LEMKEN Granit 7 User manual

Operating Instructions
5RWDU\&XOWLYDWRU
Granit 7
Safety is our concern!
Part No.: 175 1258
GB-2/02.00
TRI-AG LIMITED
Wymondham, Norfolk, England NR18 9LR
Tel.: 01953 605151, Fax: 01953 607818


1
Dear customer!
We would like to thank you for the confidence in buying this implement.
The advantages of this implement will be shown, only, when operated and used
with due care and attention.
When handing over this implement your dealer has already instructed you with
regard to operation, adjustment and maintenance. But this short introduction re-
quires an additional detailed study of the instruction book.
Therefore read this instruction book carefully before the first use. Please pay at-
tention to the safety instructions mentioned in this instruction book.
Any changes and modifications carried out not being mentioned expressly in this
instruction book, may only be carried out with a written agreement of the manu-
facturer.
Ordering spare-parts
When ordering spare-parts please state type and serial No. of the implement.
This information will be found on the identification plate.
Put down this data on the following table so that it is always available.
Type of implement:
No.:
Only use genuine Lemken spare-parts. Spurious parts negatively influence the
function of the implement, show a shorter lifetime and increase in nearly all cases
additional maintenance.
We trust that you will understand that LEMKEN unable to guarantee poor opera-
tion and damage caused by using spurious parts!

2
DEFINED USE
•Please familiarise yourself with the LEMKEN Granit and its op-
erations before putting the implement to work. Therefore use this
instruction book with the „General Health- and Safety precau-
tions“!
•The LEMKEN Granit have been designed purely for the agricul-
tural use!
Any use beyond the one stipulated above is no longer considered as defined
use!
Under „defined use“ the manufacturer’s prescribed operation-, maintenance-
and repair conditions are to be adhered to!
•The LEMKEN Granit may only be operated, maintained and repaired by such
persons who have been made acquainted with it and who have been advised
about the dangers!
•The applicable accident prevention advice as well as the generally accepted
safety technical, working, medical and road traffic rules should be adhered to!
CONTENTS
DEFINED USE ..................................................................................................................2
CONTENTS.......................................................................................................................2
1 SAFETY INSTRUCTIONS...........................................................................................4
2 WARNING STICKERS ................................................................................................7
2.1 General Instructions.............................................................................................7
2.2 Meaning of the stickers........................................................................................7
3 PREPARATION OF THE TRACTOR..........................................................................9
3.1 Tyres......................................................................................................................9
3.2 Lift rods.................................................................................................................9
3.3 Check chains / sway blocks................................................................................9
3.4 Hydraulics .............................................................................................................9
3.5 Front Weights .......................................................................................................9
4 ATTACHING AND DETACHING THE ROTARY CULTIVATOR...............................10
4.1 Attaching the rotary cultivator ..........................................................................10
4.2 Detaching of the rotary cultivator.....................................................................10
5 PTO SHAFT...............................................................................................................12
5.1 General Instructions...........................................................................................12
5.2 Changing the distance of the rotary cultivator to the tractor.........................12
5.3 Shortening the PTO shaft..................................................................................13
6 ROTOR SPEEDS ......................................................................................................14

3
6.1 Changing the rotor speeds................................................................................14
7 SETTINGS.................................................................................................................15
7.1 Horizontal position.............................................................................................15
7.2 Working depth ....................................................................................................15
7.3 Position of the feeding disc...............................................................................15
7.4 Adjustment of the bottom flap ..........................................................................15
7.5 Power take off.....................................................................................................16
7.6 Scrapers of the packer roller.............................................................................16
8 ROLLERS..................................................................................................................17
9 A-FRAME...................................................................................................................18
10 HYDRAULIC DRILL LINKAGE .................................................................................18
10.1 Assembling the linkage .....................................................................................18
10.2 Attaching a mounted implement e.g. drill........................................................18
10.3 Lowering the seed drill ......................................................................................19
11 REAR PTO DRIVE.....................................................................................................19
12 WHEEL TRACK ERADICATORS .............................................................................19
13 CHANGING THE ROTOR WAVE..............................................................................20
14 SAFETY DEVICE.......................................................................................................20
15 MAINTENANCE / SERVICING..................................................................................21
15.1 Changing the oil .................................................................................................21
15.2 Lubrication..........................................................................................................21
15.3 Scrapers of the packer roller.............................................................................22
15.4 Bolts.....................................................................................................................22
15.5 Blades and cutters .............................................................................................22
15.6 PTO drive shaft...................................................................................................22
15.7 Hydraulic drill linkage ........................................................................................22
16 TRANSPORT ON PUBLIC ROADS..........................................................................23
17 NOTES.......................................................................................................................23
18 TECHNICAL DATA....................................................................................................23
19 NOISE, AIRBORNE SOUND.....................................................................................23
20 PRODUCT REGISTRATION / GUARANTEE............................................................23
EC CERTIFICATE OF CONFORMITY............................................................................24

