KTM 250 1998 Operating instructions

‘98
7. 97 ART. NR. 3.205.20
250 / 300 / 380
REPARATURANLEITUNG MOTOR
REPAIR MANUAL ENGINE
MANUALE DI RIPARAZIONE MOTORE
MANUEL DE RÉPARATION MOTEUR
MANUAL DE REPARACIÓN MOTOR

1
2
3
4
5
6
7
8
9
1 General
2 Removing engine / Refitting engine
3 Dismantling engine
4 Servicing on individual components
5 Engine assembly
6 Electrical
7 Trouble shooting
8 Technical data / maintenance schedule
9 Wiring diagrams
(see at the end of this repair manual)

INTRODUCTION
THIS REPAIR MANUAL OFFERS EXTENSIV REPAIR-INSTRUCTIONS AND IS AN UP-TO-DATE VERSION THAT DESCRIBES THE LATEST MODELS OF
THE SERIES. HOWEVER, THE RIGHT TO MODIFICATIONS IN THE INTEREST OF TECHNICAL IMPROVEMENT IS RESERVED WITHOUT UPDATING
THE CURRENT ISSUE OF THIS MANUAL.
A DESCIRIPTION OF GENERAL WORKING MODES COMMON IN WORK SHOPS HAS NOT BEEN INCLUDED. SAFETY RULES COMMON IN THE
WORK SHOP HAVE ALSO NOT BEEN LISTED. WE TAKE IT FOR GRANTED THAT THE REPAIRS ARE MADE BY QUALIFIED PROFESIONALLY TRAI-
NED MECHANICS.
READ THROUGH THE REPAIR MANUAL BEFORE BEGINNING WITH THE REPAIR WORK.
WARNING
STRICT COMPLIANCE WITH THESE INSTRUCTIONS IS ESSENTIAL
TO AVOID DANGER TO LIFE AND LIMB.
!
CAUTION
!
NON-COMPLIANCE WITH THESE INSTRUCTIONS CAN LEAD TO
DAMAGE OF MOTORCYCLE COMPONENTS OR RENDER MOTORCY-
CLES UNFIT FOR TRAFFIC.
„NOTE” POINTS OUT USEFUL TIPS.
USE ONLY ORIGINAL KTM SPARE PARTS WHEN REPLACING PARTS.
THE KTM HIGH PERFORMANCE ENGINE IS ONLY ABLE TO MEET USER EXPECTATIONS IF THE MAINTENANCE WORK IS PERFORMED REGU-
LARLY AND PROFESSIONALLY.
FOR TECHNICAL DATA SEE LAST SECTION OF THIS MANUAL. UP-TO-DATE INFORMATION IS PUBLISHED IN OUR UPDATED SPARE PARTS CATA-
LOGUES.
KTM AUSTRIA’S CERTIFICATE OF ACHIEVEMENT FOR ITS QUALITY SYSTEM ISO 9001 IS THE BEGINNING OF AN ON- GOING TOTAL RE-
ENGINEERED QUALITY PLAN FOR A BRIGHTER TOMORROW.
KTM SPORTMOTORCYCLE AKTIENGESELLSCHAFT
5230 MATTIGHOFEN, AUSTRIA
ALL DESIGN AND ASSEMBLY MODIFICATION RIGHTS RESERVED.

1
1
1.0 General
Chap. Component / Component unit Page
1.1 Bleeding the cooling system . . . . . . . . . . . . . . . . . . . . . . . . . . . . . . . . . . . . . . . . . . . . .1-2
1.2 Carburetor adjustment . . . . . . . . . . . . . . . . . . . . . . . . . . . . . . . . . . . . . . . . . . . . . . . .1-2
1.3 Definitions . . . . . . . . . . . . . . . . . . . . . . . . . . . . . . . . . . . . . . . . . . . . . . . . . . . . . . . . .1-3
1.3.1 Idling range . . . . . . . . . . . . . . . . . . . . . . . . . . . . . . . . . . . . . . . . . . . . . . . . . . . . . . . .1-3
1.3.2 Opening up . . . . . . . . . . . . . . . . . . . . . . . . . . . . . . . . . . . . . . . . . . . . . . . . . . . . . . . .1-3
1.3.3 Part-throttle range . . . . . . . . . . . . . . . . . . . . . . . . . . . . . . . . . . . . . . . . . . . . . . . . . . . .1-3
1.3.4 Full throttle range . . . . . . . . . . . . . . . . . . . . . . . . . . . . . . . . . . . . . . . . . . . . . . . . . . . .1-3
1.4 Checking the float level . . . . . . . . . . . . . . . . . . . . . . . . . . . . . . . . . . . . . . . . . . . . . . . .1-3
1.5 Checking the setting of the TVC system . . . . . . . . . . . . . . . . . . . . . . . . . . . . . . . . . . . .1-4
1.6 Special tools . . . . . . . . . . . . . . . . . . . . . . . . . . . . . . . . . . . . . . . . . . . . . . . . . . . . . . . .1-5

1
1.2 Carburetor adjustment
Basic information on the original carburetor setting
The original carburetor setting was adapted for an altitude of approx. 500 meters (1600 ft.) above sea level, and the ambient temperature of approx.
20° C (68° F), mainly for off-road use and central European premium-grade fuel (ROZ 95 MOZ). Mixing ratio 2-stroke motor oil : super fuel
1:40 – 1:60.
Basic information on a change of the carburetor setting
Always start out from the original carburetor setting. Essential requirements are a clean air filter system, air-tight exhaust system and an intact car-
buretor. Experience has shown that adjusting the main jet, the idling jet and the jet needle is sufficient and that changes of other parts of the car-
buretor will not greatly affect engine performance.
RULE OF THUMB: high altitude or high temperatures ➞choose leaner carburetor adjustment
low altitude or low temperatures ➞choose richer carburetor adjustment
WARNING
–O
NLY USE PREMIUM-GRADE GASOLINE ROZ 95 MIXED WITH HIGH-GRADE TWO-STROKE ENGINE OIL. OTHER TYPES OF GASOLINE CAN CAUSE ENGINE FAILURE, AND
USE OF SAME WILL VOID YOUR WARRANTY.
–O
NLY USE HIGH-GRADE 2-STROKE ENGINE OIL OF KNOWN BRANDS.
–NOT ENOUGH OIL OR LOW-GRADE OIL CAN CAUSE EROSION OF THE PISTON. USING TOO MUCH OIL, THE ENGINE CAN START SMOKING AND FOUL THE SPARK PLUG.
–I
N THE CASE OF A LEANER ADJUSTMENT OF THE CARBURETOR PROCEED CAUTIOUSLY. ALWAYS REDUCE THE JET SIZE IN STEPS OF ONE NUMBER TO AVOID
OVERHEATING AND PISTON SEIZURE.
NOTE: IF DESPITE A CHANGED ADJUSTMENT THE ENGINE DOES NOT RUN PROPERLY, LOOK FOR MECHANICAL FAULTS AND CHECK THE IGNITION SYSTEM.
Basic information on carburetor wear
As a result of engine vibrations, throttle valve, jet needle, and needle jet are subjected to increased wear. This wear may cause carburetor malfun-
ction (e.g., overly rich mixture). Therefore, these parts should be replaced after 10000 kilometers (6000 miles).
1.1 Bleeding the cooling system
If the coolant has been drained, the cooling system must be bled as follows after
refilling.
– Make sure that the drain screw 1is fastened.
– Pour approx. 0.5 litres coolant into the system.
– Remove the screw 2on the right radiator and tilt the motorcycle to the right
approx. 30 degree angle.
– Now pour coolant into the system until it escapes from the right radiator free of
bubbles and replace the screw 2immediately so that no more air may reach the
right radiator.
– Return the motorcycle to its original position and top up the left radiator until
the coolant can be seen approx. 10 mm above the radiator fins.
– Check the coolant level again after a short ride.
1
2

