LaserMech FiberMINI 2.0 User manual

FiberMINI
® 2.0
With Auto Focus (AF) Operation Manual

PLMNL0286 REV. B, Effective Date: 06/06/19 iFiberMINI ®with Auto Focus (AF) Operation Manual
WARNING
WORKING AROUND HIGH-POWERED LASERS
CAN BE DANGEROUS
Laser Mechanisms, Inc.’s cutting heads must be
operated with the cutting head interlock switch
connected. The switch must be CLOSED when the
head is properly attached. In the event of a crash
and the cutting head becoming dislodged from its
normal operating position, the switch must be
OPEN. This interlock switch must be connected
in a circuit in such a way that it will immediately
turn off the laser and stop all machine motion.
Check the wiring diagrams for your system.
Serious personal injury and/or equipment
damage can occur if the head becomes
dislodged and:
The head interlock is not connected
properly.
Any interlock in the Laser Mechanisms’
product or laser system is defeated.
Laser Mechanisms, Inc. assumes no responsibility
or liability for interlock switches or circuits and all
interlocks are the sole responsibility of the purchaser
of this head.
It is the responsibility of the integrator or end user to
install, connect and activate all interlocks in
compliance with the applicable ANSI, CEN, DIN, etc.
standard.
All wiring should be done by personnel
knowledgeable in electrical wiring and in accordance
with the national and local electrical codes.
DISCLAIMER
The information in this manual is subject to change
without notice.
Laser Mechanisms, Inc. makes no warranty of any
kind with regard to the material in this manual,
including but not limited to, the warranties or
merchantability and fitness for a particular purpose.
Laser Mechanisms, Inc. shall not be liable for errors
contained herein or for incidental or consequential
damages in connection with furnishing, performance
or use of this product.
Laser Mech®is a registered trademark of Laser
Mechanisms, Inc.
Corporate names and trademarks stated herein are
the property of their respective companies.
COPYRIGHT
©2019 Laser Mechanisms, Inc. All rights reserved.
No part of this publication may be reproduced in any
form, or by any means without the prior written
permission of Laser Mechanisms, Inc.
PRODUCT WARRANTY
Laser Mechanisms, Inc. warrants this product
against defects in material and workmanship for a
period of one year from the date of shipment from
Laser Mechanisms Inc. or an authorized distributor.
During the warranty period, Laser Mechanisms, Inc.
will at its option, repair or replace products that
prove to be defective.
For all products returned to Laser Mechanisms, Inc.
for warranty service the customer must:
Call Laser Mechanisms, Inc. for a Return
Material Authorization (RMA) number.
Properly pack the product with the RMA number
on the outside of the package. Include in the
package, all cables, and all accessories shipped
with the product along with a description of the
problem.
Prepay shipping charges to Laser Mechanisms,
Inc.
Insure the shipment in case of loss or damage.
Laser Mechanisms, Inc. will not accept any
liability in case of damage or loss.
Laser Mechanisms, Inc. will pay the shipping
charges, duties and taxes for the products returned
to Laser Mechanisms, Inc. from outside the United
States.
The foregoing warranty will not apply if damage is
incurred resulting from improper or inadequate
maintenance by the customer, unauthorized
modifications or misuse, operation of the product
outside its specifications, interlocks not connected
properly, improper site preparation, parts or
assemblies not supplied by Laser Mechanisms, Inc.
or unauthorized repair by non-Laser Mechanisms,
Inc. authorized personnel.
For complete warranty information visit our web site
at www.lasermech.com.

