JAKA C Series Instructions for use

JAKA Robotics
Hardware User Manual
JAKA C Series
Original Instructions (en)
File Version: 3.2
Robot: C 5, C 7, C 12
Control Cabinet: CAB V2.1
A

II
Notice:
The definition of collaborative robots follows the ISO standards and relevant national standards to protect the
safety of operators. We do not recommend applying the robots directly to cases when the operating object is a
human. However, if there is a need for the robot to operate on a human, the robot needs to be equipped with a
safe, reliable, fully tested and certified safety protection system to protect the human, provided that the
personnel safety is fully assessed by the user or application developer.
The manual is the exclusive property of the JAKA Robotics Ltd. (hereinafter referred to as the “JAKA”) and
JAKA fully reserves its copyright and interpretation right. This manual and parts thereof must not be reproduced
or copied without JAKA’s written permission.
We will regularly revise the manual, and the content may be updated without notice. Please check the factual
product information carefully before reading this manual.
This manual is applicable to all products and/or services manufactured or provided by JAKA (hereinafter
referred to as the “products"). The information contained in the manual is provided "as is" and is subject to the
relevant laws and legislation. To the maximum extent permitted by law, this manual does not constitute any
form of express or implied representation or warranty of JAKA, neither constitute a guarantee of merchantability,
suitability for specific purposes, achievement of expected results, or non infringement of the products. JAKA
assumes no responsibility for any error or omission that may appear in this manual, or any accident or indirect
injury arising from the use of this manual and the products described therein. Before installing and operating
the product, read this manual carefully.
The pictures in this manual are for reference only.
If the robot body is transformed or disassembled, JAKA will not be responsible for after-sales services. JAKA
reminds users that they must use safety equipment when using and maintaining JAKA robots and must comply
with the safety terms.
Programmers of JAKA robots and designers and debugging personnel of robot systems must be familiar with
the way to program JAKA robots and install system applications.
Manual Instruction
This manual mainly includes the use safety precautions, mechanical and electrical interfaces, installation and
maintenance of the robot.
This manual is aimed at users who have received basic mechanical and electrical training, which will be more
helpful in the installation and operation of the robot.
More Information
For more product information, scan the QR code on the right to visit our
official website: www.jakarobotics.com.

III
Contents
Chapter 1 Safety Specification..............................................................................................................6
1.1 Introduction ....................................................................................................................................6
1.2 Warning Symbols ...........................................................................................................................6
1.3 Safety Precautions .........................................................................................................................6
1.4 General Warnings and Cautions....................................................................................................7
1.5 Liability and Risk ............................................................................................................................8
1.6 Usage.............................................................................................................................................8
1.7 Risk Assessment............................................................................................................................9
1.8 Pre-Use Assessment ...................................................................................................................10
1.9 Emergency Stop ..........................................................................................................................10
1.10 Movement without Electric Power................................................................................................10
1.11 Precautions for Transport and Handling ......................................................................................11
1.12 Labels...........................................................................................................................................11
Chapter 2 Safety Functions.................................................................................................................14
2.1 Stop Category ..............................................................................................................................14
2.2 Safety Stop Time and Distance....................................................................................................14
2.3 Safe Mode....................................................................................................................................14
2.4 Three-Position Enable Device (Optional) ....................................................................................15
Chapter 3 Quick Start...........................................................................................................................16
3.1 Overview of Robot Components ..................................................................................................16
3.2 Robot............................................................................................................................................16
3.2.1 End of the Robot...................................................................................................................17
3.2.2 Tool flange button and interface ...........................................................................................18
3.3 Control Cabinet and Control stick ................................................................................................18
3.4 Technical Specification.................................................................................................................20
Chapter 4 Mechanical Specification ...................................................................................................22
4.1 Robot Workspace.........................................................................................................................22
4.1.1 Size of the Robot ..................................................................................................................22
4.1.2 Size of the Control Cabinet...................................................................................................22
4.1.3 Robot Workspace .................................................................................................................23
4.1.4 Robot Rotation Direction.......................................................................................................25
4.2 Installation ....................................................................................................................................27
4.2.1 Installation Steps ..................................................................................................................27
4.2.2 Important Security Instructions .............................................................................................28
4.2.3 Installation of the Robot ........................................................................................................28
4.2.4 Installation of the End-effector ..............................................................................................31

IV
4.2.5 Maximum effective payload of the robot...............................................................................33
Chapter 5 Electrical Interface..............................................................................................................35
5.1 Introduction ..................................................................................................................................35
5.2 Electrical Warnings and Precautions ...........................................................................................35
5.3 Front Panel Interface of the Control Cabinet ...............................................................................36
5.3.1 Common Specifications for All Digital I/O .............................................................................38
5.3.2 Safety I/O Interface...............................................................................................................39
5.3.3 Digital Input (DI)....................................................................................................................40
5.3.4 Digital Output (DO) ...............................................................................................................41
5.3.5 Analog...................................................................................................................................42
5.3.6 High Speed Interface ............................................................................................................43
5.3.7 Remote Control Interface......................................................................................................43
5.4 Bottom Panel Interface of the Control Cabinet ............................................................................44
5.4.1 Power Adaptation..................................................................................................................45
5.4.2 Power Connection ................................................................................................................46
5.4.3 Robot Connection .................................................................................................................46
5.5 Tool Input and Output Interface....................................................................................................47
5.5.1 Definition of TIO External Interface ......................................................................................47
Chapter 6 Maintenance ........................................................................................................................52
6.1 Safety Instructions .......................................................................................................................52
6.2 Preservation of Components .......................................................................................................52
Chapter 7 Warranties ...........................................................................................................................54
7.1 Product Warranty .........................................................................................................................54
7.2 Disclaimer ....................................................................................................................................54
Appendix ...................................................................................................................................................55
Appendix 1: Stop Time and Distance......................................................................................................55
Appendix 2: Safety Function Table .........................................................................................................61

