LOGIC RAIL Grade Crossing Pro/2 User manual

1
L
OGIC
TECHNOLOGIES
R
AIL
"Sophisticated
Model Railroad
Electronics"
TM
21175 Tomball Pkwy Phone: (281) 251-5813
Suite 287 email: info@logicrailtech.com
Houston, TX 77070 http://www.logicrailtech.com
Grade Crossing Pro/2
Instructions
(covers versions GCP/2, GCP/2-IR, and GCP/2-X)
Revised 2/22/2021
Getting started
Thank you for purchasing a Logic Rail Technologies product! Please familiarize yourself with all the instructions prior to
installing this board. The Grade Crossing Pro/2 (versions GCP/2, GCP/2-IR, and GCP/2-X) provides prototypical operation
of a grade crossing. The crossing signal outputs can be used with common anode LED signals (e.g. Tomar, NJ International,
Walthers and others) or older bulb types. There is a separate output for an end-of-gate-arm light. Outputs are provided for 1-2
Tortoise motors and servo motors to drive the gate arms. Four sensors (photocells or infrared emitters and detectors) are used
for bidirectional train detection. External detectors (available from other suppliers) can also be used. The layout of the
sensors is illustrated below. You MUST install the sensors in the exact order (WF-WN-EN-EF) shown!
W E
Sensor
WF
Sensor
WN
Sensor
EN
Sensor
EF
What is different from the original version of the Grade Crossing Pro (GCP and GCP-IR)?
Signal outputs are turned on in sequence (Left Right End-of-gate arm), briefly, when power is first applied
to the board. This gives you a quick test of the signals to make sure all the connections are correct and the signals
work!
There are individual sensor status indicators on the circuit board. These not only help you when first setting up
the board but are also active when in “operating” mode.
There is no need to swap chips on the board if you want to use a photocell, infrared between-the-rails, infrared
across-the-rails, and external detectors. However, you will need to decide which sensor type (photocell or
infrared), if any, you want at the time of purchase. Both sensor types are still available separately (#PCELL or
#BTR-IR4) if you want to change types!
The board is also offered without sensors (version GCP/2-X) for use with other brands of external detectors.
The infrared detection method has been improved and no longer has strict limits on the incoming voltage. NOTE:
the IR emitter wiring is different from the previous generation product!!! Please pay close attention to this.
We added an End-of-Gate arm LED output which is on continuously when the signals are flashing.
We added support for servo motors to operate gate arms; there are separate outputs for Tortoise ™ motors.
The board has a socket for a grade crossing bell module. We are offering different versions (classic, electronic,
fast, Griswold) under our own brand. The bell sound will fade off as the signals stop flashing.
There are different “timing” options for lowering the gates and when the bell should be ringing.
Use the Grade Crossing Pro/2 Expander to handle an additional track for multi-track crossings.
How does it work?
An eastbound (left to right) train will cause the signals to begin flashing when the WF sensor is activated. If a bell module is
attached it will start ringing then too. If crossing gates are being used (GATES USED switch ON) then after a short delay
(see GATE DELAY switch description further down) the gate motor outputs will turn on and the gates will lower. The
signals will continue to flash even if the rear end of the train clears the WF sensor as long as the front end of the train reaches
the WN sensor within 35 seconds. Assuming the train does this and then subsequently reaches the EN sensor the signals will
continue flashing. Approximately 2 seconds after the rear end of the train clears the EN sensor the gate motor outputs will
shut off and the gates will begin to rise. Approximately 3 seconds later the signals will stop flashing and the bell will stop
ringing. If no gates are used (GATES USED switch OFF) then the signals will stop flashing and the bell will stop ringing
approximately 2 seconds after the rear end of the train clears the EN sensor. There are other “timing” options related to the
operation of the bell (BELL MODE and BELL SHUTOFF switches); these are described later in these instructions.

2
If the train had not reached the WN sensor within 35 seconds of clearing the WF sensor then the Grade Crossing Pro/2 will
assume the train has reversed. This “timeout” will cause the “action” to shut off as previously described above. Similar
behavior exists for a westbound train with respect to sensors EF, EN and WN (shut off occurs after the last car clears the WN
sensor). The WF and EF sensors may be located as far away from the crossing as you would like. If you are installing gates
then putting these farther out will give the gates enough time to lower before the train reaches the crossing. An HO scale
train running a scale 40 MPH would cover 12 inches in about 1.5 seconds. You will likely choose to have your gates lower in
approximately 4 seconds. So, that would suggest that you should locate WF and EF around 36 inches from the crossing;
consider more distance if you’re running faster trains or less distance if you’re running slower trains! If you are NOT
installing gates then you can choose to place WF and EF wherever convenient and whatever amount of advance notice you
want to give your scale motorists before the train reaches the crossing!
You should make all of the connections to the Grade Crossing Pro/2 before applying power to it. You can mount the Grade
Crossing Pro/2 anywhere it is convenient underneath your layout using the four mounting holes provided. The holes will
accept #4 screws; do not enlarge the holes as damage to the circuit board can result and your warranty will be voided!
The Grade Crossing Pro/2 board has a set of 9 configuration switches on it. Each switch is briefly described below with
more details later in these instructions.
