Lumio Touch Screen User manual

Lumio Touch Screen
Manual Assembly
User Guide
Version A4 3/2013
DO070201003

6355 Topanga Canyon Blvd. Suite #335, Woodland Hills CA, 91367 USA. Tel: +1 877 97 LUMIO Fax: +1 818 883 0858. Website: www.lumio.com
DO070201003
6355 Topanga Canyon Blvd. Suite #335, Woodland Hills CA, 91367 USA. Tel: +1 877 97 LUMIO Fax: +1 818 883 0858. Website: www.lumio.com
Document Revision History
Release
Date
July 2011
Revision
History
AO
A1
September 2012
•Modified glass requirements
•Added Master Bond epoxy pictures
A2
December 2012
Added FFC – sensor connectivity instructions
A3
January 2013
General Revision including:
•Work Flow
•Tools and Materials
•LED Wiring
•Flat cable connection
•Added Distribution Ready Procedure
•OQC
•Removed Glassless Assembly
•
General editing
A4
March 2013
•
General Editing
•Edited Workflow
•Added procedure for attaching sensors to panels
•
Added Index, Table of Figures, Table of Tables
This Lumio Touch Screen Manual Assembly User Guide is designed for use by qualified technicians at
Lumio authorized customers. Users must read and familiarize themselves entire manual before manually
assembling Lumio Touch Screens.
Documentation Copyright
Information herein is proprietary information and a trade secret of Lumio Inc.
© Copyright 2011 by Lumio Inc. All rights reserved.
Disclaimer
The information in this manual has been carefully examined and is believed to be reliable. Lumio Inc. shall
not be liable for any direct, indirect, incidental, special, exemplary, or consequential damages of any kind,
however incurred, through the use of this product.
Lumio Inc. reserves the right to make changes to any of its products in order to improve reliability, design
and performance. The text and drawings herein are for the purposes of illustration and reference only; the
text, drawings and specifications on which they are based are subject to change without notice.
Warning
Use only Lumio approved parts and materials. Use of non-Lumio approved materials may impair the
assembly and operation of Touch Screens.
Technical Assistance
For technical questions and troubleshooting assistance:
Contact the Lumio office closest to you.
Visit us at our website: www.lumio.com.
E-mails may be sent to: support@lumio.com.
Contact
Lumio Inc
6355 Topanga Canyon Blvd. #335, Woodland Hills, CA, USA 91367
Ph: +1 818 715 9866, Fax: +1 818 715 9853, http://www.lumio.com
Email: suppo[email protected]

6355 Topanga Canyon Blvd. Suite #335, Woodland Hills CA, 91367 USA. Tel: +1 877 97 LUMIO Fax: +1 818 883 0858. Website: www.lumio.com
6355 Topanga Canyon Blvd. Suite #335, Woodland Hills CA, 91367 USA. Tel: +1 877 97 LUMIO Fax: +1 818 883 0858. Website: www.lumio.com
DO070201003
6355 Topanga Canyon Blvd. Suite #335, Woodland Hills CA, 91367 USA. Tel: +1 877 97 LUMIO Fax: +1 818 883 0858. Website: www.lumio.com
Contents
Chapter 1 Introduction...................................................................................................................................2
1.1 Safety Warnings and Precautions................................................................................................................... 2
1.2 Reference Guides............................................................................................................................................ 2
Chapter 2 Active Barrier Overview..................................................................................................................3
Chapter 3 Work Flow .....................................................................................................................................5
Chapter 4 IQC: Incoming Quality Control ........................................................................................................6
4.1 Incoming Components Inspection.................................................................................................................. 6
4.2 Incoming Glass Panel Inspection .................................................................................................................... 7
4.3 General ........................................................................................................................................................... 7
4.4 Cleaning .......................................................................................................................................................... 7
4.5 Inspection Requirements................................................................................................................................ 7
4.6 Mechanical Requirements.............................................................................................................................. 8
4.6.1 Types of Glass .........................................................................................................................................8
4.6.2 Circular and Linear Defect Criteria .........................................................................................................8
4.6.3 Acceptance / Rejection Criteria for Glass Defects..................................................................................9
4.6.4 Glass Crack Criteria.................................................................................................................................9
4.6.5 Glass Surface Flatness ......................................................................................................................... 10
4.6.6 Glass Flatness Test............................................................................................................................... 10
4.6.7 Glass Flatness Test Components ......................................................................................................... 11
4.6.8 Glass Flatness Test Process.................................................................................................................. 11
4.6.9 Placing Components on Glass.............................................................................................................. 11
Chapter 5 Pre-Assembly: Assembling the Active Barrier ................................................................................12
5.1 Requirements ............................................................................................................................................... 12
5.2 Assembling the Active Barrier for Dual Sensor Systems .............................................................................. 12
5.3 Assembling the Active Barrier for Quad Sensor Systems............................................................................. 17
Chapter 6 Attaching the Active Barrier to the Touch Screen Glass Panel ........................................................18
Chapter 7 LED PCB Wiring.............................................................................................................................21
7.1 LED PCB wiring for Dual Sensor Systems...................................................................................................... 21
7.2 LED Wiring for Quad Sensor systems ........................................................................................................... 24
7.3 LED Wiring for Quad Sensor Systems without an Extension PCB Controller ............................................... 24
7.4 LED Wiring for Quad Sensor Systems with an Extension PCB Controller..................................................... 25
Chapter 8 Attaching Sensors to the Touch Screen Glass Panel .......................................................................26
8.1 Attaching Sensors to the Glass Panel with Dymax 3069 Epoxy.................................................................... 27
8.2 Attaching Sensors to the Glass Panel with DP 105 Epoxy ............................................................................ 31
Chapter 9 Connecting the Sensors to the PCB Controller ...............................................................................34
9.1 Connecting Jenoptic Sensors ........................................................................................................................ 34
9.2 Connecting 2 KC Sensors .............................................................................................................................. 36
9.2.1 Direct 2 KC Sensor - PCB Controller Connection................................................................................. 37
9.2.2 Connecting a 2 KC Sensor to a PCB Controller with a Flat Cable Adaptor ......................................... 38
Chapter 10 Connecting the PCB Controller to the Extension PCB Controller ...................................................40
Chapter 11 Distribution Ready Procedure .....................................................................................................42
Chapter 12 OQC Outgoing Quality Control ....................................................................................................42
12.1 Glass Inspection................................................................................................................................... 42
12.2 Cleaning ............................................................................................................................................... 42
12.3 Mechanical Criteria.............................................................................................................................. 43
12.4 Glass Crack Criteria.............................................................................................................................. 44
12.5 Components Inspection....................................................................................................................... 44
12.6 Touch Screen Dimension Verification ................................................................................................. 45
Chapter 13 Appendix A: Sensor Adhesion Requirements ...............................................................................46

