Kidde Technologies SR2033 Manual

OPERATION & MAINTENANCE MANUAL
FOR
NFI 40FT CNG BUSES AT
BC TRANSIT
(SR2033, SR2087 & SR2156)
Manual No: 181922
Revision B: Oct 25, 2017
PROPRIETARY NOTICE
THIS DOCUMENT IS THE PROPERTY OF UTC AEROSPACE SYSTEMS. YOU MAY NOT POSSESS, USE, COPY OR DISCLOSE THIS
DOCUMENT OR ANY INFORMATION IN IT, FOR ANY PURPOSE, INCLUDING WITHOUT LIMITATION, TO DESIGN, MANUFACTURE OR
REPAIR PARTS, OR OBTAIN ANY GOVERNMENT APPROVAL TO DO SO, WITHOUT UTC AEROSPCE SYSTEMS’ EXPRESS WRITTEN
PERMISSION. NEITHER RECEIPT NOR POSSESSION OF THIS DOCUMENT ALONE, FROM ANY SOURCE, CONSTITUTES SUCH
PERMISSION. POSSESSION, USE, COPYING OR DISCLOSURE BY ANYONE WITHOUT UTC AEROSPACE SYSTEMS’ EXPRESS
WRITTEN PERMISSION IS NOT AUTHORIZED AND MAY RESULT IN CRIMINAL AND/OR CIVIL LIABILITY.
EAR NOTICE
SUBJECT TO THE EAR, ECCN [EAR99].
THIS INFORMATION IS SUBJECT TO THE EXPORT CONTROL LAWS OF THE UNITED STATES, SPECIFICALLY INCLUDING THE
EXPORT ADMINISTRATION REGULATIONS (EAR), 15 C.F.R. PART 730 ET. SEQ. TRANSFER, RETRANSFER, OR DISCLOSURE OF THIS
DATA BY ANY MEANS TO A NON-U.S. PERSON (INDIVIDUAL OR COMPANY), WHETHER IN THE UNITED STATES OR ABROAD,
WITHOUT ANY REQUIRED EXPORT LICENSE OR OTHER APPROVAL FROM THE U.S GOVERNMENT IS PROHIBITED, INCLUDING
WITHOUT LIMITATION ANY DIVERSION TO A MILITARY END USER OR USE IN A MILITARY END USE APPLICATION.

181922 Rev B
2
Controlled by ECCN:EAR99
PROPRIETARY INFORMATION – Refer to the restrictions provided on the Title Page of this document.
EAR DATA - Subject to the export control restrictions on the Title Page of this document or file
TableofContents
INTRODUCTION..................................................................................................................................................3
BLOCKDIAGRAM...............................................................................................................................................3
SYSTEMOPERATION..........................................................................................................................................4
NORMALCONDITION................................................................................................................................................4
FIRESCENARIO..........................................................................................................................................................4
GASTRACELEAK(20%LEL)SCENARIO........................................................................................................................4
GASSIGNIFICANTLEAK(50%LEL)SCENARIO.............................................................................................................5
SYSTEMFAULTSCENARIO.........................................................................................................................................5
COMPONENTDESCRIPTION................................................................................................................................5
PROTECTIONPANEL(413484‐1345)..........................................................................................................................5
MANUALACTIVATIONSWITCH(421317)..................................................................................................................7
SPOTTHERMALDETECTOR(420419‐350).................................................................................................................8
GASLEAKDETECTOR(420473‐2050).........................................................................................................................9
END‐OF‐LINEDEVICE(420241)................................................................................................................................10
DISTRIBUTIONBLOCK(420588).................................................................................................................................10
NOZZLE(474946)....................................................................................................................................................10
ELECTRICALINTERCONNECTIONS...........................................................................................................................11
SYSTEMRESET..................................................................................................................................................12
FIRE:........................................................................................................................................................................12
TRACEGASLEAK:.....................................................................................................................................................13
SIGNIFICANTGASLEAK:..........................................................................................................................................13
PERIODICMAINTENANCE..................................................................................................................................14
PRE‐TRIP..................................................................................................................................................................14
EVERY3000MILESORMONTHLY(WHICHEVEROCCURSFIRST)......................................................................................14
EVERY18000MILESORSEMI‐ANNUALLY(WHICHEVEROCCURSFIRST)..........................................................................15
EVERYSIXYEARS......................................................................................................................................................15
EVERYTWELVEYEARS.............................................................................................................................................15
ADDITIONALINSPECTIONS......................................................................................................................................15
TROUBLESHOOTINGGUIDE...............................................................................................................................16
REPLACEMENTPARTSLIST................................................................................................................................20
CONTACTINFORMATION..................................................................................................................................21
REVISIONHISTORY............................................................................................................................................21

