kunzel TS 614 User manual

Installation and operating manual
Type 614 microprocessor control panel
for KÜNZEL wood gasification boiler type HV and HV-S
TS614_1_32, February 12, 2009

Contents
1 General information about the type 614 microprocessor control panel 4
1.1 Product contents ....................................... 4
1.2 Disposal of old unit ..................................... 4
1.3 Safety advice and general information about operation .................. 4
2 Installation 5
2.1 Installation of the control panel on the boiler ........................ 5
2.2 Electrical installation .................................... 5
2.2.1 Connecting sensors, control and mains power cables ............... 6
3 Indicators and controls 8
4 The menu 9
4.1 Design ............................................ 9
4.2 Boiler sub-menu ....................................... 11
4.2.1 Buffer tank min. temperature ............................ 11
4.2.2 Buffer tank monitoring system ........................... 11
4.2.3 Changeover point .................................. 12
4.2.4 Ignition period ................................... 12
4.2.5 Burn-out time .................................... 12
4.2.6 Pump mode ..................................... 12
4.2.7 Fans ......................................... 13
4.2.8 Start Mode ..................................... 13
4.2.9 Exhaust gas sensor ................................. 13
4.2.10 Exhaust gas factor ................................. 13
4.2.11 Start exhaust gas .................................. 13
4.2.12 Service ....................................... 13
4.3 Display sub-menu ...................................... 14
4.3.1 Language: ...................................... 15
4.3.2 Timeout: ...................................... 15
4.3.3 Date and time: ................................... 15
4.4 Info sub-menu ........................................ 15
4.5 Outside temperature control unit and other auxiliary modules sub-menu ......... 15
5 Mode of operation and control 15
5.1 General information ..................................... 15
5.2 Pump protection ....................................... 15
5.3 Frostguard .......................................... 16
5.4 The operating modes .................................... 16
5.5 Start ............................................. 16

5.5.1 Manuel firing .................................... 17
5.5.2 Electrical firing ................................... 17
5.5.3 Automatical ..................................... 17
5.5.4 Date ......................................... 17
5.6 Operating .......................................... 18
5.7 Adding fuel logs while the boiler is operating ....................... 18
5.8 Aborting heating procedure ................................ 19
5.9 Detection of smouldering and behaviour upon overheating ................ 19
5.10 Burnout ........................................... 19
6 Combination with other modules 20
7 Software Update 22
8 Operational malfunctions, fault messages 22
9 Maintenance and cleaning 25
10 Technical data 25
10.1 Electrical data ........................................ 25
10.2 Sensors ........................................... 26
10.3 Other information ...................................... 26
3

1 General information about the type 614 microprocessor control panel
1.1 Product contents
Please ensure that the contents of the control panel delivery box are complete:
•1 x control panel
•1 x boiler sensor, yellow, 1 x buffer tank sensor, blue, 1 x buffer tank sensor, red
•1 x connector socket, white, 3-pole, 1 x connector plug, white 3-pole, 1 x connector socket, brown,
3-pole, 1 x connector plug, black, 4-pole
•2 x cable ties, 2 x sensor plugs 10-pole
1.2 Disposal of old unit
The boilers supplied by KÜNZEL are stationary units that comply with the WEEE Directive. The
electrical and electronic components contained in the boilers do not fall within the remit of this directive
and will therefore not be taken back by KÜNZEL.
Old units still contain valuable raw materials. For this reason, return them to your dealer or take them to
your local recycling depot. Render the mains power connection unusable beforehand in order to prevent
misuse. The manufacturer cannot be held responsible for damage caused by non-compliance with the
safety advice and improper use.
1.3 Safety advice and general information about operation
Before commissioning the control unit, please read carefully the operating manual for the control
panel. Keep it in a place where it is readily available. Never pass on the units to other persons without
also providing them with the operating manual. The manufacturer is not responsible for improper or
unintended usage of this equipment. This unit complies with the statutory safety regulations. Improper
usage can cause damage to persons and property. The type 614 microprocessor control panel is only
intended for use with type HV and HV-S KÜNZEL-wood gasification boilers. The use of this control
panel in any other type of application is at one’s own risk. The manufacturer is not responsible for
damage caused by mis-operation of the unit or any usage other than its intended purpose. The application
of the control unit is the responsibility of the installation company. Please address any queries to your
heating installer.
Ensure that unauthorised persons, in particular children, do not have access to the control unit and
the heating system. Ensure that children cannot touch the control panel or the boiler while they are in
operation! Caution, risk of burns!
4

Only use the control unit in its properly installed state in order to ensure that no electrical components
can be touched.
Before starting to work on the boiler fan or any of the other 240 volt connections in the control panel,
the control panel is to be (all pole) disconnected from the mains power supply.
The unit is only electrically disconnected from the power utility grid (mains power supply) when one of
the following conditions has been met:
- The power supply cable has been disconnected from the power utility grid by an isolating switch.
Exercise caution if an external heating system is present. Ensure that this has also been disconnected
from the mains power supply.
- The circuit breaker of the local electrical installation has been switched off.
- The screw-type fuse of the local electrical installation has been removed completely.
Only the manufacturer or KÜNZEL’s authorised customer service provider is permitted to open the unit.
2 Installation
2.1 Installation of the control panel on the boiler
For further information about this, please read the instructions for the wood gasification boiler.
2.2 Electrical installation
•The electrical supply may only be connected by a qualified electrician.
•The relevant regulations pertaining to electrical installations (VDE) and the supplementary regu-
lations laid down by the local electricity / utility companies are to be observed.
•The unit complies with the EC EMC directives.
•The unit may only be connected to an electrical system that complies with VDE 0100 (in Austria
ÖVE-EN 1)
•Before connecting the control unit, compare the connection requirements (voltage and frequency)
against those of the power utility grid. It is essential that these requirements are identical. If in
doubt, please contact your electrician.
•Only permit the microprocessor control panel to be installed by a person with the necessary ex-
pertise or training using suitable tools. Incorrect installation can result in serious malfunctions and
faults that can destroy the unit.
•Only cables with a maximum continuous operating temperature of at least 120◦C are permitted to
be installed in the boiler. We recommend the application of silicone cables.
5

