ITW Dynatec DynaFiber UFD Guide

Adhesive Application Solutions | ISO 9001 certified
DynaFiber UFD
Spray Applicator, 1-6 Port
Technical Documentation
ITW Dynatec
An Illinois Tool Works Company
www.itwdynatec.com

ITW Dynatec
Information about this manual
Page 2UFD Applicator, Manual 40-43, Rev. 6.16
Information about this manual
Read all instructions before operating this equipment!
It is the customer’s responsibility to have all operators and service
personnel read and understand this information. Contact your ITW
Dynatec customer service representative for additional copies.
NOTICE:
Please be sure to include the serial number of your application
system each time you order replacement parts and/or supplies. This
will enable us to send you the correct items that you need.
ITW Dynatec Service Parts Direct Dial: 1-800-538-9540
ITW Dynatec Technical Service Direct Dial: 1-800-654-6711

Index
ITW Dynatec
UFD Applicator, Manual 40-43, Rev. 6.16 Page 3
Index
Information about this manual................................................2
Index..........................................................................................3
Chapter 1 Declaration of Incorporation..................................7
Chapter 2 Safety Instructions .................................................9
General Considerations ............................................................................................................ 9
Warning Labels ......................................................................................................................... 9
Safety Symbols in this Manual................................................................................................ 10
Safe Installation and Operation............................................................................................... 10
Explosion/ Fire Hazard............................................................................................................ 11
Use of PUR (Polyurethane) Adhesives................................................................................... 11
Eye Protection & Protective Clothing...................................................................................... 11
Electrical.................................................................................................................................. 12
Lockout/ Tagout ...................................................................................................................... 12
High Temperatures ................................................................................................................. 12
High Pressure ......................................................................................................................... 13
Protective Covers.................................................................................................................... 13
Servicing, maintenance........................................................................................................... 14
Secure transport...................................................................................................................... 14
Treatment for Burns from Hot Melt Adhesives........................................................................ 15
Measures in case of fire.......................................................................................................... 15
Keep attention to environmental protection standards ........................................................... 16
Chapter 3 Description and Technical Specs .......................17
3.1 Applicable Safety Regulations...................................................................... 17
Intended Use........................................................................................................................... 17
Unintended Use, Examples..................................................................................................... 17
Residual Risks ........................................................................................................................ 17
Technical changes .................................................................................................................. 18
Using foreign components ...................................................................................................... 18
Setting-up operation................................................................................................................ 18
3.2 Description of UFD Spray Applicator............................................................ 19
Description .............................................................................................................................. 19
Technical Data ........................................................................................................................ 21
Model Designation Guide........................................................................................................ 22
Dimensions.............................................................................................................................. 23
Chapter 4 Installation & Startup............................................25
4.1 Conditions for set-up and mounting.............................................................. 25
4.2 Installation & Startup..................................................................................... 26
Special Installation Notes on HiSpeed, Vertical Snuffback, Direct-Air Module....................... 29
Operation of Optional Drain Valve.......................................................................................... 29
Purging Adhesive Through the Applicator .............................................................................. 30
4.3 Quality of compressed Air............................................................................. 30
Chapter 5 Maintenance and Repair Notes ...........................31
5.1 Security advices for maintenance and repair................................................ 31
5.2 Re-Assembly Procedures and General Cautions......................................... 32