1
3
1.3 Definitions
Mixture too rich:
Too much fuel in proportion to air.
Mixture too lean:
Not enough fuel in proportion to air.
1.3.1 Idling range A
Operation with closed throttle valve. This range is influenced by the position of the
air control screw 1and the idle adjusting screw 2. Only make adjustments when
the engine is hot.
To this end, slightly increase the idling speed of the engine by means of the idle adju-
sting screw. Turning it clockwise produces a higher idling speed and turning the
screw counterclockwise produces a lower idling speed. Create a round and stable
engine speed using the air control screw (basic position of the air control screw =
open by 1.5 turns). Then adjust to the normal idling speed by means of the idle adju-
sting screw.
1.3.2 Opening up B
Engine behavior when the throttle opens. The idle jet and the shape of the throttle
valve influences this range. If, despite good idling-speed and part-throttle setting, the
engine sputters and smokes when the throttle is fully opened and develops its full
power not smoothly but suddenly at high engine speeds, the mixture to the carbu-
retor will be too rich, the fuel level too high or the float needle is leaking.
1.3.3 Part-throttle range C
Operation with partly open throttle valve. This range is only influenced by the jet
needle (shape and position). The optimum part-throttle setting is controlled by the
idling setting in the lower range and by the main jet in the upper range. If the engi-
ne runs on a four-stroke cycle or with reduced power when it is accelerated with
the throttle partly open, the jet needle must be lowered by one notch. If then the
engine pings, especially when accelerating under full power at maximum engine
revs, the jet needle should be raised.
If these faults should occur at the lower end of the part throttle range at a four-stro-
ke running, make the idling range leaner; if the engine pings, adjust the idling range
richer.
1.3.4 Full throttle range D
Operation with the throttle fully open (flat out). This range is influenced by the main
jet and the jet needle. If the porcelain of the new spark plug is found to have a very
bright or white coating or if the engine rings, after a short distance of riding flat out,
a larger main jet is required. If the porcelain is dark brown or black with soot the
main jet must be replaced by a smaller one.
Explanation - Example
Compared to the needle N 85 A, the jet needle N 85 C is two steps leaner in the
range from the closed position of the throttle to 1/4throttle. Otherwise, there are
not differences.
1.4 Checking the float level
Arrange the Keihin carburetor diagonally at about 60° so that the spring in the float
needle valve is not pressed together. In this position, the edge of the float should be
parallel with the float chamber sealing surface (see illustration).
jet needle throttle valve open effect
N 85 A
N 85 B 0–1/4–
N 85 C 0–1/4––
N 85 D 0–1/4– – –
N 85 E 0–1/4– – – –
NOZ E
NOZ F 0–1/4–
NOZ G 0–1/4– –
NOZ H 0–1/4– – –
NOZ I 0–1/4– – – –
N 85 C 0–1/4––
1
2
main jet
jet needle
jet needle
air control screw
idle adjusting screw
idle jet
throttle valve
60°

1.5 Checking the setting of the TVC system
NOTE: THE FUNCTION OF THE TVC SYSTEM IS CHECKED WITH THE ENGINE RUNNING.
THIS TEST CHECKS THE START OF ADVANCE AND THE END OF ADVANCE.
– For this, remove the left control cover.
– Connect a rev counter (either to the ignition cable or to the blue/white cable in
the electronics box, depending on the rev counter design).
– Start engine, accelerate gently and observe when the TVC system starts to advan-
ce (tooth segment creeps upwards).
START OF ADVANCE:END OF ADVANCE:
250: at 5400 rpm at 7550 rpm
300: at 5300 rpm at 7400 rpm
380: at 5200 rpm at 7200 rpm
– If necessary, turn the adjusting screw 1.
NOTE: TWISTING THE ADJUSTING SCREW IN DELAYS THE COMMENCEMENT OF ADJUSTMENT BY
THE TVC SYSTEM, TWISTING THE ADJUSTING SCREW OUT MEANS THAT THE TVC SYSTEM WILL
PERFORM THE ADJUSTMENT EARLIER.
1
1

1
5
FIG. PARTNO. DESCRIPTION
1 560.12.001.000 REPAIR STAND ‘96
3 546.29.003.000 HOLDING PLATE 250
4 560.12.004.000 GEAR WHEEL SEGMENT
5 546.29.009.044 PULLER FOR FLYWHEEL
6 6 276 807 PULLER FOR FLYWHEEL
7 510.12.011.000 SPECIAL CIRCLIP PLIER
8 544.12.012.000 HOLDING SPANNER FOR FLYWHEEL SEM
9 510.12.014.000 TIMING DEGREE DISC
10 510.12.016.000 PROTECTION CAP
11 546.29.012.000 HOLDING SPANNER FOR FLYWHEEL KOKUSAN
13 501.12.013.000 DIAL GAUGE
14 501.12.030.000 DIAL GAUGE SUPPORT
16 6 899 785 LOCTITE 242 BLUE
17 151.12.017.000 BEARING PULLER
18 151.12.018.100 INTERNAL BEARING PULLER 18 - 23 MM
18 151.12.018.000 INTERNAL BEARING PULLER 12 - 16 MM
18 151.12.018.200 INTERNAL BEARING PULLER 5 - 7 MM
19 546.29.027.000 RIVETTING TOOL
25 0276 179 000 EXTRACTOR PRIMARY GEAR
13
14
16
7
17
18
6
5
10
4
25
9
3
8
19
1
11
1.6 Special tools

