LTG HDF-600 User manual

Operating, Installation, Maintenance Instructions
LTG Air-Water Systems
AIR TECH
SYSTEMS
A
ctive chilled beams HDF-600
Ceiling installation

ELTG Incorporated ·PO Box 2889 ·Spartanburg, S.C. 29304, USA
Chilled beams HDF-us-OM (01/17)
Phone 864 599-6340, Fax -6344 ·info@LTG-INC.net ·www.LTG-INC.net
Former editions are invalid ·Subject to technical modifications page 2 of 30
Installation, operating and maintenance instructions
Active chilled beams HDF-600, ceiling installation
LTG Comfort Air Technology
Air Diffusers
Air Distribution
Air-Water-Systems
Contents Page
1. Safety 3
1.1 Explanation of symbols and hints 3
1.2 Operating safety directions 3
1.3 Intended use 4
2. Transportation, storage 4
2.1 Transport instructions 4
2.2 Storage 4
3. Function 4
3.1 Control system with CO2-Sensor 5
4. Technical data 6
4.1 Dimensions 6
4.2 Performance data 8
4.3 Caloric output data 13
4.4 Acoustic data 15
4.5 Hydraulic data 15
4.6 Weight 15
5. Installation 15
5.1 Notes 15
5.2 Suspension 15
5.3 Water connections 18
5.4 Check after installation 23
6. First use 24
6.1 Adjustment of the nozzle band 24
7. Operating, maintenance, repair 25
7.1 Open/close the unit 25
7.2 Heat exchanger, water connections 27
7.3 2-pipe and 4-pipe system 27
7.4 Selecting the room temperature 27
7.5 Out-of-service times 27
7.6 Repair 27
7.7 Troubleshooting and corrective action 27
7.8 Maintenance intervals of the individual
components
30
8. Spare parts 30
9. Decommissioning, disposal 30

ELTG Incorporated ·PO Box 2889 ·Spartanburg, S.C. 29304, USA
Chilled beams HDF-us-OM (01/17)
Phone 864 599-6340, Fax -6344 ·info@LTG-INC.net ·www.LTG-INC.net
Former editions are invalid ·Subject to technical modifications page 3 of 30
Installation, operating and maintenance instructions
Active chilled beams HDF-600, ceiling installation
1. Safety
Assembly, dismantling and mainte
nance must be performed by trained
personnel in order to achieve reliability,
safety and best results.
1.1 Explanation of symbols and hints
Operating safety symbol
This symbol is placed alongside every
operating safety instruction in these ope
rating instructions, wherever there is a
danger to life and limb. Observe these in
structions and in such cases proceed with
extreme caution.
Pass on all the operating safety instructions to other
users. In addition to the instructions contained in these
operating instructions, the generally applicable safety
and accident prevention regulations must be observed;
as shown here, for example: Warning of hazard point.
Information symbol
This information symbol is placed
alongside those points in the manual
which must be specifically observed in
order to ensure that the guidelines, regu
lations, instructions and correct opera
ting sequences are observed and to pre
vent damage to or destruction of the unit
and/or other components in the system.
These mandatory symbols are linked to
the operating safety instructions and
show which protective measures must be
complied with at the appropriate worksta
tions and therefore specifically mandate a
certain action, as shown here as an exam
ple: Wear protective gloves.
These prohibition symbols are linked to
the operating safety instructions banning
a dangerous or risky action, as shown
here as an example: Do not touch.
1.2 Operating safety instructions
Carefully read the safety instructions before using any
LTG active chilled beam. Always follow the safety instruc
tions!
The units meet any pertinent safety standards.
The installation and maintenance of ac
tive chilled beams may be dangerous be
cause of high pressures and electrical
components being alive. Therefore, the
installation, maintenance, and repair
must be performed by qualified and
trained staff only.
Safety instructions in the technical documentation and
on unit labels must be followed at all times.
Do not open the unit forcleaning, maintenance, orrepair
and do not remove covers and casings (air diffuser) un
less all conducting lines have been completely
disconnected.
In the heating mode a tem
perature of up to +176 °F
may be achieved. Water-
carrying parts may be hot
so do not touch with your
bare hands to avoid burns.
Heat exchanger blades and
housing parts are sharp-
edged.
The standard version of the
heat exchangers is de
signed for an operating
pressure of 145 psi (test
pressure 232 psi). High wa
ter pressures may be haz
ardous. Higher operating
pressures, therefore, re
quire LTG's express per
mission.
Parts and tools.
When working overhead.

