Lydall AFFINITY P Series User manual

Artisan Technology Group is your source for quality
new and certied-used/pre-owned equipment
• FAST SHIPPING AND
DELIVERY
• TENS OF THOUSANDS OF
IN-STOCK ITEMS
• EQUIPMENT DEMOS
• HUNDREDS OF
MANUFACTURERS
SUPPORTED
• LEASING/MONTHLY
RENTALS
• ITAR CERTIFIED
SECURE ASSET SOLUTIONS
SERVICE CENTER REPAIRS
Experienced engineers and technicians on staff
at our full-service, in-house repair center
WE BUY USED EQUIPMENT
Sell your excess, underutilized, and idle used equipment
We also offer credit for buy-backs and trade-ins
www.artisantg.com/WeBuyEquipment
REMOTE INSPECTION
Remotely inspect equipment before purchasing with
our interactive website at www.instraview.com
LOOKING FOR MORE INFORMATION?
Visit us on the web at www.artisantg.com for more
information on price quotations, drivers, technical
specications, manuals, and documentation
Contact us: (888) 88-SOURCE | sales@artisantg.com | www.artisantg.com
SM
View
Instra

AFFINITY™ P-SERIES CHILLER
User Manual D50050
Lydall Industrial Thermal Solutions Inc.
775 Route 16
Ossipee NH 03864 USA
Telephone: 603-539-3600 (Sales), 603-539-5005 (Service), Fax: 603-539-8484
Artisan Technology Group - Quality Instrumentation ... Guaranteed | (888) 88-SOURCE | www.artisantg.com

Table of Contents
Introduction
Equipment Precautions
Safety Precautions
Installation
Placement
Electrical Connection
Priming the Pump and Connecting the Coolant Loop
Control/Monitoring
Control Panel
PYX4 Microprocessor
Changing the Process Temperature Setpoint
Fault Display
PYX Controller Parameter Values
WinChill Communications
PXZ Controller
Status Lights
EMO
Operation
Operating Range
Start-up
Shutdown
Preventive Maintenance
PLC Tables
Trouble Shooting Guide
Warranty
Refrigeration Diagram
Coolant Flow Diagram
Electrical Schematic
Artisan Technology Group - Quality Instrumentation ... Guaranteed | (888) 88-SOURCE | www.artisantg.com

Introduction
Congratulations on your purchase of an Affinity™ product.
We want to personally welcome you to the Lydall larger family. In October of 2001, Lydall
purchased Affinity Industries, in an effort to expand capability as a Total Thermal Solutions
Provider. Affinity’s chillers and heat exchangers complement Lydall’s existing wide array of
Passive Thermal Solutions, augmenting Lydall’s engineered thermal solutions for use in
appliance, cryogenic, building products, and automotive markets. Our group is market driven as
a formidable thermal solution manufacturer.
Lydall, Inc. is a New York Stock Exchange listed company (NYSE: LDL) headquartered in
Manchester, CT. Our company, with ten operations in the United States, France, one in
Germany, and Sales/Service Offices in Japan and Singapore, is recognized for working with
customers to satisfy their unique thermal solution needs, and for delivering high quality,
innovative products, and exceptional service.
Affinity™ products are high-precision specialty temperature-controlled equipment. The following
product manual is designed to help you realize the full value of your purchase.
We highly recommend that you read this manual in its entirety. The manual will assist your
company with the installation, operation, and routine maintenance of your Affinity™ product.
Please keep this manual readily accessible to operation and service personnel to ensure you get
the most out of our product.
If you have any questions about this model, or have other thermal solution needs, do not hesitate
to call our Sales department (603-539-3600) or the 24/7 Service department (603-539-5005).
Thank you for your confidence in our ability to meet and/or exceed your needs and expectations.
Artisan Technology Group - Quality Instrumentation ... Guaranteed | (888) 88-SOURCE | www.artisantg.com

CE Declaration of Conformity
Lydall Industrial Thermal Solutions declares that the Lydall product referred to in this manual is in
conformity with the provisions of:
Council Directive 2004/108/EC (Electromagnetic Compatibility Directive)
European Standards:
EN55011, Group 1, Class A
EN61326, Industrial Requirements
and Council Directive 2006/95/EC (Low Voltage Directive)
European Standard:
EN60204-1
A signed declaration of conformity is available from Lydall upon request.
European Directive 97/23/EC
As of May 29, 2002, the European pressure equipment directive (PED) 97/23/EC became
mandatory for the CE marking of some pressure equipment. Lydallchillersandcondensing units
are not CE marked to the PED. Most Lydall chillers fall into the Category I or the Sound
EngineeringPractice categories asdefinedbythe PEDandsincechillers fallundertheLow Voltage
Directive (2006/95/EC), they are excluded from the scope of the PED per Article 1, paragraph 3.6
of the PED. Some chillers and condensing units using hermetic compressors of 7.5 HP or more
that are classified as Category II are not excluded from the PED. In these cases, it is the
responsibility of the end-user to assure that the final installation complies with all of the appropriate
European directives including the PED. For more information regarding the PED and other
European directives, go to http://www.newapproach.org/
Artisan Technology Group - Quality Instrumentation ... Guaranteed | (888) 88-SOURCE | www.artisantg.com