181922 Rev B
3
Controlled by ECCN:EAR99
PROPRIETARY INFORMATION – Refer to the restrictions provided on the Title Page of this document.
EAR DATA - Subject to the export control restrictions on the Title Page of this document or file
INTRODUCTION
This manual describes the operation and maintenance of the Kidde Automatic Fire Detection
and Suppression System (AFSS) and Gas Leak Detection System (GDS) as installed on the
NFI 40ft CNG buses at BC Transit.
The AFSS system is of a 1 Zone, 1 Shot type configuration. The fire detection system provides
fire detection coverage for the engine compartment and consist of:
Three (3) spot thermal detectors in the engine compartment
The suppression system provides extinguisher coverage for the engine compartment and
consist of:
A single fire extinguisher
A four (4) nozzle distribution system
The GDS provides gas leak detection coverage for vehicle. Four (4) gas detectors are installed:
Two (2) in the roof tank area
One (1) in the area above the CNG fill
One (1) in the engine compartment
BLOCK DIAGRAM
A system block diagram is shown in Figure 1.
FIGURE 1 – SYSTEM BLOCK DIAGRAM

181922 Rev B
4
Controlled by ECCN:EAR99
PROPRIETARY INFORMATION – Refer to the restrictions provided on the Title Page of this document.
EAR DATA - Subject to the export control restrictions on the Title Page of this document or file
SYSTEM OPERATION
The state of the system is constantly monitored and is displayed to the driver via the protection
panel. The system provides visual and audial indicators to the driver when the state of the
system changes.
NORMAL CONDITION
During normal operating conditions (appropriate system power applied and no fault conditions
present), the protection panel’s system “OK” indicator is illuminated solid green.
FIRE SCENARIO
When a fire sensor detects a fire in the engine compartment, the Protection Panel’s FIRE
ALARM and the DELAY ENGINE STOP indicators illuminate, an audio alarm sounds, and the
HVAC shuts down immediately. Fifteen (15) seconds later the engine automatically shuts down
and the fire extinguisher automatically discharges.
Engine shutdown and extinguisher discharge may be delayed an additional fifteen (15) seconds
by depressing the Protection Panel’s DELAY ENGINE STOP indicator/switch.
The Manual Activation Switch may be activated to immediately discharge the Fire Extinguisher
and shutdown the engine and HVAC.
The system must be reset and the extinguisher removed and replaced in accordance with the
System Reset portion of this manual.
WARNING! THE ENGINE WILL STOP 15 SECONDS AFTER THE FIRE ALARM STARTS.
THE OPERATOR MUST BE PREPARED TO BRING THE VEHICLE TO A SAFE
STOP AS SOON AS THE ALARM SOUNDS. STEERING MAY BECOME
DIFFICULT AFTER ENGINE SHUTDOWN. IF MORE TIME IS REQUIRED, THE
“DELAY ENGINE STOP” SWITCH MAY BE PRESSED AND RELEASED FOR
AN ADDITIONAL 15 SECOND DELAY.
WARNING! THE EXTINGUISHER DISCHARGE MAY CAUSE AN OBSCURING CLOUD
BEHIND AND NEAR THE VEHICLE.
GAS TRACE LEAK (20% LEL) SCENARIO
When a gas sensor detects a trace leak, the Protection Panel’s GAS LEAK indicator illuminates
(blinking).
The system will reset itself and indications will clear when the gas dissipates below the trace
leak threshold.

181922 Rev B
5
Controlled by ECCN:EAR99
PROPRIETARY INFORMATION – Refer to the restrictions provided on the Title Page of this document.
EAR DATA - Subject to the export control restrictions on the Title Page of this document or file
GAS SIGNIFICANT LEAK (50% LEL) SCENARIO
When a gas sensor detects a significant leak, the Protection Panel’s GAS LEAK indicator
illuminates (steady-on) and an audio alarm sounds. The gas LEAK indicator and the audible
alarm warnings will stay on until the TEST/RESET button on the Protection Panel is pressed.
The status indicator on the individual Gas Leak Detector that detected the significant gas leak
will remain illuminated solid red until the system is reset in accordance with system reset portion
of this manual.
SYSTEM FAULT SCENARIO
The Protection Panel continuously monitors system integrity and displays the status via the
SYSTEM OK, FIRE TROUBLE, and GAS TROUBLE indicators. Refer to the Component
Description, Protection Panel portion of this manual for the operational description of the
indicators.
COMPONENT DESCRIPTION
PROTECTION PANEL (413484-1345)
The protection panel is located in the driver’s area and displays the current system status. The
Protection panel comprises the following:
SYSTEM OK indicator
oIlluminates solid green when appropriate power is applied to the system and no
trouble conditions exists
oIlluminates blinking green when power is low (under 22VDC)
oOff when power is insufficient
oOff when TROUBLE indicator is illuminated
FIRE TROUBLE indicator
Illuminates blinking yellow when a fault exists in the fire detection and suppression
circuits
Fire ALARM indicator
oIlluminates solid red when a fire is detected
oIlluminates blinking red when the MANUAL DISCHARGE switch is activated
Gas TROUBLE indicator
Illuminates solid yellow when a fault exists in the gas detection circuit
Gas ALARM indicator
oIlluminates blinking red when trace gas is detected (greater than 20%, but less than
50%)
oIlluminates solid red when significant gas is detected (greater than 50%)
Audible alarm
oIntermittent sound indicates fault condition when SYSTEM OK indicator is
extinguished
oIntermittent sound indicates low power condition when SYSTEM OK indicator is
blinking
oContinuous sound indicates fire alarm, manual discharge, or significant gas alarm