ELTG Incorporated ·PO Box 2889 ·Spartanburg, S.C. 29304, USA
Chilled beams HDF-us-OM (01/17)
Phone 864 599-6340, Fax -6344 ·info@LTG-INC.net ·www.LTG-INC.net
Former editions are invalid ·Subject to technical modifications page 4 of 30
Installation, operating and maintenance instructions
Active chilled beams HDF-600, ceiling installation
Continuation 1.2 Operating safety instructions
The casing on site also serves as a protec
tion and should be removed for mainte
nance and cleaning only.
Avoid any additional load to the unit or the
suspensions since stability might be insufficient.
The unit must be checked by an expert immediately
- if it has been mechanically damaged
- it is suffering from a water damage,
- if the suspension or the casing show clear signs of
corrosion or ageing.
Do not put the unit back into operation before all neces
sary maintenance and repair has been performed!
1.3 Intended use
The HDF unit is intended for use in closed rooms.
It is designed for ambient temperatures of 41 °F to 104 °F
and a maximum relative humidity of up to 90% (non-con
densing). The maximum admissible supply temperature
is limited to 176 °C.
Any other operating conditions require the express and
written permission of LTG Aktiengesellschaft.
LTG Aktiengesellschaft does not assume
responsibility for any damages resulting
from unintended use.
2. Delivery, transport, storage
The unit requires dry and dust-free conditions during
transport, storage, installation, and operation.
The unit is supplied in corrugated board boxes secured
with straps.
Units are stacked on Euro or single trip pallets and se
cured with straps. Pallets may be moved using forklifts or
cranes.
Do not remove the packaging unless immediately prior to
installation on site to protect the unit from pollution and
damages.
LTG Aktiengesellschaft will not take re
sponsibility for any pollution of or dam
ages to the unit.
2.1 Transport instructions
Handle units appropriately and with care during trans
port. Do not throw, let drop to the ground or bump into
other items or walls.
Make sure that units are safely fastened during transport
and avoid damage through other items.
It is recommended to always have units handled by at
least two persons.
The packaging is not weather-resistant.
2.2 Storage
Make sure that the units are entirely protected against
weathering, humidity, and other adverse conditions that
might result in damages during storage.
The storage location must meet the following climatic re
quirements: Temperature between 41 °F and 131 °F with
a relative humidity of 90 % max. (non-condensing).
3. Function
The active chilled beam HDF is a ceiling-mounted induc
tion unit for ventilation and individual temperaturecontrol
based on the induction principle, i.e. without the use of a
fan, using processed outside air.
The low construction height (79 in) allows installation in
false ceilings offering limited space. The thus resulting
low difference in height between the heat exchanger and
the ceiling level has been considered in the chilled beam's
design which is suitablefor dry cooling without dehumidi
fication and condensate drainage.
The chilled beam is suitable for installation in grid ceilings
measuring 2 x 2 ft, 2 x 4 ft, 24.6 x 24.6 in or 24.6 x 49.2 in
and may be positioned in or adjacent to Tbar profiles.
With grid and plasterboard ceilings, installation may be
edgetoedge or overlapping.
During operation, the primary air is 100% pretreated out
side air via a central central AHU. It assures the use-de
pendent basic ventilation using outside air, e.g. in con
formity with DIN EN 13779 or DIN EN 15251
recommendations. Through uniformly arranged nozzles
over the entire unit length, the primary airis led in an injec
tor-type diffuser which induces secondary air. Depending
on the room load, this secondary air is either heated or
chilled in a 2-pipe or 4-pipe heat exchanger.
The supply air, a mixture of primary and secondary air, is
uniformly diffused to 2 or 4 sides into the room via preset,
divergent ceiling jets.
Room air humidity is controlled through the centrally de
humidified supply air avoiding involuntary dehumidifica
tion inside the chilled beam. The 2-pipe system may be
used for either cooling only or change-over operation with
cooling/reheating. The 4-pipe system with independent
water circuits automatically switches from cooling to
heating and vice versa.
Thetypeofconstruction,whichprovidescompletesepa
ration from the ceiling cavity, suppresses sound trans
mission from adjacent rooms (transmission sound insu
lation).

ELTG Incorporated ·PO Box 2889 ·Spartanburg, S.C. 29304, USA
Chilled beams HDF-us-OM (01/17)
Phone 864 599-6340, Fax -6344 ·info@LTG-INC.net ·www.LTG-INC.net
Former editions are invalid ·Subject to technical modifications page 5 of 30
Installation, operating and maintenance instructions
Active chilled beams HDF-600, ceiling installation
3.1 Control system with CO2-Sensor
Heating signal
0...10 V
24 AC
Room temperature
sensor
Signal for flow rate controller 0...10 V
Cool. signal 0...10 V
Power supply
optional
Presence sensor
VREactive Warm water valve
Cold water valve
Signal for CO2
0...10 V
Room
Unit
Window contact
The set value for the flow
rate controller depends on
actual CO2value
CO2, IST -CO
2, SOLL
Vmin (2 V)
0
Vmax (10 V)
TIST -T
SOLL0
Vmin
Vmax, 2. Temperature control circuit
Set value for flow rate controller
The highest value of the 2 control
circuits is decisive.
Low cooling load
(0...48 % of cooling capacity)
cooling valves open,
Vprim remains at Vmin
increased cooling load
(52...100 % of cooling capacity)
cooling valves are completely
opened, Vprim opens to Vmax
VCO
2
1. CO2control circuit
SOLL = nominal value, IST = actual value
Cooling
valve
Heating
valve

ELTG Incorporated ·PO Box 2889 ·Spartanburg, S.C. 29304, USA
Chilled beams HDF-us-OM (01/17)
Phone 864 599-6340, Fax -6344 ·info@LTG-INC.net ·www.LTG-INC.net
Former editions are invalid ·Subject to technical modifications page 6 of 30
Installation, operating and maintenance instructions
Active chilled beams HDF-600, ceiling installation
4. Technical data
4.1. Dimensions
Type HDF-600/2A/2, 2-way diffusion, size 1200
L
A1
~1.8 5
5 (125)
5
7.83
23.1
7.83
0.33 0.33
14.76
0,47
1.26
1.1
~2.6
1.95 0.39
Front view 2-pipe system Lateral view left side
Top view
Diffuser grille
Isometric views
23,74 (603)
25,68 (652.5)
Bracketed dimensions = mm
Shown: connection on the left side
1.5(38)
4.3(109)2(50)10.8(275)2(50)
2.8(72)
Ø 0.5 (12)
Front view 4-pipe system
Size L[“ (mm)] A1 [“ (mm)] A2 [“ (mm)] connecting pieces /
diameter [“ (mm)]
1200 47.75 (1213) 22.48 (571) -1 / Ø 5 (125)
1800 71.73 (1822) 20.94 (532) 33.46 (850) 2 / Ø 5 (125)
2400 95.74 (2432) 16.07 (408,3) 30.18 (766,7) 3 / Ø 5 (125)

ELTG Incorporated ·PO Box 2889 ·Spartanburg, S.C. 29304, USA
Chilled beams HDF-us-OM (01/17)
Phone 864 599-6340, Fax -6344 ·info@LTG-INC.net ·www.LTG-INC.net
Former editions are invalid ·Subject to technical modifications page 7 of 30
Installation, operating and maintenance instructions
Active chilled beams HDF-600, ceiling installation
Continuation 4.1 Dimensions
Type HDF-600/2A/2, 2-way diffusion, size 2400
Front view 2-pipe system Lateral view left side
Top view
Isometric view
Bracketed dimensions = mm
22.7
14.76
0.47
1.6
1.1
0.510.51
2.6~
7.83
1.95 0.39 5 (125)5 (125)5 (125)
~2.4
A2A2A1
L
2 Diffuser grilles
23.74 (603)
25.68 (652,5)
Shown: connection on the left side
1.5(38)
4.3(109)2(50)10.8(275)2(50)
2.8(72)
Ø 0.5 (12)
Front view 4-pipe system
Size L[“ (mm)] A1 [“ (mm)] A2 [“ (mm)] connecting pieces /
diameter [“ (mm)]
1200 47.75 (1213) 22.48 (571) -1 / Ø 5 (125)
1800 71.73 (1822) 20.94 (532) 33.46 (850) 2 / Ø 5 (125)
2400 95.74 (2432) 16.07 (408,3) 30.18 (766,7) 3 / Ø 5 (125)

