Loreme BGCL96 User manual

E 2LOREME 12, rue des Potiers d'Etain - 57071 Metz 03.87.76.32.51 - Fax 03.87.76.32.52 - Email: C[email protected]r - Technique@Loreme.fr
DEVICE PRESENTATION ........................................................................................................................................ p3
USERINTERFACE........................................................................................................................................... p3
1) Tare the measure ...................................................................................................................................... p4
2) Alarms threshold setup ............................................................................................................................ p4
3) Front face configuration .......................................................................................................................... p4
RS232 LINK SETTING ............................................................................................................................................. p5
TERMINAL MODE..................................................................................................................................................... p6
1) Visualization .............................................................................................................................................. p6
2) Configuration ............................................................................................................................................. p6
2.1) Method .......................................................................................................................................... p6
2.1.1) Menu selection..................................................................................................................... p6
2.1.2) Parameter selection ............................................................................................................ p6
2.1.3) Value acquisition................................................................................................................. p6
2.1.4) Remarque ............................................................................................................................ p6
2.2) Language....................................................................................................................................... p6
2.3) Input .............................................................................................................................................. p7
2.4) Display range ................................................................................................................................ p7
2.5) Analogs outputs .......................................................................................................................... p7
2.6) Special functions ......................................................................................................................... p8
2.7) Relays ........................................................................................................................................... p8
2.8) Communication............................................................................................................................. p9
2.9) Tag configuration ......................................................................................................................... p10
OFFSET ............................................................................................................................................................... p10
FIRMWARE UPLOAD ............................................................................................................................................... p11
EMC CONSIDERATION ........................................................................................................................................... p12
1) Introduction ............................................................................................................................................... p12
2) Recommendation of use .......................................................................................................................... p12
2.1) General remarks .......................................................................................................................... p12
2.2) Power Supply ............................................................................................................................... p12
2.3) Inputs / Outputs ........................................................................................................................... p12
WIRING ............................................................................................................................................................... p13
PC - DEVICE LINK .......................................................................................................................................... p13
DIAGRAM OF CONNECTION ........................................................................................................................ p13
RS485 MODBUS COMMUNICATION ...................................................................................................................... p14
MODBUS TCP COMMUNICATION........................................................................................................................... p16
PROFIBUS COMMUNICATION ................................................................................................................................ p17
CONNECTION TO COMMUNICATION NETWORK................................................................................................. p19
Table of contents

SOMMAIRE
E 3
The purpose of this configuration handbook is to allow to become familiar with the functions supplied by the device.
The programmable bargraph BGCL96 allows with his circular ramp and the display, to evaluate easily the state of his
process inputs.
It’s necessary to notice the difference between different models:
BGCL96: universal input, more than 10 types.
BGCL96/S: 1 insulated analog outputs.
BGCL96/R1: 1 relay.
BGCL96/R2: 2 relays.
BGCL96/R3: 3 relays.
BGCL96/R4: 4 relays.
BGCL96/C: 1 RS485 Modbus or Profibus link.
BGCL96/CMTCP: 1 Ethernet Modbus TCP link.
The technical data sheet is downloadable here: http://www.loreme.fr/fichtech/BGCL96_eng.pdf
USER INTERFACE
Device Presentation
The device front panel includes:
- One 4 digits dot matrix display, 10 000 points resolution,
- One 55 LED circular ramp for input measure,
- Four signaling LED:
• R1 alarm 1 signaling,
• R2 alarm 2 signaling,
• R3 alarm 3 signaling,
• R4 alarm 4 signaling,
- a 3,5mm jack socket for RS232 link,
- 3 Push-buttons:
• (Config.) Enter in configuration mode.
• (Tare) Measure tare access or <YES> button or increment button.
• (Rel.) Alarm threshold setup access or <NO> button or decrement button.
In normal operation, the device displays the input measure on the circular ramp and the 4 digits display.
In case of an internal default or sensor breaking, the message ‘Err’ is displayed on the 4 digits display and the ramp
flashes.
1 circular ramp of 55 LED
(input measure)
Alarm signaling LED
3 Push-buttons
4 digits dot matrix diplay
(measure, messages)
Custom scale
RS 232 link Jack

SOMMAIRE
E 4LOREME 12, rue des Potiers d'Etain - 57071 Metz 03.87.76.32.51 - Fax 03.87.76.32.52 - Email: C[email protected]r - Technique@Loreme.fr
1) Tare the measure
The <Tare> button permits to access the measure tare menu. The message « TARE Y/N? » scrolls on the display.
The <yes> button activates the tare and the <no> button deactivates it. After activation, zero is displayed.
Note:
The tarred measure is saved in non-volatile memory and remains active after power Off.
2) Alarms threshold setup
The access to alarms threshold setup with the push-buttons is function of the alarms configuration. It is necessary that
the alarm is active (see threshold configuration p8).
Adjustment process:
- push the <Rel.> button to access the setup. The message 'ADJUST THRESHOLD x?' is displayed and the led Rx
is on. To access the relay x threshold setup procedure, press the button or press the button to switch to
the next threshold (If it was the last threshold, the device returns in measure mode).
- After pressing the button, the alarm threshold is displayed.
- if the adjustment is authorized (local configuration with the terminal), the threshold is adjustable with the ,
buttons, otherwise, it is only displayed. The adjustment speed is function of the time the increment or decrement
button is pressed.
- the threshold adjustment is memorized by pushing the (Config) button.
- if no button is pushed during a delay of 30 seconds, the device returns in measure mode without saving the adjusted
threshold.
3) Front face configuration
It is possible to configure the device with the three button in the front panel.
Parameters that can be modified are:
- The language,
- The input type and scales,
- The display range: low scale, high scale, decimal number.
- The display filter: The display filter is adjustable from 1 seconds to 60 seconds.
- The output: output type, low scale, high scale, security value, response time.
- The relays: breaking/watchdog detection, threshold detection, threshold type, threshold value,
hysteresis, security type, activation delay and deactivation delay.
- The communication: For MODBUS/PROFIBUS, address, speed, parity and for MODBUS/TCP, the IP address.
- square root function: YES or NO.
Access to the configuration mode is done by pressing the (Config) button. If the configuration is locked, the message
'NOT ALLOWED!' is displayed. Lock/Unlock of the configuration access is only possible via the RS232 link terminal
mode.
For each step a message scrolls on the display. The (YES) activates the function or provides access to the parame-
ter setting. The (NO) disables the function or skips to the next rubric.
Setting a value is made with the ,buttons. All parameters are limited except the display range scale. (the message
LOW or HIGH is display in overflow case). Use the (Config) button to validate the value.
The message OK ! is displayed at the end of the configuration and all the parameters are memorized.
Note:
If no button is pushed during a delay of 30 seconds, the device returns in measure mode without saving the configured
parameters.