Equipment Precautions
Failure to adhere to these precautions will void the warranty and may damage the chiller.
1. This chiller has been shipped without coolant. Do not run the unit without the fluid lines
connected and filled with the proper fluid. Never run the pump dry because it will be quickly
damaged without liquid.
2. This unit is designedto use HFE-7500 as the coolant. It wastested at the factory with HFE-
7500. Consult Lydall prior to using any other fluid. Other coolants may not be compatible
with the components in the unit’s coolant loop.
3. Maximum storage temperature for the unit is 52EC (125EF).
4. The chiller is designed for indoor use only. Do not operate the chiller in ambient
temperatures below 7EC (45EF) or above 30EC (86EF). Operationabove 30EC will derate
the chiller’s cooling capacity. If the chiller has been exposed to temperatures below 7EC,
allow twenty-four hours at ambient temperature above 7ECto warm the oil in the
compressor as well as the refrigerant before starting.
5. If this unit contains refrigerant, there is an oxygen depletion risk that should be considered.
It must be placed in a room with adequate volume based on the amount of refrigerant in the
unit. If additional refrigeration equipment is in the room, additional space must be provided.
In thePlacement section, underInstallation,referto theWarning:OxygenDepletion Riskfor
more details.
6. The cabinet of the chiller is designed to vent air. Maintain free space for flow of air on the
condenser side of the chiller. The two sides or the top must have an equal amount of free
space.
7. Regularly check the air filter located in front of the compressor. Remove the filter, clean as
needed and reinstall or replace. When air flow becomes impeded, cooling capacity
decreases and electrical efficiency drops as motor load increases.
8. This chiller operates on three phase electricity. Some components aresensitive to phase
sequence. The chiller is designed and wired so that all components will operate properly
if the phase sequence is correct. This unit is protected by a Phase Reverse Relay, to
prevent it from running if the sequence is incorrect. If the chiller fails to start on installation,
reverse the phase sequence external to the chiller. Do not modify the wiring inside the
electrical box.
9. Routinely inspect the pump inlet strainer located inthereservoir for buildup of debris. Turn
the chiller off, then remove and clean the strainer as required to permit free flow of coolant.
Prevent foreign debris from entering coolant lines while the strainer is removed. Hint: A
plasticsandwich bag maybeusedto wrapthestrainerto containmostofthe debris. Failure
to keep the strainer clean will reduce coolant flow and may damage the pump.
Artisan Technology Group - Quality Instrumentation ... Guaranteed | (888) 88-SOURCE | www.artisantg.com

Equipment Precautions
10. Donotoperatethe chiller atcoolanttemperatures above orbelowthevalues itwasspecified
to deliver.
11. Do not operate the chiller with cooling loads that exceed its factory rated cooling capacity.
12. Do not operate damaged or leaking equipment.
13. The chiller must not be transported unless suitably protected. Original factory packaging in
good condition or equivalent is required. Request air-ride trucks if transporting over land.
14. Thechiller should be thoroughly drained and the coolantlines should be dry before shipping
or storing.
15. Modifying the chiller without express written consent from Lydall will void the warranty.
16. Tools required to perform inspection and maintenance on this unit are:
screwdriver
multimeter (including AC voltmeter)
safety glasses
gloves
17. Trainingrequirement: All informationcontainedinthis manualmustberead, understood,and
followed before operating or performing maintenance on this chiller.
Artisan Technology Group - Quality Instrumentation ... Guaranteed | (888) 88-SOURCE | www.artisantg.com

Safety Precautions
1. Heed all warning labels. No warning label should ever be removed from the unit.
2. Connect the chiller to a properly fused disconnect box in compliance with the National
Electric Code (NFPA-70) as well as state and local codes for American usage, or national
andlocal codes forEuropeanusage. Maximumfuses mustnotexceedthe maximumrating
found on the serial tag on the electrical box. To reduce the risk of electric shock:
!Disconnect electric power before opening the electrical box of the unit.
!Do not operate with electrical box door open.
!Referservicing of electricalboxcomponentsto qualified/certifiedpersonnel.
!Do not operate equipment with damaged electrical power cords.
!Turnoff the unit anddisconnectelectricalpower beforeservicingormoving.
!Properly ground the unit.
3. The servicing of the refrigeration system or components should be performed only by
properly certified refrigeration technicians.
4. Coolant lines, filters, and other components which connect to the unit must be capable of
withstandingthe maximum pressurethatthepump inthechillercan deliveratthemaximum
expected temperature.
5. Do not remove any warning labels.
6. When operating a pump with a magnetic coupling, pay special attention to the handling of
permanent magnetic parts. Due to potential interference from magnets, keep a safe
distance from pace makers and other devices subject to magnetic interference.
7. Fluids can be extremely hot or cold. Use appropriate precautions when contact with fluids
is possible.
Artisan Technology Group - Quality Instrumentation ... Guaranteed | (888) 88-SOURCE | www.artisantg.com

Installation
Transporting
If a forklift will be used to carry the chiller, proceed slowly and carefully to avoid jarring the unit.
If the chiller will be shipped, protect it from shock and vibration or the warranty will be void. The
chiller must not be transported unless suitably protected. Original factory packaging in good
condition or equivalent is required. Request air-ride trucks when transporting over land.
Thoroughly drain the coolant lines and blow them dry with low pressure compressed air before
shippingor storing. Lydall willnotacceptany unitcontainingmeasurableamounts offluid. Fluidleft
in the unit during shipping may damage components within the unit. Such damage is not covered
by warranty.
Placement
Select a level location, near the application, free from dripping or spraying moisture and excessive
dust. Keeping coolant lines short allows the pump to provide maximum pressure and flow to the
application. If the chiller will be placed more than 25 feet from the application, call Lydall to discuss
placement and how it might affect performance.\
WARNING: Oxygen Depletion Risk
In theevent of arefrigerantleak,refrigerant gasmaydisplaceoxygen thatcouldresultin suffocation
and death. Never place the chiller in a room that is smaller than the minimum room volume
requirementas defined below. Iftheroomis ventilated,theairdistribution systemmustbeanalyzed
todetermine the worstcasedistributionof leakedrefrigerant. Aleakdetector alarmdeviceisalways
required in a ventilated room that does not meet the minimum room volume given below. Assure
adequateand sufficient roomvolumeandventilation beforeplacingachiller thatcontainsrefrigerant
in a room. Contact Lydall at 1-603-539-5005 if you have any concerns or questions.
Pounds of refrigerant charge can be read directly from the nameplate on your chiller. Remember
to include in your calculation any refrigerant that may be stored in any other containers.
Minimum Room Volume = Pounds of refrigerant x 110 cubic feet
Example:Two chillers areplacedina room,eachcontaining6 poundsofrefrigerant. Theminimum
room volume shall be 12 x 110 cubic feet, or 1,320 cubic feet.
Installation
Artisan Technology Group - Quality Instrumentation ... Guaranteed | (888) 88-SOURCE | www.artisantg.com

