Kongsberg RSER200-4 Guide

RSER200-4
Hardware Module Description
Kongsberg Maritime Part no.603444
300993/Ap27
October 2006

Document history
Document number: 300993
Rev. Ap27 October 2006 First version.
Note
The information contained in this document remains the sole property of Kongsberg Maritime AS. No
part of this document may be copied or reproduced in any form or by any means, and the information
contained within it is not to be communicated to a third party, without the prior written consent of
Kongsberg Maritime AS.
Kongsberg Maritime AS endeavours to ensure that all information in this document is correct and fairly
stated, but does not accept liability for any errors or omissions.
Warning
The equipment to which this manual applies must only be used for the purpose for which it was
designed. Improper use or maintenance may cause damage to the equipment and/or injury to personnel.
The user must be familiar with the contents of the appropriate manuals before attempting to operate
or work on the equipment.
Kongsberg Maritime disclaims any responsibility for damage or injury caused by improper installation,
use or maintenance of the equipment.
Comments
To assist us in making improvements to the product and to this manual, we welcome comments and
constructive criticism.
e-mail: km.documentation@kongsberg.com
P. O . B o x 4 8 3
N-3601 Kongsberg,
Norway
Kongsberg Maritime AS
Telephone:+4732285000
Telefax:+4732285010
Service:+4781535355
www.kongsberg.com

Hardware Module Description
Table of contents
Glossary....................................................................................................................4
1 OVERVIEW........................................................................ 5
1.1 Document user..........................................................................................................5
1.2 Module......................................................................................................................5
2 FUNCTION ........................................................................ 6
2.1 Power supply input...................................................................................................6
2.2 Serial Line Interfaces................................................................................................7
2.2.1 Link Channel interfaces................................................................................. 8
2.2.2 Field Channel interfaces ................................................................................ 8
2.2.2.1 RS232 typical .......................................................................................... 8
2.2.2.2 RS422 typical .......................................................................................... 9
2.2.2.3 RS485 typicals......................................................................................... 9
2.2.2.4 NMEA 0183 typical ............................................................................... 10
2.3 LED indicators .......................................................................................................10
2.4 USB interface .........................................................................................................12
2.5 Watchdog................................................................................................................12
3 TECHNICAL SPECIFICATIONS ......................................... 13
4 CONFIGURATION ............................................................ 14
4.1 Module identiÞcation .............................................................................................15
4.2 P1 to P3 - Link Channel connectors.......................................................................15
4.3 P4 - USB connector ................................................................................................16
4.4 X1 to X4 - Field channel terminal rows ................................................................. 16
4.5 RBUS A and RBUS B connector ...........................................................................17
5 INSTALLATION ............................................................... 18
6 REPLACEMENT ................................................................ 19
300993/Ap27 3

Kongsberg RSER200-4
Glossary
DI Digital Input
DO Digital Output
ESD Electrostatic Discharge
GND Signal ground
IE Instrumentation Earth
I/O Input/Output
LED Light Emitting Diode
MTBF Mean Time Between Failure
NMEA National Marine Electronics Association
PE Protective Earth
RIO200 Kongsberg Maritime Remote I/O 200 module family
RBUS Remote I/O Bus that covers both communication link and power
RBUS Power Electrical power supply to the RIO200 modules including Þeld
channels
RBUS Link RIO communication link based on multi-drop 2 Mbps RS485 with
Manchester encoding
RCU Remote Controller Unit
RS232 Electrical Interface standard for single ended serial data
communication
RS422 Electrical Interface standard for single ended, differential,
balanced serial data communication
RS485 Electrical Interface standard for differential, balanced, multipoint
serial data communication
RSER200–4 Serial line interface module
USB Universal Serial Bus
4300993/Ap27

Overview
1OVERVIEW
1.1 Document user
This document is intended to be used for HW engineering,
hook-up and maintenance. Physical interfaces and capabilities
are described.
1.2 Module
The RSER200-4 is a module in the Kongsberg RIO200 module
family. These modules provide functions such as I/O interface,
network hub/repeater and serial line interface. They have the
same shape and are mechanically mounted on a horizontal
dual-rail system.
The RSER200-4 is a four channel, galvanic isolated, serial
line, interface module that can be linked to one, two or three
controllers (RCUs). The four Þeld channels are individually
conÞgurable as either RS232, RS422, RS485 or NMEA 0183 for
connection to Þeld equipment. There are three Link Channel
interfaces for connection to the controllers.
The RSER200-4 is powered by the RBUS connectors.
The RSER200-4 contains the following features:
• Isolated serial line Þeld channels
• Run/error LED on front showing module status
• Blinking LEDs on front showing transmit and receive data
activity for each channel
• All internal voltages are monitored
• Allow hot module replacement
• Compliant to standards IEC 60945 and IACS E10
300993/Ap27 5