•The control panel must be connected with the correct polarity and earthed. The fixed wiring in-
stallation itself must provide an isolating device for each pole (L1 and N). Isolating devices are
defined as switches with a contact gap of at least 3 mm. These include miniature circuit breakers,
fuses and protective devices (EN 60335). The heating emergency stop switch DOES NOT count
as an isolating device!
•The cross sectional area of the connection equals 1.5 mm2. The power supply cable is to be pro-
vided with an appropriate fuse protection (10A fuse)
•A heating emergency stop switch outside the installation space and a 10 A fuse protection are
mandatory requirements. In order to increase the level of safety, the German Association for Elec-
trical, Electronic & Information Technologies (VDE) in its guideline DIN VDE 0100 part 739
recommends fitting the unit with a residual current device with a trip current setting of 30 mA
(DIN VDE 0664 or ÖVE-SN 50).
•Sensor cables, mains power cables and load cables must be routed separately.
•Even when working on the sensors, the control panel is to be completely (all poles) disconnected
from the mains power supply.
•Remove the fuse before working on the mains power supply. Electrocution hazard!
•The plugged connectors in the unit and on the console are installation plugs and may not be ei-
ther connected or disconnected when the power is on! The wood-fired heating system is to be
disconnected completely from the mains power supply using the installed isolating device!
•The electrical safety of the unit and its optimal malfunction-free operation is only ensured if the
control panel is connected to an approved protective conductor (earthing) system. If in doubt,
please have the on-site electrical wiring system checked by an approved electrician. The manu-
facturer cannot be held responsible for damage or operational malfunctions that are caused by the
absence or breakage of an earthing conductor.
•It is not permitted to connect the unit to the power utility grid using an extension cable because
this method would not guarantee the required degree of safety.
•In regions where overvoltage hazards exist, suitable precautions should be taken (e.g. lightning
protection).
2.2.1 Connecting sensors, control and mains power cables
Caution! Do not route the sensor cables together with the current carrying cables! The routing of the
sensor cables must be kept as far apart from the current-carrying cables as possible. The mains power
and sensor cables are not permitted to come into contact with any hot parts of the boiler because there
would be a risk of a short circuit.
6

All components are to be connected in accordance with the circuit diagram for the installed plant (see
section „System suggestions„ in our planning folder wood-fired heating systems). All connector plugs
are encoded and cannot be interchanged.
Figure 1: Back of type 614 control panel
Connection of the 2-pole add-on module:
1 (left) Tx +
2 (right) Tx -
Connection of the 10-pole connector strips:
1
2
3 1 - 5 vacant
4
5
6 boiler sensor (yellow)
7 buffer tank sensor, top (red )
8 buffer tank sensor, bottom (blue)
9 contact switch for loading door
10 exhaust gas sensor (silver)
A special feature of this control panel is that external modules (from BD model series) are automatically
recognised upon connection of the BUS interface. The external heating system is always to be connected
7

to the BD600 and not to the boiler control panel! The external heating is only connected to the type 614
control panel if no BD600 has been installed.
Please ensure that the securing screws in all of the connector plugs are properly tightened. Loose terminal
connections lead to contact resistances and therefore cause faulty switching. It is essential to ensure that
no cable has insulation interfering with its proper termination. Inspect the wiring connections once a year
and re-tighten the securing screws if required.
3 Indicators and controls
Figure 2: Front of type 614 control panel
The type 614 control panel has a touchscreen (touch-sensitive display screen). This means that all
settings are made directly using this screen. Other controls, like switches and dials are not necessary.
The unit switches on automatically when the mains power is connected.
Take care! The screen is touch sensitive; do not employ sharp instruments when using it! It is
sufficient to touch the screen lightly.
Navigating between menus Navigating to and setting of values
in the menus
Return to main menu / select module Moves one page back in menu
Return to standard screen Moves one page forward in menu
Start boiler Increases the value to be set
Swap between the standard screens Decreases the value to be set
8

Swap between the standard screens Confirms the value set
Moves one menu level higher Escapes data entry mode and
moves back in the menu
If the boiler is in smouldering mode, this is indicated by a loud audible alarm. The buzzer can be si-
lenced for 5 min. by pressing the display. Please consult section 5.9 and in future prevent the smouldering
mode from occurring; it damages both the boiler and the environment.
4 The menu
4.1 Design
Once the unit is connected, the Künzel Logo appears for five seconds along with the designation of
the control unit at the lower edge of the screen (e.g. TS- 614, important information when addressing
questions to our customer support service).
After this, the display changes to the standard screen:
Figure 3: The standard screen (here: boiler actual measurements)
The and button is used to switch to a boiler diagram, the boiler temperature display
and a rapid adjustment of the BD 600 heating controller (if connected). The boiler diagram shows the
9

operating modes at a glance and indicates which components are in operation.
The operating mode is shown top, right. There are five operating modes (STANDBY, IGNITION,
START PHASE, OPERATION, BURNOUT) and two alarm indicators (SMOULDERING, LOADING
DOOR). The operating modes are explained in greater detail in section 5.
The main menu is reached by pressing on the menu button (select module). The settings for
the boiler, the display and the connected modules can be performed here. Use to return to
the standard screen. After about 60 seconds without any input, the screen automatically returns to the
standard screen.
Figure 4: The main menu
10

