LG GC-W061 series User manual

CAUTION
BEFORE SERVICING THE UNIT, READ THE "SAFETY
PRECAUTIONS" IN THIS MANUAL.
WINE CELLER
SERVICE MANUAL
GC-W061*** GC-W101*** GC-W141***

1. Product Specification.................................................................................................................................... 4
2. Component Names and Motions.................................................................................................................. 5
3. Exterior .......................................................................................................................................................... 8
4. Circuit Diagram ......................................................................................................................................... 13
5. TROBLESHOOTING......................................................................................................................................15
6. Micom Function and Circuit Diagram ..................................................................................................... 21
7. Special Features ....................................................................................................................................... 37
8. Standard Self-Diagnostic Function............................................................................................................ 38
9. Maintenance ................................................................................................................................................. 39
10. Handle Disassembling, Assembling Instruction .................................................................................... 42
11. Service Parts Chart ................................................................................................................................... 43
Please read the following instructions before servicing your
refrigerator.
1. Check the set for electric losses.
2. Unplug prior to servicing to prevent electric shock.
3. Whenever testing with power on, wear rubber gloves to
prevent electric shock.
4. If you use any kind of appliance, check regular current,
voltage and capacity.
5. Don't touch deep-frozen products in the freezer with wet
hands. This may cause frostbite.
6. Prevent water from following onto electric elements in
the mechanical parts.
7. When tilting the set, remove any materials on the set,
especially the thin plates(ex. Glass shelf or books.)
8. Leave the disassembly of the refrigerating cycle to a
specialized service center. The gas inside the circuit
may pollute the environment.
9. When you discharge the refrigerant, wear the protective
safety glasses or goggle for eye safety.
10. When you repair the cycle system in refrigerator, the
work area is well ventilated.
Especially if the refrigerant is R600a, there are no fire
or heat sources. (No smoking)
SAFETY INSTRUCTIONS
TABLE OF CONTENTS
- 2 -