181922 Rev B
6
Controlled by ECCN:EAR99
PROPRIETARY INFORMATION – Refer to the restrictions provided on the Title Page of this document.
EAR DATA - Subject to the export control restrictions on the Title Page of this document or file
ALARM SILENCE switch
oUse to silence the audible alarm
TEST/RESET switch with DELAY ENGINE STOP indicator
During normal “System OK” state:
oAllows testing of indicators and audible alarm during standby operation
During Fire Event:
oIlluminates solid red when fire event is detected
oIlluminates blinking red when pressed and released for a 15 second additional delay.
oReturns to solid red illumination after additional time delay had elapsed
oTurns off when the shutdown signal has been activated
oResets protection panel when pressed and released after a fire event or significant
gas leak
Early warning signal output
Engine shutdown signal output
Manual activation switch signal input
Operating Temperature Range -40⁰F to 158⁰F (-40⁰C to 70⁰C)
Quiescent Current 50mA (Nominal) @ 24V
Operating Voltage 9 to 32Vdc
FIGURE 2 - PROTECTION PANEL

181922 Rev B
7
Controlled by ECCN:EAR99
PROPRIETARY INFORMATION – Refer to the restrictions provided on the Title Page of this document.
EAR DATA - Subject to the export control restrictions on the Title Page of this document or file
MANUAL ACTIVATION SWITCH (421317)
The Manual Activation Switch allows immediate system activation (extinguisher discharge and
engine shutdown) by the vehicle operator at any time. Activation of the switch is accomplished
by twisting and pulling the tamper seal (not shown) to remove, lifting the cover and pressing the
red “FIRE” button for more than half a second. After the Manual Activation Switch has been
activated, the Protection Panel’s FIRE ALARM indicator will blink until power has been cycled to
the system.
FIGURE 3 – MANUAL ACTIVATION SWITCH
(Depicted without Tamper Seal)

181922 Rev B
8
Controlled by ECCN:EAR99
PROPRIETARY INFORMATION – Refer to the restrictions provided on the Title Page of this document.
EAR DATA - Subject to the export control restrictions on the Title Page of this document or file
SPOT THERMAL DETECTOR (420419-350)
Spot Thermal detectors are point thermal switches which work by contact closure to initiate an
alarm when the temperature of the area surrounding the detector exceeds its pre-set alarm
temperature. The detectors reset themselves automatically once the temperature falls below the
pre-set alarm temperature.
Operating Temperature Range -40⁰F to 257⁰F (-40⁰C to 125⁰C)
Quiescent Current 0mA (Nominal) @ 24V
Operating Voltage 9 to 32Vdc
Alarm Temperature 280°F (Blue bodied sensor)
350°F (Red bodied sensor)
450°F (Green bodied sensor)
Response Time Within 60 seconds of exposure
to flame
FIGURE 4 – SPOT THERMAL DETECTOR

181922 Rev B
9
Controlled by ECCN:EAR99
PROPRIETARY INFORMATION – Refer to the restrictions provided on the Title Page of this document.
EAR DATA - Subject to the export control restrictions on the Title Page of this document or file
GAS LEAK DETECTOR (420473-2050)
The PM-MDS Gas Leak Detector utilizes a temperature compensated metal-oxide sensing
element to detect combustible gases including CNG and LNG. The detector contains two
preset detection thresholds:
Trace alarm (20% LEL of Methane)
Significant alarm (50% LEL of Methane)
The PM-MDS Gas Leak Detector contains a Bi-colored status LED which indicates:
Status LED Indication
Solid Green Sensor operational
Flashing Red Trace Gas level detected (between 20% and 50% LEL)
Solid Red Significant Gas level detected (50% LEL or higher)
Flashing Red/Green Sensor Fault
No LED Sensor without power
NOTE: The status LED illuminates blinking green for the first 30 seconds after
power-up.
After a significant gas leak is detected, power to the detector must be cycled to reset the status
LED.
CAUTION! CARE SHOULD BE TAKEN WHEN CLEANING THE COMPARTMENTS WHICH
HOUSE GAS LEAK DETECTORS; AVOID EXPOSURE TO SILICONES OR
SOLVENTS AND AVOID DIRECTLY HITTING WITH HIGH-PRESSURE STEAM
CLEANING OR PRESSURE WASHING SPRAY.
The gas sensing element inside the detector is a consumable item with a limited service life
dependent on environmental conditions. The sensing element is field replaceable and is
included in the Combustible Gas Detector Rebuild Kit (P/N 420483).
Operating Temperature Range -40⁰F to 185⁰F (-40⁰C to 85⁰C)
Quiescent Current 40mA
Operating Voltage 9 to 32Vdc
Response Time Within 90 seconds of exposure
to alarm level concentration
Field Calibration Not Required
FIGURE 5 - PM-MDS GAS LEAK DETECTOR