SOMMAIRE
E 5
RS232 link setting
Enter name for the new
connection
Start a "hyper Terminal" connection :
- Click on "START" button
Up to XP version
- Go to "Programs \ Accessories \ Communication \ Hyper Terminal"
- Click on "Hypertrm.exe"
Or if the software was downloaded
- Go to "All programs \ HyperTerminal Private Edition"
- Click on "HyperTerminal Private Edition"
Choose:
- 9600 bauds
- 8 DATA bits
- no parity
- 1 stop bit
- XON/XOFF
The device can be configured or updated in terminal mode via an RS232 link.
Step 1: Driver installation for USB / RS232 adapter
- download driver at www.loreme.fr:
http://www.loreme.fr/aff_produits.asp?rubid=53&langue=fr
- Click on executable file to install the driver,
- Plug the cable on a USB port, Windows install a new serial communication port COMx
(x >= 4).
Note :
The use of the cable on another USB port don’t generates a new communication port.
Use of another adapter generates another communication port number (COMx) and re-
quires the reconfiguration of the HyperTerminal.
The terminal emulation software for PC « HyperTerminal » is resident in windows up to XP version. For later ver-
sions, it is downloadable on : www.loreme.fr in download part ( http://www.loreme.fr/HyperTerm/htpe63.exe )
=> Run the downloaded software to install it.
1
Step 2: Setting of terminal emulation software (PC with Windows).
2
345
Choose the communication port
related to the adapter.
The PC is now in terminal mode, connect it to the device by plugging the RS232 cable. The measure is now dis-
played on the terminal. To access configuration, press ’C’ key.
6
7
Note: to modify the parameters of terminal mode whereas this one is already started, it is necessary, after having car-
ried out the modifications, to close the terminal and to open it again so that the modifications are effective.
When leaving Hyper terminal, the following window will
appear. By saving, the terminal
session will start with the same
configuration. Thus, the shortcut will permit to communi-
cate with all LOREME devices.

SOMMAIRE
E 6LOREME 12, rue des Potiers d'Etain - 57071 Metz 03.87.76.32.51 - Fax 03.87.76.32.52 - Email: C[email protected]r - Technique@Loreme.fr
1) Visualization
After Power on, the device is automatically put in measure mode.
2 information's are available on screen:
10.00 mV Input measure value
11.9 mA Output result value (only if /S option).
2) Configuration
This manual resume in detail the different configuration possibilities:
Languages, input, display range, display filter, output (/S), relay 1, 2, 3, 4 (/Rx), communication (/C, /CMTCP), special
functions, tag.
To enter the configuration mode, type the "C" key. the message 'CONF' is displayed.
2.1) Method
At the configuration time, the user is asked different types of questions. For each one, several answers are possible.
You will find below the detailed description of each case.
2.1.1) Menu selection
example: INPUT The user makes a choice by pressing the keys "Y" or "N".
(Y-N) This choice allows to access the different menus of configuration.
2.1.2) Parameter selection
example: VOLTAGE or VOLTAGE
(Y-N) YES (Y-N) NO
Previous choice = YES: - pressing "Y" or "Enter" => choice validation = YES,
- pressing "N" => choice changing = NO with validation.
Previous choice = NO: - pressing "N" or "Enter" => choice validation = NO,
- pressing "Y" => choice changing = YES with validation.
2.1.3) Value acquisition
example: LOW SCALE
4 mA
Two cases are possible:
- validation without modification, just press "Enter",
- value modification on keyboard (simultaneous display), followed by validation with "Enter".
It is possible, when a mistake is made during a value acquisition, before validating it, to go back by pressing the
backspace key. which re-displays the message without taking notice of the wrong value.
2.2) Language
Languages possibilities are:
- French,
- English.
Note:
- In configuration mode, if there is no action, device goes back in operating mode after a two minutes delay without
taking notice of modifications made before.
- In configuration mode, if you want to go back to measure mode without taking notice of the modifications made before,
you just have to press "ESC".

SOMMAIRE
E 7
2.3) Input
The input possibilities are:
- Voltage (mV, mV differential, V)
- Current (mA)
- Resistance ()
- Frequency (Hz), duty cyle (%),
- Thermocouple (°C) internal or external compensation, linearized or not.
- Pt 100 (°C) 3 wires, linearized or not.
- Pt 100 (°C) 4 wires, linearized or not
with for each input type, the choice of low scale, high scale and display range.
Particularities:
- Thermocouple:
Choice of thermocouple type, B, E, J, K, R, S, T, N, W3, W5 (another on request).
Choice of compensation type, internal or external.
Choose internal compensation when thermocouple is extended up to device with a compensation cable.
Choose external compensation when thermocouple is not extended up to device with a compensation cable, but up
to a compensation box where temperature will be known and stabilized. This is the value of temperature that will be
typed as the external compensation value (except thermocouple type B).
- Potentiometer:
Configure voltage input (V):
- low scale: 0 V
- high scale: 5 V
Move potentiometer at the start and at the end of range, notice each value.
Change voltage input (V):
- low scale = start range value,
- high scale = end range value.
See wiring diagram for potentiometer wiring.
- Sensor power supply:
To supply a loop powered converter and measure the loop current, it's necessary to configure the device in 4-20 mA
current input. See wiring diagram for sensor power supply and current input wiring.
2.4) Display range and filter
The range interpret the input signal in a physical size, thus making the reading of the measured information easier.
Ex: Input 4-20 mA / Range 0-1000 kg
Input = 12 mA, indication = 500 kg
To configure the range, it is necessary to configure:
- the unit
- the low scale
- the high scale
- the decimal number
- the display filter
The unit of the display range is facultative and is only useful to interpret the real size on the terminal. It is limited to 4
characters.
The decimal number correspond to the number of digit displayed behind the decimal point. This number is limited to 3.
The display filter allows to reduce display instability when measured value is disturbed. It is adjustable from 1 to 60 s.
2.5) Analog output
The device can, by the /S option, provide an analog output, insulated and configurable. Analog output configuration is
presented through 2 rubrics:
- Output type:
- current output (mA),

