Kollmorgen Seidel 04S Series User manual

Transistor Controller
Series 04S
Assembly / Installation / Commissioning
Edition 12/99

Technical changes to improve the performance of the equipment
may be made without prior notice !
Printed in the Federal Republic of Germany 12/99
Mat.No. 73906
All rights reserved. No part of this document may be reproduced in any form (by printing, photocopying,
microfilm or any other method), or stored, processed, copied or distributed by electronic means without
the written permission of Seidel Corporation.
Previous editions
Edition Comment
09 / 91 First english edition
01 / 93 New layout, completely created with DTP
02 / 98 Seidel Servo Drives, CE, DIN A5
12 / 99 KMS, Layout

Contents
Contents Page - A -
Kollmorgen 12.99 Series 04S
I General
I.1 Introduction ...................................................................I-1
I.2 Prescribed usage (“Use as directed”) of the transistor controller ..........................I-1
I.3 Abbreviations used in this manual..................................................I-2
I.4 Nameplate....................................................................I-2
- A.4.028.6/10
I.5 04S equipment description .......................................................I-3
I.5.1 04S functional units ..........................................................I-4
I.6 Technical data ................................................................I-5
I.6.1 04S technical data ...........................................................I-5
I.6.2 Permissible ambient conditions, ventilation, mounting position .........................I-6
I.6.3 Cable cross-sections .........................................................I-6
I.6.4 Fusing ....................................................................I-6
I.7 Interference suppression.........................................................I-7
I.8 Ballast circuit ..................................................................I-7
II Installation and Commissioning
II.1 Important instructions ..........................................................II-1
II.2 Installation ...................................................................II-2
II.2.1 - conform connections 04S, overview ........................................II-4
- E.3.924.1/4
II.2.2 Connection diagram 04S......................................................II-5
- E.3.924.1/1
II.2.3 Module back-panels F03SMB and R03SMB.......................................II-6
II.2.3.1 Pin assignments for 04S / F03S-MB........................................II-6
II.2.3.2 Pin assignments for 04S / R03S-MB .......................................II-7
II.3 Commissioning ...............................................................II-8
II.3.1 Important instructions ........................................................II-8
II.3.2 Notes on commissioning .....................................................II-9
Contents Drawing Page
Contents ...............................................A
Safety Instructions ........................................C
Standards and Directives ....................................D
-Conformance..........................................D

Contents
Page - B - Contents
Series 04S 12.99 Kollmorgen
III Functions and Options
III.1 Important notes ...............................................................III-1
III.2 Description of the functions .....................................................III-1
III.2.1 Input functions .............................................................III-1
III.2.1.1 Setpoint inputs SW1, SW2 ...............................................III-1
III.2.1.2 Tachometer input Ta ...................................................III-1
III.2.1.3 Digital control inputs....................................................III-2
III.2.2 Output functions ............................................................III-3
III.2.2.1 Armature current monitor output ..........................................III-3
III.2.2.2 System ready contact BTB ..............................................III-3
III.2.2.3 Measurement points ...................................................III-3
III.2.3 Adjustment facilities .........................................................III-4
III.2.3.1 Tachometer potentiometer P1 ............................................III-4
III.2.3.2 Setpoint potentiometer P2 ...............................................III-4
III.2.3.3 Offset potentiometer P3 .................................................III-4
III.2.3.4 AC-GAIN potentiometer P4 ..............................................III-4
III.2.4 Other functions .............................................................III-5
III.2.4.1 Effective (r.m.s.) current IRMS ............................................III-5
III.2.4.2 Peak current IPEAK ....................................................III-5
III.2.4.3 Frequency response of the transistor controller ..............................III-5
III.2.4.4 I2t - monitoring ........................................................III-6
III.2.4.5 Indicators ............................................................III-6
III.3 Options .....................................................................III-7
III.3.1 1:1 - control ...............................................................III-7
III.3.2 IxR - control ...............................................................III-7
III.3.3 Option -24V-, external 24V auxiliary voltage ......................................III-7
III.3.4 Layout of the solder links .....................................................III-8
- E.4.924.1/2
IV Peripheral components
IV.1 Isolating transformers ..........................................................IV-1
IV.1.1 Transformer dimensions and connections .......................................IV-2
- E.4.924.4/2
IV.2 Chokes ....................................................................IV-3
IV.2.1 Choke dimensions and connections ............................................IV-3
- E.4.924.4/1
V Drawings
V.1 Front panel 04S (12TE), optional..................................................V-1
- E.4.924.4/5
V.2 Component layout 04S .........................................................V-2
- E.4.924.2/1
V.3 Back-panels F03SMB / R03SMB..................................................V-3
- E.4.911.4/8
VI Appendix
VI.1 Delivery package, transport, storage, maintenance, disposal ...........................VI-1
VI.2 Fault-finding .................................................................VI-2
VI.3 Glossary ....................................................................VI-3
VI.4 Index ......................................................................VI-4
Contents Drawing Page

