HYVST SR100 User manual

PRESSURE ROLLER
INSTRUCTION MANUAL
Note: This manual contains important warnings and
instructions, Please read and retain for reference
SR100
SR200

1
Safety Precautions
This manual contains information that must be read and understood before using the equipment.
When you come to an area that has one of the following symbols, pay particular attention and
make certain to heed the safeguard.
WARNING
This symbol indicates a potential hazard that may cause serious injury or loss of life. Important
safety information will follow.
CAUTION
This symbol indicates a potential hazard to you or to the equipment. Important information that
tells how to prevent damage to the equipment or how to avoid causes of minor injuries will follow.
NOTE: Notes give important information which should be given special attention.
WARNING
HAZARD: Injection injury - A high pressure fluid stream produced by this equipment can
pierce the skin and underlying tissues, leading to serious injury and possible
amputation. See a physician immediately.
DO NOT TREAT AN INJECTION INJURY AS A SIMPLE CUT! Injection can lead to
amputation. See a physician immediately.
The maximum operating range of the roller extensions is 3600 PSI / 24.8 MPa fluid pressure.
PREVENTION:
•NEVER aim the gun at any part of the body.
•NEVER allow any part of the body to touch the fluid stream. DO NOT allow body to touch a
leak in the fluid hose.
•NEVER put hand in front of the gun. Gloves will not provide protection against an injection
injury.
•ALWAYS lock the gun trigger, shut pump off, and release all pressure before servicing,
cleaning the tip or guard, changing tip, or leaving unattended. Pressure will not be released
by turning off the motor. The PRIME/SPRAY valve must be turned to PRIME to relieve the
pressure. Refer to the PRESURE RELIEF PRESSURE described in the pump manual.
•ALWAYS keep tip guard in place while spraying. The tip guard provides some protection but
is mainly a warning device.
•ALWAYS remove the spray tip before flushing or cleaning the system.
•Paint hose can develop leaks from wear, kinking and abuse. A leak can inject material into
the skin. Inspect the hose before each use.
•NEVER use a spray gun without a trigger lock and trigger guard in place.
•All accessories must be rated at or above the maximum operating pressure range of the prayer.
This includes spray tips, guns, extensions, and hose.

2
NOTE TO PHYSICIAN:
Injection in the skin is a serious traumatic injury. It is important to treat the injury as soon
as possible. DO NOT delay treatment to research toxicity. Toxicity is a concern with some
exotic coatings injected directly into the blood stream. Consultation with a plastic surgeon or
reconstructive hand surgeon may be advisable.
HAZARD: EXPLOSION AND FIRE - Solvent and paint fumes can explode damage can
occur.
PREVENTION:
•Provide extensive exhaust and fresh air introduction to to keep the air within the spray area
free from accumulation of flammable vapors.
•Avoid all ignition sources such as static electricity sparks, electrical appliances, flames, pilot
lights, hot objects, and sparks from connecting and disconnecting power cords or working
light switches. Do not smoke in spray area.
•Fire extinguisher must be present and in good working order.
•Place spray at least 25 feet (7.6m) from the spray object in a well ventilated area (and more
hose if necessary). Flammable vapors are often heavier than air. Floor area must be extremely
well ventilated. The pump contains arcing parts that emit sparks and can ignite vapors.
•The equipment and objects in and around the spray area must be properly grounded to
prevent static sparks.
•Use only conductive or grounded high pressure fluid hose. Gun must be grounded through
hose connections.
•Power cord must be connected to a grounded circuit.
•Always flush unit into a separate metal container, at low pump pressure, with spray tip
removed. Hold gun firmly against side of container to ground container and prevent static
sparks.
•Follow material and solvent manufacturer's warnings and instructions.
•Use extreme caution when using materials with a flashpoint below 70°F (21°C).
Flashpoint is the temperature that a fluid can produce enough vapors to ignite.
•Plastic can cause static sparks. Never hang plastic to enclose a spray area. Do not use plastic
drop cloths when spraying flammable materials.
•Use lowest possible pressure to flush equipment.
GAS ENGINE(WHEREAPPLICABLE)
Always place sprayer outside of structure in fresh air. Keep all solvents away from engine exhaust.
Never fill fuel tank with a running or hot engine. Hot surface can ignite spilled fuel. Always attach
ground wire from pump to a grounded object. Refer to engine owner’s manual for complete safety
information.
HAZARD: EXPLOSION HAZARD DUE TO INCOMPATIBLE MATERIALS-will cause
severe injury or property damage.
PREVENTION:
•Do not use materials containing bleach or chlorine.
•Do not use halogenated hydrocarbon solvents such as bleach, mildewcide, methylene
chloride and 1,1,1 - trichloroethane. They are not compatible with aluminum.
•Contact your coating supplier about the compatibility of material with aluminum.