CT1
75VA
CONNECT FOR
SYSTEM VOLTAGE
24 VAC
BLU YEL
REMOVED FROM
POWER TERMINAL
INTERCHANGE
RED AND ORN
TO CHANGE VOLTAGE PRIMARY CONNECTIONS
NOT USED MUST BE
ISOLATED AND CAPPED
ELECTRICAL SCHEMATIC
TYPICAL CONFIGURATION
NOTE: IN SOME CASES PRESSURE SCREW TERMINAL BLOCKS
ARE USED IN PLACE OF FASTON TERMINATIONS
Electrical Requirements
Connectthechillerto a properlyfuseddisconnect box incompliancewiththe NationalElectricCode
(NFPA-70) as well as state and local codes for American usage, or national and local codes for
Europeanusage. Maximum fuse sizesinthedisconnect boxmustnotexceed themaximumratings
specified on the serial tag of the chiller (found on the electrical box). The voltage, phase, and
frequency of the power source must also match the requirements specified on the serial tag.
Note: Affinity™ models that can operate at either 200-220 Volts 50 Hertz or 208-230 Volts 60 Hertz
have been set at the factory for 200-220 volt operation. If the operating voltage will be greater than
220 volts, a qualified electrician should remove the red wire from the contactor and replace it with
the orange wire taken from the dummy fuse block. Attach the red wire to the dummy fuse block as
shown in the diagram above. See the unit’s serial tag for the correct voltage range.
Warning:To reduce the risk of electric shock, do NOT remove cover from the
electrical box. It contains exposed high voltage wires. Refer servicing to qualified
personnel. Disconnect power to the chiller before performing any service.
Artisan Technology Group - Quality Instrumentation ... Guaranteed | (888) 88-SOURCE | www.artisantg.com

Installation
Priming the Pump and Connecting the Coolant Loop
DO NOT RUN THE PUMP DRY. If the pump does not establish prime, the pump shaft seal may
overheat and be damaged in less than a minute. Use the following instructions when filling and
assembling the coolant lines to prevent damage to the pump shaft seal.
1. Close the reservoir drain.
2. Fully open the flow control valve (if included).
3. Have extra HFE7500 to add as the pump primes and the coolant loop fills.
4. Fill the reservoir with HFE 7500. Do not fill above the height of the coolant loop connection
fittings or fluid may leak out.
5. Connect the coolant lines from the application to the FPT (female pipe thread) fittings near
the top of the chiller as follows. Do not over tighten theinsert and donotusea sealantthat
will lock the male threads to the female threads.
a. Connect the coolant line coming back from the application to the RETURN fitting.
b. Connect the coolant line going to the application to the SUPPLY fitting.
RETURN SUPPLY
6. This chiller is equipped with a Phase Reverse Relay. The chiller will not start if the phase
sequenceis incorrect. If the chiller fails to start upon installation, have a qualified electrical
technician check the Phase Reverse Relay in the electrical box of the chiller. If the LED is
notbrightlylit,thephase sequence is incorrect. The electrical technician should switch any
two of the wires at the incoming power source. Do not change any of the wiring in the
chiller’s electrical box. Check again for proper phase sequence before proceeding with
these instructions.
Artisan Technology Group - Quality Instrumentation ... Guaranteed | (888) 88-SOURCE | www.artisantg.com

Installation
7. When the previous steps are complete, turn the chiller on by placing the ON/OFF/SET
switch in the ON position. Immediately check for flow. If within five seconds no turbulence
is visibleinthe reservoir or the supply pressure gauge shows nopressurereading, shut the
chiller off by placing the ON/OFF/SET switch in the OFF position. If flow is established,
continue filling until fluid rises to within a few inches of the top of the reservoir. Do not allow
the reservoir to overflow.
8. If the pump does not establish prime, disconnect the SUPPLY coolant line to vent any
trapped air, reconnect the line, and repeat step 7.
9. If the pump still does not prime, use the following steps:
a. Disconnect both coolant lines (have a container handy to catch any overflow from
the RETURN fitting).
b. Force coolant into the SUPPLY fitting. The fluid will force the air out of the lines in
the chiller and out of the pump head, causing it to escape into the reservoir. Elevate
thecoolant a fewfeetabovethe chiller,connecttothe SUPPLYfitting,andlet gravity
force the air out into the reservoir. Remember to have a container handy to catch
any overflow from the RETURN fitting.
c. Reconnectthe coolant lines and repeat step 7. Stop filling when the reservoir is full
to within a few inches of the top. Do not allow the reservoir to overflow.
A stainless steel mesh strainer attaches to thepumpsuctionportnearthe bottom of the reservoir.
It caneasily be removedforcleaning. Firstturn thepumpoff,then pulloffthestrainer, rinse itclean,
and push it back on. To protect the pump, routinely inspect the strainer to be sure it is clean and
properly attached. Hint: If the strainer is coated with debris, wrap it with a plastic sandwich bag
before pulling it off to prevent most of the debris from escaping into the reservoir. Failure to clean
aclogged strainer can restrict flow, causing the FAULT light to illuminate. Turn the chiller off for a
few seconds after correcting the condition to reset the alarm.
Artisan Technology Group - Quality Instrumentation ... Guaranteed | (888) 88-SOURCE | www.artisantg.com

