Intron Plus INTROMET ITM-525 User manual

NON-DESTRUCTIVE TESTING AND TECHNICAL DIAGNOSTICS
I N T R O N P L U S
Tel.: +7 (495) 229-3747
Fax: +7 (495) 510-1769
info@intron-plus.com
www.intron-plus.com
Elektrodnaya Str., 11, Moscow, 111524, Russia
I N T R O M E T
ITM – 525
PCB copper thickness gauge
O P E R A T I N G M A N U A L


INTROMET ITM-525
Operating Manual 3
PRINCIPLE OF OPERATION
Please read this Operating Manual carefully before start operation. The
instrument includes tiny probes which must be handled with care. The
manufacturer keeps no responsibility for any damage occurred due to wrong
operation.
The INTROMET ITM-525 instrument is designed for accurate non-destructive
measurement of the copper thickness in plated through holes and copper foil on
laminate. It consists of electronic unit (Fig.1, 2) and probes (Fig. 3, 4).
Eddy current probes (US pat. 5,600,240) designed for measurement in through holes.
They are used for etched or unethed PCBs, as well as for tin-lead soldered PCBs. The
eddy current probe tips are acid-protected with special coating and can measure wet
PCB.
To measure copper thickness on laminate four-point electrical resistance method CSP
probe can be used.
Eddy current probes are detachable, consisting of a probe holder and replaceable
cartridge of certain size. To measure copper thickness in the hole, the tip of the
cartridge must be inserted into the hole up to stop.
The instrument must be properly calibrated before getting start. Calibration units
and foils are applied for this purpose. Calibration settings are stored in the instrument
memory. User can apply his own standards and store the calibration settings in the
instrument memory.
PCB parameters, measuring mode, print-out settings, etc. can be set with the
instrument keypad.
Measured data can be stored in instrument memory to be processed afterwards.
Readings and statistics taken can be displayed, downloaded to computer for printing
out.
Precautions
The tips of probes may be easily damaged if wrong operated. Please follow
advices mentioned below to extend probe life:
- use the tip protective cap when the probe is not in use
- insert the probe tip into the hole loosely and at right angles to the PCB
- do not apply force trying to insert tip into the hole
- carefully use cartridges because their tiny tips can be damaged mechanically.
- keep probe tips clean and dry
- keep cartridges away from strong magnetic field.

INTROMET ITM-525
Operating Manual4
CONTENTS
APPLICATION ............................................................................................................... 6
1.1.
Applicable PCB .......................................................................................................................................... 6
1.2.
Measuring Range and Resolution (copper in PTH) .......................................................................... 6
1.3.
Measuring Range and Resolution (copper on laminate)................................................................. 6
FEATURES .................................................................................................................... 7
CONTENT OF THE ITM-525 SET.................................................................................. 7
1.4.
Content......................................................................................................................................................... 7
POWER SUPPLY........................................................................................................... 8
OPERATION CONTROLS AND DISPLAYS.................................................................. 8
FACTORS, WHICH EFFECT READINGS.................................................................... 12
1.5.
Linear dimensions................................................................................................................................... 12
1.6.
Electric conductivity............................................................................................................................... 13
1.7.
Tin - Lead alloy coating.......................................................................................................................... 13
1.8.
Temperature.............................................................................................................................................. 13
START UP.................................................................................................................... 15
MEASURING OPERATION.......................................................................................... 15
1.9.
Measure data storage........................................................................................................................... 16
1.10.
Control through Main Menu.................................................................................................................. 16
1.11.
Measuring in Auto Start Mode.............................................................................................................. 18
1.12.
Measuring with Free-running display................................................................................................. 22
PRELIMINARY SETTING............................................................................................. 23
1.13.
Global settings......................................................................................................................................... 24
1.13.1.
Clock setting...................................................................................................................................... 24
1.13.2.
Measure unit system setting........................................................................................................... 25
1.13.3.
Turning on/off the sound and visual alarm ................................................................................... 26
1.13.4.
Display illumination setting.............................................................................................................. 27
1.13.5.
Downloading setting......................................................................................................................... 28
1.13.6.
Data storing....................................................................................................................................... 33
1.13.7.
Charge type....................................................................................................................................... 35
1.14.
File settings............................................................................................................................................... 36
1.14.1.
Definite file selection........................................................................................................................ 36
1.14.2.
File name setting.............................................................................................................................. 37
1.14.3.
Board thickness value setting......................................................................................................... 38
1.14.4.
Copper electric conductivity σvalue setting ................................................................................. 39
1.14.4.1.
Electric conductivity value setting. The Direct method........................................................... 39
1.14.4.2.
Electric conductivity σvalue setting. The Indirect method..................................................... 40
1.14.5.
Copper thickness tolerance limit setting ....................................................................................... 41
1.14.6.
Return to the default file settings.................................................................................................... 41
1.14.7.
File measure data removal............................................................................................................. 43
1.14.8.
File flushing....................................................................................................................................... 44
1.14.9.
Creation of new file .......................................................................................................................... 45

INTROMET ITM-525
Operating Manual 5
CALIBRATION..............................................................................................................46
1.15.
Calibration modes....................................................................................................................................46
1.16.
Base calibration ......................................................................................................................................46
1.17.
Master calibration....................................................................................................................................47
1.18.
Return to Base calibration.....................................................................................................................49
1.19.
Calibration with CSP...............................................................................................................................50
MEASURE DATA PROCESSING...............................................................................51
1.20.
Block data selection................................................................................................................................51
1.21.
Block name setting..................................................................................................................................52
1.22.
Block data display ...................................................................................................................................53
1.23.
Block data statistics display.................................................................................................................54
1.24.
Block data removal..................................................................................................................................55
1.25.
Create block ..............................................................................................................................................56
STATISTICAL TERMS.................................................................................................57
1.26.
Mean value.................................................................................................................................................57
1.27.
MIN, MAX and Range...............................................................................................................................57
1.28.
Standard Deviation..................................................................................................................................57
1.29.
Coefficient of Variation (COV) ..............................................................................................................57
1.30.
Capability statistics coefficients..........................................................................................................58
1.30.1.
Coefficient CP...................................................................................................................................58
1.30.2.
Coefficient CR...................................................................................................................................58
1.30.3.
Coefficient CPK.................................................................................................................................58
HAND-HELD PROBE GUIDE OPERATION..............................................................59
CARTRIDGE REPLACEMENT....................................................................................61
BATTERIES REPLACEMENT......................................................................................61
ERRORS.......................................................................................................................62
MEASURE DATA STORAGE STRUCTURE...............................................................63
TROUBLE SHOOTING................................................................................................64
SPECIFICATIONS ........................................................................................................65
DELIVERY LIST............................................................................................................66