4.2 Boiler sub-menu
Figure 5: Sub-menu HV
4.2.1 Buffer tank min. temperature
The buffer tank min. temperature is the temperature in buffer tank mode at which the buffer tank is
unloaded before it recommences operation. The value can be set to between 30 and 70◦C. The factory
setting is a buffer tank min. temperature of 55 ◦C. The boiler starts when the upper buffer tank temper-
ature falls below the buffer tank minimum temperature. When operating without an outside temperature
control unit or an outside temperature control unit from another manufacturer, the following settings
apply: When operating with a buffer tank and domestic water heating we recommend setting the buffer
tank min. temperature to at least 5◦C above the domestic water temperature (usually 50 ◦C, which would
put the buffer tank min. temperature at 55 ◦C). The buffer tank minimum temperature can be set lower
if the wood gasification boiler is only used to heat the building (i.e. no domestic water heating). These
settings must be in accordance with what you find comfortable. However, it should be considered that a
wood-fired boiler always requires a certain amount of time to get up to temperature.
4.2.2 Buffer tank monitoring system
Continuous buffer tank monitoring system:
The upper buffer tank temperature is monitored continuously. If this temperature rises above the boiler
change-over temperature, the external heating system is switched off regardless of the operating mode. It
11

is therefore, for instance, possible when feeding auxiliary sources of heat into the buffer tank (e.g. solar
heating), to switch off the external heating system using the microprocessor control panel. If the upper
buffer tank temperature falls below the boiler change-over temperature, the external heating system is
switched on. Please note: in this mode of operation the external heating system is not permitted to feed
into the buffer tank! Please observe the requirements detailed in the Künzel hydraulic diagrams.
Conditional buffer tank monitoring system:
The external heating is enabled once the HV boiler has completed the burnout phase and the tempera-
ture has fallen below the boiler change-over temperature. The buffer tank temperature is now no longer
monitored. With the switch in this position, it is possible to load the buffer tank (with solar heating,
for example) and use the external heating system in parallel. The buffer tank monitoring system is only
reinstated when the HV boiler goes into operation. The external heating system is then deactivated and
only enabled again once the burnout has completed and the temperature has fallen below the boiler
change-over temperature.
4.2.3 Changeover point
The changeover point between the wood boiler and the external heating can either be set using the HV
boiler or using the upper buffer tank temperature. As standard, the changeover is performed using the
HV boiler: As soon as the HV boiler switches to the „operating“ state, the external heating switches off.
When effecting the changeover via the top buffer tank sensor, the external heating is deactivated when
the temperature exceeds the buffer tank minimum temperature at the top buffer tank sensor. Please also
take account of the special features of the conditional buffer tank monitoring system if this is activated.
4.2.4 Ignition period
If a heating mode with an igniter has been selected, it is necessary to set an ignition period. In this period
the exhaust temperature must rise by 15◦C, otherwise the start-up attempt is considered to have failed.
Values ranging between 1 and 30 minutes can be selected. The factory setting is a value of 15 minutes.
4.2.5 Burn-out time
The burn-out time is the after-run period for the fan following the detection of burnout. Times of between
15 and 45 minutes can be set. The factory setting is a burn-out time of 30 minutes. The set value remains
saved until another value is set.
4.2.6 Pump mode
Exhaust gas : The boiler circulation pump is controlled via the exhaust temperature. The boiler
circulation pump switches according to the following conditions:
Pump ON if exhaust temperature >= start exhaust gas temperature
Pump OFF if exhaust temperature <= 87◦C and the control unit is not in the operating mode
12

HV-boiler : (Standard setting) The boiler circulation pump is controlled via the boiler temperature.
Operation without buffer tank: Pump ON if boiler temperature >= 70◦C.
Pump OFF if boiler temperature <= 65◦C.
Operation with buffer tank: Pump ON if boiler temperature >= 70◦C and boiler temperature 3k >= lower
buffer tank temperature
Pump OFF if boiler temperature <= 65◦C or boiler temperature 1k <= lower buffer tank temperature
4.2.7 Fans
The type 614 control panel permits plant operation with forced draft or ID fans. Before putting the plant
into service for the first time it is essential to set the type of fan in the menu (standard setting: forced
draft fan).
4.2.8 Start Mode
This determines when the HV boiler is to switch from the start-up phase to the „operating“ mode. Ei-
ther when the exhaust temperature has risen above the initial exhaust temperature or when the boiler
temperature has exceeded 70 ◦C.
4.2.9 Exhaust gas sensor
If operating the heating either without an exhaust gas sensor or with a defective sensor, the option „with-
out“ must be selected in the menu.
4.2.10 Exhaust gas factor
This value should only be changed after having consulted Künzel’s customer support service! The
factory setting is 65
4.2.11 Start exhaust gas
The start point setting for the start exhaust temperature determines the switching point for the changeover
from the start-up phase to the operating mode. In the start-up phase, the fan runs constantly at 100%
output. In the operating mode, the fan output is regulated in 5 stages via the exhaust temperature. Setting
range for start exhaust temperature 80 ◦C - 110◦C, factory setting 90◦C.
4.2.12 Service
Settings: All of the settings made can be read here.
Status: All of the current operating modes (e.g. pump running, fan running, etc.) are displayed here.
Statistics: The following statistics are listed under this item:
•Period of operation [h]
13

•Smouldering [h]
•Over-temperature [u]
•Ignitions [u]
•Start-up procedures [u]
•Failed start-ups [u]
•Resets [u]
•Commissioning date [TT.MM.JJ]
(Note: these figures only start to be recorded after the first hour of continuous connection to the mains
power supply)
Reset: All of the settings made can be reset to the factory preset values.
Test: (only available in „Standby“ mode)
This feature can be used to manually switch the outputs of the control panel for testing purposes.
•Pump
•Changeover R/L
•Changeover L1
•External heating
•Fans
•Ignition
4.3 Display sub-menu
Figure 6: The display sub-menu
14

This sub-menu can be used to set general options like brightness and contrast, date, time and language.
4.3.1 Language:
The selection of languages available depends on the installed software version. Up to now the languages
available are German, English, Italian and Spanish. There are plans to provide further languages.
4.3.2 Timeout:
„Timeout„ is defined as the period after which the display automatically returns to the darkened mode.
4.3.3 Date and time:
The unit does not automatically switch from summertime to wintertime.
The first press of the button, which switches the screen back from the darkened to the illuminated
mode, is NOT counted; it only serves to switch on the screen!
4.4 Info sub-menu
The version number for the software in use is saved here.
4.5 Outside temperature control unit and other auxiliary modules sub-menu
This submenu only appears once the modules have been installed and is described in the corresponding
auxiliary module operating manual.
5 Mode of operation and control
5.1 General information
A pre-requisite for unit to operate perfectly is that the boiler and the type 614 microprocessor control
panel must be installed properly. The type 614 control panel for the wood gasification boiler is charac-
terised by its user-friendly operation. This ensures a high degree of operating safety. In addition, you can
adjust your heating system to meet your precise needs. As standard, the control panel is provided with
factory settings so that no additional settings have to be made for normal operation of the unit.
5.2 Pump protection
In order to prevent the connected pumps (boiler circulation pump) becoming stuck due to an extended
period of non-use, the pumps are automatically switched on if they have not run for an extended period.
For this reason, every pump is run for 20 seconds if they have not run in the preceding 24 hours.
15

