Leguan L190 Operating manual

Operator and Service manual
Edited:
13.12.2019
NKA

2
_________________________________________________________________________________
TABLE OF CONTENTS
1. INTRODUCTION AND WARRANTY CONDITIOS 4
1.1 INTRODUCTION 4
1.2 WARRANTY CONDITIONS 4
2. GENERAL INFORMATION 7
2.1 TECHNICAL SPECIFICATIONS 8
2.2 REACH DIAGRAM AND SUPPORT DIMENSIONS 9
2.3 SIGNS AND DECALS 10
3. SAFETY INSTRUCTIONS 11
3.1 BEFORE STARTING OPERATION 11
3.2 RISK OF TIPPING OVER 12
3.3 RISK OF FALLING 12
3.4 RISK OF COLLISION 13
3.5 RISK OF ELECTRIC SHOCK 13
3.6 RISK OF EXPLOSION/FIRE 13
3.7 DAILY INSPECTION BEFORE STARTING OPERATION 14
3.8 USE OF EMERGENCY STOP SWITCHES 14
3.9 SAFETY INSTRUCTIONS FOR DRIVE CONTROL 14
3.10 DEFINING THE GRADIENT OF THE SLOPE 14
4. CONTROLS AND SWITCHES 15
4.1 CONTROLS IN PLATFORM 15
4.1.1 PLATFORM OVERLOAD INDICATOR LIGHT 16
4.1.2 DYNAMIC OUTREACH CONTROL SIGNAL LIGHT 16
4.1.3 FAULT LIGHT 16
4.1.4 INCLINATION SENSOR INDICATOR LIGHT 17
4.1.5 BOOM CENTER POSITION INDICATOR (SLEWING) 17
4.1.6 BOOM TRANSPORT SUPPORT INDICATOR LIGHT 17
4.1.7 LOW FUEL LEVEL INDICATOR 18
4.2 LOWER CONTROLS PANEL 18
4.3 WIRELESS REMOTE CONTROL (OPTION) 19
4.4 EMERGENCY LOWERING BUTTON AT GROUND LEVEL (OPTION) 20
4.5 230 VCONNECTION AND SWITCHES (OPTION) 20
5. OPERATION 21
5.1 STARTING THE COMBUSTION ENGINE /ELECTRIC MOTOR 21
5.1.1 COMBUSTION ENGINE 21
5.1.2 ELECTRIC MOTOR 22
5.2 SPEED SELECTION SWITCH 22
5.3 DRIVE CONTROL 22
5.3.1 USING THE CRAWLER TRACK CHASSIS 23
5.4 OPERATION OF THE OUTRIGGERS 24
5.4.1 AUTOMATIC LEVELING 24
5.4.2 OUTRIGGER MANUAL DRIVE 24
5.5 OPERATION OF THE BOOMS 25
5.5.1 AUTOMATIC SLEWING STOP FUNCTION 25
5.5.2 DEAD MAN SWITCH,BOOM USE (OPTION) 25
5.6 REMOTE CONTROL (OPTION) 26
5.7 ENDING THE OPERATION 26
5.8 ADDITIONAL INSTRUCTIONS FOR WINTER USE 26
6. EMERGENCY LOWERING AND EMERGENCY USE 27
6.1 HAND PUMP 27
6.2 ELECTRIC LOWER CONTROLS (OPTION) 27
6.3 OUTRIGGER CONTROL OVERRIDE 28
6.4 PLATFORM LOAD CONTROL AND PLATFORM EMERGENCY STOP BUTTON OVERRIDE 28

3
_________________________________________________________________________________
6.5 BOOM TRANSPORT POSITION MONITORING OVERRIDE 29
7. TRANSPORTATION 30
8. SERVICE, MAINTENANCE AND INSPECTION REGULATIONS 31
8.1 GENERAL INSTRUCTIONS 31
9. SERVICE INSTRUCTIONS 32
9.1 SERVICE AND CHECKS,MAINTENANCE SCHEDULE 32
9.1.1 CRAWLER TRACK SPROCKET NUTS 33
9.2 FUSES 34
9.3 GREASING 35
9.3.1 GREASING OF THE SLEW RING 35
9.3.2 GREASING THE TELESCOPIC BOOM CHAIN PULLEY AND INSPECTION OF THE CHAIN 35
9.3.3 GREASING OF TELESCOPING BOOMS 36
9.3.4 GREASING OF THE POSITION SENSOR PINS ON THE OUTRIGGERS 36
9.3.5 GREASING DIAGRAM 37
9.4 HANDLING OF FUEL AND REFUELING 38
9.5 HYDRAULIC OIL AND HYDRAULIC OIL FILTER REPLACEMENT 38
9.6 HYDRAULIC OIL LEVEL 39
9.7 BATTERY CHECK 39
9.8 CHECK OF SET-UP CONTROL SYSTEM 39
9.9 WATER LEVEL CHECK 40
9.10 HYDRAULIC PRESSURES AND ADJUSTMENTS 40
9.11 PEDESTAL VALVE HOUSING 41
9.12 OVERLOAD CONTROL COMPONENTS 42
9.14 BOOM TRANSPORT SUPPORT SENSORS 43
9.15 SAFETY VALVE TEST 45
9.16 BATTERY HANDLING 46
9.17 HANDLING OF FUEL AND OIL PRODUCTS 46
10. REPAIR INSTRUCTIONS 47
10.1 WELDING 47
11. INSTRUCTIONS FOR TEMPORARY STORAGE 48
12. INSTRUCTIONS FOR DISPOSING THE ACCESS PLATFORM 48
13. TROUBLE SHOOTING 49
14. PERFORMED SERVICE 53
Attachments:
Hydraulic schema
Electric diagram