– Notices –

2.1 Removing the engine
– Thoroughly clean the motorcycle.
– Use a suitable supporting device to jack up the motorcycle.
– Remove the seat and the tank with the spoilers.
– Drain the cooling liquid.
– Remove the exhaust system and the engine brace.
– Disconnect the radiator hoses at the engine.
– Remove the carburetor.
– Remove the engine sprocket cover and the chain.
– Disconnect the electrical wires.
– Unhook the clutch cable from the clutch lever.
– Undo the three screws 1and remove the compensation chamber 2of KTC
system including O-ring.
– Undo the engine mounting screws.
– Remove the swingarm pivot and pull the swingarm backwards.
– Lift the engine out of the frame on the left side.
NOTE: THE ENGINE NEED NOT BE REMOVED TO REMOVE THE CYLINDER HEAD AND THE CYLINDER.
IT IS ALSO POSSIBLE TO WORK ON THE CLUTCH, THE PRIMARY DRIVE AND THE SHIFT MECHA-
NISM WITHOUT PREVIOUSLY REMOVING THE ENGINE.
2
1
2.0 Removing engine / Refitting engine
Chap. Component / Component unit Page
2.1 Removing engine . . . . . . . . . . . . . . . . . . . . . . . . . . . . . . . . . . . . . . . . . . . . . . . . . .2-1
2.2 Refitting engine . . . . . . . . . . . . . . . . . . . . . . . . . . . . . . . . . . . . . . . . . . . . . . . . . . .2-2
1
2

2.2 Installing the engine
– Lift the engine into the frame from the left side, slightly grease and mount the
swingarm pivot.
– Twist in the engine mounting screws.
– Mount the engine brace.
– Insert a new O-ring into the groove of the compensation chamber of KTC system
with O-ring.
– Fix the compensation chamber with 3 screws and tighten the screws with 6 Nm.
– Connect the electrical wires.
– Mount the chain and the engine sprocket cover.
– Mount the carburetor.
– Connect the radiator hoses to the engine and fill the cooling system with a mix-
ture of 40 % antifreeze and 60 % water.
– Mount the exhaust system.
– Mount the tank with the spoilers and the seat.
– Start the engine and bleed the cooling system.
– Warm up the engine and check if the TVC system is properly adjusted.
– Check the electrical system for faultless operation.
– Adjust the carburetor.
– Test ride.
– After the test ride, check the engine and the cooling system for leaks and make
sure that all liquid levels are correct.
2

3
1
3.0 Dismantling engine
Cap. Component / Component unit Page
3.1 Drain gear oil . . . . . . . . . . . . . . . . . . . . . . . . . . . . . . . . . . . . . . . . . . . . . . . . . . . . . . .3-2
3.2 Cylinder head, cylinder, piston . . . . . . . . . . . . . . . . . . . . . . . . . . . . . . . . . . . . . . . . . . .3-2
3.3 Clutch cover . . . . . . . . . . . . . . . . . . . . . . . . . . . . . . . . . . . . . . . . . . . . . . . . . . . . . . .3-3
3.4 Clutch linings . . . . . . . . . . . . . . . . . . . . . . . . . . . . . . . . . . . . . . . . . . . . . . . . . . . . . . .3-3
3.5 Primary drive . . . . . . . . . . . . . . . . . . . . . . . . . . . . . . . . . . . . . . . . . . . . . . . . . . . . . . .3-3
3.6 Kickstarter . . . . . . . . . . . . . . . . . . . . . . . . . . . . . . . . . . . . . . . . . . . . . . . . . . . . . . . . .3-4
3.7 Shifting mechanism . . . . . . . . . . . . . . . . . . . . . . . . . . . . . . . . . . . . . . . . . . . . . . . . . .3-4
3.8 Ignition (Kokusan) . . . . . . . . . . . . . . . . . . . . . . . . . . . . . . . . . . . . . . . . . . . . . . . . . . .3-4
3.9 Ignition (SEM) . . . . . . . . . . . . . . . . . . . . . . . . . . . . . . . . . . . . . . . . . . . . . . . . . . . . . .3-5
3.10 Clutch release shaft . . . . . . . . . . . . . . . . . . . . . . . . . . . . . . . . . . . . . . . . . . . . . . . . . .3-5
3.11 Engine sprocket . . . . . . . . . . . . . . . . . . . . . . . . . . . . . . . . . . . . . . . . . . . . . . . . . . . . .3-5
3.12 Intake flange, reed valve housing . . . . . . . . . . . . . . . . . . . . . . . . . . . . . . . . . . . . . . . . .3-5
3.13 Parting of engine case . . . . . . . . . . . . . . . . . . . . . . . . . . . . . . . . . . . . . . . . . . . . . . . . .3-6
3.14 Shift mechanism, transmission . . . . . . . . . . . . . . . . . . . . . . . . . . . . . . . . . . . . . . . . . . .3-6
3.15 Crankshaft . . . . . . . . . . . . . . . . . . . . . . . . . . . . . . . . . . . . . . . . . . . . . . . . . . . . . . . . .3-6

– Cleaning the engine thoroughly.
– Place engine work stand in a vice and clamp the engine into the workstand.
– Remove the kickstarter together with the distance bushing behind and the foot
shift lever.
3.1 Draining gear oil
– Unscrew plug 1, allowing oil to drain.
3.2 Cylinder head, cylinder, piston
– Unscrew the 6 M8 collar screws.
– Remove cylinder head and the two O-rings.
– Undo the screws and remove the left control cover 2together with the gasket.
–
Undo the screws and remove the right control cover
3
together with the gasket.
– Remove the securing clip of the ball socket 4and unhook the ball socket 5
from the adjusting lever.
– Remove the 4 collar nuts on cylinder base and remove cylinder.
3
1
23
4
5

– Cover the crankcase.
– Place piston on wooden jig and remove both piston pin locking pins.
– Expel piston pin from piston without exerting undue force. Use a suitable mand-
rel if necessary.
– Remove piston and piston pin needle-bearing from conrod eye.
– Remove the cylinder base gasketS.
3.3 Clutch cover
– Remove collar screws and clutch cover including gasket.
NOTE: THE WATER PUMP COVER 1, THE OUTER COVER 2AND THE COVER LID 3DO NOT
NEED TO BE REMOVED. THE WATER PUMP AND THE CENTRIFUGAL TIMER REMAIN IN THE
CLUTCH COVER.
3.4 Clutch discs
– Loosen collar screws in diagonally opposite sequence to prevent wedging of discs
as springs expand.
– Remove collar screws, springs and spring retainer.
– Remove the pressure cap and pull out the clutch push rod together with the
thrust bearing.
– Take the disc package out of the outer clutch hub.
3.5 Primary drive
– Block the primary gear with the gear wheel segment 4(see illustration).
–
Undo the hexagon nut (LH thread) and remove it together with the detent edged ring.
– Release the lock washer of the inner clutch hub.
– Connect clutch holder 5to inner clutch hub and loosen hexagon nut (see illu-
stration).
– Remove clutch holder.
– Remove inner clutch hub and outer clutch hub together with bearing from main
shaft.
3
3
1
2
3
4
5

