INCOE VGC User manual

Instruction Manual
VGCTM
ISequential Valve Gate Control

VGCTM SEQUENTIAL VALVE GATE CONTROL
INSTRUCTION MANUAL
©INCOE® CORPORATION 2/2009 Pg.
www.incoe.com
TABLE OF CONTENTS
1
1 INTRODUCTION
1.1 Programming Pg. 2
1.2 Control Pg. 2
1.3 Signals Coming from the Injection Molding Machine Pg. 2
1.4 Connecting Signals Coming from the Press Pg. 2
1.5 Security Pg. 4
1.6 Connections for VGC Sequential Valve Gate Control Cabinet Pg. 5
1.7 Dimensions in. (mm) Pg. 5
1.8 Fuses and Circuit Breakers Pg. 5
1.9 Applicable Standards Pg. 5
1.10 Wiring Diagram of VGC Sequential Valve Gate Control Cabinet Pg. 6
1.11 Machine Interface Pg. 7
2 OPERATION
2.0 Starting Up Pg. 8
2.1 Calibration Pg. 8
2.2 Configuration of the System Pg. 9
2.2.1 Duration of the Closing Signal at the End of the Injection Cycle Pg. 9
2.2.2 Delay Before Position Control Pg. 9
2.2.3 Prolonging of Injection Signal Pg. 9-10
2.2.4 Selection of Unit for Screw Travel Pg. 10
1. Unit in % Pg. 10
2. Unit in mm Pg. 10
3. Unit in cm3Pg. 10
2.3 Manual Mode Pg. 11
2.4 Modify a Program Pg. 12
2.5 File Management Pg. 14
2.6 Management of Alarms: Pg. 15
Select and Validate the Function ALARM from the Main Page.
2.7 Main System Parameters Values Pg. 16
2.8 System Locking Pg. 16
2.9 Option Position Control of Pins Pg. 16
2.10 List of Main Spare Parts Pg. 18
3 TROUBLESHOOTING
3.1 Troubleshooting Pg. 19
4 WARRANTY
4.1 General Terms & Conditions of Sale Pg. 24
5 CONTACT
5.1 Global Service Contacts Pg. 26
5.2 Global Offices Pg. 27

VGCTM SEQUENTIAL VALVE GATE CONTROL
INSTRUCTION MANUAL
©INCOE® CORPORATION 2/2009
Pg. www.incoe.com
INTRODUCTION
2
2
1
1.0 DESCRIPTION OF THE CABINET
These cabinets are designed for the controlling of
4-8- or 12 valve gates.
1.1 PROGRAMMING
Programming a sequence is accomplished with
the integrated multi-lingual user interface. This
applies to both types of VGC cabinets (keyboard
an blue backlit LCD display), offering the following
features:
• Programming the actuation of the valve gates.
• Loading / Saving 8 sequence les.
• Manual actuation of the valve gates.
• Display cycle time.
• Display value of screw position.
Optional Limit Switches: It is possible to use
position sensors and display the valve gate pin
positions.
1.2 CONTROL
Actuation of 1 or 2 valve gates opening and closing
per cycle:
Each movement can be triggered using one of the
following signals :
• Timer function from injection start or hold start.
• Screw position in %, cm3or in mm.
1.3 SIGNALS COMING FROM THE
INJECTION MOLDING MACHINE
Injection Start Signal is required.
The others signals recomended listed below are
optional
• Injection Hold signal.
• Screw position signal.
Important Notice : It is required to connect at least
the injection start signal to program a sequence
based on time.
For connecting these signals, please refer to the
wiring diagram on Page 3.

