MAGSYS IGM11 User manual

OPERATING-
INSTRUCTIONS
INDUSTRIAL GAUSSMETER IGM11

Industrial Gaussmeter IGM11 Operating Instructions
Page 2 / 92
Stand 08/2020 © 2020 MAGSYS magnet systeme GmbH -All Rights Reserved.
© 2020 MAGSYS magnet systeme GmbH
All rights reserved. No part of these operating instructions may be reproduced or du-
plicated without the author’s written consent.
Windows®is a registered trademark of Microsoft Corporation.
Edition
Data File
IGM11_Manual_DE_2020_08.docx
Doc. Date
04.08.2020
Hardware Status
G
Software Status
25.06.2016
Status of Documentation
Concerning Page(s) n°
01/2016
Update
08/2020
Corrections / Upate

Industrial Gaussmeter IGM11 Operating Instructions
Page 3 / 92
Version 08/2020 © 2020 MAGSYS magnet systeme GmbH -All Rights Reserved
Table of Contents
Safety Instructions 5
Safety Instructions for the Device 5
Safety Instructions for Measuring Probes 5
Safety Symbols 6
Brief Introduction 7
Preparing a Measurement 7
Running a Measurement 7
Measuring Unit 8
Selecting the Measuring Range 8
Display 9
Status Display 9
Function of the Gaussmeter 10
The Hall Effect 10
3.1.1 Linear Properties of the Hall Probe 10
3.1.2 Non-linear Properties of the Hall Probe 11
Measurement Details 13
3.2.1 Sample Measurements with an NdFeB
Magnet 13
3.2.2 Remanence and Hall Gaussmeter
Measurement 14
3.2.3 Accuracy Based on Positioning and
Direction 15
3.2.4 External Static Magnetic Fields 16
Control Elements and Connections 17
Front Panel Overview 17
17
Ports Overview 18
Power Supply 19
Probe Connection 19
USB Interface 20
LAN Interface 21
Operation 23
Buttons 23
Display 24
Status Display 25
Null Balance 25
Measuring Range 25
Measuring Unit 27
DC/AC Field Measurement 27
5.7.1 DC Field Measurement 27
5.7.2 AC Field Measurement 28
Peak Value Measurement 30
5.8.1 Fast Peak Value Detection 30
Probe Data 32
Set-up Menu 33
Reset 33
Settings Overview 33
Settings 34
6.3.1 Overview 34
6.3.2 Measurement 35
6.3.3 Parameters of the Serial Interface EIA-232 36
6.3.4 Parameters of the LAN Interface 36
6.3.5 Settings of the Digital Inputs 37
6.3.6 Settings of the Digital Outputs 38
6.3.7 Settings of the Function Buttons 39
6.3.8 Display of the Error Memory 39
Power Supply Connection 40
Signal Interfaces 41
Introduction 41
Wiring of the Inputs 42
Wiring of the Outputs 43
Serial Interfaces 44
Introduction 44
Connecting the Gaussmeter to an External
Controller 45
EIA-232 Connection 46
9.3.1 Operating Mode SCPI 46
9.3.2 Operating Mode SHORT 47
9.3.3 Operating Mode FLOW 48
Connector Cable EIA-232 48
Samples of Data Transfer EIA-232 49
User Data 51
9.6.1 Character Set 51
9.6.2 Introduction to the SCPI Language 51
9.6.3 SCPI Data Types 53
9.6.4 SCPI Status Model 54
Summary of SCPI Commands 57
9.7.1 Control Commands 57
9.7.2 Main Commands 57
9.7.3 Peak Value Functions 58
9.7.4 Probe Functions 58
9.7.5 Device Functions 58
9.7.6 Memory Functions 59
9.7.7 Serial Interfaces 59
9.7.8 Digital Interfaces 59
SCPI Command Reference 60
9.8.1 Control Commands 60
9.8.2 Main Commands 65
9.8.3 Peak Value Function 68
9.8.4 Probe Functions 70
9.8.5 Memory Functions 72
9.8.6 Device Functions 73
9.8.7 Interface Functions 75
Table of Error Messages 82
Unit Conversion Table 84
Technical Data 85
Declaration of Conformity 89
Warranty and Copyright 90
Index 91