Kongsberg RSER200-4
2 FUNCTION
Figure 1 RSER200-4 function diagram
The RSER200-4 is a serial line module used for connecting
serial line equipment to RCU(s) in single or redundant controller
systems.
The module can be connected to up to three controllers (A, B, C)
via the three RJ45 connectors (P1, P2, P3), and up to four Þeld
equipment (1, 2, 3, 4) via the four terminal blocks (X1, X2, X3,
X4).
The module contains a USB interface (P4) intended for test and
service purposes. It provides functions to monitor the serial line
activity and the general status of the module.
The RSER200-4 consists of the main function blocks as shown
in the function diagram (see Figure 1 for block/function diagram
of the RSER200-4).
• Power supply
• Processor and channel logic
•LinkandÞeld interfaces
• USB interface
• LEDs (Status, RX and TX)
2.1 Power supply input
The RSER200-4 accepts single or dual 24 VDC as supply
voltage(s) via the RBUS A and RBUS B connectors.
6300993/Ap27

Function
The module is provided with “ideal diodes” to interconnect the
two power supplies without loss of voltage. It is also provided
with inrush current protection that limit the current to maximum
0.5 A. This allows plug and play functionality and system short
circuit protection.
Figure 2 Power block diagram for RSER200-4
2.2 Serial Line Interfaces
The illustration in Þgure below shows the switching principles
of RSER200-4.
One controller (A, B or C) can send serial data via one
RSER200-4 module to four serial line Þeld channels. This is
achieved by de-multiplexing.
Dual or triple redundant controllers can be connected to the
module. The controllers will receive data simultaneously, but
only one is allowed to send. The logic for which controller (A, B
or C) that shall send is determined by the controllers.
Figure 3 Serial line switching principles
300993/Ap27 7

Kongsberg RSER200-4
2.2.1 Link Channel interfaces
Three identical Link Channel interfaces A (P1), B (P2), and C
(P3) are available. Each Link Channel interface is connected
using a cable connection between one dedicated RJ45 connector
on the RCU and one of the RJ45 connectors P1, P2, and P3 on
RSER200-4. The Link Channel interfaces are implemented with
high speed RS422.
2.2.2 Field Channel interfaces
Four isolated, identical, serial line Þeld channels 1, 2, 3 and
4 are available. Each of them can be conÞgured by the system
conÞguration interface to handle either RS232, RS422, RS485 or
NMEA 0183 standards.
2.2.2.1 RS232 typical
Figure 4 RS232 interface typical
8300993/Ap27

Function
2.2.2.2 RS422 typical
Figure 5 RS422 interface typical
2.2.2.3 RS485 typicals
Figure 6 RS485 interface typical, 3 wires
300993/Ap27 9

Kongsberg RSER200-4
Figure 7 RS485 interface typical, 6 wires
2.2.2.4 NMEA 0183 typical
Figure 8 NMEA 0183 interface typical
2.3 LED indicators
The module front is provided with several LEDs on the module
front. The LED layout is shown on Figure 9 on page 11
10 300993/Ap27

Function
Figure 9 LED indicators layout
Table 1 LED indicators on module front
LED
name
Colour, state Function
Green, Þxed Normal operation. The module is OK and it has
communication with at least one RCU
Red, Þxed Serious HW or SW error condition occurred,
watchdog activated
Status
Red, ßashing During boot
RX P1 Receiving data on link channel A (P1)
RX P2 Receiving data on link channel B (P2)
RX P3 Receiving data on link channel C (P3)
RX P4
Yel low, ßashing
Receiving data on USB port (P4)
TX P1 Transmitting data on link channel A (P1)
TX P2 Transmitting data on link channel B (P2)
TX P3 Transmitting data on link channel C (P3)
TX P4
Green, ßashing
Transmitting data on USB port (P4)
RX X1 Receiving data on Þeld channel X1
RX X2 Receiving data on Þeld channel X2
RX X3 Receiving data on Þeld channel X3
RX X4
Yel low, ßashing
Receiving data on Þeld channel X4
TX X1 Transmitting data on Þeld channel X1
TX X2 Transmitting data on Þeld channel X2
TX X3 Transmitting data on Þeld channel X3
TX X4
Green, ßashing
Transmitting data on Þeld channel X4
Note
All RX, TX LEDs except for P4 will be lit during boot.
300993/Ap27 11

