Huegli Tech HT-HSG100 User manual

HT-HSG100
Intelligent Hyper Speed Governor
Identification:
HT-HSG100_MN_DN_06.01.2017
Version: 1.2
Operating instructions
1/42
Doc. Name: HT-HSG100-MN-EN-V1.2.doc
06.01.2017
HUEGLI TECH, protection endorsement in accordance with ISO 16016 standards Transmission and/or copying of this document, or utilization or communication of its
contents other than for its authorized purpose are forbidden, insofar as permission has not been expressly granted. Violators will be prosecuted. All patent and design rights reserved.
HT-HSG100
Intelligent Hyper Speed Governor
Instruction manual
Doc. No.:
HT-HSG100_MN_EN_06.01.2017
Version:
1.2
Edition:
06.01.2017
PC Software Version:
3.0.0.82
Firmware Version:
1.51
Hardware Version:
D
HUEGLI TECH AG (LTD) Switzerland

HT-HSG100
Intelligent Hyper Speed Governor
Identification:
HT-HSG100_MN_DN_06.01.2017
Version: 1.2
Operating instructions
2/42
Doc. Name: HT-HSG100-MN-EN-V1.2.doc
06.01.2017
HUEGLI TECH, protection endorsement in accordance with ISO 16016 standards Transmission and/or copying of this document, or utilization or communication of its
contents other than for its authorized purpose are forbidden, insofar as permission has not been expressly granted. Violators will be prosecuted. All patent and design rights reserved.
Support Matrix
Hardware
Version
A, B, C
Hardware
version
D
PC
software
version
<
3.0.0.81
PC
software
version
>=
3.0.0.81
Product serial
number
HTHG101C06XXXXXXXX
Product serial
number
HTHG101D07XXXXXXXX
Firmware
version
<1.51
Firmware
version
>=1.51

HT-HSG100
Intelligent Hyper Speed Governor
Identification:
HT-HSG100_MN_DN_06.01.2017
Version: 1.2
Operating instructions
3/42
Doc. Name: HT-HSG100-MN-EN-V1.2.doc
06.01.2017
HUEGLI TECH, protection endorsement in accordance with ISO 16016 standards Transmission and/or copying of this document, or utilization or communication of its
contents other than for its authorized purpose are forbidden, insofar as permission has not been expressly granted. Violators will be prosecuted. All patent and design rights reserved.
Table of contents
1Installation declaration (for an incomplete machine).................................................5
2General...........................................................................................................................6
2.1 Introduction............................................................................................................................6
2.2 Safety instructions and Warnings...........................................................................................6
2.2.1 Over-speed protection .......................................................................................................7
2.2.2 Safety protection................................................................................................................7
2.3 Guarantee terms and conditions.............................................................................................7
2.3.1 Correct use........................................................................................................................7
2.3.2 Use of Accessories............................................................................................................7
3Installation and connection..........................................................................................8
3.1 General information................................................................................................................8
3.2 Connection terminals............................................................................................................10
3.3 Electrical connection ............................................................................................................11
3.3.1 Fixed RPM, optional with load distribution or for parallel operation with the mains...........13
3.3.2 Variable Speed................................................................................................................15
3.3.3 Crank and Over-speed output..........................................................................................16
3.3.4 RPM adjustment via digital signal ....................................................................................16
3.3.5 Droop Mode.....................................................................................................................17
3.3.6 Position Mode..................................................................................................................18
3.3.7 Other inputs.....................................................................................................................19
3.3.7.1 Idle................................................................................................................................19
3.3.7.2 Gain ..............................................................................................................................19
3.4 CAN BUS Connection..........................................................................................................20
3.5 Keypad.................................................................................................................................20
4Installation of PC software .........................................................................................22
5Software use................................................................................................................23
5.1 Main Screen.........................................................................................................................23
5.1.1 Speed Parameters...........................................................................................................25
5.1.2 Options............................................................................................................................25
5.1.3 Loading/Saving Settings..................................................................................................27
5.1.4 Viewing Configuration Settings File..................................................................................27

HT-HSG100
Intelligent Hyper Speed Governor
Identification:
HT-HSG100_MN_DN_06.01.2017
Version: 1.2
Operating instructions
4/42
Doc. Name: HT-HSG100-MN-EN-V1.2.doc
06.01.2017
HUEGLI TECH, protection endorsement in accordance with ISO 16016 standards Transmission and/or copying of this document, or utilization or communication of its
contents other than for its authorized purpose are forbidden, insofar as permission has not been expressly granted. Violators will be prosecuted. All patent and design rights reserved.
5.1.5 Password Protected Parameters .....................................................................................28
5.2 PID Parameters....................................................................................................................29
PID Parameters 1 ..............................................................................................................................30
PID Parameters 2 ..............................................................................................................................30
5.3 Droop...................................................................................................................................30
5.4 CAN Bus..............................................................................................................................32
5.4.1 Supported J1939 ECU CAN Bus Register .......................................................................32
5.4.2 Supported DST CAN Bus Register ..................................................................................34
5.5 Speed Graph........................................................................................................................35
6Dimensions..................................................................................................................36
7Starting the motor .......................................................................................................36
7.1 Before starting the motor with the HSG100, follow this procedure:.......................................36
7.2 Starting and motor tuning.....................................................................................................37
7.3 Optimisation of dynamic settings (Tuning)............................................................................37
7.4 Further optimisation of dynamic settings (Tuning) ................................................................38
8Configurable parameters, values in [ ] = factory settings........................................38
9Correction system faults ............................................................................................40
9.1 Motor does not start .............................................................................................................40
9.2 Motor does not run with the correct variable RPM................................................................40
9.3 Over-speed during start process ..........................................................................................41
9.4 Overcurrent during start and/or engine running process.......................................................41
9.5 Engine unstable ...................................................................................................................41
10 Technical Data.............................................................................................................42
10.1 Performance.........................................................................................................................42
10.2 Surroundings........................................................................................................................42
10.3 Input/output parameters .......................................................................................................42
10.4 Norms/standards..................................................................................................................42
10.5 Reliability..............................................................................................................................42
10.6 Mass and weight ..................................................................................................................42
10.7 Configuration parameters.....................................................................................................42

