Intelligent Motion Systems MDrive42AC Plus Microstepping Operation manual

42T
M
MICROSTEPPING
www.imshome.com
TM
Excellence in Motion
Patent Pending
a sealed MDrive42AC Plus Microstepping
unit with circular connectors meets IP65
specifications.**
The versatile MDrive42AC Plus Micro-
stepping is available in multiple configu-
rations to fit various system needs. Two
rotary motor lengths are available and
may include an internal optical encoder, a
control knob for manual positioning or an
integrated planetary gearbox.
Interface connections are accomplished
using standard industrial circular connec-
tors. And connectivity has never been
easier with options ranging from all-in-
clusive QuickStart Kits to individual
interfacing cables. See pg 5.
The MDrive42AC Plus is a compact, pow-
erful and cost effective solution that will
reduce system cost, design and assembly
time for a large range of brushless step
motor applications.
CONFIGURING
The IMS Motor Interface software is an
easy to install and use GUI for configuring
the MDrive42AC Plus from a computer's
USB port. GUI access is via the IMS SPI
Motor Interface available at
www.imshome.com.
The IMS SPI Motor Interface features:
• Easy installation.
• Automatic detection of MDrive version
and communication configuration.
• Will not set out-of-range values.
• Tool-tips display valid range
setting for each option.
• Simple screen interfaces.
DESCRIPTION
The MDrive42AC Plus Microstepping
high torque integrated motor and step and
direction driver is ideal for designers who
want the simplicity of a motor with on-
board electronics. The integrated electron-
ics of the MDrive42AC Plus eliminate the
need to run motor cabling through the ma-
chine, reducing the potential for problems
due to electrical noise.
The unsurpassed smoothness and per-
formance delivered by the MDrive42AC
Plus Microstepping are achieved through
IMS's advanced 2nd generation current
control. By applying innovative techniques
to control current flow through the motor,
resonance is significantly dampened over
the entire speed range and audible noise
is reduced.
The MDrive42AC Plus accepts a broad
input voltage range from 95 to 264 VAC,
delivering enhanced performance and
speed. Oversized input capacitors are
used to minimize power line surges, re-
ducing problems that can occur with long
runs and multiple drive systems. An ex-
tended operating range of –40° to +75°C
provides long life, trouble free service in
demanding environments.
The MDrive42AC Plus uses a NEMA 42
frame size high torque brushless step mo-
tor combined with a microstepping driver,
and accepts up to 20 resolution settings
from full to 256 microsteps per full step, in-
cluding: degrees, metric and arc minutes.
These settings may be changed on-the-fly
or downloaded and stored in nonvolatile
memory with the use of a simple GUI
which is provided. This eliminates the
need for external switches or resistors.
Parameters are changed via an SPI port.
For use in environments where exposure
to chemical, dust and liquids may occur,
FEATURES
• Highly Integrated Microstepping Driver
and NEMA 42 High Torque 1.8°
Brushless Step Motor
• Advanced 2nd Generation Current
Control for Exceptional Performance
and Smoothness
• Single Supply: 120 or 240 VAC
• Cost Effective
• Extremely Compact
• High Positioning Accuracy
• No Tuning Required
• Stable at Low Speeds
• No Dithering at Zero Speed
• High Starting Torque
• Allows for Greater Inertia Mismatch
• Built-in Regeneration Circuitry
• 20 Microstep Resolutions up to
51,200 Steps Per Rev Including:
Degrees, Metric, Arc Minutes
• Optically Isolated Logic Inputs will
Accept +5 to +24 VDC Signals,
Sourcing or Sinking
• Automatic Current Reduction
• Configurable:
- Motor Run/Hold Current
- Motor Direction vs. Direction Input
- Microstep Resolution
- Clock Type: Step and Direction,
Quadrature, Step Up and Step Down
- Programmable Digital Filtering for
Clock and Direction Inputs
• Available Options:
- Internal Differential Optical Encoder
- Integrated Planetary Gearbox
- Control Knob for Manual Positioning
- IP65 Sealed Configuration**
• 2 Rotary Motor Lengths Available
• Setup Parameters May Be Switched
On-The-Fly
• Standard Industrial Connectors:
