LPKF ProtoMat S62 User manual

How-To Document Updated on:
11/13/2008
By:Christopher Ware
Page 1 of 13
Problem/Procedure Description
•How to exchange the head unit on the S62 and S100
Requirements
•T20 torque wrench (provided with the head unit)
•T10 torque wrench (provided with the head unit)
•T9 torque wrench (provided with the head unit)
•#2 phillips screw driver
•jewelers flat head screw driver
•Large tip flat head screw driver
•Tape
•Fiducial recognition camera (may be sent with head unit if a camera system was not purchased)
•U-Eye camera software (provided with camera)
•Boardmaster 5.0
Problem/Procedure Solution
1. Setup
a. Switch the machine on and start boardmaster
b. When prompted enter the tool status
c. If there is a tool loaded, right click on the tool select drop down menu.
i. When prompted to place the tool into the tool box, select yes.
ii. When prompted to move the machine to the pause position, select no.
iii. On the tool position window that appears, press OK.
iv. Move the machine to the exchange position.
d. Move the machine head 150mm to the right (along the X axis).
e. Shut down boardmaster
f. When prompted to discontinue communications with the machine, select yes.
g. When prompted to move the machine to the reference point, select no.
h. Turn machine power off.
2. If installed, remove the camera.
a. With a small flat head screw driver, unscrew the two (2) screws on the USB cable connector
(A in picture below)
b. Disconnect the USB cable from the camera
c. Disconnect the blue connector from the camera to the spindle control box.
(C in picture below)
d. With the T10 torque wrench, unscrew the two (2) T10 screws mounting the camera to the motor
block.
(B in picture below)
e. Remove the camera and set it aside.

How-To Document Updated on:
11/13/2008
By:Christopher Ware
Page 2 of 13
3. Removing the old machine head
a. Remove the black foot from the working depth limiter.
b. If there is no camera present, with the T10 torque wrench, loosen and remove the two (2) T10
torque screws holding the heat sink plate in place.
c. Pull the exhaust hose off of the working depth limiter
d. With the T10 torque wrench, loosen and remove the T10 screws that holds the cover to the spindle
control board. Only remove the center screw on the front panel and the screw on the left side
panel.
e. Remove the cover to the spindle control board.

How-To Document Updated on:
11/13/2008
By:Christopher Ware
Page 3 of 13
f. Disconnect the black ribbon cable from the connector.
g. With the T10 torque screw, loosen and remove the torque screw that connects the cable chain
ground wire to the head unit.
h. Lift the black ribbon cable up and secure with tape.
i. With a #2 Phillips screw driver, loosen and remove the two (2) screws connecting the cable chain
to the head unit.

How-To Document Updated on:
11/13/2008
By:Christopher Ware
Page 4 of 13
j. With the T20 torque wrench, loosen and remove the three (3) T20 screws which mount the head
unit to the base unit.
Note: If you loosen the very top and very bottom screw along the left side, it will allow the spindle motor
to slip up and down.
k. Pull the machine head towards you to separate it form the Z axis slide.
4. Mounting the new machine head
a. Place the head unit into position on the z axis slide.
i. There are two guide pins on the back of the machine head that will fit into holes on the
base unit.
b. Insert and tighten the three (3) T20 torque screws.
c. Loosen and remove the two (2) T10 torque screws on the spindle control board cover as you did
for the old machine head.
d. Place the cable chain into position.
e. Insert and tighten the two (2) Phillips screws to hold the cable chain in position.
f. Connect the multi-colored ribbon cable to the white connector on the spindle control board.
g. Attach the grounding strap from the cable chain and the strap from the spindle control board, to the
motor block with the T10 torque screws.