Industrial Gaussmeter IGM11 Operating Instructions
Page 4 / 92
Stand 08/2020 © 2020 MAGSYS magnet systeme GmbH -All Rights Reserved.
Table of Illustrations
Display 9
Basic Assembly of a Hall Probe 10
Flux Line Characteristics of an NdFeB Induction Disk 13
Field Strength Pattern of an NdFeB Induction Disk 14
Front Panel 17
Ports 18
Ports Top 18
Ports Bottom 19
Pin Assignment LAN Interface 21
Display LAN Connection 21
Display during LAN Operation 22
Display 24
Status Display 25
Measuring Ranges 26
Signal Input Plus Switched 42
Signal Input Minus Switched 42
Signal Output Plus Switched 43
Signal Output Minus Switched 43
EIA-232 Connector J4 45
EIA-232 Connector J4 45
Null Modem Cable 48

Industrial Gaussmeter IGM11 Operating Instructions
Chapter 1 Safety Instructions
Page 5 / 92
Version 078/2020 © 2020 MAGSYS magnet systeme GmbH -All Rights Reserved.
Safety Instructions
Safety Instructions for the Device
Use the measuring instrument only according to the operating instructions.
Do not replace any parts and do not modify this product without prior and written
consent by MAGSYS. Do not service this device. Return the device to MAGSYS mag-
net systeme GmbH or to your local supplier for repair and maintenance to ensure
that all safety features remain.
Handling malpractice may result in damage to the device and possibly to injuries or
death of persons.
Do not dispose of this device in normal household garbage. Contact the manufac-
turer for the proper disposal of this device.
Use only appropriate magnetic field probes for this measuring device.
Observe the labeling of the device before connecting a magnetic field probe.
Do not use the device in explosive environments or near to inflammable gases or
vapors.
Environmental Conditions:
This instrument has been designed for the use in rooms with low condensation. See
technical data.
Safety Instructions for Measuring Probes
Magnetic measurements should only be done in areas with a maximum voltage of
60V DC, 30V AC RMS. The magnetic field probes are not electrically insulated.
Please ensure that the probe holders and the housing are connected to protective
earth.
If you work in environments with voltages beyond 60V DC, 30V AC RMS or 42V
peak, act with particular caution because of electric shock hazard.
For measurements in high magnetic fields, observe the risks which might occur
through strong magnetic fields.

Gaussmeter IGM11 Operating Instructions
Chapter 1 Safety Instructions
Page 6 / 92
Version 08/2020 © 2020 MAGSYS magnet systeme GmbH -All Rights Reserved.
Safety Symbols
Safety symbols can be found on various spots of the device.
Before using this connection or function, read the corresponding reference in
the manual.
This symbol refers to information and references in the operating instructions
which the user has to follow in order to avoid injuries of persons or damage
to the device, or to gain correct measuring results.

Industrial Gaussmeter IGM11 Operating Instructions
Chapter 2 Brief Introduction
Page 7 / 92
Version 078/2020 © 2020 MAGSYS magnet systeme GmbH -All Rights Reserved.
Brief Introduction
Measurements with the gaussmeter utilize the Hall effect as principle of measure-
ment. A Hall sensor is a symmetric current-carrying semiconductor. A magnetic field
running perpendicular through this element generates an asymmetry on the chip
and thereby creates an output voltage which, at first approximation, is proportional
to the product of magnetic field strength and forced current. For higher magnetic
field strengths, this correlation is no longer linear. This effect is automatically com-
pensated in the device. Thus, the gaussmeter measures the magnetic flux density at
a point with a high local resolution. It only measures those components of the mag-
netic flux density which run perpendicularly through the sensor.
Preparing a Measurement
For measurements you need to connect a measuring probe.
A suitable measuring probe can be connected via the 8 mm socket on the top of the
device. Each measuring probe is individually calibrated. The calibration data are
stored in the probe memory. When a measuring probe is plugged in or changed,
these parameters will be read automatically.
Running a Measurement
After switching on the device, the actual measured value is shown continuously. In
addition to this, the display shows further information on the device status, the selected
measuring range as well as the measuring mode.
The measuring range, the physical display unit and the measuring mode can be
adjusted in the set-up menu.
After setting the desired measuring range and unit, insert the probe into the mag-
netic field. Especially for heterogeneous magnetic fields, such as they appear on
the surfaces and edges of magnets, pay attention that the measured magnetic
flux density strongly depends on the distance and position. Further take into con-
sideration that the magnetic field component is only measured in one direction
so that tilting the measuring probe might lead to an error.

