LESA Messtechnik PSMEGA 1 User manual

PSMEGA 1
Microcontroller, Single pump control
Options
FS PSMEGA1Freiluftsäule Messglocke V4A Schwimmschalter Tauchsensor
Operating Manual
www.lesa.de
PSMEGA1_2v0 / 04092020
LESA Messtechnik
Hegholt 59
22179 Hamburg
Germany
Phone +49 40 641 00 41
Fax +49 40 641 18 36

Table of contents
1.0 General
1.1 About this document
1.2 Safety
1.3 Identification of information in the operating instructions
2.0 Warning and safety information
2.1 Applications
2.2 Personnel qualifications
2.3 Safety instructions for the operator
2.3.1 Electrical work
2.4 Dangers of non-compliance with safety information
2.5 Operating instructions
2.6 Unauthorised modification and replacement part supply
2.7 Impermissible use
2.8 Transport and storage
3.0 General product description, properties and optional functions
3.1 Product description
3.2 Properties
3.3 Optional functions and/or components
4.0 Configuration, control elements and function display
4.1.0 Symbols on the front panel
4.1.1 Display
4.2 Operating elements
4.3 Function display via light-emitting diodes
4.4 Display
5.0 Configuration menu, images and notes on configuring the parameters
5.1 Table of possible settings.
5.2 Supplements to the individual items in the configuration menu
6.0 Error reports in the display, potential errors, assistance
6.1 Table of possible fault messages
6.2 The settings in the menu cannot be changed
6.3 Motor contactor monitoring
7.0 Installation, pneumatic and electrical connection and connection of 3~ and 1~ motors
7.1 Installation
7.2 Hose attachment
7.3 Electrical connection of power supply and pumps
7.4 Fault signaling outputs
7.5 Input for float switch dry run protection
7.6 Connection examples for the operation of the switching device with float switches
7.7 External level sensor 4 – 20 mA
7.8 Analogue outputs
7.9 Network-independent alarm
8.0 Test mode without pump
8.1 To test the control system without the pumps, please note the following
9.0 Technical data
10.0 Norms
11.0 Annex: Status LED – GSM module
12.0 Annex: Terminal connection diagrams, note for the lid and section cover
PSMEGA 1
www.lesa.de 2

1.0 General
1.1 About this document
These operating instructions are part of the product. They must be
kept in the vicinity of the product at all times. The careful observance
of these instructions is the precondition for the proper use and the
correct operation of the product. The operating instructions
correspond to the version of the product and the latest state of the
underlying safety-related standards.
1.2 Safety
These operating instructions contain essential information that must
be observed during the installation and operation. For this reason, it
is imperative that these operating instructions are read by both the
technician as well as the responsible operator before installation and
commissioning. Not only must the general safety instructions be
observed that are listed under this main item “Safety”, but also the
specific safety instructions inserted under the following main points
with hazard symbols.
1.3 Identification of information in the operating
instructions
General hazard symbol
Hazard due to dangerous electrical voltage
Important information
2.0 Warning and safety information for the
installation and commissioning of the
control
2.1 Fields of application, proper use
This switchgear has been designed for domestic and municipal
sewage, wastewater and rainwater pump stations.
Please note the following in regard to the controlling of
pumps operated in an explosive area: The switchgear itself
must be installed outside of the explosive area.
The controls are suitable for wastewater submersible motor pumps
of the type of protection “d” in zone 1 of the mains. The operating
manuals of the pumps must be observed.
When using external 4 - 20 mA level sensors and float switches
installed in an explosive area, it will be necessary to use components
with the requisite certifications.
It is essential for the switching of three-phase current motors that
both the setting of the electronic motor current monitoring as well
as for the settings of mechanical motor protection switches that the
limit values provided below are adhered to.
2.2 Personnel qualifications
Personnel tasked with the installation, commissioning and
maintenance of the switchgear must hold the requisite
qualifications.
2.3 Safety instructions for the operator
Observe the existing regulations governing accident prevention, the
VDE specifications and stipulations of the local energy supply
company. When opening the device (removal of the panel or
terminal cover) or working on the pumps, the control must be
switched off from the power supply through the fuse or a separate
main switch.
Due to safety reasons, the unused cable glands must be sealed with
blanks or blind caps.
HAZARD due to dangerous voltage
When working on the open switchgear,
there is a risk of death from electric shock. For all work on the open
device (removal of the cover or terminal cover) or work on the
pumps, the control must always be switched off via the backup fuse
or a separate main switch and secured against being switched on
again. This work may only be carried out by a qualified electrician.
2.3.1 Electrical work
HAZARD due to dangerous voltage
There is a risk of death due to electric shock in all work on open
switchgear. During all work on the open device (removal of the panel
or the terminal cover) or when working on the pumps, the control
must be switched off from the power supply through the fuse or a
separate main switch and secured against reactivation. To
disconnect the battery, pull out the red + plug and isolate the
connection with the yellow cap. This work may only be carried out by
a qualified electrician.
Beware of moisture!
The device can be damaged by penetration of moisture. When
installing, pay attention to the permissible humidity and ensure a
flood-proof installation.
For the connection, refer to chapter 6.0 "Connection". The technical
information must be observed.
2.4 Dangers of non-compliance with safety
information
The non-compliance with the safety information can lead to
endangerment for persons and product/system. Non-compliance
with the safety information can lead to the loss of all rights for
damage compensation.
2.5 Operating instructions
When installing, commissioning and maintaining the switchgear
observe the operating instructions. Always observe the limit values
cited in the manual.
A fusing on the mains side of max. 3 x 16 A must be
performed.
Standard version
5,5 KW
contactors
Three
-
phase current
400 V
Max. 12 A
Alternating current
230 V
Max. 12 A
PSMEGA 1
www.lesa.de 3