– Pulling the primary gear 1off the crankshaft.
N
OTE
: T
HE PRIMARY GEAR AND THE OUTER CLUTCH HUB BELONG TOGETHER
. A
LWAYS REPLACE
BOTH TOGETHER!
3.6 Kickstarter
– Remove circlip 2and kickstarter intermediate gear.
– Carefully release collar screw 3kickstarter spring is tensioned, release tension
on kickstarter spring and unhook spring hanger.
– Take the complete kickstarter shaft out of the housing.
– Take care of the stop disc, which stays in the housing.
!
CAUTION
!
CAREFULLY RELEASE THE KICKSTARTER SPRING! DANGER OF INJURY!
3.7 Shift system
– Press the sliding plate 4back with a screw driver so it no longer engages with
the driver for the shaft roller, at the same time remove shift shaft from the housing.
NOTE: WATCH THE STOP DISC WHICH REMAINS IN THE HOUSING.
– Remove allan head screw and take driver for roller 5and locking piece 6from
the shift roller.
– Disassemble locating lever 7only if the engine case must be replaced.
– Remove allan head screw 8and locking lever with spring.
3.8 Ignition (Kokusan)
– Undo the 5 screws and remove the ignition cover together with the gasket.
– Hold the flywheel with the holding spanner and undo the collar nut.
– Put the protection cover on the crankshaft thread, twist in the flywheel extrac-
tor and remove the flywheel.
– Undo the 3 screws and remove the stator together with the base plate.
3
2
3
4
5
6
8
7
1

3.9 Ignition system (SEM)
– Remove ignition cover and gasket.
– Hold the flywheel with the special tool and undo the collar nut.
– Place protective cap on crankshaft thread.
– Screw flywheel extractor in position and remove flywheel.
– Unscrew screws and remove stator.
– Loosen collar srews and remove base blate.
3.10 Clutch release shaft
– Unhook clutch cable.
– Remove collar screws and retaining bracket 1.
– Unscrew screw 2.
–
Turn clutch release shaft approx. 70 degrees anti-clockwise and pull out of housing.
3.11 Engine sprocket
– Remove circlip from countershaft using circlip pliers.
– Slide off engine sprocket, distance bushing and O-ring.
3.12 Intake flange, reed valve housing
– Remove the 5 collar screws.
– Remove intake flange and reed valve housing.
3
5
1
2

3.13 Parting of engine housing halves
– Top ignition-gear upwards and remove all housing screws.
– Release engine mounting brackets on work stand.
– Lift left-hand housing half with suitable tools by on the bosses provided, or part
with a few light plastic mallet blows against the countershaft from the right-hand
housing half.
!
CAUTION
!
LEVERING APART WITH A SCREW DRIVER OR SIMILAR TOOL MUST BE AVOIDED, SINCE THE SEAL
FACES ARE EASILY DAMAGED.
N
OTE
: W
ATCH GEAR SHAFT STOP DISCS
1
TO PREVENT THEM STICKING TO INSIDE OF HOUSING
.
3.14 Shift mechanism, transmission
– Pull out the shift rails 2and swing the shift forks aside.
– Pull the shift roller 3out of the bearing seat.
– Remove the shift forks.
NOTE: ALTHOUGH THE COUNTER SHAFT SHIFT FORKS ARE IDENTICAL THEY SHOULD BE REFITTED
IN THE SAME POSITION AS BEFORE IF REUSED. THEREFORE MARK ACCORDINGLY UPON REMOVAL.
– Push drive shaft 4approx. 30 mm upwards and remove countershaft 5. It is
then possible to remove the mainshaft completely from bearing.
NOTE: WATCH COUNTERSHAFT STOP DISC TO PREVENT IT STICKING TO THE HOUSING.
3.15 Crankshaft
– Pull crankshaft out of bearing seat (if necessary by tapping gently with a plastic
hammer).
– Take distance bushing 6out of seal shaft ring and remove O-ring 7.
– Clean all parts and check for wear, replace if necessary.
NOTE: WHEN AN ENGINE IS COMPLETELY OVERHAULED IT IS RECOMMENDED THAT ALL GAS-
KETS, SHAFT SEAL RINGS AND O-RINGS ARE RENEWED.
3
11
2
2
3
45
6
7

4
1
4.0 Servicing on individual components
Chap. Component / Component unit Page
4.1 Right housing half . . . . . . . . . . . . . . . . . . . . . . . . . . . . . . . . . . . . . . . . . . . . . . . . . . . . .4-2
4.2 Left housing half . . . . . . . . . . . . . . . . . . . . . . . . . . . . . . . . . . . . . . . . . . . . . . . . . . . . . .4-2
4.3 Crankshaft . . . . . . . . . . . . . . . . . . . . . . . . . . . . . . . . . . . . . . . . . . . . . . . . . . . . . . . . . .4-4
4.4 Piston . . . . . . . . . . . . . . . . . . . . . . . . . . . . . . . . . . . . . . . . . . . . . . . . . . . . . . . . . . . . . .4-4
4.5 Piston ring end gap . . . . . . . . . . . . . . . . . . . . . . . . . . . . . . . . . . . . . . . . . . . . . . . . . . . .4-4
4.6 Measuring cylinder . . . . . . . . . . . . . . . . . . . . . . . . . . . . . . . . . . . . . . . . . . . . . . . . . . . .4-4
4.7 Exhaust control in cylinder . . . . . . . . . . . . . . . . . . . . . . . . . . . . . . . . . . . . . . . . . . . . . . .4-5
4.8 Preassembly of cylinder . . . . . . . . . . . . . . . . . . . . . . . . . . . . . . . . . . . . . . . . . . . . . . . . .4-5
4.9 Nikasil coating of cylinder . . . . . . . . . . . . . . . . . . . . . . . . . . . . . . . . . . . . . . . . . . . . . . .4-6
4.10 Exhaust control in clutch cover . . . . . . . . . . . . . . . . . . . . . . . . . . . . . . . . . . . . . . . . . . .4-6
4.11 Preassembly of clutch cover . . . . . . . . . . . . . . . . . . . . . . . . . . . . . . . . . . . . . . . . . . . . . .4-6
4.12 Reed valve, intake flange . . . . . . . . . . . . . . . . . . . . . . . . . . . . . . . . . . . . . . . . . . . . . . . .4-6
4.13 Kickstarter . . . . . . . . . . . . . . . . . . . . . . . . . . . . . . . . . . . . . . . . . . . . . . . . . . . . . . . . . .4-7
4.14 Preassembly of kickstarter shaft . . . . . . . . . . . . . . . . . . . . . . . . . . . . . . . . . . . . . . . . . . .4-7
4.15 Transmission . . . . . . . . . . . . . . . . . . . . . . . . . . . . . . . . . . . . . . . . . . . . . . . . . . . . . . . .4-8
4.15.1 Assembly of main shaft . . . . . . . . . . . . . . . . . . . . . . . . . . . . . . . . . . . . . . . . . . . . . . . . .4-8
4.15.2 Assembly of countershaft . . . . . . . . . . . . . . . . . . . . . . . . . . . . . . . . . . . . . . . . . . . . . . . .4-8
4.16 Clutch . . . . . . . . . . . . . . . . . . . . . . . . . . . . . . . . . . . . . . . . . . . . . . . . . . . . . . . . . . . . .4-9
4.17 Replacing outer clutch hub . . . . . . . . . . . . . . . . . . . . . . . . . . . . . . . . . . . . . . . . . . . . . . .4-9
4.18 Shift mechanism . . . . . . . . . . . . . . . . . . . . . . . . . . . . . . . . . . . . . . . . . . . . . . . . . . . . .4-10
4.19 Preassembly of shift shaft . . . . . . . . . . . . . . . . . . . . . . . . . . . . . . . . . . . . . . . . . . . . . . .4-10
4.20 Ignition (Kokusan) . . . . . . . . . . . . . . . . . . . . . . . . . . . . . . . . . . . . . . . . . . . . . . . . . . . .4-11
4.20.1 Spark plug (NGK BR 8 ECM) . . . . . . . . . . . . . . . . . . . . . . . . . . . . . . . . . . . . . . . . . . . .4-11
4.20.2 Check stator and pulse generator (Kokusan) . . . . . . . . . . . . . . . . . . . . . . . . . . . . . . . . . .4-11
4.21 Ignition (SEM) . . . . . . . . . . . . . . . . . . . . . . . . . . . . . . . . . . . . . . . . . . . . . . . . . . . . . . .4-12
4.21.1 Spark plug (NGK BR 8 ECM) . . . . . . . . . . . . . . . . . . . . . . . . . . . . . . . . . . . . . . . . . . . .4-12
4.21.2 Check stator (SEM) . . . . . . . . . . . . . . . . . . . . . . . . . . . . . . . . . . . . . . . . . . . . . . . . . . .4-12
Engine housing
NOTE: READ THROUGH THE FOLLOWING SECTION BEFORE COMMENCING WORK. THEN DETERMINE THE ASSEMBLY SEQUENCE SO THAT THE ENGINE
HOUSING HALVES ONLY NEED TO BE HEATED UP ONCE BEFORE REPLACING THE BEARINGS.
HAVING FIRST REMOVED THE DOWELS, IN ORDER TO EXPEL THE BEARINGS OR REMOVE THEM WITH LIGHT MALLET BLOWS, THE HOUSING HALVES MUST
BE PLACED ON A SUITABLY LARGE PLANE SURFACE, SUPPORTING THE WHOLE OF THE SEALING SURFACE WITHOUT DAMAGING IT. A WOODEN PANEL IS
BEST USED AS A BASE.
BEARINGS OR SHAFT SEAL RINGS SHOULD NOT BE HAMMERED INTO THEIR SEATS. IF NO SUITABLE PRESS IS AVAILABLE, USE A SUITABLE MANDREL AND
HAMMER THEM IN WITH GREAT CARE. COLD BEARINGS WILL PRACTICALLY DROP INTO THEIR SEATS AT AN ENGINE HOUSING TEMPERATURE OF APPROX.
150° C.
AFTER COOLING, SHOULD THE BEARINGS FAIL TO LOCK IN THE BORE, THEY ARE BOUND TO ROTATE AFTER WARMING. IN THAT EVENT THE HOUSING
MUST BE REPLACED.