VGCTM SEQUENTIAL VALVE GATE CONTROL
INSTRUCTION MANUAL
©INCOE® CORPORATION 2/2009 Pg.
www.incoe.com
1
3
INTRODUCTION
1.4 CONNECTING SIGNALS COMING FROM THE PRESS

VGCTM SEQUENTIAL VALVE GATE CONTROL
INSTRUCTION MANUAL
©INCOE® CORPORATION 2/2009
Pg. www.incoe.com
INTRODUCTION
1. 5 SECURITY
a) Alarm output on open contact, activated in case of:
• Fault on hydraulic power pack (not used if no
external power pack).
• Fault on injection safety : at least one valve gate
must be programmed to the open position at
injection start.and during the hole injection
cycle.
• Fault on control card.
• Fault on valve gate pin position during the
injection cycle time (optional).
b) Input “from hydraulic power pack in “via
isolated dry set of contact:
• Indicates to controller that hydraulic pressure is
available for the valve gates.
• If the hydraulic power pack is not functioning the
controller will not allow the cycle to run.
c) Alarm input on isolated dry set of contact:
• Indicates to the controller that the injection molding
machine is currently under alarm.
• If this alarm is active the controller will not allow
the cycle to run.
4
1

VGCTM SEQUENTIAL VALVE GATE CONTROL
INSTRUCTION MANUAL
©INCOE® CORPORATION 2/2009 Pg.
www.incoe.com
1
5
1.6 CONNECTIONS FOR VGC SEQUENTIAL
VALVE GATE CONTROL CABINET
A: Connector for input signals (16 pins 10A female).
B: Connector for alarm inputs and outputs, as well
as for security on hydraulic power pack (10 pins
10A female).
C: Connector for commands to valve gates,
voltage 24V DC, 1.5 Amps per valve gate
(32 pins 10A female).
D: Option : Connector for limit switches on valve
gates (32 pins 10A male).
E: Power supply cable inlet 3G2,5mm2 (Supply
voltage 230V AC 50/60Hz).
F: Fuse holder with fuse 16A on cabinet.
G: Circuit breaker 16A (switching cabinet on / off).
IMPORTANT NOTICE:
When connecting the signals from the press to
connector A on cabinet, it is recommended to split
0-10V signals and 0-24V signals. Use a cable with
shielded pairs, connect screw position with the
first pair and hold signal, injection signal and 0-24V
supply with the other pairs.
1.7 DIMENSIONS IN. (MM)
• Cabinet VGC Seq Valve Gate Control for 12
valve gates :
17” (431mm) L x H 8.5” (216mm) H x 18.5”
(470mm) D
1.8 FUSES AND CIRCUIT BREAKERS
• Fuse 16A type gI for cabinet (size 10x38 mm).
• Circuit breaker 16A.
• Fuses 6.3A on each control card (size 5x20 mm).
1.9 APPLICABLE STANDARDS
Cabinet VGC Sequential Valve Gate Control is
approved for the Specification CE 73/23 “Low
voltage” and fullfill the EN 61010-1 standards.
They also comply with the following standards:
Electrical noise industriel environnent : EN 50081-2
Electrical Noise Immunity in industrial
environment: EN50082-2
INTRODUCTION
There MUST be a plug on connector B. Use either a dummy plug,
or a plug that is using the features intended for Connector B.

VGCTM SEQUENTIAL VALVE GATE CONTROL
INSTRUCTION MANUAL
©INCOE® CORPORATION 2/2009
Pg. www.incoe.com
1
1.10 WIRING DIAGRAM OF VGC SEQUENTIAL VALVE GATE CONTROL CABINET
INTRODUCTION
6

VGCTM SEQUENTIAL VALVE GATE CONTROL
INSTRUCTION MANUAL
©INCOE® CORPORATION 2/2009 Pg.
www.incoe.com
1.11 MAN – MACHINE INTERFACE
OPERATION 1
LCD screen Validate key Direction arrows
Key to validate.
Escape key
Key to erase partially or completely an input.
Alpha-numerical keyboard for inputs.
Display of commands to valve gates :
Command open : green LED on the left is lit.
Command close : red LED on the right is lit.
OPTION :
Display of position control of limit switches :
Control open : green LED on the left is lit.
Control close : red LED on the right is lit.
LED for communication control card - CPU
7

