LabelMill LM3612 User manual

LM3612
PRINT & APPLY
OPERATIONS MANUAL
Manufactured in USA by:
LabelMill, Inc.
2416 Jackson St.
Savanna, IL 61074
(800) 273-4707
info@labelmill.com
www.labelmill.com

LM3612 PRINT & APPLY SYSTEM
USERS MANUAL
Page 2Made in the U.S.A.
© 2021 LabelMill
06/01/2021 Model LM3612
TABLE OF CONTENTS
SECTION
PAGE
1. APPLICATOR OVERVIEW
Introduction
1-01
General System Specifications
1-02
Inventory List
1-03
Print & Apply Component Description
1-04
User Responsibility
1-05
Safety
1-05
2. SETUP AND OPERATION
Web Routing
2-01
Thermal Print Head Label Loading
2-03
Thermal Ribbon Loading
2-03
Label Sensor Adjustment
2-03
Take Up Unit Assembly
2-04
Clutch Assembly Adjustment
2-05
Hand Held Labeler Interface HLI-200
2-06
Accessory Connections Control Box
2-07
T-52 Photo Eye
2-08
Air Assist
2-09
T-150 Mounting Stand
2-10
T-Stand Adjustments
2-11
Tamp Operation
2-12
Valve Pack / Regulator Adjustments
2-13
Optional Applicator Modules
2-14
3. CONTROL BOX
Programming
3-01
System Editor
3-02
Programming Menus
3-03
Key Definitions
3-05
Set Up Of Key Features
3-06
Logic Board / Description of I/O
3-08
E-Stop Connection
3-12
4. CLEANING & MAINTENANCE
Troubleshooting
4-01
Fault Codes
4-02
Replacing Main Power Fuse
4-03

LM3612 PRINT & APPLY SYSTEM
USER’S MANUAL
Page 3Made in the U.S.A.
© 2021 LabelMill
06/01/2021 Model LM3612
SECTION 1
APPLICATOR OVERVIEW
Introduction
1-01
General System Specifications
1-02
Inventory List
1-03
Print & Apply Component Description
1-04
User Responsibility
1-05
Safety
1-05

LM3612 PRINT & APPLY SYSTEM
USERS MANUAL
Page 4Made in the U.S.A.
© 2021 LabelMill
06/01/2021 Model LM3612
LABELMILL LM3612
THERMAL PRINTER/APPLICATOR SYSTEM
INTRODUCTION
The LabelMill LM3612 is a state of the art THERMAL PRINTER & APPLICATOR SYSTEM
created with maximum flexibility for your AUTOMATIC LABELING NEEDS. The unit will print and
apply high quality labels and bar codes to your product at print speeds up to 14”/sec. and apply at
speeds up to 90 labels/min.
OPERATION
The standard configuration is External Computer Mode. The configuration allows label formats to
be sent to the standard Centronics Parallel Interface Port, or serial port, on the Printer/Applicator.
Once the format is downloaded to the Printer Job Buffer, the system LM3612 can print and apply as
normal. Standard industry label software packages can be used in conjunction with a PC to design
and load label design.
1-01

