IKA ICC control User manual

2
Item Designation
1 Operator panel and display
2 Mains switch
3 Power socket
4 Buoyage
5Heater
6Stand
7Pt 100 + Pt 1000 temperature sensor
8 Handle
9 Fan
10 RS 232 port
11 USB port
12 Clamp
13 Cable clip
14 External temperature sensor socket
Fig. 1
4
6
7
1
5
8
2
Fig. 2
3
10
7
11
14
9
12
13

3
Contents
EN
Source language: German
Page
Declaration of Conformity.........................................................................................................................4
Explication of warning symbols ................................................................................................................4
Safety instructions ....................................................................................................................................5
General information ..............................................................................................................................................5
Fluids.....................................................................................................................................................................6
Correct use................................................................................................................................................7
Use .......................................................................................................................................................................7
Range of use (indoor use only)...............................................................................................................................7
Unpacking.................................................................................................................................................7
Unpacking.............................................................................................................................................................7
Delivery scope .......................................................................................................................................................7
Preparations..............................................................................................................................................7
Setting up .............................................................................................................................................................7
Filling and draining ................................................................................................................................................7
Fluid (Standard information for IKA®fluid..............................................................................................................8
Operator panel and display .......................................................................................................................9
Commissioning........................................................................................................................................10
Setting the safety temperature ...............................................................................................................11
Operation................................................................................................................................................11
Working screen at the time of delivery.................................................................................................................11
Explanation of symbols on the working screen.....................................................................................................11
Menu navigation and structure............................................................................................................................12
Menu (Details).....................................................................................................................................................14
Interface and output ...............................................................................................................................16
Maintenance and cleaning ......................................................................................................................18
Error codes..............................................................................................................................................19
Accessories..............................................................................................................................................20
Technical data .........................................................................................................................................21
Warranty .................................................................................................................................................22
Pump performance curve ........................................................................................................................22

4
Explication of warning symbols
DANGER
CAUTION
WARNING
NOTICE
Indicates an imminently hazardous situation, which, if not avoided, will result in death, seri-
ous injury.
Indicates a potentially hazardous situation, which, if not avoided, can result in death, seri-
ous injury.
Indicates a potentially hazardous situation, which, if not avoided, can result in injury.
Indicates practices which, if not avoided, can result in equipment damage.
Reference to exposure to a hot surface!
Hot surface!
WARNING
Declaration of Conformity
We declare under our sole responsibility that this product corresponds to the regulations 2014/35/EU, 2006/42/EC,
2014/30/EU and 2011/65/EU and conforms with the standards or standardized documents: EN 61010-1, EN 61010-2-010,
EN 61010-2-051, EN 61326-1, EN 60529, DIN 12876-1 and EN ISO 12100.

5
General information:
• Read the operating instructions completely before
starting up and follow the safety instructions.
• Keep the operating instructions in a place where it can be
accessed by everyone.
• Ensure that only trained staff work with the device.
• Follow the safety instructions, guidelines, occupational
health, safety and accident prevention regulations.
• Set up the device in a spacious area on an even, stable,
clean, non-slip, dry and fireproof surface.
• Do not operate the device in explosive atmospheres,
with hazardous substances.
• Protect the device and accessories from bumping and
impacting.
• Check the device and accessories for damage before
each use. Do not use damaged components.
• Safe operation is only guaranteed with the accessories
described in the ”Accessories” section.
• The device must only be operated with the original mains
cord.
• The socket for the mains cord must be easily accessible.
• Socket must be earthed (protective ground contact).
• The voltage stated on the type plate must correspond to
the mains voltage.
• The device can only be disconnected from the mains sup-
ply by pulling out the mains plug or the connector plug.
• Disconnect the mains plug before attaching or changing
any accessories.
• Disconnect the mains plug before cleaning, maintenance
and transportation of the unit.
•
The device must only be opened by trained specialists,
even during repair. The device must be unplugged from
the power supply before opening. Live parts inside the
device may still be live for some time after unplugging
from the power supply.
Coverings or parts that can be
removed from the device with-
out the aid of any tools must
be put back on the device again to ensure safe opera-
tion, for example to keep foreign objects and liquids,
etc. from getting into the device.
• The device may only be used as prescribed and as de-
scribed in the operating instructions. This includes op-
eration by instructed specialist personnel.
• When using critical or hazardous materials in your pro-
cesses, IKA®recommends to use additional appropriate
measures to ensure safety in the experiment. For exam-
ple, users can implement measures that inhibit fire or
explosions or comprehensive monitoring equipment.
• Process pathogenic material only in closed vessels under
a suitable fume hood. Please contact IKA®application
support if you have any question.
If the power switch is not with-
in reach when device is operat-
ing, an EMERGENCY STOP
switch that can be easily accessed must be installed in
the work area.
• A laboratory circulator heats and circulates fluid accord-
ing to specified parameters. This involves hazards due to
high temperatures, fire and general hazards due to the
device of electrical energy.
The user safety can not be en-
sured simply with design requirements on the part of the
device.
Further hazard sources may arise due to the type
of tempering fluid, e.g. by exceeding or undercutting
certain temperature thresholds or by the breakage of
the container and reaction with the heat carrier fluid.
It is not possible to consider all eventualities. They re-
main largely subject to the judgment and responsibility
of the operator. For this reason, it may become neces-
sary for user to take other precautionary safety mea-
sures.
• Insucient ventilation may result in the formation of explo-
sive mixtures. Only use the device in well ventilated areas.
The safety circuit (safe tem-
perature) must be adjusted so
that the maximum permissible
temperature cannot be exceeded even in the event of a
fault. Check the safe temperature circuit on a regular ba-
sis (see section “Setting the safety temperature“) .
• Securely fix the ICC immersion circulator for use at the
bath, so that it cannot tip over.
• When device is used for external circulation, extra pre-
caution must be taken for hot fluid leakage due to dam-
aged hose.
• Use suitable hoses for connection.
• Secure hoses and tubes against slippage and avoid kinks.
• Check hoses, tubes and bath at regular intervals for pos-
sible material fatigue (cracks/leaks).
• Mains cable should not get in contact with hot parts
and fluids.
• If you are using plastic bath, observe the permitted
working temperature range and fluids.
Do not start up the device if:
- It is damaged or leaking
-
Cable (not only supply cable) is damaged.
• Be careful when filling a hot bath.
At high operating tempera-
tures, the temperature of hous-
ing parts, surfaces and tubes
can exceed 70 ° C.
Safety instructions
NOTICE
WARNING
WARNING
DANGER
WARNING