How-To Document Updated on:
11/13/2008
By:Christopher Ware
Page 5 of 13
h. Place the spindle control board cover into position.
i. Make sure that the ribbon cable is placed in the slot in the spindle control board cover.
i. Insert and tighten the two (2) T10 torque screws on the spindle control board cover.
5. If installed, Remove vacuum table
a. Switch on the machine and start boardmaster.
i. When prompted, enter the tool status.
b. Move the machine to the pause position.
c. Remove the white underlay material from the vacuum table.
d. With the T20 torque wrench remove the two (2) T20 torque screws in the vacuum table bed
e. With a large tip flat head screw driver, unscrew the six (6) flat head screws in the vacuum table
bed.
f. Unhook the two (2) vacuum tubes from the vacuum table base.
i. Allow the vacuum tubes to fold to the back of the machine.

How-To Document Updated on:
11/13/2008
By:Christopher Ware
Page 6 of 13
g. Go to the configuration menu and select settings.
h. Press the unlock button.
i. Uncheck the vacuum table check box in the upper portion of the window.
j. Press the OK button
Note: The machine will move to the exchange position.
k. When prompted, enter the tool status.
6. Initialize the machine.
a. Go to the configuration menu and select settings.
b. Press the unlock button

How-To Document Updated on:
11/13/2008
By:Christopher Ware
Page 7 of 13
c. Press the initialize button
i. When prompted to measure the motion range, select yes.
ii. When prompted to remove the black foot from the depth limiter, press OK.
Note: the machine will measure itself along the X, Y and Z axes.
d. When prompted enter the tool status.
7. Check Z axis limits
Note: You may skip this step if you have a vacuum table.
Caution: If you do not have a vacuum table and do not complete this step, there is a possibility
of damaging the table top and/or head unit, along with breaking the drill bit located in the collet.
a. Move the machine to the pause position
b. Physically remove all tools from the tool bar.
i. Label which bits they are and set them aside.
c. Press the tool dialogue icon
i. When prompted to move to the pause position, select no or yes.
d. Change one (1) of the tool position drop down menus to the 2.95mm Special Reference Drill and
press OK.

How-To Document Updated on:
11/13/2008
By:Christopher Ware
Page 8 of 13
e. In the tool selection drop down menu, select the 2.95mm Special Reference drill.
f. Go to the configuration menu and select tool box.
g. In the window that appears, click on service
h. Enter “bmaster” as the password and press OK.
i. Press the main clamp open button.
j. Lift the machine hood and manually place the 2.95mm drill into the collet.
k. While holding the tool in the collet, press main clamp close button.
l. Close the machine hood and press OK

How-To Document Updated on:
11/13/2008
By:Christopher Ware
Page 9 of 13
m. Move the machine to the home position.
n. Move the machine 150mm to the right (along the X axis)
o. Place the brown plastic strip in the center channel underneath the drill tip.
p. Go to the configuration menu and select settings.
q. Note the Z axis range in the table size portion along the bottom of the settings window.

How-To Document Updated on:
11/13/2008
By:Christopher Ware
Page 10 of 13
r. Place this number in the command line as follows:
i. !ZA(Z number with no decimal point)
s. Press the send button
t. Check to see if the brown strip can be moved side to side.
u. The tip of the drill bit should make a small groove into the plastic strip.
v. Place this command into the command line and press the send button.
i. PU;
w. Form step 8 u, if the tip breaks, or is not touching the plastic strip, proceed to step 9.
x. From step 8 u, if the tip makes a small groove in the plastic strip, go to step 10.
y. Attach the small section of vacuum hose from the hose holder to the left side of the working depth
limiter.
8. Adjusting the Z axis limits
a. Lift the vacuum hose out of the holder on the left side of the machine head.
b. With the T10 torque wrench, loosen and remove the two screws holding the vacuum hose holder.

How-To Document Updated on:
11/13/2008
By:Christopher Ware
Page 11 of 13
c. With a T9 torque wrench turn the set screw on the base unit.
i. 1 turn clockwise will raise the machine head 0.5mm
ii. 1 turn counter-clockwise will lower the machine head 0.5mm
d. Repeat the directions stated in step 8 f through w.
e. Place the vacuum hose holder into position.
f. Insert and tighten the two T10 torque screws on the vacuum hose holder.
g. Attach the bottom vacuum hose from the hose holder to the left side of the working depth limiter.
9. If previously installed, mount the vacuum table
a. Move the machine to the pause position
b. Re-attach the two (2) vacuum tubes to the vacuum table
c. Insert and hand tighten the two (2) T20 torque screws securing the vacuum table to the table top.
d. Insert and hand tighten the six (6) large tip flat head screws securing the vacuum table to the table
top.
e. Tighten all screws.
f. Place the white underlay material into the vacuum table bed.