3
HAZARD: HAZARDOUS VAPORS- Paints, solvents, insecticides, and other materials can
be harmful if inhaled or come in contact with body. Vapors can cause severe
nausea, fainting, or poisoning.
PREVENTION:
•Use a respirator or mask if vapors can be inhaled. Read all instructions supplied with the
mask to be sure it will provide the necessary protection.
•Wear protective eyewear.
•Wear protective clothing as required by coating manufacturer.
HAZARD: GENERAL-Can cause severe injury or property damage.
PREVENTION:
•Read all instructions and safety precautions before operating equipment.
•Follow all appropriate local, state, and national codes governing ventilation, fire prevention,
and operation.
•Use only manufacturer authorized parts. User assumes all risks and liabilities when using
parts that do not meet the minimum specifications and safety devices of the pump
manufacturer.
•Before each use, check all hoses for cuts, leaks, abrasion or bulging of cover. Check for
damage or movement of couplings. Immediately replace the hose if any of those conditions
exist. Never repair a paint hose. Replace with a grounded high-pressure hose.
•All hoses, swivels, guns, and accessories must be pressure rated at or above the maximum
operating range of the sprayer.
•Do not spray outdoors on windy days.
•Wear clothing to keep paint off skin and hair.
•Always unplug cord from outlet before working on equipment (electric units only).
General Description
There are two types of roller extensions described in this manual—the spray roller assembly and
the inner feed roller assembly. These roller extensions allow the use of airless spray equipment in
areas where traditional spray application is not possible. Read and follow this manual carefully for
proper setup, operating instructions, and safety information.

4
Operation
WARNING
This equipment produces a fluid stream at extremely high pressure . Read and understand
the warnings in the Safety Precautions section at the front of this manual as well as the
airless sprayer and spray gun manuals before operating this equipment.
Setup
Perform the following procedure to prepare the spray system foe operation.
WARNING
Make sure all airless hoses and spray guns are electrically grounded and rated at or above
the maximum operating range of the sprayer.
1. Set up the airless sprayer. Refer to the instructions in the sprayer’s Owner’s Manual.
CAUTION
Always keep the trigger lock on the spray gun in the locked position while preparing the
system.
2. Using a wrench , attach a minimum of 50’of 1/4”nylon airless spray hose to the sprayer.
Tighten securely.
3. Attach the opposite end of the hose to the airless spray gun. Using two wrenches (one on the
gun and one on the hose), tighten securely.
4. With the tip and tip guard off the gun, start the sprayer. Flush and prepare the spray system
according to the sprayer’s Owner’s Manual. Inspect the spray system to make sure that all
fittings are secure and that there are no leaks.
5. Perform the“Pressure Relief Procedure”described in the sprayer’s Owner’s Manual.
6. Based on the job conditions, attach either the spray roller assembly or the inner feed roller
assembly. Tighten securely with a wrench.
7. Place a gasket on the male end of the angle adapter and thread it into the double-nut end of
the extension pole assembly. Tighten securely with a wrench.
8. Place a gasket into the female end of the angle adapter and thread it onto the diffuser of the
airless spray gun. Tighten securely with a wrench.
WARNING
Make sure the airless sprayer is off, the trigger lock on the spray gun is in the locked
position, and all pressure is relieved from the system before changing roller extension
configuration.
Painting with a Spray Roller Assembly
1. Install the tip assembly into the tip guard on the spray roller assembly.
2. Position the tip so that a horizontal spray pattern will apply material to the surface just below
the roller cover.

