dymax 210 User manual


2
Dymax Model 110 & 210 Spray Valves User Guide
About Dymax
UV/Visible light-curable adhesives. Systems for light curing, fluid dispensing, and fluid packaging.
Dymax manufactures industrial adhesives, light-curable adhesives, epoxy resins, cyanoacrylates, and activator-
cured adhesives. We also manufacture a complete line of manual fluid dispensing systems, automatic fluid
dispensing systems, and light-curing systems. Light-curing systems include LED light sources, spot, flood, and
conveyor systems designed for compatibility and high performance with Dymax adhesives.
Dymax adhesives and light-curing systems optimize the speed of automated assembly, allow for 100% in-line
inspection, and increase throughput. System designs enable stand-alone configuration or integration into your
existing assembly line.
Please note that most dispensing and curing system applications are unique. Dymax does not warrant the fitness
of the product for the intended application. Any warranty applicable to the product, its application and use is
strictly limited to that contained in the Dymax standard Conditions of Sale. Dymax recommends that any
intended application be evaluated and tested by the user to insure that desired performance criteria are satisfied.
Dymax is willing to assist users in their performance testing and evaluation. Data sheets are available for valve
controllers or pressure pots upon request.

Dymax Model 110 & 210 Spray Valves User Guide
3
Contents
Introduction ......................................................................................................... 4
Introduction to the User Guide .........................................................................4
Where to Get Help ............................................................................................4
Safety................................................................................................................... 5
General Safety Considerations..........................................................................5
Specific Safety Considerations ..........................................................................5
Product Overview................................................................................................. 6
Description of the Dymax Spray Valves.............................................................6
Component Overview .......................................................................................6
Special Features and Benefits of the Dymax Spray Valve .................................8
Assembly and Setup ............................................................................................. 8
Unpacking and Inspecting Your Shipment ........................................................8
Parts Included in the Spray Valve......................................................................8
System Interconnect .........................................................................................9
Operating the Dispensing Valve.......................................................................... 11
Setup and Operation.......................................................................................11
Maintenance and Cleaning ................................................................................. 12
General Valve Maintenance............................................................................12
Routing Cleaning and Disassembly..................................................................12
Assembly Instructions .....................................................................................14
Troubleshooting ................................................................................................. 16
Spare Parts and Accessories ............................................................................... 17
Options/Accessories........................................................................................17
Specifications ..................................................................................................... 18
Specifications ..................................................................................................18
Warranty............................................................................................................ 19

4
Dymax Model 110 & 210 Spray Valves User Guide
Introduction
Introduction to the User Guide
This guide describes how to use the Dymax Model 110 standard-flow spray valve
(PN T16396) or the Model 210 high-flow spray valve (PN T17287). Sections in this guide
describe how to assemble, use, and maintain these spray valves safely and efficiently.
Intended Audience
Dymax prepared this user guide for experienced process engineers, maintenance
technicians, and manufacturing personnel. If you are new to pneumatically-operated
fluid spray equipment and do not understand the instructions, contact the Dymax
technical support team to answer your questions before using the equipment.
Where to Get Help
Dymax Customer Support and Application Engineering teams are available in the United
States, Monday through Friday, from 8:00 a.m. to 5:30 p.m. Eastern Standard Time. You
can also email Dymax at info@dymax.com. Contact information for additional Dymax
locations can be found on the back cover of this user guide.
Additional resources are available to ensure a trouble-free experience with our
products:
Detailed product information on www.dymax.com
Dymax adhesive Product Data Sheets (PDS) on our website
Material Safety Data Sheets (MSDS) provided with shipments of Dymax adhesives

Dymax Model 110 & 210 Spray Valves User Guide
5
Safety
WARNING! If you use this fluid dispensing equipment without first
reading and understanding the information in this guide, personal injury
can result from the uncontrolled release of high-pressure gas, injection
injury, or exposure to chemicals. To reduce the risk of injury, read and
understand this guide before assembling and using Dymax fluid dispensing
equipment.
General Safety Considerations
All users of Dymax fluid dispensing equipment should read and understand this user
guide before assembling and using the equipment.
To learn about the safe handling and use of dispensing fluids, obtain and read the MSDS
for each fluid before using the fluid. Dymax includes an MSDS with each adhesive sold.
MSDS for Dymax products can also be requested through the Dymax website.
Specific Safety Considerations
Using Safe Operating Pressures
Pressurizing the components in the dispensing system beyond the maximum
recommended pressure can result in the rupturing of components and serious personal
injury. To minimize the risk of rupturing components and injury, do not exceed the
maximum operating pressure of the components in your fluid dispensing system (see
system specifications on page 18).
Preventing Injection Injury
Discharging fluids or compressed air with a dispensing tip against your skin can cause
very serious injection injury. To minimize the risk of injection injury, do not place the
dispensing tip in contact with your skin.