ITW Dynatec
Index
Page 4UFD Applicator, Manual 40-43, Rev. 6.16
5.3 Stroke Limit Adjustment................................................................................ 32
5.4 Relieving Adhesive Pressure........................................................................ 33
5.5 Replacement of the Built-in Filter.................................................................. 34
5.6 Replacement of the Module.......................................................................... 36
Modules Which Are Not Serviceable ...................................................................................... 36
Replacement of the Standard Module .................................................................................... 36
Module Assembly Instructions for the PN 104993 UFD Module............................................. 37
Module Assembly Instructions for the PN 106224 UFD or 106226 HiTemp UFD Module..... 38
Module Assembly Instructions for the PN 110840 Horizontal SB and PN 111074 Vertical SB
UFD Modules .......................................................................................................................... 39
5.7 Replacement of the UFD Nozzle .................................................................. 40
5.8 Cleaning of the UFD Nozzle ......................................................................... 41
5.9 Testing of Resistance................................................................................... 43
Testing Resistance of Heater Cartridges................................................................................ 43
Testing Resistance of the RTD Temperature Sensor............................................................. 44
Testing the J-type Thermocouple Temperature Sensor......................................................... 44
Resistance Tables, Temperature sensors.............................................................................. 45
5.10 Replacement of Heater Cartridge or Temperature Sensor......................... 46
5.11 Maintenance plan ....................................................................................... 49
Chapter 6 Troubleshooting ...................................................51
Troubleshooting In General..................................................................................................... 51
Troubleshooting Guide UFD Applicator .................................................................................. 51
Chapter 7 Component Illustrations & Bills of Materials .....53
1-Port UFD Vertical & Horizontal Apply Applicator Assemblies.......................... 54
Air Preheater Assembly for 1-Port UFD Vertical & Horizontal Apply...................................... 56
Air Preheater Assembly for 1- or 2-Port UFD Slim Design..................................................... 58
2-Port UFD Vertical & Horizontal Apply, 1 or 2 Program, Applicator Assemblies60
Air Preheater Assembly for 2-Port UFD Vertical & Horizontal Apply, 1 or 2 Program............ 62
3-Port UFD Vertical & Horizontal Apply, 1, 2 or 3 Program, Applicator Assemblies
............................................................................................................................ 64
Air Preheater Assembly for 3-Port UFD Vertical & Horizontal Apply, 1 or 3 Program............ 66
Air Preheater Assembly for 3-Port UFD Slim Design ............................................................. 68
4-Port UFD Vertical & Horizontal Apply, 1 or 4 Program, Applicator Assemblies70
Air Preheater Assembly for 4-Port UFD Vertical & Horizontal Apply, 1 or 4 Program............ 72
Air Preheater Assembly PN 112793 for 4-Port UFD Slim Design .......................................... 74
6-Port UFD Vertical & Horizontal Apply, 1 or 6 Program, Applicator Assemblies76
Air Preheater Assembly for 6-Port UFD Vertical & Horizontal Apply, 1 or 6 Program............ 78
Air Preheater Assembly PN 112794 for 6-Port UFD Slim Design .......................................... 80
UFD Modules...................................................................................................... 82
UFD Spray Module Assembly, Horizontal, PN 104993 .......................................................... 82
UFD Spray Module Assembly, Vertical, Extended, PN 106224 ............................................. 84
UFD Spray Module Assembly, Horizontal, Snuffback, PN 110840 ........................................ 86
UFD Spray Module Assembly, High Speed, Vertical, PN 113778.......................................... 86
UFD Spray Module Assembly, Snuffback, Vertical, PN 111074............................................. 87
UPD Spray Module Assembly, High Speed, Vertical, PN 113346.......................................... 88
UFD Spray Module Assembly, High Speed, Horizontal, PN 113550...................................... 89
UFD Spray Module Assembly, High Speed, Horizontal, PN 115160...................................... 90
Blank Module, Horizontal & Vertica .................................................................... 91

Index
ITW Dynatec
UFD Applicator, Manual 40-43, Rev. 6.16 Page 5
Blank Module, Vertical Air Only, PN 111053 .......................................................................... 91
Blank Module, Horizontal Air Only, PN 111052...................................................................... 91
UFD Nozzle Seals .............................................................................................. 92
Festo Solenoid Assemblies, PN 115055 & 115056............................................ 93
Chapter 8 Options & Accessories ........................................95
Applicator Heater Cartridges................................................................................................... 95
Applicator RTD Sensors.......................................................................................................... 95
Filters....................................................................................................................................... 95
Filter Kits ................................................................................................................................. 96
Service Kits ............................................................................................................................. 96
High-Temp Splice Kit, PN102645 ........................................................................................... 96
UFD Nozzle Cleaning Oven.................................................................................................... 96
Pressure Transducer Tap ....................................................................................................... 97
Drain Valve PN 107820........................................................................................................... 97
Balanced Solenoid Manifold.................................................................................................... 97
Low-Profile (Slim line) Models (codes A, J, M, P)................................................................... 97
Elastic Guide Bracket Assembly, PN 107622......................................................................... 98
Extension Cable Assemblies................................................................................................... 99
Strand Coating System (SCS) .............................................................................................. 100
Recommended Service Parts List......................................................................................... 102
Chapter 9 Engineering Drawings & Schematics ...............103
Pin Connectors & Electrical Schematics............................................................................... 103
Chapter 10 Appendix............................................................105
Solenoid Valve Configurations, Schematics & Setup ........................................................... 105
Air Filter/ Regulator Installation Notes .................................................................................. 105
Section 1, 24 VDC MAC solenoid valve, 4 way, 02, 1/8 NPT, PN 100054........................... 106
Section 2, MAC solenoid valve, 4 way, 1/4 NPT................................................................... 107
Section 3, 24 VDC MAC solenoid valve, 5 way, 1/8 NPT, PN 106937................................. 108
Section 4, 24 VDC MAC solenoid valve, 4 way, 1/4 NPT, PN 112496................................. 109
Section 5, 24 VDC MAC solenoid valve, 4 way, 1/4 NPT, PN 112496................................. 110
Section 6, Air Control Kit PN 100055, Component Illustration.............................................. 111
Process (Preheater) Air Control Filter/ Regulator, PN 107404............................................. 112