Operating Manual6
APPLICATION
The ITM-525 is applied to measure copper thickness in plated through holes
(PTH) of PCB and copper thickness on laminate.
1.1. Applicable PCB
♦Single or double cladded, multilayer
♦Non-etched, etched
♦Without or with tin or tin-lead coating
PCB Thickness:
♦From 0.5 mm to 6.0 mm
Hole Diameter:
♦From 0.45 mm to 2 mm
1.2. Measuring Range and Resolution (copper in PTH)
Measuring Range:
♦From 5 µm to 60 µm
Resolution:
♦0.1 µm
1.3. Measuring Range and Resolution (copper on laminate)
Measuring Range:
♦From 15 µm to 80 µm
Resolution:
♦0.1 µm

Operating Manual 7
FEATURES
♦In-process measurement is possible
♦Only one-side access to the holes is required
♦No limitations on PCB size
♦No need for electric contact with plating
♦Reveals cracks in PTH coating
♦acid-protected probe tips
♦measures as small hole as 0.45 mm
♦Measures thickness in µm or mils
♦Two calibration modes
♦Automatic zero setting
♦Storing 15 000 measurements
♦Statistical analysis
♦USB interface
♦Measurement on laminate requires no cleaning surface
CONTENT OF THE ITM-525 SET
1.4. Content
The list of probes, parts and accessories available is as follows.
♦INTROMET ITM-525 electronic unit in leather pouch
♦Cartridge holder
♦Cartridge EP-30 for holes 0.8 to 2 mm
♦Cartridge EP-25 for holes 0.6 to 0.8 mm
♦Probe EP-20 for holes 0.45 to 0.6 mm

Operating Manual8
♦Probe shortened EP-30S for holes 0,8 to 2,0 mm)
♦Probe shortened EP-25S for holes 0,6 to 0,8 mm
♦Calibration unit EP25/30
♦Reference standard RS-52-1 for EP-30
♦Reference standard RS-52-2 for EP-25
♦Reference Standard & calibration unit RS-52-3 for EP-20
♦Probe Guide
♦CSP copper surface probe
♦CSP calibration foils
♦USBA-USBB cable
♦Plug-in type AC adapter
♦2 rechargeable AA batteries
♦Carrying Case
♦Operating Manual
POWER SUPPLY
ITM-525 is power supplied with two AA rechargeable batteries.
Continues working time - 10 hours.
"BAT LOW" displayed when batteries are low. The instrument is turned off
automatically. To charge batteries connect AC adapter and choose one of modes from
the instrument menu: Fast Charge / Normal Charge / Slow Charge. Charging time is 2 /
4 / 14 hours correspondingly. It is possible to use normal batteries (non-rechargeable).
In this case choose the No Charge mode to avoid accidental charge.
Following AC adapter is applied to recharge the batteries:
AC input: 110-240 V / 50-60 Hz
DC output: 9V, 500 mA
Outer pole: “-“
OPERATION CONTROLS AND DISPLAYS
ITM-525 has graphic LCD display and membrane keypad (Fig. 1).
Batteries compartment is from the rear (Fig. 2).
USB, probe, and AC connectors are located in the up.
Probe with cartridge installed is presented on Fig. 3, CSP probe – on Fig. 4.

Operating Manual 9
Fig.1. ITM-525. Front view
AC/DC
connector
Probe
connector
USB port
Display
Measuring
mode: close
current block
of measure
data and
open a new
block
ON/OFF
Call
statistics
for current
measure
data block
Delete the last
entered
measurement
from memory
Select menu
items and
parameter values
Forced
measurement
Select menu items
and parameter values
Direct access to Board
Thickness
1. Measure
data print-out.
2. Exit from
Master
Calibration
mode
Entry/Exit to
Main Menu
Confirm data
of item
selected

Operating Manual10
Fig.2. ITM-525. Rear view. Cover of battery compartment is open

Operating Manual 11
`
Fig. 4. CSP probe

Operating Manual12
FACTORS, WHICH EFFECT READINGS
There are factors, which effect readings of ITM-525.
The main factors are as following:
1.5. Linear dimensions
Following parameters effect readings: PCB thickness, hole diameter, copper
cladding thickness on PCB and dimensions of inner copper traces in case of multilayer
PCB.
The PCB thickness influence is eliminated by entering board thickness actual
value via the keyboard before measuring. Board core thickness variations within a
tolerance limit of 10% result in copper thickness reading variations of approx. 3%,
regardless of the copper cladding thickness.
The hole 0.8 mm to 2.0 mm diameter variation causes an additional error of the
readings taken with "EP-30" probe, not more than (1...2) µm. The measure error for
(0.45-0.6) mm and (0.6-0.8) mm hole diameters are still less.
The measurement reliability can be improved by instrument calibration applying
standards with known copper thickness in the through-holes. The copper thickness in
the standard PTH may be determined, for instance, through the metallographic cross-
section technique. However, the actual errors of standard certification should be
properly taken into account.
The effects of copper cladding thickness as well as the dimensions of contact
pads, outer and inner (for multilayer PCB), copper traces of etched PCB are usually
negligible for commonly produced PCB. However, the copper thickness reading for the
hole without contact pads around it may be significantly less than the real value. In this
case, measure result may be corrected through multiplying the reading by an
experimentally defined correcting coefficient. The correction is not necessary if the
contact pad diameter is greater than twice the hole diameter, according to IEC 326-3.

Operating Manual 13
1.6. Electric conductivity
The electric conductivity of electroplated or electrolyze deposited copper depends
basically on the plating bath conditions and chemistry.
The copper electric conductivity in the most applicable plating processes equals
approx. (50 ± 3) MS/m or (86 ± 5,3)% IACS. The value of 50.0 MS/m is taken as the
base one for the preliminary calibration of the instrument.
If the copper electric conductivity at the User's site differs significantly from the
base value of 50.0 MS/m and is definitely known, User can change the conductivity
value via the keyboard (Direct method, Chap. 9.2.4.1).
If the actual value of the electric conductivity is unknown, it can be entered
through the Indirect method (see Chap. 9.2.4.2) applying the standards with known
copper thickness produced at the User's.
1.7. Tin - Lead alloy coating
Due to the electric conductivity of tin-lead alloy is much lower than of the copper
conductivity, a 10 µthickness Sn-Pb layer results in an increase in the copper thickness
measurement of approx. 10% when the copper thickness is approx. 25 µm. This effect
decreases with increasing of copper plating thickness.
That is why the tin-lead coating influence can be stated as a negligible one.
1.8. Temperature
The copper electric conductivity is temperature dependent. The higher the
temperature, the lower the electric conductivity. Assuming the electroplated copper has
the same temperature coefficient as the pure copper, a 10°C change in temperature will
result in the 4% change of conductivity, which should be taken into consideration during
calibration.
Example:
♦Temperature of the standard at time of calibration : 25°C
♦Temperature of the board under test : 30°C
♦Change of conductivity : -2%
As the base value 50.0 MS/m of the electric conductivity is considered for base
calibration, User enters 49 MS/m value for Direct method correction (see Chap.
9.2.4.1).
Note
1 MS/m = 10
6
S/m = 10
6
1/(Ohm ⋅m);
100% IACS = 59.5 MS/m - electric conductivity of pure copper (20°C)
1 MS/m = 1.72% IACS;
1% IACS = 0.58 MS/m

