Jet HVBS-712K User manual

GB - ENGLISH
Operating Instructions
Dear Customer,
Many thanks for the confidence you have shown in us with the purchase of your new JET-machine. This manual has been
prepared for the owner and operators of a JET HVBS-712K metal band saw to promote safety during installation, operation and
maintenance procedures. Please read and understand the information contained in these operating instructions and the
accompanying documents. To obtain maximum life and efficiency from your machine, and to use the machine safely, read this
manual thoroughly and follow instructions carefully.
…Table of Contents
1. Declaration of conformity
2. JET Warranty
3. Safety
Authorized use
General safety notes
Remaining hazards
4. Machine specifications
Technical data
Noise emission
Contents of delivery
5. Transport and start up
Transport and installation
Assembly
Mains connection
Starting operation
6. Machine operation
7. Setup and adjustments
Changing blade speed
Changing sawblade
Blade guides adjustment
Guide bearing adjustment
Blade tracking adjustment
Feed speed adjustment
Vice adjustment
8. Maintenance and inspection
9. Troubleshooting
10. Available accessories
1. Declaration of conformity
On our own responsibility we hereby
declare that this product complies with
the regulations* listed on page 2.
Designed in consideration with the
standards**.
2. JET Group Warranty
The JET Group makes every effort to
assure that its products meet high
quality and durability standards and
warrants to the original retail
consumer/purchaser of our products
that each product be free from defects
in materials and workmanship as
follows:
2 YEAR LIMITED WARRANTY ON
ALL PRODUCTS UNLESS
SPECIFIED OTHERWISE.
This Warranty does not apply to
defects due to directly or indirectly
misuse, abuse, negligence or
accidents, normal wear-and-tear,
repair or alterations outside our
facilities, or to a lack of maintenance.
The Jet group limits all implied
warranties to the period specified
above, from the date the product was
purchased at retail.
To take advantage of this warranty,
the product or part must be returned
for examination, postage prepaid, to
an authorized repair station
designated by our office.
Proof of purchase date and an
explanation of the complaint must
accompany the merchandise.
If our inspection discloses a defect,
we will either repair or replace the
product, or refund the purchase price
if we cannot readily and quickly
provide a repair or replacement, if you
are willing to accept a refund.
We will return repaired product or
replacement at JET’S expense, but if
it is determined there is no defect, or
that the defect resulted from causes
not within the scope of JET’S
warranty, then the user must bear the
cost of storing and returning the
product.
The JET Group reserves the right to
make alterations to parts, fittings, and
accessory equipment which they may
deem necessary for any reason
whatsoever.
3. Safety
3.1 Authorized use
This machine is designed for sawing
machinable metal and plastic
materials only.
Machining of other materials is not
permitted and may be carried out in
specific cases only after consulting
with the manufacturer.
Never cut magnesium-
high danger to fire!
The proper use also includes
compliance with the operating and
maintenance instructions given in this
manual.
The machine must be operated only
by persons familiar with its operation
and maintenance and who are familiar
with its hazards.
The required minimum age must be
observed
The machine must only be used in a
technically perfect condition
When working on the machine, all
safety mechanisms and covers must
be mounted.
In addition to the safety requirements
contained in these operating
instructions and your country’s
applicable regulations, you should
observe the generally recognized
technical rules concerning the
operation of metalworking machines.
Any other use exceeds authorization.
In the event of unauthorized use of the
machine, the manufacturer renounces
all liability and the responsibility is
transferred exclusively to the operator.
3.2 General safety notes

Metalworking machines can be
dangerous if not used properly.
Therefore the appropriate general
technical rules as well as the following
notes must be observed.
Read and understand the entire
instruction manual before attempting
assembly or operation.
Keep this operating instruction close
by the machine, protected from dirt
and humidity, and pass it over to the
new owner if you part with the tool.
No changes to the machine may be
made.
Daily inspect the function and
existence of the safety appliances
before you start the machine.
Do not attempt operation in this case,
protect the machine by unplugging the
mains cord.
Remove all loose clothing and confine
long hair.
Before operating the machine, remove
tie, rings, watches, other jewellery,
and roll up sleeves above the elbows.
