Iveco Motors Cursor 13 Series User guide

USE AND MAINTENANCE
USO E MANUTENZIONE
UTILISATION ET ENTRETIEN
BETRIEB UND WARTUNG
USO Y MANTENIMIENTO
MARINE ENGINES CURSOR 13 SERIES
Publication edited by
Marketing - Adv. & Promotion
Print L31900013 - 12/05

1
ENGLISH
CURSOR 13 SERIES
C13 ENT M50
C13 ENT M77
USE AND MAINTENANCE
FOREWORD
Thank you for choosing IVECO MOTORS and congratulations for
your choice of engine.
Before carrying out any operation involving the engine and its
equipment, please read carefully the instructions contained in this
manual. Compliance with them is the best way to guarantee a perfect
and durable operation of your engine.
The contents of this manual only refer to the standard configuration
of the engine and the pictures are given only as an indication. Some
instructions provided describe the sequence to be applied in order to
obtain engine's and relevant equipment's expected performance. In
some cases they depend upon the configuration of controls and fittings
of the boat on which the engine is installed. Although they may differ
from the contents of this manual, please refer to yard instructions or
to a specific manual thereof.
The information contained herein are updated as of the date of their
publishing.
The Manufacturer reserves the right of applying changes without
notice and at any time, for technical or commercial reasons and in
order to make engines compliant with the law requirements of the
different countries.
The Manufacturer waives any liability for any errors or omissions.
The IVECO MOTORS Customer Service Network competence and
professionalism of the Customer Service Network is always available
wherever you are.

2
TABLE OF CONTENTS Page
GENERAL. . . . . . . . . . . . . . . . . . . . . . . . . . . . . . . . . . . . . . . . . .3
Guarantee . . . . . . . . . . . . . . . . . . . . . . . . . . . . . . . . . . . . . . . . . . . . . .3
Spare parts. . . . . . . . . . . . . . . . . . . . . . . . . . . . . . . . . . . . . . . . . . . . . .3
Liabilities. . . . . . . . . . . . . . . . . . . . . . . . . . . . . . . . . . . . . . . . . . . . . . . .3
Safety . . . . . . . . . . . . . . . . . . . . . . . . . . . . . . . . . . . . . . . . . . . . . . . . . .3
C13 ENT M50 engines technical data . . . . . . . . . . . . . . . . . . . . . . .4
C13 ENT M77 engines technical data . . . . . . . . . . . . . . . . . . . . . . .6
Labels . . . . . . . . . . . . . . . . . . . . . . . . . . . . . . . . . . . . . . . . . . . . . . . . . .8
USE . . . . . . . . . . . . . . . . . . . . . . . . . . . . . . . . . . . . . . . . . . . . . . .9
Preliminary testing. . . . . . . . . . . . . . . . . . . . . . . . . . . . . . . . . . . . . . . .9
Starting and stopping the engine . . . . . . . . . . . . . . . . . . . . . . . . . . . .9
Starting and stopping the engine from an analog instrument
panel . . . . . . . . . . . . . . . . . . . . . . . . . . . . . . . . . . . . . . . . . . . . . . . . .10
Recognizing alarm statuses . . . . . . . . . . . . . . . . . . . . . . . . . . . . . . .13
Starting and stopping the engine from digital instrument panel .14
Recognizing alarm statuses . . . . . . . . . . . . . . . . . . . . . . . . . . . . . . .16
Engine management from C13 ENT M50 relay box . . . . . . . . . .19
Engine management from C13 ENT M77 relay box . . . . . . . . . .20
For a correct use of the engine. . . . . . . . . . . . . . . . . . . . . . . . . . . .21
Special warnings . . . . . . . . . . . . . . . . . . . . . . . . . . . . . . . . . . . . . . . .22
Running-in . . . . . . . . . . . . . . . . . . . . . . . . . . . . . . . . . . . . . . . . . . . . .23
Refuelling . . . . . . . . . . . . . . . . . . . . . . . . . . . . . . . . . . . . . . . . . . . . . .24
INSPECTIONS AND MAINTENANCE . . . . . . . . . . . . . . . . .25
Maintenance staff . . . . . . . . . . . . . . . . . . . . . . . . . . . . . . . . . . . . . . .25
Accident prevention . . . . . . . . . . . . . . . . . . . . . . . . . . . . . . . . . . . . .25
Frequency . . . . . . . . . . . . . . . . . . . . . . . . . . . . . . . . . . . . . . . . . . . . .26
Prescriptions . . . . . . . . . . . . . . . . . . . . . . . . . . . . . . . . . . . . . . . . . . .28
How to. . . . . . . . . . . . . . . . . . . . . . . . . . . . . . . . . . . . . . . . . . . . . . . .28
Moving The Engine . . . . . . . . . . . . . . . . . . . . . . . . . . . . . . . . . . . . . .39
Exhaust parts dismissal . . . . . . . . . . . . . . . . . . . . . . . . . . . . . . . . . . .39
LONG ENGINE INACTIVITY. . . . . . . . . . . . . . . . . . . . . . . . .40
Engine Preparation For Long Inactivity Periods. . . . . . . . . . . . . . .40
Commissioning After An Extended Period Of Inactivity . . . . . . .40
Instructions for first startup or after an extended period of inactivity41
Page
ENGINE FAILURES . . . . . . . . . . . . . . . . . . . . . . . . . . . . . . . . . 42
EMERGENCY ON BOARD . . . . . . . . . . . . . . . . . . . . . . . . . . 43
APPENDIX . . . . . . . . . . . . . . . . . . . . . . . . . . . . . . . . . . . . . . . . . .
Oil viscosity compared to ambient temperatures.
On board panels requirements.

