt to wire circuitry while power is on. Do not attempt to examine thecomponents
and signals on the PCB while the inverter is running or power is on.
• Do not disassemble or modify internal circuitry, wiring, or components of the inverter.
• The grounding terminal of the inverter must be grounded properly according to local codes
orNEC standards.
CAUTION!
• Do not attempt to conduct dielectric strength test to internal components of the inverter. There
are sensitive semiconductor devices vulnerable to high voltage in the inverter.
• Do not connect the output terminals T1(U), T2(V), T3(W) to AC line power.
• The CMOS IC on the primary PCB of the inverter is vulnerable to static discharge. Do not
touch the primary PCB of the inverter. If removal is required, follow recommended guidelines
for static discharge control.
CAUTION
1. Before starting, read carefully instructions.
2. Verify all connections are according to drawings.
3. Verify motor supply is connected correctly, wrong connection will destroy the inverter.
4. Check device cover is properly installed.
5. High voltages are present in this device. Switch power off and after display turns off, wait 5
minutes before opening the cover.
6. Insulation resistance test with a megger requires special precautions.
7. Do not make any measurements inside the device when it is connected to main supply.
8. Do not touch the components on the circuit boards. Static voltage discharge may destroy the
IC-circuits.
9. Check all ventilation holes are clear and uncovered.
10. Check that hot air coming from brake resistors does not cause any damage to surroundings.
11. Do not make any inspections unless the supply has been disconnected by main switch.
12. It is forbidden to use portable phones near this device with the doors open.
13. All the doors and covers must be closed when crane is in operation.
A-1

Owner's Manual
Drivecon Toll Free Ph: 1-800-374-8266
Drivecon reserves the right to alter or amend the above information without notice
Examination before installation and purchase history
Every Drivecon inverter has been fully tested and examined before shipment. Please carry out
the following examination procedure after unpacking your inverter.
• Verify that the inverter model number is the same as the one you ordered.
• Check to see if there is any damage that may have occured during transit. Do not connect
the inverter to the power supply if there is any sign of damage. Report to regional sales
representative or Drivecon if you find any abnormal conditions as mentioned above.
Caution!
Failure to inspect the inverter may lead to damage of the system and possible down time. Should
you find any reason to suspect the unit itself or any part of the system to be faulty please contact
Drivecon toll free at 800-374-8266 or 847-855-9150. Be prepared to provide model number of your
controller and any other pertinant information relative to the system.
Purchase history
Please take a moment and record the following information for future reference:
Model: _______________________
Serial number: _______________________
Date purchased: _______________________
Date installed: _______________________
Installed by: _______________________
Dealer: _______________________
WARRANTY
Seller warrants that all products manufactured by it to be free from defects in material and/or
workmanship under proper and normal use by the initial user for 24 months following the date of
shipment. Seller is the sole determinant of all claims under warranty, is not responsible, and will
not issue credit for defects and damage that arise from improper installation, neglect, improper
use, unauthorized repairs or alterations, or from normal wear and tear.
During the warranty period, Seller will repair or replace, FOB its plant, any parts reported and
found to be defective by its inspection. Seller will not assume any expenses or liability for any
work done on its equipment outside its plant without its written consent, and such unauthorized
work will automatically void Seller’s warranty.
Field labor and any related expenses are not covered under this warranty. A purchase order is
required for any and all field work.
This warranty is in lieu of all other warranties expressed or implied, including warranty of mer-
chantability of fitness for a particular use.
A-2

