Hydro Instruments HC-220 User manual

1
HC-220 PID Controller
Operation and Maintenance Manual
HC-220 Rev. 11/1/18
The information contained in this manual was current at the time of printing. The most current versions of all
Hydro Instruments manuals can be found on our website: www.hydroinstruments.com

2
HC-220 PID Controller
Operation & Maintenance
Manual
Table of Contents
Safety Precautions.............................................................................................................3
I. Overview...........................................................................................................................3
II. Control Features................................................................................................................4
III. Configuration Mode..........................................................................................................7
IV. Input And Output Calibration ...........................................................................................9
V. Operation Mode ..............................................................................................................11
VI. Alarm & Output Features................................................................................................12
VII. Reference Terms .............................................................................................................13
VIII. Troubleshooting ..............................................................................................................15
Flow Charts and Drawings
Figure 1 Configuration Mode Flow Chart ...............................................................5
Figure 2 Hidden Screens .........................................................................................6
Figure 3 Operation Mode Flow Chart ...................................................................10
Figure 4 Circuit Board Drawing............................................................................16
RIGHT TO REVISE: Hydro Instruments reserves the right to make engineering
revisions and improvements at any time. Please contact Hydro Instruments if there
is any discrepancy between the literature and the product provided.

3
SAFETY PRECAUTIONS
GENERAL: Be sure to follow all applicable and prudent safety precautions when working with chemicals
and electrical equipment.
ELECTRICAL: The circuit board and incoming A/C power line do include electrical shock risk. Take care
to avoid electrical shocks and do not touch any part of the circuit board or A/C power line unless you are certain
that A/C power has been disconnected from the system.
When connecting A/C power to the instrument, it is imperative that the A/C source be well grounded. Insufficient
A/C grounding will disrupt proper operation of the instrument.
CHECK FOR DAMAGE: Before removing the product from the shipping packaging, carefully check the
equipment for damage. If any product is found damaged, do not put it into operation or install it. Contact
Hydro Instruments to discuss repair or replacement of the damaged equipment.
I. OVERVIEW
1. Modes of the HC-220 – The HC-220 PID Controller has 2 modes that can be accessed. These modes are
as follows:
a. Configuration Mode – This mode is used to set up the control and display parameters. (Flow Meter
range, Control type, Display units, alarms, etc…)
b. Operation Mode – This is the mode used during operation of the HC-220 PID Controller. It allows for
Dosage and Set Point Adjustments as well as manual control of the chemical feed rate.
2. Switching Between Modes – The Configuration Mode is password protected. The password is 220.
This can be entered by using the and buttons.
a. Operation Mode – This is the HC-220 standard mode. This can be reached from either of the other
two modes by repeatedly pressing the “up arrow” key.
b. Configuration Mode – This mode is accessed from the Operation Mode by pressing the “down arrow”
key until the password screen is reached. Then enter the password “220” and then press the “down
arrow” key.
3. Menus & Display – Within each “Mode” there is a set of “Parameters”. Parameters are represented by
the blocks in the following flow charts. To move between these parameters, use the “up arrow” and
“down arrow” keys.
4. Control Methods – The HC-220 offers four different control methods. They are Flow Pacing (Propor-
tional), Residual/ORP, Compound Loop Control, and Manual Control. The method is selected within the
“Configuration Mode”. (See Section III.)
5. Electrical Inputs – The HC-220 offers two analog input channels standard. The PV1 input channel is
used only for a Flow (e.g. proportional) signal. The PV2 input channel is used only for a Residual (e.g.
set point) signal. A third, optional analog input is sometimes included. The optional PV3 input channel is
used only for remote adjustment of the Set Point setting. Each channel can be set to accept either 4-20mA
or Modbus RS-485 signals. Each of the process variable inputs are individually selectable to be read over
any of the four analog input channels AI1, AI2, AI3, or AI4 and also over Modbus.

4
NOTE: The HC-220 can power the 4-20mA source via 24VDC for both the PV1 and PV2 inputs (e.g.
loop powered input). This will change how these inputs are connected. Refer to Figure 3 for additional
details.
PV1(Flow)
AI1/V- = Source powered 4-20mA input.
AI1/V+ = Loop powered 4-20mA input.
PV2 (Residual)
AI2/V- = Source powered 4-20mA input.
AI2/V+ = Loop powered 4-20mA input.
6. Electrical Outputs – The following outputs are available:
a. The HC-220 includes two (2) SPDT alarm relays. Each relay can be independently selected as either
representing normal alarms or whether the HC-220 is in AUTO or Manual mode.
b. 4-20mA Output – The HC-220 is equipped with two (2) 4-20mA outputs which are used to control
chemical feed rate.
7. RS-485 Modbus Communication – This feature allows the HC-220 to be monitored and controlled by a
computer. See Hydro Instruments’ Modbus Communication Setup document for further details.
II. CONTROL FEATURES
1. Keypad Operation – The keypad is used in all three modes of the HC-220. Generally the keys are used
as outlined here below. However, detailed instructions will follow.
a. & keys – These keys are used to cycle through the various display screens. These keys will be
referred to as “up arrow” and “down arrow”.
b. & keys – These keys are generally used to adjust settings and values within the screen being
displayed. These keys will be referred to as “plus” and “minus”.
2. Dip Switches – These switches are used to select whether the analog input channels are to be used for
0-10 Volts or 4-20mA.
a. Switches 1 and 2 on the MB124 circuit board are used for the PV1 (Flow) input channel.
4-20mA: 1 = On, 2 = Off
0-10V: 1 = Off, 2 = On
b. Switches 3 and 4 on the MB124 circuit board are used for the PV2 (Residual) input channel.
4-20mA: 3 = On, 4 = Off
0-10V: 3 = Off, 4 = On

