gefran KH-SIL2 Series User manual

1
85198C_Manual of Electrical Installation for Pressure Probes KH-SIL2-Mobyle-series_08-2028_ENG
Manual of Electrical Installation for
Pressure Probes KH-SIL2 series
Code 85198C
Edition 08-2022
Contents
1. General precautions pag 2
2. Transmitters with amplified analog output pag 2
2.1
Standard installation pag 2
2.2 Electrical connections pag 3
3. Protection for outdoor installations of analog sensors pag 4
4. Technical specifications pag 5
5. Functional Safety (content according to IEC/EN 62061 paragraph 7) pag 6
5.1. Application pag 6
5.2. Restrictions of use pag 6
5.3.Maintenance and periodic inspections pag 7
5.4. Indication of response time pag 7
5.5. Indications and alarms pag 7
5.6. Failures and troubleshooting pag 8
This manual is related to KH Series pressure transducer, SIL2 certified according to the
standards IEC/EN62061
G
E
F
R
A
N
S
A
F
E
T
Y
G
U
A
R
A
N
T
E
E

285198C_Manual of Electrical Installation for Pressure Probes KH-SIL2-Mobyle-series_08-2028_ENG
1. General Precautions
The system must be used only in accordance with the required protection level.
The sensor must be protected against accidental knocks and used in accordance with the instrument’s ambient characteristics and per-
formance levels.
Sensors must be powered with non distributed networks.
For outdoor installations or with cables longer than 30 m*, proceed as indicated at paragraph 3.
(*) See further limitations for Safety applications at paragraph 5.
2. Transmitters with amplified analog output
Transducers: KH SIL2 series
Outputs: 0.5...10.5V; 0.5...5.5V; 0.1...10.1V; 0.1...10V; 1...5V; 1...6V; 1...10V; 0.2...10.2; 0.5 … 4.5V ratiometric; 4...20mA, etc...
Installation remarks
- The transducer must be grounded (normally through the machine body or equipment it is installed on).
- Use a shielded cable only. The cable shield must be grounded on PLC side and left floating on machine side (on KH version with M12
electrical connector it’s possible to connect the shield on machine side by leaving floating the PLC side).
- To prevent interference, separate the power cables from the signal cables.
Machine
Press
Equipment
Transducer
Ground
Cable shield floating
PLC / Instrument
Pressure port
Cable connector
Cable shield to ground
Shielded cable
Standard installation (recommended)

3
85198C_Manual of Electrical Installation for Pressure Probes KH-SIL2-Mobyle-series_08-2028_ENG
Electrical connections
The interface with SRP/CS (Safety Related Part of a Control System) is made by mean of multipolar connectors showed
on pictures below, where the connections are specified in case of amplified voltage output (3 wire) or current output (2
wire system, the sensor is connected in series with the current loop).
Interfaces with SRP/CS and voltage devices
RATIOMETRIC AND VOLTAGE AMPLIFIED OUTPUT
CURRENT AMPLIFIED OUTPUT – mod. E
Red
Black
Red
Black
White
OUTPUT
POWER SUPPLY
SIGNAL
POWER SUPPLY
21
34
G – Deutsch DT04-4P
Z - M12 x 1 (4 pin)*
S – AMP Superseal 1.5
E - EN 175301-803 K – Metri-Pack 150
Protection IP67
Protection IP67
Protection IP67
Protection IP67
Protection IP65
LOAD DIAGRAM
(Current output)
F – 3 pole cable
Shield
White
Red
Black
Protection IP65
Ω
TOTAL LOAD RESISTANCE RL
Operating
Area
POWER SUPPLY VOLTAGE
RL = < (Vsupply - 10V) / 0.02A
* IP67 with female homologated connector mounted, tightening torque 0.6Nm + low strength threadlocker

485198C_Manual of Electrical Installation for Pressure Probes KH-SIL2-Mobyle-series_08-2028_ENG
3. Protection for outdoor installations of analog sensors
Pressure / Analog voltage output
CAL signals if any do not require protection
J1
J1
J1
J1
PLC side
+24Vdc
PLC side
+IN
PLC side
GND
PLC side
Ground
D4
D1 D2
D3
J2
J2
J2
Transducer side
+24Vdc
Transducer side
+OUT
Transducer side
GND
B72210-S-250-K01
B72210-S-250-K01
B72210-S-250-K01B72210-S-250-K01
PLC ground machine ground
1
1