Wear safety shoes; never wear leisure
shoes or sandals.
Always wear the approved working
outfit
Do not wear gloves while operating
this machine.
For the safe handling of saw blades
wear work gloves.
Insure that the workpiece does not roll
when cutting round pieces.
Use suitable table extensions and
supporting aids for difficult to handle
workpieces.
Always adjust the blade guide close to
the workpiece.
Remove cut and jammed workpieces
only when motor is turned off and the
machine is at a complete standstill.
Install the machine so that there is
sufficient space for safe operation and
workpiece handling.
Keep work area well lighted.
The machine is designed to operate in
closed rooms and must be placed
stable on firm and levelled ground.
Make sure that the power cord does
not impede work and cause people to
trip.
Keep the floor around the machine
clean and free of scrap material, oil
and grease.
Stay alert!
Give your work undivided attention.
Use common sense.
Do not operate the machine when you
are tired.
Do not operate the machine under the
influence of drugs, alcohol or any
medication. Be aware that medication
can change your behaviour.
Keep children and visitors a safe
distance from the work area.
Never reach into the machine while it
is operating or running down.
Never leave a running machine
unattended.
Before you leave the workplace switch
off the machine.
Do not operate the electric tool near
inflammable liquids or gases.
Observe the fire fighting and fire alert
options, for example the fire
extinguisher operation and place.
Do not use the machine in a dump
environment and do not expose it to
rain.
Specifications regarding the maximum
or minimum size of the workpiece
must be observed.
Do not remove chips and workpiece
parts until the machine is at a
complete standstill.
Never operate with the guards not in
place – serious risk of injury!
Connection and repair work on the
electrical installation may be carried
out by a qualified electrician only.
Have a damaged or worn cord
replaced immediately.
Make all machine adjustments or
maintenance with the machine
unplugged from the power source.
Remove defective saw blades
immediately.
3.3 Remaining hazards
When using the machine according to
regulations some remaining hazards
may still exist
The moving saw blade in the work
area can cause injury.
Broken saw blades can cause injuries.
Thrown cutting chips and noise can be
health hazards.
Be sure to wear personal protection
gear such as safety goggles and ear
protection.
The use of incorrect mains supply or a
damaged power cord can lead to
injuries caused by electricity.
4. Machine specifications
4.1 Technical data
Cutting capacity 90° Ø180 mm
□180 mm
65x300 mm
Cutting capacity 45° Ø110 mm
□180x110 mm
Vice adjustment 0° - 45°
Vice bed above floor 585 mm
Wheel diameter 300 mm
Sawblade size 20x0,9x2362 mm
Cutting speeds 20/ 32/ 45/ 72 m/min
Coolant tank 10 litre
Coolant pump 0,13 HP
Overall LxWxH 1250x520x960 mm
Weight 145 kg
Mains 230V ~1/N/PE 50Hz
Output power 0,55 kW (0,75 HP)-S1
Reference current 5 A
Extension cord (H07RN-F): 3x1,5mm²
Installation fuse protection 10 A
Mains 400V ~3/PE 50Hz
Output power 0,75 kW (1 HP)-S1
Reference current 3 A
Extension cord (H07RN-F): 5x1,5mm²
Installation fuse protection 10 A
4.2 Noise emission
Acoustic pressure level (EN 11202):
Idling 74,1 dB (A)
Operating 85 dB (A)
The specified values are emission
levels and are not necessarily to be
seen as safe operating levels.
As workplace conditions vary, this
information is intended to allow the
user to make a better estimation of the
hazards and risks involved only.
4.3 Contents of delivery
Machine stand with wheels
20mm bimetal sawblade
Adjustable material stop
Belt drive and cover
Hydraulic cylinder
Coolant facility
Assembly kit
Operating manual
Spare parts list
5. Transport and start up
5.1 Transport and installation

Lift machine off the pallet to the
desired location.
Use lifting straps and place them as
shown in Fig 1.
Fig 1
Warning:
The machine weight is 145 kg.
Assure the sufficient load capacity
and proper condition of your lifting
devices.
Never step underneath suspended
loads.