PLMNL0286 REV. B, Effective Date: 06/06/19 ii FiberMINI ®with Auto Focus (AF) Operation Manual
INITIAL INSPECTION
Inspect all shipping containers for damage as soon
as the device arrives. It is your responsibility, the
recipient, to notify the freight company of any
damage. The freight company will require you to
provide the container that any goods were shipped
in, all shipping documentation and a list of all
damages. Photographs of the damage are helpful in
settling a freight claim.
Do not return damaged goods to the factory
without a Return Material Authorization Number
(RMA number).
Although it is Laser Mechanisms, Inc.’s intent to
insure you are up and running as soon as possible,
damage incurred during shipment must be settled
with the freight company before arranging for repairs
or replacement. No return shipments will be
accepted without an RMA number clearly printed on
the outside of all shipping containers. Failure to
follow this procedure could void any warranty
coverage on your head. Call your sales engineer at
Laser Mechanisms, Inc. for an RMA number.
Carefully remove the device from its shipping
container and all packing material to avoid damage.
Save all packaging material, including the sealed,
padded pelican case, in the event the head requires
shipping or storage.
Check all items received against the packing list
to verify that all the items were received.
Please note the product you receive may differ
slightly from the illustrations in this manual.
While the drawings may differ, the basic
procedures described within remain the same.
TERMS USED IN THIS MANUAL
WARNING: The user could be injured
if the warning is not followed.
CAUTION: The device or system
could be damaged if the CAUTION is
not followed.
NOTE: Clarification of a step or steps.
SAFETY
WARNINGS: Follow all warnings in this manual.
SAFETY GLASSES: Everyone in the area
where the laser is being used must wear laser
safety glasses designed for the laser being
used.
SECONDARY REFLECTIONS: Secondary
reflections are dangerous; never expose any
part of your body to a reflected laser beam.
INTERLOCKS: Interlocks are safety devices
and should never be defeated.
ADJUSTMENTS: Always turn off or put the
laser in standby before making any adjustments
to beam delivery components.
BEAM DUCT: Never open any component of
the beam duct while the laser is operating.
Always turn the laser off before servicing any
beam duct components.
MANUALS: Always read the instruction
manuals before attempting to install or make
adjustments to any beam delivery component.

PLMNL0286 REV. B, Effective Date: 06/06/19 iii FiberMINI ®with Auto Focus (AF) Operation Manual
Table of Contents
1Introduction ........................................................................................................................................................1
2Mechanical Installation and Operation ............................................................................................................2
2.1 Mounting ............................................................................................................................................. 2
2.2 Plumbing............................................................................................................................................. 2
2.3 Cable Bundling.................................................................................................................................... 4
2.4 Fiber Input Adapter............................................................................................................................. 4
2.4.1 Inserting the Fiber ............................................................................................................5
2.4.2 Adjusting the Fiber Input Adapter Orientation..................................................................5
2.5 Centering the Beam in the Tip Orifice Using the Beam Centering Camera....................................... 6
2.6 Centering the Beam in the Tip Orifice Manually................................................................................. 8
3Electrical Installation and Operation................................................................................................................9
3.1 Electrical Connections ........................................................................................................................ 9
3.1.1 Connections to the Head..................................................................................................9
3.1.2 Discrete I/O Control Box (PLCSA0081) ........................................................................ 10
3.1.3 DeviceNet Control Box (PLCSA0082)........................................................................... 11
3.1.4 Ethernet / IP Control Box (PLCSA0083)....................................................................... 12
3.1.5 Modbus TCP Control Box (PLCSA0084)...................................................................... 13
3.2 EtherNet/IP / Modbus TCP / DeviceNet Module (If Equipped)......................................................... 14
3.3 Step and Direction Inputs ................................................................................................................. 20
3.4 Electrical Grounding and Noise........................................................................................................ 21
3.5 Control Box Mounting ....................................................................................................................... 21
3.6 Control Box Indicator Lights.............................................................................................................. 22
3.7 Interface Signals............................................................................................................................... 23
3.8 Calibration Procedure....................................................................................................................... 24
3.9 Head Indicator Lights........................................................................................................................ 24

PLMNL0286 REV. B, Effective Date: 06/06/19 iv FiberMINI ®with Auto Focus (AF) Operation Manual
4FiberMINI®Monitor.......................................................................................................................................... 25
4.1 Installation......................................................................................................................................... 25
4.1.1 Downloading FiberMINI®Monitor Software................................................................... 25
4.1.2 Installing FiberMINI®Monitor Driver.............................................................................. 25
4.2 System Requirements ...................................................................................................................... 25
4.3 Connecting........................................................................................................................................ 26
4.4 Monitor.............................................................................................................................................. 26
4.5 FiberMINI®Monitor Settings ............................................................................................................. 29
4.5.1 Unlock Settings ............................................................................................................. 29
4.5.2 Temperatures................................................................................................................ 29
4.5.3 Positioning..................................................................................................................... 30
4.5.4 Height Sensor................................................................................................................ 30
4.5.5 IN POS Function ........................................................................................................... 31
4.5.6 AUX OUT Function........................................................................................................ 31
4.5.7 Tip Selection.................................................................................................................. 31
4.5.8 EtherNet/IP (If Equipped).............................................................................................. 32
4.5.9 DeviceNet (If Equipped)................................................................................................ 33
4.6 FiberMINI®Monitor System Identification Information...................................................................... 33
5Service.............................................................................................................................................................. 34
5.1 Cleaning the Outside of the Head..................................................................................................... 34
5.2 Servicing Gas Jet Tip........................................................................................................................ 34
5.3 Servicing the Cover Glass ................................................................................................................ 35
5.4 Servicing the Tip Retainer Assembly................................................................................................ 36
5.5 Servicing the Focus Lens Cartridge.................................................................................................. 38
5.6 Servicing the Collimator.................................................................................................................... 39
5.7 Servicing the Air Blast Nozzle........................................................................................................... 42
6Specifications.................................................................................................................................................. 43
7Troubleshooting.............................................................................................................................................. 44
8Recommended User-Serviceable Parts List................................................................................................. 45