ITW Dynatec
Index
Page 6UFD Applicator, Manual 40-43, Rev. 6.16
This page intentionally left blank.

Chapter 1
Declaration of Incorporation
ITW Dynatec
UFD Applicator, Manual 40-43, Rev. 6.16 Page 7
Chapter 1
Declaration of Incorporation

ITW Dynatec
Chapter 1
Declaration of Incorporation
Page 8UFD Applicator, Manual 40-43, Rev. 6.16

Chapter 2
Safety Instructions
ITW Dynatec
UFD Applicator, Manual 40-43, Rev. 6.16 Page 9
Chapter 2
Safety Instructions
General Considerations
All operators and service personnel must read and understand this manual
before operating or servicing equipment.
All maintenance and service on this equipment must be performed by trained
technicians.
Read and adhere to the manual!
1. Read and follow these instructions.
Failure to do this could result in severe personal injury or death.
2. Keep the binding rules for accident prevention valid for your country and the place of
installation. Also keep the approved qualified technical rules for safety-conscious and
professional work.
3. Additional safety instructions and/ or symbols are located throughout this manual.
They serve to warn maintenance personnel and operators about potentially hazardous
situations.
4. Inspect the machine for unsafe conditions daily and replace all worn or defective parts.
5. Keep work area uncluttered and well lit. Remove all material or things not needed for
the production from the workspace of the equipment!
6. All covers and guards must be in place before operating this equipment.
7. Subject to technical modifications without notice!
8. To ensure proper operation of the equipment, use specified electrical and/ or air
supply sources.
9. Do not attempt to alter the design of the equipment unless written approval is received
from ITW Dynatec.
10. Keep all manuals readily accessible at all times and refer to it often for the best
performance from your equipment.
Warning Labels
1. Read and obey all of the warning labels, signs and caution statements on the
equipment.
2. Do not remove or deface any of the warning labels, signs and caution statements on
the equipment.
3. Replace any warning labels, signs and caution statements which have been removed
or defaced. Replacements are available from ITW Dynatec.

ITW Dynatec
Chapter 2
Safety Instructions
Page 10 UFD Applicator, Manual 40-43, Rev. 6.16
Safety Symbols in this Manual
1. WARNINGS and CAUTIONS are found throughout this manual.
WARNINGS mean that failure to observe the specific instructions may cause injury to
personnel.
2. CAUTIONS mean that failure to observe the specific instructions may damage the
equipment.
Safe Installation and Operation
Read and adhere to the manual!
1. Read this manual before applying electrical power to the equipment. Equipment may
be damaged by incorrect electrical connections.
2. To avoid possible failure of hoses, make sure all hoses are routed to avoid kinking,
tight radius turns (8” or less) and abrasive contact. Hot‐melt hoses should not have
prolonged contact with heat‐absorbing surfaces such as cold floors or metal troughs.
These heat‐absorbing surfaces can alter adhesive flow and cause incorrect
calibration. Hoses should never be covered with materials that prevent heat
dissipation, such as insulation or sheathing. Hoses should be spaced apart from each
other, not making direct contact.
3. Do not use adhesive that is dirty or that may be chemically contaminated. Doing so
can cause system clogging and pump damage.
4. When adhesive hand‐held applicators or other movable applicators are used, never
point them at yourself or at any other person. Never leave a hand‐held applicator's
trigger unlocked when not actually in use.
5. Do not operate the hopper or other system components without adhesive for more
than 15 minutes if the temperature is 150 degrees C (300 degrees F) or more. To do
so will cause charring of the residual adhesive.
6. Never activate the heads, hand‐held applicators and/ or other application devices until
the adhesive's temperature is within the operating range. Severe damage could result
to internal parts and seals.
7. Never attempt to lift or move the unit when there is molten adhesive in the system.
8. In case of an emergency or exceptional incident, press the emergency stop button in
order to stop the unit quickly.
9. Use the unit only as it is intended to.
10. Never let the unit run unattended.
11. Operate the unit only in a faultless and fully functional condition. Check and make
sure that all safety devices work in proper form!