1
Introduction DO070201003
6355 Topanga Canyon Blvd. Suite #335, Woodland Hills CA, 91367 USA. Tel: +1 877 97 LUMIO Fax: +1 818 883 0858. Website: www.lumio.com
13.1 Sensor Adhesion Requirements .......................................................................................................... 46
13.2 Primers................................................................................................................................................. 46
13.3 Types of Adhesives .............................................................................................................................. 47
13.4 Adhesive Curing Requirements ........................................................................................................... 48
13.4.1 Glue Curing Tool Power Density.......................................................................................................... 48
13.4.2 Glue Curing Time ................................................................................................................................. 48
13.4.3 Lumio UV Glue Curing Tool.................................................................................................................. 48
Chapter 14 Appendix B: Installing Crystal Touch Manager .............................................................................49
14.1 Installing Crystal Touch Manager ........................................................................................................ 49
14.2 Resolving Permission Issues for Vista and Win 7 OS ........................................................................... 49
Chapter 15 Appendix C: Creating a 1 mm gap between the Sensor and the Active Barrier ..............................51
15.1 Overview.............................................................................................................................................. 51
15.2 Tools .................................................................................................................................................... 51
15.3 Materials.............................................................................................................................................. 51
15.4 Creating a 1 mm gap between a Sensor and the Active Barrier in a Quad Sensor system................. 52
15.5 Creating a 1 mm gap between a Sensor and the Active Barrier in a Dual Sensor system .................. 55
15.6 Testing Sensor Signals and Boundaries ............................................................................................... 55
15.7 Calibration ........................................................................................................................................... 55
Chapter 16 Appendix D: Cleaning Materials ..................................................................................................56
Chapter 17 Appendix E Tool and Materials ...................................................................................................56
17.1 Tools .................................................................................................................................................... 56
17.2 Materials.............................................................................................................................................. 57
17.3 Kit Contents ......................................................................................................................................... 57
Chapter 18 Table of Figures ..........................................................................................................................60
Chapter 19 Table of Tables ...........................................................................................................................62

2
Introduction DO070201003
6355 Topanga Canyon Blvd. Suite #335, Woodland Hills CA, 91367 USA. Tel: +1 877 97 LUMIO Fax: +1 818 883 0858. Website: www.lumio.com
Chapter 1 Introduction
This Lumio Touch Screen Manual Assembly User Guide provides information needed to familiarize you with the
components, work flow and processes for manual assembly of Touch Screens on glass panels and for glassless
frames. This document is designated for technicians responsible for assembling Touch Screens.
1.1 Safety Warnings and Precautions
This section contains important safety information. Please familiarize yourself with all warnings and precautions
before manually assembling Touch Screens.
•Assemble Touch Screens in a clean, dust free environment
•To avoid the risk of electric shock, all equipment must be connected to a power supply that is properly
grounded
•The Lumio UV curing machine emits very strong UV radiation. UV radiation can harm your eyes. To
prevent inadequate exposure of UV radiation, wear UV protective glasses, and do not look directly at
the LEDs
•Handle the glass panels with care, to prevent breaking or scratching
•Handle components such as sensors, PCB Controllers and LED PCB wire with care
•Do not subject Touch Screen panels to unnecessary shock or stress
•Do not lift a Touch Screen panel by the Active Barrier or by its flat cables
•Large Touch Screen panels are heavy, and should be carried by at least two people
•Do not stack Touch Screen panels on top of each other
•Do not place heavy objects on the Touch Screen panels
•Ensure Touch Screen storage temperature as specified in the Lumio Design guide for Integrators
•Wear gloves when handling Touch Screens to prevent unnecessary fingerprints on the panel
•Clean Touch Screens with a dry cloth or with a soft cloth soaked in neutral detergent (after wringing dry)
•Do not use any organic solvents, acids or alkali solutions to clean glass Touch Screens (for further
cleaning instructions, see Cleaning on page 7)
•Do not perform any electrical, mechanical or other changes to Touch Screen and their components
without prior written Lumio authorization
•During assembly, disconnect the Touch Screen from the electrical supply
•Only qualified assembly personnel are authorized to assemble Touch Screens
1.2 Reference Guides
•Lumio Integrator guide
•Lumio Crystal Touch Manager User guide
•Lumio Production Wizard User guide