6
• Continuous monitoring of the bath and the filling level of
the bath fluid is required, especially at high temperatures.
• To ensure a sucient fluid circulation, the viscosity of
the bath fluid must not exceed of 50mm2/s at the lowest
operating temperature.
If water is used at higher tem-
perature, there is heavy loss of
fluid due to the evaporation.
• Untreated tap water is not recommended. It is recom-
mended to use distilled water or high purity water (ion
exchangers) and add 0.1 g soda (sodium carbonate
Na2CO3) /liter, to reduce corrosive properties.
Risk of burning caused by va-
por or hot water at the outlet
of the cooling coil (accessory).
Do not use the cooling coil with
water at bath temperatures >
95° C.
For bath temperatures > 60°C
make sure that the flow rate
through the cooling coil is high
enough.
Don't use following fluids:
- Untreated tap water
- Acids or bases
- Solutions with halides: chlorides, fluorides, bromides,
iodides or sulfur
- Bleach (Sodium Hypochlorite)
- Solution with chromates or chromium salts
- Glycerine
- Ferrous water.
When changing the bath fluid
from water to a heat transfer
fluid for temperatures above
100 °C, remove the remaining water from the complete
system (including hoses and external devices). When do-
ing this, also open the stopper and union nuts caps of
the pump outputs and inputs and blow compressed air
through all the pump outputs and inputs!
It is dangerous to touch the
heater. The temperature of the
heater can be very high.
• After a power failure during operation, the device may
start automatically (depending on operating mode).
• Transport the device with care.
• Do not transport or empty the bath while it is still hot.
This may result in accidents, especially scalding injuries.
In order to prevent the power
cable from falling into the fluid,
the mains cable must be se-
cured with the cable clamp (13, see Fig. 2).
Fluids:
Beware of the risk of burning
due to delay in boiling!
Only use fluids, which fulfill the
requirements for safety, health
and device compatibility. Be
aware of the chemical hazards that may be associated
with the bath fluid used. Observe all safety warnings for
the fluids.
• Depending on the bath fluid used and the type of opera-
tion, toxic or flammable vapors can arise. Ensure suit-
able extraction.
• Do not use any fluid which may cause dangerous reac-
tions during processing.
• Only use recommended bath fluid. Only use non-acid
and non corroding fluid.
Only process and heat up any
fluid that has a flash point high-
er than the adjusted safe tem-
perature limit that has been set. The safe temperature
limit must always be set to at least 25 ºC lower than the
flash point of the fluid used. Examine regularly the func-
tion of the safety temperature limiter.
Never operate the device with-
out sucient heat carrier fluid!
You should also be careful to
ensure that the minimum clearances and immersion
depths in the fluid are observed. Check the fluid level
detection at a regular basis (see section "Filling and
draining").
WARNING
NOTICE
WARNING
WARNING
WARNING
NOTICE
NOTICE
WARNING
NOTICE
NOTICE
NOTICE
NOTICE

7
Correct use
Use:
Use ICC (Immersion Circulator Compact) control
for heat-
ing and circulating fluids.
Intended Use: Tabletop Device
Range of use (indoor use only):
- Laboratories - Schools
- Pharmacies - Universities
This device is suitable for use in all areas except:
- Residential areas
- Areas that are connected directly to a low-voltage supply
network that also supplies residential areas.
The safety of the user cannot be guaranteed:
- If the device is operated with accessories that are not
supplied or recommended by the IKA®.
- If the device is operated improperly or in contrary to the
IKA®specifications.
- If the device or the printed circuit board are modified by
third parties.
Unpacking
Unpacking:
- Please unpack the device carefully
- In the case of any damage a detailed report must be sent
immediately (post, rail or forwarder).
Transport safety:
Remove the transport protection
under the
buoyage
(4).
Delivery scope:
- ICC control
- Mains cables
- Screwdriver (use for safety circuit)
- USB 2.0 cabel A – micro B
- User guide
- A warranty card.
NOTICE
Preparations
Setting up:
- Securely fix the immersion circulator on the bath.
- Place the device on an even, stable, clean, nonslip, dry
and fireproof surface.
- Keep at least 20 cm of open space at the front and rear
side.
- When a plastic bath is used, please ensure that the heater
does not contact the bath.
- The place for installation should be large enough and
provide sucient air ventilation to ensure the room does
not warm up excessively because of the heat from de-
vice radiates to the environment.
- Do not set up the device in the immediate vicinity of
heat sources and do not expose to sun light.
Filling and draining:
- Connect the mains plug and turn on the device with
mains switch (2).
- The low level icon ( ) appears on the display.
- Fill fluid to the bath.
Note: Pay attention to the fluid level information on
the display:
— Low level
— High level
For draining, please refer to the bath operating instruc-
tions.