3
ENGLISH
GENERAL
GUARANTEE
In order to obtain the engine best performance and to make use of
IVECO MOTORS guarantee it is necessary to strictly observe the
instruction contained in this manual. Failure to do so may cause the
guarantee to become invalid.
SPARE PARTS
In order to maintain the original integrity of the engine, it is essential to
use only IVECO MOTORS genuine spare parts.
Using non genuine spare parts may cause the guarantee to decay and
waives any IVECO MOTORS liability for the entire life of the engine.
LIABILITIES
The Manufacturer's liability is subject to the execution of the control
and maintenance interventions contained and described in this manual,
the performance of which shall be duly proven. Should any
extraordinary maintenance intervention be required, it shall be carried
out by qualified staff at IVECO MOTORS authorized shop, using the
specific instruments and equipment.
SAFETY
The following information is provided in order to bring the attention
to the use of the engine in order to prevent any damage to people and
properties arising out of misconduct.
Engines should be used exclusively for the applications stated by
the manufacturer.
Any tampering, modifications, or use of non-original par ts may
jeopardize the safety of service personnel and boat users;
absolutely avoid any change to cables or units of the engine or
to connect it to foreign electric networks.
Pay attention to the moving parts of the engine, to those with high
temperature and to the circuits with pressurized fluids, as the
electric equipment is subject to voltage and electric currents.
Engine exhaust gases can be dangerous for health.
Engine displacement should take place with suitable lifting means,
using the special eyelets provided.
Do not commission the engine before having met the safety
requirements provided for the boat on which is has been installed
and observe local rules and regulations.
Any required intervention in order to improve use and
conservation of the engine should be carried out exclusively by
IVECO MOTORS approved staff.
See INSPECTIONS AND MAINTENANCE for further safety
reccomandations.

4
C13 ENT M50 ENGINE TECHNICAL DATA
The technical acronym and the serial number are specified on the
nameplate which - based on the model - can be found on different
parts of the engine: flywheel casing, tappet cover, coolant pan.
(*)Flywheel net power compliant with ISO 3046-1 standard. Testing
conditions: T 25°C; atmospheric pressure 100 kPa; relative
humidity 30%.
Acronym C13 ENT M50
Engine family F3B
Cycle 4-Stroke Diesel
Number and arrangement
of cylinders 6, in line
Stroke boring 135 x 150 mm
Total diplacement 12,800 cm3
Air supply Boosted and post-cooled
(TCA or TAA)
Injection method Direct EUI with electronic management
Engine rotation direction Counterclockwise
(from flywheel side)
Weight without liquids 2,965.22 lb
Electrical system 24 V
Battery/ies
capacity
breakaway current
120 Ah or higher
900 A or higher
Available ratings (*) C13 ENT M50
C 382 kW (520 CV) @ 2000 rpm
D 368
kW (520 CV) @ 2000 rpm
WARNING
It is strictly forbidden to alterate the above mentioned features and
more specifically to change the information stored in the electronic
units of the injection system or the engine and relevant fitting features.
Any non observance of the above shall null any warranty and IVECO
MOTORS liability.