PLMNL0286 REV. B, Effective Date: 06/06/19 1FiberMINI ®with Auto Focus (AF) Operation Manual
1 Introduction
FiberMINI®2.0 with Auto Focus (AF) is shown
in a straight configuration. See Figure 1. Other
configurations are available upon request. See
your Laser Mechanisms’Sales Engineer for
more information.
FiberMINI®AF is simple, yet flexible to optimize
the processing head and the end user’s fiber
laser. The head is capable of cutting a wide
range of materials.
Key Features
Compatible with all leading fiber-delivered
laser systems up to 4kW
Flexible design to optimize spot size
Capacitive height sensing
Up to14 mm automated focus lens
adjustment
Quick and easy access to the cover slide
Water and air cooling
Smooth assist gas flow
Quick and easy to service the focus lens
Thermal monitoring for the optics
Internal wiring and plumbing for gasses and
coolants
Compact, lightweight design
Fully sealed optical path
This manual explains the steps of installation,
setup, operation and service of the FiberMINI®
AF.
Figure 1

PLMNL0286 REV. B, Effective Date: 06/06/19 2FiberMINI ®with Auto Focus (AF) Operation Manual
2 Mechanical Installation and Operation
2.1 Mounting
The FiberMINI®AF has an integrated
mount plate with (2) mounting holes.
Figure 2 illustrates the hole pattern.
Figure 2
A
Focus Length
132.5 mm
125 mm
157.5 mm
150 mm
207.5 mm
200 mm
2.2 Plumbing
Water Cooling
FiberMINI®AF processing heads are
equipped with a water-cooling circuit.
Water-cooling is the recommendation
when power levels exceed 1kW.
Power level should never exceed
4kW.
See Figure 3 for location and hose
size. See the table below for
recommended specifications.
The design intent of the cooling circuit is to
operate on a closed-looped cooling
system or facility tap water –as long as it
meets the requirements in the table below.
Minimum Flow Rate
1.5 liter/minute @ 2 BAR min
Inlet Pressure
5.0 Bar (72.5 psi) Max
Inlet Temperature
≥room temperature / >dew point
Hardness
(Equivalent to
CaCO3)
<250mg/liter
pH
6 to 8
Particulate Size
<200 microns in diameter
Assist Gas
See Figure 3 for location and hose size.
Maximum pressure is 20 BAR.
Impurities in the assist gas such as
hydrocarbons (THC) and moisture (H2O)
can damage optics, cause power
fluctuations and result in inconsistent cuts.
See the table below for recommended
assist gas specifications.
GAS
PURITY
MAX H2O
MAX THC
Oxygen
99.8%
<5 ppm
<1 ppm
Nitrogen
99.998%
<5 ppm
<1 ppm
Argon
99.998%
<5 ppm
<1 ppm
Helium
99.998%
<5 ppm
<1 ppm

PLMNL0286 REV. B, Effective Date: 06/06/19 3FiberMINI ®with Auto Focus (AF) Operation Manual
The supply lines can also be a source of
impurities. Non-metallic materials can
allow oxygen and moisture to permeate
the system and can be a source of dust
and hydrocarbons. The recommendation
is stainless steel lines and fittings. Use
filters that remove particles down to .01
microns and purifiers that guard against oil
or water getting into the optical system.
The recommendation is regulators with a
stainless steel diaphragm. Industrial
regulators can aspirate air and the
neoprene diaphragm can be a source of
hydrocarbons.
Nozzle Air Cooling
See Figure 3 for location and hose size.
The air-cooling must be supplied with
clean, dry air {specification to meet or
exceed ISO 8573.1:2001 Class 2.4.2};
Solids <100,000 particles per cubic meter
of 0.1-0.5 µm size, <1000 particles per
cubic meter of 0.5-1.0 µm and <10
particles per cubic meter of 1-5 µm; Water
dew point <+3º C; Oil <0.1 mg per cubic
meter.
Air cooling pressure is 2.0 –3.5 Bar
(30.0 –50.0 psi).
Figure 3 shows the typical plumbing
arrangement for the FiberMINI®AF.
Figure 3