Safety Instructions
Safety Instructions Page - C -
Kollmorgen 12.99 Series 04S
Safety Instructions
Warning symbols : You must observe the important notes in the text,
which are marked by the following symbols :
danger from electricity general warning
and its effects general notes
uOnly properly qualified persons are permitted to carry out activities such as
transport, installation, commissioning and maintenance. Properly qualified
persons are those who are familiar with the transport, installation,
assembly, commissioning and operation of the products, and who have the
appropriate qualifications for the task. The qualified personnel must know
and observe the following standards and directives:
IEC 364 / CENELEC HD 384 or DIN VDE 0100
IEC-Report 664 or DIN VDE 0110
national accident prevention regulations or VBG 4
uRead the available documentation before carrying out the installation and
commissioning. Incorrect handling of the transistor controller can lead to
injury to persons or to material damage. It is vital that you observe the
technical data and the information on connection requirements (nameplate
and documentation).
uThe transistor controllers contain electrostatic-sensitive components,
which can be damaged by incorrect handling. Discharge your body before
touching the transistor controller. Avoid contact with highly insulating
materials (artificial fibres, plastic films etc.). Place the transistor controller
on a conductive surface.
uKeep all covers and cabinet doors closed during operation. Otherwise, there
are severe hazards with the danger of death or severe injury or material
damage.
uIn operation, depending on the degree of enclosure protection, transistor
controllers can have bare components which are live and have hot surfaces.
Control and power connections can also carry a high voltage, even though
the motor is not rotating.
uNever disconnect or connect the transistor controller when it is live. There
is a risk of electric arcing with damage to contacts and personal injury.
uWait at least two minutes after disconnecting the transistor controller from
the mains supply voltage (at least five minutes if Option -24V- is fitted),
before touching live sections of the equipment (e.g. contacts, screwed
connections) or undoing any connections. Capacitors can still have a
dangerous voltage after the supply has been switched off. To be safe,
measure the voltage in the DC-link, and wait until it has fallen below 20V.

Sta
n-
dar
ds
an
d
Di-
rec
tive
s/
CE
Page - D - Standards and Directives / CE
Series 04S 12.99 Kollmorgen
Standards and Directives
Transistor controllers are components which are intended to be installed in electrical equipment
and machinery.
When the transistor controllers are incorporated into equipment or machinery, then the start of
prescribed usage is prohibited until it has been confirmed that the equipment/machine fulfils the
requirements of the EC Directive on Machines 89/392/EEC, the EC EMC Directive (89/336/EEC)
and the EC Low Voltage Directive 73/23/EEC.
EN 60204 and EN 292 must also be observed.
The Low Voltage Directive 73/23/EEC does not apply to the 04S amplifier, because of the low
rated voltage.
The manufacturer of the equipment or machine is responsible for ensuring that it meets the limits
which are laid down by EMC regulations. Advice on the correct installation for EMC – such as
shielding, grounding, arrangement of filters – is included in this documentation.
-conformance
Conformance with the following Directive is mandatory for the supply of transistor controllers
within the European Community:
since 01 January 1996 : EC EMC Directive 89/336/EEC
The 04S series of transistor controllers have been tested in an authorised testing laboratory, in a
specified configuration with the system components as shown in Chapter II.
Any divergence from the configuration and installation which are described in the documentation
means that you will yourself be responsible for carrying out new measurements to ensure that the
regulatory requirements are fulfilled.

I General
I.1 Introduction
This manual explains the installation, commissioning, adjustment and adaptation of the 04S
transistor controller.
The manual is divided into 6 chapters :
Chapter 1: General Information
Chapter 2: Notes on Installation and Commissioning
Chapter 3: Functions and Options
Chapter 4: Peripheral equipment
Chapter 5: Drawings
Chapter 6: Appendix and Ordering Information
We offer training and introductory courses on request.
I.2 Prescribed usage (“Use as directed”) of the transistor controller
The transistor controllers are intended exclusively for driving DC motors under speed and/or
torque control. The transistor controllers are installed as components in electrical systems or
machines, and it is only permissible to operate them as integral components of these systems or
machines.
Series 04S transistor controllers are operated off the 3-phase industrial mains supply, with
earthing, through an isolating transformer. This isolating transformer must meet the
specification in Chapter IV.1.
The transistor controllers may only be operated in a closed cabinet, observing the ambient
conditions defined in Chapter I.6.2.
The units must be mounted in a standard industrial 19"-rack housing, and contacts may only be
made through one of our module back-panels or a type FH24+7 mating connector.
In accordance with the EC Machine Directive and accident prevention laws, you are obliged to
carry out a hazard analysis of the machine before commissioning the transistor controller.
Chapter I General Page I - 1
Kollmorgen 12.99 Series 04S
Transport : only by personnel which know-how in the handling of
electrostic-sensitive devices.
Installation : only by qualified persons, trained in electrical engineering.
Commissioning: only by qualified persons, with extensive knowledge of
electrical engineering and drive technology.
We can only guarantee the correct functioning of the transistor controller when
our isolating transformers and accessories are used.
We can only guarantee the conformance of the transistor controller with the EC
EMC Directive 89/336/EEC under the condition that only the components shown
in Chapter II are used and that the rules for installation are followed.