4
1 SAFETY INSTRUCTIONS
General Safety Instructions
•Before using the machine, always check both it and the tractor for
roadworthiness and operational safety!
•As well as the notes in these instructions the operator is advised to
comply with the generally applicable safety at work regulations and
those relating to use of the public highway!
•The implement may only be operated, maintained and repaired by such per-
sons who have been made acquainted with it and who have been advised
about the dangers!
•When driving on public roads with a raised machine the lifting control lever
should be locked against unintentional lowering!
•The fitted warning and advisory plates give important information for safe op-
eration; adhering to these increases your own security!
•When using public roads adhere to applicable traffic rules!
•The operator should familiarise him-/herself with all controls and their functions
before starting work. During work could be too late!
•The clothing of the operator should fit tight. Avoid wearing any loose clothing!
•To avoid danger of fire keep the implement clean!
•Before beginning to drive check surroundings area (children)!
•Sitting or standing on the implement during operation or during transport is not
permissible.
•Attach implements as advised and only to the stipulated positions!
•Special care should be taken when the implement is coupled to or uncoupled
from the tractor.
•When coupling or uncoupling the implement bring the supporting stands into
the corresponding position (standing safety)!
•Fit weights only to the fixing points provided for that purposes!
•Adhere to the maximum permissible axle loads, total weights and transport
width!
•Fit and check transport gear, road lights and warning guards!
•The release ropes for quick coupler latches should hang freely and in the low-
ered position must not release the quick coupling by themselves.
•Never leave the driver’s seat whilst in motion!
•Handling behaviour, steerability and braking are influenced by mounted imple-
ments, trailers and ballast weights. Check for sufficient steerability and braking!
•When driving round bends note the width of the machine and/or changing cen-
tre of gravity of the implement.
•Put implement into operation only when all guards are fixed in position!
•Never stay or allow anyone to stay within the operating area!
•Never stay in the turning and slew area of the implement!
•Do not operate any hydraulic controls while anybody is in the operating area!
•On all pivoting parts actuated by power assistance (e.g. hydraulics) exists dan-
ger of injury by bruising and crushing!

5
•Before leaving the tractor lower the machine to the ground. Apply the parking
brake, stop the engine and remove the ignition key!
•Do not allow anybody between the tractor and implement if the parking brakes
are not applied!
Attached implements
•Before mounting or dismounting implements on/from the three-point linkage,
move the raise / lower control to the position at which accidental raising or low-
ering cannot take place!
•In the case of three-point linkage mounting, ensure that the tractor balls and
the mounting pins of the implement are of the same category!
•There is the risk of injury from pinch and shear points in the three-point linkage
area!
•When operating the external lift controls for the three-point linkage, do not
stand between the tractor and implement!
•Always ensure sufficient lateral limitation for the three-point linkage of the
tractor in the transport position of the implement!
•When driving on roads with the implement raised, the raise/lower control must
be locked to prevent lowering!
Hydraulic equipment
•The hydraulic pipes are under pressure!
•When connecting hydraulic rams, the pipes must be connected as directed!
•Always release hydraulic pressure from both tractor and implement before
coupling!
•When connecting hydraulic pipes to the tractor ensure that incorrect use is
avoided. If the connections are reversed, the opposite function is carried out
(e.g. raising/lowering) and there is a risk of accidents!
•Regularly check the hydraulic pipes and replace them in the event of damage
or signs of ageing. The replacement pipes must comply with the technical
specification as laid down by Lemken!
•When searching for leaks appropriate aids should be used because of the
danger of injury!
•Hydraulic oil escaping at high pressure can penetrate the skin and cause seri-
ous injury! When injured see a doctor immediately! Danger of infection!
•Before working on any hydraulic equipment - lower all imple-
ments/attachments, release hydraulic pressure where possible and switch off
the tractor engine!
Power take-off shaft operation
•Only drive shafts stipulated by the manufacturer may be used!

