KSB Hya-Solo DV Installation instructions

Pressure Booster System
Hya-Solo DV
From series 2014w33
Installation/Operating Manual

Legal information/Copyright
Installation/Operating Manual Hya-Solo DV
Original operating manual
All rights reserved. The contents provided herein must neither be distributed, copied, reproduced, edited or
processed for any other purpose, nor otherwise transmitted, published or made available to a third party without
the manufacturer's express written consent.
Subject to technical modification without prior notice.
© KSB Aktiengesellschaft, Frankenthal 26.03.2015

Contents
Glossary .................................................................................................5
1 General ..................................................................................................6
1.1 Principles ........................................................................................................... 6
1.2 Installation of partly completed machinery .................................................... 6
1.3 Target group ..................................................................................................... 6
1.4 Other applicable documents ............................................................................ 6
1.5 Symbols ............................................................................................................. 6
2 Safety .....................................................................................................7
2.1 Key to safety symbols/markings ....................................................................... 7
3 Software Changes .................................................................................8
4 Transport/Temporary Storage/Disposal ...............................................9
4.1 Checking the condition upon delivery ............................................................ 9
4.2 Transport ........................................................................................................... 9
4.3 Storage/preservation ........................................................................................ 9
4.4 Return to supplier .......................................................................................... 10
4.5 Disposal ........................................................................................................... 10
5 Description ..........................................................................................11
5.1 General description ........................................................................................ 11
5.2 Designation ..................................................................................................... 11
5.3 Name plate ...................................................................................................... 11
5.4 Design details .................................................................................................. 11
5.5 Configuration and function ........................................................................... 12
5.6 Noise characteristics ....................................................................................... 13
5.7 Scope of supply ............................................................................................... 13
5.8 Dimensions and weights ................................................................................ 13
5.9 Terminal wiring diagram ............................................................................... 13
6 Installation at Site ...............................................................................19
6.1 Installation to DIN 1988 ................................................................................. 19
6.2 Checks to be carried out prior to installation ............................................... 19
6.3 Installing the pressure booster system .......................................................... 19
6.4 Installing the piping ....................................................................................... 20
6.5 Installing unpressurised inlet tanks ............................................................... 21
6.6 Fitting the dry running protection device .................................................... 22
6.7 Connection to power supply .......................................................................... 22
7 Commissioning/Start-up/Shutdown ...................................................24
7.1 Commissioning/start-up ................................................................................. 24
7.2 Switching on the pressure booster system .................................................... 25
7.3 Check list for commissioning/start-up ........................................................... 25
Contents
Hya-Solo DV 3 of 54

7.4 Shutdown ........................................................................................................ 26
8 Operating the Pressure Booster System ............................................27
8.1 Control panel functions ................................................................................. 27
8.2 Menu structure ............................................................................................... 30
8.3 Access levels .................................................................................................... 31
8.4 Displaying and changing parameters ............................................................ 31
8.5 Monitoring ...................................................................................................... 32
8.6 Description of parameters ............................................................................. 33
8.7 Adjusting the settings .................................................................................... 34
9 Servicing/Maintenance .......................................................................41
9.1 General information/Safety regulations ....................................................... 41
9.2 Servicing/inspection ........................................................................................ 42
10 Trouble-shooting ................................................................................44
10.1 Hya-Solo DV .................................................................................................... 44
10.2 PumpDrive ....................................................................................................... 45
11 Related Documents ............................................................................47
11.1 List of components ......................................................................................... 47
12 EC Declaration of Conformity ............................................................49
13 Certificate of Decontamination .........................................................50
14 Commissioning Report .......................................................................51
Index ....................................................................................................52
Contents
4 of 54 Hya-Solo DV

Glossary
Accumulator
The accumulator serves to compensate for pres-
sure losses in the piping system downstream of
the pressure booster system which may be
caused by the consumption of small quantities
of water. As a result, the frequency of starts of
the pressure booster system is minimised.
Automatic mode
The pump is started as a function of pressure
and stopped as a function of flow.
Certificate of decontamination
A certificate of decontamination is enclosed by
the customer when returning the product to
the manufacturer to certify that the product
has been properly drained to eliminate any en-
vironmental and health hazards arising from
components in contact with the fluid handled.
Dry running protection
Dry running protection devices prevent the
pump from being operated without the fluid to
be handled, which would result in pump dam-
age.
Manual mode
In manual mode, the pressure booster system is
operated directly on mains power, independ-
ently of the control unit.
Glossary
Hya-Solo DV 5 of 54