6
Dymax Model 110 & 210 Spray Valves User Guide
Product Overview
Description of the Dymax Spray Valves
The Dymax Model 110 and 210 Spray Valves are low pressure, low volume, front-closing
stainless steel valves. These valves use air pressure to atomize fluids and transfer them
to a substrate. The valves can be used in a wide variety of coating applications, applying
any number of low-to-high viscosity fluids.
The Model 110 is a standard-flow spray valve and should be used with materials that
have a viscosity less than 10,000 cP.
The Model 210 is a high-flow spray valve and should be used with materials that have a
viscosity greater than 10,000 cP.
Component Overview
The valve is comprised of two major sections, the air section (red anodized portion) and
the fluid section (stainless steel portion). The air section of the valve is constructed of
an aluminum body. It contains a simple piston/cylinder combination used to open and
close the valve. This section also houses the stroke-adjustment bolt, which is located in
the upper air body. The stroke-adjustment bolt controls how far the piston and needle
assembly can retract thus regulating the rate of fluid flow.
The second section of the valve, the fluid section, is constructed of stainless steel. It
contains a needle and seat combination, which is located at the end of the Valve inside
the atomizing air cap. Fluid flows through the seat orifice as the needle retracts out of
the seat. The fluid stops as the needle moves back into the Seat. When the needle is
retracted, atomizing air is applied to spray all of the fluid from the air cap. The stroke
adjustment bolt located on the air section of the valve regulates the distance that the
needle can retract out of the seat. This controls the orifice size and the rate of fluid flow.
A precision air regulator is used to control a precise amount of atomizing air. Fluids can
include but are not limited to solvents, conformal coatings, grease, etc.
Wetted parts on the spray valve include: 303, 304 stainless steel, Teflon®, and Kalrez®

Dymax Model 110 & 210 Spray Valves User Guide
7
Figure 1. Model 110 & 210 Component Diagram
Item
Description
Item
Description
A
Air Cap, Round (Flat Available)
M
Upper Air Body
B*
Seat
N
Lock Nut
C
Needle
O
Stroke Adjuster
D*
Fluid Section
P
Machine Screw
E
Packing
Q
Machine Screw
F
Packing Nut
R
Collar Ring
G
Standoff
S
O-Ring
H
End Cap
T
Spring
I
Lower Air Body
U
Set Screw
J
O-Ring
V*
O-Ring
K
Piston
W
Seat Wrench (Not Shown)
L
O-Ring
*These parts are not interchangeable between the standard-flow and high-flow valves
MOUNTING HOLES

8
Dymax Model 110 & 210 Spray Valves User Guide
Special Features and Benefits of the Dymax Spray Valve
Feature
Benefit
Stainless Steel Construction
Compatible with a greater number of fluids
Interchangeable flat or round
spray nozzle
Spray range of 0.25" (6.35 mm) to greater than 2" (50.8 mm)
Lightweight with low trigger
resistance
Ergonomic design allows for hours of effortless spraying
Easy adjustment of material
flow and spray atomization
Greater dispensing accuracy with less material waste
Assembly and Setup
Unpacking and Inspecting Your Shipment
When your spray valve arrives, inspect the boxes for damage and notify the shipper of
box damage immediately.
Open each box and check for equipment damage. If parts are damaged, notify the
shipper and submit a claim for the damaged parts. Contact Dymax so that new parts can
be shipped to you immediately.
Check that the parts included in your order match those listed below. If parts are
missing, contact your local Dymax representative or Dymax Customer Support to resolve
the problem.
Parts Included in the Spray Valve
■Spray valve (round cap)
■Spray valve user guide