The machine is designed to operate in
closed rooms and must be placed
stable on firm and levelled ground.
For packing reasons the machine is
not completely assembled.
5.2 Assembly
If you notice any transport damage
while unpacking, notify your supplier
immediately. Do not operate the
machine!
Dispose of the packing in an
environmentally friendly manner.
Clean all rust protected surfaces with
a mild solvent.
Place the machine stable on wooden
blocking.
Wheel mount
Slide the axles (A, Fig 2) through the
swivel base and place one wheel (B)
on each side before you secure with
the supplied split pins (C).
Fig 2
Material stop mount
Insert the stop rod (A, Fig 3) into the
bed and tighten the screw (B).
Slide stock stop (C) onto the rod and
tighten the thumb screw (D).
Fig 3
Pulley cover mount
Slide the belt cover over the pulley
assemblies and fasten with screws
and washers (A, Fig 4).
Close belt cover and secure with lock
knob (B, Fig 4)
Fig 4
Coolant Tank Preparation
Use of a water-soluble coolant will
increase cutting efficiency and prolong
blade life.
Follow manufacturers instructions as
to its uses and precautions.
Fill the tank to approximately 80% of
capacity.
5.3 Mains connection
Mains connection and any extension
cords used must comply with
applicable regulations.
The mains voltage must comply with
the information on the machine
licence plate.
The mains connection must have a
10A surge-proof fuse.
Only use power cords marked
H07RN-F
Connections and repairs to the
electrical equipment may only be
carried out by qualified electricians.
5.4 Starting operation
You can start the machine with the
green on button (A, Fig 5). The red
button (B) on the switch box stops the
machine.
The coolant pump (C) can be
switched on and off independently.
The switch cover (D) has an
emergency stop function and can be
used to lock the machine.
Fig 5
Note:
The saw is equipped with an
automatic Shut-Off.
The saw should stop just after the cut
has been completed. The stop tip has
to be adjusted accordingly.
6. Machine operation
Support long workpieces with helping
roller stands.

Work only with a sharp and flawless
sawblade.
Don’t take measurements when the
machine is running
Don’t chuck too short in vice.
Use the coolant facility to keep cutting
temperatures down, reduce friction
and extend the life of your sawblade.
Make sure the cutting liquid is properly
contained to the machine.
Use only water soluble cutting
emulsions and dispose of it in an
environmentally friendly manner.
Don’t cut magnesium-
high danger to fire!
7. Setup and adjustments
General note:
Setup and adjustment work may
only be carried out after the
machine is protected against
accidental starting by pulling the
mains plug.
7.1 Changing blade speed
The general rule is the harder the
material being cut, the slower the
blade speed.
20 m/min
for tool steel, alloy steel and bearing
bronzes.
32 m/min
for mild steel, hard brass or bronze.
45 m/min
for soft brass
72 m/min
for aluminium or other light materials.
Disconnect the machine from the
power source.
Place saw arm in the horizontal
position.
Loosen the motor plate lock bolt (A,
Fig. 6).
Loosen belt tension on the hex cap
bolt and nut (B)
Fig 6
Open pulley cover and place the belt
on the desired pulley combination.
Tension the belt (don’t over tighten the
belt).
Tighten the bolt (A).
Close the pulley cover and connect to
power source.
7.2 Changing sawblade
Disconnect the machine from the
power source.
The sawblade has to meet the
technical specification.
Check sawblade for flaws (cracks,
broken teeth, bending) before
installation. Do not use faulty
sawblades.
Always wear suitable gloves when
handling sawblades.
Turn away the saw arm stop bracket
(A, Fig 7).
Fig 7
Raise the saw arm to the vertical
position and lock in place.
Open the wheel cover.
Remove the red blade guards and the
brush assembly.
Release the blade tension and
remove the blade.
Place new blade and make sure the
teeth are pointing the cutting direction
(Fig, 8).
Fig 8
Turn the blade tension knob until the
proper blade tension is achieved at
green block of tension scale (C, Fig
9).
Fig 9
Place a few drops of lightweight oil on
the blade.
Install the red blade guard, the brush
assembly and the wheel cover.
Reposition the arm stop bracket.
