Immergas MAGIS PRO 5 ERP Operating instructions

MAGIS PRO ERP
Mono-phase hydronic module to
pair with an outdoor condensing
unit
Instruction and
recommendation booklet
IE
*1.039356ENG*


Immergas S.p.A. declines all liability due to printing or transcription errors, reserving the right to make any modications to its technical and commercial
documents without prior notice.
Dear Customer,
Our compliments for having chosen a top-quality Immergas product, able to assure well-being and safety for a long period of time. As an Immergas customer
you can also count on a qualied aer-sales service, prepared and updated to guarantee constant eciency of your boiler. Read the following pages carefully: you
will be able to draw useful suggestions regarding the correct use of the appliance, the respect of which, will conrm your satisfaction for the Immergas product.
Contact our area authorised aer-sales centre as soon as possible to request commissioning. Our technician will verify the correct functioning conditions; he
will perform the necessary calibrations and will demonstrate the correct use of the generator.
For assistance and scheduled maintenance contact Authorised Immergas Aer-Sales centres: they have original spare parts and are specically trained directly
by the manufacturer.
General recommendations
All Immergas products are protected with suitable transport packaging.
e material must be stored in dry environments protected from bad weather.
e instruction book is an integral and essential part of the product and must also be given to the new user in the case of transfer or succession of ownership.
It must be stored with care and consulted carefully, as all of the warnings provide important safety indications for installation, use and maintenance stages.
is instructions manual provides technical information for installing Immergas products. As for the other issues related to the installation of products (e.g.
safety at the workplace, environmental protection, accident prevention), it is necessary to comply with the provisions of the standards in force and the principles
of good practice.
In compliance with the legislation in force, the systems must be designed by qualied professionals, within the dimensional limits established by the Law.
Installation and maintenance must be performed in compliance with the regulations in force, according to the manufacturer's instructions and by professionally
qualied sta, intending sta with specic technical skills in the plant sector, as envisioned by the Law.
Improper installation or assembly of the Immergas appliance and/or components, accessories, kit and devices can cause unexpected problems for people, animals
and objects. Read the instructions provided with the product carefully to ensure proper installation.
Maintenance must be carried out by skilled technical sta. e Immergas Authorised Aer-sales Service represents a guarantee of qualications and
professionalism.
e appliance must only be destined for the use for which it has been expressly declared. Any other use will be considered improper and therefore potentially
dangerous.
If errors occur during installation, operation and maintenance, due to non-compliance with technical laws in force, standards or instructions contained in
this book (or however supplied by the manufacturer), the manufacturer is excluded from any contractual and extra-contractual liability for any damages and
the appliance warranty is invalidated.
For further information regarding legislative and statutory provisions relative to the installation of gas heat generators, consult the Immergas site at the
following web address: www.immergas.com
Mauro Guareschi
Research & Development Director
Signature:
CE DECLARATION OF CONFORMITY
(according to ISO/IEC 17050-1)
e company IMMERGAS S.p.A., with registered oce in via Cisa Ligure 95 42041 Brescello (RE), whose design, manufacturing and aer-sales assistance
processes comply with the requirements of standard UNI EN ISO 9001:2008,
DECLARES that:
MAGIS PRO ERP hydronic units comply with the following European Directives and European Commission Delegated Regulations:
“Eco-design” Directive 2009/125/EC, “Energy labelling” Directive 2010/30/EC, EU Regulation 811/2013, EU Regulation 813/2013, “Electromagnetic
Compatibility” Directive 2004/108/EC, “Eciency” Directive 92/42/EC and “Low-Voltage” Directive 2006/95/EC.

INDEX
USER pageINSTALLER page MAINTENANCE TECHNICIAN page
1 Hydronic module installation...........................5
1.1 Installation recommendations. .........................5
1.2 Main dimensions. ..............................................6
1.3 Antifreeze protection. ........................................6
1.4 Hydronic module connection unit................... 7
1.5 Hydraulic connection......................................... 7
1.6 Connecting the chiller line................................7
1.7 Electric connection. ...........................................8
1.8 Remote controls and room chrono-thermostats
(Optional). ...........................................................9
1.9 External temperature probe...............................9
1.10 Heat regulation setting.....................................10
1.11 Filling the system..............................................11
1.12 Operating limits................................................11
1.13 Commissioning the hydronic module
(ignition)............................................................11
1.14 Circulation pump..............................................12
1.15 Hydronic module components. ......................13
1.16 Kits available on request. .................................13
2 Use and maintenance instructions .................14
2.1 Cleaning and maintenance..............................14
2.2 General warnings..............................................14
2.3 Control panel.....................................................14
2.4 System use..........................................................15
2.5 Troubleshooting................................................16
2.6 Parameters and information menu. ...............18
2.7 Switching o the hydronic module..................19
2.8 Restoring central heating system pressure. ...19
2.9 System draining................................................19
2.10 Anti-freeze protection......................................19
2.11 Case cleaning.....................................................19
2.12 Decommissioning.............................................19
3 Commissioning the package (initial check)..20
3.1 Hydronic module Hydraulic Diagram .............20
3.2 Wiring diagram.................................................21
3.3 System lter.........................................................23
3.4 Troubleshooting................................................23
3.5 Programming the P.C.B....................................24
3.6 Pump anti-lock function..................................28
3.7 3-way anti-lock function..................................28
3.8 Radiator antifreeze function............................28
3.9 Solar function....................................................28
3.10 Outdoor unit disable function. .......................28
3.11 Diverter valve management (summer / winter).
......................................................................28
3.12 Anti-Legionalla function. ................................28
3.13 Automatic vent function..................................28
3.14 Yearly appliance check and maintenance. .....28
3.15 Casing removal..................................................29
3.16 Technical data....................................................31
3.17 Product che (in compliance with regulation
811/2013). ..........................................................32
3.18 Parameters for lling in the package che.....53

5
1-1
INSTALLERUSERMAINTENANCE TECHNICIAN
1HYDRONIC MODULE IN
STALLATION.
1.1 INSTALLATION
RECOMMENDATIONS.
e Magis Pro ErP hydronic module was de-
signed solely for wall mounted installation for
heating and air conditioning and to produce
domestic hot water for domestic use and similar
purposes.
In order to operate properly, it must be paired
with an Audax Pro condensing unit; as such, all
the provisions regarding the safety and use of
both appliances must be respected.
e place of installation of the appliance and
relative Immergas accessories must have suitable
features (technical and structural), such as to al-
low for (always in safe, ecient and comfortable
conditions):
- installation (according to the provisions of the
technical legislation and technical regulations);
- maintenance operations (including scheduled,
periodic, routine and special maintenance);
- removal (to outdoors in the place for loading
and transporting the appliances and compo-
nents) as well as their eventual replacement
with appliances and/or equivalent components.
e wall surface must be smooth, without any
protrusions or recesses enabling access to the
rear part. ey are not designed to be installed
on plinths or oors (Fig. 1-1).
Only professionally enabled companies are au-
thorised to install Immergas appliances.
Installation must be carried out according to the
provisions of the laws in force and in compliance
with local technical regulations and the required
technical procedures.
Before installing the appliance, ensure that it is
delivered in perfect condition; if in doubt, contact
the supplier immediately. Packing materials (sta-
ples, nails, plastic bags, polystyrene foam, etc.)
constitute a hazard and must be kept out of the
reach of children.
Should the appliance be contained inside or be-
tween pieces of furniture, there must be enough
space for routine maintenance; therefore, it is
recommendable to leave at least 3 cm between the
unit casing and the vertical walls of the furniture.
At least 25 cm of free space must be le above, in
order to be able to carry out maintenance and,
if necessary, install an additional resistance (op-
tional). Leave space under the hydronic module
to allow the hydraulic connections to be serviced.
Keep all ammable objects away from the ap-
pliance (paper, rags, plastic, polystyrene, etc.).
Do not put household appliances under the hy-
dronic module as they could be damaged if the
safety valve trips or if the hydraulic ttings leak.
Otherwise, the manufacturer cannot be held lia-
ble for any damage to the household appliances.
For the same reasons, it is also recommendable
not to put furnishings, furniture, etc. under the
hydronic module.
In the event of malfunctions, faults or incorrect
operation, turn the appliance o immediately
and contact an authorised company (e.g. the
Immergas Technical Assistance centre, which
has specically trained sta and original spare
parts). Do not attempt to modify or repair the
appliance alone.
Failure to comply with the above implies personal
responsibility and invalidates the warranty.
• Installation regulations:
- this hydronic module can be installed out-
doors in a partially protected area. By partial-
ly protected area, we mean one in which the
unit is not directly exposed to the elements
(rain, snow, hail, etc.).
- Installation is prohibited on the vertical
projection of cooking hobs.
- Installation is also prohibited in places/en-
vironments that constitute common parts of
oce condominiums such as stairs, cellars,
entrance halls, attics, los, escape routes,
etc. if they are not located inside technical
compartments under the responsibility of
each individual building and only accessible
to the user (for the features of the technical
compartments, see the technical standards in
force).
- Using specic kits, the hydronic module can
be paired with other Immergas products
and installed inside an outdoor wall using
the specic Solar Container recessed frame
or mounted on an indoor wall in the Domus
Container.
Attention: Installing the wall recessed frame
kit must guarantee the hydronic module sta-
ble, ecient support. e recessed frame kit
ensures appropriate support only if installed
correctly (according to the rules of good
practice), following the instructions on its
instructions leaet. e recessed frame for
the hydronic module is not a load-bearing
structure and cannot replace the removed
wall. erefore, correct positioning inside
the wall must be checked. For safety reasons
to prevent leaks, the compartment that will
house the hydronic module in the masonry
wall must be plastered.
Attention: installing the hydronic module
mounted on the wall must ensure the generator
itself stable, ecient support.
e dowels (standard supplied with the unit) must
only be used to secure the unit to the wall; they can
only ensure sucient support if inserted properly
(according to the rules of good practice) on walls
built with solid or semi-hollow bricks. In the
case of walls made from hollow brick or block,
partitions with limited static properties, or in any
case walls other than those indicated, a static test
must be carried out to ensure adequate support.
ese hydronic units are used to heat water to be-
low boiling temperature at atmospheric pressure.
ey must be connected to a central heating
system and domestic hot water circuit suited to
their performance and capacity.
Attention:e storage tank unit must also be
installed in an environment in which the tem-
perature cannot fall below 0°C.
"Anti-Legionella" treatment of the Immergas
storage tank (function enabled when there is
an additional electrical resistance for domestic
hot water). During this phase, the temperature
of the water inside the tank exceeds 60°C with
the subsequent risk of burns. Keep this domes-
tic water treatment under control (and inform
the users) to prevent unforeseeable damage
to people, animals, things. If required install a
thermostatic valve on the domestic hot water
outlet to prevent scalding.
YES NO

