Jordan Valve I & M Mark 58/586 Series Installation and operating instructions

3170 Wasson Road • Cincinnati, OH 45209 USA
Phone 513-533-5600 • Fax 513-871-0105
[email protected] • www.jordanvalve.com
I & M Mark 58/586 (Air Loaded) Series
Installation & Maintenance Instructions for
Mark 58/586 Back Pressure Regulating & Relief Valve
Warning: Jordan Valve back pressure regulators must only be used, installed and repaired in accordance with these
Installation & Maintenance Instructions. Observe all applicable public and company codes and regulations. In the
event of leakage or other malfunction, call a qualified service person; continued operation may cause system failure
or a general hazard. Before servicing any valve, disconnect, shut off, or bypass all pressurized fluid. Before disas-
sembling a valve, be sure to release all spring tension.
Please read these instructions carefully!
Your Jordan Valve product will provide you with long,
trouble-free service if it is correctly installed and main-
tained. Spending a few minutes now reading these in-
structions can save hours of trouble and downtime later.
When making repairs, use only genuine Jordan Valve
parts, available for immediate shipment from the factory.
Ideal Installation
1. To protect the valve from grit, scale, thread chips,
and other foreign matter, all pipe lines and piping
components should be blown out and thoroughly
cleaned before the valve is installed.
2. Shutoff valves, pressure gauges, and bypass piping
should be installed as indicated in the diagram to
provide easier adjustment, operation, and testing.
3. A line strainer should be installed on the inlet side of
the regulator to protect it from grit, scale and other
foreign matter. A 0.033 perforated screen is usually
suitable. Line strainers are available from Jordan Valve.
4. For best control, 3’0” straight sections of pipe should
be installed on either side of the valve.
5. Install the regulators in the highest horizontal line of
piping to provide drainage for inlet and outlet pip-
ing, to prevent water hammer, and to obtain faster
regulation.
6. The regulator may be installed in a flow-through
manner as in Figure 1 or into a tee off of the main
line (with one port plugged) as shown in Figure 2.
Flow may be in either direction through the body of
the regulator. Bypassed fluid exits out of the bottom
bypass port.
7. In hot vapor lines, upstream and downstream piping
near the regulator should be insulated to minimize
condensation.
8. Expand the outlet piping at least one pipe size if the
outlet pressure (downstream) is 25% of the inlet
pressure or less. As standard tapered expander con-
nected to the outlet of the regulator is recommend-
ed. Minimizing bypass piping length and number of
elbows will improve valve performance by reducing
pressure buildup.
9. Where surges are severe, a piping accumulator is
recommended.
Condensate
Return
6
1 Inlet shut-off valve
2 MK 58 BPRV
3 Strainer and Drain Valve
4 Pressure Gauge
Ideal Installation
442
1
6
7
5
3
Main Line
Main Line
Condensate
Return
By Pass
3
6
5
1
42
7
4
8
By Pass
5 Steam trap and valve
6 Manual bypass valve
7 Bypass shut-off valve
8 Pipe plug