Gaussmeter IGM11 Operating Instructions
Chapter 2 Brief Introduction
Page 8 / 92
Version 08/2020 © 2020 MAGSYS magnet systeme GmbH -All Rights Reserved.
Measuring Unit
The gaussmeter shows measuring values in physical units of the SI-system and of the
Gauss-CGS system (preferably used in North America).
You can adjust the unit in the set-up menu.
Selecting the Measuring Range
You can select from four measuring ranges in the set-up menu.
The lower left area of the display shows the upper limit of the selected range.
If the measured value exceeds the limit of the selected
range, the display shows -OL-(Overload) instead
of the measured value.

Industrial Gaussmeter IGM11 Operating Instructions
Chapter 2 Brief Introduction
Page 9 / 92
Version 078/2020 © 2020 MAGSYS magnet systeme GmbH -All Rights Reserved.
Display
The following shows a typical example of the display.
Figure 1 Display
Status Display
Beside the currently measured value the gaussmeter displays the status information in
the upper right area.
Display
Description
LAN
The device is accessed via the network connection.
HOLD
The measurement is stopped via an assigned input.
ERR
An error has occurred. The error is stored in the error queue and can
be read via the interfaces or the set-up menu.
Measured value
with unit
Lifesign
Measuring range
and mode
Status of the digital
in- / outputs

Gaussmeter IGM11 Operating Instructions
Chapter 3 Function of the Gaussmeter
Page 10 / 92
Version 08/2020 © 2020 MAGSYS magnet systeme GmbH -All Rights Reserved.
Function of the Gaussmeter
The Hall Effect
3.1.1 Linear Properties of the Hall Probe
The measurement is based on the deflection of charge carriers in a magnetic field
inside a conductor. Thus, the basis of the measurement of the magnetic flux density is
the Lorentz force. If you apply voltage between the beginning and the end of a flat
electrical conductor, the charge carriers move with a rate of
enDrift Ev
, whereby
n
represents the charge carrier mobility inside the conductor. Due to their high mo-
bility, the charge carriers are always electrons. In a displacement by 90° to the current
direction, you can tap a voltage which is ideally proportional to the magnetic flux
density. Only the part of the flux density becomes effective which runs perpendicular
through the flat side of the conductor.
Figure 2 Basic Assembly of a Hall Probe
If you do not extract any current from the electrodes S1 and S2, but only measure the
voltage, the following applies:
B
tw
I
w
U
en Hall
e
B
S2
C2
S1
C1

Industrial Gaussmeter IGM11 Operating Instructions
Chapter 3 Function of the Gaussmeter
Page 11 / 92
Version 078/2020 © 2020 MAGSYS magnet systeme GmbH -All Rights Reserved.
This implies:
B
ten
I
U
e
Hall
1
with
e
n
Charge carriers
e
Elementary charge of the electron (1.6022 10-19 As)
w
Width of the path on which the electrons move
t
Effective force of the Hall element
B
Flux density in [Tesla]
This represents the idealized Hall effect.
In reality, the results deviate from this idealized effect.
Since there is a linear equation between the current and the measuring result, it fol-
lows:
BSB
ten
R
e
Hall
0
1
3.1.2 Non-linear Properties of the Hall Probe
In contrast to the idealized description, you find a non-linear behavior:
offsetHALLHall RBBSR 2
01
For the used Hall sensor the real description is true for flux densities up to about
5000 mT.
3.1.2.1 Reasons for the Occurrence of Roffset
The strongest deviation from the idealized Hall effect is the occurance of an offset
voltage without a magnetic field. This effect is mainly caused by geometric asymme-
tries of the Hall element.