LM3612 PRINT & APPLY SYSTEM
USER’S MANUAL
Page 5Made in the U.S.A.
© 2021 LabelMill
06/01/2021 Model LM3612
SYSTEM SPECIFICATIONS
PRINT SPEED
Up to 14”/second and approx. 90 labels/min.
(Varies depending on label and product size.)
BAR CODES
Linear and Two-Dimensional Barcodes
BAR CODE RATIOS
1:2, 1:2.5, 1:3 or individually programmable bar code widths
HUMAN READABLE FONTS
OEM Standard Fonts, Firmware Support for Downloadable TrueType
Fonts, and Additional Fonts Available
LABEL ROLL CAPACITY
12” Max. outside diameter wound on a 3” diameter core. Die cut waste
removed with a minimum of 1/8” separation between labels in running
direction.
LABEL SIZE
Minimum: 0.625” wide x 0.50” long
Maximum: 6.6” wide x 39” long
MAXIMUM PRINT AREA
6.6” wide x 39” long
(Varies dependent upon system configuration)
LABEL PLACEMENT
ACCURACY
Up to + or - 1/32” (1mm) when labels are produced to specifications
and product handling is controlled.
PRINTING METHOD
Thermal Transfer or Direct Thermal
Right-Hand or Left-Hand
INTERFACE
Standard Centronics Parallel Port
Standard RS-232C Serial Port, Ethernet port, USB
INTERFACE SENSORS
Ribbon out
Product Sensor-Photo Eye-Limit Switch
PLC input
ELECTRICAL
115VAC/60 Hz-250 W idle, 600 W running.
AIR REQUIREMENT
80 psi/3 cfm
SIZE
23” T x 30” W x 23-3/8” D
ENVIRONMENT
Operating Temp. 50-95 F (10-35 C)
15-85% RH. non-condensing
WEIGHT
60 lb. Nominal (with U-Arms)
*Options available
1-02

LM3612 PRINT & APPLY SYSTEM
USERS MANUAL
Page 6Made in the U.S.A.
© 2021 LabelMill
06/01/2021 Model LM3612
INVENTORY LIST
QTY.
Description
1
Print & Apply Assembly
1
U-Arm Mount
1
Power Cord
1
Model 3612 Operators Manual (USB)
1
Extra Cardboard Ribbon Core
1
Product Switch (specified)
a. Manual Limit Switch (optional)
b. Photo Switch (optional)
TOOLS REQUIRED FOR ASSEMBLY
:
3/32” ALLEN WRENCH
¾” WRENCH
1-1/8” WRENCH
1-03

LM3612 PRINT & APPLY SYSTEM
USER’S MANUAL
Page 7Made in the U.S.A.
© 2021 LabelMill
06/01/2021 Model LM3612
COMPONENT
DESCRIPTION / LOCATION
1-04
THERMAL
PRINTER
WEB TAKE-UP
SPOOL
VALVE
PACK
LABEL SPOOL
SPOOL LOCK
U-ARM
TAMP CYLINDER
AIR FILTER/
REGULATOR
SWING AWAY
HINGE ASSEMBLY
BRAKE ARM
REED SWITCH
AIR ASSIST
TUBE
ALARM
STACK
TAMP PAD
ASSEMBLY

LM3612 PRINT & APPLY SYSTEM
USERS MANUAL
Page 8Made in the U.S.A.
© 2021 LabelMill
06/01/2021 Model LM3612
USER RESPONSIBILITY
This equipment will perform in conformity with the description thereof contained in this manual and accompanying labels
and / or inserts when installed, operated, maintained, and repaired in accordance with the instructions provided. This
equipment must be checked periodically. Defective equipment should not be used. Parts that are broken, missing, plainly
worn, distorted, or contaminated should be replaced immediately. Should such repair or replacement become necessary,
we recommend that a request for service advice be made.
This equipment or any of its parts should not be altered without the prior written approval of LabelMill. The user of this
equipment shall have the sole responsibility for any malfunctions which results from improper use, faulty maintenance,
damage, improper repair or alteration by anyone other than LabelMill. or a service facility designated by LabelMill.
SAFETY
Only qualified personnel should use this equipment.
Before installing, inspecting or servicing equipment, turn OFF all power and air controls at the source and lock out in
accordance with OSHA Standards.
Be sure all external electrically conductive parts are connected to a good electrical ground.
Never handle live electrical equipment with bare hands while standing in water, or while hands and feet are wet.
Dangerous electrical shock can result.
Whenever the equipment is unattended, turn off all control and power supply switches.
Keep equipment clean and in good operating condition. Promptly repair or replace all worn or damaged hoses, cables or
parts.
Do not make any repairs to equipment unless you are fully qualified.
This equipment contains fast moving parts, which may move without warning. Keep hands, loose hair and clothes clear of
machines at all times.
Never place hands or any other body parts under the label platen at any time.
This equipment uses compressed air. Proper care and maintenance must be taken when handling compressed air and its
components.
These precautions are further detailed and explained where specifically required in this manual.
! WARNING
READ AND UNDERSTAND THESE INSTRUCTIONS
Protect yourself and others. Be sure this information is read and understood by all operators.
ELECTRICAL SHOCK CAN KILL!
Do not touch live electrical parts with bare skin or work with gloves or wet clothing.
NOISE CAN DAMAGE HEARING!
Wear proper ear protection.
1-05