4.1 Right-hand housing half
Heat housing half to 150° C by means of hot plate.
GROOVED BALL BEARING OF CRANKSHAFT 1
Press old grooved ball-bearing inwards. Press in new ball bearing to the stop. The
open side of the ball cage must be towards the bottom (outside) of the case.
GROOVED BALL BEARING OF MAIN SHAFT 2
Press in new ball bearing from inside up to the stop.
!
CAUTION
!
DO NOT USE FORCE WHEN PRESSING THE GROOVED BALL BEARING AGAINST THE RETAINING
BRACKET 3TO AVOID A BENDING OF THE BRACKET, WHICH WOULD RESULT IN EXCESSIVE
AXIAL PLAY OF THE MAINSHAFT.
GROOVED BALL BEARING OF COUNTERSHAFT 4
Press in new grooved ball bearing from downward to the stop. The open side of the
ball cage must be face inwards.
GROOVED BALL BEARING OF THE SHIFT ROLLER 5
Remove retaining screw Aand press bearing inwards. Press in new ball bearing
from inside to the stop and secure retaining screw with Loctite 242.
NEEDLE BUSHING OF THE SHIFT SHAFT 6
Press old needle bushing inwards, press in new needle bushing flush from the outside.
GROOVED BALL BEARING OF CENTRIFUGAL TIMER 7
The bearings usually fall out of their seat of their own accord by knocking the hou-
sinq half on a plane piece of wood when the housing has a temperature of 150° C.
If necessary use a 6 mm internal bearing extractor and guide hammer (see illustra-
tion). Press in new grooved ball bearing to the stop.
BEARING BOLT KICKSTARTER INTERMEDIATE GEAR 8
Experience has shown that it is never necessary to replace the bearing bolt. It is not
recommended to mount a used bearing bolt in a new housing half, as it is practically
impossible to remove it without causing damage.
KICKSTARTER RELEASE PLATE 9
When replacing the release plate, secure the flat-head screws with Loctite 242.
CRANKSHAFT SEAL RING bk
Press in new shaft seal ring from the outside, with sealing lip facing inward, until
flush.
STOP SCREW KICKSTARTER bl
When mounting the stop screw, it must be secured with Loctite 242. Do not forget
new copper seal ring.
RETAINING BRACKET 3
When replacing the retaining bracket, the two collar screws are to be secured with
Loctite 242.
Finally check clear passage of the crankshaft ball bearing lubrication bore S.
4.2 Left-hand housing half
NEEDLE BUSHINGS OF CLUTCH RELEASE B
Remove seal ring from bore.
Knock needle bushings out of bore using a 12-16 mm extractor and guide hammer (see
illustration). Press in new needle bushings and seal ring in succession to the stop.
4
7
S
B
8
9
610
3
7
124
6
11
5
A
A

– Remove shaft seal rings, heat housing half to 150° C by means of hot plate.
CRANKSHAFT ROLLER BEARINGS 1
Press old roller bearing inwards, press in new ball bearing to the stop with the open
side of ball cage downwards (outside).
NEEDLE BEARING OF DRIVE SHAFT 2
Pull out the old bearing with a bearing extractor. In order to apply the extractor ver-
tically, a steel plate (see special tools) should be laid on the sealing face of the hou-
sing. The extractor wedge-grip should be supported over case walls. New bearing
should then be pressed in from inside.
GROOVED BALL BEARING OF COUNTERSHAFT 3
Press old ball bearing inwards, press in new ball bearing to the stop from inside.
GROOVED BALL BEARING OF SHIFT ROLLER 4
Ball bearing falls out of its seat of its own accord when housing half has been hea-
ted to approx. 150° C.
If necessary, knock housing half on a plane piece of wood. Press in new grooved ball
bearing to the stop.
NEEDLE BUSHING OF SHIFT SHAFT 5
Remove shaft seal ring and press old needle bushing inwards. Press in new needle
bushing from the outside to the collar D.
CRANKSHAFT SEAL RING 6
Press in new crankshaft seal ring from the outside, with sealing lip facing inwards.
The seal ring is 1 mm (0.03 in) lower than the upper edge ot the collar (see sketch).
COUNTER SHAFT SEAL RING 7
Press in the new shaft seal ring, until it is flush with machined surface.
SHIFT SHAFT SEAL 8
Press in the new shaft seal ring, until it is flush with machined surface.
When housing half has cooled off, check to see that the bearings are tight.
– Finally check free passage of crankshaft roller bearing lubrication bore S.
4
3
1
2
3
4
5
B
7
6
8
D
6
1 mm
6
S
This manual suits for next models
2
Table of contents
Other KTM Engine manuals