Kongsberg RSER200-4
2.4 USB interface
A USB port (USB 2.0, full speed, 12 Mbit) is included on the
module to facilitate direct communication with the module
controller for test and service purposes. The interface uses a USB
B type connector (P4) and is protected by a transient suppressor.
2.5 Watchdog
A built-in watchdog resets the module program if a software
error occurs.
12 300993/Ap27

Technical speciÞcations
3 TECHNICAL SPECIFICATIONS
Table 2 Technical speciÞcations
Power speciÞcations
Input voltage +24 VDC nominal (+18 - +32 VDC)
Power ON rise time Maximum 20 ms/V monotonic
Current consumption 50 mA
Power ON inrush current Maximum 0.5 A
Link Channels
Bit rate 1 Mbps
Cable length, maximum 100 m
Cable for link channels Most important parameter: Capacitance <= 50 pF/m
Interface type RS422
Serial line Þeld channels
Interface types RS232, RS422, RS485, NMEA 0183
Bit rate 300 bps - 115 kbps
Connections
Power supply RBUS A and RBUS B, Phoenix 5-pole T-BUS™
connectors
Link channels (P1 to P3) RJ45 unshielded
Field channels ( on X1 to X4) Terminal blocks w/screw connections
USB port (P4) Standard USB B connector
Watchdog
Watchdog timeout Maximum 1 sec., programmable
Mechanical speciÞcation
Size (WxHxD) 35 x 130 x 130 mm
Weight 0.34 kg
Mounting Snap on dual DIN-rail
Environmental requirements
Operating temperature -15 °C - +70 °C
Storage temperature -25 °C - +70 °C
Vibration 0.7 g
IP class IP20
Compliant to standards IEC 60945 and IACS E10
Life cycle speciÞcations
MTBF Not available
300993/Ap27 13

Kongsberg RSER200-4
4 CONFIGURATION
The illustration below shows the layout of the RSER200-4
module.
Figure 10 Layout of RSER200-4
The following sections describe the module label layout, and the
connectors’ layout and pin allocation.
14 300993/Ap27

ConÞguration
4.1 Module identiÞcation
There is a module identiÞcation label on each module. For any
communication with Kongsberg Maritime on this module you
should refer to the part number (Part#), revision (Rev.) and serial
number (Serial#). The information is also available from the
system.
Figure 11 Module identiÞcation label
4.2 P1 to P3 - Link Channel connectors
These connectors are RJ45, 8 pin, unshielded.
The Link Channel connection to RCU has to use a straight (not
crossed) cable with all 8 pins in use.
Figure 12 Front view of RJ45 with pin layout
(Vs090019a)
1
8
Table 3 Link Channel connectors (RJ45) pin allocation
Pin no. Name Function
1RXn-P Link Channel #n Receive, Positive terminal
2RXn-N Link Channel #n Receive, Negative terminal
3TXn-P Link Channel #n Transmit, Positive terminal
4CTSn-P
Link Channel #n Clear To Send, Positive
terminal, Input
5CTSn-N Link Channel #n Clear To Send, Negative
terminal, Input
6TXn-N Link Channel #n Transmit, Negative terminal
7Not connected
80V
0 V, signal reference terminal
where n = 1 for P1, 2 for P2, 3 for P3
300993/Ap27 15

Kongsberg RSER200-4
4.3 P4 - USB connector
This connector i an USB type B, 6 pin, shielded.
Table 4 USB B pin allocation
Pin no. Name Function
1VCC
+5 VDC from host computer
2USB_D-
USB Transceiver Data Low
3USB_D+
USB Transceiver Data High
40V
0 V, signal reference terminal
Note
Connector housing of USB connector is terminated to 0 V via an
HF capacitor within the module.
4.4 X1 to X4 - Field channel terminal rows
There are four terminal rows on the front of the module (X1 to
X4). Each terminal row is associated with one Þeld channel.
Each terminal row is divided into two terminal blocks.
The terminal blocks are provided with a removable header with
threescrewterminals(terminalsnumbered1to3and4to6
respectively) on each (see Þgure below). Each terminal block
is provided with coding pins that prevent you from swapping
headers between X1 and X2, and between X3 and X4.
Figure 13 X1 to X4 terminal layout
Table 5 Field channel terminal allocation
Pin no. Name Function
1RX_n/RXP_n RX for RS232 or RXP for RS422/485/NMEA
2CTS_n/RXN_n CTS for RS232 or RXN for RS422/485/NMEA
3 SERn_0V Signal ground reference for n
4TX_n/TXP_n TX for RS232 or TXP for RS422/485/NMEA
5RTS_n/TXN_n RTS for RS232 or TXN for RS422/485/NMEA
6 SERn_0V Signal ground reference for n
16 300993/Ap27