VGCTM SEQUENTIAL VALVE GATE CONTROL
INSTRUCTION MANUAL
©INCOE® CORPORATION 2/2009
Pg. www.incoe.com
2.0 STARTING UP
Plant power 230V AC 50/60 Hz Single Phases cable
supplied.
Make sure that all connections to the backside
of the cabinet are correct (command signal,
alarms….). Switch the cabinet on with the 16A
circuit breaker.
The following pages appear after 5 seconds :
Important Notice: When the cabinet VGC Seq Valve
Gate Control is not in service, the A connector on
the backside of the cabinet must be disconnected
in order not to interfere with the signals from the
injection machine.
2.1 CALIBRATION
For proper use of the controller with the injection
molding machine, it is required to calibrate the
screw travel first.
To access the calibration page, simply select the
SYST function on white background, validate and
then select the SCRCAL function.
Select SCRCAL to calibrate the screw travel.
The following page is displayed.
Validate the function CALIBR to enter the calibration
process from this page and enter the calibration
values one after the other by moving the screw on
the injection machine.From this point, the process
must be brought to the end.
Guiding messages for the operator
Notice: The machine number is important information
to enter and to confirm which machine the calibration
process has been done on the controller.
Please note that if this controller is moved to another
machine, it must be recalibrated if you wish to use
the screw position signal for programming.
All words preceded by “MES.“ are values read
from the injection machine.
All words preceded by “VAL. “ are inputs made by
the operator.
OPERATION
2
8

VGCTM SEQUENTIAL VALVE GATE CONTROL
INSTRUCTION MANUAL
©INCOE® CORPORATION 2/2009 Pg.
www.incoe.com
2.2 CONFIGURATION OF THE SYSTEM
The system configuration pages are to set up control
parameters (date, time, language, etc.) as well as
to set up injection related parameters such as closing
duration after injection signal, prolonging of the
injection signal, etc.
To access the configuration page, select the SYST
function shown on white background.
Press the Validate key.
The following is displayed: these are the machine
parameters.
Default Factory Settings
Command for closing is held to all valve gates
after the injection signal has dropped
This is the time between the command and the
moment position control of the pin is made
(valid if option is purchased)
Prolonging the duration of the injection signal
2.2.1 DURATION OF THE CLOSING
SIGNAL AT THE END OF THE INJECTION
CYCLE
This is the time the closing command is sent to all
valve gates when the control cabinet is switched
on or when the injection signal drops. The default
value is set at 1 second. Set 0 to disable this function.
2.2.2 DELAY BEFORE POSITION CONTROL
(OPTIONAL)
This is to set a response time between the
electrical command sent to the solenoid valve and
the confirmation of the pin position by the limit
switch.
2.2.3 PROLONGING OF INJECTION SIGNAL
This function extends the injection signal by a
certain time (t1) in order to command the valve
gates for a longer period of time. When set at
0, and as soon as the injection signal drops, a
command for closing is sent to all valve gates.
Using this function can delay the command
for closing by a certain time when the injection
signal drops. The delay is adjustable in 1/100 sec
(see graph 3.1). Valve gate commands can be
programmed during this time.
OPERATION 2
Graph 3.1
9