PLMNL0286 REV. B, Effective Date: 06/06/19 4FiberMINI ®with Auto Focus (AF) Operation Manual
2.3 Cable Bundling
The cables need to be bundled in a
manner allowing complete tool movement
without pinching or pulling of the cables.
The FiberMINI®AF head design orients all
cable inputs in the same direction –
allowing a sleek, easy-to-manage bundle.
Cabling should not be tethered to the fiber
input connector or the fiber optic cable.
The manner in which the
cables are bundled is one of
the keys to having a successful
cutting cell. The end user is
responsible for documenting
and training personnel on the
best bundling methods for their
application.
2.4 Fiber Input Adapter
The purpose of the fiber input adapter is to
provide an interface to connect the laser
fiber optic cable to the head. FiberMINI®
AF will adapt to most industrial fibers.
Each fiber type has a unique method
of securing it to the fiber input adapter.
Refer to the fiber manufacturer’s
information for specific instructions.
The head arrives with the adapter for
the requested fiber type.
See Figure 4.
Note that the clear aperture of
the head is 25 mm.
Figure 4

PLMNL0286 REV. B, Effective Date: 06/06/19 5FiberMINI ®with Auto Focus (AF) Operation Manual
2.4.1 Inserting the Fiber
It is the responsibility of the end user to
verify correct fiber type and installation
according to the manufacturer
specifications.
Take great care to ensure the
optics remain clean. Wipe any
excess debris from the head
according to Section 5.1 before
servicing.
The head is orientated with
vertical beam input. Whenever it
is possible, rotate the head to
HORIZONTAL to prevent debris
from falling onto the optics.
See Figure 5.
Figure 5
2.4.2 Adjusting the Fiber Input Adapter
Orientation
Many fiber optic cables have a key and
only fit into the fiber input adapter (FIA)
in one orientation. You can rotate the
FIA to match the orientation of the fiber
end and reduce twisting of the fiber optic
cable.
To reorient the FIA on the FiberMINI®
AF (see Figure 6):
1. Loosen, but do not remove, the M4
SHSS by 1/4 turn.
2. Loosen, but do not remove, the (4)
M4 clamping bolts by 1/4 turn.
3. Rotate the FIA clockwise to match
the orientation of the fiber optic
cable.
4. Once the FIA is orientated correctly
tighten the (4) M4 SHCS clamping
bolts and the M4 SHSS.
Figure 6

PLMNL0286 REV. B, Effective Date: 06/06/19 6FiberMINI ®with Auto Focus (AF) Operation Manual
2.5 Centering the Beam in the Tip
Orifice Using the Beam
Centering Camera
Beam centering in the tip orifice is
essential to any laser process. It is
the customer’s responsibility to
center the laser beam in the tip
orifice.
If desired, it is possible to perform this
procedure manually. In that case, see
Section 2.6.
The beam MUST be centered in the gas
jet tip.
Check beam alignment:
oDuring initial installation.
oAfter replacing the fiber.
oAfter replacing the collimator
optics.
oAfter replacing the focus lens.
Laser Mechanisms’ beam centering
camera (PLFXT0269) is used for tip
centering.
It shows the position of the red aiming
beam in the orifice of the gas jet tip.
The beam centering camera requires
a Windows computer with a USB port
and Plugable 250X Digital USB
Microscope software or equivalent.
1. Download and install the latest version
of Plugable 250X Digital USB
Microscope software to the
appropriate computer.
http://www.lasermech.com/productupdates
The Plugable.com website also
has the software available to
download and videos with more
details on the features and uses of
the microscope.
2. Verify the high power beam is
disabled.
3. Install a gas jet tip with a 2 mm or
larger orifice. See Section 5.2 for
more details.
4. Turn on the red aiming beam from the
fiber laser.
5. Connect the beam-centering camera
(PLFXT0269) to the computer using a
USB cable.
6. Open the Plugable 250X Digital USB
Microscope software.
7. Install the beam-centering camera
onto the tip assembly. See Figure 7.
Rotate the camera until it seats
fully against the tip retainer
assembly.
O-rings in the beam-centering
camera help keep it in place.
Figure 7