ConÞguration
where n = 1 for X1, 2 for X2, 3 for X3, 4 for X4
4.5RBUSAandRBUSBconnector
The two RBUS A and RBUS B connectors are of type 5-pole
Phoenix T-BUS™connectors. They are located on the dual-rail
and provides RBUS Power connections.
The module is provided with printed circuit board based
connectors that ÞttotheT-BUS™connectors.
Figure 14 RBUS A/B rail connector terminal layout
Table 6 RBUS A and RBUS B connector terminal allocation
Pin no. Name Function
1RE Reference Earth
2
3
Not connected
4 0 VDC 0 VDC, power terminal
524 VDC +24 VDC, power terminal
300993/Ap27 17

Kongsberg RSER200-4
5INSTALLATION
Caution
The module can be unpacked and handled without ESD
protection, but electrostatic discharge can damage
components on the module when terminating wires and
cables to it. Therefore always wear a correctly-connected
earthing strap when working on the module.
1Open the module front door.
2Label the module with the appropriate module name.
3Hook the RSER200-4 on to the lower DIN rail in a 30° angle
and snap it to the RBUS connectors and upper DIN rail in
one rotating movement.
4Connect the link channel patch cables to the connectors P1
to P3 as appropriate.
5Connect the Þeld channel cable wires to the terminal blocks
X1 to X4 on the RSER200-4 as appropriate. Use a ßat-bit
screwdriver to fasten the wires. The terminal blocks accept
up to 2.5 mm2wire dimension.
6Turn ON power. The module status LED will be lit red
initially during start-up. The module status LED will be
lit green when the RSER200-4 communication with a
controller (RCU) is established.
18 300993/Ap27

Replacement
6REPLACEMENT
Caution
The module can be unpacked and handled without ESD
protection, but electrostatic discharge can damage
components on the module when terminating wires and
cables to it. Therefore always wear a correctly-connected
earthing strap when working on the module.
1Remove the terminal block headers on X1 to X4 that are
in use (the ones with wires attached). Use a ßat-bladed
screwdriver and jack the headers out in a vertical direction
according to steps 1 to 4 in the following illustration.
2Unplug the Link Channel cables connected to connectors
P1 to P3.
300993/Ap27 19

Kongsberg RSER200-4
3Remove the RSER200-4 module from the bus rails by using
a screwdriver to unlock spring buckle.
4Put the module aside and label it with its fault symptoms.
5Label the new RSER200-4 module.
6On the new module remove the same terminal block headers
as were removed on the replaced module, by using a
ßat-bladed screwdriver and jack them out, one by one.
7Hook the RSER200-4 on to the lower DIN rail in a 30° angle
and snap it to the RBUS connectors and upper DIN rail in
one rotating movement.
20 300993/Ap27
This manual suits for next models
1
Table of contents
Popular Control Unit manuals by other brands
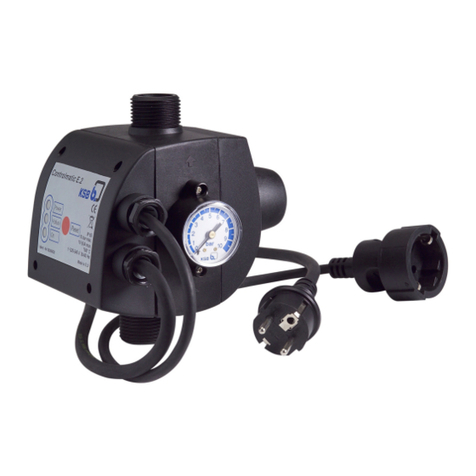
KSB
KSB Controlmatic E.2 Installation & operating manual
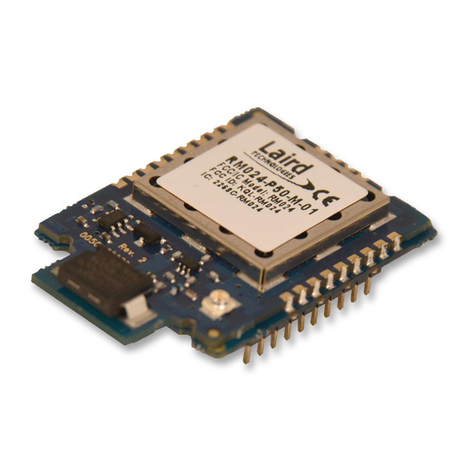
Laird
Laird RM024 Hardware integration guide