5
00.00 0.000
00000 000.0
% GPM MGD LPM
MLD GPD M3/H LPH
Flow Input Name
FLO
FLO PV1 H2OPRO
Input Signal Loss
Maintain Valve Posn
Flow Input Units
%
Flow Decimal Posn
000.0
000.0 00.00
0.000 00000
Flow Full Scale
10.0 %
Flow Threshold
0.0 %
Flow Filter Time
10 secs
Flow Low Set
0.0 %
Maintain Valve Posn
Close Valve
PPM MG/L mV
pH NTU %
Res Input Name
RES
RES ORP pH Ch1 SCM
TDS DO CON TUR PV2
Input Signal Loss
Maintain Valve Posn
Res Units
PPM
Res Decimal Posn
00.00
Res Full Scale
5.00 PPM
Res Minimum Value
0.00 PPM
Res Filter Time
10 secs
Maintain Valve Posn
Close Valve
FLO RES
SETUP: FLO RES
OUT ALM
Control Type
Flow Pacing
Flow Pacing
Residual/ORP
Compound Loop
Dual Input Feed Fwd
Res Low Set
0.00 PPM
Res High Set
5.00 PPM
Res Dead Band
0.10 PPM
Res Integral Value
20.0 %
Cl2SO2
Output Units
KG/H
KG/H GPH GPM GPD
LPM LPH %PPD GR/H
000.0 00.00
0.000 00000
Output Decimal Posn
000.0
Output Full Scale
10.0 KG/H
Out Gas Feed Type
Cl2
OUT
Alarm Delay Time
10 secs
Output Relay 1 Usage
Normal Alarms
Normal Alarms
Auto(Off)/Manl(On)
Output Relay 2 Usage
Normal Alarms
Normal Alarms
Auto(Off)/Manl(On)
ALM
AI1 Cal: 4 mA 20 mA
AI2 Cal: 4 mA 20 mA
Input Value
Was Changed!
A01 Cal: 4mA= 803
20mA= 3992
A02 Cal: 4mA= 800
20mA= 4000
AI3 Cal: 4 mA 20 mA
AI4 Cal: 4 mA 20 mA
OUT
Screens shown with grey border
are hidden screens,
accessed by holding -
at the appropriate screen
(typically 2nd to last in the branch)
HOLD
Lag Time Mode
1 Point Var Lag Time
Lag Time Mode
2 Point Var Lag Time
FA1= 50% TA1= 60s
FA2= 75% TA2= 40s
A= 0.0 F= 0
B= 0.0 T= 60
Lag Time Mode
Fixed Lag Time
Res Lag Time
60 secs
Res Reset Value
0 GPM
Flow at Variable Lag
500 GPM
Res Lag Time
60 secs
Maximum Lag Time
1800 secs
Maximum Lag Time
1800 secs
Res Reset Value
0 GPM
Res Reset Value
0 GPM
FIGURE 1
CONFIGURATION MODE