HT-HSG100
Intelligent Hyper Speed Governor
Identification:
HT-HSG100_MN_DN_06.01.2017
Version: 1.2
Operating instructions
5/42
Doc. Name: HT-HSG100-MN-EN-V1.2.doc
06.01.2017
HUEGLI TECH, protection endorsement in accordance with ISO 16016 standards Transmission and/or copying of this document, or utilization or communication of its
contents other than for its authorized purpose are forbidden, insofar as permission has not been expressly granted. Violators will be prosecuted. All patent and design rights reserved.
1 Installation declaration (for an incomplete machine)
Installation declaration
(Directive 2006/42/EC, Appendix II B)
The manufacturer: Huegli Tech Murgenthalstrasse 30 4900 Langenthal Switzerland
hereby declares that the incomplete machinery:
General description: HT-HSG100
complies with the basic health and safety requirements of machinery directive 2006/42/EC Appendix
I.
The special technical documents in compliance with Appendix VII part B have been produced.
The incomplete machine corresponds with the following other EC directives:
Low tension directive 2006/95/EC
The following harmonised norms were applied:
EN ISO 12100-1; EN ISO 12100-2; EN ISO 14121-1;
Authorised representative for creation of the technical documents:
E. Uzunlar Murgenthalstrasse 30 4900 Langenthal
The special technical documents are transmitted in electronic form as required by individual state of-
fices.
Operating the incomplete machine is not permitted until the incomplete machine is built into a
machine that conforms to the provisions of the machinery directive and an EC conformity dec-
laration in compliance with Appendix II A is provided.
Langenthal 01.12.2014 Huegli Tech AG,
Uzunlar, Emrah Huegli, Daniel
Product Manager President

HT-HSG100
Intelligent Hyper Speed Governor
Identification:
HT-HSG100_MN_DN_06.01.2017
Version: 1.2
Operating instructions
6/42
Doc. Name: HT-HSG100-MN-EN-V1.2.doc
06.01.2017
HUEGLI TECH, protection endorsement in accordance with ISO 16016 standards Transmission and/or copying of this document, or utilization or communication of its
contents other than for its authorized purpose are forbidden, insofar as permission has not been expressly granted. Violators will be prosecuted. All patent and design rights reserved.
2 General
2.1 Introduction
The HT-HSG100 is an intelligent electronic engine speed governor for managing motor RPM that
works hand in hand with the spring less version of HT-TM2200-75 rotary actuator to provide fast re-
sponse, precise control and reliability when required to react to load changes.
A closed control circuit using an actuator, magnetic RPM sensor and the position feedback signal
from the HT-TM2200-75, the HSG100 can be operated for a large number of motors in both an isoch-
ronous and static fashion. High precision and robust construction makes it possible to use in the
harshest motor use conditions.
The microprocessor design provides precise and user-specific performance and functionality. The
HSG100 enables exact (< 0.25%) isochronous rotation speed control. The permanent memory saves
the settings even if the power supply is interrupted and thanks to a wide voltage range of 12-24 VDC
the HSG100 has a wide range of uses.
2.2 Safety instructions and Warnings
Before installing and starting the device, please read the operating instructions. These contain im-
portant notes for safety and use.
No liability can be accepted for damage arising from failure to follow the instructions or any inappro-
priate use.
The governor may only be used for the manner of operation prescribed in the operating instructions
and only in connection with third-party devices and components recommended or installed by us or
software supplied by us. Any other use shall be considered inappropriate use and will result in the
voiding of all liability and warranty claims against the manufacturer.
Interventions and alterations that influence the safety technology and the functionality of the governor
may be carried out only by the manufacturer.
Fault-free and safe operation is conditional upon competent transport, assembly and installation as
well as qualified use and correct maintenance.
All relevant accident prevention regulations and other generally recognised technical safety and
health and safety at work rules are to be observed. Fault-free functioning of the machinery and its
peripheral components is only guaranteed with original accessory parts and spare parts.
The HSG100 engine speed governor is robust enough to be placed in a control cabinet with other
operating control devices or installed on the motor. If water, mist or condensation can come into con-
tact with the controller, it should be mounted vertically, allowing the liquid to flow away from the con-
troller. Extremes of heat should be avoided.

HT-HSG100
Intelligent Hyper Speed Governor
Identification:
HT-HSG100_MN_DN_06.01.2017
Version: 1.2
Operating instructions
7/42
Doc. Name: HT-HSG100-MN-EN-V1.2.doc
06.01.2017
HUEGLI TECH, protection endorsement in accordance with ISO 16016 standards Transmission and/or copying of this document, or utilization or communication of its
contents other than for its authorized purpose are forbidden, insofar as permission has not been expressly granted. Violators will be prosecuted. All patent and design rights reserved.
2.2.1 Over-speed protection
IMPORTANT
An over-speed shut down mechanism must be installed separately from
the control system as a safety measure, to prevent motor faults that
may result in damage or injury to machinery or persons.
A secondary shut down device (fuel valve) must be installed.
2.2.2 Safety protection
IMPORTANT
Protective Earth (PE) must be connected with Battery Minus
terminal always.
2.3 Guarantee terms and conditions
2.3.1 Correct use
The device is intended for exclusive use under the conditions described in the "Technical Data" rubric.
Other uses are potentially dangerous. Huegli-Tech AG cannot accept liability for damage which re-
sults from incorrect use or application other than that for which it was intended.
2.3.2 Use of Accessories
Accessory parts may be installed or added only when they have been explicitly authorised by Huegli
Tech AG. Any claims under guarantee, warranty or product liability shall be void if other parts are
used.
The general guarantee terms and conditions of Huegli Tech AG shall apply.

