Leyman Hide-A-Way LHS2500 User manual

Installation Manual
LHS & LLBS Hide-A-Way®
Tuckunder Style
10335 Wayne Avenue •Cincinnati, OH 45215
Ph: 513-891-6210 •Toll-Free: 866-539-6261
Fax: 513-891-4761
LML00136-4/22/16

Page 2
TABLE OF CONTENTS
WordsofCaution 3
General View “Truck Mounting” 4
LHS2500 Truck Preparation 5
LLBS2500 Truck Preparation 6
Notch Rear Sill and Weld Extension to Rear Sill 7
Cut off Mounting Brackets and Mounting Gate Illustration 8
Mounting Gate, listing of Steps, 5-14 Illustration “B” 9 - 10
5-15 Illustration “C”, & 5-16 Illustration “D” 11
5-17 Illustration “F” & 5-18 Recommended Oils 12
Installation of Optional Adjustable Steps 13 - 15
Installation of UP / DOWN Switch 16
Operation of the Lift Gate 17
Trouble Shooting Chart LHS & LLBS 18
Electrical Diagram 19
Installing Safety Decals 20
Final Inspection 21
Notes 22

Page 3
WORDS OF CAUTION
1. Before any maintenance is performed on this unit, read and understand this
manual completely.
2. Do not stand on or behind the platform when operating gate in the folded
position.
3. Make sure the ground is clear under the platform when lowering.
4. Do not stand in front of platform when lowering from vertical position or operating
in any manner.
5. Never exceed the rated load capacity of this gate.
6. Do not allow persons to operate the unit unless they have been properly trained
to do so.
7. Use only factory authorized parts for replacement.
8. Check the area around the unit for persons before operating the lift gate.
9. This lift gate should operate smoothly and the only noise that should be heard is
the power unit. Any audible sounds other than the normal power unit operation
sound should be thoroughly inspected and the cause of the noise should be pin-
pointed and corrected.
10. Do not over load – the maximum rated capacity is based on an evenly distributed
load all over the platforms flat surface.
11. Always load as close to the center of the platform and as close to the center of
the truck sill as possible.
12. 150 Amp circuit breaker (not supplied) must be installed between the starter
solenoid and the battery source.
Order from factory as option #111-Circuit Breaker.
We urge the installation of a safety cut-off switch for all truck mounted lift gates. These
are installed in the cab of the vehicle, so the power to the lift gate can be turned on/off.
WARNING: Since this gate has greaseless bearings in the main pivot points,
(tension and compression arms or platform parts) any welding on these parts must be
grounded or you will damage the cylinder.
WARNING: Pressure relief valve in power unit must NEVER be set above 2500
psi. Pressures above 2500 psi can damage lifting arms. Failure to follow this warning could
result in accident or injury.

Page 4
GENERAL VIEW TRUCK MOUNTING
CAUTION! Mounting Plates to Lift Gate Frame Tube must be welded
on BOTH sides. Continuous weld required on outside faces. 8” long
weld (half way around) required on inside faces.
SEE MOUNTING DIMENSIONS ON NEXT PAGE

Page 5
LHS2500 TRUCK PREPARATION
See Chart for Mounting Dimension
LHS2500 Mounting Dimension Chart
Floor Height “B” “C” “D” REF. “E” MAX.
42 22-1/2 in 19-1/2 in 28-5/8 in 4-1/4 in
43 22-1/2 in 19-1/2 in 28-5/8 in 4-1/4 in
44 22-1/2 in 19-1/2 in 28-5/8 in 4-1/4 in
45 22-1/2 in 19-1/2 in 28-5/8 in 4-1/4 in
46 23-11/16 in 18 in 26-3/4 in 4-1/4 in
47 23-11/16 in 18 in 26-3/4 in 4-1/4 in
48 23-11/16 in 18 in 26-3/4 in 4-1/4 in
49 23-11/16 in 18 in 26-3/4 in 4-1/4 in
50 23-11/16 in 18 in 26-3/4 in 5-1/8 in
51 23-11/16 in 18 in 26-3/4 in 5-1/8 in
52 24-11/16 in 17-5/8 in 26-1/4 in 5-3/4 in
53 24-11/16 in 17-5/8 in 26-1/4 in 5-3/4 in
54 24-3/16 in 17-5/8 in 26-1/4 in 6-1/4 in
55 25-5/16 in 16 in 25 in 6-1/4 in
56 26-5/8 in 15 in 23-7/16 in 6-1/4 in
NOTE: ADD 3-5/8 IN TO DIM “D” FOR OVER ALL LENGTH
NOTE: MAX./MIN. SPREAD OF GATE MOUNTING PLATES
37” MAXIMUM to 31.5” MINIMUM

