JDS Uniphase TB9 Series User manual

-~
ARTISAN
®
~I
TECHNOLOGY
GROUP
Your definitive source
for
quality
pre-owned
equipment.
Artisan Technology
Group
Full-service,
independent
repair
center
with
experienced
engineers
and
technicians
on staff.
We
buy
your
excess,
underutilized,
and
idle
equipment
along
with
credit
for
buybacks
and
trade-ins
.
Custom
engineering
so
your
equipment
works
exactly as
you
specify.
•
Critical
and
expedited
services
•
Leasing
/
Rentals/
Demos
• In
stock/
Ready-to-ship
•
!TAR-certified
secure
asset
solutions
Expert
team
ITrust
guarantee
I
100%
satisfaction
All
tr
ademarks,
br
a
nd
names, a
nd
br
a
nd
s a
pp
earing here
in
are
th
e property of
th
e
ir
r
es
pecti
ve
ow
ner
s.
Find the VIAVI Solutions / JDSU TB9226-Z-FP at our website: Click HERE

TB9 SERIES
OPTICAL GRATING FILTER
User’s Manual
Artisan Technology Group - Quality Instrumentation ... Guaranteed | (888) 88-SOURCE | www.artisantg.com

Artisan Technology Group - Quality Instrumentation ... Guaranteed | (888) 88-SOURCE | www.artisantg.com

SD000290 Rev. 500 April 2001
Contents
Safety Information, Instructions, and Symbols.......................................................................1
Safety Information...........................................................................................................1
Classification .......................................................................................................1
Disconnecting from Line Power...........................................................................1
Line Power Requirements ...................................................................................1
Fuse Type............................................................................................................1
Safety Instructions...........................................................................................................2
Before Initializing and Operating the Unit ............................................................2
Operating the Unit ...............................................................................................2
Safety Symbols...............................................................................................................4
Compliance.....................................................................................................................5
CE Compliance....................................................................................................5
UL Compliance....................................................................................................5
General Information and Specifications ..................................................................................6
General Information ........................................................................................................6
Optics .................................................................................................................6
Key Features.......................................................................................................7
Applications.........................................................................................................7
Standard Accessories..........................................................................................7
Specifications..................................................................................................................7
Getting Started..........................................................................................................................9
Before Initializing and Operating the Unit........................................................................9
Initial Inspection...............................................................................................................9
Operating Environment .................................................................................................10
Temperature......................................................................................................10
Humidity.............................................................................................................10
Ventilation..........................................................................................................10
Storing and Shipping.....................................................................................................10
Claims and Repackaging...................................................................................10
Returning Shipments to JDS Uniphase .............................................................10
Cleaning Connectors.....................................................................................................11
Cleaning the UCA Bulkheads........................................................................................13
Powering and Warming up the Grating Filter ................................................................14
Operating and Maintenance Instructions..............................................................................16
Front Panel....................................................................................................................16
Connector Panel................................................................................................17
Rear Panel....................................................................................................................17
Setting the Wavelength.................................................................................................17
Activating the 5 V Output ..............................................................................................17
Setting the GPIB Address.............................................................................................18
Calibrating the Grating Filter .........................................................................................18
Maintaining the Grating Filter........................................................................................18
Artisan Technology Group - Quality Instrumentation ... Guaranteed | (888) 88-SOURCE | www.artisantg.com

SD000290 Rev. 500 April 2001
Programming Guide................................................................................................................19
GPIB Interface...............................................................................................................19
GPIB Interface Pin Assignment and Functions..................................................19
RS232 Interface............................................................................................................20
RS232 Pin Assignment and Functions..............................................................20
RS232 Driver Pin Assignment.......................................................................................20
Connecting the PC Serial Port to the TB9 Grating Filter...............................................21
Operation and Query Commands .................................................................................22
Command Parser Rules.....................................................................................22
Operation Commands........................................................................................22
Query Commands..............................................................................................23
Status Reporting and Service Request Control.............................................................24
Status Register ..................................................................................................25
SRQ Mask Register ...........................................................................................25
GPIB Programming Examples.......................................................................................26
Sending Commands..........................................................................................26
Querying Status.................................................................................................26
Serial Polling the Status Register ......................................................................27
Generating a Service Request Interrupt ............................................................27
RS232 Interface Programming Example.......................................................................28
For sales and service information,
contact JDS Uniphase or your local representative.
JDS Uniphase Corporation
570 West Hunt Club Road
Nepean, Ontario, Canada
K2G 5W8
Phone: 613 727-1303
Fax: 613 727-8284
E-mail: sales@jdsunph.com
Website: http://www.jdsunph.com
Artisan Technology Group - Quality Instrumentation ... Guaranteed | (888) 88-SOURCE | www.artisantg.com

Safety – 1
Safety Information, Instructions, and Symbols
Safety Information
Classification
The unit consists of an exposed metal chassis that is connected directly to earth via a power
cord and, therefore, is classified as a Class 1 instrument. Class 1 refers to equipment relying
on ground protection as a means of shock protection.
The following symbol is used to indicate a protective conductor terminal in the unit.
Disconnecting from Line Power
Some of the circuits are powered whenever the unit is connected to the AC power source (line
power). To ensure that the unit is not connected to the line power, disconnect the power cord
from either the power inlet on the unit’s rear panel or from the AC line-power source
(receptacle). The power cord must always be accessible from one of these points. If the unit is
installed in a cabinet, the operator must be able to disconnect the unit from the line power by
the system’s line-power filter.
Line Power Requirements
The unit can operate from any single-phase AC power source that supplies between 100 and
240 V at a frequency range of 50 to 60 Hz. The maximum power consumption is 80 VA.
Fuse Type
The fuse type used by the unit is 1 A, 250 V AC 5 X 20 mm.
Artisan Technology Group - Quality Instrumentation ... Guaranteed | (888) 88-SOURCE | www.artisantg.com