SOMMAIRE
E 8LOREME 12, rue des Potiers d'Etain - 57071 Metz 03.87.76.32.51 - Fax 03.87.76.32.52 - Email: C[email protected]r - Technique@Loreme.fr
- voltage output (V).
And for each output type, the low and high scale.
- Output parameters:
- security value,
- limitation,
- response time.
The security value allows to set the output on a known state when there is a sensor breaking or a measure range
overflow. This value will be transferred to output.
The limitation allows to bound the output signal swing to the configured output scales for all input signal values. Only
security value goes beyond this function.
The response time is adjustable from 0 to 60 s.
2.6) Specials functions
The device disposes of some special functions to adapt its operation.
The front face configuration lock allows the user to lock the configuration procedure accessible via the front face but-
tons.
The square root function executes a square root on the input range percentage. The result is reported on analog output
and on the displayed value.
The special linearization function allows the user to create a personalized response
curve by configure points of correspondence between measured input signal and the
display range. When this function is choose, it is directly activated, but linearization
points are not modified. To modify linearization points, it is necessary to validate by
YES the configuration question.
When special linearization is enabled, the device uses linearization curve corre-
sponding to configure points (2).
To personalize a response curve (2), it's necessary to set for each curve point the
input value and the corresponding display range value (maximum 26 points including
input points 0 % and 100 %). So, for each measured point, the device will make cor-
respondence to the linearized display range value.
2.7) Relays
The device can, by /R1, /R2, /R3 or /R4 option, provide respectively 1, 2, 3 or 4 independently configurable alarm relays.
Relays configuration is presented through 2 rubrics:
- Detection type:
- breaking detection/watchdog function,
- threshold detection.
The breaking/watchdog detection activates alarm on sensor breaking and on internal failure.
The threshold detection activates alarm on threshold overstepping. It is necessary to choose threshold type, high or
low, threshold and hysteresis value. The two detections types can be activated simultaneously.
The threshold detection works in this manner:
- high threshold detection:
.alarm is activated when measure goes above threshold,
.alarm is removed when measure goes below threshold minus hysteresis.
- low threshold detection:
.alarm is activated when measure goes below threshold,
.alarm is removed when measure goes above threshold plus hysteresis.
Output
Correspondingvalues
(1)Converterresponsecurve
((2)Speciallinearisation
INPUT
Measurementvalues
Note: The hysteresis value is relative to the display range scale and can be configured between 0 % and 99 %.

SOMMAIRE
E 9
- Relay parameter:
- adjustable,
- security,
- delay.
When alarm is used in threshold detection, it is possible to access the threshold adjustment in front face with the push-
buttons. This possibility can be deactivated if the adjustment must be inaccessible in front face, only the visualization is
then possible.
Each relay can be set in positive security or negative security. This function allows to choose between the activation
or the de-activation of the relay when alarm is activated:
- in positive security, relay is switched when alarm is active, "works" contact is closed on alarm, opened out of alarm,
"back" contact is opened on alarm, closed out of alarm.
- in negative security, relay is switched when alarm is inactive, "works" contact is opened on alarm, closed out of alarm,
"back" contact is closed on alarm, opened out of alarm.
The delay value, configurable from 0 to 14400 s (4 hour), determines the time above which alarm changes its state af-
ter event appearance and disappearance. The device provide for each relay a configurable delay when alarm is acti-
vated and when alarm is removed.
2.8) Communication
This part of configuration is accessible only on a device with the option /C or /CMTCP.
2.8.1) MODBUS TCP
The parameters are the IP address and the network mask. The entry is made in 3digits, the character separation ‘.’ is
display automatically.
Note: When using the buttons in front panel, only the IP address can be modify.
2.8.2) MODBUS
The communication parameters are:
- Network Address of the device (1 to 255),
- baud rate : 1200, 2400, 4800, 9600,19200, 38400 bauds,
- parity: odd, even, none.
The data are present in several format:
- floating 32 bits IEEE format,
- 16 bits unsigned integer (percentage of the measurement range),
- 32 bits reversed signed integer (value x 100).
Event time measure is reseted
after event disappearing
Event
Alarm
Relay in +
security
Relay in -
security
Delay Delay before
activation Delay before
de-activation
active
Switched off
Switched on
Switched on
Switched off

SOMMAIRE
E 10 LOREME 12, rue des Potiers d'Etain - 57071 Metz 03.87.76.32.51 - Fax 03.87.76.32.52 - Email: Comm[email protected] - Techni-
2.8.3) PROFIBUS
The communication parameters are:
- Network Address of the device (1 to 126)
- baud rate : 9600, 19200, 93.75K, 187.5K,0.5M, 1.5Mbauds
The data exchange are : measure value in float 32bits IEEE, state of alarm 1 and 2, input state.
2.9) Tag configuration
The tag allows to easily identify the converter. It can be made of up to 10 alphanumerical characters. The user only have
to enter the tag on the keyboard and validate it with the "Return" key. The tag will now be displayed on each configura-
tion access.
OFFSET
Sometimes, it may be interesting to modify the measure by a simple terminal keyboard intervention.
It can be used in many situations as sensor aging, an input refinement as a result of magnifying effect...
To shift the measure, it is necessary:
- to be in measure mode,
- type on "+" or "-" to access the function,
- on terminal the display become:
100.5 DC measure value with offset,
OFFSET 10 offset function, offset value.
- use keys "+" and "-" to adjust offset, measure is directly modified.
- type on "ENTER" to memorize offset.
When the device is not supplied or is in configuration mode, offset stay active. To reset offset, it is necessary to start
"OFFSET" function, put this value to zero with the "+" and "-" keys, then validate by "ENTER". In offset control mode,
when there is no action on "+", "-" or "ENTER" keys during 20 s, the device leave the mode without keeping the ad-
justed offset.
Attention, the offset has no effect on the measure when the converter is in frequency or duty cycle mode !!!