8
• Fluid (Standard information for IKA®fluid):
IKA
®Designation
Operating temperature
range for open bath
application
(°C)
Operating temperature
range for closed bath
applications
(°C)
Safety temperature
(°C)
Flash point
(°C)
CF.EG28.N10.80.8
-10 ... 80 -10 … 80 90 115
CF.EG39.N20.80.16
-20 … 80 -20 … 80 90 115
CF.EG44.N25.80.19
-25 … 80 -25 … 80 90 115
CF.EG48.N30.80.22
-30 … 80 -30 … 80 90 115
UF.Si.N30.150.10LV
-30 … 130 -30 … 150 145 n>170
HF.Si.20.200.50
20 … 200 20 … 200 255 >280
HF.Si.20.250.50A
20 … 200 20 … 250 255 >280
H
2
O (Water) o
5 … 95 5 … 95 - -
Customized 1
p
Customized 2
p
Check the suitability of the fluid according to your application.
Nomenclature for IKA
®
fluid:
CF.EG28.N10.80.8 --
(5) Addition information
(4) Kinematic viscosity (8
mm²/s
)
(3) Temperature range (- 10–80 °C)
(2) Chemical composition (Ethylene Glycol 28 %)
(1) Classification (Cooling fluid)
(1) Classification:
HF: Heating Fluid
CF: Cooling Fluid
UF: Universal Fluid
(2) Chemical composition:
Si: Silicone oil
EG: Ethylene Glycol
(3) Temperature range: (
Minimum temperature. Maximum temperature)
N: Negative Temperature
(4) Viscosiy:
Viscosiy at 25 °C for Heating Fluid (HF)
Viscosity at -20 °C for Cooling Fluid (CF)
Viscosity at 25 °C for Universal Fluid (UF)
Dynamic viscosity [mPa•s] is a product of kinematic viscosity [mm²/s] and density [kg/m³] of the fluid divided by 1000.
(5) Additional information:
A: Oil Additives
LV: Low Viscosity
n
Note: for open bath application!
o
Note: Tap water may be unsuitable for operation because the calcium carbonate content may cause calcification.
High purity water (from icon exchangers) and distilled or bi-distilled water are unsuitable for operation due to corrosive
properties of these media. High purity water and distillates are suitable as a medium after adding 0.1 g soda (Na2CO3,
sodium carbonate) per liter of water.
pNote: The limits can be adjusted according to the fluid used.

9
G
B
A
J
K
O
L
M
N
Fig. 3
Operator panel and display
DE
F
HI
Item Designation Function
A ON/OFF button: Switch on/off the circulator.
B Adjustable safety circuit: Adjust the safety temperature limit with delivered screwdriver.
D “Temp” button:
Start/stop the heating function.
E “Temp (+)” button:
Increase the temperature setting value.
F “Temp (-)” button:
Decrease the temperature setting value.
G “OK/Pump” button:
Start/stop the pump function.
Select and open the menu options.
Confirm the menu settings.
H “Pump (+)” button:
Increase the pump speed setting value.
Navigation and changing the setting in the menu.
I “Pump (-)” button:
Decrease the pump speed setting value.
Navigation and changing the setting in the menu.
J "Menu" button:
Press it once: menu option is display.
Press it a second time: back to the working screen.
K "
Back" button: Return to the previous menu level.
L"int/ext" button: Switch between the internal and external temperature display and control.
M
"Timer/Pump" button: Switch between the timer and pump display.
N Graph button: Display time/temperature graph
O Key button:
Lock/unlock keys.

10
Check whether the voltage given on the type plate cor-
responds to the available mains voltage.
The socket used must be earthed
(fitted with earth contact).
If these conditions have been met, the machine is ready
for operation when the mains plug is plugged in.
If these conditions are not met, safe operation is not guar-
anteed and the machine could be damaged.
Observe the ambient conditions (temperature, humidity,
etc.) listed under “Technical Data”.
After switch on the mains switch (2) at the back of the de-
vice or pressing the power key (A), the screen displays the
device designation and the software version after a beep.
Commissioning
Then the working screen in standby status appears and
the device is ready for operation.
Change the temperature setting with “Temp (+)“ button
(E) or “Temp (-)“ button (F).
Change the pump speed setting with “Pump (+)“ button
(H) or “Pump (-)“ button (I).
In standby status, activate the heating function by press-
ing the “Temp“button (D). The device start heating func-
tion, meanwhile the pump start to run.
In working status, stop the pump function by pressing the
“OK/Pump“button (G). The heating function and pump
stops.
In standby status, press the “OK/Pump“button (G) to
start the pump function. The heating function will not be
activated.
In running status, press the “Temp“button (D) to stop the
heating function, the pump keep running.
The control elements of the device allow to be locked
by pressing the key button (O), so no accidental changes
during operation are possible (key symbol appears in the
display) .
By pressing the key button (O) again, the controls are re-
leased (key symbol disappears from the display).
Fig. 4
Fig. 5
Fig. 6
After several seconds, screen display the information of
device.
IKA®
Circulator
ICC control
Version 1.2.008
Information
Internal Max: 95 °C
Internal Min: 5 °C
External Max: 95 °C
External Min: 5 °C
Fluid: H2O (Water)
A
0.00
int °C
ext °C
int 5.00 1000
set °C Pump rpm
Safe Temp °C

