KW DAVID-613 User manual

MANUAL
PROCESSORSYSTEM DAVID-613
IN GENERAL
MOUNTING
TEACH IN
EXAMINATION AUTHORITIES
FAULT MANAGEMENT

KW Aufzugstechnik GmbH ASSEMBLY INSTRUCTIONS DAVID-613
DAVID-D613-Inbetriebnahme-V122-E 26.05.2020 Page - 2 -
KW Aufzugstechnik GmbH Teach-In-DAVID-613
Version V1.22 of 26.05.2020
All rights reserved. No part of this publication may be reproduced, stored in a retrieval system, or trans-
mitted in any form or by any means, electronic, mechanical, photocopying, recording, or otherwise,
without the prior written permission of KW Aufzugstechnik GmbH. The information contained herein is
designed only for use with this lift controller system.
Neither KW Aufzugstechnik GmbH nor is affiliates shall be liable to the purchaser of this product or third
parties for damages, losses, costs, or expenses incurred by the purchaser or third parties as a result of:
accident, misuse, or abuse of this product or unauthorized modifications, repairs, or alterations to this
product, or (excluding the U.S.) failure to strictly comply with KW Aufzugstechnik GmbH’s operating and
maintenance instructions.
KW Aufzugstechnik GmbH shall not be liable for any damages or problems arising from the use of any
options or any consumable products other than those designated as Original KW Aufzugstechnik GmbH
Products.
General Notice: Other product names used herein are for identification purposes only and may be
trademarks of their respective owners.
Copyright © 2001 - 2020 KW Aufzugstechnik GmbH, Oberursel
KW AUFZUGSTECHNIK GmbH
Zimmersmühlenweg 69
D-61440 Oberursel / Germany
Ph. +49 (0) 6171-9895-0
Fax. +49 (0) 6171-9895-19
Int. www.kw-aufzugstechnik.de
Hotline Ph. +49 (0) 6171-9895-12 / -13

KW Aufzugstechnik GmbH ASSEMBLY INSTRUCTIONS DAVID-613
DAVID-D613-Inbetriebnahme-V122-E 26.05.2020 Page - 3 -
CONTENT
STEP 00
MR/ Roomless –Fitting locations of the Components
5
STEP 01
MR/ Roomless –Mounting of the Switching cabinet –Example KW04M
6
STEP 02
MR/ Roomless –Assembly of the Mounting screws
6
STEP 03
MR/ Roomless –Positioning the Switching cabinet in order to mark the Assembly-Holes above
6
STEP 04
MR/ Roomless –Making the Assembly-Drills above
6
STEP 05
MR/ Roomless –Final-Mounting –Mounting of the Switching cabinet
6
STEP 06
MR/ Roomless –Optional –Usage of a socket of a Switching cabinet
6
STEP 07
Cabinet –Description of the Control panel installations
7
STEP 08
Cabinet –Preparing the Power Supply
9
STEP 09
Cabinet –Connection of the Power Supply-Wire
9
STEP 10
Cabinet –Connection of the Shaft pit box
9
STEP 11
Cabinet –Connection of the Shaft top box
9
STEP 12
Cabinet –Optional - Connection of the Motor-PTC-Wire
9
STEP 13
Cabinet –Optional - Connection of the Brake-Element-Monitoring
9
STEP 14
Cabinet –Optional - Connection of the Speed Restrictor MR
10
STEP 15
Cabinet –Optional - Connection of the Emergency-Stop-Switch Machineroom / Rollsroom
10
STEP 16
Cabinet –Optional - Connection of the Bolt-Contacts
10
STEP 17A
Cabinet –Hydraulic - Connection of the Motor-Wires 1 & 2
10
STEP 18A
Cabinet –Hydraulic - Connection of the Relevelingaggregate
10
STEP 19A
Cabinet –Hydraulic - Connection of the Oilcooler / Oilheating
10
STEP 20A
Cabinet –Hydraulic - Connection of the Valve-Wires
11
STEP 21A
Cabinet –Hydraulic –Optional- Connection of Lower- / Overpreasure-Contakts of the Aggregate
11
STEP 17B
Cabinet –Rope - Connection of the Brake-Coil-Wire
11
STEP 18B
Cabinet –Rope - Connection of the Motor-Wire
11
STEP 19B
Cabinet –Rope - Mounting & Connection of the Brake-Resistor-Wire
11
STEP 20B
Cabinet –Rope - Connection of the Encoder (Inverter)
12
STEP 21B
Cabinet –Rope - Connection of the external Encodersystem Solution (Rope) Old-machines
12
STEP 22B
Cabinet –Optional - Connection of the Overloadmeasure-Switch
13
STEP 23
Cabinet –Optional - Connection of the Emergencypower-Evacuation
14
STEP 24
Cabinet –Optional - Connection of the Fire-Evacuation
14
STEP 25
Cabinet –Optional - Connection of the Input „Controller and Carlight OFF“
14
STEP 27
Cabinet –Optional - Connection of the potentialfree Messages
14
STEP 28A
Cabinet –Connection of the Buswire for the Remotestation ER-2013
14
STEP 29
Cabinet –Connection of the Power-Buswire for the Remotestation ER-2014
14
STEP 30
Cabinet –Connection of the Power-Buswire for the Remotestation ER-2018
14
STEP 31
Cabinet –Connection of the Handheldterminal HPG-60 to the Centralunit
15
STEP 32
Cabinet –Communication of the KW IPhone-App to the Controller
15
STEP 33
Cabinet –Navigation with the Handheldterminal HPG-60 / IPhone-App
15
STEP 34
Cabinet –Connection of the Mounting-Handheldbox / Activation of the Assembly-Drive
15
STEP 35
Shaft pit –Mounting of the Shaft pit box X6
16
STEP 36
Shaft pit - Connection of the Shaft pit box
16
STEP 37
Shaft pit - Connection of the Shaft light
16
STEP 37B
Shaft pit - Connection of the LED shaft lighting type 3
16
STEP 38
Shaft pit - Connection of the Second Emergency-Stop-Switch S1B
16
STEP 39
Shaft pit - Connection of the Pit-Door / Pitch-Ladder-Contact S1C
16
STEP 40
Shaft pit - Connection of the Restrictor-Weight Contact S1D
17
STEP 41
Shaft pit - Connection of the Burstpipe Contact (Hydraulic) S1E
17
STEP 42
Shaft pit - Connection of the Emergency-End-Switch Bottom S2E
17
STEP 43
Shaft pit –Mounting of Emergency-End-Switch Bottom
17
STEP 44
Shaft pit - Connection of the Buffer Contacts for Cabin and Counterweight S2F & S2G
17
STEP 45
Shaft pit - Connection of the Shaft-Door Contacts S7.1 to S7n
17
STEP 46
Shaft pit - Schematic diagram - reduced pit Reduced head
18
STEP 47
Shafttop –Connection of the door release contacts S9.1 of the lowest shaft door
19
STEP 48
Shaft top - Connection of the reset key switch at the bottom shaft door
19
STEP 49
Shafttop –Connection of Si-Kr. Folding support cabin S3M / S4M VSG
19
STEP 50
Shafttop - Connection of the closer folding support cabin traffic light 5L & 5M
19
STEP 51
Carroof - Installation of the H21 protective area traffic at VSG
19
STEP 52
Shafttop - Connection of the reset key switch at the bottom shaft door
19
STEP 53
Shafttop –Connection of Si-Kr. Folding support cabin S3M / S4M VSG
19
STEP 54
Carroof –Connection of the closer folding support cabin traffic light 5M & 5N
19
STEP 55
Carroff - Mounting of the Inspectionbox X7
20
STEP 56
Carroof- Connection of the Speed-Restrictor-Contacts for Cabin and Counterweight
20
STEP 57
Carroof Connection of the Distance-Limiter-/Emergency-End-Switch Top 1 & 2
20
STEP 58
Carroff –Monting of the emergency empting top
20
STEP 59
Carroof Connecting of the remote control and reset speed cabin
20
STEP 60
Carroof –Connecting of the remote control and reset speed cabin
20
STEP 61
Carroof –Connection of the door unlocking contacts of the shaft doors S.9.2 to S.9.n at VSK
20
STEP 62
Caroof –Mounting of the inspectionsbox
21