FUJI
ELECTRIC EC
PV OUT2
ALM1
ALM2
:::: ::::
8. 8. 8.8.
8. 8. 8. 8.
SEL
SV
::::
OUT1
Control/Monitoring
Control Panel
Thevariouselementson the control panel are described in thesectionsbelow. AdvancedWinChill
Communications are available through the 9-pin connector. To run the unit without the software
running, set the Station Number (Stno on the controller parameters, see Parameter Values) to 15.
Turn the unit off, set the ON/OFF/SET switch to the ON position, cycle the breaker and in
approximately 10 seconds, the unit will start.
PYX4 Microprocessor
The microprocessor (Figure 1) becomes operative when the breaker is closed and five seconds
after the SET/OFF/ON switch is placed in either the ON or SET position.
Figure 1
The microprocessor receives a temperature signal from the RTD (Resistance Temperature
Detector) located in the process cooling line leaving the evaporator. This temperature value is
displayed in the PV (Process Value) readout on the controller.
The SV (Setpoint Value) readout has two distinct functions.
!To establish the basic program of the microprocessor.
!To set the control temperature of the fluid out of the evaporator.
Changing the Process Temperature Setpoint
Change the Setpoint Value by pressing the (>) key on the controller keypad. SV will change to a
leading zero display. Continue pressing (>) until the appropriate digit flashes. Press (v) to
increase the value or press (w) to decrease the value. Continue pressing (>) until the last digit
flashes. Press (>) one more time and all leading zeroes extinguish. This locks in the Setpoint
Value.
Caution: Never program in a Setpoint Value of less than -45EC.
Artisan Technology Group - Quality Instrumentation ... Guaranteed | (888) 88-SOURCE | www.artisantg.com

Control/Monitoring
To power the controller without powering the chiller, place the SET/OFF/ON switch in the SET
position. The digital display will light in about 5 seconds. The number next to PV is the actual
process fluid temperature. The number next to SV is the Setpoint Value (desired) temperature.
To view the program depress the SEL key until LoCT appears in the PV section of the controller
and 0002 appears in the SV section. Change 0002 to 0003. Continuing to depress the (w) key
will bring up the remainder of the program. Toggle through the program using the (>), (v), and
(w) keys to change the appropriate digits until the display reads as desired. To change a
parameter value, press (>). The value in PV will begin flashing. While flashing, the value may
be changed by pressing (v) to increase the value or by pressing (w) to decrease the value.
When the correct value is visible on the display, press SEL to lock in the value. Return to the
PV/SV displays will be automatic after a minute, or by pressing and holding the SEL key for a
few seconds.
Fault Display
If UUUU appears on the PV display, one of the following has occurred:
!RTD burnout.
!RTD disconnected.
!Input is more than 5% of the full range above the high limit (Sv-h, see below in program
listing).
If LLLL appears on the PV display, one of the following has occurred:
!RTD short circuit.
!RTD disconnected.
!Input is more than 5% of the full range below the low limit (Sv-L, see below in program
listing).
PYX Parameter Values
Press and hold the SEL key to get to the PYX controller parameter menu. Use arrow buttons to
change values. Display returns to PV/SV after about one minute if parameters are not being
changed. Set the following values:
LoCt 3All parameters user changeable
oUT1 ?Cannot be set - anything but 0.0 indicates control output #1 is
energized
Mod AUTo Mode - Auto or Manual
Artisan Technology Group - Quality Instrumentation ... Guaranteed | (888) 88-SOURCE | www.artisantg.com

Control/Monitoring
AT oFF Normal control - not auto-tuned
P9.0 Proportional band
i10 Integral time
d0.0 Derivative time
Ar 15.0 (EC), 27.0 (EF) Anti-reset windup - limits integral range to control overshoot
Man 65.0 Manual resetting value (eliminates offset from P-only
control)
AL1T 0021 Alarm 1 type - high & low absolute
AL11 81.0 (EC),or 174.0 (EF) Alarm 1 setpoint 1 (high)
A11h 1.0(C or F) Alarm 1 hysteresis 1
AL12 -41.0 (EC), or -42.0 (EF) Alarm 1 setpoint 2 (low)
A12h 1.0 (EC or F) Alarm 1 hysteresis 2
AL2T 0041 Alarm 2 type - high absolute and low deviation - used to
operate heater
AL21 28.0 (EC), 100.0 (EF) Alarm 2 setpoint 1 - energizes heater when PV is above
this temp
A21h 1.5 (EC), 3.0 (EF) Alarm 2 hysteresis
AL22 5.0 (EC), 9.0 (EF) Alarm 2 setpoint 2 - heater is on when PV >AL22 below SV
A22h 1.0 (EC), 2.0 (EF) Alarm 2 hysteresis 2
Loop 0.0 Loop break detection time (alarms on abnormal input)
PvT 0500 (EC) 100 Ohm RTD, -100 to 200EC, 1 degree resolution
0501 (EF) 100 Ohm RTD, -148 to 392EF, degree resolution
TF 5.0 Input Filter time in seconds
SFT 0Process Variable shift
Sv-h 80.0 (EC), 176 (EF) Setpoint Variable high limit
Sv-L -40.0 (EC or F) Setpoint Variable low limit
CTrL FUZY Control type
dT 0.5 Not supported - always 0.5
rEv1 rEv Control output #1 action - reverse for modulating HGV
Mv-h 100.0 Manipulated variable (control output) high limit in percent
Mv-L 0.0 Manipulated variable (control output) low limit in percent
bUrn 1Output value when input is abnormal (set to -3% when
bUrn = 1)
Stno 1Station number for RS-485 communications (may not be
used in all cases)
Go through the parameters twice, then set LoCt to 2, some parameters user changeable
WinChill Communications
For units with WinChill RS232 Communications to meet CE Compliance, the external RS232
cable which connects the unit to the customer’s equipment must be shielded. This is required
to meet the EMC immunity requirements of EN61326 for industrial locations. The cable must
not exceed 30 feet in length. The shield construction must be a braid (minimum 85% tinned
copper) over aluminum foil (minimum 100% coverage) shield with a 360Eshield termination at
each end of the cable. One possible source for cable meeting this requirement is Black Box,
part number EGM12D.
Artisan Technology Group - Quality Instrumentation ... Guaranteed | (888) 88-SOURCE | www.artisantg.com