Chapter 2
Safety Instructions
ITW Dynatec
UFD Applicator, Manual 40-43, Rev. 6.16 Page 11
Explosion/ Fire Hazard
1. Never operate this unit in an explosive environment.
2. Use cleaning compounds recommended by ITW Dynatec or your adhesive supplier
only.
3. Flash points of cleaning compounds vary according to their composition, so consult
with your supplier to determine the maximum heating temperatures and safety
precautions.
Use of PUR (Polyurethane) Adhesives
1. PUR adhesives emit fumes (MDI and TDI) that can be dangerous to anyone exposed
to them. These fumes cannot be detected by the sense of smell. ITW Dynatec strongly
recommends that a power‐vented exhaust hood or system be installed over any PUR
system.
2. Consult with your adhesive manufacturer for specifics about required ventilation.
CAUTION
Because of the nature of PUR adhesives to strongly bond in the presence of moisture,
care must be taken to prevent them from curing inside ITW Dynatec equipment.
If PUR adhesive solidifies in a unit, the unit must be replaced. Always purge old PUR
adhesive from the system per your adhesive manufacturer's instructions and time table.
ALLOWING PUR ADHESIVE TO CURE IN A UNIT OR ITS COMPONENTS VOIDS ITW
DYNATEC'S WARRANTY.
Eye Protection & Protective Clothing
WARNING
EYE PROTECTION & PROTECTIVE CLOTHING REQUIRED
1. It is very important that you PROTECT YOUR EYES when working around
hot melt adhesive equipment!
2. Wear a face shield conforming to ANSI Z87.1 or safety glasses with side
shields which conform to ANSI Z87.1 or EN166.
3. Failure to wear a face shield or safety glasses could result in severe eye injury.
4. It is important to protect yourself from potential burns when working around hot melt
adhesive equipment.
5. Wear heat-resistant protective gloves and long‐sleeved, protective clothing to prevent
burns that could result from contact with hot material or hot components.
6. Always wear steel‐reinforced safety shoes.

ITW Dynatec
Chapter 2
Safety Instructions
Page 12 UFD Applicator, Manual 40-43, Rev. 6.16
Electrical
DANGER HIGH VOLTAGE
1. Dangerous voltages exist at several points in this equipment. To avoid personal injury,
do not touch exposed connections and components while input power is on.
2. Disconnect, lockout and tag external electrical power before removing protective
panels.
3. A secure connection to a reliable earth ground is essential for safe operation.
4. An electrical disconnect switch with lockout capability must be provided in the line
ahead of the unit. Wiring used to supply electrical power should be installed by a
qualified electrician.
5. Notify the maintenance personnel immediately, if cables are damaged. Provide for
exchanging the defective components immediately.
Lockout/ Tagout
Switch the unit voltage-free before working!
Main switch OFF!
1. Follow OSHA 1910.147 (Lockout/ Tagout Regulation) for equipment's lockout
procedures and other important lockout/tagout guidelines.
2. Be familiar with all lockout sources on the equipment.
3. Even after the equipment has been locked out, there may be stored energy in the
application system, particularly in the capacitors within the panel box. To ensure that
all stored energy is relieved, wait at least one minute after removing power before
servicing electrical capacitors.
High Temperatures
WARNING HOT SURFACE
1. Severe burns can occur if unprotected skin comes in contact with molten adhesive or
hot application system parts.
2. Face shields (preferred) or safety glasses (for minimum protection), heat-resistant
protective gloves and long-sleeved clothing must be worn whenever working with or
around adhesive application systems.