Features of refrigerant (R600a)
• Achromatic and odor less gas.
• Flammable gas and the ignition (explosion) at 494°C.
• Upper/lower explosion limit: 1.8%~8.4%/Vol.
Features of the R600a refrigerator
• Charging of 60% refrigerant compared with a R134a model
• The suction pressure is below 1bar (abs) during the operation.
• Because of its low suction pressure, the external air may flow in the
cycle system when the refrigerant leak, and it causes malfunction in
the compressor.
• The displacement of compressor using R600a must be at least 1.7
times larger than that of R134a.
• Drier type is XH-9.
• The EVAPORATOR or any other cycle part that has welding joint is
hidden in the foam. (If not hidden inside, the whole electric parts
must be tested with the LEAKAGE TEST according to the IEC
Standard.)
• The compressor has label of the refrigerant R600a.
• Only the Service man must have an access to the system.
Installation place
• Must be well ventilated.
• Must be 20 m
3
or larger.
• Must be no-smoking area.
• No ignitable factors must be present.
Utilities
• Refrigerant cylinder (MAX NET 300g)
• Manometer
• Vacuum pump (600L/min)
• Piercing Clamp
• Quick coupler
• Hoses (5m-1EA, 1m-3EA)
• LOKRING
• Portable Leakage detector (3g/year¯)
• Nitrogen cylinder (for leakage test)
• Concentration gauge
Make sure before Servicing
• Refrigerant
Confirm the refrigerant by checking Name Plate on innerliner and
the label on the compressor.
• If the refrigerant is R600a, you must not weld or apply a heat source.
Air Recharging in Compressor
Before refilling the refrigerant, you must perform the test according to
Chapter 5 (TROUBLESHOOTING CHART). When the defects are
found, you must discharge the residual refrigerant (R600a) in the
outdoor. For discharging the refrigerant R600a, break the narrow
portion of tube extension by hand or with a pipe cutter as shown in
Figure 1. Leave it for 30min in outside to stabilize the pressure with
ambient. Then, check the pressure by piercing the dryer part with
piercing pliers. If the refrigerant is not completely discharged, let the
refrigerator alone for more 30min in outside.
Attach the service tube installed with a Schrader valve (one-way
valve) by using the LOKRING (Figure 2). Then, connect the Schrader
valve (one-way valve) to the pump that is connected to the
discharging hose leading to the outside. When discharging the
residual refrigerant, repeat 3 cycle that includes 3min of the pump
running->pump off->30sec of the compressor running.
After the refrigerant (R600a) is completely discharged, repair any
defective parts and replace the dryer. At any case you must use the
LOKRING for connecting or replacing any part in the cycle (No Fire,
No Welding). Connect the Schrader valve to pump with the coupler.
And then turn the pump on for vacuum state (Figure 3). Let the pump
run until the low-pressure gauge indicates the vacuum (gauge
pressure 0, absolute pressure -1atm or -760mmHg). Recommended
vacuum time is 30 min. Charge the N2 gas in order to check for
leakage from welding points and the LOKRING. If leakages are
found, repair the defects and repeat the vacuum process.
After the system is completely vacuumed, fill it with the refrigerant
R600a up to what has been specified at your refrigerator Name Plate.
The amount of refrigerant (R600a) must be precisely measured within
the error of ±1g by an electron scale (Figure 4).
If you use the manifold connected with both the refrigerant (R600a)
cylinder and the vacuum pump simultaneously, make sure the pump
valve is closed (Figure 5).
Connect the charging hose (that is connected to the refrigerant
(R600a) cylinder) to the Schrader valve installed on the service tube.
Then, charge the refrigerant (R600a) by controlling the Throttle valve.
When you do so, do not fully open the Throttle valve because it may
make damage to the compressor. Gradually charge the refrigerant
(R600a) by changing open and close the Throttle Valve (5g at each
time). The charging hose must use a one-way valve to prevent the
refrigerant refluence. Close the Schrader valve cap after the
refrigerant (R600a) is completely recharged.
After you completely recharge the refrigerant (R600a), perform the
leakage test by using a portable leakage detector or soapy water.
Test the low pressure (suction) parts in compressor off time and high
pressure parts in compressor on time. If the leakages are found,
restart from the refrigerant (R600a) discharging process and repairs
defects of leaks.
After the leakage test, check the temperature of each parts of the
cycle. Check with hands if the CONDENSER and the case
(HOT-LINE pipe) that is contacted to the door gasket are warm.
Confirm that frost is uniform distributed on the surface of the freezer
room and the back wall of fridge room.
SERVICING PRECAUTIONS
- 3 -
POINT TO BE
BROKEN CHARGE TUBE
EXTENSION
SCHRADER VALVE
(ONE-WAY VALVE)
LOKRING
SERVICE TUBE
EXTENSION
Figure 1 Figure 2
TO THE
VACUUM
PUMP
PRESSURE
GAUGE
Figure 3
WEIGH SCALE
THROTTLE
VALVE
COUPLE
REFRIGERANT
(R600a)
CHARGING HOSE
Figure 4
FILLING OR
CHARGE TUBE
VALVE TO BE OPENED
WHEN REFILLING
VALVE TO BE CLOSED
AFTER VACUUM
TO THE VACUUM PUMP
TO THE
REFRIGERATION
SYSTEM
TO THE CHARGE
CYLINDER
Figure 5

1. Product Specification
1-1. Rated, product specifications
1-2. Component Details
•
Interior Heater: Heat up the interior when surrounding temperature is lower than the set temperature.
- 4 -
PRODUCT SPECIFICATION
Model Name GC-W061*** GC-W101*** GC-W141***
Regular Contents 135Li 214Li 283Li
Exterior measurements
(Width X Depth X Height) 595 X 580 X 820 595 X 580 X 1185 595 X 580 X 1475
Rated Voltage/Frequency 230V / 50Hz
Power Consumption 72W 80W 85W
Weight 47kg 64kg 71kg
Cooling Method Cool Air Automatic Circulation Type
Temperature Control Device MICOM
Outer Case Material Vynil Coated Metal
Inner Case Material A.B.S Resin
OUT DOOR Indium Thin Oregan Triple Layers Glasses/Aluminium Deco
Insulation Material Poly Urethane Foam (Insulation Foam Gas: Cyclopentane)
693 X 717 X 946 693 X 717 X 1296 693 X 717 X 1586
51kg 74kg 81kg
Package Exterior
Measurement
(Width X Depth X Height)
Package Weight
Package
Details
Model Name GC-W061*** GC-W101*** GC-W141***
Compressor MB69NAEG MB98NBEG
Overload Protect 4TM149NFB 4TM205RFB
P.T.C P330MC P330MC
Heater UPPER: 8W (1EA) UPPER: 8W (2EA)
UPPER: 4W (2EA) UPPER: 5W (2EA)
Interior Light 12V / 3W / 0.25A
Power Cord (Length) 1.9m
Temperature Sensor Heat Reducing Load Resistance Device