ELTG Incorporated ·PO Box 2889 ·Spartanburg, S.C. 29304, USA
Chilled beams HDF-us-OM (01/17)
Phone 864 599-6340, Fax -6344 ·info@LTG-INC.net ·www.LTG-INC.net
Former editions are invalid ·Subject to technical modifications page 8 of 30
Installation, operating and maintenance instructions
Active chilled beams HDF-600, ceiling installation
4.2. Performance data
Size 1200, 2-way diffusion, 2-pipe system
VP
cfm
Δp
in H2O
LA18
dB(A)
LwA
dB(A)
QP/Δt
BTU/h·Δt-1
Qc/Δt
BTU/h·Δt-1
Qc1)
BTU/h
Woc / Δpw
gpm / Ft H2O
37 0.28 15 21 40 95 2439
0.75 / 1
45 0.40 20 26 48 114 2903
54 0.60 25 31 57 124 3255
47 0.28 19 25 49 103 2750
56 0.40 24 30 61 116 3162
67 0.60 29 35 72 131 3645
58 0.28 23 29 63 106 3023
70 0.40 27 33 76 122 3526
84 0.60 33 39 91 141 4134
73 0.28 26 33 78 110 3366
89 0.40 31 37 95 125 3930
106 0.60 36 42 114 150 4702
Size 1800, 2-way diffusion, 2-pipe system
VP
cfm
Δp
in H2O
LA18
dB(A)
LwA
dB(A)
QP/Δt
BTU/h·Δt-1
Qc/Δt
BTU/h·Δt-1
Qc1)
BTU/h
Woc / Δpw
gpm / Ft H2O
59 0.28 17 23 63 152 3856
0.75 / 1.5
72 0.40 19 25 76 179 4563
86 0.60 24 30 91 194 5110
74 0.28 18 24 80 165 4372
90 0.40 23 29 95 182 4991
108 0.60 28 34 114 209 5787
93 0.28 22 28 99 167 4770
112 0.40 27 33 120 192 5559
135 0.60 32 38 144 222 6531
116 0.28 26 32 124 175 5345
141 0.40 30 36 150 198 6229
168 0.60 35 41 179 236 7439

ELTG Incorporated ·PO Box 2889 ·Spartanburg, S.C. 29304, USA
Chilled beams HDF-us-OM (01/17)
Phone 864 599-6340, Fax -6344 ·info@LTG-INC.net ·www.LTG-INC.net
Former editions are invalid ·Subject to technical modifications page 9 of 30
Installation, operating and maintenance instructions
Active chilled beams HDF-600, ceiling installation
Continuation 4.2 Performance data
Size 2400, 2-way diffusion, 2-pipe system
VP
cfm
Δp
in H2O
LA18
dB(A)
LwA
dB(A)
QP/Δt
BTU/h·Δt-1
Qc/Δt
BTU/h·Δt-1
Qc1)
BTU/h
Woc / Δpw
gpm / Ft H2O
81 0.28 15 21 87 209 5284
0.75 / 2
98 0.40 20 26 105 243 6232
118 0.60 25 31 125 264 6977
102 0.28 19 25 108 224 5967
123 0.40 23 29 131 251 6824
148 0.60 28 34 158 283 7891
127 0.28 23 29 135 228 6518
154 0.40 27 33 163 260 7592
184 0.60 32 38 196 302 8928
159 0.28 26 32 169 238 7286
192 0.40 31 37 205 272 8531
231 0.60 36 42 245 323 10,176
The chart shows examples for the unit design. A special
selection program is available for other flow rates, pri
mary pressures, temperatures and water flow rates.
Data refer to the unit including a secondary air grille
²63 % free surface
Correction for other flow rates see section 4.3 (Caloric
output data).
1) Water supply temperature: 61 °F
Air inlet temperature or return air temperature: 79 °F
2) Water supply temperature: 104 °F
Air inlet temperature or return air temperature: 72 °F
Primary air temperature: 61 °F
VP- primary air flow rate (±3%)
p- static pressure at the primary air connection
LA18 - sound pressure level at 18 m2Sabine (±3dB)
LwA - sound power level (±3dB)
QP- air-side cooling capacity (primary air ±3%)
Qc- water-side cooling capacity (secondary ±6%)
t- temperature difference between air inlet and
water supply
woc - standard water flow rate (cooling)
pw- water-side pressure loss

ELTG Incorporated ·PO Box 2889 ·Spartanburg, S.C. 29304, USA
Chilled beams HDF-us-OM (01/17)
Phone 864 599-6340, Fax -6344 ·info@LTG-INC.net ·www.LTG-INC.net
Former editions are invalid ·Subject to technical modifications page 10 of 30
Installation, operating and maintenance instructions
Active chilled beams HDF-600, ceiling installation
Continuation 4.2 Performance data
Size 1200 (2' x 4'), 4-pipe-system - cooling and heating, air diffusion on 2 sides
VP
cfm
Δp
in H2O
LwA
dB(A)
NC QP/Δt
BTU/h·Δt1
Qc/Δt
BTU/h·Δt1
Qctot1)
BTU/h
woc
gpm
Δpw
feet
Qh/Δt
BTU/h·Δt1
Qhtot2)
BTU/h
woh
gpm
Δpw
Ft H2O
37 0.28 21 15 39.8 88.0 2,286
0.75 2
63.3 2,051
0.48 2.3
45 0.40 26 19 48.2 102.5 2,711 73.2 2,373
54 0.60 31 23 57.8 119.0 3,190 84.3 2,733
47 0.28 25 20 49.8 95.7 2,602 68.3 2,212
57 0.40 30 25 60.3 111.4 3,098 78.8 2,554
68 0.60 35 30 72.2 129.3 3,620 90.6 2,937
59 0.28 29 24 62.2 102.2 2,962 72.2 2,340
71 0.40 33 28 75.4 119.0 3,506 83.2 2,697
85 0.60 39 29 90.3 138.1 4,116 95.5 3,094
73 0.28 33 27 77.8 106.5 3,311 74.3 2,408
89 0.40 37 30 94.2 124.0 3,913 85.4 2,768
106 0.60 42 34 112.9 143.9 4,625 97.8 3,167
Size 1800 (2' x 6'), 4-pipe-system - cooling and heating, air diffusion on 2 sides
VP
cfm
Δp
in H2O
LwA
dB(A)
NC QP/Δt
BTU/h·Δt1
Qc/Δt
BTU/h·Δt1
Qctot1)
BTU/h
woc
gpm
Δpw
feet
Qh/Δt
BTU/h·Δt1
Qhtot2)
BTU/h
woh
gpm
Δpw
Ft H2O
59 0.28 23 17 63.1 138.8 3,627
0.75 2.8
98.0 3,175
0.48 3.3
72 0.40 25 18 76.5 161.6 4,276 112.9 3,659
86 0.60 30 22 91.6 187.6 5,027 129.5 4,197
74 0.28 24 19 78.9 150.9 4,150 105.2 3,409
90 0.40 29 24 95.6 175.7 4,893 120.9 3,918
108 0.60 34 29 114.5 203.9 5,746 138.3 4,482
93 0.28 28 23 98.6 161.2 4,676 110.7 3,586
112 0.40 33 28 119.5 187.7 5,528 126.9 4,111
135 0.60 38 28 143.2 217.8 6,500 144.7 4,687
116 0.28 32 26 123.3 167.9 5,256 113.2 3,666
140 0.40 36 29 149.3 195.5 6,202 129.2 4,187
168 0.60 41 33 178.9 226.9 7,315 146.8 4,756