3
Active Barrier Overview DO070201003
6355 Topanga Canyon Blvd. Suite #335, Woodland Hills CA, 91367 USA. Tel: +1 877 97 LUMIO Fax: +1 818 883 0858. Website: www.lumio.com
Chapter 2 Active Barrier Overview
The Lumio Touch Screen is a pre-calibrated plug and play optical Touch Screen that is integrated into various
environments according to customer needs. Successful integration is dependent on the implementation of the
requirements specified in this guide.
The following diagrams display Dual and Quad Sensor systems.
Figure 1 Dual Sensor System
Figure 2 Quad Sensor System

4
Active Barrier Overview DO070201003
6355 Topanga Canyon Blvd. Suite #335, Woodland Hills CA, 91367 USA. Tel: +1 877 97 LUMIO Fax: +1 818 883 0858. Website: www.lumio.com
The following table displays the Touch Screen’s system components.
Table 1: System Components
Glass The glass is the substrate or surface for all optical components
Sensor Module Sensor Module: The Sensor is a module featuring high accuracy, high resolution and high
sensitivity. Each system includes two / four optical Sensors are placed in each corner of the panel
(In Dual Sensor systems, the sensors are placed on the top corners of the panel). The sensors are
assembled on the glass
IR Rod The Rod is an optical element that distributes the light uniformly. The Rod is inserted into the Rod
Holder
Reflectors A white plastic strip affixed to the back of the IR Rod, adding light to the system
Rod Holder The Rod Holder encases the Rod and protects the Rod from humidity, dust and particles. The Rod
Holder is assembled on the glass
Decorative Rod A rod placed on the top of the Active Barrier system in a Dual Sensor system, used for decorative
purposes only
Led PCB Wire The LED PCB Wire is a cable upon which the IR LEDs are affixed and which is connected to the PCB
Controller
Extension LED Wire Connects the LED PCB Wire to the PCB Controller. This wire enables the PCB Controller to be
placed in the system according to requirements
PCB Controller The board controlling and interfacing with all system components
FFC (Flat) Cables A flexible flat cable connecting the sensors to the PCB Controller, transferring signal data from the
Active Barrier to the PCB Controller
USB Cable A communications / power supply cable
Extension PCB
Controller
A controller enabling high power support for large systems

5
Work Flow DO070201003
6355 Topanga Canyon Blvd. Suite #335, Woodland Hills CA, 91367 USA. Tel: +1 877 97 LUMIO Fax: +1 818 883 0858. Website: www.lumio.com
Chapter 3 Work Flow
The flowchart below displays the work flow for manual assembly of Touch Screens.
Figure 3: Workflow
IQC: Incoming
Quality Control
Pre-Assembly –
Assemble the Active
Barrier
Attach the Active
Barrier to the Glass
Panel
LED Wiring
Attach Sensors to the
Glass Panel
Connect the Sensors
to the PCB Controller
Distribution Ready
Procedure
Production Wizard
application
OQC: Outgoing
Quality Control
For Quad Sensor
Systems: Connect the
PCB Controller to the
Extension PCB
Controller

6
IQC: Incoming Quality Control DO070201003
6355 Topanga Canyon Blvd. Suite #335, Woodland Hills CA, 91367 USA. Tel: +1 877 97 LUMIO Fax: +1 818 883 0858. Website: www.lumio.com
Chapter 4 IQC: Incoming Quality Control
Comply with the following Input Quality Control (IQC) inspection and acceptance requirements prior to
assembling Touch Screens.
•Incoming Components Inspection below
•Incoming Glass Panel Inspection on page 7
4.1 Incoming Components Inspection
Compare the components received from Lumio to the Crystal Touch Kit / Panel Content packing list supplied by
Lumio with the shipping documents. The packing list includes the name and amount of the component, the
component part number, and additional information such as the Active Barrier dimensions and so on.
The following table is an example of a packing list.
Note: Each packing list is different and suits a particular order – the following packing list is only an example.
Table 2: Lumio Packing List

7
IQC: Incoming Quality Control DO070201003
6355 Topanga Canyon Blvd. Suite #335, Woodland Hills CA, 91367 USA. Tel: +1 877 97 LUMIO Fax: +1 818 883 0858. Website: www.lumio.com
4.2 Incoming Glass Panel Inspection
The incoming glass inspection includes the following sections:
•General below
•Cleaning below
•Inspection Requirements below
•Mechanical Requirements on page 8
4.3 General
The following general Touch Panel glass requirements apply:
•Prior to inspection, clean the glass and ensure that finger prints and other foreign materials are
removed
•If protective film covers the glass, it should be removed before inspection, and returned afterwards
4.4 Cleaning
The following Touch Panel glass cleaning requirements apply:
•Cleaning should be performed before and after each activity during the integrating process
•Clean the glass Touch Panel with clean cloth and windows’ dedicated liquid
•Use alcohol based solvents to dissolve oily contaminations and marks
•Do not use acid based solvents such as WD-40 to clean the glass
Note: For further cleaning requirements, see Appendix D: Cleaning Materials on page 56
4.5 Inspection Requirements
Ensure that the following conditions apply prior to and during the Touch Panel inspection. Only Touch Panel
anomalies detected under the above inspection conditions constitute grounds for rejecting the Touch Panel.
Table 3: Touch Panel Inspection Conditions
Inspection Inspection Condition / Result
Inspection area Active / View area
Inspector's viewing angle 90 degrees
Viewing distance while inspecting the Touch
Panel
•≤52 inch Touch Screen: 40cm - 50 cm;
•>52 inch Touch Screen: 70cm – 90cm
Ambient illumination 800 - 1200 Lux (nominal 1000 Lux)
Background Black
Ambient temperature 25° C ±5° C
Inspection time For Touch Panels up to 24”: 10 ÷ 20 sec
For Touch Panels between 26” - 52”: 15 ÷ 25 sec
For Touch Panel sizes larger than 52”: 20 ÷ 30 sec
Note: Only Touch Screen anomalies detected during inspection under the above conditions constitute grounds for
rejecting the Touch Screen.