Switch Name Meaning when OFF/OPEN Meaning when ON/CLOSED
SETUP
GCP
/2
is in normal operating mode
GCP
/2
is in
sensor
setup mode
TRUE L
AMP
2
Signals don’t
fade on/off (like modern signals)
Signal
s fade on and off (like older signals)
SEN TYPE Sensors are photocells or external current
detectors
Sensors are infrared
SEN POL
See text in the Sensor Modes section
See text in the Sensor Modes section
FLASH
RATE
Normal f
lashing
rate
Fast (2X) f
lashing
rate
(see page 3)
GATES USED
Crossing gates are NOT used
Crossing gates are used
GATE DELAY
Signals flash for ~3 seconds before gates lower
Signals flash for ~1.5 seconds before gates lower
BELL MODE The bell rings continuously while the signals
are flashing
The bell rings only when the gates are moving up
or down (must also have GATES USED ON)
BELL SHUTOFF
The bell shuts off when the flashing stops
See text in the Bell section
Wiring Tomar’s LED-based crossing signals
Tomar’s LED-based crossing signals are pre-wired in a common anode (positive) manner. Since these are dual-sided signals
(i.e. LEDs on both sides of each signal mast) there are 2 yellow and 2 red wires (one from each LED’s cathode) and one
common white wire. Figure 1 below shows you how to wire ONE signal. The Grade Crossing Pro/2 will support two dual-
sided signals; if you are using two signals then simply replicate the wiring shown for the second signal. Note that EACH
LED connection requires a current limiting resistor. The value of the resistor is dependent upon the voltage applied to the
GCP. You can use Table 1 to determine the MINIMUM resistor value. You can always substitute a ½ watt resistor for a ¼
watt resistor. You can always use a higher value resistor (i.e. more OHMS!) if your signals are too bright to your liking.
Common (white)
Left Front (yellow)
Left Rear (yellow)
Right Front (red)
Right Rear (red)
Figure 1 – Wiring Tomar’s LED-based signals
Voltage supplied to
GCP/2
Minimum Resistor
Value
9V DC
390 ohm,
1/4W
12V DC
470 ohm, 1/4W
14V DC
680 ohm 1/4W
7
V AC
39
0 ohm, 1/4W
9
V AC
560
ohm, 1/
4
W
12
V AC
1K
ohm, 1/
4
W
16V AC
1.2K ohm, 1/4W
Table 1 – Current limiting resistors

3
Wiring other LED-based crossing signals (including Walthers)
If you are using another brand of LED-based crossing
signals, or are scratch-building your own, you MUST wire
them in a common anode (positive) manner. NOTE: some
manufacturers use a black wire for the common wire but that
does NOT mean that it is a negative or ground wire! Figure 2
at right shows you how to wire ONE single-sided signal; if
you are using multiple signals, or dual-sided signals, simply
duplicate the wiring shown for the additional LEDs. Each of
the Grade Crossing Pro/2’s signal outputs can handle loads
up 180mA (~12 LEDs). Note that EACH LED connection
requires a current limiting resistor. The value of the resistor
is dependent upon the voltage applied to the Grade Crossing
Pro/2. You can use Table 1 above to determine the minimum
resistor value. Note that some of the resistors can be ¼ watt
whereas others must be ½ watt. You can always substitute a
½ watt resistor for a ¼ watt resistor but you CANNOT
substitute a ¼ watt resistor for
a ½ watt resistor!
common anode
Figure 2 – Wiring LED-based crossing signals
Wiring bulb-based crossing signals (e.g. NJ International)
Crossing signals constructed with bulbs do not have a
polarity like LED-based signals do. However, some bulb-
based signals may be pre-wired with a common wire. If your
signal does not, then you will simply create a common
connection from one lead of each bulb (it doesn’t matter
which lead is used). Figure 3 at right shows you how to wire
ONE single-sided bulb-based signal. The Grade Crossing
Pro/2 will support two dual-sided signals; if you are using
multiple signals, or dual-sided signals, simply duplicate the
wiring shown for the additional bulbs. Note that current
limiting resistors are shown. These are only required IF the
voltage provided to the Grade Crossing Pro/2 is greater than
the rating on the bulbs; most bulbs are rated at 12V AC or
DC but you should check the instructions that come with the
signal. If the Grade Crossing Pro/2 voltage source exceeds
the bulb rating then add current limiting resistors as shown;
we recommend a value of 100Ω, ¼ watt.
Common
Figure 3 – Wiring bulb-based crossing signals
Flashing effects (True Lamp2 and Flash Rate)
As shown in the table on page 2 the Grade Crossing Pro/2 has two configuration switches related to the crossing flasher
outputs (LO and RO). The first is TRUE LAMP2. When this switch (#2) is in the ON position the LO and RO outputs will
fade on and off which emulates older prototype crossing signals (when they used light bulbs). When this switch is OFF the
LO and RO outputs will simply turn on and off during the flashing activity; this setting emulates newer prototype crossing
signals which may use LEDs. If you are using bulb-type model railroad crossing signals we strongly suggest that you keep
this switch OFF.
The other flashing effect is the flash rate itself. The normal flash rate is selected when the FLASH RATE switch (#5) is in the
OFF position. If you prefer the faster (2X speed) rate you MUST have BOTH the FLASH RATE switch in the ON position
AND have the TRUE LAMP2 switch in the OFF position. As such you CANNOT have the faster flash rate and the signal
on/off fading effect at the same time.