Owner's Manual
Drivecon Toll Free Ph: 1-800-374-8266
Drivecon reserves the right to alter or amend the above information without notice
Safety Precautions Precautions of operation Before turning ON power
CAUTION!
• Choose appropriate power source with correct voltage setting as the input
voltage specification of the inverter. Check line voltage phase to phase and
phase to ground for compliance.
WARNING!
• The input power source must be connected to main input power terminals L1, L2,
and L3.
• Special care must be taken while wiring the power circuit. The (L1, L2 and L3)
terminal must be connected to input power source and must not be connected to
T1, T2, or T3 output terminals by mistake. This will damage the inverter when the
power is turned on.
CAUTION!
• Do not attempt to transport the inverter by the front cover. Securely hold the inverter
by the chassis to prevent the inverter from falling.
• Install the inverter onto firm metal base or other nonflammable material. Do not
install the inverter near any flammable material to avoid fire.
• Additional ventilation fan should be installed if several inverters are installed into
one control panel to lower the temperature inside to below 50°C to avoid
overheating.
• Turn off the power supply before removal or installation of the operating panel.
Carry out installation procedure according to instructions given to avoid poor-
contact resulting in operating panel malfunction or display malfunction.
• The inverter can be easily operated over a wide speed range. Please confirm the
operating range of motor and machinery with respective manufacturers.
• Do not examine the signals on the PCB of the inverter while it is operating.
• All inverters have been adjusted properly at the factory. If adjustment is required
consult the manual and do not exceed normal operating values.
• Do not disassemble or examine the inverter before ensuring that the power is off
and the charge indicator has been extinguished.
• Insure that all safety devices on the machine are operating correctly such as: limit
switches, brakes, etc.
A-3

Owner's Manual
Drivecon Toll Free Ph: 1-800-374-8266
Drivecon reserves the right to alter or amend the above information without notice
When power is turned ON
WARNING!
• Do not attempt to install or remove the control panel connector to or from the
inverter when the power supply is turned on. Otherwise, the control panel may be
damaged due to surge peak caused by the insertion or removal.
Under Operation
WARNING!
• Do not switch the motor ON with a contactor connected to the inverter's output
while the inverter is operating, otherwise the inverter may be damaged.
• Do not remove the front cover of the inverter while the power is ON to avoid
personal injury caused by electrical shock.
• When the automatic restart function is enabled, the motor machinery will be
restarted automatically. Keep a safe distance to avoid personal injury. It is not
advisable to enable this function on any manually operated system.
• Do not use an input contactor to cycle inverter ON and OFF. Repeated cycling may
cause inverter damage.
CAUTION!
• Do not touch the heatsink base.
• The inverter can be easily operated from a low-speed to high-speed range. Please
confirm the operating range of the motor and the machinery you are controlling with
their respective manufacturers.
• Do not examine the signals of the PCB of the inverter when it is under operation.
• All inverters are properly adjusted and set by the factory prior to delivery. However,
every system may require minor adjustments to be complete at time of installation.
Do not exceed the specified limits of the equipment or inverter.
• Do not proceed with disassembly or examination procedure before ensuring that the
power is off and the Power LED extinguished.
• Dangerous voltages are stored within the inverter for up to 2 minutes after removal
of line power.
• Use caution when operating from the direct keypad mode as safety travel limits will
not function.
• Do not suspend or handle loads directly over people. Refer to ANSI B30.16 as to
safe crane operating procedures.
A-4

Owner's Manual
Drivecon Toll Free Ph: 1-800-374-8266
Drivecon reserves the right to alter or amend the above information without notice
During examination and maintenance
CAUTION!
• Inverter environment should be within the following specifications: 0°C - 50°C for
inverters located inside cabinet. -10°C - 40°C for inverters located outside cabinet.
Humidity should be under 95% RH non-condensing. Also, the surrounding
environment should be free from moisture or metal dust.
Typically the inverter requires no special maintenance. However we suggest
inspection of the inverter paying special attention to loose wiring connections.
Excessive accumulation of dust or dirt will also shorten the expected life of the
inverter. Periodic cleaning of the inverter with dry compressed air may be required.
WARNING!
• Insure power supply is switched OFF and the LED charge indicator has
extinguished prior to inspection or maintenance of inverter. Lock out all
equipment under repair or inspection.
A-5