ELTG Incorporated ·PO Box 2889 ·Spartanburg, S.C. 29304, USA
Chilled beams HDF-us-OM (01/17)
Phone 864 599-6340, Fax -6344 ·info@LTG-INC.net ·www.LTG-INC.net
Former editions are invalid ·Subject to technical modifications page 11 of 30
Installation, operating and maintenance instructions
Active chilled beams HDF-600, ceiling installation
Continuation 4.2 Performance data
Size 2400 (2' x 8'), 4-pipe-system - cooling and heating, air diffusion on 2 sides
VP
cfm
Δp
in H2O
LwA
dB(A)
NC QP/Δt
BTU/h·Δt1
Qc/Δt
BTU/h·Δt1
Qctot1)
BTU/h
woc
gpm
Δpw
feet
Qh/Δt
BTU/h·Δt1
Qhtot2)
BTU/h
woh
gpm
Δpw
Ft H2O
81 0.28 21 15 86.4 189.6 4,968
0.75 3.7
131.4 4,258
0.48 4.3
98 0.40 26 19 104.7 220.7 5,842 150.9 4,890
118 0.60 31 23 125.5 256.2 6,864 172.4 5,586
102 0.28 25 20 108.0 206.0 5,664 140.5 4,552
123 0.40 29 24 130.9 239.9 6,689 160.8 5,210
147 0.60 34 29 156.8 278.5 7,838 183.1 5,932
127 0.28 29 24 135.1 220.1 6,389 147.1 4,765
154 0.40 33 28 163.6 256.3 7,550 167.7 5,433
184 0.60 38 28 196.0 297.5 8,885 190.1 6,160
159 0.28 32 26 168.8 229.3 7,167 149.4 4,841
192 0.40 37 30 204.5 267.0 8,491 169.6 5,495
230 0.60 42 34 245.0 309.9 10,006 191.3 6,199
The chart shows examples for the unit design. A special
selection program is available for other flow rates, pri
mary pressures, temperatures and water flow rates.
Data refer to the unit with secondary air grille
>63 % free surface
Correction for other flow ratessee section 4.3 (Caloric out-
put data)
1) 61_F water supply temperature
79_F air inlet temperature or return air temperature
61_F primary air temperature
2) 104_F water supply temperature
72_F air inlet temperature or return air temperature
61 °F primary air temperature
VP- primary air flow rate (± 3%)
Δp- static pressure at the primary air connection
LwA -soundpower(±3dB)
NC - expected Noise Criterion adhered based on a
total room sound absorption of 10 dB
QP- air-side cooling capacity (primary air ± 3%)
Qc- water-side cooling capacity (secondary ± 6%)
Qctot - total cooling capacity
Δt- temp. differ. between air inlet and water supply
woc - standard water flow rate (cooling)
Δpw- water-side pressure loss
Qh- water-side heating capacity (secondary ± 6%)
Qhtot - total heating capacity
woh - standard water flow rate (heating)