181922 Rev B
10
Controlled by ECCN:EAR99
PROPRIETARY INFORMATION – Refer to the restrictions provided on the Title Page of this document.
EAR DATA - Subject to the export control restrictions on the Title Page of this document or file
END-OF-LINE DEVICE (420241)
The End-of-Line device is required for supervision of the fire and gas detection circuits. It
consists of a resistor installed into a connector and is environmentally sealed with potting
compound. The End-of-Line device is installed on the last detector in each series of detectors.
FIGURE 6 – END-OF-LINE DEVICE
DISTRIBUTION BLOCK (420588)
The distribution block is a manifold that is used as part of the distribution system to direct the
flow of dry chemical fire extinguishing agent from the extinguisher to individual nozzles.
The distribution block is constructed of plated steel and contains an integral mounting flange. It
has one ¾” NPT female inlet port and four ½” NPT female outlet ports.
FIGURE 7 – DISTRIBUTION BLOCK
NOZZLE (474946)
This nozzle is constructed of plated steel and contains a 45° steel cone, causing the nozzle to
disperse a cone shaped spray of dry chemical. The nozzle has a silicone rubber protective cap
that is blown off by the dry chemical discharge.
FIGURE 8 – NOZZLE

181922 Rev B
11
Controlled by ECCN:EAR99
PROPRIETARY INFORMATION – Refer to the restrictions provided on the Title Page of this document.
EAR DATA - Subject to the export control restrictions on the Title Page of this document or file
FIRE EXTINGUISHER (421220-22)
The Fire Extinguisher is an electrically operated, stored pressure type extinguisher that contains
25 pounds of BC rated ‘Purple K’ dry chemical extinguishing agent pressurized with nitrogen.
A fast opening valve is mounted on a DOT certified cylinder. The extinguisher is installed
horizontally in the bottle-mounting bracket (421222) with the gauge right.
CAUTION! THE EXTINGUISHER WILL NOT FUNCTION AS INTENDED IF ORIENTED
INCORRECTLY
WARNING! THE ANTI-RECOIL PLUG SHALL BE INSTALLED ON THE VALVE OUTLET
PORT AT ALL TIMES EXCEPT WHEN THE EXTINGUISHER IS
CONNECTED TO THE DISTRIBUTION PIPING OR WHILE THE
EXTINGUISHER IS BEING FILLED.
Operating Temperature Range -65⁰F to 200⁰F (-53⁰C to 93⁰C)
Pressure 360 psi
Mounting Bracket 421222
FIGURE 9 – FIRE EXTINGUISHER
(DEPICTED IN VERTICAL MOUNT ORIENTATION)
ELECTRICAL INTERCONNECTIONS
The vehicle harness connects the components that make up the fire and gas system together.
The vehicle harness also connects the fire and gas system’s vehicle interface outputs to the
vehicle’s multiplex system allowing the activation of features such as HAVC shutdown and
engine shutdown. Refer to the System schematic, 475921, for more information.