Owner's Manual
Drivecon Toll Free Ph: 1-800-374-8266
Drivecon reserves the right to alter or amend the above information without notice
Operating Environment Considerations
• Avoid direct sunlight
• Keep away from corrosive gas or liquid
• Keep away from oil, grease, and petroleum products
• Avoid exposure to rain or dripping water
• Avoid metal dust and dusty environments
• Avoid areas of high vibration
• Avoid extreme heat
• Keep away from high electro-magnetic interference or ultra-high frequency
energy sources. (such as arc welders or other similar machinery)
• Keep away from radioactive materials or environments
• Keep away from flammable material
• Keep surrounding area between -10 ~ +40°C.
Installation sit conditions will directly influence the service life of the
inverter. Please provide a suitable location.
Indoor mounting: 0°C - 50°C Humidity should be under 95% RH non-condensing.
Outdoor mounting: -10°C - 40°C for inverters located outside cabinet. Humidity should be
under 95% RH non-condensing.
A-6

Owner's Manual
Drivecon Toll Free Ph: 1-800-374-8266
Drivecon reserves the right to alter or amend the above information without notice
Understanding and selecting the correct part number
In order to specify the correct part number to suit your needs please refer to the type code
shown below.
XT d 4 009 0 xx V
A-7

Owner's Manual
Drivecon Toll Free Ph: 1-800-374-8266
Drivecon reserves the right to alter or amend the above information without notice
Chapter B - TECHNICAL DATA
Introduction
Figure 2-1 represents the block diagram of the inverter. The inverter mechanically
consists of two units, the Power Unit and the Control Unit.
The three-phase AC line inductor (1) at the mains together with the DC bus capacitor (2)
form an LC-filter, which, together with the diode bridge (4) produce the DC-voltage supply
to the IGBT Inverter Bridge (3) block. The AC line inductor also functions as a filter
against High Frequency disturbances from the mains as well as against those caused by
the IGBT inverter to the mains. It improves the form factor of the DC bus input to the
IGBT inverter section. The entire power drawn by the inverter from the mains is active
power. The IGBT Inverter Bridge produces a symmetrical, 3-phase PWM AC-voltage to
the motor.
The Motor and Application Control Block is microprocessor based. The microprocessor
controls the motor based on the information it receives from internal sensors, parameter
settings, control I/O and control keypad. The motor and application control block controls
the motor control ASIC which, in turn, calculates the IGBT switching patterns. Gate driver
circuitry amplifies these signals for driving the IGBT inverter bridge.
Figure B-1
B-1

Owner's Manual
Drivecon Toll Free Ph: 1-800-374-8266
Drivecon reserves the right to alter or amend the above information without notice
GENERAL - Technical data
Power class 4004 4005 4009 4012 4016 4022 4031 4038 4045 4061 4072 4087 4105 4140 4168 4210
Horsepower 2 3 5 7.5 10 15 20 25 30 40 50 60 75 100 125 150
Output capacity (kVA) at
460V 4.3 4.3 7.2 9.6 12.7 17.5 24.7 30.3 35.9 48.6 57.4 69.3 83.7 111.5 133.9 170
Nominal continuous output
current In (A) 4 5.4 9 12 16 22 31 38 45 61 72 87 105 140 168 210
Max. current 1min (A) 10 10 15 20 27 36 48 63 72 90 113 135 165 225 270 315
Overloadability 1.5 x In , 1min/10min / 2.5 x In , 2s/20s (<50% speed)
Max. output voltage Equal to supply voltage
Supply
Supply voltage 380-500VAC
Allowable voltage
fluctuation +/- 10%
Nominal supply frequency 50/60Hz +/-5%
Signal input levels
Digital controls S1, S2, DIA3, DIA4, DIA5, DID1, DID2, DID3, DID4, DID5: 48 … 240VAC; 15mA
Analog references AIN1: +/- 10VDC, AIN2: 0-10VDC, 200 kOhm load.0.5% accuracy.
Encoder feedback EA+/-and EB+/-; 0/24V; 3k ohm load; floating differential inputs
Control features
Control method Open loop scalar, Open loop vector, Closed loop vector
Frequency control range 0-250Hz, 2 or 3 step infinitely variable, 2-5 preset speeds.
Frequency command Potentiometer, 0-10V analog signal
Limit switch functions Slowdown and stop limit inputs for both directions
Speed control range Open loop vector control. sN ... 100% (sN= motor nominal slip) Closed loop vector control. 0-100%.
Speed accuracy Open loop vector control. 1% of nominal speed at speed range 10- 100%. 1/3 of motor nominal slip at speed below 10%
Closed loop vector control. 0.01% of nominal speed.
Extended speed range Open loop vector control
Braking torque 1% of nominal speed at speed range 10 ... 100%
Protections
Stall prevention During acceleration and constant speed
Motor overload protection Thermistor based temperature measurement
Overload protection Fault is detected if the current momentarily exceeds 280% of rated current
Undervoltage / blown fuse Fault is detected if DC bus voltage drops below 65% of rectified supply voltage
Overvoltage protection Fault is detected if DC bus voltage exceeds 911V
Momentary power loss Immediate fault stop
Inverter overtemperature Temperature sensor on the heat sink
Mechanical brake control Control relay output. Control of braking chopper module and DB resistor.
Internal dynamic braking
transistor Electronic supervision for the braking chopper and for the braking resistor
Ground fault detection Provided by built in electronic circuitry
Overspeed / stall, speed
difference supervision Provided through SSU card and encoder feedback.
Ambient temperature 10°C ... +55°C (14°F ... 131°F) for ED?60%
Storage temperature 40°C ... +60°C (-31°F ... 140°F) dry
Humidity <95%RH (no condensation)
Altitude Maximum 3300 ft. at In. Above 3300 ft.: In reduces 1% per each 3300 ft. Above 9900 ft.: consult factory.
Vibration Operation: maximum displacement amplitude 0.12" at 2-9Hz.
Maximum acceleration amplitude 0.5g (16.5 f.t/sec.²) at 9-200Hz
Conforms to LV and EMC directives.
B-2