5
3. Start up the airless sprayer. Follow the startup procedure and
safety precautions outlined in the airless sprayer’s Owner’s
Manual.
4. Adjust the fluid pressure on the sprayer until the spray is
completely atomized. Always spray at the lowest pressure
necessary to get the desired results.
NOTE: The spray tip determines the size of spray pattern
and coverage. When more coverage is needed, use a
large tip instead of increasing fluid pressure.
5. To clear a clogged tip:
a. Rotate the tip 180°so that the arrow on the tip handle is
pointing opposite the spray direction.
b. Trigger the gun once into a waste bucket so that the
pressure can blow the clog out.
CAUTION
Never pull the trigger more than once at time with the tip in the reverse position.
c. Continue this procedure until the tip is clear of the clog.
6. When applying material to the surface, use the following technique:
a. Roll with an up and down motion while maintaining contact between the roller and the
surface.
b. Spray during the downward stroke until the roller is parallel with the floor. At this point,
release the trigger and continue to roll to the bottom of the stroke. During the upward stroke,
overlap and back-roll the downward stroke.
Application Technique

6
NOTE: Never spray during the upward stroke. This will result in an uneven finish.
NOTE: The use of a tip with a larger orifice is assembly. He large tip size will reduce the
chance of clogs and can be supported by most pumps. The recommended fan width
is a 14’’ pattern, which will result in an 8’’fan due to the close positioning of the tip
to the surface.
NOTE: Standard 9’’roller covers can be used with the spray roller assembly.
Painting with an Inner Feed RollerAssembly
1. Start up the airless sprayer. Follow the startup procedure and safety precautions outlined in
the airless sprayer’s Owner’s Manual.
2. Adjust the fluid pressure on the sprayer to the lowest setting.
3. Trigger the spray gun with short bursts until material begins to come through the roller cover.
4. Begin moving the roller until material is evenly distributed throughout the roller cover.
5. Trigger the spray gun with short bursts as material is needed.
NOTE: Keep the roller cover wet during operation. Do not roll the cover dry as this will slow
production.
Cleanup
WARNING
Special cleanup instructions for use with flammable solvents:
•Always flush spray gun preferably outside and at least one hose length from spray pump.
•If collecting flushed solvents in a one gallon metal container, place it into an empty five
gallon container, then flush solvents.
•Area must be free of flammable vapors.
•Follow all cleanup instructions.
CAUTION
The sprayer, hose, and gun should be cleaned thoroughly after daily use. Failure to do so
permits material to build up, seriously affecting the performance of the unit.
WARNING
Always spray at minimum pressure with the gun nozzle tip removed when using mineral
spirits or any other solvent to clean the sprayer, hose, or gun. Static electricity buildup may
result in a fire or explosion in the presence of flammable vapors.
1. Follow the“Pressure Relief Procedure”outlined in the airless sprayer’s owner’s manual.
2. Follow the“Cleanup”procedure outlined in the airless sprayer’s and spray gun’s owner’s
manual.
3. Clean the roller cover and spray tip in the appropriate solvent.
4. Store the roller extension in a clean, dry area.

7
Parts List
SR100
1. End Sleeve; 2. Roller cover; 3. 9’’ paint distributor and Auger; 4. End cap and seal
assembly; 5. 9’’ roller tube assembly; 6. Plastic position holder; 7. Plastic baffle plate;
8. Extension pole assembly, Ф24, 90cm/Ф24, 180cm(optional); 9. HYVST Gun.
SR200
1. End Sleeve; 2. 9’’ paint distributor; 3. End cap and seal assembly; 4. Roll cover;
5. 9’’roller tube assembly; 6. Plastic position holder; 7. Pivot screw; 8. 517 tip; 9. Tip
guard; 10. Swivel connector; 11. Extension pole assembly, Ф24, 90cm/Ф24, 180cm(optional);
12.HYVST Gun.