Chapter 2
Safety Instructions
ITW Dynatec
UFD Applicator, Manual 40-43, Rev. 6.16 Page 13
High Pressure
WARNING HIGH PRESSURE PRESENT
1. To avoid personal injury, do not operate the equipment without all covers, panels and
safety guards properly installed.
2. To prevent serious injury from molten adhesive under pressure when servicing the
equipment, disengage the pumps and relieve the adhesive system's hydraulic
pressure (i.e. trigger the heads, hand‐held applicators, and/or other application
devices into a waste container) before opening any hydraulic fittings or connections.
3. IMPORTANT NOTE: Even when a system's pressure gauge reads “0” psi, residual
pressure and trapped air can remain within it causing hot adhesive and pressure to
escape without warning when a filter cap or a hose or hydraulic connection is
loosened or removed. For this reason, always wear eye protection and protective
clothing.
4. Either of the two High Pressure symbols shown may be used on ITW Dynatec
equipment.
5. Keep the given operating pressure.
6. Notify the maintenance personnel immediately, if hoses or components are damaged.
Provide for exchanging the defective components immediately.
Protective Covers
WARNING
DO NOT OPERATE WITHOUT GUARDS IN PLACE
1. Keep all guards in place!
2. To avoid personal injury, do not operate the application system without all covers,
panels and safety guards properly installed.
3. Never get your extremities and/or objects into the danger area of the unit. Keep your
hands away from running parts of the unit (pumps, motors, rolls or others).

ITW Dynatec
Chapter 2
Safety Instructions
Page 14 UFD Applicator, Manual 40-43, Rev. 6.16
Servicing, maintenance
1. Only trained and qualified personnel are to operate and service this equipment.
2. Before any service work disconnect the external power supply and the pressure air
supply!
3. Never service or clean equipment while it is in motion. Shut off the equipment and lock
out all input power at the source before attempting any maintenance.
4. Follow the maintenance and service instructions in the manual.
5. Keep the maintenance rates given in this documentation!
6. Any defects in the equipment that impact safe operation have to be repaired
immediately.
7. Check screws that have been loosened during the repair or maintenance, if they are
tight again.
8. Replace the air hoses in preventive maintenance regularly, even if they have got no
viewable damages! Adhere to the manufacturers` instructions!
9. Never clean control cabinets or other houses of electrical equipment with a jet of
water!
10. Adhere to the current safety data sheet of the manufacturer when using hazardous
materials (cleaning agents, etc.)!
Secure transport
1. Examine the entire unit immediately after receipt, if it has been delivered in perfect
condition.
2. Let damages in transit certify by the carrier and announce them immediately to ITW
Dynatec.
3. Use only lifting devices that are suitable for the weight and the dimensions of the
equipment (see drawing of the equipment).
4. The unit has to be transported upright and horizontally!
5. The unit has to cool down to room temperature before packaged and transported.

Chapter 2
Safety Instructions
ITW Dynatec
UFD Applicator, Manual 40-43, Rev. 6.16 Page 15
Treatment for Burns from Hot Melt Adhesives
Measures after being burned:
1. Burns caused by hot melt adhesive must be treated at a burn center. Provide the burn
center's staff a copy of the adhesive's M.S.D.S. to expedite treatment.
2. Cool burnt parts immediately!
3. Do not remove adhesive forcibly from the skin!
4. Care should be used when working with hot melt adhesives in the molten state.
Because they rapidly solidify, they present a unique hazard. Even when first solidified,
they are still hot and can cause severe burns.
5. When working near a hot melt application system, always wear safety shoes, heat-
resistant protective gloves, safety goggles and protective clothes that cover all
vulnerable parts of the body.
6. Always have first-aid information and supplies available.
7. Call a physician and/or an emergency medical technician immediately. Let the burns
medicate by a medic immediately.
Measures in case of fire
1. Please heed that not covered hot parts of the engine and molten hot melt may cause
heavy burns. Risk of burns!
2. Work very carefully with molten hot melt. Keep in mind, that already jelled hot melt can
be very hot, too.
3. When working near a hot melt application system, always wear safety shoes, heat-
resistant protective gloves, safety goggles and protective clothes that cover all
vulnerable parts of the body!
Measures in case of fire:
Wear safety shoes, heat-resistant protective gloves, safety goggles and protective
clothes that cover all vulnerable parts of the body.
Firefighting - burning hot melt:
Please keep attention to the safety data sheet given by the adhesive manufacturer.
EXTINGUISH FIRE
Appropriate extinguishing agents:
Foam extinguisher, Dry powder, Spray, Carbon dioxide (CO2), Dry sand.
For safety reasons not appropriate extinguishing agents: None.
Firefighting - burning electrical equipment:
Appropriate extinguishing agents:
Carbon dioxide (CO2), Dry powder.

ITW Dynatec
Chapter 2
Safety Instructions
Page 16 UFD Applicator, Manual 40-43, Rev. 6.16
Keep attention to environmental protection standards
1. When working on or with the unit, the legal obligations for waste avoidance and the
duly recycling / disposals have to be fulfilled.
2. Keep attention, that during installations, repairs or maintenance matters hazardous
to water, like adhesive / adhesive scrap, lubricating grease or oil, hydraulic oil,
coolant and cleaner containing solvent not pollute the ground or get into the
canalization!
3. These matters have to be caught, kept, transported and disposed in appropriate
reservoirs!
4. Dispose these matters according to the international, national and regional
regulations.