2. Component Names and Motions
2-1. Interior
• Interior Light (Interior Ceiling, CASE DISPLAY & BARRIER installed in the lower column) Interior light operates by the
control panel regardless of door opening or closing.
• Interior light uses DC voltage. Please see 1-2, component details.
• 2 or 3 interior lights are installed according to model sizes and light turns on and off by control panel operation button.
2-2. Wine Rack
• Wine rack detail may vary according to the model types.
• Each rack can hold 8 wine bottles and top rack holds 9 bottles.
2-3 Others
• Glass Holder
-Hangs wine glasses. (GC-W141***)
• Wine Rack
-Stores leftover wine (tilted). (GC-W141***, GC-W101***)
• Locking Device
-Key is enclosed in the inside of the refrigerator.
• Leg Adjustor (Front & Back, Left & Right, one each)
-Please level the product using the leg adjustor.
COMPONENT NAMES AND MOTIONS
- 5 -
Model Name GC-W061*** GC-W101*** GC-W141***
Standard Capacity 41bottles 65bottles 81bottles

GC-W141***
COMPONENT NAMES AND MOTIONS
- 6 -
*Glass tray
Operation panel
Wine shelf
Adjustable support
Can be adjusted when
the fridge is not stable.
Light bulb
• Light bulb inside the wine
fridge can be turned on or
off by pressing the button
on the operation panel.
• Light bulb inside the wine
fridge will automatically
turn off after the door is
open for an hour.
Top/Bottom
Separation Panel
• The partition is separated
into 'Top' partition and
'Bottom' partition based on
the top/bottom separation
panel. Temperature is
adjusted with 'Top' button
and 'Bottom' button
respectively.

GC-W101***
GC-W061***
COMPONENT NAMES AND MOTIONS
- 7 -
Operation panel
Wine shelf
Adjustable support
Can be adjusted when
the fridge is not stable.
Light bulb
• Light bulb inside the wine
fridge can be turned on or
off by pressing the button
on the operation panel.
• Light bulb inside the wine
fridge will automatically
turn off after the door is
open for an hour.
Top/Bottom
Separation Panel
• The partition is separated
into 'Top' partition and
'Bottom' partition based on
the top/bottom separation
panel. Temperature is
adjusted with 'Top' button
and 'Bottom' button
respectively.
Operation panel
Wine shelf
Adjustable support
Can be adjusted when
the fridge is not stable.
Light bulb
• Light bulb inside the wine
fridge can be turned on or
off by pressing the button
on the operation panel.
• Light bulb inside the wine
fridge will automatically
turn off after the door is
open for an hour.

- 8 -
3. Exterior
3-1. Exterior
GC-W061***
EXTERIOR

GC-W101***
EXTERIOR
- 9 -

EXTERIOR
- 10 -

GC-W141***
EXTERIOR
- 11 -

EXTERIOR
- 12 -

- 13 -
4. Circuit Diagram
4-1. Circuit Diagram
: Indicated component is a safety part. (In case of a replacement, please use a designated part for its function and your
safety.)
GC-W061***
CIRCUIT DIAGRAM
This product is powered by electricity. Once the power is plugged out,
please wait at least 5 minutes before you plug it back in. If you plug the
power right back in, it will cause a malfunction in the cooling machine.
MODEL: GC-W061***
Power Plug
Compressor
Exterior Temperature Sensor
Interior Temperature Sensor (Top)
Cooling Sensor (Top)
Heater (Top)
Heater (Bottom)
Case Display
Interior Light
Control Panel
BK : BLACK BL :BLUE BO : BROWN OAK BN :BROWN
YL :YELLOW PR :PURPLE GY :GRAY WH : WHITE
Temperature Indicator,
Control Panel
Interior Light