Safety – 2
Safety Instructions
The following safety instructions must be observed whenever the unit is operated, serviced, or
repaired. Failure to comply with any of these instructions or with any precaution or warning
contained in the user’s manual is in direct violation of the standards of design, manufacture,
and intended use of the unit. JDS Uniphase assumes no liability for the customer’s failure to
comply with any of these safety requirements.
Before Initializing and Operating the Unit
Inspect the unit for any signs of damage, and read the user’s manual thoroughly.
Install the unit as specified in the Getting Started section.
Ensure that the unit and any devices or cords connected to it are properly grounded.
Operating the Unit
Warning
To avoid the risk of injury or death, always observe the following precautions
before initializing the unit:
•If using a voltage-reducing autotransformer to power the unit, ensure that
the common terminal connects to the earthed pole of the power source.
•Use only the type of power cord supplied with the unit.
•Connect the power cord only to a power outlet equipped with a protective
earth contact. Never connect to an extension cord that is not equipped with
this feature.
•Do not interrupt the protective earth grounding. Any such action can lead to
a potential shock hazard that can result in serious personal injury. If an
interruption to the protective grounding is suspected, ensure that the unit
remains inoperative
•Never look into the end of an optical cable connected to an optical output
device that is operating. Laser radiation is invisible, and direct exposure can
severely injure the human eye. Depending on input power, output power of
TB9P can emit “class IV” laser light. For more information, see the user’s
manual of the laser source in use.
•Dirty fiber connector can be damaged under high power input. Always
make sure fiber connector is cleaned properly.
•Turning off the power to the device does not always block the externally
supplied radiation to the connector at the output of the unit.
•Do not use the unit outdoors.
•To prevent potential fire or shock hazard, do not expose the unit to any
source of excessive moisture.
•Do not operate the unit when its covers or panels have been removed.
Artisan Technology Group - Quality Instrumentation ... Guaranteed | (888) 88-SOURCE | www.artisantg.com

Safety – 3
•Use only the type of fuse specified by the manufacturer as appropriate for
this unit. Do not use repaired fuses, and avoid any situations that can short-
circuit the fuse.
•Unless absolutely necessary, do not attempt to adjust or perform any
maintenance or repair procedure when the unit is opened and connected to
a power source.
•Repairs are to be carried out only by a qualified professional.
•Do not attempt any adjustment, maintenance, or repair procedure to the
unit’s internal mechanism if immediate first aid is not accessible.
•Disconnect the power cord from the unit before adding or removing any
components.
•Operating the unit in the presence of flammable gases or fumes is
extremely hazardous.
•Do not perform any operating or maintenance procedure that is not
described in the user’s manual.
•Some of the unit’s capacitors can be charged even when the unit is not
connected to the power source.
Artisan Technology Group - Quality Instrumentation ... Guaranteed | (888) 88-SOURCE | www.artisantg.com

Safety – 4
Safety Symbols
The following symbols and messages can be marked on the unit (Table 1). Observe all safety
instructions that are associated with a symbol.
Table 1: Safety Symbols
Symbol
Description
Laser safety. See the user’s manual for instructions on handling and operating
the unit safely.
See the user’s manual for instructions on handling and operating the unit
safely.
Electrostatic discharge (ESD). See the user’s manual for instructions on
handling and operating the unit safely.
Frame or chassis terminal for electrical grounding within the unit.
Protective conductor terminal for electrical grounding to the earth.
WARNING
The procedure can result in serious injury or loss of life if not carried out
in proper compliance with all safety instructions. Ensure that all
conditions necessary for safe handling and operation are met before
proceeding.
CAUTION
The procedure can result in serious damage to or destruction of the unit if not
carried out in compliance with all instructions for proper use. Ensure that all
conditions necessary for safe handling and operation are met before
proceeding.
Artisan Technology Group - Quality Instrumentation ... Guaranteed | (888) 88-SOURCE | www.artisantg.com

Safety – 5
Compliance
CE Compliance
The unit has been designed and tested to comply with directive 73/23/EEC and its subsequent
amendments by the European Community (EC or CE). The directive relates to electrical
equipment designed for use within certain voltage limits. It ensures that electrical equipment is
constructed with good engineering practice in safety matters.
The unit has been designed and tested to comply with directive 89/336/EEC and its
subsequent amendments. The directive relates to electromagnetic compatibility. It demands
that electromagnetic disturbance does not exceed a prescribed level; that the equipment be
immune to a prescribed level of ambient interference; that the equipment be protected against
electrostatic discharges; and that the equipment be immune to all electrical shock wave
disturbances. As of 1997, measures have been added to test for fire hazard, electric shock
hazard, and also external exposure to other forms of energy.
The requirements specified by directive 89/336/EEC are as follows. CE compliance requires
that the manufacturer or its authorized representative established within the Community affix
the EC conformity mark to the apparatus or else to the packaging, instructions for use, or
guarantee certificate. The EC conformity mark shall consist of the letters CE as specified and
the figures of the year in which the mark was affixed. This mark should, where appropriate, be
accompanied by the distinctive letters used by the notified body issuing the EC type-
examination certificate. Where the apparatus is the subject of other Directives providing for the
EC conformity mark, the affixing of the EC mark shall also indicate conformity with the relevant
requirements of those other Directives.
UL1Compliance
The unit complies with Underwriters Laboratories (UL) standard 1950, the Standard for Safety
Information Technology Equipment.
The unit complies with Underwriters Laboratories (UL) standard 3101.1, Electrical Equipment
for Laboratory Use; Part 1: General Requirements.
1UL is a registered trademark of Underwriters Laboratories Inc.
Artisan Technology Group - Quality Instrumentation ... Guaranteed | (888) 88-SOURCE | www.artisantg.com