5
ENGLISH
CURSOR C13 ENT M50 Engine
1. Air filter - 2. Fuel filters switch lever (opt.) - 3. Fuel filter - 4. Air-sea water
heat exchanger - 5. Sacrificial anode - 6. Sacrificial anode - 7. Coolant - sea
water tube bundle heat exchanger - 8. Sea water drain plug - 9 Pulleys and
joints for power take-offs coupling (opt.) - 10. Auxiliary elements tensioning
belt - 11. Alternator location - 12. Inverter oil heat exchanger (opt.) - 13. Sea
water pump intake - 14. Electrical starter motor - 15. Seat for flywheel tool
insertion - 16. Engine fuel intake pipe - 17. Fuel pipe to tank.
CURSOR C13 ENT M50 Engine
1. Location of thermostatic valve - 2. Coolant refill cap - 3. Lifting padeye - 4.
Oil filters - 5. Lubricating oil dipstick - 6. Lubricating oil refill cap - 7. Lubrication
oil hand pump - 8. Lifting padeye - 9. Location of oil steam filter and filter
clogging sensor - 10. Chimney exhaust gas (pot.) - 11. Accelerator
potentiometer lever - 12. Electronic control unit - 13. Lubricating oil heat
exchanger - 14. Lubricating oil drain plug- 15. Coolant drain plug - 16. Auxiliary
items belt tensioner casing.
05_101_C
05_102_C

6
C13 ENT M77 ENGINE TECHNICAL DATA
The technical acronym and the serial number are specified on the
nameplate which - based on the model - can be found on different
parts of the engine: flywheel casing, tappet cover, coolant pan.
(*)Flywheel net power compliant with ISO 3046-1 standard. Testing
conditions: T 25 °C; atmospheric pressure 100 kPa; relative
humidity 30%.
Acronym C13 ENT M77
Engine family F3B
Cycle 4-Stroke Diesel
Number and arrangement
of cylinders 6, in line
Stroke boring 135 x 150 mm
Total displacement 12,800 cm3
Air supply Boosted and post-cooled
(TCA or TAA)
Injection method Direct EUI with electronic management
Engine rotation direction Counterclockwise
(from flywheel side)
Weight without liquids 1380 kg
Electrical system 24 V
Battery/ies
capacity
breakaway current
120 Ah or higher
900 A or higher
Available ratings (*) C13 ENT M77
A1 567 kW (770 CV) @ 2300 rpm
A2 515 kW (700 CV) @ 2300 rpm
B 442 kW (600 CV) @ 2300 rpm
C 397 kW (540 CV) @ 2300 rpm
WARNING
It is strictly forbidden to modify the above mentioned features and
more specifically to change the information stored in the electronic
units of the injection system or the features of the engine and relevant
fittings. Any non observance of the above shall null any warranty and
IVECO MOTORS liability.

7
ENGLISH
CURSOR C13 ENT M77 Engine
1. Air
filter - 1. Fuel filters switch lever (opt.) - 3. Fuel filter - 4. Air-sea water
heat exchanger - 5. Sacrificial anode - 6. Sacrificial anode - 7. Coolant - sea
water tube bundle heat exchanger - 8. Sea water drain plug - 9 Pulleys and
joints for power take-offs coupling (opt.) - 10. Auxiliary elements tensioning
belt - 11. Alternator location - 12. Inverter oil heat exchanger (opt.) - 13. Sea
water pump intake - 14. Electrical starter motor - 15. Seat for flywheel tool
insertion - 16. Engine fuel intake pipe - 17. Fuel pipe to tank.
CURSOR C13 ENT M77 Engine
1. Location of thermostatic valve - 1. Coolant refill cap - 2. Lifting
padeye - 3. Oil filters - 4. Lubricating oil dipstick - 5. Lubricating oil refill
cap - 6. Lubrication oil hand pump - 7. Lifting padeye - 8. Location of
oil steam filter and filter clogging sensor - 9.
Chimney exhaust gas (pot.) -
11. Accelerator potentiometer lever - 12. Electronic control unit - 13.
Lubricating oil heat exchanger - 14. Lubricating oil drain plug- 15. Coolant
drain plug - 16. Belt tensioner carenatura.
05_103_C
05_104_C

8
LABELS
Below you can find the explanation of the caution labels located on
the engine.
NOTE: Labels with an exclamative point highlight a potential
danger.
Lifting point (engine only).
Fuel refill plug
(on tank, if available).
Lubricant refill plug.
Lubricating oil dipstick.
Burn hazard:
Pressurised hot water expulsion.
Burn hazard:
High temperature parts.
Fire hazard:
Fuel presence.
Hazard of collision and contact
with moving parts:
Presence of fans, pulleys, belts or other.