11
Setting the safety temperature
Adjust the safety temperature with screwdriver included
with the device.
The safety temperature setting will appear on the display.
Factory setting: maximum value
Adjustment range: 0 –160 °C
Note: The safe temperature limit must always be set to
at least 25 ºC lower than the flash point of the fluid used.
Operation
• Working screen at the time of delivery:
The start and information screen (see section "Commis-
sioning") appears for a few seconds after the device is
switched on. After this, the following working screen ap-
pears automatically in the display.
• Explanation of symbols on the working screen:
The symbols displayed change depending on the status
and settings of the device. The screen below shows the
most significant symbols on the working screen.
A
100.00
int °C
ext °C
int 100.00 1000
set °C Pump rpm
Safe Temp °C
PC
100.00 160
Fig. 8
Fig. 9
Fig. 7
A
0.00
int °C
ext °C
int 5.00 1000
set °C Pump rpm
Safe Temp °C
Lock:
This symbol means that the function of the keys for con-
trolling the device are disabled.
The symbol no longer appears if the functions are en-
abled once again by pressing the key button a second
time.
Temperature Sensor:
This symbol appears when the external temperature
sensor is connected.
A Operating Mode:
This symbol indicates the operating mode currently se-
lected (A, B, C, D).
USB:
This symbol means the device is communicating with a
PC via a USB cable.
Heating
This symbol indicates that the heating function is active.
J J indicate active heating process.
Fluid level
This symbol indicates fluid level.
The red symbol means the fluid is above the maximum
fluid level. Excess fluid should be drained out.
The red symbol means the fluid is below the minimum
fluid level. Please add fluid.
Pump:
This symbol indicates that the pump is activated.
Warning:
This symbol indicates that warning is active.
PC PC Control:
This symbol means that the device is connected to a
computer and is being controlled from the computer.
PR Program Control:
This symbol indicates that the device is controlled by a
program (see "PROGRAMS").

12
• Menu navigation and structure:
Menu navigation
)Press the "Menu" key (J).
)Select the menu option by
pressing the
“Pump (+)” button (H)
or
“Pump
(-)” button (I)
.
)Open the menu item by pressing the "OK/Pump" button (G).
)
Press the “Pump (+)” button (H) or “Pump (-)” button (I) to select the desired
menu option and edit the values or settings.
)
Press the the "OK/Pump" button (G) to get into sub menu items to active/
inactive to switch settings or to confirm settings ("OK").
)Press the "Back" button (K) to a setting or cancel to return to the previous
menu.
)
Press the "Menu" button (J) to return directly to the working screen.
Note: If you press the “Menu“ button (J), the system skips directly back to the working screen.
If you press the “Back“ button (K), the system skips back to the previous screen.
Menu
Menu navigation: ¼Press the “Menu“ button (J),
"OK/Pump" button (G)
and “Pump (+)” button (H) or “Pump (-)” button (I)
»Press the ”Back” button (K) or the ”Menu” button (J).
A
0.00
int °C
ext °C
int 0.00 1000
set °C Pump rpm
Safe Temp °C
TEMPERING
Menu
BackBackBackBack
MENU Tempering
Control
Limits
Temperature Sensor
>
Tempering
Control
Control Mode
Control Parameters
Fluids
> Tempering > Control
Control Mode
Internal (int)
External (ext)
Fig. 11
Note: When the tempering or pump functions are active, the menu is locked. On the display, the active menu option is
highlighted in yellow. The active status of a menu item is marked with a check (√).
G
J
K
HI
Fig. 10

13
TEMPERING Control Control Mode
Fluids
Control Parameters
Internal (int) activated
-
-
-
-
-
-
-
-
-
-
-
-
-
-
-
-
-
-
-
activated
activated
activated
95 °C
5°C
100 °C
100 %
± 0.0 K
60.0, 5.0, 0.3, 3 s, +1.00 K, -1.00 k
1.0, 15.0, 0.0, 90 s, +1.00 K, -1.00 k
-
Automatic Accurate
Internal
Internal
Internal (Kp, Ti, Td, Ts, Prop_Bp, Prop_Bn)
2 Point Calibration
2 Point Calibration
Fast
Manual
Eternal (ext)
Eternal (ext)
I T (int - ext)I
Power Output
Calibration
Reset Calibration
Heating
Maximum
Minimum
Eternal
Eternal
Eternal (Kp, Ti, Td, Ts, Prop_Bp, Prop_Bn)
3 Point Calibration
3 Point Calibration
Information (Kp, Ti, Td, Ts, Prop_Bp, Prop_Bn)
Limits
Temperature Sensor
Notification
Hysteresis
Sound Infinite
Beep
ON
CF.EG28.N10.80.8
CF.EG39.N20.80.16
CF.EG44.N25.80.19
CF.EG48.N30.80.22
UF.Si.N30.150.10LV
HF.Si.20.200.50
HF.Si.20.250.50A
H
2
O (Water)
Customized 1
Customized 2
TIMER Set
Display
00:00 [hh:mm]
-
GRAPH Automatic
Manual Axis Assignment Set Temperature
Actual Internal Temp.
Actual External Temp.
X - Axis
Y - Axis
15 min
30 min
60 min
120 min
Axis Scaling
Maximum
Minimum
-
-
-
activated
activated
activated
activated
activated
95 ºC
5 ºC
PROGRAMS Program 1
...
Program 10
-
-
-
OUTGAS Speed
Interval
1000 rpm
10 s
DISPLAY Main Screen Pump
Timer -
activated
Factory Settings
Menu
PUMP Limits Speed
Pressure
Maximum
Maximum
Minimum
3200 rpm
1000 rpm
0.4 bar
MODE A
C
B -
-
activated
SAFETY Password
Safe Temp. Confirmation
000
-
SETTING Languages
Display
Sound
Factory Settings
Communication
Information
English
Background
Key Tone
Tempering
Safety
Intro
Device Name
Pump
Software
Firemware Update Info
Firmware Update Info
Black
White
Deutsch
... -
activated
Circulator
-
-
-
yes
yes
yes
yes
yes
yes
-
activaed
D -
Menu structure:

14
• Menu (Details):
TEMPERING:
Control:
Control Mode:
Internal (int): The temperature is regulated according to
the internal temperature sensor.
Extern (ext): The temperature is regulated according to
the external temperature sensor.
Control parameters:
Automatic: The optimal control parameters for PID tem-
perature control are determined automatically. This is the
recommended mode.
Selecting "Automatic" allows you to set the dynamics
for temperature control:
Accurate: precise tempering without overshooting.
Fast: fast tempering with minimal overshooting.
Manual: The control parameters for PID temperature
control can be set manually.
"Manual" should only be used in the event of special
temperature control requirements.
When "Manual" is selected, the following parameters
can be set for "Internal (int)" and "External (ext)" tem-
perature control:
Kp: Proportional coecient
The proportional coecient Kp is the controller amplifi-
cation and determines how strongly the control deviation
(the difference between the target temperature and ac-
tual temperature) directly affects the control variable (on-
time of the heater). Kp-values that are too large can lead
to the controller overshooting.
Ti: Integral time
The integral time Ti (s) is the correction time and deter-
mines how strongly the duration of the control deviation
affects the control variable. Ti compensates for an ex-
isting control deviation. A high Ti means a smaller and
slower effect on the control variable. Ti-values that are
too small can lead to instability of the controller.
Td: Differential time
The differential time Td (s) is the derivative time and de-
termines how strongly the rate of change of the control
deviation affects the control variable. Td compensates for
rapid control deviations. A high Td means a smaller and
slower effect on the control variable. Td-values that are
too large can lead to instability of the controller.
Ts: Sampling time
The sampling time Ts (s) is the time interval over which the
control deviation is determined and the respective control
variable (dependent on Kp, Ti and Td) is calculated.
Ts must be adjusted to match the response characteristic
(total of all time constants) of the closed loop controlled
system, so that the control variable can deliver a uniform
and measurable change in the control deviation. Ts val-
ues that are too small or too large can lead to instability
of the controller.
Fluids:
Under the option "Fluids", a variety of heat transfer fluids
can be selected.
The selected fluid limits the setting range of the target
temperature. See table in the section “Fluids“.
The maximum and minimum temperature values of the
selected fluid can be set within these limitations.
Limits:
Under the option "External (ext)", the maximum and
minimum temperature for external temperature control
can be set.
Under "l Δ T (int - ext) l", the maximum difference be-
tween the internal and external temperature can be set.
Under "Power Output", the maximum heating output
can be set as a percentage.
Temperature sensor
The internal and external temperature measurement can
be calibrated and compensated for.
By "calibration (Reset Calibration)", the calibration value
for the internal or the external temperature sensor will
be deleted.
Notification:
ON:
This menu option allows you to activate/deactivate the
“Notification“ function. A green check mark and a beep
informing when the target value (hysteresis) has been
reached.
Hysteresis:
This menu option allows you to set the hysteresis from 0
to ±2.0 K.
Sound:
Infinite: Beep until you press the “Back” key.
Beep: Single beep.
TIMER
Set:
The user can set a target time (duration).
When device functions are started normally, this time is
displayed on the working screen. The device functions
stop automatically once this time has expired. The run-
ning time is then displayed again on the display.
Note: To deactivate the target time specification, set the
target time to 00:00.
Display:
Activate the timer display on the main display (working
screen).
PUMP
Limits:
In “Limits“ option, the user is allowed to set the max-
imum and minimum speed to the pump, and also the
maximum pressure.

15
MODE
Operating Mode A:
After power-on/power failure no automatic restart of
functions.
Operating Mode B:
After power-on/power failure automatic restart of func-
tions, depending on previous settings.
Operating mode C:
Set values (set in Aor B) cannot be changed.
After power-on/power failure automatic restart of func-
tions, depending on previous settings.
Operating mode D:
Confirmation request for set value changes, if functions
are active. After power-on/power failure no automatic
restart of functions.
GRAPH
In this menu, you can set the options for the time-tem-
perature diagram.
Automatic:
The scaling of the temperature axis (Y-axis) is automati-
cally determined, depending on the target temperature
and the actual internal and external temperature.
The time axis (X-axis) is permanently scaled to 30 min-
utes.
Manual:
Axis Assignment:
The temperature values to be displayed can be selected.
Axis scaling:
Scaling of the time (X) and temperature axis (Y) can be
selected or set.
DISPLAY
In the “Display“ menu the user can specify what infor-
mation will be displayed on the screen.
PROGRAMS
Under programs, 10 user-defined temperature-time pro-
files can be created. A program can consist of up to 10
segments.
Once a program has been selected, the following options
are available:
Start:
Starts the program upon request of loop mode.
Infinite loop: Upon completion of the last segment, the
program continues with the first segment until the user
ends the program by stopping a device function.
Loop Count: Indicates the total number of loop cycles
until program end.
Note: At the end of the program all device functions are
switched off.
Edit:
Edit/change program parameters.
Seg No.: Segment number.
Ctrl. Sensor (int/ext): Determines whether control is
through the internal (int) or external (ext) temperature
sensor.
Temp.: Target temperature.
Ctrl.Mode (Time / +/- x.x K): In "Ctrl.Mode Time" the
target values and settings of the segment are valid for the
duration indicated in the column "Time hh:mm".
Afterwards, the next program segment is automatically
executed.
In "Ctrl.Mode +/- x.xx K", the hysteresis (tolerance) of
the actual temperature to the target temperature is set
(e.g. +/- 0.1 K). The target values and settings of the seg-
ment are valid until the actual temperature reaches the
target temperature +/- hysteresis for the first time.
Afterwards, the next program segment is automatically
executed.
Pump rpm: Target speed of pump.
Delete:
Deletes the selection highlighted in yellow (segment or
program).
Insert: Inserts a new program segment after the selected
segment.
Save: Saves changes.
View:
Temperature-time overview displays for the program with
segments of the selected program.
Note: If hysteresis is set as "Ctrl.Mode +/-x.xx K" for
one or more segments in the program, the duration of
the program cannot be determined.
Press
the
“Pump (+)” button (H)
or
“Pump (-)” button
(I)
and
"OK/Pump" button (G) to display the segment
details.
Cancel: Cancels the process.
Note: Once the program has been started, the program
no., segment no. (active/total) and the remaining duration
of the segment or hysteresis are displayed in the graph.
OUTGAS
In the option, the user is allowed to set the outgas speed
in range of 1000 rpm to 3200 rpm and outgas interval
from 10 seconds to 240 seconds.
This function can be used when filling external devices
such as laboratory reactors.