File Version: 3.2 5 / 62 JAKA C Series Hardware User Manual
Preface
The JAKA C series robots will serve you wholeheartedly.
The robot pioneers in the control mode with a mobile smart terminal plus an APP connected to the robot, so
that one mobile terminal can match multiple robots. Operators do not need to master professional programming
technology, but only need to manually guide the robot to complete the programming. In this way, man-machine
collaboration is easier, which greatly improves the productivity.
JAKA C series are intelligent, lightweight, 6-DOF modular collaborative robots, falling into the JAKA modular
collaborative robot series.
Product List
When you buy one of the whole set of the JAKA C series robots, the delivery you will receive is as shown in
the following table:
Name
Quantity
1
Robot
1
2
Control cabinet and its key
1
3
Control stick
1
4
Control cabinet power cable
1
5
Robot connection cable
1
6
TIO cable
1
7
Product qualified certificate
1
8
After-sales service warranty card
1
Important Safety Notice
According to 2006/42/EC Machinery Directive, JAKA robot is partly completed machinery, and a risk
assessment must be performed for each robot installation. All safety instructions in chapter 1 must be followed.

File Version: 3.2 6 / 62 JAKA C Series Hardware User Manual
Chapter 1Safety Specification
1.1 Introduction
This chapter mainly introduces the safety principles and standards that should be observed in the use of the
robot or robot system. Users should carefully read and strictly abide by the content related to safety in this
manual. Operators should fully recognize the complexity and danger of the robot system, and pay special
attention to the content related to warning signs.
1.2 Warning Symbols
The danger level in this manual is described with the following warning symbols. Contents related to safety
should be strictly observed.
DANGER:
This sign indicates a potentially dangerous power consumption situation which, if not
avoided, may result in injuries to personnel or serious damage to equipment.
DANGER:
This sign indicates a potentially dangerous situation which, if not avoided, may result
in injuries to personnel or serious damage to equipment.
WARNING:
This sign indicates a potentially dangerous hot surface that may result in injuries to
personnel if touched.
1.3 Safety Precautions
This section focuses on the protection for operators and the relevant precautions of the first installation. Users
need to read the security warnings in this manual carefully. There are many possibilities, and it is impossible to
cover all of them, but we have described as many situations as possible herein.
1. All JAKA hardware and software must be installed/configured in strict accordance
with the instructions and cautions provided in this manual.
2. The installation of the power cut-off switch should be positioned within the height
range of 0.6 meters to 1.9 meters to facilitate prompt and convenient power
disconnection in the event of an emergency.
3. Prior to the initial use of any JAKA products, a comprehensive inspection of all
electrical components and safety protection systems must be conducted to verify their
integrity and absence of prior damage.
4. Operators possessing the necessary qualifications for robot operation are
instructed to perform a thorough assessment of all safety functions and ensure the
accuracy of parameters and programs before initiating the power supply to the robot.

File Version: 3.2 7 / 62 JAKA C Series Hardware User Manual
1. Technical personnel are instructed to carry out the installation and commissioning
procedures for any JAKA products in strict accordance with the provided
specifications.
2. Adjustment and alteration of any JAKA product parameters must be executed
exclusively by authorized personnel to safeguard against unauthorized modifications
by individuals lacking appropriate operating know-how.
3. It is recommended not to frequently toggle the power supply on/off. Each joint of
the JAKA collaborative robot range is equipped with a brake mechanism to maintain
its posture for safety reasons in the event of a power failure. Brake mechanisms can
be damaged during unexpected power downs.
4. In the event that the applied force on the robot surpasses a predefined threshold,
triggered by JAKA’s collision detection feature, it will cease its motion to prevent
potential harm to the robot itself or injury to operators. Associated risks of the use of
control cabinets not supplied by JAKA is solely the responsibility of the operator.
1. Ensure the proper installation of both the robotic arm and its associated tools to
the manufacturer's specifications.
2. Verify that there is adequate space available for unobstructed movement of the
robotic arm.
3. To prevent damage, refrain from connecting safety equipment to the standard I/O
interface (use safety I/O interface).
4. Confirm the accuracy of installation settings, including installation angles, Tool
Center Point (TCP) position, tool mass, TCP offset and the robot's safety
configuration.
5. Ensure that tools and obstacles do not possess sharp corners or points and
maintain a safe distance between all personnel and the robot.
6. Connecting the robot to different machinery may increase existing hazards or
introduce new ones. Conduct a comprehensive risk assessment for the entire system
installation.
7. Do not make modifications to the robot, as such alterations may create unforeseen
hazards for which JAKA cannot be held liable.
1. Both the robot and the control cabinet generate heat during operation. Avoid
contact with the robot and the control cabinet during operation and after shutdown. In
both instances allow approximately 1 hour for the equipment to cool down.
1. When connecting external equipment that may pose a threat to the robot, it is
advisable to independently check all robot functions and programs. Utilize temporary
waypoints located outside the mechanical workspace to verify the robot's program.
2. Exposure to strong magnetic fields can damage the robot; hence, avoid exposing
it to permanent magnetic fields.
1.4 General Warnings and Cautions