I.3 Abbreviations used in this manual
Abbrev. Meaning Abbrev. Meaning
AGND analog ground PELV protected low voltage
BTB system ready for operation PSTOP limit-switch input for clockwise rotation
CE European Community PWM pulse-width modulation
DGND digital ground TA tacho generator
DIN Deutsches Institut für Normung
(German Standards Institute) RBallast ballast resistor
EMC electromagnetic compatibility PLC programmable logic controller
EN European standard SW setpoint
ESD electrostatic discharge V AC AC voltage
IDC analog current monitor V DC DC voltage
LED light-emitting diode VDE
Verein deutscher Elektrotechniker
(Association of German Electrical
Engineering Technicians)
NSTOP limit-switch input for CCW rotation VTA analog speed monitor
I.4 Nameplate
The nameplate illustrated below is fixed to the transistor controller. The information shown
below is printed in the individual sections.
- A.4. 028.
6/10
Page I - 2 General Chapter I
Series 04S 12.99 - A.4.028.6/10 Kollmorgen
Trans. controller type Serial number Options
Power supply,
Installed load
Rated current Protection

I.5 04S equipment description
Design
Plug-in 19”-rack module, connection through module back-panels or mating connector FH24+7
Size
Unit Format Height units (HE) Width units (TE)
04S Eurocard,
220mm insertion depth 3HE (100mm) 12TE (approx. 61mm)
Options
-24V- supply for the electronics from an external 24V power supply
-IxR- speed control without a tachometer
--- front panel
Mains power supply
— 3-phase via isolating transformer
— 1-phase via isolating transformer
— DC-supply (battery)
Function
The 04S transistor controller is equipped for driving DC motors in 4-quadrant operation with
tachometer feedback. The power section is implemented as a pulse-width modulated transistor
stage with V-MOS transistors.
Variants
04S-M60-8-PB : rated output current 8A, with “soft” ballast characteristic
04S-M60-12-PB : rated output current 12A, with “soft” ballast characteristic
Accessories
Isolating transformers : series 3TxxK-60 (see Chapter IV.1)
-FH24+7- : mating connector DIN41612-M24+7 with solder contacts
F back-panels : instrument connections are accessible from the back,
via plug terminals for the control signals and studs/flat pin
connectors for the power connections
R back-panels : instrument connections are accessible from the front,
plug terminals for the control signals and studs/flat pin
connectors for the power connections
19”-rack modules : 19” base units in various widths, with F or R back-panels
Chapter I General Page I - 3
Kollmorgen 12.99 Series 04S
The following transistor controllers must be operated with forced convection:
— all 04S transistor controllers with rated output currents > 8A
— all 04S transistor controllers at ambient temperatures > 45°C

I.5.1 04S functional units
The following circuit sections are built onto a single Eurocard, 199x100x12TE with
SMD-technology:
n3-phase power supply with smoothing capacitors (-P-)
nsingle phase supply (any phase with the rated voltage, possibly with extra
smoothing capacitance) is possible
nfuses for DC-link, ballast circuit and auxiliary power supply
nballast circuit with -w- characteristic
n4-quadrant output stage (V-MOS transistors)
nauxiliary supply, optionally (solder links) supply from the DC-link
or an external 24 V DC source
n2 differential setpoint inputs
ninput for DC tacho
nEnable input
nlimit-switch inputs positive / negative
nintegral-off input for driving up to a fixed stop
nI2t monitoring for actual current value
nPI current and speed controller
ntrimmer potentiometer and fixed components for all important settings
nsolder links for changing to IxR compensation for optional operation with
tachometer or armature voltage control
n24 V logic with electrically isolated optocouplers for the control signals, PLC-compatible
nsystem ready (BTB) relay with floating contact
ndisplay LEDs for operational readiness / fault
n±15 V auxiliary voltage outputs, ±20 mA
Protective and monitoring functions
nprotected from short-circuit / earth short on the motor connection terminals
nmonitoring of the operating voltages
ntemperature monitoring of the output stage
nfuse-protection of: ballast circuit, DC-link, auxiliary supply
nI2t monitoring of the amplifier and motor
novervoltage protection
Page I - 4 General Chapter I
Series 04S 12.99 Kollmorgen