Control/Monitoring
For units with WinChill RS485 communications, the cable must not exceed one thousand feet in
length.
PXZ Controller
A second controller (Figure 2), located inside the electrical box, is for heater safety. It has been
programmed at the factory and should not be changed. The following values are provided for
information purposes only.
Figure 2
To check the program:
1. Press and hold the SEL key until the P-n1 menu appears (3-5 secs.)
2. Toggle through the P-n1 menu until dSP1 appears.
3. Program the following values:
dSP1 65 Parameter masking - used to hide the display of
unused parameters
dSP2 255
dSP3 251
dSP4 255
dSP5 3
dSP6 186
dSP7 127
Artisan Technology Group - Quality Instrumentation ... Guaranteed | (888) 88-SOURCE | www.artisantg.com

Control/Monitoring
4. Push the PV/SV key, then the SEL key. P-n2 will appear. Set the following:
F. C.
P-n1 2Direct acting, fails to zero output
P-n2 2Input type - Type J thermocouple
P-dF 3.0 Input filter constant in seconds
P-SL -40 -40 Lower limit of setpoint range
P-SU 320 160 Upper limit of setpoint range
P-AL 12 High and low zone alarm
P-AH 0
P-dP 0Number of digits to the right of the decimal point
P-F F. C.
5. Push and hold the Sel key for 3-5 seconds, until P appears. Program as follows:
P0.0
i0
d0.0
AL 32 0 Heater is off below this temp
AH 302 150 Heater is off above this temp
HYS 0.0
6. Push and hold the SEL key for 3-5 seconds. Toggle to dSP1. Set: the following:
dSP1 207
dSP5 135
7. Press the PV/SV key until SV shows. Set SV to 320EF or 160EC.
8. Push and hold the SEL key for 3-5 seconds, until AH appears. Set: LOC to 1, all
parameters locked.
Artisan Technology Group - Quality Instrumentation ... Guaranteed | (888) 88-SOURCE | www.artisantg.com

FUJI
ELECTRIC EC
PV OUT2
ALM1
ALM2
:::: ::::
8. 8. 8.8.
8. 8. 8. 8.
SEL
SV
::::
OUT1
Control/Monitoring
Status Lights
Figure 3
The various lights are described below. Note that a fault light indicates unit shutdown.
LEVEL - Amber Located on the lower left side of the
controller. Flashing when a high level
warning condition exists in the reservoir.
Remove excess fluid. Solid when a low
level alarm condition exists. More fluid
should be added immediately.
Artisan Technology Group - Quality Instrumentation ... Guaranteed | (888) 88-SOURCE | www.artisantg.com

Control/Monitoring
HIGH (REFRIGERANT) PRESSURE - Red Located on the upper left side of the
controller. Flashing when a high
compressor discharge pressure condition
exists (warning). If pressure continues to
increase and exceeds the setpoint, the light
will become solid (alarm) and the unit will
shut down.
REFRIGERANT - Red Located on the upper right side of the
controller. Flashing when a low refrigerant
level is sensed in the receiver. The light will
become solid when the unit shuts down on
low suction pressure (after the time delay).
COMPRESSOR OVERLOAD (FAULT) - Red Located on the lower right side of the
controller. 3 flash sequence.
Activated after a 2 second time delay
by the current sensor in one of the
leads to the compressor motor when
the motor has been shut down due
to excessive temperature.
PUMP OVERLOAD (FAULT) - Red Located on the lower right side of the
controller. 2 flash sequence. Activated
when the pump amperage exceeds the
overload setting.
PUMP LOW FLOW (FAULT) - Red Located on the lower right side of the
controller. Single flash. Activated when the
pump flow falls below setpoint to warn the
operator of an impending low flow condition.
PHASE REVERSAL (FAULT) - Red Located on the lower right side of the
controller. Solid light. Activated when
phases of the unit need to be reversed.
This may happen on initial start up of the
unit. If it occurs, switch phases external to
the unit and power the unit again.
To restart the unit after any fault occurs, the power must be cycled. To cycle the power, place
the ON/OFF/SET switch in the OFF position and open the main circuit breaker for a few
seconds. When power is reapplied and the ON/OFF/SET switch is placed in the ON position,
the unit should restart.
Artisan Technology Group - Quality Instrumentation ... Guaranteed | (888) 88-SOURCE | www.artisantg.com