Owner's Manual
Drivecon Toll Free Ph: 1-800-374-8266
Drivecon reserves the right to alter or amend the above information without notice
Chapter C - INSTALLATION INSTRUCTIONS
1) Before installation, check that none of the components of the inverter is live.
2) If the inverter is installed outside a switchgear, enclosure or electrical room, it must
be equipped with a protective cover as provided by the regulations for IP21
protection class. For installations in a switchgear, enclosure or electrical room, the
cable protection plate is normally not necessary.
3) Route the motor cables clear of other cables:
• Avoid placing the motor cables in long parallel lines close to other cables
• If the motor cables run in parallel with other cables, note the minimum distances
between the motor cables and other cables given in table below.
• The given distances also apply between the motor cables and signal cables of other
systems.
• The maximum length of the motor cables is 990 ft. on all units.
• The motor cables should cross other cables at an angle of 90 degrees.
4) If cable insulation checks are needed, see Chapter D.
5) Connect the cables:
• Strip the motor and mains cables as shown in Table 3-2 and Figure 3-2.
• Remove the screws of the cable protection plate.
• Make holes into and pass the cables through the rubber grommets on the bottom of
the power unit.
• Connect the mains, motor and control cables into their respective terminals.
• For Information on cable installation according to UL regulations see Chapter D
• Make sure that the control cable wires do not come in contact with the electronic
components of the unit.
• If an external brake resistor is used, connect its cable to the appropriate terminal.
• Check the connection of the ground cable to the motor and the inverter terminals
marked with ground symbol.
• If shielded power cables are used, connect the separate shield of the power cable
to the ground terminals of the motor and enclosure ground terminal.
• Attach the cable protection plate with the screws.
• Ensure that none of the wiring is trapped between the frame and the protection
plate.
C-1