I.6 Technical data
I.6.1 04S technical data
Rated data units 04S-M60/8-PB 04S-M60/12-PB
Rated supply voltage V~ 3x43 3x43
Rated installed load kVA 0.5 0.75
Rate DC-link voltage V= 60 60
Minimum DC-link voltage V= 18 18
Rated output current A 8 12
Peak output current A 20 20
Switch-on threshold of ballast circuit V 85 85
Switch-off threshold of ballast circuit V 75 75
Pulse power of ballast circuit W 1000 1000
Continuous power of ballast circuit W 35 35
Overvoltage switch-off threshold V 100 100
Form factor of the output current (under rated conditions
with 0.5mH min. load inductance of the motor ) — 1.01 1.01
Bandwidth of the subordinate current controller kHz 1 1
Output stage clock frequency kHz 8.5 8.5
Residual voltage drop at rated current V 4 4
Quiescent dissipation, output stage disabled W 7 7
Dissipation at rated current ( incl. power supply losses,
without ballast dissipation ) W40 80
Auxiliary voltage outputs V ±15 ±15
mA 20 20
Inputs
Setpoint 1, fixed setting V ±10 ±10
Setpoint 2, adjustable 0 — 100% V ±10 ±10
Max. common mode voltage (both setpoint inputs) V ±10 ±10
Input resistance (both setpoint inputs) kW20 20
Max. input drift (both setpoint inputs) µV/K ±15 ±15
Tacho input, adjustable V ±8..75 ±8..75
Logic inputs V 24 24
mA 8 8
Connections
Controller: control signals and power signals DIN 41612 - M24 + 7
Backplane: control signals F03SMB Combicon 5.08 16-pin
R03SMB Combicon 5.08 2x8-pin
Power leads Studs M6
Mechanical
Weight kg 0.5
Dimensions mm
199x100x45
(single Eurocard,12 TE) compatible
with 220mm insertion depth
Chapter I General Page I - 5
Kollmorgen 12.99 Series 04S

I.6.2 Permissible ambient conditions, ventilation, mounting position
Transport temperature/humidity see Chapter VI.1
Storage temperature/
humidity/duration see Chapter VI.1
Supply voltage tolerances
power stage
aux. supply (Option -24V-)
3x43V AC ±10%
min. 20V DC / max. 30V DC referred to -GND
Ambient temperature TAMB.
in operation
0 ... +45°C under rated conditions
+45 ... +55°C with derating 2.5%/°C (forced convection)
Humidity in operation 5 ... 85 % rel. humidity, no condensation
Site altitude up to 1000m a.m.s.l. without restriction
1000 ... 2500m a.m.s.l. with derating 1.5%/100m
Pollution level pollution level 2 according to EN60204/EN50178
Protection class IP 00
Mounting location / position in closed switchgear cabinet / normally vertical
Ventilation cont. current < 8A
and TAMB. < 45°C
cont. current ³8A
or TAMB. > 45°C
self-ventilating with natural convection (we always recommend
forced convection at higher loads or in narrow spaces).
forced convection
ensure that the incoming air is dust-free and that there is an
adequate supply of cooling air to the cabinet.
I.6.3 Cable cross-sections
In accordance with EN 60204 and taking account of the operating conditions in multi-axis
systems, we recommend the following cross-sections :
Controller type
Dimension
04S-M60/8-PB
[mm²]
04S-M60/12-PB
[mm²]
AC connection 4i x 1.5 4i x 2.5
DC-link 2 x 1.5 2 x 2.5
Motor leads 3i x 1.5 3i x 2.5
Tacho 2 x 0.25 (twisted, shielded)
Setpoints 2 x 0.25 (twisted, shielded)
Control signals, BTB 0.5
+24 V / GND 1.0 (Option -24V-)
I.6.4 Fusing
Rated data Type 04S-M60/8-PB 04S-M60/12-PB
Fuse S1 (DC-link, 5x20mm) AT 10 12.5
Fuse S2 (auxiliary supply, Microfuse) AM 1 1
Fuse S3 (ballast, 5x20mm) AT 2.5 2.5
Page I - 6 General Chapter I
Series 04S 12.99 Kollmorgen