Page 6
LLBS2500 TRUCK PREPARATION
See Chart for Mounting Dimension
LLBS2500 Mounting Dimension Chart
Floor Height “B” “C” “D” REF. “E” MAX.
36 15-1/2 in 24 in 32-3/4 in 4-1/4 in
37 15-1/2 in 24 in 32-3/4 in 4-1/4 in
38 18-1/2 in 22 in 31 in 4-1/4 in
39 18-1/2 in 22 in 31 in 4-1/4 in
40 18-1/2 in 22 in 31 in 4-1/4 in
41 19 in 21-3/16 in 30-5/8 in 4-1/4 in
42 19 in 21-3/16 in 30-5/8 in 4-1/4 in
43
44 USE LHS GATE AT
45
46 THESE FLOOR HEIGHTS
47
48
49
NOTE: ADD 3-5/8 IN TO DIM “D” FOR OVER ALL LENGTH
NOTE: MAX./MIN. SPREAD OF GATE MOUNTING PLATES
37” MAXIMUM to 31.5” MINIMUM

Page 7
NOTCH REAR SILL
Notch rear sill
Check the height of the rear sill
See chart if the height of the rear sill is larger than the dimension “E” max, the sill
must be notched
See illustration below
Note: After notching the rear sill, add material to reinforce such as 3” x 3” x 3/8” angle
or 1” square bar etc. The area cut away must be rebuilt to maintain strength.
WELD EXTENSION TO REAR SILL

Page 8
CUT OFF MOUNTING BRACKETS
“A” is the dimension that you can trim the mounting brackets to be able to install the
gate. Experience tells us that dimension “A” is approximately 4 in. Depending on the
dimension of your truck body or chassis, this cut may not be necessary, if the mounting
brackets fit well and do not interfere with the body.
MOUNTING GATE ILLUSTRATION

Page 9
MOUNTING GATE
1. Unfold the secondary platform.
2. Clamp the secondary platform to the forks of the lift truck. Approximately
centered (See illustration).
3. There are two angles in the shipping kit, 5” x 3” x 1/4” x 3” lg. Lay these two
angles on top of the extension plate to space the platform out 1/4” (See sketch).
4. Pick up the gate assembly. Center on the floor extension, and push against the
floor extension and the 1/4 spacers. With two pieces of scrap channel or angle,
clamp platform flush with floor. Use four clamps. Clamp channels to extension
and platform. Tip of the platform should be 1” higher than the floor extension.
5. With a floor jack and a piece of 4” x 4” wood, swing and raise the main tube until
it is at dimension “B” (mounting plates should be outside the truck frame).
6. With a large pipe wrench, rotate the main tube, so that the clevis plate edges are
vertical. Then check the rod of the lift cylinder. You should see about 1/2” of
polished rod.
7. Now tack weld the main support plates and tube in position, strong enough to
hold, so you can run the gate up and down, without a load on it. This is to check
the gate functions properly.
8. Unclamp the four clamps holding the platform to the floor extension.
Caution: Do not unclamp the tip of the platform from the forks.
9. Let the lift truck forks down slowly until they will not go any more. (They will stop
about 1/2 way down, when they meet resistance from the oil in the lifting
cylinder).
10. Install the gate control switch in the desired location and route the wire to the
power unit. Slide a piece of supplied shrink tube over the thermal switch wire and
connect the black control wire to thermal switch wire using the butt connector
pre-installed on the wire. Move the shrink tube to cover the connection and heat
to shrink and seal the connection. Connect the white control wire to the lowering
valve in the same manner. Attach the green control wire with ring terminal to the
large open post of the starter solenoid. See page 14 for switch mounting details.
11. For temporary power, use a 12 volt battery. Run a wire from the battery to the
starter solenoid, run a ground wire to the truck. The gate will now run. Lower the
gate to the ground and check / add oil before attempting to run the motor to raise
the gate. See chart 5-18 Recommended Oils.
12. After oil has been checked, run gate up and down to check its operation.