SOMMAIRE
E 11
To access to the firmware update function, you must first open an HyperTerminal session on a PC, connect the device
to the PC with the RS232 link cable and then power on the device.
The following character is send to the terminal:
><———————— The device sends this character then it waits the « F » key during 0.5 s.
If the user has pressed the « F » key in the allowed time, the following message is displayed in the HyperTerminal win-
dows:
FIRMWARE LOADER Rev3
READY TO TRANSFER...
The device is now in file waiting mode, This file is provided by LOREME. This file contain the firmware code in intel HEX
format. Selected the « Transfer », « Send a text file... » in the HyperTerminal menu
Select the directory and the file, click on « OPEN ». The HyperTerminal program begins to send the file to the device.
FIRMWARE LOADER Rev3
READY TO TRANSFER...
*********** The star characters appears to show the progress of the uploading.
At the end, the message « PROGRAMMING OK !» is display if no error occurs. If not, several messages are display:
- SERIAL COM ERROR ! Error during receipt.
- SERIAL TIMEOUT ! Waiting time of receipt elapsed.
- PROGRAMMING FAILED ! Programming error in the internal flash memory..
Attention
If an error occurs during the programming process, it is necessary to start again the whole procedure.
A bad programming leads to an inoperative device.
Firmware update

SOMMAIRE
E 12 LOREME 12, rue des Potiers d'Etain - 57071 Metz 03.87.76.32.51 - Fax 03.87.76.32.52 - Email: Comm[email protected] - Techni-
1) Introduction
To meet its policy concerning EMC, based on the Community directives 2014/30/EU & 2014/35/EU, the
LOREME company takes into account the standards relative to this directives from the very start of the con-
ception of each product.
The set of tests performed on the devices, designed to work in an industrial environment, are made in accor-
dance with IEC 61000-6-4 and IEC 61000-6-2 standards in order to establish the EU declaration of confor-
mity. The devices being in certain typical configurations during the tests, it is impossible to guarantee the re-
sults in every possible configurations. To ensure optimum operation of each device, it would be judicious to
comply with several recommendations of use.
2) Recommendations of use
2.1 ) General remarks
- Comply with the recommendations of assembly indicated in the technical data sheet (direction of assembly,
spacing between the devices, ...).
- Comply with the recommendations of use indicated in the technical data sheet (temperature range, protec-
tion index).
- Avoid dust and excessive humidity, corrosive gas, considerable sources of heat.
- Avoid disturbed environments and disruptive phenomena or elements.
- If possible, group together the instrumentation devices in a zone separated from the power and relay cir-
cuits.
- Avoid the direct proximity with considerable power distance switches, contactors, relays, thyristor power
groups, ...
- Do not get closer within fifty centimeters of a device with a transmitter (walkie-talkie) of a power of 5 W, be-
cause the latter can create a field with an intensity higher than 10 V/M for a distance fewer than 50 cm.
2.2 ) Power supply
- Comply with the features indicated in the technical sheet (power supply voltage, frequency, allowance of the
values, stability, variations ...).
- It is better that the power supply should come from a system with section switches equipped with fuses for
the instrumentation element and that the power supply line be the most direct possible from the section
switch.
- Avoid using this power supply for the control of relays, of contactors, of electrogates, ...
- If the switching of thyristor statical groups, of engines, of speed variator, ... causes strong interferences on
the power supply circuit, it would be necessary to put an insulation transformer especially intended for instru-
mentation linking the screen to earth.
- It is also important that the installation should have a good earth system and it is better that the voltage in
relation to the neutral should not exceed 1V, and the resistance be inferior to 6 ohms.
- If the installation is near high frequency generators or installations of arc welding, it is better to put suitable
section filters.
2.3 ) Inputs / Outputs
- In harsh conditions, it is advisable to use sheathed and twisted cables whose ground braid will be linked to
the earth at a single point.
- It is advisable to separate the input / output lines from the power supply lines in order to avoid the coupling
phenomena.
- It is also advisable to limit the lengths of data cables as much as possible.
EMC Consideration

SOMMAIRE
E 13
PC - DEVICE LINK
3.5 stereo
jack 9 female
pins to PC
DIAGRAMS OF CONNECTIONS
mV, Tc input: terminal D (+), terminal F (-)
V/Frequency input: terminal B (+), terminal F (-)
mA input: terminal C (+), terminal F (-)
Potentiometer input: terminal G (supply), terminal B (+), terminal F (-)
Strain gauge input : terminal G (supply +),terminal F (supply -)
terminal E (measure +), terminal D (measure -)
Sensor supply input: terminal H (+), terminal F (-)
Resistance,
Pt100 input (3-wires): terminal D (+),terminal F (-), terminal E (line)
Pt100 input (4-wires): terminal A (line +), terminal D (+), terminal F (-), terminal E (line -)
Analog output: terminal Analog+, terminal Analog-
Relay 1,2,3,4: terminal Rx (rest), terminal Tx (work), terminal Cx (common)
Power supply (AC/DC): terminals L+, N-
Wirings