Chapter 3
Description and Technical Specs
ITW Dynatec
UFD Applicator, Manual 40-43, Rev. 6.16 Page 17
Chapter 3
Description and Technical Specs
3.1 Applicable Safety Regulations
Intended Use
The UFD Applicator may be used only to apply suitable materials, e.g. adhesives. When
in doubt, seek permission from ITW Dynatec.
If the unit is not used in accordance with this regulation, a safe operation cannot be
guaranteed.
The operator - and not ITW Dynatec - is liable for all personal injury or property damages
resulting from unintended use!
Intended use includes, that you
•read this documentation,
•heed all given warnings and safety instructions, and
•do all maintenance within the given maintenance rates.
Any other use is considered to be unintended.
Unintended Use, Examples
The UFD Applicator may not be used under the following conditions:
•In defective condition.
•In a potentially explosive atmosphere.
•With unsuitable operating/processing materials.
•When the values stated under Specifications are not complied with.
The UFD Applicator may not be used to process the following materials:
•Toxic, explosive and easily flammable materials.
•Erosive and corrosive materials.
•Food products.
Residual Risks
In the design of the UFD Applicator, every measure was taken to protect personnel from
potential danger. However, some residual risks cannot be avoided.
Personnel should be aware of the following:
•Risk of burns from hot material.
•Risk of burns from hot Applicator components.
•Risk of burns when conducting maintenance and repair work for which the system
must be heated up.
•Risk of burns when attaching and removing heated hoses.
•Material fumes can be hazardous. Avoid inhalation. If necessary, exhaust material
vapors and/or provide sufficient ventilation of the location of the system.
•Risk of pinching parts of the body at running parts of the unit (pumps, motors, rolls or
others).
•The safety valves may malfunction due to hardened or charred material.

ITW Dynatec
Chapter 3
Description and Technical Specs
Page 18 UFD Applicator, Manual 40-43, Rev. 6.16
Technical changes
Any kind of technical changes having impact to the security or the operational liability of
the system should only be done by written agreement of ITW Dynatec. Suchlike changes
made without given a corresponding written agreement will lead to immediate exclusion
of liability granted by ITW Dynatec for all direct and indirect subsequent damages.
Using foreign components
ITW Dynatec takes no responsibility for consequential damages caused by using foreign
components or controllers that have not been provided or installed by ITW Dynatec.
ITW Dynatec does not guarantee that foreign components or controllers used by the
operating company are compatible to the ITW Dynatec-system.
Setting-up operation
We recommend asking for an ITW Dynatec-service technician for the setting-up
operation, to ensure a functioning system. Let yourself and the people working with or
working on the system be introduced to the system on this occasion.
ITW Dynatec takes no responsibility for damages or faults caused by any untrained
personal.

Chapter 3
Description and Technical Specs
ITW Dynatec
UFD Applicator, Manual 40-43, Rev. 6.16 Page 19
3.2 Description of UFD Spray Applicator
Description
ITW Dynatec’s UFD Spray Applicators are air-operated, single or multi-module hot melt
adhesive applicator assemblies with integrated basket filters, which prevent particulate
matter from obstructing flow through the heads.
The Applicator is heated by replaceable cartridge heating elements which are controlled
by an integrated sensor and electronic control. Each model can be configured for ITW
Dynatec’s DynaControl, MCV or Upgrade control schemes or for Allen-Bradley PLC
controls. Pressure transducer ports are standard features for all Applicators. A choice of
adhesive inlets and an angled filter nut allows either vertical or horizontal spray.
Four standard UFD models supporting up to six modules, are available, ranging in width
from 50mm to 150mm (2” to 6”). Their design is metric.
Theory of Operation
Each Applicator features one or more modules (adhesive valve) mounted to a single
service block. Each module is opened and closed by air pressure (solenoid valve).
Springs are used to keep the stem closed when no air pressure is supplied to the head.
The rate of adhesive flow from the applicator is determined by the adhesive pressure
applied by the Adhesive Supply Unit’s (ASU’s) pump, the nozzle type and the stem stroke
adjustment.
As shown in the illustration below, the heated adhesive supply hose may be connected at
the rear of the applicator or at the top. Adhesive flows from the hose into the service
block, through the filter and then to the module. Air pressure (Control Air) opens the
module, allowing adhesive to flow through the module’s nozzle.
Adapters are available to allow industry-standard pressure transducers (1/2-20 thread) to
be connected to monitor adhesive pressure within the service block.
On the UFD spray models, an air preheater is located below the service block. The
preheater supplies heated air (Process Air), used to fiberize the adhesive streams, to the
UFD modules. The air preheater is thermally isolated from the service block and its
temperature is controlled independently.
The adhesive pressure in the system is influenced by the following parameters:
•Temperature and viscosity of the adhesive
•Size and speed of the Adhesive Application Unit’s (ASU’s) pump
•Cross-section and length of the adhesive hoses
•Adjusted adhesive pressure at Applicator (if adjustable pressure relief valve)
•Nozzle type
See illustration typical parts of UFD Applicator on next page.
Nozzles compatible with UFD Applicator:
Two different UFD nozzles (Omega and Random) are available to fiberize the
adhesive streams:
UFD Omega:
UFD Random:

ITW Dynatec
Chapter 3
Description and Technical Specs
Page 20 UFD Applicator, Manual 40-43, Rev. 6.16
Illustration: Standard UFD Spray Applicator
Filter Cap
Glue Inlet
Alternate Hose
Inlet
Process Air Inlet
Air Preheater
Fiberizing Nozzle
Piston
Accessory Port
UFD Module
Control Air Inlet
Electrical
Connection
Alternate Glue
Inlet
Mounting screw
Nozzle
Filter
Basket
O-ring
Filter Nut
Lock
Nut
Optional Drain
(Purge) Valve
Stroke Adjustment Screw
Table of contents
Other ITW Dynatec Paint Sprayer manuals
Popular Paint Sprayer manuals by other brands
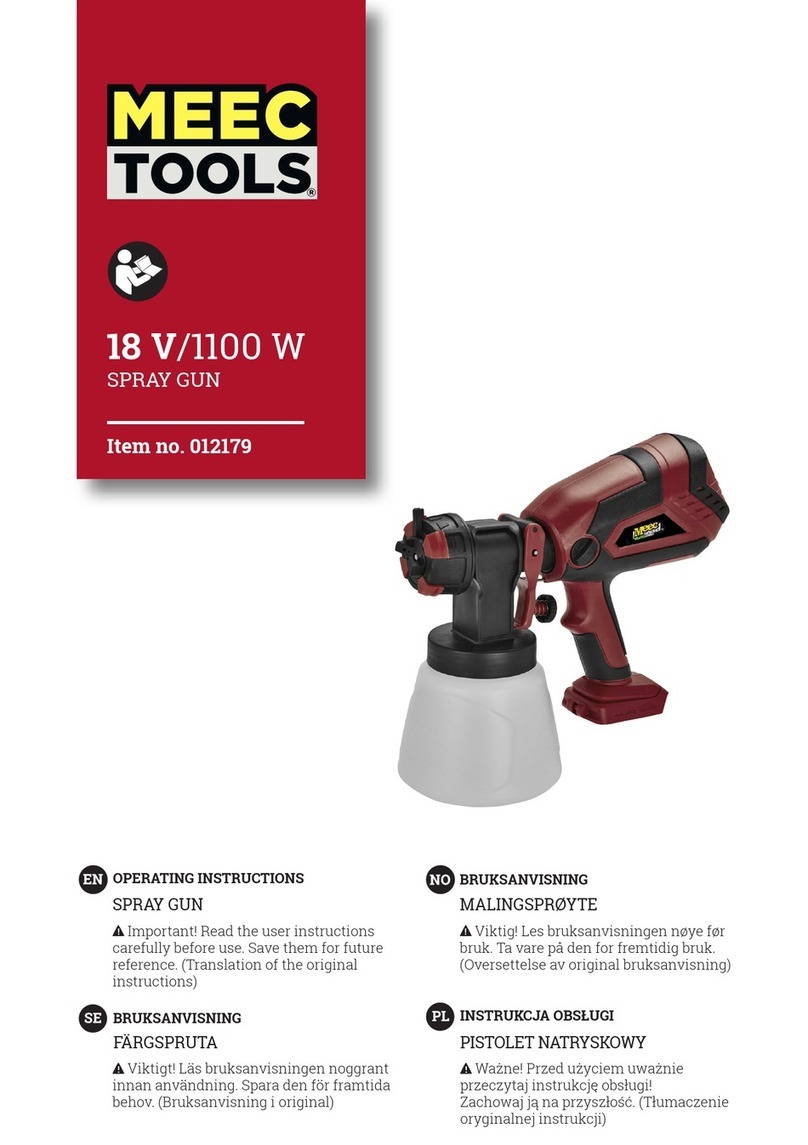
Jula
Jula Meec tools 012179 operating instructions