Page 10
13. Finish weld the mounting plates and main tube. CAUTION! Mounting Plate to
Lift gate Frame Tube must be welded on BOTH sides. Continuous weld required
on outside faces. 8” long weld (half way around) required on inside faces.
14. Weld shims to stop blocks on platform for proper slope and preload. 16 gauge
shims are provided and will give proper slope for average installation (see 5-14
Illustration “B”).
15. Weld on stop block for latch, which holds the gate up in the stored position.
There should be a 1/16 gap between the block and the latch (see 5-15 Illustration
“C”).
16. Weld on brackets to protect the hydraulic cylinder (see 5-16 Illustration “D”).
17. Run 2 gauge power line from starter on the gate to the truck battery.
Caution: Make sure there is a ground wire from battery to chassis.
18. Take the ground cable located inside of the power unit box and ground to the
truck chassis. Seal ground connection at chassis.
19. If purchased, install optional step assemblies
20. Paint unit. Apply decals (see decal placement illustration). Lubricate grease
fitting at lock pin. Check oil level in power unit tank, when platform is on ground.
5-14 Illustration “B”
Weld shims to stop blocks on platform for proper slope and preload. View with platform
unfolded, and in the full up position. Platform should slope 1-1/2” on the LHS gate and
3/4" on the LLBS gate toward the truck bed.
Caution: Ground stop blocks before welding shims

Page 11
5-15 Illustration “C” Latch Block
Weld latch block to tension arm
Maintain 1/16 gap. This block will hold the gate in the stored position in the event
of hydraulic failure.
Caution: Ground arms before welding latch block
5-16 Illustration “D” Standard Platform
With the platform in position shown (folded horizontal) weld platform brackets (angles
supplied) to tension arms, so that platform is resting on brackets approximately 1/2"
above cylinder. Weld solid down two sides as shown (1/4 wide fillet weld).
Caution: Ground arms before welding brackets

Page 12
5-17 Illustration “F” Wedge Platform
With the platform in position shown (folded horizontal) weld platform brackets (angles
supplied) to tension arms, so that platform is resting on brackets approximately 1/2"
above cylinder. Weld solid down two sides as shown (1/4 wide fillet weld).
Caution: Ground arms before welding brackets
5-18 Chart - Recommended oils
Level1 Normal
Conditions
Manufacturer Type Temperature Range
Chevron RYKON ISO-15 -15oF to + 150oF
Mobil DTE-11 -15oF to + 150oF
Shell TELLUS-T15 -15oF to + 150oF
Level2 Cold
Conditions
Manufacturer Type Temperature Range
Chevron AVIATION-A -50oF to + 80oF
Mobil AERO-HFA -50oF to + 80oF
Shell AERO FLUID #4 -50oF to + 80oF
Mil H-5606 -50oF to + 80oF

Page 13
INSTALLING OPTIONAL ADJUSTABLE STEPS
General method:
1. Measure bed height UNLADEN.
2. Refer to the chart that covers a range of bed heights. Use the corresponding line in
the chart that your measurement most closely matches to determine assembly
dimensions. Curb side view is shown. Driver’s side view is a mirror image.
3. Trim the lower portion of the Step Mounting Tubes, if required. Use a method
that generates minimal heat so paint damage is reduced. An Extreme Shield
Touch-Up Kit is provided to re-paint ends.
4. Assemble Step Rung Assembly to Step Mounting Tubes using the appropriate
holes referenced in the chart. Leave hardware loose. Then bolt Step Mounting
Tubes to Bed Extension using pre-drilled holes. Verify distance from top step to
Bed Extension. Enough hardware was shipped to cover all possible cases, so not
all hardware may be used for your case.
5. Assemble Cover Plate if required. Drill #11 (0.191) holes and use pop rivets.
6. Assemble Step Gusset as shown. C-channel will need to be trimmed at top end.
Any extra materials needed to anchor top end of gusset to vehicle is the installer’s
responsibility. Tighten all hardware.
The following parts are included in the kit. Kits are specific to each model of gate so
some parts listed may not be included.
Index Req'd Part No. Description Mat'l Size SLP SLP-WLB
1 4 BP-802-190 STEP MOUNTING TUBE
1 4 BP-802-205 STEP MOUNTING TUBE
2 2 BA-802-191 STEP RUNG ASSEMBLY
2 2 BA-802-206 STEP RUNG ASSEMBLY
3 1 BA-802-194 STEP GUSSET - RH
3 1 BA-802-207 STEP GUSSET - RH
4 4 P11061 HEX HD CAP SCREW 3/8-16 X 3
5 16 P11037 HEX HD CAP SCREW 3/8-16 X 3-1/4
6 4 P11060 HEX HD CAP SCREW 3/8-16 X 3-1/2
7 4 P26501 FLAT WASHER 3/8 STD
8 28 P26523 FLAT WASHER 3/8 HEAVY
9 20 P23501 LOCK NUT 3/8-16
10 2 AP-802-195 COVER PLATE 1.5"
11 2 AP-802-196 COVER PLATE 3.5"
12 8 P49097 POP RIVET 3/16 DIA.
13 1 BA-802-203 STEP GUSSET - LH
13 1 BA-802-211 STEP GUSSET - LH