LM3612 PRINT & APPLY SYSTEM
USER’S MANUAL
Page 9Made in the U.S.A.
© 2021 LabelMill
06/01/2021 Model LM3612
SECTION 2
SETUP AND OPERATION
Web Routing
2-01
Thermal Print Head Label Loading
2-03
Thermal Ribbon Loading
2-03
Label Sensor Adjustment
2-03
Take Up Unit Assembly
2-04
Clutch Assembly Adjustment
2-05
Operator Interface (HLI-200)
2-06
Accessory Connector Panel
2-07
T-52 Photo Eye
2-08
Air Assist
2-09
T-150 Mobile Mounting Stand
2-10
T-Stand Adjustment
2-11
Tamp Operation
2-12
Valve Pack / Regulator Adjustments
2-13
Optional Tamp Module Configuration
2-14
Optional Corner-Wrap Module Configuration
2-15
Optional Adjacent Panel Module Configuration
2-16
Optional Blow-On Module Configuration
2-17
Optional Table-Top Configuration
2-18

LM3612 PRINT & APPLY SYSTEM
USERS MANUAL
Page 10 Made in the U.S.A.
© 2021 LabelMill
06/01/2021 Model LM3612
WEB ROUTING
(Right Hand Configuration Shown Below)
Step
Operation
1
Load web onto label storage spool (A) so it unloads in a clockwise direction.
2
Feed the web to the right around guide roller (B), to the left and around brake arm (C), to
the right of roller (D) and to the left and below roller guide (E).
3
Feed the web into the thermal printer.
4
Finish the process by loading the waste backing paper onto the web take up spool (F).
The take up spool rotates in a clockwise direction.
5
Adjust the (2) plastic web guide clips so the web is guided straight and even. Make sure
clips do not bind the web.
*For a detailed illustration of this procedure, see Figure 2-1 below.
FIGURE 2-1
2-01
SPOOL LOCK
A
B
C
D
E
F

LM3612 PRINT & APPLY SYSTEM
USER’S MANUAL
Page 11 Made in the U.S.A.
© 2021 LabelMill
06/01/2021 Model LM3612
SUPPLY SPOOL
SPOOL LOCK REMOVAL:
To remove the label storage spool, turn the spool lock counterclockwise until you reach a stop. The spool will now slide
off. To secure the spool, simply turn the spool lock clockwise until snug. DO NOT over tighten!
2-02
SPOOL LOCK

LM3612 PRINT & APPLY SYSTEM
USERS MANUAL
Page 12 Made in the U.S.A.
© 2021 LabelMill
06/01/2021 Model LM3612
LOADING THERMAL PRINT HEAD
REFER TO PRINTER MANUAL
LABEL & RIBBON ROUTING
REFER TO PRINTER MANUAL
THERMAL RIBBON LOADING
REFER TO PRINTER MANUAL
NOTE: The printer will not operate unless the front cover is in the fully closed position. For your continued
safety, do not override the front cover interlock switch.
LABEL SENSOR ADJUSTMENT
REFER TO PRINTER MANUAL
2-03

LM3612 PRINT & APPLY SYSTEM
USER’S MANUAL
Page 13 Made in the U.S.A.
© 2021 LabelMill
06/01/2021 Model LM3612
TAKE-UP UNIT ASSEMBLY
The Take-Up Assembly is located on the backside of the main panel. To adjust the clutch, the side
panels must be removed to gain access. The mounting bolts for the Take-Up Assembly can be found
directly behind the aluminum spool.
WARNING!!! Be sure power is off before performing any service.
2-04