8
IQC: Incoming Quality Control DO070201003
6355 Topanga Canyon Blvd. Suite #335, Woodland Hills CA, 91367 USA. Tel: +1 877 97 LUMIO Fax: +1 818 883 0858. Website: www.lumio.com
4.6 Mechanical Requirements
This section includes:
•Types of Glass below
•Circular and Linear Defect Criteria below
•Acceptance / Rejection Criteria for Glass Defects on page 9
•Glass Crack Criteria on page 9
•Glass Surface Flatness on page 10
4.6.1 Types of Glass
The following table describes the types of glass available for Touch Screens, and the requirements for each type.
Verify that the glass panel supplied meets the requirements.
Table 4 Types of Glass
Type of Glass Requirements
Floated Glass Soda Lime complies with ASTM C1036/DIN EN 572 art 1, Part 2 and Part 9
Strengthened Glass Tempered Glass complies with EN12150 / DIN1249D / ASTMC1048 / GB15763.2
Chemically Strengthened glass complies with ASTMC1422
Tempered & Chemically Strengthened glass complies with UL 60950-1 test
method
Safety Laminated Glass complies with BS EN 14449 : 2005
Safety laminated glass complies with EN12600 Class 2 Type B2 test method
Single sided AR 2 Layer (@ wavelength
400mm to 700mm)
Glass Transmittance >93%
Glass Reflectance <5.5%
Double sided AR 2 Layer (@ wavelength
400mm to 700mm)
Glass Transmittance >96%
Glass Reflectance <2.0%
Single sided AR 4 Layer (@ wavelength
400mm to 700mm)
Glass Transmittance >94%
Glass Reflectance <5.0%
Double sided AR 4 Layer (@ wavelength
400mm to 700mm)
Glass Transmittance >98%
Glass Reflectance <1.0%
4.6.2 Circular and Linear Defect Criteria
The following table defines circular and linear defect limitations for Touch Screen glass panel acceptance.
Table 5 Touch Screen Glass Panel Circular and Linear Defect Limitations
Type of Glass Defect Description
Circular Defect
Linear Defect

9
IQC: Incoming Quality Control DO070201003
6355 Topanga Canyon Blvd. Suite #335, Woodland Hills CA, 91367 USA. Tel: +1 877 97 LUMIO Fax: +1 818 883 0858. Website: www.lumio.com
4.6.3 Acceptance / Rejection Criteria for Glass Defects
The following table defines mechanical criteria for Touch Screen acceptance.
Table Key
D: Panel dimension.
N: Number of defects permitted.
L: Panel length. The Touch Screen panel size is measured in inches.
Table 6 Touch Screen Glass Panel Mechanical Acceptance / Rejection Criteria
4.6.4 Glass Crack Criteria
The following table defines Glass Crack criteria for Touch Screen acceptance.
Table 7 Touch Screen Glass Crack Criteria
Defect Style Defect Definition Acceptance Criteria Rejection Criteria Notes
Corner Fragments
X≦2.5mm
Y
≦
2.5mm
Z <
glass thickness
X>2.5mm
Y
>
2.5mm
Z =
glass thickness
Allowed only
outside the active
area
Defects and Acceptance / Rejection Criteria*
Defect Style Panel
≤
24” 24”< Panel <47” 47”< Panel
≥
70” Panel >70”
Opaque / Bubble Accept: 0.3 < D
≦
0.8
N
≦
3
0.3 < D
≦
1.0
N
≦
4
0.3 < D
≦
1.2
N
≦
5
0.3 < D
≦
1.4
N
≦
6
Reject: D>0.8
N>3
D>1.0
N>4
D>1.2
N>5
D>1.4
N>6
Scratch
Translucent
(Hair Line)
Accept: 0.03 < W
≦
0.07
L
≦
20
N
≦
4
0.03 < W
≦
0.07
L
≦
25
N
≦
5
0.03 < W
≦
0.07
L
≦
30
N
≦
6
0.03 < W
≦
0.07
L
≦
35
N
≦
7
Reject: W > 0.07
L>20
N>4
W > 0.07
L>25
N>5
W > 0.07
L>30
N>6
W > 0.07
L>35
N>7
Scratch
Accept: 0.05 < W
≦
0.15
L
≦
6
N
≦
3
0.05 < W
≦
0.15
L
≦
8
N
≦
4
0.05 < W
≦
0.15
L
≦
10
N
≦
5
0.05 < W
≦
0.15
L
≦
13
N
≦
6
Reject: W > 0.15
L>6
N>3
W > 0.15
L>8
N>4
W > 0.15
L>10
N>5
W > 0.15
L>13
N>6
Minimum Distance
Between Defects
Accept: ≥10 ≥10 ≥10 ≥10
Reject: <10 <10 <10 <10
Maximum Allowable
No. of Defects
Accept: N
≦
3 N
≦
4 N
≦
5 N
≦
7
Reject: N>3 N>4 N>5 N>7