KW Aufzugstechnik GmbH ASSEMBLY INSTRUCTIONS DAVID-613
DAVID-D613-Inbetriebnahme-V122-E 26.05.2020 Page - 4 -
STEP 63
STEP 64
STEP 65
Caroof - Mounting of the Hanging cables
Carroof - Connection of the Hanging-Wire on the Cabin
Carroof –Connection of the Safetygear-Contact
21
21
21
STEP 66
Carroof –Connection of the Low-Restrictor-Weight-Contact - 1
22
STEP 67
Carroof –Connection of the Low-Restrictor-Weight-Contact –2
22
STEP 68
Carroof –Connection of the Carroof-Opening/ Car-Position-Contact
22
STEP 69
Carroof –Connection of the Emergency-Stop-Switch Cabin
22
STEP 70
Carroof –Connection of the Inspection-End-Switch
22
STEP 71
Carroof –Connection of the Folder-Railing-Switch - 1
23
STEP 72
Carroof –Connection of the Folder-Railing-Switch - 2
23
STEP 73
Carroof –Assembly of the safety room head H22 at VSK
23
STEP 74
Carroof –Connection of the protection room head H22 at VSK
23
STEP 75
Carroof –Connection of the Car-Door-Contacts
23
STEP 76
Carroof –Connection of the Car-Light
23
STEP 77
Carroof –Connection of the Car-Fan
24
STEP 78
Carroof –Connection of the Powersupply of Loadmeasurement-Unit / Photocells
24
STEP 79
Carroof - Connection of the Powersupply Door-Engines 230V AC
24
STEP 80
Carroof –Connection of the Door-Commands for 3 Door
24
STEP 81
Carroof –Connection of the 400V AC Door-Engine
24
STEP 82
Carroof –Connection of the Photocell Door-1, Door-2 & Door-3
25
STEP 83
Carroof –Connection of the Audiovisual Alert H69
25
STEP 84
Carroof - Connection of the Door-End-Switch, Revers-Contact
25
STEP 85
Carroof –Connection of the Bolt-Magnet-Coils
25
STEP 86
Carroof –Connection of the Cabin-Gong-Loudspeaker
25
STEP 87
Carroof –Connection of the KW-Loadmeasurement-Sensor
26
STEP 88
Carroof –Connection of the Over, Full- and Lowload-Sensorson the Cabin
26
STEP 89
Shaft –Connection of the Hall-Zone-Switch HSK01 for the Zone S71
26
STEP 90
Shaft –Connection of the Absolute-Encoder (Shaftcopying)
26
STEP 91
Shaft –Connection of the Inkremental-Encoder (Shaftcopying)
26
STEP 92
Shaft –Connection of the CANopen Components (Door-Engines-Loadm.-Senors -Shaftcopying)
26
STEP 93
Shaft - Connection of the Car-Panels
27
STEP 94
Shaft –Connection of the KW TFT-Displays
27
STEP 95
Shaft –Connection of the KW-Matrix-Displays
27
STEP 96
Shaft - Mounting of the LED-Shaftlight
28
STEP 97a
Shaft –Mounting the V-Shaft-Flags
29
STEP 98a
Shaft –HSK-01 Installation Instructions
30
STEP 97b
Shaft –Installation instructions for HSK90 / HSK46
33
STEP 98b
Shaft –Mounting of the Shaft-Flag-Holder ESF for HSK90
37
STEP 99a
Teach-In - Assembly of the Variotech-ANTS System
39
STEP 99b
Teach-In - Assembly of the Variotech-ANTS SAFE System
41
STEP 99c
Teach-In - Mounting of the ELGO LIMAX 2M
43
STEP 99d
Teach-In- Mounting of the ELGO LIMAX-SAFE- CP33
45
STEP 99e
Teach-In- Mounting of the KÜBLER-LES02-SAFE System
49
STEP 99f
Mounting the Schmersal UPS
51
STEP 99g
Mounting the WDG Silent Systems
52
STEP 100a
Assembly Instruction for Shaftbus with Remotestations ER-2013
54
STEP 100b
Assembly Instruction for Shaftbus with Remotestations ER-2014
62
STEP 101
Connection of the 7-pole Landing-Call-Wire
70
STEP 102a
Teach-In with digital Absolute copying with zone -switch
71
STEP 102b
Teach-In with digital relative copying w. incremental encoder
73
STEP 102c
Teach-In with digital Absolut copying CANopen ANTS SAFE
76
STEP 102d
Teach-In with digital Absolut copying CANopen ELGO LIMAX-SAFE CP33
84
STEP 103
Functional test –Self Monitoring for the Braking Elements after EN 81-1/2:1998+A3:2009
93
STEP 104a
ANTS-SAFE instructions for ANTS-ASA2-ASE & Kübler-PSU-LES02 (TÜV)
94
STEP 104b
LIMAX-SAFE instructions for LIMAX SAFE CP33 (TÜV)
95
STEP 104c
Functional test –Bypass of the Door –and bolt magnet
97
STEP 105
Functional test –Detection of an unintended car movement EN 81-20
98
STEP 106
Functional test –M.Brake-Opening in landing and the car door is not in the close position EN 81-20
99
STEP 107
Inspector - Session
100
STEP 108
Checklist of safety functions after the learning trip
105

KW Aufzugstechnik GmbH ASSEMBLY INSTRUCTIONS DAVID-613
DAVID-D613-Inbetriebnahme-V122-E 26.05.2020 Page - 5 -
STEP 00
Fitting Location of the Compo-
nents
Fitting- and Connecting positions at the elevator
Switching-Cabinet X1/
Component / Switch
PIN
Powersupply
X1-XPL1.2.3
Motor-/ Aggregat-Connection
U-V-W
Bakes- / Valve-Connection
720 bis 725
Motor-PTC
151- 152
Opt.Speed Restrictor MRoom
2 –2A
Emergency-Stop-Switch MRoom
4R –4S
Bolt-Contacts
6C - 7
Shaftbus-Connection
BIS-70
Overloadconnection / Light-OFF
BIS-70
Emergency Power evacuation
BIS-70
Fire-Evacuation
BIS-70
Shafttopbox X7/
Component / Switch
PIN
Remote Control Speed Restr. Car
761
Reset Remote Control Speed Car
762
Remote Control Speed Counterw.
763
Reset Remote Control Counterw.
764
Speed Restrictor Car
2 –2A
Speed Restrictor Counterw.
2A –2B
Emergency-End-Switch-1 Top
2B –2C
Emergency-End-Switch-2 Top
2C –2D
Inspectionsbox X11/
Component / Switch
PIN
Inspectionshandbox Car
Fix
Door-Engines-1 to 3
L20-PE-N20
Car-Fan
L54-PE-N4
Car-Light –Working-Lamp
L51-PE-N4
Bolt-Magnett-1 & 2
715-PE-716
Powersupply LMS & LG 230V
L40-PE-N4
Safetygear-Contact
3 –3A
Lower-Rope Contacts1 & 2
3A- 3B- 3C
Position-Contact /Roof Opening C
3C –3D
Opt. Emergency-Stop-Switch Car
3D –3E
Foldering-Railing-1 RSH
3L-M/4L-M
Foldering-Railing -2 RSH
3M-N/4M-N
Cardoor-1 & 2 & 3
6A-6B-6C
Inspection-End-Switch
4D –4E
Commands Door / CANopen
FKR
Shaftcopying System
FKR
Zone-Switch
FKR
Shaftpitbox X6/
Component / Switch
PIN
Inspektionshandbox Shaftpit
Fix
2. Emergency-Stop-Switch Opt.
1A - 1B
Contact Pit-Door / Ladder
1B –1C
Restrictor-Weight-Contact
1C –1D
Burstpipe-Contact (Hydraulic)
1D –1E
Emergency-End-Switch Bottom
2D –2E
Buffer-Contact Car
2E –2F
Buffer-Contact Counterweight
2F –2G
Folder Support Car RSB
3L-M/4L-M
Folder Support Counterw. RSH
3M-N/4M-N
Shaftdoors Side-1
5A –5B
Shaftdoors Side-2
5B - 6
Connection Shaft-Light
L42-PE-N4

KW Aufzugstechnik GmbH ASSEMBLY INSTRUCTIONS DAVID-613
DAVID-D613-Inbetriebnahme-V122-E 26.05.2020 Page - 6 -
STEP 1
Mounting of the Switching Cabinet –Example KW04M
The control cabinets KW01 and KW04 are intended for mounting on the wall.
If a switch cabinet socket is provided, the control cabinet is installed
with the Step 6.
Back to wall mounting: The control cabinets KW01 and KW04 have a guide groove
At the bottom of the bottom -> see picture Step 3. First, two screws are fixed in the wall,
whereupon the cabinet can be placed so that the top fixing holes can be marked and
drilled ...
Ensure that the fans are able to dissipate the heat to the right and left unhindered.
STEP 2
Assembly oft he Mounting Screws
As a first step, the two lower fixing holes are drilled into the masonry. First make sure that
the masonry has the necessary load bearing capacity. Otherwise, the use of a base is
recommended.
2 screws M8 with universal universal lever are used. The drilling distances are:
Distance of the drill holes in the cabinet KW04M: 490mm
Distance of drill holes in cabinet KW01N: 685mm
STEP 3
Positioning the Switching Cabinet in order to markt he As-
sembly-Holes above
Do not screw the screws completely into the wall so that the cabinet with its guide groove
can be placed on it and snapped into place.
Secure the cabinet with one hand against the drifting and mark the upper holes.
Now the cabinet can be safely placed on the floor again.
STEP 4
Making the Assembly-Drills above
Like the two lower ones, the two upper fixing holes are now drilled into the masonry.
To use are again 2 pieces of 10 universal blinds.
STEP 5
Final-Mounting - Mounting of the Switching Cabinet
Now the cabinet can be parked on its guide groove and click into place. The above
screws can be screwed in with a wrench or the ratchet.
Then the lower screws are tightened with a wrench.
If necessary (obstruction of the escape route) change the door stop.
For installations with a machine room, the cable duct is now installed.
STEP 6
Optional –Usage of a Socket of a Switch-
ing Cabinet
The KW06 and KW07 cabinets are supplied with a base as standard.
Optional sockets are available for cabinets KW03, KW04, KW240.
Before assembling the base, please make sure you know how to feed
the cables and make the corresponding cutouts!
The strain relief of the cables takes place in the base.