6
•Both halves of the protective tube of the PTO shaft must be anchored to pre-
vent rotation - and be in working order!
•At PTO shafts always see to the advised tube overlapping in transport- and
working position!
•Fit and remove the PTO shaft only when the power take-off drive is discon-
nected, the engine is switched off and the ignition key has been removed!
•Always ensure the correct assembly and safety of the PTO shaft!
•Prevent PTO guard from spinning by fixing the provided chain to a nearby
static part!
•Before engaging the power take-off drive, ensure that the selected speed of
the tractor’s power take-off shaft matches the permissible speed of the power
harrow!
•When using the speed-related PTO shaft take into account that the PTO speed
depends on the driving speed and that the turning direction is reversed when
driving backwards!
•Before engaging the power take-off drive, ensure that nobody is standing in the
hazard area of the power harrow!
•Never connect the power take-off shaft when the engine is switched on!
•When working with the power take-off shaft, nobody must stand in the area of
the rotating power take-off shaft.
•Always disengage the power take-off drive if excessive angular displacements
occur.
•Caution: After disengaging the power take-off drive, the rotors take a few sec-
onds to come to rest. Do not approach the power harrow too closely during this
time. Work must not be carried out upon it until it comes to a complete stand-
still!
•Clean, lubricate or adjust the appliance driven by the power take-off shaft only
when the power take-off shaft is disconnected, the engine is switched off and
the ignition key has been removed!
•Retain the uncoupled PTO shaft on the mount provided!
•After removing the PTO shaft replace the screw-on guard over the tractor PT0.
•In the event of damage, rectify it prior to continuation of work.
Maintenance
•Repair-, maintenance- and cleaning operations as well as adjustments and
remedy of function faults should principally be conducted with engine stopped
and brakes applied. Remove ignition key!
•Check and tighten nuts and bolts regularly!
•When conducting maintenance work on a lifted implement always place suit-
able supports underneath!
•For replacing any tools with cutting edges always use suitable tools and
gloves!
•Dispose of old oils, grease and filters as prescribed by law.

7
•Before working on the electric gear disconnect battery cables!
•When conducting electrical welding operations on the tractor or on the
mounted implement remove cable from the generator and the battery!
•Any spare parts fitted must meet with the implement manufacturer’s fixed tech-
nical standards! This is for example ensured by using genuine spare parts!
2 WARNING STICKERS
2.1 General Instructions
The LEMKEN Granit is equipped with all features to ensure safe operation.
Where potential danger areas of the implement can not be fully safeguarded,
warning stickers are fitted which draw attention to these.
2.2 Meaning of the stickers
Familiarise with the meaning of the stickers. The following descriptions inform
about them in detail.
WARNING: Read and adhere to this Instruction
book and these "General Health-
and Safety precautions", before
putting the implement to work!
WARNING: Keep well clear of the working and
swinging area of the implement!
WARNING: Pinch Point!

8
WARNING: Do not climb on the machine!
WARNING: Clockwise direction!
WARNING: Danger due to revolving parts!
WARNING: Shut off engine and remove key
before performing maintenance or
repair work!

9
3 PREPARATION OF THE TRACTOR
3.1 Tyres
Ensure that rear tyre pressures are equal and correct!
3.2 Lift rods
Ensure that the lift rods are of equal length! (Refer to the tractor handbook).
3.3 Check chains / sway blocks
Check chains or sway blocks must be adjusted so that the lower links are suffi-
ciently free to move sideways during work.
3.4 Hydraulics
Whilst working the tractor hydraulics must
be set to ‘floating position’ or ‘mixed
control’.
3.5 Front Weights
Fit manufacturer’s standard front weight kit
or equivalent. Extra front ballast may be re-
quired following a check on stability with the
power harrow raised or whilst working with
maximum weight transference. If at least 20
% of the tractor weight is on the tractor front
axle with raised power harrow, a safe stee-
rability to the tractor is ensured, when dri-
ving carefully.

10
4 ATTACHING AND DETACHING THE ROTARY CULTIVATOR
4.1 Attaching the rotary cultivator
−Set tractor hydraulics to ‘position
control’.
−Connect and secure the tractor lower
links to the drawbar (2)!
−Connect and secure the tractor top link
to the headstock so that top link rises
slightly towards the rotary cultivator du-
ring work!
−Secure top link!
−Remove the PTO shaft (1) from its
mount (3) and connect to the tractor
PTO!
−Connect to the hydraulic pipes of the drill linkage (if fitted)!
−Swing mount (3) of the PTO shaft (1) upwards and lay it down in the clamp!
−Fit marker boards and lighting equipment if the power harrow must be
transported along public roads.
−If a seed drill is fitted to the rear linkage, raise the seed drill until the lower links
of the rear lift are fixed by the headstock.
−Close the lock valve of the hydraulic ram.
4.2 Detaching of the rotary cultivator
This is done in the opposite sequence to the above. The rotary cultivator must al-
ways be parked on firm and level ground. If a seed drill is fitted via the rear linka-
ge, lower the seed drill fully before detaching the rotary cultivator from the tractor.
−Set tractor hydraulics to ‘position control’.
−Lower the rotary cultivator fully!
−Lower the rear linkage with seed drill fully (if fitted)!
−Disconnect the hydraulic hose(s) and fit caps!
−Detach top link implement sided!
−Swing mount (3) of the PTO shaft (1) downwards!
−Detach PTO shaft tractor sided and lay it into the holder!
−Detach the tractor lower link from the drawbar (2)!
•Any drill etc. mounted on the power harrow must be completely lo-
wered before detaching the power harrow!
•Special care should be taken when the implement is coupled to or
uncoupled from the tractor!
•Adhere to the maximum permissible axle loads, total weights and
transport measurements!
•The release ropes for quick coupler should hang freely and in the lowered posi-
tion must not release the quick coupling by themselves!