- Circular 19-Pin M23
- Circular 3-Pin Euro AC
• Graphical User Interface (GUI) for Quick
and Easy Parameter Setup
**Consult Factory for Availability.
new

2 MDrive42AC Plus Microstepping REV060208
MDrive
42AC Plus
MICROSTEPPING
Holding Torque Detent Torque Rotor Inertia Weight (Motor+Driver)
SINGLE LENGTH 1147 oz-in / 810 N-cm 35 oz-in / 25 N-cm 0.0917
oz-in-sec
2
/ 6.5
kg-cm
2
14.07 lb / 6.38 kg
DOUBLE LENGTH 2294 oz-in / 1620 N-cm 84 oz-in / 59 N-cm 0.1833
oz-in-sec
2
/ 13.0
kg-cm
2
21.25 lb / 9.64 kg
MOTOR SPECIFICATIONS
INPUT VOLTAGE Range 120 V MDrive – 95 to 132 VAC @ 50/60 Hz
240 V MDrive – 95 to 264 VAC @ 50/60 Hz
ISOLATED INPUT
Step Clock, Direction and Enable
Voltage Range +5 to +24 VDC Sourcing or Sinking
MOTION
Digital Filter Range 50 nS to 12.9 µS (10 MHz to 38.8 kHz)
Clock Types Step/Direction, Quadrature, Step Up/Step Down
Step Frequency (Max) 2 MHz
Resolution
Number of Settings 20
Steps Per Revolution
200,
400, 800, 1000, 1600, 2000, 3200, 5000,
6400, 10000, 12800, 20000, 25000, 25600,
40000, 50000, 51200, 36000 (0.01 deg/µstep),
21600 (1 arc minute/µstep), 25400 (0.001mm/µstep)
TEMP OUTPUT WARNING Open-Drain Type +5 to +24 VDC 50 mA Current
THERMAL Operating Temperature
Heat Sink –40° to +75°C (non-condensing)
Motor –40° to +90°C (non-condensing)
PROTECTION Type Thermal, Internal Fuse†
STANDARD SPECIFICATIONS
SETUP PARAMETERS
Function Range Units Default
MHC Motor Hold Current 0 to 100 percent 5
MRC Motor Run Current 1 to 100 percent 25
MSEL Microstep Resolution
1, 2, 4, 5, 8, 10, 16, 25, 32, 50,
64, 100, 108, 125, 127, 128,
180, 200, 250, 256
µsteps per full step 256
DIR Motor Direction Override 0/1 — CW
HCDT Hold Current Delay Time 0 or 2–65535 mSec 500
CLK TYPE Clock Type Step/Dir, Quadrature, Up/Down — Step/Dir
CLK IOF Clock and Direction Filter 50 nS to 12.9 µS
(10 MHz to 38.8 kHz) nS (MHz) 200 nS (2.5 MHz)
USER ID User ID Customizable 1–3 characters IMS
EN ACT Enable Active High/Low — High
WARN TEMP Over Temperature Warning 0 to 125°C °C 80°C
All parameters are set using the supplied IMS SPI Motor Interface GUI and may be changed on-the-fly.
An optional Communication Converter is recommended with first orders.
ENCODER SPECIFICATIONS
Note: All encoders come with an index mark, except the 400 line count.
INTERNAL DIFFERENTIAL
OPTICAL ENCODER
Pin Assignments
19-Pin M23 Connector Function
Pin 3 Index +
Pin 4 Channel B +
Pin 5 Channel B –
Pin 7 Channel A +
Pin 14 Index –
Pin 15 Channel A –
Line Count Part Number
100 EA
200 EB
400 ED
500 EH
512 EX
1000 EJ
1024 EY
†Designed for line-neutral systems.