10
IQC: Incoming Quality Control DO070201003
6355 Topanga Canyon Blvd. Suite #335, Woodland Hills CA, 91367 USA. Tel: +1 877 97 LUMIO Fax: +1 818 883 0858. Website: www.lumio.com
Defect Style Defect Definition Acceptance Criteria Rejection Criteria Notes
Side Fragments
X≦2.5mm
Y
≦
2.5mm
Z < glass thickness
X>2.5mm
Y
>
2.5mm
Z = glass thickness
Allowed only
outside the active
area
Progressive Crack
N=0 N>0 Not Allowed
4.6.5 Glass Surface Flatness
Overview
The Sensors and LED PCB’s are assembled on the Touch Screen glass panel. The sensors must detect the LED
PCBs in their field of view. Therefore, glass flatness is essential in order to ensure that the sensors detect the
LED PCB’s, and must be tested prior to Touch Screen assembly.
The following table displays glass flatness requirements for panels.
Table 8 Glass Flatness for Panels
Glass size [inches] Glass Flatness Requirements for System Integration (mm)
Less than 27 1.0 mm
28 to 52
1.5 mm
More than 52 2.0 mm
4.6.6 Glass Flatness Test
The glass flatness test establishes whether the glass meets glass flatness requirements. Assemble the
components specified below, and perform the glass flatness test. The following diagram displays glass flatness
test components.
Figure 3 Glass Flatness Test

11
IQC: Incoming Quality Control DO070201003
6355 Topanga Canyon Blvd. Suite #335, Woodland Hills CA, 91367 USA. Tel: +1 877 97 LUMIO Fax: +1 818 883 0858. Website: www.lumio.com
4.6.7 Glass Flatness Test Components
Prepare the following components for the glass flatness test.
Table 9 Glass Flatness Test Components
Component Description
A standard flat table The table must be as large as the glass / frame / overlay under test
Egg Foam The egg foam absorbs all table tolerances, and prevents the bending and distortion
of the reference surface
Reference Surface The reference surface is a 10mm thick piece of glass with 0.2mm flatness, as large
as the glass / frame / overlay under test. The reference surface can also be a
polished granite block, the size of the glass / frame / overlay under test
Shim spacer Sheets or spacers of increasing thickness – 0.5 mm, 1 mm, 1.5 mm, 2 mm, 3 mm, 4
mm, 5 mm, 6 mm, 7 mm
Glass / Frame / Overlay under test
4.6.8 Glass Flatness Test Process
Assemble the test components as shown in Figure 3 Glass Flatness Test above.
To test glass flatness:
1. Place the glass / frame / overlay under test on top of the reference surface.
2. Insert the thinnest shim spacer between the glass / frame / overlay under test and the reference surface.
3. If the thinnest shim spacer can be inserted, insert the next sized shim spacer.
When a shim spacer cannot be inserted, glass flatness is established, that is the last shim spacer that
was inserted between the glass / frame / overlay under test and the reference surface, represents the
glass flatness.
4. Flip the glass / frame / overlay under test over and place it on top of the reference surface.
5. Repeat steps 2 -3 above in order to determine glass flatness of the flip side.
The glass flatness test passes if the results meet requirements specified in Glass Surface Flatness on page 10.
4.6.9 Placing Components on Glass
If the glass is not flat, but passes the test requirements, place the components (Such as sensors etc.) on the
concave side of the glass.
To place the components on the concave side of the glass:
1. Compare the glass flatness test results for each side of the glass panel (To compare the glass flatness test
results see Glass Flatness Test Process above).
The side of the glass with the best test flatness result is the concave side.
2. Place the components on the concave side of the glass.

12
Pre-Assembly: Assembling the Active Barrier DO070201003
6355 Topanga Canyon Blvd. Suite #335, Woodland Hills CA, 91367 USA. Tel: +1 877 97 LUMIO Fax: +1 818 883 0858. Website: www.lumio.com
Chapter 5 Pre-Assembly: Assembling the
Active Barrier
5.1 Requirements
After inspecting and approving the incoming components, prepare the tools and materials required to assemble
the Touch Screens (See Appendix E Tool and Materials on page 56)
This section includes instructions for assembling the Active Barrier for the following systems:
•Assembling the Active Barrier for Dual Sensor Systems below
•Assembling the Active Barrier for Quad Sensor Systems on page 17
5.2 Assembling the Active Barrier for Dual Sensor Systems
Dual Sensor systems include the following features:
•A Sensor is placed in each corner of the top side of the panel
•There is only one long Rod Holder placed on the bottom side of the panel
•The other long “Rod Holder” is a plastic bar used for decorative purposes only, which is placed on the top of
the panel
•IR Rods and LED PCB wiring are not inserted into the Decorative Holder
•A right angle LED (SMT) Corner Housing (hereafter: “Corner Housing”) is placed in each corner of the bottom
side of the panel.
The following diagram describes the Dual Sensor system layout.
Fig 5: Dual Sensor System Layout

13
Pre-Assembly: Assembling the Active Barrier DO070201003
6355 Topanga Canyon Blvd. Suite #335, Woodland Hills CA, 91367 USA. Tel: +1 877 97 LUMIO Fax: +1 818 883 0858. Website: www.lumio.com
The following picture displays the Dual Sensor system components.
Fig 6: Dual Sensor System Components
To assemble the Active Barrier for Dual Sensor Touch Screen systems:
1. Insert the IR Rods into the Rod Holders.
Note:
•IR Rod dimensions are supplied in the Crystal Touch Kit / Panel Content packing list
•The short IR Rods are inserted into the Rod Holders adjacent to the sensors and corners of the Active
Barrier
•The short IR Rod adjacent to the sensor has a white painted end. The painted end faces the sensor
EXAMPLE: The following picture displays a cross section of a Rod Holder with IR Rods. Note that the short IR
Rods are placed at the ends of the Rod Holder.
Figure 4 Rod Holder Cross Section
a. Insert a side IR Rod into the right angle LED (SMT) Corner Housing (hereafter: “Corner Housing”).
Verify that the IR Rod is fully inserted into the Corner Housing, and that the flat side with the
painted white line faces the outer side of the Corner Housing.
The following pictures display the IR Rod inserted into the Corner Housing.
Figure 5 Side Rod - Corner Housing Insertion