End-of-Gate (EOG) LED
The Grade Crossing Pro/2 has a separate output (EOG) which can be used to turn on an LED wired to the end (tip) of a
crossing gate. Like the prototype crossing gates, this output will be active (on) whenever the signals are flashing. It will be on
steady (the True Lamp2 configuration switch setting does not affect it). You will wire this LED just like the LO or RO LEDs
shown in Figures 1 and 2. Don’t forget the current limiting resistor! This output can handle loads up 180mA (~12 LEDs).

4
Wiring a slow motion motor to drive a crossing gate
The Grade Crossing Pro/2 will directly drive a slow motion
motor that is typically used with crossing gates such as those
from Tomar. Figure 4 shows how the Grade Crossing Pro/2
is connected to a motor; the Grade Crossing Pro/2 can drive
a max of two motors (one per gate if you prefer to use
separate motors). If the gates are raised when the signals are
flashing and lower when the signals are not flashing then you
simply need to reverse the motor connections. You can
adjust the speed of the gate motor on the Grade Crossing
Pro/2. Using a flat blade screwdriver insert it into the gate
speed adjustment pot (from the top of the circuit board).
Turning the screwdriver clockwise will increase the gate
speed while turning the screwdriver counter-clockwise will
decrease the gate speed. You MUST have the GATES
USED configuration switch in the ON position!
M
1
8
Tortoise TM
Figure 4 – Gate Motor Wiring (Tomar example)
NOTE: You must check the instructions for your gate motor to determine the maximum voltage that the motor can
accept. For example, Tomar uses Circuitron’s Tortoise™ which has a maximum voltage rating of 12V DC or AC. If
the voltage provided to the GCP is greater than the rating on the motor then you will need to add a current limiting
resistor (we recommend a value of 390Ω, ½ watt) in the connection path between one of the GCP/2’s GM outputs and
the turnout motor.
Wiring a servo motor to drive a crossing gate
Sensor modes
The Grade Crossing Pro/2 supports four different sensor (detector) modes: photocell, between-the-rails infrared, across-the-
rails infrared, and external detector. When you purchased this product it either came with photocells, infrared components or
neither (board only, for use with external detectors). The sensor mode is selected using the switches labeled SEN_TYPE and
SEN POL as depicted in Table 2 below.
Photocell
SEN TYPE – OFF
SEN POL - OFF
Between-the-rails Infrared
SEN TYPE – ON
SEN POL - ON
Across-the-rails Infrared
SEN TYPE – ON
SEN POL - OFF
External Detector
SEN TYPE – OFF
SEN POL - ON
Table 2 – Sensor mode selection

5
Using photocells for train detection
The photocells should be mounted between the rails in the
general area where you will locate the signal. Drill a 9/64"
hole through the ballast, roadbed, and sub-
roadbed. For the
smaller scales this drilling may end up hitting the ties. Take
your time so y
ou don’t mangle them! Figure 5
illustrates the
placement of a photocell in between the rails. Insert the leads
of the photocell into the hole from the top of your layout. One
of the photocell leads has a piece of insulation on it so be sure
the two leads d
on't touch each other! If the leads do not
Figure 5 – photocell placement
protrude enough from the underside of your layout then it will be necessary to extend the leads; soldering wires to them is t
he
most common method; make
sure you insulate any connections you make to the photocell leads so that they don't short out.
Once you have wired the photocells to the Grade Crossing Pro/2
and verified their operation you may wish to put a dab of
white glue under the photocell to hold
it in place; make sure you don't get glue on the top surface of the photocell as this may
prevent it from operating properly. Figure 6
illustrates the photocell wiring; make sure you have the photocells in the correct
order as shown at the top of page 1.
Photocells do not have any polarity so you can connect either lead to the GND terminal
and connect the remaining lead to the appropriate photocell input.
Photocells require a light source above them to
function properly. On most layouts the room
lighting should be sufficient. However, if the
photocells are located in an area that doesn't get
much overhead lighting or if you have simulated
"nighttime" operations then it will be necessary
to locate light sources on the layout near the
photocells. Streetlights and yard lights are
common light sources. Locate the light sources
slightly to the left or right of the photocells and
not directly over them; this will allow the Grade
Crossing Pro/2 to still properly detect a train
that has stopped over any photocell with the gap
between cars over a photocell.
EN EF
WNWF
Figure 6 – Photocell wiring
Photocell sensitivity setup
You can adjust the sensitivity of each photocell on the circuit board using a small slotted head
screwdriver. Along one each of the board are four potentiometers (or “pots”) that are labeled
"WF", “WN”, “EN” and “EF”. The Grade Crossing Pro/2 supports a SETUP mode to make
this adjustment process easier. To enable this mode, you must have the switch labeled SETUP
in the ON/CLOSED position as shown in Figure 7. In this mode the signals will not flash. The
Grade Crossing Pro/2 circuit board contains four sensor status LEDs; one near each of the four
adjustment pots. These LEDs will assist you in setting the photocell sensitivity.
Figure 7 - SETUP mode
Now follow these steps
after you have connected power
(see page 9
)
to the board
:
1. Remove all obstacles that may be covering the photocells or blocking overhead light to them.
2. Insert the blade of the screwdriver (from the edge of the circuit board, not from the center of the board) into the
adjustment pots, one at a time. Turn the screwdriver completely counter-clockwise (left) in all FOUR of the pots.