2.6 Unauthorized modification and replacement part
supply
Changes to the product are only permissible in coordination with the
manufacturer. In the interest of safety, use original replacement parts
and accessories authorized by the manufacturer. Using other parts
can void liability for the resulting consequences.
2.7 Impermissible use
The operational safety of the product supplied is only guaranteed for
proper use as laid out in section 2.1 of the operating instructions. The
threshold values specified on the data sheet must be met in all cases.
2.8 Transport and storage
Store and transport the switchgear in such a manner that damage as
a result of shock, impact and temperatures outside the range of -
30 °C to +60 °C are excluded.
3.0 General product description, properties and
optional functions
3.1 Product description
The pump control PSMEGA 1 is used for the level control of liquid
levels. The filling level is optionally determined via dynamic pressure,
bubbler system, external sensor (4 - 20 mA) or float switch. The motor
contactor directly controls two pumps with a max. output of 5.5 kW.
Furthermore, 2 relay contacts are available for the output of fault
messages. Control and configuration are extremely easy. Switching
points, times and motor current monitoring are configured using a
digital potentiometer. All values can be queried on the LC display.
LEDs indicate operational states and fault messages. There are
further keys available for the Manual - 0 - Auto functions.
3.2 Properties
- Graphical display
(display of the level and motor current using a bar graph)
- Thermal and electrical monitoring of the pump
- Manual - 0 - Auto functions
- Pump deactivation via switch-off point and overrun
- Acknowledge button
- Electronic 3~ monitoring of the motor current
- Runtime monitoring
- Rotating field and phase failure control (activate in the menu)
- Forced switch-on of the pump
- Variable staggered start (delayed switch on)
- Internal audible alarm
- Collective fault alarm fixed voltage and potential-free
- High water alarm potential-free
- Memory, number of pump starts
- Operating hours counter
- Ammeter
- Pump change
- Forced switchover
- High interference immunity
- Easy to operate
- ATEX mode
- Service mode
- Input for float switch dry run protection
- Analogue outputs 0-10 V and 4-20 mA
- Fault memory stores the last 4 faults
- Automatic display illumination switch off (after 30 seconds) can be
disabled
- Mains-independent alarm (9 volt battery, not included in delivery)
- In manual operation it shuts off automatically after a running time
of 2 minutes
- Level detection optionally via internal pressure transducer,
external 4 - 20 mA sensor or float switch
- Measuring range of the external 4 - 20 mA level sensor can be
selected via the menu in the range of 0 - 10 m
- Connection to remote control systems via digital and analogue
inputs and outputs
- All settings and various error messages are saved in non-volatile
memory
- All functions of the previous version have been maintained
- Spare inputs for telecontrol module, timer switch or other
(are only integrated in the program when required)
- parameters can be saved on an SD card and imported again
- an event log is written on the SD card
NEW:
- Monitoring of all three phases
- Motor contactor monitoring
3.3 Optional functions and/or components
(only included in delivery if specified specifically in the
order)
- External locking (the dry run protection is omitted here)
- Additional pressure sensor for redundant flood alarm with a
switching on of the pumps
- GSM modem
- RTU-MOD bus
- Bluetooth module
- Mains-independent alarm
- With the PSMEGA 1-E version, the control is also optionally
available with a motor protection switch according to EN 60947,
main switch according to EN 60947, ground fault circuit interrupter
or EX barrier (not together with motor protection switch) available.
4.0 Configuration, control elements and
function displays
4.1.0 Meaning of the symbols on the front panel
LED red – Fault / high water alarm
LED yellow – pump / overrun operation
LED green – Manual / automatic operation
LED blue – Status GSM
PSMEGA 1
www.lesa.de 4

Pushbutton switch – Manual operation
Pushbutton switch – Off
Pushbutton switch – Automatic operation
Pushbutton switch – Selection / acknowledgement
Rotary knob – Display
4.1.1 Display
All information and settings can be queried using the digital
potentiometer display. If a setting is to be changed, the regulator is
adjusted until the corresponding setting appears on the display.
Now press the select / cancel button. The value last saved will start to
blink. The digital potentiometer display can now be used to change
the setting. Quick turns will change the values more rapidly, while
slow turns make it possible to make more precise changes. Once the
desired value has been reached, use the select / cancel button to
confirm. The value will stop blinking and be stored. Check all values
prior to commissioning. The display will automatically return to the
default setting after 20 seconds.
The operating hours and pump starts are counted
continuously, it is not possible to adjust or reset them.
4.2 Operating elements
Pressing the digital potentiometer will query all settings as
well as error messages, operating hours, number of pump
starts and motor current. Moreover, the settings are
performed using the digital potentiometer. If the knob is not moved
for more than 20 seconds, then the display will jump back to the
default setting. (see above, Configuration chapter)
Pressing this button will confirm the errors overcurrent,
pump without load and thermal error 2 after removal of
the cause. In the event that an error should continue to be
present, then only the common error report relay and the piezo
buzzer will be shut off. This also applies to all other errors and the
high water alarm. Settings can still be changed using the button.
Pressing this button will manually put the pump into
operation. The green LED will blink. If the pump is being
run via the manual function, then it will automatically shut off after
2 minutes and the green LED will flash irregularly.
The automatic and manual operation are shut down using
this button. The green LED is off.
The pump is switched based on the level. The green LED is
lit continuously.
If power is interrupted during manual mode, then the
control system will return to the automatic mode. The
operation modes “Auto” and “0” are stored in non-volatile
memory.
4.3 Function display via light-emitting diodes
LED - red = Fault, high water alarm
LED - solid yellow = The pump is in operation
LED - flashing yellow = The pump is in operation
via the overrun function
LED - solid green = Automatic mode
LED - flashing green = Manual mode
LED - irregular green flashing = Manual mode
has shut off after 2 min
LED - blue: (Function only with module)
Continuous flashing= The board is in the initialization
Phase
Continuous light = The board is initialized and has
connected to the provider
Single Flash,
Long break = The modem does not answer
Double Flash,
Long break = The SIM card cannot be found
Triple Flash = The GSM signal strength is too weak
4.4 Display
In the upper area of the display, there is a bar graph for the level (L)
and two bar graphs for the current of the pumps (I). In the display’s
basic setting, the level and the operating hours are additionally
displayed in numbers below the bar graph displays. If the pump is in
operation, the motor current will be displayed. If any disruptions
occur, then they will be displayed alternatingly on the display’s
bottom line.
4.4.1 Automatic deactivation of the background
lighting:
If no further settings are performed on the device, the background
lighting switches off automatically after 30 seconds. As soon as the
rotary switch or one of the pushbutton switches is actuated, the
background lighting switches on again. This function can be disabled
via the menu and then the background lighting remains switched on.
PSMEGA 1
www.lesa.de 5