6
1-2
INSTALLERUSERMAINTENANCE TECHNICIAN
1.2 MAIN DIMENSIONS.
Key:
V - Electrical connection
RR - System lling
RU - Storage tank unit return
MU - Storage tank unit ow
R - System return
M - System ow
LP - Chiller line - liquid phase
GP - Chiller line - gaseous phase
Height
(mm)
Width
(mm)
Depth
(mm)
760 440 250
CONNECTIONS
CHILLER LINE DOMESTIC
HOT WATER SYSTEM
LG GP RR R - M RU - MU
G 3/8” G 5/8” 1/2” 3/4” 3/4”
1.3 ANTIFREEZE PROTECTION.
Minimum temperature -5°C. e hydronic unit
comes standard with an anti-freeze function that
activates the condensing unit when the temper-
ature of the water inside of it falls below 4°C.
In these conditions, the hydronic unit is protected
against freezing up to an ambient temperature
of -5℃.
Minimum temperature -15°C. In the event the
hydronic unit is installed in a place where the
temperature falls below -5°C, it is possible for
the appliance to freeze.
To prevent the risk of freezing follow the instruc-
tions below:
- protect the central heating circuit from freezing
by inserting a good-quality antifreeze liquid
into this circuit, which is specially suited for
central heating systems and which is manu-
facturer guaranteed not to cause damage to
the heat exchanger or other components of
the hydronic module. e antifreeze liquid
must not be harmful to one's health. e in-
structions of the manufacturer of this liquid
must be followed scrupulously regarding
the percentage necessary with respect to the
minimum temperature at which the system
must be kept. An aqueous solution must be
made with potential pollution class of water 2
(EN 1717:2002).
e materials used for the hydraulic circuits of
Immergas hydronic units resist ethylene and
propylene glycol based antifreeze liquids (if the
mixtures are prepared perfectly).
For life and possible disposal, follow the sup-
plier's instructions.
- Protect the domestic hot water circuit against
freezing by using an accessory that is supplied
on request (antifreeze kit) comprising two
electric heating elements, the relevant cables
and a control thermostat (carefully read the
installation instructions contained in the ac-
cessory kit pack).
In these conditions, the hydronic unit is protected
against freezing up to a temperature of -15°C.
Hydronic unit anti-freeze protection (both -5°C
and -15°C) is only ensured if:
- e hydronic unit and the condensing unit are
properly connected to each other and to the
electrical supply voltage circuits;
- e units are continuously powered;
- e units are not in "o" mode.
- e units are not in anomaly (parag. 2.5);
- e unit and/or kit essential components are not
faulty.
e warranty does not cover damage due to inter-
ruption of the electrical power supply and failure
to comply with that stated on the previous page.
N.B.: if the hydronic unit is installed in places
where the temperature drops below 0°C, the
domestic hot water connection pipes must be
insulated.

7
1-3
LP GP
RU MU RR R
M
RU
MU
VRR RM
LP GP
V
INSTALLERUSERMAINTENANCE TECHNICIAN
e hydraulic connection kit includes:
2 - adjustable expansion bolts
2 - hydronic module support hooks
1 - 3/4” storage tank unit return pipe (RU)
1 - 3/4” storage tank unit ow pipe (MU)
1 - 1/2” system lling pipe (RR)
1 - 1/2” ball valve (RR)
1 - 3/4” system return pipe (R)
1 - 3/4” system ow pipe (M)
1 - 3/4” ball valve (M)
2 - Insulating sheath for system pipes (R - M)
4 - 3/4” telescopic ttings (RU - MU - R)
Gaskets, screws and seal O-Ring
e R410A circuit wall connection kit (optional) includes:
1 - G 3/8” liquid phase chiller line pipe (LP)
1 - G 5/8” gaseous phase chiller line pipe (GP)
Already installed on the module:
1 - System interception tap with 3/4” lter (R)
Key:
V - Electrical connection
RR - System lling
RU - Storage tank unit return
MU - Storage tank unit ow
R - System return
M - System ow
LP-Chiller line - liquid phase
GP-Chiller line - gaseous phase
1.4 HYDRONIC MODULE
CONNECTION UNIT.
- e hydraulic connection unit is standard sup-
plied with Magis Pro ErP. Make the hydraulic
connection as shown below, making sure to
protect the system ow and return pipes with
their supplied insulating sheaths.
- The R410A circuit wall connection unit is
supplied as an extra kit. Connect the circuit,
following the instructions provided in the
condensing unit instructions booklet.
1.5 HYDRAULIC CONNECTION.
Attention: in order not to void the product war-
ranty, before making unit connections, carefully
clean the heating system (pipes, radiators, etc.)
with special pickling or de-scaling products to
remove any deposits that could jeopardise proper
hydronic module operation.
A chemical treatment of the heating system water
is required, in compliance with the technical
standards in force, in order to protect the system
and the appliance from deposits (e.g. scale),
slurry or other hazardous deposits.
Hydraulic connections must be made rationally,
using the couplings on the hydronic module
template.
Attention: Immergas declines all liability in the
event of damage caused by the inclusion of auto-
matic lling that is not its own brand.
In order to meet the system requirements es-
tablished by EN 1717 regarding the pollution
of drinking water, we recommend installing the
IMMERGAS anti-backow kit upstream of the
hydronic unit cold water inlet connection. We
also recommend using a category 1, 2 or 3 heat
transfer uid (ex: water + glycol) in the hydronic
unit primary circuit (CH circuit), as dened in
the EN 1717 standard.
Attention: to preserve appliance duration and
eciency features, we recommend installing a
suitable water treatment device if the water has
features that can lead to limescale deposits.
1.6 CONNECTING THE CHILLER LINE.
As far as connecting the chiller line is concerned,
all the instructions contained in the Audax Pro
condensing unit instructions booklet must be
followed.
Make the connections directly on the hydronic
module couplings, or use the rear outlet kit
(optional).

8
1-4
1-5
c
c
d
2
1
a
b
a
a
a
1
1
1
INSTALLERUSERMAINTENANCE TECHNICIAN
1.7 ELECTRIC CONNECTION.
e appliance has an IPX4D degree of protection;
electrical safety of the appliance is achieved only
when it is properly connected to an ecient
earthing system, as specied by current safety
standards.
Attention: Immergas S.p.A. declines any respon-
sibility for damage or physical injury caused by
failure to connect the hydronic module to an
ecient earthing system or failure to comply
with the reference standards.
- Connection cables must respect the prear-
ranged routes. Use 3 clips (c) (not supplied)
to group the individual cables (max. 1.5 mm2
into the lower terminal board. Use the specic
fairleads (d) on the le side, making sure to put
at most 2 multi-polar cables (max 3 x 1 mm2)
in each fairlead.
As an example, gure 1-5 shows cables in a
hypothetical connection. To make the connec-
tions based on your own requirements, see the
instructions below.
• Open the control panel connections compart-
ment (Fig. 1-5).
To carry out electrical connections, all you have
to do is open the connections compartment as
follows.
- Remove the front panel (Fig. 3-5b).
- Remove the cover (b g. 1-4).
1) Loosen the screws (a).
2) Remove the cover (b) from the control
panel (c).
- At this point, you can access the terminal board.
Also ensure that the electrical installation corre-
sponds to the maximum absorbed power speci-
Key:
86 /87 - Summer winter switch 3-way valve
81-2 / 82-2 - Zone 2 circulator
83-2 / 84-2 / 85-2 - Zone 2 mixing valve
82-1 / 81-1 - Zone 1 circulator
89 / L - Audax Pro disabling contact
88 / L - Solar inlet
69 / 70 - Domestic hot water integrated resistance control
38 / 39 - External Probe
37 / 38 - Domestic hot water probe (eliminate R8)
42-1 / 43 - Zone 1 CARV2
42-2 / 43 - Zone 2 CARV2
23-1 / 24 - Zone 1 humidistat or humidity probe
23-2 / 24 - Zone 2 humidistat or humidity probe
25 - Humidity sensor supply voltage
29-1 / 30-1 - Zone 1 dehumidier
29-2 / 30-2 - Zone 2 dehumidier
T+ / T- (MC) - Audax Pro communication bus
T+ / T- (RS485) - Other Immergas appliance communication
bus
41-1 / 40-1 - Zone 1 room thermostat
41-2 / 40-2 - Zone 2 room thermostat
66 / 65 - Puer central heating probe
65 / 64-2 - Zone 2 ow probe
CLOSED OPEN DHW
DIS. AUDAX PRO
COM.