9
ENGLISH
USE
PRELIMINARY TESTING
Before each engine startup:
Make sure that the sea water intake valve is open. Dry operation of
the pump would cause in few seconds irreparable damages to the
internal rotor.
Check technical fluids level (fuel, engine oil and coolant).
STARTING AND STOPPING THE ENGINE
For boats equipped with instrument panel not
manufactured by IVECO MOTORS
Startup and stop procedures described below are provided assuming
a genuine IVECO MOTOR instrument panel is assembled on board.
Should the boat be equipped with a customized dashboard which has
been manufactured at the Yard or by the Boat builder, such
procedures may change based on the panel's specific features. In such
cases please observe the Yard's startup/stop sequences and read the
indication instruments as specified in the relevant documentation.
Engines equipped with pre-lubrication electric
system
The pre-lubrication feature is started by acting on the power switch of
the electrical system and the relevant warning light lits up.
The engine startup sequence described in the following pages shall
take place after the required pre-lubrication time has elapsed and the
warning light is turned off.
WARNING!
Before starting up the engine make sure no comburent
vapour or gas is in the engine room.

10
STARTING AND STOPPING THE ENGINE
FROM AN ANALOG INSTRUMENT PANEL
Startup procedure from IVECO MOTORS main
panel (provided upon request)
Make sure that the electric switch with ENGINE ROOM - BRIDGE label
on the Relay box unit, (usually located in the engine room) is turned to
BRIDGE, then proceed as follows:
1. Lift the key switch safety cover (8), insert the key and turn it to the
right, to 8B position.
2. Check that the analog instruments provide acceptable reading with
the values of the relevant physical parameters (temperature,
battery voltage and oil pressure).
3. Wait for the acoustic alarm to stop and that the alarm warnings (5)
on the signaling module are switched off (except for "alternator
anomaly" and "oil low pressure"). At the same time check that
testing of indicators is successful (see relevant section as regards
test reading and module indication instructions).
4. Turn the key to 8C position and realeas it without accelerating
when the engine has started.
5. Check that the analog instruments provide acceptable reading with
the new values of the relevant physical parameters (temperature,
battery voltage and oil pressure).
6. In case startup fails, you can resume startup position only after
releasing the key and after turning the switch 8A to the stop
position.
1. Coolant temperature indicator - 2. Tachometer and hour counter -
3. Voltmeter - 4. Horn - 5. Alarms and signaling module 6. Engine oil
pressure indicator - 7. Panel instruments light switch - 8. Key switch for
engine startup/stop - 9. Engine stop push button - 10. Horn silencing
push button.
1
2
3
4
5
6
7
89
10
04_354_N
8A 8B
8C
04_356_N
Switch key detail

11
ENGLISH
Startup procedure from IVECO MOTORS
secondary panel or fly-bridge (provided upon request)
1Enable the secondary panel operation by turning the key
switch on the main panel to 8B position (see instructions
and procedure described in the previous paragraph).
2. Wait for the acoustic alarm to stop and that the warning lights (5)
on the signaling module are switched off (except for "alternator
recharge" and "oil low pressure"). At the same time check that
testing of indicators is successful (see relevant section as regards
test reading and module indication instructions).
3. Press the green push button (5) and release it upon startup.
4. Check that the revolution indicator reading is acceptable.
1. Tachometer and hour counter - 2. Horn - 3. Alarms and signaling
module - 4. Horn silencing push button - 5. Engine Start push button -
6. Engine stop push button.
WARNING
For the onboard control panels to fully perform their relevant
operations during navigation, it is essential that the engine startup is
done only after the completion of warning lights and horn testing.
5
1 3
2
6
4
04_355_N

12
Engine stop
Before stopping the engine it is recommended to keep it running at
idle and unloaded for few minutes; this will allow for a uniform
reduction of temperature and avoid harmful thermal shocks.
A. To stop the engine from IVECO MOTORS main panel, turn the
key switch to the stop position 8A or act on any similar control if
your boat is equipped with a customized dashboard.
B. To stop the IVECO MOTORS secondary panel press the red push
button (6) located on it.
To stop the IVECO MOTORS main panel for the engines equipped
with "in eccitazione" device (available upon request or prescribed by
certification authorities), press the red push button(9).
To restart the engine from the main panel:
1. Turn the key switch to the stop position 8A to reset any panel
operation enabled.
2. Proceed as shown.
To restart the engine from the secondary panel:
1. Make sure the panel is enabled (key switch on the main panel
turned to 8B).
2. Press the green push button (5) and release it when it has started,
making sure that the revolution indicator reading is acceptable.