CIRCUIT DIAGRAM
- 14 -
GC-W101***/GC-W141***

5. Trobleshooting
5-1. COMPRESSOR AND ELECTRIC COMPONENTS
TROBLESHOOTING
- 15 -
1
2
3
4
5
2
4
3
3
4
4
5
5
NO
NO
NO
NO
NO
YES
YES
YES
YES
Power Source
Check the
resistance of the
Compressor Motor.
Check the starting
state at the regular
voltage above.
Check the
resistance of
the PTC.
Check OLP.
Check the starting
state.
Separate the PTC-STARTER from the
Compressor and measure the voltage
between M and C of the Compressor.
Equal to the applied
voltage. (Rating
voltage ±10%)
Advice the customer to
use in the specified
range.
If not 0 or
Advice the customer to use
in the specified range.
Measure minimum starting voltage
after checking steps 1-3 above.
Measure the pressure balance of the
PTC at the interval of more than 5 min.
Starts at the voltage of more
than 90%.
Replace OLP.
Normal.
Normal.
Replace the PTC.
Replace the
PTC-STARTER.
The applied voltage is not in the range
of Rating Voltage ±10%.
Test the resistance among
M-C, S-C, and M-S.
Check if applying a
regular OLP.
Test the resistance of the both
terminals in the PTC-STARTER.
Replace the Compressor.
Starts at the voltage
of 85% below.

5-2. PTC
- 16 -
YES
NO
Poor starting or no
operating of the
Compressor.
First, separate the PTC from the
Compressor and check the voltage
between NO 5 and 6 in the PTC
with a multitester or Wheatstone
Bridge.
Observation value is
220~240V/50Hz :
The value is 0.
The value is .
Check another
electric
components.
Replace the PTC.
Normal
Abnormal
Abnormal Replace the PTC.
Separate the OLP from the
Compressor and check
resistance value between two
terminals of OLP with Tester.
Check other electric
components.
Replace OLP.

5-3. ANOTHER ELECTRIC COMPONENTS
5-3-1. No Cooling
- 17 -
The Compressor
doesn't run.
Poor running of the
Compressor.
Compressor runs.
Measure the starting
voltage.
Check if the current flows
at the contacting point of
the starting system.
Frost doesn't form on the
back wall of freezer and
fridge room when operating
set for more than 30 min.
Poor contacting point
Shorted or Broken
Coil shorted
Low voltage Increase the voltage.
Replace the device.
Repair the Compressor.
Shorted Poor contacting
point and broken
Refrigerant leaks. Poor
compressing.
Check the current flowing
of starting system.
Check the components
on the main circuit.
Check if the current flows
at the contacting point of
the Thermostat.
Check if the current flows
at the main coil of the
Comprossor.
Replace the
Thermostat.
Replace the device.
Replace the
components.
Replace the
Compressor.

5-4. REFRIGERATING CYCLE
5-4-1. Troubleshooting chart
- 18 -
DEFECT EFFECT CAUSE REMEDY
SYSTEM
PARTIALLY OR
COMPLETELY OUT
OF REFRIGERANT
CHARGE
EXCESSIVELY
FULL
HUMIDITY IN THE
SYSTEM
PRESENCE OF AIR
IN THE SYSTEM
BLOCKED
CAPILLARY
MOTOR-
COMPRESSOR
DOSE NOT
COMPRESS
NOISY MOTOR-
COMPRESSOR
Freezer and fridge room do
not frost even though motor-
compressor runs continually.
This defect is indicated by the
presence of water outside the
refrigerator near the motor caused by
formations of ice on the return tube.
This defect is indicated by the partial
frosting of the freezer room and by
continual defrosting cycles determined
by the interruption of the flow of gas
on the evaporator. The motor
compressor keeps running.
Poor performance of the refrigerant
system which is indicated on the
evaporator with a slight frost which
does not freeze and an excessive
overheating of the condenser and
motor-compressor.
Because of the lack of circulation
isobutane in the system, there is no
frosting of the evaporator, while a
slight overheating of the first spiral of
the condenser is noted.
No frost forms on the evaporator, even
if the motor-compressor is running.
In case of mechanical failure in the
motor-compressor there in an
excessive noise when the system is
functioning. In case a suspension
spring is unhooked, banging will be
heard and there will be especially
strong vibrations when the system
starts up and stops.
An empty refrigerant system indicates
a leakage of isobutane (R600a). This
loss is generally to be looked for at the
soldering points connecting the
various components or in an eventual
hole in the evaporator made by the
user.
If in the refrigerant system a quantity
of R600a is introduced which is
greater than that indicated, the excess
gas does not terminate its expansion
in the evaporator but proceeds into the
return tube.
The refrigerant system is humid when
there is a small percentage of water
present, which, not completely
retained by the dehydrator filter, enters
into circulation with isobutane and
freezes at the capillary exit in the
evaporator.
There is air in the refrigerating system
when during the filling phase vacuum
is not effected or it is not adequately
done.
Impurities contained in isobutane or
in the components of the refrigeration
system before assembly and not
retained by the filter can obstruct the
capillary.
In this case there is a mechanical
failure in the diaphram valves which
remaining continually open, do not
permit the compressor to operate.
Consequentely, isobutane does not
circulate in the system.
The cause of the excessive noise is
normally to be sought for in a
mechanical breakdown, and only
rarely in the unhooking of one of the
suspension springs.
Leakage must be eliminated by
resoldering the defective point .
The system must be emptied and
subsequently refilled introducing the
correct quantity of R600a.
The system must be emptied and then
refilled after eliminating the humidity.
Group must be drained and
subsequently refilled after carefully
creating vacuum.
Do away with the refrigerator.
The motor-comprossor must be
replaced and then proceed with
refilling.
The motor-compressor must be
replaced and then proceed with the
refilling.