9
1-6 1-7
45
31
58
INSTALLERUSERMAINTENANCE TECHNICIAN
cations shown on the hydronic unit data plate.
e hydronic units are supplied complete with
a special “X”-type power cable without a plug.
e power supply cable must be connected to a
230V ±10% / 50Hz mains supply respecting L-N
polarity and earth connection; this network
must also have a multi-pole circuit breaker with
class III over-voltage category.
To protect from possible dispersions of DC volt-
age, it is necessary to provide a type A dierential
safety device.
When replacing the power supply cable, contact a
qualied company (e.g. the Immergas Authorised
Aer-Sales Technical Assistance Service). e
power cable must be laid as shown (Fig. 1-3).
If the fuses on the electronic boards must be
replaced, use:
- P.C.B.: a T 3.5 A fuse
- heat pump communication board: a T 5.0 A
fuse
For the main power supply to the appliance,
never use adapters, multiple sockets or exten-
sion leads.
1.8 REMOTE CONTROLS AND
ROOM CHRONOTHERMOSTATS
OPTIONAL.
The hydronic module is set up for room
chrono-thermostats or remote controls, avail-
able as optional kits (Fig. 1-6). A maximum of
2 thermo-regulators can be applied directly to
the appliance.
All Immergas chrono-thermostats are connected
with 2 wires only. Carefully read the user and
assembly instructions contained in the acces-
sory kit.
• On/O Immergas digital chrono-thermostat.
e chrono-thermostat allows:
- set two room temperature value: one for
daytime (comfort temperature) and one for
night-time (reduced temperature);
- set a weekly program with four daily switch
on and switch o times;
- select the required operating mode from the
various possible alternatives:
• manual operation (with adjustable tempera-
ture).
• automatic operation (with set programme).
• forced automatic operation (momentarily
changing the temperature of the automatic
programme).
e chrono-thermostat is powered by two 1.5V
LR 6 type alkaline batteries.
• Comando Amico Remoto Remote Control
Device V2 (CARV2) with climate chrono-ther-
mostat function. In addition to the functions
described in the previous point, the CARV2
panel enables the user to control all the im-
portant information regarding operation of
the appliance and the heating system with the
opportunity to easily intervene on the pre-
viously set parameters, without having to go
to where the appliance is installed. e panel
is equipped with self-diagnosis to show any
appliance operating anomalies on the display.
e climate chrono-thermostat incorporated
into the remote panel enables the system ow
temperature to be adjusted to the actual needs
of the room being heated or cooled, in order
to obtain the desired room temperature with
extreme precision and therefore with evident
savings in running costs. e CARV2 is powered
directly by the hydronic module by the same
2 wires used to transmit data between the
hydronic module and the device.
Important: the hydronic module is set up to be
able to work with two CARV2 used to control two
separate hydraulic zones.
Comando Amico Remoto Remote Control V2
or On/O chrono-thermostat electrical con-
nections (Optional). e operations described
below must be performed aer having removed
the voltage from the appliance.
-On/O ambient thermostat or chrono-ther-
mostat: must be connected to the 40-1 / 41-1
terminals, eliminating the X40-1 jumper for
zone 1 and 40-1 / 41-1 for zone 2. Make sure
that the On/O thermostat contact is of the
“clean” type, i.e. independent of the mains volt-
age, otherwise the P.C.B. would be damaged.
- V2 Comando Amico Remoto remote control
must be connected to terminals 42-1 / 43 for
zone 1 and 42-2 / 43 for zone 2, keeping the
X40-1 jumper for the CARV2 in zone 1 and add-
ing another one for zone 2 on terminals 40-2
and 41-2, being careful not to invert polarity
in the connections.
e connections must be made on the terminal
board inside the appliance control panel as de-
scribed in gure 1-5.
Important: if the Comando Amico Remo-
to Remote Control V2 or any other On/Off
chrono-thermostat is used, arrange two separate
lines in compliance with current regulations re-
garding electrical systems. e hydronic module
pipes must never be used to earth the electrical
or telephone system. Make sure this does not
happen before making the hydronic module
electrical connections.
1.9 EXTERNAL TEMPERATURE PROBE.
In general, Magis Pro ErP uses the probe stand-
ard supplied on the condensing unit to read the
outdoor temperature.
If the condensing unit is positioned in an area
that is not suitable for temperature reading, it
is advisable to use an additional external probe
(Fig. 1-7), which is available as an optional kit.
Refer to the relative instruction sheet to position
the optional external probe.
e probe can be connected directly to the hy-
dronic module electrical system and allows the
system ow temperature to be set automatically
based on the outdoor temperature in order to
adapt the heat or cooling provided to the system.
e external probe always operates when con-
nected, regardless of the presence or type of room
chrono-thermostat used and can work in com-
bination with Immergas chrono-thermostats.
e correlation between system ow temperature
and outdoor temperature is managed dierently
based on whether the system is managed directly
by the hydronic module or by the CARV2; the
parameters set on the chrono-thermostat take
priority over those set on the hydronic module.
- Hydronic module: the system ow temperature
is determined by the setting on the "Heat reg-
ulation" menu and by the "User" menu for the
oset values based on the curves shown in the
diagram (Fig. 1-8).
- CARV2: the system ow temperature is deter-
mined by the setting on the central heating
selector (which can be adjusted from 0 to 9)
and by the "Oset" value on the "Regulat." menu
based on the curves shown in the correspond-
ing instructions booklet.
N.B.: if the system is divided into two zones,
the ow temperature is calculated based on the
zone with the higher temperature in central
heating mode and with the lower temperature
in cooling mode.
e electric connection of the external probe
must be made on terminals 38 and 39 on the
terminal board on the hydronic module control
panel (Fig. 1-5).

10
1-8
R13
R12
R11 R10
U05
R17
R16
R15 R14
U06
Set Risc
U01
Z1
Z2
Set Raresc
U02 Z2
Z1
R04
R05
R02 R03
U03
R08
R09
R06 R07
U04
INSTALLERUSERMAINTENANCE TECHNICIAN
Zone 1 ow temperature in central heating mode, with
external probe
Zone 1 ow temperature in cooling mode, with exter-
nal probe
Flow temperature in central heating mode without
external probe
Flow temperature in cooling mode without external
probe
Zone 2 mixed ow temperature in central heating
mode, with external probe
Zone 2 mixed ow temperature in cooling mode, with
external probe
Key:
Rxx - "Heat regulation" menu parameter
TE - Outdoor temperature
TM - Flow temperature
U01 - Zone 2 ow temperature in "User" menu central
heating mode
U02 - Zone 2 ow temperature in "User" menu cooling
mode
U03÷06 - Oset value compared to the curve set by the
external probe
Zx - Heating system zone
1.10 HEAT REGULATION SETTING.
By setting the parameters in the "Heat regulation"
menu, you can adjust how the system operates.
e curves (Fig. 1-8) show the default settings in
the various operating modes available both with
external probe and without.

11
1-9
INSTALLERUSERMAINTENANCE TECHNICIAN
1.11 FILLING THE SYSTEM.
Once the hydronic module is connected, ll the
heating system using the lling cock (Fig. 1-33
and 1-4). Filling must be done slowly to allow
the air bubbles in the water to escape through
the vents in the hydronic module and the heating
and air conditioning system.
e hydronic module has one incorporated automatic
vent valve located on the circulator and another on
the central heating manifold. Make sure that the hoods
are loosened.
e lling cock must be closed when the hy-
dronic module pressure gauge indicates approx-
imately 1.2 bar.
N.B.: during these operations, enable the "Vent-
ing" functions by setting the "M01" parameter to
ON, which lasts about 18 hours (see the "P.C.B.
programming" paragraph).
System minimum water content.
Minimum water content is mainly important to
provide proper execution of defrosting cycles.
To this end, the minimum amount of water to
guarantee is 7 l/kW for any type of system.
N.B.: it is also important to check that the
dehumidier line has a minimum of 3 l/kW
(dehumidier hydraulic circuit connection).
1.12 OPERATING LIMITS.
e system was designed to work in a specic
range of temperatures and at a specic maximum
ow temperature. e graphic (Fig. 1-9) shows
these limits.
1.13 COMMISSIONING THE HYDRONIC
MODULE IGNITION.
The following requirements must be met to
commission the hydronic module in order to
issue the Declaration of Conformity, if required
by the technical standards in force (the following
operations must be done only by professionally
qualied personnel and in the presence of pro-
fessionals only):
- check that the internal system is properly sealed
according to the specications set forth by
technical regulations in force;
- check connection to a 230V-50Hz power
mains, correct L-N polarity and earthing
connection;
- switch on the hydronic module and check for
proper ignition;
- check the operation of the main switch located
upstream of the hydronic module and on the
module itself;
Should even just one of these checks have a
negative outcome, the system must not be
commissioned.
Operating limits in central heating mode Operating limits in cooling mode
Key:
TE = Outdoor temperature.
TM = Flow temperature

12
1-10
INSTALLERUSERMAINTENANCE TECHNICIAN
1.14 CIRCULATION PUMP.
e hydronic modules are supplied with a varia-
ble speed circulator, which operates at the speed
set in the "A04" parameter (which can be set
between 55% and 100%). e minimum speed
set on the "A03" parameter is used for special
functions (e.g. pump anti-locking function).
Attention: for proper system operation, make
sure that the minimum ow in operating condi-
tions never drops below 500 l/h.
Pump release. If, aer a prolonged period of
inactivity, the circulation pump is blocked, turn
the motor sha using a screwdriver. Take great
care during this operation to avoid damage to
the motor.
Total head available to the system.
Head (kPa)
A+B = Head available with by-pass closed
B = Head available with by-pass open
C+D = Power absorbed by the pump with by-pass open (dotted area)
D = Power absorbed by the pump with by-pass closed (dotted area)
By-pass Regulation (part. 17 Fig. 1-11). e
hydronic module comes out of the factory with
the by-pass closed.
If necessary, the by-pass can be regulated to
system requirements from minimum (by-pass
closed) to maximum (by-pass open). Adjust
using a at head screwdriver, turn clockwise
and open the by-pass, anticlockwise it is closed.
Circulator pump absorbed power (W)
Flow rate (l/h)
A
B
C
D
Max. speed
Max. speed
Min. speed

13
1-11
INSTALLERUSERMAINTENANCE TECHNICIAN
1.15 HYDRONIC MODULE COMPONENTS.
Key:
1 - Domestic hot water inlet valve
2 - System lling valve
3 - 3-bar safety valve drain tting
4 - Inspectable lter
5 - 3 bar safety valve
6 - Hydronic unit circulator
7 - Vent valve
8 - Liquid phase detection probe
9 - System expansion vessel
10 - Flow probe
11 - Plate heat exchanger
12 - Vent valve
13 - Central heating integrated electrical
resistance cap (optional)
14 - Central heating manifold
15 - System ow meter
16 - Return probe
17 - By-pass
18 - ree-way valve (motorised)
19 - System draining valve
20 - System cut-o tap
21 - System cut-o tap
1.16 KITS AVAILABLE ON REQUEST.
• 3 kW heating system integrated resistance
kit. Should it be necessary, you can install an
electrical resistance to supplement the central
heating system; this resistance can be installed
directly inside the hydronic module.
• 2 zone kit (1 direct and 1 mixed). Should it be
necessary, you can install the zone kit, which
allows you to divide the heating system into
two separate zones - one direct and one mixed.
• Congurable relay interface kit. e module
is set up for a relay board, which amplies the
appliance features and, thus, the operating
possibilities.
• 2 relay board kit. e hydronic module can
manage up to two dehumidiers. A 2 relay
board that manages dehumidier enabling is
available to pair the appliances.
• R410A circuit connection kit. For R410A
circuit wall connections, there is a kit with the
two pipes necessary to create the circuit.
e above-mentioned kits are supplied complete
with instructions for assembly and use.