Operating Manual14
For Indirect correction (see Chap. 9.2.4.2) User can apply the standard board with
the same temperature as the board under test.
In any case, be careful in evaluating the standard reliability and measurement
errors of an arbitrary method, e.g. of a cross-section method. These above mentioned
errors may be significantly more in value than the errors of the ITM-525.
RECOMMENDATIONS
To make sure the instrument readings are correct compare the readings
taken with the results of measurements in the same holes by another
technique, e.g., by microscope when the cross-section method is applied.
This comparison can be useful when User starts instrument application.
If readings differ from the measure results of an arbitrary method both
systematically and significantly, it is possible that the actual electric
conductivity value differs significantly from the base value of 50.0 MS/m.
In this case User can apply Direct or Indirect methods of reading
correction through entering the actual value of conductivity. Setting lower
conductivity you increase readings and vice versa.

Operating Manual 15
START UP
Plug appropriate cartridge to the cartridge holder and connect the probe to the
electronic unit. Remove protective cap.
Turn the instrument on and calibrate it if requested. Calibration is recommended
each time before getting start. The ITM-525 stores default BASE SETTINGS:
- calibration characteristic - Base;
- copper plating thickness indication - in µm;
- board thickness - 1.6 mm;
- copper electric conductivity - 50.0 MS/m;
- measure data is stored;
- out of tolerance measured copper thickness sound and visual alarm is on;
- lower limit of copper thickness in the hole - 15.0 µm;
- upper limit of copper thickness in the hole - 35.0 µm.
Settings can be changed (excepting "measure data is stored") through the Main
Menu of the instrument and held on for the next measurement sessions.
Recommendation:
Application of CSP does not require cleaning the copper surface prior to measurement.
However for better results degreasing is recommended. This can be done effectively
with eraser.
MEASURING OPERATION
"Measuring" is the main mode of the instrument operation. The instrument is
ready to measure just after been turned on.
Two modes of measuring are available:
1. Auto start measuring mode.
2. Free-running display mode.
In the Auto start measuring mode a measurement is taken automatically at the
moment when the probe tip is inserted into a hole. The reading appears on the main
display and is stored in the instrument memory.
In Free-running display mode measurements are performed continuously in the
cycle of 1 S and display. Measurements are not stored in the instrument memory.
To get reading of copper thickness in through hole the tip of probe is to be inserted in
the hole under test for 1-2 seconds.
To get reading on the surface of laminate CSP probe is to be put on the surface tightly,
so 4 pins of the probe get contact copper surface reliably. Reading appears
automatically.

Operating Manual16
1.9. Measure data storage
When measurements are performed in the Auto Start measuring mode sequences
of measurements are integrated in BLOCKS in the instrument memory. Month, date,
hour and minute of the BLOCK creation form its initial name. Later User can change a
block name for any desired(Chap. 11.2.). Data blocks can be called out for display,
printing and removal from the instrument memory by their names. The block created
during the current measuring session, is named ACTIVE. When measuring session has
been completed and "NEW BLOCK" key pressed, the current block is closed (becomes
non-active) and a new data block opens and becomes ACTIVE. If the "NEW BLOCK"
key not pressed after measuring session, the current block stays ACTIVE.
Thus, after the instrument is turned on, the ACTIVE BLOCK is the one which was
current before turning off.
All the measurement data blocks are combined into 8 FILES with initial names:
APPL0 ... APPL7. File names can be changed for desired too (Chap. 9.2.2).
Each file has one block as an ACTIVE one.
The instrument has two groups of preliminary settings.
1. Actual for all the data files - global settings:
- built-in clock (Chap. 9.1.1)
- measure system unit ( Chap. 9.1.2)
- sound and visual alarm on/off ( Chap. 9.1.3)
- backlight on/off (Chap. 9.1.4)
- print-out parameters (Chap. 9.1.5).
2. Actual for the individual file only - file settings:
- board thickness (Chap. 9.2.3)
- copper electric conductivity σ(Chap. 9.2.4)
- copper plating thickness tolerance limits: upper and lower (Chap. 9.2.5).
According to the above mentioned, measure data can be stored in different files
according to the calibration parameters: board thickness, copper conductivity σand
plating tolerance limits.
Measure data can be removed from the instrument memory in the following ways:
- the last measurement taken in the ACTIVE block through pressing “DEL” key in
the measuring mode (see Chap. 8.3);
- an individual measurement in the open block through pressing “DEL” in
“BLOCK/VEIW” mode (see Chap. 11.3);
- an individual block separately in the selected file through command
“BLOCK/Deleting” (see Chap. 11.5);
- all the blocks of the selected file simultaneously through command “FILE/Clear”
(see Chap. 9.2.7).
1.10. Control through Main Menu
The instrument operates under the control of the special software embedded in
the instrument program memory. Software provides User to control the instrument