VGCTM SEQUENTIAL VALVE GATE CONTROL
INSTRUCTION MANUAL
©INCOE® CORPORATION 2/2009
Pg. www.incoe.com
Press NEXT for accessing further system parameters
to select the unit for screw position, date, time,
language, etc….
Display and set system date and time
Select language
Modify keyboard password
Selection of Unit for Screw travel
OPERATION
2
10
Select MODIF to modify one of these 5 parameters
and validate. Possible choices are displayed above
the arrows as far as the language and the unit for
screw position. Enter the required value with the
keyboard for time, date and password.
1. Unit in (%):
This unit is related to the injected volume of
material. 0% is set at injection start and 100%
is reached when the screw is empty. This unit is
directly linked to the injection shot size of the
machine. If a sequence programmed on a machine
with an injection unit A is loaded on the controller
used on a machine with a different injection unit
B, the new shot size must be set so that the values
programmed in % remain valid.
2. Unit in (mm):
Values programmed using this unit depend on
the screw position not on the volume of injected
material. This unit does not rely on the shot size
but on the calibration of the screw position
signal received by the controller. A programmed
sequence using this unit relates to the machine
and any file using this unit should be modified to
be used on a different machine.
3. Unit in (cm3):
This unit depends on the calibration of the screw
position and on the injected volume of material. It
is independent from the shot size. A programmed
sequence using this unit can be used on a
different machine if the controller has been re-
calibrated for the new machine.
Advantages and disadvantages are on the
compatibility of saved sequence files loaded on
different injection units:
• Programs in % Re-calibration is not
required.
• Programs in mm: Re-calibration is required.
New calculation of
command values.
• Programs in cm3Re-calibration is required.
CAUTION: The programmed sequence is lost if the
unit for screw position is changed.
CAUTION: Check the programmed sequence after
changing the unit.
2.2.4 SELECTION OF UNIT MEASURE FOR SCREW TRAVEL
2.2.3 PROLONGING OF INJECTION SIGNAL (CONT’D)

VGCTM SEQUENTIAL VALVE GATE CONTROL
INSTRUCTION MANUAL
©INCOE® CORPORATION 2/2009 Pg.
www.incoe.com
2.3 MANUAL MODE
The manual mode is to open or close the valve
gates manually in order to make sure that everything
is functioning before production.
Select and validate the MANU function from the
main page. The page below is displayed.
Selection frame
Valve gate output is disabled (OFF)
OPERATION 2
* The shadowed icon means that the valve gate
output is disabled (not used).
* This valve gate output receives a command for
closing during the injection cycle.
* The white icon means that the valve gate output
is enabled.
* A valve gate output under alarm is displayed in
this way:
Important notice: Select a valve gate output us-
ing the arrows for moving up and down. Select
a command using the arrows for moving left or
right for opening (OPEN), for closing (CLOSE), or
for stopping the preceding command (STOP), for
selecting a single valve gate output (SELECT) or
all channels (ALL).
OPEN: Permanent command for opening a valve
gate.
CLOSE:Permanent command for closing a valve
gate.
STOP: For stopping previous commands for
opening or closing.
SELECT: To select or unselect a valve gate output.
ALL: To select or unselect all valve gate outputs in
the configuration.
Important Notice: No valve gate can be opened or
closed if the hydraulic power pack is switched off
and/or if the alarm contact is validated.
11

VGCTM SEQUENTIAL VALVE GATE CONTROL
INSTRUCTION MANUAL
©INCOE® CORPORATION 2/2009
Pg. www.incoe.com
OPERATION
2
Valve gate number to be
programmed
Opening and closing No1
for selected valve gate
Opening and closing No2
for selected valve gate
Switch on/off valve gate
Triggering signal for opening
Triggering signal for closing
Value for valve gate actuation
(in the unit corresponding to
the selected command mode)
Cursor
12
2.4.1 MODIFY A PROGRAM
This mode is to program the movements required
for each valve gate during the injection cycle
(injection signal, screw position, etc.)
Select and validate PROG for accessing the page
for programming from the main menu :
The page below is displayed:
To program another valve gate, enter the required
valve gate number on the alpha-numerical keyboard
and validate.
To switch a valve gate on or off, move the cursor
accordingly to ON or OFF.
Then validate the function MODIF to select from
ON or OFF with the arrows.
Then validate again to move to the next field.
Example of a program:
Validate MODIF when it appears to select another
signal. Then select the required signal with the
arrows by moving left or right.
Move the cursor on the field to modify values for
triggering moments and enter the required value
on the alpha-numerical keyboard and validate.
One can select among 3 triggering signals for
programming.
The values for programming are:
1) Injection start: the value to enter is the delay
between the injection start signal and the required
triggering moment.
2) Hold start: the value to enter is the delay between
the hold start signal and the required triggering
moment.
3) Screw position: The value to enter depends on
the selected unit:

VGCTM SEQUENTIAL VALVE GATE CONTROL
INSTRUCTION MANUAL
©INCOE® CORPORATION 2/2009 Pg.
www.incoe.com
• Unit in %: The value is the percentage of injected
volume of material before actuating the valve gate.
• Unit in mm: The value to enter is the stroke of
the injection screw before actuating the valve gate
(and not the position of the injection screw).
• Unit in cm3: The value to enter is the injected
volume of material before actuating the valve gate.
OPERATION 2
Important Notice: Select NONE with the left and
right arrows to erase a signal. This action will
automatcally erase the selected step and the
following if relevant.
Please note that the sequence programmed for
a channel is carried out until the injection signal
drops. Therefore, it is recommended to erase all
lines that are not required.
13

VGCTM SEQUENTIAL VALVE GATE CONTROL
INSTRUCTION MANUAL
©INCOE® CORPORATION 2/2009
Pg. www.incoe.com
2.5 FILE MANAGEMENT
Select and validate the FILE function from
the main page.
The page below is displayed :
OPERATION
2
The arrow shows the file selected in
the list
File on a white background: the
current sequence originates
from this file
Various info about the selected file
This page is for the management of sequence files.
Some information like date and time of creation
and comments can be saved as well.
The name of the
current file is
displayed in all
pages
This floppy icon is shown when the current sequence
has been modified but has not been saved as a file.
NEW: to create a new sequence file.
SAVE: to save or modify the selected file.
The current program is saved as the selected file.
LOAD: to load the sequence saved in the
selected file.
DELETE: to cancel the selected file.
Important Notice:
• The le name on a white background is the
current sequence file and is always displayed
in the top right section of all pages in the
program.
• Maximum 8 les can be saved in this menu
FILE. You must delete unused files for saving
a new file.
14

VGCTM SEQUENTIAL VALVE GATE CONTROL
INSTRUCTION MANUAL
©INCOE® CORPORATION 2/2009 Pg.
www.incoe.com
OPERATION
2.6 MANAGEMENT OF ALARMS
Select and validate the function ALARM from the
main page.
The page hereunder is displayed :
Alarm hydraulic power pack : shows the absence
of the external power pack or of the shunt between
pins 1 and 6 inside the B connector on the backside
of the controller
Alarm external system : alarm contact coming
from whatever device around the sequential
control cabinet.
Faulty control card : shows that a control card for
actuating outputs is faulty.
Fault position control open (valid if option position
control is present) : shows that the limit switch did
not confirm the actual pin on opening.
Fault position control close (valid if option po-
sition control is present) : shows that the limit
switch did not confirm the actual pin on closing.
No opening command : shows that no valve gate
was programmed to open in the injection cycle. If
so the injection cycle is stopped.
Program not valid : shows an error in program-
ming (not corresponding to screw calibration for
instance, etc…).
This page shows the current alarms.
RESET : to reset both alarm contacts for injection
safety.
Press ESC to go back to main page.
Various types
of alarms
The LED shows that the
corresponding alarm is
active
2
15