181922 Rev B
12
Controlled by ECCN:EAR99
PROPRIETARY INFORMATION – Refer to the restrictions provided on the Title Page of this document.
EAR DATA - Subject to the export control restrictions on the Title Page of this document or file
SYSTEM RESET
FIRE:
After a fire, the system is restored to operational status as follows:
1. Disconnect system power by removing the system fuses. The system has two fuses.
2. Remove the Fire Extinguisher:
a. Disconnect the electrical connector on the extinguisher valve from the vehicle harness.
b. Install a shorting plug to the electrical connector on the extinguisher valve.
c. Remove the distribution piping from the valve outlet port and install the anti-recoil
plug.
WARNING! THE ANTI-RECOIL PLUG SHALL BE INSTALLED ON THE VALVE OUTLET
PORT AT ALL TIMES EXCEPT WHEN THE EXTINGUISHER IS CONNECTED
TO THE DISTRIBUTION PIPING OR WHILE THE EXTINGUISHER IS BEING
FILLED.
d. Loosen the mounting clamps and remove the extinguisher.
CAUTION! DO NOT ATTEMPT TO REBUILD THE EXTINGUISHER. HAVE THE FIRE
EXTINGUISHER REBUILT BY A QUALIFIED FIRE PROTECTION EQUIPMENT
COMPANY FAMILIAR WITH KIDDE DUAL SPECTRUM EQUIPMENT. REBUILD
SHALL INCLUDE SQUIB, VALVE SEALS, AND DRY CHEMICAL
REPLACEMENT.
3. Blow out the distribution tubing with dry compressed air to insure the tubing is dry and free
of debris and/or residual agent.
4. Replace any damaged or missing nozzle blow-off caps.
CAUTION! NOT INSTALLING ALL OF THE NOZZLE BLOW-OFF CAPS BEFORE
PREFORMING A DRY CHEMICAL CLEANUP CAN RESULT IN
COMTAMINATES GETTING IN THE DISTRIBUTION SYSTEM WHICH
COULD RESULT IN COMPROMISED PREFORMAMCE OF THE
SUPRESSION SYSTEM.
5. Clean up dry chemical agent according to “Dry Chemical Clean-Up Procedure”, R9866.
6. Repair and/or replace any damaged detection devices and/or electrical harnessing.
7. Replace the fire extinguisher:
a) Inspect the new extinguisher; verify it is the correct part number to ensure it is the
correct configuration for the application and verify the anti-recoil plug and the shorting
plug are installed.
b) Install the extinguisher in the mounting bracket and oriented per the instructions on the
extinguisher nameplate. Tighten the mounting clamps. Do NOT connect the electrical
connector at this time.
CAUTION! THE EXTINGUISHER WILL NOT FUNCTION AS INTENDED IF ORIENTED
INCORRECTLY

181922 Rev B
13
Controlled by ECCN:EAR99
PROPRIETARY INFORMATION – Refer to the restrictions provided on the Title Page of this document.
EAR DATA - Subject to the export control restrictions on the Title Page of this document or file
c) Remove the anti-recoil plug and immediately connect the distribution piping.
d) Connect system power by replacing the system fuses and verify the red fire ALARM
indicator on the Protection Panel is NOT on.
NOTE: A FIRE TROUBLE INDICATOR WILL BE ON BECAUSE THE ELECTRICAL
CONNECTOR ON THE EXTINGUISHER VALVE IS NOT CONNECTED.
CAUTION! IF THE PROTECTION PANEL IS IN ALARM CONDITION, THE EXTINGUISHER
MAY DISCHARGE IF IT IS CONNECTED TO THE SYSTEM. BE SURE THE
RED FIRE ‘ALARM’ INDICATOR ON THE PROTECTION PANEL IS NOT
ILLUMINATED BEFORE PROCEDING FURTHER.
e) Remove the shorting plug from the electrical connector on the extinguisher valve.
f) Attach the vehicle harness to the electrical connector on the extinguisher valve.
7. Verify the green SYSTEM OK indicator on the Protection Panel is on.
TRACE GAS LEAK:
The system will automatically reset itself and indications will clear when the gas dissipates
below the trace leak threshold.
SIGNIFICANT GAS LEAK:
After a significant gas leak, the system is restored to operational status as follows:
1. Disconnect system power by removing the system fuses. The system has two fuses.
2. The system and all of the fire and gas detectors will reset.
NOTE: IF ONLY THE TEST/RESET BUTTON ON THE PROTECTION PANEL IS
PRESSED AFTER A SIGNIFICANT GAS LEAK ALARM THE SYSTEM WILL
RESET, HOWEVER THE STATUS INDICATOR ON THE INDIVIDUAL GAS
LEAK DETECTOR THAT DETECTED THE SIGNIFICANT GAS LEAK WILL
REMAIN ILLUMINATED SOLID RED. POWER MUST BE CYCLED TO RESET
DETECTOR STATUS INDICATORS.

181922 Rev B
14
Controlled by ECCN:EAR99
PROPRIETARY INFORMATION – Refer to the restrictions provided on the Title Page of this document.
EAR DATA - Subject to the export control restrictions on the Title Page of this document or file
PERIODIC MAINTENANCE
PRE-TRIP
Verify the Protection Panel’s green ‘SYSTEM OK’ indicator is illuminated and that all
other indicators are OFF.
Press the TEST/RESET Switch. The following should occur:
oAll indicators and switches on the Protection Panel should illuminate.
oAn audible alarm should sound.
EVERY 3000 MILES OR MONTHLY (WHICHEVER OCCURS FIRST)
General
Verify neither the protected equipment nor the hazard has changed
Verify no obvious physical damage or condition exists that might prevent system
operation
Protection Panel
Verify all warning indicators and the audible alarm are operational by pressing the
‘TEST/RESET’ button
Manual Activation Switch
Verify tamper seal is intact and access to switch is unobstructed
Fire Detectors
Spot Thermal Detector
Verify there is no obvious physical damage and the device is free of excess
contamination (dirt, oil, grease, etc). If necessary, clean using water soaked non-
abrasive towel.
Gas Leak Detectors
Verify status indicator on the detector is on solid green
Verify there is no obvious physical damage and that unit is free of excess contamination
(dirt, oil, grease, etc) - if necessary, clean using water soaked non-abrasive towel.
CAUTION: DO NOT USE CHEMICAL CLEANERS
Verify no silicone based materials have been used near detector
Electrical Harness
Verify electrical connectors and electrical wiring have no visible damage and all
connectors are securely seated