HT-HSG100
Intelligent Hyper Speed Governor
Identification:
HT-HSG100_MN_DN_06.01.2017
Version: 1.2
Operating instructions
8/42
Doc. Name: HT-HSG100-MN-EN-V1.2.doc
06.01.2017
HUEGLI TECH, protection endorsement in accordance with ISO 16016 standards Transmission and/or copying of this document, or utilization or communication of its
contents other than for its authorized purpose are forbidden, insofar as permission has not been expressly granted. Violators will be prosecuted. All patent and design rights reserved.
3 Installation and connection
3.1 General information
The magnetic RPM sensor cable should be shielded to guarantee that no electromagnetic interfer-
ence can reach the engine speed governor. The shield should be on-sided on the battery negative.
To maintain the correct distance between the flywheel and the magnetic RPM sensor, the sensor
must be rotated in until the flywheel clicks and then rotated out again for ¾ of a rotation. This
achieves the correct spacing between flywheel and sensor. To be able to start the motor, the sensor
must generate at least 1V AC RMS during the start.
Cross-section of the battery and actuator cable at terminals S,T,U, and V:
1.5 mm2for 24 VDC or
2.5 mm2for 12 VDC

HT-HSG100
Intelligent Hyper Speed Governor
Identification:
HT-HSG100_MN_DN_06.01.2017
Version: 1.2
Operating instructions
9/42
Doc. Name: HT-HSG100-MN-EN-V1.2.doc
06.01.2017
HUEGLI TECH, protection endorsement in accordance with ISO 16016 standards Transmission and/or copying of this document, or utilization or communication of its
contents other than for its authorized purpose are forbidden, insofar as permission has not been expressly granted. Violators will be prosecuted. All patent and design rights reserved.
IMPORTANT
The pick-up must be mounted so as to sense the teeth of a full
gear. The flywheel ring-gear is suitable.
Note: any missing teeth will negatively affect the pick-up signal.
For longer cables (>5m) the cable cross-section is to be increased appropriately to keep the voltage
drop low.
Battery positive (+) input, connection V, should be fused 6 A.
The governor should be installed such that the housing has connection with the chassis of the
control cabinet.
The cable of the actuator must be shielded along its entire length.
The cable of the magnetic engine speed sensor must be shielded along its entire length.
The cable of the variable RPM speed input can be up to 5m long. For longer cables, a shield-
ed cable must be used.
The shielding must always be grounded such that it does not come into contact with the chas-
sis of the machine. This is to prevent stray signals from entering the governor and causing in-
terference. The shield must be grounded at one end.
Important: The HSG100 is equipped with over-current protection on the (Terminal S & T) output to
actuator. Please note that even through overcurrent protection is in place, repeatedly subjecting the
actuator output to overcurrent or short circuit condition can result in permanent damage to the prod-
uct. Overcurrent protection is activated when the digital display on the HSG100 shows = = = =.

HT-HSG100
Intelligent Hyper Speed Governor
Identification:
HT-HSG100_MN_DN_06.01.2017
Version: 1.2
Operating instructions
10/42
Doc. Name: HT-HSG100-MN-EN-V1.2.doc
06.01.2017
HUEGLI TECH, protection endorsement in accordance with ISO 16016 standards Transmission and/or copying of this document, or utilization or communication of its
contents other than for its authorized purpose are forbidden, insofar as permission has not been expressly granted. Violators will be prosecuted. All patent and design rights reserved.
3.2 Connection terminals
Connection Terminal
Description
Definition
Type
SPEED2
Optional preconfigured speed selection
Binary Input
SPEED3
Optional preconfigured speed selection
Binary Input
IDLE
Idle
Binary Input
GAIN
Preconfigured PID set2 selection
Binary Input
IN-COM
Input Common Connection
Common Connection for Binary Input
+5VDC
5VDC Power Supply
Power Supply
GND
Ground / chassis
Ground
BOUT1
Crank Termination Output
Binary Output
BOUT2
Over-speed Output
Binary Output
OUT-COM
Output Common Connection
Common Connection for Binary Output
+5VDC
5VDC Power Supply(Feedback sensor)
Power Supply Output
FEEDBACK
Feedback position signal input
Analog Input(0-5Vdc)
GND
Ground / chassis
Ground
+5VDC
5VDC Power Supply
Power Supply Output
SPEED TRIM
Speed Trim input
Analog Input(0-5Vdc)
GND
Ground
Ground
EXT SPEED
Load distribution / synchronisation
Analog Input(0-10V)
GND
Ground
Ground

HT-HSG100
Intelligent Hyper Speed Governor
Identification:
HT-HSG100_MN_DN_06.01.2017
Version: 1.2
Operating instructions
11/42
Doc. Name: HT-HSG100-MN-EN-V1.2.doc
06.01.2017
HUEGLI TECH, protection endorsement in accordance with ISO 16016 standards Transmission and/or copying of this document, or utilization or communication of its
contents other than for its authorized purpose are forbidden, insofar as permission has not been expressly granted. Violators will be prosecuted. All patent and design rights reserved.
ACTUATOR +
Actuator (Plus)
PWM Output
ACTUATOR-
Actuator (Minus)
PWM Output
BATTERY-
Battery (Minus)
Power Supply Input
BATTERY+
Battery (Plus)
Power Supply Input
PICKUP-
Pickup (Ground)
PWM Input
PICKUP+
Pickup (Plus)
PWM Input
CAN LO
CAN high
Communication Interface
CAN HI
CAN high
Communication Interface
DROOP
Droop
Droop enable signal
3.3 Electrical connection
The HSG100 has a range of different connection options for various applications. The digital inputs
and outputs of the HSG100 are galvanic isolated. Therefore you have option to connect the digital
inputs and outputs in either galvanic isolated or non-galvanic isolated configuration depending on your
application/system requirement.
Non-galvanic Isolated Binary Input Configuration