KW Aufzugstechnik GmbH ASSEMBLY INSTRUCTIONS DAVID-613
DAVID-D613-Inbetriebnahme-V122-E 26.05.2020 Page - 7 -
STEP 7
Explanation of the control panel devices
Danger!
To disconnect the entire elevator system from the power supply, in addition to the main switch Q1, the
fuses F4, F5, F6, F7 and optional motor protection switches must also be switched off.
Q1 Main switch the main switch is used to turn the elevator system, drive control, door drive and
safety circuit off and on. According to European law EN81, the shaft and cabin lighting must be in op-
eration despite the main switch Q1 being switched off. Therefore, observe the following safety instruc-
tions:
F1A-C Main fuses the main fuses F1A to F1C are used to secure the SAG-90 soft starter and the
main drive.
Fi01 Fault-current circuit breaker the residual-current circuit breaker Fi01 is located in front of
the fuse F4 and monitors the leakage currents across the earth in this circuit. The trip current is 30
mA.
Fi02 Fault-current protection switch the residual-current circuit-breaker Fi02 is located in front
of the fuses F6, F7 and F20 and monitors the leakage currents across the earth in this circuit. The trip-
ping current is 30 mA.
F4 Shaft light The F4 fuse protects the chimney lighting, the socket in the control panel, the socket
shaft pit and the socket carcass roof as standard with B 10A.
F5 Parking light & emergency power unit the fuse F5 secures the entire lighting circuit L5 with
the car lighting, the car fan and the emergency power unit with B 10A.
F6 Control fuse the control fuse F6 secures the entire circuit L6 for the processor system as well as
any additional power supply NG24 with B 10A.
F7 Safety circuit the fuse F7 secures the entire safety circuit with B 2A.
F20 Door drive the fuse F20 secures the 230V AC door drive with B 10A. The main switch Q1 acti-
vates the voltage supply of F20. An optional motor protection switch must be used for 400V door
drives.
S51 Pushbutton remote triggering of the sinking prevention If there is a VSG and a sinking
prevention is installed on the GB, this can be triggered with the pushbutton S51.
S53 Bridging the descent stopping system If a descent stopping system has triggered and
interrupted the SiKr, the SiKr can be closed with the S53 for the purpose of liberation.

KW Aufzugstechnik GmbH ASSEMBLY INSTRUCTIONS DAVID-613
DAVID-D613-Inbetriebnahme-V122-E 26.05.2020 Page - 8 -
S61 Service control The Service control allows the car to move in manual control characteristics
when bridging the SiKr-catching contact. The return switch includes the following functions:
Switch position
Function
0: Service control S61 OFF
Normal Operation active
1 and 2: Service control S61 ON
Switch ON the Service-Mode
UP: Service-drive UP S61A
Car-travel in UP-direction
DOWN: Service-drive DOWN
S61B
Car-travel in DOWN-direction
S20 Bypass-switch
The bypass switch enables the car to be moved with an open car
door or shaft door in the hand control characteristic of the EN81-20
/ 50 standard.
The switch is operated with a special tool (triangular door release)
The bypass switch has the following functions:
Switch position
Function
0: Bypass-Switch S20 OFF
Normal Operation active
Left: Bypass-Switch S20A
Driving the elevator car with the shaft door open (bridged)
Right: Bypass-Switch S20B
Driving the elevator car with the cabin door open (bridged)
Down: Bypass-Switch S20C
Travel of the elevator car with open locking device contacts
(optional)
S10 RESET-button on VSG &/ VSK
S10A Reset button on VSK (shortened pit brow)
If there is a VSK, you can reset it with the S10A button
be carried out with the shaft doors closed.
S10B Reset button on VSG (shortened shaft pit)
If there is a VSG, you can reset it with the S10B button
be carried out with the shaft doors closed.
Button shaft ligt S133
The S133 shaft button is used to switch the shaft light on and off. H21 shows the activated shaft light.
Maintenance switch S65
The maintenance switch S65 is used to switch on maintenance operation. H65 shows the activated main-
tenance mode.
Connection RS-232 for the HPG-60
The 9-pin D-Sub socket is used to connect the HPG-60, the universal programming device for KW elevator
technology.
Cabin light switch OFF S30
The cabin light switch off S30 is used to switch off the car light and initiate quiet driving with the aim of
switching off the controls and the cabin light.
Switch Control OFF S33
The switch control off from S33 is used to switch off the DAVID-613 processor unit.
Switch exterior controller S36
The switch exterior controller S36 dient zur Abschaltung der Außenrufe.
Button S50 remote Release / RESET
The S50 button is used to trip the coil of the remote release. This can only be done when the remote release
function is activated. Activation takes place in the TÜV menu C4. Please follow the instructions in the manual.

KW Aufzugstechnik GmbH ASSEMBLY INSTRUCTIONS DAVID-613
DAVID-D613-Inbetriebnahme-V122-E 26.05.2020 Page - 9 -
STEP 8
Preparing the Power Supply
Before connecting the main supply wire:
Switch main switch, all fuses, all switches off!
Attention! also with TÜV approval - insulation meas-
urement -> Switch off all switches and fuses!
STEP 9
Connection of the Power Supply-Wire
Attention! The mains supply may only be connected when the power is
disconnected!
Connect all 5 wires of the main line (L1, L2, L3, N & PE)
After applying the main voltage, check all phases (L1 / L2 / L3) against
"N"! The voltages must always be 230V AC!
If a rotary field measuring device should be available, please carry out the
measurement. The rotating field should always be a right-hand rotation
field!
STEP 10
Connection of the Shaft-Pitch-Box
If there is a sub-distribution with separate protection of the lighting circuit,
the lighting circuit must be connected as follows:
The connection may only be made when the power is off! The terminals
for the connection can be found on the X1-XP circuit board.
(Wiring diagram sheet 1 of 8).
Light voltage 230V AC
LL
Neutralleiter 0V AC
NL
Earth PE
PE
STEP 11
Connection of the Shaft-Top-Box X6
Danger! The SGS-92 pit box may only be connected when the power is
off!
The terminals for connection can be found on the circuit board X1, namely
X1 / 3, X1 / 4 and X1 / 5.
In addition, the pit bus cable (color gray / green) must be plugged into the
right RJ-45 connector on the BIS-80.
(Wiring diagram sheet 4 of 8 and Sheet 6 of 1).
STEP 12
Connection of the X7 pit brow box
The connection cable is to be led through the wall opening to the control
cabinet.
Attention! The pit brow box may only be connected when the power is off!
The terminal for the connection can be found on the circuit board X1,
namely X1 / 7
(Wiring diagram sheet 1 of 8)
STEP 13
Optional –Connection of the PTC thermistor
If the existing control device does not evaluate the PTC thermistor of
the motor, the motor PTC thermistor can be connected to module X1.
Danger! The PTC thermistor contact may only be connected when de-
energized! The terminal for connecting the PTC thermistor can be
found on the circuit board X1 /. (Circuit diagram sheet 1 of 8).
The terminals are 151 and 152

KW Aufzugstechnik GmbH ASSEMBLY INSTRUCTIONS DAVID-613
DAVID-D613-Inbetriebnahme-V122-E 26.05.2020 Page - 10 -
STEP 14
Optional - Connection of the Speed-Restrictor MR
If an engine room with speed restrictor (SR) is available, the SR
can also be connected directly to the X1 and not to the shaft
head box!
Attention! The connection may only be carried out in a voltage-
free state! The terminal for the connection of the speed restric-
tor in the machine room can be found on the circuit board X1 /,
(wiring diagram sheet 4 of 8). The terminals are 2 and 2B
STEP 15
Optional - Connection of the Emergency-Stop-Switch Mas-
chineroom/ Roperoom
For machine rooms with not completely covered rotating parts or Roperooms an addi-
tional emergency Stop switch must be installed!
Attention! The connection of the safety circuit contacts may only be carried out in the de-
energized state!
The terminal for connection of the emergency brake switch MR / RR can be found on the
circuit board X1 /, (wiring diagram sheet 4 of 8).
The terminals are 4R and 4S.
STEP 16
Optional –Connection of the Bolt-Contacts
If the shaft doors of the elevator system have a locking magnet or if additional mechanical
unlocking is required, the doors have a blocking agent contact!
Attention! The connection of the safety circuit contacts may only be carried out in the de-
energized state!
The terminal for the connection of the blocking-contact contacts can be found on the cir-
cuit board X1 /, (wiring diagram sheet 4 of 8).
The terminals are 6C and 7. In this case, no shaft door contacts must be con-
nected, only the blocking agent contacts !!!
STEP 17A
Hydraulic - Connection of the Motorwires 1 & 2
Attention! The connection of the motor cable must only be carried out in a voltage-
free state! The motor cable is already installed in the control unit as standard for all
KW controls. It is designed as a flexible cable. (Circuit diagram sheet 1 of 8).
Motorwire 1
1
phase U1
2
phase V1
3
phase W1
PE
Earth
Motorwire 2
1
phase W2
2
phase U2
3
phase V2
PE
Earth
STEP 18A
Hydraulic - Connection of the Releveling-Ag-
gregat
Attention! The connection of the motor cable must only be carried out in a voltage-
free state! The motor cable is already installed in the control unit as standard for all
KW controls. It is designed as a flexible cable. (Circuit diagram sheet 1 of 8).
Motorleitung
719
phase U1
720
phase V1
721
phase W1
PE
Earth
Ventilansteuerung
717
phase Releval-Valve Down
PE
Earth
718
N / Gem. Releval-Valve Down
STEP 19A
Hydraulic - Connection of the Oilcooler /
Connection of the Oilheating
Attention! The connection may only be carried out in a voltage-free state!
(Circuit diagram sheet 1 of 8).
Motorwire
Öilcooler
Thermostat
727
phase U1
728
phase V1
729
phase W1
PE
Earth
730
phase Thermostat ON
731
Neutral Thermostat ON
Wire
Oilheating
M12
phase
N
Neutral
PE
Earth