5-4-2. General Control of Refrigerating Cycle
- 19 -
NO. ITEMS CONTENTS AND SPECIFICATIONS REMARKS
WELDING
ROD
(1) H 30
• Chemical Ingredients
• Ag: 30%, Cu: 27%, Zn: 23%, Cd: 20%
• Brazing Temperature: 710~840 °C
(2) Bcup-2
• Chemical Ingredients
• Cu: About 93%
• P: 6.8~7.5%
•The rest: within 0.2%
• Brazing Temperature: 735~840 °C
• Recommend H34 containing 34% Ag in the
Service Center.
FLUX • Make amount for only day.
Holding period: 1 day
• Close the cover of container to prevent dust
putting in the FLUX.
• Keep it in a stainless steel container.
LOKRING
(Figure 15,16)
(1) Both of the tube is inserted up to the stop.
(2)
Both of the LOKRING is pushed up to the stop
(3) The bending point is not too close to the
joint ending.
(4) During the assembly it is important that
both ends remain completely within the
joint.
• For a hermetically sealed metal/metal
connection, the tube ends have to be clean.
• LOKPREP is distributed all of out-surface of
the tube ends.
DRIER
ASM
(1) Assemble the drier within 30min.
after unpacking.
(2) Keep the unpacked drier at the temperature
of 80~100 °C.
• Don't keep the drier in a outdoors because
humidity damages to it.
VACUUM (1) When measuring with pirant Vacuum
gauge the charging M/C, vacuum
degree is within 1 Torr.
(2) If the vacuum degree of the cycle inside is
10 Torr. below for low pressure and 20 Torr.
for high pressure, it says no vacuum
leakage state.
(3) Vacuum degree of vacuum pump must be
0.05 Torr. below after 5 min.
(4) Vacuum degree must be same to the
value described item (2) above for more than
20 min.
• Apply M/C Vacuum Gauge without fail.
• Perform vacuum operation until a proper
vacuum degree is built up.
• If a proper vacuum degree isn't built up,
check the leakage from
the Cycle Pipe line part and
• Quick Coupler Connecting part.
(1) The pressure of dry air must be more
han 12~16kg/cm 2
(2) Temperature must be more than
-20~-70 °C.
(3) Keep the pressure at 12~6kg/cm 2also
when substituting dry air for Nitrogen Gas.
NIPPLE
AND
COUPLER
(1) Check if gas leaks with soapy water.
(2) Replace Quick Coupler in case of leakage.
• Check if gas leaks from joint of the
Coupler.
PIPE • Put all Joint Pipes in a clean box and
cover tightly with the lid so that dust or
humidity is not inserted.
1
2
3
4
5
6
7
8
DRY AND
AIR
NITROGEN
GAS
• Ingredients and how to make
Borax 30%
Borax 35%
Fluoridation kalium: 35%
Water: 4%
Mix the above ingredients and boil until
they are transformed into liquid.