File Version: 3.2 8 / 62 JAKA C Series Hardware User Manual
1. Operators who use the robot system are strictly prohibited to wear loose
clothes and jewelry. Those with long hair should ensure that the hair is tied back.
2. During the operation of the equipment, even if the robot appears to have
stopped, it may be in a state of imminent action because it is waiting for a start
signal. In such state, the robot should be regarded as running.
3. During the operation of the robot, ensure that the connection of the control
cabinet power cable and the robot power cable are proper. It is strictly forbidden
to plug or unplug the power cables and terminals in the running mode.
4. Warning lines should be drawn on the floor to mark the movement range of
the robot so that operators can see the movement range of the robot with
gripping tools (mechanic arms, tools, etc.).
5. Ensure that safety measures (e.g., guardrails, ropes, or protective screens)
are in place near the operation area of the robot to protect operators and
surrounding people. Locks should be provided as necessary to make the robot
power inaccessible to anyone other than the operator in charge.
6. In emergencies or abnormal situations when a person is trapped by the robot,
after pressing the emergency stop button, you may push or pull its arm to force
the joint to move. Manual movement of the robot without electric power is limited
to emergencies and may lead to joint damage.
1.5 Liability and Risk
Liability
This manual does not involve any applications of how to design, install and operate the robot, nor does it involve
any peripheral equipment that may affect the security of the robot system.
It is the responsibility of users of JAKA robot to ensure that relevant practical national laws and regulations are
followed, and that no significant hazards lie in the whole robot application.
All safety information in this manual cannot be considered as a guarantee of JAKA. Even if all safety instructions
are followed, injuries or damage may still be caused by operators.
JAKA will keep improving the performance and reliability of our robots. We are not responsible for errors or
omissions in this manual and reserve the right of final interpretation of this manual.
Risk
When there is interaction between operators and the robot, there is inevitably direct or indirect physical contact.
When touching the robot, users must have sufficient awareness of self-protection. Users need to be cautious
when using the robots. Some possible hazards are as follows:
The robot drops and cause any injury when it is moved;
The fastening bolts or screws of the robot get loose and cause any injury;
During the operation, the robot clamps your fingers or collide with you;
The robot causes any injury due to lack of prompt repair of faults;
Potential danger when sharp-end actuators or sharp tool coupling ends are used;
Potential injury when the robot is operated in toxic or corrosive environments.
Use it in strong magnetic environment.
1.6 Usage
JAKA C series is an industrialized collaborative robot. It is suitable for the industrial environment, such as using
it to manipulate equipment or fixed tools and to process or pass spare parts or products. JAKA C series can

File Version: 3.2 9 / 62 JAKA C Series Hardware User Manual
only be used in specified conditions and environments.
JAKA C series has special security rating features specially designed for collaborative operation, that is, the
robot can work without guardrails or work with people. Collaborative operation is only suitable for danger-free
applications, that is, complete applications where tools, workpieces, obstacles and other machines have been
proven not to have a significant risk following an application-specific risk assessment.
Any use or application that violates the intended use is not allowed, including but not limited to:
Use it in an environment where dust explosion may occur;
Use it in medical treatment and vitally important matters;
Use it without risk assessment;
Use it when the performance level is assessed as unqualified;
Operate it without the permitted operating parameters;
1.7 Risk Assessment
Robots are partly completed machinery, and the way the robot is integrated plays a decisive role in whether the
robot is installed safely (e.g. end effectors, communication equipment, etc.). Risk assessment is an important
thing that integrators need to perform. This is required by law in many countries. It is recommended that the
integrator needs to perform the risk assessment according to ISO 12100 and ISO 10218-2, with the option of
using ISO/TS 15066 as additional guidance. The risk assessment performed by the integrator should consider
all matters within the robot's lifetime, including but not limited to:
1. Teaching of the robot during robot installation, set-up and development;
2. Operations of the robot installation;
3. Troubleshooting and maintenance;
The risk assessment must be carried out before the robot is powered up for the first time. The risk
assessment performed by integrator to identify safety configuration settings, assess whether additional
emergency stop buttons or other protective measures required for specific robotic applications are required.
Proper safety configuration is especially important for the use of robots. Cobots have specific safety functions,
which can be configured through settings. These functions are especially important when integrators conduct
risk assessments:
1. Force limit: refers to the force required by the robot to issue a collision alarm when the robot is in contact
with the external environment, showed as a percentage. The higher the percentage, the greater the force
required for the robot to stop;
2. Momentum limit: refers to restricting the momentum of the robot during movement. The limit will directly
affect the speed of the robot. When the momentum of the robot exceeds the limit, the robot speed will be
reduced;
3. TCP speed limit: refers to limiting the absolute speed of the end TCP point during the movement of the
robot. The path speed will be kept within the TCP speed limit;
4. Power limit: refers to limiting the mechanical power during the robot movement. This limit will directly affect
the speed of the robot. When the mechanical power of the robot exceeds the limit, the robot speed will be
reduced.
Integrators must prevent unauthorized personnel from modifying safety configurations.
When performing a risk assessment, the integrator should take into account exposures due to potential misuse,
i.e.:
1. The possibility of a potential collision;
2. The possibility of avoiding potential collisions;
3. The severity of the potential collision;
If the robot is installed in a non-collaborative robot application and the risk cannot be eliminated by configuring
the robot's safety functions. Integrators should consider adding additional protective measures when
conducting risk assessments.