KW Aufzugstechnik GmbH ASSEMBLY INSTRUCTIONS DAVID-613
DAVID-D613-Inbetriebnahme-V122-E 26.05.2020 Page - 11 -
STEP 20A
Hydraulic - Connection of the Valve-Wires
The connection of the valve line may only be carried out in a voltage-free state! The terminal for
the connection of the valves can be found on the terminal block X1 / (wiring diagram sheet 1 of
8). Check the valve voltage according to the rating plate and the data in the circuit diagram! For
DC voltage, Valves must be equipped with varistors!
BUCHER
LRV &
iValve
Valve-Wire 1
1
Valve UP
721
2
Valve UP Common
723
PE
Earth
PE
Valve-Wire 2
1
Valve DOWN
722
2
Valve DOWN Common
724
PE
Earth
PE
4-Ventilkopf, wie ALGI, Leistritz,
Blain, ...
Bei 3-Ventilkopf sind die ent-
sprechenden Adern zu brücken!
Valve Fast UP
721
Valve Slow UP
723
Valve Fast DOWN
722
Valve Slow DOWN
724
Common Connection
720
Earth
PE
STEP 21A
Hydraulic - Optional - Connection of the Lower- / Over-
preasure-Contacts of the Aggregat
In the case of controlled hydraulic blocks, the evaluation is usually carried out via the
control electronics - see wiring diagram page 1 of 8!
Attention! The connection of the low / high pressure contact may only be carried out in
the de-energized state (230V AC)!
The terminal for connection is located on the printed circuit board X1 /
(Wiring diagram sheet 4 of 8).
The terminals are 1F and 1G.
STEP 17B
Rope –Connection of the Brake-Coil-Wire(s)
Attention! The connection of the brake line may only be carried out in a voltage-free state! The
terminal for connection is located on circuit board X1 / (circuit diagram sheet 1 of 8).
Common Connection of the
brake coils
+ Brake coil pos. Voltage
721
- Brake coil 0V
720
Earth
PE
Separate Connection of the
brake coils (MRL)
+ 1. Brake coil pos. Voltage
721
+ 2. Brake coil pos. Voltage
722
-Brake coils 0V
720
Earth
PE
Check the brake voltage according to the brake type plate and the data in the wiring diagram!
Ensure proper interference of the magnet coil -> varistor, RC-erase, free-wheeling diode ....
STEP 18B
Rope –Connection of the Motor-Wire
Attention! The connection of the motor cable must only be carried out in a voltage-
free state!
The motor cable is already installed in the control unit as standard for all KW controls.
It is designed as a flexible cable. In the case of frequency-controlled systems, the ca-
ble is equipped with a CU shield, which must be placed in a metal fitting on the motor
clamping box. If there is no metal screw connection, the shield must be twisted and
connected to the PE terminal (Pig-tail shielding) and a metal screw connection must
be installed immediately!
STEP 19B
Mounting & Connection of the Brake-Resistor
Attention! The connection of the brake resistor may only be carried out in a voltage-
free state!
The brake resistor wire is already installed in the control system as standard for all
KW controllers. It is designed as a shielded cable. The screen must be connected to
the cable clamp. The cable must be shortened if necessary and should not be placed
in squiggles (EMC interference!).

KW Aufzugstechnik GmbH ASSEMBLY INSTRUCTIONS DAVID-613
DAVID-D613-Inbetriebnahme-V122-E 26.05.2020 Page - 12 -
STEP 20B
Optional- Connection external ventilation 1-phase
If the motor has a single-phase (230VAC) forced ventilation, connect it as
follows:
The connection may only be made when the power is off! The terminal for
the connection can be found on the circuit board X1-XP (circuit diagram
sheet 1 of 8)
External ventilation voltage 230V AC
M12
Neutralladder 0V AC
N
Earth PE
PE
Attention!
The distance between the pulse gen-
erator cable and the motor cable must
be at least 200 mm!
STEP 21B
Connection of the Encoder (Inverter)
at the GOLIATH-90
Attention! The connection of the pulse generator may only be carried out in a volt-
age-free state! Check whether the existing plug is compatible with the KW pulse
generator connection! If a pulse generator kit has been supplied by KW, then this is
checked and equipped with the corresponding 9-pin connector:
The following connections are available for asynchronous machines:
40
Shield –Earth-Potential
41
Encoder Channel A
42
Encoder Channel B
43
Encoder Channel A/
44
Encoder Channel B/
44
GND 0 V DC
26
Voltage V variable DC
Synchronous machines:
In most conventional synchronous machines
(gearless or geared, eg the companies Mon-
tanari, Ziehl-Abegg, Thyssen, Loher, Wittur-
SAD, ...), an absolute value encoder is used
to measure the actual speed as well as the
rotor angle for use. The interface is a 15-pin
Sub-D socket.
Pin/Term.
EnDAT Interface
1
DATA +(Data-Channell)
2
DATA –(Datta-Channel)
3
N.c. or +5V Sensor
4
+5V DC
5
OV GND
6
N.c.
7
B+ (Cos-Encoder-channel)
8
N.c.
Pin/Term.
BiSS-C Interface
1
DATA +(Data-Channell)
2
DATA –(Datta-Channel)
3
N.c. oder +5V Sensor
4
+5V DC
5
OV GND
6
N.c.
7
B+ (Cos- Encoder-channel)
8
N.c.
For a more detailed description, see the Manual GOLIATH-90!

KW Aufzugstechnik GmbH ASSEMBLY INSTRUCTIONS DAVID-613
DAVID-D613-Inbetriebnahme-V122-E 26.05.2020 Page - 13 -
STEP
22B
Rope -Connection of the exteral Encoder-System Solution
The mountingset of the SOLUTION-Encodersystem has the fol-
lowing components:
- SOLUTION-Encoder with 10meter wire and plug for GOLIATH-
60 inverters.
- Metal-screwstick with exact Mxx screw.
- Holder, constructed as a Z-spring with 3 pieces of M3 screws.
The encoder is tested inside of the company. Please handle it very
carefully!
The holder avoids a motion of the encoder during the motor is
running.
.
The encoder should not mounted very hard with motor-casing.
The Z-spring helps to reach a flexible fixing with the motor-casing
Screw the treaded rod into bore of drive shaft. All mandrels have
been tested on synchronization. Avoid knocking shaft jour-nals!
For Thyssen winds W149 is a spezial manrel type W149 availa-
ble.
For Kasper external rotor are extended mandrels available.
Pull very carefully the encoder only with your hand, without any
tool, on the screwstick and fix the mounting.
After that please fix the metalholder with the casing of the ma-
chine. The encoder should not move with the machine, but the
fixing must not so hard that vibrations make damages inside of
the encoder!

KW Aufzugstechnik GmbH ASSEMBLY INSTRUCTIONS DAVID-613
DAVID-D613-Inbetriebnahme-V122-E 26.05.2020 Page - 14 -
STEP 23
Connection of the Overloadmeasure-Switch
The terminal for connection is located on the PCB To-80
(Circuit diagram sheet 6 of 8).)
+24V DC Voltage
208
+24V or 0V DC Input Overloadmessage
63
0V DC GND
500
STEP 24
Connection of the Emerency-Power-Evacuation
Attention! The connection of the emergency power lines may only be carried out in the de-en-
ergized state (230V AC)! The terminals for connection are located on the PCB To-80
(Circuit diagram sheet 9 of 9)
230V AC Emergency-Power-Operation
401
230V AC Emergency-power-Travel
402
230V AC Switching of the emergency-Power-Travel
403
Neutralladder 0V AC
N
STEP 25
Connection of the Fire-Evacuation
Attention! The connection of the signal lines of the fire case may only be carried out in the de-
energized state (+ 24V DC)! The terminals for connection are located on the PCB To-80
(Circuit diagram sheet 9 of 9).
+24V DC Controller voltage
210
+24V DC Input Fire-Evacuation Priority-Floor 01
405
+24V DC Input Fire-Evacuation Priority-Floor 02
406
+24V DC Input Fire-Evacuation Priority-Floor 03 or RWA
407
STEP 26
Connection of the Input „Controller and Car-Light OFF“
Attention! The connection of the emergency line emergency line may only be carried out in the de-ener-
gized state (+ 24V DC)! The terminals for connection are located on the PCB To-80
(Circuit diagram sheet 9 of 9).
+24V DC Controller voltage
208
+24V DC Input „Controller and Car-Light OFF“
201
STEP 27
Connection of the potentialfree Messages
Alert-Message Closer NO.
30a
Alert-Message Common COM.
30b
Alert-Message Opener NC.
30c
General Error Message Closer NO.
31a
General Error Message Common COM.
31b
General Error Message Opener NC.
31c
Out of Order Message Closer NO.
32a
Out of Order Message Common COM.
32b
Out of Order Message Opener NC.
32c
Evacuation Message Closer NO.
33a
Evacuation Message Common COM.
33b
Evacuation Message Opener NC.
33c
STEP 28A
Connection of the Buswire for Remotestations ER-2013
The RJ45 terminal for the connection of the shaft bus can be found on the PCB To-80 (wiring
diagram sheet 6 of 8).
The 5A motor vehicle fuse limits the current on the shaft bus!
STEP 29
Connection of the Buswire for Remotestations ER-2014
The RJ45 terminal, as well as the two-pole power connector for connecting the shaft bus, can
be found on the circuit board To-80 (wiring diagram sheet 6 of 8).
STEP 30
Connection of the Buswire for Remotestations für ERG-
2018
The RJ45 terminal for connecting the shaft bus can be found on the far right on the To-80 cir-
cuit board (circuit diagram sheet 6 of 8 / column 1).
It is used for the bus connection of the floor computer for the shaft pit.