Operating Manual 17
operation, to make various parameter settings via keyboard. The structure of the
program is presented in Fig. 5.
The program is built as a system of menus and submenus of the different levels.
These menu items are presented on the main display during the instrument operation.
Main Menu (Top level).
Items: FILE, CAL, BLOCK and SETUP form the Main Menu.
The items of the Main Menu present menus of the second level which are lists of
commands and submenus.
To enter the Main Menu from Measuring mode, press “PARAM” key.
To select the item required User moves through the Main Menu using "↑
↑↑
↑" and
"↓
↓↓
↓" “Arrow” keys. The list of items can be scrolled through like a “closed ribbon”. This
movement is indicated on the main display through changing item names displayed. To
entry the item required, select the item and confirm the selection by pressing “ENTER”
key. To return from the Main Menu into Measuring mode, press “PARAM” key again.
Menus (Second level).
Items of the second level are arranged in the lists of submenus and groups of
commands according to the item of Main Menu as a heading.
To select the item of the menus, enter the proper item of Main Menu and select
the required item of the second level applying vertical arrow keys ↑
↑↑
↑ and ↓
↓↓
↓.
To confirm the item selection press “ENTER” key.
To exit from menu to Main Menu press “PARAM” key.
Submenus and commands.
Submenus and commands are the items of the second level menus. By selecting
these items User can set up various parameters: PCB parameters, tolerance limits,
alarms, clock and so on, look through the measure data stored in memory or delete
some measure data from the memory if needed.
Inside submenus vertical arrow keys “↑
↑↑
↑” and “↓
↓↓
↓” are used
- to scroll the file/ block lists of contents;
- to change parameter values up and down.
In the submenus when one of the items in the row on display is highlighted via
“negative picture”, the keys “PARAM” and “STAT” change their meaning to the
horizontal arrows “←
←←
←” and “→
→→
→”. These horizontal “arrow” keys are used for selecting
items inside the submenus only.
To exit from submenu press “ENTER” key.

Operating Manual18
File
↔
↔↔
↔
Calibration
↔
↔↔
↔
Settings
↔
↔↔
↔
Block
↓
↓↓
↓
↓
↓↓
↓
↓
↓↓
↓
↓
↓↓
↓
Select file
Calibration
Time
Select block
↓
↓ ↓
File name
Print
Block name
↓
↓
↓
Boundaries
Alarm
New block
↓
↓
↓
Thickness
Units
Delete block
↓
↓
↓
Conductivity
Light
Block Data
↓
↓
Ind. conduct
Store Data
↓
↓
Basic Charge Type
↓ ↓
Flush file Format
↓
Create file
↓
Delete file
Fig. 5 Structure of Main Menu.
1.11. Measuring in Auto Start Mode
In this mode a current measurement is taken at the moment when the probe tip is
inserted into a hole up to the stop. The instrument indicates the measurement by a
short-time sound, displays the reading and holds it till next measurement. The measure
data is stored in the ACTIVE block of the current file.
Functions available through key pressing:
“NEW BLOCK” - close the current block and open a new one which becomes
ACTIVE;
“PARAM” - entry into Main Menu;
“PRINT” - transfer the measured data of the ACTIVE block to computer
via USB port;
“MEAS” - force the measurement when copper plating thickness in a hole
is very low: 2...5 µ (measurement auto start may not work).
Press the key holding probe tip in the hole;
“Bd TH” - entry directly into “Board thickness” item of Main menu;
“STAT” - display statistics of the ACTIVE block data;

Operating Manual 19
“DEL” - delete the measurement performed the last in order.
In the Auto Start Mode a measurement is taken in the manner as it is illustrated in
the following example:
KEY DISPLAY OPERATION
1. ON/OFF Self
calibration
Turn on the instrument. Probe tip is in air.
“Self calibration” indicates for 10 seconds.
2. Def. File 1
C=50.0MS/mT=1.50 mm
Min:15.0µ Max:35.0µ
Instrument is ready to measure.
3.
T=1.5
C=50
25
.3µ(*)
Insert probe tip into the hole under test.
Sound signal indicates the measurement
is taken and reading appears on display.
Measurement is stored in active block of a
current file
4.
T=1.5
C=50
25
.3µ(*)
Take probe tip out of the hole. Display
holds the reading
5. Repeat Operations 3, 4 for another hole
to be tested (***)
6. DEL
T=1.5
C=50
35
.3 µ
(
*
)
Press “DEL” key to delete measurement
taken the last in order
7.
T=1.5
C=50
0
.0 µ
Erroneous measurement disappears from
display.
Attention
Please, make sure there is free space under the board, so the probe tip
when inserted into the hole down to the stop could protrude through the
hole by 1...1.5 mm on the board opposite side
NOTE
To delete the last-in-order measurement, press "DEL" key. Erroneous
reading disappears from display and memory.
The last measurement of the block cannot be deleted. For this
measurement removal use “BLOCK/Deleting” routine