HT-HSG100
Intelligent Hyper Speed Governor
Identification:
HT-HSG100_MN_DN_06.01.2017
Version: 1.2
Operating instructions
12/42
Doc. Name: HT-HSG100-MN-EN-V1.2.doc
06.01.2017
HUEGLI TECH, protection endorsement in accordance with ISO 16016 standards Transmission and/or copying of this document, or utilization or communication of its
contents other than for its authorized purpose are forbidden, insofar as permission has not been expressly granted. Violators will be prosecuted. All patent and design rights reserved.
Galvanic Isolated Binary Input Configuration
Important: To achieve galvanic isolation, grounding and power supply used by the HSG100 cannot be
the same as that of the device that the input/output is interfaced with.
Galvanic Isolated Binary Output Configuration
Important: To achieve galvanic isolation, grounding and power supply used by the HSG100 cannot be
the same as that of the device that the input/output is interfaced with.

HT-HSG100
Intelligent Hyper Speed Governor
Identification:
HT-HSG100_MN_DN_06.01.2017
Version: 1.2
Operating instructions
13/42
Doc. Name: HT-HSG100-MN-EN-V1.2.doc
06.01.2017
HUEGLI TECH, protection endorsement in accordance with ISO 16016 standards Transmission and/or copying of this document, or utilization or communication of its
contents other than for its authorized purpose are forbidden, insofar as permission has not been expressly granted. Violators will be prosecuted. All patent and design rights reserved.
Non-galvanic Isolated Binary Output Configuration
The following describes the applications and relevant connection configurations.
3.3.1 Fixed RPM, optional with load distribution or for parallel operation with the mains
With this application, up to three fixed RPM speeds can be selected by wiring in inputs Speed 2(A)
and Speed 3 (B) as shown in section 3.3. The RPM settings can be set using the HSG100 PC Con-
figuration software.
Speed2
Input
Speed3
Input
Active Speed
Open
Open
Speed1
Close
Open
Speed2
Open
Close
Speed3
Close
Close
Speed3

HT-HSG100
Intelligent Hyper Speed Governor
Identification:
HT-HSG100_MN_DN_06.01.2017
Version: 1.2
Operating instructions
14/42
Doc. Name: HT-HSG100-MN-EN-V1.2.doc
06.01.2017
HUEGLI TECH, protection endorsement in accordance with ISO 16016 standards Transmission and/or copying of this document, or utilization or communication of its
contents other than for its authorized purpose are forbidden, insofar as permission has not been expressly granted. Violators will be prosecuted. All patent and design rights reserved.
If a load distribution and/or synchronisation/load control (for parallel operation with the mains) is addi-
tionally required, this can be achieved by wiring in the input EXT SPEED. Here a signal of 0 –10 V
DC (zero point = Bias voltage) is required. The HSG100 can work on both negative or positive princi-
ple depends on the configuration. The Sync/Load Sharing functions must be activated using the HT
Speed Governor Configuration software.
Example
1. Negative speed regulation
Input
Voltage
(Ext
Speed)
Bias
Voltage
Full
Scale
voltage
Requested
Speed
0.0V
5.0V
10.0V
1550rpm
5.0V
5.0V
10.0V
1500rpm
10.0V
5.0V
10.0V
1450rpm
2. Positive speed regulation
Input
Voltage
(Ext
Speed)
Bias
Voltage
Full
Scale
voltage
Requested
Speed
0.0V
5.0V
10.0V
1450rpm
5.0V
5.0V
10.0V
1500rpm
10.0V
5.0V
10.0V
1550rpm
Note: This option only available on Firmware version>=1.51 and PC software >=3.0.0.81

HT-HSG100
Intelligent Hyper Speed Governor
Identification:
HT-HSG100_MN_DN_06.01.2017
Version: 1.2
Operating instructions
15/42
Doc. Name: HT-HSG100-MN-EN-V1.2.doc
06.01.2017
HUEGLI TECH, protection endorsement in accordance with ISO 16016 standards Transmission and/or copying of this document, or utilization or communication of its
contents other than for its authorized purpose are forbidden, insofar as permission has not been expressly granted. Violators will be prosecuted. All patent and design rights reserved.
3.3.2 Variable Speed
a. Potentiometer
If the motor has to be run with a variable Speed setting, this can be achieved with an external potenti-
ometer (5 or 10 kOhm type) using a 3 wire connection. This is to be connected according to the fol-
lowing diagram.
The External Speed Trim function must be activated in the HT Speed Governor Configuration soft-
ware with the right input type chosen. In addition, the Speed Trim DS and Speed Trim FS parameters
of the desired values can also be set
b. Voltage Input
PC Software
PC Software

HT-HSG100
Intelligent Hyper Speed Governor
Identification:
HT-HSG100_MN_DN_06.01.2017
Version: 1.2
Operating instructions
16/42
Doc. Name: HT-HSG100-MN-EN-V1.2.doc
06.01.2017
HUEGLI TECH, protection endorsement in accordance with ISO 16016 standards Transmission and/or copying of this document, or utilization or communication of its
contents other than for its authorized purpose are forbidden, insofar as permission has not been expressly granted. Violators will be prosecuted. All patent and design rights reserved.
3.3.3 Crank and Over-speed output
HSG100 has 2 binary output (can be set as sourcing or sinking output depending on the wiring
configuration).
BOUT1 turns on when crank termination speed is reached and will turn off when engine speed reach-
es 0 rpm. BOUT2 turns on when over-speed event occurs and will turn off depends on over-speed
latch setting
BOUT2 turn off during next crank
Press ‘Fn’ key or power ‘off’ and ‘on’ to turn
off BOUT2
3.3.4 RPM adjustment via digital signal
If the speed setting is required to be set via a digital signal, this is also possible with the HSG-100.
This may be necessary during parallel operation with the mains if the motor control only delivers
digital signals for synchronisation and/or load control. The Binary Speed Up Down function in the
Speed Governor Configuration software must be activated.