Warning:
It is essential that the two red
guards and the wheel cover are
installed after the new blade has
been fitted. Failure to comply may
cause serious injury!
Connect to the power source.
7.3 Blade guides adjustment
Disconnect the machine from the
power source.
Loosen the lock knobs (A, B, Fig 10).

Slide blade guide assemblies as close
as possible without interfering the
material being cut.
Fig 10
7.4 Guide bearing adjustment
Disconnect the machine from the
power source.
Loosen nut (B, Fig 11) and turn
eccentric shaft to adjust bearing to a
clearance of 0,05mm. Tighten nut to
lock.
Fig 11
Fig 12
Place a machinist's square on the
table and check that blade is square
Fig 12.
If adjustment is necessary, loosen bolt
(A) and rotate the blade guide
assembly.
7.5 Blade tracking adjustment
Warning:
Blade tracking adjustment requires
running the saw with the wheel
cover open. This adjustment must
be completed by qualified persons
only.
Failure to comply may cause
serious injury!
The blade tracking has been set at the
factory and should not need
adjustments.
Confirm that the blade tension is set
properly.
Run the saw at lowest speed.
The blade should run next to but not
tightly against the wheel flange.
If blade tracking needs to be adjusted
loosen the bolt (A, Fig 13).
Fig 13
Turning the set screw (B) clockwise
tracks the blade closer to the wheel
flange.
The tracking is sensitive, start with ¼
turn of the set screw.
Once tracking is set, tighten bolt (A)
firmly.
7.6 Feed speed adjustment
You can control the sawblade
downward feeding with the valve
control knob (A, Fig 14) and lock the
saw with the on/off valve (B).
Fig 14
The cutting of thin-walled workpieces
(profiles, tubes etc.) requires slow
feeding to avoid excessive wear of
sawblade.
Adjusting bow weight
Bow weight has been set at the
factory and should not need
adjustment .
Adjustment can be made on screw (A,
Fig 15) :
Fig 15
7.7 Vice adjustment
Use the handle (A, Fig 16) to open
and close the vice for clamping.
The vice can be adjusted for square
and mitre cuts. Loosen the hex cap
bolts (C) and adjust the vice for the
cut.

Fig 16
Adjust the movable vise parallel to the
fixed vise by loosening bolt (A, Fig.17).
Fig 17
There is a scale on the back side of
the bed to aid in setting up the vice.
(Always check the vice setup with a
combination square against the blade
and vice).
To set vise for maximum width of
stock cutting remove the nut and bolt
assemblies (C, Fig 16).
8. Maintenance and inspection
General notes:
Maintenance, cleaning and repair
work may only be carried out after
the machine is protected against
accidental starting by pulling the
mains plug.
Repair and maintenance work on the
electrical system may only be carried
out by a qualified electrician.
Clean the machine regularly.
Only use sharp and properly set saw
blades.
Replace a defective sawblade
immediately.
All protective and safety devices must
be re-attached immediately after
completed cleaning, repair and
maintenance work.
Defective safety devices must be
replaced immediately.
Regularly lubricate the vice lead screw
with grease.
Changing Gearbox Oil:
Change gear box oil after the first 3
months of operation (respectively after
50 operating hours).
There after, change the oil once a
year (respectivel every 500 operating
hours)
Disconnect the machine from the
power source.
Place the saw arm in the horizontal
position.
Remove screws (A, Fig. 18) from the
gear box and remove the cover plate
and gasket.
Fig 18
Hold a container under the lower right
corner of the gear box while slowly
raising the saw arm.
Place the saw arm in the horizontal
position again.
Wipe out remaining oil with a rag.
Fill the gear box with approximately
0,350 liters of
Mobil Gear 634 ( ISO VG 460)
gear oil or equivalent.
Replace the gasket and cover.
9. Trouble shooting
Motor doesn’t start
*No electricity-
check mains and fuse.
*Defective switch, motor or cord-
consult an electrician.
Machine vibrates excessively
*Stand on uneven floor-
adjust stand for even support.
*sawblade has cracks-
replace sawblade immediately
*Tool heavy a cut-
reduce feed pressure and feed speed.
Cut is not square
*Vice setting is bad.