PLMNL0286 REV. B, Effective Date: 06/06/19 7FiberMINI ®with Auto Focus (AF) Operation Manual
8. Rotate the brightness knob and adjust
the camera to full brightness (see
Figure 7).
If it is too bright, rotate the
brightness knob slightly, to suit.
9. Rotate the camera focus knob
(see Figure 7) until the end of the gas
jet tip is in focus with a clear image.
See Figure 8.
You should be able to see tooling
marks on the end of the tip.
Figure 8
10. Move the focus lens to the center of
travel. See Section 4 for more details.
Do not look directly into the red
beam.
If the beam is not centered in the tip
orifice, proceed to step 11.
11. Use a 1/8 inch hex wrench to loosen
or tighten the (2) adjusting screws so
the beam is centered in the tip orifice.
See Figure 9.
Figure 9
The image on the screen should
be similar to Figure 10.
Figure 10
Beam is centered
It is sometimes helpful to rotate the
camera while it is seated against the tip
retainer assembly to confirm the beam
centering.

PLMNL0286 REV. B, Effective Date: 06/06/19 8FiberMINI ®with Auto Focus (AF) Operation Manual
2.6 Centering the Beam in the Tip
Orifice Manually
Beam centering in the tip orifice is
essential to any laser process. It is
the customer’s responsibility to
center the laser beam in the tip
orifice.
Visually locating the beam inside the
tip orifice can be difficult. Adequate
lighting and a magnifying glass are
highly recommended.
If desired, it is also possible to
perform this procedure using the
centering tool (PLFXT0269). In that
case, see Section 2.5.
The beam MUST be centered in the gas
jet tip.
Check beam alignment:
oDuring initial installation.
oAfter replacing the fiber.
oAfter replacing the collimator
optics.
oAfter replacing the focus lens.
To center the beam in the tip orifice
manually:
1. Verify that the high power beam is
disabled.
2. Install a gas jet tip with a 2 mm or
larger orifice. See Section 5.2 for
more details.
3. Put a piece of translucent tape on the
end of the gas jet tip.
4. Move the focus lens to the center of
travel. See Section 4 for more details.
5. Turn on the laser’s internal red
pointing beam and observe the
position of the beam on the tape.
Do not look directly into the red
beam.
If the beam is not centered in the tip
orifice, proceed to step 6.
6. Use a 1/8 inch hex wrench to loosen
or tighten the (2) adjusting screws so
the beam is centered in the tip orifice.
(see Figure 11):
Figure 11

PLMNL0286 REV. B, Effective Date: 06/06/19 9FiberMINI ®with Auto Focus (AF) Operation Manual
3 Electrical Installation and
Operation
Laser Mechanisms offers multiple control box
styles to accommodate your application.
Control Box
Style
Connections
PLCSA0081
Discrete I/O
Section 3.1.2
PLCSA0082
Device Net
Section 3.1.3
PLCSA0083
Ethernet IP
Section 3.1.4
PLCSA0084
Modbus TCP
Section 3.1.5
For more info on using the DeviceNet,
EtherNet/IP and Modbus TCP control boxes,
see Section 3.2.
See your Laser Mechanisms Sales Engineer
for more control box models and other details.
The FiberMINI®AF requires a control cable
designed with wires in twisted pairs. There are
(2) standard options:
Control Cable
Length
PLCAB0608
8 Meters
PLCAB0701
20 Meters
3.1 Electrical Connections
3.1.1 Connections to the Head
There are (3) cable connections to the
head.
The control cable (PLCAB0608 or
PLCAB0701) connects at the top of
the electrical box.
The straight end of the tip wire
(PLTTW0003) connects at the
bottom of the electrical box.
The right angle end of the tip wire
connects at the tip retainer
assembly.
See Figure 12.
Figure 12
For steps 1 to 3, see Figure 12.
1. Insert the female end of the control
cable into the top of the electrical
box.
2. Insert the straight end of the tip
wire into the bottom of the electrical
box.
It may be helpful to wrap
the tip wire around the tip
retainer assembly during
installation.
3. Insert the right angle end of the tip
wire into the tip retainer assembly.