Owner's Manual
Drivecon Toll Free Ph: 1-800-374-8266
Drivecon, reserves the right to alter or amend the above information without notice
Stripping lengths of motor and main cables
Typical for shielded cables and conventional individual stranded conductors.
Figure C-2
Inverter
type XTd- Frame
size Cable striipping length - inches
or XTe A1 B1 C1 D1 A2 B2 C2 D2
4004 1 .59 1.38 .39 .79 .28 1.97 .28 1.38
4005 1 .59 1.38 .39 .79 .28 1.97 .28 1.38
4009 1 .59 1.38 .39 .79 .28 1.97 .28 1.38
4012 1 .59 1.38 .39 .79 .28 1.97 .28 1.38
4016 2 .79 1.57 .39 1.18 .79 2.36 .39 1.57
4022 2 .79 1.57 .39 1.18 .79 2.36 .39 1.57
4031 3 .79 1.57 .39 1.18 .79 2.36 .39 1.57
4038 3 .79 3.54 .59 2.36 .79 3.54 .59 2.36
4045 3 .79 3.54 .59 2.36 .79 3.54 .59 2.36
4061 4 .79 3.54 .59 2.36 .79 3.54 .59 2.36
4072 4 .98 4.72 .98 4.72 .98 4.72 .98 4.72
4087 4 .98 4.72 .98 4.72 .98 4.72 .98 4.72
4105 5 .98 4.72 .98 4.72 .98 4.72 .98 4.72
4140 5 .91 9.45 .91 9.45 .91 9.45 .91 9.45
4168 5 1.10 9.45 1.10 9.45 1.10 9.45 1.10 9.45
4210 6 1.10 9.45 1.10 9.45 1.10 9.45 1.10 9.45
Table C-2
C-2

Owner's Manual
Drivecon Toll Free Ph: 1-800-374-8266
Drivecon reserves the right to alter or amend the above information without notice
Cooling
Enough free space shall be left around the inverter to ensure sufficient air circulation and
cooling. You will find the required dimensions for free space in the table below. If several
units are mounted above each other the required free space equals space B + space C
(see figure on next page). Moreover, the outlet air used for cooling by the lower unit must
be directed away from the inlet air to be used by the upper unit.
Dimensions - inches (mm)
Cooling
air
required
FT3/min
(CFM)
Inverter type
XTdor XTe-
Frame
size
A
Distance
from one
inverter to
the next
B C
4004 1 .787 (20) .394 (10) 3.94 (100) 1.97 (50) 41.20
4005 1 .787 (20) .394 (10) 3.94 (100) 1.97 (50) 41.20
4009 1 .787 (20) .394 (10) 3.94 (100) 1.97 (50) 41.20
4012 1 .787 (20) .394 (10) 3.94 (100) 1.97 (50) 41.20
4016 2 .787 (20) .394 (10) 4.72 (120) 2.36 (60) 111.83
4022 2 .787 (20) .394 (10) 4.72 (120) 2.36 (60) 111.83
4031 3 .787 (20) .394 (10) 4.72 (120) 2.36 (60) 111.83
4038 3 1.18 (30) .394 (10) 6.29 (160) 3.15 (80) 250.15
4045 3 1.18 (30) .394 (10) 6.29 (160) 3.15 (80) 250.15
4061 3 1.18 (30) .394 (10) 6.29 (160) 3.15 (80) 250.15
4072 4 1.18 (30) .394 (10) 6.29 (160) 3.15 (80) 250.15
4087 4 2.95 (75) 2.95 (75) 11.81 (300) 3.94 (100) 250.15
4105 4 2.95 (75) 2.95 (75) 11.81 (300) 3.94 (100) 250.15
4140 5 2.95 (75) 2.95 (75) 11.81 (300) 3.94 (100) 382.58
4168 5 2.95 (75) 2.95 (75) 11.81 (300) 3.94 (100) 382.58
4210 6 2.95 (75) 2.95 (75) 11.81 (300) 3.94 (100) 450.00
C-3