I.7 Interference suppression
If interference occurs in the CNC, or the analog or digital path measurement systems, then there
are some additional measures, listed below:
nadditional ferrite rings on the motor leads
nwiring in armature chokes (please use the types supplied by us)
nHF filter on the CNC setpoint output (RC combination 1kW/10nF)
In each case you will have to try out which measures bring sufficient reduction in interference.
I.8 Ballast circuit
When the motor is braked, energy is fed back to the transistor controller. This energy is
converted into heat in the ballast resistor. The ballast resistor is switched into circuit by the
ballast circuit.
The ballast circuit starts to respond at a DC-link voltage of 85V.
Repetitive loading causes the switch-on threshold of the ballast circuit to rise to 90V, thanks to
the built-in -w- characteristic, so that power sharing is achieved if several modules are
connected in parallel on the same DC-link bus.
You should make a rough calculation of the ballast power dissipation which is to be
expected, from the known drive data – especially for single axes.
The following method has proved itself for normal servo applications:
peak ballast power peak power of all amplifier0.33>× s
å
continuous power 0.03 continuous power ofballast >× all motors
å
Our in-house application department can provide further assistance in calculating the required
ballast power capacity for your system.
Chapter I General Page I - 7
Kollmorgen 12.99 Series 04S

This page has been deliberately left blank
Page I - 8 General Chapter I
Series 04S 12.99 Kollmorgen

II Installation and Commissioning
II.1 Important instructions
nInspect the nameplate of the controller. Check that the rated voltage and rated current
match the transformer and motor data.
nDo not switch on the operating voltage before you have read Chapter II of this manual
(Commissioning).
nMake sure that the maximum permissible rated voltage of 43V~ on terminals 20 , 22 , 32
is not exceeded. An excessive voltage on these terminals will destroy the ballast circuit
in the controller.
nMake sure that the controller has sufficient ventilation :
up to 8A rated current : vertical mounting, natural convection
above 8A rated current : vertical mounting, additional fan,
forced convection
An incorrect mounting position or a missing fan for rated currents above 8A will lead to
destruction of the controller.
nEnsure that the cables have an adequate cross-section, to avoid excessive losses and
overheating in the cables.
nUse twisted cables for setpoint, tacho and motor cables. Tacho and setpoint cables must
also be shielded. Observe the notes in Chapter II.2.1 .
nEarth the DC-link (Pin 28 or stud —GND/PE). A DC-link circuit which is not earthed can
endanger the operator of the equipment, in the event of an earth short in the motor or fault
currents in the GND lead. Furthermore,the electronics can be destroyed if the earth is
missing when there is a fault. An earth short in the motor will no longer be recognised if
the earth connection is missing.
nAll earth connections must be led out from a common star point, to avoid earth loops and
potential drops in the earth lead. Connect all earth leads to a PE busbar, for instance in
the switchgear cabinet.
nDo not earth the tachometer cable, since one side of the tacho connection in the
controller has a low-impedance connection to Analog-GND.
nTake care that the shielding is connected correctly :
Tacho shielding to the controller (Pin 28/stud —GND/PE)
or to the shielding connection terminal
Setpoint shielding to CNC-GND on the controls (single ended)
Motor cable shielding to the PE busbar, using a shielding terminal
nLoop the BTB contact (Pins 8bd or terminals 8,9) into the safety circuit of the system. Only
so can you be sure that the controller-ready function is monitored.
nThe ±15V auxiliary voltages must not be led out of the cabinet. This avoids capacitively or
inductively induced interference.
Chapter II Installation and Commissioning Page II - 1
Kollmorgen 12.99 Series 04S
Warning
Never connect or disconnect the transistor controller while the system is live.
In unfavourable circumstances this could result in the destruction of the electronics.
Capacitors can still have a residual charge up to 120 sec. after switching off the mains
supply. Measure the voltage in the DC-link, and wait until it has fallen below 20V.
Even when the motor is not rotating, control and power cables can still be live.

II.2 Installation
Only professional staff who are qualified in electrical engineering are allowed to install
the transistor controller.
The installation procedure is described as an example. A different procedure may be sensible or
necessary, depending on the application of the equipment.
We provide further know-how through training courses (on request).
Page II - 2 Installation and Commissioning Chapter II
Series 04S 12.99 Kollmorgen
Warning !
Protect the transistor controller from impermissible stress.
In particular, components must not be bent or insulation distances altered dur-
ing transport and handling.
Avoid touching electronic components and contacts.
Caution !
Only install and wire up the equipment when it is not live, i.e. when neither the
mains power supply nor the operating voltages of any other connected equip-
ment is switched on. Take care that the switchgear cabinet is safely discon-
nected (with a lockout, warning signs etc.).
The individual voltages will be switched on for the first time during commission-
ing.
Ground and PE symbols
The ground symbol X, which you will find in all the wiring diagrams, indicates
that you must take care to provide an electrically conductive connection with
the largest possible area between the component indicated and the mounting
plate in the switchgear cabinet. This connection is for the effective grounding of
HF interference. It must not be confused with the PE symbol W(protective meas-
ure to EN 60204) .
Grounding system and protective earthing
The DC-link circuit is earthed on one side, and supplied from the mains via an
isolating transformer which has a screen winding.
The reference potentials 0V/GND/PE (DC-link –) and AGND (control electronics)
are connected inside the instrument, for functional reasons.
The central connection to PE is made on the back-panel.