Getting Started – 6
General Information and Specifications
General Information
This user’s manual for the TB9 Series Optical Grating Filter contains complete operating
instructions.
The TB9 grating filter is designed for high performance laboratory and production testing of
single-mode fiber-based components and subsystems (Figure 1). Single- and double-pass
grating configurations are available to provide high rejection and narrow bandwidth. Optical
performance for the C-band is optimized in the 1530 to 1570 nm window, but the filter can be
controlled over the wavelength range of 1460 to 1575 nm. Optical performance for the L-band
is optimized in the wavelength range of 1525 to 1625 and has a tuning range of 1460 to 1575.
Six standard models are available with different bandwidths and optical performance.
Figure 1: TB9 Optical Grating Filter
The TB9 grating filter contains a lens that collimates light from the input fiber. A diffraction
grating reflects collimated light back through the lens. This filtered light is then focused into the
output fiber.
The angle of the diffraction grating is controlled by a stepper motor that is driven by the
microprocessor of the TB9 grating filter. On power-up, the microprocessor positions the angle
of the grating to 1460 nm or to 1525 nm for extended-range models. Each time a wavelength
command is entered, the microprocessor determines how many steps this wavelength is from
the reference position and moves the diffraction grating to the required angle.
Optics
The optics of the TB9 grating filter are bi-directional, and therefore either fiber port can be
used as the input. If an optional coupler or switch is installed, the user must ensure that the
connections to these are appropriate.
Artisan Technology Group - Quality Instrumentation ... Guaranteed | (888) 88-SOURCE | www.artisantg.com

Getting Started – 7
Key Features
•Grating-based optical filter
•Full width at half maximum (FWHM) as low as 0.22 nm
•High rejection
•Single-mode fiber in and out
•GPIB parallel interface and RS232 serial interface
Applications
•Spontaneous emission suppression
•Tunable laser-based testing
•Erbium doped fiber amplifier (EDFA) testing
•Wavelength division multiplexer (WDM) and denseWDM (DWDM) component testing
Standard Accessories
•AC power cord
•Rack-mount kit with assembly instructions
•User’s manual
Specifications
The following optical specifications describe the warranted characteristics of the TB9 (Table 2).
Supplementary specifications describe the typical non-warranted performance of the unit
(Table 3).
Table 2: Optical Specifications
Parameter TB9226 TB9166 TB9223 TB9126 TB9116 TB9106
Tuning Range 1460-
1575
or
1525-
1625
1460-
1575 1460-
1575
or
1525-
1625
1460-
1575 1460-
1575 1460-
1575
-3 dB bandwidth (±15%) 0.22 nm 0.25 nm 0.55 nm 0.55 nm 1.1 nm 1.4 nm
-20 dB bandwidth (±15%) 0.6 nm 0.7 nm 1.5 nm 1.5 nm 3.0 nm 4.0 nm
Insertion loss 1530-1570
1525-1625 ≤6.0 dB
≤7.0 dB ≤4.0 dB ≤5.5 dB
≤7.0 dB ≤3.0 dB ≤3.0 dB ≤3.0 dB
PDL 1530-1570
1525-1625 ≤0.2 dB
≤0.5 dB ≤0.6 dB ≤0.2 dB
≤0.5 dB ≤0.6 dB ≤0.6 dB ≤0.6 dB
Input Power Standard
High Power 300 mW
1 W 300 mW
1 W 300 mW
1 W 300 mW
1 W 300 mW
1 W 300 mW
1 W
Resolution 0.01 nm
Return loss >45 dB
Artisan Technology Group - Quality Instrumentation ... Guaranteed | (888) 88-SOURCE | www.artisantg.com

Getting Started – 8
Repeatability 0.05 nm
Accuracy 0.2 nm
Table 3: Other specifications
Electrical
Input voltage 100 to 240 V AC, 50 to 60 Hz
Power consumption 80 VA maximum
Physical
Weight 4 kg
Dimensions (W x H x D)
19 in (48.26 cm) rack-
mount
21.2 x 8.9 x 35.5 cm
2U high, ½ rack width
Environmental
Storage temperature 0 to 50 °C
Operating temperature 10 to 40 °C
Humidity maximum 95% RH up to 40 °C, decreasing at 5% per °C from 40
to 50 °C
Artisan Technology Group - Quality Instrumentation ... Guaranteed | (888) 88-SOURCE | www.artisantg.com