HT-HSG100
Intelligent Hyper Speed Governor
Identification:
HT-HSG100_MN_DN_06.01.2017
Version: 1.2
Operating instructions
17/42
Doc. Name: HT-HSG100-MN-EN-V1.2.doc
06.01.2017
HUEGLI TECH, protection endorsement in accordance with ISO 16016 standards Transmission and/or copying of this document, or utilization or communication of its
contents other than for its authorized purpose are forbidden, insofar as permission has not been expressly granted. Violators will be prosecuted. All patent and design rights reserved.
Non-Galvanic Isolated Configuration Galvanic Isolated Configuration
Speed2
Input
Speed3
Input
Bin Speed Rate Up
(milliseconds)
Bin Speed Rate Down
(milliseconds)
Requested Speed
(rpm)
Open
Open
200
300
No Change in Requested
speed
Close
Open
200
300
Requested speed + 1 for
every 200 milliseconds
Open
Close
200
300
Requested speed -1 for
every 300 milliseconds
Close
Close
200
300
No Change in Requested
speed
3.3.5 Droop Mode
Droop is for load sharing purpose. Droop
function reduces the reference speed as
load increases. It allows the engine to
run at higher speed during no load and at
rated speed at load. Droop mode can be
enabled on HSG by Terminal Z1 (Droop)
to GND (Terminal R).
Depending on the software configuration,
the requested speed can be change via a
5k ohms potentiometer or by a 0-10Vdc
via the EXT Speed input.
Software configuration related to Droop can
be found in section 5.3

HT-HSG100
Intelligent Hyper Speed Governor
Identification:
HT-HSG100_MN_DN_06.01.2017
Version: 1.2
Operating instructions
18/42
Doc. Name: HT-HSG100-MN-EN-V1.2.doc
06.01.2017
HUEGLI TECH, protection endorsement in accordance with ISO 16016 standards Transmission and/or copying of this document, or utilization or communication of its
contents other than for its authorized purpose are forbidden, insofar as permission has not been expressly granted. Violators will be prosecuted. All patent and design rights reserved.
3.3.6 Position Mode
Position Voltage Configuration
Input Voltage vs Actuator Position
Input Voltage
(volts)
Bias Voltage
Setting
Full-scale Voltage
Setting
Speed
Regulation setting
Actuator
Movement range
0.0 - 5.0
5.0V
10.0V
Positive
0%
5.0 - 10.0
5.0V
10.0V
Positive
0 to 100%
5.0 - 0.0
5.0V
10.0V
Negative
0 to 100%
5.0 - 10.0
5.0V
10.0V
Negative
0%
Once the position mode is activated, the PC software will show that the position mode feature is ac-
tive and PID parameter 2 will be selected.
HSG-100 provides a special function
named position mode. When it use, it
allows the HSG-100 to work like an
electronic throttle control.

HT-HSG100
Intelligent Hyper Speed Governor
Identification:
HT-HSG100_MN_DN_06.01.2017
Version: 1.2
Operating instructions
19/42
Doc. Name: HT-HSG100-MN-EN-V1.2.doc
06.01.2017
HUEGLI TECH, protection endorsement in accordance with ISO 16016 standards Transmission and/or copying of this document, or utilization or communication of its
contents other than for its authorized purpose are forbidden, insofar as permission has not been expressly granted. Violators will be prosecuted. All patent and design rights reserved.
It is important to know that the PID Parameters determine the response of the actuator once the Posi-
tion Mode is active.
The Position Mode function is mainly used for Parallel-To-Mains applications. Once the engine is
Synchronized to the grid there is no longer a speed governing required because the engine is “pulled
“by the grid frequency.
On Parallel-To-Mains application. The terminals Q + R (Ext. Speed) are connected to the speed regu-
lation output of the genset controller (for example DST 4602). This signal must be set to a bias of 5 V
with negative characteristic for speed regulation, it means signal < 5 V = Speed up, signal >5 V =
Speed down.
As long the engine is not connected to the grid (GCB open) the HSG-100 works in normal speed gov-
erning mode (Input A open) with the signal at Q + R (Ext. Speed) coming from the genset controller
the engine the engine is synchronized to the grid. Once the GCB is closed the HSG-100 must be set
to position mode by switching input A (Speed 2) to GND. This can be done by a free feedback con-
tact of the GCB.
3.3.7 Other inputs
3.3.7.1 Idle
If this contact is closed, the motor runs at the configured idle speed.
3.3.7.2 Gain
HSG100 has two set of the PID. If the contact is open, parameter set 1 is active, when the contact is
closed, parameter set 2 is active. For some applications it may be necessary to use other parameters
in idle as under load.