14
Pre-Assembly: Assembling the Active Barrier DO070201003
6355 Topanga Canyon Blvd. Suite #335, Woodland Hills CA, 91367 USA. Tel: +1 877 97 LUMIO Fax: +1 818 883 0858. Website: www.lumio.com
The following diagram displays a cross-section of the IR Rod inserted into the Corner Housing.
Figure 6 Rod inserted into Corner Housing
b. Insert the side IR Rod into the side Rod Holder.
Ensure that:
•The IR Rod is fully inserted and placed straight inside the Rod Holder
•The Rod Holder fits into the Corner Housing
The following picture displays the colored end of the IR Rod.
Figure 7 Top End of Rod
The following picture displays insertion of the side IR Rod into the Rod Holder.
Figure 8 Inserting the Side Rod into the Holder
The following diagram displays a cross-section of the Side Rod Holder with an IR Rod, inserted into the
Corner Housing.
Figure 9 Inserting the Side Rod into the Holder

15
Pre-Assembly: Assembling the Active Barrier DO070201003
6355 Topanga Canyon Blvd. Suite #335, Woodland Hills CA, 91367 USA. Tel: +1 877 97 LUMIO Fax: +1 818 883 0858. Website: www.lumio.com
2. Insert a Reflector on top of the IR Rod.
Note:
•Distance the Reflector 30 mm from the LED PCB’s
•Do not distance the Reflector from sensors
•As the Reflectors are distanced 30 mm away from the LED PCBs, they are correspondingly shorter than
the IR Rods that they are placed on (30 mm when the IR Rod is connected to one LED PCB, 60 mm when
the IR Rod is connected to two LED PCBs, one at each end of the rod)
The following picture displays a reflector being inserted into a Rod Holder.
Figure 10 Inserting a Reflector into a Rod Holder
3. Insert a Dummy LED PCB into the Rod Holder, immediately after the IR Rod.
4. Insert an IR Rod on the other side of the Dummy LED PCB. (Adjacent to the Dummy LED).
5. Insert a reflector on top of the second IR Rod.
The following picture displays a Dummy LED inserted in a Rod Holder between two IR Rods.
Figure 11 Dummy LED PCB
The following diagram displays a cross section of a Rod Holder with a Dummy LED PCB inserted into the
Rod Holder, between two IR Rods.
Figure 12 Dummy LED PCB Cross Section
The following picture displays a cross section of IR Rods in a Rod Holder with reflectors and Dummy LED PCBs.

16
Pre-Assembly: Assembling the Active Barrier DO070201003
6355 Topanga Canyon Blvd. Suite #335, Woodland Hills CA, 91367 USA. Tel: +1 877 97 LUMIO Fax: +1 818 883 0858. Website: www.lumio.com
Figure 13 Rod Holder Cross Section
6. Remove the Dummy LED.
The following picture displays a cross section of an assembled Rod Holder (Without LED PCB wiring).
Figure 14 Assembled Rod Holder
7. Attach Tesa double sided tape to the side of the Rod Holder that will be attached to the glass.
Note: Ensure that the tape is attached to the Corner Housing as well as the Rod Holder.
The following picture displays tape attachment to the Rod Holder and Corner Housing.
Figure 15 Attaching Double Sided Tape to Rod Holder and Corner
8. Repeat steps 1 to 7 above for the second side Rod Holder and the long Bottom Rod Holder (As there are only
two sensors, the top long holder is a decorative holder with no components).
The following picture displays a Dual Sensor system panel ready for assembly.
Figure 16 Dual Sensor System Panel