1
1
1
1
1
Pressure / Analog current output
CAL signals if any do not require protection
J1
J1
J1
PLC side
+24Vdc
PLC side
+IN
PLC side
Ground
D1 D3
J2
J2
Transducer side
+24Vdc
Transducer side
+OUT
B72210-S-250-K01B72210-S-250-K01
PLC ground machine ground
1
1
1
1
1
D2
B72210-S-250-K01

5
85198C_Manual of Electrical Installation for Pressure Probes KH-SIL2-Mobyle-series_08-2028_ENG
4. Technical specifications
Output signal VOLTAGE RATIOMETRIC CURRENT
Accuracy at room temperature (1) < ± 0.5% FS
Pressure ranges (2) From 4 bar to 1000 bar (See table)
Overvoltage 32 Vdc max
Overpressure (without degrading performance) See table
Pressure containment (burst test) See table
Pressure Media Fluids compatible with Stainless Steel AISI 430F and 17-4 PH
Housing Stainless Steel AISI 304
Power supply 15...30Vdc 5V ±0.25 V 10...30Vdc
Dielectric strenght 250 Vdc
Zero output signal 0.1V; 0.2V; 0.5V; 1V (*) 0.5 V 4 mA
Full scale output signal 5V; 10V; 10.1V; 10.5V (*) 4.5 V 20 mA
Allowed load ≥ 5KΩ see load diagram
Long term stability < 0.2% FS/per year
Operating temperature range (process) -40...+125°C (-40...+257°F)
Operating temperature range (ambient) -40...+105°C (-40...+221°F)
Compensated temperature range -20...+85°C (-4...+185°F)
Storage temperature range -40...+125°C (-40...+257°F)
Temperature effects over compensated range (zero) ± 0.01% FS/°C typ (± 0.02% FS/°C max.)
Temperature effects over compensated range (span) ± 0.01% FS/°C typ (± 0.02% FS/°C max.)
Response time (10...90%FS) < 1 msec.
Warm-up time (3) < 30 sec.
Mounting position effects Negligible
Humidity Fino a 100%RH non-condensing
Weight 80-120 gr. nominal
Mechanical shock 100g/11msec according to IEC 60068-2-27
Vibrations 20g max at 10...2000 Hz according to IEC 60068-2-6
Ingress protection IP65/IP67 (M12 version) with female homologated connector mounted, tightening
torque 0.6Nm + low strength threadlocker
Output short circuit and reverse polarity protection YES
EC Conformity According to EMC Directive 2014/30/EU
Lifetime 10 years
(*) Other voltage values of Zero and Full Scale available on request.
FS = Full scale
1Incl. Non-Linearity, Hysteresis, Repeatability, Zero-offset and Span-offset (acc. to IEC 61298-2)
2The operating pressure range is intended from 0.5% to 100% FS
3Time within which the rated performance is achieved
RANGE
(Bar) 4 6 10 16 20 25 40 60 100 160 200 250 400 600 1000
Overpressure
(Bar) 8 12 20 32 40 50 80 120 200 320 400 500 800 1200 1200
Burst pressure
(Bar) 16 24 40 64 80 100 160 240 400 640 800 1000 1500 1500 1500

685198C_Manual of Electrical Installation for Pressure Probes KH-SIL2-Mobyle-series_08-2028_ENG
5. Functional Safety (content according to IEC/EN 62061 paragraph 7)
5.1 Application
The pressure sensor KH performs the following safety function:
correct reading and transduction of pressure to individuate overpressure. Reading and transduction is considered cor-
rect when it is within the specifications declared in the datasheet and in the Operating Manual.
The SIL parameters of the transducer are shown in the table below:
Parameter Value Measuring Unit
Architecture 1oo1 --
HFT 0 --
bfactors Not relevant --
lDD
Current output 1,56E-08 1/h
Voltage output 1,56E-08 1/h
Ratiometric Voltage Output 1,65E-08 1/h
lDU
Current output 6,53E-08 1/h
Voltage output 6,62E-08 1/h
Ratiometric Voltage Output 6,74E-08 1/h
SFF
Current output 90,47 %
Voltage output 90,32 %
Ratiometric Voltage Output 90,30 %
PFHD
Current output 6,53E-08 1/h
Voltage output 6,62E-08 1/h
Ratiometric Voltage Output 6,74E-08 1/h
SIL 2 --
The diagram “A” (Fig. 1) shows a possible application: the sensor detects the pressure and transduces it in an analog
electrical signal proportional to the value of the measured value; the SRP / CS compares the signal with the one set as
the alarm threshold: in case of exceeding the threshold it shall disable the elements of pressure generation.