5.0 Configuration menu
5.1 The following table shows the configuration possibilities. The display’s top line shows the
option, the bottom line is the value that can be changed.
1. line of Display
Option for Setting
Explanation
Last fault 1-4 Delete value The last 4 errors remain stored in the non-volatile memory and can be deleted
in the position “Last fault 1” using the acknowledge pushbutton.
Level ON 0 – 100 (200) cm The value determines start level of pump
Level OFF 0 – 100 (200) cm The value determines stop level of pump
High water level 0 – 100 (200) cm Once predetermined value is exceeded, the collective fault report relay and the
high-water relay are activated
Running time max 0 – 60 Min. The value 0 deactivates this function. If the value is set between 1-60 min. the
pump shuts off if the set operating time has been exceeded without
interruption
Start delay 0 – 900 sec. After a power outage the pump will only start after the pre-set time is over. The
display will show the remaining time.
Stop delay 0 – 180 sec. After the Stop level is reached, the pump will keep running until the pre-set
time is over.
Current limit 0.3 – 16.0 A If the pump exceeds the set power intake for a certain time, it shuts off. The
display shows: Overload. The pump will only be re-activated after the button
“Quittung” has been pressed
Inspection
All xxx Days Is deactivated,
90, 180 and 365 Days
The setting con only be changed by the service personnel.
Force activation Is deactivated,
0 – 10 sec.
Is activated = If the pump has not been activated for 24 hrs, it will automatically
run for duration of the set time.
Acoustic alarm Is deactivated,
Is activated
Is activated = In case of a malfunction the internal piezo-buzzer will sound
Intermitt. alarm Is deactivated,
Is activated
Is activated = The fault information-relay will be synchronized
Instead of a flashing light it is possible to use a more economic steady burning
light
Thermal fault 1 Is deactivated,
Is activated
Is deactivated = There is no bimetallic contact (alarm contact) connected to
terminal 12, 13.
Rot. field fault Is deactivated,
Is activated
Is activated = in case the phase sequence is wrong or if L2/L3 have been missed
an alarm will be triggered and the pumps cannot be activated.
3~ Monitoring Is deactivated,
Is activated
Is activated = The motor current of all 3 phases is monitored.
Is deactivated = Only L1 is monitored, 230 V operation
Light off autom. Is deactivated,
Is activated
If no further settings are actuated on the device, the background lighting
switches off automatically after 2 minutes.
ATEX - Mode Is deactivated,
Is activated
Is activated = If no liquid can be measured by the level sensor the pumps
cannot be activated. This is valid for the Manual mode as well as the Forced
activation and the remote-control systems.
Service - Mode Is activated,
Is deactivated
Is activated = All settings can be adjusted
Is deactivated= Settings are shown but cannot be adjusted
Level Control Intern. converter
Floating switch
4 – 20 mA Interface
Determination of level by impact pressure or air supply.
Determination of level by floating switch
Determination of level by external sensor ( 4 – 20 mA)
Bar Level max. 0 – 1000 cm The resolution of the bar graph display for the level can be adjusted. The max.
value corresponds to the full deflection of the display..
Bar Current max. 0 – 1000 cm The resolution of the bar graph display for the level can be adjusted. The max.
value corresponds to the full deflection of the display..
20mA =>Level 0 – 1000 cm The effective range of the external level sensor can be adjusted
Language da-de-en-fr-it-es-pt-
nl-no-pl-cz
The displayed language can be adjusted
PSMEGA 1
www.lesa.de 6

5.1.1 Menu items factory settings, data import and
export
5.2 Supplements to the individual items in the
configuration menu
5.2.1 Start Delay
The delay configured will only be active after a loss in power
(staggered start in projects). For each further start, the pumps will
immediately turn on when they are triggered via the level.
5.2.2 Lowest level configurations (On/Off)
If a switch-on point lower than 5 cm is selected, then the software will
automatically use 5 cm as the switch-on point. If a switch-off point
lower than 3 cm is selected, then the software will automatically use
3 cm as the switch-off point. This also applies to starting overrun
time, which will then start at 3 cm. This is necessary for the safe
operation of the switchgear system.
5.2.3 Stop Delay, Overrun
Overrun facilitates draining below the level sensor, e.g. for dynamic
pressure systems.
5.2.4 Runtime monitoring, Running time max.
The menu can be used to access the item maximum runtime. In the
default setting, this value is set to zero, i.e. the function is disabled.
When a value of 1 – 60 minutes is set, then
a deactivation of the pump occurs when the pump runs without
interruption for longer than the set value. Moreover, an alarm will be
triggered and a corresponding error report will be shown on the
display. The pump will not run again until the error has been
confirmed. The runtime monitoring applies to both the automatic as
well as the manual mode.
5.2.5 Current monitoring (max. current)
The nominal current of the corresponding pumps can be set
immediately. The software in the control adds a certain percentage
to the set value to compensate tolerances. The triggering occurs
according to an I² / t function and with this, the increased initial
current of the pump is taken into account.
5.2.6 Inspection
The PSMEGA 1 can issue a message on the display on when servicing
is to be performed. The configuration possibilities are 90, 180 or
365 days. The function can also be turned off at this point in the
menu (factory settings).
Only service personnel are able to change or reset the
settings.
5.2.7 Th. fault 1, Th. fault 2
For pumps whose temperature monitoring consists of only one
bimetallic contact per pump, thermal error 1 can be deactivated
accordingly in the menu. Thermal error 2 cannot be turned off in the
menu.
5.2.8 Error memory, Last fault
The last 4 errors that occurred remain stored in non-volatile memory
and can be retrieved in the menu under “Last fault”. Caution Last
fault 1 is the last fault that occurred. If “Last fault 1” is called up in the
menu, the last errors can be deleted from the memory with the
acknowledge button.
5.2.9 Rotary field error
The rotary field monitoring monitors both the phase sequence as
well as the lack of a phase. The pumps are locked in the event of a
phase error, an alarm is issued and the message “Rotary field error”
appears on the display. The rotary field monitoring can be activated
and deactivated via the menu.
The rotary field monitoring must be switched during
the operation of 1~ motors.
5.2.10 3~ monitoring
Display, evaluation and monitoring of the motor current on all three
phases. In the event of the deactivation of the 3~ monitoring, only a
single phase (L1) is monitored. This enables the operation of 1~
motors. (See page 10, point 7. Electrical connection)
5.2.11 ATEX – Mode
ATEX mode has to be activated for pumps implemented in EX zones.
ATEX mode impedes the pumps from being turned on via manual
function, via forced switch-on or via remote control system until the
switch-off point is met. If the pumps are started via the overrun time
or manual function while the switch-off point is exceeded, then
draining can occur below the switch-off point.
The manual function will be automatically interrupted after
2 minutes. When the ATEX function hinders pumps from turning on,
the display will show the report “ATEX: Level below switch-off point.”
5.2.12 Service – Mode
The default setting is for service mode to be activated, i.e. all setting
can be changed. When the service mode is turned off in the menu,
the settings can only be queried using the digital potentiometer.
When the service mode is deactivated, no settings can be
changed other than the local language.
Menüpunkt
Erklärung
Preferences reset
All settings can be reset with this function.
Attention: Pump starts, operating hours,
error memory and maintenance status are
preserved.
FatFS: Filename
An input menu can be opened here to assign
a file name. Now the current settings and log
files can be saved under this file name.
FatFS: Read
The file with the setting parameters is read
by the SD card
FatFS: Write
The file with the current parameters is
written by the SD card.
FatFS: Log
The operating hours, pump starts an
d error
notifications are transferred to the memory
card.
PSMEGA 1
www.lesa.de 7