6
Sel Inputs: PV1= AI1
PV2= AI2 PV3= AI3
AI1 AI2
AI3 AI4 Mod
Modbus Baud= 19200
Node= 1 Data= 8/N/1
Modbus Baud= 19200
Node= 1 Data= 8/N/1
1 2
Modbus Baud= 19200
Node= 1 Data= 8/N/1
2400
4800
9600
19200
38400
57600
115200
250000
8/N/1
8/N/2
8/E/1
8/O/1
PV1Stop= 00 % D= 0
AUTO RES -1.24 PPM
¹¹¹¹ PO1 0.0KG/H
Set Point Res/ORP
2.00 PPM
Alarm Status
None
MANL RES -1.24 PPM
¹¹¹¹ PO1 0.0KG/H
Set PO1(Valve)
¹¹¹¹ 0.0KG/H
Alarm Status
None
Set Point Res/ORP
2.00 PPM
AUTO RES -1.24 PPM
¹¹¹¹ PO1 0.0KG/H
AUTO FLO -24.9 %
¹¹¹¹ PO1 0.0KG/H
Set Point Res/ORP
2.00 PPM
Set Dosage
1.00
Alarm Status
None
MANL RES -1.24 PPM
¹¹¹¹ PO1 0.0KG/H
MANL FLO -24.9 %
¹¹¹¹ PO1 0.0KG/H
Set Point Res/ORP
2.00 PPM
Set PO1(Valve)
¹¹¹¹ 0.0KG/H
Alarm Status
None
Set Dosage
1.00
HOLD HOLD
AUTO FLO -24.9 %
¹¹¹¹ PO1 0.0KG/H
Set Dosage
1.00
Alarm Status
None
MANL FLO -24.9 %
¹¹¹¹ PO1 0.0KG/H
Set PO1(Valve)
¹¹¹¹ 0.0KG/H
Alarm Status
None
Set Dosage
1.00 HOLD
HOLD
“Flow Pacing” AUTO / MANL
“Residual/ORP” AUTO / MANL
“Compound Loop” AUTO / MANL
“Dual Input Feed Fwd” AUTO / MANL
AUTO RES -1.24 PPM
¹¹¹¹ PO1 0.0KG/H
AUTO FLO -24.9 %
¹¹¹¹ PO1 0.0KG/H
MANL RES -1.24 PPM
¹¹¹¹ PO1 0.0KG/H
MANL FLO -24.9 %
¹¹¹¹ PO1 0.0KG/H
Set Dosage
1.00
Alarm Status
None
Set PO1(Valve)
¹¹¹¹ 0.0KG/H
Alarm Status
None
Set Dosage
1.00
These hidden screens,
shown with a grey border,
are accessed by holding -
at the screen immediately
preceding the Alarm Status screen.
Which screen is appropriate
depends on the active Control Type.
FIGURE 2
HIDDEN SCREENS

7
III. CONFIGURATION MODE
How to Enter: See Section I.2b on page 3.
Overview: This mode is used to set permanent control parameters. With the exception of Dosage and
Residual (or other) Set Point, all other parameters are set in this mode.
NOTE: The following is a flow chart showing each parameter in this mode. Notes follow the chart with
explanations of each parameter. The selection of “Control Type” in the first parameter will determine which
of the three branches below is followed.
NOTE: Refer to Section VII for explanation and definitions of terms.
I. Control Type: Select the control mode that will be used to operate the PID Controller.
a. Flow Pace (PV1) OR
b. Residual Control (or pH or ORP) (PV2)
c. Compound Loop (PV1 and PV2)
1. Flow Pace Setup (Flow Input/PV1): Control and display settings for PV1 input.
1a. Flow Input Name. FLO, PV1, H2O, PRO
1b. Input Signal Loss. Maintain Output / Zero Output (Select One)
1c. Select the units for display. %, GPM, MGD, LPM, MLD, GPD, M3/H, LPH
1d. Select Decimal Location. (0, 0.0, 0.00, 0.000)
1e. Enter Full Scale Flow Value. (xxxx)
NOTE: Calibrates Flow Input signal from zero to this Full Scale value.
1f. Enter Threshold Value. (In the units from point b above.)
NOTE: This parameter should be set at zero (0) unless you do not want the valve to respond until this
threshold value is reached by the 4-20mA flow input signal. The valve will then scale the input from
threshold to full scale as (0-100% of input signal).
1g. Select Flow Filter Time. (xxxx) (seconds)
NOTE: Controller will apply a filter to the input signal over this time span.
1h. Set Low Level Set Point. (in units chosen above)
NOTE: When the flow signal drops below this level the Low Flow Alarm will trip.
2. Residual (or ORP or pH) Control Setup (Residual/PV2): Control and display settings for PV2 input.
2a. Residual Input Name. RES, ORP, pH, PV2
2b. Input Signal Loss. Maintain Output / Zero Output (Select One)
2c. Select units for display. PPM, MG/L, mV, pH, NTU, %
2d. Select Decimal Location. (0, 0.0, 0.00, 0.000)
2e. Full Scale Res Value. (+ or - xxxx)
2f. Minimum Value. (+ or - xxxx)
2g. Res Filter Time. (xxxx) (seconds)
NOTE: Controller will apply a filter to the input signal over this time span.
2h. Filter Constant. (Value range from 0 to 1.0. Default is 0.7)
2i. Low Set Point Limit. (xxxx)