3. For the adjustment pot labeled WF turn the screwdriver clockwise (right) until the red LED near the pot just lights
up. Then turn the screwdriver back counter-clockwise until that LED goes out.
4. Repeat step 3 for the three remaining pots with corresponding LEDs.
5. Exit SETUP mode by putting the SETUP switch in the OFF/OPEN position (“operational” mode). The flashing and
other action should now operate properly. It may be necessary to repeat this procedure if layout lighting conditions
change significantly. Note that the Grade Crossing Pro/2 will activate the sensor status LEDs when the associated
sensor detects a train in “operational” mode; this is different from the previous generation Grade Crossing Pro!
Turning the pots clockwise adjusts for brighter overhead lighting conditions while turning the pots counter-clockwise
adjusts for dimmer overhead lighting.

6
Using between-the-rails infrared
The IR components should be mounted between the rails. Drill two 11/64” holes, through
the ballast, roadbed, and sub-roadbed. These holes should be located one tie apart (Figure
8a) and drilled at a slight angle from vertical (see Figure 8b). The benefit of mounting
them at an angle is increased detection reliability in smaller scales or irregular bottoms on
rolling stock. For the smaller scales this drilling may end up hitting the ties. Take your
time so you do not mangle them! Insert the leads of one IR emitter (white and black
wires) into one of the holes (it does not matter which one!) from the top of your layout.
Repeat for the IR detector (blue and black wires). The tops of the components should sit
no higher than the top of the ties for optimal IR performance; in some cases (e.g. false
triggering) it may be necessary to locate the components a little below the ballast line.
You can extend the leads with similar (or larger) wire. We recommend soldering and
insulating these connections. We also recommend using terminal blocks/strips since you
will have multiple +5V and GND connections to make. Once you have wired the IR
components and verified their operation you may wish to put a dab of white glue or
silicone caulk where the wires exit the holes underneath the layout. This will help to hold
the components in place; make sure you do not get any substance (e.g. ballast or glue) on
the top surface of the IR components as this may prevent them from operating properly. In
extreme cases where you may be getting interference from overhead lighting you can
mount the IR detector in some plastic or metal tubing. You can also recess the IR detector
slightly below the ties and roadbed.
Figure 8a
Figure 8b
Using across-the-rails infrared
With this sensor mode and physical arrangement a train is detected when the
infrared (IR) beam is broken by the train. The IR components should be located
across the track as shown in Figure 9a and 9b; the distance between them has
been tested up to 16 inches. The detectors (dark lens, blue and black wires)
should be mounted with a slight downward angle in order to minimize the
possibility of false triggering from visible light sources; this is illustrated in
Figure 9a. We would also recommend that you angle the emitters and detectors
across the track as shown in Figure 9b. This will minimize false “clear”
situations due to the space between rolling stock. You can bend the IR emitter
and detector components IF you are VERY careful and, preferably, use a pair of
“smooth jaw” (no teeth/serration) pliers!! Make the bend on the IR component
NO CLOSER than 0.5” from the tip. You don’t want to pierce the insulated heat
shrink tubing and potentially cause a short.
In the event the leads do not reach the circuit board you can extend them with
similar (or larger) wire. We recommend soldering these connections or using
terminal blocks/strips especially when you have multiple connections to make.
Aligning the IR components for reliable detection might be a bit challenging.
We recommend the use of a straight edge or ruler for initial “rough” alignment.
You can tweak the final alignment once you are ready to test the circuit.
Since the IR components are located trackside, you will probably want to
consider “hiding” them. There are numerous ways to do this such as using
shrubbery, small equipment buildings or fixtures. We leave this exercise up to
your imagination and creativity! We would strongly suggest that you get the
circuitry working properly first, and then address the physical appearance.
Figure 9a
Emitter
Detector
Figure 9b

7
IR component wiring
Please note that the IR emitter wiring is DIFFERENT
from the previous generation Grade Crossing Pro!
Figure 10 illustrates the wiring for ONE
set of IR
components (shown for sensor location “WF”).
REPLICATE the same wiring for the three
remaining sensor inputs!
Four 68 ohm ¼ watt
resistors (Blue-Gray-Black color bands)
are included
with the Grade Crossing Pro/2
. When properly wired
the emitters
will have a very faint red glow. You can
“see” the infrared light using your digital camera or
smartphone camera!
For safety reasons do NOT point
the IR emitter directly into your eye or stare at the
IR emitter!!! The Grade Crossing Pro/2
supports a
SETUP
mode which can be used to verify proper
operation of the sensors. To enable this mode, you must
have the switch labeled SETUP in the ON/CLOSED
position as shown in Figure 7. In this mode the signals
will not flash.
There are four sensor status LEDs; one
68 ohms
1/4 watt
Detector
Blue
wire
Black
wire
Emitter
Black
wire
White
wire
Figure 10 – IR component wiring
(WF input shown; replicate for WN, EN and EF inputs respectively)
near each of the four photocell sensitivity adjustment pots. NOTE: The four adjustment pots have NO affect when using
either infrared sensor mode! Do the following after you have connected power (see page 9) to the board:
With nothing over
or blocking any of the IR components the red sensor status LEDs on the circuit board should all be OFF. Place a piece of
rolling stock at each detection location, one at a time, and confirm that the associated red sensor status LED turns ON. Don’t
forget to turn OFF the SETUP switch when finished!