181922 Rev B
15
Controlled by ECCN:EAR99
PROPRIETARY INFORMATION – Refer to the restrictions provided on the Title Page of this document.
EAR DATA - Subject to the export control restrictions on the Title Page of this document or file
Extinguisher & Distribution System
Verify the extinguisher is oriented correctly.
Verify the extinguisher pressure gauge pointer is in the green arc at room temperature.
Verify distribution piping and nozzles are intact, unobstructed, and that nozzle blow-off
caps are in place.
Visually inspect the extinguisher for damage such as pits, gouges, dents, or corrosion. If
a pit, gouge, or cut exceeds a depth of 0.08 inches; if the depth of a dent exceeds 0.25
inches or one-tenth of the average diameter of the dent; or corrosion exceeds a depth of
0.05 inches or a coverage area larger than 15% of the extinguisher’s outer surface, have
the extinguisher evaluated by a qualified fire protection equipment company familiar with
Kidde equipment.
EVERY 18000 MILES OR SEMI-ANNUALLY (WHICHEVER OCCURS FIRST)
Perform a comprehensive fire system test according to KAD Generic AFSS Checkout
Procedure, R10027 using a Kidde Fire System Test Set (Thermal Detection Test Kit P/N
4208971-1)
Perform a comprehensive gas leak system test using the KAD Gas Sensor Test Kit, P/N
420756, for CNG, LNG, and Propane.
EVERY SIX YEARS
Have the fire extinguisher assembly rebuilt and inspected by a qualified fire protection
equipment company familiar with Kidde equipment. The date of manufacture of the
extinguisher assembly is stamped (MM/YY) on the top neck of the cylinder. This is the date
that should be used to determine the 6 year service interval date.
EVERY TWELVE YEARS
Have the fire extinguisher cylinder hydrostatically tested by a qualified fire protection
equipment company familiar with Kidde equipment. The date of manufacture of the cylinder
is stamped (MM/YY) on the neck of the cylinder. This is the date that should be used to
determine the12 year service interval date.
ADDITIONAL INSPECTIONS
A thorough inspection should be performed after any major engine work is done to ensure
components have not been damaged or relocated.

181922 Rev B
16
Controlled by ECCN:EAR99
PROPRIETARY INFORMATION – Refer to the restrictions provided on the Title Page of this document.
EAR DATA - Subject to the export control restrictions on the Title Page of this document or file
TROUBLESHOOTING GUIDE
SYMPTOM PROBABLE CAUSE CORRECTIVE ACTION
All Protection Panel indicators
off. No power to protection panel
Check protection panel fuse
(15A).
Check power and ground
connections & voltage to
protection panel.
(NOTE: Below 9 volts the
system will not function.)
If the power (~24Volts) and
ground are present at the
protection panel, replace it.
Protection Panel green
SYSTEM OK indicator
blinking. Low battery voltage
Check connections & voltage
to system.
Below 22 volts the system will
provide low voltage indication.
Protection Panel green
SYSTEM OK indicator off,
yellow fire TROUBLE
indicator on, red fire ALARM
indicator on solid and audible
alarm on.
System automatically
discharged
Correct the cause of the
system activation and reset
the system as described in
the system reset portion of
this manual
Protection Panel green
SYSTEM OK indicator off,
yellow fire TROUBLE
indicator on, red fire ALARM
indicator on blinking and
audible alarm on.
System manually discharged
Correct the cause of system
activation and reset the
system as described in the
system reset portion of this
manual