KW Aufzugstechnik GmbH ASSEMBLY INSTRUCTIONS DAVID-613
DAVID-D613-Inbetriebnahme-V122-E 26.05.2020 Page - 15 -
STEP 31
Connection of the Handheldterminals HPG-60 to the
Centralunit
The HPG60 can communicate with the microprocessor system in two places:
1.) On the central computer ZR (control cabinet)
2.) On the car computerr FKR (on the car roof)
The control parameters can be changed by pressing the LEFT & LOWER red but-
tons simultaneously. Press again -> jump back to the control.
STEP 32
Communikation of the KW IPhone-App with the con-
troller
The HPG app is the universal programming and parameterization interface for the
complete control and regulation system of the DAVID-613.
All parameters can be viewed and changed. Permanent status messages on the
display indicate the current actions of the control system. Calls and other actions can
also be given via the app.
Controls, such as the GOLIATH-90 frequency inverter series, or SAG-90 softstart-
unit can also be parameterized and queried via this app.
STEP 33
Navigation with the Handheldterminal HPG-60
The HPG60 hand-held programmer is the universal input and output device for the
complete control and regulation system. It has 6 buttons, a four-line LCD display, a
red light-emitting diode, as well as a 9-pin RS232 interface.
With the HPG60 all parameters can be viewed and changed. Permanent status
messages on the display indicate the current actions of the control system. All col-
lected errors can be viewed in the error memory.
Calls can also be given via the hand-held programming device.
STEP 34
Conection of the KW-Mounting-Handheldbox / Aktiva-
tion of the Assembly-Drive
Attention! The connection of the mounting Handheldbox may only be carried out in
a voltage-free state!
When mounting without suspension cables and inspection boxes, it is possible to
disconnect the return pear connection and connect a mounting Handheldbox.
The plug & socket of the return control is located in the control cabinet at the bot-
tom left.
This connection must be disconnected and the KW mounting bulb should be con-
nected instead.
In the submenu C7, point C70 assembly travel, these parameters can be activated
with active return control.
When installing an elevator system, the safety circuit switches are not set at the
beginning. This function, although the safety inputs U3 to U12 are without voltage,
permits a travel movement with the restoring control. The prerequisite is that voltage
is applied to U1 and U2.
This is achieved automatically by using a KW mounting bulb.
Attention! Observe national and company internal safety regulations!

KW Aufzugstechnik GmbH ASSEMBLY INSTRUCTIONS DAVID-613
DAVID-D613-Inbetriebnahme-V122-E 26.05.2020 Page - 16 -
STEP 35
Installation of the SGS92 shaft pit
Attention!
The pit may only be entered if it is longer than 15 minutes if the
car is fixed with a support!
The shaft pit is to be installed at a height of 2.0 m. The grip area should be
approx. 0.75m!
STEP 36
Connection of the shaft pit terminal box
The pit pit terminal box is as-
sembled as standard with three
multi-pin plugs and is plugged
into the control cabinet on the
circuit board X1 / 3, X1 / 4 & X1
/ 5 to the left of the hanging ca-
bles. In addition, the bus cable
gray is plugged into the BIS-80.
Safety circuit switches that are
not present are bridged in the
terminals
STEP 37
Connection of the shaft lighting socket strip SDL-92 in
the pit box
Attention! The socket strip for the shaft lighting may only be connected when the power is off!
Fuse F4 -> OFF! The clamp for connecting the shaft lighting can be found on the circuit board
X6 / (circuit diagram sheet 3 of 8).
Shaft lighting
phase 230V AC
L42
Earth
PE
Neutral
N4
STEP37B
Connection of the LED shaft lighting type 3
The assembly of the plug
socket strip as in the pic-
ture on the left!
Up to 4 shaft lighting
strings can be connected.
Plugs & cables are strain
relieved with cable ties.
STEP 38
Connection of the tape break switch (ELGO-LIMAX-Safe)
or 2nd emergency brake switch S1B
When using the Limax Safe system, the tape break switch must be connected here. If
the pit is very deep or there is a second shaft door access, a second emergency
brake switch is required! The terminal can be found on the X6 / (wiring diagram 4/8).
The terminals are 1A and 1B.
STEP 39
Connection of the pit door / pit ladder contact S1C
Danger! The pit door contact may only be connected when de-energized (230V AC)!
The terminal for the connection can be found on the pit pit box X6 / (wiring diagram
sheet 4 of 8). If there is no contact, please bridge terminals. The terminals are 1B
and 1C.

KW Aufzugstechnik GmbH ASSEMBLY INSTRUCTIONS DAVID-613
DAVID-D613-Inbetriebnahme-V122-E 26.05.2020 Page - 17 -
STEP 40
Connection of the Restrictor-Weight-Contact S1D
(Rope)
Attention! The connection of the regulator voltage contact must only be carried out
in a voltage-free state (230V AC)!
The terminal for connection is located on the shaft pit box X6 / (wiring diagram
sheet 4 of 8). Since a hydraulic system usually has no regulator weight,
please bridge the jumper.
The Terminals are 1C and 1D.
STEP 41
Connection of the Burstpipe-Contact S1E (Hydraulic)
Attention! The connection of the tube break contact must only be carried out in a
voltage-free state (230V AC)!
The terminal for connection is located on the shaft pit box X6 / (wiring diagram
sheet 4 of 8). For cable systems, please bridge the terminals.
The Terminals are 1D and 1E.
STEP 42
Connection of the Emergency-End-Switch Bottom S2E
Attention! The connection of the emergency stop switch must only be carried out in
a voltage-free state (230V AC)!
The terminal for connection is located on the shaft pit box X6 / (wiring diagram
sheet 4 of 8). Since a hydraulic system usually has no emergency limit
switch, please bridge the jumper.
The Terminals are 2D and 2E.
STEP 43
Mounting of the Emergency-End-Switch Bottom
The mechanical roller switches are mounted on the rail brackets, which in turn
are attached to the rails with the enclosed claws. The switching curve must be
attached to the cabin in such a way that the emergency limit switches can be
operated safely.
STEP 44
Connection of the Buffer Contact for Cabin and Coun-
terweight S2F & S2G
Attention! The connection of the buffer contacts must only be carried out in the de-
energized state.
The terminal for connection is located on the shaft pit box X6 / (wiring diagram
sheet 4 of 8).
If not present, please provide bridges with terminals!!
S2F Buffer Contact Cabin
X6/ 2E & 2F
S2G Buffer Contact Counterweight
X6/ 2F & 2G
STEP 45
Connection of the Shaft-Door-Contacts S7.1 –S7n
Attention! The connection of the safety circuit contacts may only be carried out in
the de-energized state! The terminals for the connection of the shaft door contacts
can be found on the circuit board X6 /, (wiring diagram sheet 4 of 8 / columns 7-
8).
The terminals are 5A and 5B / 5B and 6.
If only one door is available, please connect terminals 5B and 6!

KW Aufzugstechnik GmbH ASSEMBLY INSTRUCTIONS DAVID-613
DAVID-D613-Inbetriebnahme-V122-E 26.05.2020 Page - 18 -
STEP 46
Schematic diagram- reduced pit
Reduced head
Functional Flow –Reduced shaft pit
Pos
activity
1
Opening the bottom landing door
➔Shelter shows RED
2
Press the emergency brake switch
3
Press the shaft light button
4
Anchoring the pit ladder
5
Erect the service support under the cab
➔Temporary shelter made
➔Shelter shows GREEN
... Further activities according to action plan
Assembly Effort - Reduced shaft pit
Pos
Component / switch
clamp
1
Assembly maintenance support cab
2
Connection NC contact for SiKr.
Maintenance support cabin in X6
3L & 3M
3
Connection NO contact for
Maintenance support cabin in X6
4L & 4M
4
Connection NO contact for traffic light
Maintenance support cabin in X6-XP
5L & 5M
5
Mounting shelter lamp pit
6
Connection in Schachtbox X6-XP
GR-500-GG
Functional flow –Reduced pit brow
Pos
activity
1
Opening the bottom landing door
2
Actuation of the emergency brake switch
3
Actuation of the Shaft light switch
4
Anchoring the pit ladder
5
Erecting the maintenance support Counterweight
➔Temporary shelter cabin made
6
Leaving the pit by reversing the
Measures mine tail ladder & emergency brake
switch
7
Open the corresponding landing door to access the
cabin
Reach the roof
➔Shelter shows GREEN
8
Actuation of the emergency brake switch
9
Erecting the cabin folding railing
10
Switching on the inspection switch
➔Inspection operation possible!
Assembly Effort -Reduced pit brow
Pos
Component / switch
clamp
1
Mounting service support Counter-
weight
Connection NC contact for SiKr.
Maintenance support cab at X6
3M & 3N
Connection NO contact for SiKr.
Maintenance support cab at X6
4M & 4N
2
Connection NO contact Mainte-
nance support Counterweight
5M & 5N
4
Mounting of the protective room
lamp Kabi-roof
5
Connecting the traffic light in the in-
spection box to X11-SRA
KR-500-KG
6
Assembly of the folding railing cabin
7
Connection NC contacts for SiKr.
Folding railing 1 & 2 at X11
3F & 3G
3G & 3H
8
Connection normally open contacts
for SiKr. Fold railings 1 & 2 to X11
4F & 4G
4G & 4H