8
NOTE: Will trip Low Set Point Alarm if reading or Set Point becomes lower.
2j. High Set Point Limit. (xxxx)
NOTE: Will trip High Set Point Alarm if reading or Set Point becomes higher.
2k. Res Dead Band. (xxxx) (This is in PV2 units)
NOTE: Controller will set a dead band this amount above and below set point. As long as the signal
is within this dead band the HC-220 will consider it to be on set point.
2l. Select Integral Value. (xxx) (%) (0.0 to 100.0) (Default value 10.0)
NOTE: Value used in Residual and Compound Loop calculation for control. This controls the
magnitude of each adjustment. If the value is too high then the residual will overshoot the set point.
If it is too low then the residual will never reach the set point.
2m. Residual Lag Time. (xxxx) (seconds)
NOTE: Lag time for obtaining accurate Residual/ORP readings after feed changes. The HC-220 will
make residual adjustments only once per lag time (1-1800 seconds).
3. Compound Mode Only:
3a. Flow Stop. (xx)(%)(0 to 99%)
Used only in Compound Loop Control to prevent output adjustment based on the residual set point
when water flow has stopped. This feature allows the operator to enter a PV1 (Flow) value below
which the HC-220 will zero its output.
3b. Residual Reset Value. The residual reset value allows you to set a Flow/PV1
value (0-100% Flow/PV1 full scale) below which the residual signal will be ignored. When the
Flow/PV1 value rises above the entered value, the unit will automatically resume considering the re-
sidual signal.
NOTE: This feature is for use in Compound Loop Control only. This feature is included in units
shipped after January 2009.
3c. Fixed or Variable Lag Time. Selecting Fixed lag will keep the lag time constant at
all times. Selecting Variable lag will cause the program to constantly adjust the lag time based on the
current flow value and the Flow at Variable Lag Time Parameter. (Variable lag time increases as flow
decreases.) Two variable lag types are available. Single point variable lag is ok for systems with small
variations in flow rates, but two point variable lag should be used for systems with a big variation in
water flow rates (more than 2:1 change in flow).
3d. Maximum Lag Time. Default/Max. Allowable is 1800 sec./30 min.
3e. Flow at Variable Lag Time. Actually time the lag time and enter the average value
for the Flow Meter in units above during this test. The HC-220 will then scale the lag time according
to changes in the Flow input signal.
4. Display of Chemical Feed Rate (Linearized): (Purpose) Calibrate for display purposes.
4a. Choose Output Units. %, PPD, GR/H, KG/H, GPH, GPM, GPD, LPM, LPH
4b. Choose Decimal Position. 0, 0.0, 0.00, 0.000
4c. Choose Full Scale Value. xxxx
NOTE: If in Set-Point (RES) or Compound Loop Control Mode, PO1 units must be set to a minimum
of 3 integers. If PO1 Full Scale is set to a number less than 100, one decimal position must be used.
5. Chemical Feed Type (Accounts for opposite effect of SO2and Cl2on Res/ORP/pH):
5a. Select Chemical Type. (Cl2– If it has positive effect on Res/ORP/pH)
(SO2– If it has negative effect on Res/ORP/pH)

9
IV. INPUT AND OUTPUT CALIBRATION
How to Enter/Exit: The input and output calibration screens are hidden. See Figure 1 - Configuration Mode
for how to find and enter the PV1 (Flow) and PV2 (Residual) input calibration screens as well as the PO1
output calibration screens.
Overview: The analog inputs are calibrated by Hydro Instruments. Should the inputs need to be recalibrated
the following steps explain how to calibrate the AI1 through AI4 analog inputs.
1. Input Electrical Calibration: AI1 through AI4 are calibrated electrically.
2. Output Electrical Calibration: AO1 and AO2 (4-20mA) are electrically calibrated.
NOTE: Navigate to the HIDDEN “OUT” screens on Figure 1 to electrically calibrate the four input
channels AI1 through AI4 and two output channels AO1 and AO2. These are all 4-20mA input and output
channels.

10
FIGURE 3
OPERATION MODE
AUTO RES -1.24 PPM
¹¹¹¹ PO1 0.0KG/H
AUTO FLO -24.9 %
¹¹¹¹ PO1 0.0KG/H AUTO MANL
AUTO MANL
“Dual Input Feed Fwd” AUTO
Enter Password
220
Set Dosage
1.00
Alarm Status
None
increments of 1
0.01 increments
MANL RES -1.24 PPM
¹¹¹¹ PO1 0.0KG/H
MANL FLO -24.9 %
¹¹¹¹ PO1 0.0KG/H MANL AUTO
MANL AUTO
“Dual Input Feed Fwd” MANL
Set PO1(Valve)
¹¹¹¹ 0.0KG/H
Alarm Status
None
Enter Password
220 increments of 1
0.1 increments
Set Dosage
1.00 0.01 increments
Enter Password
220
AUTO RES -1.24 PPM
¹¹¹¹ PO1 0.0KG/H
AUTO FLO -24.9 %
¹¹¹¹ PO1 0.0KG/H
Set Point Res/ORP
2.00 PPM
Set Dosage
1.00
Alarm Status
None
AUTO MANL
AUTO MANL
0.01 increments
increments of 1
0.01 increments
“Compound Loop” AUTO
MANL RES -1.24 PPM
¹¹¹¹ PO1 0.0KG/H
MANL FLO -24.9 %
¹¹¹¹ PO1 0.0KG/H
Set Point Res/ORP
2.00 PPM
Set PO1(Valve)
¹¹¹¹ 0.0KG/H
Alarm Status
None
Enter Password
220
MANL AUTO
MANL AUTO
0.01 increments
increments of 1
0.1 increments
Set Dosage
1.00 0.01 increments
“Compound Loop” MANL
AUTO RES -1.24 PPM
¹¹¹¹ PO1 0.0KG/H
Set Point Res/ORP
2.00 PPM
Alarm Status
None
Enter Password
220
AUTO MANL
increments of 1
0.01 increments
“Residual/ORP” AUTO
MANL RES -1.24 PPM
¹¹¹¹ PO1 0.0KG/H
Set PO1(Valve)
¹¹¹¹ 0.0KG/H
Alarm Status
None
Enter Password
220
MANL AUTO
increments of 1
0.1 increments
Set Point Res/ORP
2.00 PPM 0.01 increments
“Residual/ORP” MANL
AUTO FLO -24.9 %
¹¹¹¹ PO1 0.0KG/H
Set Dosage
1.00
Alarm Status
None
Enter Password
220
AUTO MANL
increments of 1
0.01 increments
“Flow Pacing” AUTO
MANL FLO -24.9 %
¹¹¹¹ PO1 0.0KG/H
Set PO1(Valve)
¹¹¹¹ 0.0KG/H
Alarm Status
None
Enter Password
220
MANL AUTO
increments of 1
0.1 increments
Set Dosage
1.00 0.01 increments
“Flow Pacing” MANL