Owner's Manual
Drivecon Toll Free Ph: 1-800-374-8266
Drivecon reserves the right to alter or amend the above information without notice
Installation
The inverter should be mounted vertically on the wall or on the subpanel of an enclosure.
Enough space shall be reserved around the inverter in order to ensure sufficient cooling, see
diagram below. Also see to that the mounting plane is flat. The inverter shall be fixed with four
screws (or bolts, depending on the unit size).
Installation space diagram shown at left. Dotted line represents
perimeter distance around inverter. Refer to Table 3-5, 3-6, and
3-7 for mounting hole dimensions.
Hardware Instructions and Installation
Operating Environment
The installation site of the inverter poses direct impact to the full functionality and life expect-
ancy of your inverter. Please carefully choose an appropriate installation site based on the
following criteria:
• Environment temperature: -10°C to +40°C enclosed without external casing: -10°C to
+55°C chassis mount
• Avoid water dripping or humid environment
• Avoid direct sunlight
• Avoid oily atmospheres
• Avoid corrosive liquid or gas
• Prevent foreign dusts or metal scraps from entering interior
• Keep away from radioactive or flammable material
• Avoid electromagnetic interference (arc welding or power machinery)
• Avoid vibration. If vibration can not be avoided, shock mounts should be installed to
reduce vibration.
• If there are several inverters installed in the same control panel, additional cooling fans
should be installed to lower the environment below 40°C for enclosed units.
• Inverter should be installed facing forward and upright.
• Inverter must be installed as to leave room on all sides for proper heat dissipation. If
installed in an enclosure, the dust cover may be removed for better heat dissipation.
C-4
A
inverter
A
B
C
A

Owner's Manual
Drivecon Toll Free Ph: 1-800-374-8266
Drivecon reserves the right to alter or amend the above information without notice
Inverter dimensions. Frame size 1, 2, and 3.
Table C-5
Model
Number XTD- Frame
size H1
(inches) H2
(inches) W1
(inches) W2
(inches) D1
(inches) Hole diameter
(inches) Weight
(lbs.)
4004-000 1 12.874 12.323 5.039 3.937 7.480 0.276 13.40
4005-000 1 12.874 12.323 5.039 3.937 7.480 0.276 13.40
4009-000 1 12.874 12.323 5.039 3.937 7.480 0.276 13.40
4012-000 1 12.874 12.323 5.039 3.937 7.480 0.276 13.40
4016-000 2 16.496 15.984 5.669 3.937 8.425 0.276 21.70
4022-000 2 16.496 15.984 5.669 3.937 8.425 0.276 21.70
4031-000 3 21.969 21.299 7.677 5.827 9.331 0.354 49.56
4038-000 3 21.969 21.299 7.677 5.827 9.331 0.354 49.56
4045-000 3 21.969 21.299 7.677 5.827 9.331 0.354 49.56
C-5

Owner's Manual
Drivecon Toll Free Ph: 1-800-374-8266
Drivecon reserves the right to alter or amend the above information without notice
Inverter dimensions. Frame size 4.
Table C-6
Model Number
XTD-
Frame
size
H1
(inches)
H2
(inches)
W1
(inches)
W2
(inches)
D1
(inches)
Hole diameter
(inches)
Weight
(lbs.)
4061-000 4 24.803 24.173 9.331 7.480 10.118 0.354 93.77
4072-000 4 24.803 24.173 9.331 7.480 10.118 0.354 93.77
4087-000 4 24.803 24.173 9.331 7.480 10.118 0.354 93.77
C-6

Owner's Manual
Drivecon Toll Free Ph: 1-800-374-8266
Drivecon reserves the right to alter or amend the above information without notice
Inverter dimensions. Frame size 5.
Table C-7
Model
Number XTD-
Fram
e size
H1
(inches)
H2
(inches)
W1
(inches)
W2
(inches)
D1
(inches)
Hole diameter
(inches)
Weight
(lbs.)
4105-000 5 29.331 28.386 11.220 10.039 11.339 0.354 155.38
4140-000 5 29.331 28.386 11.220 10.039 11.339 0.354 155.38
4168-000 5 29.331 28.386 11.220 10.039 11.339 0.354 155.38
C-7

Owner's Manual
Drivecon Toll Free Ph: 1-800-374-8266
Drivecon reserves the right to alter or amend the above information without notice
Inverter dimensions. Frame size 6.
Table C-8
Model
Number XTD-
Fram
e size
H1
(inches)
H2
(inches)
W1
(inches)
W2
(inches) D1 (inches) Hole diameter
(inches)
Weight
(lbs.)
4210-000 6 53.149 16.54 20.86 7.87 14.251 0.354 264.55
C-8