SOMMAIRE
E 14 LOREME 12, rue des Potiers d'Etain - 57071 Metz 03.87.76.32.51 - Fax 03.87.76.32.52 - Email: Comm[email protected] - Techni-
1) Feature
Protocol: MODBUS RTU
Link: RS485
Baudrate: 1200 to 38400 bds
Parity: even, odd, none
Address: 1 to 255
Connector: 3 points spring connector
Reading request: function code 03,04
Type of data: electrical measurement.
data format: Measure in 32 bits IEEE floating point, 32 bits signed integer format, 16 bits unsigned integer.
2) Data desciption
2.1) Available data
All measures are accessible in reading mode.
Data's are available in different formats:
- 2 words, 4 bytes, for the 32 bits IEEE floating point format,
- 1 word, 2 bytes, for the measure in 16 bits integer format. The value is in percent of the input scale,
- 2 words, 4 bytes, for the 32 bits signed integer format,
=> Consult the enclosed tables for data's detail.
2.2) Exception frame
If the slave receive an corrupted frame (CRC16 or parity), it doesn’t answer. If it is a frame error (data address, function,
value), the slave send a exception frame.
The exception frame is a 5 bytes long.
Details of the exception frame:
The function code of the exception frame is identical to the question frame, but this MSB bit is set to 1.
The error code indicate the reason of the exception frame
Error code Details
$01 Function code not allowed. Only the function code $03 or $04 are used by the BGCL96
(register reading function).
$02 Data address not allowed
$04 Slave busy. The internal communication slot is not in connection with the measure part.
2.3) Data format
- Data in 32 bits IEEE floating point format
Data are transmitted Most Significant Byte first, 4 bytes or 2 words long.
$FFFFFFFF = sensor braking.
RS485 MODBUS communication
Sign Exponent Mantissa

SOMMAIRE
E 15
MSW LSW
byte 3 byte 4 byte 1 byte 2
31 24 23 16 15 8 7 0
Byte 1 Byte 2
15 MSB 8 7 LSB 0
- Data in 16 bits integer format.
Data are transmitted most significant byte first, 2 bytes or 1 word long.
The 16 bits unsigned integer values correspond to the percentage of the input measure scale.
$0000 ou $FFFF = sensor breaking.
$0001 = Low overstepping of input scale,
$FFFE = High overstepping of input scale.
$0002 à $FFFD = Percentage of input scale.
Example:
- input PT100 (scale: -200 /800°C), 16 bits measure = 37442 => [((37442 - 2)/65531) * (800+200)] - 200 = 371,3°C
- input Tc K (scale: -200 /1350°C), 16 bits measure = 20900 => [((20900 - 2)/65531) * (1350+200)] - 200 = 294,3°C
- Data in 32 bits signed integer format.
Data are transmitted Least significant word first, 4 bytes or 2 words long.
The 32 bits signed integer value correspond to the measure x 100.
3) measure in 32 bits floating format
4) measure in 16 bits format
5) measure in 32 bits format
Address in decimal
(Hexadecimal) Designation
4096 ($1000) Measure in IEEE 32 bits floating point Word 1
4097 ($1001) Word 2
Address in decimal
(Hexadecimal) Designation
0000 ($0000)
or
12288 ($3000)
Measure in 16 bits integer Word 1
Percentage of input scale
40960 ($A000) Measure x100 in 32bits signed integerWord 1
40961 ($A001) Word 2

SOMMAIRE
E 16 LOREME 12, rue des Potiers d'Etain - 57071 Metz 03.87.76.32.51 - Fax 03.87.76.32.52 - Email: Comm[email protected] - Techni-
MODBUS TCP communication
1) Features
Protocol: MODBUS TCP
Link: Ethernet
Speed: 10/100 base T
Defaut IP address: 192.168.0.253
Connector: RJ45
Reading operation: Code function 03, 04
Writing operation: Not allowed
2) Data description
The available data are the same as for the MODBUS communication (see pages 14/15).
3) Response time
It is the delay between a read request send by the master and the response frame send by the BGCL96/CMTCP.
The BGCL96 device answer in less of 30 ms to a read of 4 registers.
4) Use with more than one Modbus TCP master
The BGCL96/CMTCP supports to be access by masters with different IP address. However, the network load have to be
less then 30 requests /second. A too high network load could lead to communication errors.

SOMMAIRE
E 17
RS485 PROFIBUS communication
Total
b7 b6 b5 b4 b3 b2 b1 b0 word byte
Channel 1 byte 1 word 1 1 1
byte 2 2
byte 3 word 2 2 3
byte 4 4
Channel 2 byte 1 word 1 3 5
byte 2 6
byte 3 word 2 4 7
byte 4 8
Channel 3 byte 1 word 1 5 9
byte 2 10
byte 3 word 2 6 11
byte 4 12
Channel 4 byte 1 word 1 7 13
byte 2 14
byte 3 word 2 8 15
byte 4 16
1) Features
This device meet the PROFIBUS specification EN 50710 volume 2
Supported baud rate: 9.6K, 19.2K, 93.75K, 187.5K, 0.5M, 1.5Mbauds
Type of transmission: RS485, 8bits data, 1 stop, even parity
Connector: unpluggable 2 wires
2) Implementation
The network address and the baud rate should be configured in the device. All communication information's are in the
GSD file provide with the device (or may be download from www.loreme.fr )
This information's are in 3 parts:
- Information about the functionality of the device,
- data configuration,
- list of alarms and parameters
2.1) Explanation of input/output data
A data exchange frame has 105 byte long:
- 96 bytes for the measure in 32bits IEEE floating point number
- 3 bytes for the alarm 1 status (1bit by channel, set to 1 if alarm activated)
- 3 bytes for the alarm 2 status (1bit by channel, set to 1 if alarm activated)
- 3 bytes for the input status (1bit by channel, set to 1 if input is breaking)
2.2) Explanation of diagnostic data
There are 6 byte of standard diagnostic data and 2 byte for device specific data.
2.3) Data exchange information:
Remark: Only the channel 1 is use by the BGCL96 and the alarms 1 and 2 are always 0.