Getting Started – 9
Getting Started
The TB9 Series Optical Grating Filter consists of the filter unit, an AC power cord, a user's
manual, the test report and a warranty card.
Before Initializing and Operating the Unit
Inspect the unit for any signs of damage.
Read the user’s manual thoroughly, and become familiar with all safety symbols and
instructions to ensure that the unit is operated and maintained safely.
Initial Inspection
Warning
To avoid electrical shock, do not initialize or operate the unit if it bears any sign
of damage to any portion of its exterior surface, such as the outer cover or
panels.
Check that the unit and contents are complete:
1. Wear an anti-static wrist strap, and work in an electrostatic discharge (ESD) controlled
area.
2. Inspect the shipping container for any indication of excessive shock to the contents, and
inspect the contents to ensure that the shipment is complete.
3. Inspect the unit for structural damage that can have occurred during shipping.
4. Connect the unit to a power source, using the AC power cord provided.
5. Set the power switch to I(on) and observe the power-up sequence. The key lamps and
status LEDs will illuminate. The version of the software is displayed briefly followed by
“TB9(CRLF) AD”. CRLF is the message terminating sequence <CR> <LF>, AD is the
GPIB address (a number between 1 and 32). After the power-up sequence is complete the
instrument will display the wavelength that corresponds with start of the tuning range (1460
or 1525 depending on the model). If a malfunction is detected during power-up, an error
message is displayed.
6. Allow the instrument to stabilize for two hours before use.
7. Keep the packaging.
Immediately inform JDS Uniphase and, if necessary, the carrier if the contents of the shipment
are incomplete, if the unit or any of its components are damaged or defective, or if the unit
does not pass the initial inspection.
Artisan Technology Group - Quality Instrumentation ... Guaranteed | (888) 88-SOURCE | www.artisantg.com

Getting Started – 10
Operating Environment
In order for the unit to meet the warranted specifications, the operating environment must meet
the following conditions for temperature, humidity, and ventilation.
Temperature
The unit can be operated in the temperature range of 10 to 40 °C.
Humidity
The unit can be operated in environments with up to 95% relative humidity (up to 40 °C),
decreasing 5% per °C from 40 to 50 °C. Do not expose it to any environmental conditions or
changes to environmental conditions that can cause condensation to form inside the unit.
Ventilation
The unit contains a built-in cooling fan. Do not install it in any location where the ventilation is
blocked. For optimum performance, the unit must be operated from a location that provides at
least 75 mm (3 inches) of clearance at the rear and at least 25 mm (1 inch) of clearance at the
bottom. Blocking the air circulation around the unit can cause the unit to overheat,
compromising its reliability.
Warning
•Do not use the unit outdoors.
•To prevent potential fire or shock hazard, do not expose the unit to any
source of excessive moisture.
Storing and Shipping
To maintain optimum operating reliability, do not store the unit in locations where the
temperature falls below 0 °C or rises above 50 °C. Avoid any environmental condition that can
result in internal condensation. Ensure that these temperature and humidity requirements can
also be met whenever the unit is shipped.
Claims and Repackaging
Immediately inform JDS Uniphase and, if necessary, the carrier, if
•The contents of the shipment are incomplete
•The unit or any of its components are damaged or defective
•The unit does not pass the initial inspection
In the event of carrier responsibility, JDS Uniphase will allow for the repair or replacement of
the unit while a claim against the carrier is being processed.
Returning Shipments to JDS Uniphase
JDS Uniphase only accepts returns for which an approved Return Material Authorization
(RMA) has been issued by JDS Uniphase sales personnel. This number must be obtained prior
to shipping any material to JDS Uniphase. The owner’s name and address, the model number
Artisan Technology Group - Quality Instrumentation ... Guaranteed | (888) 88-SOURCE | www.artisantg.com

Getting Started – 11
and full serial number of the unit, the RMA number, and an itemized statement of claimed
defects must be included with the return material.
Ship return material in the original shipping container and packing material. If these are not
available, packaging guidelines are as follows:
1. Cover the front panel with a strip of anti-static foam.
2. Wrap the unit in anti-static packaging. Use anti-static connector covers.
3. Pack the unit in a reliable shipping container.
4. Use enough shock-absorbing material (10 to 15 cm or 4 to 6 in on all sides) to cushion the
unit and prevent it from moving inside the container. Pink poly anti-static foam is the best
material.
5. Seal the shipping container securely.
6. Clearly mark FRAGILE on its surface.
7. Always provide the model and serial number of the unit and, if necessary, the RMA number
on any accompanying documentation.
8. Please contact the RMA department using the contact information at the beginning of this
document to obtain an RMA number and a shipping address.
Cleaning Connectors
Caution
•Connecting damaged or dirty connectors to the unit can damage the
connectors on the unit.
•Dirty connectors can be damaged when exposed to high power.
•Never force an optical connector. Some connectors have a ceramic ferrule
that can easily be broken.
The following items are required for cleaning:
•Filtered compressed air or dusting gas (for example, Tech Spray Envi-Ro-Tech Duster
1671 gas, available from http://www.techspray.com/1671.htm)
•Lint-free pipe cleaners (for example, from 3M2) or lint-free swab
•Lint-free towels (for example, 10 x 10 cm or 4 x 4 in HydroSorb III wipers, available from
http://www.focenter.com/acctech/hydrosobr_wipers.htm)
•Optical grade isopropyl alcohol or optical grade 200° ethanol (do not use rubbing alcohol,
which contains 30% water)
23M is a trademark of 3M.
Artisan Technology Group - Quality Instrumentation ... Guaranteed | (888) 88-SOURCE | www.artisantg.com