Owner's Manual
Drivecon Toll Free Ph: 1-800-374-8266
Drivecon reserves the right to alter or amend the above information without notice
Chapter D - WIRING AND SIZING INFORMATION
Cable installation and the UL standards
To meet the UL (Underwriters Laboratories) regulations, a UL-approved copper cable with
a minimum heat-resistance of +60-75C must be used.
The tightening torques of the terminals are given in table below.
Tightening torques of terminals
* Tightening torque of terminal connection to the isolative base in Nm/in-lbs.
XT inverter type Frame Tightening torque[Nm] Tightening torque in-lbs.
4004~4012 1 0.5—0.6 4—5
4016~4022 2 1.2—1.5 10—13
4031~4045 3 4 35
4061~4087 4 10 85
4105~4140 5 20 170
4168 5 40 340
4210 6 50 425
Cable and motor insulation checks
1. Motor cable insulation checks
Disconnect the motor cable from terminals U, V and W of the inverter and from the
motor. Measure the insulation resistance of the motor cable between each phase
conductor as well as between each phase conductor and the ground. The insulation
resistance must be >1M ohm.
2. Mains cable insulation checks
Disconnect the mains cable from terminals L1, L2 and L3 of the frequency converter
and from the mains. Measure the insulation resistance of the mains cable between
each phase conductor as well as between each phase conductor and the ground. The
insulation resistance must be >1M ohm.
3. Motor insulation checks
Disconnect the motor cable from the motor in the motor connection box. Measure the
insulation resistance of each motor winding and ground. The measurement voltage
must equal to at least the motor nominal voltage but not exceed 1000 V. The insulation
resistance must be >1M ohm.
D-1
Other manuals for XT Series
7
This manual suits for next models
16
Table of contents
Other Drivecon DC Drive manuals
Popular DC Drive manuals by other brands
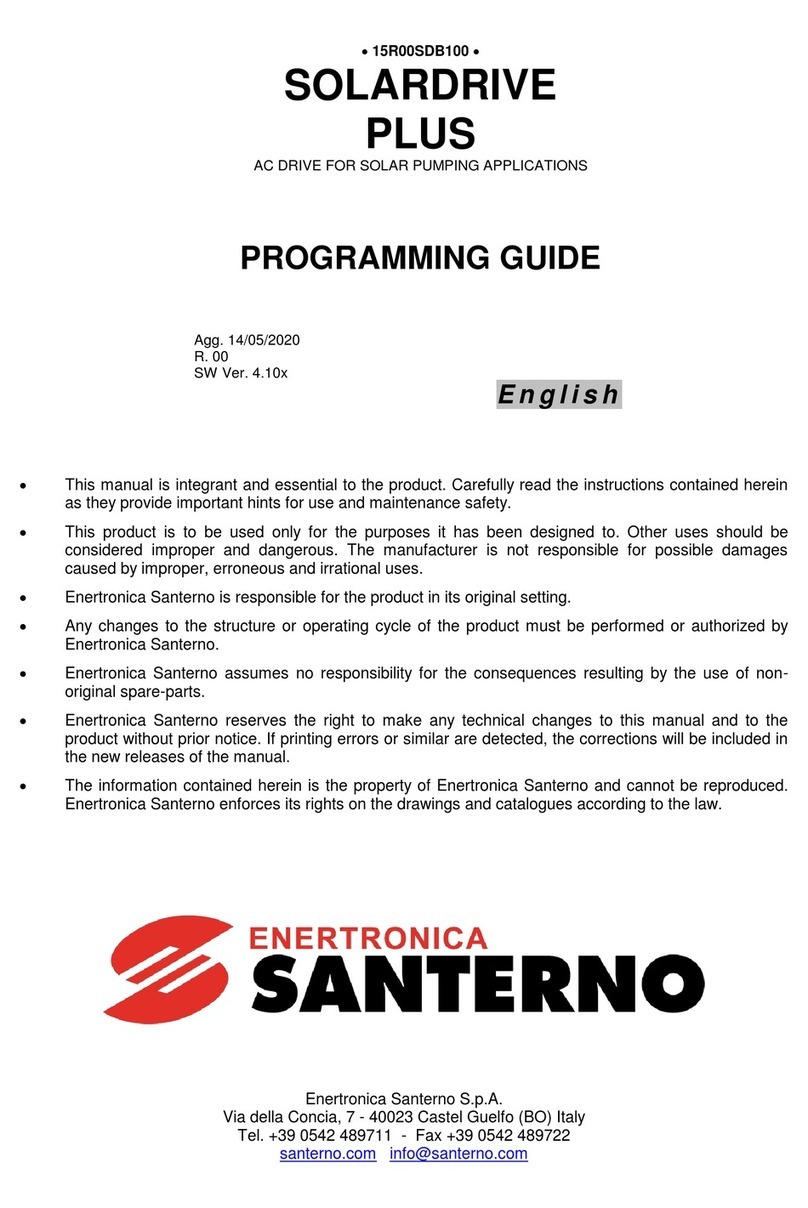
Enertronica Santerno
Enertronica Santerno SOLARDRIVE PLUS Programming guide