File Version: 3.2 10 / 62 JAKA C Series Hardware User Manual
The JAKA identifies the following significant dangers that integrators must consider.
Note: Specific robotic applications may present other significant hazards.
1. Sharp edges and sharp points on end effectors or end effector connectors stab the skin.
2. Sharp edges and sharp points on obstacles in and near the robot workspace stab the skin.
3. Bruised due to contact with the robot.
4. Sprain or fracture caused by the impact between the heavier load on the end of the robot and the hard
surface.
5. Consequences caused by loose bolts or screws used to fasten robots or end effectors.
6. Consequences of items falling from end effectors.
7. Mis-operation due to different emergency stop buttons on different machines.
8. Error due to unauthorized changes to safety configuration parameters.
Information on stopping times and stopping distances are found in 2.2 and Appendix 1.
1.8 Pre-Use Assessment
After using the robot for the first time or making any modifications, the following tests must be performed.
Ensure that all safety inputs and outputs are correct and connected correctly. Test that all connected safety
inputs and outputs are functioning. Ensure that the payload is configured correctly. The following tests are
required:
1. Test if the emergency stop button and input can stop the robot and engage brakes.
2. Test whether the safeguard input can stop the robot motion. If safeguard reset is configured, check if
activation is required before resuming motion.
3. Check whether the reduced mode input can switch the motion mode to the reduced mode.
4. Test whether the 3- position enabling device must be pressed to enable motion in manual mode and the
robot is under deceleration control.
5. Test whether the emergency stop output of the system can actually bring the entire system into a safe state.
6. Test whether the system connected to the robot moving output, robot non-stop output, reduced mode output,
or non-reduced mode output can actually detect output changes.
7. Test whether the payload configuration matches the current actual payload of the robot.
1.9 Emergency Stop
When an emergency occurs, press the emergency stop button to stop all the movements of the robot
immediately. Emergency stop cannot be used as a risk reduction measure, but it can be regarded as secondary
protection equipment and is only used in emergencies. If you need to stop the robot movement under normal
circumstances, please adopt other measures. After risk assessment, if you need to install an emergency stop
button, the button must meet the requirements of IEC-60947-5. The time and distance of emergency stop of
JAKA robot have been tested. See Appendix 1 for the test data.
Warning:
When the emergency stop button is pressed, the robot system will cut off the robot power. In this case, although
the brakes between the joints will lock the joints automatically, there will still be a slight downward movement
of the robot under gravity, so there is a risk of clamping or collision.
1.10 Movement without Electric Power
In an emergency when the power supply of the robot fails or is not used, the robot joints can be forced to move
in two different ways:
1. Forced manual drive: By pushing or pulling the robot arm, you can force the joint to rotate. The brake in each
joint has a friction clutch. When the torque applied to the joint is greater than the safe torque of the friction
clutch, the joint rotates.

File Version: 3.2 11 / 62 JAKA C Series Hardware User Manual
2. Manual brake release: After removing several screws used for fixed joint lid, remove the joint lid and press
the slider in the small electromagnet (as shown in the figure below) to manually release the brake.
Figure1-1 Manual brake release
Warning:
1. Forced manual movement of the robot arm is limited to emergencies and may lead to joint damage. It should
not be used as a routine operation.
2. If the brake is released manually, the joint of the robot may move under gravity, so it is necessary to effectively
support the robot and tools or workpieces installed on the robot before manually releasing the brake.
1.11 Precautions for Transport and Handling
The original packaging needs to be fixed during transportation to ensure that the robot is stable and dry.
When the robot is hoisted, corresponding measures should be taken for positioning to avoid damage caused
by accidental movement.
When moving the robot from its packaging to the installation position, hold the robot until all the screws on the
robot base are tightened.
Warning:
1. Ensure that the back or other body parts of operators are not overloaded when the equipment is hoisted.
Use appropriate hoisting equipment. JAKA is not responsible for damage incurred during the transport of the
equipment.
2. Ensure that installation instructions are strictly followed when the robot is installed.
1.12 Labels
The following labels are safety warning labels and product label on the robot and the control cabinet. During
the operation, be sure to follow the instructions and warnings on the labels to ensure safety. Do not remove the
labels at will and control stick labeled parts or units and their surrounding area with caution to avoid damage to
the labels. Labels are only for reference.

File Version: 3.2 12 / 62 JAKA C Series Hardware User Manual
A
Product label
B
Beware of collision
C
Beware of pinching
D
Beware of electric shock
E
Grounding
F
Warning hot surface

File Version: 3.2 13 / 62 JAKA C Series Hardware User Manual
Note: Product labels and robot model figures are only for reference, actual varies by robot model.