ELTG Incorporated ·PO Box 2889 ·Spartanburg, S.C. 29304, USA
Chilled beams HDF-us-OM (01/17)
Phone 864 599-6340, Fax -6344 ·info@LTG-INC.net ·www.LTG-INC.net
Former editions are invalid ·Subject to technical modifications page 12 of 30
Installation, operating and maintenance instructions
Active chilled beams HDF-600, ceiling installation
Continuation 4.2 Performance data
Size 1200 (2' x 4'), 2-pipe-system - cooling or heating, air diffusion on 4 sides
VP
cfm
Δp
in H2O
LwA
dB(A)
QP/Δt
BTU/h·Δt-1 Qc/Δt
BTU/h·Δt-1 Qctot1)
BTU/h
woc
gpm
Δpw
feet
Qh/Δt
BTU/h·Δt-1 Qhtot2)
BTU/h
woh
gpm
Δpw
Ft H2O
32 0.28 18 34.1 85.3 2,143
0.75 2.3
75.8 2,119
0.48 1.0
38 0.40 23 39.8 100.5 2,508 89.1 2,446
46 0.60 28 49.3 119.4 3,033 106.1 2,931
39 0.28 22 41.7 94.8 2,446 83.4 2,276
47 0.40 27 49.3 108.0 2,852 96.7 2,600
58 0.60 32 60.7 130.8 3,432 115.6 3,091
49 0.28 26 51.2 102.4 2,784 91.0 2,405
59 0.40 30 62.5 117.5 3,238 104.2 2,729
72 0.60 35 75.8 140.3 3,886 125.1 3,217
62 0.28 30 64.4 111.8 3,170 98.6 2,511
74 0.40 34 77.7 127.0 3,681 113.7 2,825
90 0.60 39 94.8 149.7 4,411 134.6 3,306
77 0.28 33 81.5 119.4 3,613 106.1 2,579
92 0.40 38 96.7 136.5 4,190 121.3 2,880
112 0.60 43 117.5 161.1 5,015 142.2 3,340
98 0.28 37 104.2 128.9 4,193 115.6 2,607
118 0.40 42 123.2 145.9 4,862 130.8 2,876
Size 1200 (2' x 4'), 4-pipe-system - cooling and heating, air diffusion on 4 sides
32 0.28 18 34.1 77.7 1,989
0.75 2.3
55.0 1,436
0.48 1.0
38 0.40 23 39.8 91.0 2,368 66.3 1,699
46 0.60 28 49.3 113.7 2,921 81.5 2,088
39 0.28 22 41.7 87.2 2,323 62.5 1,576
47 0.40 27 49.3 104.2 2,753 73.9 1,839
58 0.60 32 60.7 127.0 3,367 87.2 2,201
49 0.28 26 51.2 98.6 2,702 70.1 1,696
59 0.40 30 62.5 115.6 3,183 81.5 1,948
72 0.60 35 75.8 138.4 3,855 96.7 2,300
62 0.28 30 64.4 108.0 3,125 75.8 1,774
74 0.40 34 77.7 125.1 3,654 87.2 1,992
90 0.60 39 94.8 147.8 4,381 102.4 2,276
77 0.28 33 81.5 119.4 3,589 81.5 1,791
92 0.40 38 96.7 134.6 4,159 92.9 1,938
112 0.60 43 117.5 155.4 4,920 104.2 2,095
98 0.28 37 104.2 127.0 4,152 87.2 1,682
118 0.40 42 123.2 140.3 4,756 92.9 1,696
The chart shows examples for the unit design. A special
selection program is available for other flow rates, pri
mary pressures, temperatures and water flow rates.
Data refer to the unit with secondary air grille >63 % free
surface.
Correction for other flow rates see section 4.3 (Caloric …)
1) 61_F water supply, 79_F air inlet or return air,
61_F primary air
2) 104_F water supply, 72_F air inlet or return air,
61 °F primary air
VP- primary air flow rate (± 3 %)
Δp- static pressure at the primary air connection
LwA -soundpower(±3dB)
NC - expected Noise Criterion adhered based on a
total room sound absorption of 10 dB
QP- air-side cooling capacity (primary air ± 3 %)
Qc- water-side cooling capacity (secondary ± 6 %)
Qctot - total cooling capacity
Δt- temp. differ. between air inlet and water supply
woc - standard water flow rate (cooling)
Δpw- water-side pressure loss
Qh- water-side heating capacity (secondary ± 6 %)
Qhtot - total heating capacity
woh - standard water flow rate (heating)

ELTG Incorporated ·PO Box 2889 ·Spartanburg, S.C. 29304, USA
Chilled beams HDF-us-OM (01/17)
Phone 864 599-6340, Fax -6344 ·info@LTG-INC.net ·www.LTG-INC.net
Former editions are invalid ·Subject to technical modifications page 13 of 30
Installation, operating and maintenance instructions
Active chilled beams HDF-600, ceiling installation
4.3 Caloric output data
Caloric output data were determined at a test stand in the
LTG test lab. Data are valid if the following applies:
- unit at operating temperature, steady-state condition
- steady-state condition during measurements
- no condensation at the heat exchanger in the cooling
mode
- water without additives (drinking water quality)*
- water supply temperatures from
54 °F to 61 °F_in the cooling mode and
122 °F to 140 °F in the heating mode.
Parameters used:
- specific heat capacity of the water 1.0 BTU/lb °F
- specific heat capacity of the air 0.24 BTU/lb °F
- Air density 0.076 lb/ft3
To ensure easy transferability, the specific caloric outputs
- i.e. the absolute caloric outputs in relation to the temper
ature difference between water intake and induction air
before entering the heat exchanger - are given.
The outputs given in the chart do apply with specific nomi
nal flow rates only. These are stated for each type and
size.
The correction charts give a graphic illustration of how
outputs change with other flow rates compared to nomi
nal flow rate output.
Flow rates have been determined through calculation and
mayvarybyabout10%.
* Addition of ethylene glycol to lower the freezing
point: To lower the freezing point, cooling water is often
mixed with ethylene glycol. The lower specific thermal ca
pacity of the mixture reduces the unit's cooling capacity.

ELTG Incorporated ·PO Box 2889 ·Spartanburg, S.C. 29304, USA
Chilled beams HDF-us-OM (01/17)
Phone 864 599-6340, Fax -6344 ·info@LTG-INC.net ·www.LTG-INC.net
Former editions are invalid ·Subject to technical modifications page 14 of 30
Installation, operating and maintenance instructions
Active chilled beams HDF-600, ceiling installation
Continuation 4.3 Caloric output data
Cooling/heating capacity with different water
flow rates for 2-pipe heat exchanger
Water flow rate [gpm]
60
70
80
90
100
110
120
0.25 0.5 0.75 1
Cooling/heating cap. in % of nom.
cap.
Capacity with different water flow rates for 4-pipe heat exchanger
Cooling capacity Heating capacity
60
70
80
90
100
110
120
Cooling capacity in % of nominal cap.
Water flow rate [gpm]
Heating capacity in % of nominal cap.
Water flow rate [gpm]
0.25 0.5 0.75 1
60
70
80
90
100
110
120
0.25 0.5 0.75 1
Water-side pressure loss for 2-pipe heat exchanger / 4-pipe heat exchanger
1.0
3.0
5.0
Water flow rate [gpm]
Cooling
Heating
0.25 0.5 0.75 1
Water-side pressure loss [ft
H2O]
2.0
4.0
0
1.0
3.0
5.0
Water flow rate [gpm]
0.25 0.5 0.75 1
Water-side pressure loss [ft
H2O]
2.0
4.0
0

