IBC SL Series Installation instructions

INSTALLATION &
OPERATING MANUAL
Commercial Condensing Boiler
SL 26-260 G3
SL 40-399 G3
WARNING
If the information in this manual is not followed exactly, a fire or explosion may result causing
property damage, personal injury, or loss of life.
Do not store or use gasoline or other flammable vapors and liquids or other combustible
materials in the vicinity of this or any other appliance.
If you smell gas:
Do not try to light any appliance.
Do not touch any electrical switch; do not use any phone in your building.
Immediately call your gas supplier from a nearby phone. Follow the gas supplier’s
instructions.
If you cannot reach your gas supplier, call the fire department. Installation and service must
be performed by a qualified installer, service agency or the gas supplier.

Water quality
Warning
Water quality has a significant impact on the lifetime and performance of a boiler's heat
exchanger.
Improperly prepared water in a heating circuit may cause damage to the heat exchanger
through fouling or corrosion. Repeated or uncontrolled water fills will increase the potential
for damage.
High levels of dissolved solids or minerals may precipitate out of the fluid onto the hottest part
of the heat exchanger, impairing heat transfer and resulting in overheating and premature
failure. The amount of solids that may form on the heat exchanger will depend on the degree
of hardness and the total water volume in the system. A high water volume system with a low
hardness count may cause as much damage as a system with less volume and higher
hardness, so it is recommended to treat water so as to reduce dissolved solids to 30 ppm.
Other water chemistry allowable limits are as follows:
Acidity pH is to be between 6.6 and 8.5
Chloride is to be less than 125 mg/l
Iron is to be less than 0.3 mg/l
Cu less than 0.1 mg/l
Conductivity is to be less than 400μS/cm at 77°F (25°C)
7 grains/ gal (120 ppm)
Important: Ensure that these limits are acceptable for the other water-side components in
the system.
Shipped with the boiler:
1 x Wall mounting bracket (P-9100)
1 x Condensate trap assembly
1 x 30 psig pressure relief valve
1 x Outdoor temperature sensor
6 x ¼" x 2 ½" Lag screws/w flat washers

Safety information
Manual safety markings
Danger
Points out an immediate hazardous
situation that must be avoided to
prevent serious injury or death.
Warning
Points out a potential hazardous
situation that must be avoided to
prevent serious injury or death.
Caution
Points out a potential hazardous
situation that must be avoided to
prevent possible moderate injury
and/or property damage.
Note
Points out installation, maintenance and
operational notes to enhance efficiency,
longevity and proper operation of the
boiler.
Important safety instructions
Installation, start-up and servicing of IBC boilers must be performed by competent, qualified, licensed
and trained heating technicians.
Failure to read and comply with all instructions and applicable national and local codes may result in
hazardous conditions that could result in property damage and injury to occupants, and in extreme
cases to death. Keep instructions near the air handling appliance for future reference.
Danger
Should overheating occur or the gas supply fails to shut off, do not turn off or disconnect
the electrical supply to the pump. Instead shut off the gas supply at a location external to
the appliance.
Danger
Do not store or use gasoline or other flammable vapors or liquids in the vicinity of this or
any other appliance. If you smell gas vapors, do not try to operate any appliance - do not
touch any electrical switch or use any phone in the building. Immediately, call the gas
supplier from a phone located remotely. Follow the gas supplier’s instructions, or if the
supplier is unavailable, contact the fire department.
3
Safety information

Warning
If the boiler is likely to be exposed to fluid temperatures below 34°F (1°C), use a method
to prevent freezing of condensate. Contact the factory for further information.
Warning
Do not use this boiler if any part has been under water. Immediately call a qualified
service technician to inspect the boiler and to replace any part of the control system and
any gas control that has been under water.
Warning
Improper installation, adjustment, alteration, service or maintenance can cause
property damage, personal injury, or loss of life. Read and understand the entire
manual before attempting installation, start-up, operation, or service. Installation and
service must be performed only by an experienced, skilled installer or service agency.
Failure to follow all instructions in the proper order can cause personal injury or death.
Read all instructions, including all those contained in component manufacturers’
manuals before installing, starting up, operating, maintaining, or servicing the
appliance.
Warning
Disconnect power supply before any wiring/service is performed. Failure to do so could
result in damage to appliance and/or electric shock.
Caution
The boiler must be installed so that electrical components are not exposed to water
during operation.
Known Corrosive Contaminants to Avoid
Cements and glues Refrigerant leaks from cracks in coils
Paint or varnish removers Sodium chloride or potassium chloride used for
water softening
Adhesives used to fasten building products
and other similar products
Chemicals in perming solutions
Chlorinated waxes or cleaners Chlorofluorocarbon chemicals found in spray cans
Chlorine-based swimming pool chemicals Antistatic dryer sheets in clothes dryers
Hydrochloric acid or muriatic acid used in
household cleaning and stain removal
Chlorine-type bleaches, detergents, and cleaning
solvents found in household laundry rooms
Calcium chloride used for snow clearing
4
Section: Safety information