File Version: 3.2 14 / 62 JAKA C Series Hardware User Manual
Chapter 2Safety Functions
JAKA robot has a series of safety functions to guarantee the safety of man-machine collaboration. This chapter
introduces these safety functions, and users should strictly abide by the requirements and precautions.
2.1 Stop Category
According to the IEC 60201 standard, three stop categories have been set for JAKA robot: stop category 0 (Cat.
0), stop category 1 (Cat. 1), and stop category 2 (Cat. 2). Among them, Cat. 0 is uncontrollable stop, while Cat.
1 and Cat. 2 are controllable stop. If Cat. 0 is triggered, the power to the robot is immediately cut off and the
robot stops running immediately. If Cat. 1 is triggered, the robot actuators remain powered until the robot stops,
and the driving power supply is disconnected after it is completely stopped. If Cat. 2 is triggered, the robot stops
while maintaining the trajectory, and it remains powered after being stopped with the programs suspended.
2.2 Safety Stop Time and Distance
Safety stop time is the time it takes to stop the robot from the moment when the emergency stop button is
pressed or a safety protection function is triggered; the stop distance is the distance the end of the robot moves
during the safety stop time. Among them, pressing the emergency stop button falls into Cat. 1, while triggering
the safety protection function falls into Cat. 2. During this period, the robot is still moving and may harm the
personnel or other equipment. Therefore, users and integrators should consider this time and distance in risk
assessment.
The test conditions are as follows:
• Reach: 100%, 66%/72.5%, 33%;
• Speed: 100%, 66%, 33%;
• Payload: See the table below.
Model
Payload (kg/lb)
C 5
5/11.02
C 7
7/15.43
C 12
12/26.46
See Appendix 1 for the respective stop distance and time of Cat. 1 and Cat. 2.
2.3 Safe Mode
JAKA robot have two configurable safe modes: the emergency stop mode and the protective stop mode.
1. Emergency stop: When an emergency occurs, this mode can be triggered for protection.
Users can trigger the configuration via the emergency stop button on the control stick, the EI interface on the
control cabinet panel P8, and the safety IO function in the safety settings.
When the robot is in the emergency stop state, its states are as follows:
Emergency stop
Robot movement state
Stop
Joint motor state
Stop after deceleration
Robot power
Off
Program execution
Interrupted and to be re-powered
for execution

File Version: 3.2 15 / 62 JAKA C Series Hardware User Manual
Brake state
Braking status
2. Protective stop: The protective stop is a stop type triggered when the robot controller detects an error.
Users can trigger the configuration via the SI interface on the control cabinet panel P8, and the safety IO and
safety plane function in the safety settings.
When the robot is in the protective stop state, its states are as follows:
Protective stop
Robot movement state
Stop
Joint motor state
Enabled
Robot power
On
Program execution
Paused
Brake state
Release status
2.4 Three-Position Enable Device (Optional)
JAKA robot support a three-position enable function, which can be used in conjunction with external three-
position enable device. The standard product delivery of JAKA robot does not include this device. The three-
position enabling safety input interface is available for users and the design meets the certification requirements.
For this optional device, please contact the authorized integrator of JAKA.
When you use three-position enable device and configure the corresponding function in the software, the robot
can only be moved and controlled after the three-position switch is pressed.
The corresponding robot control states for different states of the three-position switch are as follows:
Switch state
Robot state
Manual control
(JOG, debugging)
Automatic control
(program operation)
1
Unpressed
Protective stop (Cat. 2)
Prohibited
When an operation program
is started, the three-position
enabling function is
switched off.
2
Pressed lightly
Normal
Started
3
Pressed heavily
Protective stop (Cat. 2)
Prohibited
The schematic diagram of the three-position enabling switch is as follows:
Figure 2-1 Schematic diagram of the three-position enabling switch

File Version: 3.2 16 / 62 JAKA C Series Hardware User Manual
Chapter 3Quick Start
Before reading this chapter, ensure that you have read in detail and fully understood the safety specifications
in Chapters 1 and 2.
This chapter will introduce the basic components and use methods of JAKA collaborative robots as a
preliminary understanding of the robot. For detailed mechanical electrical specifications refer to other chapters.
3.1 Overview of Robot Components
Figure 3-1 Overview of robot components
As is shown in Figure 3-1, JAKA robot use a wireless interconnection and requires the following components
in its use:
1. Robot: The main moving component to make movements as user desires. Ring-shaped indicators, buttons
for dragging and programming, and an IO interface for connecting tools (the TIO interface) are also arranged
at the end of the body to indicate the robot’s state.
2. Robot connection cable: Connect the robot and the control cabinet.
3. Operation terminal: The equipment for users to program, set parameters, etc.
4. Control stick: Power on/off and enable on/off the robot, etc.
5. Control cabinet power supply cable: Provide power supply to the control cabinet.
6. Control cabinet: The control cabinet includes the core computing components and various electrical
interfaces.
7. Router and network cable: The control cabinet comes with a wireless module that allows the operation
terminal to be connected to the wireless LAN of the control cabinet (the wireless network name is the control
cabinet number) to operate and control the robot. It is also accessible to connect the network port of the control
cabinet to the router and the operation terminal to the wireless network of this router at the same time. It is
recommended to configure a separate router for the robot to prevent conflicts with other devices.
3.2 Robot