MDrive42AC Plus Microstepping REV060208 3
P3: POWER CONNECTOR
Euro AC (Male) Function
Pin 1 Chassis Ground
Pin 2 AC Power Line
Pin 3 AC Power Neutral
P1: I/O & COMM (SPI) CONNECTOR
M23 Circular (Male) Function Function with Encoder
Pin 1
Optocoupler Reference Optocoupler Reference
Pin 2
Enable Input Enable Input
Pin 3
No Connect Index +
Pin 4
No Connect Channel B +
Pin 5
No Connect Channel B –
Pin 6
No Connect No Connect
Pin 7
No Connect Channel A +
Pin 8
SPI Master Out – Slave In SPI Master Out – Slave In
Pin 9
SPI Chip Select SPI Chip Select
Pin 10
+5 VDC Output +5 VDC Output
Pin 11
Communications Ground Communications Ground
Pin 12
Shell Connect Shell Connect
Pin 13
CW/CCW Direction Input CW/CCW Direction Input
Pin 14
No Connect Index –
Pin 15
No Connect Channel A –
Pin 16
SPI Clock SPI Clock
Pin 17
SPI Master In – Slave Out SPI Master In – Slave Out
Pin 18
Step Clock Input Step Clock Input
Pin 19
Temp Output Warning Temp Output Warning
LMAX2 Option
Ø 1.90
(Ø 48.3)
Ø 0.87
(Ø 22.1)
Connectors
P1: 19-Pin M23
(Male)
P3: 3-Pin Euro AC
(Male)
Ø 0.87
(Ø 22.1)
MDrive Lengths Inches (mm)
Control Knob
P3
0.65
(16.51)
Ø 0.75
(Ø 19.05)
Ø 2.185
(Ø 55.5)
P1
0.83
(21.08) 4.50
(114.3)
0.1875
(4.76)
6.75
(171.45)
7.4
(187.96)
0.335
(8.51)
3.0
(76.2)
4.331 SQ.
(110.0 SQ.)
3.50 SQ.
(88.88 SQ.)
0.75
(19.05)
0.059
(1.5)
0.49
(12.5)
2.17
(55.0)
1.375
(34.9)
LMAX
LMAX2
600
800
1000
1200
400
200
Torque in Oz-In
Torque in N-cm
424
565
706
847
282
141
Speed – Full Steps/Second (RPM)
0 2000
(600)
4000
(1200)
6000
(1800)
10000
(3000)
8000
(2400)
0
1400
1600
1800
989
1130
1271
Double Motor Length
Single Motor Length
MECHANICAL SPECIFICATIONS
Dimensions in Inches (mm)
MDrive42AC Plus
SPEED-TORQUE
MDrive42AC – 120VAC
MDrive42AC – 240VAC
LMAX LMAX2
Motor
Length
SINGLE SHAFT or
ENCODER VERSION
CONTROL KNOB
VERSION
Single 7.4 (187.96) 9.4 (238.76)
Double 9.4 (238.76) 11.4 (289.56)
600
800
1000
1200
400
200
Torque in Oz-In
T
orque
i
n
N
-cm
424
565
706
847
282
141
Speed in full steps per second (RPM)
0 2000
(600)
4000
(1200)
6000
(1800)
10000
(3000)
8000
(2400)
0
1400
1600
1800
989
1130
1271
Double Motor Length
Single Motor Length
PIN ASSIGNMENTS
Connectivity details:
www.imshome.com/cables_cordsets.html
I/O & Comm Power

Planetary Gearbox for MDrive42Plus
Dimensions in Inches (mm)
Permitted
Output Torque
(oz-in/Nm)
Gearbox
Efficiency
Maximum