11
•Mount the implement as described!
•Never leave the driver’s seat whilst in motion! Handling characteristics, steera-
bility and braking are influenced by mounted implements, trailers and ballast
weights. Check sufficient steerabiltiy and braking!
•When fitting the hydraulic hoses to the tractor hydraulic sockets always ensure
that the hydraulic system at the tractor’s as well as at the implement side is
without pressure!
•To avoid wrong hydraulic connection sockets and probes should be marked.
This helps to prevent contrary function and reduces the danger of accident!
•Regularly check hydraulic hoses and pipings and exchange if found defective.
The replacement hoses and pipings must meet with the implement manufactu-
rer’s technical standards!
•When fitting the machine to the three-point linkage of the tractor bring all
control levers into such a position that unintentional lifting or lowering is impos-
sible!
•When fitting to the three-point linkage the mounting categories at the tractor
and the implement must be compatible or must be made compatible!
•There is a danger of being crushed in the area of the three-point linkage. Be
careful!
•When actuating the control levers for the three-point linkage from outside the
tractor cab never step between tractor and implement!
•Always minimise the sideways swing of the 3-point linkage when in transport!

12
5 PTO SHAFT
5.1 General Instructions
The PTO shaft (1) may not be pushed to-
gether fully in any working condition. Not only
with lowered rotary cultivator but also in wor-
king position - also with maximum working
depth - a rest-overlapping of the profile pipes
and of the protection tubes of at least 150 mm
must always be available. If the PTO shaft
doesn’t meet these requirements
1. the distance of the rotary cultivator to the
tractor must be increased or
2. the PTO shaft (1) must be shortened professionally
and that when the PTO shaft (1) is too long.
When the PTO-shaft is too short, the distance of the rotary cultivator to the tractor
must be shortened.
5.2 Changing the distance of the rotary cultivator to the tractor
If the PTO shaft (1) doesn’t come up to the above mentioned requirements and a
shortening of the PTO shaft isn’t required, the distance of the rotary cultivator to
the tractor can be adapted by means of adjusting the support (4) and therewith
the drawbar (2) corresponding.
A compact attachment of the rotary cultivator in order to reduce the necessary
demand of lifting capacity and of the release of the front axle will also be reached
by adjusting the support (4) and therewith of the drawbar (2). Tighten screws (S)
carefully after adjusting!

13
5.3 Shortening the PTO shaft
If the PTO shaft (1) is too long and an increasing of the distance between rotary
cultivator and tractor is not required, the PTO shaft must be shortened as follows:
Shorten both halves of both the profile and protective tubes by the same amount!
De-burr the newly cut face!
Lubricate the profile tubes slightly and push the two halves together, ensuring that
they slide together and come apart freely!
Attach the PTO shaft! The overlap coupling may only be fit tractor sided.
•Use only the PTO shaft supplied with the power harrow!
•The overload coupling end of the PTO shaft must be fitted to the power harrow!
•Regularly lubricate the PTO shaft and secure the outer tube to
prevent rotation.
•Guard tube and cones of the PTO-shaft as well as the tractor and
implement side PTO guard must be fitted and kept in a proper
condition!
•At PTO-shaft always see to the advised tube overlapping in transport- and wor-
king position!
•Fit and remove the PTO-shaft, only when engine is stopped!
•Prevent PTO-guard from spinning by fixing the provided chain to a nearby static
part.
•Before switching on the PTO-shaft ensure that the chosen PTO-speed of the
tractor corresponds to the allowable implement input speed.