16
SAFETY
Password:
In the "Password" menu, the menu settings can be
locked by a 3-digit password.
Safe Temp. Confirmation:
This menu can confirm (safety temperature of the station)
at start-up of the set “Safe Temp”. A check mark (√) indi-
cates that the function is activated.
SETTING
Languages:
The “Languages“ option allows the user to select the
desired language.
Display:
The ”Display“ option allows the user to change the
background color of the working screen.
You can also activate the “Firmware Update Info“ screen
in this menu.
Interface and output
The device can be operated in “Remote” mode via the RS 232
interface (10) or the USB interface (11) connected to a PC and
with the laboratory software Labworldsoft®.
Note: Please comply with the system requirements togeth-
er with the operating instructions and help section included
with the software.
USB interface:
The Universal Serial Bus (USB) is a serial bus for connecting
the device to the PC. Equipped with USB devices can be
connected to a PC during operation (hot plugging). Con-
nected devices and their properties are automatically recog-
nized. Use the USB interface in conjunction with labworld-
soft®for operation in "Remote" mode and also to update
the firmware.
USB device drivers:
First, download the latest driver for IKA®devices with USB
interface from:
http://www.ika.com/ika/lws/download/usb-driver.zip.
Install the driver by running the setup file. Then connect the
IKA®device through the USB data cable to the PC.
The data communication is via a virtual COM port. Configu-
ration, command syntax and commands of the virtual COM
ports are as described in RS 232 interface.
RS 232 interface:
Configuration
- The functions of the interface connections between the
stirrer machine and the automation system are chosen
from the signals specified in EIA standard RS 232 in ac-
cordance with DIN 66 020 Part 1.
-
For the electrical characteristics of the interface and the al-
location of signal status, standard RS 232 applies in accor-
dance with DIN 66 259 Part 1.
- Transmission procedure: asynchronous character transmis-
sion in start-stop mode.
- Type of transmission: full duplex.
-
Character format: character representation in accordance
with data format in DIN 66 022 for start-stop mode. 1
start bit; 7 character bits; 1 parity bit (even); 1 stop bit.
- Transmission speed: 9600 bit/s.
- Data flow control: none
- Access procedure: data transfer from the stirrer machine to
the computer takes place only at the computer’s request.
Command syntax and format:
The following applies to the command set:
- Commands are generally sent from the computer (Master)
to the device (Slave).
- The device sends only at the computer’s request. Even
fault indications cannot be sent spontaneously from the
device to the computer (automation system).
- Commands are transmitted in capital letters.
- Commands and parameters including successive param-
eters are separated by at least one space (Code: hex 0x20).
Sound:
The ”Sound” option allows the user to activate/deacti-
vate the key tone.
Factory Settings:
Select the ”Factory settings” option with "OK/Pump"
button. The system requests confirmation to restore the
factory settings. Pressing the ”OK” button resets all the
system settings to the original standard values set at dis-
patch from the factory (see "Menu structure").
Communication:
The ”Device name” menu option allows you to edit the de-
vice name.
Information:
The ”Information” option offers the user an overview of
the most important system settings of the device.

17
- Each individual command (incl. parameters and data) and
each response are terminated with Blank CR Blank LF
(Code: hex 0x20 hex 0x0d hex 0x20 hex 0x0A) and have a
maximum length of 80 characters.
-
The decimal separator in a number is a dot (Code: hex
0x2E).
The above details correspond as far as possible to the recommendations of the NAMUR working party (NAMUR recommenda-
tions for the design of electrical plug connections for analogue and digital signal transmission on individual items of laboratory
control equipment, rev. 1.1).
The NAMUR commands and the additional specific IKA
®
commands serve only as low level commands for communication
between the device and the PC. With a suitable terminal or communications programme these commands can be transmitted
directly to the circulator equipment. The IKA
®
software package, Labworldsoft
®
, provides a convenient tool for controlling
circulating equipment and collecting data under MS Windows, and includes graphical entry features, for pump motor speed
ramps for example.
Commands:
Commands
Function
IN_PV_1
Read the external actual temperature
IN_PV_2
Read the internal actual temperature
IN_PV_3
Read the safety actual temperature
IN_PV_4
Read the pump actual speed
IN_SP_1
Read the internal setting temperature (if 0: internal control)
Read the external setting temperature (if 1: external control)
IN_SP_3
Read the safety setting temperature
IN_SP_4
Read the pump setting speed
IN_TMODE
Read temperature control
0: internal control
1: external control
OUT_SP_1 xxx
Set the internal setting temperature XXX (
if 0: internal control
)
Set the external setting temperature XXX (if
1: external control
)
OUT_SP_12@n
Set the WD safety temperature with echo of the set (defined) value.
OUT_SP_4 xxx
Set the pump speed XXX
OUT_SP_42@n
Set the WD-safety speed with echo of the set (defined) value.
OUT_TMODE_0
Set to Internal temperature control
OUT_TMODE_1
Set to External temperature control
OUT_WD1@n
Start the watchdog mode 1 and set the time for the watchdog to n (20...1500) seconds.
Echo of the Watchdog time.
During a WD1-event, the heating and pump functions are switched off.
This command needs to be send within the watchdog time.
OUT_WD2@n
Start the watchdog mode 2 and set the watchdog time to n (20...1500) seconds.
Echo of the watchdog time.
During a WD2-event, the set temperature is changed to the WD safety temperature and the pump set
speed is set to the WD safety speed.
This command needs to be send within the watchdog time.
RESET
Reset the PC control and stop the device functions.
START_1
Start the heating function
START_4
Start the pump function
STOP_1
Stop the heating function
STOP_4
Stop the pump function