1 General
1.1 Principles
This operating manual is supplied as an integral part of the type series and variants
indicated on the front cover. The manual describes the proper and safe use of this
equipment in all phases of operation.
The name plate indicates the type series/size, the main operating data and the order
number. The series/serial number uniquely identifies the pressure booster system and
serves as identification for all further business processes.
In the event of damage, immediately contact your nearest KSB service centre to
maintain the right to claim under warranty.
Noise characteristics see (⇨ Section 5.6 Page 13)
1.2 Installation of partly completed machinery
To install partly completed machinery supplied by KSB refer to the sub-sections under
Servicing/Maintenance.
1.3 Target group
This operating manual is aimed at the target group of trained and qualified specialist
technical personnel.
1.4 Other applicable documents
Table 1: Overview of other applicable documents
Document Contents
Sub-supplier product literature Operating manuals, logic diagram and other
product literature of accessories and integrated
machinery components
1.5 Symbols
Table 2: Symbols used in this manual
Symbol Description
✓Conditions which need to be fulfilled before proceeding with the
step-by-step instructions
⊳Safety instructions
⇨Result of an action
⇨Cross-references
1.
2.
Step-by-step instructions
Note
Recommendations and important information on how to handle
the product
1 General
6 of 54 Hya-Solo DV

2 Safety
All the information contained in this section refers to hazardous situations.
2.1 Key to safety symbols/markings
Table 3: Definition of safety symbols/markings
Symbol Description
!DANGER
DANGER
This signal word indicates a high-risk hazard which, if not avoided,
will result in death or serious injury.
!WARNING
WARNING
This signal word indicates a medium-risk hazard which, if not avoi-
ded, could result in death or serious injury.
CAUTION
CAUTION
This signal word indicates a hazard which, if not avoided, could re-
sult in damage to the machine and its functions.
General hazard
In conjunction with one of the signal words this symbol indicates a
hazard which will or could result in death or serious injury.
Electrical hazard
In conjunction with one of the signal words this symbol indicates a
hazard involving electrical voltage and identifies information
about protection against electrical voltage.
Machine damage
In conjunction with the signal word CAUTION this symbol indicates
a hazard for the machine and its functions.
!DANGER
2 Safety
Hya-Solo DV 7 of 54

3 Software Changes
The software has been specially created for this product and thoroughly tested.
It is impermissible to make any changes or additions to the software or parts of the
software. Software updates supplied by KSB are excluded from this rule.
3 Software Changes
8 of 54 Hya-Solo DV

4 Transport/Temporary Storage/Disposal
4.1 Checking the condition upon delivery
1. On transfer of goods, check each packaging unit for damage.
2. In the event of in-transit damage, assess the exact damage, document it and no-
tify KSB or the supplying dealer (as applicable) and the insurer about the dam-
age in writing immediately.
4.2 Transport
NOTE
The pressure booster system is bolted to a pallet and wrapped in plastic foil for
shipping and temporary storage. All connecting points are capped.
DANGER
Pressure booster system tipping over
Risk of injury by falling pressure booster system!
▷Never suspend the pressure booster system by its power cable.
▷Observe the applicable local accident prevention regulations.
▷Pay attention to the weight data and the centre of gravity.
▷Use suitable and permitted transporting equipment, e.g. crane, forklift or ele-
vating platform truck.
▷Attach the pressure booster system to crane lifting tackle as shown, or use a
forklift or pallet truck to move the pallet.
Fig. 1: Transporting the pressure booster system
✓The pressure booster system has been checked for in-transit damage.
1. Make sure the transport equipment is suitable for safely carrying the indicated
load.
2. Transport the pressure booster system to the place of installation.
3. Attach the pressure booster system to the lifting tackle as shown, lift it off the
pallet and dispose of the pallet.
4. Use suitable lifting equipment to lift the pressure booster system and carefully
put it down at the place of installation.
4.3 Storage/preservation
If commissioning is to take place some time after delivery, we recommend that the
following measures be taken when storing the pressure booster system:
4 Transport/Temporary Storage/Disposal
Hya-Solo DV 9 of 54