5.3 Frostguard
Pump ON if boiler temperature <= 4◦C.
Pump OFF if boiler temperature >= 6◦C
5.4 The operating modes
STANDBY: The boiler is switched off and is waiting for the start signal.
IGNITION: The START button has been pressed, the start option has been selected (manual, electrical,
etc.), the boiler fires up
PAST FIRING: The exhaust temperature has risen by at least 15◦C (the fire is burning) and the igniter is
deactivated
OPERATING:
with exhaust gas sensor: the exhaust temperature has risen above the set „start exhaust“ temperature
without exhaust gas sensor: The boiler temperature has risen above 55◦C
BURNOUT:
with exhaust gas sensor: the exhaust temperature falls below the set „Start exhaust“ temperature for an
extended period of time. For more information refer to section 5.10
without exhaust gas sensor: the boiler temperature falls below 55◦C for longer than the period set for the
„Burnout time„
SMOULDERING: The boiler can no longer dissipate the heat and the fan shuts down. Refer to section
5.9
FUEL DOOR: The fuel door is open or the start-up flap rod is not locked in position
5.5 Start
The type 614 microprocessor control panel permits the start-up procedure to be done conventionally or
using an electrical igniter. You have filled the wood gasification boiler with fuel logs in accordance with
the specifications in your boiler description.
Please note:
Should your application require an electrical start despite having a filled buffer tank, this is also possible
after a warning. However, please consider that this could lead to a smouldering fire in your boiler if
the heat dissipation is too low, and can lead to excessively high temperatures or can trip the thermal
discharge safety device. The operator of the plant must immediately ensure that the heat consumption is
sufficient following the start-up.
Once the START button has been pressed, the type of ignition is requested:
16

Figure 7: Selection of type of ignition
5.5.1 Manuel firing
Light the fuel logs, close the loading door and follow the instructions in the boiler operating manual.
Do not leave the loading door open during the start-up phase because flying sparks represent a fire
hazard!
5.5.2 Electrical firing
Press the START button and select electrical ignition.
Following a successful start, the igniter remains active until:
- the exhaust temperature has risen by 15◦C or
- the exhaust temperature has risen above +90◦C or
- the ignition period has expired (see item „Setting the maximum firing time“ ).
5.5.3 Automatical
The „Start, when buffer tank is empty“ function is an extremely useful and convenient feature (not shown
if the buffer tank is already empty, in this case a start-up can begin immediately). It permits the wood
gasification boiler to start automatically once a thermally filled buffer tank has been discharged. The
procedure is as followed: Once the buffer tank has been filled and the burn-out phase completed, the
boiler can be refilled with fuel logs in accordance with the specifications in your boiler description.
Important: the boiler may not have any remaining firebed, otherwise there is a risk of a smoulder-
ing fire developing!
If the upper buffer tank temperature falls below the buffer tank minimum temperature, a start-up is
automatically initiated with the electrical igniter. The pre-requisites for this are: the buffer tank sensor
must be connected and there must be an exhaust gas sensor fitted.
for connected BD 600:
The wood boiler does not start before it receives the start signal from the outside temperature control
unit.
5.5.4 Date
A fixed starting time (date, time) can be set here for the boiler ignition system. This of course requires
the HV boiler to be filled and ready for service.
17

5.6 Operating
Once the START button is pressed, the fan starts to run continuously. If the exhaust temperature exceeds
the value set under „Start exhaust“ , the start-up phase ends and the control panel switches to the OPER-
ATING mode. All further actions are now performed automatically. Automatic operation is discontinued
as soon as a fault or the burn-out mode is detected.
The fan speed reduction feature is activated if the boiler temperature rises above 82◦C. This reduction
takes place automatically in 5 stages, depending on the boiler temperature and the exhaust temperature.
The fan speed reduction feature is also activated if during operation the exhaust temperature rises above
the value necessary for the rated output of the boiler. This avoids the generation of excessively high
exhaust temperatures and therefore a deterioration in efficiency. It also reduces the wear and tear upon
burner components. The maximum boiler temperature is set at 88◦C and cannot be changed.
5.7 Adding fuel logs while the boiler is operating
If the buffer tank is more than 80% full, which can be determined from the grey bar in the boiler diagram,
no more wood should be added to the boiler. There is otherwise a risk of smouldering fire developing
within the boiler.
Figure 8: At this point, no more wood may be added to the boiler!
Please always bear in mind that flames can escape when the boiler is opened! This is particularly
true when operating the boiler with a forced draft fan. In order to add fuel logs sufficient remaining
firebed must be present in the boiler, otherwise a renewed start-up phase is required. HV (forced draft
fan): The fan is switched off while the loading door remains open. HV-S (ID fan): The fan continues to
run while the loading door is open.
Provided the start-up flap (and the loading door) is not open for more than 30 min., the control panel will
remain in the OPERATING mode once the loading door is closed, the fan restarts automatically and it is
18