File Version: 3.2 17 / 62 JAKA C Series Hardware User Manual
The robot is as shown in Figure 3-2, including six joints and two connecting arms, the upper arm and the lower
arm. There is an indicator representing the robot’s state at the end of the robot, together with a pause/resume
button, and there are two buttons on the outside of the tool flange.
Figure 3-2 Robot
3.2.1 End of the Robot
There is an indicator and a pause/resume button at the end of the robot.
The positions of the ring-shaped indicator and the button are shown in Figure 3-3, and the color indication
meanings are shown in
Table 3-1. When the robot runs a program, you may press the button at the end of the robot to pause it, and
you may press again to resume the movement.
1. Ring-shaped indicator
2. Pause/Resume button
Figure 3-3 Ring-shaped indicator and Pause/Resume button
Table 3-1 Ring-shaped indicator
Color
Working state
Blue
Powered but not enabled
Green
Enabled
Red
Failure/Protective stop
Yellow
Freedrive mode
1.Base
2.Joint 1
3.Joint 2
4.Lower Arm
5.Joint 3
6.Upper Arm
7.Joint 4
8.Joint 5
9.Joint 6
10.Tool flange

File Version: 3.2 18 / 62 JAKA C Series Hardware User Manual
Yellow Flash
Pause
Yellow Flash
Single-step program debugging
Warning:
The use of the buttons at the end requires users to fully assess the possible risks of the sudden start and stop
of the robot, which may cause injury to personnel or damage to the equipment.
3.2.2 Tool flange button and interface
JAKA robot is equipped with a tool IO interface and two buttons on the side of the tool flange. The two buttons
are a freedrive button (FREE) and a position recording button (POINT), as shown in Figure 3-4.
1. Freedrive button
2. Position recording button
Figure 3-4 FREE and POINT button
For details of the tool IO, see Chapter 5 Electrical Interface.
When FREE is pressed, the robot can program in teaching mode, where users can directly drag the robot to
the expected point.
POINT button is used with the robot operating software, JAKA Zu APP. When this button is pressed, the
corresponding position will be recorded by the operating software. (For specific operation, see the JAKA
Software Manual)
Warning:
The use of FREE button requires users to fully assess the possible risks. They must ensure that the robot’s
installation posture, end payload, TCP, and other parameters are correctly set, otherwise it may cause injury to
personnel or damage to equipment.
3.3 Control Cabinet and Control stick
The control cabinet is supplied with a control stick to power on the robot without using the JAKA Zu APP if the
program is already prepared and loaded by default.
The control stick sends control commands to the controller by keys, the functions of which are described as
follows:

File Version: 3.2 19 / 62 JAKA C Series Hardware User Manual
Figure 3-5 Functions of the control stick buttons
1
Emergency
stop button
For emergency stop
Note: The emergency stop button is limited to emergencies and should not be used
as regular power-off equipment.
2
Power on/off
button
Power on: Press the power button for 1s and release. The control stick beeps, and
the control cabinet is switched on.
Power off: Hold down the power button for 3s or more. The control stick beeps 6-7
times, and the control cabinet is switched off.
3
Enable button
Robot power-on: Press the enabled button, waiting for the indicator of flange to turn
blue, which means the robot is powered on.
Robot power-off: Press the enabled button, waiting for the indicator of flange to go
off, which means the robot is powered off.
Enable robot: When the robot powered on, press and hold the lock button, and then
press the enable button at the same time until the indicator of flange to turn green,
which means the robot is enabled.
Disable robot: With the robot enabled, press and hold the lock button, and then
press the enable button at the same time until the indicator of flange to turn blue,
which means the robot is disabled.
4
Start/Stop
button
Start the program: Press the button to start the default program, operate the robot
until it reaches the initial position of the program, and then execute the default
program.
Stop the program: Press to terminate the program when the robot runs the
program.
5
Reset button
Reset: After the robot is enabled, press and hold the reset button during the process
of the non-operation program to control the robot to return to safety orientation set
by the JAKA Zu APP. When the program is run to the default position, press and hold
the button, and the lock indicator is blue.
6
Pause/Resum
e button
Pause: During the automatic operation of the robot, press the button to pause
program execution.
Resume: Press the button to resume program execution when the robot movement