4
_________________________________________________________________________________
1. INTRODUCTION AND WARRANTY CONDITIOS
1.1 Introduction
LEGUAN LIFTS wants to thank you for purchasing this Leguan access platform. It is the result of
Leguan’s long experience in design and manufacturing of access equipment.
We ask you that you read and understand the contexts of this manual completely before operating the
access platform. This will improve your operating and maintenance efficiency, help avoid breakdowns
and damage and extend the life of your machine.
Pay special attention to this symbol. It indicates important safety factors that require special attention.
Every operator must read and understand this manual before starting operation, and the instructions
in this manual must be followed. If you are lending the access platform out to somebody, make sure
that he familiarizes himself with and understands these instructions. If there is anything unclear with
the operation, please contact your Leguan dealer.
If spare parts are needed, use only original LEGUAN parts. They will provide your machine with the
maximum life expectancy and ensure optimum safety.
It is not possible to give explicit operating instructions to all operating conditions of the machine.
Therefore, the manufacturer is not responsible for any damage caused by eventual faults in this
Operators Manual.
The manufacture does not accept any responsibility for consequential losses resulting from the use of
this self-propelled access platform.
1.2 Warranty conditions
This product is warranted for a period of twenty-four (24) months without hour limit. In the event a fault
occurs which is attributable to manufacturing or assembly defect, contact the dealer without delay.
Warranty covers manufacturing and material defects. All warranty obligations end when the warranty
period ends. Warranty repair that has been started will be completed regardless of the ending date of
warranty period.
A condition for the warranty is that both the buyer and the seller have accepted the delivery. If the
buyer is not present when the delivery takes place and doesn’t make a complaint within 14 days of
delivery of this access platform, it is considered that the sale is closed and the warranty period has
started.
Warranty is limited to the repair of a faulty access platform without cost at an authorized Leguan
service workshop. Warranty period for parts that are changed in connection with the repair will end
when the warranty period for the access platform ends. Parts that have been changed in the warranty
repair will remain Leguan Lifts’ property without compensation.

5
_________________________________________________________________________________
Warranty does not cover:
-Damages caused by wrong or negligent use of this product, or mischief.
-Any repairs or modifications to the product, performed without the prior authorization of the
manufacturer.
-Damages caused by not following service and maintenance instructions.
-Adjustments, repairs and spare parts replacements caused by normal wear.
-Damages caused by excessive loads on the access platform, sudden unexpected incident,
natural disaster.
-Damages caused by external mechanical or chemical reasons (paint damages, especially
caused by stone chips, air and environmental pollution and strong cleaning agents)
-Eventual visible patterns or unevenness of painted surfaces.
-Warranty claims that haven’t been sent to the manufacturer within 14 days from the date the
buyer has noticed the defect. In all conditions the buyer shall act so that his action doesn’t
make the eventual defect(s) worse.
The manufacturer does not accept any responsibility for consequential losses resulting from
the use of this access platform.
In the event a fault occurs which is attributable to manufacturing or assembly defect, contact
the dealer without delay.

6
_________________________________________________________________________________
ALKUPERÄINEN EY-VAATIMUSTENMUKAISUUSVAKUUTUS
ORIGINAL EC DECLARATION OF CONFORMITY FOR MACHINERY
TÄTEN VAKUUTAMME, ETTÄ
HEREWITH DECLARES THAT
HENKILÖNOSTIN NIMELLISKUORMA
AERIAL PLATFORM NOMINAL LOAD
MALLI NOSTOKORKEUS
MODEL PLATFORM HEIGHT
SARJANUMERO VALMISTUSVUOSI
SERIAL NR YEAR OF CONSTRUCTION
ON KONEDIREKTIIVIN 2006/42/EY ASIAAN KUUULUVIEN SÄÄNNÖSTEN MUKAINEN
IS IN ACCORDANCE WITH THE REGULATIONS LAID OUT IN THE MACHINERY
DIRECTIVE: 2006/42/EC
KONE TÄYTTÄÄ LISÄKSI MUIDEN EY-DIREKTIIVIN VAATIMUKSET: 2004/108/EY THE
MACHINE ALSO FULFILLS THE REQUIREMENTS LAID OUT IN THE DIRECTIVES
2004/108/EY
SEURAAVIA EUROOPPALAISIA YHDENMUKAISIA STANDARDEJA ON SOVELLETTU
SUUNNITTELUSSA: EN280:2015
FOLLOWING EUROPEAN HARMONIZED STANDARDS ARE USED WHEN
THE MACHINERY WAS DESIGNED: EN280:2015
Teknisen tiedoston on valtuutettu kokoamaan: LEGUAN LIFTS OY
Storage address of original documents: Ylötie 1, FI-33470 Ylöjärvi,
Finland
Ilmoitettu laitos / Notified Body INSPECTA TARKASTUS OY, NB0424
Testausraportti / Test Report No. 16038-2017
Paikka / Place, Päiväys / Date
Ylöjärvi, FINLAND xx.xx.20xx
Valmistaja / Manufacturer:
LEGUAN LIFTS OY
Ylötie 10, FI-33470 Ylöjärvi, Finland
____________________________________
XXXXX
Toimitusjohtaja / Managing Director
LEGUAN
L190
00XXXXX
230 kg
17,0 m
20XX