Backlash
Output Side with Ball Bearing
Maximum Load
(lb-force/N)
Weight
(lb/kg)
Radial Axial Gearbox w/Flange
PM105
1-STAGE 4956/35.0 0.80 1.0° 135/600 27/120 9.7/4.4 10.0/4.5
2-STAGE 14869/105.0 0.75 1.5° 202/900 40/180 13.2/6.0 13.6/6.2
3-STAGE 27614/195.0 0.70 2.0°
337/1500
67/300
16.8/7.6 17.3/7.8
PM120
1-STAGE 7080/50.0 0.80 0.55° 135/600 27/120 12.3/5.6 12.7/5.8
2-STAGE 21242/150.0 0.75 0.60° 202/900 40/180 17.6/8.0 18.1/8.2
3-STAGE 42484/300.0 0.70 0.65°
337/1500
67/300
22.9/10.4 23.5/10.7
Ratios and Part Numbers
Planetary
Gearbox
Ratio
(Rounded)
Part Number‡
PM105
Model
PM120
Model
1-Stage 3.71:1 ** G1A1 G2A1
1-Stage 5.18:1 G1A2 —
1-Stage 6.75:1** G1A3 G2A3
2-Stage 13.73:1** G1A4 G2A4
2-Stage 15.88:1 G1A5 —
2-Stage 18.37:1 G1A6 —
2-Stage 19.20:1 G1A7 —
2-Stage 22.21:1 G1A8 —
2-Stage 25.01:1** G1A9 G2A9
2-Stage 26.85:1 G1B1 —
2-Stage 28.93:1 G1B2 —
2-Stage 34.98:1 G1B3 —
2-Stage 45.56:1** G1B4 G2B4
3-Stage 50.89:1** G1B5 G2B5
3-Stage 58.86:1 G1B6 —
3-Stage 68.07:1 G1B7 —
3-Stage 71.16:1 G1B8 —
3-Stage 78.72:1 G1B9 —
3-Stage 92.70:1** G1C1 G2C1
3-Stage 95.18:1 G1C2 —
3-Stage 99.51:1 G1C3 —
3-Stage 107.21:1 G1C4 —
3-Stage 115.08:1 G1C5 —
3-Stage 123.98:1 G1C6 —
3-Stage 129.62:1 G1C7 —
3-Stage 139.14:1 G1C8 —
3-Stage 149.90:1 G1C9 —
3-Stage 168.85:1** G1D1 G2D1
3-Stage 181.25:1 G1D2 —
3-Stage 195.27:1 G1D3 —
3-Stage 236.10:1 G1D4 —
3-Stage 307.55:1** G1D5 G2D5
PM105 Model
PM120 Model
**Indicates limited ratios available for PM120 gearbox.
‡ Include optional planetary gearbox by adding –G plus
3 characters to the end of an MDrive part number.
4.20 SQ.
(106.7 SQ.)
3.35 ±0.004 SQ.*
(85.0 ±0.1 SQ.)
k1 ±0.02 (±0.5)
M8 x 0.630 (16.0) Deep*
4x 0.33 (Ø 8.5) Hole
*Gearbox without Flange
†Gearbox with Flange
Ctrg. DIN 332-D M10
Key DIN 6885-A-8x7x40mm
0.20*
(5.0) 0.079
(2.0)
2.33 ±0.02*
(59.1 ±0.5)
2.04 ±0.02
(51.7 ±0.5)
Ø 2.76*
(Ø 70.0)
Ø 0.98
(Ø 25.0)
Ø 4.13
(Ø 105.0)
MDrive42AC Plus
0.35*
(9.0)
†
†
†
Ø 2.187
(Ø 55.54)
†
†
3.50
(
88.9
)
or
or
0.50
(12.7)
†
or
MDrive42AC Plus
*Gearbox without Flange
†Gearbox with Flange
Ø 3.15*
(Ø 80.0)
Ø 2.187
(Ø 55.54)
or
M10 x 0.866 (22.0) Deep*
4x 0.35 (Ø 9.0) Hole†
†
†
†or
or
k1 ±0.02 (±0.5)
Ctrg. DIN 332-D M12
Key DIN 6885-A-10x8x50mm
0.20*
(5.0) †
0.079
(2.0)
†
0.24
(6.2)
0.59*
(15.0)
2.86 ±0.02*
(72.7 ±0.5)
2.53 ±0.02
(64.2 ±0.5)
Ø 1.26
(Ø 32.0)
Ø 4.72
(Ø 120.0)
4.33 SQ.
(110.0 SQ.)