Contents
Safety information 3
Manual safety markings 3
Important safety instructions 3
Specifications 5
Cabinet dimensions 6
SL 26-260 G3 6
SL 40-399 G3 7
Connection specifications 9
1.0 Introduction 11
1.1 Standard features and benefits 12
1.2 Warranty 12
2.0 Before installation 13
3.0 Installation 15
3.1 Code requirements 15
3.2 Removing an existing boiler 15
3.3 Determining location of the appliance 16
Best installation conditions 17
3.4 Mounting the boiler 17
3.5 Connecting the vent and air intake pipes 18
3.6 Installation clearances 19
3.7 Exhaust venting and air intake 20
3.7.1 Venting code 21
3.7.2 Venting options 21
3.7.3 Exhaust vent material 21
3.7.4 Direct vent 22
3.7.5 Rooftop vent termination 27
3.7.6 Sidewall vent termination 29
3.7.7 Combustion air filtration system 37
3.8 Closet installations 37
3.9 Installing the condensate trap 37
3.10 Installing a condensate neutralizer 41
3.11 Water Piping 42
1

3.11.1 General piping best practices 46
3.11.2 System piping 46
3.12 Gas piping 55
3.12.1 Gas pressure 55
3.13 Electrical connections 56
3.13.1 Power management, quality and electrical protection 57
3.13.2 120VAC line-voltage hook-up 57
3.13.3 Other wiring 58
3.13.4 Zone valve hook-up 59
3.13.5 Thermostat / sensor wiring 59
3.13.6 Thermostat heat anticipator 59
4.0 About the boiler controller 61
4.1 Controller 61
4.2 Control interface 62
5.0 Before operating the boiler 63
Important pre-ignition checks 63
Checklist for electrical conditions, ducting and water connections 63
6.0 Boiler operation 65
6.1 Lighting and shutting down the boiler 65
6.2 Testing the ignition safety shutoff 66
6.3 Commissioning 66
6.3.1 Checking a boiler's fuel source 67
6.3.2 Performing a fuel conversion 67
6.3.3 Adjusting the gas valve 69
7.0 Service and maintenance 73
7.1 Maintenance checklist for homeowner 73
7.2 Maintenance checklist for heating contractor 73
7.2.1 Touchscreen boiler controller 74
7.2.2 General boiler maintenance 74
7.3 Replacing the fan, gas valve, and burner 78
7.3.1 Replacing the fan 80
7.3.2 Replacing the gas valve 82
7.3.3 Replacing the burner 85
2
Section: Contents

7.4 Cleaning the condensate trap 89
8.0 Troubleshooting 93
8.1 Electronic components 93
8.1.1 Temperature sensors 93
8.1.2 Fan 94
8.1.3 Water pressure sensor 95
8.1.4 Safety and Ignition Module (SIM) 95
8.2 Troubleshooting error messages 96
8.2.1 Maximum ignition trials error 97
8.2.2 Hi Limit cut-off temperature error 97
8.2.3 Low Water Cut-off error 98
8.2.4 Aux. Interlock 1 or 2 98
8.3 Miscellaneous touchscreen controller errors 98
8.3.1 Ignition issues 99
8.3.2 Temperature issues 101
8.3.3 Miscellaneous issues 102
8.3.4 Cycling issues 103
Appendices 105
Wiring diagrams 105
V-10 Controller electrical diagram 105
Internal wiring diagram 106
Sequence of operations 107
Exploded views of boiler parts 108
Boiler part diagrams - SL 26-260 G3 108
Boiler part diagrams - SL 40-399 G3 111
Installation & Commissioning Report 115
3