Gaussmeter IGM11 Operating Instructions
Chapter 3 Function of the Gaussmeter
Page 12 / 92
Version 08/2020 © 2020 MAGSYS magnet systeme GmbH -All Rights Reserved.
3.1.2.2 Reasons for the Field Dependence of the Sensitivity
There are several influences for the flux density dependence of the sensitivity:
The mobility of the charge carriers depends on the flux density. This influence gener-
ally leads to a negative αHall and is irrelevant for the used Hall sensors. More im-
portant is the geometry of the used sensors. The lamellar structure generates a ge-
ometry-based field dependence of the sensitivity. The non-homogeneous distribution
of the current density in such a structure causes this effect. Already in field-free
cases, this current distribution on the Hall element is relatively complex. This entails
a lowering of S0and influences the field dependence of the sensitivity. A complex
real-time correction of the gaussmeter IGM11 compensates for the inherent non-
linearities of the used Hall probes and thus ensures a stable zero point.
3.1.2.3 Field Dependence of the Cross-Current Resistance
The current distribution is the cause of the Hall probe resistance. Current components
which –alike the Hall voltage –run vertically to the direction of the current feed, cause
a diverted Hall effect. This becomes noticeable as a flux density modulated resistance.
For measuring fast magnetic impulses, the device must have sufficiently high dynamics
in order to equalize this effect. The gaussmeter IGM11 is optimized for this operating
mode.
3.1.2.4 Temperature Dependence of the Sensitivity
Due to the large band gap of the used Hall sensors the temperature dependence of
the probe sensitivity is low. It is approx. −0.06 %/ºC.
3.1.2.5 Temperature Dependence of the Cross-Current Resistance
The temperature dependence of the cross-current resistance is appox. 0.3 %/ºC and
is automatically equalized by the device.

Industrial Gaussmeter IGM11 Operating Instructions
Chapter 3 Function of the Gaussmeter
Page 13 / 92
Version 078/2020 © 2020 MAGSYS magnet systeme GmbH -All Rights Reserved.
Measurement Details
The used Hall sensors contain a very small active semiconductor area ranging at ap-
prox.100 µm. The local resolution of this mesasuring method is thus rather high. Also
notice that single Hall sensors measure one field component only.
3.2.1 Sample Measurements with an NdFeB Magnet
Due to the high local resolution, the near-surface measurement with magnets may
lead to misinterpretations because of the large field-strength gradients.
Figure 3 Flux Line Characteristics of an NdFeB Induction Disk
Figure 3 shows an NdFeB magnet with a material remanence of 1400 mT. In this exam-
ple the magnetic disk has a thickness of 5 mm with a diameter of 20 mm. The magnet is
supposed to be measured in 1 mm distance from the surface.

Gaussmeter IGM11 Operating Instructions
Chapter 3 Function of the Gaussmeter
Page 14 / 92
Version 08/2020 © 2020 MAGSYS magnet systeme GmbH -All Rights Reserved.
Figure 4 Field Strength Pattern of an NdFeB Induction Disk
The diagram in figure 4 shows the measurement with a Hall probe which is moved in
parallel to the surface of the magnet within a distance of 1mm to the measuring surface.
A minimum of the flux density emerges in the center of the magnet. Here approx. 230mT
are measured. Due to the locally changing working points on the radius of the magnet,
the flux density increases toward the outside. In the center the magnet carries the highest
magnetic load in air and therefore provides the lowest flux density.
3.2.2 Remanence and Hall Gaussmeter Measurement
The remance Bris a mesure for the aligned magnetic dipoles in the center of the magnet.
Bris the theoretically maximum flux density that can be achieved if the magnet is in mag-
netic idle. If it works against a magntetic resistance, it is always B< Br.
On the surface of an individual magnet B< Br/2 applies even more.
Which value is actually measured in the pole center depends on the geometry of the
magnet.