14
6 ROTOR SPEEDS
The desired working effect depends, among other things, on the forward speed
and the rotor speed. The lowest rotor speed possible should be used at which the
required result is achieved. Excessively high rotor speeds mean high wear and
commensurate fuel consumption.
Gear box variations Gear box with angles Gear box with change
gears
Granit 7/200 standard ---
Granit 7/250 alternative alternative
Granit 7/300 --- standard
In connection with the gear box with angles the rotor speed can only be changed
by changing the PTO shaft speed.
But the rotor speeds with the gear box with
change gears can be changed by changing
the gear wheels.
6.1 Changing the rotor speeds
The Granit 7 with gear box with change gears
is equipped as standard with the pair of gear
wheels 23/21 (.../...). Therewith a rotor speed
of 145 1/min with 540 rotor speed of PTO
shaft and 268 1/min with 1000 rotor speed of
PTO shaft will be reached. The rotor speed
can be varied by means of changing the gear
wheels or using an other pair of gear wheel.
The possible rotor speeds are listed in the
following schedule:
Rotor speed
No. of teeth
Drive Output
Rotor speed of PTO
shaft (1/min)
540 750 1000
Rotor speed
(1/min)
18 26 110 152 203
19 25 120 167 223
21 23 145 201 268
23 21 174 241 322
25 19 208 288 384
26 18 229 318 ---
To change the gear, switch off the
PTO and also the tractor engine.
Remove the ignition key.
Remove cover (6), paying particular
attention to the seal. Exchange the
pairs of gears according to the table.
Replace the cover (6), ensuring that
the seal is positioned correctly.
Tighten the studs carefully.

15
7 SETTINGS
•Only clean, lubricate or adjust the power harrow or PTO shaft when the PTO
shaft is disconnected, the tractor engine is switched off and the
ignition key removed.
•Change gears with completely lowered power harrow and seed drill
(if fitted) only.
7.1 Horizontal position
During work the rotary cultivator should be horizontal fore/aft. Adjustment is made
by altering the tractor top link length.
7.2 Working depth
The required working depth of the rotary culti-
vator depends on the desired working effect.
The depth adjustment ensues by means of
changing the position of the upper pin (7). The
clearance between the roller and the ground
when the rotary cultivator is lifted is depending
on the position of the lower pin (8). The upper
pins should be positioned as low as possible
and as high as necessary to maintain clearance with lifted rotary cultivator.
7.3 Position of the feeding disc
The feeding disc (Z) should nearly work so
deep as the tines or blade. This ensures a
good joining to each working row. The depth
adjustment ensues by means of the pin ad-
justment with pin (ST). Additionally the fee-
ding discs are lateral adjustable, in order to
adjust the exact working width of 2,0 m, 2,5 m
or 3 m. For the transport the feeding discs
must be dismounted from the Granit 7/300, fit
from above into the U-guiding (4) and secu-
red. So it is ensured that the allowed transport width of 3 m will not be exceeded.
The lateral protection tubes (SR) must be swung-in and secured.
7.4 Adjustment of the bottom flap
The bottom flap (B) shows 2 adjustments
(VS) and (HS). When operating the ad-
justment (VS), the height and the distance
between the soil lid and the rotor wave will
be changed. For facilitation a key can be fit
on the hexagon head (SK), whereby the
bottom flap (B) after pulling up the lever (HE)
can be adjusted easily.
When adjusting the soil lid by means of the

16
adjustment (HS) with pin, the horizontal distance to the rotor shaft will be chan-
ged.
As little the distance, as better is the crumbling effect
As larger the distance, as bigger is the ... = more soil can be mastered
7.5 Power take off
The PTO must only be engaged when the rotary cultivator has been lowered
within a few centimetres of the ground and the lateral protection pipes are swung
out and secured. It must be disengaged when the rotary cultivator is more than a
few centimetres above the ground.
7.6 Scrapers of the packer roller
The scrapers (14) must be adjusted regularly. They should be positioned 0,5 - 1
mm to the surface of the roller by the adjuster nuts (15). When soil is gathered at
the roller shell, the scrapers must be adjusted.
•Do not ride on the power harrow during work or transport!
•Do not stand in the working area of the power harrow!
•Only start the power harrow when all guards and protective devi-
ces are in position!
•Do not leave the tractor without first lowering the power harrow to
the ground, disconnecting the PTO, switching off the tractor engine and remo-
ving the ignition key!
Further instructions regarding the safe operation of the power harrow are listed in
the „safety instructions“ section of this book.

17
8 ROLLERS
The rotary cultivators GRANIT are available with Tube bar rollers; Flexi-Coil rol-
lers; packer rollers and Trapezring rollers. Due to that a wide range of rollers are
available for different requirements.
Packer roller ZPW with standard scra-
pers, hard faced scrapers or synthetic
scrapers. The scrapers must be ad-
justed carefully to prevent a clogging of
the roller. See also section 7.5.
Flexi-Coil rollers with scrapers. The
scrapers must be adjusted so that the
inner edge shows a distance to the
outer edge of the roller of 8 mm. Ensu-
re that the scrapers can turn always
easily.
Tube bar roller RSW Trapezring roller TRW
After the daily work., clean the rollers carefully by removing the soil. Only this will
ensure a proper function and a long life time.
Grease the bearings regularly.
The working effect of the rollers will be improved in combination with a levelling
bar which is fitted between power harrow and roller.