Honeywell
Honeywell V5421C installation instructions
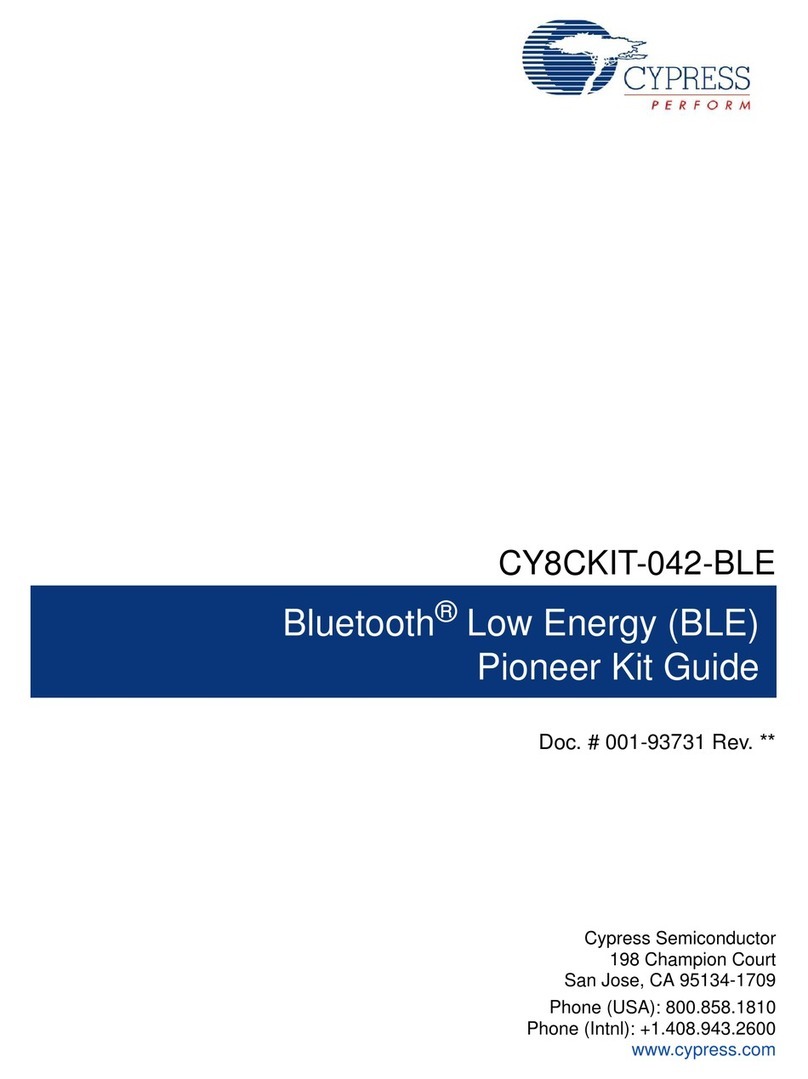
Cypress Semiconductor
Cypress Semiconductor CY8CKIT-042-BLE Guide
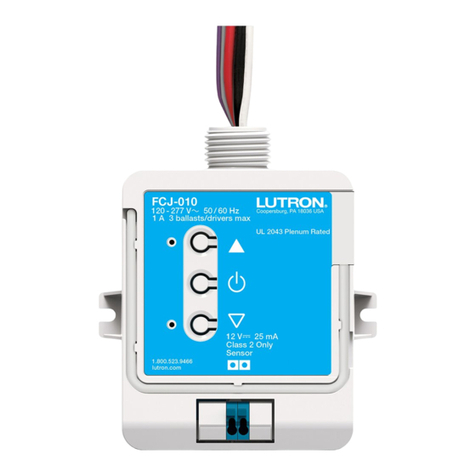
Lutron Electronics
Lutron Electronics PowPak FC-SENSOR manual
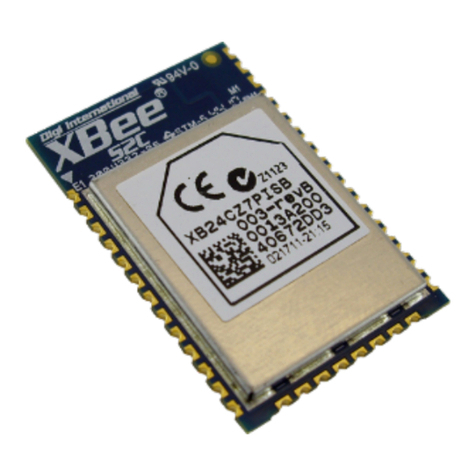
Digi
Digi XBee ZigBee S2C Getting started guide