14
2-1
INSTALLERUSERMAINTENANCE TECHNICIAN
2USE AND MAINTENANCE
INSTRUCTIONS
2.1 CLEANING AND MAINTENANCE.
Attention: to preserve system integrity and keep
the distinguishing safety features, performance
and reliability unchanged over time, you must
execute maintenance operations at least on a
yearly basis in compliance with what is stated in
the point regarding “annual appliance check and
maintenance”. Annual maintenance is essential to
validate the conventional warranty of Immergas.
We recommend stipulating a yearly cleaning and
maintenance contract with your zone Immergas
Authorised Aer-sales Service.
2.2 GENERAL WARNINGS.
Do not expose the hydronic module to direct
steam from cooking surfaces.
Children and unskilled persons are not allowed
to use the hydronic module.
Should you decide to temporarily shut down the
hydronic module, you must:
a) drain the heating system if antifreeze is not
used;
b) shut o the electrical and water supply.
Never clean the appliance or connected parts
with easily ammable substances.
Never leave containers or ammable substances
in the same environment as the appliance.
• Attention: using any components that use
electrical power requires some fundamental
rules to be observed:
- do not touch the appliance with wet or moist
parts of the body; do not touch when bare-
foot;
- never pull electrical cables or leave the appli-
ance exposed to weathering (rain, sunlight,
etc.);
- the appliance power cable must not be re-
placed by the user;
- in the event of damage to the cable, switch
off the appliance and contact exclusively
qualied sta for replacement;
- if the appliance is not to be used for a certain
period, disconnect the main power switch.
N.B.: the temperatures shown on the display
have a tolerance of +/- 3°C due to environmen-
tal conditions that cannot be attributed to the
hydronic module.
At the end of its service life, the appliance must
not be disposed of like normal household waste
nor abandoned in the environment, but must
be removed by a professionally authorised
company. Contact the manufacturer for disposal
instructions.
2.3 CONTROL PANEL.
Key:
1 - Operating mode (winter - heating/air
conditioning - summer - stand-by - o)
and parameter conrm button
2 - Menu selection button
3 - Reset and exit menu button
4 - Domestic hot water temperature selec-
tion buttons
5 - Heating system temperature selection
buttons
6 - Hydronic module pressure gauge
7 - Remote control connection (optional)
8 - Condensing unit operation in progress
9 - Not used
10 - Dispensed output level
11 - Operation with external temperature
probe active (optional)
12 - Connection to other Immergas units
13 - Room central heating mode active
14 - Temperature indicator, hydronic module
info and error codes
15 - Room cooling mode operation active
16 - Operation in cooling mode
17 - Operation in winter mode
18 - Operation in summer mode
19 - Stand-by mode
20 - Not used
21 - Hydronic module locked, requiring
release by "RESET" button
22 - Operation in dehumidication mode
23 - DHW production phase operating mode
active
ESC OK
bar

15
INSTALLERUSERMAINTENANCE TECHNICIAN
2.4 SYSTEM USE.
Before ignition, make sure the system is full of
water, checking that the pressure gauge needle
(6) points to a value between 1 and 1.2 bar and
make sure that the chiller circuit has been lled
as described in the condensing unit instructions
booklet.
- Press the button (1) until the display switches
on. e system now goes back to the state prior
to switch-o.
- If the hydronic module is in stand-by, press the
button (1) again to activate it. Otherwise, go to
the next point.
- en press the button (1) in sequence and set
the system to summer ( ), winter ( ) or
heating/air conditioning ( ) position.
• Summer ( ):in this mode, the system only
works to produce domestic hot water, the
temperature is set using the buttons (4) and
the corresponding temperature is shown on
the display by the indicator (14).
Summer and DHW heating in
progress mode 2-2
• Winter ( ):in this mode, the system works
both to product domestic how water and room
central heating. e temperature of the DHW
is always regulated via buttons (4), the central
heating temperature is regulated via buttons
(5) and the relative temperature is shown on
the display by the indicator (14).
Winter and room central heating in
progress mode 2-3
•Heating/air conditioning ( ): in this mode,
the system works both to produce DHW and to
cool the room. e temperature of the DHW
is always regulated via buttons (4), the cooling
temperature is regulated via buttons (6) and the
relative temperature is shown on the display by
the indicator (14).
Heating/Air conditioning and room
cooling in progress mode 2-4
From here on, the system works automatically.
If there are no requests (room central heating,
DHW production or cooling), the system goes
into the "stand-by" function. Each time the
condensing unit ignites, the display shows the
corresponding symbol (8) with the correspond-
ing power scale (10).
• Operation with Comando Amico RemotoV2
(CARV2) (Optional). If the CARV2 is connected,
the ( ) symbol will appear on the display.
e system regulation parameters can be set via
the CARV2 control panel and the reset button
(3) remains active on the hydronic module
control panel, along with the switch-o button
(1) (“o” mode only) and the display showing
the functioning state.
e system is set up to manage two CARV2.
e CARV2 connected to the main zone (zone
2 or low temperature) is considered as the
hydronic module mount panel, while the
CARV2 connected to the secondary zone (zone
1 or high temperature) manages the requests
in the corresponding zone. Consequently, the
"secondary" CARV2 is not to be considered as
the hydronic module mount panel.
Attention: if the hydronic module is switched
“o” the CARV2 will display the connection
error symbol “ERR>CM”. e CARV2 is still
powered constantly so as not to lose the saved
programs.
•Operation with external probe ( ).e
system is set up to use the condensing unit
external probe or an optional external probe.
With the external probe connected, the system
ow temperature for room heating and air
conditioning is managed by the external probe
based on the outdoor temperature measured
(Parag. 1.9). You can change the ow tempera-
ture by choosing the oset value in the specic
user menu. If the CARV2 is connected, you can
change the operating curve using the controls
on it, selecting a value from "0 to 9" (See CARV2
instructions). In this case, any settings made
on the hydronic module will not aect system
operation.
• Dehumidify ( ). If the system is paired with
a humidistat (optional) or a humidity temper-
ature sensor (optional), you can manage the
room humidity in summer air conditioning
mode.
- If paired with a humidistat, set the degree
of humidity on the humidistat itself (see the
instructions booklet).
- If paired with a humidity temperature sensor,
set the humidity percentage in the corre-
sponding user menu or, if there is a CARV2,
you can set it on the remote control itself from
the "S UR %" parameter.
Heating/Air conditioning and
Dehumidication active mode 2-5
• In central heating or cooling request mode,
if the temperature of the water in the system
meets the request, the system can work simply
by activating the circulator.
• “Stand-by” mode. Press button (1) repeatedly
until the symbol ( ) appears. From then on,
the system remains inactive and the antifreeze
function, pump anti-block function and 3-way
and signalling of any anomalies is guaranteed.
N.B.: in these conditions the system must still
be considered powered.
• “O” mode. By holding the button (1) down
for 8 seconds, the display switches o and the
hydronic module is completely o. e safety
functions are not guaranteed in this mode.
N.B.: in these conditions, the hydronic module
must still be considered powered even if there
are no functions active.
• “Automatic vent” mode. Every time the
hydronic module is electrically powered, the
system automatic vent function is activated
(lasting 8 minutes). is function is displayed
via a countdown signalled by the indicator (14).
During this period the DHW and CH functions
are not active.
e “automatic vent” can be annulled by press-
ing the “reset” button (3).
• Display operation. e display lights up while
the control panel is being used; aer a set in-
activity period, the brightness drops until only
the active symbols are displayed. e lighting
mode can be varied via parameter t8 in the
P.C.B. programming menu.