Intentionally left empty

5
Specifications
Boiler Specification SL 26-260 G3 SL 40-399 G3
CSA Input (Natural Gas or Propane) 26 - 260 MBH 40 - 399 MBH
CSA Input (Natural Gas or Propane) 7.6 - 76.2 kW 11.7 - 117 kW
CSA Output 24.9 - 239 MBH 38.4 - 383 MBH
CSA Output 7.31 - 70.0 kW 11.2 - 112 kW
A.F.U.E 95% -
Combustion Efficiency - 96%
Thermal Efficiency (ANSI/AHRI-1500) - 96%
Minimum gas supply pressure (Natural Gas or Propane) 4" w.c. 4" w.c.
Maximum gas supply pressure (Natural Gas or Propane) 14" w.c. 14" w.c.
Minimum Ambient temperature 32°F / 0°C 32°F / 0°C
Maximum Ambient temperature 122°F / 50°C 122°F / 50°C
Max. relative humidity (non-condensing) 90% 90%
Minimum water temp. 34°F / 1°C 34°F / 1°C
Maximum water temp. (electronic hi-limit) 190°F / 88°C 190°F / 88°C
Max. ΔT - supply/return (electronic fence) 40°F 40°F
Max. Water Temperature Lockout Limit 201°F / 94°C 201°F / 94°C
Power use (120Vac/60Hz) @ full fire (less pumps) 127 W 190 W
Weight (empty) 162 lbs / 74 Kg 240 lbs /110 Kg
Heating Surface Area 22.71 ft2/ 2.11 m236.56 ft2/ 3.40 m2
Pressure vessel water content 4.64 USG/ 17.6 L 6.66 USG/ 25.2 L
Maximum boiler flow rate 25 USgpm 45 USgpm
Minimum boiler flow rate 6 USgpm 20 USgpm
Maximum operating water pressure* 30 psig/ 206 kPa 80psig/ 551 kPa
Minimum water pressure 8 psig / 55 kPa 8 psig / 55 kPa
Approved installation altitude - ASL 0 - 12,000’ 0 - 12,000’
Maximum equivalent vent length , each side (vent & air
intake) - Natural gas or propane. Air intake options:
either direct vent or indoor supply
200’ (3") 200’ (4")
* Boilers are shipped with a 30 psig pressure relief valve.

Ignition Stages Timings
Fan Pre-purge 15 seconds
Trial for Ignition 4 seconds
Flame Failure Response <0.8 second
Table 1 Ignition stages timings
Cabinet dimensions
SL 26-260 G3
Figure 1 : Front and side view - SL26-260 G3
6
Section: Specifications

Figure 2 : Top view - SL 26-260 G3 Figure 3 : Bottom view - SL 26-260 G3
SL 40-399 G3
Figure 4 : Front and side view - SL40-399 G3
7
SL 40-399 G3

Figure 5 : Top view - SL 40-399 G3 Figure 6 : Bottom view - SL 40-399 G3
8
Section: Specifications

Connection specifications
The following table displays the required connection specifications.
SL 26-260 G3 SL 40-399 G3
A Flue Outlet 3" Schedule 40 4" Schedule 40
B Combustion Air Inlet 3" Schedule 40 4" Schedule 40
C Safety Relief Valve and Air
Vent
¾" NPT - F
D LCD Display 2¼" x 4"
E Water Outlet 1½” NPT-M
F Water Inlet 1½” NPT-M
G Knock-outs (8) ½"
H Gas Inlet ¾" NPT-F
I Condensate Outlet ¾" Hose
Table 2 Connections
9
Connection specifications

Intentionally left empty

11
1.0 Introduction
The gas-fired modulating boilers are low pressure, fully condensing units with a variable input range.
Approved as “Category IV” vented appliances, the boilers use direct vent (sealed combustion) or
indoor combustion air.
Figure 7 View from the front - SL 26-260 G3
Figure 8 View from the front - SL 40-399 G3