3.94 SQ.*
(
100.0 SQ.
)
3.50 SQ.
(88.9 SQ.)
or
0.59
(15.0)
†
MDRIVE42AC PLUS WITH PLANETARY GEARBOX
The MDrive42AC Plus is available with a Planetary Gearbox option developed to increase torque at lower speeds, enable better
inertia matching and produce finer positional resolutions. These efficient, low maintenance Planetary Gearbox come fully assembled
with the MDrive and are offered in a large number of reduction ratios in 1-, 2- and 3-stage configurations. An optional NEMA Output
Flange allows mounting the Planetary Gearbox to the load using a standard NEMA bolt circle. Planetary Gearbox may be combined
with other MDrive42AC Plus options, however are unavailable with Linear Actuators.
Planetary Gearbox Parameters
Gearbox Lengths Inches (mm)
k1
GEARBOX* with FLANGE†
1-Stage 5.73 (145.5) 5.9 (149.9)
2-Stage 7.07 (179.6) 7.13 (181.0)
3-Stage 8.41 (213.7) 8.35 (212.0)
Gearbox Lengths Inches (mm)
k1
GEARBOX* with FLANGE†
1-Stage 6.23 (158.2) 6.58 (167.2)
2-Stage 7.57 (192.4) 7.93 (201.4)
3-Stage 8.92 (226.6) 9.28 (235.6)
4 MDrive42AC Plus Microstepping REV060208

© Intelligent Motion Systems, Inc. All Rights Reserved. REV060208
IMS Product Disclaimer and most recent product information at www.imshome.com.
Intelligent Motion Systems, Inc.
370 North Main Street, P.O. Box 457
Marlborough, CT 06447 - U.S.A.
Tel. +00 (1) 860 295-6102 - Fax +00 (1) 860 295-6107
e-mail: [email protected]
http: //www.imshome.com
U.S.A. SALES OFFICES
Eastern Region
Tel. 862 208-9742 - Fax 973 661-1275
e-mail: [email protected]
Central Region
Tel. 260 402-6016 - Fax 419 858-0375
e-mail: [email protected]
Western Region
Tel. 602 578-7201
e-mail:
IMS ASIA PACIFIC OFFICE
30 Raffles Pl., 23-00 Caltex House
, Singapore 048622
Tel. +65/6233/6846 - Fax +65/6233/5044
e-mail: [email protected]
IMS EUROPEAN SALES MANAGEMENT
4 Quai Des Etroits
69005 Lyon, France
Tel. +33/4 7256 5113 - Fax +33/4 7838 1537
e-mail: [email protected]
IMS UK Ltd.
Sanderson Centre, 15 Lees Lane
Gosport, Hampshire PO12 3UL
Tel. +44/0 2392-520775 - Fax +44/0 2392-502559
e-mail: [email protected]
TECHNICAL SUPPORT
Tel. +00 (1) 860 295-6102 - Fax +00 (1) 860 295-6107
e-mail: [email protected]
–N
Control
Knob
Example: MDM1MSZ42B2–N adds a rear control knob to
example #1. Not available with sealed –65 versions.
–E
Internal
Encoder
OPTIONS
Example: MDM1MSQ42B2–EX adds an internal 512-line differential
optical encoder with index mark to example #1.
Refer to encoder specifications section for line counts and part numbers.
–G
Planetary
Gearbox
Example: MDM1MSZ42B2–G1A2 adds a PM105 1-stage
planetary gearbox with 5.18:1 ratio to example #1.
Add –F for optional NEMA flange.
Refer to gearbox page for complete
table of ratios and part numbers.
– FOptional NEMA Flange
MDM MSZ42 –
A = Single Length
B = Double Length
Example #1: Part Number MDM1MSZ42B2
is an MDrive42AC Plus
Microstepping
with
19-pin M23 circular I/O & SPI communications
interface, NEMA 42 double length motor and
240 input voltage.