Plug Removal & Diaphragm
Replacement
1. Remove all pressure from the line as outlined under
Warning.
2. Remove the compression of the adjusting spring (11)
by rotating the adjusting screw (14) counterclock-
wise.
3. Remove the spring housing (9). Remove spring (11),
spring seat (12) and ball bearing (13).
4. Remove the diaphragm assembly. The diaphragm
assembly consists of the upper diaphragm plate (8),
diaphragm washer (7), washer (6), stem (5) and plug
(4). The plug is attached loosely to the stem. DO
NOT DROP.
5. Secure the upper diaphragm plate in a vise. Use a
wrench on the stem and turn counter-clockwise to
remove.
6. Remove the diaphragm, clean the parts and install
the new diaphragm in reverse order. The radius
edge of the washer goes against the diaphragm.
Clean and degrease the stem threads and apply one
drop of #290 Loctite to them before threading the
stem into the diaphragm plate. When an elastomer
diaphragm is used, thread the parts together hand
tight and then tighten 1/4 turn. When a metal dia-
phragm is used, pull the parts up together tight.
7. Clean the diaphragm seating surfaces on the spring
housing (9) and on the body (1). Remove adjusting
screw (14).
8. Unscrew the cage (2) approximately two turns. Place
the plug, diaphragm assembly, spring, spring seat
and ball bearing back into the valve body. (Metal
diaphragms nest into the counterbore in the body).
Do not lubricate the plug.
9. Install spring housing.
10. Check to see that ball is below the tapped hole for
the adjusting screw and reinstall adjusting screw to
contact ball.
11. Tighten bolts (10) evenly per chart on next page.
12. Thread cage back into the body and pull up snug.
Readjust adjusting screw.
Cage Removal
1. Remove all pressure from the line as outlined under
Warning.
2. Remove the compression of the adjusting spring
(11) by rotating the adjusting screw (14) counter-
clockwise.
3. Turn the hux end on the cage (2) counter-clockwise
and remove it from the body. The o-ring (3) which is
used to seal the cage to the body main remain on
the cage or stay in the body when you remove the
cage.
4. Place the cage in a vise and grip it on the hex to
prevent damage to machined surfaces. The plug will
Start-up Procedure
With the inlet and outlet shut-off valves closed:
1. Throttle the manual bypass valve so that the pres-
sure to be controlled is maintained near the set
point.
2. Slowly open the inlet shut-off valve.
3. Open the outlet shut-off valve.
4. Slowly close the bypass valve, but do not close it
fully until you are certain that the regulator has con-
trol of the system.
5. To change the controlled pressure, turn the adjust-
ing screw clockwise to increase pressure, counter-
clockwise to decrease pressure.
WARNING:
6. Never substitute a longer length adjusting screw.
Personal injury and damage to the valve may result.
Troubleshooting
Erratic Control:
1. Oversizing causes cycling and hunting and reduces
the rangeability of the valve. Make certain that your
sizing is correct.
2. Steam traps downstream may need attention.
3. Safety valve may be jammed open.
4. Excessive foreign matter on seats or plug (4*). Clean
them. Inspect seating surface on plug for deterioration.
5. Valve plug may not be moving freely. Check cage
bore (2).
6. Surges in piping system.
7. Check accumulator.
Will not operate:
1. Diaphragm ruptured. Replace.
2. Adjusting spring broken. Replace.
3. Improper spring setting. Reset.
Maintenance
Warning:
Be sure that there is no pressure in the valve before
loosening any fittings or joints. The following steps are
recommended.
1. Close the inlet shut-off valve.
2. Back off adjusting screw to allow inlet pressure to
open seats.
3. Allow pressure to bleed off through downstream
piping.
4. When inlet pressure gauge indicates no pressure in
the line, close the outlet shut-off valve.
5. Valve may now be removed or serviced.
* Refer to the drawings for the proper orientation of the
parts and for proper nomenclature.

-3-
remain with the stem. To remove plug see preceding
section.
5. Inspect parts for wear and replace as required. It is
recommended that the o-ring be replaced.
6. Clean all parts and the o-ring seating surfaces in the
body and on the cage. Lightly lubricate these sur-
faces and the o-ring. Do not lubricate bore of cage
where the plug operates.
7. Check to see that the ball (13) is below the tapped
hole for the adjusting screw and reinstall the adjust-
ing screw to just contact the ball.
8. Install the cage o-ring and screw the cage into the
body until it bottoms out and tighten. Readjust ad-
justing screw.
Torque Procedure
1. Install all bolts hand-tight.
2. Torque the bolts in order of the bolt pattern to a
value equal to 1/4 of the recommended torque
valve.
3. Retorque each bolt to recommend value using the
same bolt pattern as shown.
When ordering spare parts, first make a note of the fol-
lowing information on the valve’s nameplate:
— Serial Number
— Model and Size
— Body Material and End Connections
— Range
53
1
6
4
2
5
3
1
64
2
7
8
6 bolts (or multiples) 8 bolts (or multiples)