Using an external detector
Use this sensor mode if you would prefer to use a different type of detector such as an NCE BD20 current sensing detector.
Any brand of detector should work provided that its output is an open collector, “active low” polarity, which means that
when a train is detected the output is pulled to ground. When no train is sensed the detector output is an open circuit or
“floating.” You will need 3 detection blocks or zones. Figure 11 shows how they would be partitioned. Figure 12 shows how
simple it is to connect the BD20 block detectors to the Grade Crossing Pro/2. NOTE: The four adjustment pots have NO
affect when using this mode!
W E
WO ow
Crossing
section
East
approach
section
West
approach
section
Figure 11 – External detector zone partitioning
STOP

8
West
approach
detector
GND OUT
Center
block
detector
GND OUT
East
approach
detector
GND OUT
GND
2
1
OUT
Figure 12 – External detector wiring (NCE BD20 shown)
Grade crossing bell
The Grade Crossing Pro/2 can control a grade crossing bell sound module in two ways. The preferred way, and less
expensive option, is to plug in one of the bell modules we offer (#BELL-CL, #BELL-MD, #BELL-FA, #BELL-GS). If you
use one of these modules the Grade Crossing Pro/2 will fade the sound off when shutting off the bell. There are two sockets
on the board to accept the module as shown in Figure 13a below. Carefully install the bell module by lining up the pins on
the bottom of the module to the mating sockets on the Grade Crossing Pro/2 board. Note that when the module is properly
installed the bell module label will have the printing oriented in the same direction as the Grade Crossing Pro/2’s main chip.
Also, there will be two open socket locations along the top end of the lefthand socket. A properly installed bell module is
shown in Figure 13b below. The bell module requires an 8Ω speaker connected to the SPKR outputs as shown in Figure 13b.
You can adjust the volume of the bell sound using the potentiometer labeled VOLUME next to the SPKR terminals.
Figure 13a -
Location for bell module
8Ω
Figure 13b – Bell module installed
Figure 14 shows the wiring for an external grade crossing bell sound module. Shown is the ITT sound module version from
2018 through the date on this document; contact us if you have a different version! You will need a 6 conductor ribbon cable
(available from us, part number X-CABLE) to make the connections. The black connector end plugs onto the 6 pin header
labeled “EXPAND” on the Grade Crossing Pro/2 board. Make sure that the red stripe on the cable is closest to the edge of
the board; there is a white stripe printed on the board to the left of the 6 pin header as a hint! Pin 1 (red stripe) of the cable
provides +DC power to the bell module while pin 6 of the cable provides the “ground” connection to the bell module when it
is turned on by the Grade Crossing Pro/2. Note that you must install a small wire jumper between the two terminals on the
bell module labeled SW. Finally, connect any 8 ohm speaker to the bell module. The ITT sound modules have their own
volume control; the volume control on the Grade Crossing Pro/2 does NOT affect an external bell module!

9
Jumper wire
8Ω
1 6
Figure 14 – External bell module
Gate and bell timing options
The Grade Crossing Pro/2 has three configuration switches which give you several options for the timing of the gates
lowering and ringing the bell (if a bell module is installed or attached externally). The crossing gate motor outputs will
activate (i.e. to lower the gate arms) either approximately 3 seconds after the signals start flashing (GATE DELAY switch in
the OFF position) or approximately 1.5 seconds after the signals start flashing (GATE DELAY switch in the ON position).
There are examples of prototype crossing gate behaving either way!
The bell module will always be turned on as soon as the signals start flashing. When the bell rings after that is based on the
combination of the GATES USED, BELL MODE and BELL SHUTOFF switches. The behavior is described below.
GATES USED BELL MODE BELL SHUTOFF Bell behavior
OFF
(doesn’t matter)
(doesn’t matter)
Ring
s
continuously
while signals are flashing
ON
OFF
OFF
Rings continuously while signals are flashing
ON
OFF
ON
Stops ringing as the train clears but before flashing stops
ON
ON
OFF
Only rings while gates are lowering or raising
ON ON ON Only rings while gates are lowering; no ringing when gates
rise!
Once again there are examples of prototype crossing bells behaving in each of these ways!
Power
The Grade Crossing Pro/2 accepts AC or DC power (7 - 16V). Power consumption, including the signals, ranges from ~90
mA (photocell version) to ~225 mA (infrared version). If you are only using a single board then you can use the AC terminals
to provide power as shown in Figure 15a. You can use the accessory terminals on your throttle/power pack. If you are using
more than one Grade Crossing Pro/2 (for example, if you’re interlocking with turnout positions) then you should consider
powering them all from a single DC source as shown in Figure 15b. Watch the polarity and make sure you know what is
positive! Contact us if you are uncertain! When power is first applied the signal outputs will turn on briefly in sequence (Left
Right End-of-gate-arm).