7
_________________________________________________________________________________
2. GENERAL INFORMATION
LEGUAN 190 is a self-propelled Mobile Elevating Work Platform –or commonly called access
platform, designed for indoor and outdoor use. An access platform is destined for lifting of persons
and their equipment only. It is not allowed to use an access platform as a crane.
LEGUAN is designed and built in accordance with the international safety standards and MEWP
(Mobile Elevating Work Platform) standards.
The picture below (Figure 1) shows the main parts of this access platform:
1. Chassis
2. Transmission, either
with wheels or
crawler tracks
3. Outrigger
4. Outrigger cylinder
5. Slewing ring
6. Connection box of
control system
7. Lower controls
8. Self levelling bar 1
9. Pedestal
10. Lift cylinder
11. Lower boom 1
12. Valve box
13. Linkage piece 1
14. Self levelling bar 2
15. Lower boom 2
16. Linkage piece 2
17. Upper boom cylinder
18. Self levelling
cylinder, ”master”
19. Telescoping cylinder
20. Upper boom
21. Telescoping boom 1
22. Telescoping boom 2
23. Jib boom
24. Self levelling bar 3
25. Jib boom cylinder
26. Controls at platform
27. Platform
28. Self levelling
cylinder, ”slave”
Figure 1 Main parts

8
_________________________________________________________________________________
2.1 Technical specifications
Working height
19,0 m
Max. platform height
17,0 m
Max. outreach @ 230 kg
8,1 m
Max. outreach @ 120 kg
9,8 m
Safe working load
230 kg
Transport length
5,07 m
Transport length without platform
4,32 m
Transport height
2,11 m
Width
1,25 m
Platform dimensions, W x L, 2 persons
1,33 x 0,75 m
Max. allowed levelling inaccuracy
1,0º
Platform rotation
± 45º
Slewing
360º
Gradeability
50 % (27º)
Gradeability sideways
35 % (20º)
Support dimensions
3,78 x 3,83 m
Max. gradient of slope for set up
22 % (13º)
Weight, depending on equipment
2660 kg
Drive system
4WD or tracks
Drive speed
max. 2,6 km/h
Speed when drive motors connected in series (option)
max. 5,2 km/h
Lowest operating temperature
-20 °C (storage -40 °C)
Starter battery / electric system
60 Ah / 12V
Sound power level at platform controls, LWA
94 dB (A)
Max. outrigger force
20 kN
Max. load under wheels
0,3 N/mm2 (3 bar)
Vibration emission, awmax (uncertainty K=1,0 m/s2)
2,6 m/s2

9
_________________________________________________________________________________
2.2 Reach diagram and support dimensions
Figure 2 Reach diagram
Figure 3 Support dimensions

10
_________________________________________________________________________________
2.3 Signs and decals
1. Type plate and CE-marking
2. Safe working load (SWL)
3. Max. horizontal force and wind speed
4. General user instructions
5. Daily inspection
6. Always use outriggers
7. Control symbols decal
8. Emergency lowering (option)
9. Residual current device
10. Electric motor voltage
11. Max. outrigger force
12. Distance from energized electric wires
13. Tie down points
14. Tyre pressure
15. Leguan 190 decal
16. Lower controls’ decal
17. Lift points
Figure 4 Signs and decals