5.2.13 Level control
It can be selected whether the control system will run via the internal
level sensor (dynamic pressure, bubbler system), an external 4 -
20 mA level sensor or a float switch. The input for the high water
alarm (terminal 19 / 20) is always active and can be used as a
redundant system. When using external 4 - 20 mA level sensors and
float switches installed in an explosive area, it will be necessary to use
components with the requisite certifications.
5.2.14 20 mA => Level
This setting adapts the switch points and the display of the level to a
connected external 4 - 20 mA level sensor. The processor converts
the input signal such that the correct level is displayed. When the
measurement range for the 4 - 20 mA sensor is changed in the
configuration menu, the switch points will have to be re-configured,
as they will have changed determined by the system. Thus, the
correct order will always be to first configure the sensor’s
measurement range and then the switch points. The corresponding
regulations must be observed for the use in the EX zone, i.e. a 4 -
20 mA sensor with corresponding certification and a matching EX
barrier. If the switch points are outside the level sensor’s configured
range, then the message “Check switching points” will be shown.
5.2.15 Bar Level max. / Bar Current max.
In order to allow for a practical resolution of the bar graph display,
the maximum value of the respective display can be set here. If AUTO
is selected in the menu item, the maximum value of the respectively
set level or the max. current will be used automatically.
5.2.16 Local language
The scope of delivery includes German / English / French / Italian /
Spanish / Portuguese / Dutch / Swedish / Norwegian / Danish / Polish
/ Czech. The country language can also be changed when service
mode is deactivated.
5.2.17 Menu items data import and export
The PSMEGA 1 offers the option of writing and reading
configuration files:
5.2.18 FatFS: Filename
At this point, the file name is assigned for the configuration and log
files. The file name PSMEGA 1 is preset. A code page can be opened
by pressing the select/ acknowledge button. A character can be
selected with the knob and accepted with the select/acknowledge
button.
Delete characters
Save the file name and exit the menu
Leave menu without saving the changes
5.2.19 FatFS: Read
By pressing the select/acknowledge button, a configuration file with
the set name is read from the memory card and the settings are taken
over. If there is no corresponding file on the memory card or if no
memory card is inserted, a corresponding error notification will
appear in the display.
5.2.20 FatFS: Write
By pressing the select/acknowledge button, the current settings are
written on the memory card. The configuration file receives the
previously entered name. If a memory card is not in the holder, a
corresponding error notification will appear. If a file with the same
name is already on the card, a prompt will appear asking if the file
should be overwritten.
5.2.21 FatFS: Log
By pressing the select/acknowledge button, a log file is written on
the memory card with the current operating hours, pump starts and
errors. The log file can be read with any text editor.
Memory card size up to 64 GB!
Menüpunkt
Erklärung
FatFS: Filename
An input menu can be opened here to assign a
file name. Now the current settings and log
files can be saved under this file name.
FatFS: Read
The file with the setting parameters is read by
the SD card
FatFS: Write
The file with the current parameters is written
by the SD card.
FatFS: Log
The operating hours, pump starts and error
notifications are transferred to the memory
card.
PSMEGA 1
www.lesa.de 8

6.0 Fault messages, possible malfunctions, corrections
6.1 Fault messages on the display
Message on Display
Possible cause
Correction
Thermal Fault 1 The controller contact of the
according pump initiates.
If the pump in use does not come with the required thermal
motor protection contact the mode needs to be deactivated in
the menu (compare to 5.2.7.Thermal Fault 1, Thermal fault 2).
Check the pump. If it is plugged, clean out the foreign matter.
Check the motor for sufficient cooling (dry run).
Thermal fault 2 The limiting contact of the
according pump initiates.
If the pump in use does not have the required thermal motor
protection contact every pump that is used needs to be bridged.
(compare to 7.3.3 Thermal motor protection contact).
Check the pump. If it is plugged, clean out the foreign matter.
Check the motor for sufficient cooling (dry run).
After the pump has cooled off, push the button “Quittung” in
order to unlock the pump.
Pump off Phase 2 is missing or the control
unit is being operated without
charge.
Check feed-in, pump cables, and pump
High-water-Alarm The level has exceeded the
flood setting
Check pump for mode or high-water level
High-water switch Contact for the high-water
switch has closed
Check if pump/ floating switch are functioning
Reverse signals
start/stop level The settings for start and stop
levels interfere.
Check level settings
Reverse signals
start/flood level The settings for high-water
alarm and start level interfere
Check settings for level
Runtime error Pumps run without interruption
for longer than the time set.
Check function of pump
Floating switch
malfunction Validation of floating switches,
wrong order
Check if floating switch is functioning and check if it is
connected to power correctly
Dry run protection
activated Contact for dry run protection
has been activated
Check functioning of pump / floating switch
Interface < 3 mA Signal of external level sensor
lower than 3 mA
Check level sensor, Ex-barrier, and electrical connections
Please check control
settings The effective range of the
external level sensor has been
changed. The level settings lie
outside the effective range.
Check settings for level
Rotating field One or two phases are missing,
or rather the rotating field is not
correct
Check if all 3 phases are adjacent and if the rotating field is
correct.
ATEX: level less than
stop level The ATEX mode has been
activated and the level lies
below the stop level of the
chosen pump.
Before being able to activate the pumps, the level in the Ex-area
needs to rise over the stop level of the pump.
As long as the pumps are not in the Ex-area, the ATEX mode can
be deactivated in the menu.
PSMEGA 1
www.lesa.de 9