7-16V
DC
Power
Source
7-16V
+
-
Figure 15a – AC power Figure 15b – DC power

10
Multi-track grade crossings (using photocell detection)
There is an obvious tendency to just add additional photocells to handle additional tracks when you have a multi-track grade
crossing. The problem with this implementation is that the Grade Crossing Pro/2 cannot differentiate between two trains
traveling in opposite directions on different tracks. As such it could easily get “confused” and not provide the prototypical
sequencing (i.e. the action starts when the train covers a far photocell and the action stops when the train clears the near
photocell on the other side of the crossing). If you will have multiple trains traveling through the crossing area (with outer
boundaries defined by the far photocells) at the same time then you must use one Grade Crossing Pro/2 for the first track and a
Grade Crossing Pro/2 Expander for each additional track. See the next section for details on how to connect the Grade
Crossing Pro/2 Expander(s). IF you operate your trains such that only ONE train can possibly go through the crossing area at a
time then you CAN simply add additional photocells (part number PCELL; $2.00 each available from us) for the additional
tracks. In this implementation you will wire the additional photocells in series with their counterparts on adjacent tracks. Figure
16 below illustrates the photocell wiring for a two-track crossing. You MUST go through the photocell sensitivity adjustment
process on pages 5. Do NOT use more than 3 photocells in series for each sensor input (i.e. 3 tracks) as we cannot guarantee
reliable operation!
EN1 EF1
WN1WF1
EN2 EF2
WN2WF2
Figure 16 – Two track crossing using extra photocells
Multi-track grade crossings (using between-the-rail infrared detection)
There is an obvious tendency to just add additional sensors to handle additional tracks when you have a multi-track grade
crossing. The problem with this implementation is that the Grade Crossing Pro/2 cannot differentiate between two trains
traveling in opposite directions on different tracks. As such it could easily get “confused” and not provide the prototypical
sequencing (i.e. the action starts when the train covers a far sensor and the action stops when the train clears the near sensor on
the other side of the crossing). If you will have multiple trains traveling through the crossing area (with outer boundaries defined
by the far sensors), at the same time, then you must use one Grade Crossing Pro/2 for the first track and a Grade Crossing
Pro/2 Expander for each additional track. See the next section for details on how to connect the Grade Crossing Pro/2
Expander(s). IF you operate your trains such that only ONE train can possibly go through the crossing area at a time then you
CAN simply add additional sensor sets (available from us) for the additional tracks. In this implementation you will wire the
additional sensors the same way you did for their counterparts on the first track (i.e. per Figure 10). For example, the blue wire
from ALL of the WN detectors will connect to the WN terminal on the Grade Crossing Pro/2.
Multi-track grade crossings (using across-the-rail infrared detection)
There is an obvious tendency to just space out the IR emitters and detectors such that they span all tracks for a multi-track grade
crossing. The problem with this implementation is that the Grade Crossing Pro/2 cannot differentiate between two trains
traveling in opposite directions on different tracks. As such it could easily get “confused” and not provide the prototypical
sequencing (i.e. the action starts when the train covers a far sensor and the action stops when the train clears the near sensor on
the other side of the crossing). To avoid this situation you will need to use one Grade Crossing Pro/2 for the first track and a
Grade Crossing Pro/2 Expander for each additional track. See the next section for details on how to connect the Grade
Crossing Pro/2 Expander(s).

11
Multi-track grade crossings using the Grade Crossing Pro/2 Expander
For the most realistic, “no operational exceptions” grade crossing behavior you will need one Grade Crossing Pro/2 Expander
for each additional track beyond the first one. The Grade Crossing Pro/2 Expander connects to the Grade Crossing Pro/2
with a single cable which is included with each Grade Crossing Pro/2 Expander. Connect one end of the cable, with the red
stripe aligned to the left edge of the circuit board, as shown in Figure 17a, to the lower 6-pin header on the Grade Crossing
Pro/2 Expander board; use the upper 6-pin header to connect any additional Grade Crossing Pro/2 Expander boards.
Connect the other end of the cable to the 6-pin header on the Grade Crossing Pro/2 board; again, align the red stripe to the
left edge of the board as shown. Zoomed in views are shown in Figures 17b and 17c. Please refer to the Grade Crossing
Pro/2 Expander instructions for all other details on wiring, switch configuration and setup.
Figure 17a – Connecting the GCP/2 and GCP/2 Expander
Figure 17b – GCP/2 Expander with cable attached
Figure 17c – GCP/2 with cable attached
Troubleshooting – photocell sensing
If your signals do not flash when the sensors are covered or flash all the time you can perform the following tests. First, verify
that you have the sensor mode configured correctly (see Table 2 on page 4). Second, revisit the photocell sensitivity adjustment
process on pages 5. A loose or missing wire connection on a photocell will cause its status LED to stay on all the time!
Troubleshooting – Between-the-rails infrared sensing
If your signals always flash even when no train is present then you will probably see one or more of the red sensor LEDs lit up
on the Grade Crossing Pro/2 board. You may have the IR components sitting too high. Make sure they are no higher than the
top of the railroad ties otherwise the IR “light” can leak across and be seen by the detector. Also make sure that none of the
detector blue and black wires are touching each other. This would be will be interpreted as an activated sensor.
If your signals fail to flash yet one or more of the red sensor LEDs is lit up then double check the signal wiring. A typical error is
assuming that the common wire connects to ground (GND); it doesn’t! The common wire must connect to the DC terminal
regardless of the color of that wire!
If your signals fail to flash when you cover a particular sensor location then double-check your sensor wiring. A missing sensor
connection (missing wire or open circuit) will be interpreted as a cleared sensor. Verify the glow of the IR emitters using a
digital camera or smartphone camera. Also verify that you have the sensor mode configured correctly (see Table 2 on page
4).