13
ENGLISH
RECOGNIZING ALARM STATUSES
IVECO MOTORS onboard panels equipped with analog instruments
include an electronic module with indicator lights and interface circuits,
timing and saving of alarms.
The figure shows the module quadrant and the legend contains the
meaning of the alarm pictorial corresponding to each light indicator; in
some engine type and relevant fitting are not equipped with all of the
features mentioned herein.
Moreover these instructions may change based on the technical
features provided by the boat manufacturer.
Operation
By rotating the key switch to 8B position the alarms and signaling
module performs a 5 seconds efficiency test of all light indicators,
except for those concerning “Pre-lubrication”, “Pre-post heating”,
“EDC system fault”, and the horn beeps.
The beep may be silenced before the end of the test, by pushing the
relevant button.
During the startup phase and for the next 15 seconds, any alarm
function is inhibited; after such time interval each alarm condition
detected by sensors on the engine causes the relevant indicator to
blink and a simultaneous sound signal. The horn silencing obtained by
pressing the relevant push button causes the non-blinking indicator to
turn on and saves the alarm until the next engine stop.
1. Maximum allowed speed (on request) - 2. Water in the fuel pre-
filter- *3. Engine coolant low level - 4. Alternator anomaly - *5. Oil
filter clogging - *6. Oil vapors filter clogging - *7. Pre-lubrication
running - 8. Air filter clogging - *9. Fuel filter clogging - 10. Coolant high
temperature - 11. Oil low pressure - *12. Pre-post heating - 13. EDC
injection system fault.
*Alarm features not available with standard fitting.
12 12
11101334
5 6 8 9
7
04_234_N

14
STARTING AND STOPPING THE ENGINE
FROM A DIGITAL INSTRUMENT PANEL
(C13 ENT M50 engine only)
Startup procedure from IVECO MOTORS main
panel (provided upon request)
Make sure that the electric switch with ENGINE ROOM - BRIDGE label
on the Relay box unit, (usually located in the engine room) is turned to
BRIDGE, then proceed as follows:
1. Lift the key switch safety cover (8), insert the key and turn it to the
right, to 8B position.
2. Check that the analog instruments provide acceptable reading with
the new values of the relevant physical parameters.
3. Wait for the acoustic alarm to stop and that the warning lights (5)
on the signaling module are switched off (except for "alternator
anomaly" and "oil low pressure"). At the same time check that
testing of indicators is successful (see relevant section
RECOGNIZING ALARM STATUSES).
4. Turn the key to 8C position and release it without accelerating
when the engine has started.
5. Check that the analog instruments provide acceptable reading with
the new values of the relevant physical parameters (temperature,
battery voltage and oil pressure).
6. In case startup fails, you can resume startup position only after
releasing the key and after turning the switch 8A to stop position.
1. Engine coolant temperature indicator - 2. Lubrication circuit
pressure indication - 3. Service and alarm signals - 4. Revolution
counter - 5. Air booster pressure indicator - 6. Voltmeter - 7.
Alphanumeric display - 8. Engine start/stop key switch - 9. Accessory
functions programming key - 10. Additional information slide selection
key - 11. “Programmed maintenance” reset key - 12. Horn silencer -
13. Horn.
1
2
4
6
5
8
91112
13
3 3
10
7
04_357_N
8A 8B
8C
04_356_N
Switch key detail

15
ENGLISH
Startup procedure from IVECO MOTORS
secondary panel orfly-bridge (provided upon request)
1. Enable the secondary panel operation by turning the key switch on
the main panel to 8B position (see instructions described in the
previous paragraph).
2. Wait for the acoustic alarm to stop and that the warning lights (5)
on the signaling module are switched off (except for "alternator
anomaly" and "oil low pressure"). At the same time check that
testing of indicators is successful (see relevant section
RECOGNIZING ALARM STATUSES).
3.
Press the green
START
(11) push button and release it when the
engine has started
. Check that instruments and analogic reading are
acceptable.
1. Engine coolant temperature indicator - 2. Lubrication circuit
pressure indication - 3. Service and alarm signals- 4. Revolution
counter - 5. Air booster pressure indicator - 6. Voltmeter - 7.
Alphanumeric display - 8. Engine stop button - 9. Additional
information slide selection key - 10. Horn silencer - 11. Engine start
button.
1
2
6
5
3 3
4
7
1011 9 8
04_358_N