ELTG Incorporated ·PO Box 2889 ·Spartanburg, S.C. 29304, USA
Chilled beams HDF-us-OM (01/17)
Phone 864 599-6340, Fax -6344 ·info@LTG-INC.net ·www.LTG-INC.net
Former editions are invalid ·Subject to technical modifications page 15 of 30
Installation, operating and maintenance instructions
Active chilled beams HDF-600, ceiling installation
4.4 Acoustic Data
Acoustic data have been determined in a reverberation
chamber in the LTG test lab.
The technical data sheet contains the A weighted sound
pressure levels LA18 for different primary air flow rates/
static pressures at primary air socket.
Sound pressure levels apply to a room absorption surface
of 194 ft2Sabinewhich equals a room absorption of about
6 dB(A). Thus, sound power levels may easily be calcu
lated.
LWA =L
A18 +6,5dB(A)
The data given apply to one unit, i.e. one room axle. If more
than one unit is installed in the same room, the sound
pressure level will rise accordingly.
Increase in sound level with several sound sources of the
same type:
Number of sound sources of
thesametype 1 2 3 4
Sound level increase [dB] 0 3 5 6
Measuring accuracy is ± 10%.
4.5 Hydraulic Data
Heat exchangers are approved for an operating pressure
of 145 psi max. (test pressure 232 psi). Pressures exceed
ing 145 psi require the express permission of LTG.
Water-side pressure losses have been measured directly
at the heat exchanger connections. Further resistances
will have to be added.
Measuring accuracy is 10%.
4.6 Weight (standard units without water)
Type Size Weight [lb]
HDF 300 1200 approx. 37
HDF 300 1500 approx. 48
HDF 300 1800 approx. 60
HDF 300 2100 approx. 71
HDF 600 1200 approx. 75
Installation in different ceiling systems
5. Installation
5.1 Notes
Shipping of Unit
If not required otherwise, units are shipped in wrapping
boxes which may also serve as a protection during instal
lation. Boxes must be stored in an upright position as indi
cated by the arrow on the box. Thepackaging is disposable
and not to be returned to LTG.
Timing of Installation
Installation of the units should not be performed unless
the prefabricated floor has been finished, the window sill
installed, the intermediate ceiling and any other dust pro
ducing work completed.
Handling of Units
Handle units with care during transport and installation.
Avoid dropping to the ground.
5.2 Suspension
For reasons of stability and rigidity, never
use bolts with a property class inferior to
the one indicated. Fixing elements are not
included in the delivery.
Do not use other than the holes provided forto fasten fix
ing elements.
Do not use the air conditioning units as load-bearingele
ments for other components and avoid any other load
ing.
Fixing elements must be chosen in a way to ensure that
any sound transmission is avoided.
Parts and tools.
When working overhead.
23.3 / 24.3 23.9/24.3/24.5 23.2
Metal ceilings
(T-Bar-System)
Grid ceilings (install.
on joint edge to edge)
Plasterboard ceilings
(install. overlapped)

ELTG Incorporated ·PO Box 2889 ·Spartanburg, S.C. 29304, USA
Chilled beams HDF-us-OM (01/17)
Phone 864 599-6340, Fax -6344 ·info@LTG-INC.net ·www.LTG-INC.net
Former editions are invalid ·Subject to technical modifications page 16 of 30
Installation, operating and maintenance instructions
Active chilled beams HDF-600, ceiling installation
Continuation 5.2 Suspension
A
3/8 " all-thread rod
Detail A
0.43
0.32
Isometric view
A
open-end wrench
box-end wrench
min. 0.8
not correct
Detail A Detail A
Detail A
Isometric view
3/8 " all-thread rod

ELTG Incorporated ·PO Box 2889 ·Spartanburg, S.C. 29304, USA
Chilled beams HDF-us-OM (01/17)
Phone 864 599-6340, Fax -6344 ·info@LTG-INC.net ·www.LTG-INC.net
Former editions are invalid ·Subject to technical modifications page 17 of 30
Installation, operating and maintenance instructions
Active chilled beams HDF-600, ceiling installation
Continuation 5.2 Suspension, 4-way diffusion
It is necessary to always have units handled by at least
two persons.
Before installing the diffuser grille check the clips for
damage (being bent or crooked). If damage is visible they
have to be replaced. Then center the clips in the openings.
The diffuser grille should not be tilted during installation
or removal. It needs to be parallel to the chilled beam
when moved upwards or downwards.
The clips need to engage with an audible clicking sound.
Example line assembly
23.3
2xL

ELTG Incorporated ·PO Box 2889 ·Spartanburg, S.C. 29304, USA
Chilled beams HDF-us-OM (01/17)
Phone 864 599-6340, Fax -6344 ·info@LTG-INC.net ·www.LTG-INC.net
Former editions are invalid ·Subject to technical modifications page 18 of 30
Installation, operating and maintenance instructions
Active chilled beams HDF-600, ceiling installation
5.3 Water Connections
Remove the heat exchanger plugs prior to
water connection!
Units are provided with heat exchangers with copper
tubes and aluminum blades for4-pipeoperation with sep
arate heating and cooling circuits or for 2-pipe operation.
The heat exchangers have been approved for a maximum
operating pressure of 145 psi (other pressures on re
quest).
Depending on the unit type, water connections are sup
plied in the following versions:
1. copper fitting with 0.47 in outer diameter.
This connection is only suitable for flexible
connections with quick coupling.
Connections must be strainless.
Connecting lines must be able to expand.
Attention: Prior to allowing water to enter
the unit the flexible water connection
hoses will have to be checked for proper and leakproof
connection. Even though hoses to the heat exchanger
are preinstalled, connections might have loosened dur
ing transport or installation of the unit on site.
You may use off-the-shelf control valves and shut-off
valves.
When tightening the fittings, avoid damaging the heat ex
changer pipes through bending or twisting. Pipe fittings
must always be flush. Tighten acc. to industry standards.
In order to adjust the water volume specified in the selec
tion data, a regulating device or restricting olive will be re
quired. If identical units with exactly the same water vol
ume and pressure losses are used, an individual
regulating device for each unit is unnecessary. In this
case, one regulating device for the entire line may be suffi
cient. Otherwise, a regulating device will be required for
each heat exchanger.
If removal of a heat exchanger without draining the entire
system is a requirement, two or four isolation valves will
have to be provided for each unit. You may use off-the-
shelf shut-off valves.
The unit fitting will only be provided with an integrated
vent if specifically asked for. The water speed inside the
heat exchanger is usually sufficient to carry along air bub
bles. A ventilation per line is therefore appropriate. In a
case of emergency, the line may be ventilated by slightly
loosening the standard fitting of the unit.
Included in the unit price and also in general provided with
the unit - (unless special fittings such as transitions,
straight-way or angle valves or hose connections are or
dered) is a complete compression fitting for unit-side wa
ter connection, appropriate to take copper pipes with a
1/2 in outer diameter, suitable for connecting hoses. The
union nut is fixed to the heat exchanger pipe's flared end,
while olive and banjo bolt will be delivered in packs of 2 or
4 - according to type of unit - in a bag attached to the unit.
Due to possible condensation, the connections to the heat
exchanger for cooling should be insulated, e.g. using Ar
maflex insulation.
A
Isometric view
Heating
Cooling
Ø0.47
Detail A