You can determine if the sensor inputs are working correctly by TEMPORARILY disconnecting all blue sensor wires from
the board. If any of the red sensor LEDs are lit then the main chip on the board may be at fault. Contact us for further help.
Otherwise, connect each sensor input (WF, WN, EN, EF) to GND, ONE sensor input at a time. An activated sensor appears
to the board like a low voltage connection so you are, in effect, mimicking an activated sensor with this test. If the sensor’s
associated red LED does NOT come on when you make that temporary connection then you may have a problem with the
board and you should contact us. If the sensor red LED did light up with the temporary connection then you may have a
defective IR detector.

12
Troubleshooting – Across-the-rails infrared sensing
[This section still needs to be written!!!]
Warranty
This product is warranted to be free from defects in materials or workmanship for a period of one year from the date of purchase.
Logic Rail Technologies reserves the right to repair or replace a defective product. The product must be returned to Logic Rail
Technologies in satisfactory condition. This warranty covers all defects incurred during normal use of this product. This
warranty is void under the following conditions:
1) If damage to the product results from mishandling or abuse.
2) If the product has been altered in any way (e.g. soldering to the circuit board).
3) If the current or voltage limitations of the product have been exceeded.
Requests for warranty service must include a dated proof of purchase, a written description of the problem, and return shipping
and handling ($8.00 inside U.S./$20.00 outside U.S. - U.S. funds only). Except as written above, no other warranty or
guarantee, either expressed or implied by any other person, firm or corporation, applies to this product.
Technical Support
We hope the preceding instructions sufficiently answer any questions you might have about the installation of this product.
However, technical support is available should you need it. You can reach us via phone or email; our contact information can be
found on the top of page 1.
This manual suits for next models
3
Table of contents
Other LOGIC RAIL Control Unit manuals
Popular Control Unit manuals by other brands
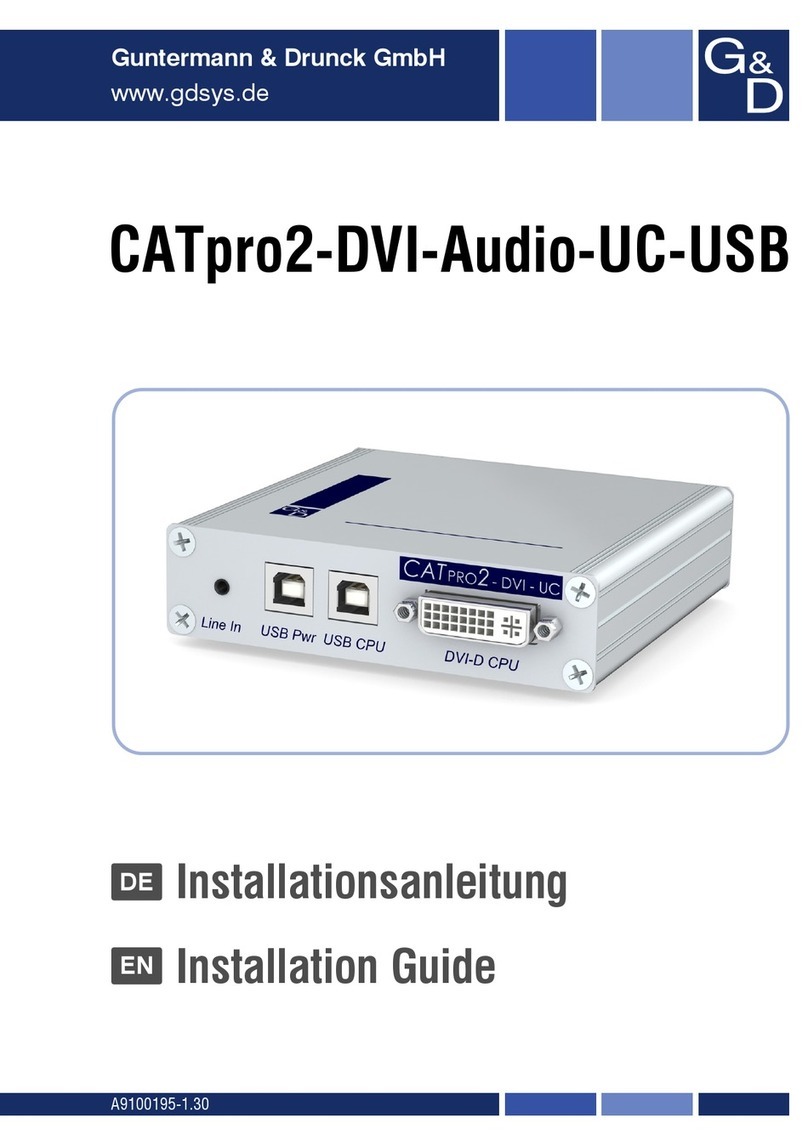
Guntermann & Drunck
Guntermann & Drunck CATpro2-DVI-Audio-UC-USB installation guide
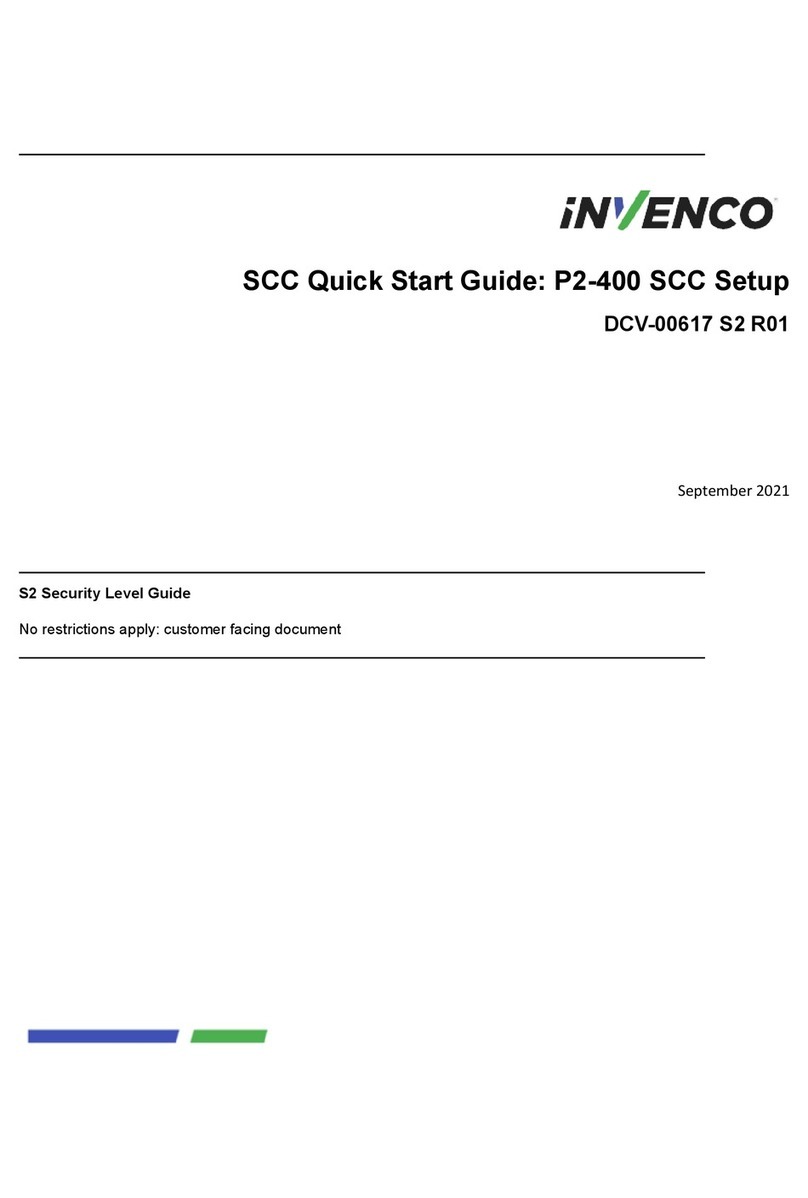
Invenco
Invenco P2-400 SCC quick start guide

Alderon Industries
Alderon Industries Big Switch Pump Control Operation, maintenance and installation manual

Micro control systems
Micro control systems MCS-BMS-GATEWAY-see manual
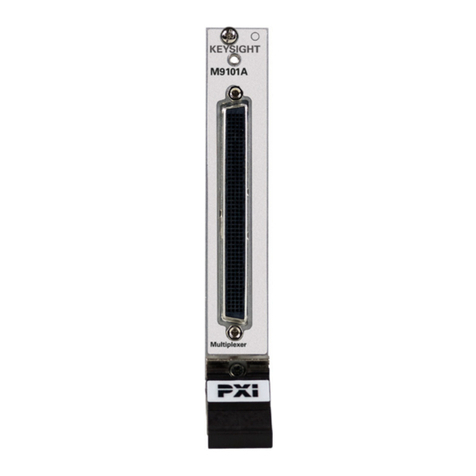
Keysight Technologies
Keysight Technologies M9101A Maintenance Guide
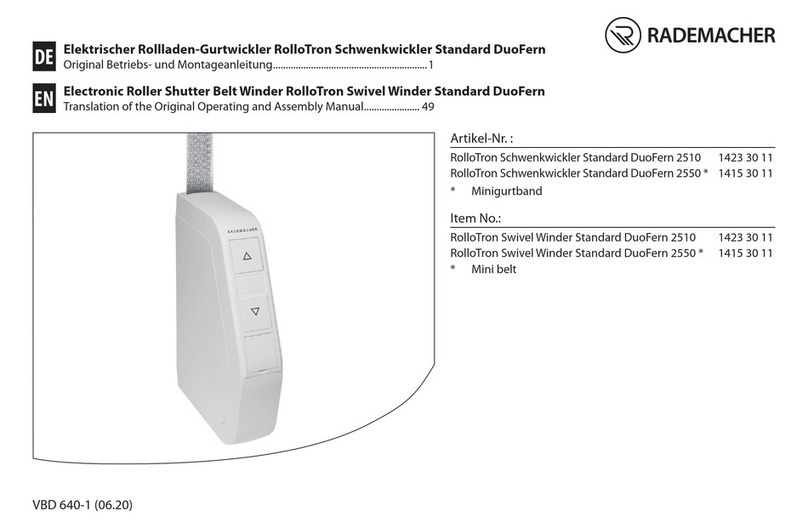
RADEMACHER
RADEMACHER RolloTron Swivel Winder Standard DuoFern... Translation of the Original Operating and Assembly Manual