Cross Section View
3170 Wasson Road • Cincinnati, OH 45209 USA
Phone 513-533-5600 • Fax 513-871-0105
[email protected] • www.jordanvalve.com
Bulletin IM-MK58-0915
3
1
10
4
7
2
9
8
12
1By-Pass
Item Description
1 Body
2 Cage Sub-Assembly*
3 O-Ring
4 Plug
5 Stem
6 Washer
7 Diaphragm
8 Upper Diaphragm Plate
9 Spring Housing
10 Cap Screw
11 Range Spring
12 Spring Seat
14 Adjusting Screw
15 Jam Nut
16 Name Plate
* Consists of seat, seat o-ring,
and cage
5
6
11
16
15
14
Other Jordan Valve Control Unit manuals
Popular Control Unit manuals by other brands
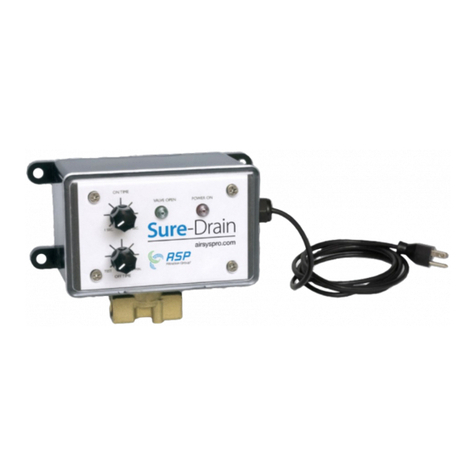
ASP
ASP Sure-Drain SD11 Installation & operation manual
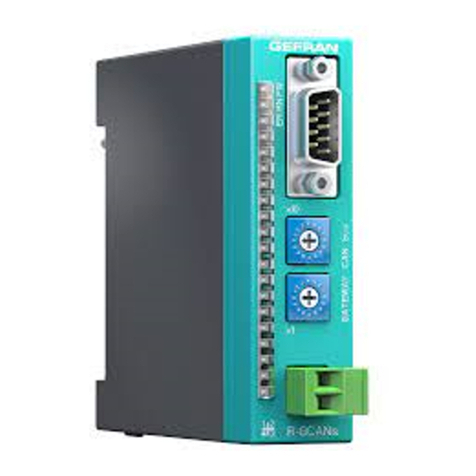
gefran
gefran R-GCANs Installation and operation manual
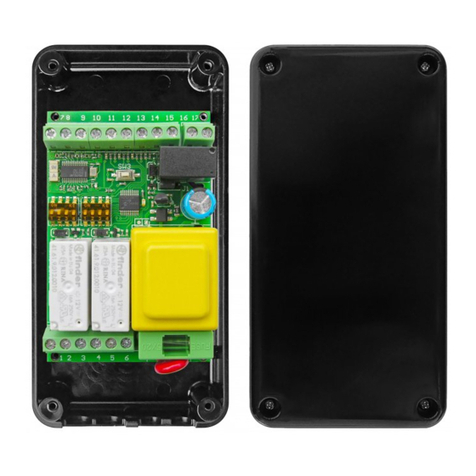
EB TECHNOLOGY
EB TECHNOLOGY START-S1XL v2 operating guide

Honeywell
Honeywell Braukmann T100A Product data
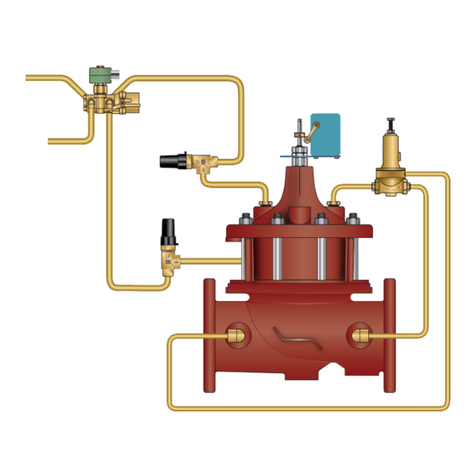
Watts
Watts 985GD-20 Installation, operation and maintenance

Ebyte
Ebyte E70 Series user manual