OPTION
Input Voltage
1 = 120 Volt
2 = 240 Volt
MDrive Version
P1: I/O & Communications,
19-Pin M23 Circular Connector
P3: Power, 3-Pin Euro AC Connector
**Consult Factory for Availability.
Motor
Plus
base version
Plus2-65**
IP65 sealed
QuickStart Kit
details above
K
1 = Plus
2 = Plus-65 (sealed)**
ORDER INFORMATION — MDrive42AC Plus Microstepping
CONNECTING
QuickStart Kit
For rapid design verification, all-inclusive QuickStart Kits have com-
munication converter, prototype development cable(s), instructions
and CD for MDrivePlus initial functional setup and system testing.
Communication Converter
Electrically isolated, in-line converter pre-wired with mating connec-
tor to conveniently set/program communication parameters for a
single MDrivePlus via a PC's USB port. Length 12.0' (3.6m).
Mates to connector:
5-Pin M12 ............................................MD-CC301-001
Prototype Development Cables
Speed test/development with pre-wired mating connectors that
have flying leads other end. Single-ended cordsets are PVC jack-
eted with foil shield and unconnected drain wire. Length 13.0'
(4.0m).
Mates to connector:
19-Pin M23
Straight Termination ..........................MD-CC100-000
Right Angle Termination .....................MD-CC101-000
3-Pin Euro AC