File Version: 3.2 20 / 62 JAKA C Series Hardware User Manual
is paused
7
Lock button
Lock the control stick: Hold down the lock button for 3s, and the lock indicator is
orange.
Unlock the control stick: Hold down the lock button for 3s, and the lock indicator
goes out.
Combination function: Other buttons can be used with the lock button.
8
Lock Indicator
Lock state: In the lock state, the indicator is orange, and all buttons except the lock
button and power button are disabled. The APP can control the robot.
Unlock state: In the unlock state, the indicator goes out, and the control stick can be
used. The APP interface is gray, and you cannot use the APP to control the robot.
9
Control stick
Indicator
During the control cabinet power-on process, the control stick indicator first flashes
red, blue and green alternately with three beeps, and then it turns orange, waiting
for the control cabinet to start. The control stick indicator flashes blue when the
controller program is running normally. After the robot is enabled, the control stick
indicator flashes green.
Note:
Once the control cabinet is powered on, the control stick will beep twice per second if any button is pressed.
When using the control stick to operate the robot, ensure that the robot you are operating is within your sight
and follow the relevant safety guidelines to avoid any harm to personnel or equipment near the robot.
3.4 Technical Specification
1. Technical specification of JAKA C series robot:
Model
C 5
C 7
C 12
Payload
5kg/11lb
7kg/15.4lb
12kg/26.4lb
Weight (including cables)
23kg/50.71lb
22kg/48.50lb
41kg/90.39lb
Reach
954mm/37.5in
819mm/32.2in
1327mm/52.2in
Repeatability
±0.05mm/±0.00196in
Degree of freedom
6
Programming
Graphical programming, and freedrive programming
Demonstrator type
Mobile terminal (PAD/mobile phone) APP
Collaborative operation
Collaborative operation as ISO 10218-1: 2011
Range of action
Joint 1
±360°
Joint 2
-85°~+265°
Joint 3
±175°
Joint 4
-85°~+265°
Joint 5
±360°
Joint 6
±360°
Joint speed
Joint 1
180°/s
180°/s
120°/s
Joint 2
180°/s
180°/s
120°/s
Joint 3
180°/s
180°/s
120°/s
Joint 4
180°/s
180°/s
180°/s
This manual suits for next models
3
Table of contents
Other JAKA Robotics manuals
Popular Robotics manuals by other brands
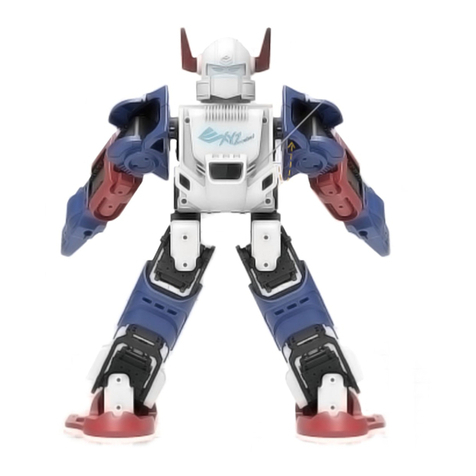
XYZrobot
XYZrobot BOLIDE CRAWLER user manual
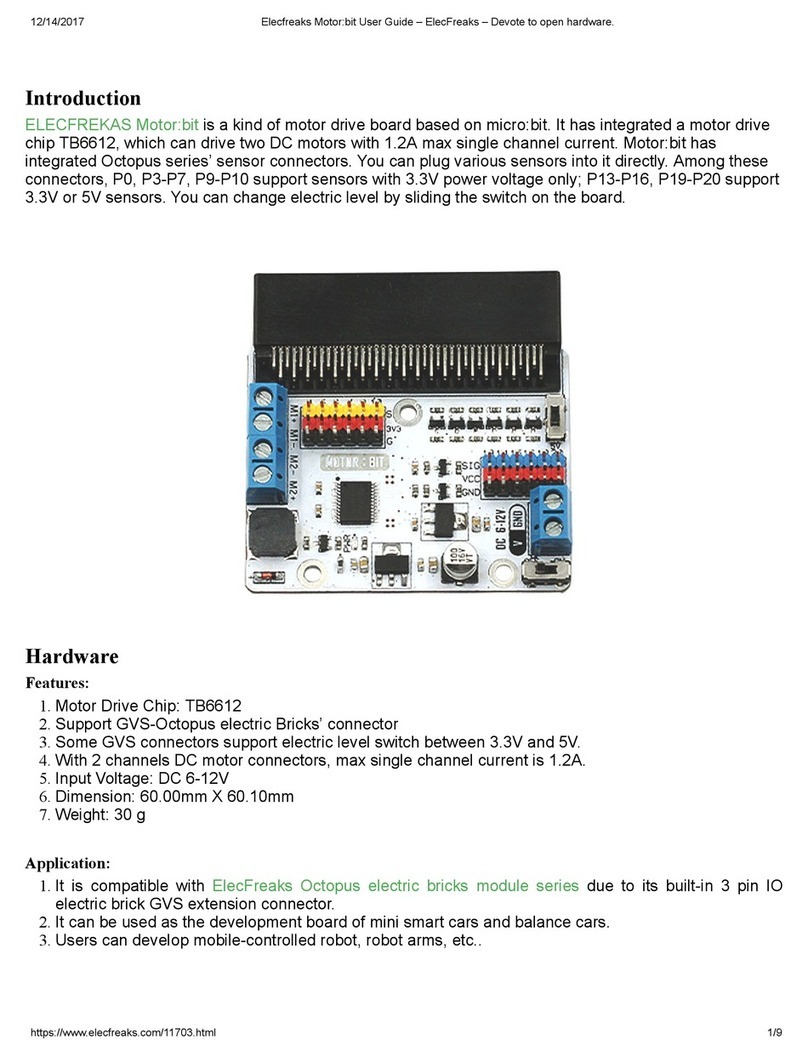
Elecfreaks
Elecfreaks Motor:bit user guide
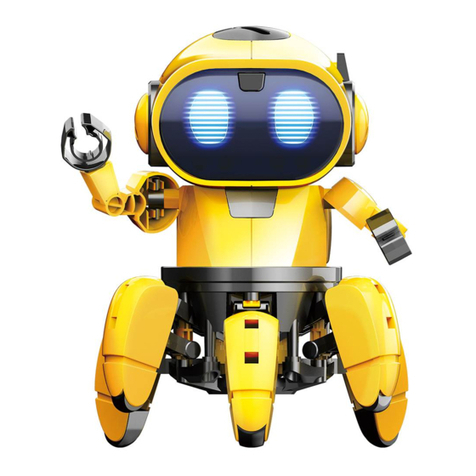
Pro's Kit
Pro's Kit Probbie The Robot GE-893 Assembly & instruction manual
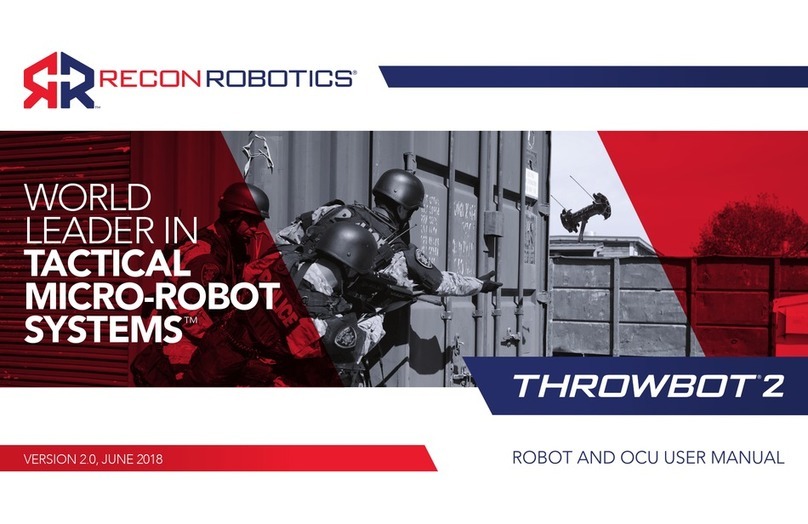
ReconRobotics
ReconRobotics THROWBOT 2 user manual
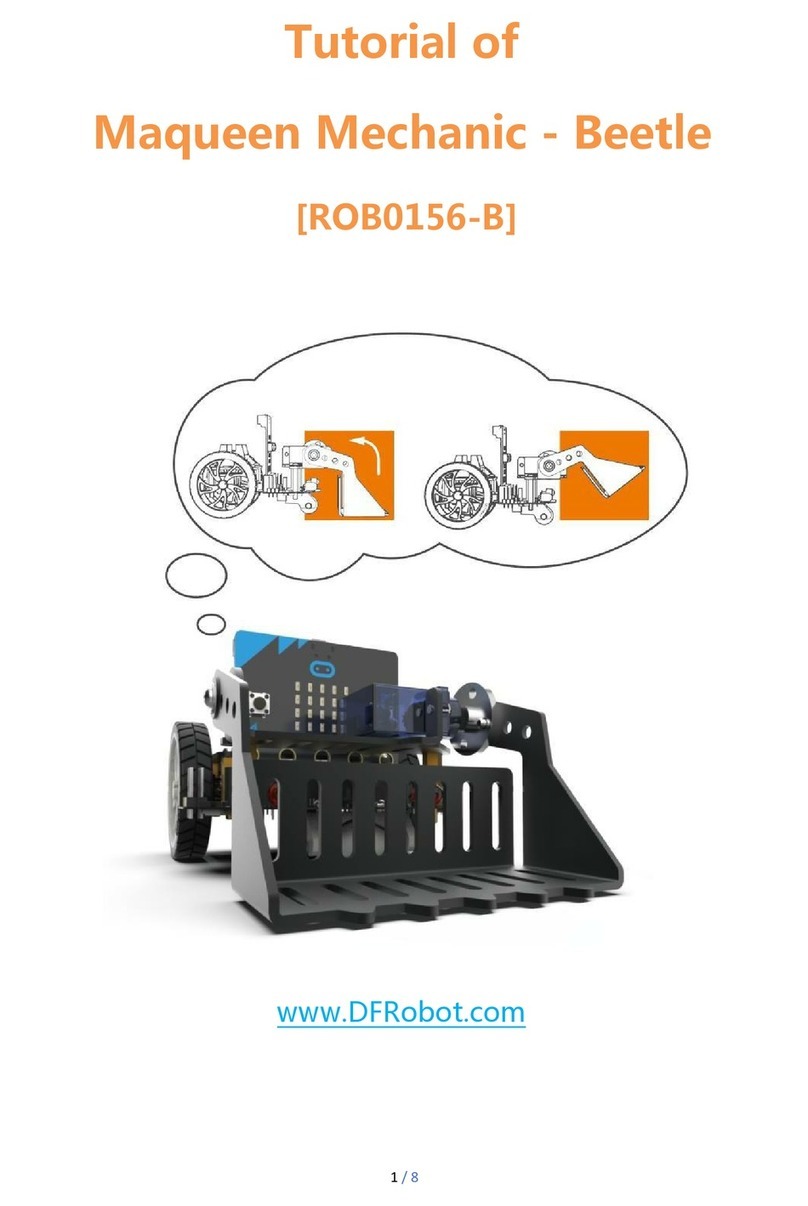
DF ROBOT
DF ROBOT Maqueen Mechanic-Beetle Tutorial
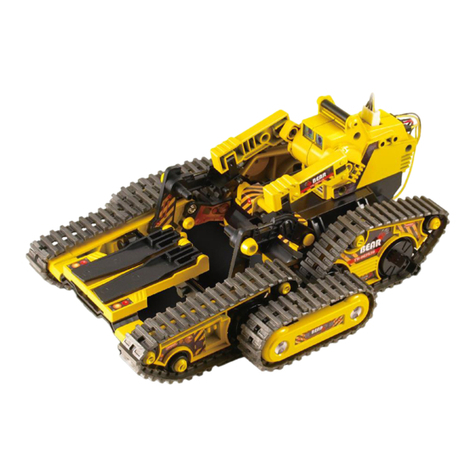
Pro's Kit
Pro's Kit GE-536N Assembly & instruction manual