Dymax Model 110 & 210 Spray Valves User Guide
9
System Interconnect
Air
The valve is a normally-closed spray valve. It requires a 2-position, 4-way air solenoid
valve to actuate the air section. The valve should be operated with clean, dry air
between 60-100 psi. Two #10-32 threaded air ports are located on the air section of the
valve. The air port located furthest from the midsection of the valve is the air line to
close the valve. The air port located closest to the mid-section of the valve is the air line
to open the valve. Quick-connect air fittings are typically supplied with the spray valve
to fit 5/32" tubing.
Atomizing air is connected to the valve through the #10-32 threaded port located on the
fluid section (D). The atomizing air should be connected so that it turns on only when
the valve is cycled to the open position. There are two configurations that can be used
to connect the atomizing air.
The first configuration uses a single solenoid with one output. This configuration can be
seen in Figure 2. The single solenoid in this configuration is used to simultaneously open
the valve and pressurize the atomizing air regulator.
The second configuration, which can be seen in Figure 3, uses a dual solenoid to allow
independent control of the atomizing air.
Fluid
The spray valve requires a material reservoir or pressure tank to draw material from.
The material reservoir should be connected to the valve via the 3/8" OD push-to-
connect fitting already installed on the stainless steel fluid section (D) of the valve.

10
Dymax Model 110 & 210 Spray Valves User Guide
Figure 2. Single Solenoid Setup Configuration
Figure 3. Dual Solenoid Setup Configuration

Dymax Model 110 & 210 Spray Valves User Guide
11
Operating the Dispensing Valve
Setup and Operation
Refer to Figure 1 for part reference designation.
1. Plumb the valve as outlined in the set-up procedures.
2. Regulate the air pressure operating the valve between 60-100 psi.
3. Making sure that the valve is not aimed toward anyone, cycle the valve several
times. When the valve is cycling, the Piston (K) can be heard hitting the Stroke
Adjuster (O), and the Needle (C) can be seen going up and down in the center.
4. Adjust the atomizing Air Pressure Regulator between 1-2 psi. Air should be felt
flowing from the end of the valve when the valve cycles open.
NOTE: If the valve is not cycling properly, refer to the Troubleshooting Section of
this manual.
5. When the Fluid Delivery System is connected to the valve, pressurize the material
to be dispensed.
6. Once again, cycle the valve open to purge. Fluid should begin to spray from the tip
of the Air Cap (A).
7. Continue cycling the valve until all air is removed from the Fluid Line and a steady
spray pattern of material can be seen.
8. Adjust the atomizing air pressure to achieve proper spray of material. This pressure
will vary due to the viscosity of the fluid.
9. Check the Fluid Connection and Packing Nut (F) for leaks. If the valve is leaking,
refer to the Troubleshooting Section of this manual.
10. Turn the Stroke Adjuster (O) until the desired flow rate is achieved. Turning the
Stroke Adjuster (O) clockwise will decrease the material flow rate and counter-
clockwise will increase the material flow rate. If the Stroke Adjuster (O) is turned
all the way down, it will stop fluid flow entirely.
11. Once the stroke adjustment setting is determined, use an adjustable wrench to
tighten the Lock Nut (N) up against the Upper Air Body (M).
NOTE: Refer to the Troubleshooting Section for any problems.

12
Dymax Model 110 & 210 Spray Valves User Guide
Maintenance and Cleaning
General Valve Maintenance
Lubricate the Packing (E) on the valve every 200 hours by placing a few drops of mineral
oil or other light oil inside the Packing Nut (F).
The Packing Nut (F) will require occasional tightening as wear occurs in order to prevent
leaks through the Packing (E).
Routing Cleaning and Disassembly
Cleaning and rebuilding the valve will be required from time-to-time. A spare parts kit is
available with all the normal wear parts included. Refer to Figure 1 for part reference
designation.
1. Begin disassembly by removing air and fluid pressure from the valve.
2. Remove all pneumatic tubing and fluid delivery fittings, hoses, etc. from the valve.
3. Loosen the Packing Nut (F) by using the tip of a 3/32" Allen key.
4. Remove the two Machine Screws (Q) located on the same corners as the Standoffs
(G) with a 3/32" Allen key.
NOTE: During removal, the valve’s Spring (T) will force the air section away from
the fluid section.
5. Pull the Air Section (M, I) away from the Fluid Section (D).
6. Clean off the tip of the stainless steel Needle (C).
7. Unthread and remove the Packing Nut (F) and Packing (E) from the fluid section (D)
of the valve.
8. Using soft tip pliers unthread and remove the two Standoffs (G) from the fluid
section (D).
9. Unthread and remove the Collar Ring (R) followed by the Air Cap (A).