KW Aufzugstechnik GmbH ASSEMBLY INSTRUCTIONS DAVID-613
DAVID-D613-Inbetriebnahme-V122-E 26.05.2020 Page - 19 -
STEP 47
Connection of the door release contacts S9.1 of the lowest
shaft door
Attention! The door unlocking contacts may only be connected when de-energized!
The terminals for connecting the door release contacts can be found on ERG-2018 (cir-
cuit diagram sheet 6 of 8 / column 1-2).
The terminals are 9.1 and 9.1.
STEP 48
Connection of the reset key switch at the bottom shaft door
Attention! The reset button may only be connected when the power is off!
The terminals for connecting the door release contacts can be found on ERG-2018 (cir-
cuit diagram sheet 6 of 8 / column 1-2).
The terminals are 200 and 68R.
The red button is used to reset when locked in the pit!
STEP 49
Connection of Si-Kr. Folding support cabin S3M / S4M RSP
Attention! The safety circuit contacts may only be connected when the power is off!
The terminals for connecting the maintenance folding jack switch in the case of a short-
ened pit are on the X6 /, (wiring diagram sheet 4 of 8 / column 5-6).
Terminals: 3L and 3M (normally open ), as well as 4L and 4M
(normally closed).
If not available, please bridge the terminals!
STEP 50
Connection of the normally open contact folding support
cabin VSG for the traffic light H21
Attention! The normally open contact may only be connected when the power is off!
The clamps for connecting the closer of the maintenance folding support in the case of a
shortened shaft pit can be found on ERG-2018, (circuit diagram sheet 5 of 8 / column 5-
6).
The terminals are 5L and 5M.
STEP 51
Installation of the H21 protective area traffic at RSP
Attention! The protective area traffic are installed in such a way that the view of the traffic
lights is guaranteed when the bottom shaft door is opened. If there is a through-loading in
the lowest stop, two protective area traffic must be installed.
STEP 52
Connection of the protective area traffic pit H21 with RSP
Attention! The connection may only be made when the power is off!
You can find the terminals for connecting the protective room traffic light pit in the case of
a shortened shaft pit on ERG-2018, (wiring diagram sheet 5 of 8 / column 6-8).
The terminals are GR-500-GG.
STEP 53
Connection of the Si-Kr. Folding support counterweight S3N
/ S4N VSK
Attention! The safety circuit contacts may only be connected when the power is off!
The terminals for connecting the maintenance jack support contacts with a shortened
shaft head can be found on the circuit board X6 /, (circuit diagram sheet 4 of 8 / column 5-
6).
Terminals: 3M and 3N (normally open), as well as 4M and 4N
(normally closed).
If not available, please bridge the terminals!
STEP 54
Connection of the normally open contact folding support
cabin VSG for the protective area traffic H22
Attention! The normally open contact may only be connected when the power is off!
The terminals for connecting the maintenance folding jack switch in the case of a short-
ened shaft pit can be found on ERG-2018, (wiring diagram sheet 5 v.8 / column 6-8).
The terminals are5M and 5N

KW Aufzugstechnik GmbH ASSEMBLY INSTRUCTIONS DAVID-613
DAVID-D613-Inbetriebnahme-V122-E 26.05.2020 Page - 20 -
STEP 55
Connection of the Shaft-Top-Box X7
The Shaft Top Box is standardized with a 9-pin plug and is plugged into the control box on the
printed circuit board X1 / 7 to the right of the hanging cable. The plugging may only be carried out in
the de-energized state. The terminal box has the clamping pads for the following switches / compo-
nents:
S2A Speed Restrictor Cabine
X7/ 2 & 2A
S2B Speed Restrictor Counterweight
X7/ 2A & 2B
S2C Emergency-End-Switch –1 Top
X7/ 2B & 2C
S2D Emergency-End-Switch –1 Top
X7/ 2C & 2D
Y61 Remote-Control Speed Restrictor Cabine
X7/ 761 & 760
Y62 RESET Remote-Control Speed Restrictor Cabine
X7/ 762 & 760
Y63 Remote-Control Speed Restrictor Counterweight
X7/ 763 & 760
Y64 RESET Remote-Control Speed Restrictor Count
X7/ 764 & 760
Non-existent safety circuit breakers are jumpered in the terminals
STEP 56
Connection of the Speed-Restrictor-Contacts
for Cabin and Counterweight
Attention! The speed restrictor contact must only be connected in a voltage-free state.
The terminal for connection is located on the shaft header box X7 / (wiring diagram sheet 4 of 8).
S2A Speed Restrictor Cabin
X7/ 2 & 2A
S2B Speed Restrictor Counterweight
X7/ 2A & 2B
STEP 57
Connection of the Distance-Limiter-
/Emergency-End-Switch Top 1 & 2
Attention! The connection of the stroke limiting / emergency limit switch may only be carried out in a voltage-free
state (230V AC)!
The terminal for connection is located on the shaft header box X7 / (wiring diagram sheet 4 of 8).
A second emergency stop switch is required for hydraulic double piston systems. If not available, please bridge!
S2C Emergency-End-Switch –1 Top
X7/ 2B & 2C
S2D Emergency-End-Switch –2 Top
X7/ 2C & 2D
STEP 58
Mounting of Emergency-End-Switch Top
The mechanical roller switches are mounted on the rail brackets, which in turn are
attached to the rails with the enclosed claws. The switching curve must be attached to
the cabin in such a way that the emergency limit switches can be operated safely.
STEP 59
Connection of the Remote-Control &
RESET Speed-Restrictor Cabin
Attention! The connection of the remote control speed restrictor and the optional RESET
coil may only be carried out in the de-energized state!
The terminal for connection is located on the box header box X7 / (wiring
diagram sheet 3 of 8).
Y61 Remote-Control Speed Restrictor Cabine
X7/ 761 & 760
Y62 RESET Remote-Control Speed Restrictor Cabine
X7/ 762 & 760
STEP 60
Connection of the Remote-Control & RESET Speed-Restrictor
Counterweight
Attention! The connection of the remote control speed counterweight and the optional
RESET coil may only be carried out in the de-energized state!
The terminal for connection is located on the box header box X7 / (wiring
diagram sheet 3 of 8).
Y63 Remote-Control Speed Restrictor Counterweight
X7/ 763 & 760
Y64 RESET Remote-Control Speed Restrictor Coun
X7/ 764 & 760
Other manuals for DAVID-613
1
Popular Computer Hardware manuals by other brands
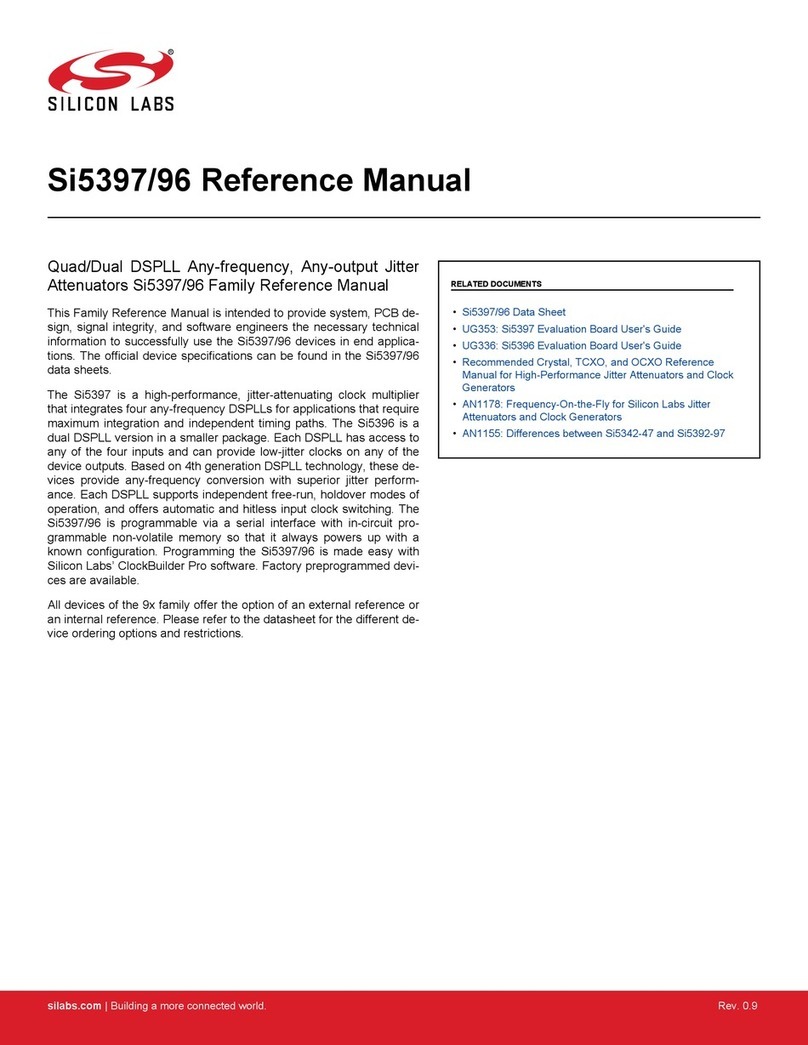
Silicon Laboratories
Silicon Laboratories Si5397 Series Reference manual
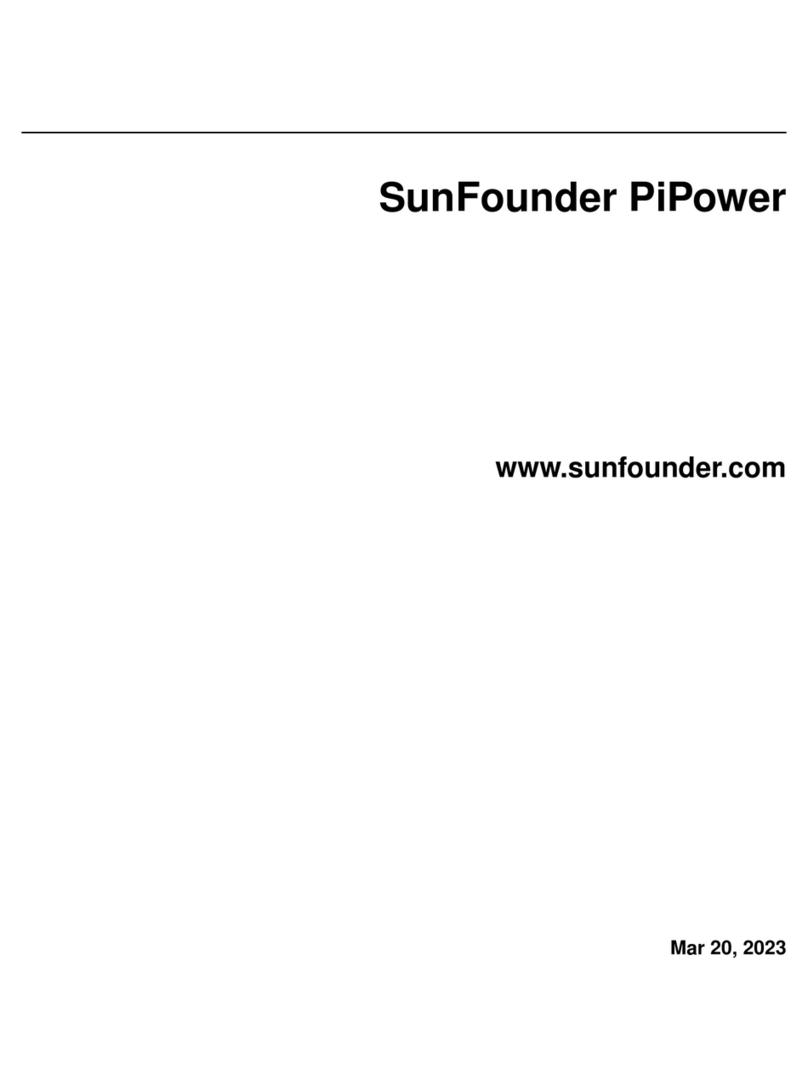
SunFounder
SunFounder PiPower instructions