LM3612 PRINT & APPLY SYSTEM
USERS MANUAL
Page 14 Made in the U.S.A.
© 2021 LabelMill
06/01/2021 Model LM3612
CLUTCH ADJUSTMENT
To reduce waste web tension, move the lock collar 1/32" away from the take-up spool. To increase
web tension, move the lock collar 1/32" toward the take-up spool.
CAUTION! Too much web tension may cause web breakage, label drifting, or premature failure of
the take-up spool assembly.
2-05
TAKE-UP
SPOOL
DC
MOTOR
LOCK
COLLAR

LM3612 PRINT & APPLY SYSTEM
USER’S MANUAL
Page 15 Made in the U.S.A.
© 2021 LabelMill
06/01/2021 Model LM3612
HAND HELD LABELER INTERFACE
HLI-200
2-06
TOUCH-SCREEN
DISPLAY
INTERFACE PORT

LM3612 PRINT & APPLY SYSTEM
USERS MANUAL
Page 16 Made in the U.S.A.
© 2021 LabelMill
06/01/2021 Model LM3612
ACCESSORY CONNECTIONS
LOCATED ON BACK OF LABELER CONTROL ENCLOSURE
2-07
MAIN POWER ENTRY
HLI-200 PORT
PRINTER INTERFACE
LOW LABEL & WARNING
LIGHT KIT / AUX
AUX 1 PORT
START INPUT /
REMOTE TRIGGER
TAKE-UP MOTOR
FUSE
HEAD UP /
AUX PORT
SOLENOIDS
POWER SWITCH
SMART TAMP /
PRE-PRINT
LOW LABEL & WARNING
LIGHT KIT / AUX
AUX 2 PORT
ENCODER
AUX
PORTS
AUX
PORTS

LM3612 PRINT & APPLY SYSTEM
USER’S MANUAL
Page 17 Made in the U.S.A.
© 2021 LabelMill
06/01/2021 Model LM3612
T-52 PHOTO EYE
(Remote Trigger)
***Refer to Section 3 for I/O details***
2-08

LM3612 PRINT & APPLY SYSTEM
USERS MANUAL
Page 18 Made in the U.S.A.
© 2021 LabelMill
06/01/2021 Model LM3612
AIR ASSIST TUBE
2-09
The Air Assist Tube must be adjusted to
clear the trailing edge of the printed labels
and the Label Platen. An adjustment
screw is used to adjust the position of the
air holes in relation to the labels. An angle
of 45 degrees is required.
One slot is provided to make the
appropriate adjustments desired.
Air Assist
Tube
Label Platen
Airflow
Mount
Bracket
Air
Assist
Tube
Clamp screw
Label
Platen
Valve Pack

LM3612 PRINT & APPLY SYSTEM
USER’S MANUAL
Page 19 Made in the U.S.A.
© 2021 LabelMill
06/01/2021 Model LM3612
OPTIONAL T-150 MOUNTING STAND
2-10