CAUTION
Damage during storage by frost, moisture, dirt, UV radiation or vermin
Corrosion/contamination of pressure booster system!
▷Store the pressure booster system in a frost-proof room. Do not store outdoors.
CAUTION
Wet, contaminated or damaged openings and connections
Leakage or damage of the pressure booster system!
▷Only open the openings of the pressure booster system at the time of installa-
tion.
Store the pressure booster system in a dry, protected room where the atmospheric
humidity is as constant as possible.
4.4 Return to supplier
1. Drain the pressure booster system as per operating instructions.
2. Always flush and clean the pressure booster system, particularly if it has been
used for handling noxious, explosive, hot or other hazardous fluids.
3. If the pressure booster system has handled fluids whose residues could lead to
corrosion in the presence of atmospheric humidity or could ignite upon contact
with oxygen, the pressure booster system must also be neutralised and treated
with anhydrous inert gas to ensure drying.
4. Always complete and enclose a certificate of decontamination when returning
the pressure booster system. (⇨ Section 13 Page 50)
Always indicate any safety and decontamination measures taken.
NOTE
If required, a blank certificate of decontamination can be downloaded from the
KSB web site at: www.ksb.com/certificate_of_decontamination
4.5 Disposal
WARNING
Fluids, consumables and supplies which are hot and/or pose a health hazard
Hazard to persons and the environment!
▷Collect and properly dispose of flushing fluid and any residues of the fluid han-
dled.
▷Wear safety clothing and a protective mask, if required.
▷Observe all legal regulations on the disposal of fluids posing a health hazard.
1. Dismantle the pressure booster system.
Collect greases and other lubricants during dismantling.
2. Separate and sort the pump materials, e.g. by:
- Metals
- Plastics
- Electronic waste
- Greases and other lubricants
3. Dispose of materials in accordance with local regulations or in another control-
led manner.
4 Transport/Temporary Storage/Disposal
10 of 54 Hya-Solo DV

5 Description
5.1 General description
▪Pressure booster system
5.2 Designation
Example: Hya-Solo DV / 04 05 / 2 - 4
Table 4: Key to the designation
Code Description
Hya-Solo Pressure booster system with one pump
DV Model with three-phase motor, speed-controlled, pres-
sure-dependent starting and flow-dependent stopping
04 Pump size
05 Number of pump stages
2 - 4 Inlet pressure in bar
5.3 Name plate
Werk-Nr.
14w4102.rN-neireS:noitisoP1-5054/2 LF VD ouD - ayH
Förderstrom 5,0 m3/h Druckbehälter: Motorleistung P2 1 x 1,10 kW
Anlagensolldruck (pE) 6,0 bar Vorpreßdruck 5,3 bar Betriebsspannung / Frequenz 400 V 50 Hz
Förderhöhe 30,0 m Inhalt Bruttovolumen 8,0 Liter Steuerspannung / Frequenz Hz
mortsnnenrotoMm5,050=Q ieb ehöhredröF 2,40 A
Vordruck 3,0 - 3,
0
:.rN nalptlahcSrab BD 706 878
Betriebsdruck max. 16,0 bar
Ident Nr: xx xxx xxx Vor Inbetriebnahme Betriebsanleitung beachten ! ZNI 1448J
9971834055
000200
1 2 3
4
5
6
7
8
9
101112
18
17
16
13
14
15
Fig. 2: Name plate (example) of a Hya-Solo DV
1Type series, size 2 Order item number
3 Order number 4 Series code
5 Motor power P2 6 Operating voltage/frequency
7 Control voltage/frequency 8 Nominal motor current
9 Circuit diagram 10 Gross vol. content
11 Pre-charge pressure 12 Accumulator
13 Maximum operating pressure 14 Inlet pressure
15 Head at Q = 0 16 Head
17 System setpoint pressure 18 Flow rate
Key to the series code
Calendar year Week
2014 w33
5.4 Design details
Design
The pressure booster system consists of a non-self-priming multistage high-pressure
centrifugal pump with suction and discharge side shut-off valves. The shut-off valves
enable dismantling of the pump or check valve without draining the piping system.
The check valve on the discharge side prevents backflow through the pump when the
pump is not running and reduces the load on the mechanical seal.
An accumulator, a pressure transmitter and a pressure gauge are fitted on the dis-
charge side of the pressure booster system.
5 Description
Hya-Solo DV 11 of 54