6.2 The settings in the menu cannot be changed
Check in the menu whether the service mode has been activated.
6.3 Motor contactor monitoring
When the contactor is not requested by the control and nevertheless
a current is measurable on one or more phases, then the error
message “Contactor error” will appear in the display and the audible
alarm will sound.
7.0 Installation, electrical connection
7.1 Installation
The control unit PSMEGA 1 is placed in a control box that measures
250 x 225 x 115 mm (H x W x D) with screw fittings and air
connection). There are 4 drill holes on the switch cabinet for
mounting, which become visible when the cover is opened.
7.2 Hose attachment
As standard, a hose screw connection 8/6 mm is delivered for the
hose connection. Optionally, the switching device can be delivered
with other hose screw connections. The subsequent replacement of
the hose connection is also possible. The hose screw connection
must feature an internal thread of G1/8" towards the unit. During
replacement, it is important that a 14 mm spanner is used to secure
the corresponding nut. In any case, the threaded connection must be
used in combination with a suitable sealant.
7.3 Electrical connection power supply and pumps
The electrical connection must be performed by a qualified
electrician in accordance with the applicable VDE regulations.
HAZARD due to dangerous voltage!
Improper handling of electrical work may result in a risk of death
due to electrical voltage!
A time-lag fusing on the mains side of max. 3 x 16 A must be
performed.
Mains connection (3~) PE , L1, L2, L3, N (image 1a in the
annex)
The connecting terminals have been designed for a max. cable cross
section of 4 mm². Attention must be paid that a right rotary field is
created. The terminals are labelled L1, L2, L3, N. The PE terminals are
implemented as a brass rail.
7.3.1 Connection of the pump:
The connections L1 L2 L3 of the pump are directly attached to the
motor contactor. The protective earth conductor is connected to the
remaining PE terminal. The bimetallic contact, which unlocks the
pump after it has cooled down, needs to be connected to terminal
12/13; the bimetallic contact that unlocks the pump after pressing
the “Quittung” button needs to be connected to terminal 13/14 on
the upper circuit board. (In case Temp.1 is not being connected,
thermal fault 1 needs to be deactivated in the menu).
To operate 1 ~ motors (230V AC) a bridge between input
terminal N an L3 are necessary.
7.3.2 Power supply of the pumps (1~)
The pump is connected to contactor T1 = L and T3 = N
7.3.3 Protective winding contacts
Regulator contact Temp 1 / terminal 12/13
The pump is released automatically after cooling down.
Limiter contact Temp 2 / terminal 13/14
The pump is only released after actuation of the acknowledge push
button.
This temperature monitoring must be used for pumps
located in the EX area.
When Temp. 1 is not used, then the function must be disabled in
the menu (see above chapter 5.2.7.).
When Temp. 2 is not used, then a wire jumper must be used from
terminal 13 to 14.
For pumps, in which the bimetallic contact has been switched in such
a manner that this directly interrupts the current of the pump, the
message “Without load” appears, when the bimetallic contact has
been triggered. The pump can only be taken into operation again
following the acknowledgement.
The inputs of the controls for the thermal errors are designed for the
evaluation of the protective winding contacts. Separate evaluation
devices must be used for motors with embedded temperature
sensors (e.g. PTC resistor) as thermal protection.
PSMEGA 1
www.lesa.de 10

7.4 - 9 Electrical connection of the fault signalling
outputs and the signal inputs (image 2 annex)
7.4 Fault signalling outputs
Terminal 1 / 2 / 3 = High water alarm, potential-free, 2 / 3 closed in
case of alarm.
Terminal 4 / 5 / 6 = Overall failure, potential-free, 5 / 6 closed in case
of alarm
Terminal 7 / 8 = Relay output for every failure potential-bound.
In case of an alarm there are 230 V/AC adjacent
(this port is protected by a micro-fuse 1 A T).
7.5 Input for float switch dry run protection
Terminal 10 /11 = Dry run protection
Polarity of the terminals: 10 = positive and 11 = negative (24 V/AC
10 mA)
When a float switch is connected to terminal 10-11, then it can be
prevented that the cutting unit or impeller appears from the
medium. The dry run protection is active in both automatic as well as
manual operation.
For use in the EX zone, the corresponding requirements
must be complied with.
This input is optionally also used for locking the unit when a specific
program has been agreed upon.
7.6 Connection examples for the operation of the
switching device with float switches
The display shows which switch is connected. Closing contacts must
always be used. “Float switch” must be selected in the menu under
“Level control”. The input for the high water alarm (terminal 19/20) is
always active.
Operation with a common line of float switches is not possible.
For use in the EX zone, the corresponding requirements
must be complied with.
7.7 External level sensor 4 – 20 mA
“4 - 20 mA interface” must be selected in the menu under “Level
control”. An external sensor 4 - 20 mA two-wire technology (passive
sensor) can be connected to the terminals 25 (-) and 26 (+). The
sensor is supplied with a stabilized direct voltage of approx. 24 volt.
In the delivered state, the measuring range of the level sensor is set
in such a manner that it matches the measuring range of the internal
pressure sensor. In the event that the level sensor should be
connected with a different measuring range, then the corresponding
setting must be changed in the menu (see section 5.2.14). The output
is active, i.e. the sensor is supplied with voltage by the control.
For use in the EX zone, the corresponding requirements
must be complied with.
In the event of the connection of an active sensor (external voltage
supply), the positive line of the sensor must be connected to the
negative terminal (25) of the input. The negative line of the sensor
must be connected to the common internal earth (negative),
terminal 28 or 30 (negative of the analogue outputs).
7.8 Analogue outputs
The analogue outputs are intended for the connection to the
control system. The signals change proportionally to the level.
0 - 10 V = Terminal 27 (+) and 28 (-) resistant up to
max. 10 mA
4 – 20 mA = Terminal 29 (+) and 30 (-) burden max.
250 ohm
The length of the lines for the analogue outputs must not exceed
1.50 m, and must not be laid along with lines prone to interference.
7.9 Network-independent alarm:
By using a 9V block battery, a mains-independent alarm message can
be issued in the event of a power failure. A continuous acoustic signal
is emitted as an alarm which cannot be acknowledged, even if the
acoustic alarm has been deactivated in the menu. To deactivate, the
battery must be disconnected.
Please pay attention to the correct polarity when inserting the
battery!
To ensure that it functions properly, the battery must be fully
charged before being inserted or it must be charged in the
switchgear for 24 hours.
Attention! Under no circumstances should normal
batteries be used.
The following batteries may be used:
Nickel metal hydride accumulator (NiMH)
PSMEGA 1
www.lesa.de 11