LM3612 PRINT & APPLY SYSTEM
USERS MANUAL
Page 20 Made in the U.S.A.
© 2021 LabelMill
06/01/2021 Model LM3612
T-STAND ADJUSTMENT
2-11
Column Crank
Column Lock
Table of contents
Popular Saw manuals by other brands
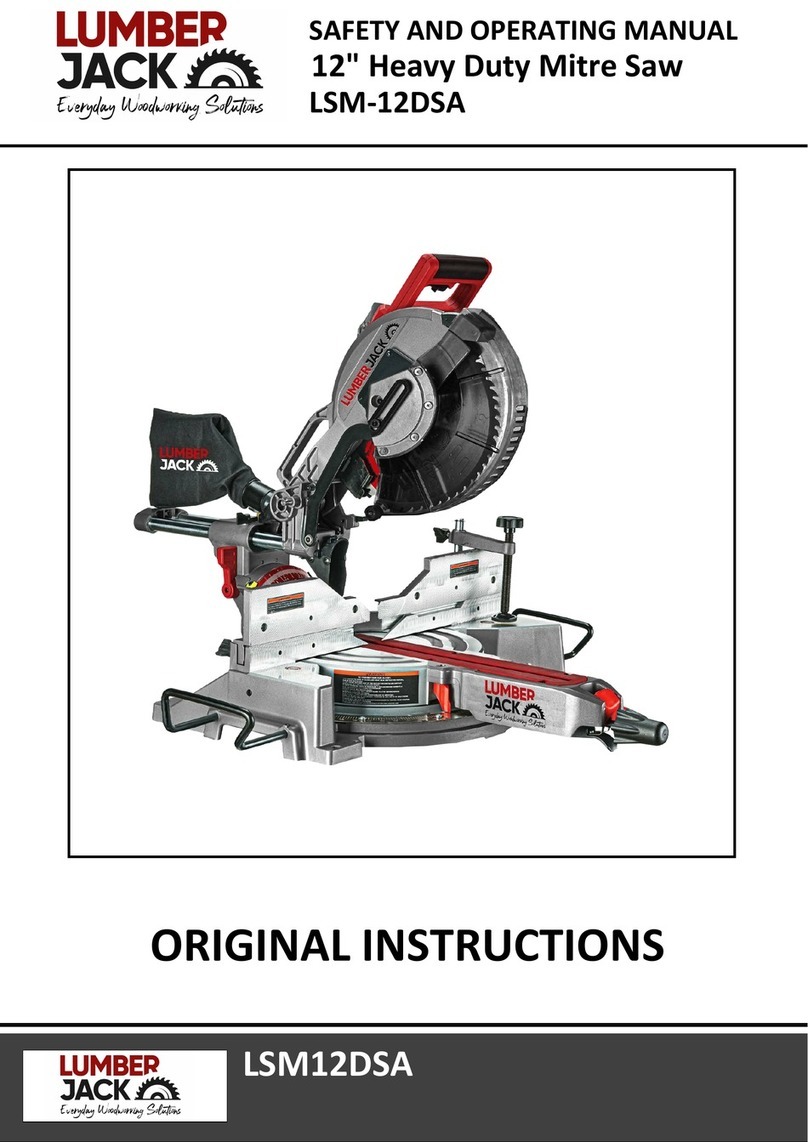