8
Warranty
HYVST warrants all equipment referenced in this document which is manufactured by HYVST and bearing its
name to be free from defects in material and workmanship on the date of sale to the original purchaser for use.
With the exception of any special, extended, or limited warranty published by HYVST, HYVST will, for a period
of twelve months from the date of sale, repair or replace any part of the equipment determined by HYVST to be
defective. This warranty applies only when the equipment is installed, operated and maintained in accordance with
HYVST’s written recommendations.
This warranty does not cover, and HYVST shall not be liable for general wear and tear, or any malfunction,
damage or wear caused by faulty installation, misapplication, abrasion, corrosion, inadequate or improper
maintenance, negligence, accident, tampering, or substitution of non-HYVST component parts. Nor shall HYVST
be liable for malfunction, damage or wear caused by the incompatibility of HYVST equipment with structures,
accessories, equipment or materials not supplied by HYVST, or the improper design, manufacture, installation,
operation or maintenance of structures, accessories, equipment or materials not supplied by HYVST.
This warranty is conditioned upon the prepaid return of the equipment claimed to be defective to an authorized
HYVST distributor for verification of the claimed defect. If the claimed defect is verified, HYVST will repair or
replace free of charge any defective parts. The equipment will be returned to the original purchaser transportation
prepaid. If inspection of the equipment does not disclose any defect in material or workmanship, repairs will be
made at a reasonable charge, which charges may include the costs of parts, labor, and transportation.
THIS WARRANTY IS EXCLUSIVE, AND IS IN LIEU OF ANY OTHER WARRANTIES, EXPRESS OR
IMPLIED, INCLUDING BUT NOT LIMITED TO WARRANTY OF MERCHANTABILITY OR WARRANTY
OF FITNESS FOR A PARTICULAR PURPOSE.
HYVST’s sole obligation and buyer’s sole remedy for any breach of warranty shall be as set forth above. The
buyer agrees that no other remedy(including, but not limited to, incidental or consequential damages for lost
profits, lost sales, injury to person or property, or any other incidental or consequential loss) shall be available. Any
action for breach of warranty must be brought within two (2) years of the date of sale.
HYVST MAKES NO WARRANTY, AND DISCLAIMS ALL IMPLIED WARRANTIES OF
MERCHANTABILITY AND FITNESS FOR A PARTICULAR PURPOSE, IN CONNECTION WITH
ACCESSORIES, EQUIPMENT, MATERIALS OR COMPONENTS SOLD BUT NOT MANUFACTURED
BY HYVST. These items sold, but not manufactured by HYVST (such as electric motors, switches, hose, etc.), are
subject to the warranty, if any, of their manufacturer. HYVST will provide purchaser with reasonable assistance in
making any claim for breach of these warranties.
In no event will HYVST be liable for indirect, incidental, special or consequential damages resulting from HYVST
supplying equipment hereunder, or the furnishing, performance, or use of any products or other goods sold hereto,
whether due to a breach of contract, breach of warranty, the negligence of HYVST, or otherwise.