Industrial Gaussmeter IGM11 Operating Instructions
Chapter 3 Function of the Gaussmeter
Page 15 / 92
Version 078/2020 © 2020 MAGSYS magnet systeme GmbH -All Rights Reserved.
As Bras well as Bis measured in the unit Tesla, the magnetic field measured on the
outside is often mixed up with the remanence.
Please note that a magnet without back iron only shows a value clearly below the rema-
nence on the surface. Due to the local and geometry-dependent measurement, the
remanence of the workpiece cannot be checked reliably with a gaussmeter.
3.2.3 Accuracy Based on Positioning and Direction
Since the measuring value depends on the position, an accurate and repeatable meas-
urement depends on the exact positioning of the probe during the measurement.
The measurement on the pole center of the magnet is most uncritical. When moving the
probe on the pole surface of the magnet, the measuring value hardly changes at first.
When changing the distance though, the measuring value varies considerably.
The smaller the magnet to be measured, the stronger even slight misalignments change
the measuring value. For quality-related research it is essential to ensure the positioning
accuracy.
Since a Hall probe only records one field strength vector, the correct alignment relative
to the magnet is important.
Please be particularly careful when measuring at the zero point at pole transitions. By
slightly tilting the probe, you measure additional lateral field shares that seem to dis-
place the zero passage.
In normal applications, a maximum flux density value is usually determined at a given
position. The measuring probe is placed in position and varied in location and direction
until the maximum is found. The device supports this measurement with the peak hold
feature.

Gaussmeter IGM11 Operating Instructions
Chapter 3 Function of the Gaussmeter
Page 16 / 92
Version 08/2020 © 2020 MAGSYS magnet systeme GmbH -All Rights Reserved.
3.2.4 External Static Magnetic Fields
Particularly in sensitive measuring ranges, an external static magnetic field, as e.g. the
Earth’s field, can already become clearly noticeable. These external magnetic fields
lead to a corruption of the measuring result.
To compensate external magnetic stray fields or asymmetries of the Hall probe, the de-
vice can be reset.
For this purpose please hold the measuring probe into a field-free area, e.g. a zero
Gauss chamber, or orient the measuring probe in a free field in east-west direction and
activate the null balance.
The values are stored so that this balancing has to be carried out only in seldom cases.
If the magnetic field is too high during the automatic balancing, the correction is
stopped with an error message.

Industrial Gaussmeter IGM11 Operating Instructions
Chapter 4 Control Elements and Connections
Page 17 / 92
Version 078/2020 © 2020 MAGSYS magnet systeme GmbH -All Rights Reserved.
Control Elements and Connections
Front Panel Overview
Figure 5 Front Panel
Display
Output of the measured value
Status info
ENTER-button
Control of the set-up menu
NEXT-button
USB-socket
Connection to a PC

Gaussmeter IGM11 Operating Instructions
Chapter 4 Control Elements and Connections
Page 18 / 92
Version 08/2020 © 2020 MAGSYS magnet systeme GmbH -All Rights Reserved.
Ports Overview
Probe Port (J1)
(Probe)
EIA-232 Port (J5)
24V IO Ports (J6)
Power
Supply
(J4)
Network
Port
Figure 6 Ports
Figure 7 Ports Top
PROBE
Interface
Probe port
Serial port EIA-232 for PC and
control

Industrial Gaussmeter IGM11 Operating Instructions
Chapter 4 Control Elements and Connections
Page 19 / 92
Version 078/2020 © 2020 MAGSYS magnet systeme GmbH -All Rights Reserved.
Figure 8 Ports Bottom
For add-ons
Interface
Power Supply
LAN
Do not use
Port for PLC sig-
nals
Port for power sup-
ply for the device
and the PLC signals
RJ45 port for the LAN
connection
Power Supply
The gaussmeter can be operated at a voltage of 12 V to 24 V DC. The current con-
sumption is approx. 120 mA at 12 V or approx. 85 mA at 24 V. An electrical sepa-
ration does not take place. Please notice that the shielding of the probes (if so, the
metal housing) will be connected with the earth conductor of your control via this
port.
Probe Connection
The measuring probe is plugged into the probe port (M8-socket IEC 61076-2-104)
on the top of the device.
Note
Only use measuring probes which are approved by the manufac-
turer to operate with this device.
Note
The probe plugs must not be connected to the electric potential, the
protective conductor or the plug shell. If you measure near current
conducting parts, make sure that there is sufficient distance and a
sufficiently good insulation.