The PumpDrive speed control system is mounted on and ready-wired to the pump
set.
The system comes with separate rubber anti-vibration pads.
5.5 Configuration and function
1
5
2
3
6
4
Fig. 3: Hya-Solo DV
1Master switch 2 Accumulator
3 Pump 4 Pressure transmitter
5 PumpDrive 6 Valves
The fully automatic pressure booster system is equipped with a non-self-priming ver-
tical high-pressure pump (3) for pumping the fluid handled to the consumer installa-
tions at a constant pressure.
The pump is started as a function of pressure and stopped as a function of flow by a
fully automatic control unit. If the pressure drops below the pre-set pressure, the
pump starts up and the frequency inverter controls the unit to maintain the set pres-
sure, so that the pressure is kept constant.
As the consumption decreases, the speed is reduced. At zero flow, the pressure boos-
ter system stops after a set after-run period (45 to 360 seconds).
A key for manual operation is provided on the control panel. In manual mode the
pump operates at the pre-set minimum speed, independently of the automatic sys-
tem (pressure transmitter) or an External ON/OFF signal.
NOTE
Continuous manual mode is reserved exclusively for emergencies!
Continuous operation of the pressure booster system in manual mode may result in
waste of energy and water.
In manual mode, a minimum flow (see table below) is essential to prevent the fluid
handled and the pump from overheating when no water is consumed at the consum-
er installations.
Minimum flow for pump in manual mode
Table 5: Minimum flow per pump in manual mode
Pump Minimum flow per pump in manual mode
[l/h]
Movitec 2B 200
Movitec 4B 400
Movitec 6B 600
Movitec 10B 1100
Movitec 15B 1600
Movitec 25B 2800
Movitec 40B 4600
Movitec 60B 6100
Movitec 90B 8500
Design
Function
Automatic mode
Function
Manual mode
5 Description
12 of 54 Hya-Solo DV

An open 1/2-inch tap equals a water consumption of approx. 800 to 1,200 l/h.
The dry running protection function is active in automatic mode and manual mode.
A digital input is provided for connecting dry running protection equipment. When
the input is open, the control unit detects dry running and stops the pressure booster
system after approx. 10 seconds (factory setting).
5.6 Noise characteristics
For the noise level of the individual pumps please refer to the pump's operating in-
structions.
5.7 Scope of supply
Depending on the model, the following items are included in the scope of supply:
▪Pressure booster system
▪One Movitec vertical high-pressure centrifugal pump
▪Check valve
▪Shut-off valves
▪Membrane-type direct-flow accumulator on the discharge side
▪Pressure transmitter on the discharge side
▪Vibration damping
▪Pressure gauge for pressure indication
PumpDrive
▪Self-cooling motor-mounted frequency inverter (PumpDrive) for pressure-control-
led starting and demand-based stopping
▪Plain-text display (for voltage, current, power, speed, frequency)
▪Control panel with operating keys (manual-0-automatic), navigation and func-
tion keys
▪LEDs signalling operational availability (green), warning (yellow), alert (red)
▪Two freely parameterisable relay outputs (operation/fault, alert, etc.)
▪Two NO contacts 250 V AC/1 A
▪Analog input for external setpoint adjustment
▪Analog output for transmitting the actual value, motor speed, etc.
▪Lockable master switch (repair switch)
5.8 Dimensions and weights
For dimensions and weights refer to the outline drawings of the pressure booster sys-
tem.
5.9 Terminal wiring diagram
5.9.1 Power terminals
NOTE
The PumpDrive is wired to the master switch, the motor and the pressure sensor at
the factory. Work at the power terminals is only required if the PumpDrive needs to
be removed.
The power terminals are located underneath the V-shaped cover.
Example
Function
Dry running protection
5 Description
Hya-Solo DV 13 of 54

DANGER
Electrical connection work by unqualified personnel
Danger of death from electric shock!
▷Always have the electrical connections installed by a trained and qualified elec-
trician.
▷Observe regulations IEC 60364 and, for explosion-proof models, EN 60079.
NOTE
The housing cover must not be opened.
Non-compliance will result in forfeiture of any and all warranty claims.
Removing the L-shaped cov-
er.
Remove the cross-head screws on the L-shaped cable cover for the control cables and
remove the cover.
Removing the V-shaped cov-
er.
Remove the cross-head screws on the V-shaped cover for the mains and motor con-
nection and remove the cover.
Route the mains cable and motor cable through the cable glands and connect them
to the specified terminals.
When closing the covers, make sure that the sealing elements are properly seated.
NOTE
The screws fastening the cover of the mains and motor terminal box must be tight-
ened to a torque of 1.2 Nm to ensure that the device has IP55 enclosure protection.
DANGER
Open terminals and connectors of brake resistor.
Danger to life!
▷Do not open the terminals and connectors of the brake resistor.
5 Description
14 of 54 Hya-Solo DV

+24VIN 0
PTC
PE L1 L2 L3
PE
L1
L2
L3
N
1 2 3 4 5 6 U V W
B
A
M
3~
Fig. 4: Power supply and motor wiring up to 7.5 kW
AAnalog input 2 B Brake resistor
+24VIN 0
PTC
PE L1 L2 L3
PE
L1
L2
L3
N
1 2 3 4 5 6
U V W
B
A
M
3~
Fig. 5: Power supply and motor wiring from 11 kW
AAnalog input 2 B Brake resistor
5 Description
Hya-Solo DV 15 of 54