1.1 Standard features and benefits
High thermal efficiency
Turn-down ratio 10 to 1
Control of up to 5 pumps – 1 boiler pump and 4 separate load pumps
Outdoor reset control
Load combining – simultaneous operation of two similar water temperature loads
Load zoning – simultaneous operation of up to four loads with the same control settings
Ability to manage and/or operate in a network of up to 24 IBC SL boilers
Internet/LAN connectivity for software updates and remote access through the IBC V-10
Portal
BACnet over IP compatible
Easy-to-use touchscreen
1.2 Warranty
For residential applications, IBC offers a 5-year warranty on all parts against defects in materials
or workmanship and failures due to thermal shock. In addition, IBC offers a heat exchanger
limited warranty with registration, according to the following terms:
0 - 10 years (100% coverage)
11+ years (25% coverage).
IBC offers a limited heat exchanger warranty with no registration of 0-5 years (100% coverage).
For non-residential applications, IBC offers a 5-year warranty on all parts against defects in
materials or workmanship and failures due to thermal shock. In addition, IBCoffers a heat
exchanger limited 10 year warranty with registration, according to the following terms:
0 - 5 years (100% coverage)
6 - 7 years (50% coverage)
8 years (40% coverage)
9 years (30% coverage)
10 years (20% coverage).
To view the full warranty statement for the SL 26-260 G3 and the SL 40-399 G3, and to register your
product, go to ibcboiler.com.
12
Section: Introduction

13
2.0 Before installation
Before installing the appliance, it is important to review and observe the following checklist of
precautions:
Precautions Check
Care must be taken to properly size the boiler for its intended use. Prolonged full fire run
time, over-sizing or under-sizing, and incorrect flow rates through the appliance can lead to
increased maintenance costs, equipment stress and premature failure.
□
Ensure you install the appliance where the combustion air source is not subject to
chemical fouling or agricultural vapors. Exposure to corrosive chemical fumes such as
chlorinated and/or fluorinated hydrocarbons can reduce the life of a boiler. Cleaners,
bleaches, air fresheners, refrigerants, aerosol propellants, dry-cleaning fluids, de-greasers
and paint-removers all contain vapors that can form corrosive acid compounds when
burned in a gas flame. Airborne chlorides such as those released with the use of laundry
detergents are also to be avoided.
□
Locate the appliance where water leakage will not result in damage to the area. If there is
no suitable location, install a suitable drain pan under the boiler. Do not install above
carpeting.
□
At a new construction site, or during renovations, protect the appliance from drywall dust or
other construction related contaminants. Draw combustion air from a clean source (e.g.,
outdoors) and isolate the boiler from interior dust sources. Do not seal boiler case
openings directly when firing - allow for air circulation and ventilation in the immediate
area.
□
Place the exhaust outlet 12" minimum above the down-turned intake to avoid exhaust re-
ingestion.
□
For sidewall venting options, place the inlet and exhaust terminations on the same side of
the building. The elevation of both pipes can be raised in “periscope style” after passing
through the wall to gain required clearance above grade and snow level.
□
If using the indoor combustion air option, ensure combustion air openings to the boiler
room remain unblocked and free of obstructions.
□
Examine the condensate outlet to ensure proper disposal of condensate will occur during
operation. If condensates are to be discharged into building drain piping materials that are
subject to corrosion, a neutralization package must be used.
□
Ensure that the pressure relief valve is installed with no valves or other means of isolation
between its inlet and the boiler. Make sure the relief valve outlet is piped with unobstructed
piping (minimum ¾" diameter) to a safe discharge location.
□
If the appliance is likely to be exposed to fluid temperatures below 34° F (1° C), a method
of protection to prevent freezing of condensate should be employed. Contact the factory
for further information.
□
When the appliance is in operation, assess the impact of the steam plume typical of a
condensing boiler's exhaust terminal. Generally, intake and exhaust pipes should
terminate at a rooftop or sterile wall location. Boiler condensate is corrosive. Protective
□

Precautions Check
measures must be taken to prevent corrosion damage to metal roofs or other metal
building components in contact with the condensate. Keep exhaust plumes well away from
all building air intakes including those of neighboring properties.
Caution
Care must be taken to properly size the boiler for its intended use. Prolonged full fire run
time, over-sizing or under-sizing, and incorrect flow rates through the boiler can lead to
increased maintenance costs, equipment stress and premature failure.
14
Section: Before installation