Lumberjack
Lumberjack LSM-12DSA Safety and operating manual
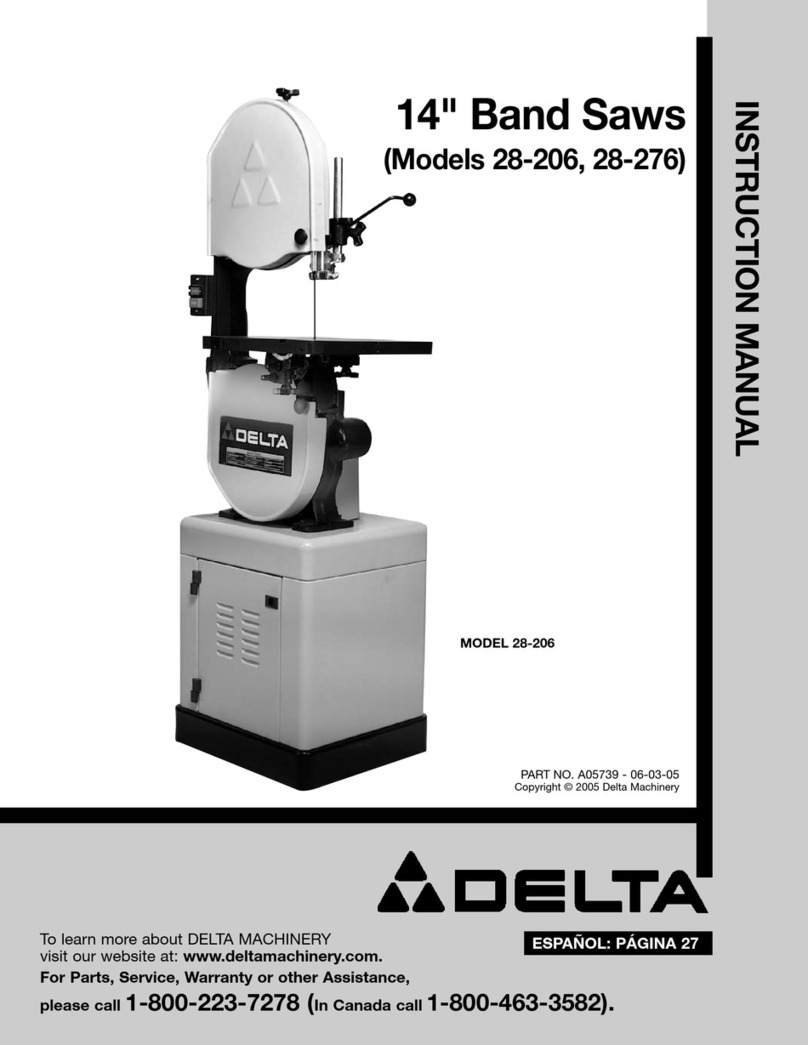
Delta
Delta 28-206 instruction manual
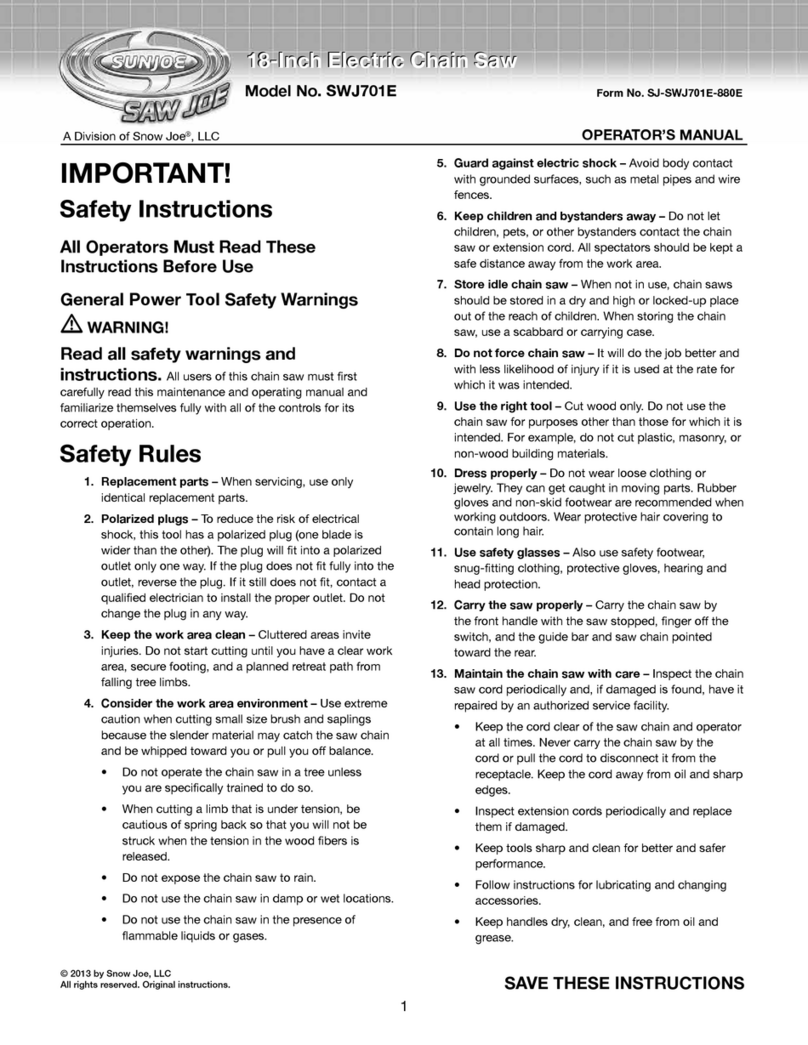
sunjoe
sunjoe SWJ701E Saw Joe Operator's manual