KTM
KTM 125 Operating instructions

KTM
KTM 2005 Guide

KTM
KTM 500 LC4 User manual
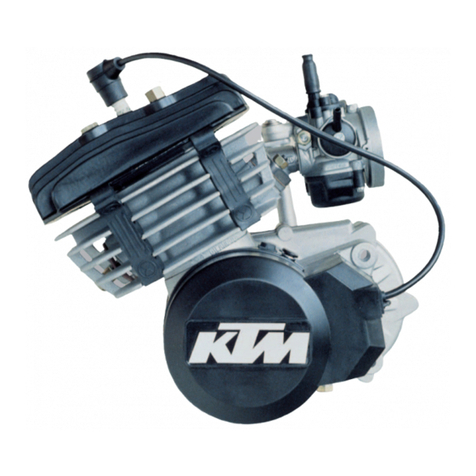
KTM
KTM S5-E Operating instructions

KTM
KTM EXC Operating instructions
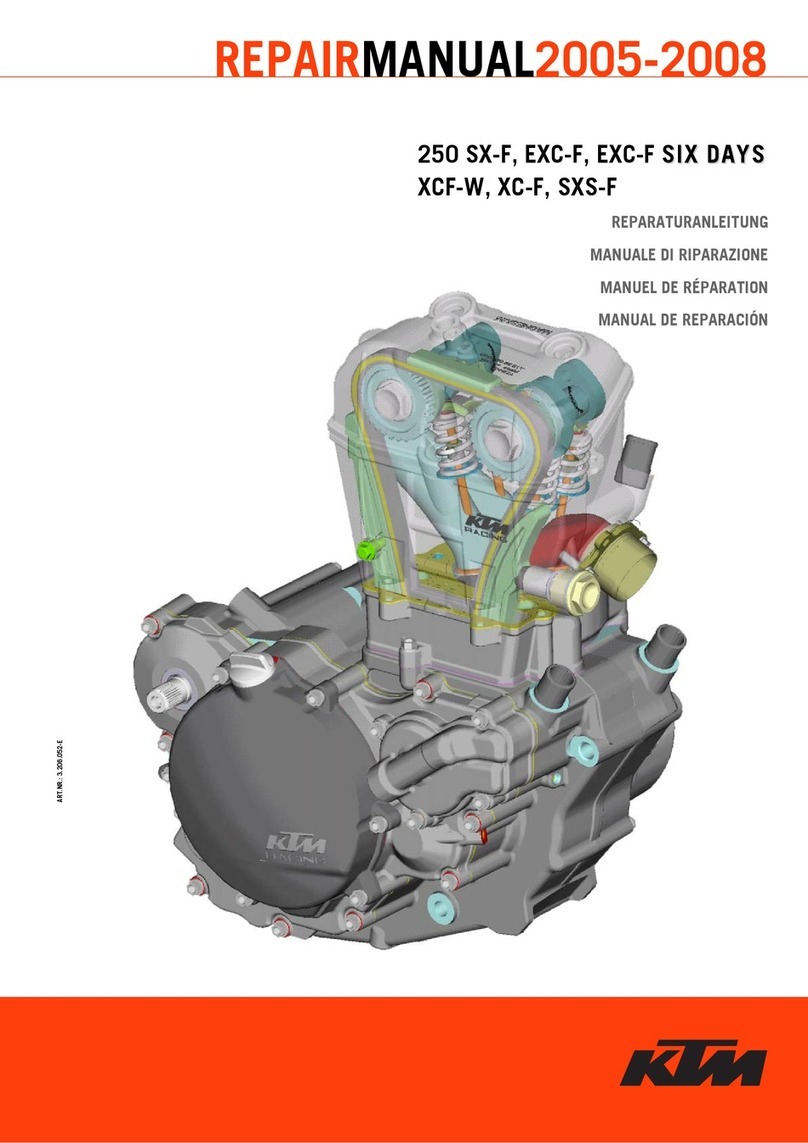
KTM
KTM 250 SX-F 2005 Operating instructions
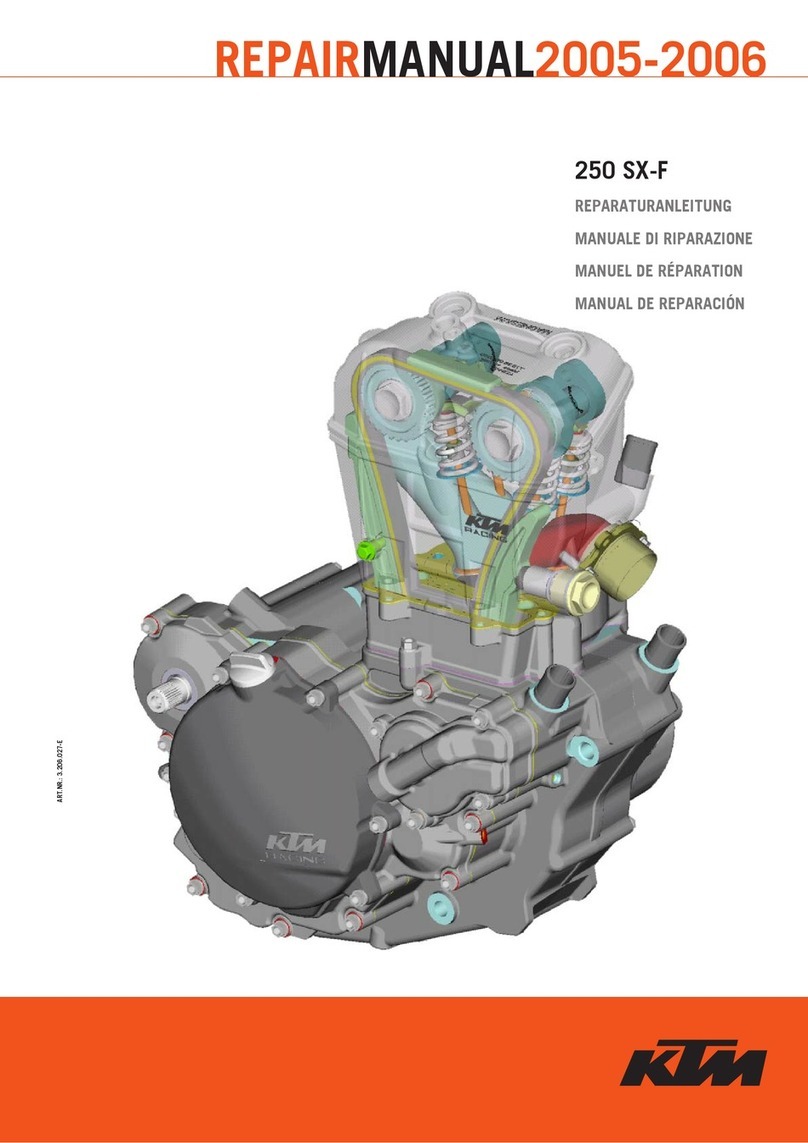
KTM
KTM 250 SX-F 2006 Operating instructions
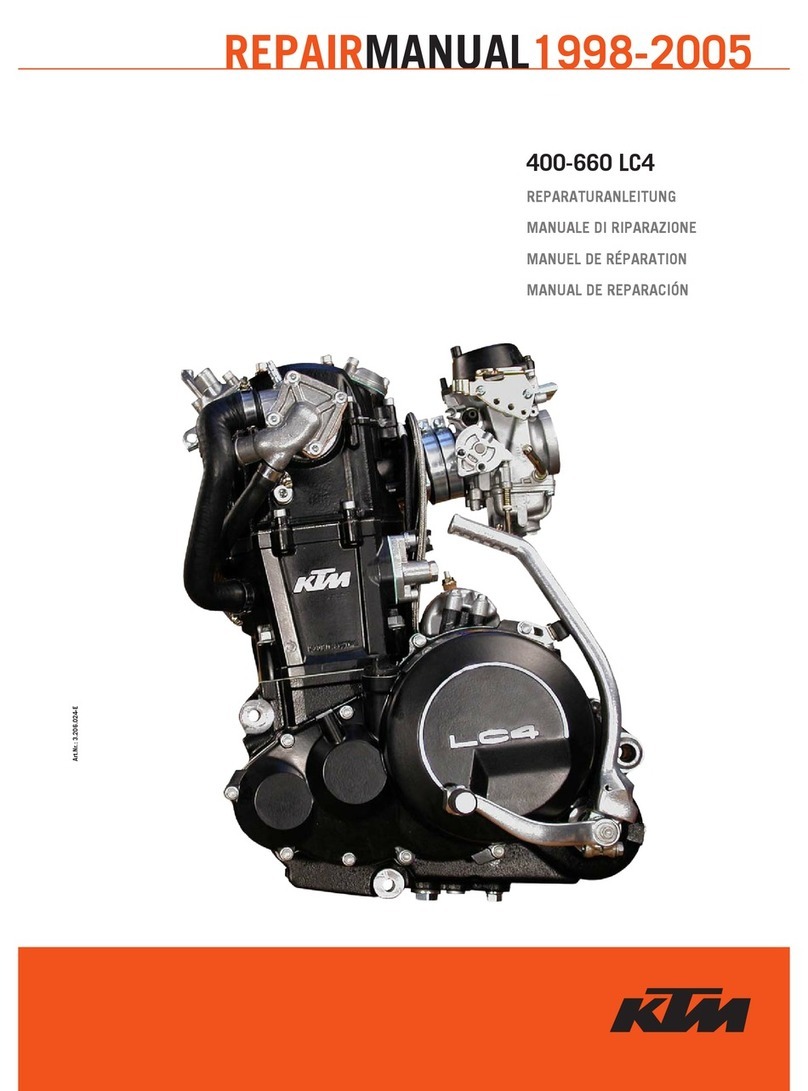
KTM
KTM 400-660 LC4 1998-2005 Operating instructions