11
_________________________________________________________________________________
3. SAFETY INSTRUCTIONS
The operator must know and follow all safety instructions. The operator must receive sufficient
instructions in order to be able to use the lift correctly and safely. This Operators Manual must always
be kept in the box on the platform.
ATTENTION!
In order to prevent unpermitted use of the access platform, take the ignition key that is located on
ground level with you after ending operation.
CAUTION! DANGER!
THE ACCESS PLATFORM IS NOT VOLTAGE INSULATED. NEVER USE IT NEAR ANY
VOLTAGE CARRYING PARTS OR DEVICES. DO NOT DRIVE ANY PART OF THE
ACCESS PLATFORM OR PLATFORM CLOSE TO UNINSULATED CABLES OR OTHER
VOLTAGE CARRYING PARTS OR DEVICES.
WHEN WORKING WITH THE ACCESS PLATFORM THE OPERATOR(S) MUST ALWAYS
WEAR CERTIFIED SAFETY HARNESS WHICH IS PROPERLY CONNECTED TO THE
PLATFORM.
3.1 Before starting operation
-All warnings and labels must be read carefully.
-Only persons with min. 18 years of age are allowed to use the access platform. They must
have received sufficient operating instructions.
-Operator must know all the functions of this access platform as well as the Safe Working
Load, loading instructions and safety instructions.
-If there is heavy traffic in the working area, it must be fenced off widely enough and marked
with a fence or with a line. Road traffic regulations must be followed as well.
-Make sure that there are no bystanders in the working area.
-Do not use faulty access platform. Inform about all faults and defects and make sure that they
are repaired before starting operation.
-Follow check and service instructions and intervals.
-The operator must check this access platform visually at the beginning of each work shift. This
check is necessary in order to make sure that the machine is all right before making the daily
inspection prior to starting operation.
-If combustion engine is used indoors, make sure that the ventilation is sufficient.

12
_________________________________________________________________________________
3.2 Risk of tipping over
-Safe working load (230 kg), number of persons (2) and additional load on the platform must
never be exceeded.
-When wind speed is equal to or greater than 12,5 m/s - 28 mph, the use of the access
platform must be discontinued immediately and the platform must be lowered down to
transport position.
-Ensure that the access platform is used on dry, solid, level ground only. The ground is solid
enough if it can carry min. 3 kg/cm2. On softer grounds use extra support plates under the
outriggers (plate dimensions 400 x 400 mm).
-Do not use a ladder, chair, stool, scaffolding or by any other means try to increase reach
capability of this access platform.
-In case the platform has got stuck or jammed, or it is too close to a building or a wall to be
moved, do not try to release the platform by operating the controls. All persons must leave the
platform first (with the help of a rescue service of fire brigade if necessary), only after that one
can try to lower the platform by using the emergency lowering.
-Do not increase the area of the platform or the load. Increasing of the area exposed to wind
will weaken the stability of the access platform.
-Weight must be equally distributed on the platform. Make sure that additional weight cannot
shift on the platform.
-Do not drive on gradients that are steeper than the max. values given for this access platform
and for the slope.
-Never use this access platform as a crane or an elevator. This access platform is intended for
lifting of the max. allowed number of persons and additional load only.
-Check and make sure that all tyres are in good condition. If the tyres are air filled, make sure
that there is correct pressure in the tyres.
-In order to ensure the safe operation of this access platform the manufacturer has conducted
approved tests for the LEGUAN 190 in accordance with the standard EN 280:2013+A1:2015
static stability test in accordance with paragraph 6.1.4.2.1 and dynamic overload test in
accordance with paragraph 6.1.4.3 of the EN 280:2013+A1:2015.
3.3 Risk of falling
-The operator(s) must always wear certified safety harnesses when operating this access
platform. The harnesses must be connected to the fastening point at platform mounting
bracket.
-Do not stretch or reach out over the handrails. Stand steadily on the platform floor.
-Keep platform floor clean.
-Always close the platform gate before starting operation.
-Do not drop or throw any material down from platform.
-It is not allowed to go to or step out from the platform when the booms are lifted.

13
_________________________________________________________________________________
3.4 Risk of collision
-Adjust the drive speed so that it is safe in regards to the ground conditions.
-The operator must follow all regulations concerning the use of safety equipment on the work
site.
-Make sure that there are no overhead obstacles on the work site that could prohibit lifting of
the platform, or objects that might cause a collision.
-Do not operate this access platform in the working area of another overhead lifting device or
similar equipment that is moving, unless this lifting device is secured so that there is no risk of
collision.
-Beware of crushing hazard when holding the handrail of the platform in an eventual collision
situation.
-When operating the lift, beware of eventual limited visibility and trapping hazard.
3.5 Risk of electric shock
-This access platform is not voltage insulated nor protected against contact with voltage
carrying parts, or when approaching them.
-Do not touch the machine if it comes in contact with voltage carrying electric line.
-Persons on the platform or at ground level must not touch or operate the platform before
power has been cut off from the electric line.
-During welding repairs, it is not allowed to use any part of this access platform as earth
conductor.
-Do not use this access platform during thunderstorm or high winds.
-Leave clearance to electric lines taking into account movements of platform, movements of
electric line, and high winds and gusts.
The minimum safety clearances to voltage carrying electric lines are shown in the following table.
These clearances must be respected.
VOLTAGE
MIN DISTANCE
0 - 1000 V
2 m
1 - 45 kV
3 m
110 kV
5 m
220 kV
5 m
400 kV
5 m
3.6 Risk of explosion/fire
-It is not allowed to start the combustion engine / electric motor in a place where one can smell
LPG, petrol, solvent or other flammable substance.
-Do not fill with fuel when the engine is running.
-Charge the battery only in places with sufficient ventilation, where there is no open fire or no
works which could cause spark emissions (like welding).
-In case of fire it is recommended to use carbon dioxide fire extinguisher. Dry powder
extinguisher can also be used but in this case the machine must be cleaned and inspected
thoroughly because the powder is corrosive.