PLMNL0286 REV. B, Effective Date: 06/06/19 10 FiberMINI ®with Auto Focus (AF) Operation Manual
3.1.2 Discrete I/O Control Box
(PLCSA0081)
There are (5) connection locations for
the discrete I/O control box
(PLCSA0081).
For steps 1 to 5, see Figure 13.
1. Insert the male end of the control
cable into the 14-pin connection on
the electrical control box (no label).
2. Connect the USB cable
(PLCAB0718) to the connection on
the control box labeled USB.
The USB port provides the
interface connection
between the FiberMINI®
AF and a computer. Laser
Mechanisms provides PC
software called FiberMINI®
Monitor that allows
monitoring of the head and
changing of the settings.
3. Connect the optional user-supplied
Step/Direction input into the 15 pin
D-sub connector on the control box
(no label). See Section 3.3 for
more details.
4. Connect the user-supplied, 24V DC
power source to the three position
terminal block on the control box
labeled with +24V, 0V and Ground.
5. Connections to your system are
made through the 16 position
terminal block on the control box.
For the Discrete I/O control box
(PLCSA0081), there is no industrial
network connection. See Figure
13.
Figure 13

PLMNL0286 REV. B, Effective Date: 06/06/19 11 FiberMINI ®with Auto Focus (AF) Operation Manual
3.1.3 DeviceNet Control Box (PLCSA0082)
There are (6) connection locations for
the DeviceNet control box.
For steps 1 to 6, see Figure 14.
1. Insert the male end of the control
cable into the 14-pin connection on
the electrical control box (no label).
2. Connect the USB cable
(PLCAB0718) to the connection on
the control box labeled USB.
The USB port provides the
interface connection
between the FiberMINI®
AF and a computer. Laser
Mechanisms provides PC
software called FiberMINI®
Monitor that allows
monitoring of the head and
changing of the settings.
3. Connect the optional user-supplied
Step/Direction input into the 15 pin
D-sub connector on the control box
(no label). See Section 3.3 for
more details.
4. Connect the user-supplied, 24V DC
power source to the three position
terminal block on the control box
labeled with +24V, 0V and Ground.
5. Connections to your system are
made through the 16 position
terminal block on the control box.
6. Connect the user-supplied network
cable to the DeviceNet Industrial
Network module. See Section 3.2
for more details.
Figure 14

PLMNL0286 REV. B, Effective Date: 06/06/19 12 FiberMINI ®with Auto Focus (AF) Operation Manual
3.1.4 Ethernet / IP Control Box
(PLCSA0083)
There are (6) connection locations for
the Ethernet / IP control box.
For steps 1 to 6, see Figure 15.
1. Insert the male end of the control
cable into the 14-pin connection on
the electrical control box (no label).
2. Connect the USB cable
(PLCAB0718) to the connection on
the control box labeled USB.
The USB port provides the
interface connection
between the FiberMINI®
AF and a computer. Laser
Mechanisms provides PC
software called FiberMINI®
Monitor that allows
monitoring of the head and
changing of the settings.
3. Connect the optional user-supplied
Step/Direction input into the 15 pin
D-sub connector on the control box
(no label). See Section 3.3 for
more details.
4. Connect the user-supplied, 24V DC
power source to the three position
terminal block on the control box
labeled with +24V, 0V and Ground.
5. Connections to your system are
made through the 16 position
terminal block on the control box.
6. Connect the user-supplied network
cable to the Ethernet / IP Industrial
Network module. See Section 3.2
for more details.
Figure 15

PLMNL0286 REV. B, Effective Date: 06/06/19 13 FiberMINI ®with Auto Focus (AF) Operation Manual
3.1.5 Modbus TCP Control Box
(PLCSA0084)
There are (6) connection locations for
the Modbus TCP control box.
For steps 1 to 6, see Figure 16.
1. Insert the male end of the control
cable into the 14-pin connection on
the electrical control box (no label).
2. Connect the USB cable
(PLCAB0718) to the connection on
the control box labeled USB.
The USB port provides the
interface connection
between the FiberMINI®
AF and a computer. Laser
Mechanisms provides PC
software called FiberMINI®
Monitor that allows
monitoring of the head and
changing of the settings.
3. Connect the optional user-supplied
Step/Direction input into the 15 pin
D-sub connector on the control box
(no label). See Section 3.3 for
more details.
4. Connect the user-supplied, 24V DC
power source to the three position
terminal block on the control box
labeled with +24V, 0V and Ground.
5. Connections to your system are
made through the 16 position
terminal block on the control box.
6. Connect the user-supplied network
cable to the Modbus TCP Industrial
Network module. See Section 3.2
for more details.
Figure 16

PLMNL0286 REV. B, Effective Date: 06/06/19 14 FiberMINI ®with Auto Focus (AF) Operation Manual
3.2 EtherNet/IP / Modbus TCP / DeviceNet Module (If Equipped)
The Industrial Network module is optional. If you purchased the optional module, it is pre-installed
in the controller.
If you did not purchase the optional module, a blank plate is pre-installed in the controller.
There are (2) status LEDs located on the front of the Industrial Network module.
Ethernet-based networks have additional link and activity lights located on the RJ-45
connectors.
LED NS –Network Status
STATE
STATUS
Green
Online, connection(s) established
Green, flashing
Online, no connections established
Red
Duplicate IP address/Critical link failure
Red, flashing
Connection(s) timed out
Off
No power or no IP address
LED MS –Module Status
STATE
STATUS
Green
Controlled by Scanner in Run state
Green, flashing
Not configured or Scanner in Idle state
Red
Major fault
Red, flashing
Recoverable fault
Off
No power