HT-HSG100
Intelligent Hyper Speed Governor
Identification:
HT-HSG100_MN_DN_06.01.2017
Version: 1.2
Operating instructions
20/42
Doc. Name: HT-HSG100-MN-EN-V1.2.doc
06.01.2017
HUEGLI TECH, protection endorsement in accordance with ISO 16016 standards Transmission and/or copying of this document, or utilization or communication of its
contents other than for its authorized purpose are forbidden, insofar as permission has not been expressly granted. Violators will be prosecuted. All patent and design rights reserved.
3.4 CAN BUS Connection
Using the CAN Bus connection, the bus cable must be connected to the terminals Q (Can HI) and P
(Can LO). If the HSG100 is the first or the last device in the bus, a termination resistor (120Ohms) is
required. Shielded cable (for example, HELUKABEL CAN BUS 2x0.22) must be used for the CAN
Bus connection.
3.5 Keypad
The HSG100 has three menu buttons, with which all parameters can be set locally. The set values
are indicated on the LED display. In normal operating mode, the RPM is indicated on the display.
The keypad are locked by default to prevent any accidental misconfiguration. To lock or unlock the
keypad, Press & Hold [Fn] and [+] button for 3 seconds to lock/unlock.
The functions listed below can be accessed using the Fn (Function) button. Each press of the Fn
button makes the next menu active. The active menu is shown on the LED display for 2 seconds, af-
ter which the relevant value of this function appears. Settings are changed with the arrow keys [+] [-]
and raise/lower the value by 1 or 0.1 depending on configuration type. If the arrow keys [+] or [-] held
down longer, the value increases or decreases at a greater rate.
Table of contents
Popular Control Unit manuals by other brands
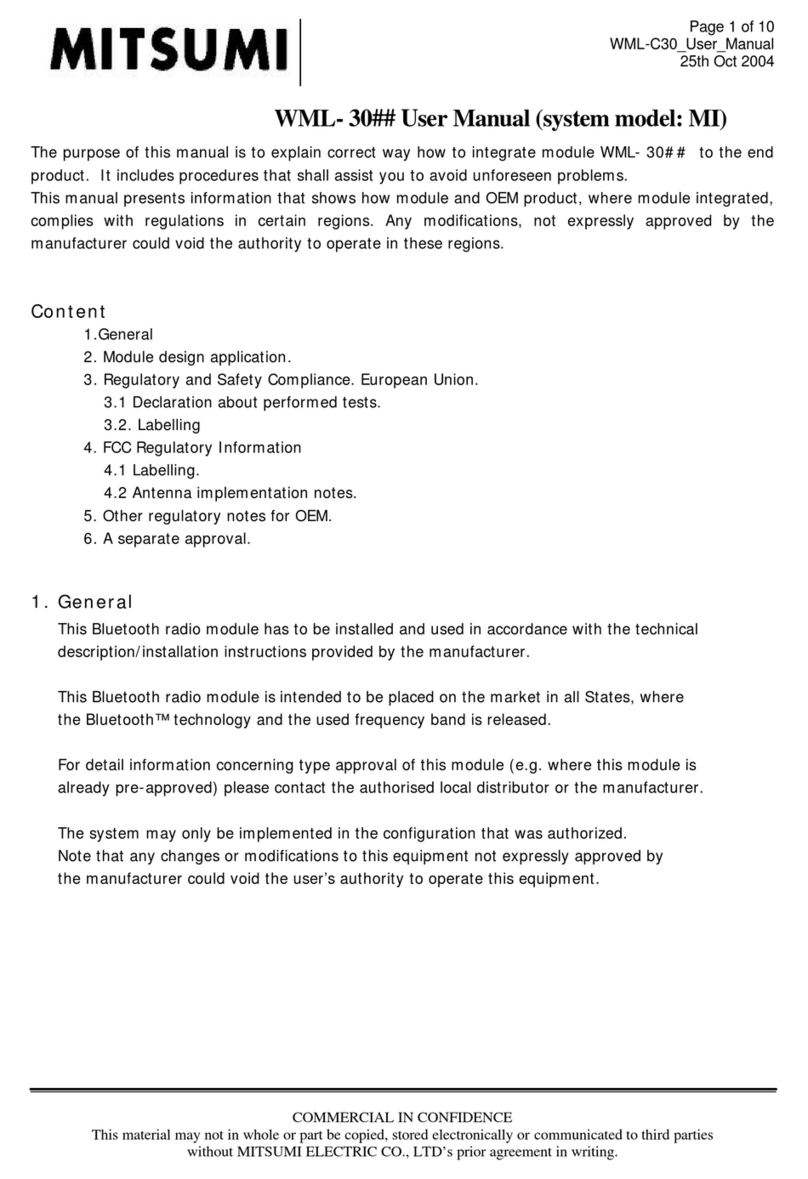
Mitsumi
Mitsumi WML-30 Series user manual
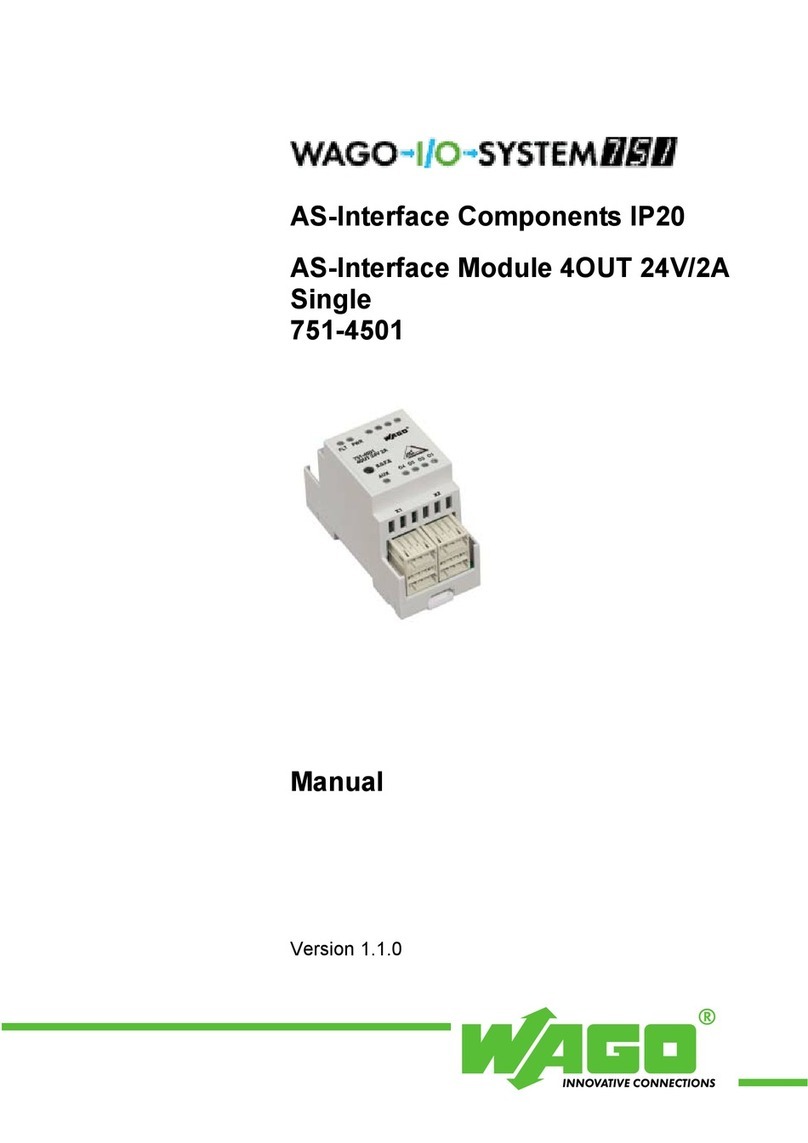
WAGO
WAGO 751-4501 manual
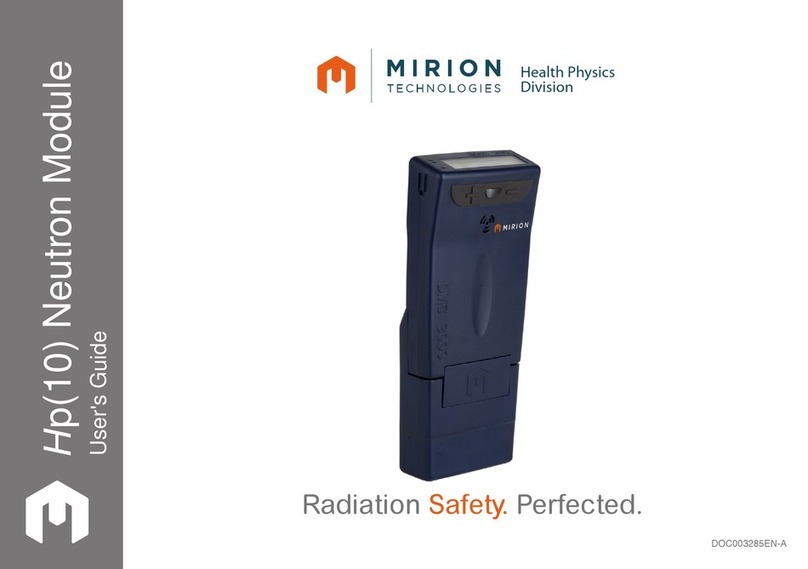
Mirion Technologies
Mirion Technologies Neutron Hp 10 user guide
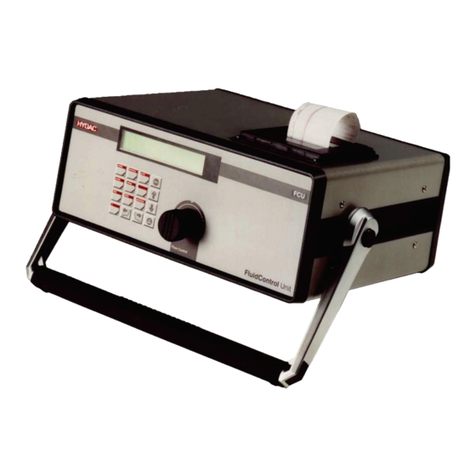
HYDAC FILTER SYSTEMS
HYDAC FILTER SYSTEMS FluidControl FCU 8111 Operating and maintenance instructions
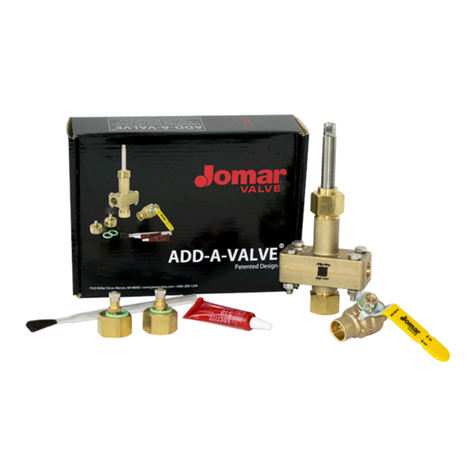
JOMAR
JOMAR Add-A-Valve installation instructions