14
_________________________________________________________________________________
3.7 Daily inspection before starting operation
- Ground - Controls
- Supports - Operating area
- Horizontal levelling - Platform
- Emergency stop button - Oil leakages
- Emergency lowering - Working area
3.8 Use of emergency stop switches
-To use an emergency stop or kill switch just press down the switch’s red cap (figure 5 (25)
and figure 6 (4)).
-Kill switches are used in emergency situations when normal shutting down procedures are not
possible. For example in accidents and other dangerous situations involving the lift or its user.
-Kill switches shut down the engine but outrigger monitoring stays switched on.
-Kill switches in upper and lower control panels can be used at any time.
-Kill switches can be returned to neutral position by twisting its red cap clockwise.
-The emergency stop button in remote control unit will only operate when the remote
control use is selected
3.9 Safety instructions for drive control
1. Do not exceed maximum inclination for drive.
2. Make sure the driving surface is solid.
3. Fasten tools and other materials to prevent them falling.
4. Wear safety harnesses and keep them fastened whenever operating the machine.
3.10 Defining the gradient of the slope
Measure the slope with a digital clinometer, or do as follows:
Take a water level, a straight piece of wood at least 1 m long, and a pocket tape measure.
Place the wood on the gradient. Put the water level on the lower edge of the stick and lift the stick
until it is in horizontal position. Keep the stick level and measure the distance from the lower end of
the stick to the ground. Divide the distance (height) by the length of the wood stick (distance) and
multiply the result by 100.
Example:
Wood length = 2 m
Height = 0,5 m
(0,5 / 2) * 100 = 25 % slope
ATTENTION! When crossing slopes always drive up or down the slope, not sideways.
If you have to drive sideways on a slope, lower the downhill side outriggers so that
they are close to the ground. This prevents the machine from tipping over.
ATTENTION! If you note faults or missing equipment on this access platform, do not
put it into operation before the faults have been corrected. Never set the access
platform up in a place where the ground may be too soft. Beware of soft grounds and
potholes in particular.

15
_________________________________________________________________________________
4. CONTROLS AND SWITCHES
4.1 Controls in platform
The controls and indicators on the control panel at platform may be slightly different in different
models. Indicators and switches that are marked as options are not mounted on all models.
Figure 5: Upper control panel’s levers, switches and buttons
1. Diesel- and electric motor start- and stop-
button
2. Glow light
3. Speed selection switch
4. Automatic leveling switches (see 5.4.1)
5. Automatic leveling indication light (blinks) /
boom use allowed (continuously ON)
6. Outrigger control switches (see 5.4.2)
7. Platform overload indicator light (see 4.1.1)
8. Outreach control indicator light (see 4.1.2)
9. Fault light (see 4.1.3)
10. Boom center position indicator (slewing)
(see 4.1.5)
11. Boom transport support indicator light (see
4.1.6)
12. Low fuel level indicator
13. Inclination sensor indicator light (see 4.1.4)
14. 1st Boom control lever
15. 2nd boom control lever
16. Boom slewing control lever
17. Telescope boom control lever
18. Jib boom control lever
19. Platform tilting control lever
20. Outrigger monitoring override button (see
6.4)
21. Platform rotation
22. Horn / outrigger beacons’ switch (option)
23. Control panel / platform work light switch
(option)
24. Emergency lowering selector and button
(option)
25. Emergency stop switch (see 3.8)
14
13
12
11
10
3
2
6
1
9
8
7
15
4
16
17
18
19
20
25
21
22
23
24
5

16
_________________________________________________________________________________
4.1.1 Platform overload indicator light
This access platform is equipped with automatic platform overload system which
prevents all boom movements in case the 230 kg safe working load is exceeded.
Should this happen, there is an audible warning signal and an indicator light up at
the control panel (Figure 5 (7)). The booms can be operated again after the
overload has been removed from the platform.
NEVER OVERLOAD THE PLATFORM!
4.1.2 Dynamic outreach control signal light
This access platform is equipped with dynamic outreach control. Outreach
depends on the actual load on the platform.
-Red dynamic outreach control signal light (Figure 5 (7)) will blink and an
audible sound alarm can be heard when the telescope boom is about to
reach the current maximum outreach.
-The frequency of the blinking light as well as the audible sound will
increase as the telescopic boom closes the maximum outreach.
-When the maximum outreach is achieved red dynamic outreach control
signal light will stay continuously on and:
-Telescope boom movement out is prevented.
-2nd boom movement down is prevented.
-Continuous audible sound will signal that the maximum outreach is achieved.
2nd boom cannot be lowered before moving the telescope boom slightly in.
4.1.3 Fault light
The fault light will signal errors and faults on the equipment. Possible faults are
divided into two categories based on their severity.
When an ERROR occurs, the red fault light will BLINK.
-Equipment can be used with extreme caution.
-Some features are prevented.
-If the red fault light blinks, return booms onto their transport positions,
perform daily inspection (0) and remove possible cause of the error.
-If the problem persists, contact your Leguan dealer.
When a FAULT occurs, the red fault light will stay ON continuously.
-Ensure neither emergency stop button is pushed down.
-If the emergency buttons are not active, one of the safety components has failed and
prevented the use of the equipment.
-Return booms on their transport supports, stop working with the equipment and contact your
local Leguan dealer.
Possible errors and faults can be diagnosed with a separate service display (option).