17
Pre-Assembly: Assembling the Active Barrier DO070201003
6355 Topanga Canyon Blvd. Suite #335, Woodland Hills CA, 91367 USA. Tel: +1 877 97 LUMIO Fax: +1 818 883 0858. Website: www.lumio.com
5.3 Assembling the Active Barrier for Quad Sensor Systems
Quad Sensor systems include the following features:
•A sensor is attached to each corner of the panel
•Unlike Dual Sensor systems, all sides of the panel contain IR Rods and LED PCB’s
•There are no Corner Housings
The following diagram describes the Quad Sensor system layout
Fig 18: Quad Sensor System Layout
Quad Sensor system components are identical to Dual Sensor system components (See Assembling the Active
Barrier for Dual Sensor Systems on page 12) but have 4 sensors and a Rod Holder including an IR Rod, Reflector and
PCB LED wire instead of the Decorative Rod on the top side of the Active Barrier.
To assemble the Active Barrier for Quad Sensor systems
The procedure for assembling the Active Barrier for Quad Sensor systems is identical to the procedure for
assembling the Active Barrier for Dual Sensor systems (See Assembling the Active Barrier for Dual Sensor Systems on
page 12) with changes due to the different systems as mentioned above.
Table of contents
Other Lumio Touchscreen manuals
Popular Touchscreen manuals by other brands
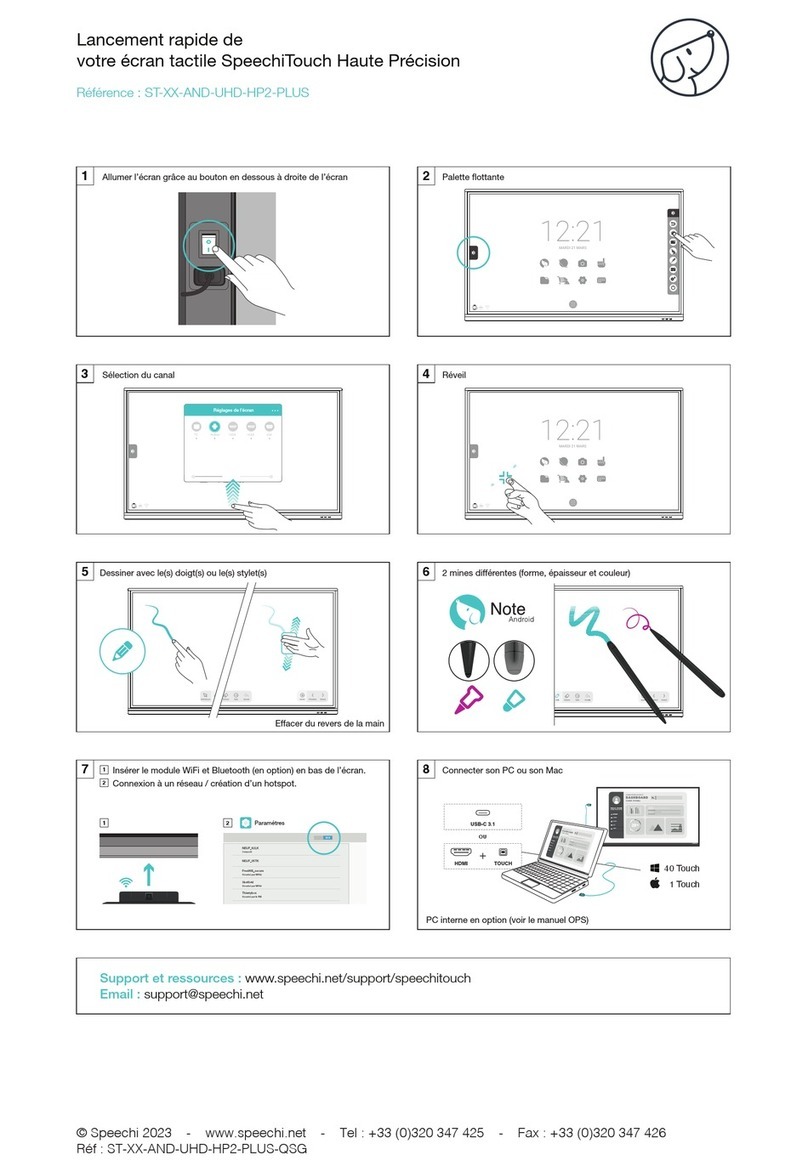
Speechi
Speechi SpeechiTouch ST-XX-AND-UHD-HP2-PLUS quick start guide
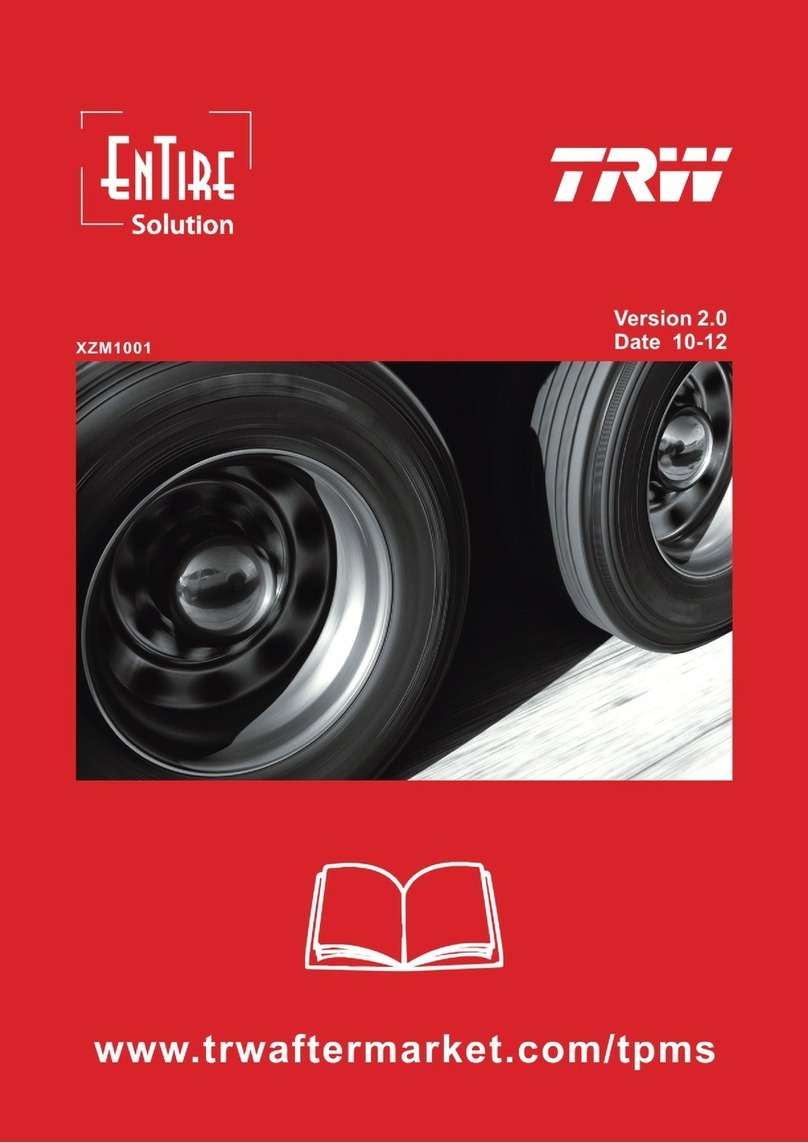
TRW
TRW EnTire Solution TPMS user manual
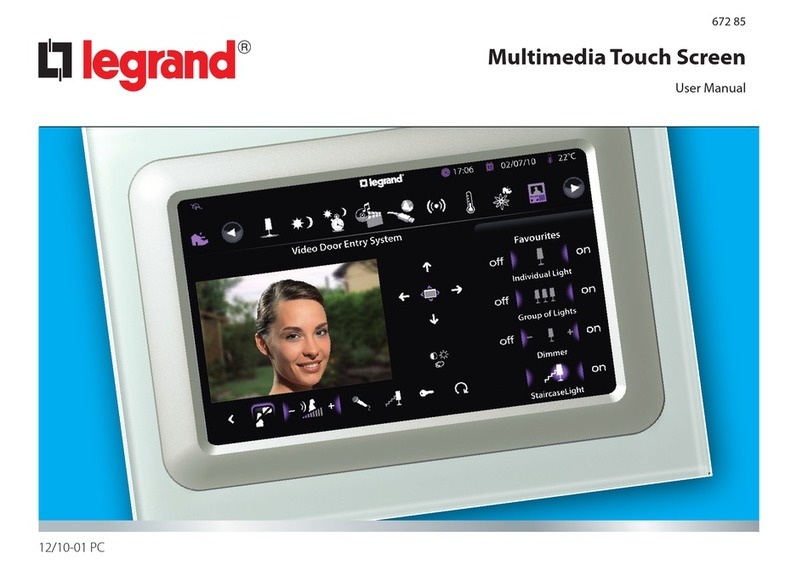
LEGRAND
LEGRAND 7" Video Touch Screen user manual
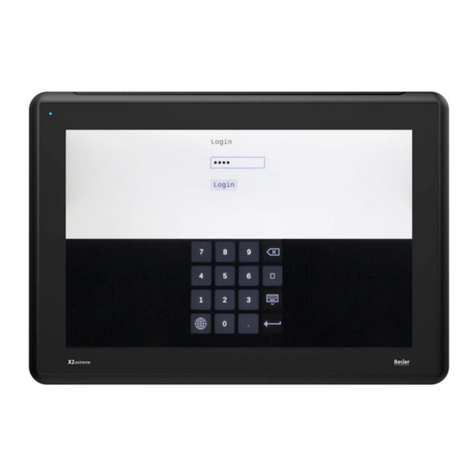
Beijer Electronics
Beijer Electronics X2 control user guide
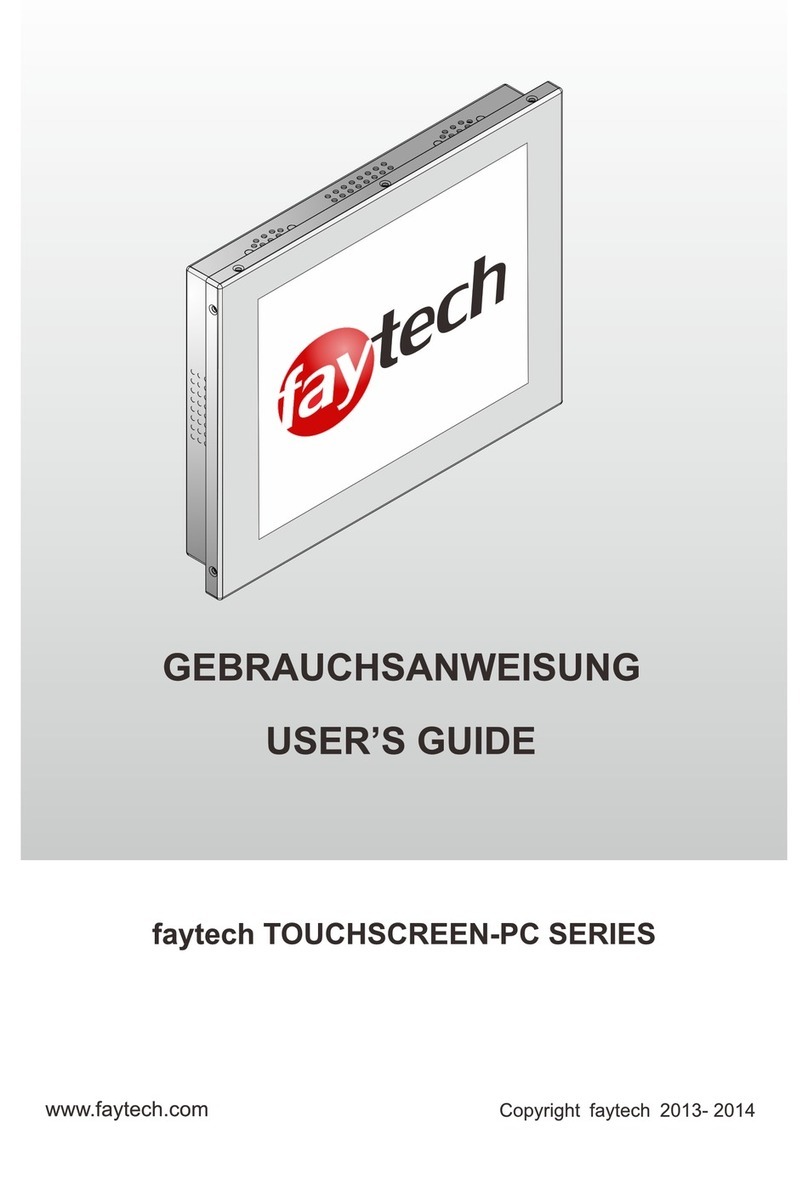
Faytech
Faytech TOUCHSCREEN-PC SERIES user guide

Zeta
Zeta PREM1ER QUATRO installation manual