Page 14
ADJUSTABLE STEPS - LHS

Page 15
ADJUSTABLE STEPS - LLBS

Page 16
INSTALLATION OF UP / DOWN SWITCH
Switch Housing must be located at a height that can be reached while standing on the
ground on the curb side of the vehicle, and also while standing on the platform when at
bed height.
Switch cable is routed to power unit box as noted in each sketch. Connect as shown on
wiring diagram. Green wire connects to battery post on start solenoid. Black wire butt
connects to motor temperature switch lead, unless equipped with option Maintenance
Minder 2. White wire butt connects to drain valve. Use heat shrink provided to seal butt
connectors.

Page 17
OPERATION OF THE LIFT GATE
Before operating the lift, read and understand this decal, urgent warning decal,
and the Owner’s Manual.
Do not stand behind the lift gate while unfolding or using the platform.

Page 18
TROUBLE SHOOTING CHART LHS & LLBS
PROBLEM POSSIBLE CAUSE SOLUTION
The motor is running but the
platform will no go up, or
reach floor of vehicle or gate
will not lift rated load.
1. Insufficient oil in power
unit tank
2. Lowering valve is stuck
partially or fully open.
3. Power unit relief valve is
set too low.
1. Fill tank
2. Clean or replace
3. Check and adjust
pressure. Do not exceed
2500 psi.
The platform will not go up
or reach floor level and the
motor does not run.
1. Battery is low
2. Power line is loose
3. Poor switch connections
4. Cab switch is turned off
5. Defective starter
solenoid
6. Tripped circuit breaker
1. Recharge battery
2. Check the connections, if
loose tighten. Also check
for corrosion and clean if
necessary
3. See #2
4. Turn switch on
5. Replace part
6. Reset the circuit breaker
Platform will not lower 1. Battery is low
2. Bad ground or electrical
connection
3. Lowering valve is bad
1. Recharge battery
2. Check for corrosion and
tighten
3. Check the coil
Platform creeps downward 1. Defective cylinder or
piston seal
2. Lowering valve is not
seating or partially open
1. Remove vent line
activate to see if there is
a continuous flow of oil
2. Clean and inspect
Platform goes down slowly 1. Lowering valve not fully
open or clogged
2. Lines are restricted or
flow control is clogged
1. Clean or replace the
lowering valve
2. Check for bent or
pinched lines. Clean or
replace the flow control.
Bent latch pin 1. Latch block welded too
far from the latch pin –
allowing mechanism to
bounce
2. Cylinder leaking
1. Weld block 1/16 away
from pin
2. Remove vent line,
activate to see if there is
a continuous flow of oil
Hydraulic oil leak from
cylinder rod end. 1. Worn seal
2. Cylinder rod pitted 1. Replace seals in cylinder
2. Replace cylinder

Page 19
ELECTRIC DIAGRAM

Page 20
INSTALLING SAFETY DECALS
Part # Qty Description
P55199 1 Urgent warning decal
P55198 2Stand clear decal
P55201 1 Power shut off decal
P55202 1 Secure latch decal
P55203 1 Read and understand decal
P55242 1 Low voltage decal
P55307 1 Operation of lift gate
P55200 1 LHS 2500 max. capacity decal
P55200 1 LLBS 2500 max. capacity decal
OPERATION OF THE
LIFT GATE
DECAL
MAX. CAPACITY
DECAL
URGENT WARNING
DECAL
READ AND UNDERSTAND
DECAL
CUT OFF POWER DECAL
LOW VOLTAGE DECAL
STAND CLEAR DECAL
BOTTOM OF PLATFORM SECURE LATCH DECAL
Extreme Shield Decal
P55439
This manual suits for next models
1
Table of contents
Popular Lifting System manuals by other brands
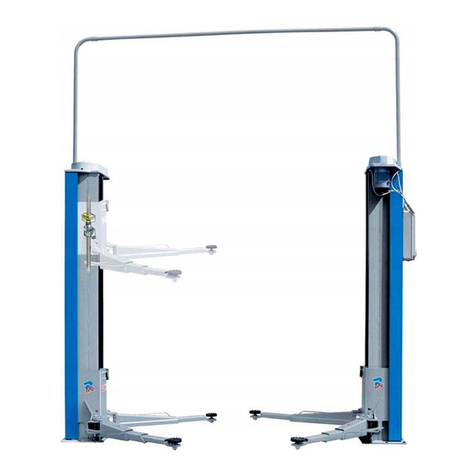
Ravaglioli
Ravaglioli KPX341 Translation of the original instructions