VGCTM SEQUENTIAL VALVE GATE CONTROL
INSTRUCTION MANUAL
©INCOE® CORPORATION 2/2009
Pg. www.incoe.com
2.7 MAIN SYSTEM PARAMETERS VALUES
Select and validate the function MSPV from the
main page
The page below is displayed :
The cycle time and the actual screw position in the
selected unit are displayed on this page.
Notice : the percentage shown on this page is
expressed for the total screw stroke and 0% means
an empty screw.
The status of input signals (injection start, hold
start, hydraulic power pack and alarm input) a are
displayed above.
Press ESC to go back to main page.
2.8 SYSTEM LOCKING
Select and validate the function CODE from the
main page.
The page below is displayed :
It is possible to lock or unlock the system from
this page by entering a password with the alpha-
numerical keyboard.
A message confirming the current status is
displayed in the top left section of the page once
the password has been entered.
The default password factory set is 123456.
Use the function SYST and validate with NEXT
to modify the password in page 2 of system
parameters.
Then select the line “MODIF PASSWORD” and
validate when MODIF is on a white background.
The page below is displayed.
2OPERATION
16

VGCTM SEQUENTIAL VALVE GATE CONTROL
INSTRUCTION MANUAL
©INCOE® CORPORATION 2/2009 Pg.
www.incoe.com
2.9 OPTION POSITION CONTROL OF PINS
The option position control can be fitted on VGC
Sequential Valve Gate Control cabinet to show
the actual pin position of each valve gate (open or
closed).
An extra function called CONFIG is shown if the
option is used. This function enables the position
control of the pins.
Select and validate CONFIG on a white background
from the main page shown below.
Press validate.
The page below is displayed:
This arrow confirms the pin is controlled
on opening
This arrow confirms the pin is controlled on closing
Important Notice: Use up an down arrows like in
manual mode to select a valve gate output. Left and
right arrows enable control ON / OFF, on opening
(CTLOPN), on closing (CTLCLO), select a single
valve gate (SELECT) or select all valve gate(ALL).
ON/OFF: To switch on or off the
corresponding valve gate.
CTLOPN: To enable or disable position control
on opening. Control open
CTLFER: To enable or disable position control
on closing. Control closing
SELECT: To select or unselect a valve gate
output.
ALL: To select or unselect all valve gate
outputs in the CONFIG page.
OPERATION 2
Follow the procedure as explained.
Enter old password.
Enter new password.
Confirm new password.
Important Notice: Please use the contact
information if the password has been forgotten. A
new procedure will be provided to go back to the
factory setting.
17

VGCTM SEQUENTIAL VALVE GATE CONTROL
INSTRUCTION MANUAL
©INCOE® CORPORATION 2/2009
Pg. www.incoe.com
2.10 LIST OF RECOMMENDED SPARE PARTS
Item Description – Part number Quantity
3042 Control card VGC Sequential Valve Gate Control 1
6438 Supply 230V/12-5V – MEAN WELL PD-45A 1
6271 Screen LCD 128x64 – LWM12864D-EW-WCB 1
5455 Fuse type GI 16A - 10x38 mm 1
6272 Supply 230V/24V – 12,5A – SP320-24 1
18
OPERATION
2

VGCTM SEQUENTIAL VALVE GATE CONTROL
INSTRUCTION MANUAL
©INCOE® CORPORATION 2/2009 Pg.
www.incoe.com
3.1 TROUBLESHOOTING
IMPORTANT NOTICE
• Any repair on the controller should be carried out by qualied personal.
• Any component being replaced must have the same specication.
TROUBLESHOOTING 3
Failure
• No hydraulic pres-
sure
• No command to
valve gate(s)
• Cycle does not
start
• No command to
valve gates/
cycle does not start
Display
“Alarm hydraulic
pressure”
(Displayed in alarm page).
“Failure control card” (dis-
played in alarm page) and
no blinking yellow LED for
communication on control
card.
No action and the cause
are displayed in the alarm
page.
The blinking yellow
communication
lights are
functioning.
Causes
• No hydraulic
pressure connected.
• Control card not
connected or out of
order.
• The press does not
deliver the analog
signal required.
• The wiring of
signals from the
press is not correct.
• Other alarms pre-
vent cycle start
(eg. : no hydraulic
pressure...)
• The programmed
sequence is not
correct.
• Do have a 24v
injection start signal
Solutions
• Check connection and
if the signal “Hydraulic
on” is properly wired to
cabinet (plug B).
• Check supply to con-
trol card and the link
to motherboard. Test
outputs on control card.
• Replace control card.
• Check input signals
from the press.
• Check if this wiring is
correct.
• Check if no other
alarms on alarm page.
• In the sequence, at
least one gate must be
open when injection
starts.
• Make sure the dummy
plug is installed in
connector “B” on the
back of the VGC unit.
19
Table of contents
Popular Controllers manuals by other brands
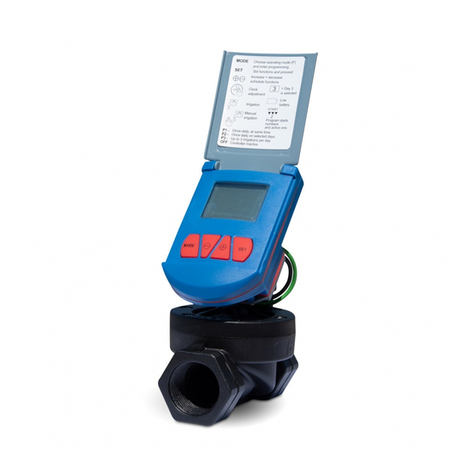
Baccara
Baccara G75 user guide