16
Engine stop
Before stopping the engine it is recommended to keep it running at
idle and unloaded for few minutes; this will allow for a uniform
reduction of temperature and avoid harmful thermal shocks.
A. From the IVECO MOTORS main panel: rotate the key
switch to the stop 8A position.
B. From the IVECO MOTORS secondary panel: press the red
STOP push button (8) located on it.
To restart the engine from the main panel:
1. Turn the key switch to the stop position 8A to reset any panel
operation enabled.
2. Proceed as shown in the relevant paragraph.
To restart the engine from the secondary panel:
1. Make sure the panel is enabled (key switch on the main panel
turned to 8B).
2. Press the green START (11) push button and release it when the
engine has started. Check that instruments and analogic reading are
acceptable.
RECOGNIZING ALARM STATUSES
The following the legend contains the meaning of the alarm pictorial
corresponding to each light indicator on the main and secondary panel;
in some engine type and relevant fitting are not equipped with all of the
features mentioned herein. Moreover these instructions may change
based on the technical features provided by the boat manufacturer.
* Alarm features not available with standard fitting.
* Clogging
oil vapor filter
Alternator
anomaly
Low oil
pressure
High temperature
of
coolant
Overrun
*Low level
of
coolant
EDC engine control
system failure
* Clogging
air filter
Maintenance interval
expiry
* Clogging
oil filter
* Pre-lubrication
running
* Pre-post
heating
* Clogging
fuel
filter
Water
in the fuel
filter
04_359_N

17
ENGLISH
Operation
By rotating the key switch to 8B position the module performs a 5
seconds efficiency test of all light indicators, except for those
concerning “Pre-lubrication”, “Pre-post heating”, “EDC system fault”,
and the horn beeps. The beep may be silenced before the end of the
test, by pushing the relevant button.
During the startup phase and for the next 15 seconds, any alarm
function is inhibited; after such time interval each alarm condition
detected by sensors on the engine causes the relevant indicator to
blink and a simultaneous sound signal. The sound alarm silencing
obtained by pressing the relevant push button causes the non-blinking
indicator to turn on and saves the alarm until the next engine stop.
Alfanumeric display
The information provided by this indicator are:
• engine revolution speed
• total hours of operation (see note A)
• exhaust gases temperature (upon request)
• instant fuel consumption (see note B)
To select the requested information, press the "Slide selection" push
button available on the main and secondary panel.
Detail of the main panel
7. Alphanumeric display - 9. Accessory functions programming button -
10. Accessory information slide selector - 11. “Programmed
maintenance” reset button - 12. Horn silencer.
(A)The electronics inside the panel is programmed in order to
combine the hours of operation to the release of the warning when
the ordinary maintenance hours limit has been reached. This
feature requires that after each maintenance intervention, the
count is reset from the main panel as follows:
- Press and hold the "Prog" (9) and "Slide selection" (10) buttons,
turn the key switch from 8A position to 8B and wait for the display
to show the previous data set (ex.: 600 hours). Release the buttons
and press only once the "Prog" button (9) to restart the new count.
9
7
12 11 10
04_360_N

18
In case the information set does not correspond to what provided for
the type of oil used (see REFUELLING and FREQUENCY), proceed
as follows:
- After having displayed the hour information previously set, release
the push buttons and repeatedly press only the "Slide selection"
(10) button until the required information blinks (as detailed in
FREQUENCY section), then press "Prog" (9) to confirm the
information and start a new count.
(B)The information regarding the immediate fuel consumption require
the correct programming of the maximum information entered
relating to the engine performances. To check proceed as follows:
- Press and hold the "Prog" key (9) until the display reads the
maximum value entered (ex.: 195 mg/trk), then release it and
compare the information with those provided in the tale below.
- In case it does not correspond, you can change it by repeatedly
pressing the "Slide selection" (10) button until the required one it
displayed (blinking mode).
- Press and hold the “Prog” (9) button until the engine revolution
speed is displayed, meaning that the information has been saved.
In case of any mistake in the programming procedure, the display
reading will be "Pr. Err.". You will need to repeat the procedure.
C13 ENT M50
C13 ENT M77
Maximum power(CV) Maximum insertion (mg/strk)
520
500
Maximum power(CV) Maximum insertion (mg/strk)
770
700
600
540