11
V. OPERATION MODE
How to Enter/Exit: See Section I.2a on page 3.
Overview: When the HC-220 is in use it should be in this mode. This mode displays input values, output
value and alarm conditions. This mode is used to set dosage, Residual (or ORP or pH) setpoint
and for manual override of chemical feed rate.
1. Flow Pacing Mode: Operation in direct proportion to a flow meter signal.
1a. Select Automatic or Manual Control Mode.
Choose AUTO/MANL (Use
to change selection)
DISPLAY (PV1) H2O Flow Rate (%, GPM, MGD, …)
DISPLAY (PO1) Chemical Feed Rate (%, PPD, …)
1b. Select the Dosage level which is desired.
DOSAGE 0.01-9.99 adjustable with and keys
1c. In Manual Mode the feed rate will be displayed and can be adjusted with and keys.
DISPLAY (PO1) Chemical Feed Rate (%, PPD, …)
1d. Alarm messages are displayed.
DISPLAY ALARMS (none, Flow Signal Loss, …)
2. Residual/ORP/pH Control Mode: Control by Residual, ORP, or pH input only.
2a. Select Automatic or Manual Control Mode.
Choose AUTO/MANL (Use
to change selection)
DISPLAY (PV2) PV2 Reading (PPM, MGL, mV, pH)
DISPLAY (PO1) Chemical Feed Rate (%, PPD, GPH, …)
2b. Select the Residual/ORP/pH Set Point which is desired.
PV2 Set Point (SV2) Adjustable with and keys
2c. In Manual Mode the feed rate will be displayed and can be adjusted with and keys.
DISPLAY (PO1) Chemical Feed Rate (%, PPD, …)
2d. Alarm messages are displayed.
DISPLAY ALARMS (none, Res/ORP Signal Loss, …)
3. Compound Loop Mode: (PID Control by Flow and Residual/ORP/pH inputs)
3a. Select Automatic or Manual Control Mode.
Choose AUTO/MANL (Use
to change selection)
DISPLAY (PV1) H2O Flow Rate (%, GPM, MGD, …)
DISPLAY (PO1) Chemical Feed Rate (%, PPD, …)
3b. Select Automatic or Manual Control Mode.
Choose AUTO/MANL (Use
to change selection)
DISPLAY (PV2) PV2 Reading (PPM, MGL, mV, pH)
DISPLAY (PO1) Chemical Feed Rate (%, PPD, GPH, …)
3c. Select the Residual/ORP Set Point which is desired.
PV2 Set Point (SV2) Adjustable with and keys
3d. Select the Dosage level which is desired.
DOSAGE 0.01-9.99 adjustable with and keys