EOS
EOS EMOTEC L 09 Relay Assembly and operating instructions
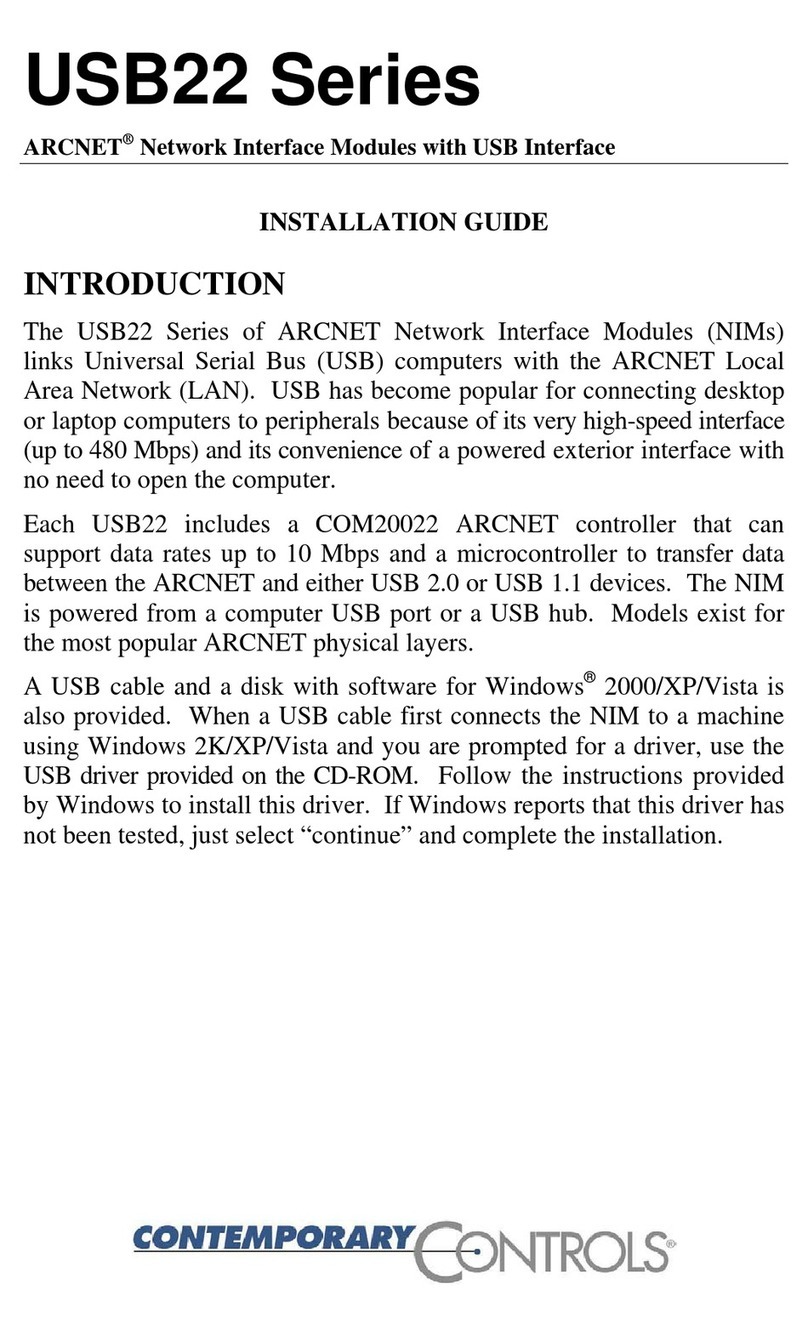
Contemporary Controls
Contemporary Controls ARCNET USB22-485 installation guide