18
9 A-FRAME
The A-frame (KD) is used for simple attach-
ment of the seed drill. The turnbuckle enables
an adjustment of the centre of rotation (DP).
The turnbuckle must be adjusted so that the
seed drill is in the working position which is
prescribed by the manufacturer concerned.
10 HYDRAULIC DRILL LINKAGE
10.1 Assembling the linkage
The linkage is mounted onto the headstock of
the power harrow by means of bolts - which
must be tightened carefully. The hydraulic ram
mounting plate must also be fitted as shown
and the bolts fully tightened.
In order to keep the centre of gravity of any
power harrow / drill combination as close to
the rear of the tractor as possible, adjustment
is provided in the form of holes (16) in the lo-
wer connecting links (17) and the upper con-
necting link (12).
The lengths of the upper and lower connecting links must be kept equal, thus
maintaining a parallel lift for the drill.
The catch hooks (19) are adjustable vertically and are connected to the mounting
frame (20); their position from the roller is adjustable.
10.2 Attaching a mounted implement e.g. drill
To attach a mounted implement the spring clips (21) are removed, and the locking
bars (22) are lifted and locked by means of the spring clips. After mounting the
implement the locking bars are once again lowered and secured.
The bolt (23) is used to connect the implement top link.
During work the check valve (24) must be opened.
If a double acting ram is fitted, the tractor hydraulics must be set in the „float“ po-
sition. If, on the other hand, a single acting ram is fitted, the tractor hydraulics
must be set in the „lower“ position.
For transport with the mounted implement raised, the check valve (24) must be
closed. When doing so, ensure that the lower connecting links (17) are pressed
firmly against the stop (25). This stop is bolted to the headstock and is adjustable.
The forward position must be selected for the double acting ram and the rearward
position for the single acting ram.
Table of contents
Other LEMKEN Tiller manuals
Popular Tiller manuals by other brands
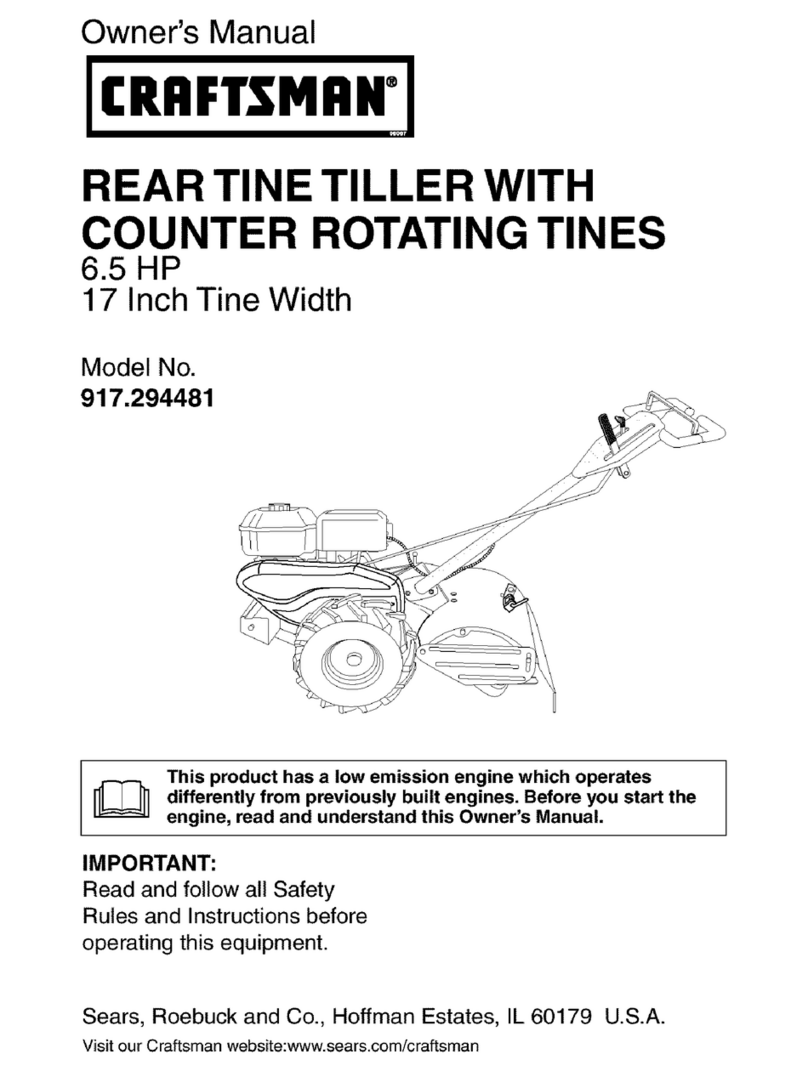
Craftsman
Craftsman 917.294481 owner's manual
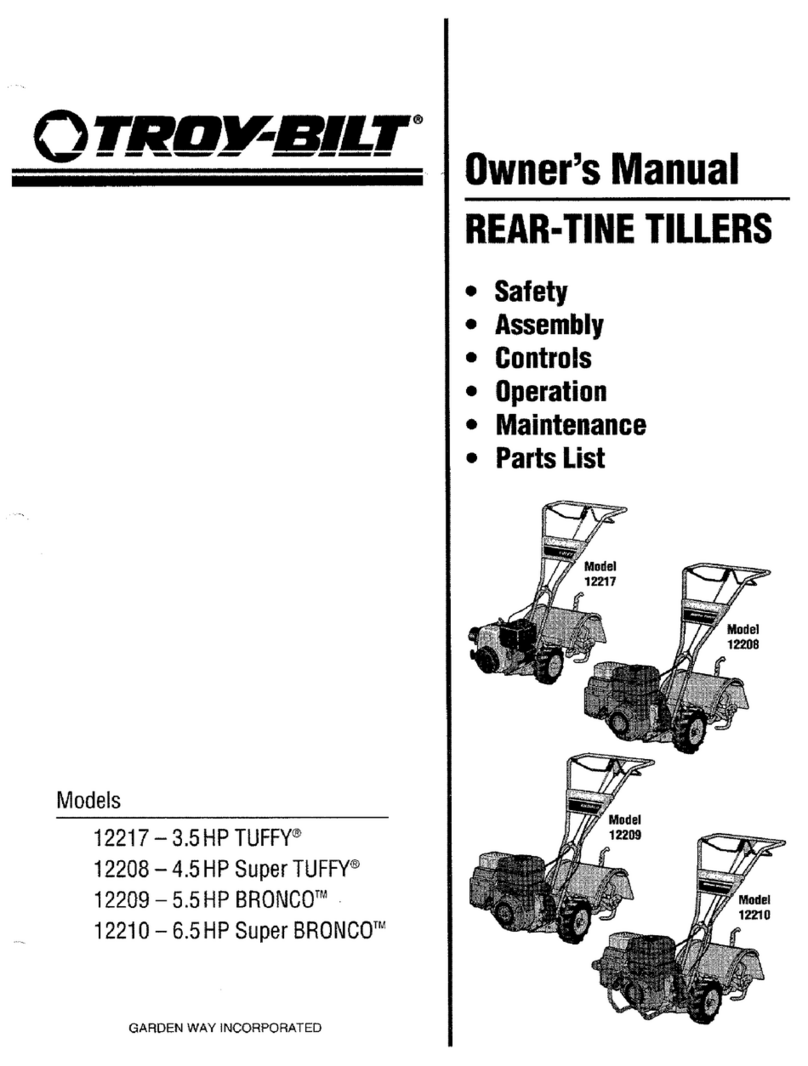
Troy-Bilt
Troy-Bilt 12208 owner's manual
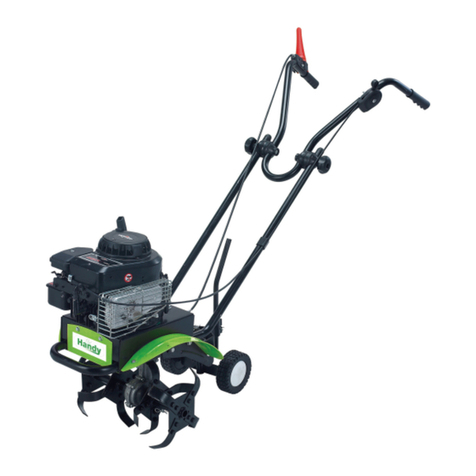
The Handy
The Handy THTILL3.5 Operator's manual and parts list