Getting Started – 12
•No. 0 Phillips screwdriver
Cleaning the jumper connector:
Figure 2: Typical jumper connector
1. Apply alcohol to a small area of a lint-free towel and rub the end of the ferrule over the wet
area.
2. Wipe the ferrule on a dry area of the lint-free towel.
3. Using the dusting gas or compressed air, blow the end of the ferrule.
4. Apply the alcohol or ethanol to a lint-free pipe cleaner or swab and wipe off the remaining
parts of the connector.
5. With the other end of the pipe cleaner or swab, dry the areas cleaned.
6. Using the dusting gas or compressed air, blow the areas cleaned.
Cleaning the mating sleeve:
1. Blow compressed air inside the opening of the mating sleeve to remove trapped particles
(Figure 3).
2. Moisten a fresh pipe cleaner with alcohol. Gently clean the opening by inserting the pipe
cleaner using a rotating motion.
3. Blow compressed air inside the opening to remove any remaining material.
Artisan Technology Group - Quality Instrumentation ... Guaranteed | (888) 88-SOURCE | www.artisantg.com

Getting Started – 13
Figure 3: Typical Mating Sleeve
Cleaning the UCA Bulkheads
Cleaning Procedure:
The TB9’s are manufactured with protective covers to shield users from the potentially
harmful signal that could be emitted from the optical ports. The covers are designed to
provide sufficient clearance for maintenance, cleaning, and for changing or replacing
adapters. Before cleaning it is recommended that all jumpers be disconnected, as the TB9
can transmit signal even when the power is turned off. To avoid injury, do not reconnect
jumpers until all ports have been cleaned.
1. Remove the two adapter mounting screws with the No. 0 Phillips screwdriver (see
Figure 4). Removing the adapter will expose the internal connector that is fastened to
the base plate. The internal connectors are mounted at the factory and should not
have to be adjusted under normal operating conditions.
2. Apply alcohol to a small area of a lint-free towel and gently rub the connector end to
clean. Do not to apply excessive pressure while rubbing, to avoid scratching and pitting.
Discard tissues after a single use to avoid contamination.
3. Gently wipe flat surface of the base plate to ensure a clear mating surface during re-
assembly.
Artisan Technology Group - Quality Instrumentation ... Guaranteed | (888) 88-SOURCE | www.artisantg.com

Getting Started – 14
Figure 4: Universal Connector Adapter
4. Clean the internal cavity with a pipe cleaner and alcohol (a rotating motion will yield the
best results). The adapter is a critical component that can provide highly reliable mating
of optical connector, if properly maintained.
5. Gently wipe the flat surface of the adapter to ensure a clear mating surface during re-
assembly.
6. To insert the adapter sleeve into the base plate, align the center axis of the two parts
and make sure the alignment key will mate with the alignment hole on the flat surface
of the base plate. Once in position, fasten the two adapter mounting screws to secure
the parts together.
7. Clean all ports by repeating Steps 1 - 4.
8. All jumper connectors used to mate other equipment with the TB9 should be cleaned
thoroughly (see connector cleaning section).
Powering and Warming up the Grating Filter
To power up the TB9 grating filter:
1. Connect the TB9 grating filter to the AC power source, using the AC power cord provided.
2. Set the power switch to I(on) and observe the power-up sequence. The key lamps and
status LEDs will illuminate. The version of the software is displayed briefly followed by
“TB9(CRLF) AD”. CRLF is the message terminating sequence <CR> <LF>, AD is the
GPIB address (a number between 1 and 32). After the power-up sequence is complete the
instrument will display the wavelength that corresponds with the start of the tuning range
Artisan Technology Group - Quality Instrumentation ... Guaranteed | (888) 88-SOURCE | www.artisantg.com