Badger Air-Brush
Badger Air-Brush 150 Instruction book
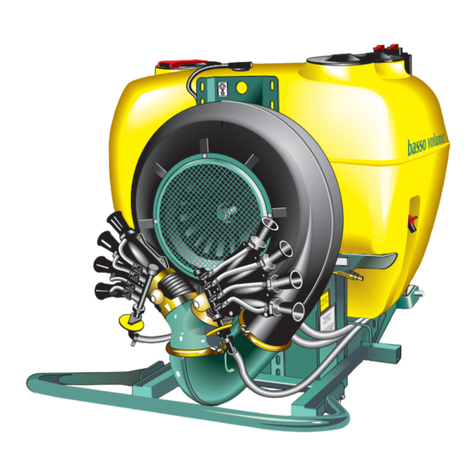
Cima
Cima PLUS Operation and maintenance instructions

Mesto
Mesto 3598BM Instructions for use

Enduraplas
Enduraplas ICEMASTER LIQUID MASTER T Series owner's manual
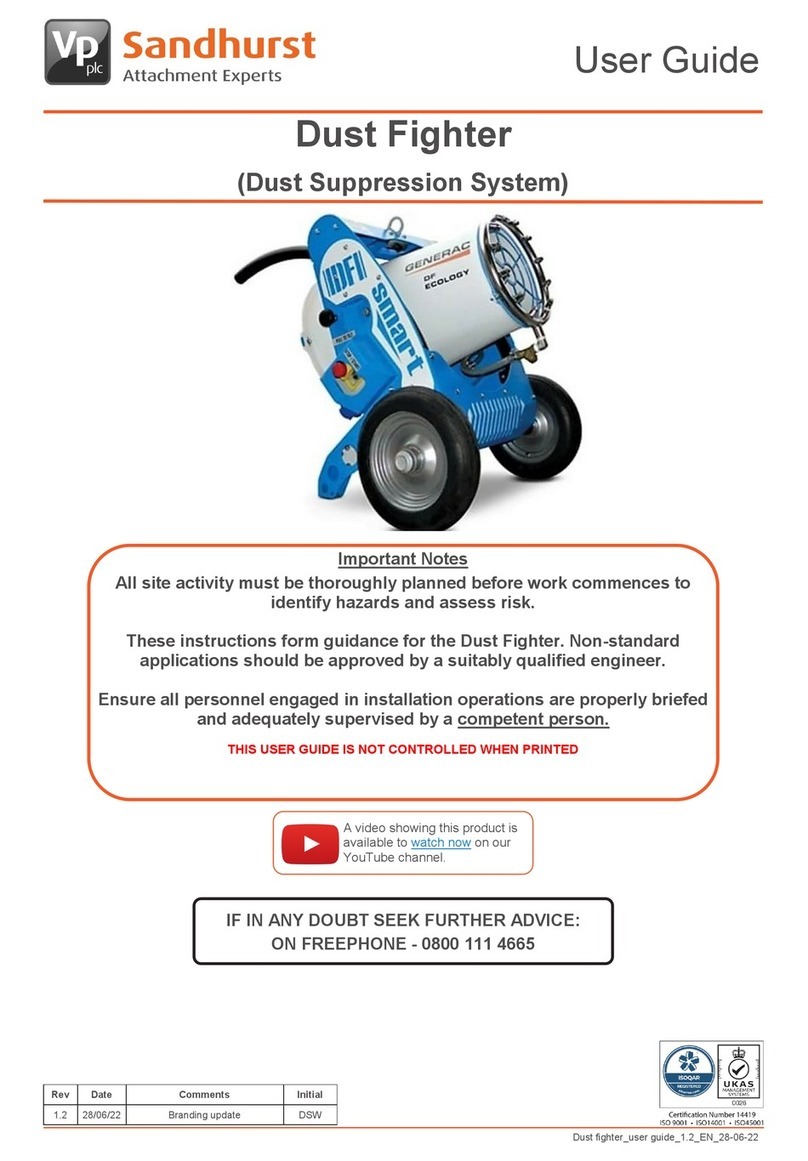
Generac Power Systems
Generac Power Systems Dust Fighter DF Smart user guide