15
3.0 Installation
Refer to the Specifications section for dimensional drawings and connection specifications. Use these
drawings to find a suitable location for the appliance.
3.1 Code requirements
The appliances are tested and certified under CSA 4.9 / ANSI Z21.13. Below are the code
requirements for every installation.
Canada US
Conform to local codes, or in the absence of
these, with the latest editions of CAN/CGA
B149.1 and the Canadian Electrical Code Part 1
CSA C22.2 No. 1.
Where required by jurisdiction, installation must
conform to the Standard for Controls and Safety
Devices for Automatically Fired Boilers,
ANSI/ASME CSD-1.
If there is any conflict, follow the more stringent
regulations.
Conform to the current National Fuel Gas Code
ANSI Z223.1 and the National Electrical Code
ANSI/NFPA 70.
Where required by jurisdiction, installation must
conform to the Standard for Controls and Safety
Devices for Automatically Fired Boilers,
ANSI/ASME CSD-1.
If there is any conflict, follow the more stringent
regulations.
Table 3 Code requirements by country
3.2 Removing an existing boiler
When an existing boiler is removed from a common venting system, the common venting system
may be too large for proper venting of the appliances that remain connected to it. When resizing
any portion of the common venting system, use the minimum size according to the appropriate
tables in the National Fuel Gas Code, ANSI Z223.1 - latest edition. In Canada, follow the B149.1
Installation Code.
When removing an existing boiler, the following checks must be carried out for each of the
appliances still connected to the common exhaust system, by operating them one at a time:
Seal any unused opening in the common venting system.
Visually inspect the venting system for proper size and horizontal pitch. Determine that there
is no blockage or restriction, leakage, corrosion and other deficiencies that could cause an
unsafe condition.
(Where practical) Close all doors and windows such as doors adjacent to appliances
remaining connected to the common venting system and other spaces of the building.

Turn on clothes dryers and any appliance not connected to the common venting
system.
Turn on any exhaust fans, such as range hoods and bathroom exhausts, so they
will operate at maximum speed. Do not operate a summer exhaust fan.
Close fireplace dampers.
Place in operation the appliance being inspected.
Follow the lighting instructions.
Adjust the thermostat so that the appliance operates continuously.
After determining that each appliance remaining connected to the common venting
system properly vents when tested as outlined above, return doors, windows, exhaust
fans, fireplace dampers and any other gas-burning appliance to their previous condition.
Any improper operation of the common venting system should be corrected, so the
installation conforms with the National Fuel Gas Code, ANSI Z223.1 - latest edition. In
Canada, all installations must conform with the current CAN/CGA - B149.1-10
Installation Code and/or local codes.
3.3 Determining location of the appliance
The boilers are designed and approved for indoor installation (wall or rack mounting) in areas
such as an alcove, basement, or utility room. These areas should have a surrounding
temperature of 32 °F (0°C) to 122 °F (50 °C) and less than 90% relative humidity.
Danger
Do not common vent appliances with other existing appliances or with a new
appliance.
Warnings
Keep the area around a boiler clear of combustible materials, gasoline, and
other flammable vapors and liquids.
Ensure combustion air is not drawn from areas containing corrosive air such as
swimming pools or spas, including air directly next to outdoor pools and spas.
Ensure that a boiler is not exposed to water leaks from piping or components
located overhead, including condensation from uninsulated cold water lines
overhead.
Protect the gas ignition system components from water (dripping, spraying,
rain, etc.) during appliance operation and when servicing (pump replacement,
condensate trap servicing, control replacement, etc.).
Ensure that combustible materials do not make contact with exposed water
piping and associated components (relief valves, circulators, etc.). Check local
codes for required clearances and/or provide adequate insulation.
16
Section: Installation
This manual suits for next models
2
Table of contents
Other IBC Boiler manuals
Popular Boiler manuals by other brands

Westen
Westen STAR CONDENS Instruction manual for users and fitters
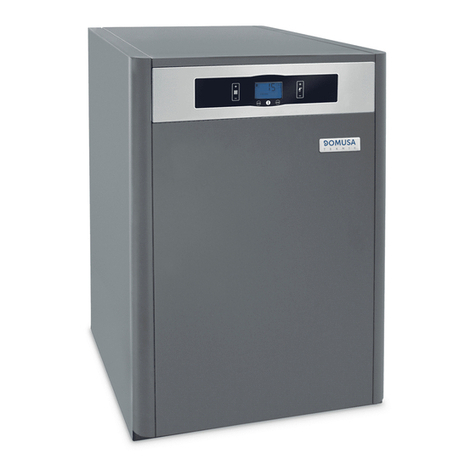
Trianco
Trianco TRO Evolution System Series Installation and operating instructions