Getting Started – 15
(1460 or 1525 depending on the model). If a malfunction is detected during power-up, an
error message is displayed.
3. Allow the instrument to stabilize for two hours before use. An electrical current is supplied
continuously to the heater elements of the TB9 grating filter until its internal temperature
reaches the set point.
Artisan Technology Group - Quality Instrumentation ... Guaranteed | (888) 88-SOURCE | www.artisantg.com
This manual suits for next models
6
Table of contents
Popular Water Filtration System manuals by other brands
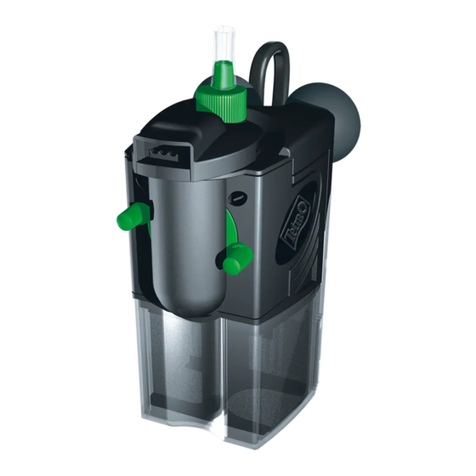
Tetra
Tetra IN 300 plus instruction manual
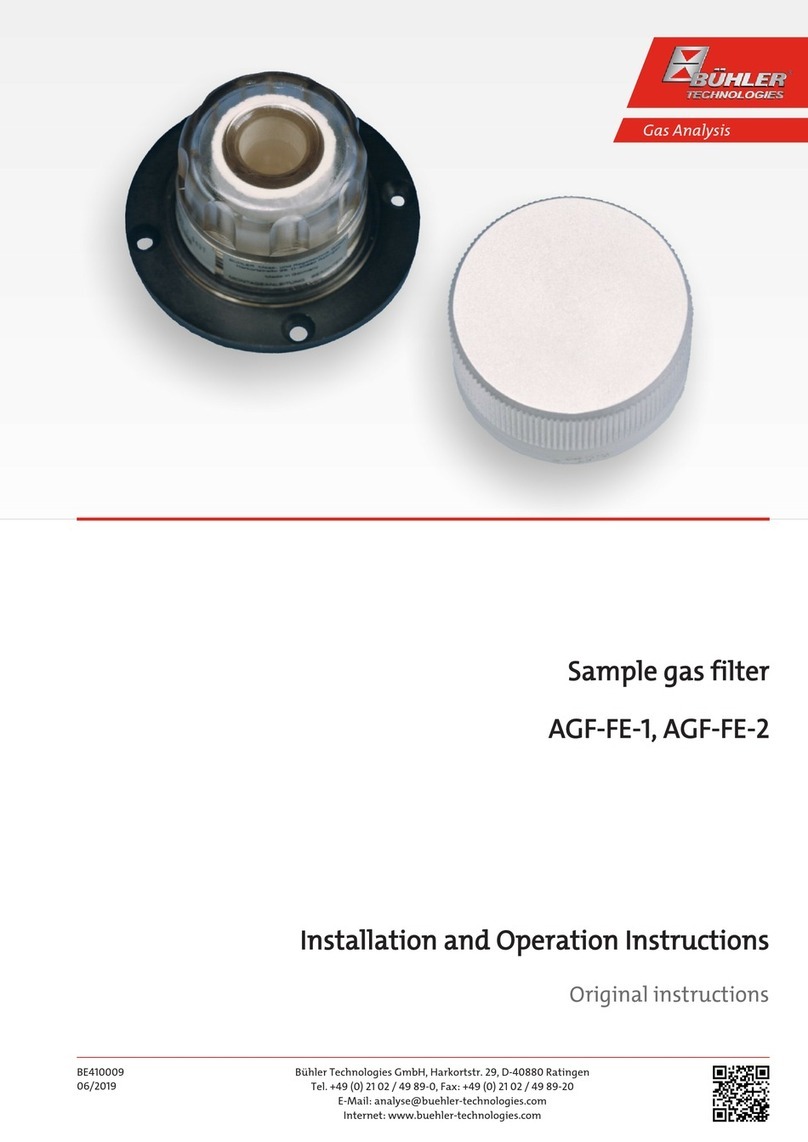
Bühler technologies
Bühler technologies AGF-FE-1 Installation and operation instructions
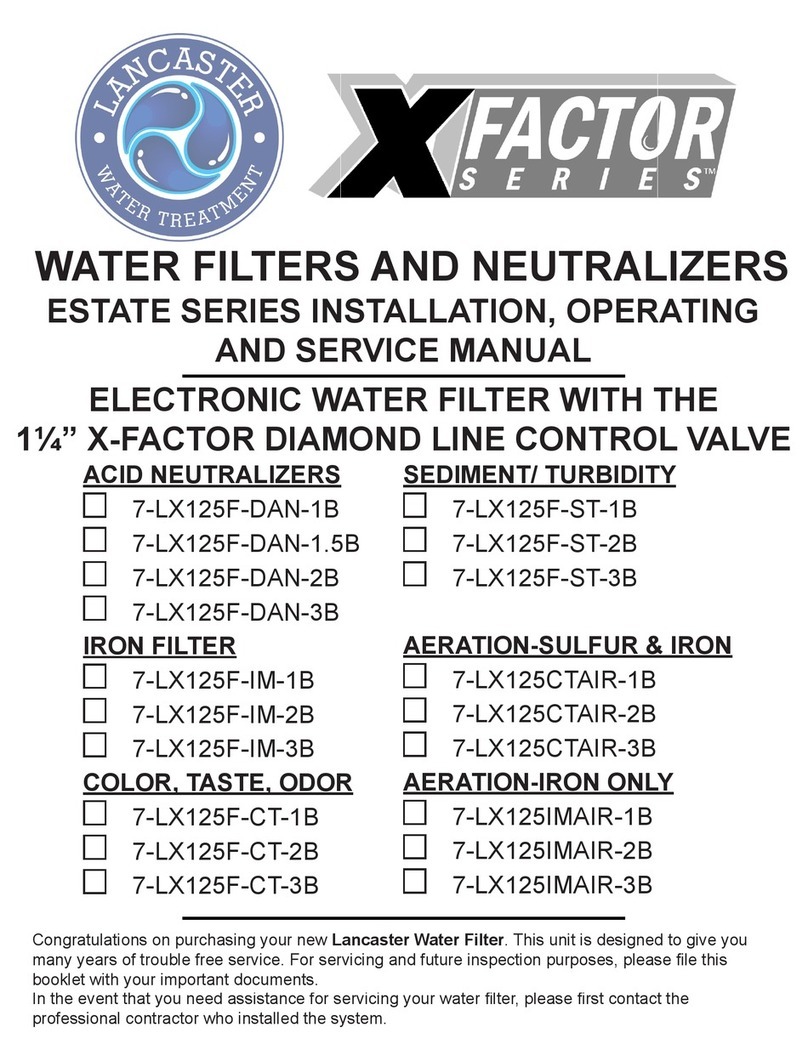
Lancaster
Lancaster XFACTOR 7-LX125F-DAN-1B Installation, operating and service manual
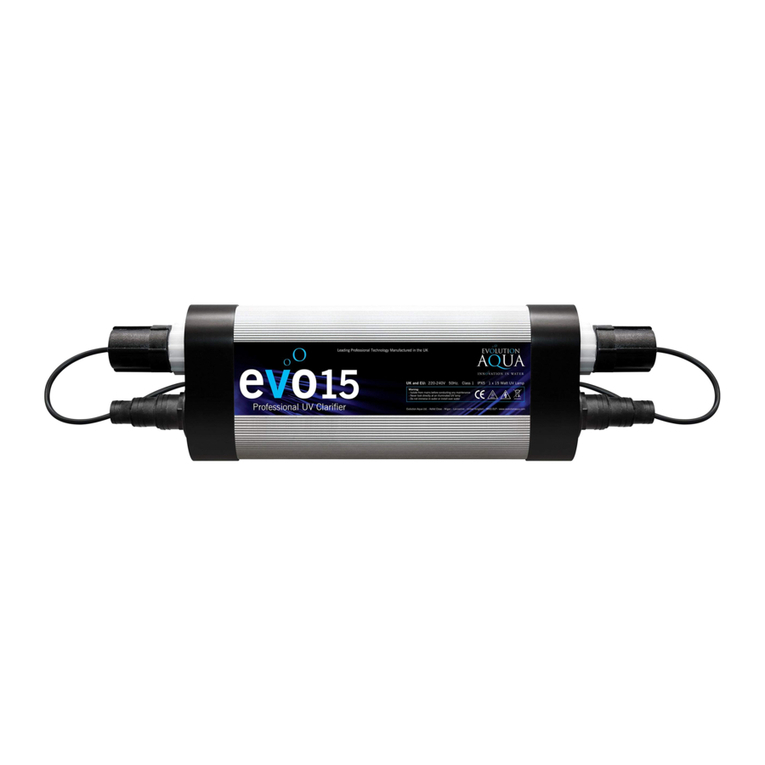
Evolution Aqua
Evolution Aqua evo15 Installation and operating manual