oventrop
oventrop AV9 operating instructions
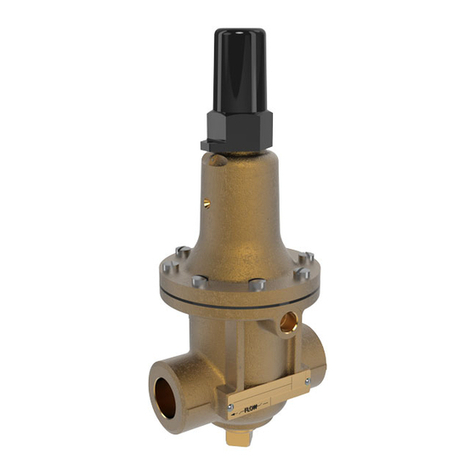
CLA-VAL
CLA-VAL CRL-60 Installation operation & maintenance

Transition Networks
Transition Networks CWDM-MXxxLCR-B Series user guide
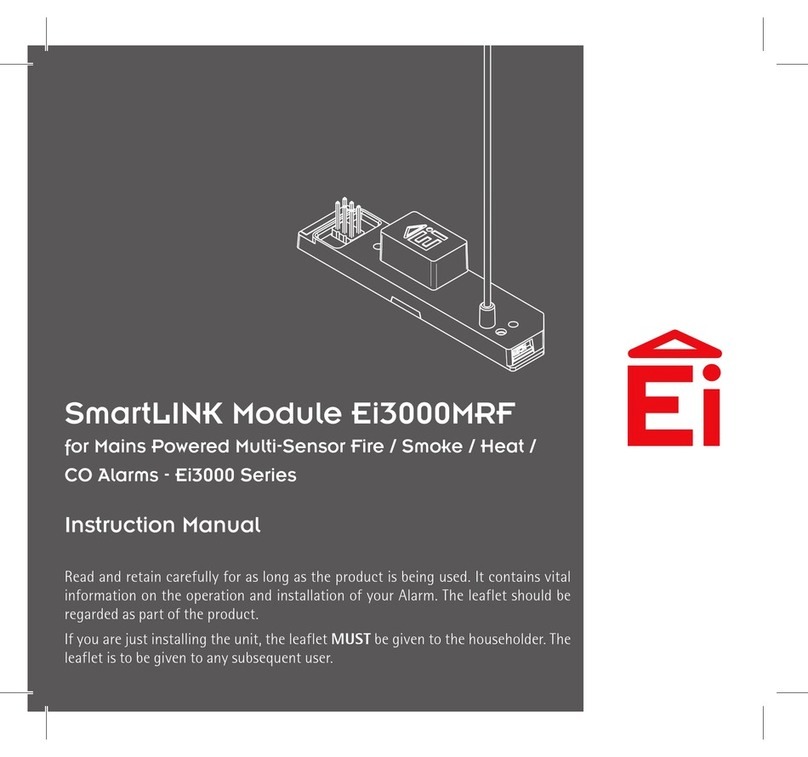
Ei Electronics
Ei Electronics Ei3000 Series instruction manual

Viessmann
Viessmann VITOTRONIC 100 Technical data manual