Dymax Model 110 & 210 Spray Valves User Guide
13
10. Using a seat wrench, unthread and remove the Seat (B) and the 007 Kalrez® O-Ring
(V).
NOTE: The teeth of the seat wrench are tapered so the wrench will only fit on one
side.
11. Clean all of the wetted parts thoroughly with an appropriate solvent.
12. On the Air Section (A), remove the final two Machine Screws (P) that thread into
the End Cap (H) by using a standard 3/32" Allen key.
NOTE: During removal, the Spring (T) will force the Air Section apart.
13. Separate the Upper Air Body (M) from the Lower Air Body (I) and remove the
Spring (T).
14. Slide the End Cap (H) off the Needle (C).
15. Holding the Lower Air Body (I) in one hand, grab the Needle (C) and push the
Needle and Piston (K) assembly out of the Lower Air Body (I).
16. Remove the 004 Buna O-Ring (S) from the Lower Air Body (I).
17. Hold the Piston (K) with an adjustable wrench and use a 5/64" Allen key to
unthread and remove the Set Screw (U).
18. Remove the Needle (C) and the 014 Buna O-Ring (J) from the Piston (K).
19. Remove the 014 Buna O-Ring (J) from the Upper Air Body (M) and the 008 Buna O-
Ring (L) from the Stroke Adjuster (O).
20. Unthread the Stroke Adjuster (O) from the Upper Air Body (M) and remove the 008
Buna O-Ring (L).
21. Replace all worn components with new components.

14
Dymax Model 110 & 210 Spray Valves User Guide
Assembly Instructions
Refer to Figure 1 for part reference designation.
General
■All O-Rings must be lubricated with a small amount of silicone grease.
■A small amount of removable thread locker should be applied to the Set Screw (U)
and the male threads of the Standoffs (G).
■Assemble the air section (M,I) and fluid section (D) separately prior to connecting
the assemblies.
Air Section
1. Assemble the Stroke Adjuster (O) and Lock Nut (N) with the hex head toward the
knurled end of the bolt.
2. Mount one 008 Buna O-Ring (L) on the inside groove of the Stroke adjuster (O).
3. Assemble the Stroke Adjuster (O) assembly into the Upper Air Body (M).
4. Mount one 014 Buna O-Ring (J) on the end of the Upper Air Body (M) and the other
008 Buna O-Ring (L) on the end groove of the Stroke Adjuster (O).
5. Back out the Stroke Adjuster (O) by turning it counter-clockwise to the end of its
travel.
6. Drop the Needle (C) into the Piston (K) and assemble with the Set Screw (U) using
an adjustable wrench and 5/64" Allen key to tighten.
7. Mount the 014 Buna O-Ring (J) onto the Piston (K).
8. Apply a small amount of silicone grease to the inside of the Lower Air Body (I) then
drop in the Piston (K) and Needle (C) assembly.
9. Mount the 004 Buna O-Ring (S) on the end of the Needle (C) and slide it down into
the groove in the end of the Lower Air Body (I).
10. Slide the End Cap (H) onto the Needle (C) up to the Lower Air Body (I), place the
Spring (T) on top of the Piston (K), and assemble the two air bodies using two
Machine Screws (P) tightening with a 3/32" Allen key.

Dymax Model 110 & 210 Spray Valves User Guide
15
NOTE: Be sure the air holes are lined up on the same face and will align with the
air hole on the Fluid Section (D).
Fluid Section
1. Screw the Standoffs (G) into the Fluid Section (D) using soft tip pliers to tighten.
2. Drop the Packing (E) into the Fluid Section (D), and screw in the Packing Nut (F) but
leave finger tight until assembled with the Air Section (M, I).
3. Mount the 007 Kalrez® O-Ring (V) on the Seat (B) and thread the Seat (B) into the
Fluid Section (D). Tighten using the seat wrench.
4. Place the Air Cap (A) onto the Fluid Section (D) over the Seat (B) and secure it by
threading the Collar Ring (R) in place.
Assemble Sections
1. Back out the Stroke Adjuster (O) by turning it counter-clockwise until the end of its
travel.
2. Apply a small amount of silicone grease to the end of the Needle (C) then insert it
into the Packing Nut (F) and slide the two sections together.
3. Align the air holes of the Air Section (M, I) on the same face as the atomizing air
hole of the Fluid Section (D) then connect the sections using the two Machine
Screws (Q), tightening them down evenly using a 3/32" Allen key.
4. Using the tip of a 3/32" Allen key, tighten the Packing Nut (F).