5.9.2 Connecting the control terminals
DANGER
Power supply not disconnected
Danger to life!
▷Pull the mains plug or disconnect all electrical connections and secure against
unintentional start-up.
NOTE
The housing cover must not be opened.
Non-compliance will result in forfeiture of any and all warranty claims.
The control terminals are located underneath the control panel.
This must be removed as follows.
1. Remove the cross-head screws on the L-shaped cover for the control cable and re-
move the cover.
2. Remove the cross-head screws on the control panel and remove the control pan-
el.
NOTE
The screws fastening the cover of the mains and motor terminal box must be tight-
ened to a torque of 1.2 Nm to ensure that the device has IP55 enclosure protection.
The control terminal assignment is shown below.
The maximum cable cross-sections (wire size) which can be connected to the control
terminals of terminal strip P4 and terminal strip P7 are:
Table 6: Max. cable cross-sections to be connected to control terminals
Control termi-
nals
Rigid and flexible cables Flexible cable with wire end sleeve
Terminal strip
P4
0.2 - 1.5 mm20.75 mm2
Terminal strip
P7
0.2 - 2.5 mm20.25 - 1.5 mm2
Fig. 6: Removing the cover
for the control cable
5 Description
16 of 54 Hya-Solo DV

1
10
2
3
4
5
6
7
8
9
10
2
3
4
6
7
8
9
20
19
18
17
16
15
14
13
12
11
1
5
4070:0011
P7
P4
GND P4
D16
D15
D14
D13
D12
D11
+24V
AGND
AN-OUT
SB1-GND
SB1+
SB1-
SB1-GND
SB1+
SB1-
SB1Z-
SB1Z+
AGND P7
AIN1
GND
AIN2
+24V
NO2
COM2
NO1
COM1
Fig. 7: Inputs/output control terminals
Table 7: Terminal strip P4
Terminal Signal Description
20 0V Ground for +24 V
19 DIG IN6 Digital input (15/28 V DC)
18 DIG-IN5 Digital input (15/28 V DC)
17 DIG-IN4 Digital input (15/28 V DC)
16 DIG-IN3 Digital input (15/28 V DC)
15 DIG-IN2 Digital input (15/28 V DC)
14 DIG-IN1 Digital input (15/28 V DC)
13 +24 V +24 V DC voltage source
Max. load 200 mA
12 0V-AN Ground for AN-OUT
11 AN OUT Analog output 0-10 V.
Max. load 5 mA
10 SB1-GND Ground for CAN
9 SB1 + CAN signal
8 SB1 - CAN signal
7 PE (GROUND) Ground
6 PE (GROUND) Ground
5 SB1-GND Ground for CAN
4 SB1 + CAN signal
3 SB1 - CAN signal
2 SB1Z- Bus terminator for CAN
1 SB1Z+ Bus terminator for CAN
5 Description
Hya-Solo DV 17 of 54

Table 8: Terminal strip P7
Terminal No. Signal Description
10 0V-AN Ground for AIN1/2
9 AN1-IN Programmable analog input 1
0-10 V or 0-20 mA
8 PE (GROUND) Ground
7 0V Ground for +24 V
6 AN2-IN Programmable analog input 2
0-10 V or 0-20 mA
5 +24 V +24 V DC voltage source
Max. load 200 mA
4 NO2 NO contact "NO" No. 2
(250 V AC, 1 A)
3 COM2 NO contact "COM" No. 2
(250 V AC, 1 A)
2 NO1 NO contact "NO" No. 1
(250 V AC, 1 A)
1 COM1 NO contact "COM" No. 1
(250 V AC, 1 A)
5 Description
18 of 54 Hya-Solo DV

6 Installation at Site
6.1 Installation to DIN 1988
Install pressure booster systems either in the technical equipment room or in a well-
ventilated, frost-free, lockable room used for no other purpose. No harmful gases are
allowed to enter the place of installation. An adequately sized floor drain (leading to
a sewer or equivalent) must be provided.
The system is designed for a maximum ambient temperature of 0 °C to +40 °C at a
relative humidity of 50 %.
NOTE
Do not install pressure booster systems next to sleeping or living quarters.
If expansion joints (KSB accessory) are used for damping vibrations, their fatigue
strength (endurance limit) must be given due consideration. Expansion joints must be
installed to allow quick and easy replacement.
6.2 Checks to be carried out prior to installation
Place of installation
WARNING
Installation on mounting surfaces which are unsecured and cannot support the load
Personal injury and damage to property!
▷Use a concrete of compressive strength class C12/15 which meets the require-
ments of exposure class X0 to EN 206-1.
▷The mounting surface must have set and must be completely horizontal and
even.
▷Observe the weights indicated.
NOTE
The anti-vibration mounts of the pressure booster system provide adequate insula-
tion against solid-borne noise.
1. Check the structural requirements.
All structural work required must have been prepared in accordance with the
dimensions stated in the outline drawing.
6.3 Installing the pressure booster system
WARNING
Top-heavy pressure booster system
Risk of personal injury by pressure booster system tipping over!
▷Pressure booster systems awaiting final installation must be secured against tip-
ping over.
▷Firmly anchor the pressure booster system.
Remove all packaging before installing the pressure booster system. Connect the
pressure booster system's inlet line and discharge line to the corresponding site distri-
bution lines.
6 Installation at Site
Hya-Solo DV 19 of 54