- 20 -
ASSEMBLY JAWS
BOLT
TOOL
TUBE LOKRING
LOKRING JOINT
Figure 15. LOKRING
Figure 16. LOKRING TOOL
This manual suits for next models
3
Table of contents
Other LG Wine Cooler manuals
Popular Wine Cooler manuals by other brands
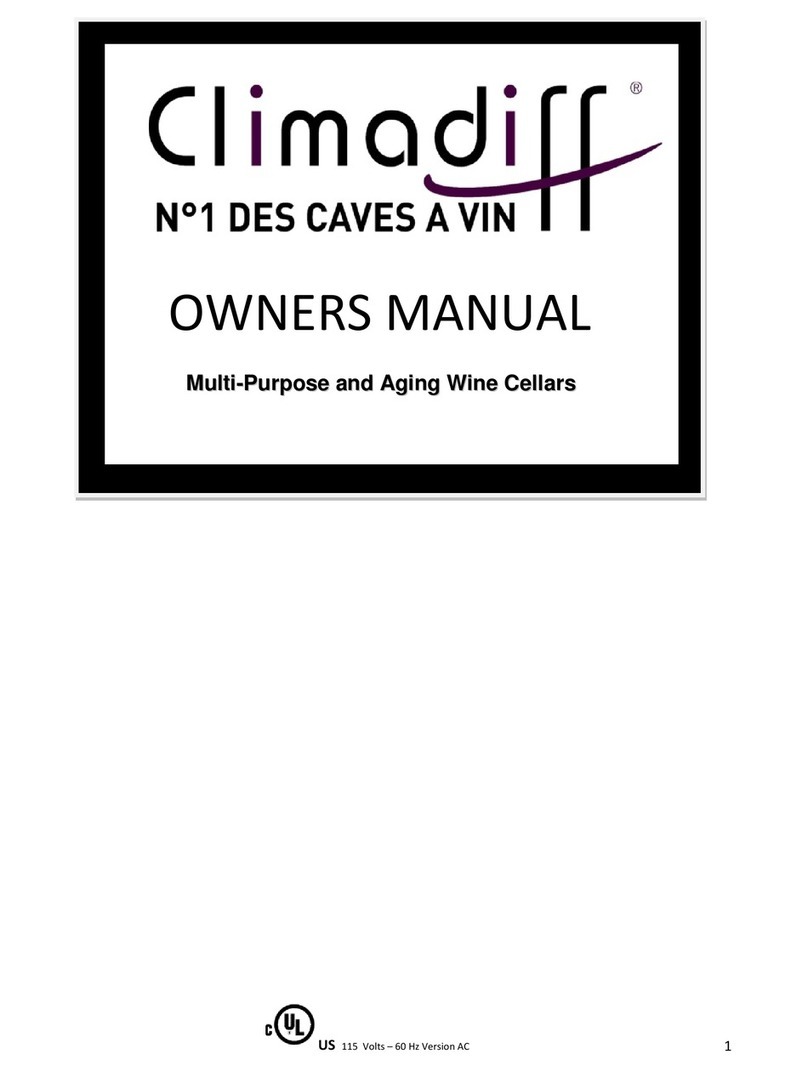
Climadiff
Climadiff Multi-Purpose and Aging Wine Cellars owner's manual