PLMNL0286 REV. B, Effective Date: 06/06/19 15 FiberMINI ®with Auto Focus (AF) Operation Manual
I/O Mapping
Device: ABCC CompactCom 40 Connection: Exclusive Owner
Input: 19 INT (38 Bytes), Connection Point 100 Output: 2 INT (4 Bytes), Connection Point 150
Generic EDS files are available for download at http://www.lasermech.com/fiberminiupdates
Use FiberMINI®Monitor PC software to set IP configuration or node address before use.
WORD
TYPE
NAME
WEB ID
0
Input Data
Status Bits
2.0
1
Input Data
Active Faults
2.1
2
Input Data
Historical Faults
1
3
Input Data
Upper Assembly Temperature
2.2
4
Input Data
Lower Assembly Temperature
2.3
5
Input Data
Electronics Temperature
2.4
6
Input Data
HSU Voltage
2.5
7
Input Data
Actual Lens Position
2.6
8
Input Data
Target Lens Position
2.7
9
Input Data*
Upper Assembly Temp Limit
3.0/21.0
10
Input Data*
Lower Assembly Temp Limit
3.1/21.1
11
Input Data*
Electronics Temp Limit
3.2/21.2
12
Input Data*
Temp Difference Limit
3.3/21.3
13
Input Data*
Steps per mm
3.4/21.4
14
Input Data*
Control Options
3.5/21.5
15
Input Data*
Home Minimum
3.6/21.6
16
Input Data*
Home Maximum
3.7/21.7
17
Input Data*
Focus Position
3.8/21.8
18
Input Data
Maximum Position
3.9
0
Output Data
Command Bits
11
1
Output Data
Set Position (Remote)
13
N/A
Web Only
Set Position (Web)
22
N/A
Web Only
Head Firmware
94
N/A
Web Only
Head Revision
95
N/A
Web Only
Head Serial Number
96
N/A
Web Only
Controller Firmware
97
N/A
Web Only
Controller Revision
98
N/A
Web Only
Controller Serial Number
99
* Output Data also available using the Web Interface.
Sensor and limit values are displayed in the following units:
1. Temperature: °C x 10 (i.e. 300 = 30.0 °C), 999 = Sensor Error
2. Voltage: See HSU Voltage chart
3. Position: mm x 100 (i.e. 850 = 8.50 mm)
Table of contents
Popular Measuring Instrument manuals by other brands

Galvanic Applied Sciences
Galvanic Applied Sciences ProTech903W Operation manual
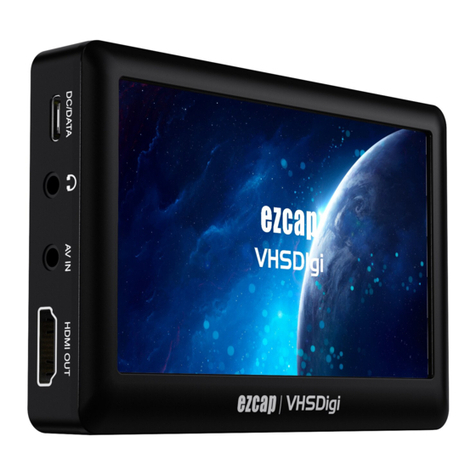
EzCAP
EzCAP VHSDigi ezcap180 manual