16
INSTALLERUSERMAINTENANCE TECHNICIAN
2.5 TROUBLESHOOTING.
e hydronic module signals any anomalies by
ashing a code on the display (14) according to
the following table.
Hydronic module error codes are preceded by
the letter "E", while error codes referring to
the condensing unit are preceded by the letter
"A". For the latter, refer to the condensing unit
booklet for the complete list of all the anomalies.
e CARV2 displays error codes with only the
last two digits (e.g. E184 = ERR 84).
Error
Code Anomaly signalled Cause Hydronic module status / Solution
E 2
Safety thermostat
block (over-temper-
ature)
During normal operation, if a fault causes excessive overheating
internally, the boiler goes into overheating block. Press the Reset button (1)
E 5 Flow probe anomaly e board detects an anomaly on the ow NTC probe. e system does not start (1).
E 12 Storage tank probe
anomaly e board detects an anomaly on the storage tank probe e hydronic module is unable to pro-
duce domestic hot water (1).
E 23 Return probe anomaly e board detects an anomaly on the return NTC probe e system does not start (1).
E 24 Push button control
panel anomaly e board detects an anomaly on the pushbutton panel.
If normal conditions are restored, the
system restarts without having to be reset
(1).
E 26 System owmeter
anomaly
e board detects an anomaly on the system owmeter.
Return pump (optional) always working.
e system does not start (1).
Make sure the return pump (optional) only
activates when requested.
E 27 Insucient circulation
is happens when the hydronic module overheats due to poor water
circulation in the primary circuit. e causes can be:
- low system circulation; check that no shut-o devices are closed on
the central heating circuit and that the system is free of air (deaer-
ated);
- pump blocked; free the pump.
Press the Reset button (1).
E 31
Loss of communica-
tion with the CARV2
(zone 1)
is happens when an incompatible remote control is connected or
when communication between the hydronic module and CARV2 is lost.
Cut power to the hydronic module then
power it back on. If the Remote Control is
still not detected at restart, the system will
switch to local operating mode, i.e. using
the controls on the control panel. In this
case the “Central Heating” (1) mode cannot
be activated.
E 32 Low temperature zone 2
probe anomaly
If the board detects an anomaly on the low temperature zone 2 probe,
the system cannot work in the aected area. (1)
E 37 Low power supply
voltage
is occurs when the power supply voltage is lower than the allowed
limits for correct system operation.
If normal conditions are restored, the sys-
tem restarts without having to be reset (1)
46 Low temperature safety
thermostat (optional)
During normal operation, if an anomaly causes excessive overheating
of the ow temperature in the low temperature zone, the unit indicates
the malfunction.
e unit does not meet the zone central
heating requirement. (1)
E 50 External probe missing
or faulty
In the event the external probe is not connected or is faulty, the
anomaly is indicated.
Check the external probe connection.
e system continues to operate with the
external probe integrated in the condensing
unit (1).
E 54
Central heating storage
tank probe anomaly
(optional)
e central heating storage tank has an out of range resistive value Puer mode is disabled. (1)
E 129 Zone 1 humidity probe
anomaly
Anomaly on the zone 1 humidity probe (optional). Zone humidity
cannot be checked.
In addition to the humidity, the dew point
is not calculated for the zone (1) either
E 130 Zone 2 humidity probe
anomaly
Anomaly on the zone 2 humidity probe (optional). Zone humidity
cannot be checked.
In addition to the humidity, the dew point
is not calculated for the zone (1) either
E177 DHW maximum time
alarm
Domestic hot water production is not met within the pre-estab-
lished time
e system continues to operate with
non-optimal performance (1)
E178 Anti-Legionella cycle
not successful
e anti-Legionella cycle is run without success within the pre-es-
tablished time (1)
E179 Liquid phase probe
anomaly e board detects an anomaly on the liquid phase NTC probe. e system does not start (1).
(1) If the block or anomaly persists, contact an authorised company (e.g. Immergas Technical Aer-Sales Service).

17
INSTALLERUSERMAINTENANCE TECHNICIAN
Error
Code Anomaly signalled Cause Hydronic module status / Solution
E181
Loss of communica-
tion with the CARV2
(zone 2)
is happens when an incompatible remote control is connected
or when communication between the hydronic module and second
zone CARV2 is lost.
Cut power to the hydronic module then
power it back on. If the Remote Control is
still not detected at restart, the system will
switch to local operating mode, i.e. using
the controls on the control panel. In this
case the “Central Heating” (1) mode cannot
be activated.
E182 Condensing unit alarm An anomaly appears on the condensing unit
e system does not work, see the
anomaly on the condensing unit and its
instructions booklet (1)
E183 Condensing unit in test
mode A signal noties that the condensing unit is in test mode
During this time, room heating/air condi-
tioning and domestic hot water produc-
tion requirements cannot be met
E184 Communication error
with condensing unit
A signal noties an anomaly due to a communication problem
between the hydronic module and the condensing unit.
Have the electrical connection between
the units checked.
e system does not start (1).
E188 Request with tempera-
ture out of range
A request is made with the outdoor temperature exceeding the
operating limits (parag. 1.12) e system does not start (1).
E189 Time out alarm with
communication board
If communication between the printed circuit boards is lost, an
anomaly is signalled. (1)
(1) If the block or anomaly persists, contact an authorised company (e.g. Immergas Technical Aer-Sales Service).

18
INSTALLERUSERMAINTENANCE TECHNICIAN
2.6 PARAMETERS AND INFORMATION
MENU.
Pressing the "MENU" button (2), the display
cyclically shows the "Data" menu, "User" menu
and a menu protected by a "0000" access code
with the rst ashing digit reserved for a qualied
technician.
Id
Parameter Description Range
D 03 Storage tank unit temperature 0 ÷ 99 °C
D 04 Value calculated for system setting 0 ÷ 99 °C
D 05 Value set for DHW setting 0 ÷ 99 °C
D 06 Outdoor temperature (if the condensing unit external probe is connected or if the optional external probe is availa-
ble) - 20 ÷ 50 °C
D 08 System return water temperature 0 ÷ 99 °C
D 09 List of the last ve anomalies.
(to scroll through the list, press the "OK" button (1)) D91 ÷ D95
D 10 Anomaly list reset. Once "D 10" is displayed, press the "OK" button. Deletion is conrmed via the "88" symbols
ashing for two seconds. -
D 14 Circulator ow rate 0 ÷ 9999
(x 100 l/h)
D 20 System ow temperature 0 ÷ 99 °C
D 22 DHW 3-way (DHW = domestic hot water, CH = central heating) DHW - CH
D 24 Chiller circuit liquid temperature - 20 ÷ 99 °C
D 25 Zone 2 ow temperature (if congured) 0 ÷ 99 °C
D 26 Probe for primary solar storage (puer) 0 ÷ 99 °C
D 28 System circulator instantaneous speed 0 ÷ 100 %
D 31 DHW integration function OFF - ON
D 32 System integration function OFF - ON
D 35 Solar system inlet OFF - ON
D 41 Zone 1 relative humidity 0 ÷ 99 %
D 42 Zone 2 relative humidity 0 ÷ 99 %
D 43 Zone 1 humidistat OFF - ON
D 44 Zone 2 humidistat OFF - ON
D 45 Dehumidier zone 1 OFF - ON
D 46 Dehumidier zone 2 OFF - ON
D 47 Zone 1 circulator pump OFF - ON
D 48 Zone 2 circulator pump OFF - ON
D 49 Central heating / cooling system separation 3-way (CL = cooling, HT = heating) CL - HT
D 51 Zone 1 remote control OFF - ON
D 52 Zone 2 remote control OFF - ON
D 53 System setting with remote connection in zone 1 0 ÷ 99 °C
D 54 System setting with remote connection in zone 2 0 ÷ 99 °C
D 55 Zone 1 thermostat OFF - ON
D 56 Zone 2 thermostat OFF - ON
D 61 Appliance model denition MP
D 62 Communication with outdoor condensing unit OFF - ON
D 63 Communication with other Immergas devices OFF - ON
D 71 Condensing unit operating frequency 0 ÷ 150 Hz
D 72 Condensing unit compressor temperature 0 ÷ 200 °C
D 73 Compressor outlet instantaneous temperature 0 ÷ 100 °C
D 74 Evaporator coil temperature 0 ÷ 100 °C
D 75 Condensing unit compressor absorption 0 ÷ 10 A
D 76 Condensing unit fan speed 0 ÷ 100 rpm
D 77 Electronic expansion valve position 0 ÷ 500
D 78 4-way side (CL = cooling, HT = heating) HT / CL
D 91 Soware version
To access an individual menu, once it appears,
press the "OK" button (1).
To scroll through the menu items and to edit the
values, use the DHW temperature regulation but-
tons (4). Pressing the "OK" button (1) conrms
the parameter, pressing the "ESC" button (3) goes
back to the previous menu or exits.
A minute aer the last operation, the system
automatically exits any of the menus.
Data Menu.

19
INSTALLERUSERMAINTENANCE TECHNICIAN
2.7 SWITCHING OFF THE HYDRONIC
MODULE.
Switch o the hydronic module, putting it in
"o" mode. Switch o the omni-polar switch
outside the unit. Never leave the unit powered if
le unused for prolonged periods.
2.8 RESTORING CENTRAL HEATING
SYSTEM PRESSURE.
Periodically check the system water pressure.
e hydronic module pressure gauge must show
a value between 1 and 1.2 bar.
If the pressure is less than 1 bar (with the system
cold), you must restore it using the cock located at
the bottom of the unit (Fig. 1-3).
N.B.: close the cock aer the operation.
If pressure values reach around 3 bar the safety
valve may be activated.
In this case, remove water from an air vent valve
of a radiator until reaching pressure of 1 bar, or
ask for assistance from professionally qualied
personnel.
In the event of frequent pressure drops, contact
qualified staff for assistance to eliminate the
possible system leakage.
2.9 SYSTEM DRAINING.
To drain the hydronic mdule, use the special
drain tap (Fig. 1-3).
Before draining, ensure that the lling cock is
closed.
2.10 ANTIFREEZE PROTECTION.
e hydronic module has an anti-freeze function
that automatically switches on the condensing
unit when the temperature drops below 4°C
(standard protection up to a minimum temper-
ature of -5°C). All information relative to the
anti-freeze protection is stated in Par. 1.3. In
order to guarantee the integrity of the appliance
and the domestic hot water heating system in
areas where the temperature drops below zero,
we recommend protecting the central heating
system using anti-freeze liquid and installing the
Immergas Anti-freeze Kit in the hydronic mod-
ule. In the case of prolonged inactivity (second
case), we also recommend that:
- disconnect the electric power supply;
- completely empty the central heating circuit
and the hydronic module domestic hot water
circuit. In systems that are drained frequently,
lling must be carried out with suitably treated
water to eliminate hardness that can cause lime-
scale.
2.11 CASE CLEANING.
Use damp cloths and neutral detergent to clean
the hydronic module casing. Never use abrasive
or powder detergents.
2.12 DECOMMISSIONING.
Should the system be shut down permanently,
have professional sta carry out the procedures,
making sure that the electrical and water supply
lines have been previously shut o.
Id
Parameter Description Range Default Value
range
U 01 Zone 2 central heating setting 25 ÷ 55 °C 25
U 02 Zone 2 cooling setting 7 ÷ 25 °C 20
U 03 Zone 1 central heating oset You can edit the ow temperature with respect to the
external probe regulation curve in central heating
mode (Fig. 1-xx Oset value)
- 15 ÷ + 15 °C 0
U 04 Zone 2 central heating oset - 15 ÷ + 15 °C 0
U 05 Zone 1 central heating oset You can edit the ow temperature with respect to the
external probe regulation curve in cooling mode (Fig.
1-xx Oset value)
- 15 ÷ + 15 °C 0
U 06 Zone 2 central heating oset - 15 ÷ + 15 °C 0
U 07 Zone 1 humidity setting e humidity temperature sensor (optional) denes
room humidity in the corresponding area
30 ÷ 70 °C 50
U 08 Zone 2 humidity setting 30 ÷ 70 °C 50
U 11 Night function
is function can only be activated if CARV2 (optional)
is available
Activating the function allows you to disable condensing
unit operation during the time slot set in the U 12 and
U 13 parameters.
Make sure the additional power sources needed to meet
potential requirements that may present themselves
during active operation are available (e.g. additional
resistances)
OFF - ON OFF
U 12 Night function enabling time 0 ÷ 23 0
U 13 Night function disabling time 0 ÷ 23 0
N.B.: the parameters referring to zone 2 can only be displayed if there is a zone 2 on the system and it is congured correctly.
User Menu.