IEI Technology
IEI Technology SPCIE-C2260 Quick installation guide
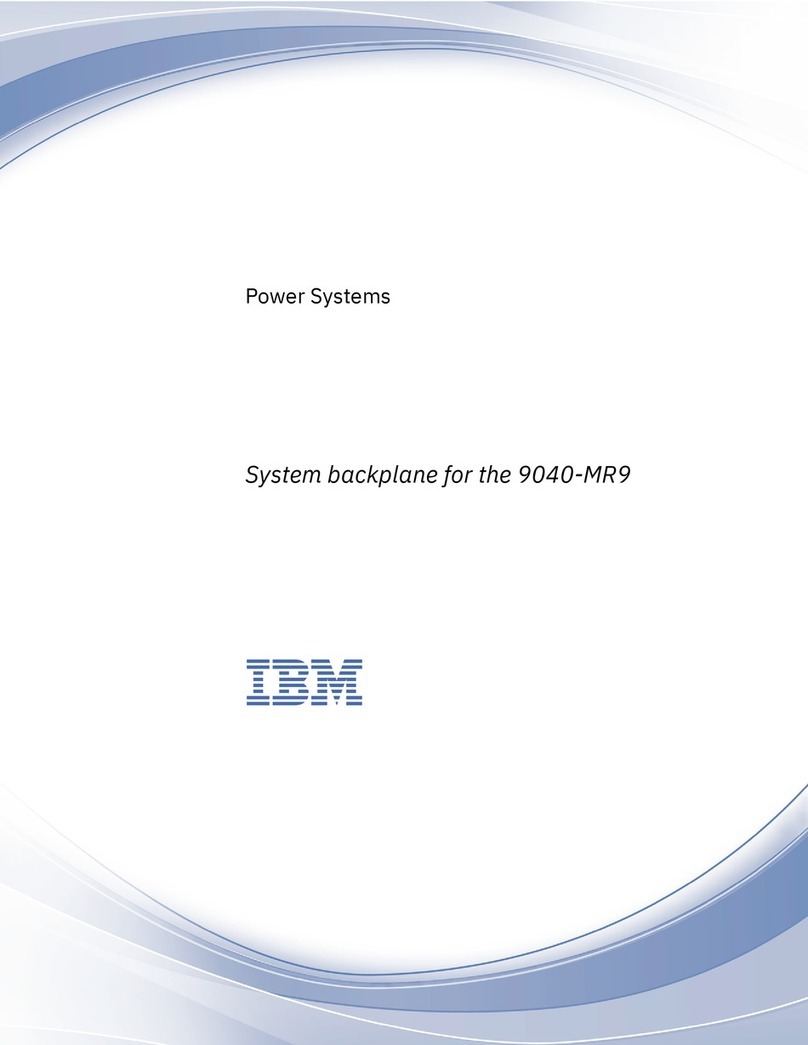
IBM
IBM 9040-MR9 manual
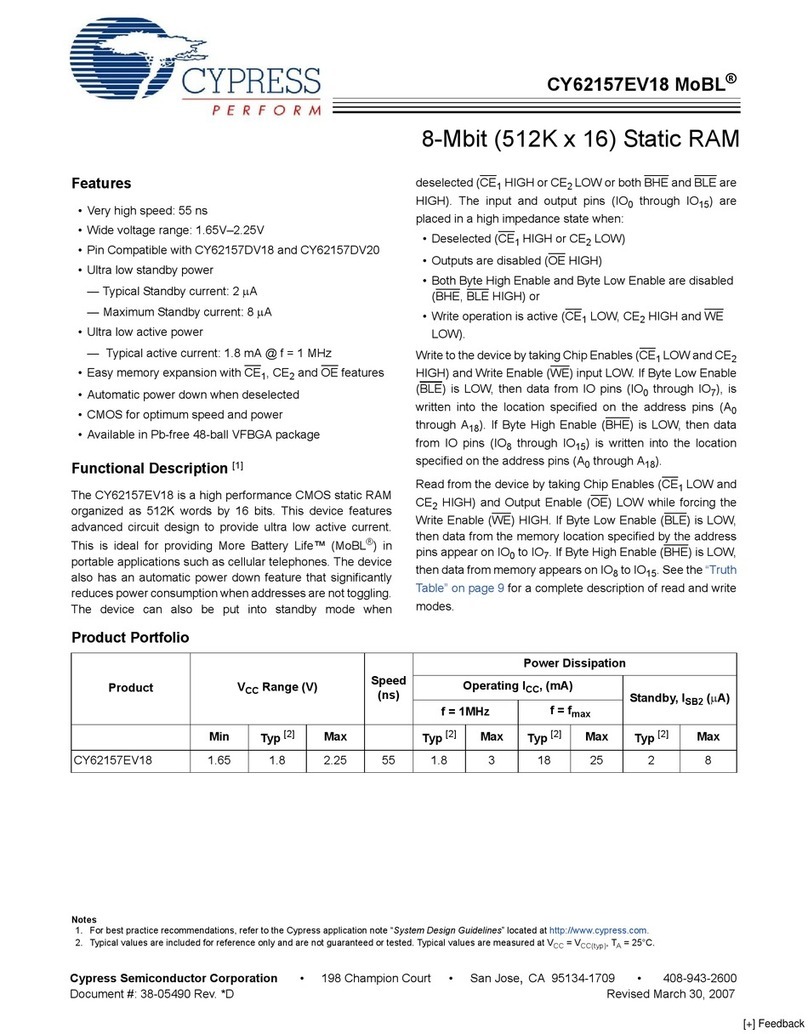
Cypress
Cypress CY62157EV18 Specification sheet