nekos
nekos SKY 650 instruction manual
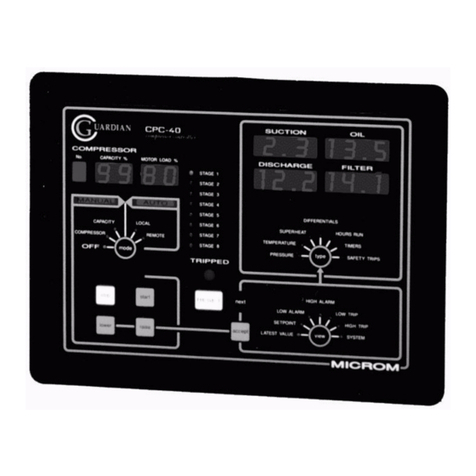
Guardian Controls International
Guardian Controls International RCC-50 OPERATION AND SETUP MANUAL
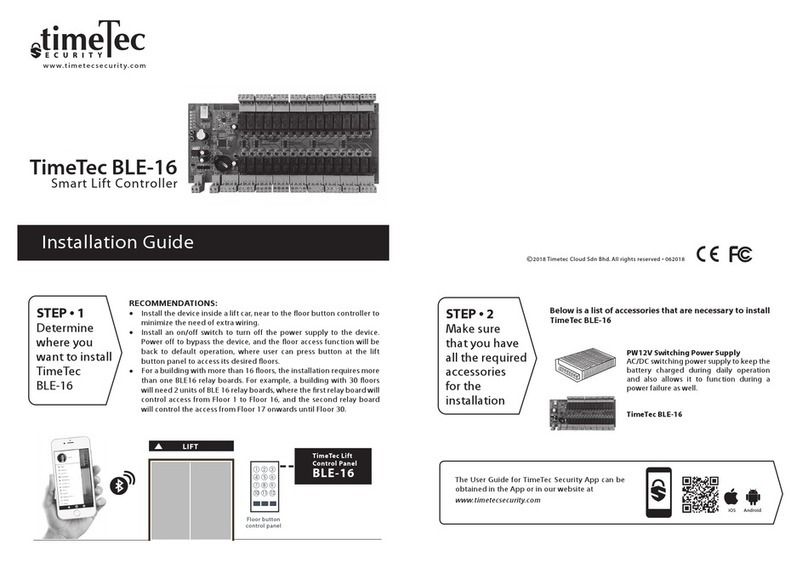
TimeTec Security