KTM
KTM 690 LC4 2007 Operating instructions
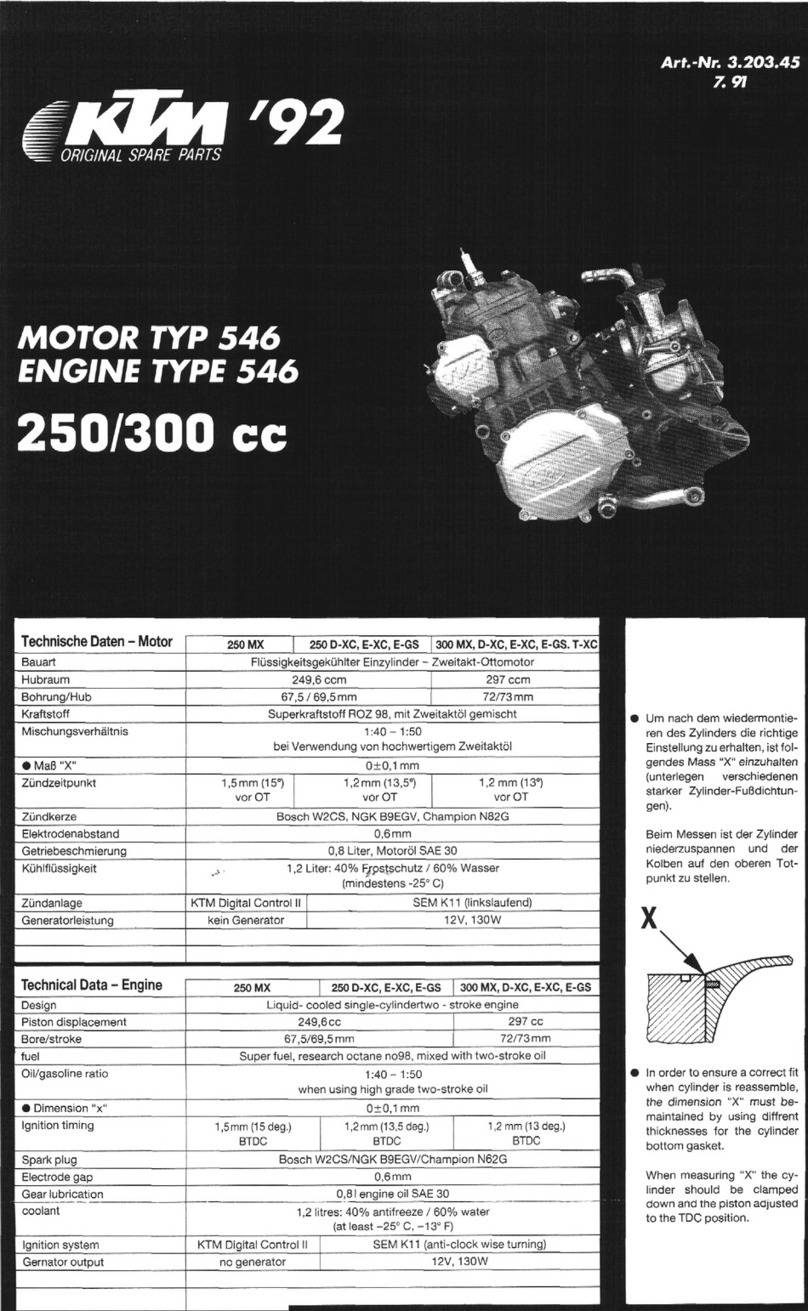
KTM
KTM 250 MX User manual
Popular Engine manuals by other brands