12
VI. ALARM & OUTPUT FEATURES
1. 4-20 mA Output – Two 4-20mA outputs are provided at terminals AO1/V- and AO2/V-. These signals
are proportional to the chemical feed rate.
2. RS-485 Modbus Communication – This feature allows the HC-220 to be monitored and controlled by
a computer. See Hydro Instruments’ Modbus Communication Setup document for further details.
3. Alarm Relay Output – Power ratings: 10A @ 277VAC, 12A @ 125VAC or 5A @ 250VAC.
4. Acknowledgement – Press the “minus” key to acknowledge the alarm.
NOTE: Any of the below contacts will activate this alarm relay. The alarm is non latching.
Control Mode Alarm Condition Description Action
Flow Pacing Flow Signal Loss PV1 Signal below 3 mA Valve Close or Hold Position**
Flow Pacing Low Flow PV1 Signal below set point* None
Residual/ORP Res/ORP Signal Loss PV2 Signal below 3 mA Valve Close or Hold Position**
Residual/ORP Low Set Point PV2 Signal below set point*** None
Residual/ORP High Set Point PV2 Signal above set point*** None
Compound Loop Flow Signal Loss PV1 Signal below 3 mA
Switch to Residual/ORP Condn 1
Compound Loop Low Flow PV1 Signal below set point* None
Compound Loop Res/ORP Signal Loss PV2 Signal below 3 mA Switch to Flow Pacing Control
Compound Loop Low Set Point PV2 Signal below set point*** None
Compound Loop High Set Point PV2 Signal above set point*** None
* See Section III.1.i. – User defined flow signal level below which alarm is activated.
** See Section III.1.b. and III.2.b. – User selects this parameter in Configuration Mode.
*** See Section III.2.i. & III.2.j. – User selects an acceptable range for Residual/ORP/pH.
3e. In Manual Mode the feed rate will be displayed and can be adjusted with and keys.
DISPLAY (PO1) Chemical Feed Rate (%, PPD, …)
3f. Alarm messages are displayed.
DISPLAY ALARMS (none, Flow Signal Loss, …)

13
VII. REFERENCE TERMS
1. Contact – On/off channel used as an alarm output. Also referred to as a relay.
2. Compound Loop Control – Refers to the P.I.D. control method. This method controls chemical feed rate
using both flow and residual/other (proportional and setpoint) inputs. The method essentially reacts in
proportion to the flow input, while it also adjusts the chemical feed rate to maintain a (residual/other) set
point.
3. Dead Band – This is a dead band around the set point. As long as the residual/other reading is within (+ or -)
this amount from the set point, the device will consider the system to be at set point. This is used to avoid
excessive, continual adjustment of the valve position that would reduce the life of the mechanical parts.
4. Dosage – In the context of flow control dosage this is a factor that is multiplied to the incoming flow signal.
For example, if incoming flow signal is at 50% (12 mA) and the dosage is set to 2.0 then the HC-220 will
adjust chemical feed to 100% (in Flow Pacing Control) or in the same example if dosage is set to 0.5 the
HC-220 will adjust chemical feed to 25% (in Flow Pacing Control).
5. Filter – In the context of input signal (PV1 or PV2) filter time this is a time over which the signal will be
continually averaged. This is used to smooth out the input signal and reduce motion of the valve that
could be caused by rapid fluctuations of the input signals (electrical noise or other rapid signal fluctuations).
6. Flow Pacing Control – Refers to the proportional control method. In this method the valve adjusts
chemical feed rate in proportion to input signal.
7. Full Scale (In terms of Input Full Scale) – The value (in %, Flow, Residual, or other expressed in appro-
priate units) represented by a 20 mA (or 5 V) input signal.
8. Integral – A factor used in calculation of adjustments to chemical feed rate in both Residual/Other and
Compound Loop Control. This value ranges between 0 and 100%. Essentially the program makes a
calculation of how much the chemical feed rate needs to be adjusted in order to reach set point and this
factor. The integral setting determines what percentage of this adjustment will be done in each step (i.e.,
if it is set to 15% then the valve will move 15% of the calculated amount). If the integral is set at 0% it
will never move. If the integral is set at 100% it will probably adjust too much each time and continually
overshoot the set point.
9. Lag Time – In the context of Residual/other lag time this is the time that elapses between a change in
chemical feed rate and the change in input signal PV2 from the Residual/Other analyzer (considering a
constant water flow). This time is the sum of the time it takes the water to travel from the injection point
to the analyzer plus the time it takes the analyzer to react to a change.
10. Minimum (In terms of Input Minimum) – The value (in %, Flow, Residual, or Other expressed in ap-
propriate units) represented by a 4 mA (or 1 V) input signal.
11. Mode – In terms of the three modes of the HC-220. (See Section I.1)
12. ORP – Oxidation Reduction Potential. The units of measure are mV. It can be positive and negative.
In terms of the HC-220, discussion is focused on the 4-20mA or 1-5V signal representing the ORP value.
13. Parameter – In this manual, this term refers to that which is shown on the display screen simultaneously.
The HC-220 is moved from one parameter to the next using the “up arrow” and “down arrow” keys.
14. PO1 (Process Output 1) – Represents the chemical feed through the valve.
15. Proportional – Equivalent to Flow Pacing. The valve reacts in proportion to the incoming signal on
channel PV1.
16. PV1 (Process Variable 1) – Refers to analog input one. Normally this is used for the proportional input
signal.