AREBOS
AREBOS AR-HE-RH400KG user manual
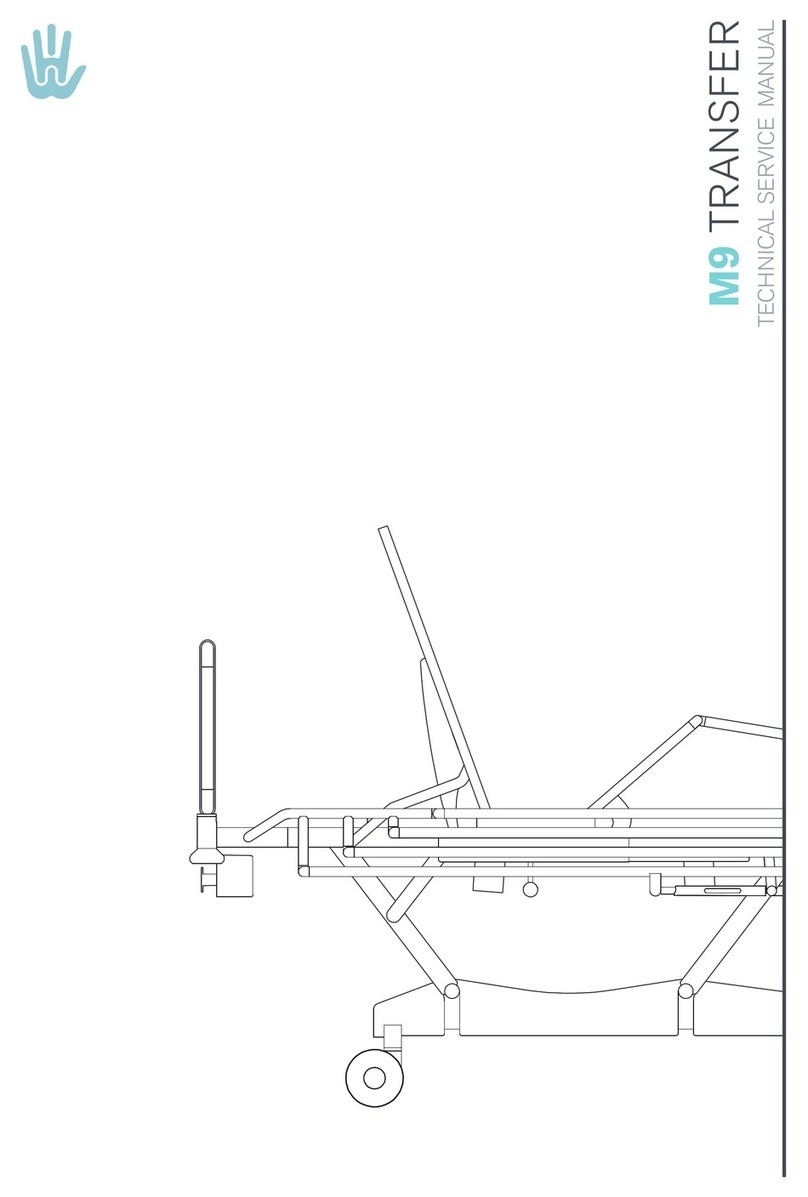
Howard
Howard M9 Technical & service manual