181922 Rev B
17
Controlled by ECCN:EAR99
PROPRIETARY INFORMATION – Refer to the restrictions provided on the Title Page of this document.
EAR DATA - Subject to the export control restrictions on the Title Page of this document or file
SYMPTOM PROBABLE CAUSE CORRECTIVE ACTION
Protection Panel green
SYSTEM OK lamp off, yellow
fire TROUBLE lamp on solid
and audible alarm beeping.
Component not connected or
damaged harness in the
extinguisher circuit
Check the harness connection
at the extinguisher
Use a value simulator and
starting at the first connection
in the extinguisher circuit
systematically check the
voltage at each connection
until the section where the
fault exists is identified.
NOTE: The valve circuit
voltage should measure in the
millivolts.
Protection Panel green
SYSTEM OK indicator off,
yellow fire TROUBLE
indicator on blinking and
audible alarm beeping.
Component not working, not
connected, or damaged
harness in the fire detection
or extinguisher circuits
Check Fire sensors.
Check harness connections at
fire sensors.
Check EOL connections
Check for the correct voltage
values on each of the fire
circuits. (Pin A: 22-26 volts,
Pin B: Ground, Pin C: 11-15
volts
If the voltage at Pin A or C is
low, use an EOL and starting
at the first connection in the
Fire circuit systematically
check the voltage at each
connection until the section
where the fault exists is
identified.
Protection Panel green
SYSTEM OK indicator off,
yellow gas TROUBLE
indicator on solid and audible
alarm beeping.
Gas leak detector fault
Check gas detectors’ LED
indicators.
If a gas detector’s LED
indicator is blinking red/green,
refurbish with p/n 420483
refurbishment kit or replace
sensor.

181922 Rev B
18
Controlled by ECCN:EAR99
PROPRIETARY INFORMATION – Refer to the restrictions provided on the Title Page of this document.
EAR DATA - Subject to the export control restrictions on the Title Page of this document or file
SYMPTOM PROBABLE CAUSE CORRECTIVE ACTION
Component not connected or
damaged harness in gas
detection circuit
Check gas detectors’ LED
indicators. If any are not
illuminated this is an
indication that power is not
being received.
Check harness connections at
the gas detectors.
Check for the correct voltage
values on the gas circuit. (Pin
A: 22-26 volts, Pin B: Ground,
Pin C: 11-15 volts).
NOTE: The gas detectors will
not be powered if Pin B is not
equal to Ground.
If the voltage at Pin A or C is
low, use an EOL and starting
at the first connection in the
gas circuit systematically
check the voltage at each
connection until the section
where the fault exists is
identified.
Protection Panel green
SYSTEM OK indicator on
solid, red gas LEAK indicator
blinking.
Trace gas leak present
Correct the cause of the leak.
System will reset itself when
trace gas leak dissipates
below detection threshold.
Protection Panel green
SYSTEM OK indicator on
solid, red gas “LEAK”
indicator on solid and audible
alarm on.
Significant gas leak alarm has
occurred and may or may not
still be present.
Locate gas sensor that
initiated alarm by checking
sensor status indicators.
Correct the cause of the leak.
Reset system as described in
the system reset portion of
this manual and monitor for
alarm.
Status indicator on gas sensor
blinking green Power up period Allow 30 seconds after power-
up for indicator to turn solid
green

181922 Rev B
19
Controlled by ECCN:EAR99
PROPRIETARY INFORMATION – Refer to the restrictions provided on the Title Page of this document.
EAR DATA - Subject to the export control restrictions on the Title Page of this document or file
SYMPTOM PROBABLE CAUSE CORRECTIVE ACTION
Extinguisher pressure gauge
reading is low
Extinguisher cold
Let extinguishers warm up to
room temperature (about
70°F) and recheck the gauge.
If the pointer is then within the
green arc no corrective action
is required
Extinguisher leaking or
discharged
Have the fire extinguisher
serviced by a fire protection
equipment company familiar
with Kidde equipment

181922 Rev B
20
Controlled by ECCN:EAR99
PROPRIETARY INFORMATION – Refer to the restrictions provided on the Title Page of this document.
EAR DATA - Subject to the export control restrictions on the Title Page of this document or file
REPLACEMENT PARTS LIST
Part Number Description
413484-1345 CONTROL PANEL, FIRE & GAS ICD
421317-1 Manual Activation Switch
421317-2 Manual Activation Switch Tamper Seal
420419-350 350⁰F Spot Thermal Detector
420473-2050 Methane Gas Sensor
420483 Methane Detector Rebuild Kit
420241 EOL, End of Line
421220-22 Extinguisher, 25Lbs, PK, Gauge Right
421222 Bracket, Extinguisher, 25Lb.
420588 Distribution Block
474946 Nozzle, Dry Chemical
475922 HARNESS, MAIN, CNG, NFI
475839 Hrns Assy - Power Lead
476713 Hrns-Eng Compt Fire Supn D/S
475852-4 Hrns-Roof Gas Det DS 4' TWR
475851-8 Hrns-Roof, Gas Det DS 8' Shrd.
447352-3 INTERCONNECT HARNESS HI-TEMP 3FT
447352-6 INTERCONNECT HARNESS HI-TEMP 6FT
447333-8 INTERCONNECT HARNESS SHIELDED 8FT
475974-3 INTERCONNECT HARNESS STD 3FT
420871-1 Fire System Test Kit (Linear)
420756 Gas Sensor Test Kit
This manual suits for next models
2
Table of contents
Popular Smoke Alarm manuals by other brands
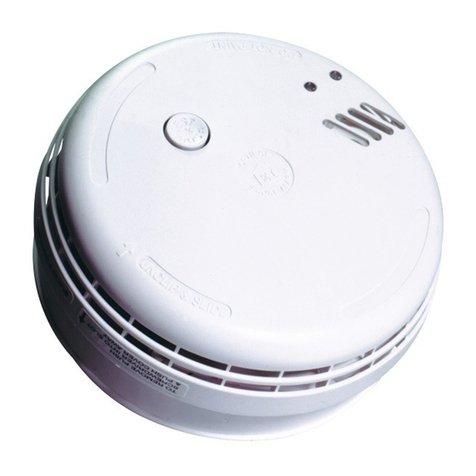
Ei Electronics
Ei Electronics Ei405TY RF Optical Technical specifications