18
USB 2.0 cable A - Micro B:
This cable is required to connect USB port (11) to a PC.
USB micro B USB A
A
Fig.13
PC 1.1 Cable:
This cable is required to connect RS 232 port (10) to a PC.
1
2 RxD
3 TxD
4
5 GND
6
7 RTS
8 CTS
9
1
RxD 2
TxD 3
4
GND 5
6
RTS 7
CTS 8
9
PC
1
2
3
4
5
6
7
8
9
9
8
7
6
5
4
3
2
1
Fig. 12
Maintenance and cleaning
The device is maintenance-free. It is only subject to the
natural wear and tear of components and their statistical
failure rate.
Cleaning
Disconnect main plug prior to
cleaning!
Use only cleaning agents which have been approved by
IKA®to clean IKA®device.
Dirt Cleaning agent
Dye isopropyl alcohol
Construction material
water containing tenside/isopropyl alcohol
Cosmetics
water containing tenside/isopropyl alcohol
Foodstuffs water containing tenside
Fuel water containing tenside
For materials which are not listed, please request in-
formation from IKA®application support.
Wear protective gloves while cleaning the device.
Electrical device may not be placed in the cleansing agent for
the purpose of cleaning.
Do not allow moisture to get into the device when cleaning.
Before performing a non-recommended method of clean-
ing or decontamination, the user must ascertain with IKA®
that this method will not damage the device.
Spare parts order
When ordering spare parts, please give:
- Machine type
- Serial number, see type plate
-
Item and designation of the spare part,
see www.ika.com, spare parts diagram and spare parts list.
- Software version.
Repair
Please send device for repair only after it has been
cleaned and is free from any materials which may
constitute a health hazard.
For this you should request the “Decontamination Cer-
tificate” from IKA®, or use the download printout of it
from the IKA®website www.ika.com.
Return the device in its original packaging. Storage packag-
ing is not sucient. Please also use suitable transport pack-
aging.

19
Error codes
Any malfunctions during operation will be identified by an error message on the display.
Proceed as follows in such cases:
)
Switch off device using the main switch at the back of the device
)
Carry out corrective measures
)
Restart device
Error code Effect Cause Solution
Error 01 Pump off
Heating off
No external temperature sensor
Check this sensor
Error 02 Pump off
Heating off
Motor over current (rate current) - Reduce pump motor speed
- Use fluid with lower viscosity
- Check if the pump impeller is blocked
Error 03 Pump off
Heating off
Motor over current (max current) - Reduce pump motor speed
- Use fluid with lower viscosity
- Check if the pump impeller is blocked
Error 04 Pump off
Heating off
Motor hall signal missing - Reduce pump motor speed
- Use fluid with lower viscosity
- Check if the pump impeller is blocked
Error 05 Pump off
Heating off
Too high liquid level - Check the liquid level and buoyage
Error 06 Pump off
Heating off
Too low liquid level - Check the liquid level and buoyage
Error 07 Pump off
Heating off
Too high voltage - Check the mains power
Error 08 Pump off
Heating off
Too low voltage - Check the mains power
Error 09 Pump off
Heating off
Device internal temperature is too
high
- Check the ambient temperature and let the device
cool down
Error 10 Pump off
Heating off
PC communication failure - Check communication cable
Error 11 Pump off
Heating off
Temperature difference between
control sensor and safety sensor is
too much
- Check safety temperature circuit and bath fluid
Error 12 Pump off
Heating off
Safety temperature alarm - Check the bath temperature measurement
Error 13 Pump off
Heating off
Heater switched off by safety circuit
- Check safety temperature set value, liquid level
Error 14 Pump off
Heating off
Fan error
- Check the fan and clean the grids at the rear side
If the actions described fails to resolve the fault or another error code is displayed then take one of the following steps:
- Contact the service department
- Send the device for repair, including a short description of the fault.

20
Accessories
•
Tubing, hoses, adapters and couplings
LT 5.20 Metal hose (isolated M16 x 1)
LT 5.21 PTFE hose (isolated M16 x 1)
H.PVC.8 PVC hose (nominal width 8)
H.PVC.12 PVC hose (nominal width 12)
H.SI.8 Silicone hose (nominal width 8)
H.SI.12 Silicone hose (nominal width 12)
•
Tubing Insulations
ISO. 8 Insulation (8 mm)
ISO.12 Insulation (12 mm)
•
Bath vessels
IB eco 8 Plastic bath (8 litre)
IB eco 18 Plastic bath (18 litre)
IB pro 9 Stainless steel bath (9 litre)
IB pro 12 Stainless steel bath (12 litre)
IB pro 20 Stainless steel bath (20 litre)
•
Bridges and Covers
BS.ICC Small bridge (for IB eco 8, IB pro 9)
BL.ICC Large bridge (for IB eco 18, IB pro 12,
IB pro 20)
CS.ICC Samll cover (for IB eco 8,IB pro 9)
CM.ICC Medium cover (for IB pro 12)
CL.ICC Large cover (for IB eco 18,IB pro 20)
•
Additional accessories
PCS.ICC Pump set
Pt 100.3 Temperature sensor
PC 1.1 Cable (RS 232)
Labworldsoft®
See more accessories on www.ika.com.
Other manuals for ICC control
2
Table of contents
Other IKA Thermostat manuals
Popular Thermostat manuals by other brands
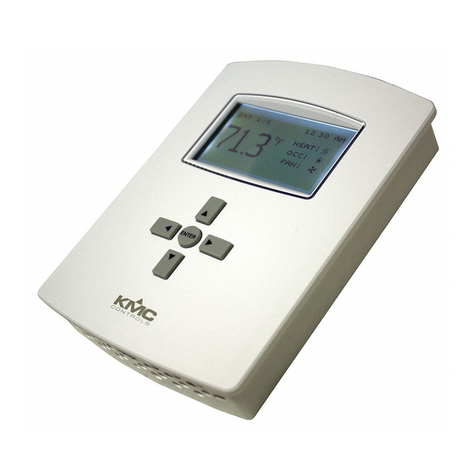
KMC Controls
KMC Controls FlexStat BACnet Operation guide