*Blade guide setting is bad.
*Sawblade is dull.
Cutting surface is bad
*Wrong sawblade chosen
*Sawblade is dull
*Blade guide setting is bad
*Blade tension too low
*Feed pressure too high
*Feed speed too high
10. Available accessories
Refer to the JET-Pricelist
for various saw blades.
Other manuals for HVBS-712K
1
Table of contents
Other Jet Saw manuals
Popular Saw manuals by other brands

Parkside
Parkside 308629 1910 Translation of the original instructions

Metabo
Metabo KGS 301 Operating instruction
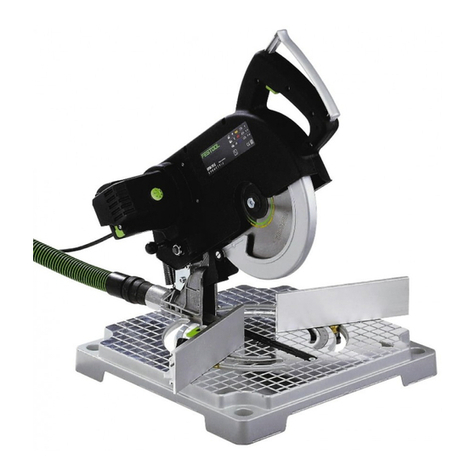
Festool
Festool Symmetric SYM 70 E Original operating manual
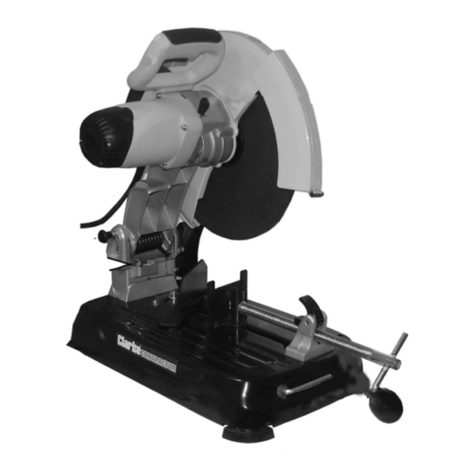
Clarke
Clarke CON14 Operation & maintenance instructions
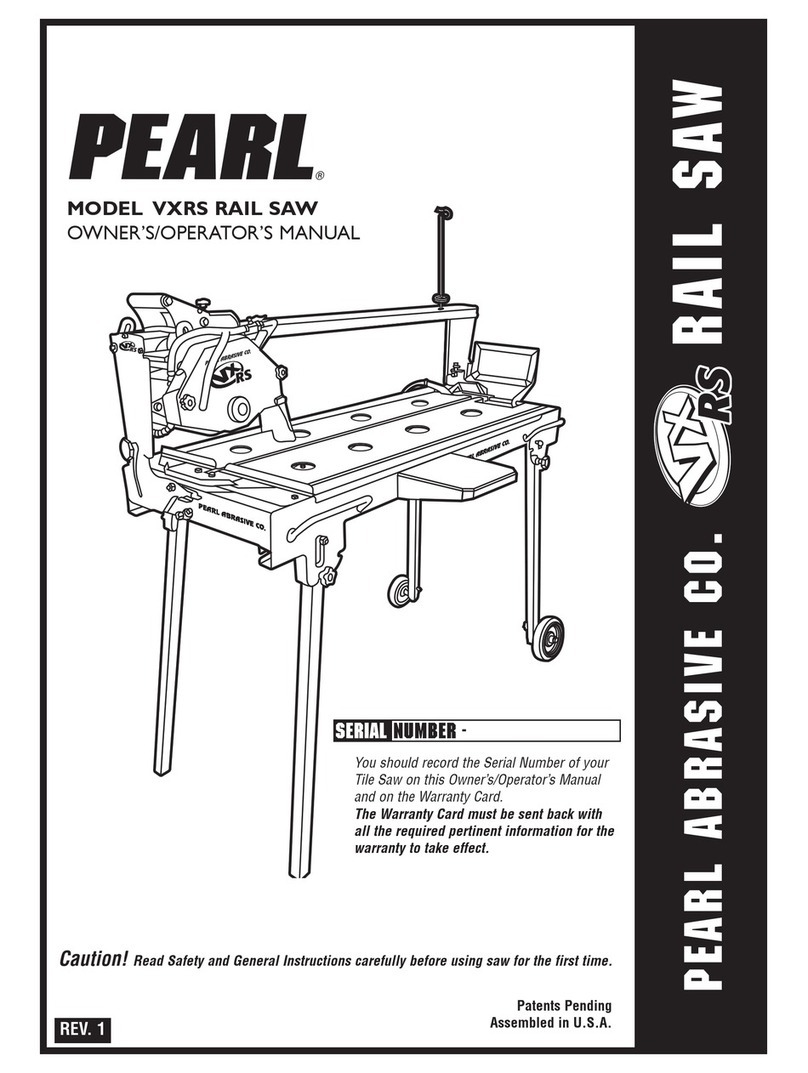
Pearl Abrasive
Pearl Abrasive X10RS Owner's/operator's manual
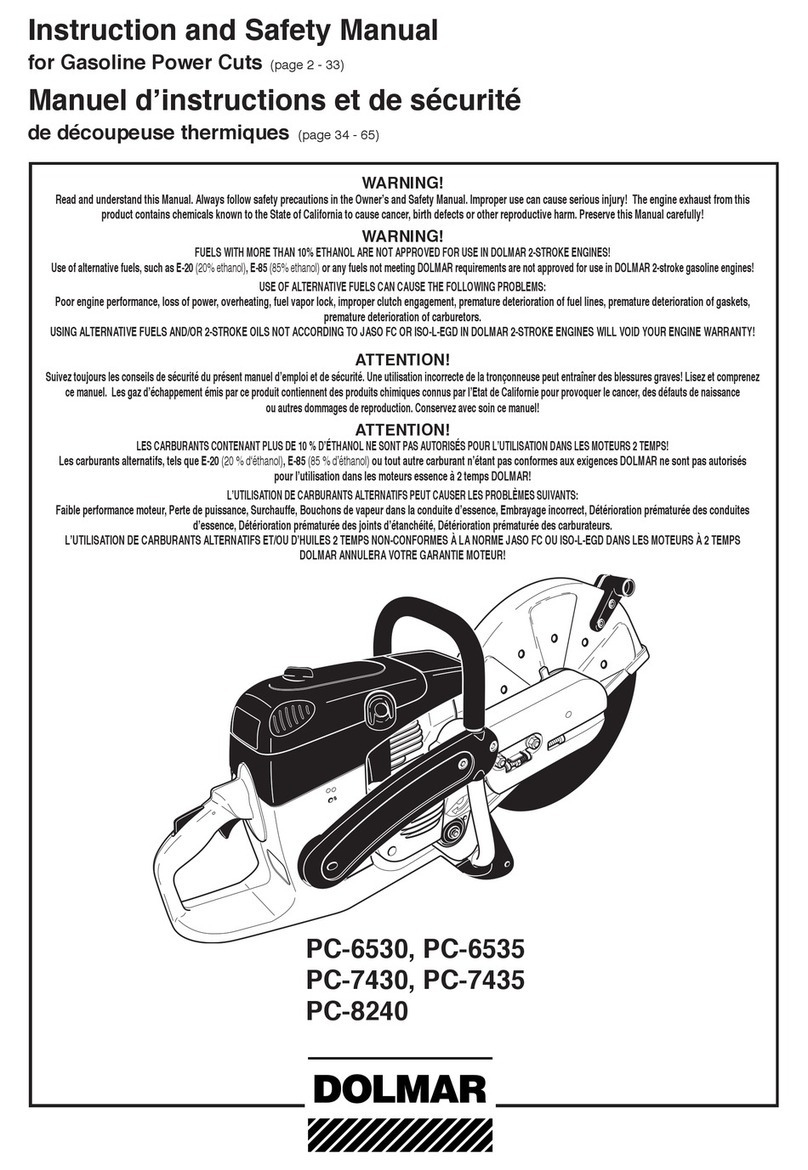
Dolmar
Dolmar PC-6530 Instruction and safety Instruction and safety manual