Control/Monitoring
Emergency Stop
The momentary EMO has two sets of normally closed contacts. Both contacts must be closed
to energize the master control relay coil. Continuity between pins 1 and 2 of the 4 pin Amp
connector external to the unit must also be present. To start the unit, ensure that the EMO is not
depressed, then momentarily press the red POWER ON button located on the control panel
below the EMO. The customer’s EMO, when connected to pins 1 and 2 of the 4 pin Amp
connector, will provide the same functionality. The customer can use pins 3 and 4 of the 4 pin
Amp connector to allow the unit’s EMO to turn off other equipment when properly connected.
Artisan Technology Group - Quality Instrumentation ... Guaranteed | (888) 88-SOURCE | www.artisantg.com
Table of contents
Other Lydall Chiller manuals
Popular Chiller manuals by other brands
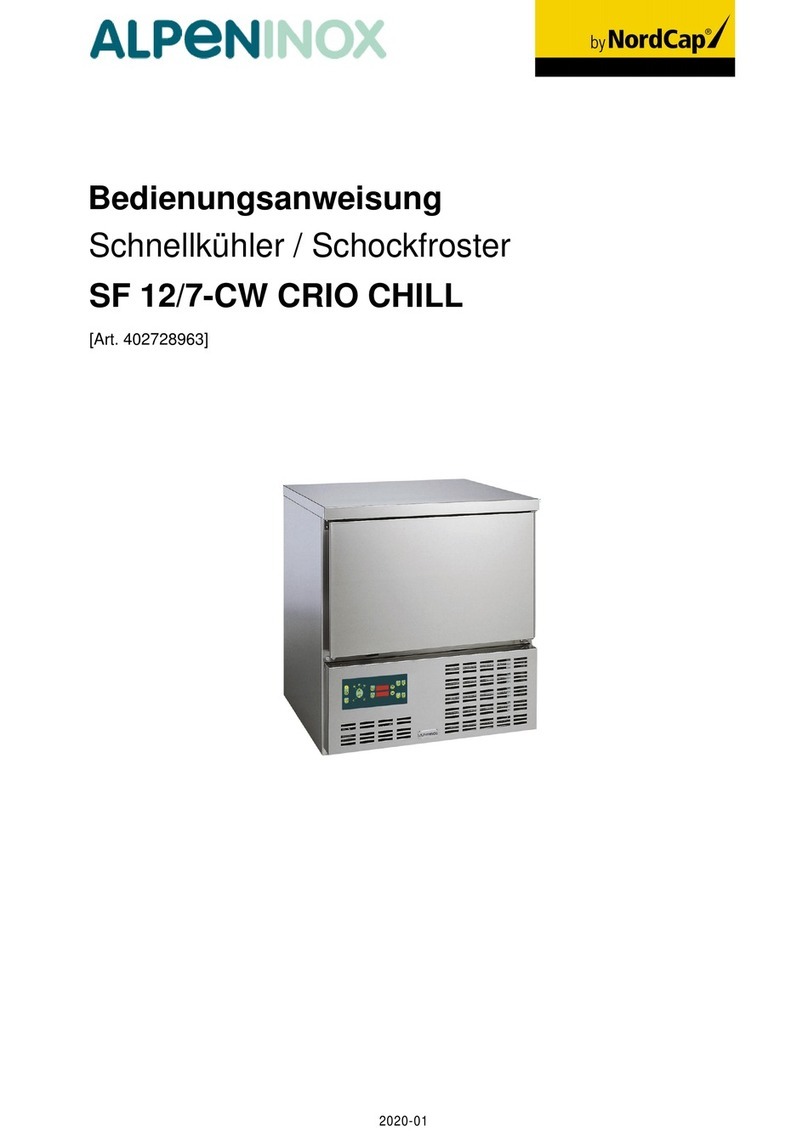
Nordcap
Nordcap SF 12/7-CW CRIO CHILL manual
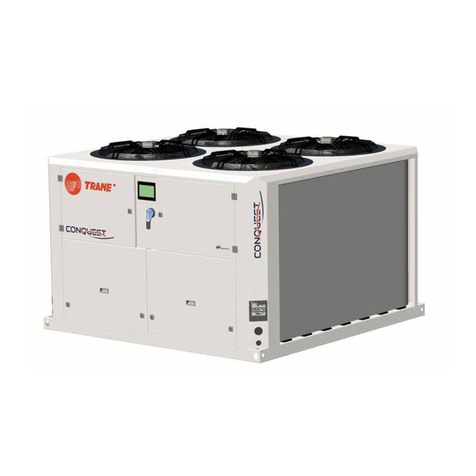
Trane
Trane CONQUEST CGAX 015 Installation operation & maintenance
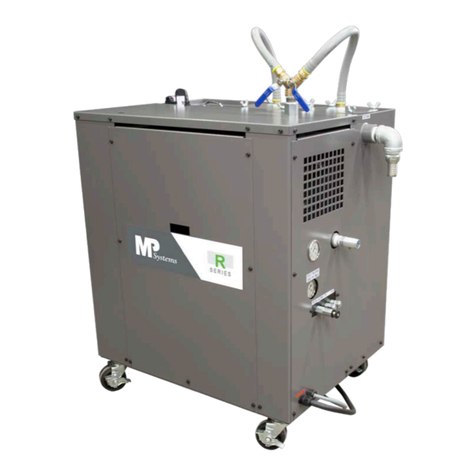
MP Systems
MP Systems R Series Installation, operation & maintenance manual
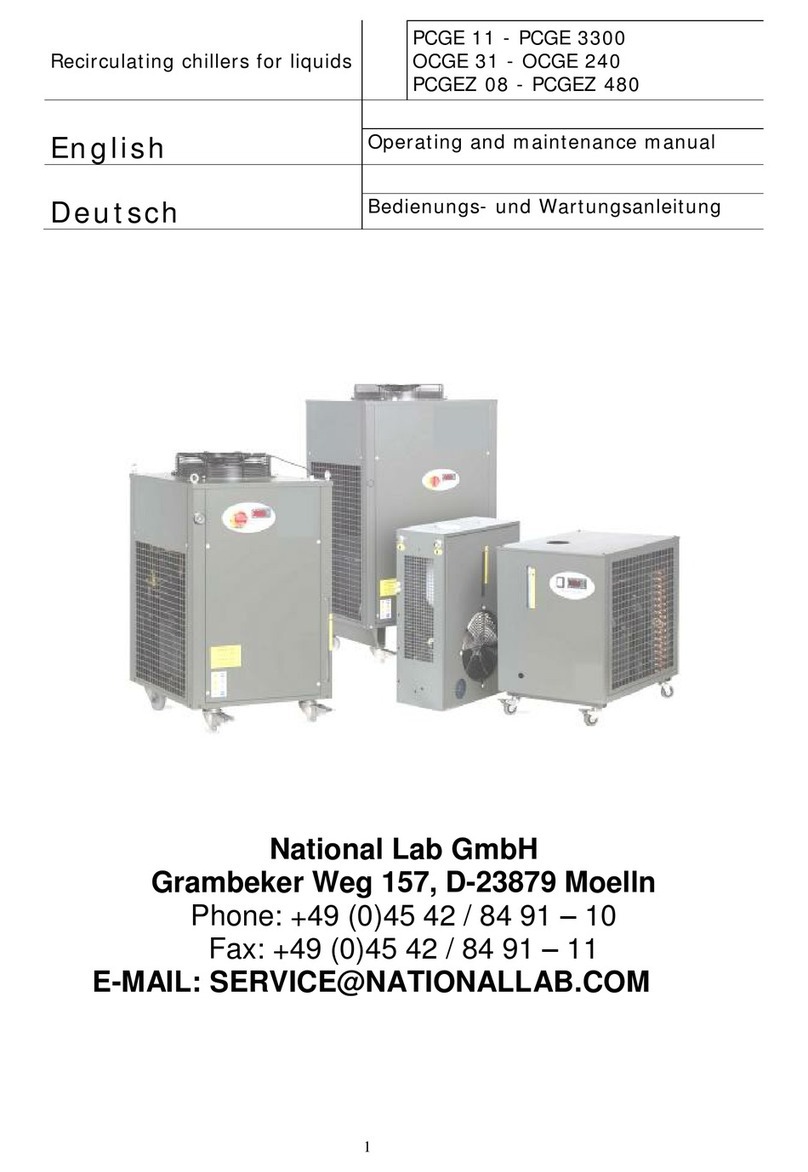
National Lab
National Lab PCGE Series Operating and maintenance manual
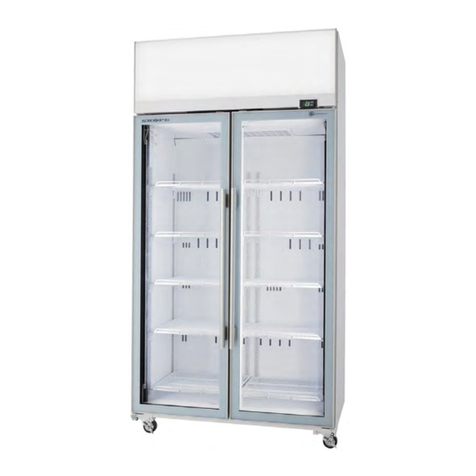
Skope
Skope TME-N ActiveCore Service manual
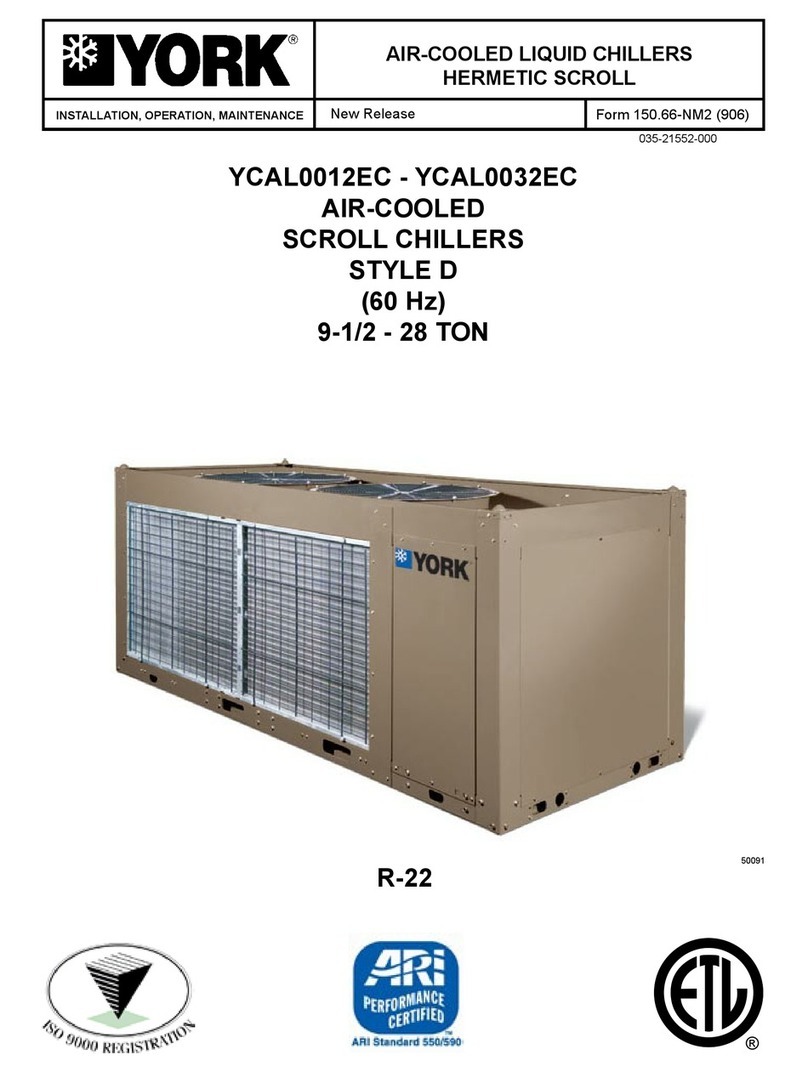
York
York YCAL0012EC Installation operation & maintenance
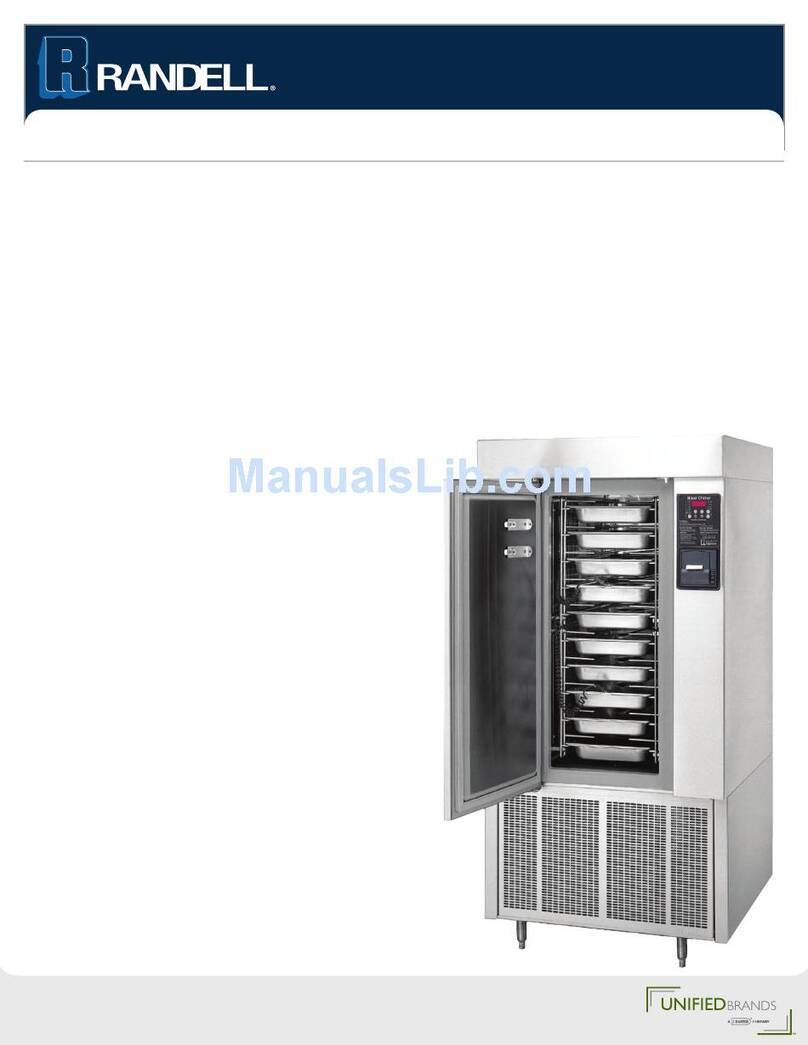
Randell
Randell BC-10 Specifications
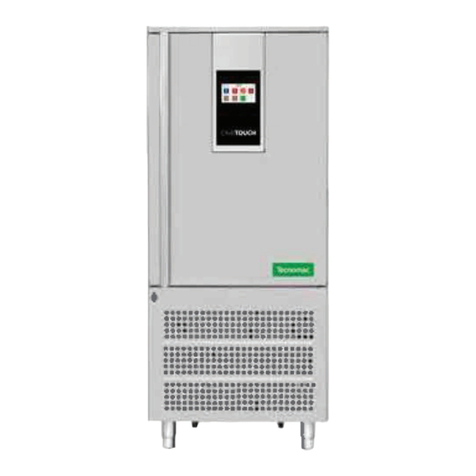
Castel MAC
Castel MAC CT10.35 user manual