All written and visual data contained in this document reflects the latest product information
available at the time of publication. HYVST reserves the right to
make changes at any time without notice.
YONGKANG OCEAN IMP & EXP CO.,LTD.
ADD: 23 F, Jinsong Mansion, Headquarter Center,
Yongkang City, Zhejiang Province, China.
Tel:+86 579 87172043
Fax:+86 579 87172042
Http:// www.hyvst.com
www.sprayertech,com
This manual suits for next models
1
Table of contents
Popular Tools manuals by other brands
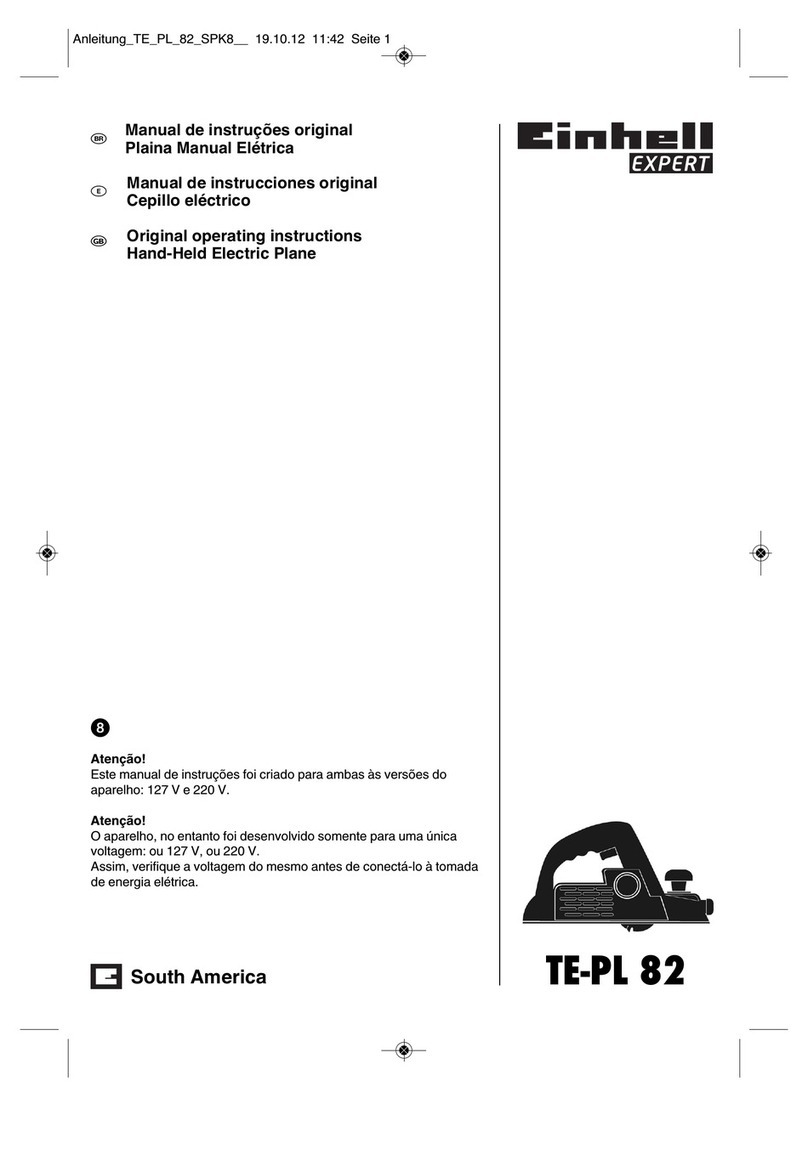
EINHELL Expert
EINHELL Expert TE-PL 82 Original operating instructions