Straight Termination ..........................MD-CC200-000
Right Angle Termination .....................MD-CC201-000
OPTIONS
Internal Encoder
An internal 512-line (2048 count) differential optical
encoder with index mark is available factory-mounted.
Control Knob
‡
For manual shaft positioning, a factory-mounted rear control
knob is available.
Planetary Gearbox
Efficient, low maintenance planetary gearboxes are
offered factory-mounted. Refer to details and part num-
bers on the back cover.
‡ Not Available with Sealed –65 Versions.
Connectivity details: www.imshome.com/cables_cordsets.html
PART NUMBERING
CONNECTIVITY OPTIONS
new
new
This manual suits for next models
1
Table of contents
Other Intelligent Motion Systems Engine manuals
Popular Engine manuals by other brands

Shanghai Diesel Engine
Shanghai Diesel Engine H Series Operation and maintenance manual
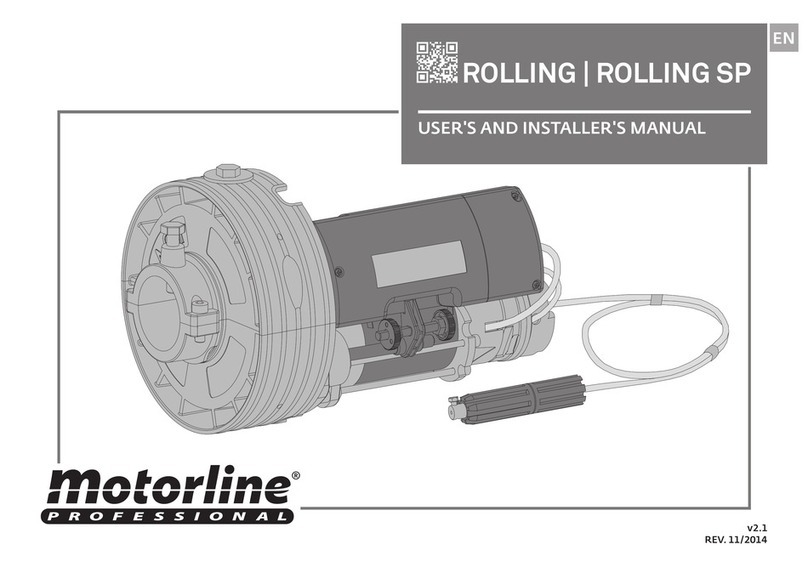
Motorline professional
Motorline professional ROLLING Series User's and installer's manual
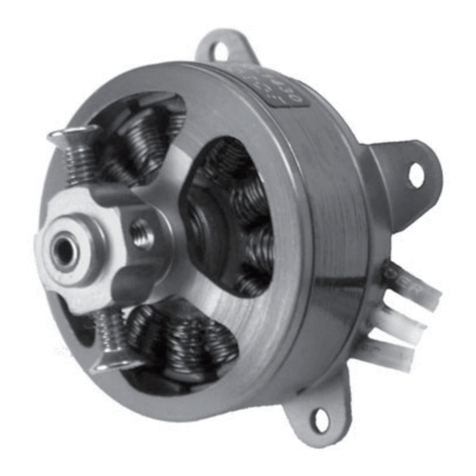
MPI
MPI Himax HC2805-1430 quick start guide

MPI
MPI Himax HB2815 Series quick start guide
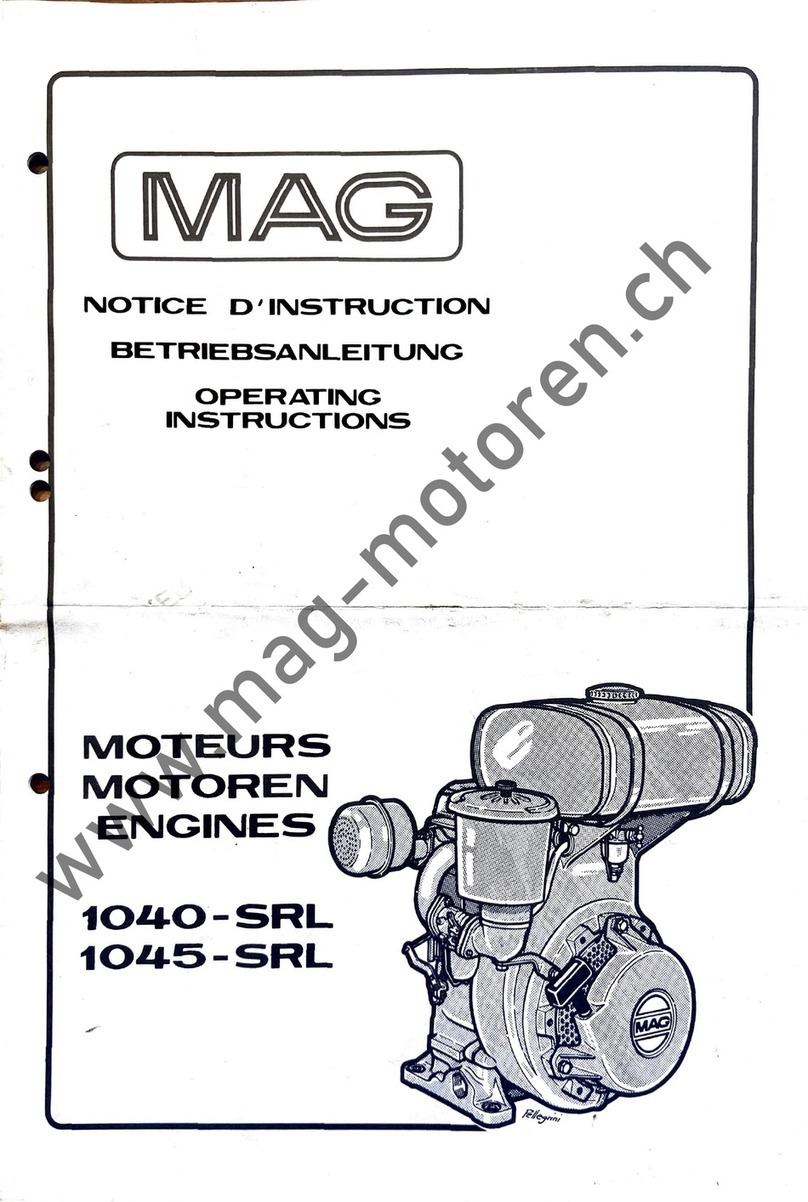
MAG
MAG 1040-SRL operating instructions

A.O. Smith
A.O. Smith Century Centurion Installation maintenance and service manual