16
Dymax Model 110 & 210 Spray Valves User Guide
Troubleshooting
Table 1. Troubleshooting Chart for the Dymax Spray Valve
Problem
Possible Cause
Corrective Action
Valve does not
cycle
Air pressure to air section too
low
Increase air pressure to 60-100 psi
Packing Nut (F) is too tight
Loosen Packing Nut (F) until valve
just begins to cycle, retighten
Stroke Adjuster (O) is bottomed
out
Back out Stroke Adjuster (O) by
turning it counter-clockwise
Material is cured in the valve
Disassemble and clean valve
Valve was assembled without
lubricating the O-ring seals
Disassemble valve, lubricate seals
and re-assemble
Material leaks
from valve tip
Needle (C) and/or Seat (B) are
worn
Replace parts as necessary
Seat (B) is not tightened enough
against Fluid Section (D)
Use seat wrench to tighten Seat
(B) onto Fluid Section (D)
Valve leaks from
mid-section
Packing Nut (F) is loose
Tighten Packing Nut (F) until snug
Packing (E) is worn
Replace Packing (E)
Valve does not
spray anything
Fluid pressure is to low
Increase fluid pressure
Material cured in Fluid Section (D)
Disassemble valve and clean
Air bubbles in
fluid
Valve not properly purged
Flip valve upside down and cycle
until air bubbles are removed
Problem with fluid delivery
system
Diagnose and repair
Atomizing air pressure set too
high
Reduce atomizing air pressure
Spray rate too
fast
Stroke Adjuster (O) set out too
far
Turn Stroke Adjuster (O) clockwise
toward the zero mark
Spray rate too
slow
Stroke Adjuster (O) set too
close to the zero mark
Turn Stroke Adjuster (O) counter-
clockwise

Dymax Model 110 & 210 Spray Valves User Guide
17
Table 1 Continued
Problem
Possible Cause
Corrective Action
Poor spray pattern
Cured material at tip of
Needle (C) and Seat (B)
Remove air cap and clean tip
Cured material in Air Cap (A)
Remove air cap and clean
Incorrect atomizing air
pressure
Adjust atomizing air pressure
Damaged Needle (C) and or
Seat (B)
Replace parts as necessary
Spare Parts and Accessories
Options/Accessories
Item
Part Number
Nozzles
Flat Spray Nozzle
T15697
Parts Kits
Model 110 (Standard-Flow Valve) Spare Parts Kit
includes seat, seat wrench, needle, Teflon packing, and Buna and Kalrez o-rings
T15696
Model 210 (High-Flow Valve) Spare Parts Kit
includes seat, seat wrench, needle, Teflon packing, and Buna and Kalrez o-rings
T17288
Stands
Front Closing Stand with Drip Cup
T15454

18
Dymax Model 110 & 210 Spray Valves User Guide
Specifications
Specifications
Property
Specification
Part Numbers
T16396 Model 110 standard-flow spray valve with round cap
T17287 Model 210 high-flow spray valve with round cap
Valve Type
Normally closed, needle spray valve
Construction Material
Body - Aluminum & Stainless Steel
Wetted Parts - 303 & 304 Stainless Steel, Teflon®, Kalrez®
Operating Air Pressure
60-100 psi [4.14 - 6.89 bar]
Maximum Inlet Fluid
Pressure
2,500 psi [172.37 bar]
Viscosity Range
Model 110
1 –10,000 cP
Model 210
> 10,000 cP
Spray Pattern Width
Flat
0.75" - 2+"[1.91 cm - 5.08+ cm]
Round
0.25" - 2" [0.64 cm - 5.08 cm]
Maximum Tubing Size
Supplied with 0.375" (0.95 cm) OD tubing
Activation
Single or dual-solenoid valve
Dimensions (W x D x H)
0.87" x 0.87" x 5.80" [2.2 cm x 2.2 cm x 14.7 cm]
Weight
9 oz [0.26 kg]
Unit Warranty
1 year from purchase date