ELTG Incorporated ·PO Box 2889 ·Spartanburg, S.C. 29304, USA
Chilled beams HDF-us-OM (01/17)
Phone 864 599-6340, Fax -6344 ·info@LTG-INC.net ·www.LTG-INC.net
Former editions are invalid ·Subject to technical modifications page 19 of 30
Installation, operating and maintenance instructions
Active chilled beams HDF-600, ceiling installation
Continuation 5.3 Water Connections
The water connection side is to be specified when ordering
the unit. Some units offer a possibility to still change the
side during installation by removing 4 bolts.
Execute the heat exchanger connection as follows:
- Vertical heat exchangers:
water supply below, water return above
- Horizontal heat exchangers:
unit's front side: water supply,
unit's back side: water return
Example for water connection using flexible hose (quick coupling connection to heat exchangers)
Hose without insulation. For insulated hoses, dimensions will change accordingly
(10 mm Armaflex insulation).
Hose for connection to heat exchanger with smooth tube end diameter 0.47 in,
connection types: quick coupling, quick coupling with venting
Different hose connections, thread diameter acc. to customer requirements or standard 1/2”
min. 5.9
min.1.4
min.1.4
min.R20
approx. 3.9
approx. 7.9
min. 5.9
min. 1.4
min. 1.4
min. R20
approx. 3.9
approx. 7.9
Ø 0.67 DN 0.47
Ø 0.67 DN 0.47
Example for water connection using transition - LTG description VSG 10/ 2 EH (venting),
straight-way valve and flexible hose
min. 1.4
min. 1.4
min. R20
Hose without insulation. For insulated hoses, dimensions will change accordingly.
Hose for connection to angle or straight-way valve,
connection type: AGK, external thread, tapered 1/2”
Different hose connections, thread diameter acc. to customer requirements or standard 1/2”
Ø0.59 DN 0.4

ELTG Incorporated ·PO Box 2889 ·Spartanburg, S.C. 29304, USA
Chilled beams HDF-us-OM (01/17)
Phone 864 599-6340, Fax -6344 ·info@LTG-INC.net ·www.LTG-INC.net
Former editions are invalid ·Subject to technical modifications page 20 of 30
Installation, operating and maintenance instructions
Active chilled beams HDF-600, ceiling installation
5.3.1 Instructions for installation of water connections using flexible hoses
Warranty will only apply if the following
instructions are observed and if installa
tion is performed in compliance with DIN-
EN regulations.
In particular, corrosive, electrochemical,
and bacteriological charges are to be ex
cluded taking appropriate preventive
measures.
Pressure and exposition to heat may result in slight
elongation of the hose.
Therefore, newly placed hoses must consider such
potential elongation.
Do not fall below the admissible bending
radius Rmin (chart), neither during transport, nor dur
ing installation or when installed.
If it should turn out impossibleto keep theadmissible
bending radius, choose a different installation type.
For minimum length see chart below.
If the hose is being placed by bending it, check
whether there is sufficient hose length to allow for an
open bow in order to avoid
kinking and destruction of the hose at the connecting
points.
Absolutely avoid distorting or kinking the flexible
connection.
Do not subject the hose to any tensile or pressure
loads applied from outside, neither during installa
tion nor operation.
Do not retighten rigid connections (outer thread) af
ter fixing the second connection since this might re
sult in distortion of or damage to the hose.
In general, tightness of the connection (hose/connec
tor) is the responsibility of the technician performing
the installation. Do not over-tighten.
Any sealing material included in the delivery is to be
verified by the technician for its
suitability since the hose manufacturer has no infor
mation about the material or geometry of the connec
tions.
correct incorrect
Table of contents
Other LTG Chiller manuals
Popular Chiller manuals by other brands
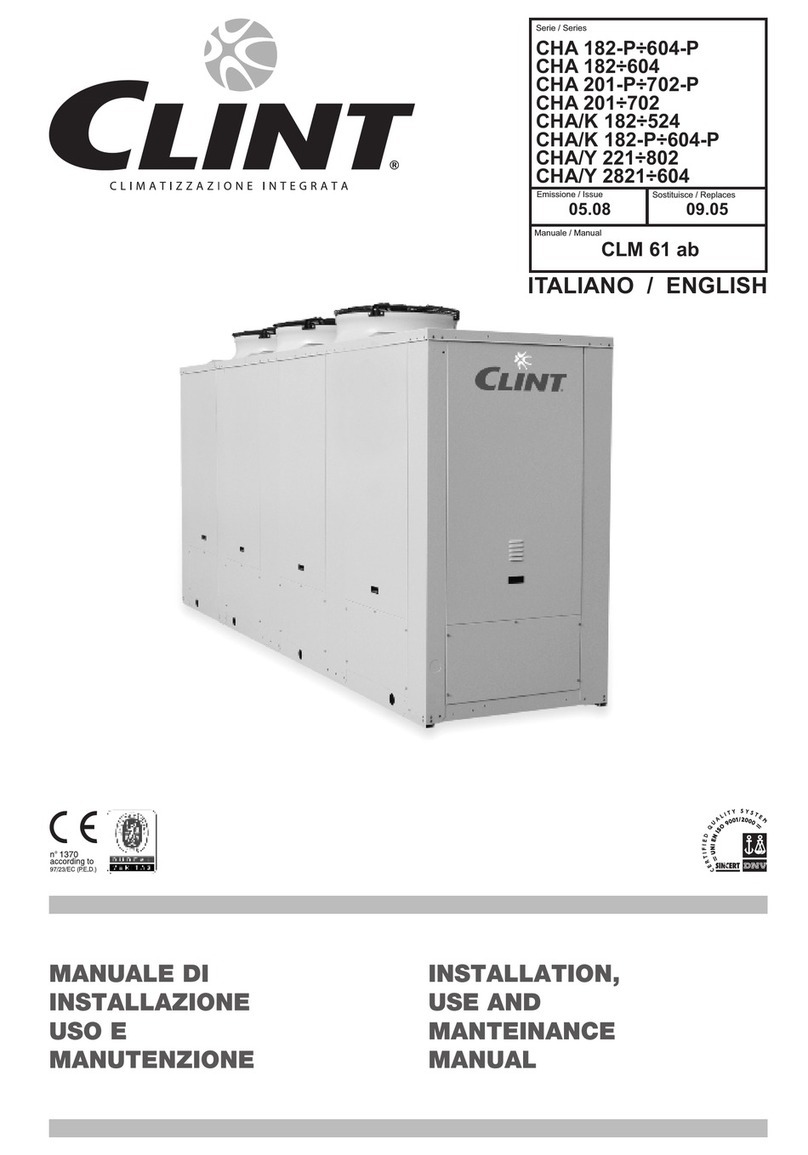
Clint
Clint CHA 182-P-604-P INSTALLATION, USE AND MANTEINANCE MANUAL
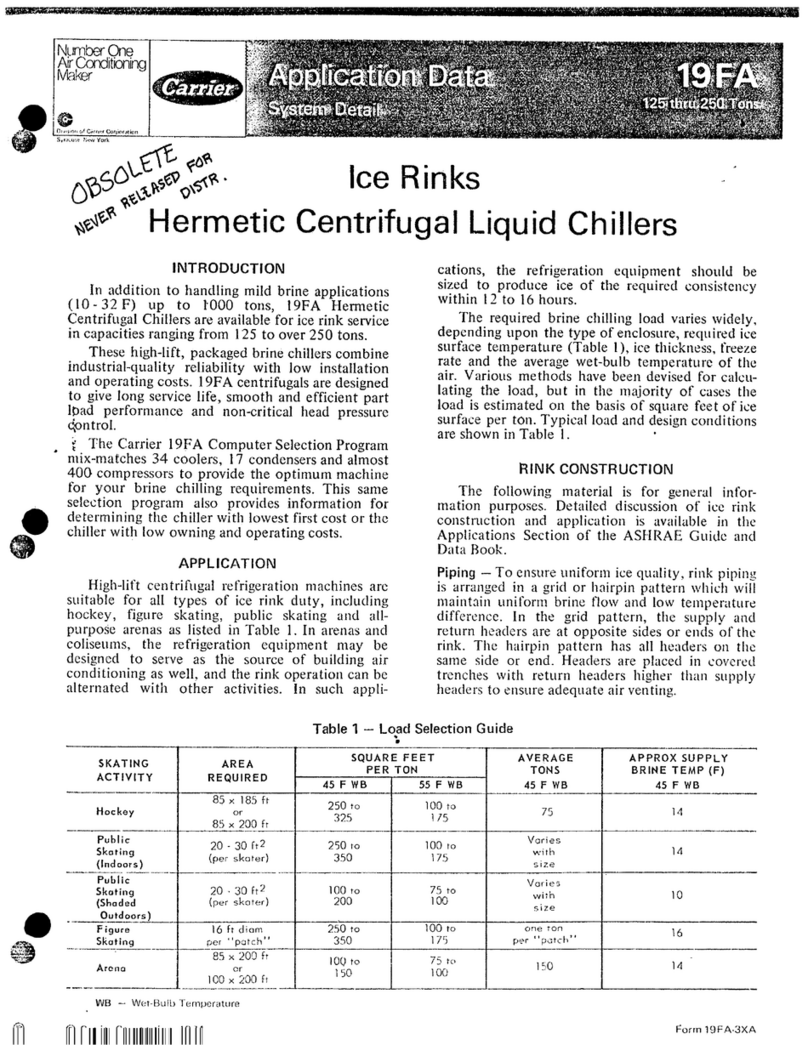
Carrier
Carrier 19FA Series Application data