SOMMAIRE
E 18 LOREME 12, rue des Potiers d'Etain - 57071 Metz 03.87.76.32.51 - Fax 03.87.76.32.52 - Email: Comm[email protected] - Techni-
Words bytes
Channel 24 byte 3 word 2 48 95
byte 4 96
AL1 Channel1 to 8 byte 1 97
Status Channel 9 to 16 byte 2 98
Channel 17to 24 byte 3 99
AL2 Channel 1 to 8 byte 1 100
Status Channel 9 to 16 byte 2 101
Channel 17 to 24 byte 3 102
Sensor Channel 1 to 8 byte 1 103
braking Channel 9 to 16 byte 2 104
Status Channel17 to 24 byte 3 105
2.4) Alarms and input Status byte
When a bit is set to 1, the corresponding channel is in alarm or input breaking
b7 b6 b5 b4 b3 b2 b1 b0 bit
State of channel 1 to 8 8 7 6 5 4 3 2 1 byte 1
State of channel 9 to 16 16 15 14 13 12 11 10 9 byte 2
State of channel 17 to 24 24 23 22 21 20 19 18 17 byte 3
2.5) Device specific diagnostic data
byte 1 à 6 : standard bytes
0 0 0 0 0 0 1 0 byte 7: header
0 0 0 0 0 0 0 0/1 byte 8: diagnostic
b7 b6 b5 b4 b3 b2 b1 b0 bit0: measure default
The ‘Measure Default’ appears when the communication slot don’t receive data from the measure part within a 3s delay.
(It’s the case if the user enter the device in configuration mode by RS232 link or front panel)
In this case ALL data exchanged are set to 0 !!
2.6) Data format for measure value (only channel 1)
- Date in IEEE 32 bits floating point number.
Data are transmitted Most significant byte first, 4 bytes long.
$FFFFFFFF = sensor breaking.
Sign Exponent Mantisse

SOMMAIRE
E 19
Connection to the communication network
12 12
A
B
INL35 INL35
RS 485
1
2
INL35
RxD/TxD - N
RxD/TxD - P
Green (8)
Red (3)
Profibus cable wire color Pin DB9 Designation
1) Connection to a MODBUS network
2) Connection to a PROFIBUS network
1 2 3
1 2 3
The terminal (3) is not connected
The terminal (3) is not connected
Table of contents
Other Loreme Measuring Instrument manuals
Popular Measuring Instrument manuals by other brands
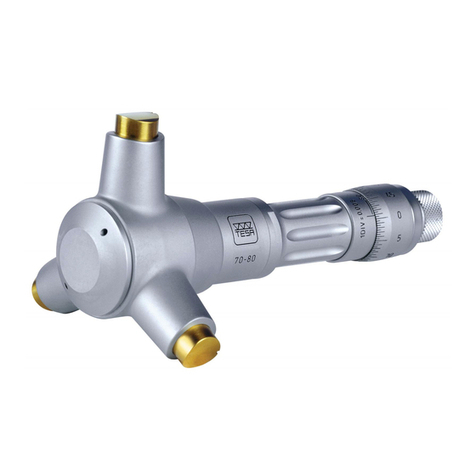
Hexagon
Hexagon TESA IMICRO instruction manual