Westfalia
Westfalia 41 42 68 instruction manual
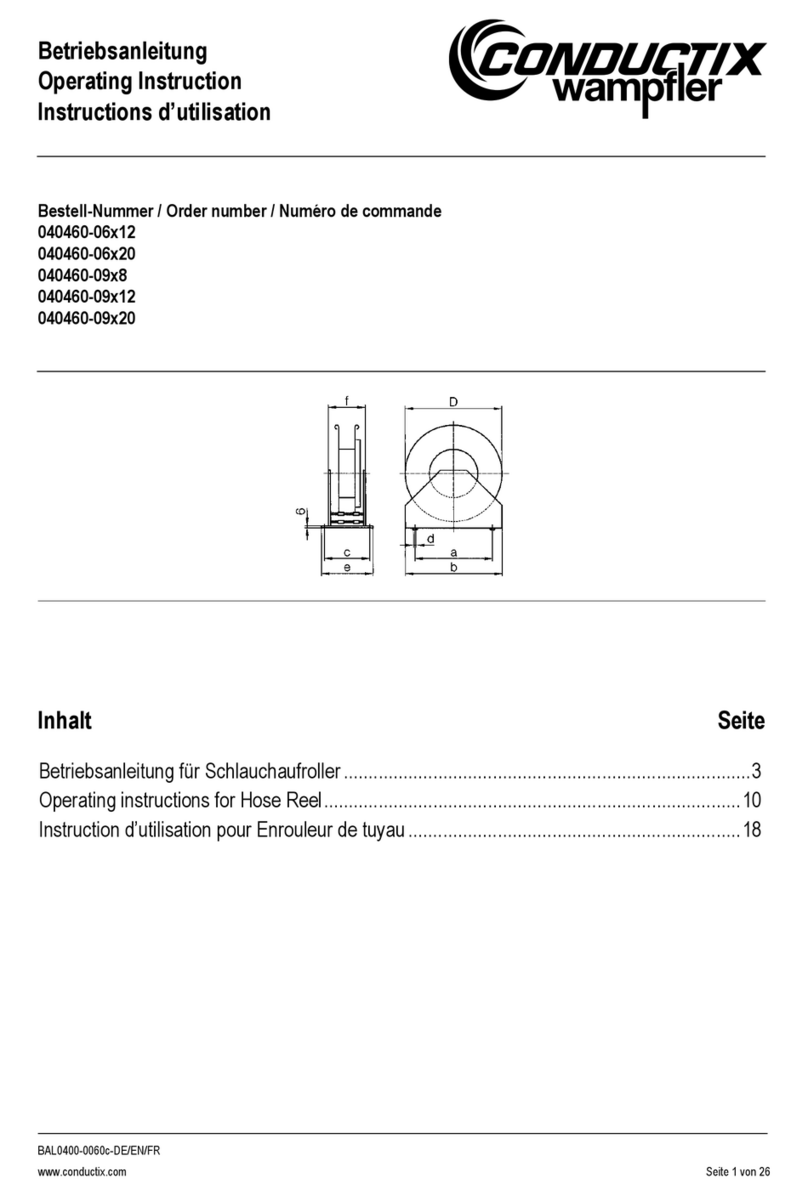
Conductix-Wampfler
Conductix-Wampfler 040460-06x12 operating instructions
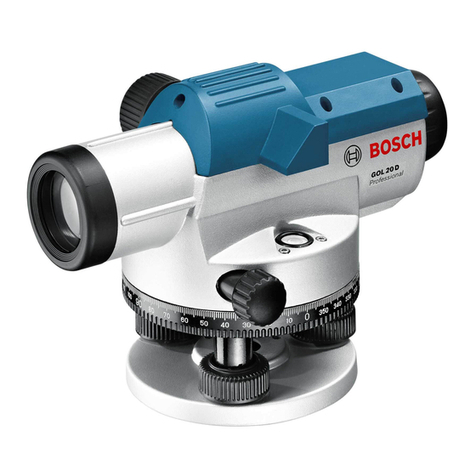
Bosch
Bosch GOL 20 D Professional Original instructions
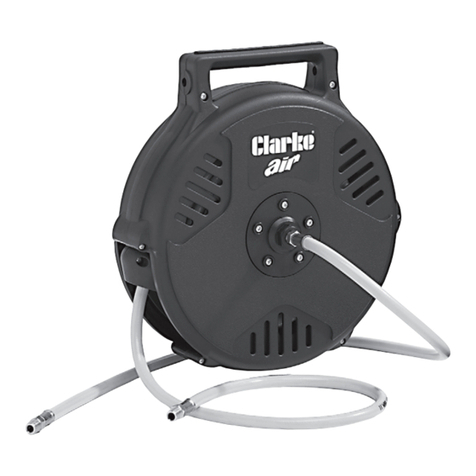
Clarke
Clarke Air CHR9P Instructions for use
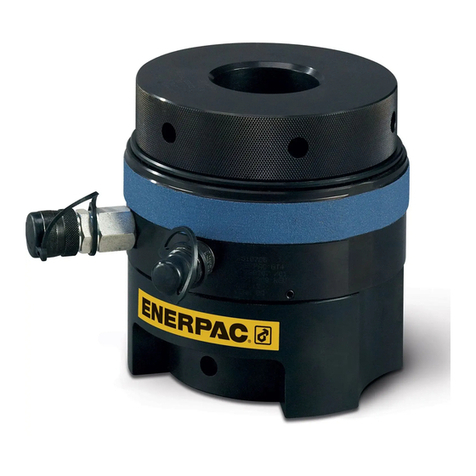
Enerpac
Enerpac GT Series instruction sheet