Gaussmeter IGM11 Operating Instructions
Chapter 4 Control Elements and Connections
Page 20 / 92
Version 08/2020 © 2020 MAGSYS magnet systeme GmbH -All Rights Reserved.
USB Interface
The transfer of the measuring values and the entire gaussmeter control are
possible via the installed standard USB interface on the front panel.
The interface is specified according to the USB (Universal Serial Bus) 2.0
standard. The interface is not insulated. Please note that the shielding of the
measuring probes (e.g. the metallic handle) might be connected to the pro-
tective conductor of your personal computer via this USB interface.
The device supports the USB device class HID. The installation of a special
driver on the computer is required.
Via the driver all functions and parameters of the device can be adjusted
using SCPI commands, and the measued values can be read out automati-
cally.
In seldom cases, there might be troubles when connecting the device. In
these cases, we recommend the connection via a USB hub.
Other manuals for IGM11
1
Table of contents
Other MAGSYS Measuring Instrument manuals
Popular Measuring Instrument manuals by other brands
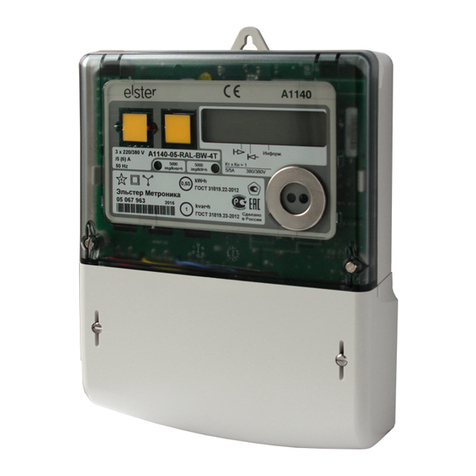
Elster
Elster A1140 user manual
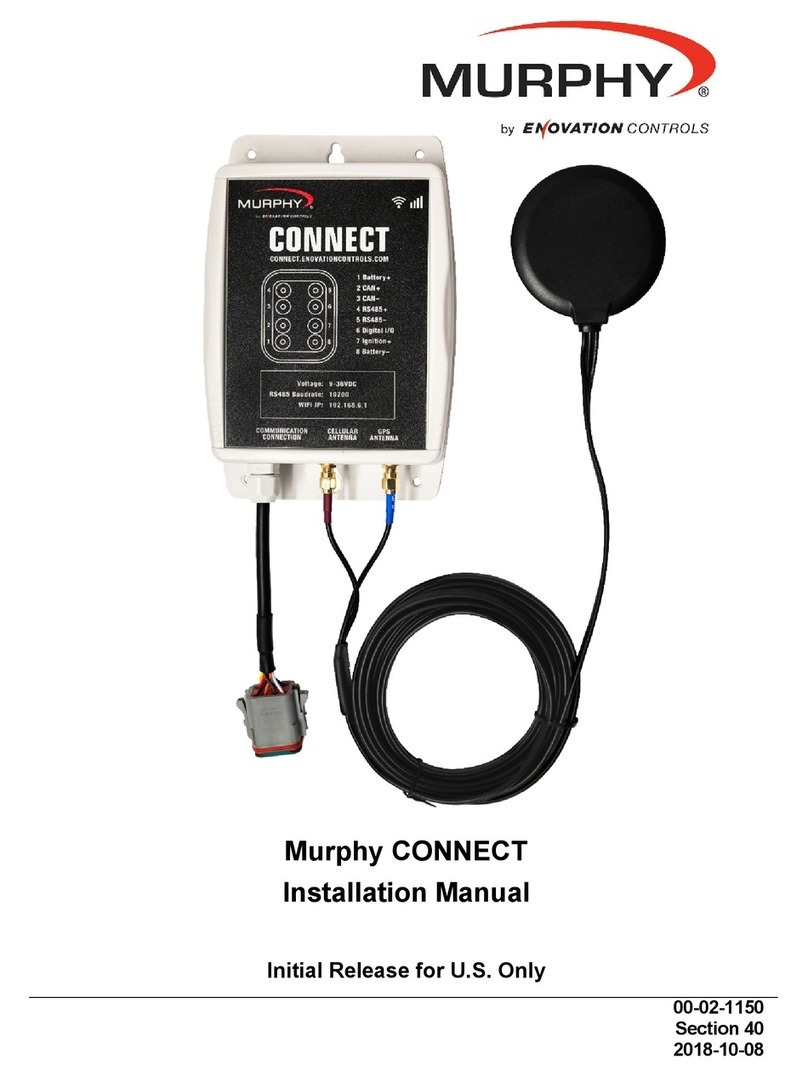
Enovation Controls
Enovation Controls Murphy CONNECT installation manual
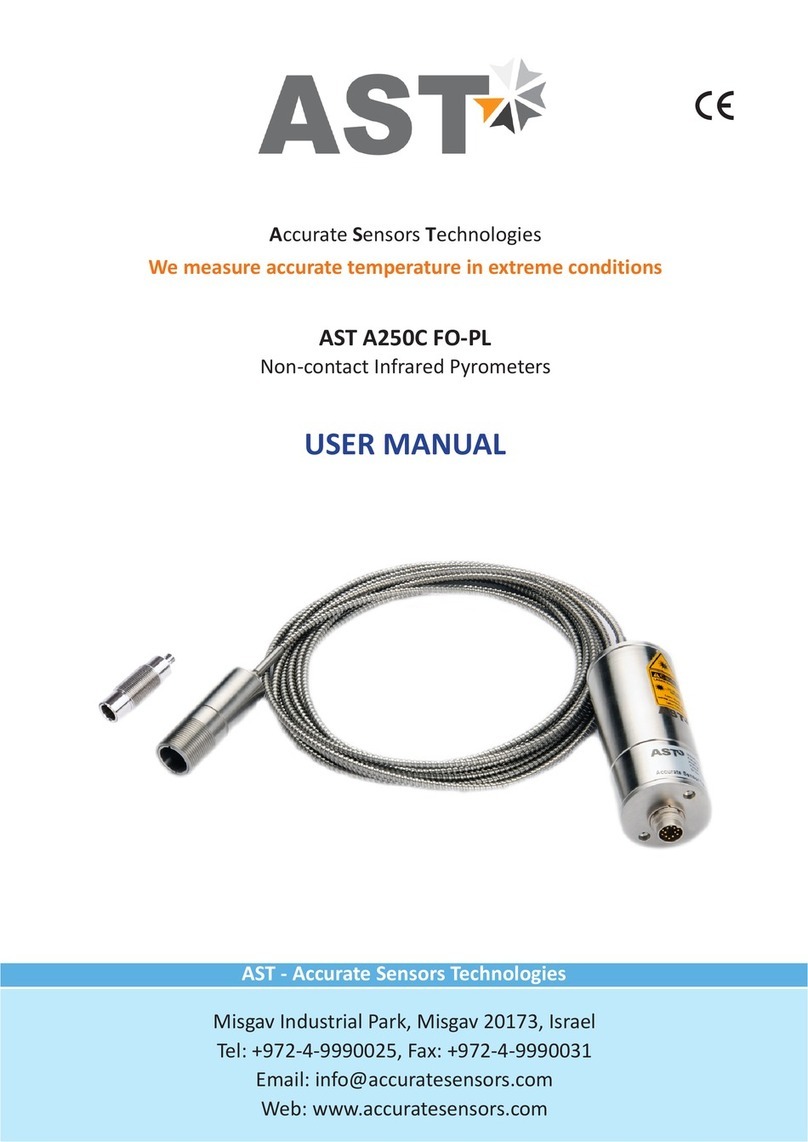
AST
AST A250C FO-PL user manual
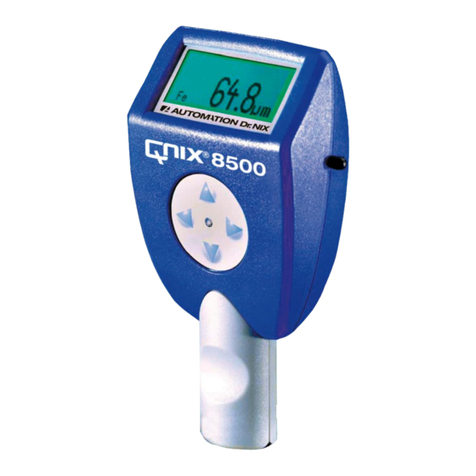
Automation Dr. Nix
Automation Dr. Nix QNix 8500 instruction manual

National Geographic
National Geographic 90-33000 operating instructions

Morehouse
Morehouse C705P instruction manual