8.0 Test mode without pump
8.1 In order to test the control unit without pumps
the following needs to be considered
- It is sufficient to connect N1 and L1
- Unless the motor current protection is set to 0 A, the
message “L pump off” will appear
- Terminals 13 / 14 need to be bridged, otherwise the
message “Thermal Fault 2” will appear.
- Thermal fault 1 need to be deactivated in the settings
menu, otherwise the message “Thermal Fault 1” will
appear.
9.0 Technical data
Operating voltage: 3 ~ 400V (L1, L2, L3, N, PE)
Frequency 50 / 60 Hz
Control voltage: 230V / AC
Power consumption:
(Contactor activated) < 7,5 W
Power consumption in idle state < 5 W
Max. installed power P2 < 5,5 KW
Range of the electrical motor current
monitoring 0,3 – 16 A
(Here, the limit values featured in the table under point 1.1 of the
safety instructions must be adhered to)
Alarm contact 230 V 1 A
Alarm contact potential-free 3 A
Housing: ABS
Protection class: IP 54
Pressure range (internal sensor): 0 - 1 mWs (0 - 2mWs Option)
Transport and storage temperature - 30° bis + 60°C
Operating temperature range: - 20° bis + 50 °C
Dimensions: 250 x 225 x 115 mm (HxWxD)
Dimensions with cable gland and air connection
Fuse: 5 x 20 1AT (alarm output)
Voltage supply for
4-20 mA sensor
and float switch 24V / DC
Cable glands: 2 x M25 x 1,5
1 x M16 x 1,5
3 x M16 x 1,5 blind plug
Hose attachment: 6/8 mm
(Other hose connections are available on request.)
Software version: Ver. 0.3
When opening the device (removal of the panel or terminal cover)
or working on the pumps, the control must be switched off from the
power supply through the fuse or a separate main switch.
Technical specifications subject to modification!
10.0 Norms:
Applicable EC directives:
EC Low Voltage Directive 2014/35/EC
EC Electromagnetic Compatibility Directive 2014/30/EC
Applied harmonised standards, in particular:
EN 60204 - 1: 2014
EN 60730 - 1: 2016
IEC 61000 - 6 - 3: 2006
IEC 61000 - 6 - 2: 2016
11.0 Annex:
Status LED – GSM module:
Flashing constantly = The board is in the initialisation phase
Illuminated constantly = The board has initialised and has
connected with the provider
Flashes once briefly,
then extended pause = The modem is not responding
Flashes twice briefly,
then extended pause = The SIM card has not been found
Flashes three times briefly = The GSM signal strength is too weak
PSMEGA 1
www.lesa.de 12

12.0 Annex: Terminal block wiring diagrams
Terminal connection of 3~ motors
Terminal connection of 1~ motors
Caution! When connecting 1~ motors the
maximum connected load is 2,4 KW.
PSMEGA 1
www.lesa.de 13