not necessary to press the START button. If the fan does not restart after the loading door is closed (can
be seen on the boiler on the standard screen), the START button must be pressed once again.
5.8 Aborting heating procedure
A previously started heating procedure can be aborted by simply pressing the STOP button (if T exhaust
< 90◦C). This is only possible during the start-up procedure! Ensure there is sufficient heat dissipation
for the remaining firebed!
5.9 Detection of smouldering and behaviour upon overheating
If, despite reducing the fan speed (and therefore the boiler capacity), the boiler temperature reaches 88◦C,
the fan is switched off and a loud audible alarm is triggered! This can occur if the wood boiler is started
despite the buffer tank being fully charged, the boiler circulation pump fails during operation or the heat-
ing system has been incorrectly dimensioned (buffer tank too small). The generated heat can no longer
be dissipated and it is necessary to reduce the fire to a minimum for safety reasons. The boiler is now
in a state of smouldering fire, which is detrimental for both the boiler and the environment. The micro-
processor control panel detects this state and triggers a (continuous) audible alarm and simultaneously
displays an alarm message. A smouldering fire occurs if the control panel has to shut off the fan while
it is operating because the boiler temperature is too high. A smouldering fire is caused by insufficient
heat consumption or a premature or excessively frequent adding of fuel logs to the furnace. The state
of „smouldering“ is to be avoided under any circumstances because it leads to corrosion and tar-
ring of the boiler. The alarm signal is switched off automatically once the unit has cooled down to the
temperature necessary for the resumption of normal operations. The aggregate period during which the
boiler is in a smouldering state is recorded in the statistics. The buzzer can be silenced for 5 minutes by
touching the display! The boiler circulation pump continues to run during this time in order to dissipate
the heat from the boiler. You can find out how to avoid overheating the boiler by consulting the operating
manual. The alarm is cancelled once the boiler temperature falls below 86◦C, the fan restarts and the
combustion process is restarted.
5.10 Burnout
If the exhaust temperature falls below the temperature set in „Burnout time“ during the burn-out phase
for more than the period set in „Start exhaust“ , the control panel switches to buffer tank mode and the
fan is switched off.
Under some circumstances this can also occur during the re-filling or stoking procedure if it takes too
long. The exhaust gas sensor is not surrounded by hot exhaust gas while this takes place and cools.
Always ensure that the fan restarts after closing the loading door (see boiler diagram). If this is not the
case, the START button must be pressed once again.
Please note: If the control panel is in BURNOUT mode and the boiler temperature is still greater than
67◦C, opening the loading door will trigger a restart. The fan begins to run again once the loading door
19

has closed. If the boiler is not to be used any further, the STOP button must be pressed.
6 Combination with other modules
The control panel recognises all of the modules automatically once they have been connected. Consult
the corresponding operating manual to find out how to configure these modules.
Proceed as follows when connecting modules: all modules are to be connected in series. At the start
of this chain is always a device that contains the control software. This is either a control panel from
the 600 model series or the display unit for the type BD600A outside temperature control unit. The
following modules are connected to another via the two-pole BUS interface. The remote control / room
control unit (A600), if present, is always located at the end of the chain. If another module is fitted to the
end of the chain, the bus connection must be switched on there! Two small connector plugs are used for
this purpose. See the operating manual for the modules.
At present, the following modules are available:
-BD600 : This is a module for controlling heating systems. It controls mixing valves, pumps and other
heating boilers and (in conjunction with the type 614 control panel) regulates the entire heating system
and domestic water system depending on the time of day, outside/ inside temperature and buffer tank
status.
-F600 : Expansion kit for a second heating circuit (in conjunction with BD600), incl. add-on software
-A600 : This is a remote display unit that is, for instance, installed in the occupied areas of the building.
The values can be read from here and also modified. Only in conjunction with the BD600!
under development:
-SO600 : This is a module for the incorporation of a solar heating system.
20
Table of contents
Popular Control Panel manuals by other brands
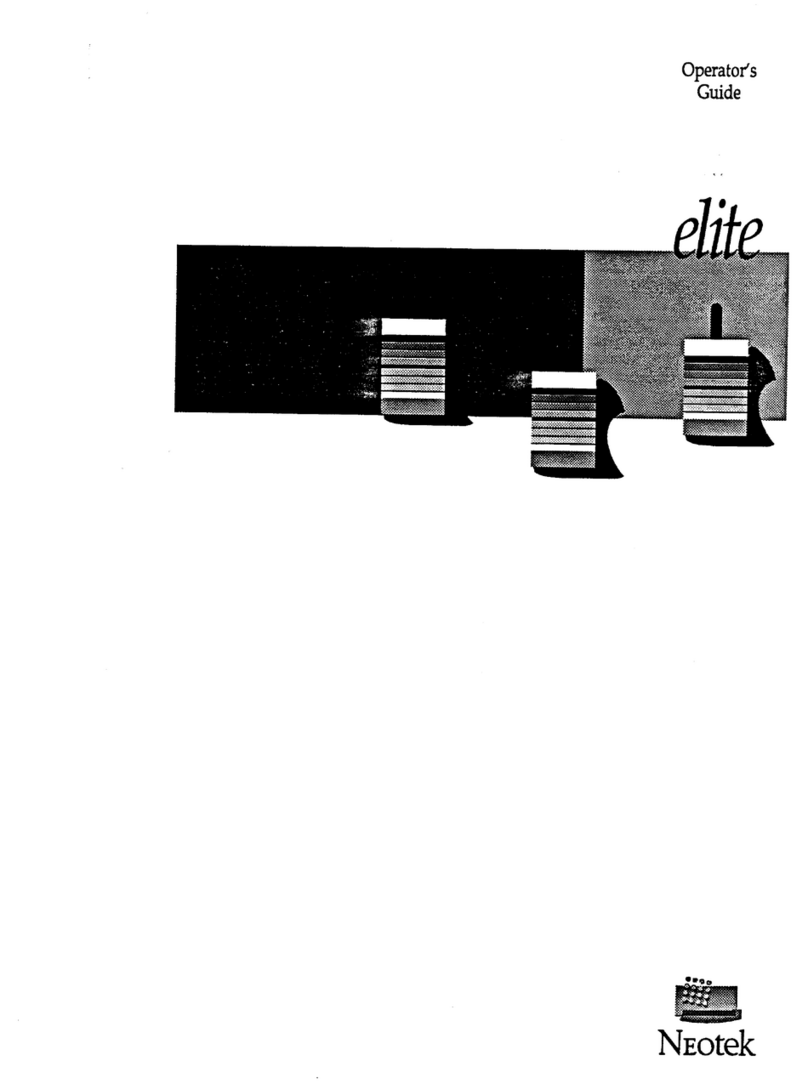
Neotek
Neotek elite Operator's guide