Brinly-Hardy
Brinly-Hardy Thatcher 1690819 Operator's manual
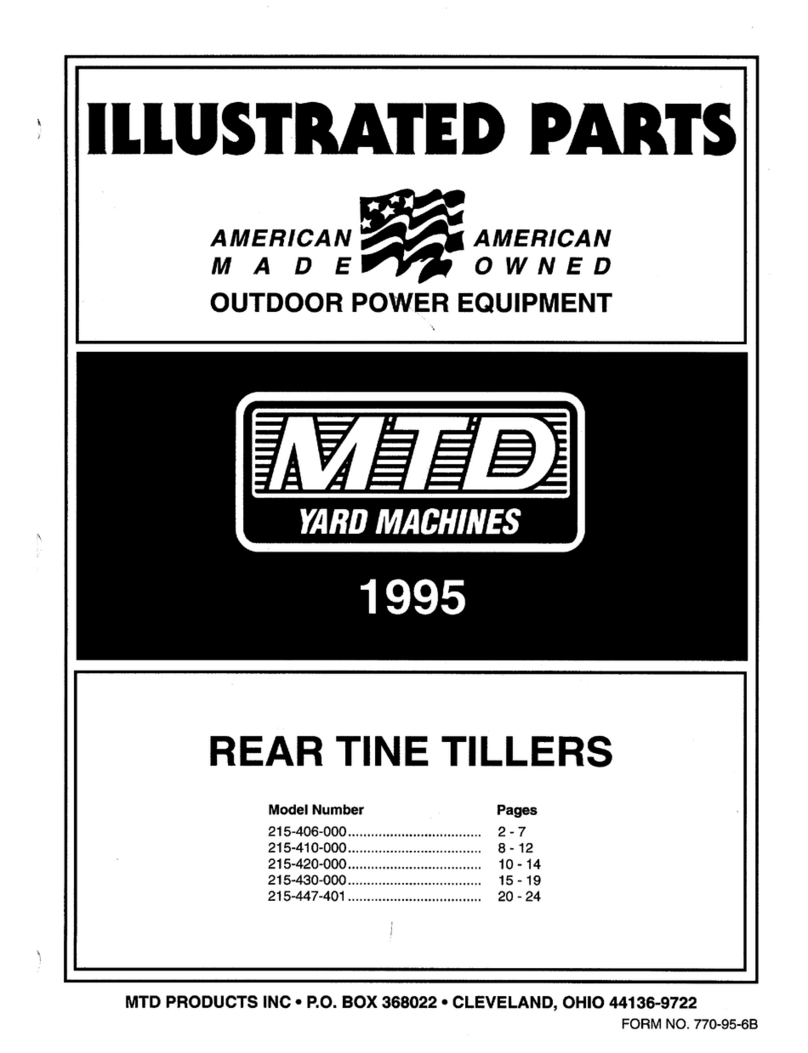
Yard Machines
Yard Machines 215-406-000 Illustrated parts list
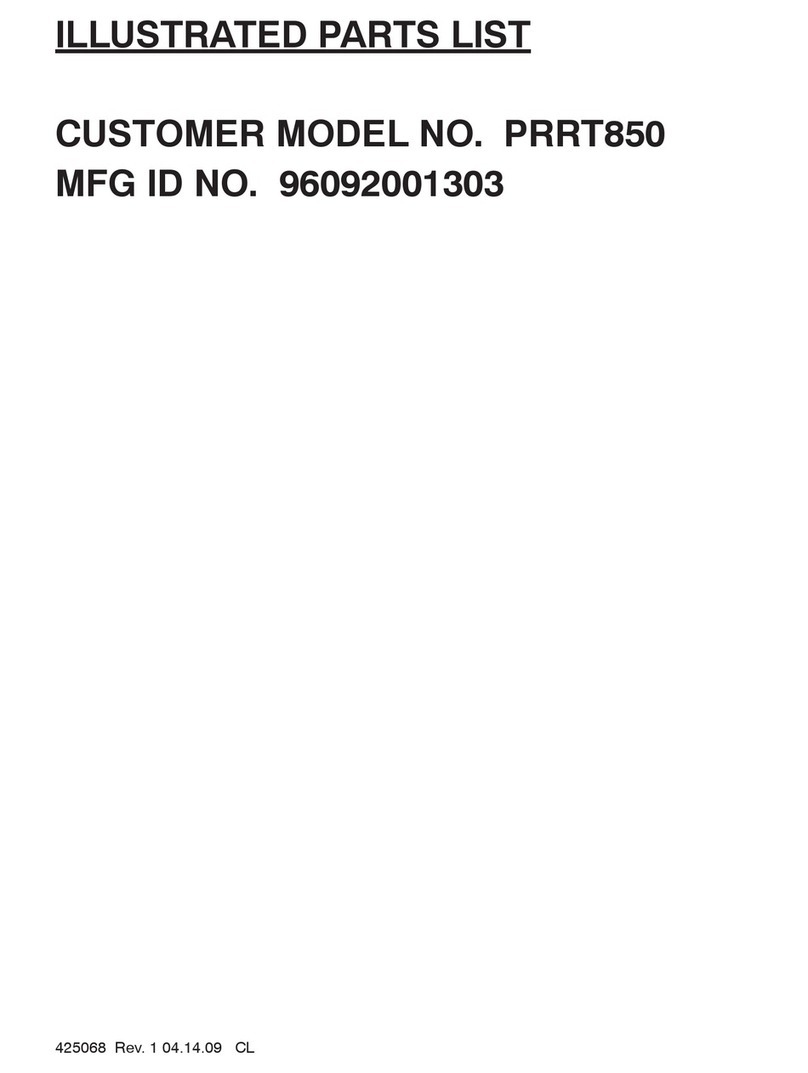
Poulan Pro
Poulan Pro 96092001303 Illustrated parts list