20
3-1
INSTALLERUSERMAINTENANCE TECHNICIAN
3COMMISSIONING THE
PACKAGE INITIAL
CHECK
To commission the package, you must:
- make sure that the declaration of conformity
for installation is supplied with the appliance;
- check connection to a 230V-50Hz power
mains, correct L-N polarity and the earthing
connection;
- make sure the central heating system is lled
with water and the hydronic module pressure
gauge reads a pressure of 1÷1.2 bar;
- make sure the chiller circuit has been lled
according to what is described in the Audax
Pro condensing unit instructions booklet;
- check the operation of the main switch located
upstream of and on the hydronic module.
- ensure activation of all adjustment devices;
- check the production of domestic hot water;
- check sealing eciency of water circuits;
Even if just one single safety check provides a
negative result, do not commission the system.
3.1 HYDRONIC MODULE HYDRAULIC DIAGRAM
Key:
1 - System cut-o tap
2 - 3 bar safety valve
3 - Hydronic unit circulator
4 - Vent valve
5 - System draining valve
6 - Liquid phase detection probe
7 - System ow meter
8 - System expansion vessel
9 - Return probe
10 - Plate heat exchanger
11 - Vent valve
12 - Central heating integrated electric
resistance (optional)
13 - Central heating manifold
14 - Flow probe
15 - System lling cock
16 - ree-way valve (motorised)
17 - By-pass
18 - System with inspectable lter cut-o
tting
19 - System cut-o tap
LP - Chiller line - liquid phase
GP - Chiller line - gaseous phase
RU - Storage tank unit return
MU - Storage tank unit ow
RR - System lling
R - System return
M - System ow
This manual suits for next models
3
Table of contents
Other Immergas Control Unit manuals
Popular Control Unit manuals by other brands
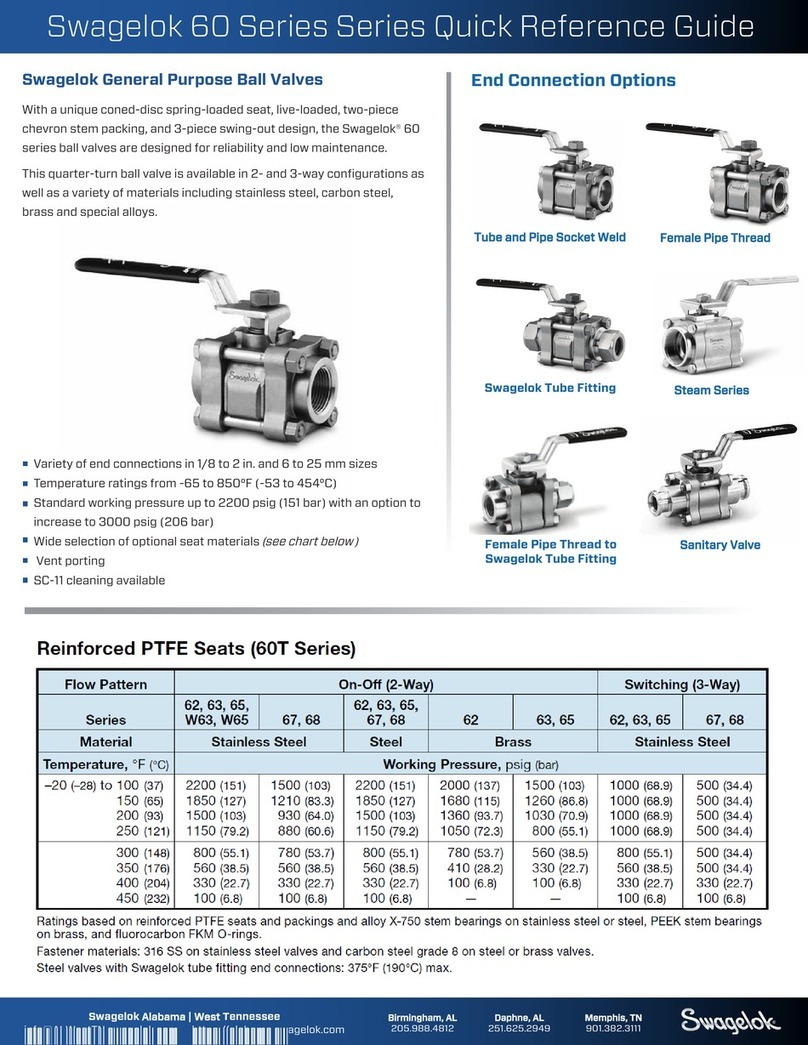
Swagelok
Swagelok 60 Series Quick reference guide
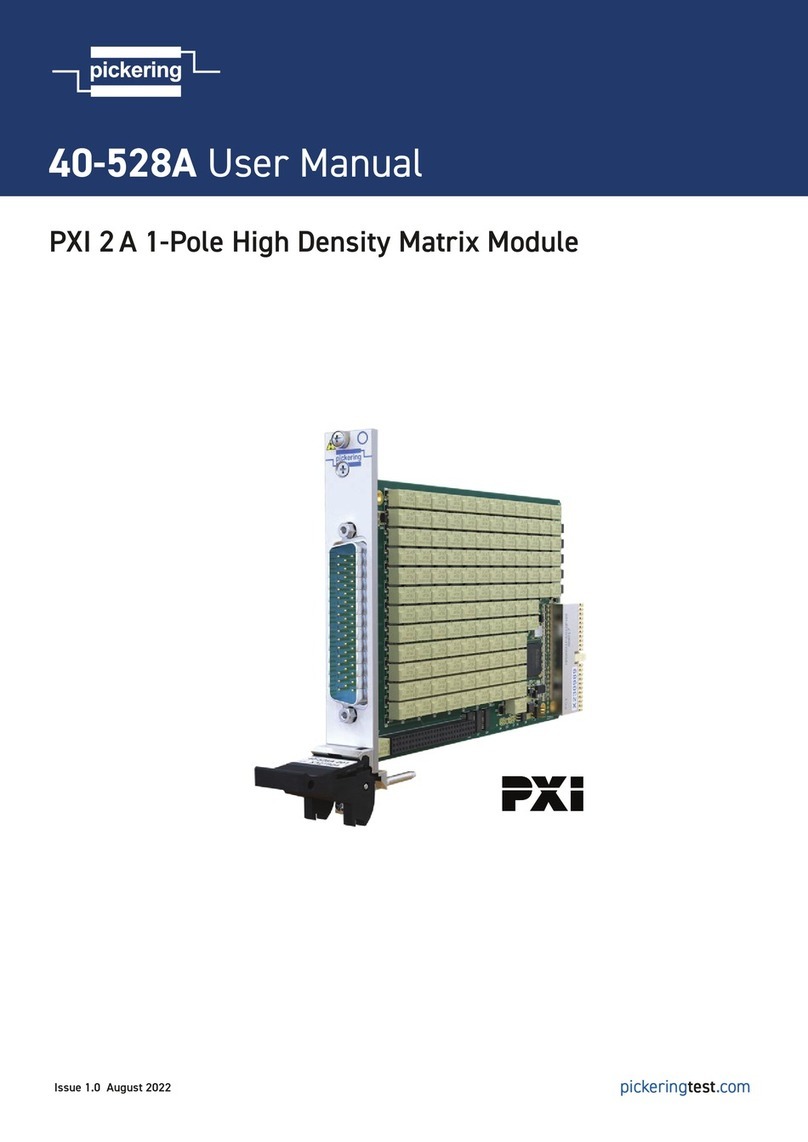
Pickering
Pickering 40-528A user manual