Fig. 1: application diagram A
VOLTAGE OUTPUT AND RATIOMETRIC
CURRENT 2-WIRE OUTPUT

7
85198C_Manual of Electrical Installation for Pressure Probes KH-SIL2-Mobyle-series_08-2028_ENG
5.2 Restrictions of use
The device must only be used in accordance with these operating instructions for mechanical installation, electrical con-
nection, environmental conditions and use in order
to maintain the declared SIL. The sensors must be powered by non-distributed networks and in any case with a length
of less than 30 m.
5.3 Maintenance and periodic inspections
Periodic maintenance to carry-out in order to guarantee the justified exclusion of failures are:
- Visual inspection of the status of the electrical and mechanical connections.
The maintenance is designed to evaluate possible problems due to situations of incorrect mounting endured over time
or particular aggressiveness of the material processed.
Frequency: every two years
Check obstruction of the channel under pressure
- The maintenance has the purpose to verify that there are no occlusion of the pressure channel, which would lead to
malfunctioning.
The inspection is visual, after removing the probe from the process seat.
Frequency: every year.
Testing the sensor calibration
- The test is intended to check the correctness of the transduction curve of the sensor. It’s done by applying known
pressure points to the transducer and checking the output values of the probe.
Frequency: every four years.
5.4 Indication of response time
The response time to the pressure transduction is equal to 1 ms
5.5 Indications and alarms
The KH Series pressure sensors in the case of some specific anomalies provide output saturation (positive HIGH or
negative LOW).
The table 1 indicates the detected failures, their effect on the electrical output, and the recovery mode of the device.
Table 1: failures, effects on the outputs
Failure Current
output
Voltage
output Ratiometric
FS<= 6V FS > 6V Power supply 5V
Power supply cable broken LOW < 3.8mA LOW < 0.05 V LOW < 0.25 V
Sensor not connected LOW < 3.8mA LOW < 0.05 V LOW < 0.25 V
Power supply broken LOW < 3.8mA LOW < 0.05 V LOW < 0.25 V
Broken bridge *LOW < 3.8mA *LOW < 0.05 V *LOW < 0.25 V
*HIGH > 22mA *HIGH > 7 V *HIGH > 11.5 V *HIGH > 4.75 V
(*) variable according to the type of failure

885198C_Manual of Electrical Installation for Pressure Probes KH-SIL2-Mobyle-series_08-2028_ENG
via Sebina, 74 - 25050 PROVAGLIO D’ISEO (BS) - ITALIA
tel. 0309888.1 - fax. 0309839063 - Internet: http://www.gefran.com
5.6 Failures and troubleshooting
In case of failures or malfunctions, on Table 2 you can find the most common failures and the means of appropriate search:
Table 2: troubleshooting
Failure Possible causes Means of research
The sensor does not feel pressure Obstruction of pressure
channel
Fault on electronics output
stage
1. Power down and remove the sensor
2. Verify eventual occlusion of the channel
under pressure. Clean any residues and
material caps
The sensor is in alarm mode type
“HIGH”
Bridge broken
Detachment of pins
Failure on primary element
1. Power down and remove the sensor
2. Check for overheating of electronics hou-
sing. Remove the causes of overheating, wait
until it cools down and power the sensor.
3. Powered the probe again, if the problem
persists, you should send back the probe to
Factory for repair.
The sensor is in alarm mode type
“LOW”
Power supply cable /connector
broken
Sensor not connected
Sensor not powered
Bridge broken
1. Power down and remove the sensor
2. Check that the power supply is connected.
If necessary, restore the power supply.
3. Check for continuity between the pins of
the connector and the power supply.
If necessary, replace the cable and the con-
nector.
4. Check if the power values are within the
specications indicated in this manual. If
necessary, replace the power supply.
5. If the problem persists, you should send
back the probe to Factory for repair.