Operating Manual20
8. STAT Data Amount
N= 9 Number of measurements in block
displays
9. ↑
↑↑
↑
Average
26.2 µ Average value of block measurements
displays
10. ↑
↑↑
↑
Minimum
49.1 µ Minimum value of block measurements
displays
11. ↑
↑↑
↑
Maximum
25.6 µ Maximum value of block measurements
displays
12. ↑
↑↑
↑
Range
1.0 µ Range value of block measurements
displays
13. ↑
↑↑
↑
Deviation
0.3 µ Standard deviation of block
measurements displays
14. ↑
↑↑
↑
Coeff.Var.
0.69 % Coefficient of variation of block
measurements displays
15. ↑
↑↑
↑
CP
24.005 Coefficient CP displays
16. ↑
↑↑
↑
CR
0.042 Coefficient CR displays
17. ↑
↑↑
↑
CPK
-14.068 Coefficient CPK displays
18. Param
T=1.5
C=50
0
00
0
.0 µ
Return to measuring mode. Instrument is
ready to measure
19. PRINT PRINTING ... Measure data is being transferred out.
After transferring completed, string
"PRINTING" disappears from display
NOTE
For ACTIVE block statistics calling, press "STAT" key. Active block
statistics display
NOTE
For transferring the active block data via USB-port press "PRINT" key
Table of contents
Popular Measuring Instrument manuals by other brands
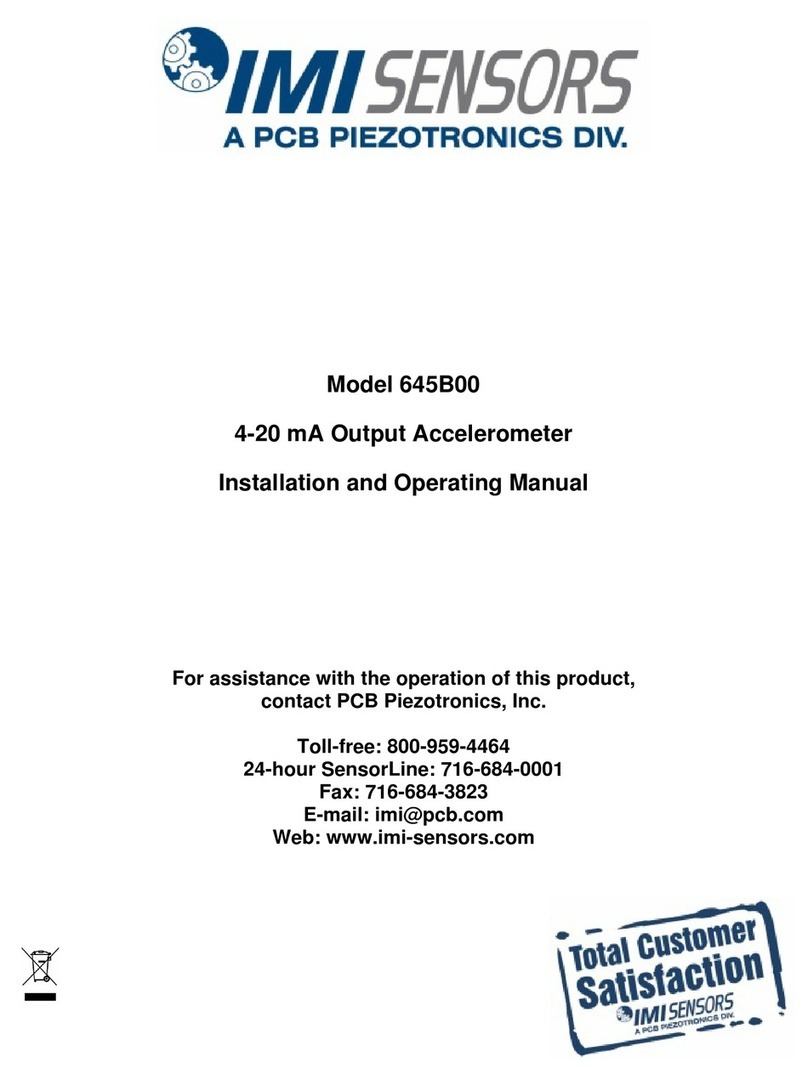