17
_________________________________________________________________________________
4.1.4 Inclination sensor indicator light
This access platform is equipped with inclination sensor which alerts when the
inclination of the chassis exceeds the given limits.
If the limits are exceeded while driving an orange indicator light will blink and
give an audible alert can be heard. Drive the machine to more even surface.
While using booms the inclination sensor alert will have two stages:
If the ALARM limit is exceeded:
-Orange indicator light will blink and give an audible alert can be heard.
-Return all booms CAREFULLY on to their transport support
-Check that the ground is solid enough
-Re-level
If the ALERT limit is exceeded:
-Orange indicator light will stay on continuously and give an audible alert can be heard.
-Telescope boom movement out is prevented.
-2nd boom movement down is prevented.
-Return all booms CAREFULLY on to their transport support
-Check that the ground is solid enough
-Re-level
4.1.5 Boom center position indicator (slewing)
The slew ring of the access platform is equipped with inductive sensor which lights
the green boom center position indicator light whenever the 1st boom is above the
transport support. Indicator light is only an aid and does not guarantee that booms
will lower straight to transport supports.
4.1.6 Boom transport support indicator light
Boom transport support indicator light will stay continuously green when all booms
are properly placed on their transport supports.
Always visually ensure that the booms are properly placed on their transport
supports!
Do not reach, slew or lift the booms when the inclination alert light is on! RISK OF
TIPPING OVER!

18
_________________________________________________________________________________
Figure 6: Lower controls panel
4.1.7 Low fuel level indicator
Low fuel level indicator light will be lit when there is approximately 4,5 liters of fuel
left. This quantity will be enough for about 3 h of continuous working.
Fuel tank capacity is 12,5 liters.
When the low fuel indicator light is lit refuel as soon as possible (see 9.4).
4.2 Lower controls panel
1. Ignition key switch / selection upper / lower controls
2. Diesel- and electric motor start- and stop-button (see 5.1)
3. Glow light (see 5.1.1)
4. Emergency stop switch (see 3.8)
5. Inclination sensor indicator light (see 4.1.4)
6. Platform overload indicator light (see 4.1.1)
7. Dynamic outreach control indicator light (see 4.1.2)
8. Dead man switch, boom use (option) / remote control selection switch (option)
9. Outrigger control / platform emergency stop and platform overload override switch (see 6.4)
10. Hand pump cover lid release
11. Hand pump handle and release
12. Jib boom control lever
13. Telescopic boom control lever
14. Boom slew control lever
15. 2nd boom control lever
16. 1st boom control lever
2
3
1
8
10
13
12
11
B
A
4
6
7
5
9
14
15
16

19
_________________________________________________________________________________
4.3 Wireless remote control (option)
This access platform can be equipped with wireless remote control. The remote can be used to
operate outriggers and drive functions. The remote, spare battery and a battery charger are located
underneath the pedestal valve box.
Figure 7: Remote storage
1. Remote
2. Spare battery
3. Battery charger
Protect the remote from snow and ice. If lower controls is not selected, keep the remote in the storage
enclosure. The minimum temperature for the remote storage and use is -20 °C, store the remote
indoors if necessary.
Figure 8: Wireless remote
1. Emergency stop button (The remote emergency stop will only operate when the remote
control use is selected.)
2. Automatic levelling switch
3. Start button for remote
4. Drive speed selector
5. Outrigger control levers, left side
6. Outrigger control levers, right side
7. Electric motor start/stop switch
8. Combustion engine start/stop switch
9. Levers for driving
2
3
1