14
17. PV2 (Process Variable 2) – Refers to analog input two. Normally this is used for the set point input signal.
18. Relay – In this manual, this refers to the alarm output contact. When an alarm condition is satisfied the
contact (relay) will close the N/O (Normally Open) relay and open the N/C (Normally Closed) relay.
19. Residual – Refers to either Free or Total Chlorine Residual reading. The units of measure are either mg/l
or PPM and it must be a positive number or zero. In terms of the HC-220, discussion is focused on the
4-20mA or 1-5V signal representing the Residual value.
20. Residual/Other Control – Refers to the Set Point control method. In this method, the user indicates
the desired Residual or Other set point and the HC-220 will automatically adjust chemical feed rate to
maintain that set point.
21. Set Point – In this manual, this refers to a desired value for the Residual or Other reading. It is the specific
Residual or Other reading that is chosen by the user and that the user would like the system to maintain.
22. Threshold – In this manual, this refers to the parameter selected in PV1 input setup (See Section III.1f.).
This is the value of PV1 that will be considered as zero PV1 input for control purposes. For PV1 between
minimum and threshold, the control calculations will consider PV1 to be zero. For control purposes, the
HC-220 will rescale the PV1 input (linearly from 0 – 100%) from PV1 Threshold to PV1 Full Scale.
The threshold value is expressed in the units used to display the PV1 input.

15
VIII. TROUBLESHOOTING
A. FACTORY DEFAULT – If there is an electronics problem that cannot be solved by any of the below
efforts, then you might consider performing a factory default. However, when this is done all calibration
data is lost and must be reset. Therefore it is best to try other steps first because you will have to go
through both the Advance Calibration Mode and the Configuration Mode to enter all control and calibration
settings. The factory default can eliminate glitches that may arise in the software by erasing all settings
and entering the factory default settings. In order to perform a factory default follow these steps:
1. Turn off the power to the HC-220.
2. Hold both the “up arrow” key and the “down arrow” key on the front panel.
3. While holding both keys, turn on the power to the HC-220.
NOTE: After reapplying the factory defaults you will have to re-calibrate the controller’s input and
output signals.
B. POSSIBLE PROBLEMS and Recommended Steps to take:
1. Insufficient or Excessive Chemical Feed in Proportional/Flow Pacing Control.
a. Adjust Dosage Level – See Section V.1b. Increase dosage for more chemical feed and decrease
dosage for less.
b. Check Items 1a. – 1d. above – If actual chemical feed remains low, then check the suggestions in
item 1a. through 1d. above.
2. Failure to reach set point in Residual/ORP or Compound Loop Control.
a. Lag Times – The lag times set in section III.2.m or III.3.a through III.3.c may be too long for the
system.
b. Integral – The integral value set in section III.2.l may be too low. If it is too low then the HC-220
will not react quickly enough to reach set point.
c. Dead Band – The dead band set in section III.2.k may be too large. The valve will consider set
point met if Residual/Other remains within this amount of set point.
3. Repeated Overshooting of Set Point in Residual/Other or Compound Loop Control.
a. Lag Times – The lag times set in section III.2.m or III.3.a through III.3.c may be too short for the
system.
b. Integral – The integral value set in section III.2.l may be too high. If it is too high then the HC-220
will react too quickly and it will repeatedly drive the Residual/Other reading below and above set
point.
c. Dead Band – The dead band set in section III.2.k may be too small. The valve will only consider
set point met if Residual/Other remains within this amount of set point. If it is set to zero the
HC-220 will almost never be satisfied and will continue to adjust the valve position.
iv. Thread the Valve Stem hand tight onto the Intermediate Valve Stem.