PCB Piezotronics
PCB Piezotronics IMI SENSORS 645B00 Installation and operating manual
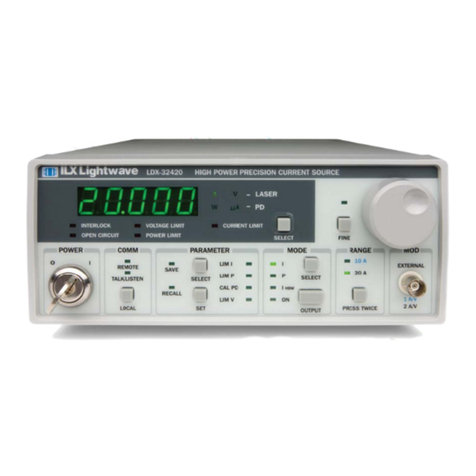
ILX Lightwave
ILX Lightwave LDX-32420 user guide
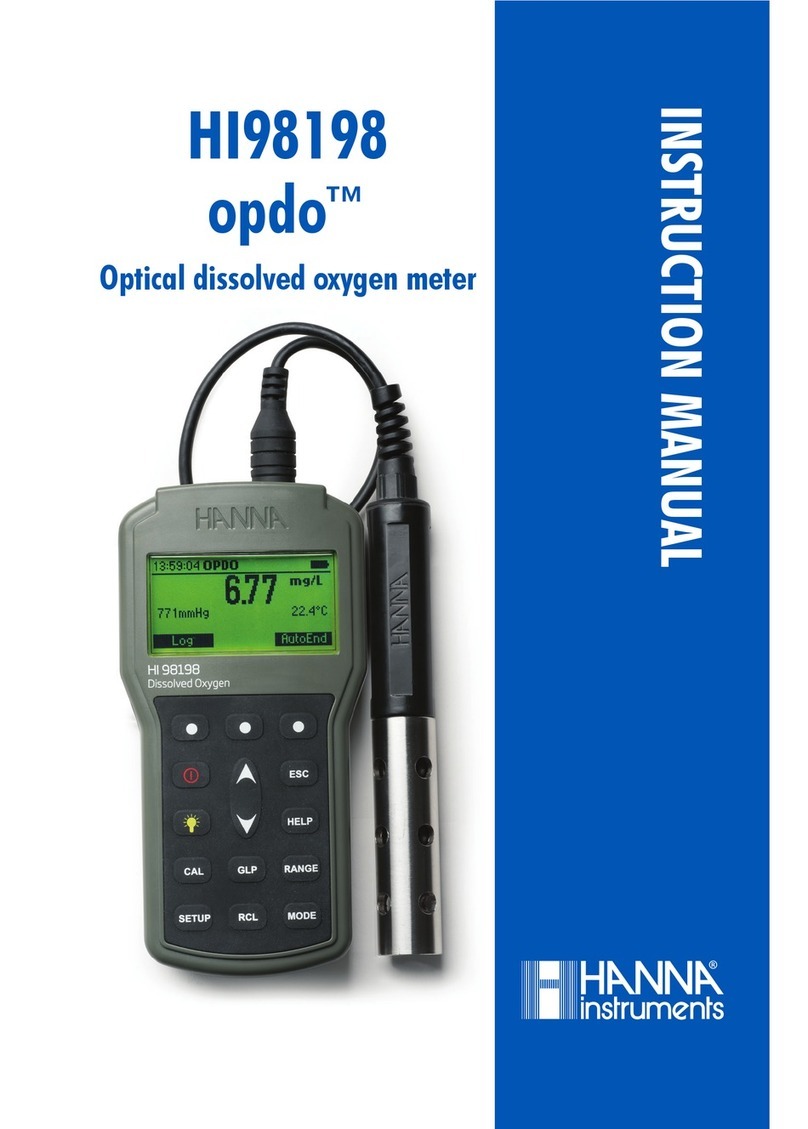
Hanna Instruments
Hanna Instruments HI98198 OPDO instruction manual
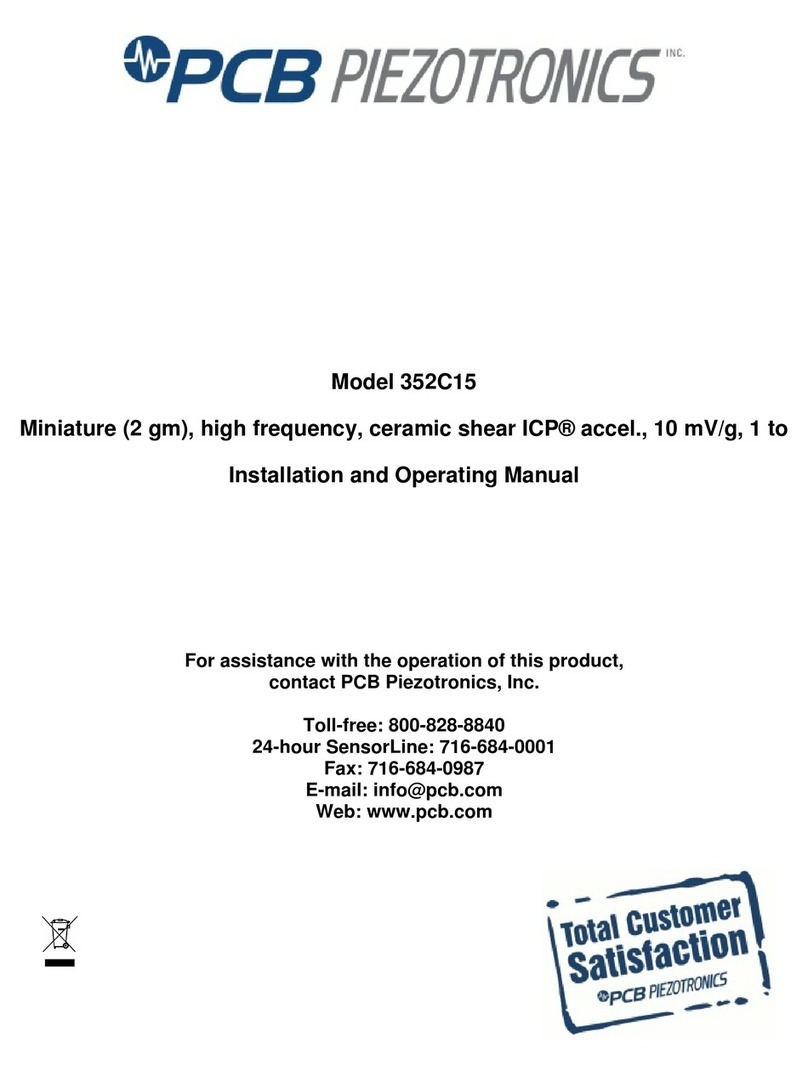
PCB Piezotronics
PCB Piezotronics 352C15 Installation and operating manual
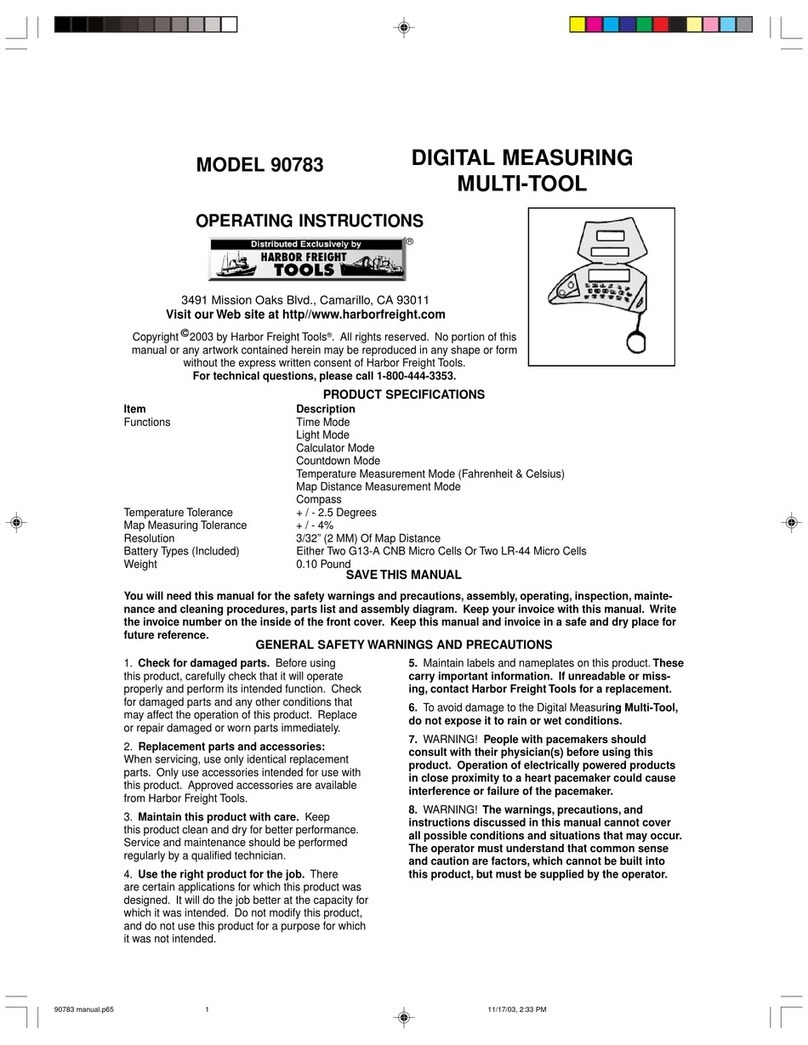
Harbor Freight Tools
Harbor Freight Tools 90783 operating instructions
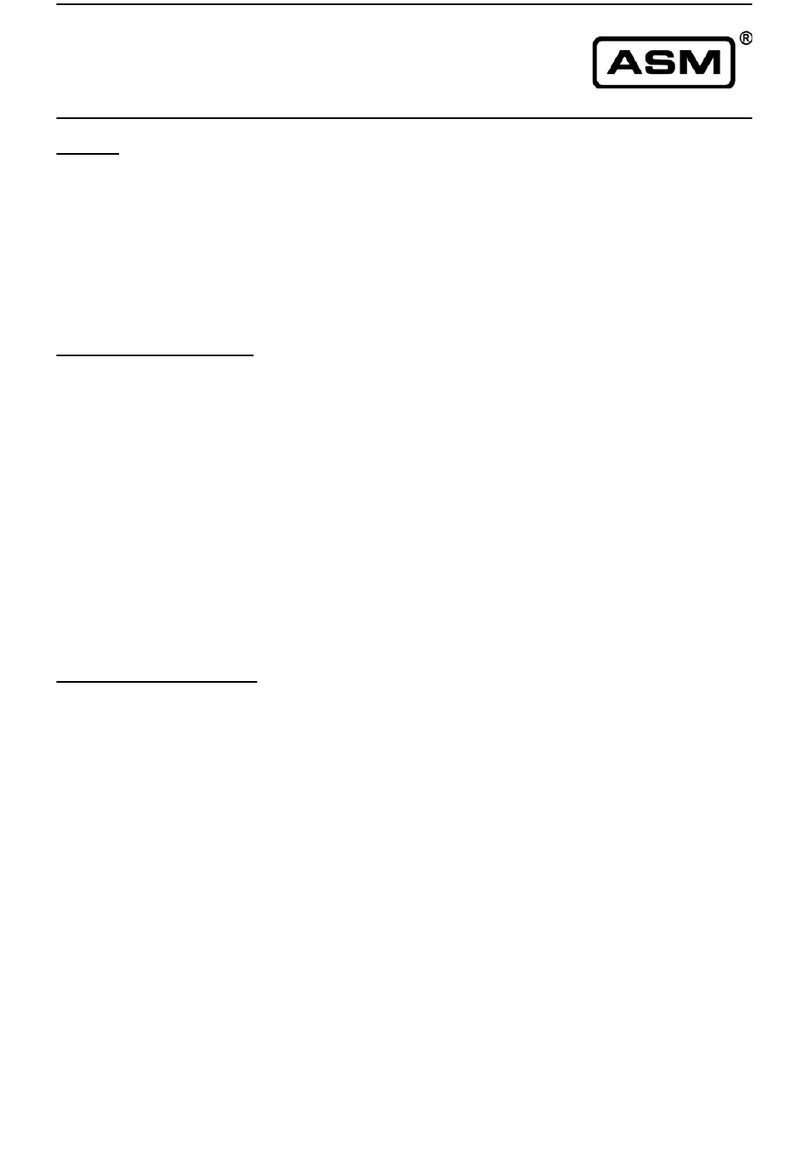
ASM
ASM NMG2 quick reference