Elkay
Elkay HRC4-191B installation instructions

York
York YCAL0080SC Installation operation & maintenance
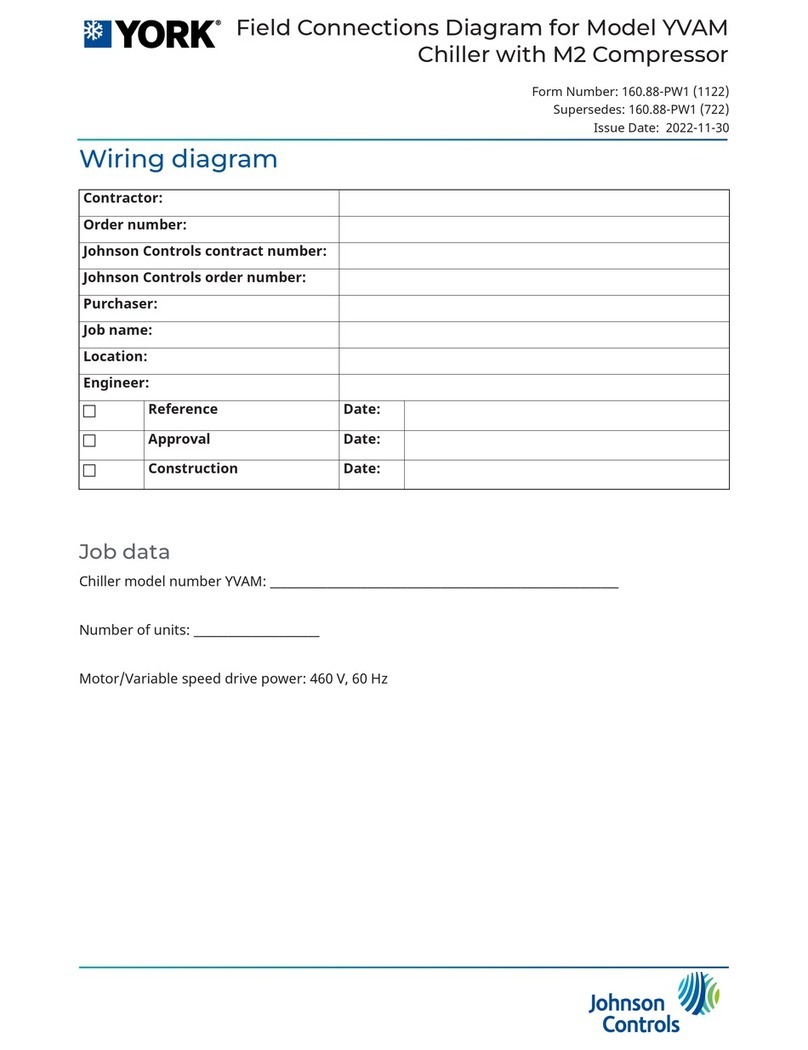
Johnson Controls
Johnson Controls YVAM 350 Wiring diagram

Daikin
Daikin RKJ09NV1S Service manual