The following notes should make it easier for you to carry out the installation in a sensible
sequence, without overlooking anything.
19" rack module in a closed switchgear cabinet.
Follow Chapter I.6.2 .
The site must be free from conductive or aggressive materials.
Check that the transistor controller is properly ventilated and
keep to the permissible ambient temperature, Chapter I.6.2.
Mount the 19" rack module and peripheral components close
together, on an earthed mounting plate in the cabinet (see II.2.1).
Select cables according to EN 60204 and our specification
in Chapter I.6.3.
EMC-conform shielding and earthing: see Chapter II.2.1
Earth the mounting plate, motor housing, isolating transformer,
DC-link, and the CNC-GND of the controls (see Chapter II.2.1).
—Route power leads and control cables separately
—Loop the BTB contact into the safety circuit of the system
— Connect up the logic/digital control inputs to the controller
— Connect up the analog setpoint input and AGND
— Connect the tacho, with all shielding connected to shielding
terminals or EMC connectors
— Connect the motor leads, with the chokes close to the servo
amplifier and shielding to shielding terminals or EMC connectors
— Connect the main power voltage (see Chapter I.6.2 for max.
permissible values, use Seidel isolating transformer 3Txx )
Final check of the implementation of the wiring according to the
wiring diagrams which have been used.
Chapter II Installation and Commissioning Page II - 3
Kollmorgen 12.99 Series 04S
Site
Ventilation
Assembly
Grounding
Shielding
Cable selection
Final check
Wiring

II.2.1 - conform connections 04S, overview
- E.3.924.1/4
Page II - 4 Installation and Commissioning Chapter II
Series 04S 12.99 - E.3.924.1/4 Kollmorgen

II.2.2 Connection diagram 04S
- E.3.924.1/1
Chapter II Installation and Commissioning Page II - 5
Kollmorgen 12.99 - E.3.924.1/1 Series 04S