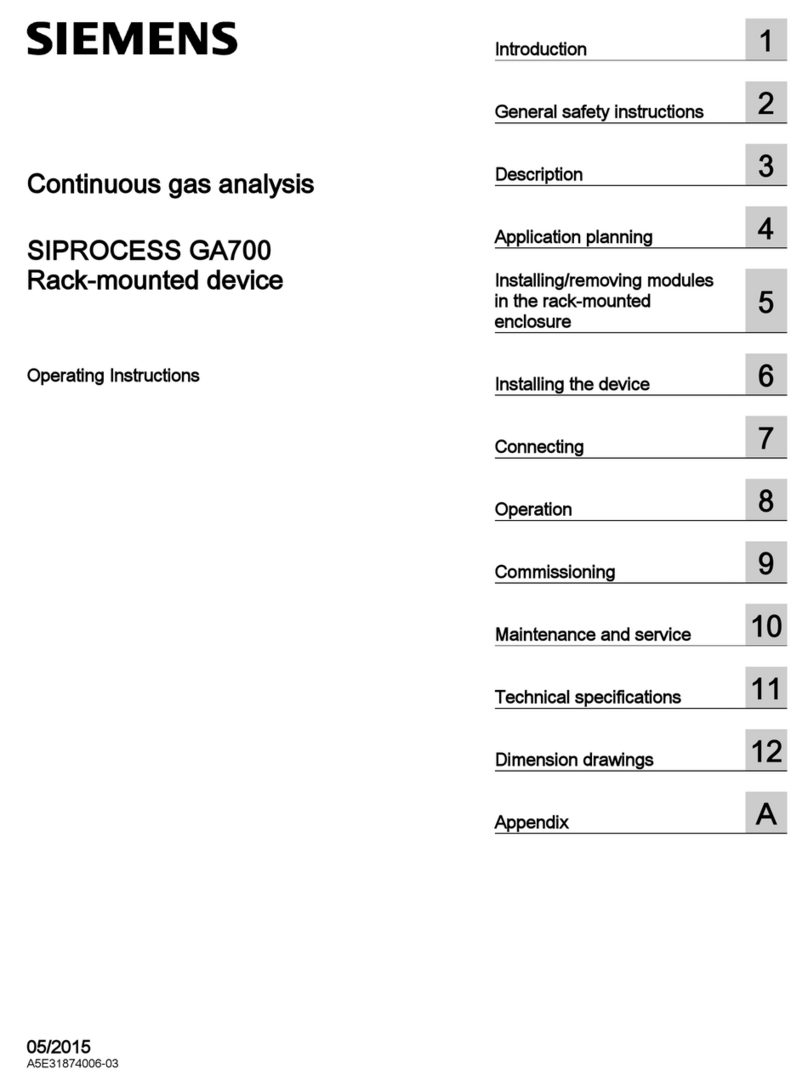
Siemens
Siemens SIPROCESS GA700 operating instructions
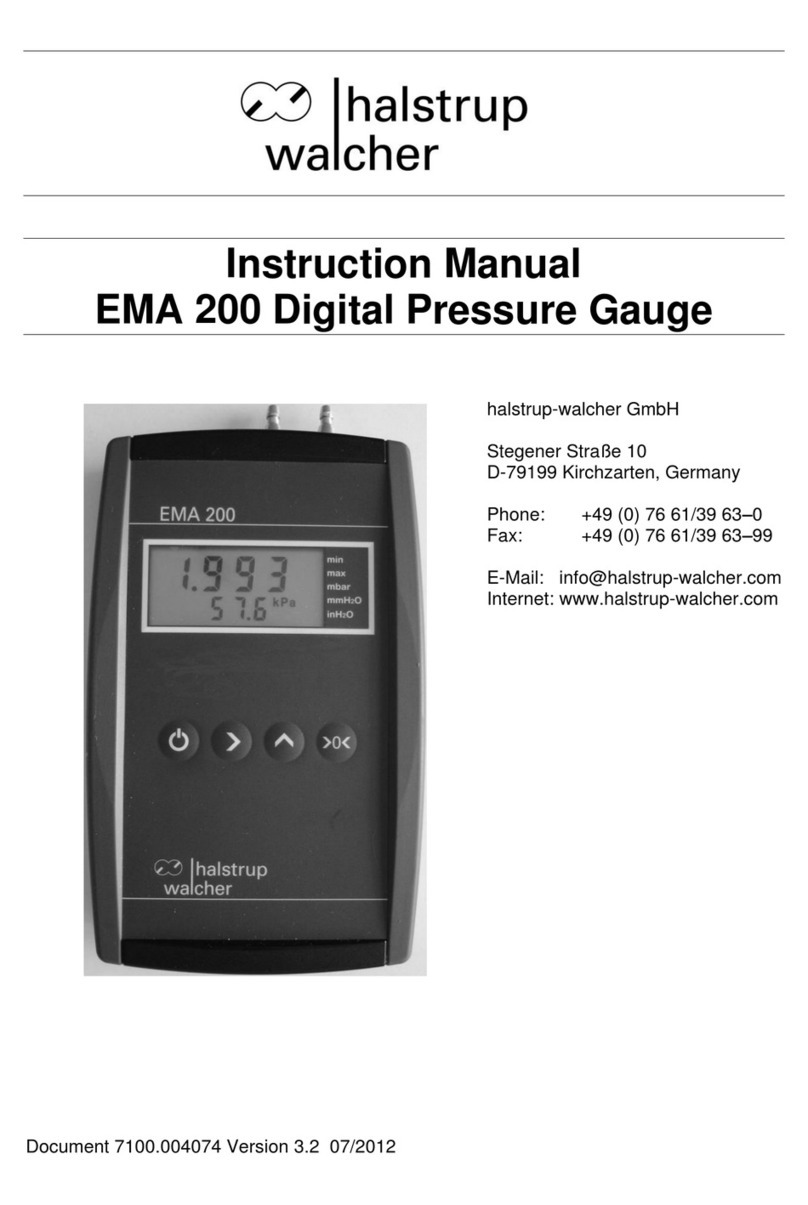
halstrup-walcher
halstrup-walcher EMA 200 instruction manual
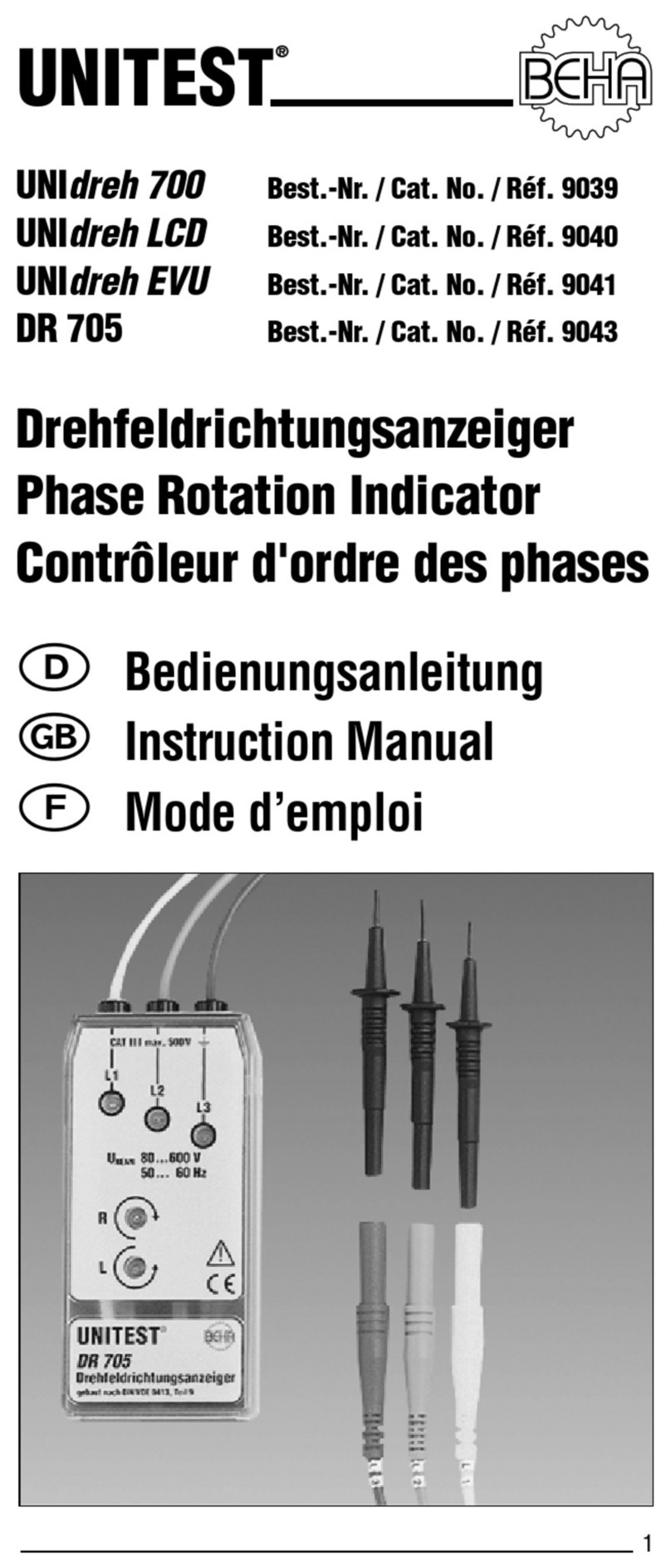
BEHA
BEHA Unitest UNI dreh 700 instruction manual
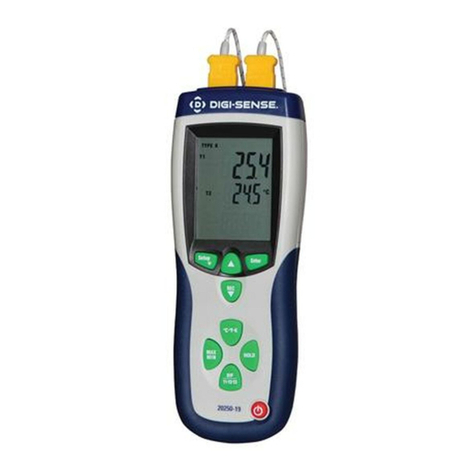
Digi-Sense
Digi-Sense 20250-19 user manual
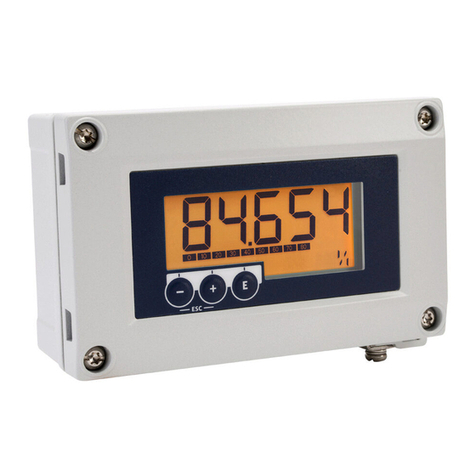
AutomationDirect
AutomationDirect ProSense LPM1 Series operating instructions
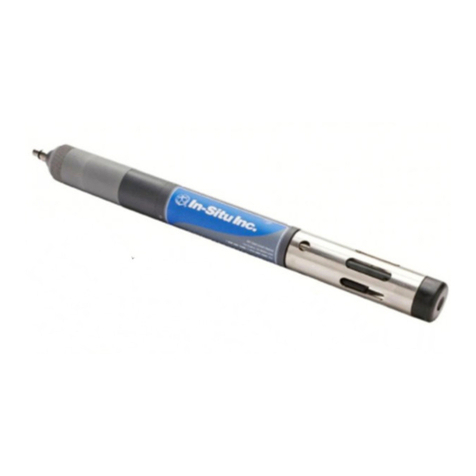
In-situ
In-situ MP TROLL 9500 quick start guide