Bodine
Bodine BSL06T3FL installation instructions
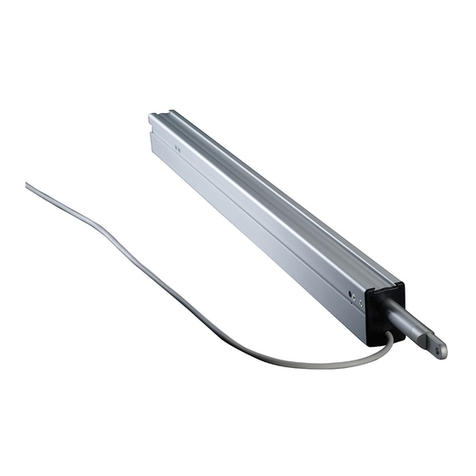
STG-BEIKIRCH
STG-BEIKIRCH M2 Series Technical information and operating instruction
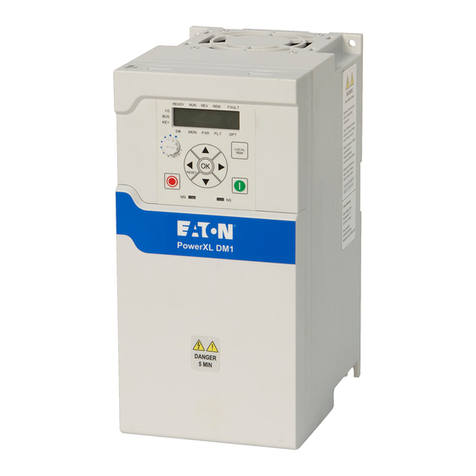
Eaton
Eaton PowerXL DM1 Series Applications manual
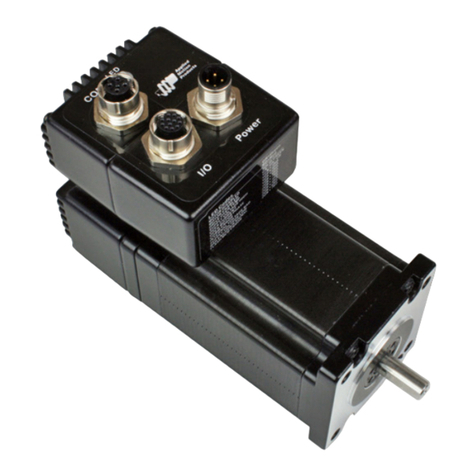
Moons'
Moons' Applied Motion Products SWM24 Quick setup guide
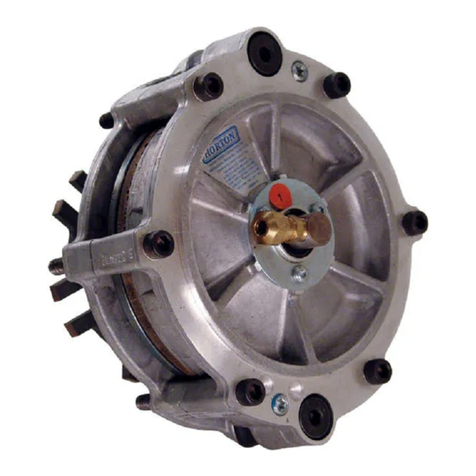
Horton
Horton HT650 Service instructions