master mechanic
master mechanic 134455 owner's manual
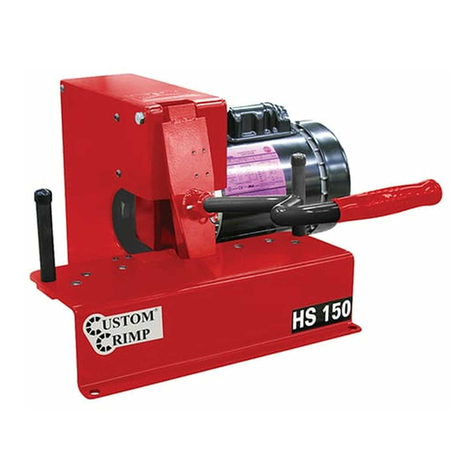
CustomCrimp
CustomCrimp HS-150 manual
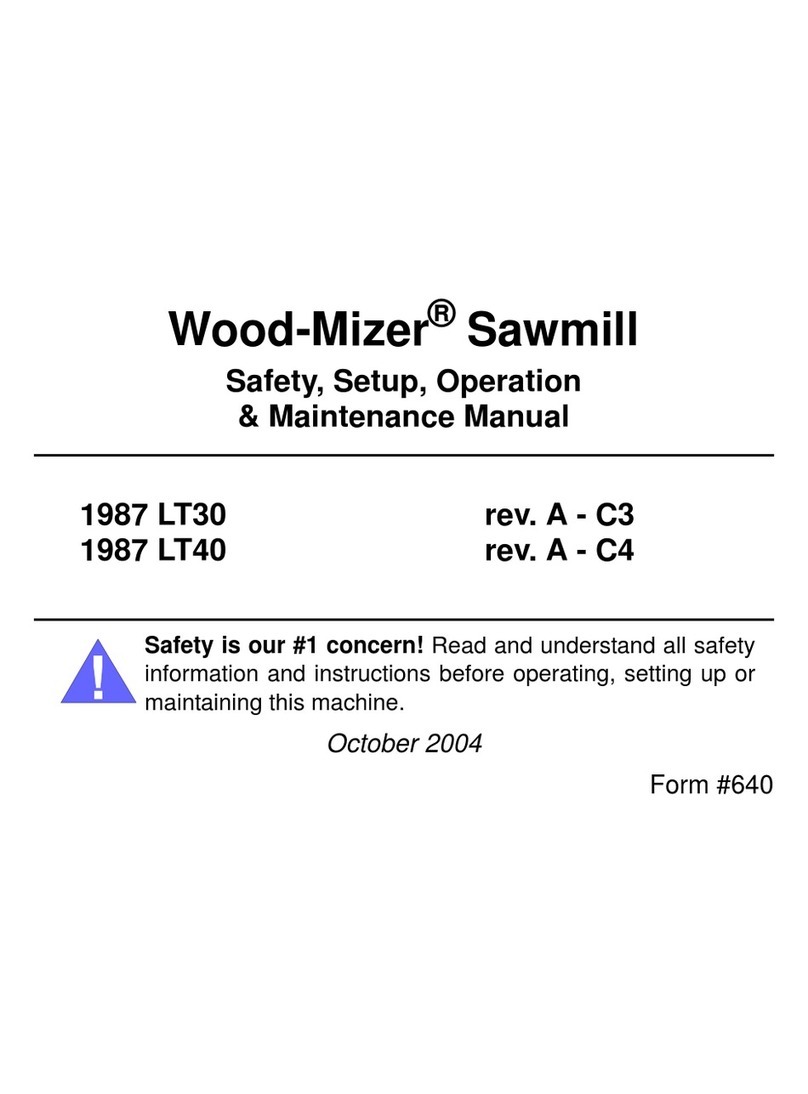
woodmizer
woodmizer 1987 LT30 Safety, Setup, Operation & Maintenance Manual