technoswitch
technoswitch ORYX200 Series Installation & operation manual
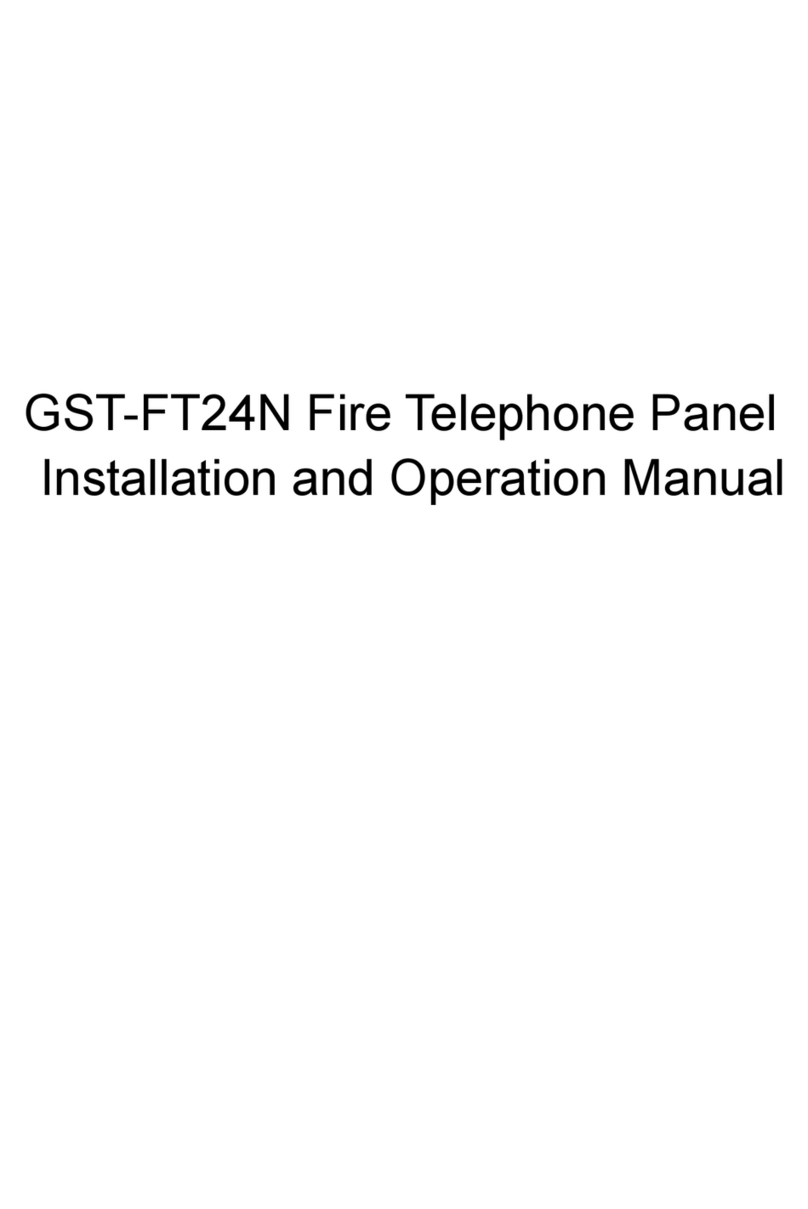
GST
GST GST-FT24N Installation and operation manual