Rosehill Wine Cellars
Rosehill Wine Cellars 6ft Premier Cru Kit Rack Assembly instructions
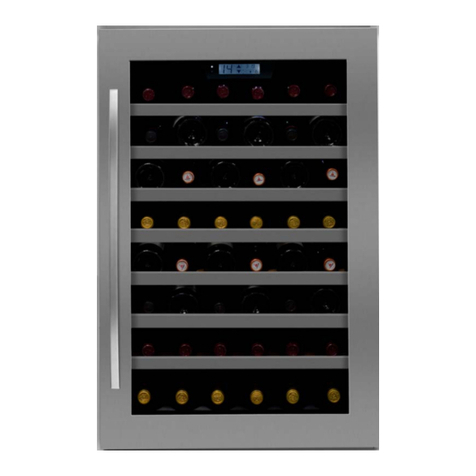
Caple
Caple WC6115 instruction manual
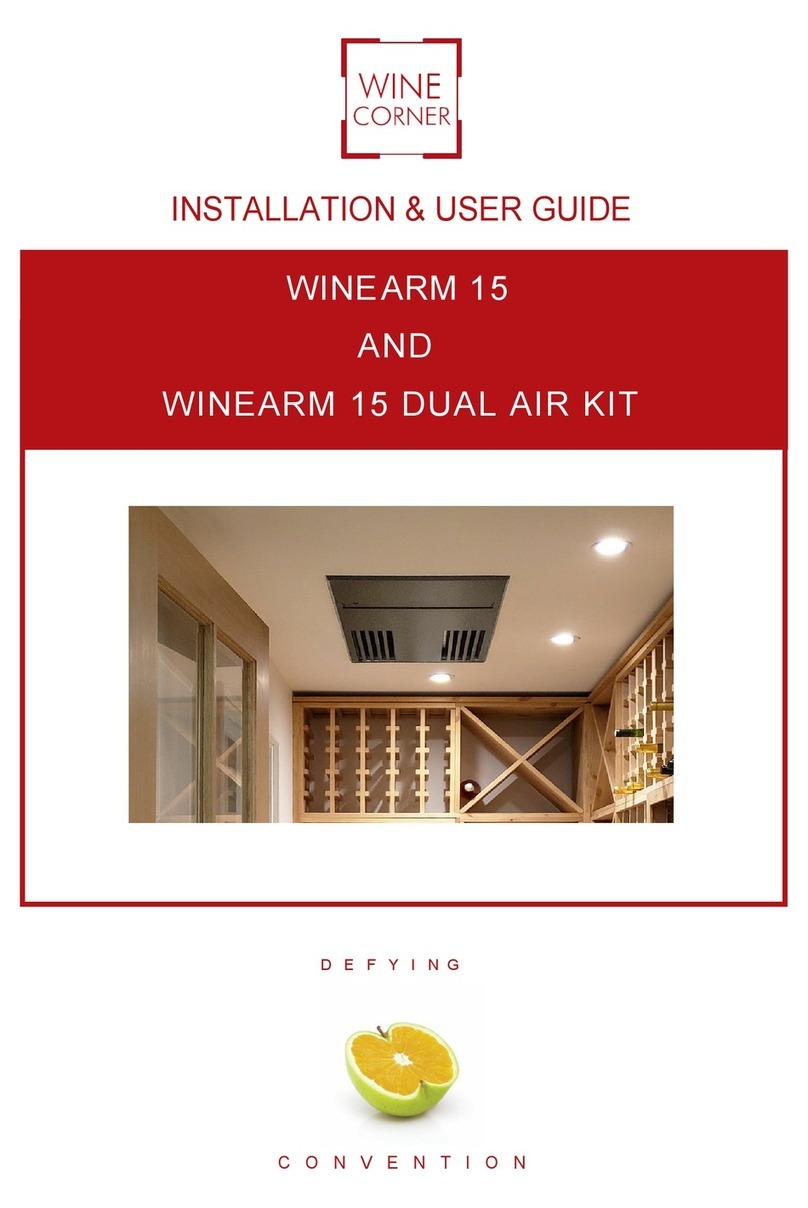
Wine Corner