How-To Document Updated on:
11/13/2008
By:Christopher Ware
Page 12 of 13
g. Go to the configuration menu and select settings.
h. Press the unlock button.
i. Place a check box in the vacuum table box in the upper portion of the settings window.
j. Press the OK button.
Note: the machine will move to the exchange position.
k. When prompted, enter the tool status.
10. Mount the camera system
a. See the installation document “installing the fiducial recognition camera.”
b. This document comes with the camera.
11. Adjust camera offset
a. Re-attach the black foot to the bottom of the working depth limiter.
b. See the how to document “how to set camera offset.”
12. Align toolbar
a. See the document “how to align toolbar on S series.”
13. Drill new set pins
a. See the document “how to drill set pins”
i. This is optional if you have a camera installed.
14. Exchanging the head unit process is now complete.
Other manuals for ProtoMat S62
1
This manual suits for next models
1
Other LPKF Power Tools manuals
Popular Power Tools manuals by other brands
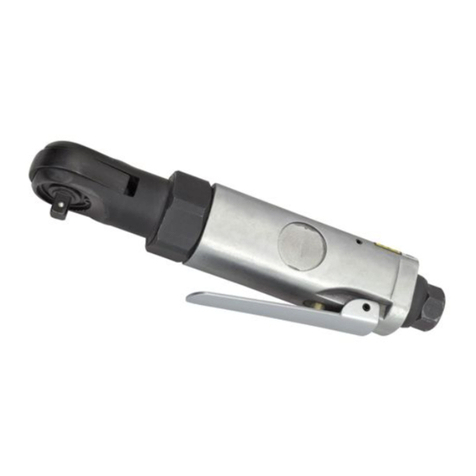
Central Pneumatic
Central Pneumatic Central Pneumatic 1/4" Stubby Air Ratchet... operating instructions
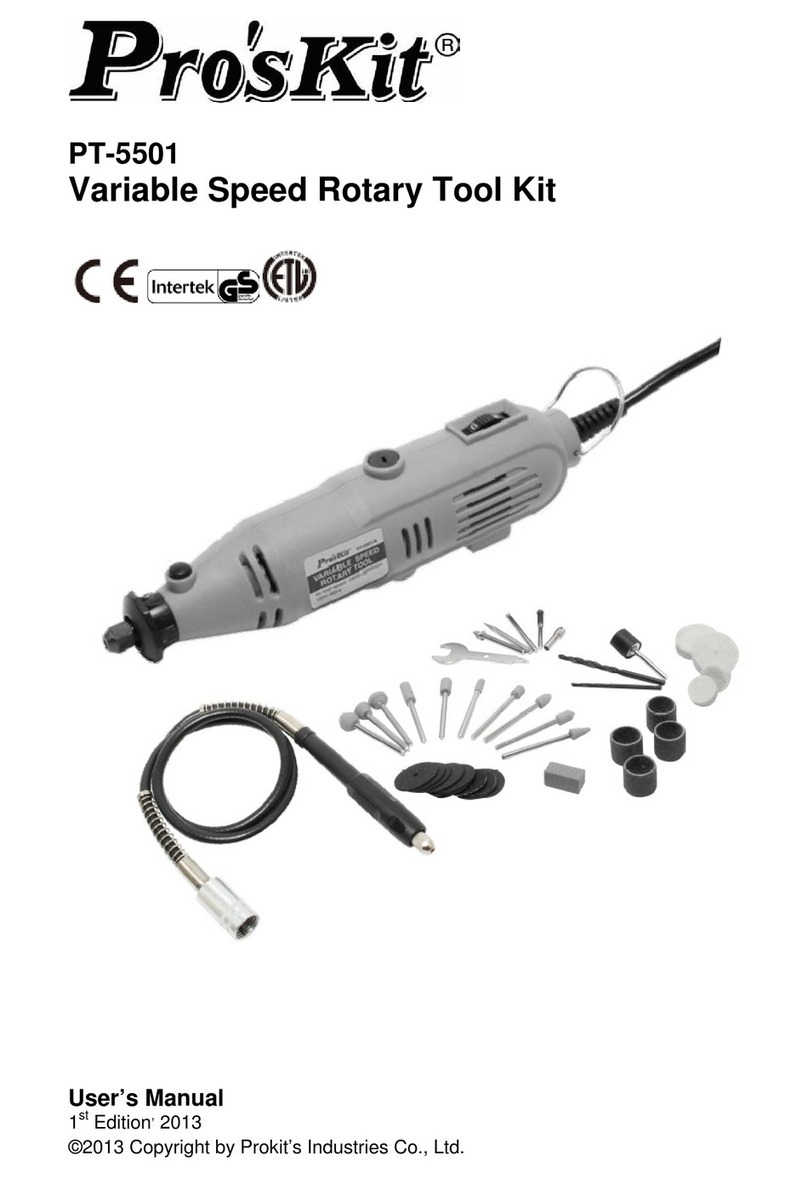
Pro's Kit
Pro's Kit PT-5501 user manual