Thermo Scientific
Thermo Scientific Shandon Excelsior ES Operator's guide

ekwb
ekwb EK-FB GA X299 GAMING Monoblock installation manual
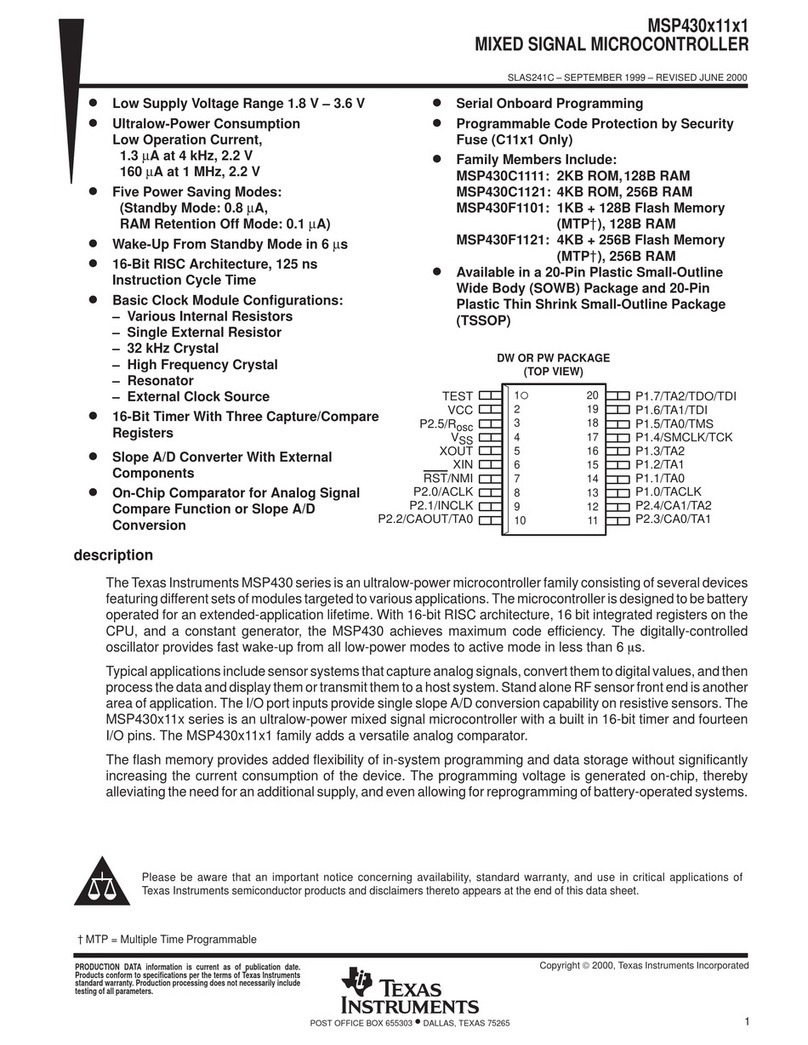
Texas Instruments
Texas Instruments MSP430x11x1 Specification sheet
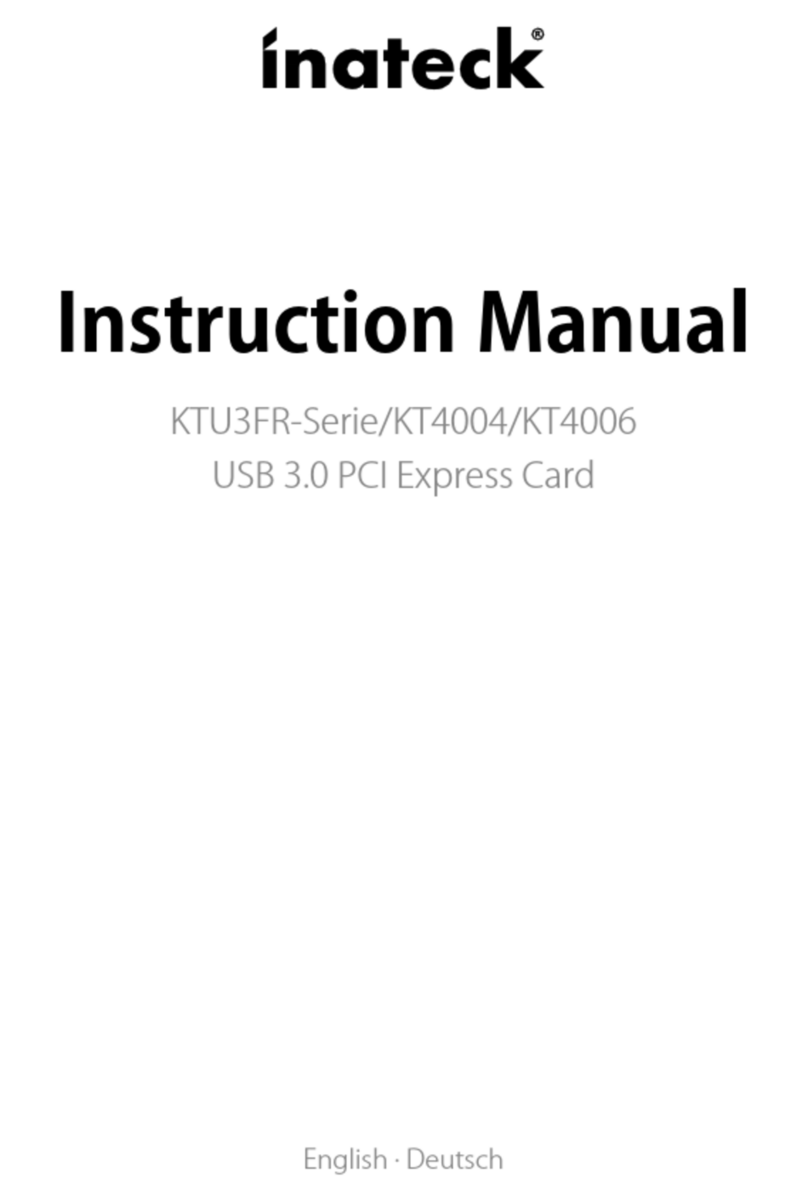
Inateck
Inateck KTU3FR Series instruction manual
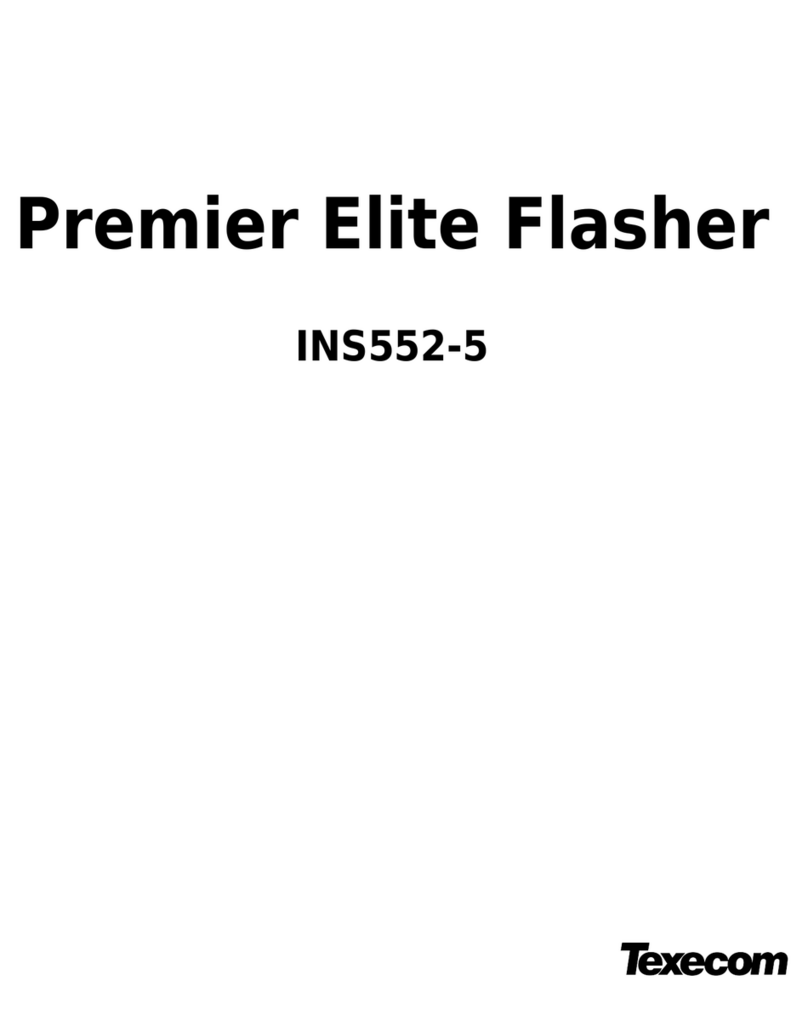
Texecom
Texecom Premier Elite Flasher quick start guide
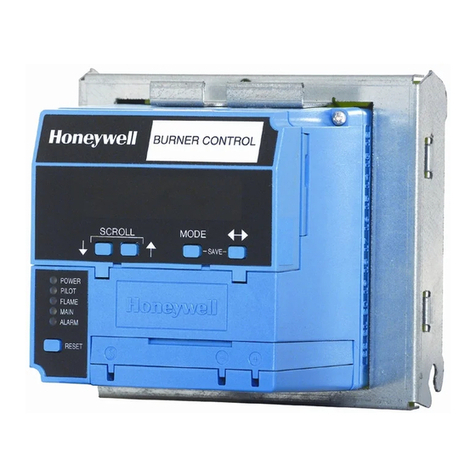
Honeywell
Honeywell RM7895 Series Wiring diagrams
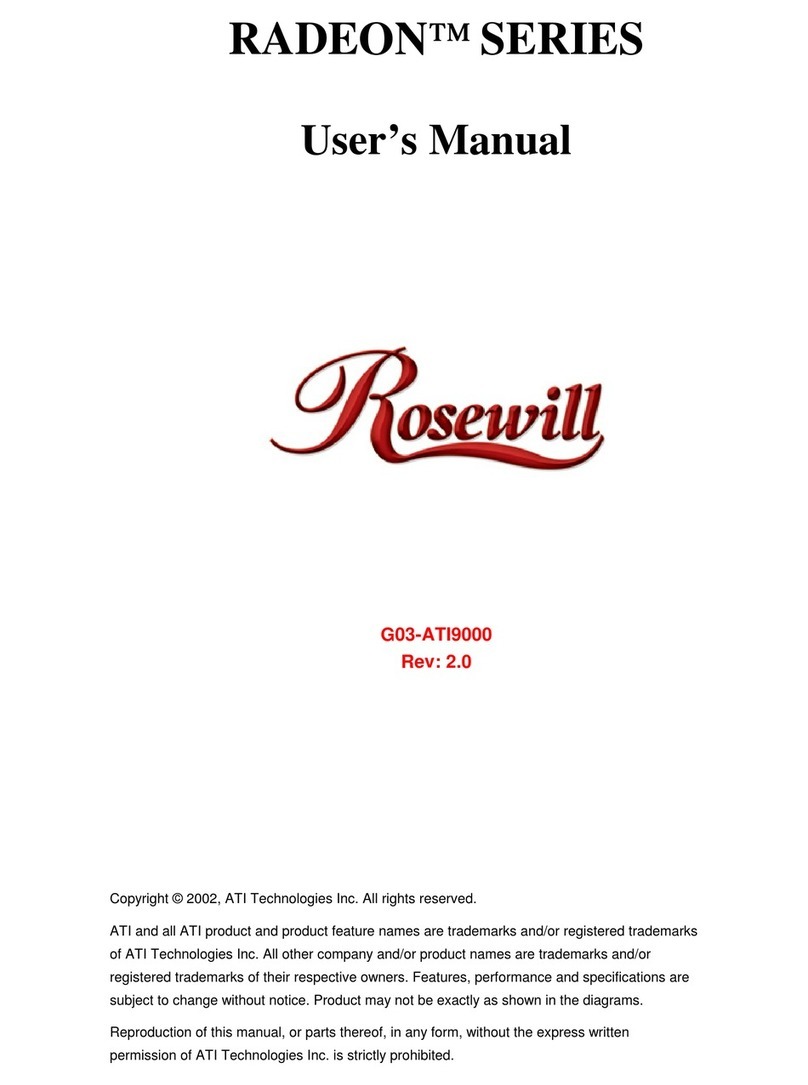
Rosewill
Rosewill RADEON G03-ATI9000 user manual