Omega Lift
Omega Lift MagicLift 25037 operating instructions

Autoquip
Autoquip FLH Installation, operation and service manual

ARO
ARO 651612 Series Operator's manual

Blue Giant
Blue Giant H7012 Installation & technical manual
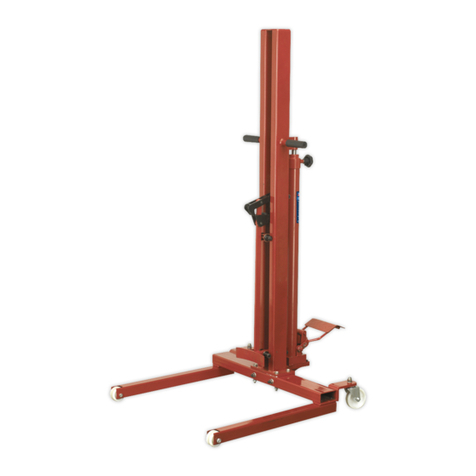
Sealey
Sealey DH03.V2 instructions
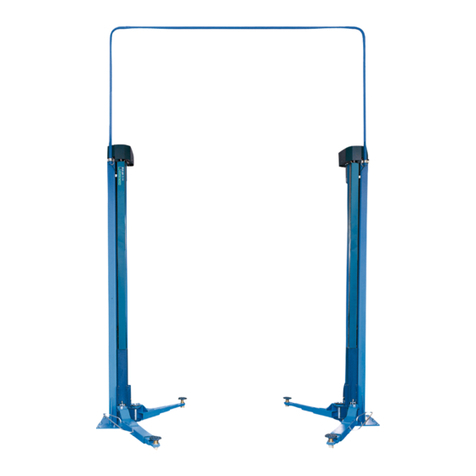
Hofmann
Hofmann duolift MTE 3000 Operation manual
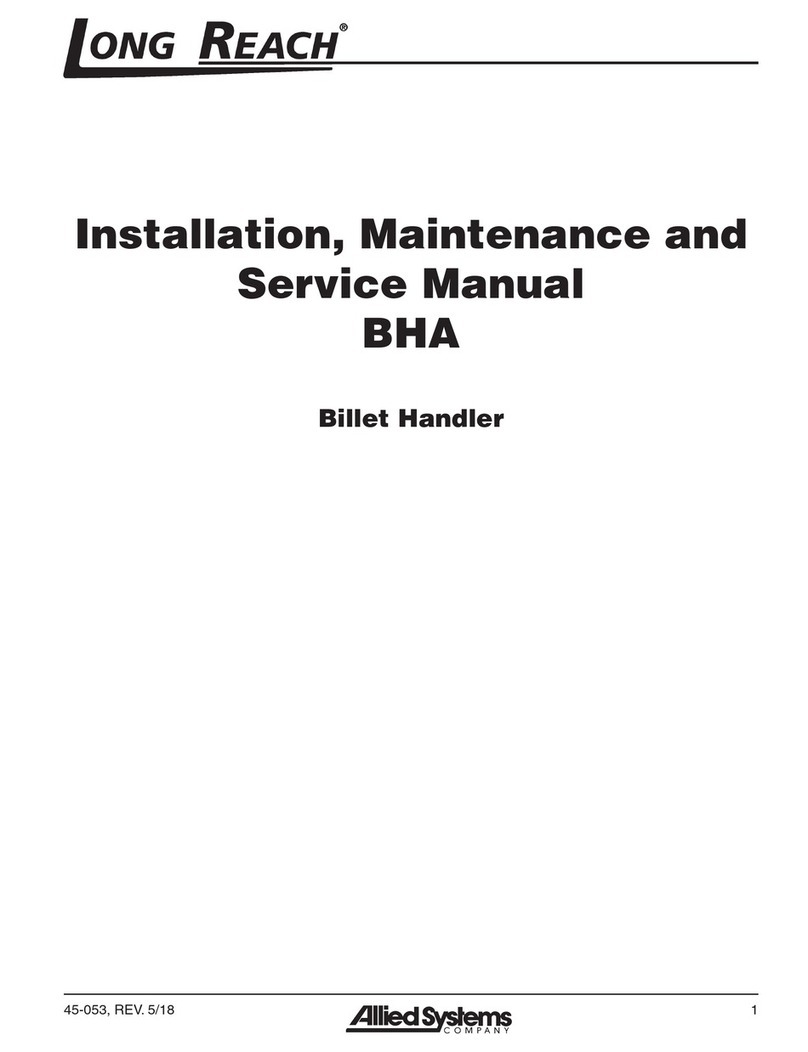
Allied Systems
Allied Systems Long Reach BHA Series Installation maintenance and service manual

Leroy-Somer
Leroy-Somer unidrive sp Installation and commissioning manual

ARKSEN
ARKSEN 005-TH-50071 owner's manual