Kohler
Kohler Confidant ZT710 owner's manual
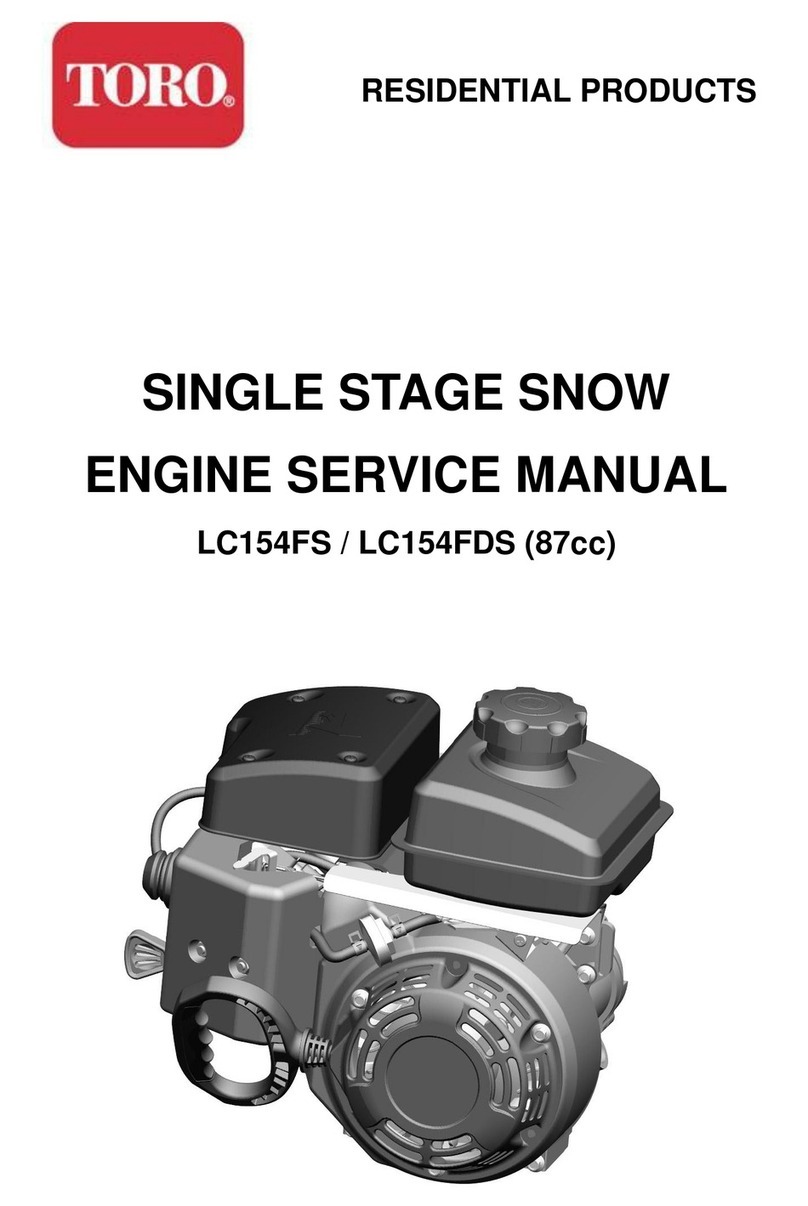
Toro
Toro LC154FS Service manual
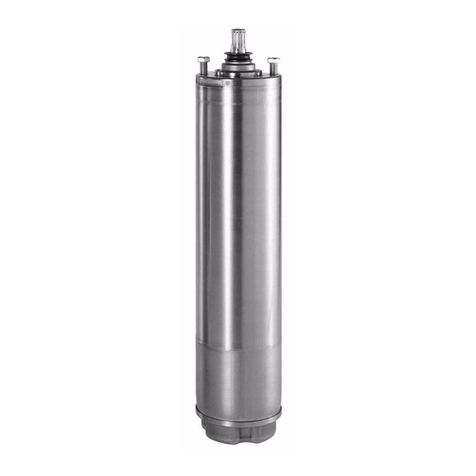
Grundfos
Grundfos MS Series Installation and operating instructions

Mitsubishi Electric
Mitsubishi Electric meiki series instruction manual

Bosch
Bosch Rexroth Hagglunds CA Series Installation & maintenance manual
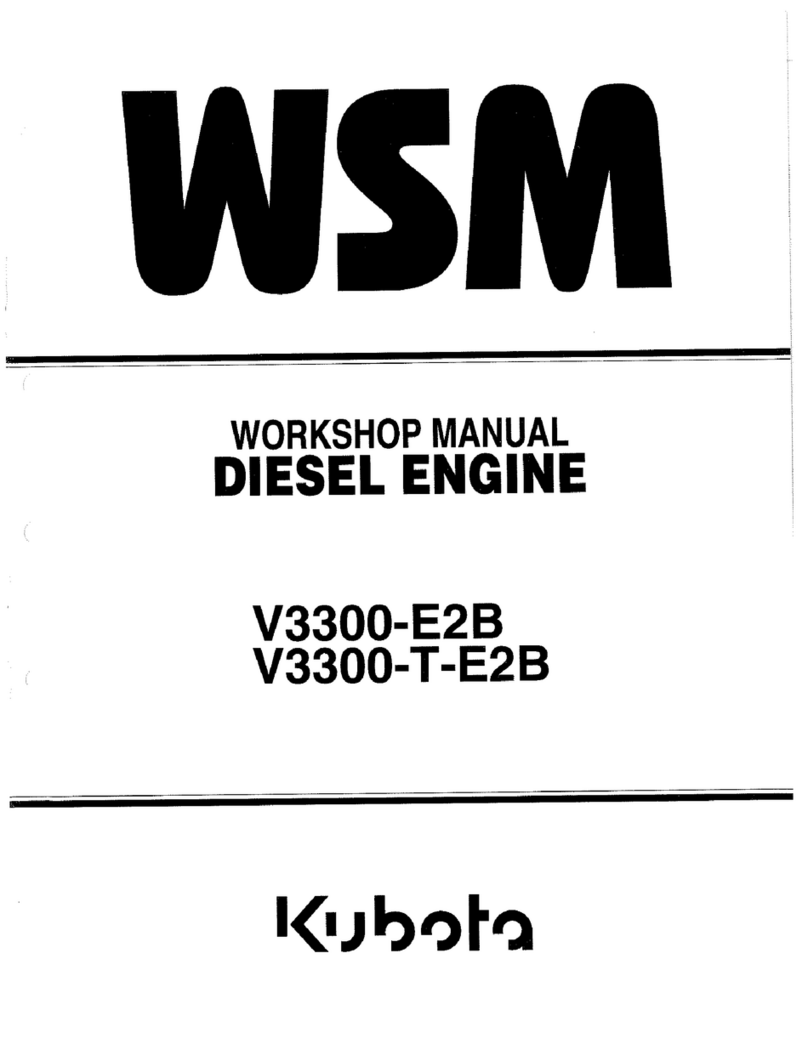
wsm
wsm V3300-E2B Workshop manual