Table of contents
Other gefran Measuring Instrument manuals
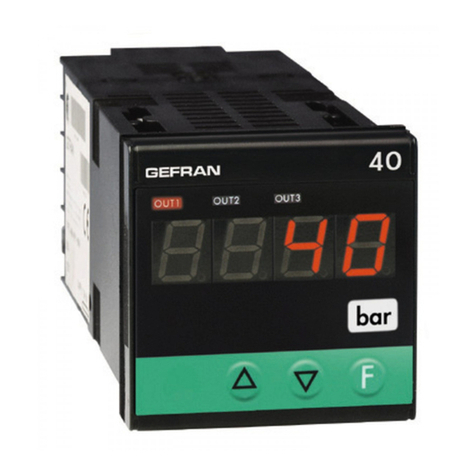
gefran
gefran 40B 48 User manual

gefran
gefran 40F 96 User manual
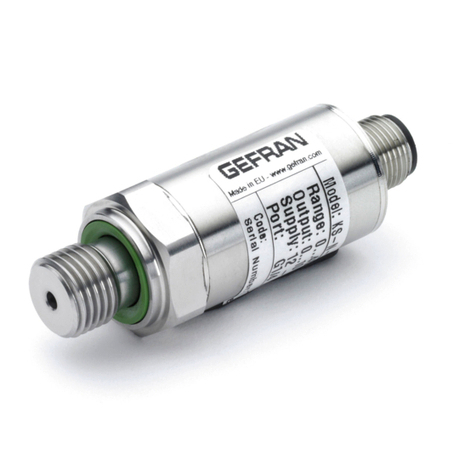
gefran
gefran KS Series User manual