Fire-Lite Alarms
Fire-Lite Alarms D350P Installation and maintenance instructions
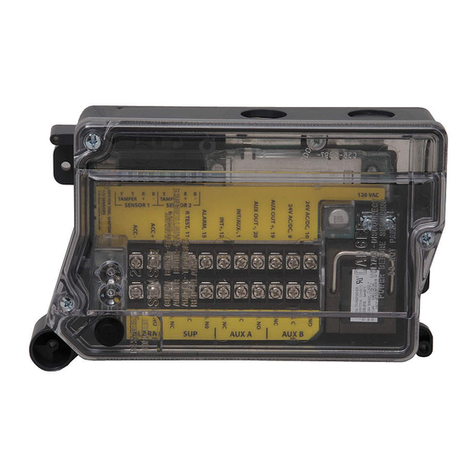
System Sensor
System Sensor D4P120 installation instructions

Smoke hollow
Smoke hollow SH3616DW owner's manual

Weller
Weller WFE 2ES operating instructions
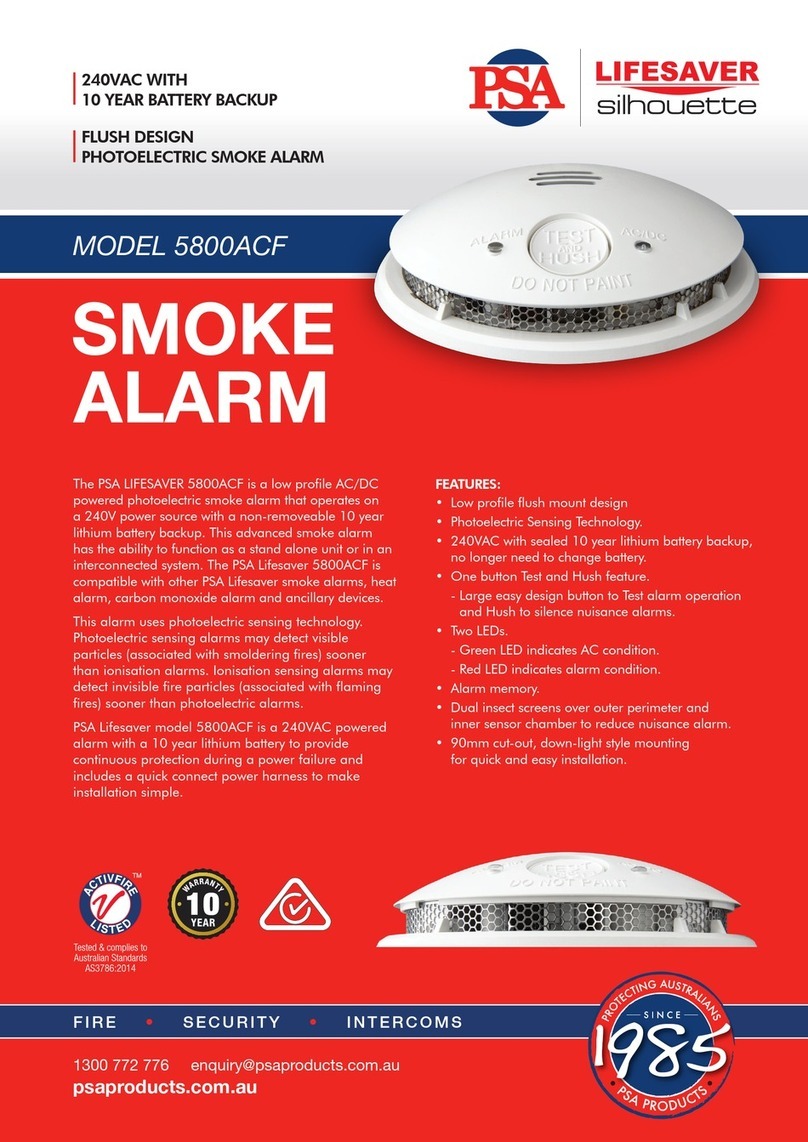
PSA Products
PSA Products LIFESAVER silhouette 5800ACF instructions