NOTE
In order to avoid transmission of piping forces onto the pressure booster system and
transmission of solid-borne noise, we recommend installing length-limited expan-
sion joints.
Allow sufficient space for maintenance and repair work.
✓All structural work required has been checked.
✓The dimensions of the concrete foundation are correct, and the concrete has set
firmly.
1. Mark out the anchoring holes on the floor as shown in the outline drawing.
2. Drill the holes (max. diameter: 12 mm).
3. Insert plug fixings of appropriate size.
4. Set the pressure booster system down in its correct installation position.
5. Use suitable bolts to firmly anchor the pressure booster system.
6.4 Installing the piping
Make sure that piping is installed without transmitting any stresses or strains. The use
of length-limited expansion joints (see accessories) is recommended.
CAUTION
Air pockets in suction line
Pressure booster system cannot prime!
▷Lay piping with a continuously rising slope (as shown).
Suction lift operation
Incorrect Correct
NOTE
For suction lift operation install suitable swing check valves at the suction line ends
which are submerged in the fluid handled. Take into account the head losses caused
by these swing check valves.
Do not exceed the maximum suction lift of the pumps.
6.4.1 Fitting an expansion joint
DANGER
Sparks and radiant heat
Fire hazard!
▷Take suitable precautions to protect the expansion joint if any welding work is
carried out nearby.
CAUTION
Leaking expansion joint
Flooding of installation room!