II.2.3 Module back-panels F03SMB and R03SMB
Type: F03SMB for 04S controllers, connections at the back
R03SMB for 04S controllers, connections at the front
The module back-panels are attached from behind in the 19” module. The transistor controller is
inserted into the module and plugged in to the back-panel. The electrical signals are made
available on the back-panel through terminals, studs and flat-pin connectors.
You can find an illustration of the back-panels in Chapter V.3 .
The table below shows the assignments of the signals to the connector pins.
II.2.3.1 Pin assignments for 04S / F03S-MB
Edge conn. 16-pin Short
M7/24 Combicon-conn. Signal name
(pin no.) (terminal no.) designation (solder print)
2d 1 Setpoint 1+ SW 1 +
2b 10 Pos.Stop PSTOP
2z 2 Setpoint 1- SW1-
4d 3 Setpoint 2+ SW 2 +
4b 11 Neg.Stop NSTOP
4z 4 Setpoint 2- SW2-
6d 6 Tacho– TA
6b 15 Integral Off IAB
6z 5 Tacho+ TA
8d 8 System Ready- BTB
8b 9 contact BTB
8z 16 Enable E
10db 12 Analog-GND (AGND) GND
10z --- Digital-GND (DGND) ---
12dbz 13 + 15V + 15
14dbz --- – 15V ---
--- 14 --- -15/24
16d --- 24V-DC aux. voltage ---
16b 7 Armature current R(IDC)
20 M6 stud ~25...43V ~ U1
22 M6 stud ~25...43V ~V1
24 M6 stud + Ucc +Ucc
26 Faston tab - 6.3 + Motor +M
28 M6 stud – Ucc / Analog-GND –GND/PE
30 Faston tab - 6.3 – Motor –M
32 M6 stud ~25...43V ~ W1
Page II - 6 Installation and Commissioning Chapter II
Series 04S 12.99 Kollmorgen
This manual suits for next models
2
Table of contents
Popular Controllers manuals by other brands
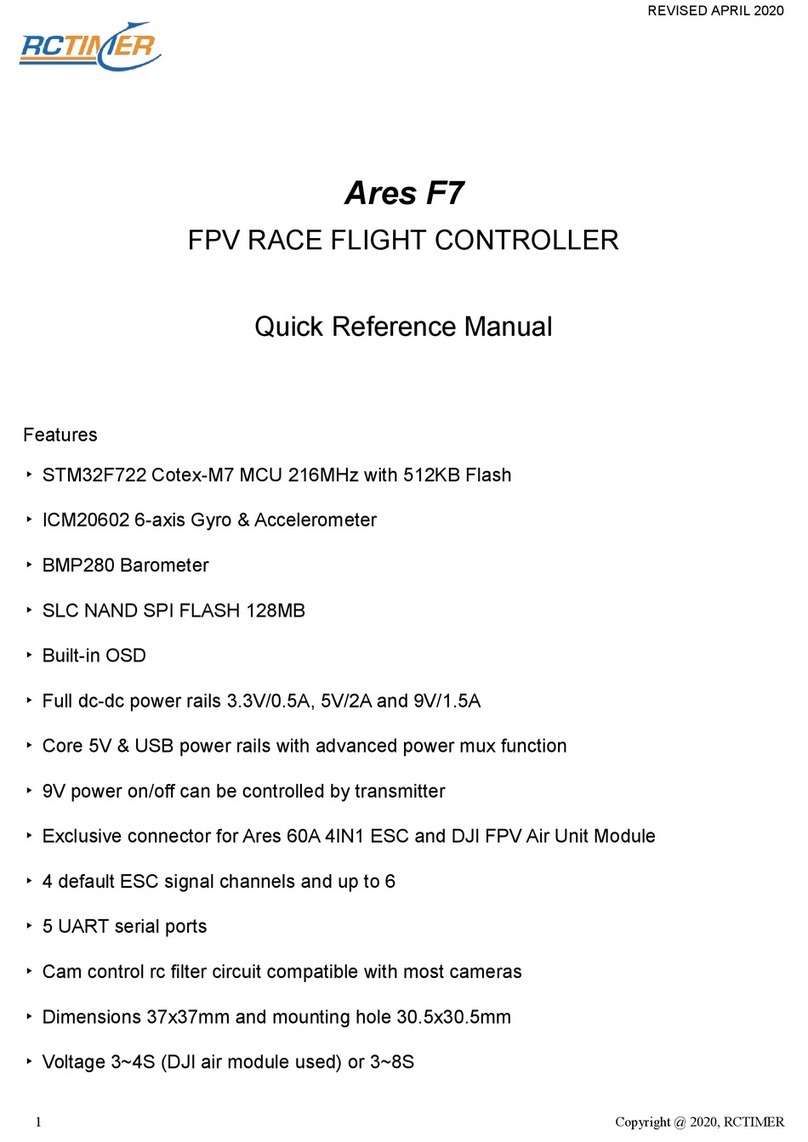
RCTimer
RCTimer Ares F7 Quick reference manual
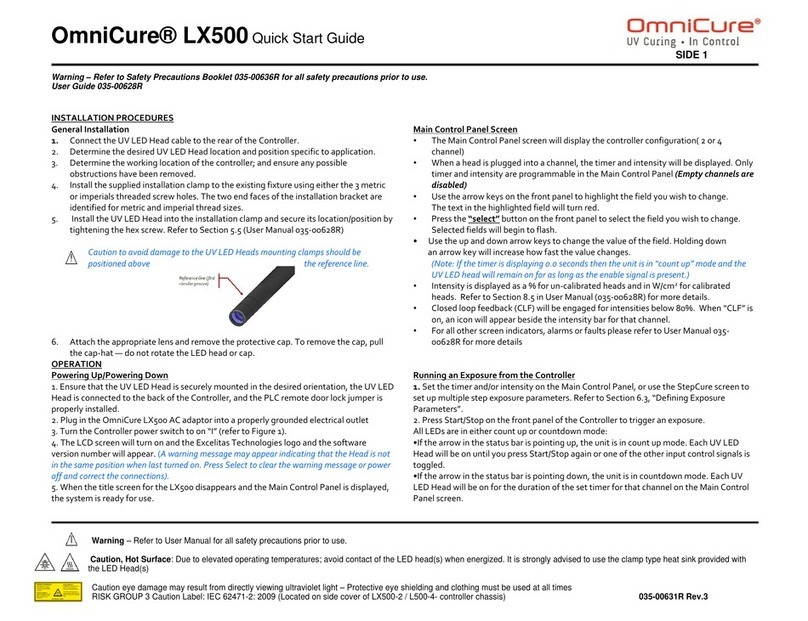
OmniCure
OmniCure LX500 quick start guide
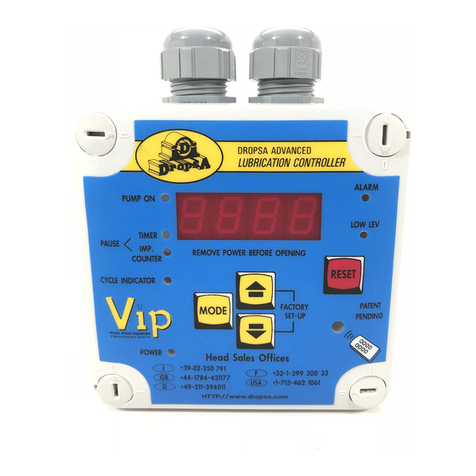
DROPSA
DROPSA ADVANCED LUBRICATION CONTROLLER INSTRUCTION AND PRODUCT DATA SHEET
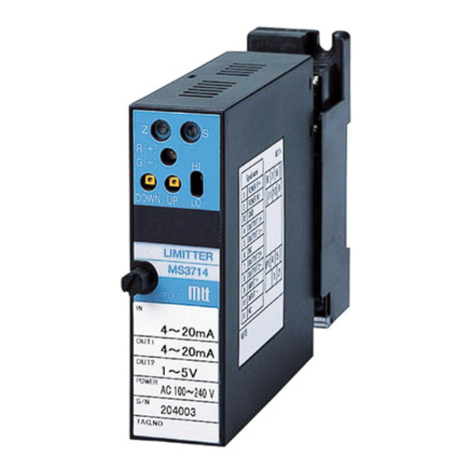
MTT
MTT MS3714 user manual
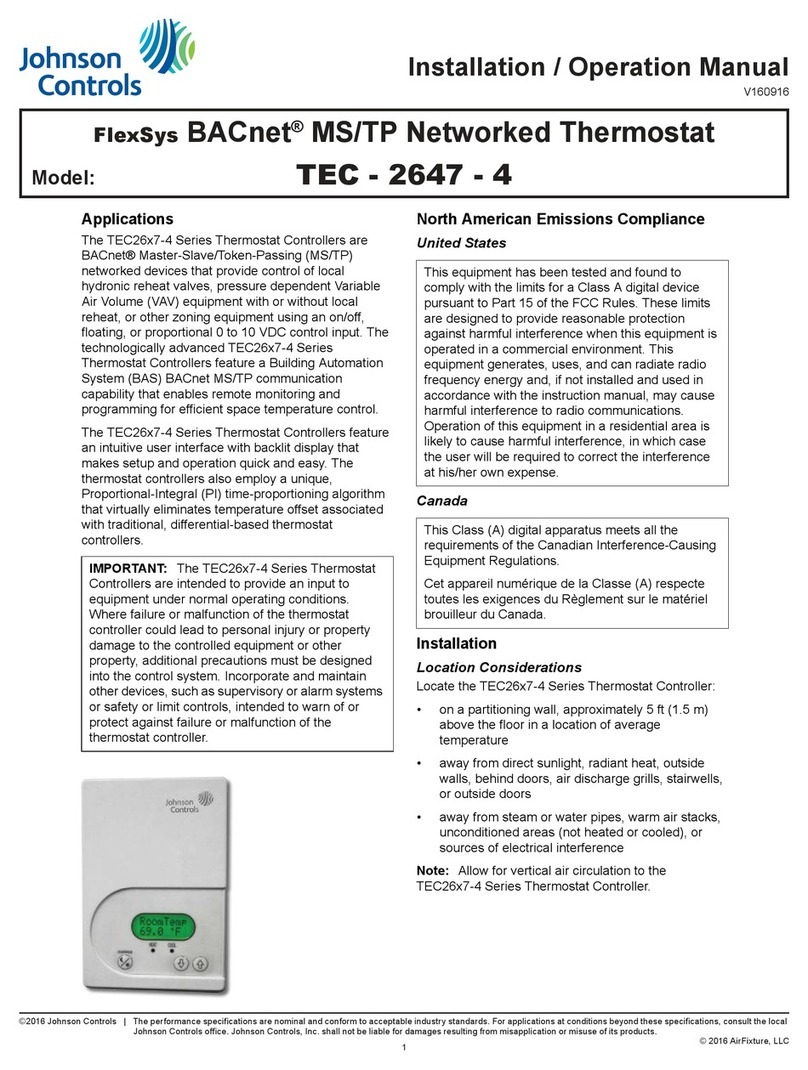
Johnson Controls
Johnson Controls TEC-2647-4 Installation & operation manual

Eurotech
Eurotech Helios Platform Hardware reference manual