Dymax Model 110 & 210 Spray Valves User Guide
19
Warranty
From date of purchase, Dymax Corporation offers a one-year warranty against defects in
material and workmanship on all system components with proof of purchase and
purchase date. Unauthorized repair, modification, or improper use of equipment may
void your warranty benefits. The use of aftermarket replacement parts not supplied or
approved by Dymax Corporation will void any effective warranties and may result in
damage to the equipment.
IMPORTANT NOTE:
DYMAX CORPORATION RESERVES THE RIGHT TO INVALIDATE
ANY WARRANTIES, EXPRESSED OR IMPLIED, DUE TO ANY REPAIRS PERFORMED OR
ATTEMPTED ON DYMAX EQUIPMENT WITHOUT WRITTEN AUTHORIZATION FROM
DYMAX. THOSE CORRECTIVE ACTIONS LISTED ABOVE ARE LIMITED TO THIS
AUTHORIZATION.

© 2012 Dymax Corporation. All rights reserved. All trademarks in this guide, except where noted, are the property of, or used under license by Dymax Corporation, U.S.A.
Teflon is a registered trademark of DuPont.
Please note that most dispensing system applications are unique. Dymax does not warrant the fitness of the product for the intended application. Any warranty applicable to the
product, its application and use is strictly limited to that contained in Dymax standard Conditions of Sale published on our website. Dymax recommends that any intended
application be evaluated and tested by the user to ensure that desired performance criteria are satisfied. Dymax is willing to assist users in their performance testing and
evaluation. Data sheets are available for valve controllers or pressure pots upon request. T16397 MAN029 7/09/2012
Dymax Corporation
860.482.1010
www.dymax.com
Dymax Europe GmbH
+49 (0) 611.962.7900
info_de@dymax.com
www.dymax.de
Dymax Asia Pacific Pte. Ltd.
+65.6752.2887
info_ap@dymax.com
www.dymax-ap.com
Dymax Asia (H.K.) Limited
+852.2460.7038
dymaxasia@dymax.com
www.dymax.com.cn
Dymax Korea LLC
+82.2.784.3434
www.dymax.com/kr
Dymax Oligomers & Coatings
860.626.7006
info_oc@dymax.com
www.dymax-oc.com
Dymax Engineering Adhesives
Ireland Ltd.
+353.1.231 4696
www.dymax.ie
Dymax UV Adhesives &
Equipment (Shenzhen) Co Ltd
+86.755.83485759
dymaxasia@dymax.com
www.dymax.com.cn
Dymax UV Adhesives &
Equipment (Shanghai) Co Ltd
+86.21.37285759
dymaxasia@dymax.com
www.dymax.com.cn
This manual suits for next models
1
Table of contents
Other dymax Control Unit manuals
Popular Control Unit manuals by other brands
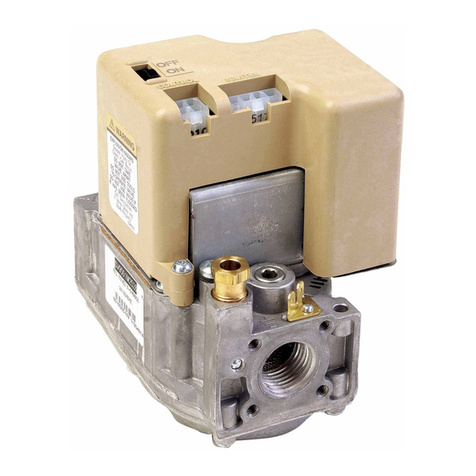
resideo
resideo SmartValve SV9401 installation instructions

Tridonic
Tridonic modularDIM installation instructions
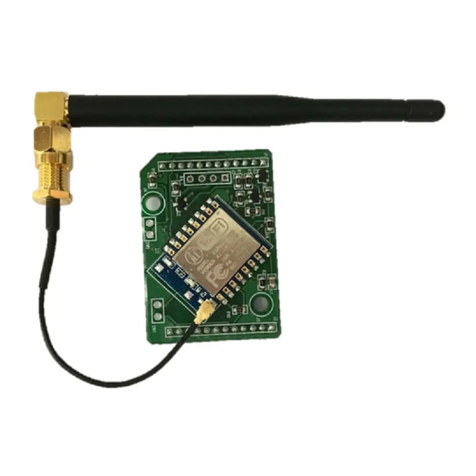
GUNPOWER
GUNPOWER GPR-WIFI-001 manual