Bell
Bell QS-9004-VRZ How to use

Simplex
Simplex MINIPLEX 4100ES Series quick start guide
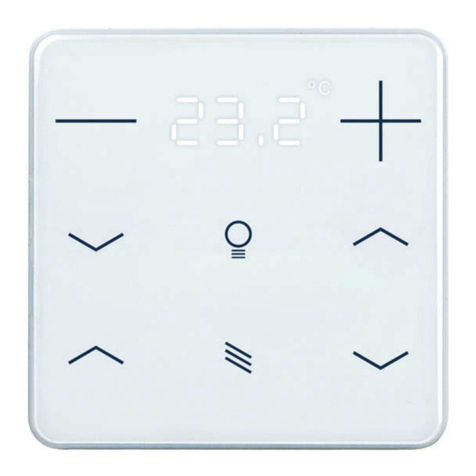
elsner elektronik
elsner elektronik KNX eTR 208 Technical specifications and installation instructions
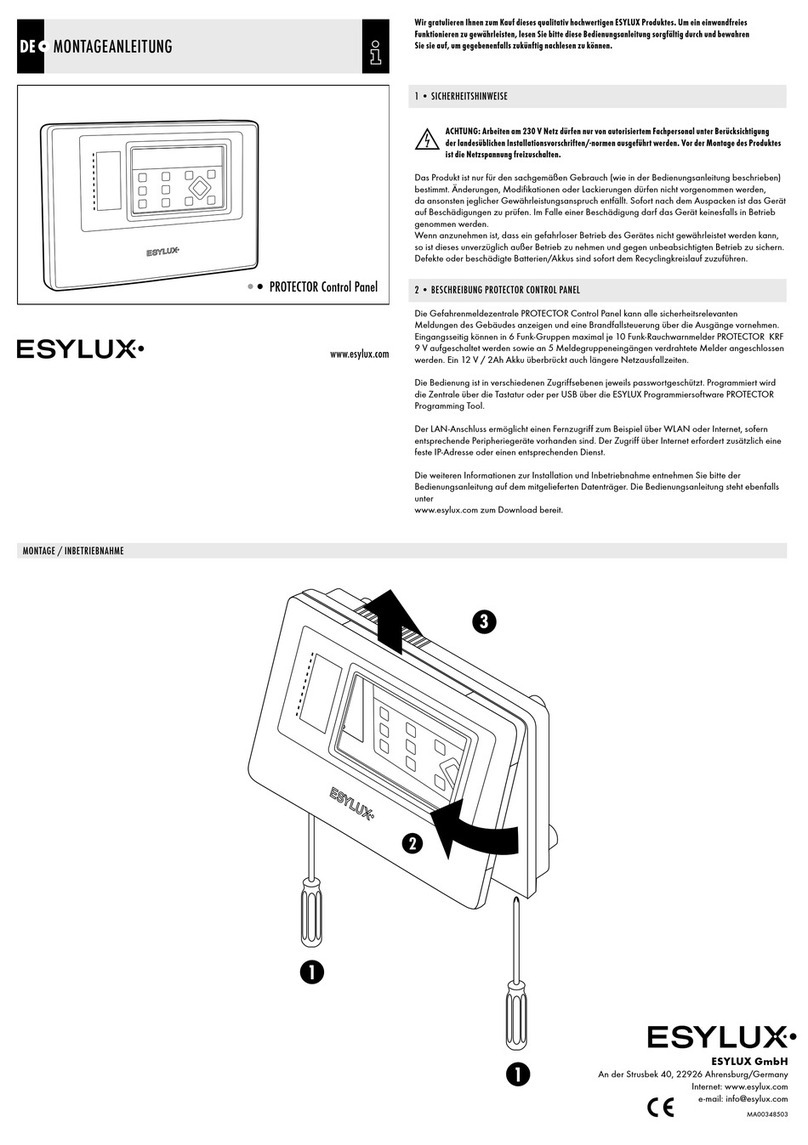
ESYLUX
ESYLUX PROTECTOR installation instructions
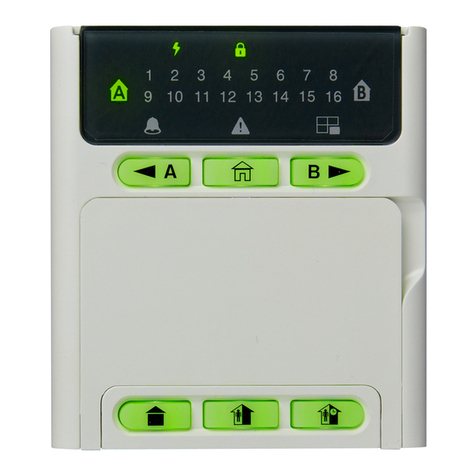
Teletek electronics