19
ENGLISH
ENGINE MANAGEMENT FROM RELAY BOX
(C13 ENT M50 engine only)
The engine fitting includes a "Box relay" unit which is usually located
near the engine room and which provides management of the
following functions:
Start and stop.
Control post selection: bridge or engine room.
Revolution speed increasing and decreasing.
Self-diagnosis test (only for Customer Service Network).
1. Control post selection - 2. Start/stop control - 3. Manual accelerator -
4. Accelerator push button enabling (3) - 5. Blink code emission push
button - 6. EDC fault signaling led and blink code - 7. Diagnosis tool
connector.
Startup procedure
1. Turn the switch to 1ENGINE ROOM. The START-STOP (2) push
button nearby is enabled; this action disables any function of
on boardpanels located on the bridge and fly-bridge.
2. Press the 2push button to ENGINE START position and release it
upon startup.
Speed management procedure
1. Turn the 4 switch to PTO ON position;
2. To speed up: press and hold the 3button in the PTO+ position
until the required speed is reached, then release it.
3. To speed down: press and hold the 3button in the PTO- position
until the required speed is reached, then release it.
Once the required speed has been reached, it will be maintained until
the 4switch is turned to PTO OFF position or the engine is stopped.
%.').%
2//-
%.').%
34/0 04/
04/
/.
"2)$'% %.').%
34!24
04/ 04/
/&&
#(%#+
6 7
04_002_C
1 2 3 4 5
WARNING!
When the engine is rotating, do not operate the ENGINE
ROOM / BRIDGE switch.
This manual suits for next models
2
Table of contents
Other Iveco Motors Engine manuals
Popular Engine manuals by other brands
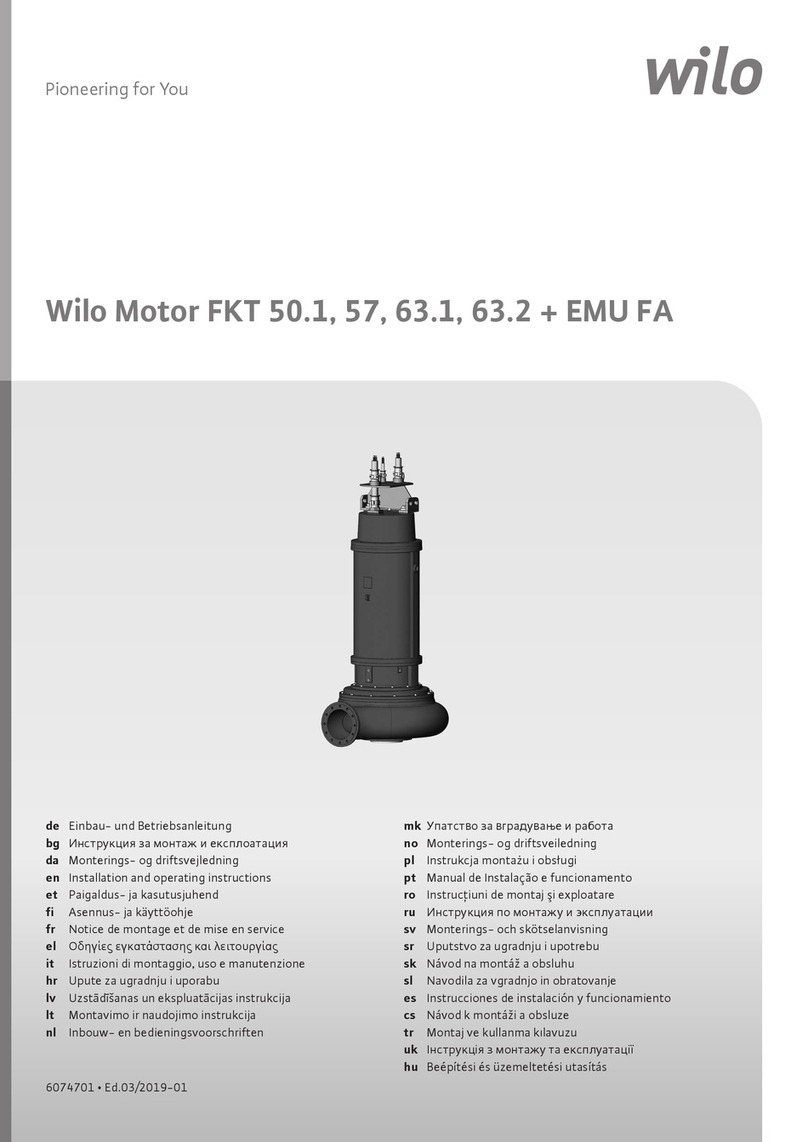
Wilo
Wilo FKT 50.1 Series Installation and operating instructions