Osmio
Osmio Clarity user manual
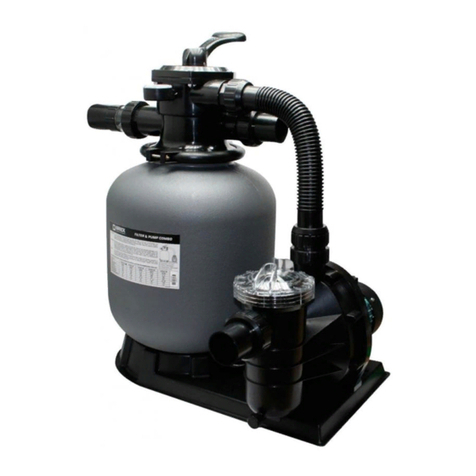
Brilix
Brilix FSP350 Installation and user guide
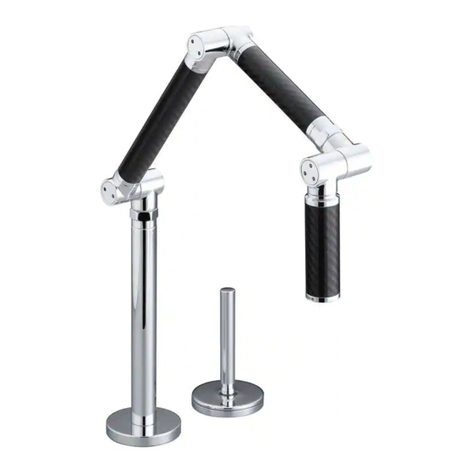
Kohler
Kohler K-6227 Installation and care guide