Wine Corner WINEMASTER WINE ARM 15 Installation & user guide
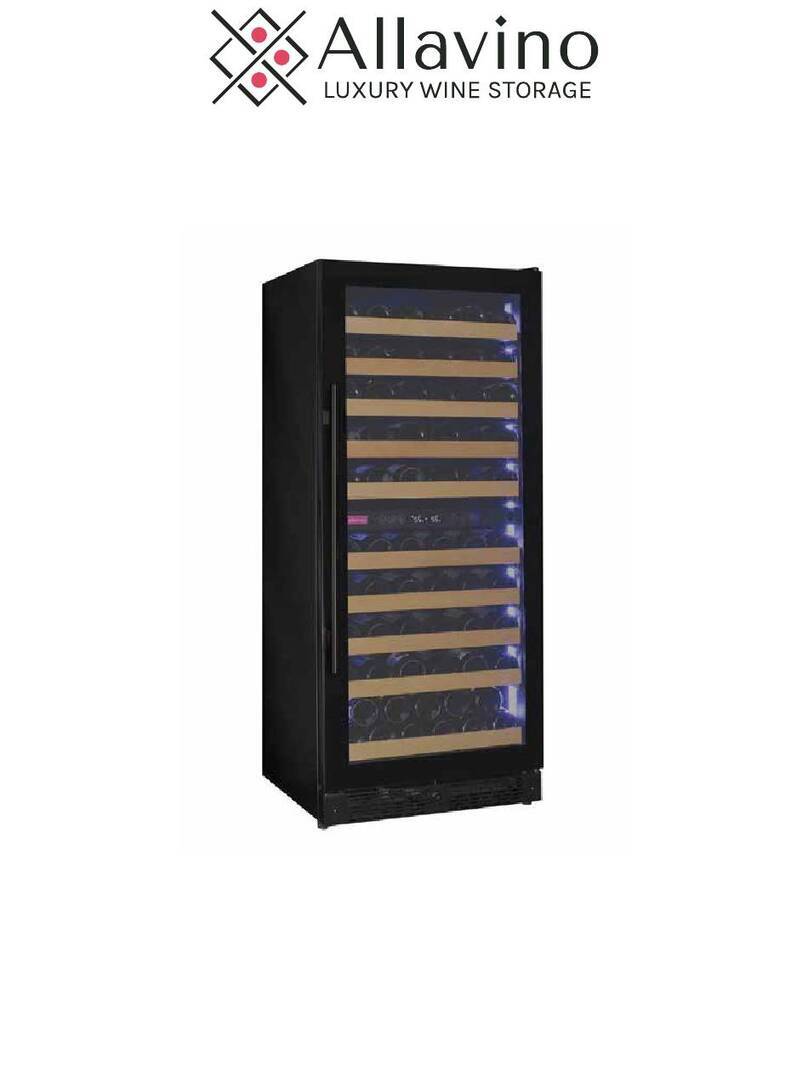
Allavino
Allavino Reserva VSW19955D-2 instruction manual
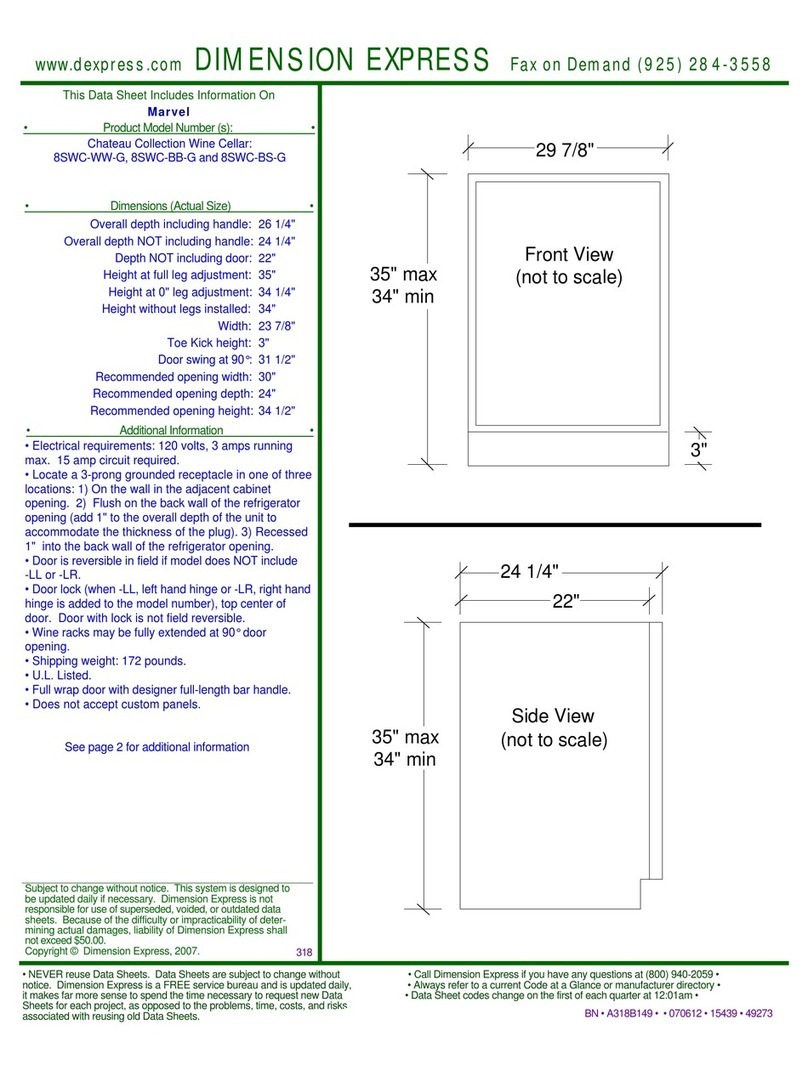
Marvel
Marvel 8SWC-BB-G datasheet