20
_________________________________________________________________________________
Figure 9: Emergency lowering at ground level
4.4 Emergency lowering button at ground level (option)
1. Hour meter
2. Electric emergency lowering selection
switch and button (1st boom, 2nd boom, jib)
(option)
4.5 230 V connection and switches (option)
1. 230 V, 50 Hz, 16 A connection
2. Residual current device
3. Battery charger. Two Led-indicators will indicate the
battery level:
Yellow = battery level low
Yellow + green = battery level almost fully charged
Green = battery fully charged / trickle charge
The RCD-unit switch (1) must be up in order to have any
230 V device working including the 230 V outlets at
platform. One can test the function of the RCD-unit by
pressing the test button in the unit. If the switch in the unit
will not go down, there is either a defect on the unit or the
connecting cable is not attached to mains.
1
2
1
2
2
3
1
Table of contents
Popular Network Hardware manuals by other brands
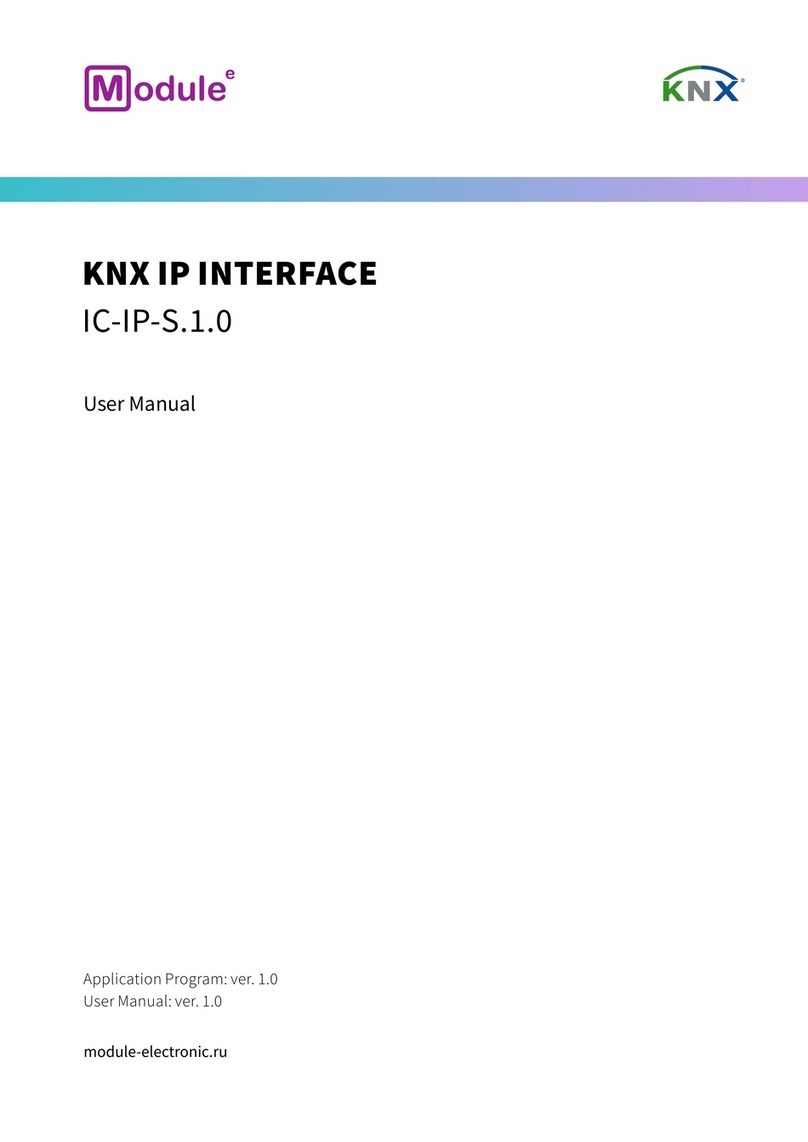
KNX
KNX Module IC-IP-S.1.0 user manual
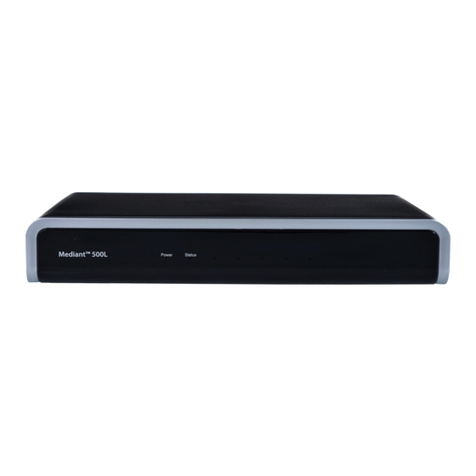
AudioCodes
AudioCodes Mediant Series Quick setup guide
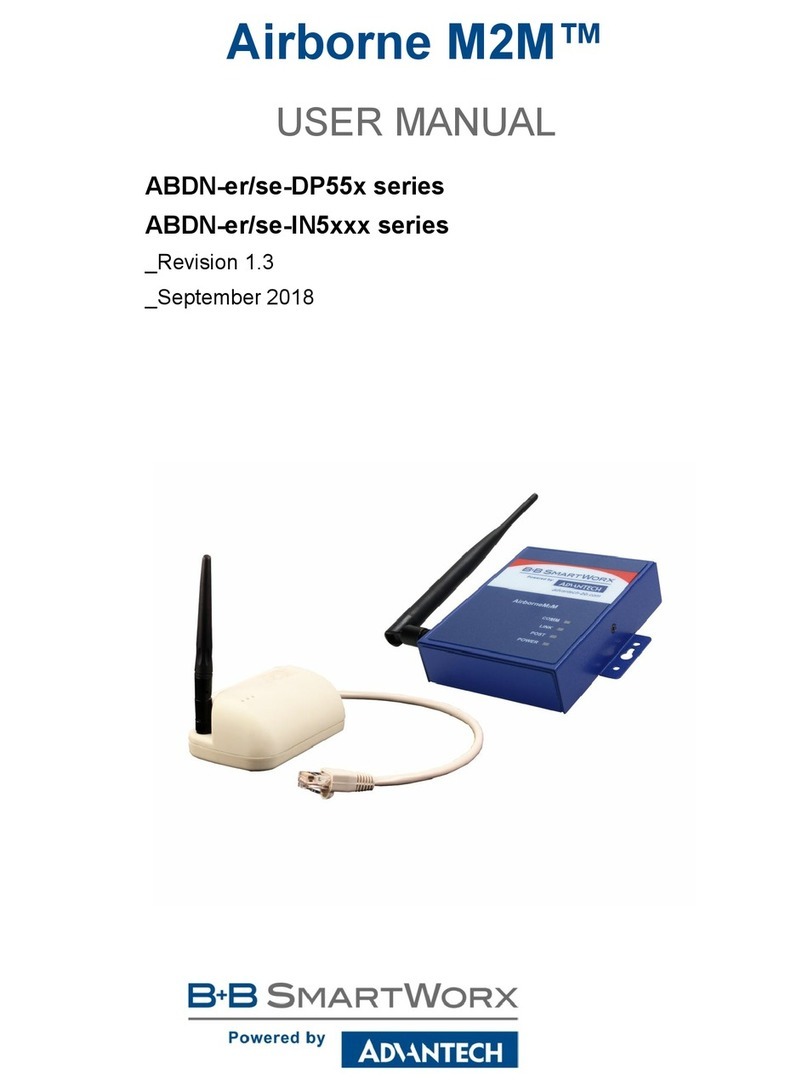
B+B SmartWorx
B+B SmartWorx Airborne M2M ABDN-er-DP55 Series user manual