16
FIGURE 4 – HC-220 Controller Electronics
Date: 2018-10-24-v1
Dwg. No. HC-220-
CONTROLLERHC-220- CONTROLLER
Table of contents
Popular Controllers manuals by other brands
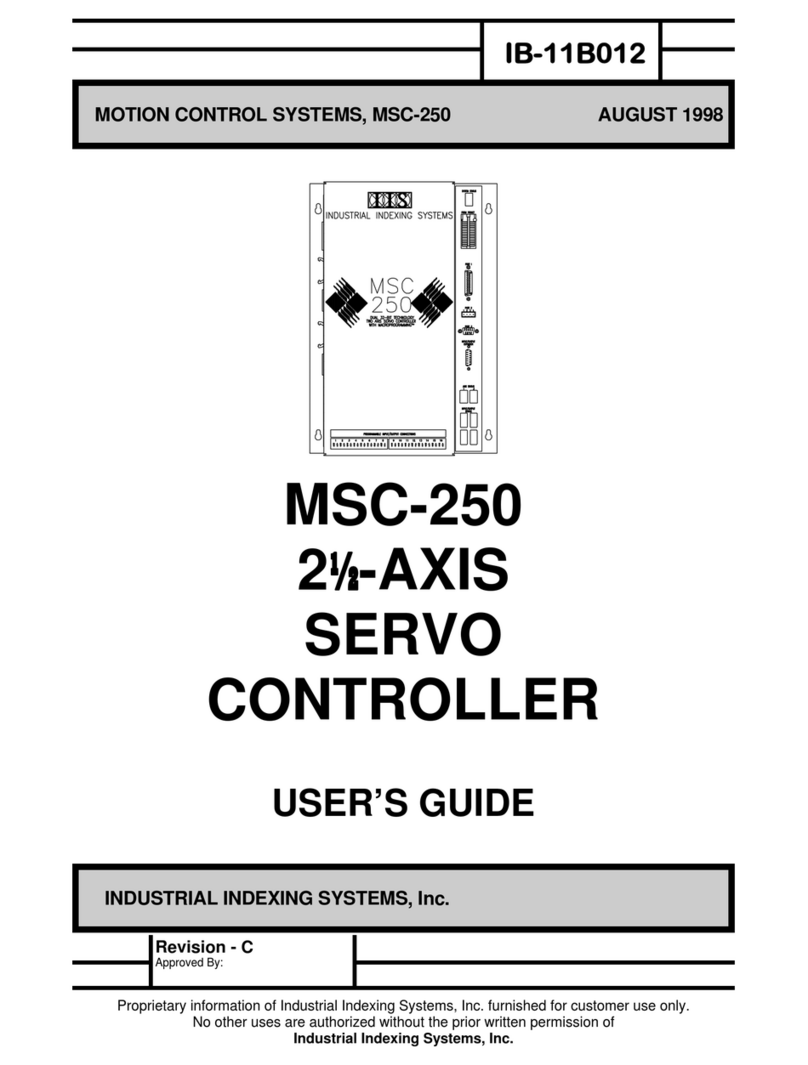
Industrial Indexing Systems
Industrial Indexing Systems MSC-250 user guide

Mitsubishi Electric
Mitsubishi Electric NZ2GN2S-D41P01 user manual
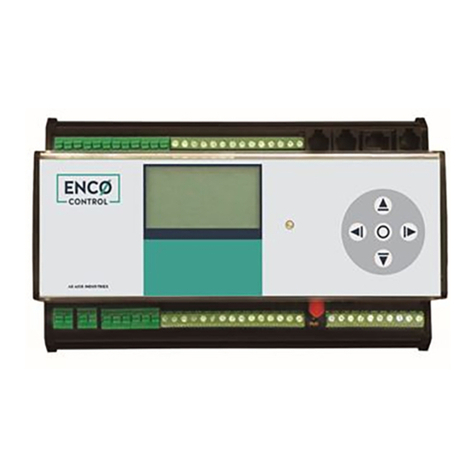
Enco
Enco Control Technical description
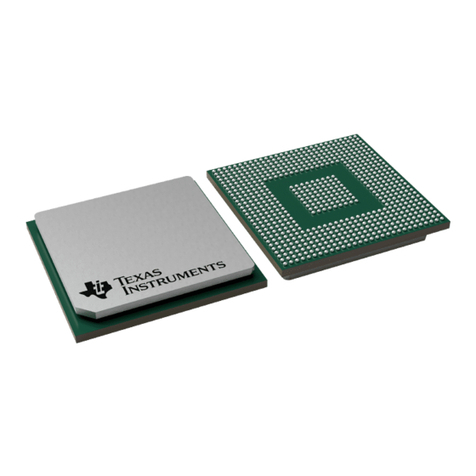
Texas Instruments
Texas Instruments TMS320C6455 user guide
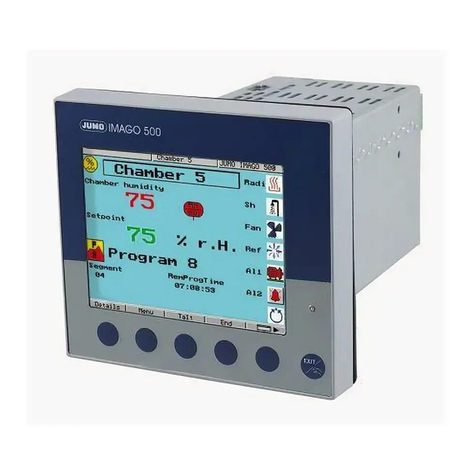
JUMO
JUMO IMAGO 500 Interface description
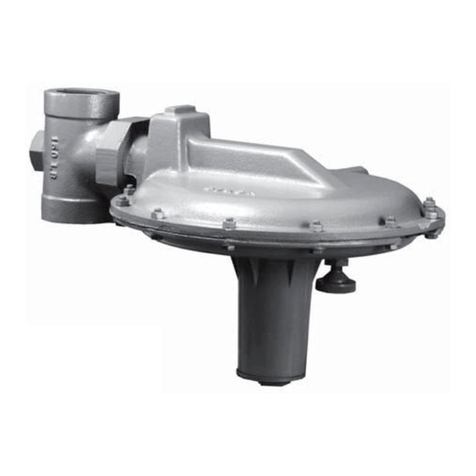
Emerson
Emerson Fisher Y696 instruction manual