Precision Digital Corporation
Precision Digital Corporation ProtEX-MAX PD8-6060 instruction manual
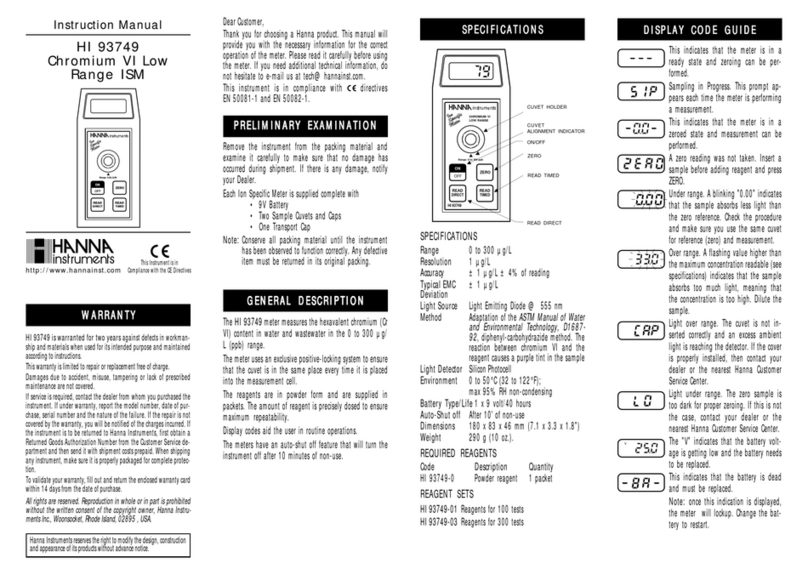
Hanna Instruments
Hanna Instruments HI 93749 instruction manual
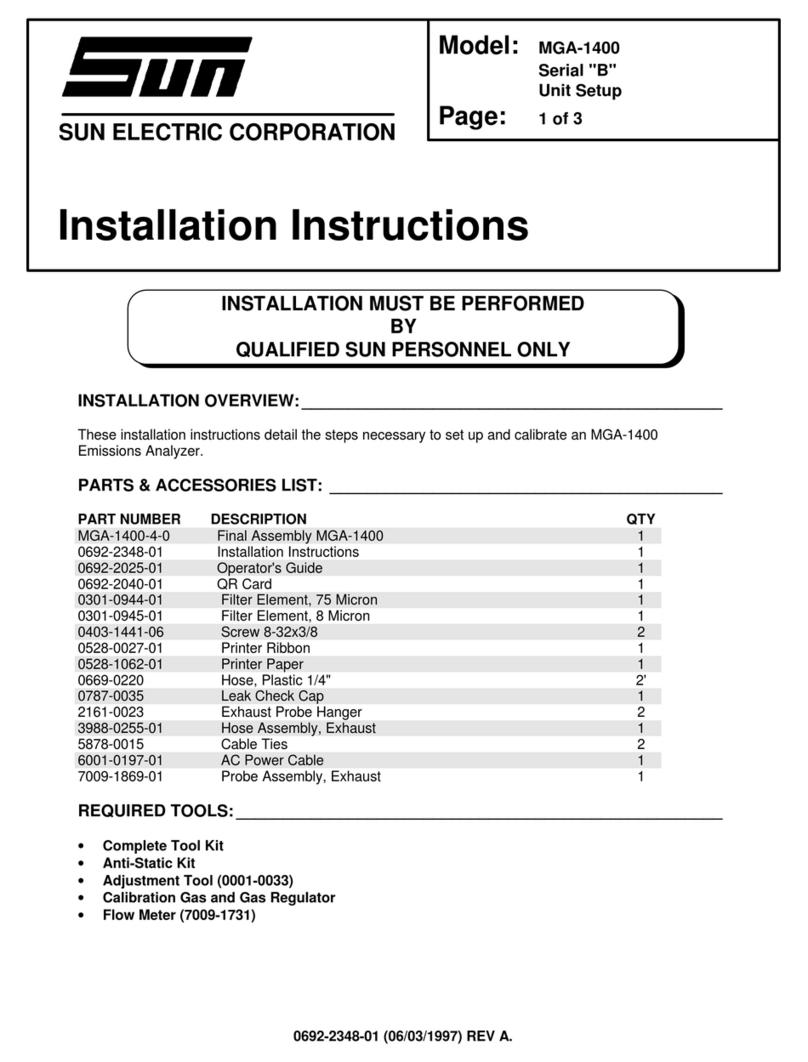
Sun Microsystems
Sun Microsystems MGA-1400 installation instructions
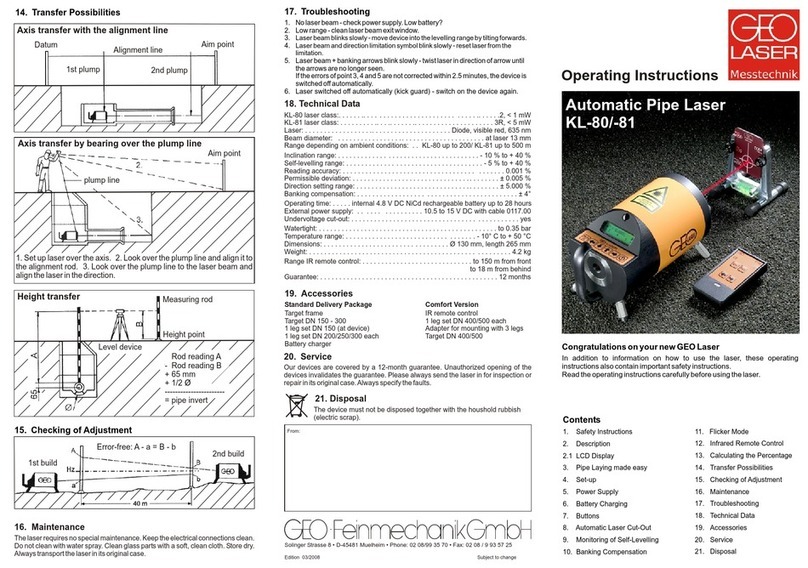
Geo
Geo KL-80 operating instructions
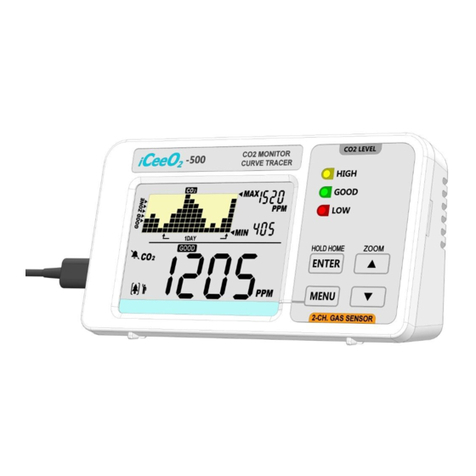
iCeeO2
iCeeO2 500 instruction manual
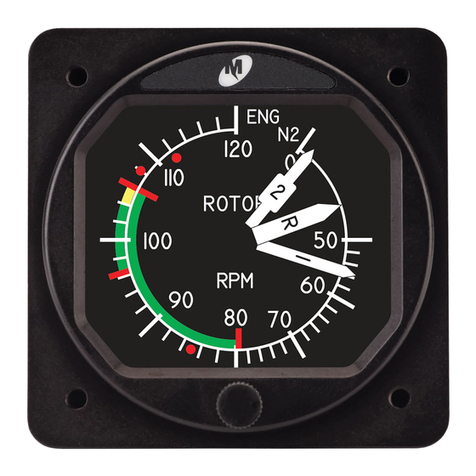
Mid-Continent Instrument
Mid-Continent Instrument MD23-104 user guide