Aerotech
Aerotech BM Series Hardware manual
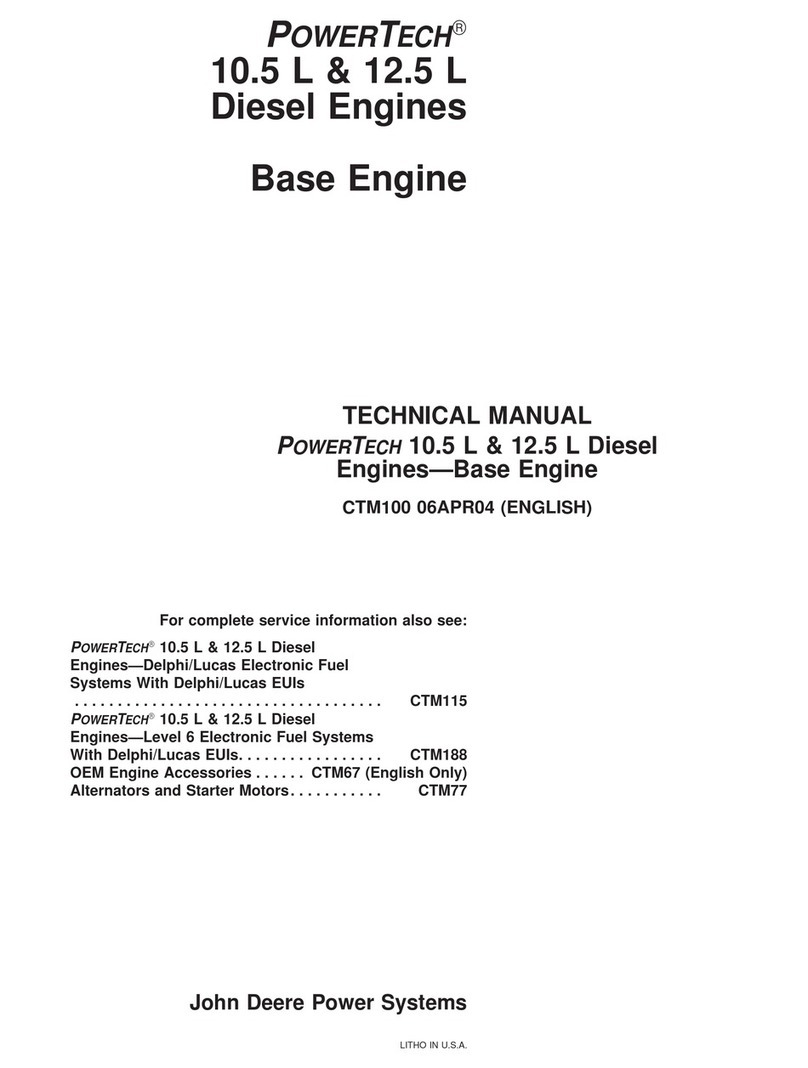
PowerTech
PowerTech 6105HF Technical manual

Hyundai Seasall
Hyundai Seasall S250S Installation & operation manual

Kohler
Kohler Courage SV710 Service manual
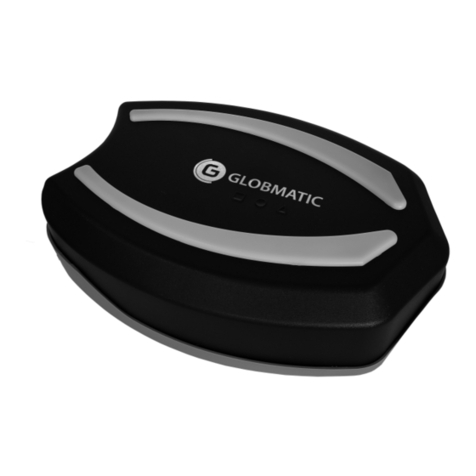
Globmatic
Globmatic FENIX II 650 User's and installer's manual