Ubiquiti
Ubiquiti 0810354025402 quick start guide

Intermec
Intermec MaxiScan 3010 installation guide
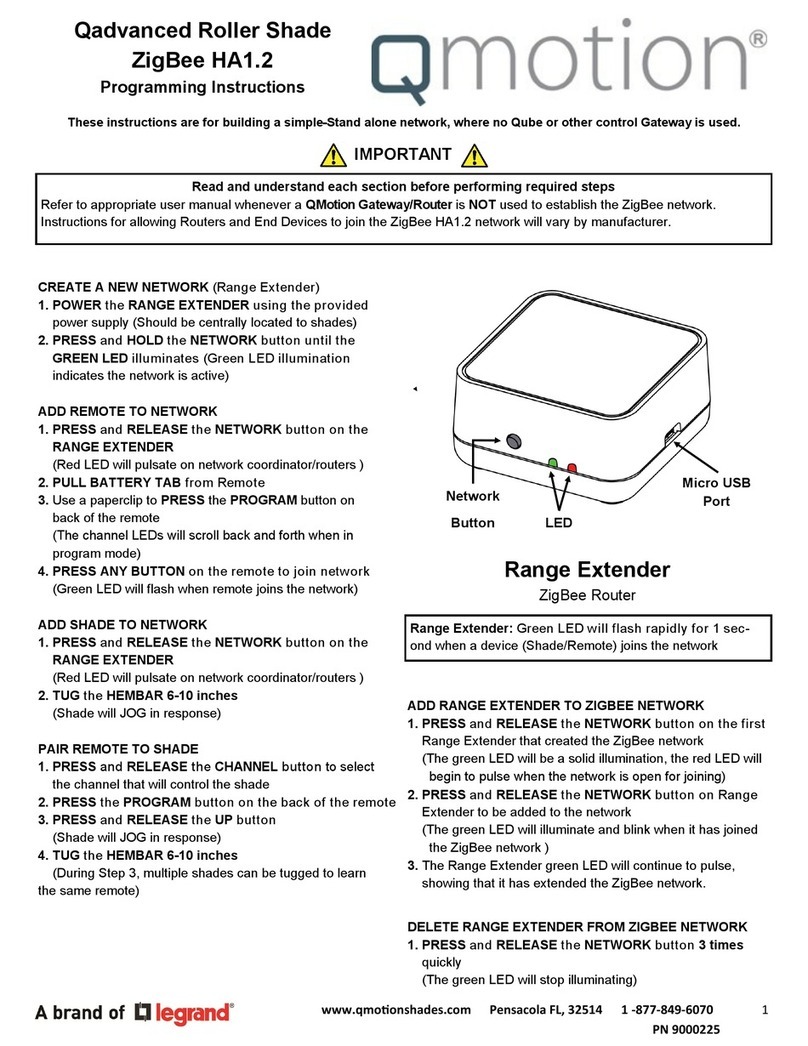
LEGRAND
LEGRAND Qmotion Range Extender Programming instructions