Analyticon
Analyticon Hemolyzer 5 Service manual

Eastron
Eastron SDM72DM user manual
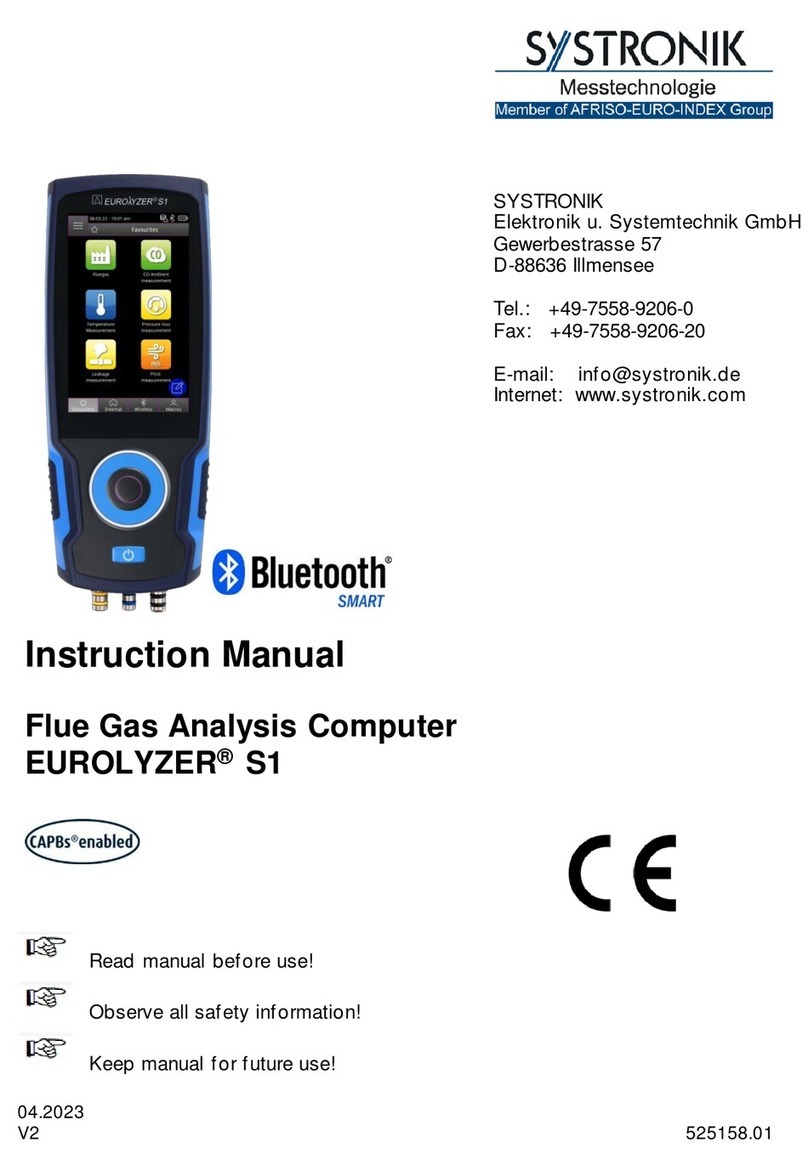
SYSTRONIK
SYSTRONIK EUROLYZER S1 instruction manual
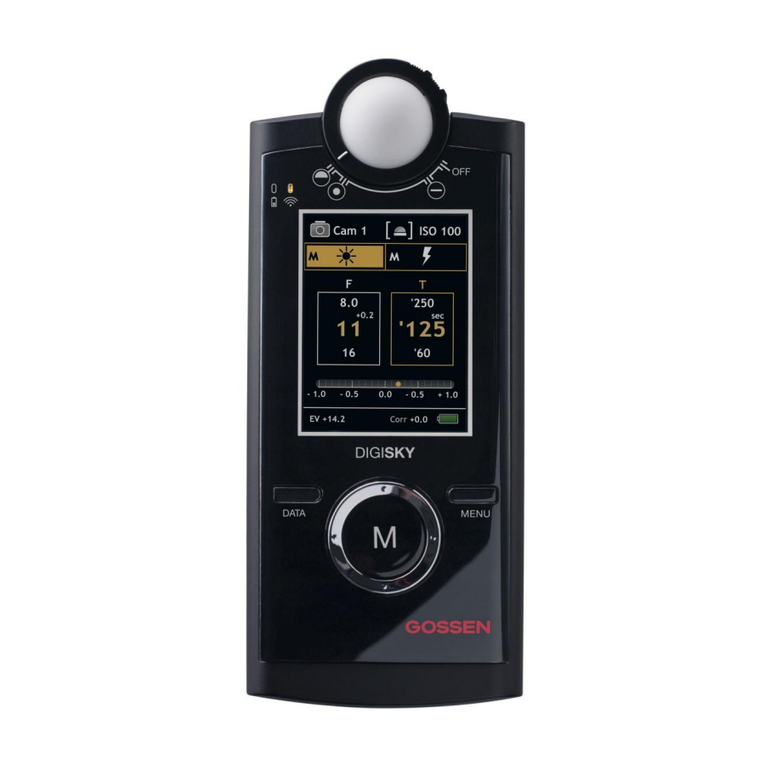
Gossen MetraWatt
Gossen MetraWatt DIGISKY quick start guide