▷Regularly check for cracks or blisters, exposed fabric or other defects.
6 Installation at Site
20 of 54 Hya-Solo DV
Table of contents
Other KSB Extender manuals
Popular Extender manuals by other brands
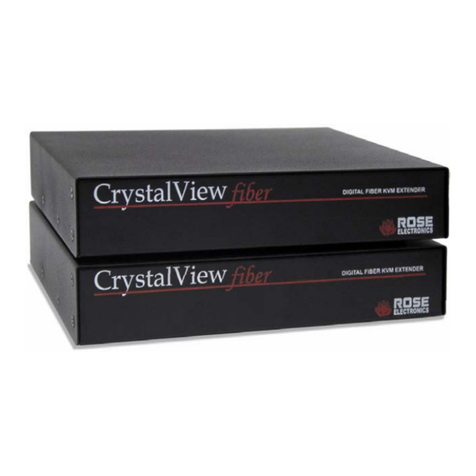
Rose electronics
Rose electronics CrystalView fiber CRK-1DFM/SUN Installation and operation manual
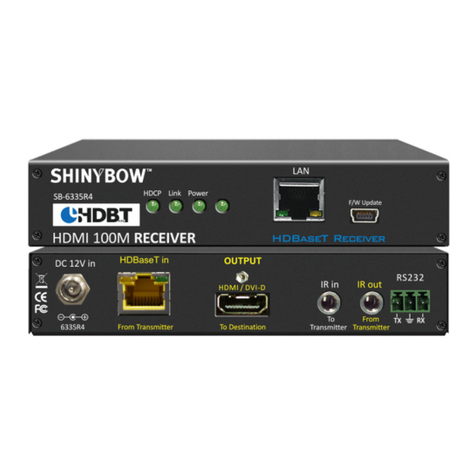
Shinybow USA
Shinybow USA SB-6335R4 instruction manual
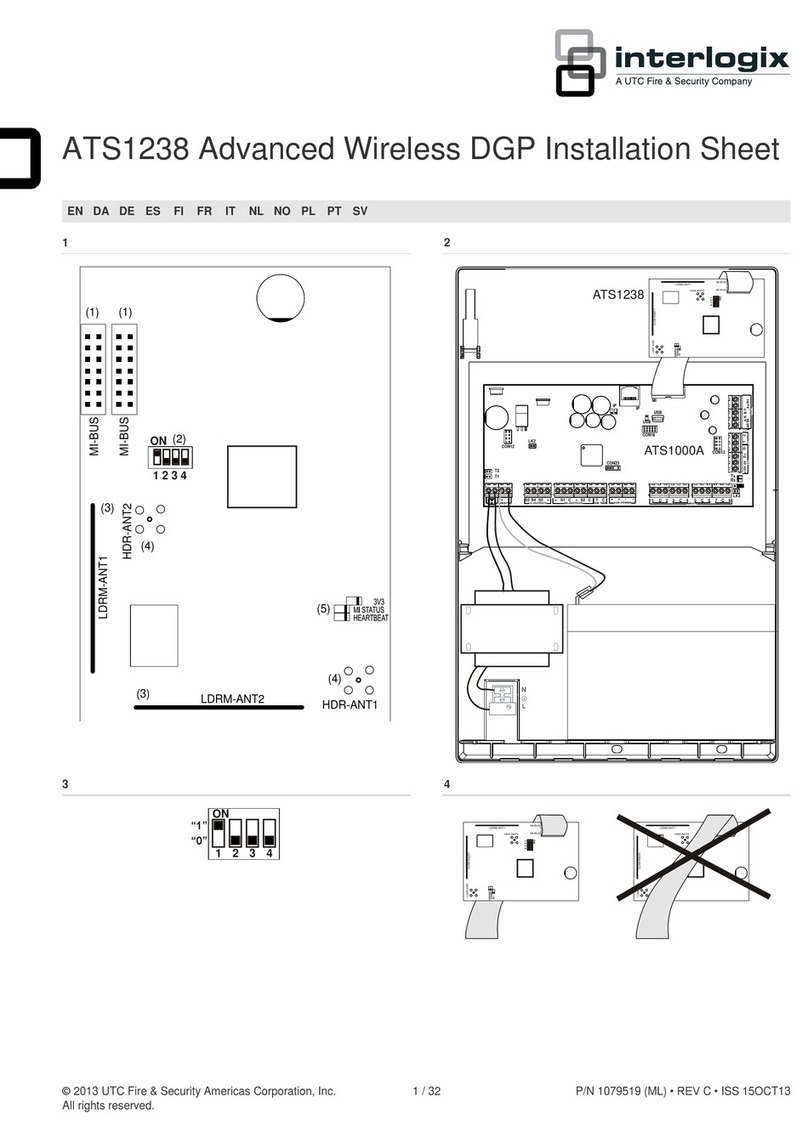
Interlogix
Interlogix ATS1238 Installation sheet
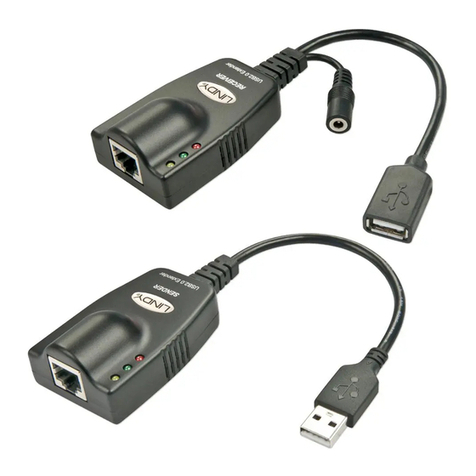
Lindy
Lindy 42694 user manual
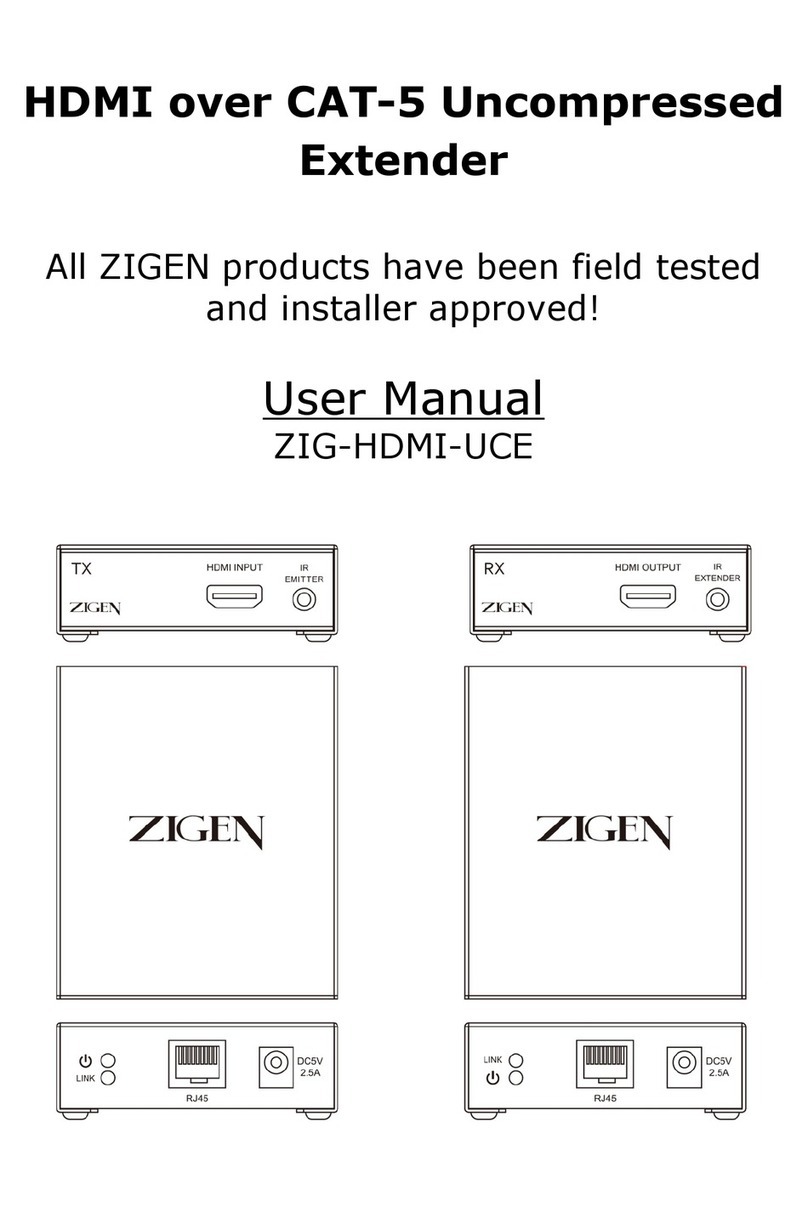
Zigen
Zigen ZIG-HDMI-UCE user manual
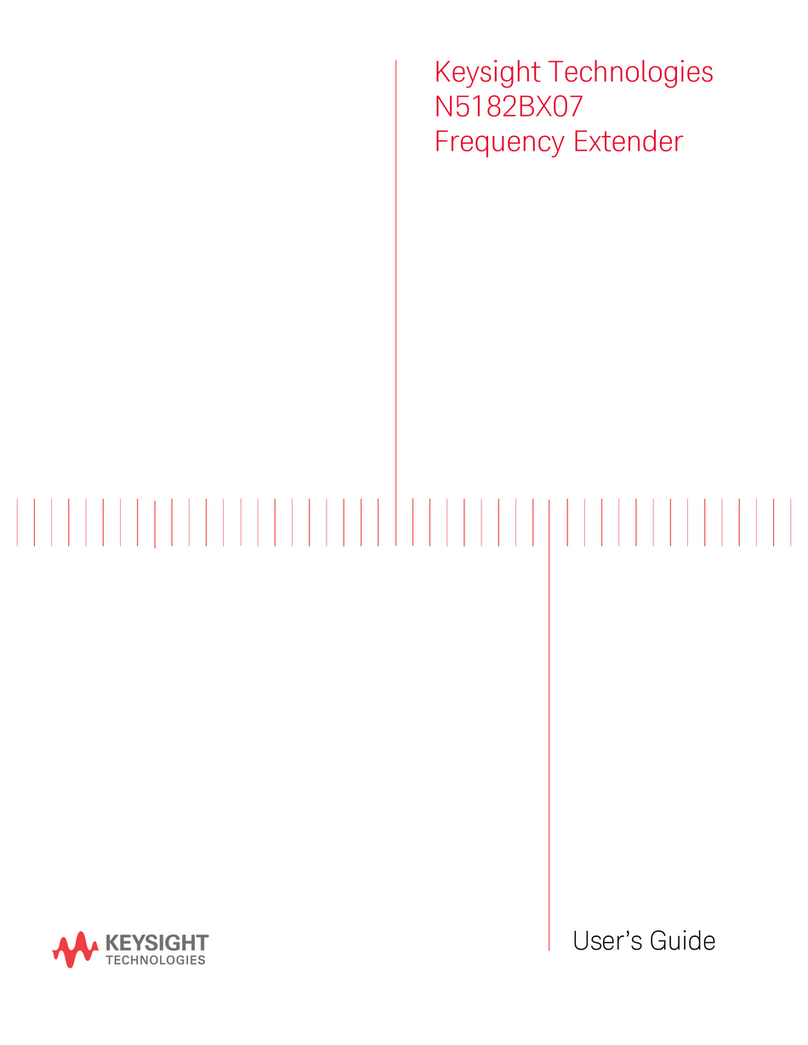
Keysight Technologies
Keysight Technologies N5182BX07 user guide