Teletek electronics ECLIPSE 8 User and Manager Operation and Programming Short Manual
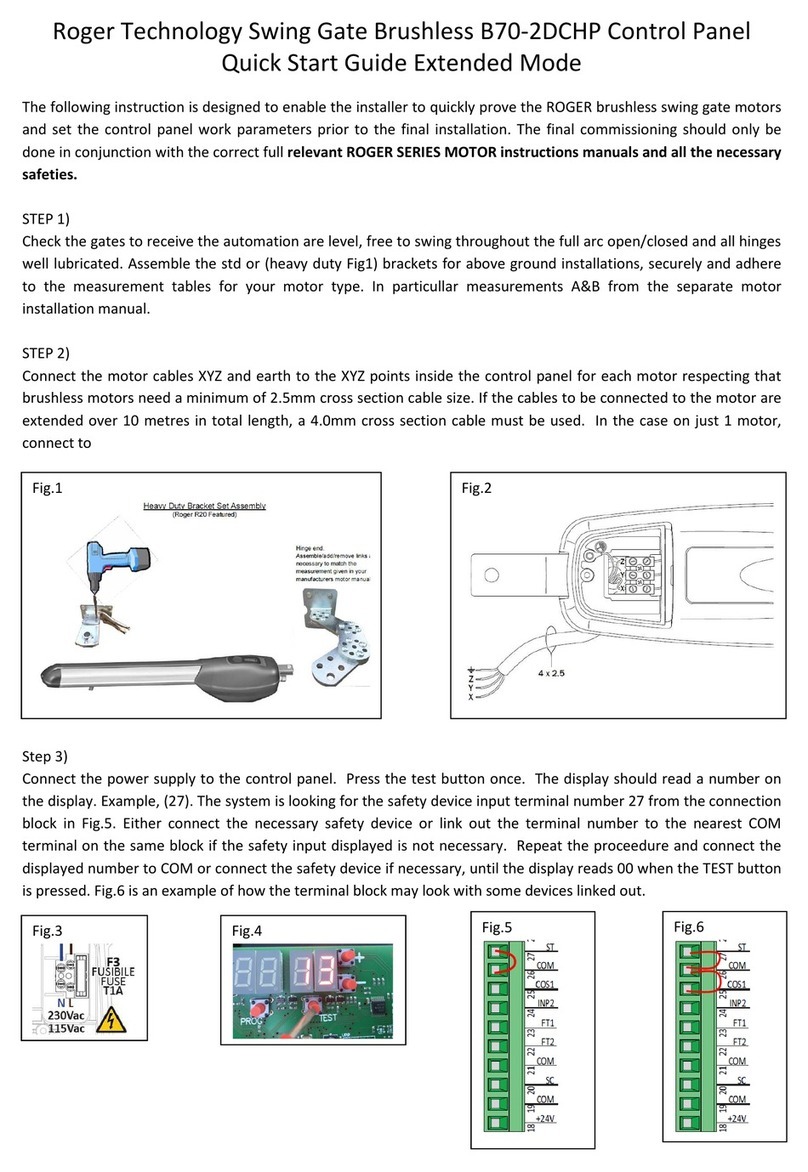
Roger Technology
Roger Technology B70-2DCHP quick start guide
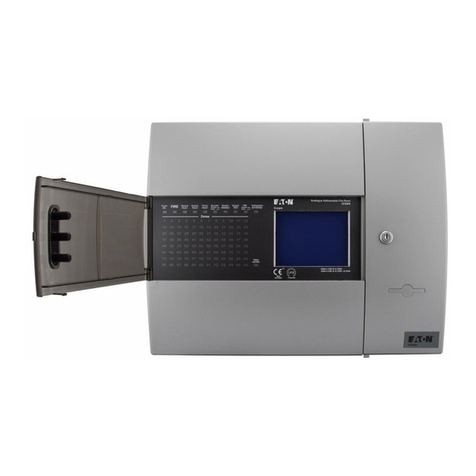
Eaton
Eaton CF3000 Installation and operation manual
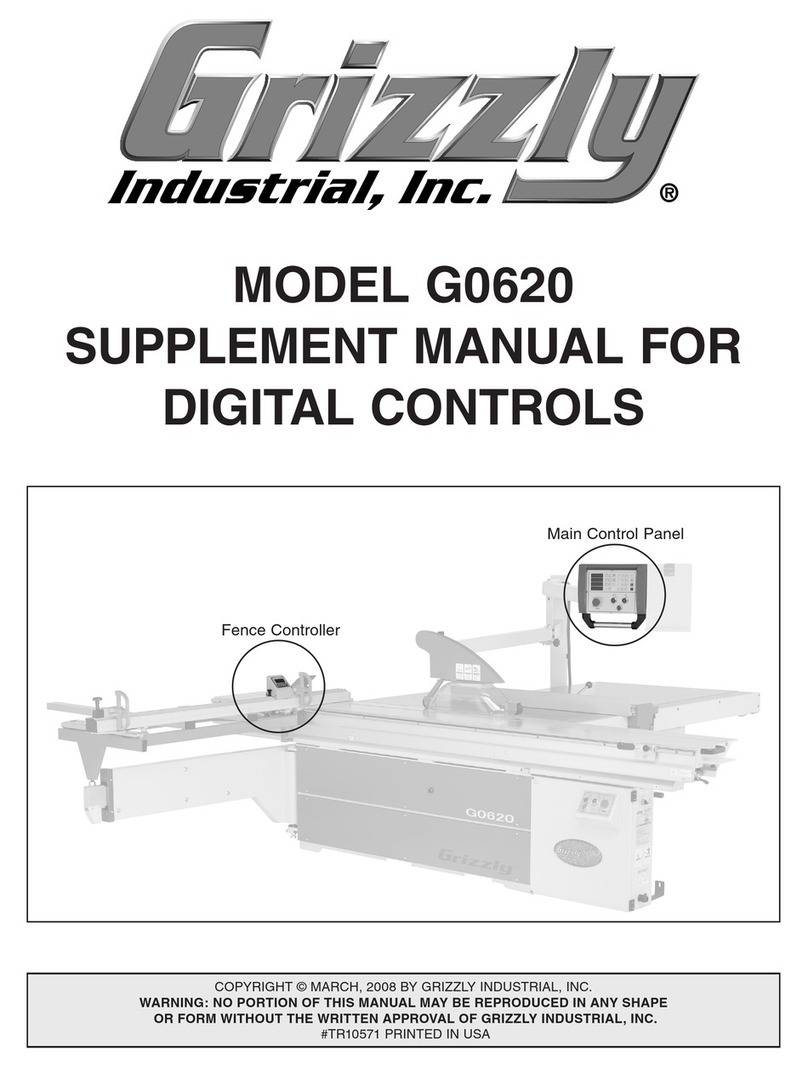
Grizzly
Grizzly G0620 Supplement manual
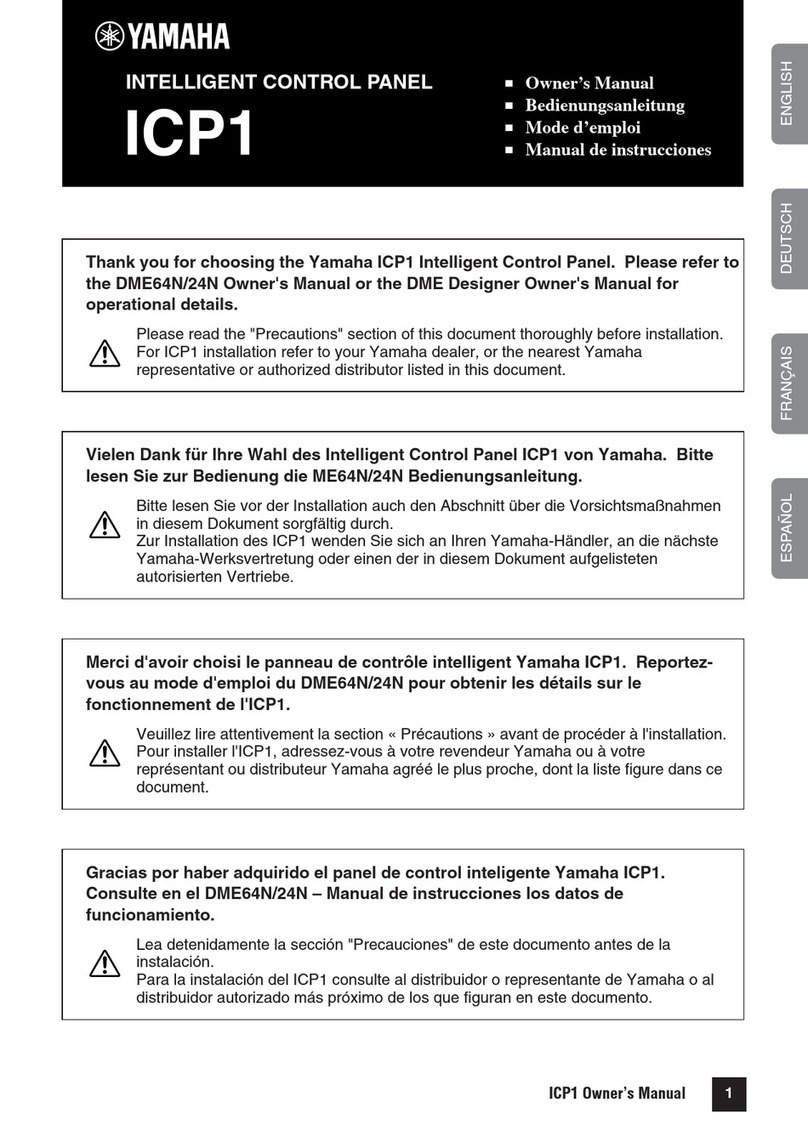
Yamaha
Yamaha ICP1 owner's manual