TimeTec Security BLE-16 installation guide
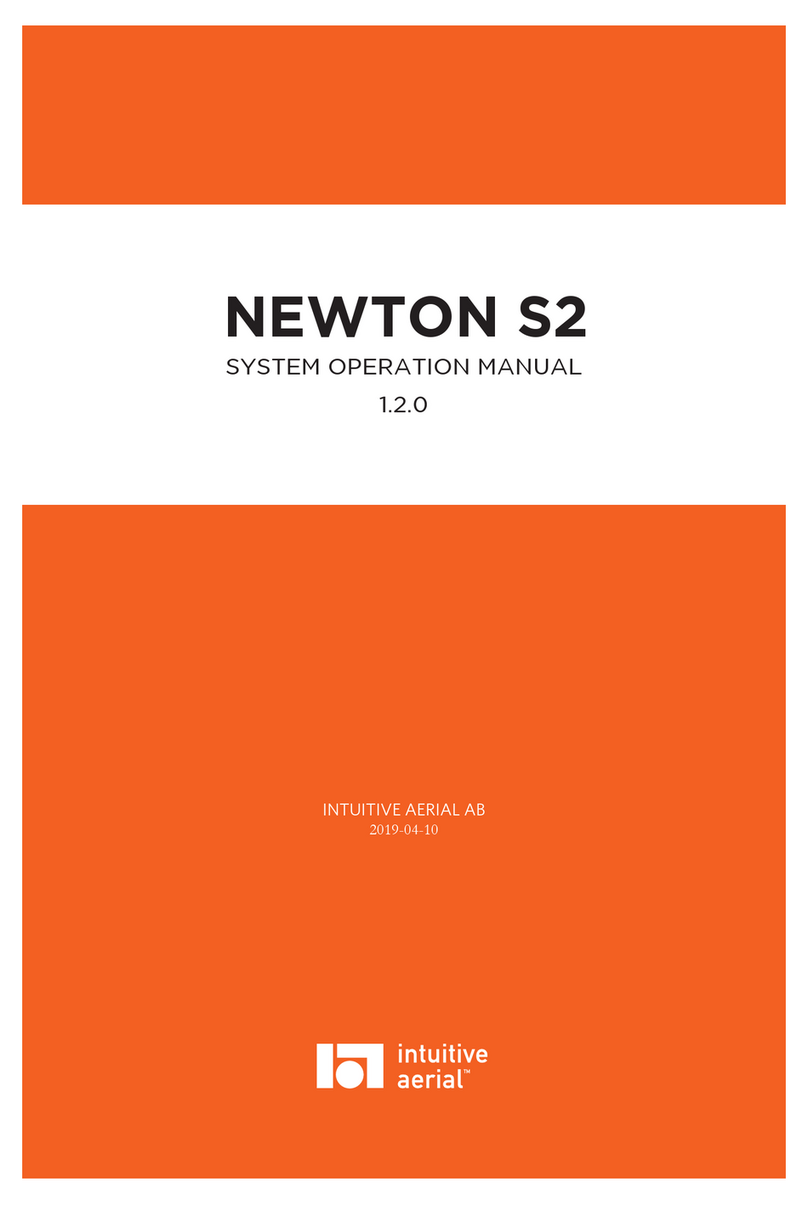
Intuitive Aerial
Intuitive Aerial Newton S2 3G System operation manual
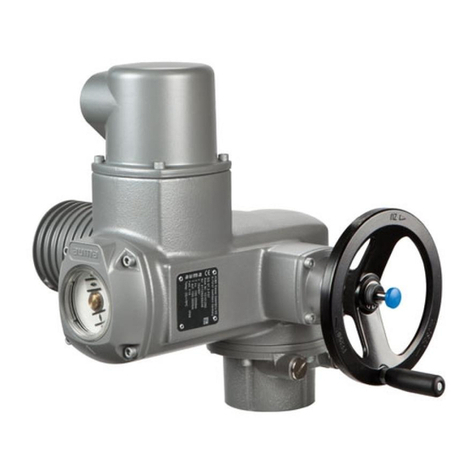
AUMA
AUMA SG 05.1-F05 operating instructions