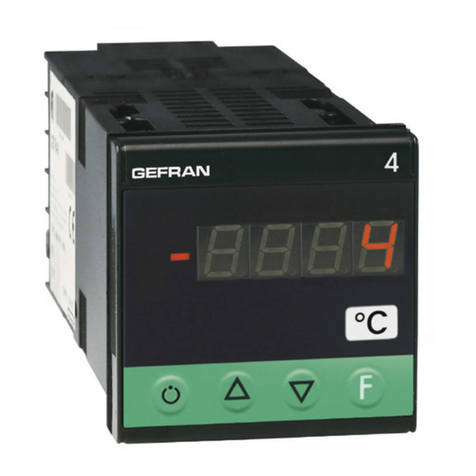
gefran
gefran 4A 48 User manual
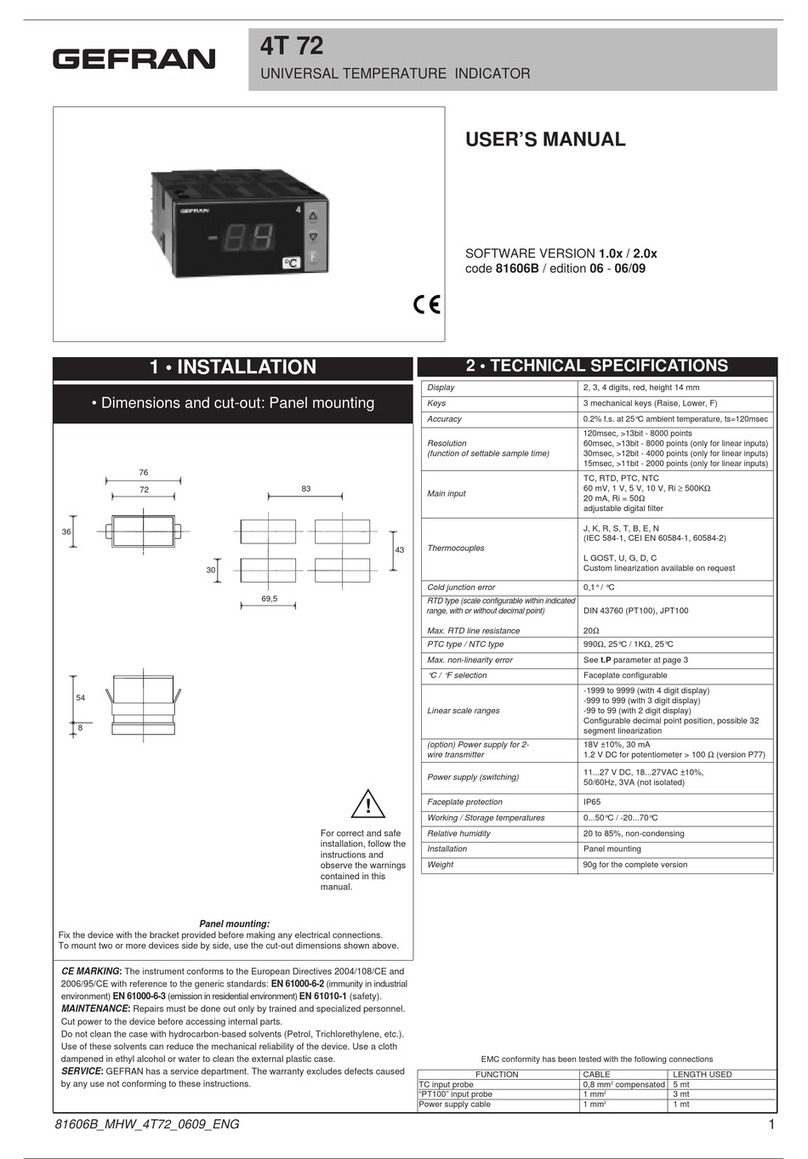
gefran
gefran 4T72 User manual
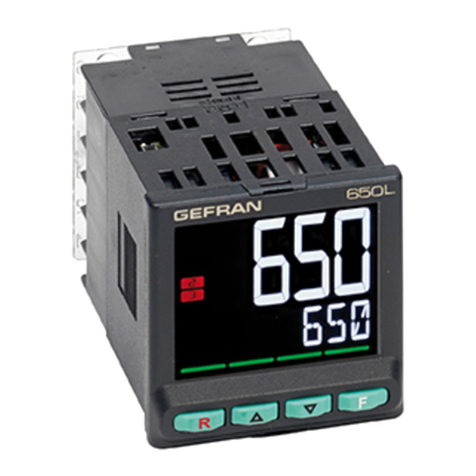
gefran
gefran 650 L Quick guide