Sterlco
Sterlco AquaSnap 30RA010-055 Operation and service guide

York
York YK Style H Operation manual
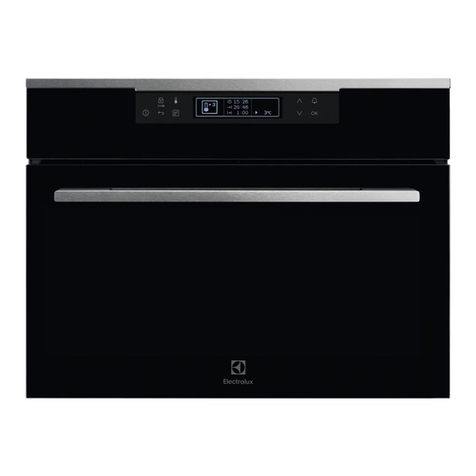
Electrolux
Electrolux KBB5X operating instructions
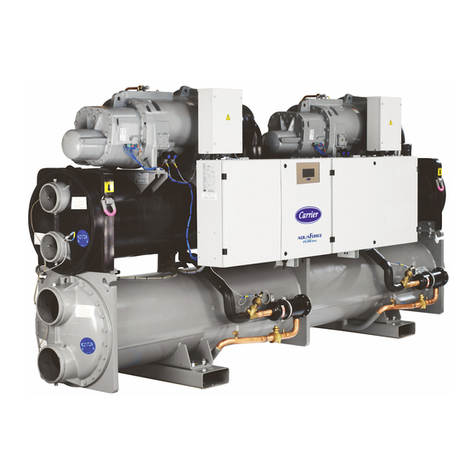
Carrier
Carrier AquaForce PUREtec 30XWHPZE 301 Installation, operation and maintenance instructions