Worx Nitro
Worx Nitro WG330E.X Safety and operating manual

Flex
Flex GCE 6-EC manual
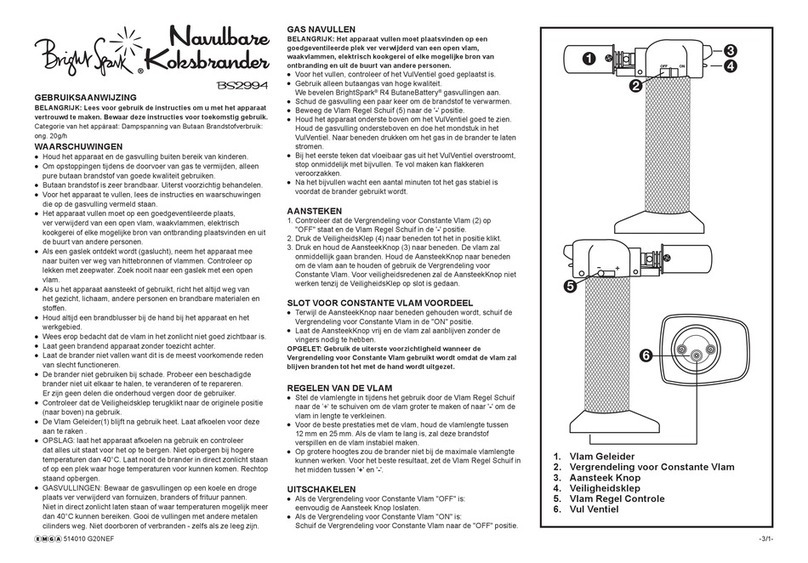
Bright Spark
Bright Spark BS 2994 Instructions for use
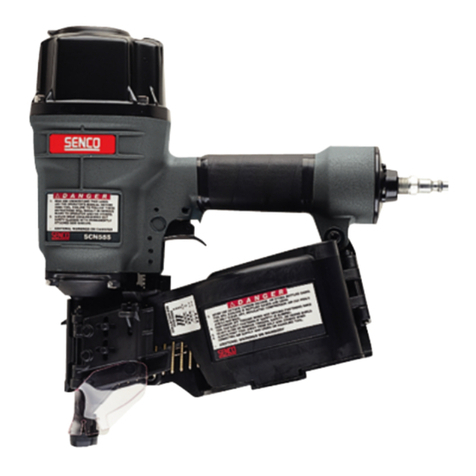
Senco
Senco SCN55S operating instructions