Thermona
Thermona THERM 90 KD.A MANUAL FOR INSTALLATION, OPERATION AND MAINTENANCE
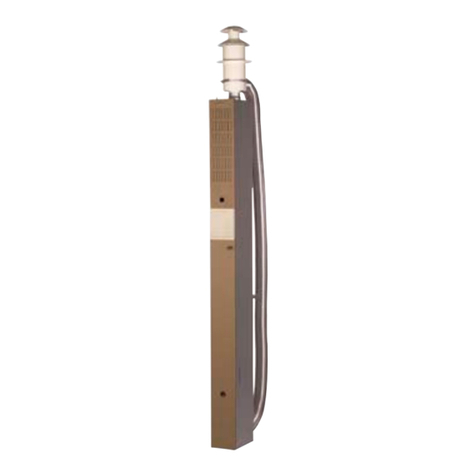
Alde
Alde Comfort 2923-2928 Service manual
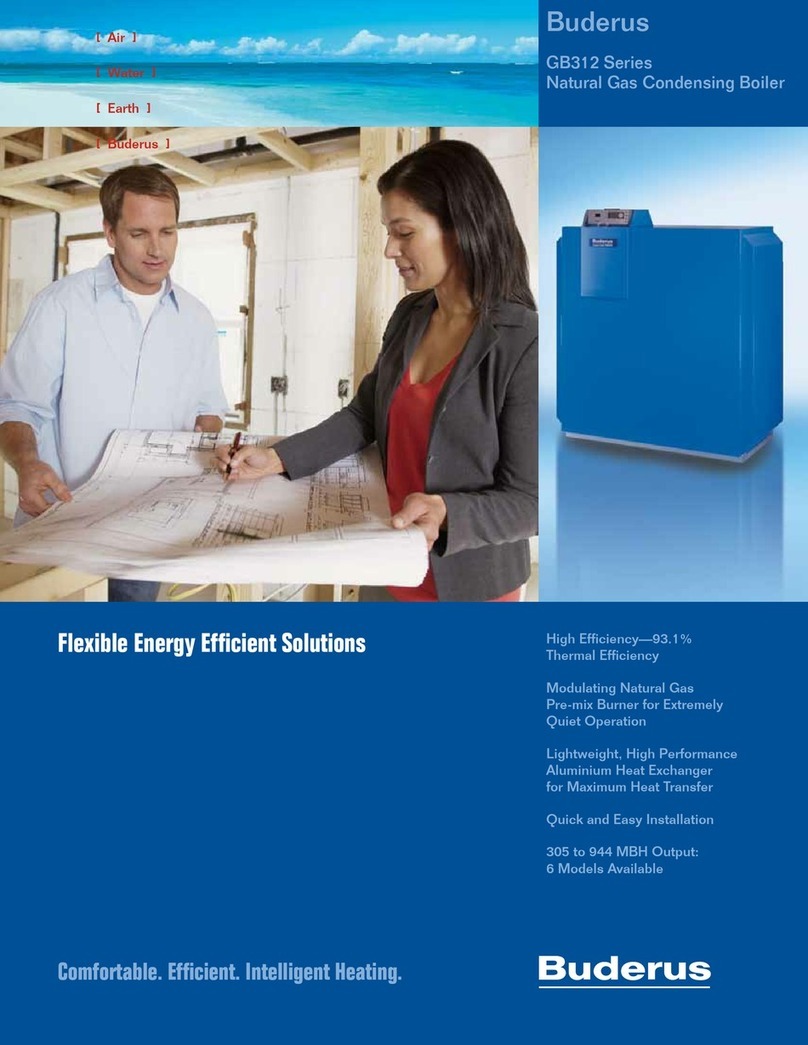
Buderus
Buderus GB312 Series Brochure & specs
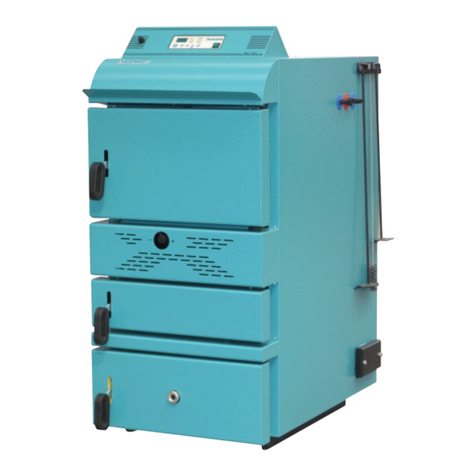
Centrometal
Centrometal Bio-Tec Series Technical manual