Milwaukee
Milwaukee MW12 user manual
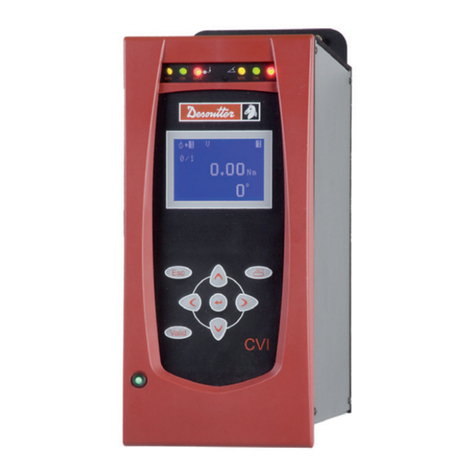
Desoutter
Desoutter CVILeco Original instructions
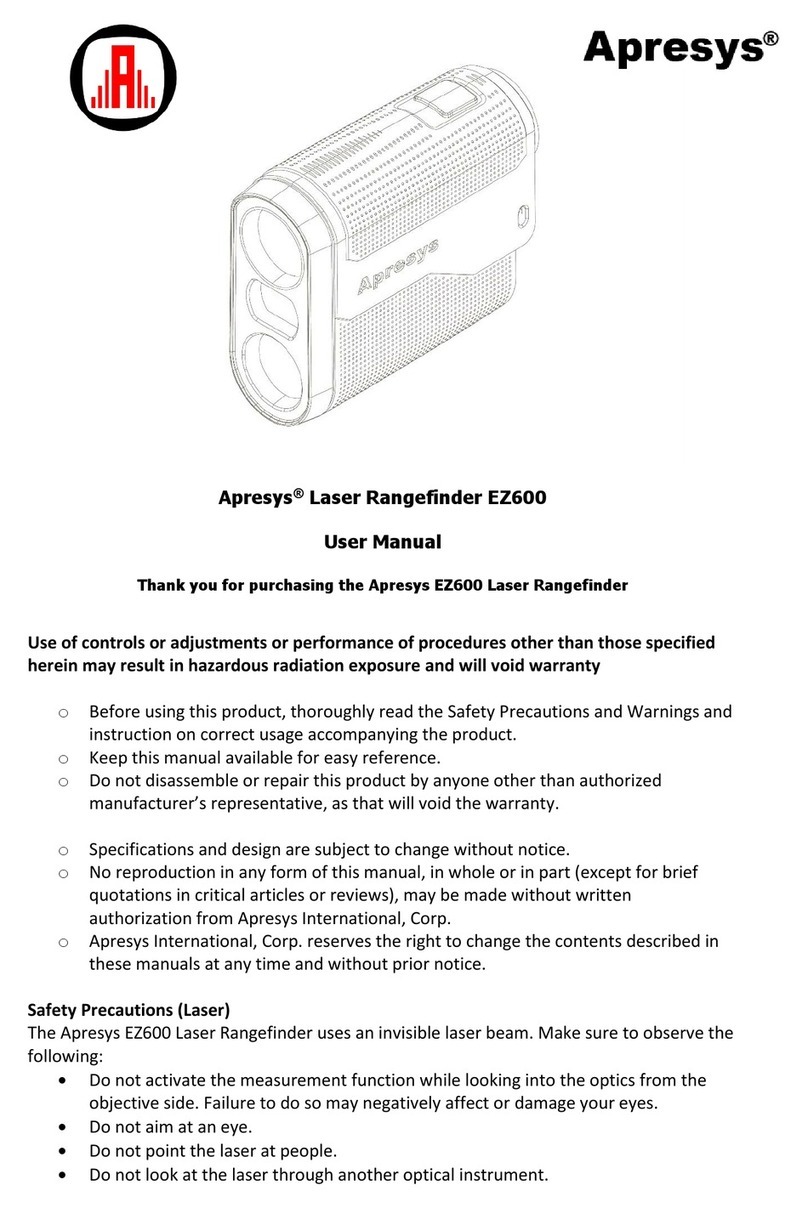
APRESYS
APRESYS EZ600 user manual
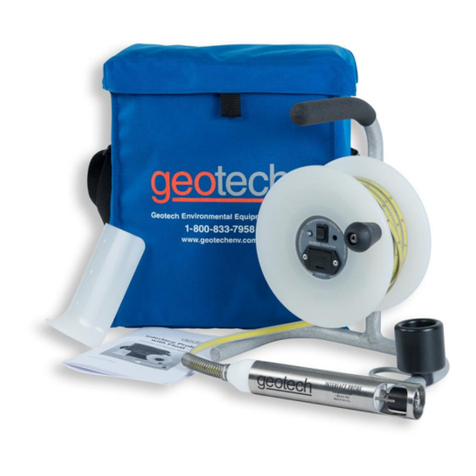
Geotech
Geotech Interface Probe with Float Installation and operation manual
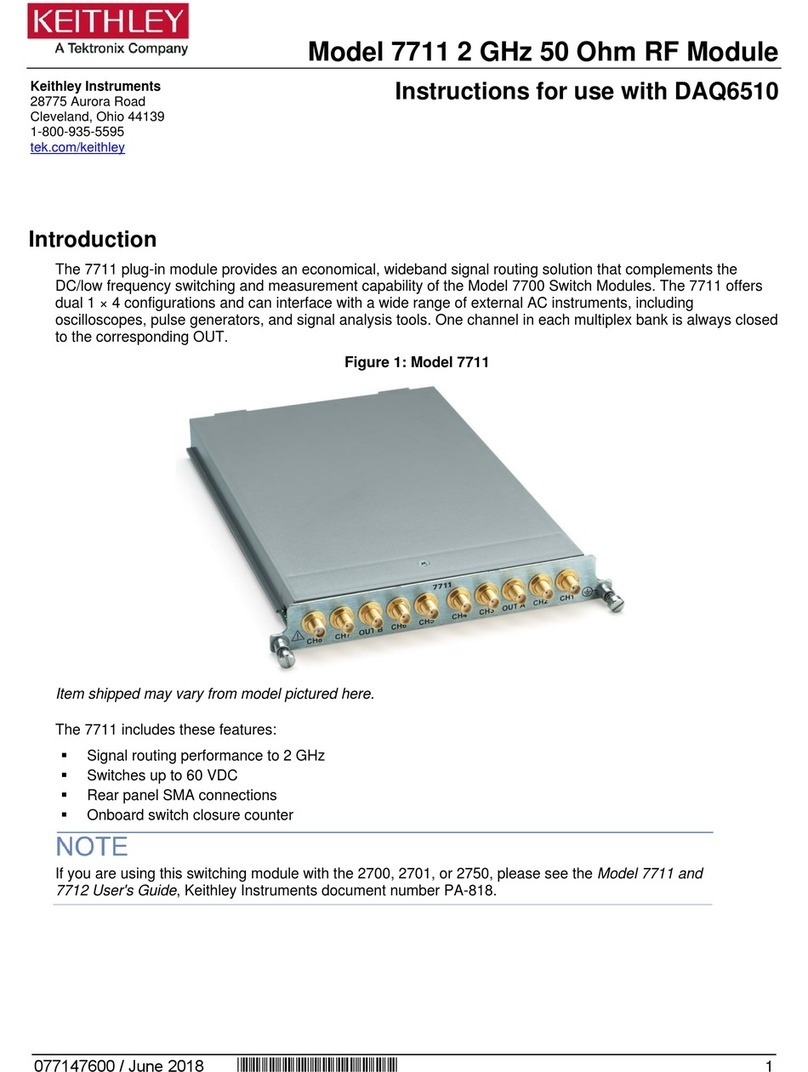
Tektronix
Tektronix Keithley 7711 instructions