UTEPO
UTEPO SFP-1.25G-550M quick start guide
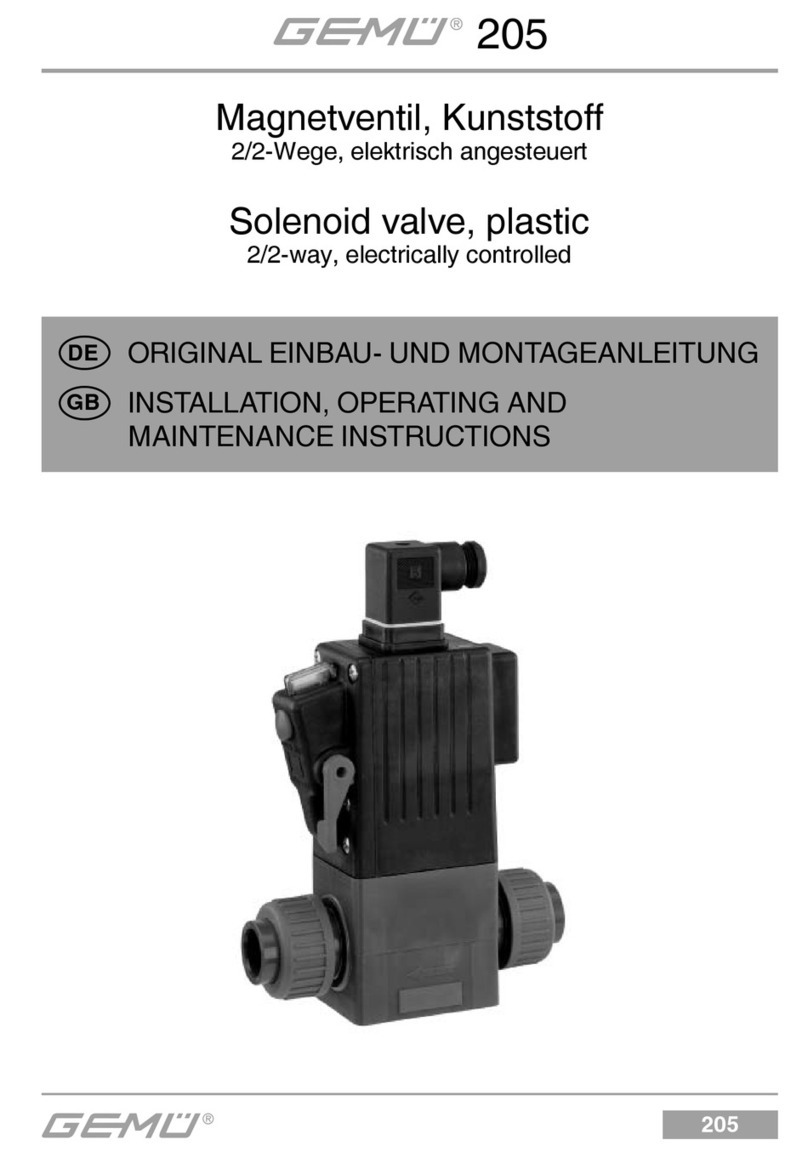
GEM
GEM 205 Installation, operating and maintenance instructions
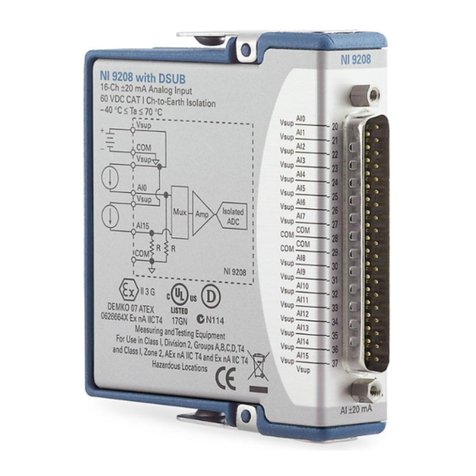
National Instruments
National Instruments NI-9208 Getting started