Braeburn
Braeburn Economy Series Installer manual

ROOTECH
ROOTECH Accura 2350-TEMP user guide
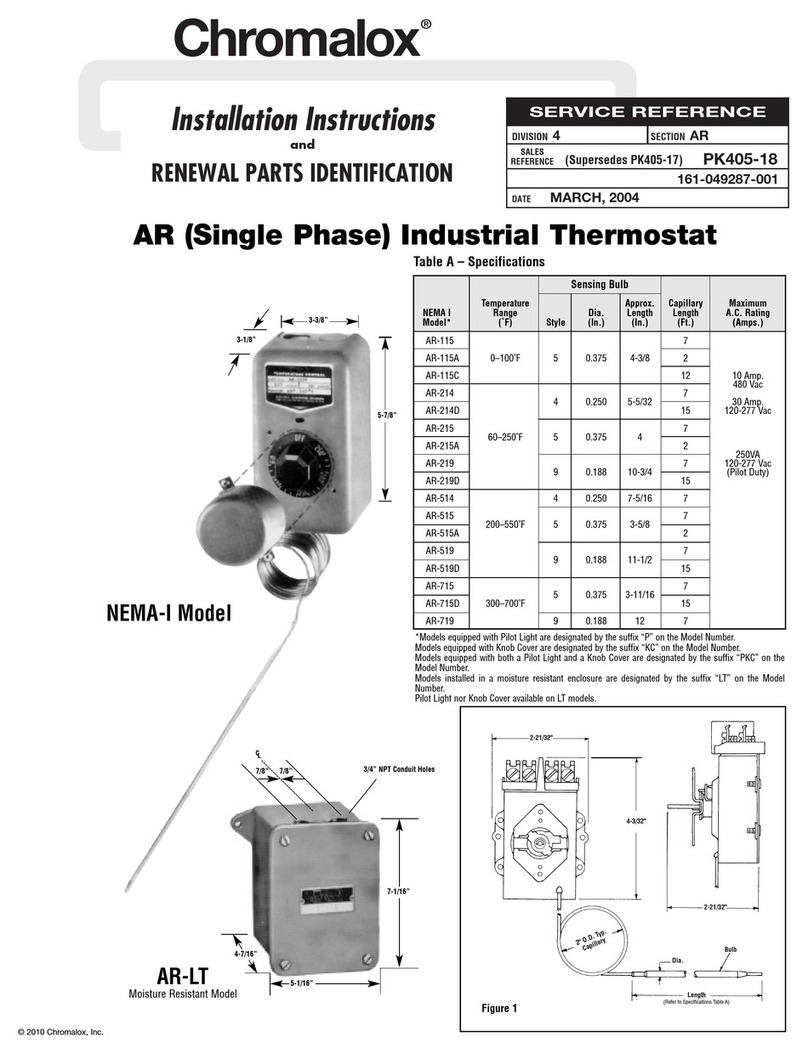
Chromalox
Chromalox PK405-18 Installation Instructions and RENEWAL PARTS IDENTIFICATION
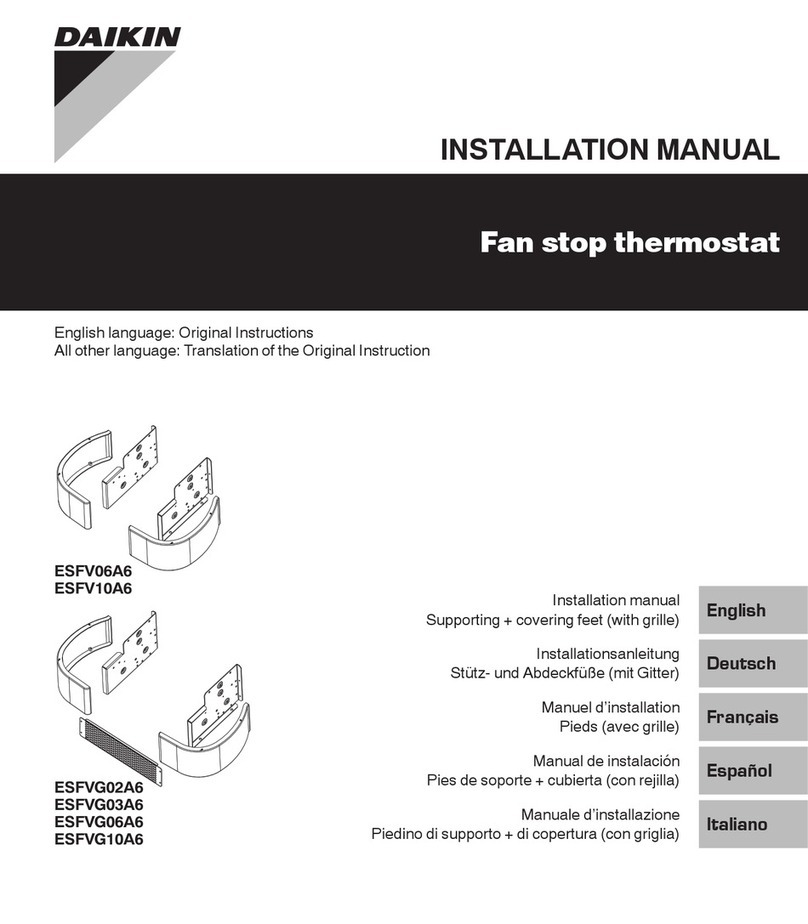
Daikin
Daikin ESFV06A6 installation manual

QUBINO
QUBINO FLUSH ON/OFF THERMOSTAT 2 user manual