Trion
Trion AIR BOSS owner's manual
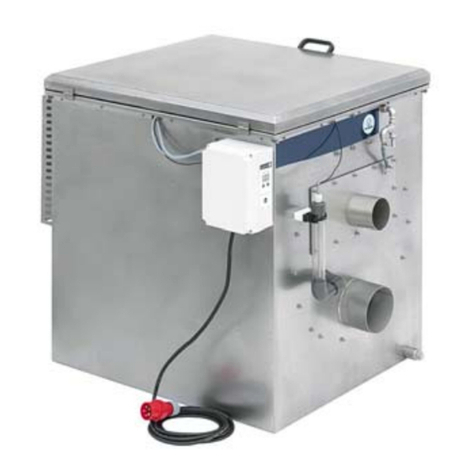
Fiap
Fiap TrommelSieve Active Series operating instructions
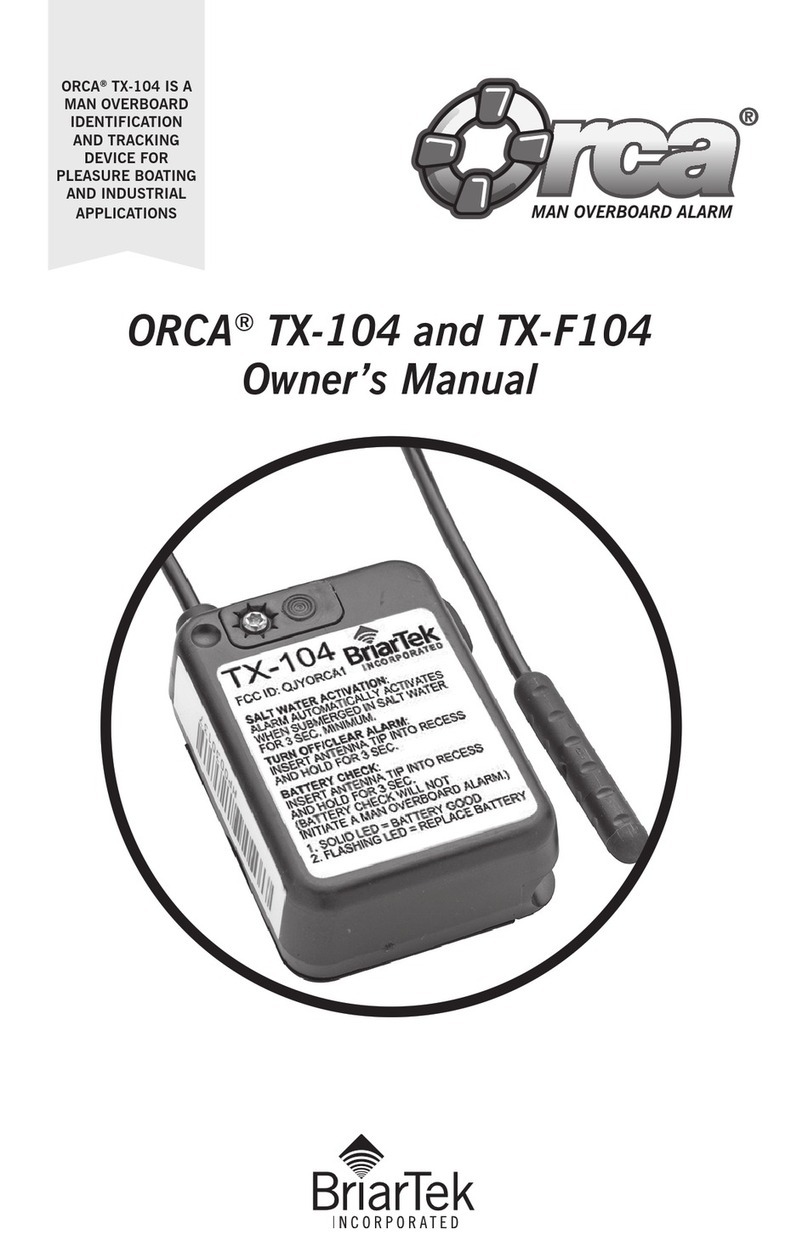
BriarTek
BriarTek ORCA TX-104 owner's manual
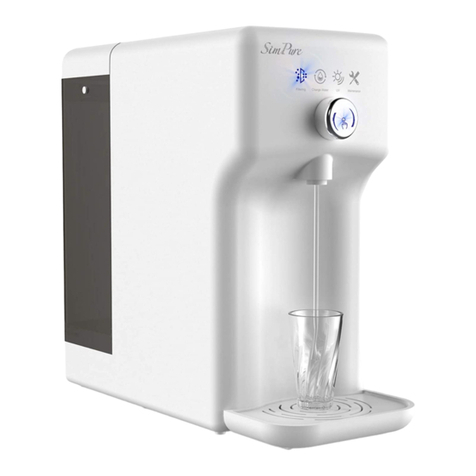
SimPure
SimPure Y6 owner's manual
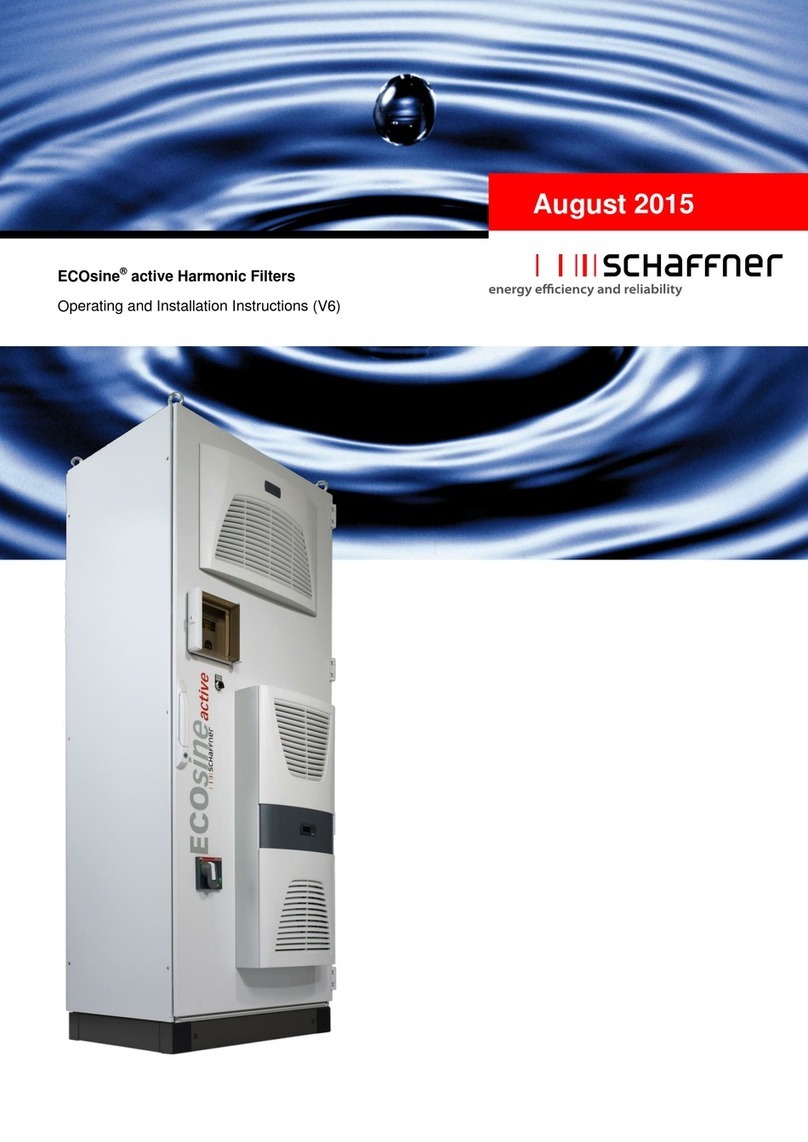
Schaffner
Schaffner ECOsine active FN3420-030-3 Series Operating and installation instructions