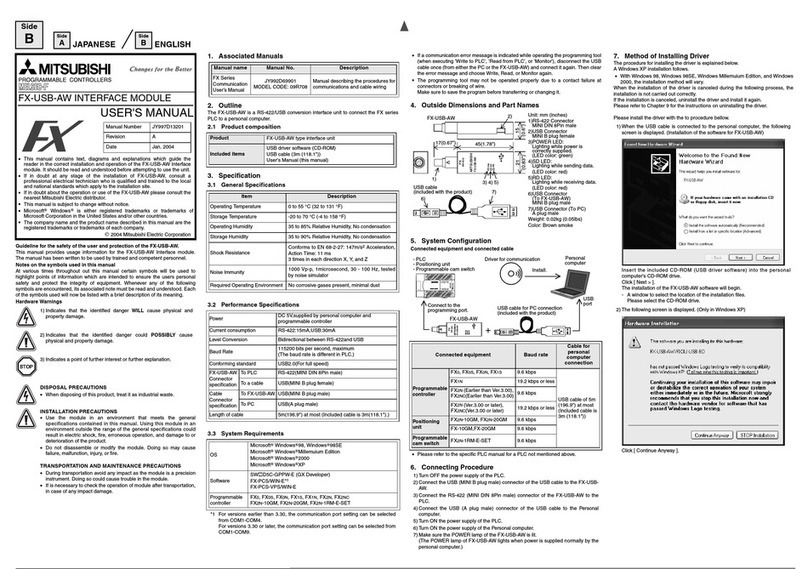
Mitsubishi Electric
Mitsubishi Electric FX-USB-AW user manual
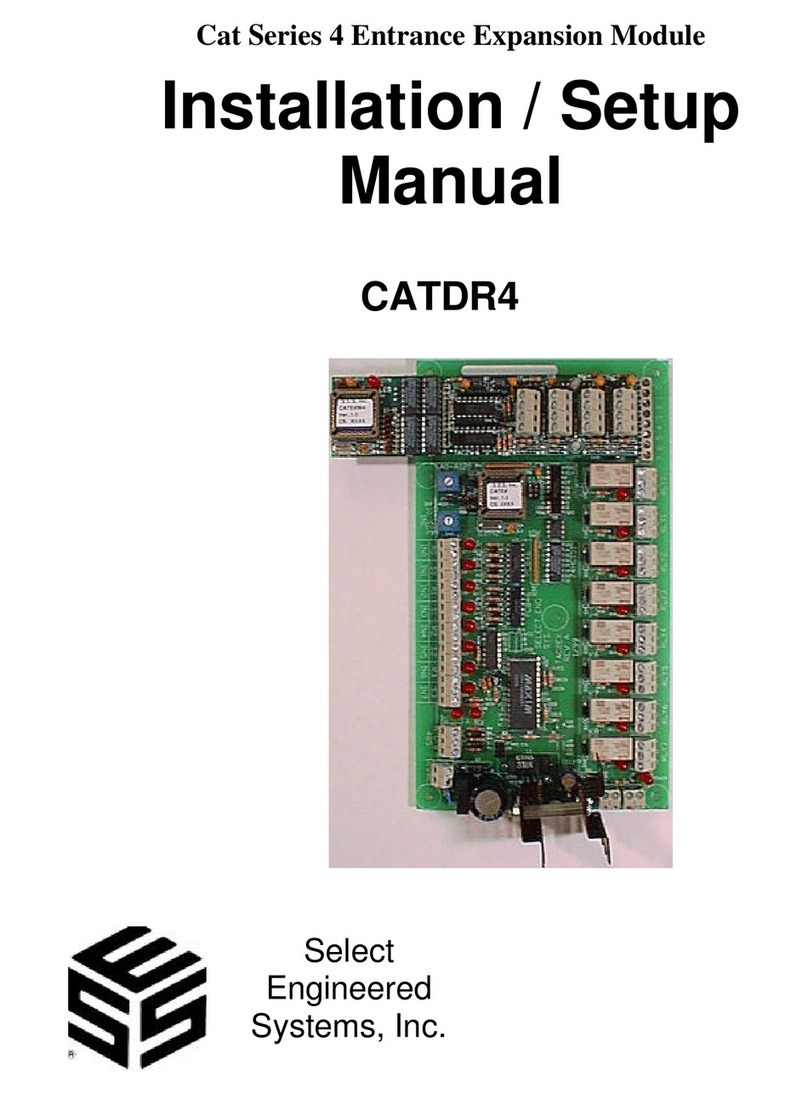
Select Engineered Systems
Select Engineered Systems CATDR4 Installation setup manual
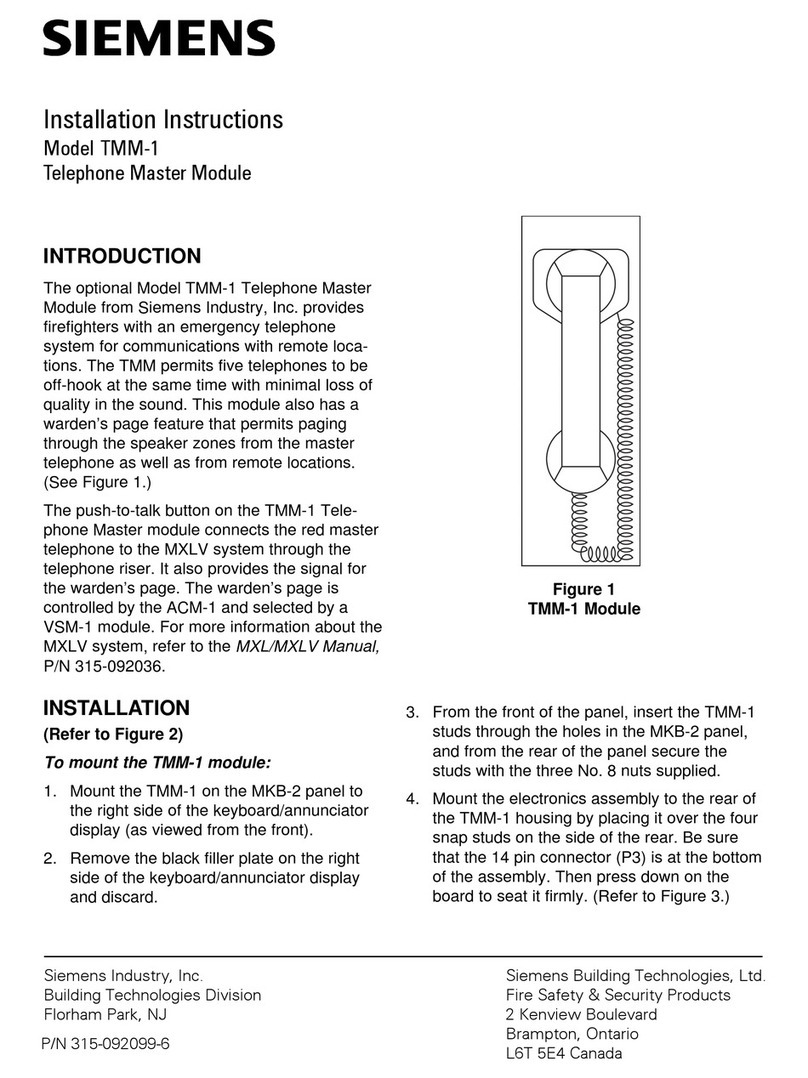
Siemens
Siemens TMM-1 installation instructions
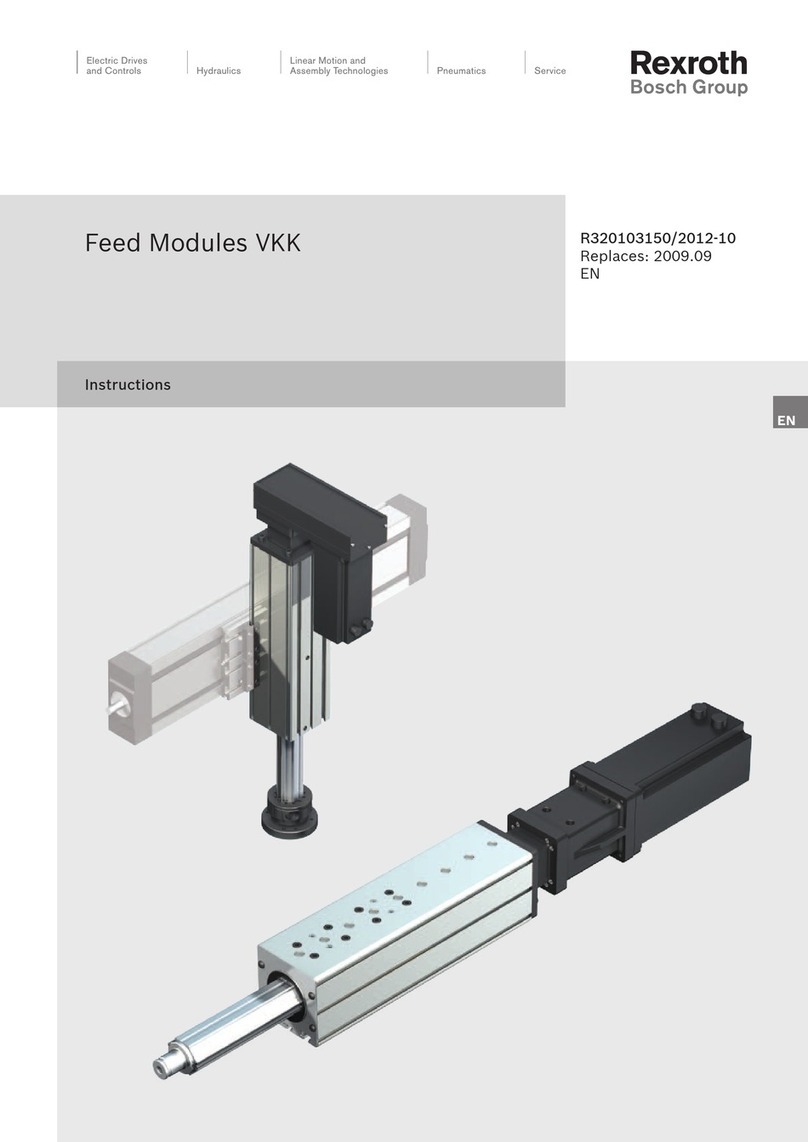
Bosch
Bosch Rexroth VKK instructions
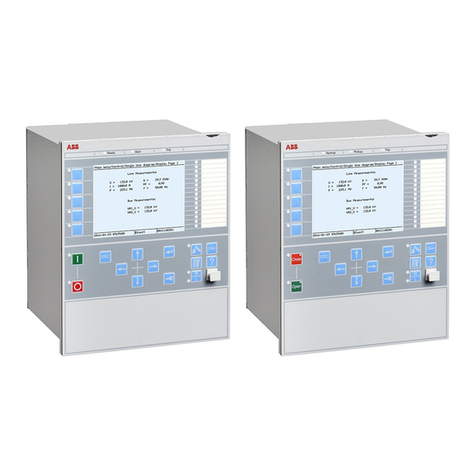
ABB
ABB RELION 650 SERIES Point List Manual
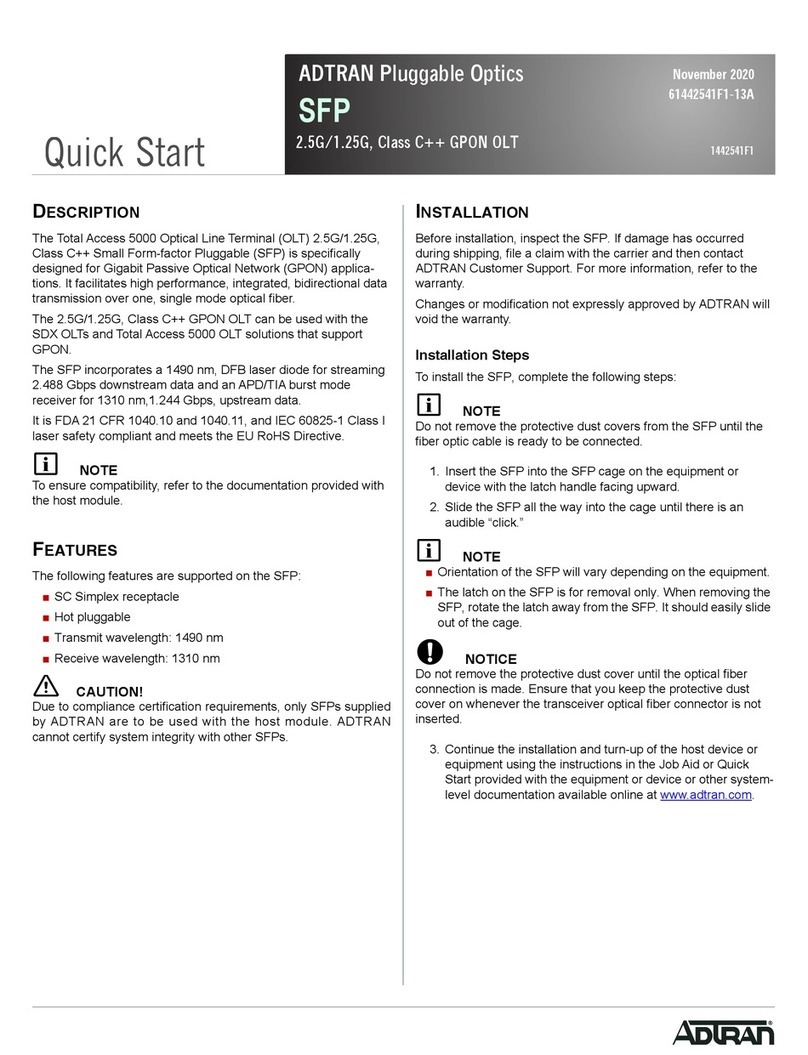
ADTRAN
ADTRAN SFP quick start
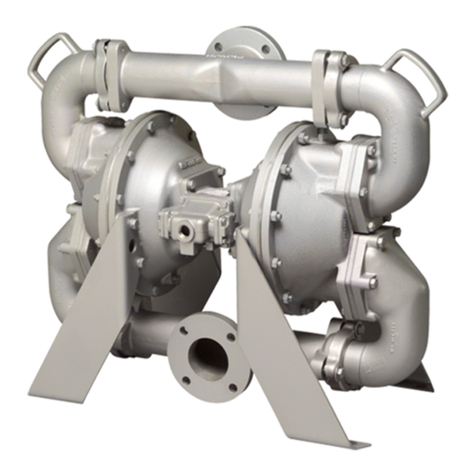
Idex
Idex Warren Rupp Sandpiper HDF3-M Service and operating manual
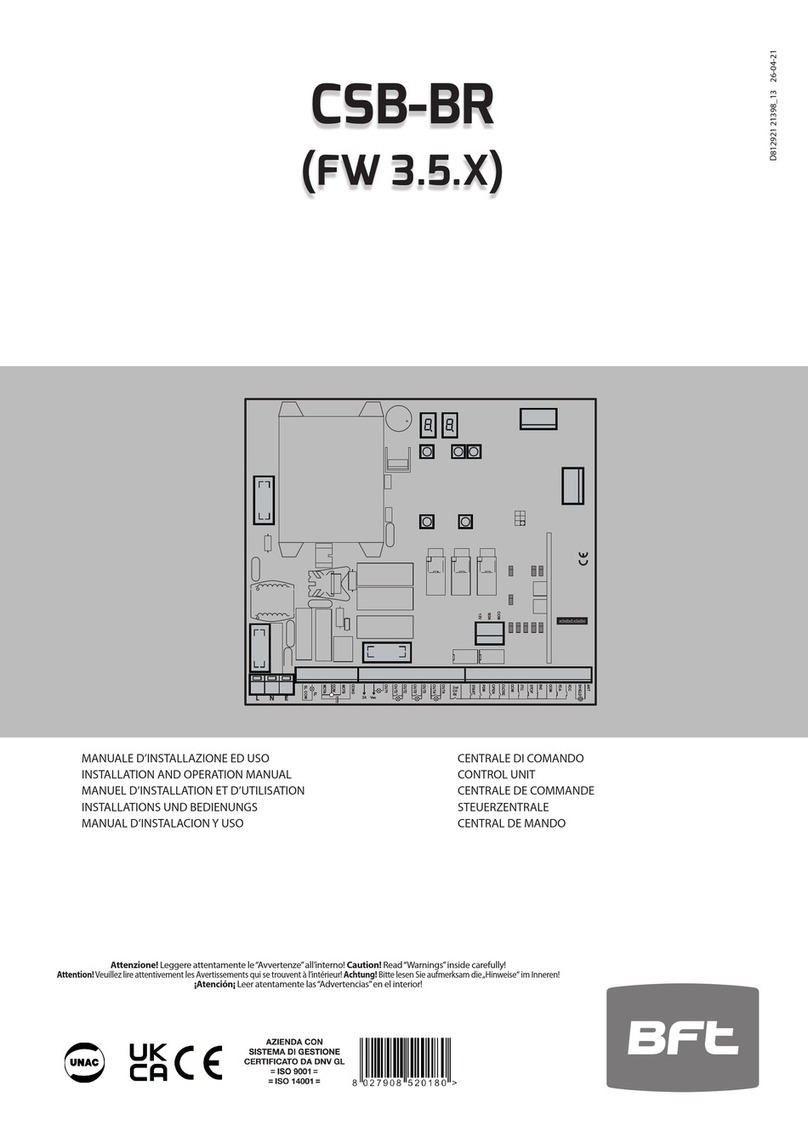
BFT
BFT CSB-BR Installation and operation manual
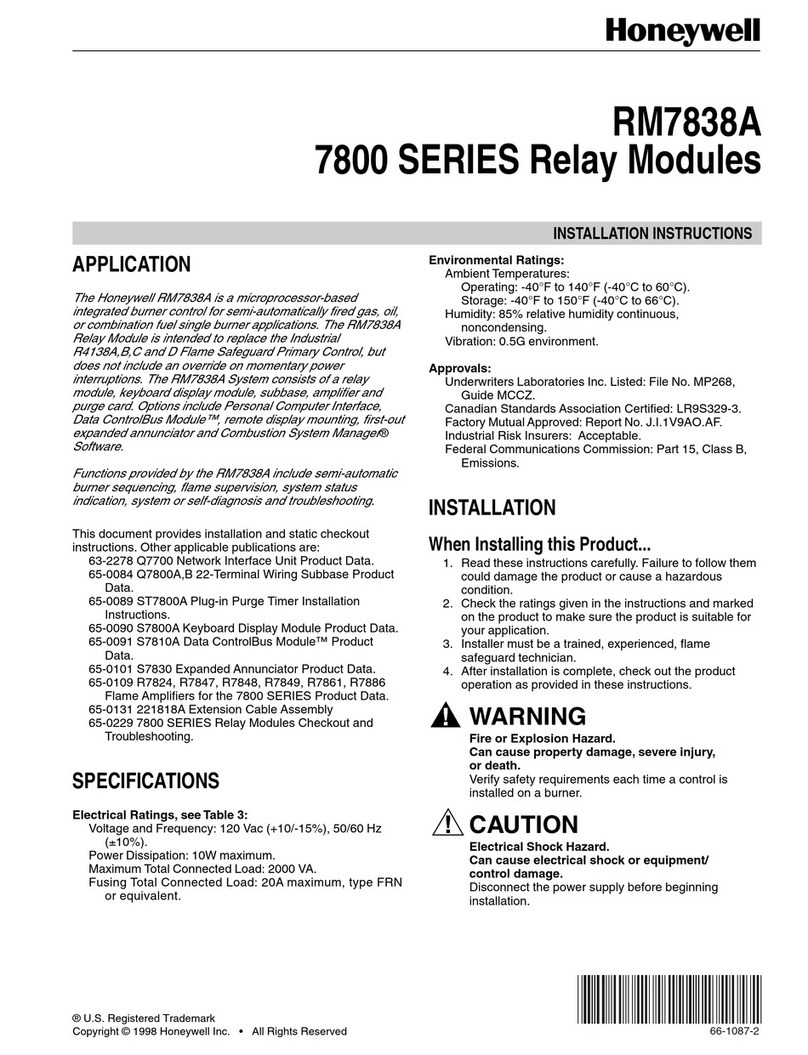
Honeywell
Honeywell 7800 SERIES installation instructions

HYDAC International
HYDAC International FCU 2110-5 Operating and maintenance instructions