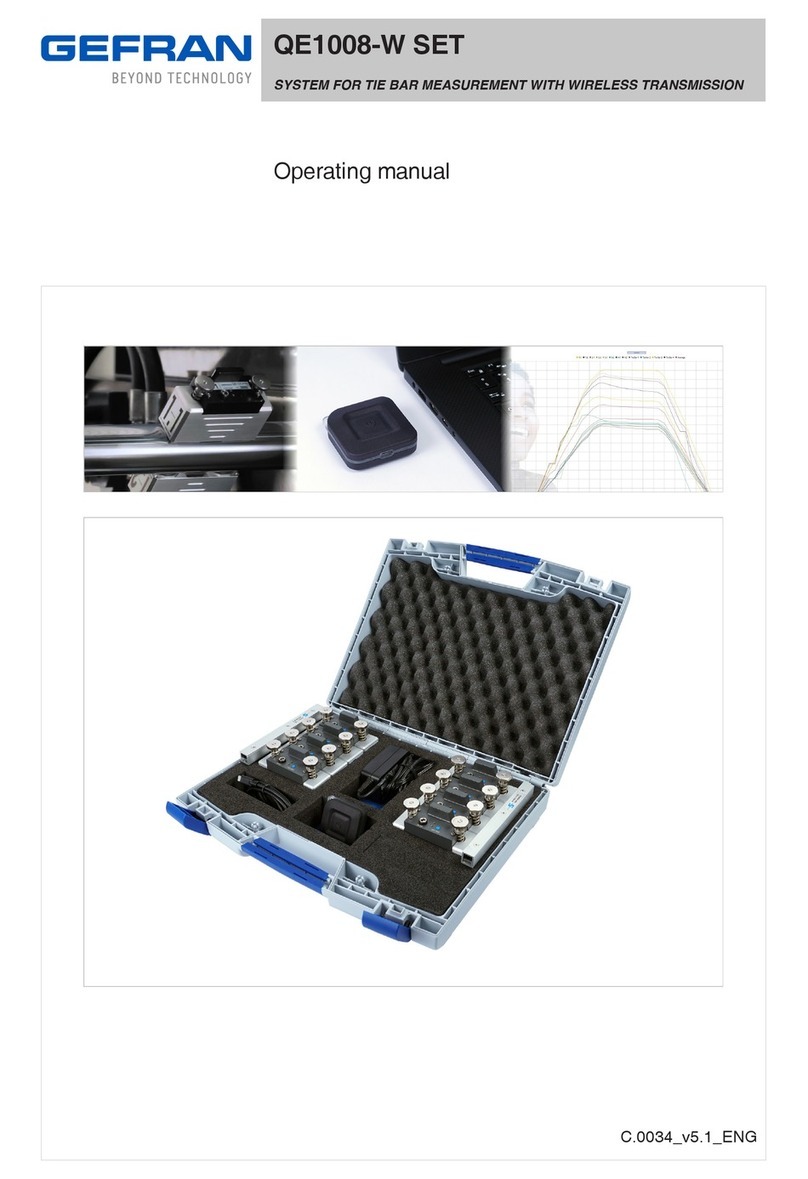
gefran
gefran QE1008-W SET User manual
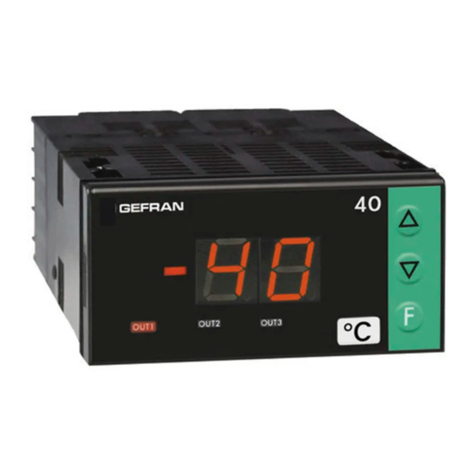
gefran
gefran 40T 72 User manual

gefran
gefran 40A 48 User manual
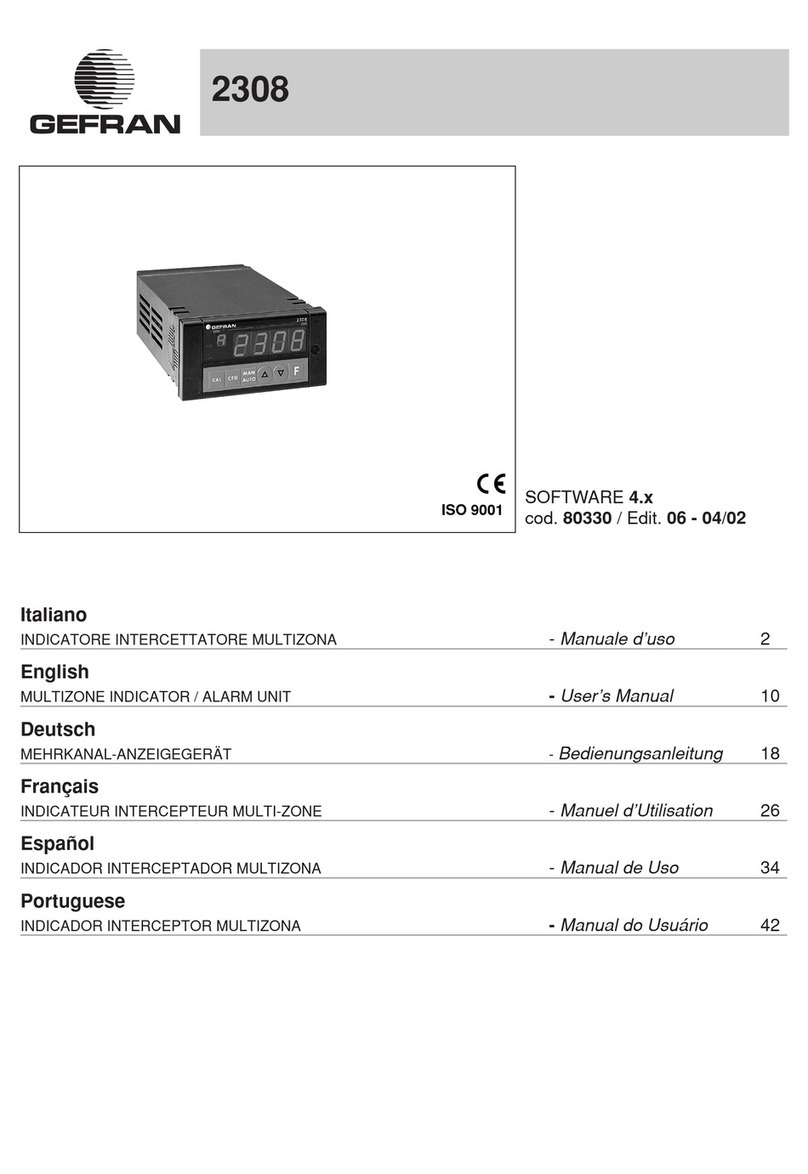
gefran
gefran 2308 User manual