Relay outputs, signal inputs and analogue outputs
PSMEGA 1
www.lesa.de 14

A=180 mm
B=180mm
o = 5,0mm
PSMEGA 1
www.lesa.de 15

PSMEGA1 Messglocke V4A LESA Micro-Kompakt PLC TOUCH Grossanlage
PLC TOUCH-System
Kompaktschrank
LESA- GSM 8 Kompaktschaltschrank
LCD2 - System Metall
Kompaktschaltschrank
mit Noteinspeisung
und EVU-Anschluß
weitere Produkte
* Pumpensteuerungen
*Pumpenschaltmodule
*Alarmmodule
*GSM-Module
*Messumformer
* Fernwirk- Pumpsysteme
* Messglocken
* Pneumatische Leitung
* Schaltanlagenbau - Automatisierung -
Fernwirktechnik
*Freiluftsäulen komplett bestückt
mit PS1.LCD / PS2.LCD
* Kompaktschaltschrank LCD2 - System
Metall
* GfK- Außenschränke / Leersäulen
* EVU- Anschlusssäule
* Verschraubungen für pneumatische Leitung
* Schwimmschalter
*Tauchsensoren
*Ultraschallsensoren
* Stabsonden
* Druckschalter
* Anzeiger, elektrisch, mechanisch
* Kompressoren, Einperltechnik
Table of contents
Popular Microcontroller manuals by other brands
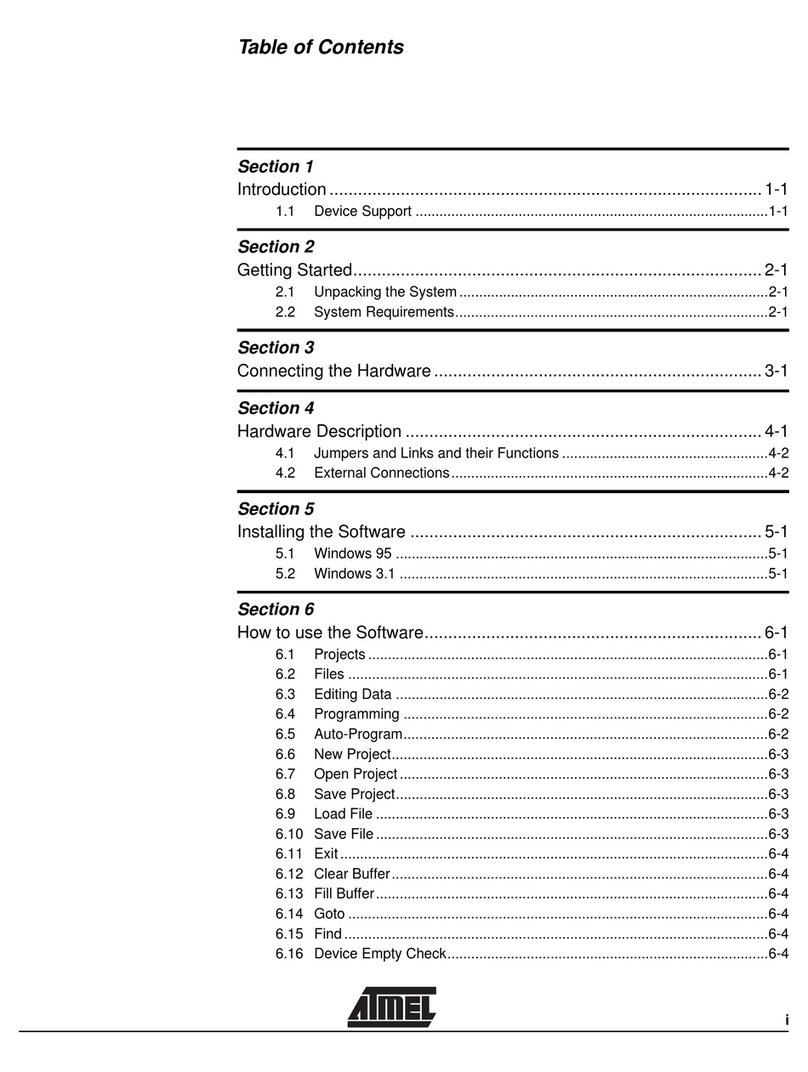
Atmel
Atmel STK200 manual
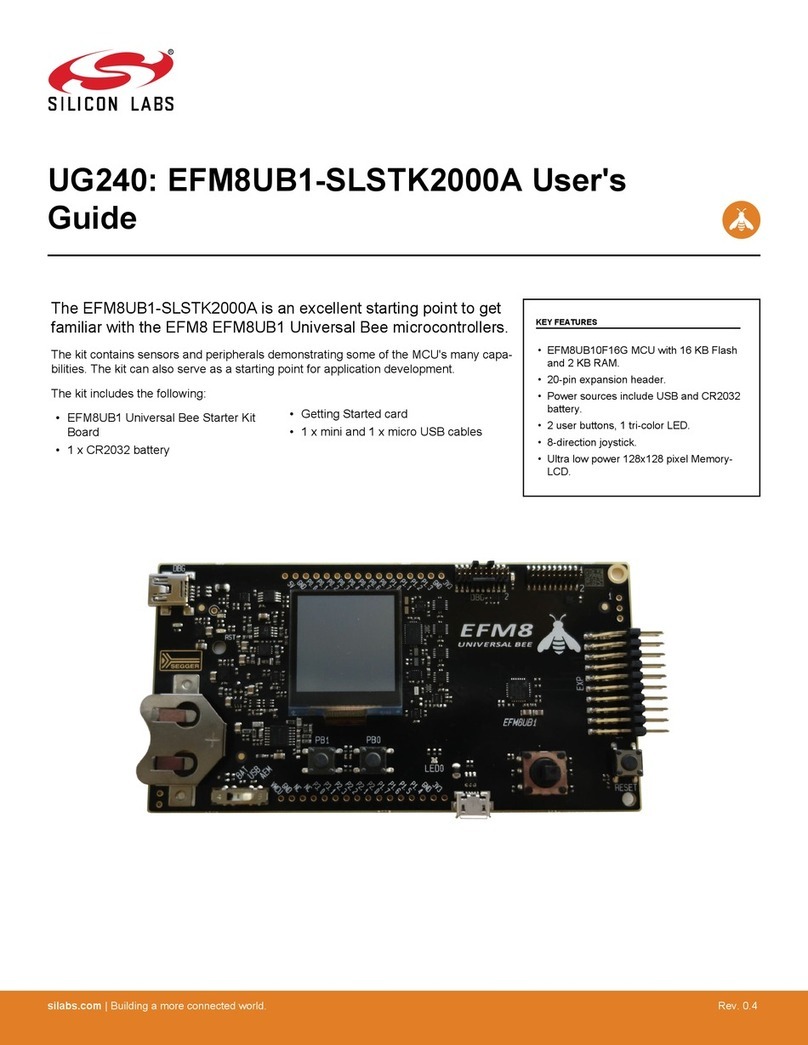
Silicon Laboratories
Silicon Laboratories EFM8UB1-SLSTK2000A user guide
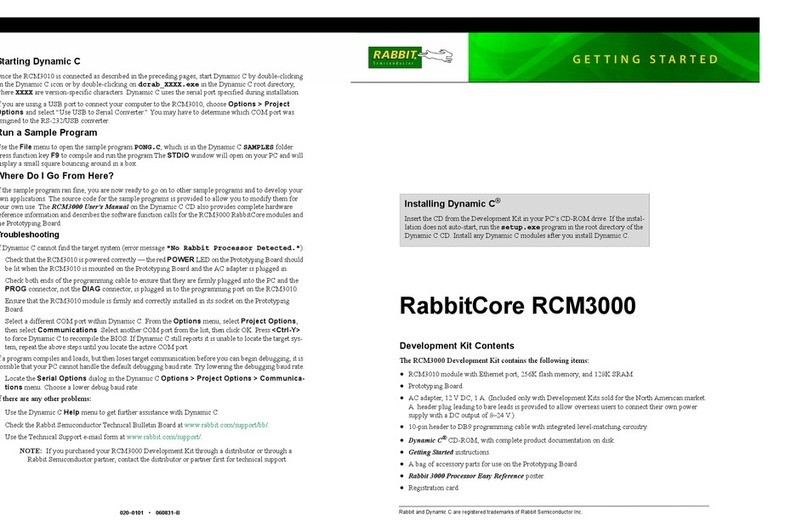
Rabbit
Rabbit RabbitCore RCM3000 Getting started
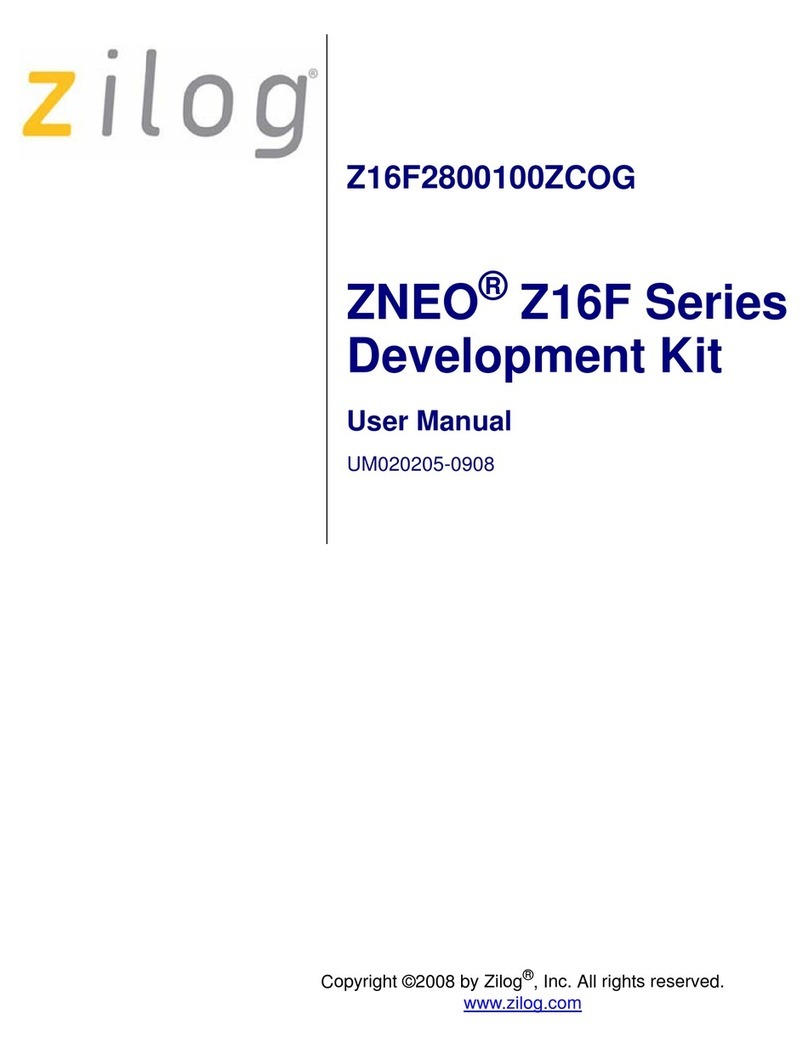
ZiLOG
ZiLOG ZNEO Z16F Series user manual
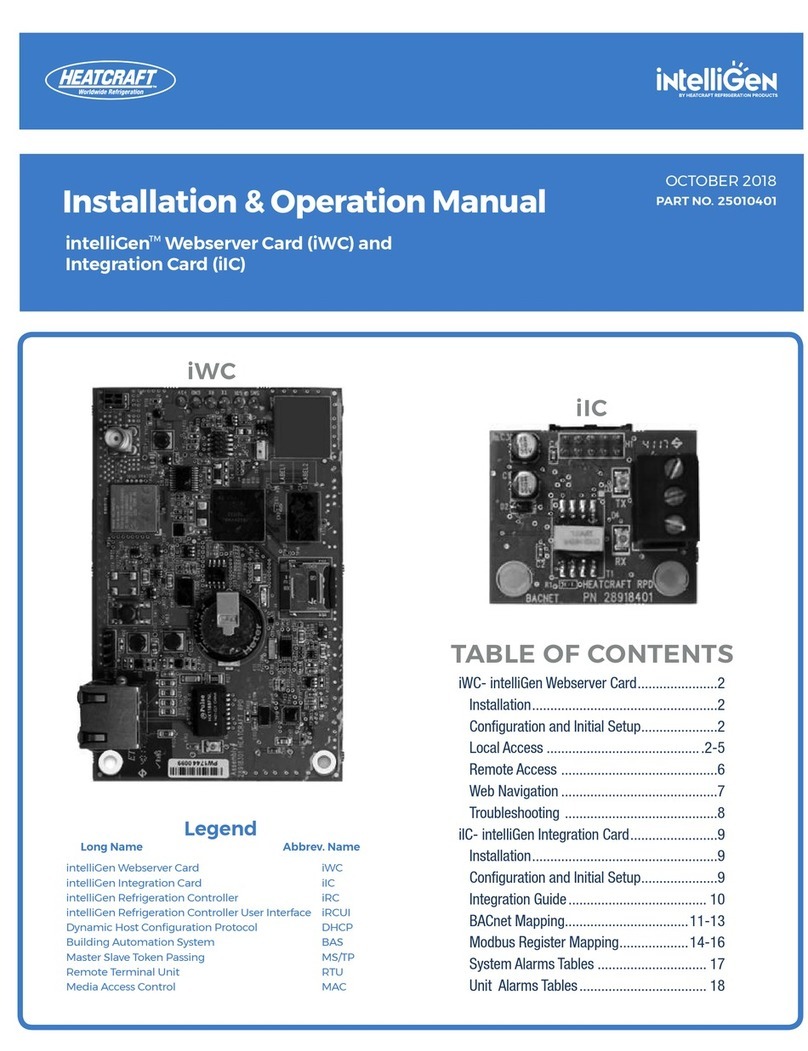
Heatcraft
Heatcraft intelliGen Integration Card iIC Installation & operation manual
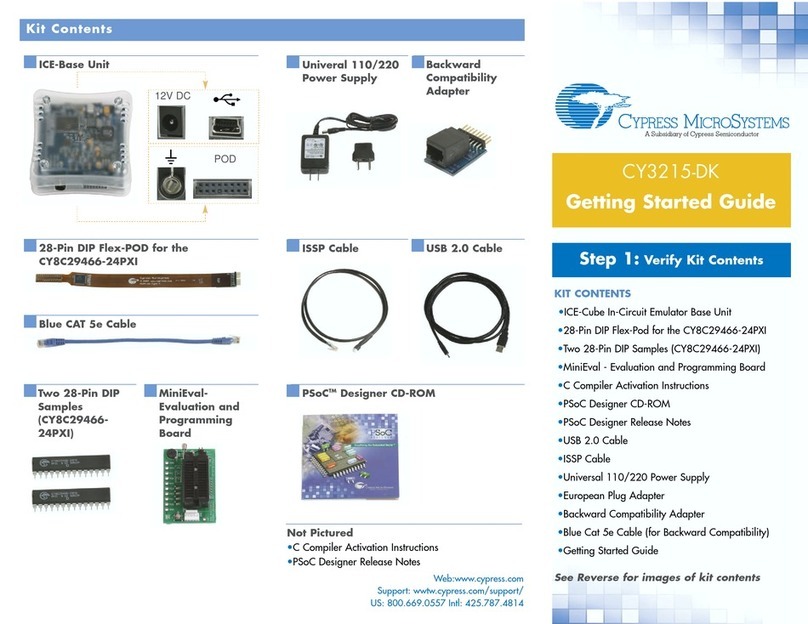
Cypress MicroSystems
Cypress MicroSystems CY3215-DK Getting started guide